Knightscope K5 robot
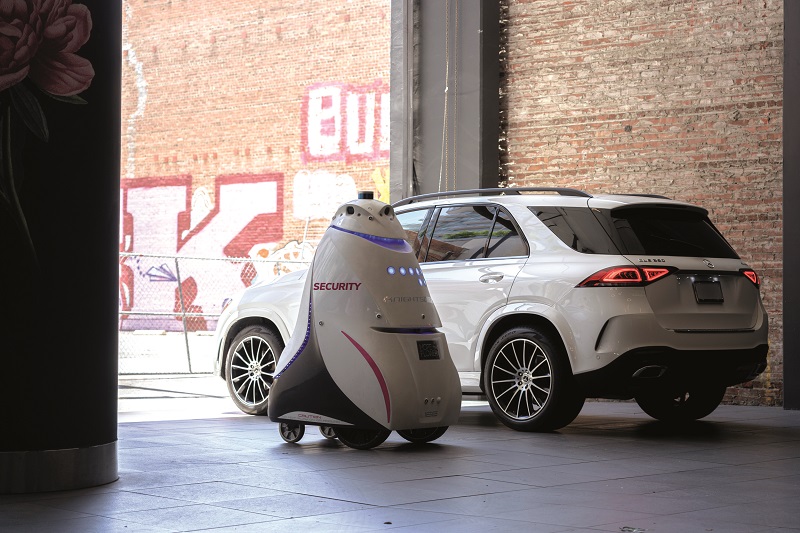
In safe hands
The K5 security robot’s ‘crawl, walk, run’ approach limits the risks associated with autonomous operation. Peter Donaldson reports
Now in its fifth generation, Knightscope’s K5 outdoor autonomous security robot (ASR) stands as a pioneering venture in autonomous security technology, based on merging advanced robotics with a strong public safety ethos.
Launched in 2013 by CEO William (Bill) Santana Li and Stacy Stephens, the company was motivated by a mission to transform public safety in the US, following events such as the Sandy Hook shooting, the Boston Marathon bombing and the 9/11 attacks.
Li, reflecting on these formative moments, emphasises a desire to “make the United States of America the safest country in the world”. This goal underscores Knightscope’s ambition to integrate one million autonomous robots into security networks nationwide, alleviating the demands on human law enforcement, and providing continuous surveillance and response.
He is optimistic about expanding Knightscope’s reach and its portfolio shows over 10,000 machines deployed so far. Its ASR fleet has accumulated more than 2.5 million operational hours in various US locations and climates.
The K5 is part of a family of security robots and other public safety-related sensing technologies, including automated gunshot-detection, laser object-detection and classification devices, and emergency communications systems.
As well as law enforcement, the ASRs are in service in sectors such as banking, healthcare, airports, residential and office complexes, hotels, casinos, car parks and storage facilities. In the summer, Knightscope sealed new contracts and renewals with clients, including Huntington Park Police Department in California, for example, which signed up for its sixth year in August.
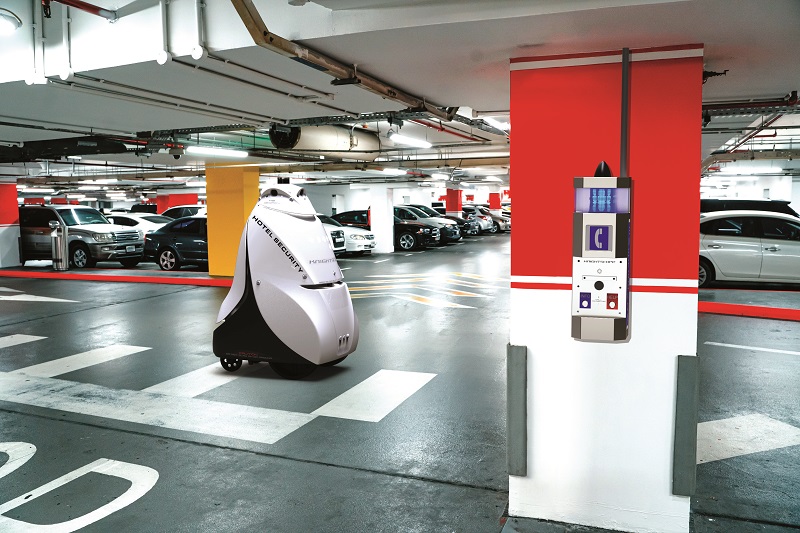
Design and impact
Knightscope’s design philosophy centres on using the K5 as a tangible, visible deterrent to crime; a function that Li believes to be underappreciated outside of public safety circles. The scale, appearance and illumination of the robot underscore its role as an active security presence, intentionally drawing attention while performing patrol and surveillance functions.
In public spaces, the K5 has demonstrated this deterrent capacity, countering criminal activities such as vehicle theft and unauthorised access through its sheer presence. Li likens the robot’s presence to the effect of placing a marked police car in a high-risk area, adding that a significant psychological effect occurs when a potential offender encounters “a 5 ft tall, 400 lb machine… with strobe lights flashing”.
For Knightscope, this focus on deterrence rather than physical force is crucial, and Li stresses that arming its robots is a “bright red line” he will not cross. “If you’re trying to get society to reimagine public safety and you want to build some trust in the technology, the last thing you need to be doing is tasing anyone, shooting anyone, or doing anything on the offensive side.”
He envisions the K5 bridging a gap in US public safety infrastructure, and addressing what he sees as a stark disparity in technological support between military personnel and domestic security agents.
This disparity is “horrifying” when comparing the intelligence and surveillance tools available to a US soldier with those available to the average security guard, who may rely on “a number two pencil and a notepad” to document incidents, he says.
Knightscope’s ASRs are therefore intended to grant “superpowers” to human officers by enhancing situational awareness and actionable intelligence across wide coverage areas without the need for their immediate presence. The K5 can also alleviate workloads by taking over “monotonous computational, heavy work”, Li adds.
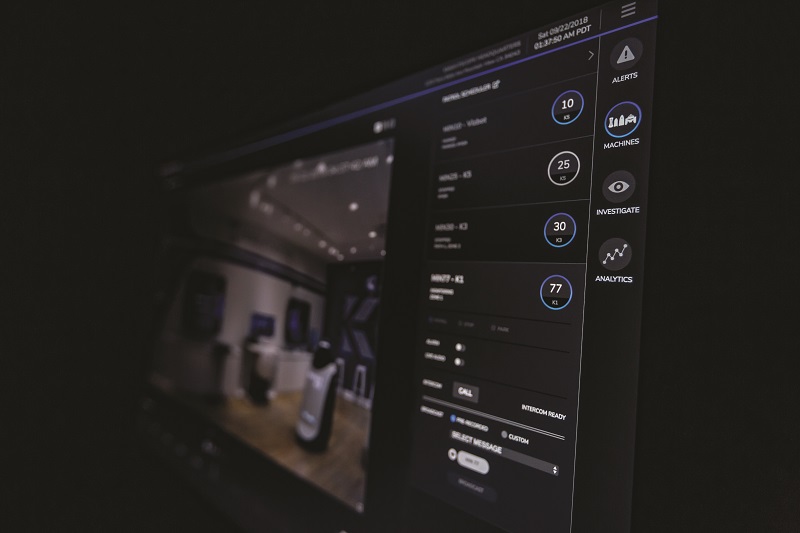
Core capabilities
The K5 operates continuously year-round without human teleoperation or direct control, equating to Level 5 autonomy. This is facilitated through the fusion of advanced sensors and software, artificial intelligence, robotics and EV technologies.
The suite of sensors includes 360o video coverage from four cameras with daylight, low-light and zero-light capabilities, plus four microphones for live audio and a public address system that can put out prerecorded messages, and a text-to-speech facility for a control-centre supervisor.
Three main monitoring strategies have emerged around the K5. First, when contracted to law enforcement agencies, security feeds from the robot are available to 911 dispatchers or assigned officers in real time. Secondly, for private-sector clients, such as apartment complexes, where continuous monitoring is not feasible, the company’s risk and threat exposure (RTX) analysts provide round-the-clock surveillance and support.
Thirdly, the company monitors the health of robots remotely from the Knightscope Security Operations Center (KSOC). Using the KSOC interface, clients can adjust patrol schedules, and direct the robot to park itself or initiate alarms. Clients also have access to a real-time messaging feature, which provides instant communication with Knightscope’s support team, allowing them to address any emerging technical issues in real time. Staff can be alerted to any issues with power levels or battery health, and they can address any necessary maintenance or upgrades.
The KSOC is a browser-based interface that provides access to live HD video streams from the robot’s 360o camera system, recording and storing the video and downloadable files for evidential purposes, plus many other functions, including the automated detection of intruders, alerts to the presence of people in restricted areas and direct communication with them.
The K5’s thermal cameras provide early detection of fires, heat blooms from recently driven vehicles, which can be important in locating suspects, for example, and can detect people concealed in darkness and shadows.
K5 and other machines in Knightscope’s product suite operate on a Machine-as-a-Service (MaaS) model, with clients paying between $650 (£512)and $5,500 (£4,335) per month to deploy ASRs on a full-time basis, Li says.
MaaS includes not just the robot itself, but an entire operational support structure: docking, software upgrades, maintenance and, if desired, the company’s 24/7 RTX service. This model eliminates the need for clients to establish their own technical support, making ASRs more accessible and user-friendly to security-focused organisations.
Li emphasises that this maintenance strategy, embedded in the MaaS concept, is informed by practical field experiences, where theoretically maintenance-free parts sometimes proved otherwise under real-world conditions, as elaborated on later.
Conservative approach
Knightscope’s approach diverges from other models of robotics development by emphasising slower, high-persistence operation rather than striving for high-speed or human-like intelligence. As Li explains, the philosophy follows a model based on gradual advances in speed and complexity. So, rather than designing the robot to function at variable speeds under diverse conditions, the K5 achieves optimal results at a low speed, maximising safety and reliability.
Li’s background as an automotive executive informs his critical perspective on the approach to autonomous vehicle (AV) technology in the robotics industry. He is skeptical of the AV industry’s aggressive push towards high-speed, full autonomy, asserting that the commercial viability of such systems remains uncertain after billions of dollars in investment.
Its approach resembles “the aerospace equivalent of trying to go to Pluto before even visiting the Moon”, focusing on achieving advanced goals without the requisite foundational experience, he says.
Li is more than critical of overambitious robotics projects, particularly where autonomous road vehicles are concerned. “I’m in violent disagreement about the path to commercialise the technology,” he says.
“I think it’s an idiotic assignment to say, hey, I need to put a 4,000 lb uncrewed vehicle on a public road at a random time of day in a random climate with no legal framework, no insurance framework, no safety framework, and please make sure it works 100% of the time and doesn’t kill anyone. I’ve been saying this for 10 years.”
Knightscope’s more conservative philosophy is anchored in creating immediate, revenue-generating solutions that function reliably within defined operational limits. This philosophy has proven effective, positioning the company as one of the few that currently operates at scale with full autonomy.
The K5’s “crawl, walk, run” approach limits the risks associated with autonomous operation, allowing for real-world testing, continuous improvement and the ability to generate a steady revenue. By establishing these realistic boundaries, Knightscope can consistently deliver a practical, functioning system that is useful and trustworthy, aligning with public safety requirements rather than speculative technical aspirations, Li says.
Public perception
A significant element of Knightscope’s strategy involves public education to counteract misperceptions about robotic technology in security. Li acknowledges that while the K5’s large and mobile presence deters crime, it also evokes a certain unease in a public conditioned by fictional portrayals of robots as dangerous or invasive.
Knightscope emphasises transparency and accessibility in its deployment of the K5, which is not only unarmed but limited in its operational scope. Li believes that by demystifying the K5’s capabilities and purpose, Knightscope can foster public trust and increase the adoption of security robotics.
For Li, these fears resemble the public concerns that accompanied the introduction of ATMs, where speculation initially cast doubt on the technology’s viability. Over time, as the K5 and other ASRs continue to operate safely and effectively, he anticipates that skepticism to wane.
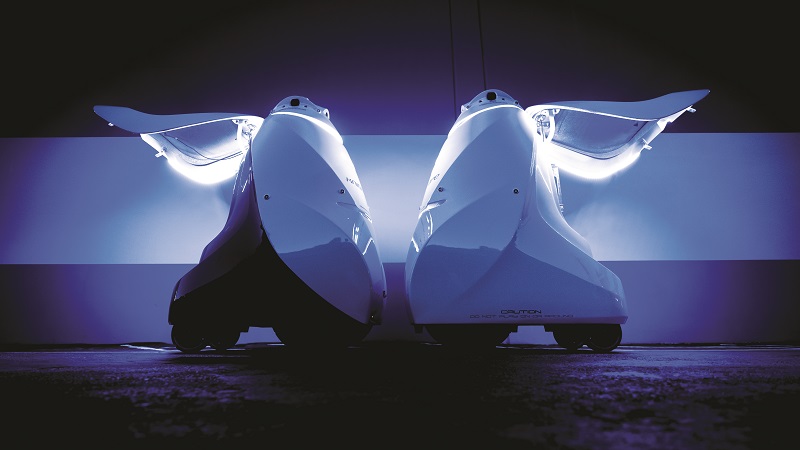
Hardware and configuration
Built with automotive-grade composites and aluminium, the fifth-generation K5 is engineered to withstand demanding outdoor conditions while maintaining a manageable weight. Li describes the design as “akin to a body-on-frame construction”, which ensures structural robustness and modularity for maintenance.
The robot’s hardware configuration has evolved to reduce assembly time significantly, from a labour-intensive 100-120 hours to an ongoing goal of less than 20 hours.
This efficiency has been largely achieved by simplifying the structure into three primary parts – head, body and door – to make assembly and field repairs more manageable.
The wheels and propulsion system have also seen significant design modifications to accommodate variable terrain. Originally positioned at 3 and 9 o’clock, the two powered wheels have been relocated to the front, while a pair of castors is positioned at the rear.
This arrangement improves terrain adaptability, enabling the K5 to navigate surfaces that meet the requirements of the Americans with Disabilities Act (ADA), while remaining effective on other smooth, flat areas. Each powered wheel has its own electric motor.
Lithium-ion batteries power the K5, whose advanced battery monitoring system connects directly to KNOC.
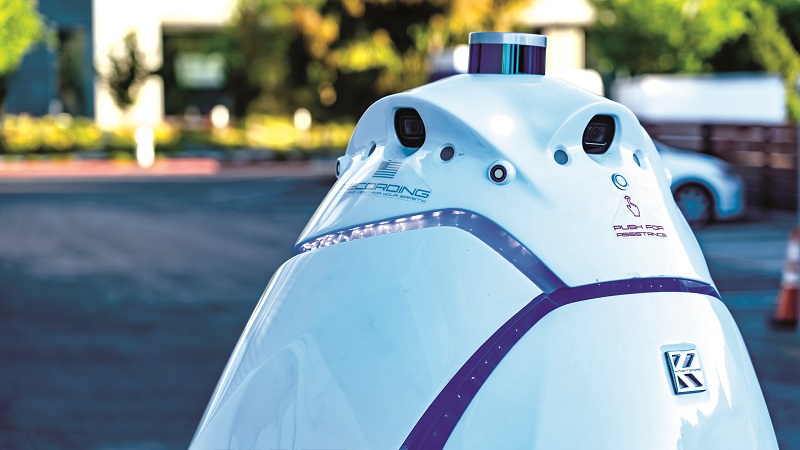
Sensors and navigation
The K5’s ability to navigate dynamic environments autonomously relies on a combination of Lidar, sonar, inertial measurement units (IMUs) and wheel encoders. The outputs of these sensors are fed into simultaneous localisation and mapping (SLAM) software, enabling the robot to map its surroundings and position itself in complex environments.
“Because they provide the fastest and most hyper-accurate mapping”, these sensors allow the K5 to navigate high-traffic areas safely, Li says.
The microphone array on the K5 assists with intercom functionality and enhances its situational awareness. While GNSS is included, the limitations of satellite-based positioning in “urban canyons” and indoor settings mean the robot relies primarily on its SLAM-based system for precise navigation.
The design emphasises high-mounted cameras, which reduce rain interference on the lens and improve field-of-view stability, optimising the performance of onboard machine-learning algorithms.
By angling the cameras slightly downwards, the K5 avoids capturing excessive overhead visuals, which would otherwise skew analysis and situational accuracy, Li explains.
Safety considerations are embedded in the K5’s design to mitigate risks to people and the robot itself. Li compares the K5’s safety framework to that of a self-driving car, which relies on its Lidar, sonar and other sensor arrays to detect obstacles and navigate around them. The K5’s sensors allow it to respond dynamically to pedestrians, vehicles and other environmental changes in real time.
Additionally, the robot incorporates cybersecurity protocols strong enough to have enabled Knightscope to achieve over two million operational machine hours without any major security incident.
Deployment and setup
Site setup involves a thorough analysis to ensure optimal placement and functionality. Knightscope offers a virtual site survey during the sales process, followed by an in-person visit to assess practicalities such as the docking station location and signal strength for telecommunications, so all logistical needs are met prior to deployment.
The physical installation and virtual debugging process can take three to five days each, depending on the complexity of the site.
During this period, Knightscope engineers validate all operational configurations and ensure the ASR is correctly calibrated to meet the site’s specific security needs.
Challenges and iterations
Li emphasises that K5, like all of Knightscope’s technologies, is an entirely in-house project. The company designed, engineered and built the K5 from scratch, although external suppliers are used. Li recalls this decision was driven by the fact that there was no existing robotic platform that met the strict requirements of public safety and usability in populated environments.
The journey from prototype to commercial deployment involved numerous engineering challenges and an adaptive approach. Reflecting on early assumptions, Li described the development process as one where “everything we worried about didn’t happen, and everything that wasn’t on the whiteboard did happen”.
Knightscope’s engineers initially focused on ensuring uninterrupted communications, anticipating that established networks would provide 24/7 connectivity. However, real-world conditions proved otherwise. Even in metropolitan areas, unexpected outages with providers underscored the criticality of redundancy in communications.
Another core challenge was achieving reliable, 24/7 operation across various environmental conditions. The requirement for continuous service posed wear and tear issues, especially on battery management and component durability. Li drew an analogy to automotive wear rates, pointing out that vehicles are designed to be inactive for 90% of the time, whereas the K5 runs nearly continuously, accumulating wear far beyond typical consumer products.
“If I were to ask you to drive your car 24/7 for an entire month, and we’d take care of your fuel or recharging as needed, you would likely need maintenance at the end of that month. And, depending on the speed you were doing, you’d likely void the automaker’s entire warranty for the vehicle,” he says.
The K5’s continuous operation imposes its own constraints on hardware architecture, says Li.
“You might find a component or subsystem that in theory will never break. You think it will be fine, so you bury it at the bottom of the machine, thinking you’ll never have to touch it. So you have a plan, but then you get punched in the face,” he says, paraphrasing ‘Iron Mike’ Tyson.
“And now you’re in the field, having to take that machine almost all apart to fix it. So, for the next version, you rethink how you go about doing things.”
Consequently, the design process has been highly iterative, with new hardware introduced every three to nine months, and software updates rolled out bi-weekly to optimise performance.
The K5’s iterative development cycle has led to substantial revisions in parts layout and sensor positioning, particularly with camera and wheel placements, to enhance durability and reduce complexity. For instance, the component count has been significantly reduced to improve assembly times and reduce the potential for in-field malfunctions.
For the fifth-generation, “we did a complete ground-up redesign on the K5”, says co-founder Stephens. “In doing so, we took advantage of manufacturing efficiencies to create a more serviceable machine that is also more durable and reliable.”
He says this has led to a significant increase in customer commitment. “A lot of clients who were maybe on the fence about the reliability of some of the technology are elated with the improvements, and, as a result, we’ve been able to announce a lot of contract renewals this year.”
Stephens also believes this repeat business can be credited to the MaaS model, and the direct communication between Knightscope and its customers. “We are always getting requests for new capabilities, which are all captured in an ongoing list of things to investigate and prioritise, according to demand, etc.”
It also gives operators regular access to new technology beyond software updates at no extra cost, including the fifth-generation K5. “We own the asset, so we can come in and do a hot swap,” he says. “We pick up their old robot, drop off a new robot and it goes to work.”
Future integrations
In terms of future operational capabilities, Knightscope is working towards full integration with other security technologies, both in-house and from outside vendors.
Integrated facial recognition, available in the K1 Hemisphere stationary system, for example, enables alerts for key people/VIPs and user-generated watchlists for use in the prevention of workplace violence, while automatic licence-plate recognition enables the identification of approved or denied vehicles and helps to monitor parking.
Further, the company’s gunshot-detection system can locate the origin of a shot to within 2 m in less than 2 s, Stephens says.
“Given that location, the robot may be directed to move towards it while public safety professionals are getting prepared. They’re able to tap directly into the robot’s feed and see things unfold in real time. That way, when they arrive on scene, they’re more aware of what that situation entails, so they can remain safe,” he adds.
The same principle applies to Knightscope’s new, laser-based, K1 object-detection and tracking system for perimeter protection, and UAVs for which the company has signed a partnership with multicopter manufacturer Draganfly.
Stephens expects the robot will become part of a networked system of systems in which the whole is greater than the sum of its parts.
Key specifications
- K5
- Height: 64.6 in (164.08 cm)
- Length: 44.6 in (113.28 cm)
- Width: 34.9 in (88.65 cm)
- Weight: 420 lb (190.51 kg)
- Speed: up to 3 mph (4.83 kph)
- Sensors and effectors: 4 x HD cameras with wide-angle lenses,1 x infra-red (thermal) camera,4 x microphones, 1 x amplified speaker/horn, 4 x strobe lights
- Navigation sensors: 6 x Lidar sensors, 13 x sonar sensors
- Communication: 4G LTE cellular, intercom button directed to client-specified phone number
- Terrain capabilities: ADA-compliant surfaces and ramps with gradients up to 20%
- Operating temperature: 0-46 C outside ambient
Key suppliers
- Automated manufacturing: E and M Inc
- Body panels: Quigley’s Auto Body
- Cloud manufacturing: Fast Radius
- Lidar sensors: Ouster
- Repair services: Konica Minolta
UPCOMING EVENTS
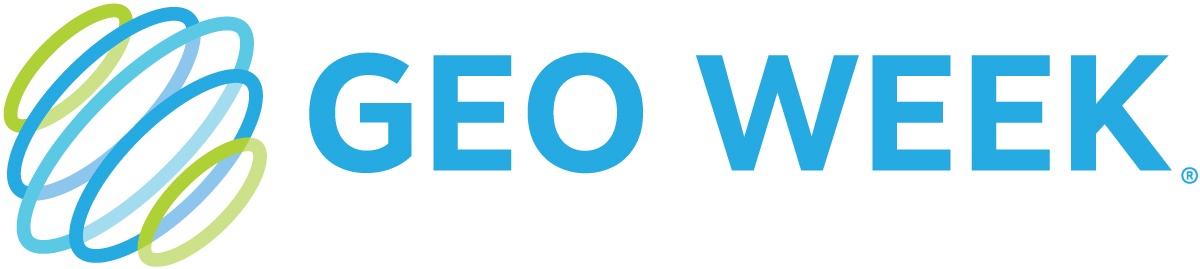
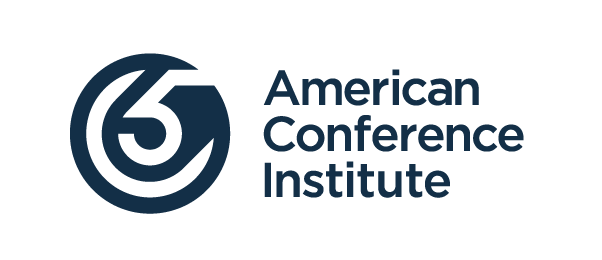
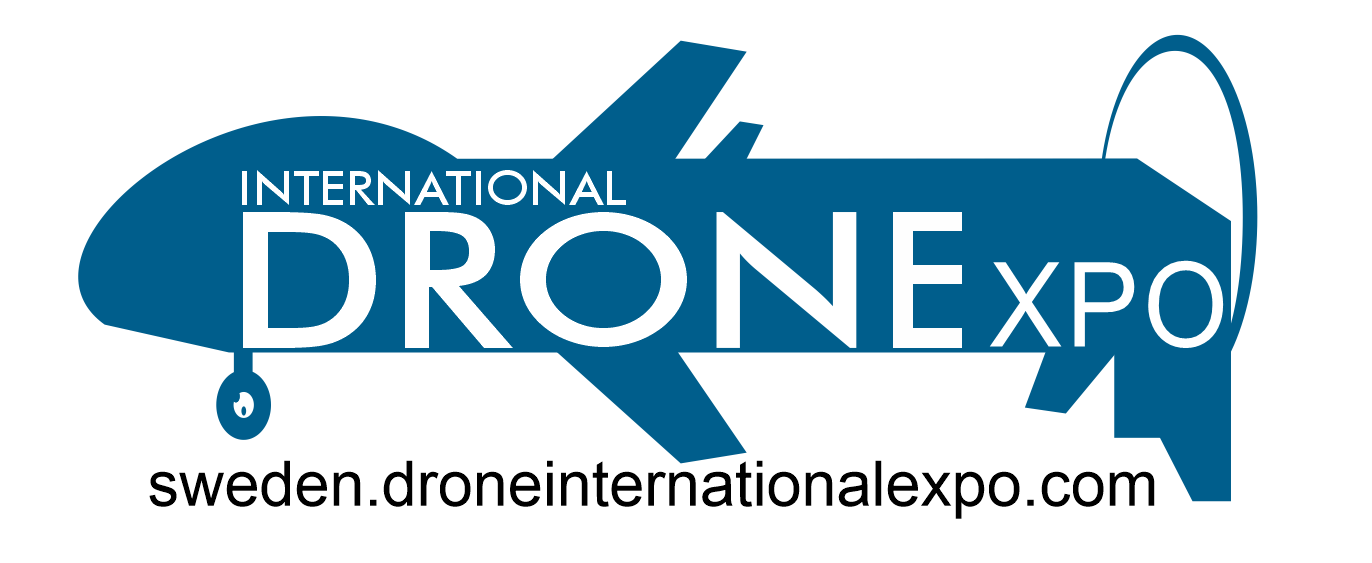
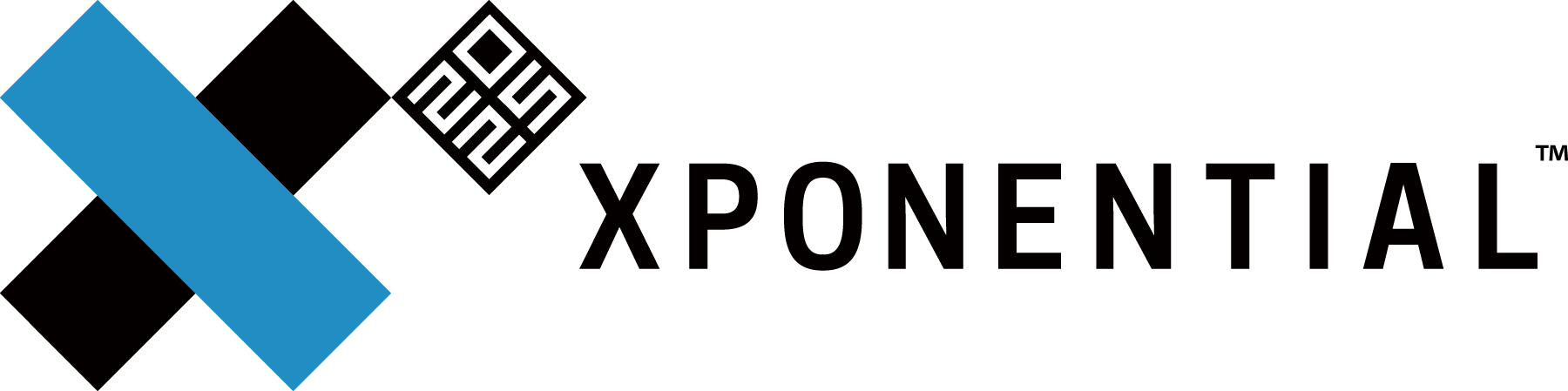
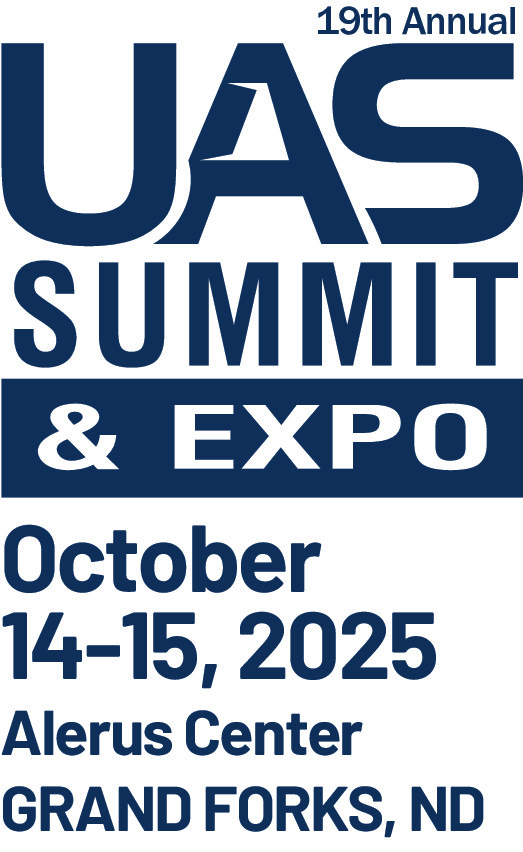

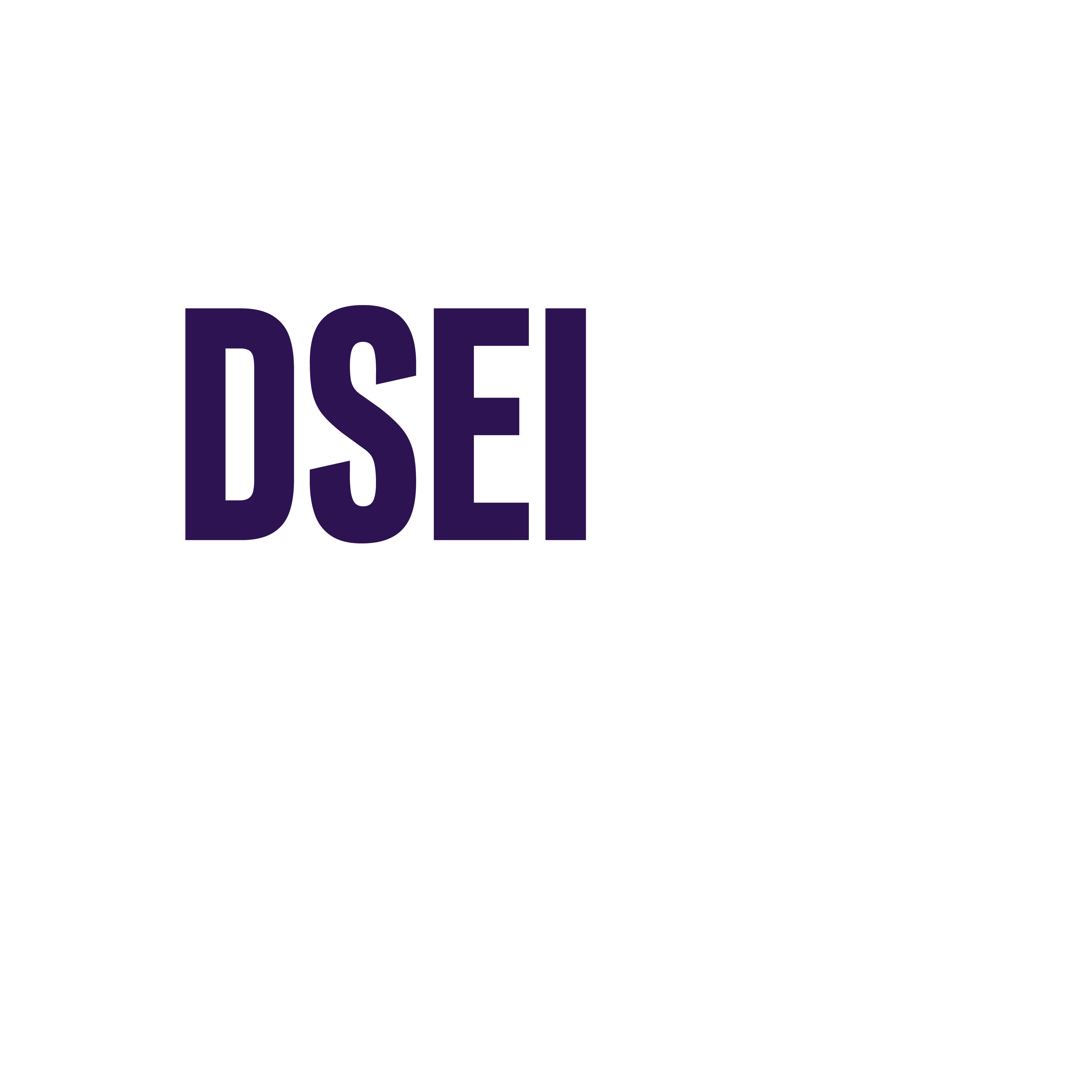
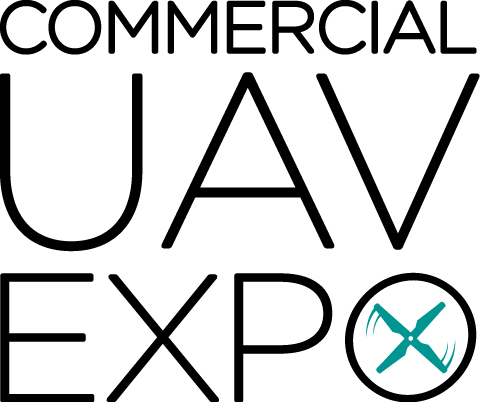
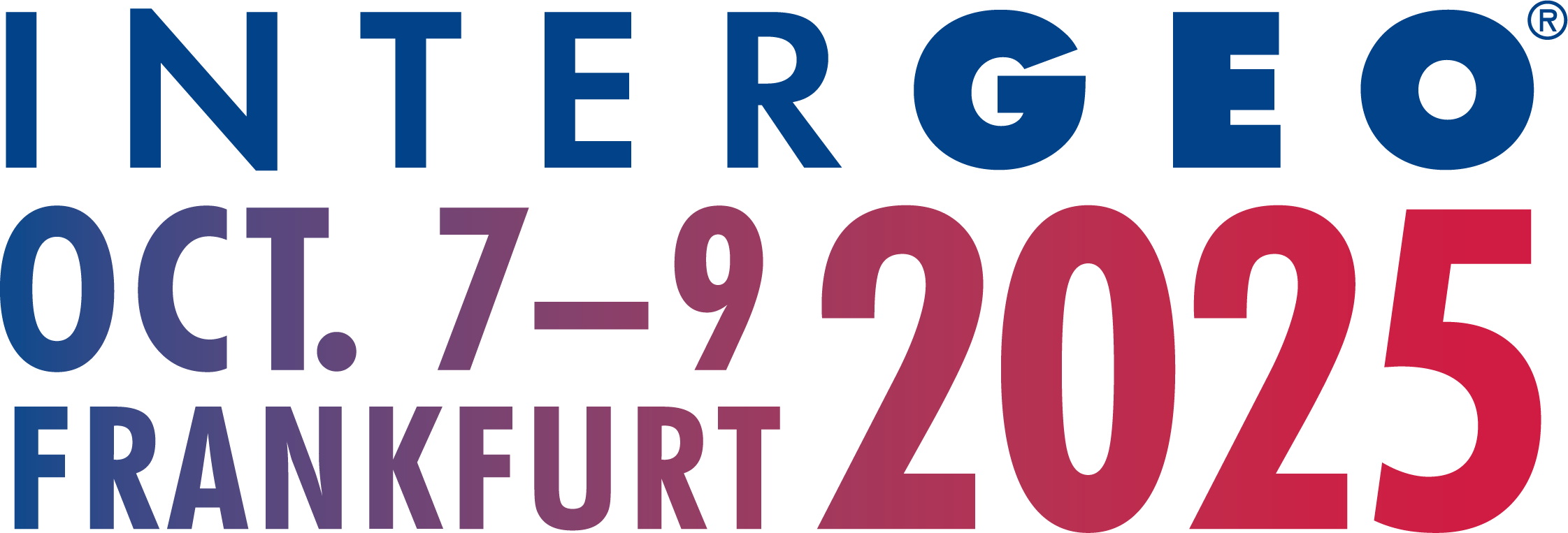
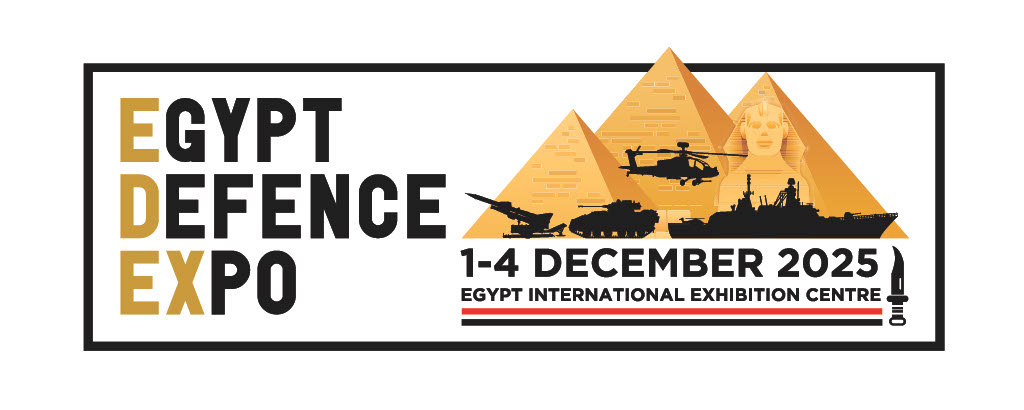
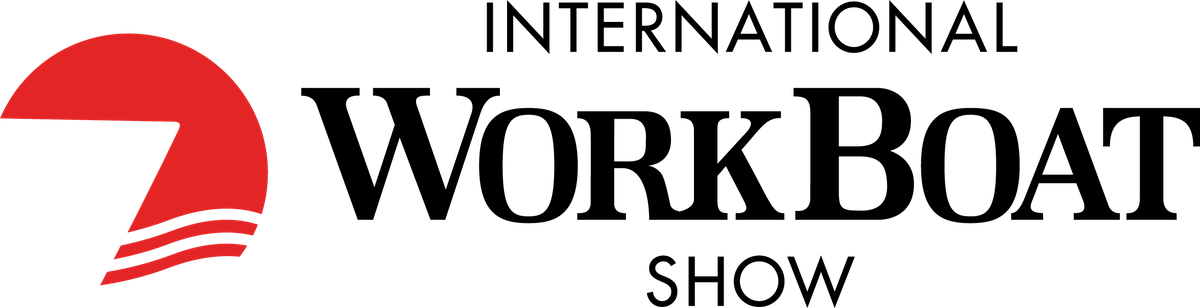