Magazino logistics UGV
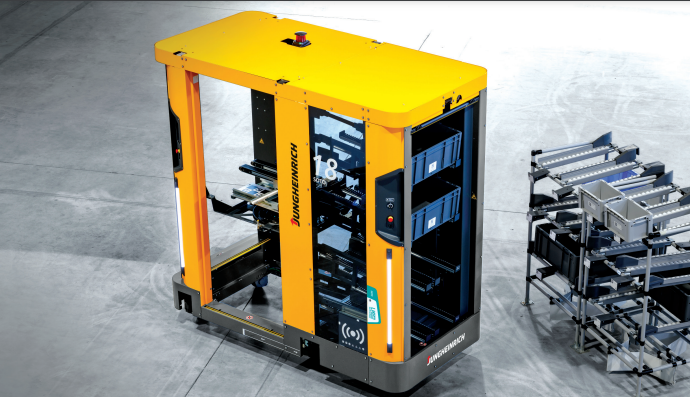
Moving parts
A firm is building this large mobile robot to move large quantities of materials around factories, without major infrastructural needs, as Rory Jackson finds out
The Federal Republic of Germany stands at a turning point, with key political and economic issues that its government parties must contend with. A variety of short and medium-term issues within its borders, as well as threats from further afield, must be countered or outmanoeuvred. But casting shadows over these are a few long-term problems requiring significant, lengthy investment and tangible innovation to reshape Europe’s largest economy into a form that will continue to lead the continent into the 21st century.
Arguably, the biggest problem is an ageing workforce. While this issue affects much of Europe, it is significantly pronounced in Germany, whose employment of 55 to 64-year-olds grew from 62% in 2012 to almost 72% in 2021. When these older staff retire, the country’s labour supply will drop off sharply, and much of the remainder will be needed to care for the retirees, leading to a squeeze on available workers for the vast German factory base.
As a result, there are growing calls to automate factory processes and provide ergonomic relief for the remaining industrial workers from executives who see the potential efficiency gains of autonomous systems, and from labour eyeing more comfortable working conditions.
Munich-based Magazino has a noticeable headstart on this problem, as the indoor uncrewed ground vehicles (UGVs) or autonomous mobile robots (AMRs) it designs and manufactures are already at work in Central European industrial facilities.
The largest is SOTO, which was originally conceived to resolve the lack of autonomous solutions for material logistics between small-parts storage areas and production lines. The overwhelming majority of factories still move small components manually; for instance, with humans driving tug trains that pull small-load carriers.
“Conventional goods-to-person systems can automate those processes, but they require a high initial investment, and come with limited flexibility and scalability, because they need a lot of space, and typically still need humans to pick and place their goods onto whatever transport mechanism the system entails, so provide some ergonomic relief, but they’re not true end-to-end autonomous solutions,” says Magnus Eldevik, product marketing manager at Magazino.
“We wanted to make something that could fulfil end-to-end automation of material supply inside factories – so comprehensive in how it tackled just-in-time deliveries from automated storage spaces to assembly lines that you could completely reorientate your human beings towards other tasks, and give them complete ergonomic relief from material-handling work.”
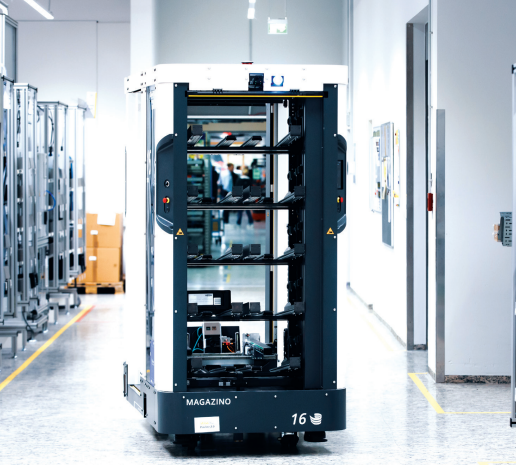
While the cuboid Magazino SOTO is physically imposing, at roughly 2160 mm tall and 2146 mm long, its 1060 mm width means that walkways of just 1.65 m are wide enough for it to move and turn freely, including among people.
Designed to be as large as is feasible to maximise transport capacity and minimise the number of models needed for timely material handling, SOTO’s internal dimensions enable it to carry up to eight 600 x 400 mm Euro containers (VDA 4500 standard industrial stacking boxes that are 280 mm tall – also called Euroboxes, KLTs from the German word KleinLadungsTräger or SLCs, meaning “standard loading containers”) full of small parts, or up to 24 Euro containers measuring either 300 x 200 mm or 400 x 300 mm.
“We’d previously made and successfully sold our TORU UGV, which is smaller than SOTO and aimed at carrying shoeboxes for the fashion industry. But, for SOTO, we’d need to add mechanisms that could interact with both conveyors and shelves,” Eldevik recounts.
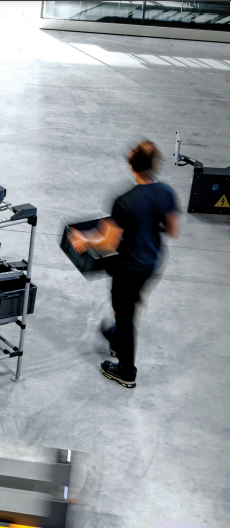
“Factories don’t want to add significant modifications to their production environments, so as well as minimising traffic, SOTO would add to factory floors by handling many KLTs per run. Its gripper mechanism lets it grab SLCs from shelves or flow racks, stow them in its ‘backpack’ and place them into flow racks conveying into assembly lines for personnel or machines to then use in the production process.
“SOTO interacts with inexpensive flow racks made out of plastic or metal. That keeps things simple and scalable, and it’s especially useful for companies that injection-mould parts, because SOTO can swap KLTs in and out of the injection-moulding machines exactly in time with their output cycle times.”
Just as Euro containers were originally standardised for the automotive industry, so is auto manufacturing a particular target application for SOTO.
In early 2024, German multinational MAN Truck & Bus purchased 12 SOTOs for its new engine factory in Nuremberg (with further SOTOs planned for an upcoming battery plant in the same location), having previously been a SOTO pilot customer, along with Magazino’s close partners at ZF. OEMs and Tier 1s across other industries are also applicable markets for the robot.
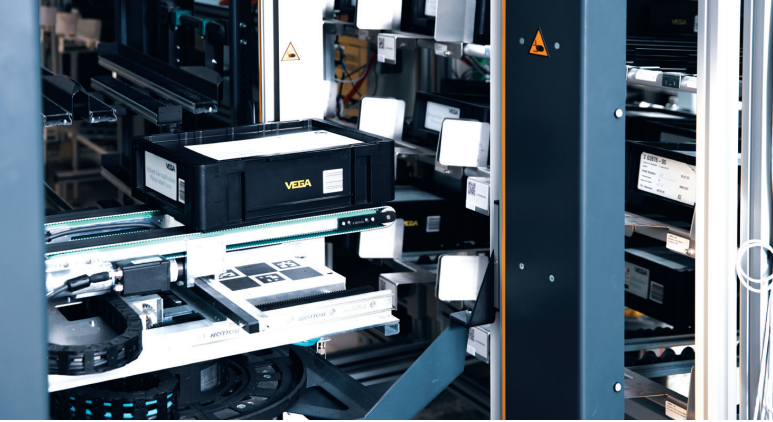
All about grip
SOTO broadly consists of its front ‘gripper’ half and rear ‘backpack’ half atop a flat, square drivebase. The latter is a motorised shelf system that can be configured to accommodate a combination of SLCs, depending on operational requirements. The shelves are designed to tilt safely during transport and retrieval, and they are open to the frontal gripper for easy insertion and retrieval of crates.
As well as being open to the backpack, the gripper section is also open on its front, left and right sides for taking or unloading goods in all three directions. Though called a gripper, it actually functions via a conveyor belt, rubberised and corrugated for high stiction, and mechanised to push outwards for handing off crates onto shelves or pulling boxes onboard from a slight distance.
“It can handle up to 20 kg per SLC, and a total load of 240 kg, so the gripper had to handle 20 kg carriers in different orientations, especially since space-constrained environments won’t always permit payloads to be handed over in a longitudinal way,” Eldevik says.
“Our gripper can therefore pivot objects up to 270° for when crates are stored in different orientations; it also contains a vertical axis mechanism for taking or giving SLCs at different heights. We also have something we call an SLC press inside the ceiling for holding an imperfectly oriented SLC in place, so the gripper can rotate underneath into the correct orientation for putting the container into the backpack.”
A Blaze 3D camera from Basler is mounted at the rear of the gripper, feeding data into an autonomy system developed by Magazino. This system incorporates box-tracking computer-vision algorithms (originally developed for the TORU robot) to track the attitude and, in particular, the distance of boxes relative to the gripper. This information is used to guide the gripper’s movements.
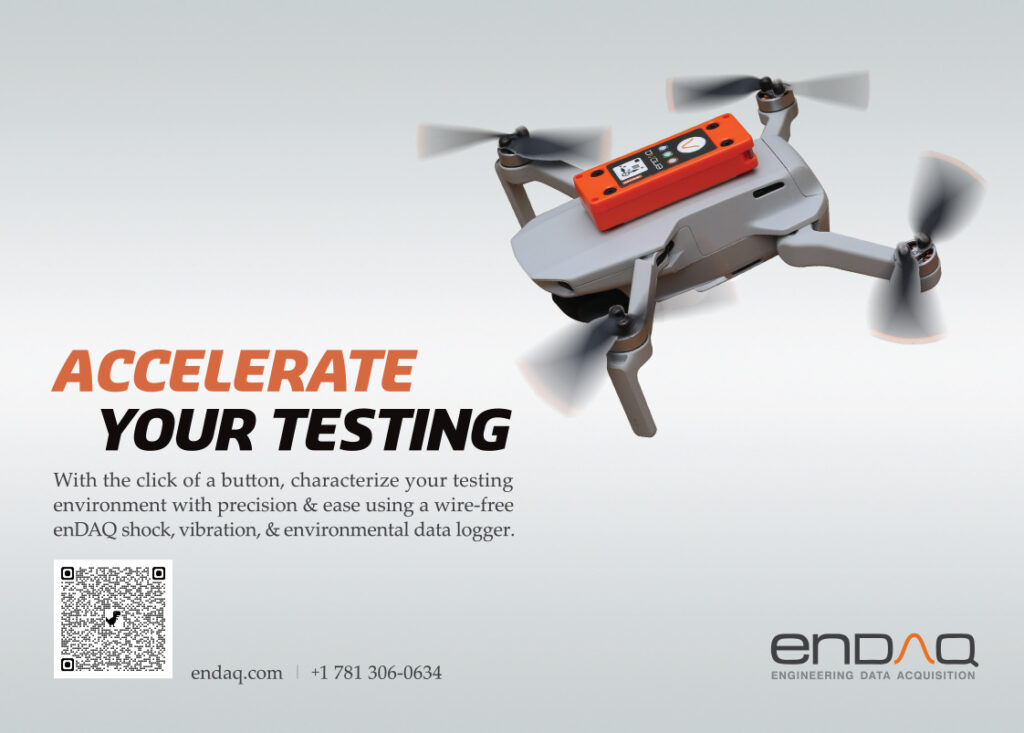
Another Basler Blaze 3D camera in the ceiling looks down onto the gripper, as a key functional watchdog for how securely crates are held and positioned by it, ensuring they will not get stuck inside SOTO, or in conveyor belts or racks.
To identify crates correctly, and ensure exact material tracking and traceability from warehouse to factory, laser scanners first identify the shapes of shelves to validate that SOTO has arrived at the right location. An LED paired with a 2D camera near the front flashes to capture the barcode of the compartment where the SLC is to be placed or picked up for transport.
The 2D camera also tracks QR codes along racks (for feeding parts into assembly lines, or empty crates into refilling systems) to account for correct heights and compartments, according to the requirements of the warehouse management system.
“Those QR codes can be made by us if needed, which we place on special and easily installed adapters that we additively print very inexpensively through our partner network,” Eldevik adds.
The adapter includes a special piece of reflective tape, which SOTO identifies using an additional LED. This ensures the robot is aligned correctly with the shelf, allowing it to safely deactivate the light curtain, which prevents accidents by ensuring no objects or human staff can reach into the robot (this is discussed later).
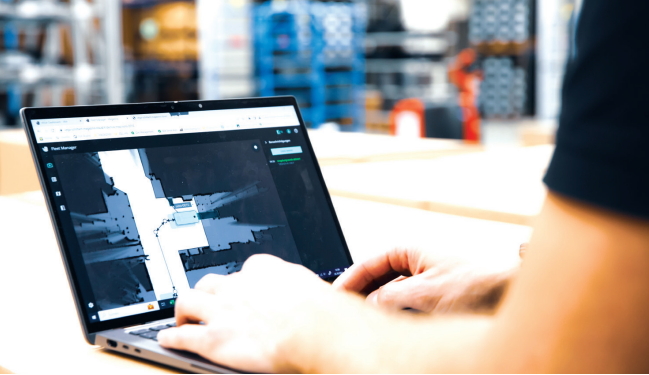
Indoor mapping
Given the importance of integrating SOTOs into existing production environments and logistics processes without any significant modifications, an extendable laser scanner is installed atop the robot body for recording a 3D map of the entire working area. This is done prior to beginning any routine operations to facilitate localisation during work without needing GNSS or installing indoor localisation beacons. It also increases SOTO’s maximum possible height to 2240 mm when the scanner extends to its full reach.
“When SOTO is first delivered to a customer environment, the first step of deployment is to map out that environment,” Eldevik says.
“We provide a handheld remote controller, which is quite similar to a gaming console controller. The onsite technician selects Mapping Mode on the SOTO display, allowing them to manually drive the robot around their production or warehouse area while the map forms on the robot’s display. The laser scanner at the top, as well as additional scanners at the bottom, all record the environment for a highly precise and detailed map.”
The scanners at the bottom record everything up to a 12 cm height off the ground (with their horizontal angle sometimes capturing the exact position of handover stations for SLCs), while the upper scanner records everything up to a 220 cm height. This information is uploaded via wi-fi to Magazino’s proprietary Fleet Manager software, where it is stored. Customers can also access the map to enrich it with their own parameters for refining their logistics processes.
“That could, for example, include specifying the number of layers in a shelf, or the heights of compartments in a shelf, or specifying whether something is a stationary shelf or a conveyor,” Eldevik says.
“You can also add particular waypoints that you want the robots to take; for instance, avoiding areas where human foot traffic is highest or driving around certain objects on their left- or right-hand side, and other safety-related actions, such as specifying zones where its speed should reduce to a minimum or where it simply shouldn’t go at all.
“When in doubt, the robot will orient itself towards the centre of the driving graph in any corridor it is allowed to follow, per our programming, to maintain predictable driving behaviour. Naturally, they can specify parking spaces for when they’re waiting for tasks or for traffic to clear up, and charging locations.”
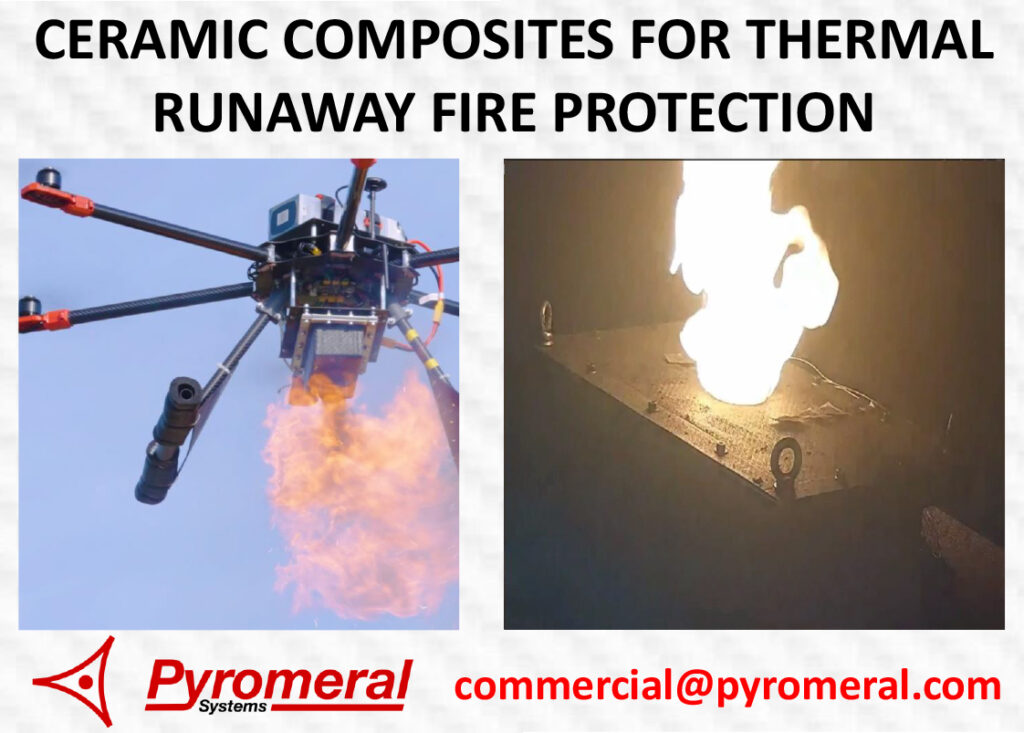
Trusted colleague
Numerous safety certifications have been complied with and achieved in SOTO’s development, and Magazino has implemented some unique functional safety features into its operation.
For one, the openings at the gripper’s front, left and rear are equipped with light curtains (based on NIR sensors), such that if anyone reaches through them, both the gripper and the drivebase, and every one of SOTO’s mechanisms ceases operation. The incident is logged internally as a ‘safety event’, and a worker must acknowledge it on one of SOTO’s touchscreens (positioned at front and rear at roughly face height) before it can continue working.
“In addition to the light curtains, the laser scanners around the base of the robot create a 360° safety field around it, which determine how fast SOTO can move, while front and rear 3D cameras atop the robot use machine vision to identify human beings and other obstacles in its surroundings,” Eldevik explains.
“Using point-cloud technology to granularly analyse movement and object distances, SOTO can drive around obstacles within the predefined parameters of where it is allowed to navigate in the production environment. If the space is too constrained it will slow down and wait for the traffic to clear.”
If there are no people around SOTO, it can drive at its full, 1.5 m/s speed, but as an irregular object or a person gets closer it will reduce its speed and fully stop if it gets too close.
As indicated, a minimum travelling width of 1650 mm is needed for SOTO to be permitted to move safely by its own autonomy system; any less than that and it holds position. When close to the minimum movement space, the robot will go at only 0.3 m/s – at least 2510 mm of space is needed for maximum speed.
Eldevik notes that choosing and configuring the touchscreens was safety-critical, both for interacting with the robot (when the safety system is triggered) and for giving clear graphical indications of the robot’s status to those nearby.
“At any given time, personnel can look at either screen and see what tasks the SOTO is presently completing, and which tasks are scheduled for the near future, and if there’s any issue, a tutorial alert flashes on the screen, telling people exactly what they need to do in a pictorial format to rectify the error,” he says.
“That ensures trained customer staff can take appropriate action and there’s no interruption to process flows in the production environment. We really wanted to make sure no manufacturer or warehouse would need to wait for a Magazino technician to come along and operate the robot. We and our customers needed their trained personnel to rectify any errors and ensure SOTO can keep operating efficiently.”
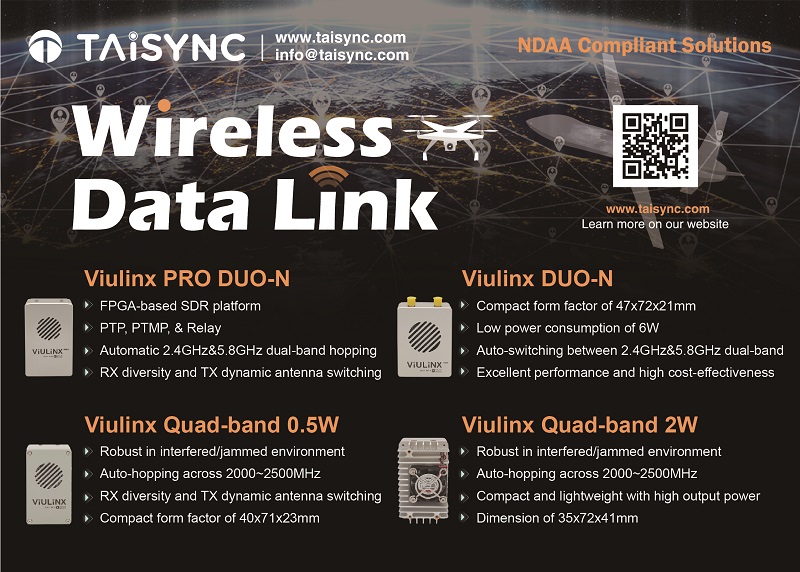
Electric eight
Despite the high-power nature of its heavy material movement application, SOTO has been designed from the outset as a fully electric solution, which enables the precise, digital control needed for all its movements, as well as preventing any exhaust emissions in the confined, indoor spaces in which it is intended to function.
The battery pack onboard the SOTO contains eight Li-ion modules, each being a 25.6 V device storing up to 21 Ah of energy, resulting in total vehicle energy capacity of 168 Ah. The battery design comes with a nominal lifespan of 8000 charge/discharge cycles.
Recharging cycles are carried out using inductive charging stations, chosen to further the practical autonomy of the SOTO vehicles. Inductive chargers eliminate the need for humans to physically approach and plug/unplug charging connectors for every recharging session, and present less of a safety concern than the electrical exposure inherent to automated conductive charging.
Inductive charging stations are installed in locations and quantities per the end-user’s specifications. To recharge SOTO from empty to full takes 1.6 hours (96 minutes). Compared with its operating endurance of eight hours, the company points out that this gives a 5:1 ratio of operation versus downtime – a statistic often used in combination with SLC throughput to inform the number of SOTOs on a factory floor if the customer wants to guarantee a rotation of units working at any given time per eight-hour shift over a 24-hour cycle.
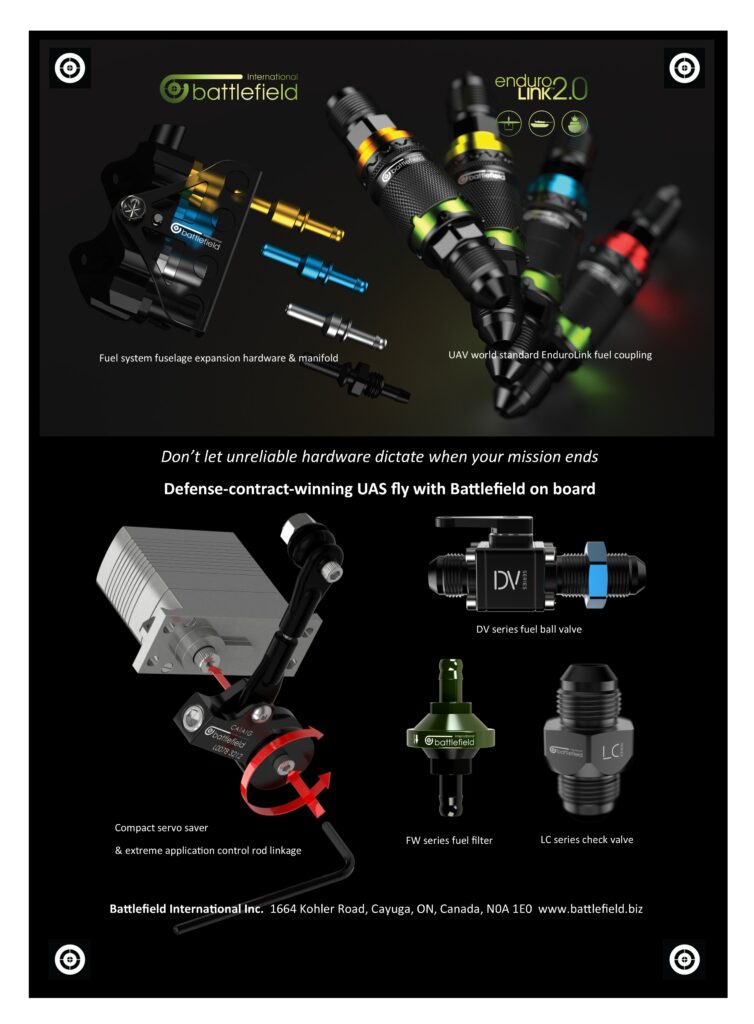
Argo cargo
With this, Magazino usually achieves an ROI of under three years in a two-shift operation in western EU countries, as well as roughly 60% cost savings on the customer’s part.
“But, even more important for us than choosing safe and energy-efficient batteries was the concept of the drivebase,” Eldevik says.
“It was critical that the robot could be engineered with an omnidirectional driving capability, because we knew SOTO would need to be able to manoeuvre through spaces that were narrow relative to its size. It would also need flexibility in how it could dock to different kinds of shelves and conveyors, including the capacity for sideways movement, for docking and transferring materials using its two side windows, and the gripper’s rotating motion.
“That could only be achieved through omnidirectional driving. If you have differential steering, then you actually increase the minimum space needed for movement by a factor similar to that of SOTO’s width-to-length ratio – and its length is quite significant.
“On top of that, the fact that SOTOs are meant for moving 240 kg of large SLCs at once – plus its own weight of about 700 kg on average – meant we’d need a very powerful drivebase with the power to move that 940 kg or more from a stationary position, or brake effectively at 1.5 m/s.”
To achieve all these qualities, Magazino integrates the ArgoDrive mobility system from fellow German company ebm-papst Group, which in turn has been configured by Magazino to run on electric motors from industrial BLDC motor manufacturer AS Sämisch (also German).
The drivebase consists of four of ebm-papst’s ArgoDrive wheels, each rated to carry up to 500 kg, so the SOTO drivebase’s maximum capacity is 2000 kg.
An ArgoDrive wheel consists of two electric motors (one of which rotates in the yaw axis, principally for azimuthing the wheel in place without resorting to differential steering) and a gearbox. The latter enables flexible adjustment of output speed, power and direction (forward or reverse) at the wheel, enabling higher power for moving the fully loaded SOTO from a standstill. Perhaps most notably, it connects to both electric motors, such that both can be used for output power.
For added safety, each ArgoDrive contains redundant wheel encoders for consistent speed and distance measurements, as well as safety rated braking and additional sensing systems, and communication via CANopen, EtherCAT or Profinet for real-time diagnostic information on myriad e-motor performance and system-wide health parameters. The wheel itself is designed to be quickly replaceable for easy maintenance.
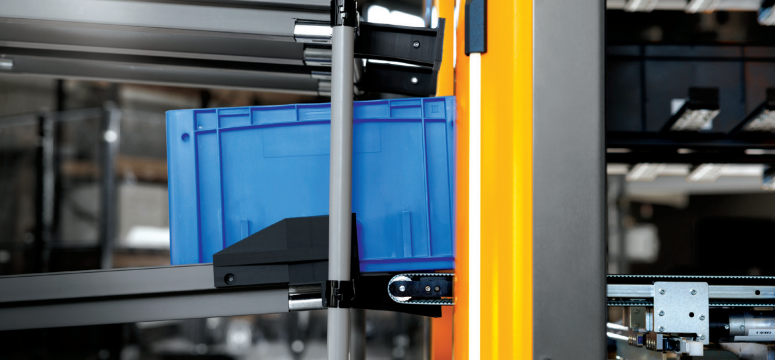
Stretch and grow
During each charging cycle, either Magazino or its customers will perform what is referred to as a “stretching”. This term refers collectively to thorough checks of all hardware and software to ascertain optimal working order.
This includes requesting automated self-checks, for the robot to run tests of its gripper, laser systems, and other mechanical, electric and electronic systems, which are typically done on a daily basis during chargings.
“We also provide a checklist of things the customer needs to check themselves, largely being very basic things like seeing that the gripper and lasers are clean, and performing an occasional cleaning. These components won’t always be working in the cleanest environments ever, so they can get very dusty, but these are checks and wipings that anyone can perform, so nothing demanding,” Eldevik says.
“And now that we’ve been acquired by Jungheinrich Group, we have access to a wide network of field engineers that can visit our customers all over Europe to perform servicings, component exchanges and so forth. They also conduct periodic visits to robot locations for more thorough testing, often including stress tests of the robot to make certain each unit remains capable of the most strenuous tasks its customer might need of it.”
Magazino’s acquisition by Jungheinrich also means the former is now focused on expanding its network across Europe, having previously been confined largely within Germany, Switzerland and Austria.
“That means SOTOs can work in any European country that’s strong in manufacturing, so we’re looking at various primes and OEMs, the UK and the Nordics, so we’re planning to show SOTO and what we’re doing at different trade fairs all over Europe in the year ahead.” Eldevik concludes.
Key specifications
- SOTO
- UGV/AMR
- Fully electric
- Omnidirectional drive
- Length: 2230 mm
- Width: 1060 mm
- Maximum operating height: 2240 mm (laser scanner extended)
- Typical operating height: 2160 mm
- Minimum required floor space for movement: 2500 x 1310 mm
- Maximum speed: 1.5 m/s
- Maximum endurance: eight hours
- Charging time: 96 minutes
- Empty weight: 686-735 kg (depends on backpack configuration; 695 kg default)
- Maximum payload: 200-249 kg (depends on backpack configuration; 240 kg default)
Some key suppliers
- 3D cameras: Basler
- Laser scanners: SICK
- Electric motors: AS Sämisch
- Driving/steering mobility system: ebm-papst Group
UPCOMING EVENTS
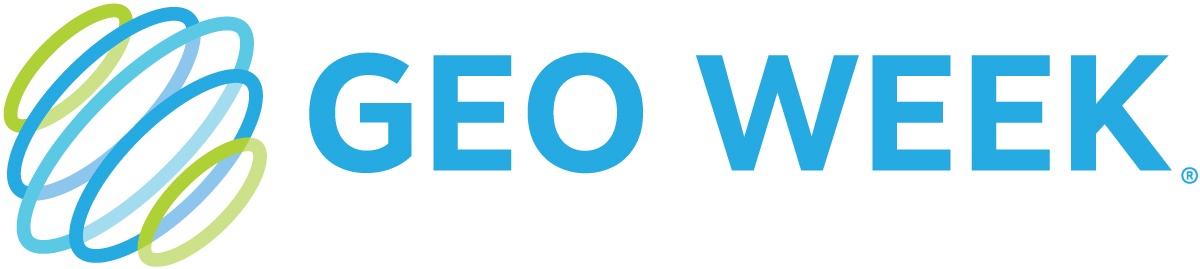
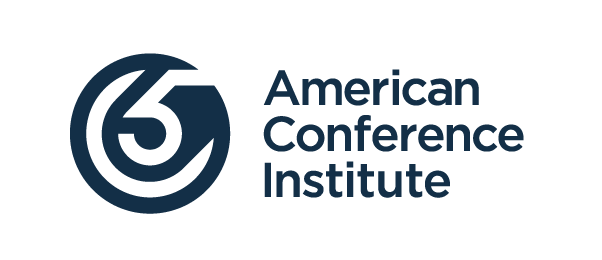
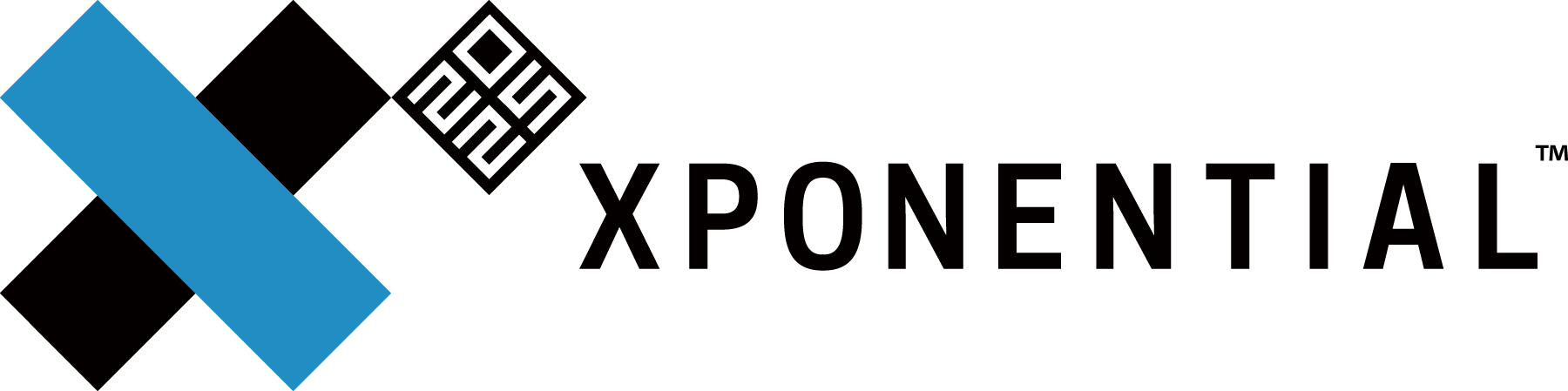
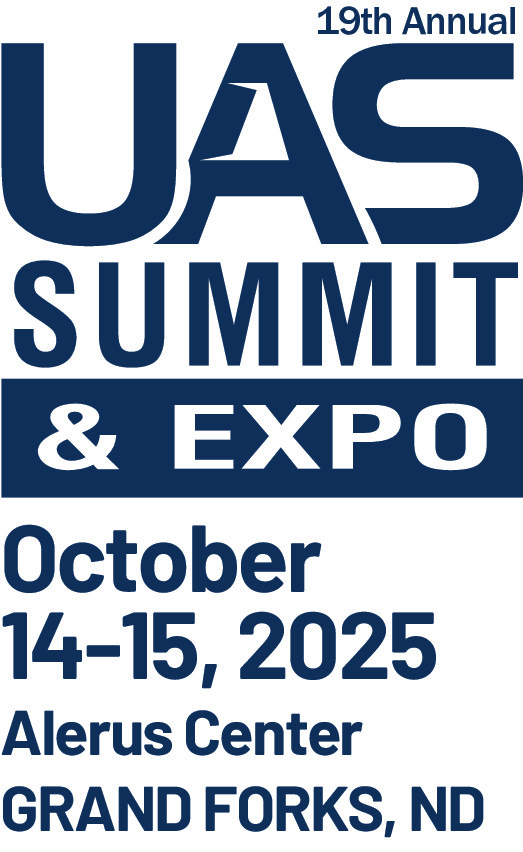
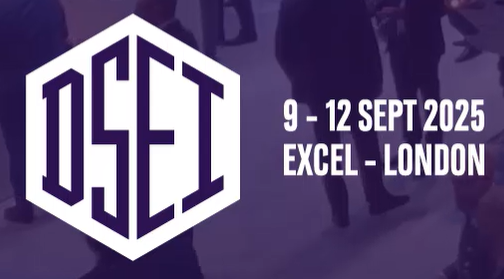
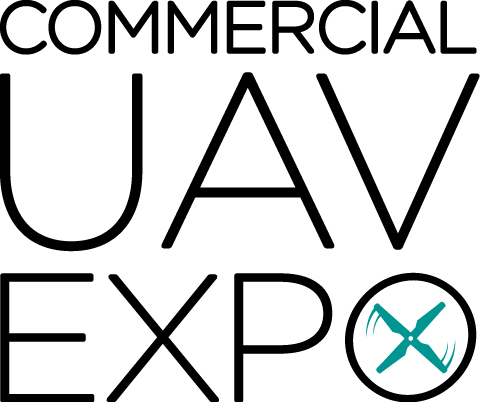
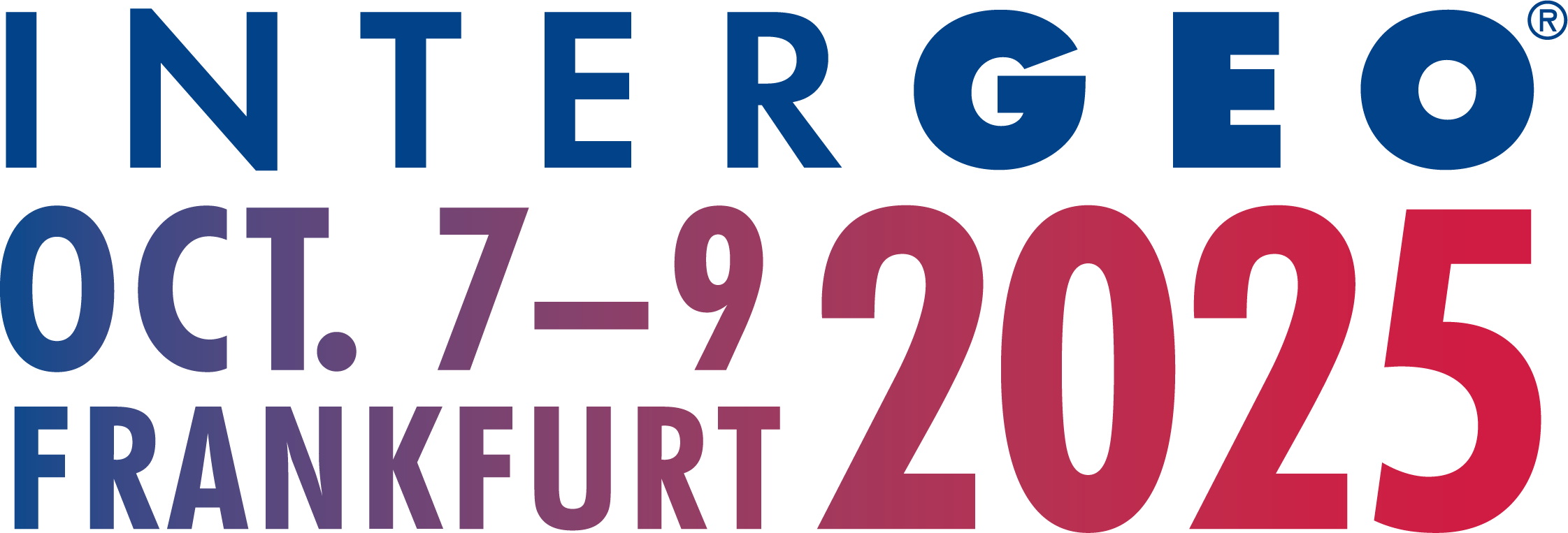
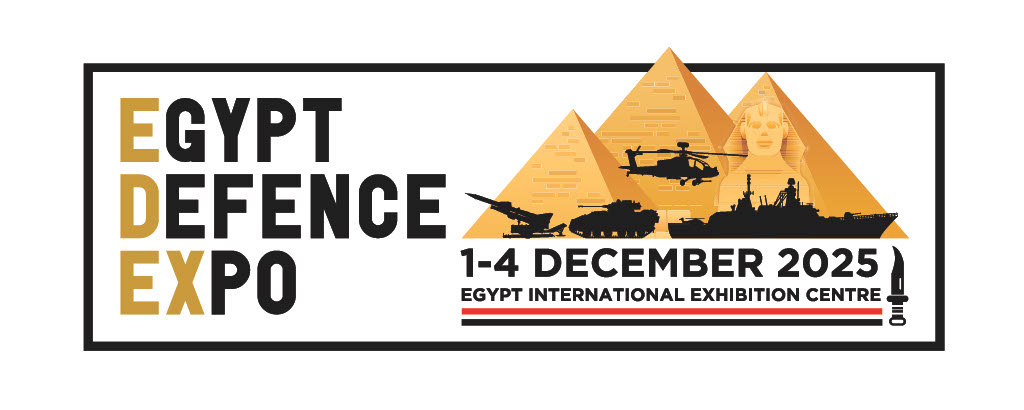
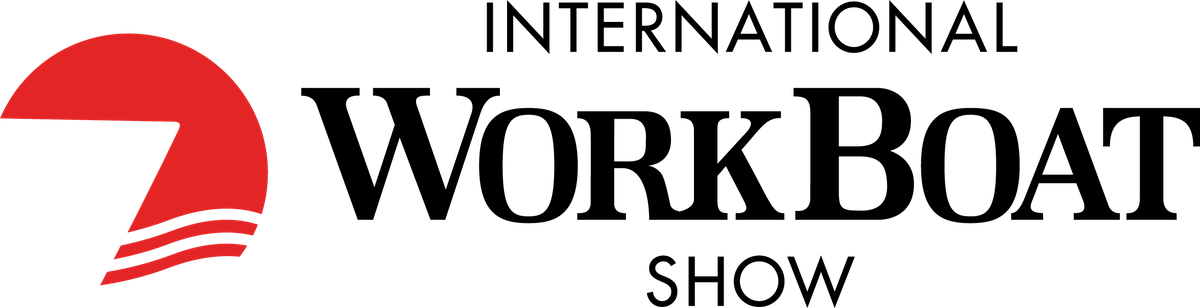
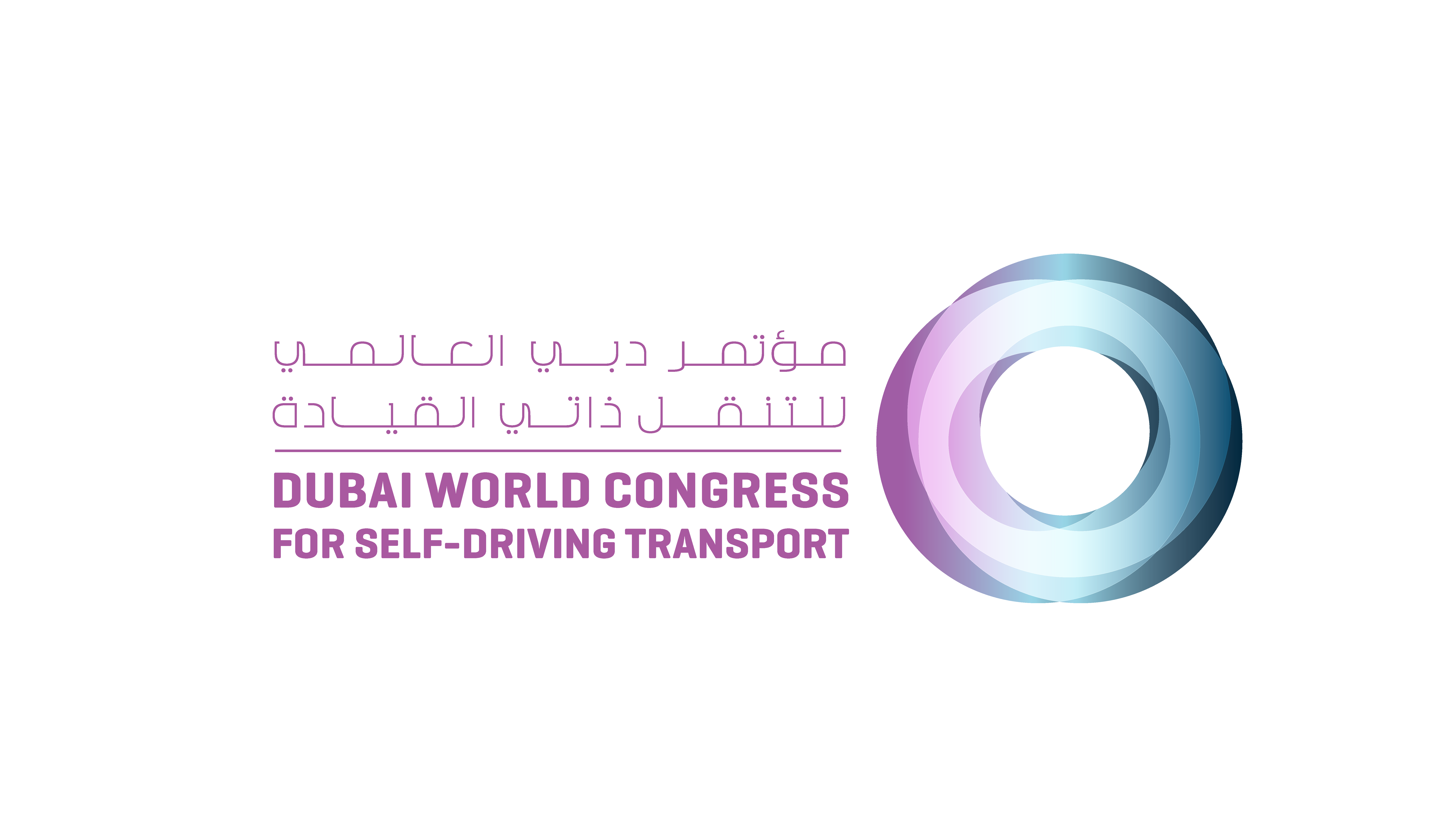
