Launch & recovery
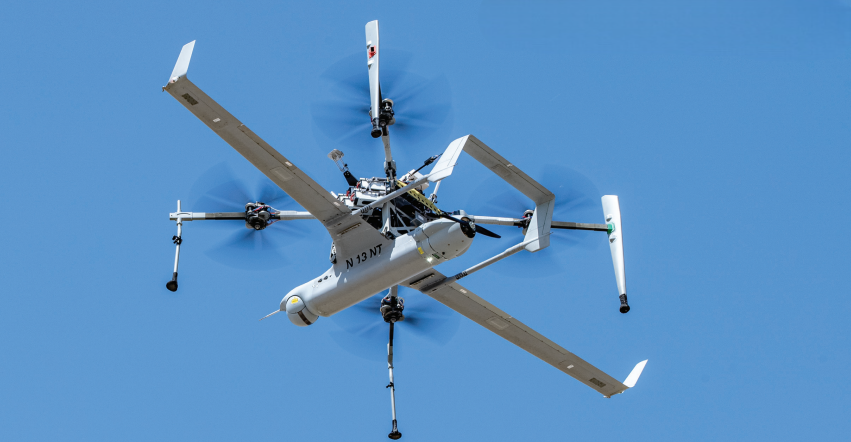
Up, up and away
Rory Jackson looks at the array of launch-and-recovery devices and backup equipment on offer
Despite there being many VTOL-capable UAVs that can take off and land without needing a runway or special equipment, a vast number operating today require and benefit hugely from precision-engineered launch and recovery solutions.
Using external launch-and-recovery equipment enables UAV airframe designers to avoid the need to add lift motors or tiltrotors to wings, reducing maintenance requirements and optimising aerodynamic efficiency. While many end-users will opt for the flexibility of an uncrewed system that requires no external infrastructure, many missions and applications will be made more productive when conducted by a combination of vehicles and static launch-and-recovery systems.
Meanwhile, internal recovery systems such as parachutes and airbags are gaining popularity across a wide range of UAVs, as are several innovations for non-static launch and recovery.
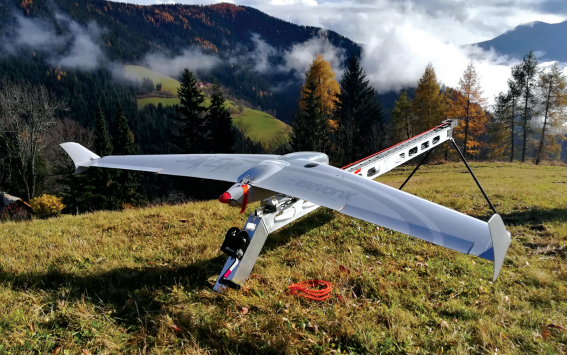
Launch catapults
Pneumatic catapults are an iconic staple of the UAV world, and associated in people’s minds with long-running success stories in highly professional autonomous systems, such as the Insitu ScanEagle. However, they are also among the heaviest launch or recovery items for UAVs, and require quite a bit of training to use, not to mention that teams of three or more people are often needed for them to be assembled in a timely fashion.
The need for more mobile, flexible uncrewed operations has driven a rising supply of more SWaP-optimised, non-pneumatic and often customised catapults to enable more efficient launching and flying of smaller UAVs (especially those weighing less than 30 kg) with minimal logistics and maintenance overheads.
Optimising the catapult to the UAV requires getting numerous specifications right, such as the angle of the launcher rail relative to the ground plane, the amount of launching power (typically measured in kilojoules) the catapult is designed to produce and the range of environmental temperatures it is designed to work in.
Each specification can then depend on numerous factors of the UAV and its mission. The right launch angle, for example, can be linked to the mission’s operating altitude and the capacity for the aircraft to carry sufficient fuel to power climbing as well as the subsequent endurance needed.
Launch power is tied closely to the weight of the UAV and its users’ desired speed at the point of release from the catapult. A 2 kj launcher should work optimally for deploying a 12 kg UAV at around 23 m/s, whereas an 18 kg UAV using something weighing around 4 kj would get about 26 m/s at launch.
In both cases, a somewhat heavier UAV would still probably work with such catapults, with the tradeoff of a slightly slower launch speed, whereas a slightly lighter UAV would get a faster one, but potentially risk damaging the aircraft due to the force with which it is launched.
For a wide range of working temperatures, pneumatics work well, but to build a small catapult either metal springs or elastic slings are typically used as a source of potential energy for launching. These come with different environmental considerations: metallic springs tend to function far better than elastic in very cold environments, particularly as traditional elastics could not be certified to work in -20 C (losing launch power due to thermal contraction).

However, a couple of suppliers have recently come out with the ability to provide elastic that retains its operative qualities down to -20 C. As a result, lightweight, elastic-based catapults weighing 40-60 kg are proliferating throughout the UAV industry, with their transportability enabling more survey work with small, cost-effective, non-VTOL, fixed-wing aircraft, and teams of no more than two people.
Weight is a major concern, especially for infrastructure owners who want to be able to transport everything needed for a day’s survey in a single, small road vehicle. The elastic needed to launch 10-20 kg UAVs tends to weigh around 5 kg, whereas an equivalent metal spring is likely to be 25-35 kg, thus potentially doubling the weight of an existing elastic-powered catapult.
The mechanical design of the catapult bears close optimisation, particularly to ensure the elastic (or other launch material) can stretch to the exact length needed, as the relationship between launching force and length of extension is not linear: stretching a sling to exactly 90% of its optimal length, for instance, will give considerably less than 90% of its optimal launching energy.
For a 2 kj launcher, the elastic must be able to stretch to a length of about 650 mm, whereas for 4 kj it is likely to be stretched to 1100 mm. A company that skimps on such length to provide a more compact and thus outwardly convenient catapult will find its solution fails to give the degree of ‘push’ during takeoff that its end-users might like.
The more force imparted by the energetic device inside the catapult, the more important it is to build it with sufficient housing and ruggedisation. Over time, some cracking in the metal or elastic is inevitable, raising the risk of breakage and debris flying out, which poses an injury hazard, so extra weight in ruggedness can be vital for the safety case. Aluminium remains a predominant choice for catapults for its high tensile strength relative to weight.
Naturally, if catapults can be automated, at least partially, that could remove the risk of injury to humans and make the overall operation more efficient.
While we have yet to see any concept for a UGV mounting a catapult on its back – which could travel to remote areas and catapult-launch a long-range, fixed-wing UAV – some solutions integrate battery- or mains-powered electric winches for automatically pulling their elastics or springs to full tension and then releasing them, all by remote trigger. In contrast, mechanical winches must be operated by hand.
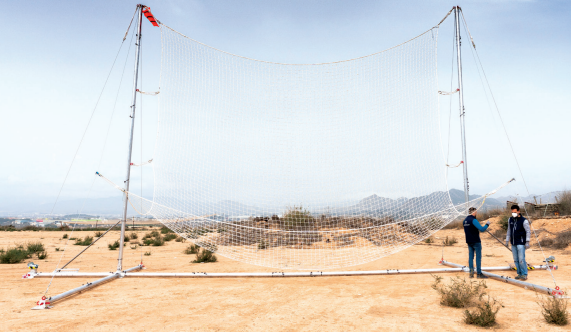
Recovery nets
Given that what goes up must come down, a number of different recovery systems are in use across the industry, and recovery nets continue to be employed for catching UAVs at speed in precisely designated recovery locations.
Much like catapults, nets must be engineered for the force with which a UAV is to be recovered; that being a function of their weight and expected operating speed. The greater these are, the larger or more stringently engineered a net must be in order to sufficiently dissipate the kinetic energy from the aircraft’s movement, such that no damage to either the UAV or the net occurs.
The design of nets must also take into account the height and width of the aircraft. A flying-wing UAV will typically need a recovery net with a flat, wide shape.
Alternately, a UAV with a long, thin fuselage extending ahead of its wings will need a net with thick, vertical straps to enable the fuselage to pass through before the wings are caught; otherwise, all the force of recovery will concentrate at the nose, potentially risking damage to an expensive gimballed payload.
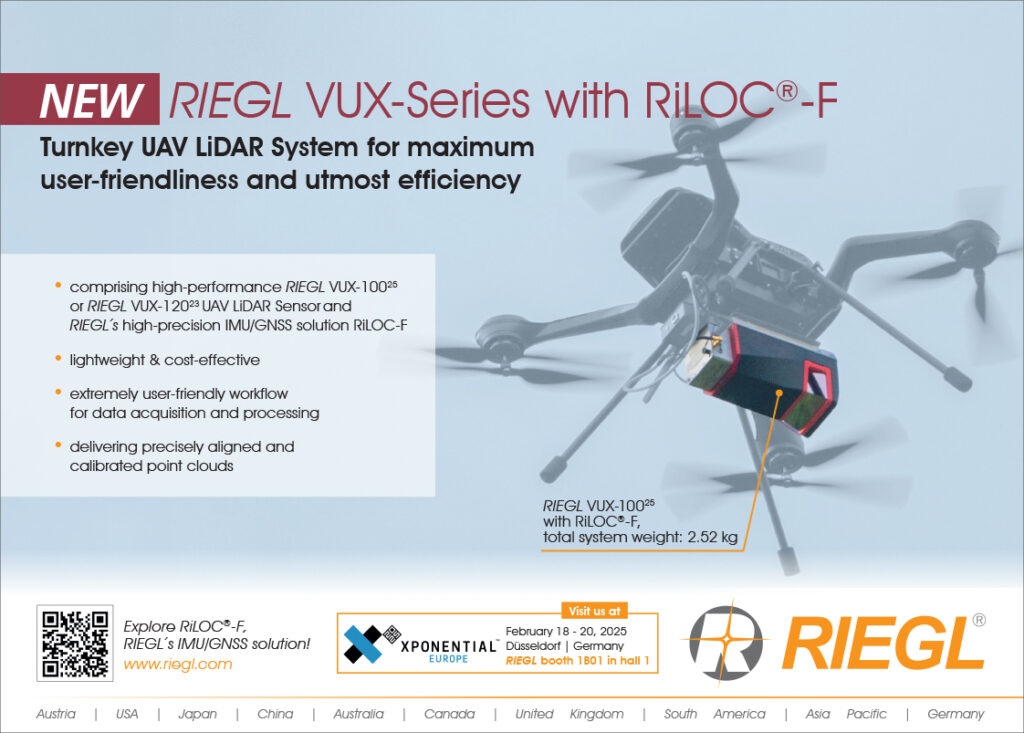
However, as UAVs become larger (to carry more energy and payload per mission), nets risk growing inordinately huge to perform recovery safely. As an alternative to building such unwieldy things, one approach is to design a kind of two-stage, mechanical net.
That design features a fixed base of struts at the ground, with a net above contained in a structure that can flex, with a mode of energy dissipation somewhat analogous to that occurring when a car body crumples during a crash. The net’s flexing allows it to surround the aircraft during recovery, enabling ‘grabbing’ of its wings and other surfaces to prevent the tension being concentrated in one part to the point of breaking.
These collectively comprise the design’s first stage, during which the large, uncrewed aircraft’s speed is greatly diminished, with ballast integrated to prevent the UAV’s impact force from pulling the net away or knocking the net structure over. Next, the upper net structure is permitted to rotate atop its struts, which consumes the UAV’s remaining kinetic energy.
That minimises mechanical stress on both the aircraft and the ground equipment by allowing the energy to dissipate over time, rather than attempting to delete it all at once. Naturally, this two-stage design reduces the size of net needed for a given, large UAV, although balances of width, length, ballast, bearings and other engineering qualities can be customised to suit individual companies and aircraft or operating cases.
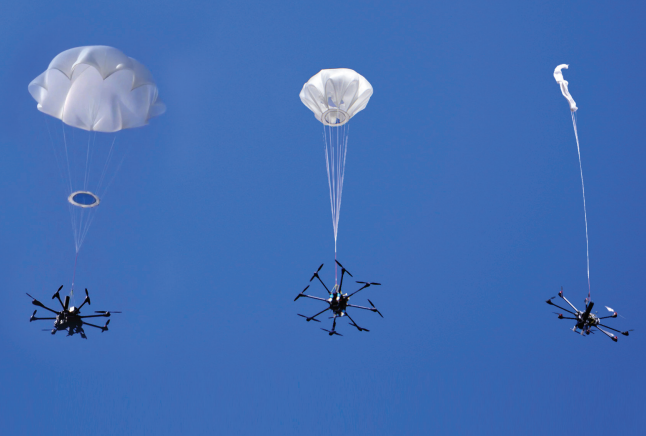
Parachutes
As well as recovery systems external to the uncrewed vehicle, those mounted internally to UAVs – including parachutes, air bags and floatation devices for water landings – remain popular for the significantly gentler landings they provide than belly landings, landing gear, and standing recovery infrastructure such as nets and hooks, despite the weight penalty they place on the aircraft carrying them.
Unlike ground-recovery infrastructure, parachute-type systems can provide an emergency, backup capability following the failure of onboard propulsion systems, including VTOL lift motors integrated to make recovery equipment unnecessary.
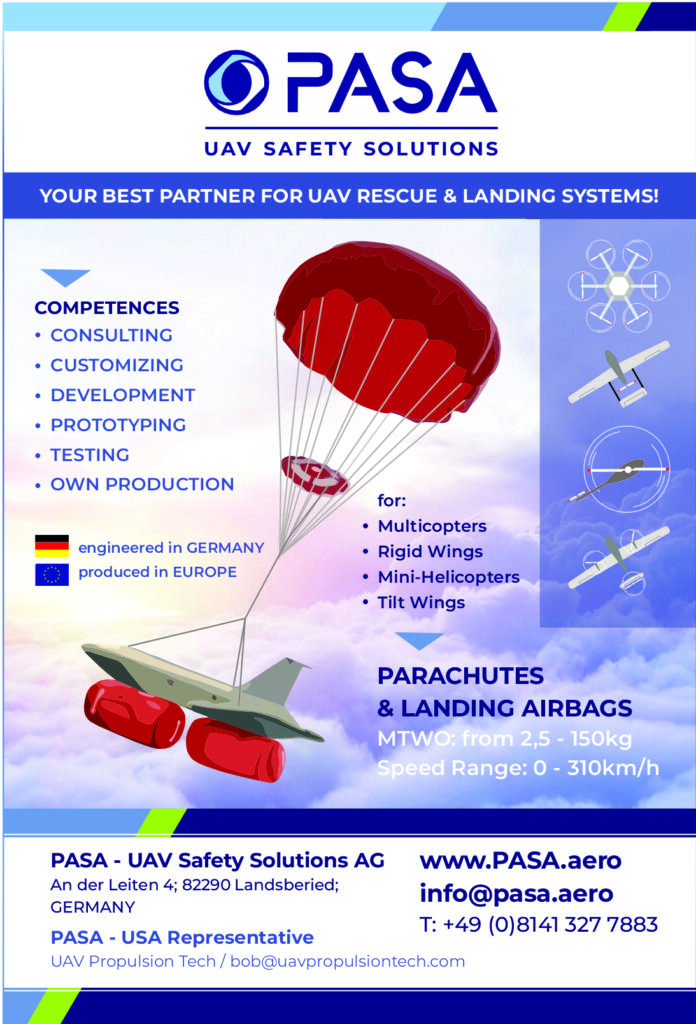
Key design targets for parachutes, airbags and the like include ease of integration (and hence testing and evaluation) into existing airframes to ensure UAV manufacturers or operators can use them in different platforms with a minimum of engineering overheads.
Depending on the use-case and mission environment, parachutes and airbags may be periodically damaged and need replacing for safety reasons. Hence, designing systems for manufacturability is vital as potentially tens of thousands of units are needed across the UAV world today.
Naturally, as a safety-critical component, reliability is vital, across not only the various plastics and fabrics used to capture air but also the launching mechanisms and computing systems within turnkey parachute or airbag products.
All of these important components must be chosen and optimised to work together as a reliable package. To start with, many launch or actuation mechanisms exist for parachutes as they must be able to deploy and rapidly fill with air, as a rotor failure at low altitude could fail to slow the UAV before impact with the ground, or worse, people.
The optimal selection of a launch actuator largely hinges on the size and weight of the UAV to be ferried gently to the ground. At the lower end, springs and elastic bands can work well for parachutes weighing up to a few kilograms, although these can be heavy relative to the deployment energy they release, making their efficiency debatable.
As parachutes get bigger and heavier, it becomes too cumbersome to rely on springs or bands large enough to launch them, so it is increasingly common to resort to pyrotechnic devices, which can pack in considerable force and speed of deployment relative to their weight. These are much like those used in safe, certified automotive airbags and seatbelts, and not harmful explosives.
Speed of deployment is a factor not to be underestimated, particularly as UAVs increasingly perform missions at high altitude, such as surveys of mountains or skyscrapers. In such locations, faster parachute deployment using pyrotechnics can ensure sufficient air catchment – even in low-density air – to prevent impact against high surfaces, which could destroy expensive inspection sensors.
Proving launch processes can be performed in various ways, such as crane tests, where the parachute is deployed from a range of heights to see how well it reduces impact force at increasingly lower dropping altitudes.
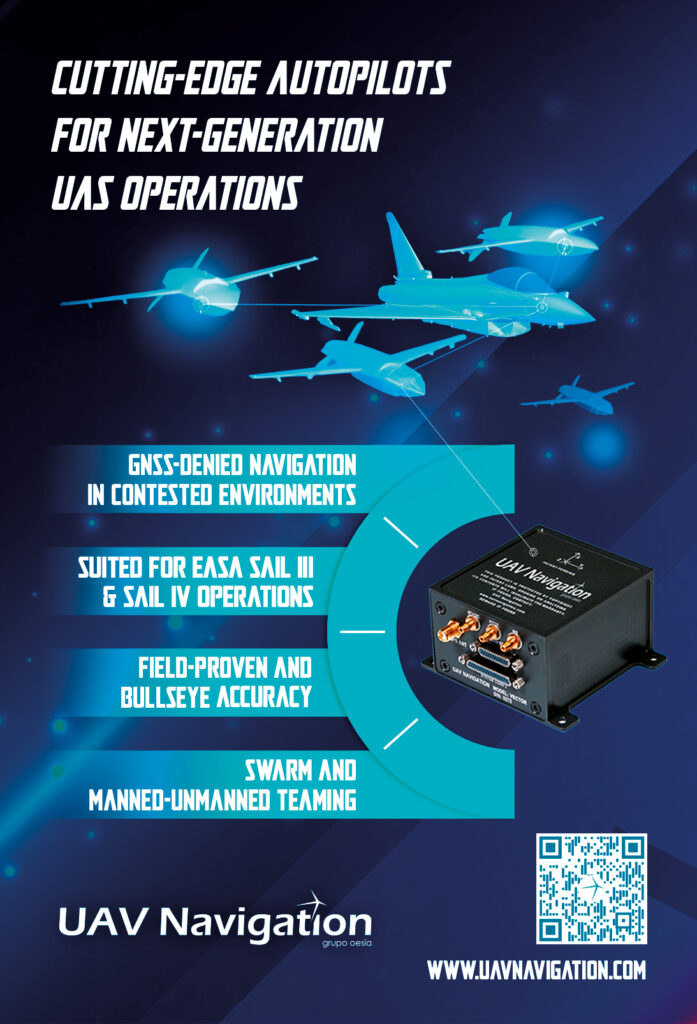
Reaction speed also depends on the computer responsible for managing parachutes or airbags. Many of today’s products come with dedicated control computers to relieve the burden of managing a timing-critical parachute on autopilots or flight controllers, which must already be the right size for overseeing numerous core and auxiliary components across a professional-grade UAV.
A dedicated computer will have optimised hardware and software to carry out deployment reliably and efficiently, with its own IMU for recognising movements indicative of propulsion failure. The computer needs redundancy and the capacity to recognise false positives, lest the parachute be wasted unnecessarily due to an incorrect reading.
Today, modern parachute-type recovery systems are even being trained using AI systems to learn the operational envelopes of the UAVs in which they will be integrated. Rather than having strict binary rules over when a recovery system should or shouldn’t be deployed, it can be flexible and adaptive; for instance, by recognising when the UAV is not falling uncontrollably, despite multiple anomalous sensor readings seeming to suggest it is.
Design and engineering of parachute-type solutions is also guided by certain regulatory standards. ASTM International’s F3322-22 Standard Specification for Small Unmanned Aircraft System parachutes, released in 2018, defines requirements on designing, manufacturing and testing them for the uncrewed aerial space.
That standard is arguably the most important and rigorous for parachutes in this industry, and it requires pushing products to their limits in 40-50 different tests, simulating a wide variety of failures, but ensuring any system passing all of them is output as a highly mature recovery solution.
However, like many UAV components, parachutes themselves cannot be certified. Systems are only certified with platforms, so UAV manufacturers or operators must work with parachute suppliers to gain ASTM certification, as and when that becomes mission-critical.
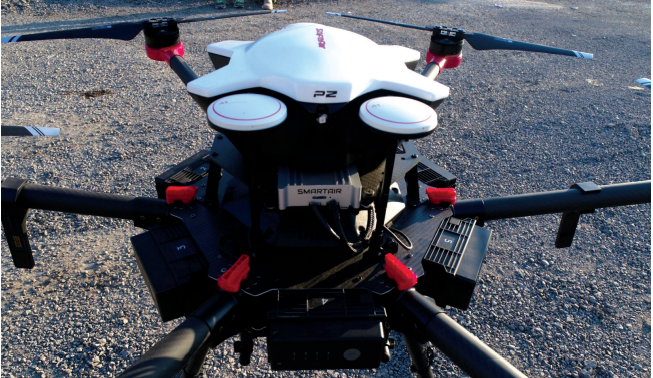
Mobile launch and recovery
Over the course of this publication we have seen a handful of UGV and USV systems that could carry VTOL-capable UAVs, and serve as their takeoff and landing platforms.
However, numerous defence and commercial organisations are taking increasing interest in ways to launch and recover fixed-wing, non-VTOL UAVs on moving vehicles – not only on road vehicles, but also on trains, crewed aircraft and non-carrier vessels with a latent capacity for facilitating valuable uncrewed survey, logistics or emergency response missions.
In such use-cases, both current and proposed, having VTOL UAVs land on moving platforms is frequently unfeasible due to the highly complex aerodynamics involved, so a mobile launch-and-recovery solution for relatively stable fixed-wing drones is the preferred option for many.
One well-known method for airborne release and recovery of fixed-wing UAVs involves using a multirotor aircraft to lift UAVs into the air as a payload, mechanically release them once their engines are at cruising power, and later catch them with a carried recovery hook or tether, potentially at varying distances from the original deployment location.
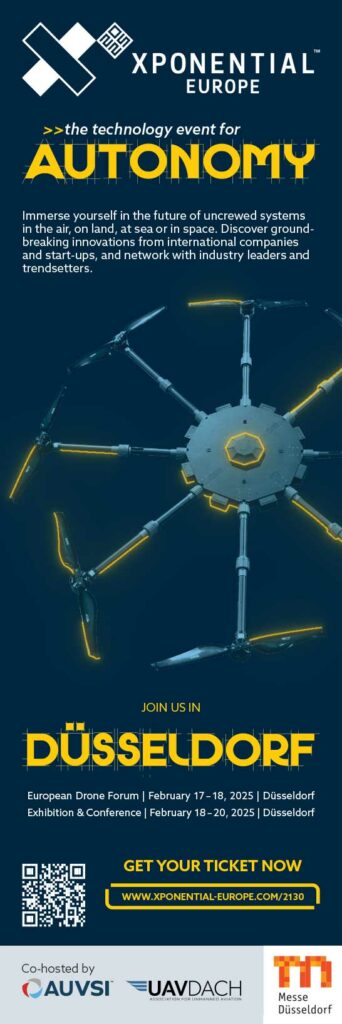
That multirotor solution is built with considerable hardware redundancy, with potentially up to 16 rotors, although much of the software tuning needed to perform this sort of launch and recovery must be embedded in and tailored to the fixed-wing aircraft at the heart of the mission.
The former aircraft must track key timing and altitude stepping points through its internal clock, while the latter must track altitude as well as the activities and attitudes of the former in order to pace its sequences for engine startup, and for release into free, fixed-wing flight.
Hence, significant custom work is needed for the system to work from one UAV to the next, although the system gives enormous advantages in transportability due to it being more collapsible than ground infrastructure, and it also remains far superior than most VTOL-transitioning UAVs in terms of gust and wind rejection when near ground level.
Another approach to mobile launch and recovery – designed particularly for integration on delivery vans, military vehicles and more – consists of an electromechanical sandwich of two horizontal plates, each holding arrays of soft-tipped, telescopic, stainless-steel pins, such that a UAV can fly into the horizontal space between those pins before the plates are actuated to close about the UAV and hold it gently but securely in place.
The pins are electromechanically controlled and tightly monitored to avoid crushing or snapping anything sensitive on the UAV, such as antennas (they have been proven in tests to be able to hold an egg without breaking it), through sensors and the UAV optionally communicating details on its architecture. The pins typically complete their movements within less than a second to avoid generating turbulence.
Prior to that, this launch-and-recovery device senses the incoming UAV, and localises it relative to its own position with sub-millimetre accuracy while broadcasting that localisation information to the UAV in real time.
The UAV, meanwhile, uses a software-based, wraparound layer about its flight controller in order to use that information, and by fusing it with GNSS and inertial data it adjusts its position to within 2 cm accuracy as it comes in for recovery.
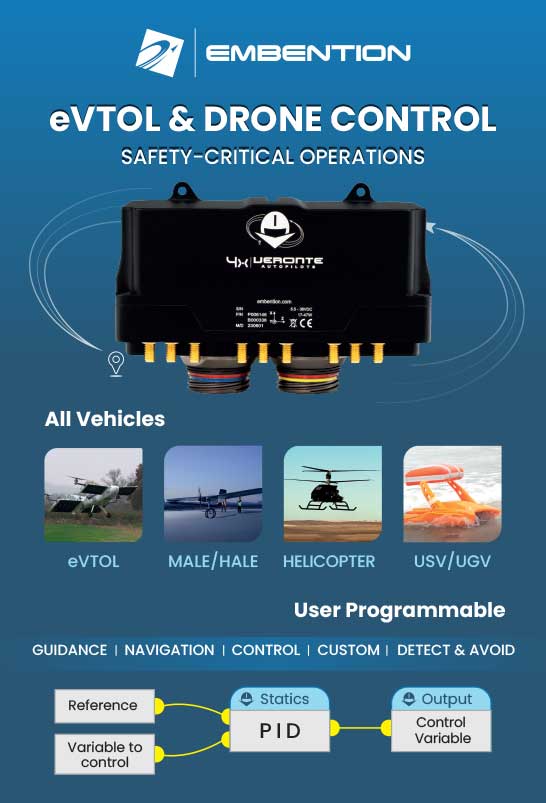
Using this approach, the UAV can be recovered at speeds of over 60 mph without disruption from turbulent air, whether atop a van or under a vast, crewed aircraft. Similarly, the UAV can spool up its engines or motors freely without the pins disturbing them, and the device will release once enough power is achieved to enable a stable free flight.
Several key details of the components are key to the solution working effectively. For one, having a UAV localise itself relative to a moving, constantly changing, local point of reference is a major challenge. Today, this relies on the launch-and-recovery device using high-speed, optical, sensor-based tracking of UAVs with a 100 Hz update rate.
Additionally, the wraparound software layer around the flight controller is fed by data up to 150 Hz from a separate, lightweight companion computer (to minimise interference with end-users’ existing hardware), which performs sensor fusion using data from both the UAV and the recovery system.
The exact timing and selection of pins for closing on the UAV can be based on combined localisation data coming from both the aircraft and the launch-and-recovery system, or solely from the latter if minimising comms is important (as it tends to be for military users).
Key advantages of the system include greatly reducing the launch and recovery costs of last-mile and point-to-point deliveries by UAV (with estimated 85-95% reductions, compared with conventional equipment).
The system can also streamline deliveries by moving sensitive goods from container ships directly to trucks or trains, bypassing harbours and loading bays, and the accidents that sometimes happen there. The UAV may also stow itself in a nearby, appropriately equipped vehicle, rather than returning to its launch point if the former option is a more energy- and time-efficient course of action.
The solution is now tapped for use in various applications, including moving military convoys, commercial package delivery, disaster relief, agriculture, and land and livestock management.
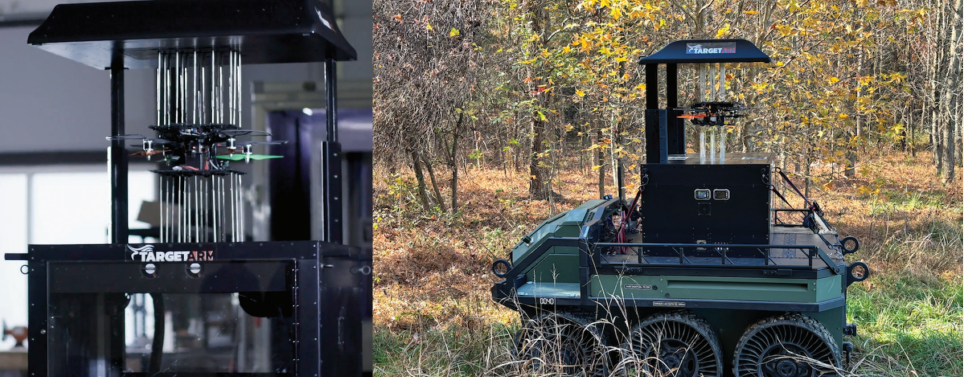
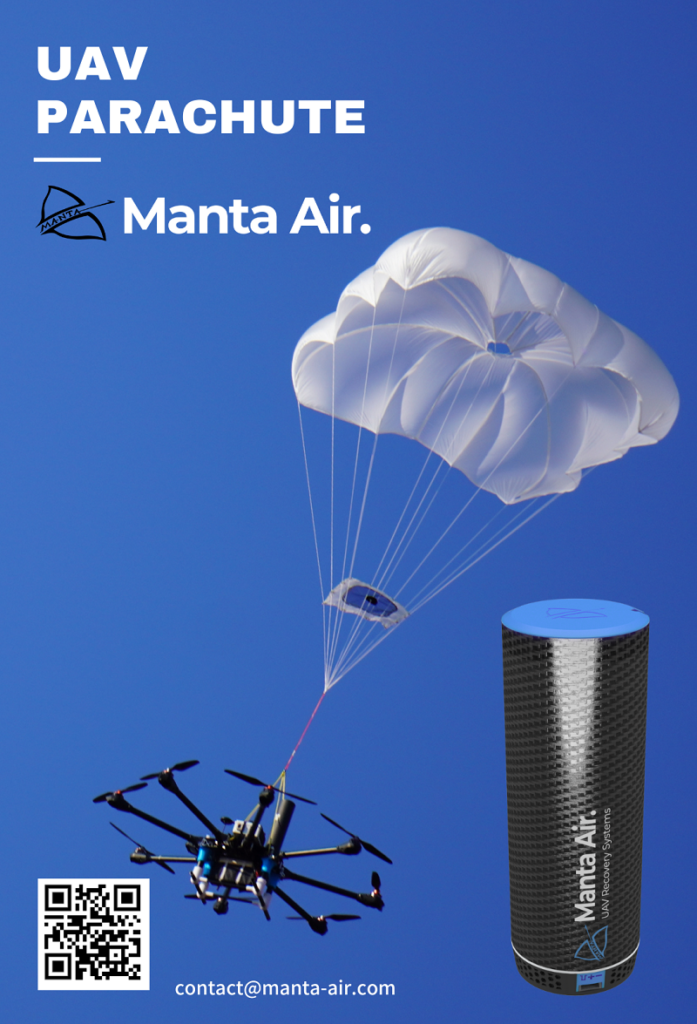
Summary
Despite the many new launch-and-recovery solutions that have appeared over the last decade, it is worth noting that none of the older ones have been made obsolete in a practical sense. Catapults, nets and hooks remain in use across numerous organisations, and the new, innovative forms are making step improvements and optimisations over what came before.
As time goes on, the industry can expect to see an increasing number of solutions that are operated entirely remotely, and subsequently function in a fully automated fashion, such is the trend towards removing human technicians from potentially dull, dirty or dangerous work.
Once that has been achieved, uncrewed motherships for launching and recovering vehicle swarms are likely to proliferate, given the mass survey requirements of ocean floors, wind farms and protected environmental areas, as well as the mass logistical needs of disaster-relief zones, militaries and certain freight operators.
When that day comes, launch-and-recovery system developers can be expected to get in step with today’s autopilot and navigation system companies by producing thousands of units per year to facilitate the connected, autonomous world of tomorrow.
Acknowledgements
Thanks to Jeffrey McChesney and Ryan Bigham of Target Arm, Tomaz Plesec and Matej Meglic of ElevonX, Samuel Bugallo of Embention, Denis Grab of Manta Air and Yuval Gilad of ParaZero.
Some examples of launch-and-recovery systems suppliers
AUSTRIA
Drone Rescue Systems | +43 316 41 81 41 | www.dronerescue.com |
Palfinger Marine | +43 662 4864 0 | www.palfingermarine.com |
CANDA
AVSS – Aerial Vehicles Safety Solutions | – | www.avss.co |
CZECHIA
Galaxy GRS | +420 48 510 44 92 | www.galaxysky.cz |
ESTONIA
ELI | +372 648 0242 | www.eli.ee |
FINLAND
Robonic | – | www.robonic.fi |
FRANCE
Opale Aero System SARL | +33 9 81 14 43 87 | www.opale-parachutes.com |
GERMANY
PASA – UAV Safety Solutions | +49 8141 32 77 883 | www.pasa.aero |
ISRAEL
Manta Air | +972 54 787 5909 | www.manta-air.com |
Parazero | +972 08957 7011 | www.parazero.com |
Sealartec | +972 54 571 9786 | www.sealartec.com |
ITALY
Comelli | +39 521 368 650 | www.comellisrl.com |
NORWAY
Kongsberg Maritime | +47 32 28 50 00 | www.kongsberg.com/maritime |
Vestdavit | +47 55 54 92 00 | www.vestdavit.com |
SLOVENIA
ElevonX | +386 68 69 47 90 | www.elevonx.com |
SPAIN
Aries | +34 915 702 737 | www.aries.com.es |
Embention | +34 965 115 421 | www.embention.com |
UAV Navigation Grupo Oesia | +34 91 657 2723 | www.uavnavigation.com |
USA
Aero Systems West – Parasafe | +1 408 599 2791 | www.aerosystemswest.com |
Aero Telemetry | – | www.aerotelemetry.com |
Butler Parachute Systems | +1 540 342 2501 | www.butlerparachutes.com |
Fruity Chutes | +1 855 462 4883 | www.fruitychutes.com |
FXC Corporation | +1 714 556 7400 | www.fxcguardian.com |
Hood Technology | +1 541 387 2255 | www.hoodtechmechanical.com |
Target Arm | +1 888 500 1976 | www.targetarm.com |
UAV Propulsion Tech | +1 810 441 1457 | www.uavpropulsiontech.com |
UPCOMING EVENTS
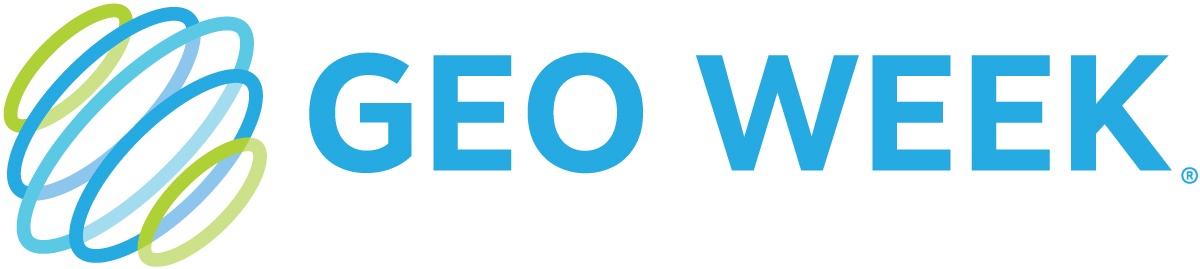
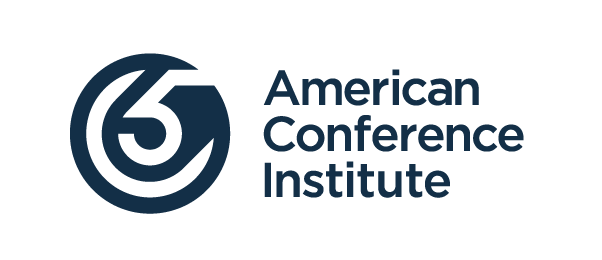
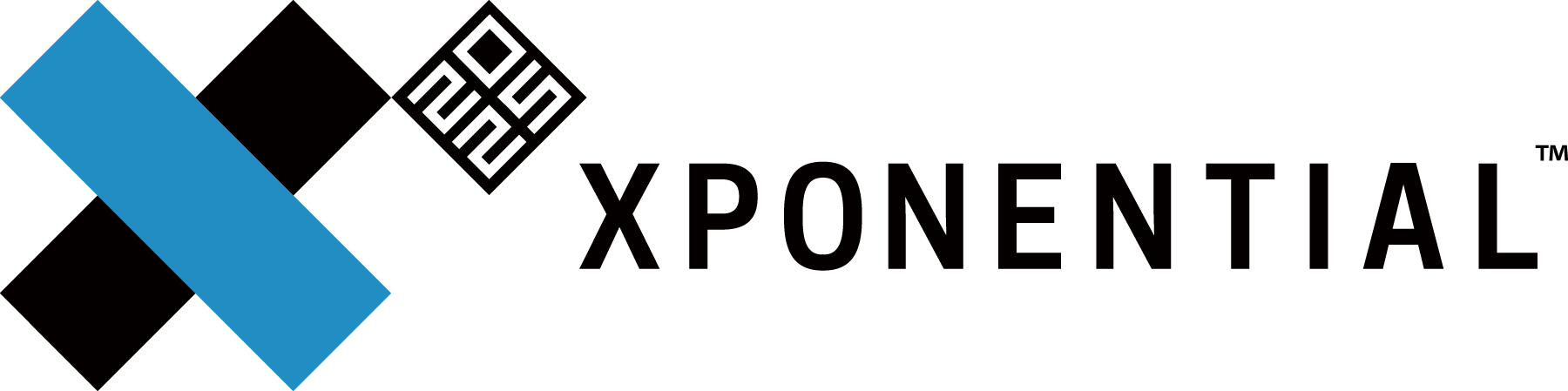
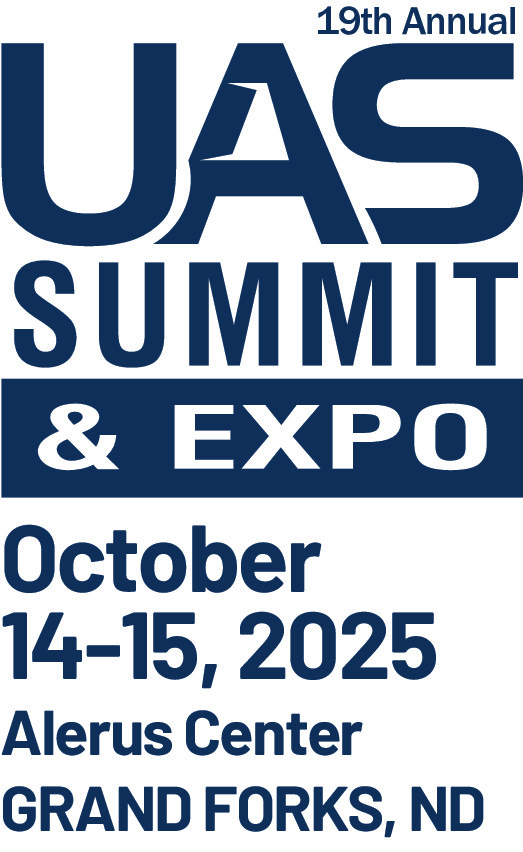
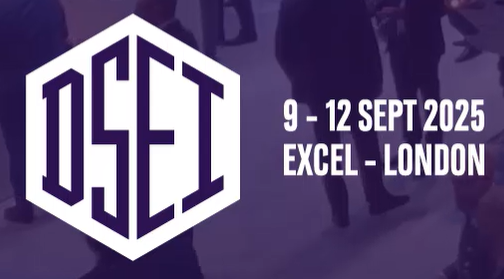
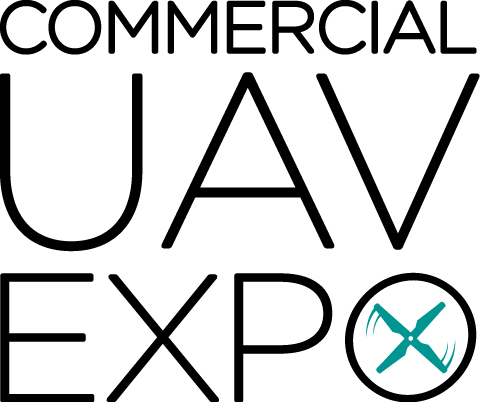
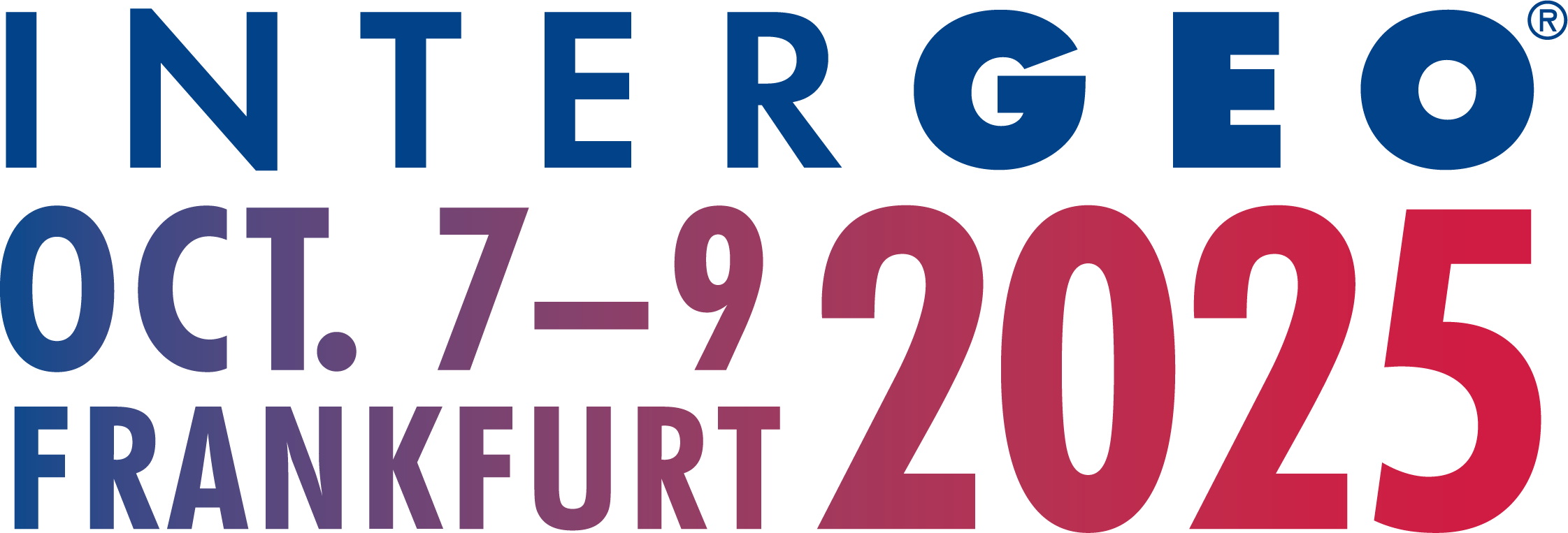
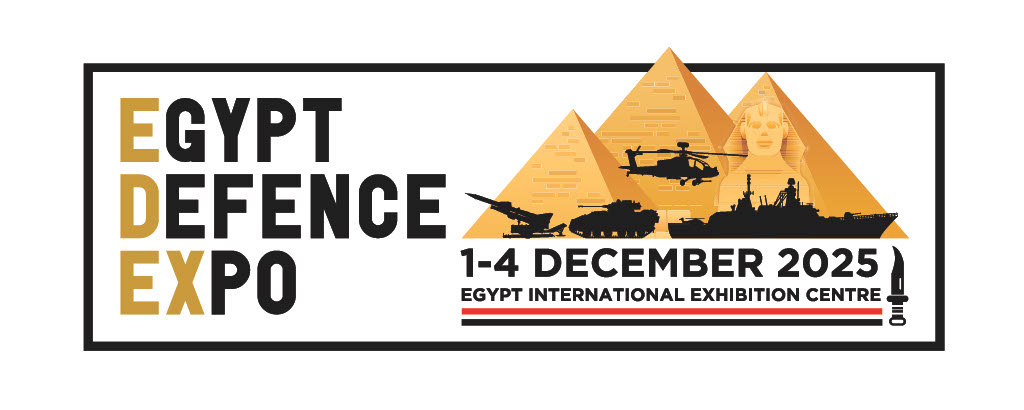
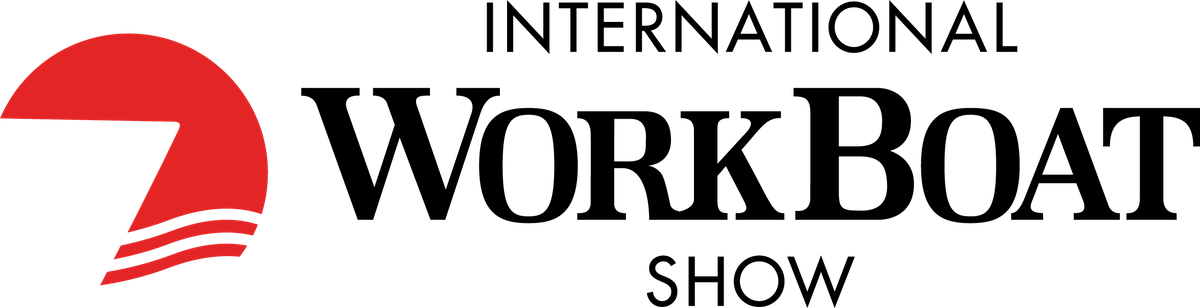
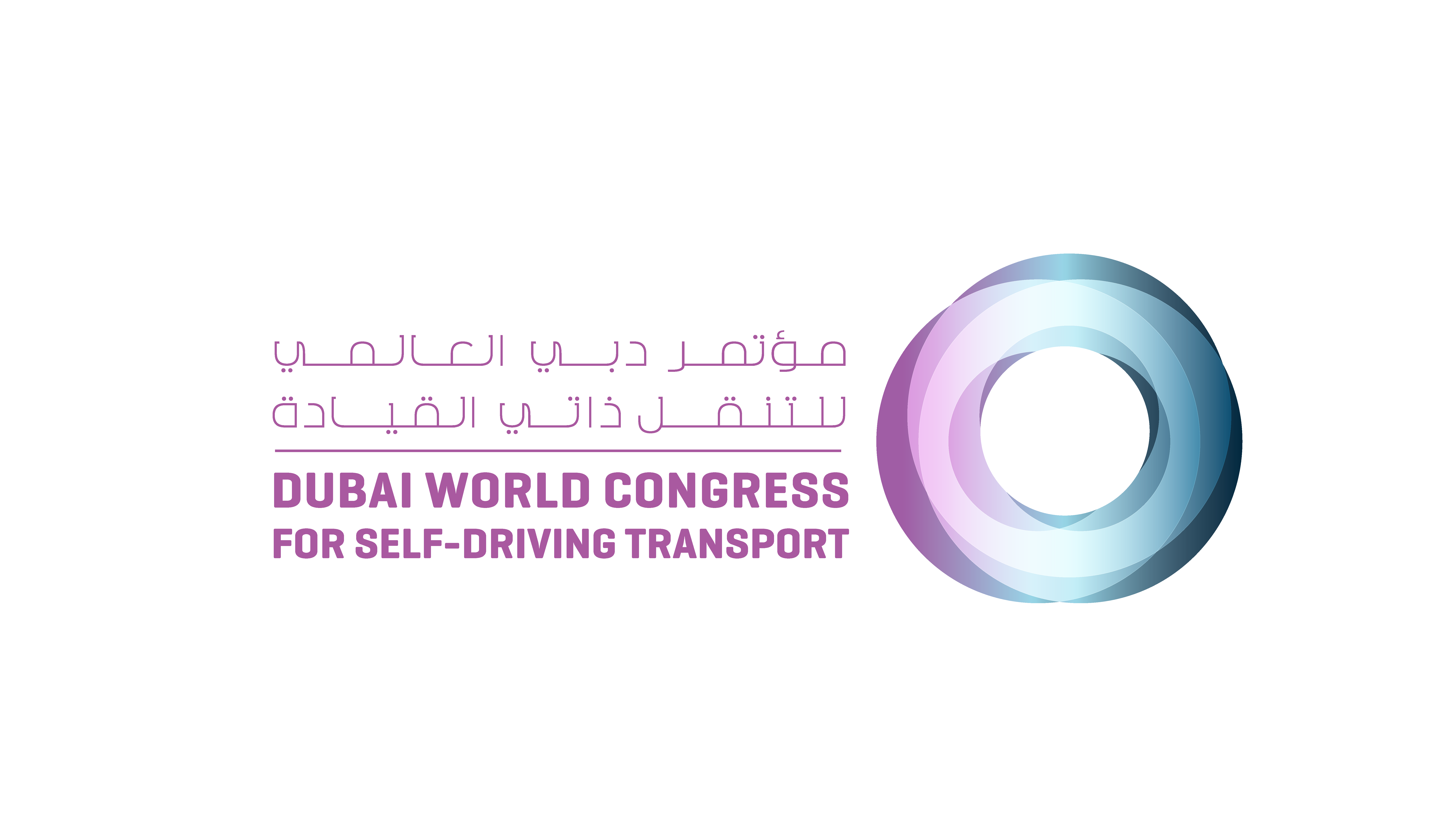

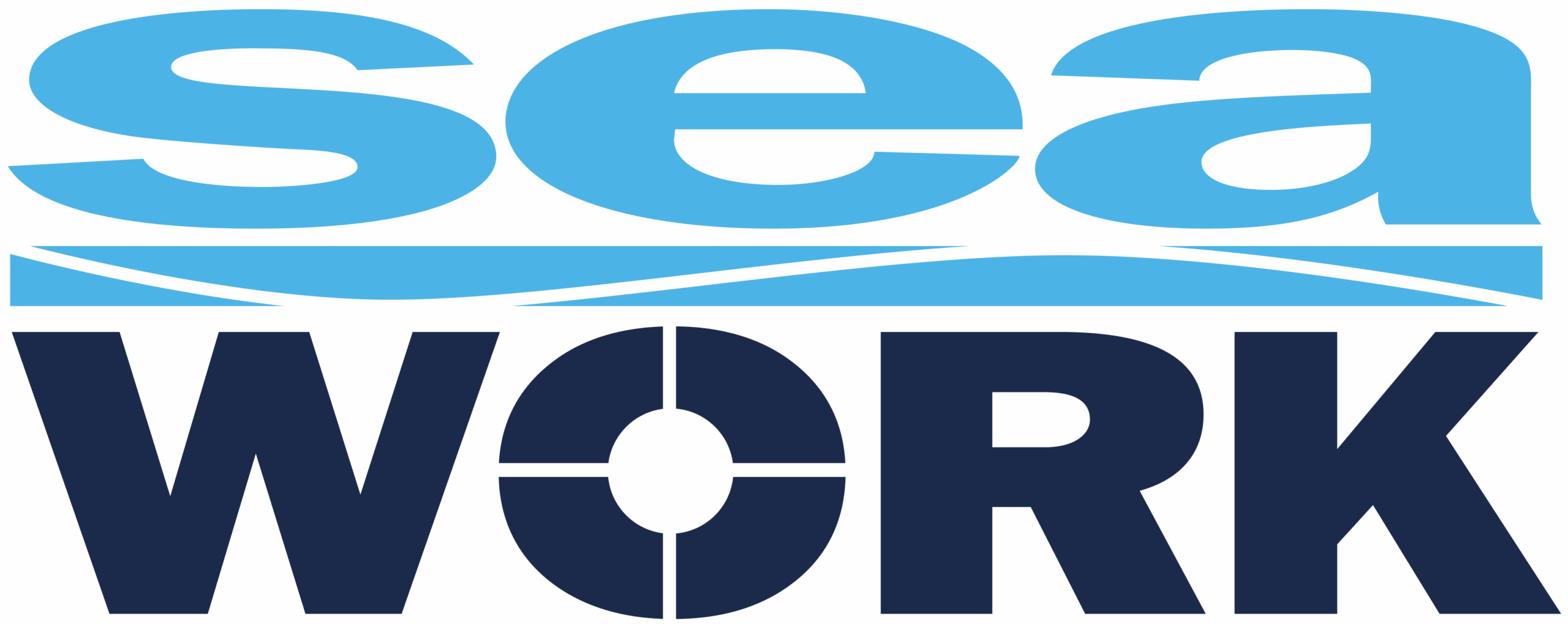