ISS Aerospace Sensus L heavy-lift multicopter
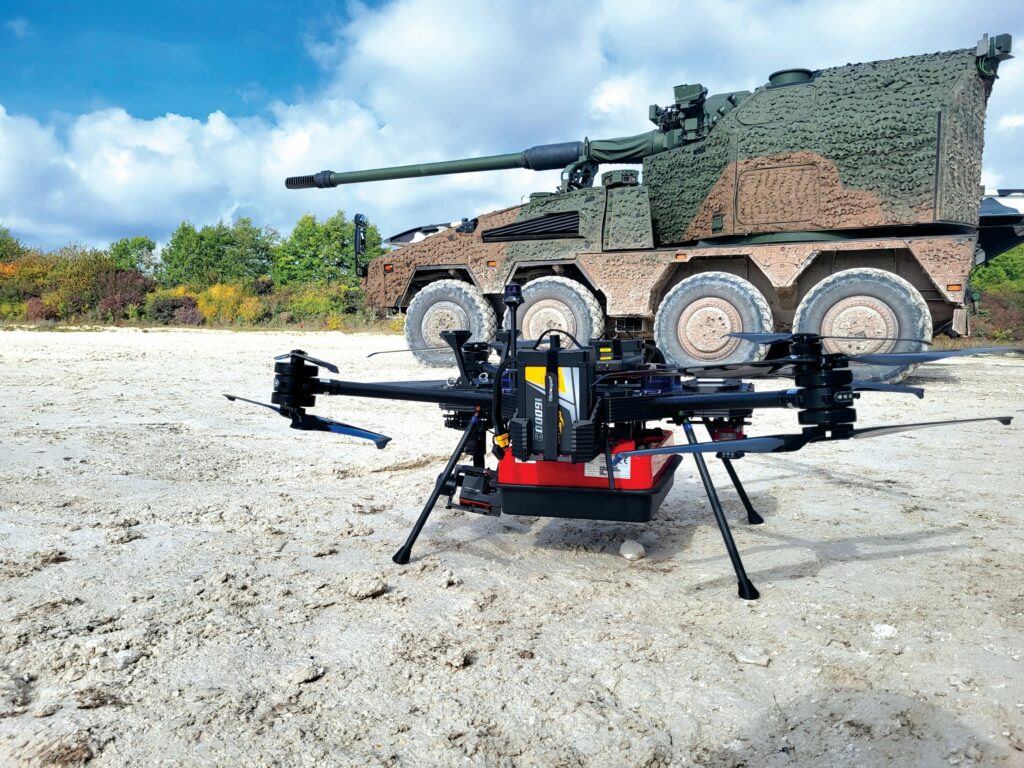
(All images courtesy of ISS Aerospace)
Stealthy modularity
Peter Donaldson examines a heavy-lift multicopter built to support data-intensive payloads
Developed by ISS Aerospace in Chieveley, Berkshire, in England’s Thames Valley, the Sensus L is a modular heavy-lift multicopter built to handle demanding, data-intensive tasks in a variety of industries. Initially created to tackle oil giant Total’s METIS programme for the deployment of thousands of wireless geophones for 4D seismic survey work in Papua New Guinea, the vehicle has since won customers in defence, energy, environmental management, and logistics.
Bracketed by the Sensus Nano with a maximum take-off weight (MTOW) of 1 kg, and the 600 kg Heavy Lift UAS Sensus MX8 under development for the UK MoD, Sensus L is positioned in the middle of the company’s line-up, with MTOW figures of 24 kg for the Sensus L4 and 38 kg for the Sensus L8, which are variants of the same basic airframe with 4 and 8 rotors respectively.
“Its design allows for mounting of up to three large payloads, making it effective for comprehensive data collection and meaningful analysis during a single mission,” according to CEO Ryan Kempley.
Sensus L features what the company describes as a unique central payload interface as well as front and rear payload support rails with a total carrying capacity of up to 18 kg.
“This makes it especially suited for complex, multi-sensor data fusion tasks requiring real-time processing,” Kempley notes.
He explains that in developing a vehicle with these capabilities, the company’s engineers faced challenges related to its structural integrity, particularly in the hull of the airframe, the mounting of payloads particularly as far as weight and balance are concerned. Further, integrating the ISS Unified Avionics Architecture into a larger platform required careful tuning.
“As the system is modular, and designed to be agnostic to payloads, much work was put into the data in/out connections available at the payload areas,” Kempley says.
These challenges drove iterative refinements, resulting in a system now in its fourth development phase, with over 9000 flight hours logged across the Sensus range. Each phase enhanced hull rigidity, power systems, and performance.
Materials, structure and stealth
Additive manufacturing is fundamental to the construction of the Sensus UAS range. The core hull consists of 3D-printed nylon reinforced with carbon fibre strands, with key components further strengthened using continuous carbon fibre, glass fibre, or Kevlar. The Sensus L alone incorporates over 190 3D-printed parts, while high-wear and stress-prone areas are CNC-machined from aerospace-grade aluminium.
The Sensus range features a common frame structure made from these composite materials. The fusion of 3D printing and carbon fibre reinforcement creates a strong yet lightweight structure, ensuring durability in demanding missions. The printed material offers aluminium-like strength at a fraction of the weight, allowing for enhanced resilience without compromising efficiency, Kempley notes.
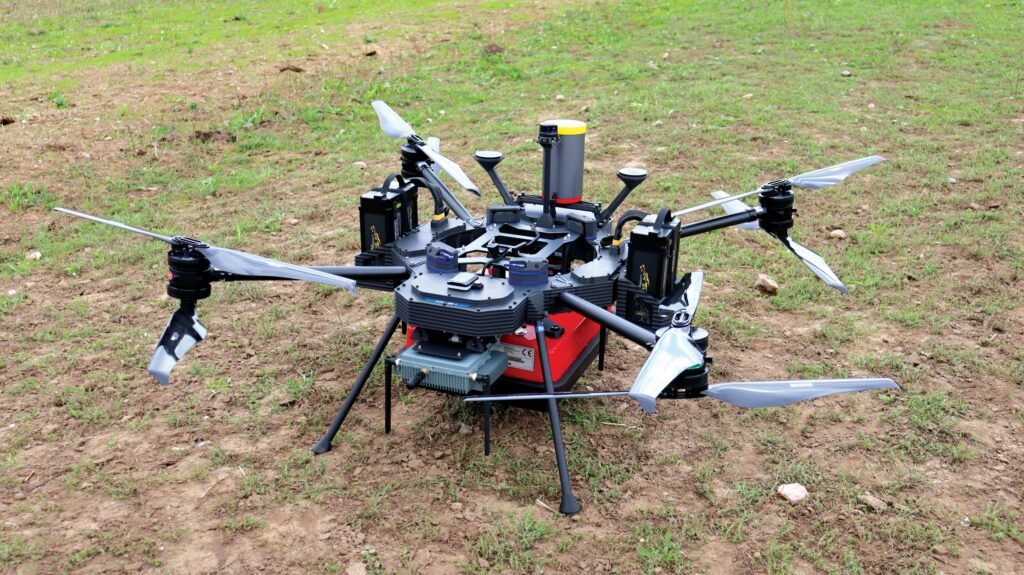
A variety of metals including aluminium, titanium, and marine-grade A4 stainless steel are also used for specific components and fittings. For example, custom 7068 aluminium pressure spreaders secure the main boom fixings, while A4 stainless steel bolts provide superior corrosion resistance. “The robustness and corrosion resistance of these far outweighs any weight penalty they impose,” Kempley emphasises. Finally, specialist aerospace plastic inserts integrate components to complete the structure.
Through stress analysis and load testing, critical areas were identified and selectively reinforced while lighter regions were optimized. This data-driven approach ensures a well-balanced structure, maximizing both strength and weight efficiency, he adds.
Staying smooth
For a UAV that must carry high-resolution cameras, minimising vibration is critical and preserving that smoothness through the platform’s evolution is equally important, as Kempley explains. “After any initial design, or iteration of the platform, we conduct vibration tests to identify any areas of concern. However, integral to the design of the platform is a number of “break” points, where vibrations are eliminated through material choice. We also ensure correct balance on all motors and propellers, again to minimise any disturbances.”
For a UAV with military applications, a degree of stealth is always an asset, and this attribute is now incorporated into the company’s vehicles. “At the V2 revision of the Sensus M, we were asked to consider having a lower radar profile on the platform,” Kempley recalls. “This led to the now iconic zigzag pattern of the side hulls on our entire range of UAS. The idea is that it removes several flat/perpendicular surfaces, and it was tuned, to a degree, for the optimal reflection patterns.”
Propulsion and control
Propulsion and control forces are generated by either 4 or 8 brushless direct current (BLDC) motors, each rated at 100 Kv. The Kv rating relates the motor’s speed to the voltage applied to it without a propeller or any other load, so a 100 Kv motor will spin at 100 rpm per volt. A
100 Kv motor has a relatively low Kv rating, so it will spin more slowly for a given voltage but typically generate higher torque than a higher Kv motor of the same power rating, assuming similar design and efficiency. Such motors are well suited to large propellers and heavy loads.
Each motor can generate 8 kg of thrust while consuming 900W at full throttle. In the Sensus L vehicles, however, they are generally run at just 55% of their capacity even when the UAV is loaded to its maximum weight. This puts them in a good efficiency band within their performance profile, Kempley explains. This is also likely to optimise the balance between performance and longevity.
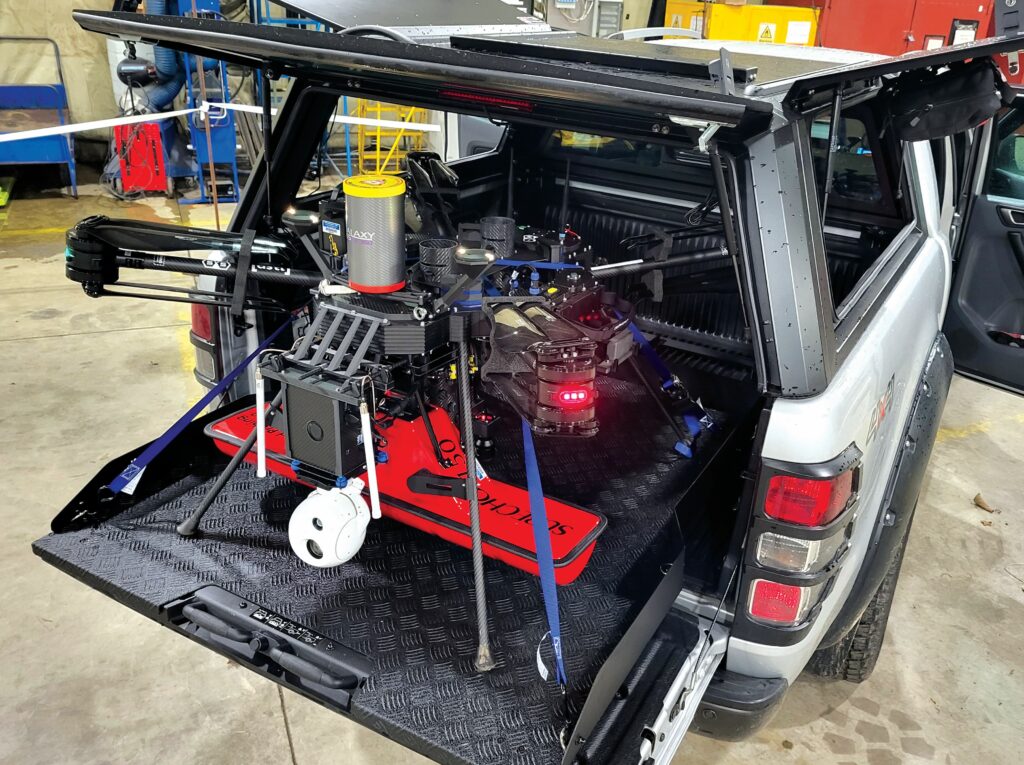
In the larger Sensus L8, the motors are mounted in coaxial pairs, providing higher thrust in a compact configuration and allowing for greater payload capacity without increasing the UAV’s footprint. Further, it enhances redundancy and reliability, ensuring continued operation if one motor fails, which is critical in BVLOS and heavy-lift missions, he emphasises. Other benefits include better yaw control in strong winds, better weight distribution for greater stability. Coaxial designs are also more portable (thanks to their compactness) and rugged, he says, making deployment easier in confined spaces and other challenging environments.
“While there is a minor efficiency loss due to airflow interference between the propellers, this can be mitigated through proper tuning. Overall, coaxial motors provide the extra power, stability, and reliability needed for demanding UAV applications,” Kempley continues.
The propulsion system’s modular design means that it can easily be re-configured for different missions and tasks in minutes rather than hours, Kempley adds. This is facilitated by the use of non-propriety data and power interfaces, quick release latching mechanisms and open source software.
In terms of energy storage, the company offers either lithium polymer (LiPo) batteries or a hydrogen fuel cell system on both the Sensus L and its smaller sibling the Sensus M. In fuel-cell-powered form, the larger is known as the Sensus H2L and can fly for up to 150 minutes, depending on payload and configuration while with batteries it can fly for between 25 and 55 minutes, depending on payload. The fuel cell system is the lightweight Fuel Cell Power Module (FCPM) from Intelligent Energy and is rated at 2.4 kW. With this powerplant, the Sensus H2L can take on missions that involve long loiter times such as surveillance, and those that require significant range such as deliveries in logistics operations.
At the heart of the flight control system is a CubePilot autopilot running Arducopter software. The autopilot also uses the Mavlink protocol to communicate with onboard companion computers including an NVIDIA Orin AGX AI board and an Intel NUC Extreme i9 data processing unit. Mavlink provides efficient data exchange for both high-level mission commands and certain low-level control functions. It is this combination that allows the aircraft to process data from multiple sensors in real time, facilitating both autonomous navigation and immediate data analysis.
“This is achieved by direct ROS2 agents and nodes on the AGX interfacing with the autopilot. We then call upon the various data sources during our route planning routines,” Kempley explains.
Each of these systems is part of the company’s Unified Avionics Architecture (UAA), which is used across the Sensus range. Designed using an open systems approach, the UAA provides a proven avionics backbone, allowing for seamless integration of various payloads and sensors. It is agnostic towards datalink and command-and-control (C2) systems, providing full IP-based networking that connects the aircraft, payloads, and ground control stations.
Both Sensus L4 and Sensus L8 have a typical maximum speed of 25 m/sec (90 kph) and resist wind speeds as high 18 m/sec (64.8 kph). This difference might seem anomalous, but any multicopter’s top speed is self-generated motion in controlled conditions, while wind resistance is a battle against external forces, often requiring much more power and control effort to remain stable. Hence, the top speed is typically higher than the maximum wind speed it can resist.
In light of this, ISS has long worked with Arducopter developers to make sure that the system is tuned to all of its envelope limits. “Therefore, to the operator, the system behaves in the same way at both ends of the environmental conditions scale,” Kempley emphasises.
Navigation and collision prevention
Sensus L features dual redundant RTK GNSS GPS receivers for precise navigation, a system based on active sensors for obstacle detection and avoidance, a 200m laser altimeter for accurate measurement of the vehicle’s height above the terrain, and a Mode S ADS-B transceiver for enhanced air traffic awareness.
The laser altimeter enables terrain following flight in which the vehicle maintains a consistent height above the ground while following a route planned within the ground control station. “Depending on the customer’s configuration, this can use both dual laser and dual radar altimeters for precise and redundant control,” according to Kempley.
The active obstacle avoidance system combines a laser, a radar and an infrared time-of-flight (ToF) sensor. This, Kempley says, enhances the vehicles’ ability to navigate safely in complex environments and inside buildings etc, while having enough breadth of sensor types to mitigate varying environmental conditions.
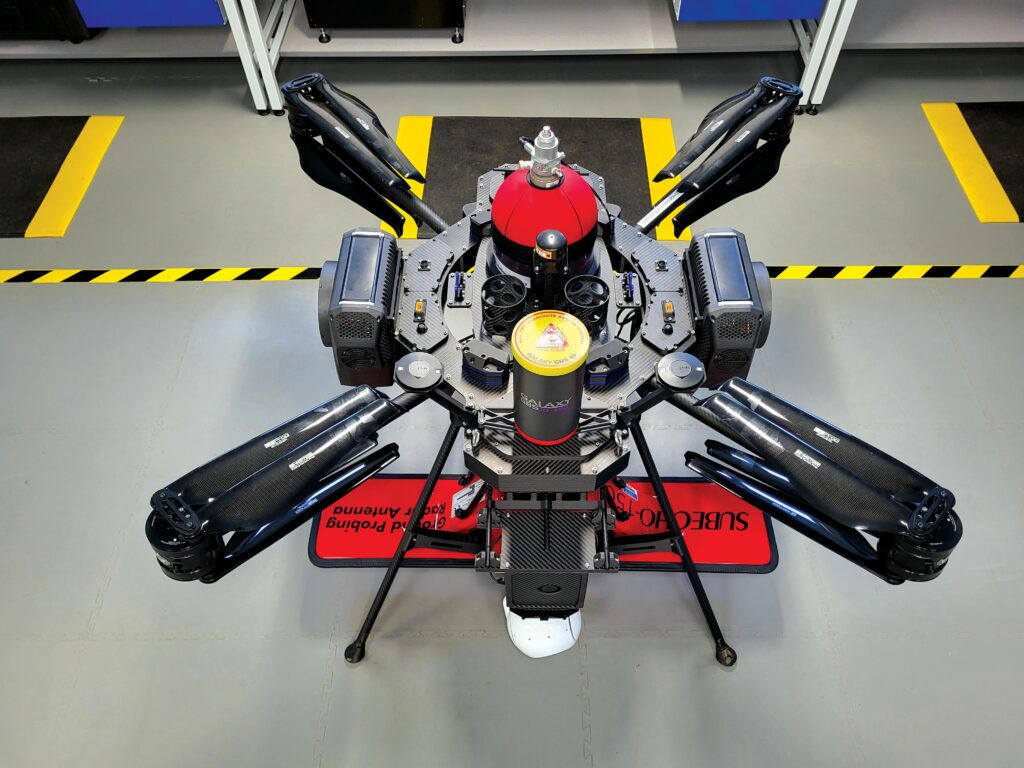
“Running real time RL/AI routines, the system can learn the environment and understand where obstacles are after first encounters,” Kempley explains. “This means it can then iterate faster during complex exploration. It is then still capable of seeing ad-hoc and new obstructions as well as dynamic obstruction scenarios. Feeding back into the model to improve its understanding of the local environment. If running in swarms, this can then be shared with its cohorts, forming a data driven mesh of exploration.”
The navigation system also supports navigation in GPS-denied environments using a variety of technologies including external aids, integrated sensors and advanced software-based techniques. These can include infra-red (IR) and radio frequency (RF) beacons in controlled, localised operations. Such beacons support precise position holding and guided movement, albeit with the limitation of requiring pre-installed infrastructure. Another capability is visual inertial odometry (VIO), which uses a combination of maps, cameras and inertial measurement units (IMUs), although its navigation accuracy is tied to the quality of the available maps and on lighting conditions. When no maps are available, the system can use simultaneous localisation and mapping (SLAM) algorithms to process sensor data, relying on high levels of processing power. Finally, high-grade inertial navigation sensors enhanced with radar velocity detection give very accurate results, although only for short periods as they are subject to drift with time.
Using either GPS with RTK or beacons, Sensus L can achieve take-off and landing accuracies of better than 10 cm, Kempley notes, adding that these systems can be augmented with AprilTags (similar to QR codes) and optical cameras to find and home in on its touchdown location. “Additionally 360 degree radar/laser sensors can alert the system to obstructions in the area during these phases.”
Communications agnostic
Using IP-based networking, the Sensus range is essentially communications agnostic, meaning any type of UDP/TCIP radio system will work out of the box, according to Kempley. However, ISS often uses data links from Codan company Domo Tactical Communications (DTC). All the links used on the vehicles offer encryption options up to AES256, reinforced by secure login procedures for both GCS equipment and onboard processors, he emphasises. “The most common radios we use also utilise anti-spoofing technology to further resist rogue RF communications.”
Anti-jamming capabilities also feature, including frequency hopping, encryption, and redundant communication links. With the latter, it can automatically switch to alternative frequencies or communication methods if interference is detected. “Additionally, onboard AI may recognise and mitigate jamming attempts by adjusting flight parameters or activating autonomous return-to-home (RTH0205) functions.”
In this vein, multiple fail-safe communication protocols are used, including redundant RF, satellite (Starlink/Iridium), and 4G/5G LTE links with automatic switching. If all links fail, the vehicle follows emergency procedures such as RTH, loitering, autonomous landing, or – if it has beyond-visual-line-of-sight (BVLOS) approval – mission continuation. In addition to the flight termination system, geofencing helps ensure safety.
Customisation is possible with modular RF bands, encrypted data links, and bespoke systems for specific missions. The UAV integrates with cloud platforms like AWS and Azure for real-time data analysis. Future advancements may include AI-driven communication for intelligent bandwidth allocation.
Depending on the handset and GCS selected, the maximum operating range of a Sensus L is 90 km from its take-off point. However, ISS also offers satcom-based control, including Starlink Mini and other, more secure systems.
The vehicles also have an onboard gigabit network for high-speed comms between connected devices, and options for 10 Gb optical fibre lines. The latter are particularly useful for data and C2 comms when the UAVs are employed in tethered operations.
Environmental resistance
Robustness to the operating environment is also a key consideration in material selection. “We look for materials that are corrosion resistant, have a long shelf life, and that are compatible with our machining and manufacturing techniques,” Kempley says. “They also need to meet the requirements for our standard IP ratings, ie non-porous, and have the ability to withstand consistent temperatures above 55 C.”
In terms of environmental resistance, all variants are offered with an ingress protection rating of IP54 with the option to upgrade that to IP65 to ensure reliable performance in a wide range of weather conditions without limitations, he emphasises.
The result is that Sensus L and the rest of the family can operate comfortably within a temperature range of -19 to +55 C, and in climatic conditions ranging from very humid to very dry. In large measure, this ability to shrug off very high temperatures is enabled by extensive cooling features integrated into the vehicle’s processing infrastructure. This helps manage heat generated by onboard electronics and power systems even in high ambient temperatures. For example, they have been flown in Kuwait, Oman, Saudi Arabia, Abu Dhabi, Canada, the Atacama Desert in Chile, and Papua New Guinea.
“Depending on the rating required by the customer we have a number of heat transfer technologies that can be used to efficiently regulate the internal temperatures of the system,” says Kempley. These include heat sink and heat pipe designs that effectively remove heat from inside the airframe and transfer it to the ambient air.
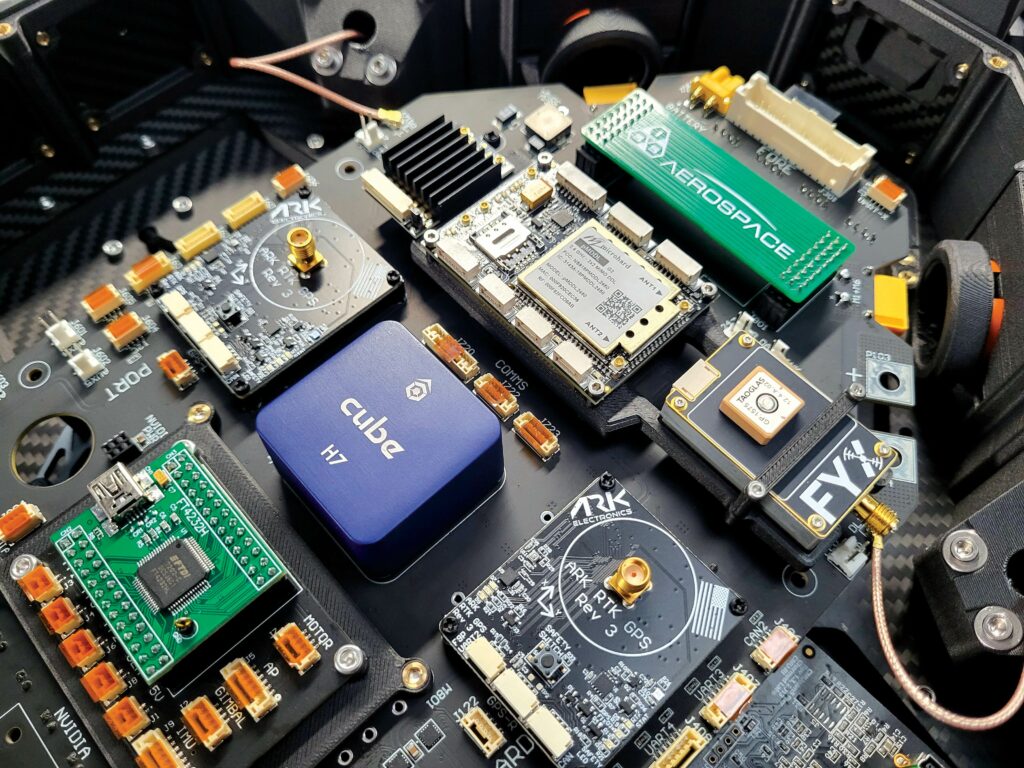
Sensus L is offered with an ingress protection rating of IP54 as standard and IP65 as an option. The latter ensures protection against dust and water splashes, allowing it to operate in hostile weather. However, Kempley points out that its usefulness in such conditions depends on its pilotage sensors and payloads. “We can offer payload pods for optical cameras and for the pilot FPV camera to retain visual effectiveness in low visibility.”
The combination of modular design and the large percentage of each vehicle that is manufactured in house ensures repair or replacement of damaged components is streamlined and consistent, Kempley says. The company provides a 2-year warranty on all its systems as standard, but recommends that customers buy the extended warranty so that they can be checked and, if necessary, repaired to the manufacturer’s standards in a timely manner throughout their service lives.
Emergency response
As with the rest of the Sensus range, the Sensus L variants can optionally be fitted with a ballistic parachute recovery system to ensure that they can be brought down safely in the event of critical failure in flight. There is also a safety “kill-switch” on the pilot’s handset, plus a separate flight termination switch that activates a radio operating on a different frequency from the main command and control transceiver to avoid mutual interference. The L8 model (as well as the smaller M8) have redundant motors, allowing the vehicle to remain operational and under control even if two motors fail on the same arm.
Rules and regs
Regulatory compliance varies by region and variant. Sensus L4 (24kg MTOW) complies with various regulatory frameworks across the UK, Europe, and the USA. In the UK, it falls under the Civil Aviation Authority (CAA) UKPDRA01 pre-defined risk assessment for drones under 25kg, aligning with CAP 722 regulations within the “specific” category.
European (EASA) regulations classify it under the specific category (4-25kg), requiring an operational authorisation based on a specific operations risk assessment (SORA). Operators must hold either standard scenario (STS) certification or a light UAS operator certificate (LUC) for company-based operations, ensuring compliance with EU regulations 2019/947 & 2019/945. Depending on the use case, it carries a CE marking (C3-C6).
In the USA, the Sensus L4 qualifies under FAA Part 107 as it remains below 55 lbs. Operators need a remote pilot certificate, with potential waivers required for BVLOS (Beyond Visual Line of Sight) operations or flights over people.
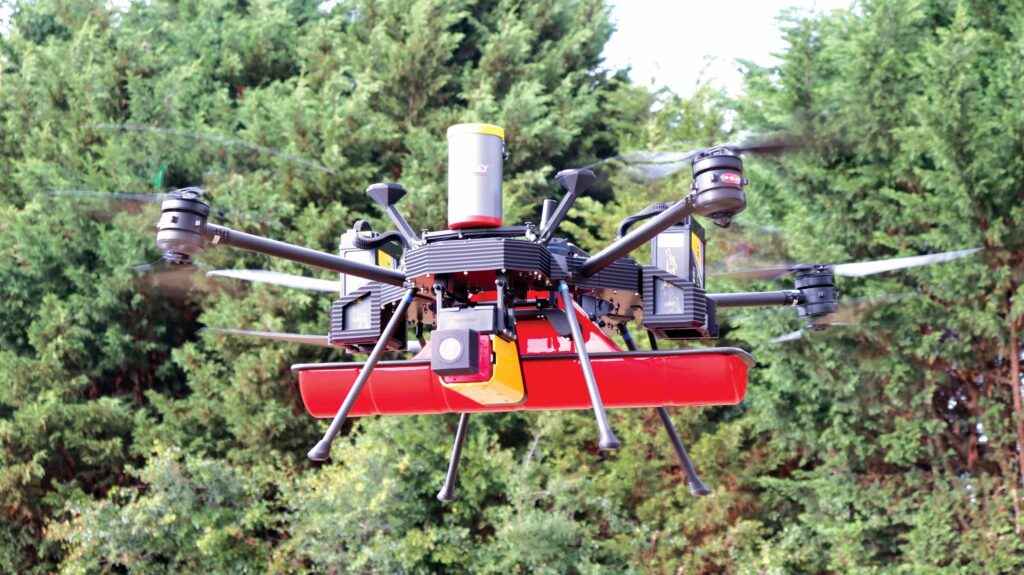
The Sensus L8 (38kg MTOW) adheres to more stringent requirements due to its increased weight. In the UK, it operates under the specific category, requiring an operational authorization (OA) and potentially UK Part 21 certification if flown in certified airspace or complex environments. Compliance involves a SORA risk assessment and adherence to CAP 722 and CAP 722H standards for heavy UAS operations.
Within Europe (EASA), UAVs above 25kg require a SORA-based operational risk assessment, with the option of a LUC for repeat operations. Flightworthiness must be demonstrated based on risk classification. In the USA, the Sensus L8 exceeds the FAA Part 107 weight limit and requires a Part 107 waiver. More advanced operations may necessitate FAA Part 91 certification or FAA type certification for commercial use in complex environments, adhering to ASTM F3389/F3298 airworthiness standards.
For military and government applications, ISS Aerospace ensures compliance with NATO STANAG 4703 (military UAV standards), DEFSTAN 00-970 (UK defence airworthiness standard), and additional approvals as required by defence and security agencies.
Heavylift, multi-role UAS for demanding missions under challenging conditions is an increasingly important and competitive market segment, in which ISS’ Sensus family has built itself a strong position.
Key specifications
Power Source: x2 Lithium Polymer Batteries
Max Flight Time: Up to 55 mins (no payload) & 25 mins (max. payload)
Range: up to 82.5 km
Maximum payload capacity: up to 18.0 kg
MTOW: up to 38 kg
Service Ceiling: 3,500 m
Pitch Angle: 45o
Wind resistance: 18 m/sec Weather rated to IP54 as standard with option to upgrade to IP65 (Hydrogen option limits to IP43)
Some key suppliers
Autopilot software: Arducopter
GPS receivers and RTK GNSS: ARK Electronics
Autopilot hardware: CubePilot
Rugged mesh radios, datalinks and modems: DTC
Rugged GCS handsets and controllers: UXV Technologies
Processors, data analysis, sensor fusion: Intel
Nav/collision avoidance LiDaR: Lightware
3D printing equipment suppliers: Mark3D/Markforged
AI-powered real-time processing: Nvidia
Long-range 3D mapping LiDaR: Ouster
UPCOMING EVENTS
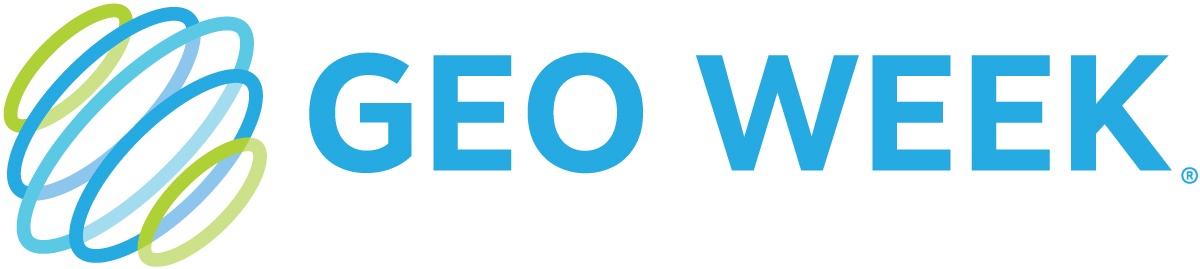
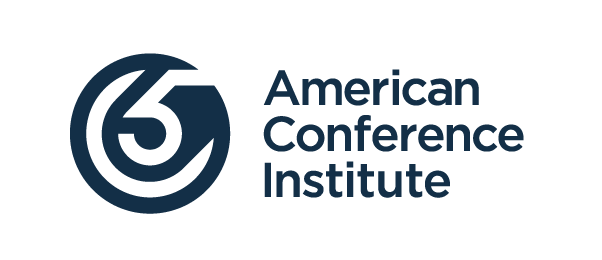
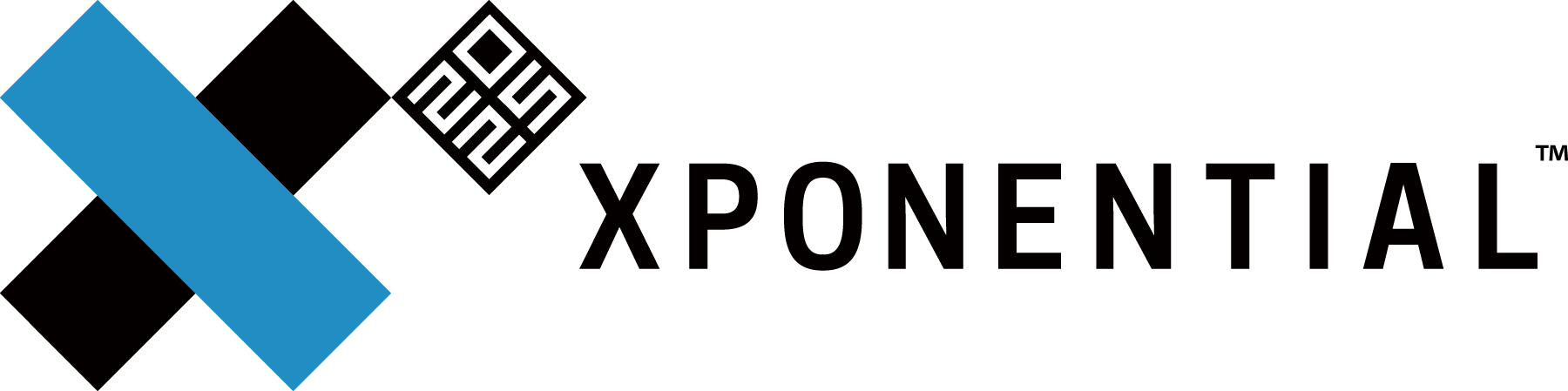
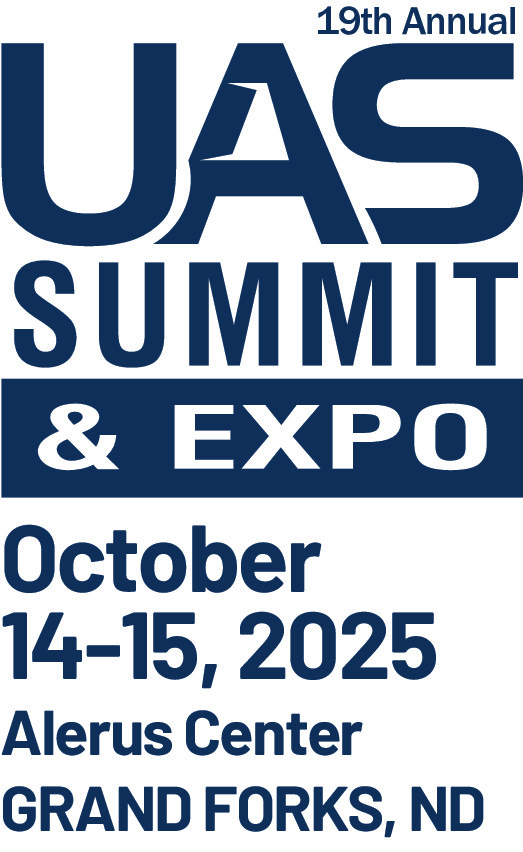
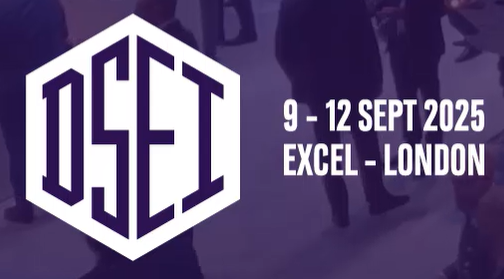
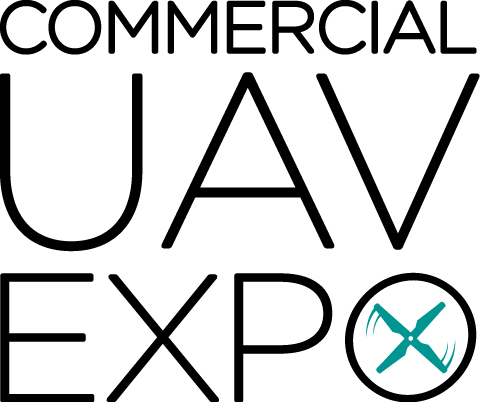
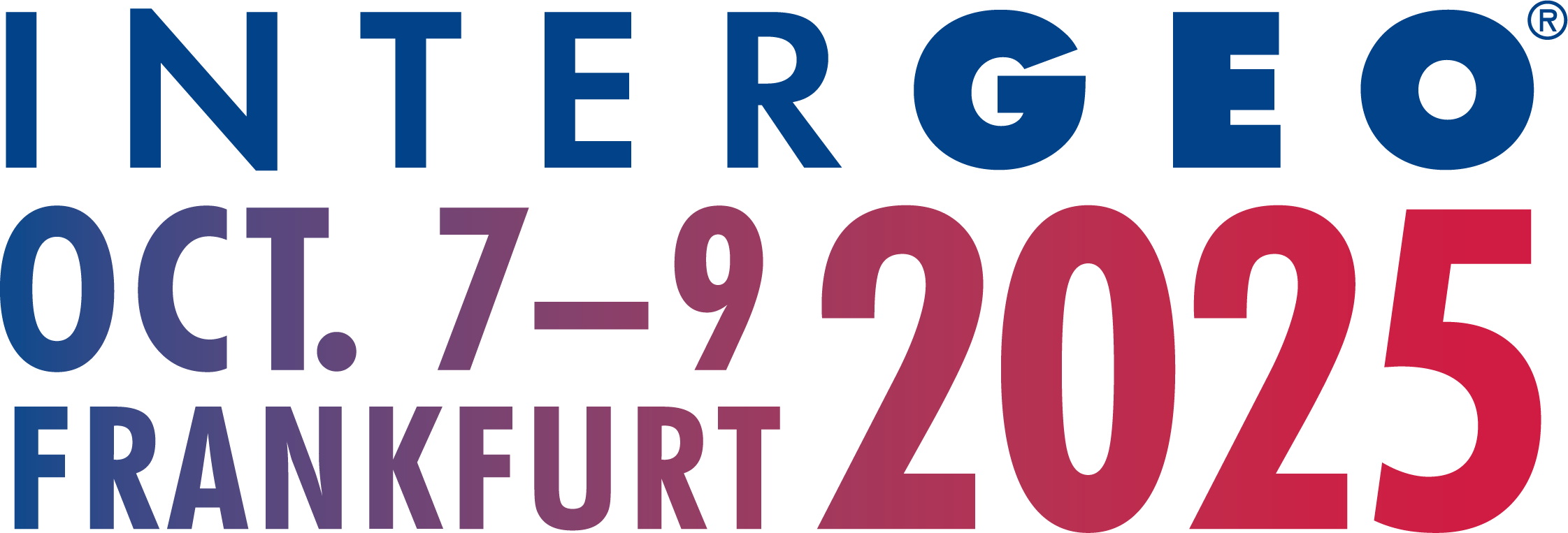
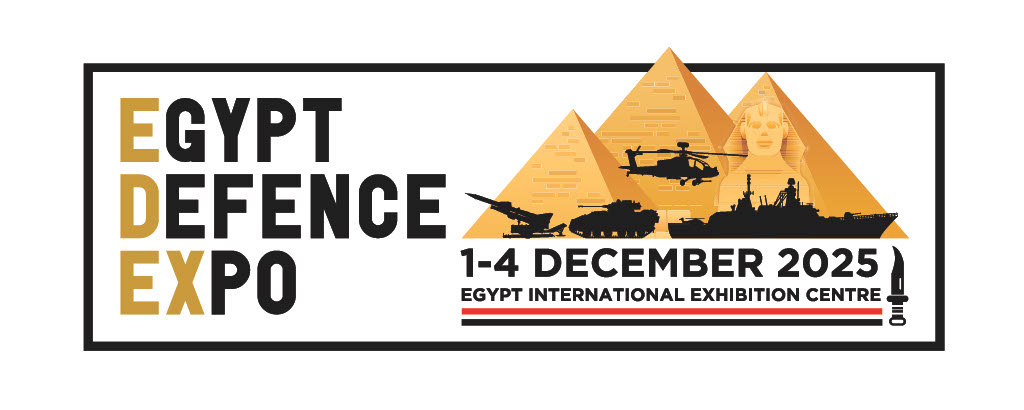
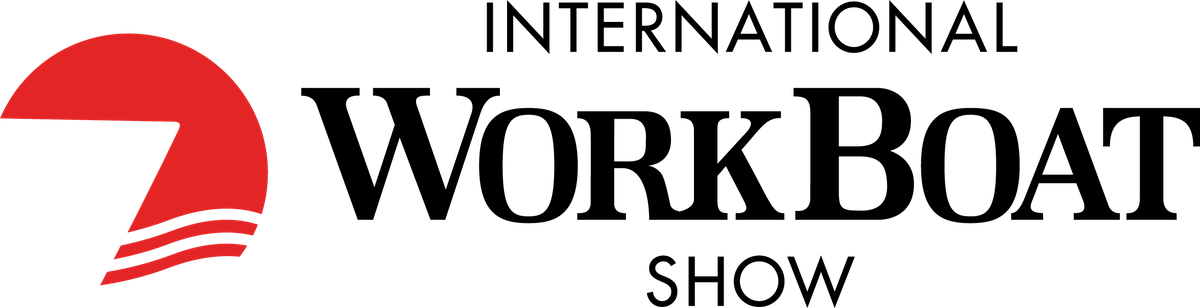
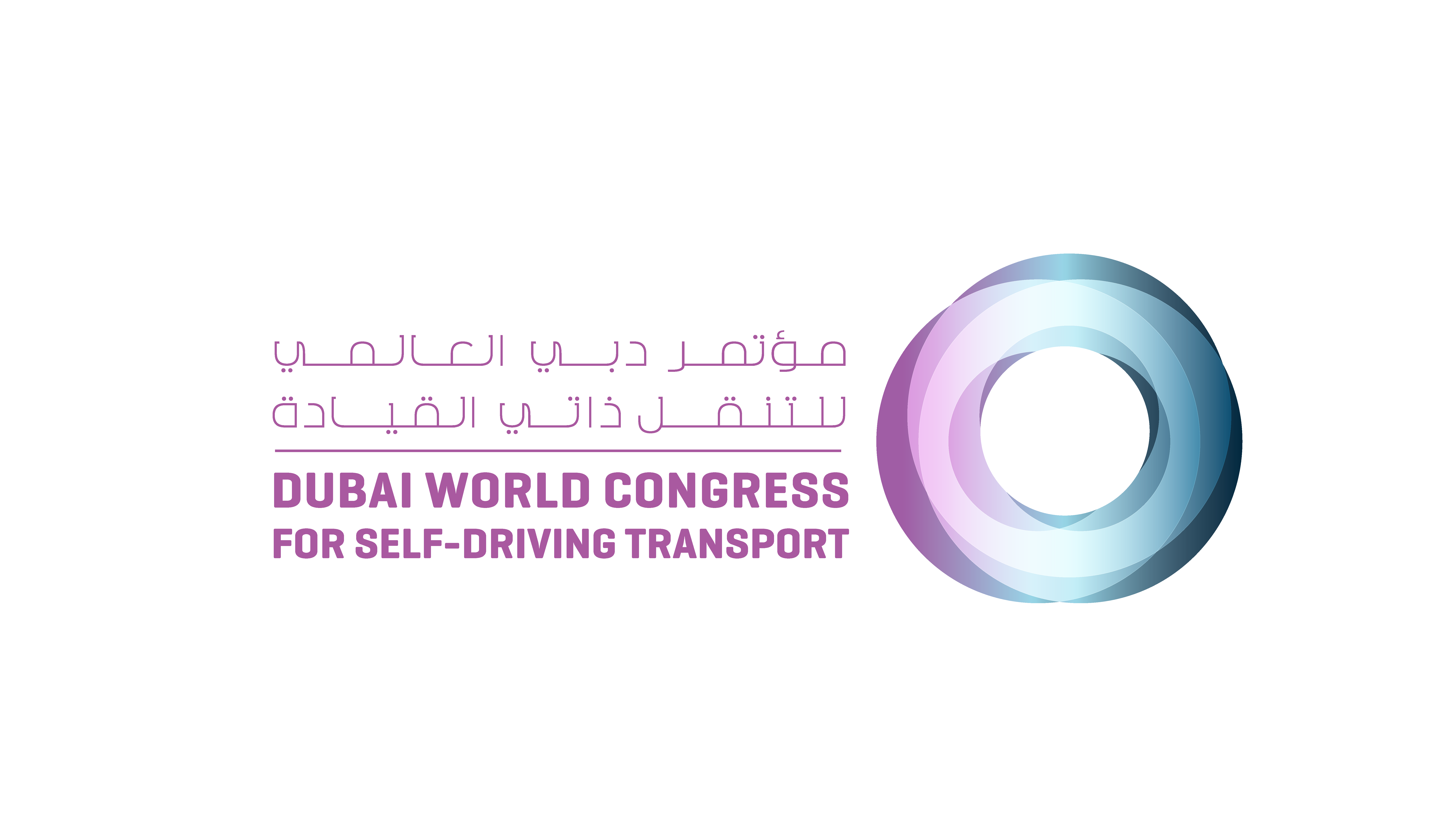
