Robotican’s Goshawk
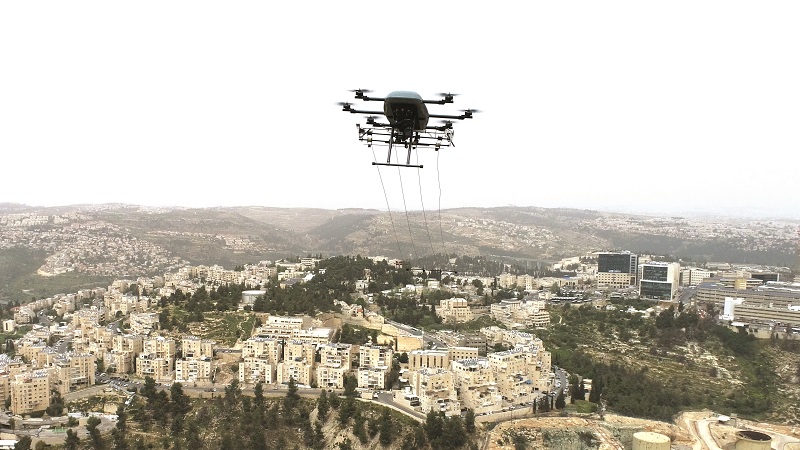
Rory Jackson investigates a counter-UAS system modelled on a hawk
As uncrewed aircraft evolve, so too must counter-UAS (C-UAS) solutions. For most of the last decade, the latter has consisted of many strategies, which can be arranged to work together to protect vital assets such as defence bases, industrial installations or airports from attacks by hostile agents operating UAVs.
Particular praise has been levelled towards static or handheld devices for taking aim at hostile or non-compliant UAVs and pulling a trigger to jam their data links. The typical response of disposable and remotely piloted UAVs (such as those of DJI or Yuneec) to such jamming has been to freeze, start descending or return to their launch point.
Beyond this, there are situations where, upon detection of a hostile drone, it is perfectly safe and acceptable to simply destroy it by firearm or similar means, but in cases where people or infrastructure below may be harmed by falling debris, or if there is a risk of a chemical agent or other substance onboard the trespassing drone, a non-destructive approach such as jamming is desirable.
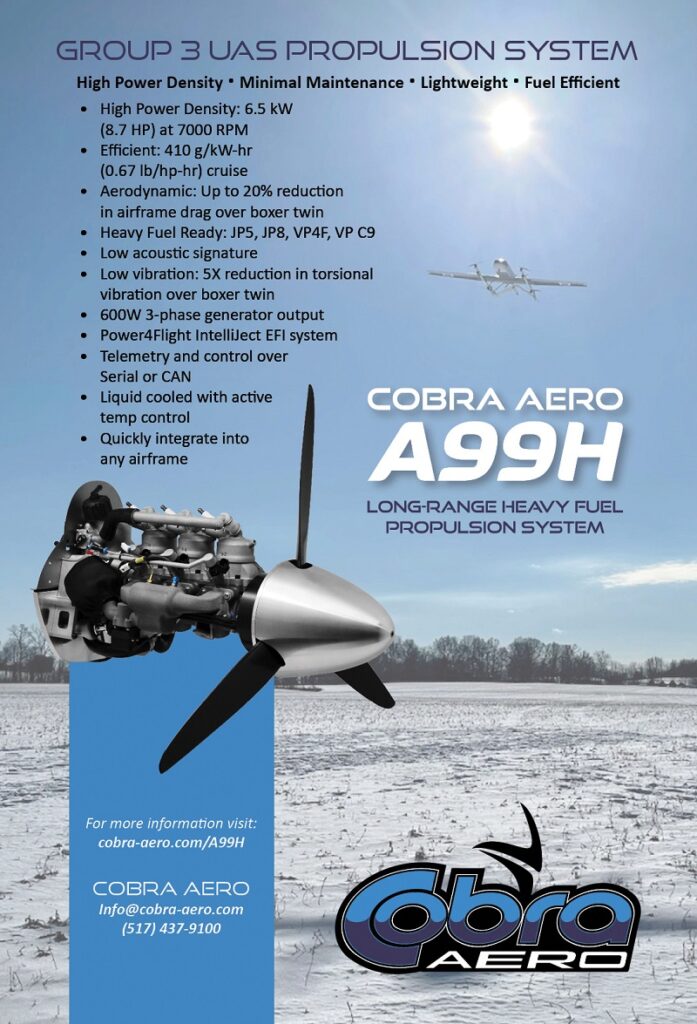
As UAVs become more autonomous, with open-source communities and others making algorithms for full autonomy (including simultaneous location and mapping (SLAM) and collision avoidance) available to all, C-UAS jamming solutions become dramatically less useful.
An autonomous drone does not have to lose control in response to jamming as remotely piloted ones do; it can continue flying towards its target or loiter obstructively in forbidden airspace, causing lengthy and costly disturbance, akin to the rogue drone flown over London Gatwick in December 2018.
Israel-based Robotican has developed its Goshawk Interceptor UAV solution and the infrastructure key to its operations to enable the physical capture of hostile drones in a non-destructive way. The firm has developed the craft to autonomously outmanoeuvre hostile autonomous drones on behalf of key customers across defence and other industries.
“In civilian and defence sectors alike, you now need some kind of physical, autonomous mitigation to counter the rising threat of intelligent, autonomous systems by hostile actors now that full autonomy can practically be bought by anyone off-the-shelf. Such UAVs can keep flying while their comms are jammed and will still be dangerous until physically detained,” says Robotican CTO Yam Geva.
“In the years ahead, attacks from swarms of hostile drones may become intermittent occurrences. How many places in the world are equipped to counter that with a swarm-like number of C-UAS jamming guns with enough personnel trained to use them? A defending swarm or fleet, by contrast, can react autonomously and quickly, and it doesn’t need to be trained beyond the prior development of its AI. As such, we see autonomous C-UAS vehicles such as Goshawk being an important piece of the puzzle to future defence and safety infrastructure.”
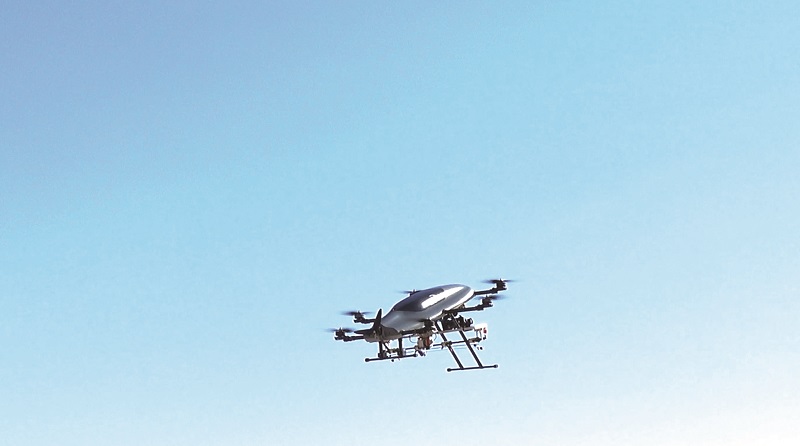
The Goshawk
Robotican’s Goshawk Interceptor is a battery-electric hexacopter, featuring six rotor arms extending widthways and parallel to each other from the 97 cm-long ovular aircraft body. It weighs approximately 21 kg, and flies at an airspeed of 30 m/s (108 kph) for a maximum endurance time of at least 10 minutes between recharges.
The system has successfully intercepted 261 hostile drones in a total of 1543 hours of flight. While the airframe is conventional for industrial UAVs, including the use of carbon-composite tubes as rotor arms for their light weight and mechanical stability, the system’s autopilot and flight behaviours have taken inspiration from the natural world – the goshawk bird of prey.
“A hawk needs to be able to fly fast, it needs to track and pursue its prey, and it needs to be bigger and stronger than its prey in order to carry it, so we’ve carefully engineered our sensors for its autonomous intelligent vision, and our motors for fast flight and heavy lifting. Capturing trespassing and hostile drones is done by a net because effective talons don’t exist yet, and for other advantages which we’ll explore later,” says Hagai Balshai, CEO of Robotican.
The Goshawk Interceptor and its parts have been fully developed in-house at Robotican, as its engineering team and departments cover the gamut of disciplines needed to put a high-speed, high-power autonomous UAV in the field.
“From software to electro-optics, gimbals, mechanical hardware and avionics, everything was designed in-house, with just some mass-fabrication solutions like PCBs done by outside suppliers,” Geva says.
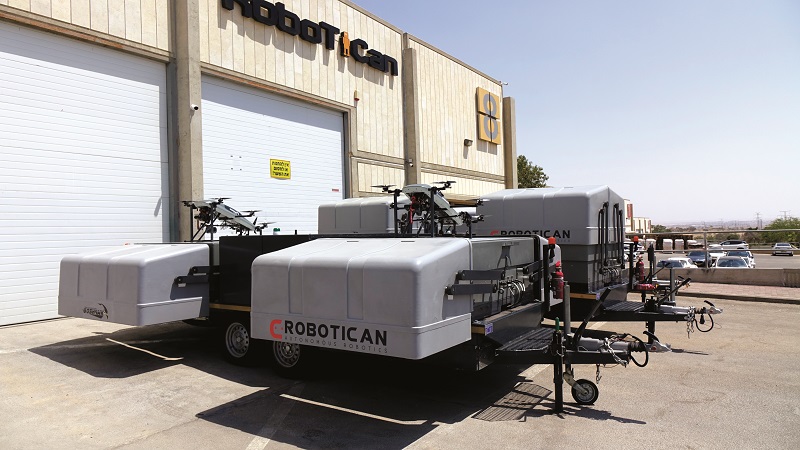
The Smart Nest
Whenever a Goshawk Interceptor is not flying or undergoing repair, it is enclosed inside a base station, designed and manufactured by Robotican, which it calls the Smart Nest.
The Smart Nest’s critical functions include safe housing of the Goshawk against weather and other environmental sources of wear, an automated door for opening or closing over the vehicle (with minimum maintenance requirements for the electric motors governing the door), monitoring the UAV’s health between operations and recharging its battery.
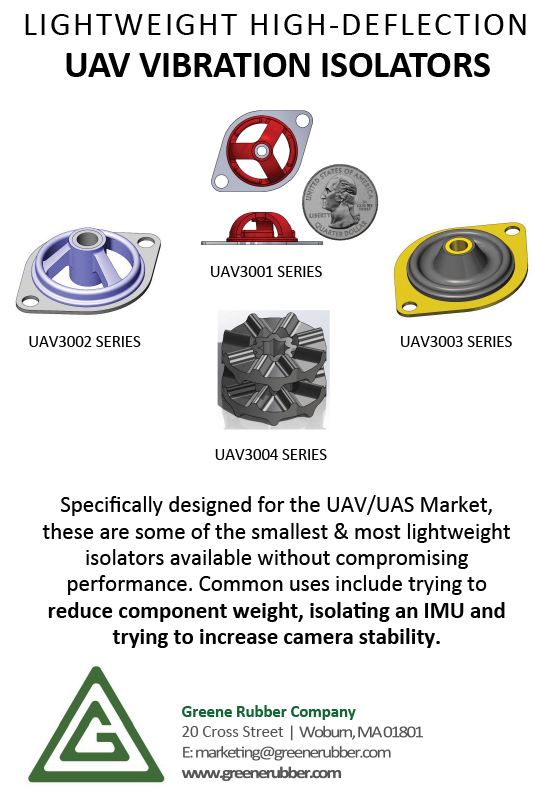
“Monitoring and recharging are carried out in an automated way inside the Nest, such that it keeps the UAV ready for its next flight, with defence customers in particular being really insistent that the UAV has to be ready to launch at a moment’s notice,” Balshai says.
“The door is designed to open within six seconds of a threat detection signal being delivered to the Smart Nest, and the monitoring system is designed to prime the UAV for take-off within that same timeframe. For defence-type or similar kinds of site deployments where a threat spells a really urgent response requirement, the embedded monitoring software works in a standby mode.”
In that mode, the Goshawk is always powered-on in a steady way for all hours of the day and night, its subsystems being checked to pre-clear it for potential flight within a few moments. This makes its usage and power cycling quite different from the commercial drone-in-a-box use-case, in which one can picture UAVs stationed at an industrial asset taking off once a week at most for mapping and inspection flights, with their batteries preserved at a lifespan-extending 60% state of charge (SoC) between those flights and all their avionics switched off or routinely power-cycled.
“Our UAV doesn’t get that kind of downtime – a hostile drone attack could come at any moment. We’ve had to rethink and reengineer the usual way of doing drone boxes so our Smart Nest will always open successfully, always seal against dust and weather properly, and always monitor accurately. It contains redundancies for electricity, battery recharging, switching between generators or grid connections depending on how power is run to it, and many related areas,” Balshai adds.
Each Smart Nest integrates a meteorological station for tracking weather conditions over its UAV, as well as radios and antennas for communicating over a data link configured to the customer’s preferred frequency band and encryption. Therefore, if conditions overhead are not fit for a safe take-off and expedient flight, it can communicate via a neighbouring Smart Nest if the use of a mesh network is required to a flight operations and monitoring team using Robotican’s mission-management software.
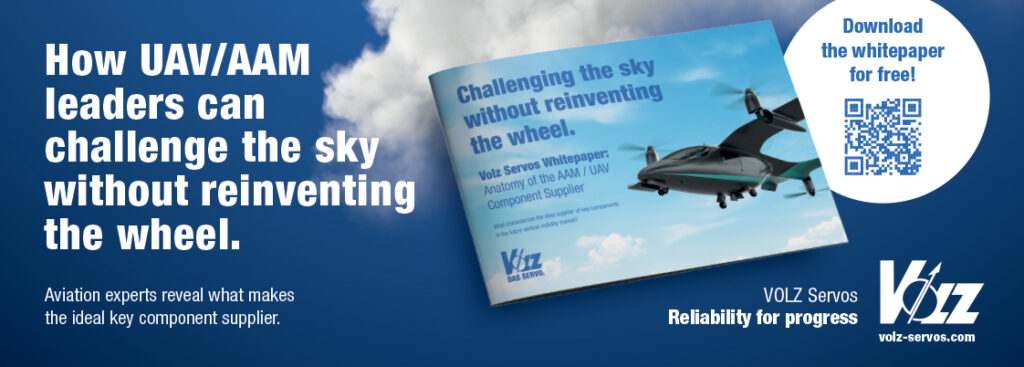
The Interception Management System
The company’s software interface for flight monitoring, fleet management, and mission planning and configuration is the Interception Management System (IMS). Its capacity for plug-ins is designed such that it is agnostic to the form of detection system, so any end-user – regardless of their radar, signals intelligence (SIGINT), machine vision, thermal or other sensor network – can integrate their security network into the IMS, so long as a digital alert (preferably automated, per the autonomous nature of the Goshawk) can be triggered and delivered to it.
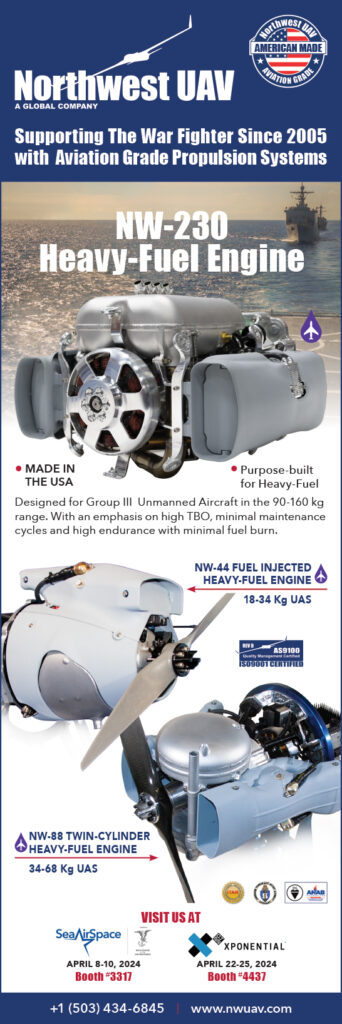
“Through the IMS, and the wireless links to the Smart Nests and Goshawks, the monitoring team can bring up displays of all Interceptors’ live aerial imagery, their flight and health statuses, and the estimated locations of all targets,” Geva says.
“There are several flight-management parameters that the end-user can specify, as needed. You can, for instance, delineate no-fly areas, or even draw preferred routes or corridors that you want some of your UAVs to keep to when they have to cross through certain areas. For example, if you’re in a city and there are some populated areas, you don’t want a Goshawk to fly directly over; otherwise it will generally opt for taking the most direct, straight-line route to catch the target as fast as possible.”
The IMS allows remote monitoring and diagnosis of all the Smart Nests, as well as the user’s own detection hardware, and it keeps track of Goshawk part inventories for maintenance purposes. Fleet management measures, such as ad hoc selections and prioritisations of targets to engage, can also be performed, if multiple hostiles present themselves simultaneously. In such an event, the management software will automatically select the best Interceptors for the jobs, such as the closest ones that present no potential health issues, possess sufficient battery energy for the range requirement and have the least blockages in terms of no-fly geofences.
“Once the drones for the engagement are selected by the user or by the IMS itself, that’s where the IMS’s involvement ends – it’s a monitoring system, not a control system,” Geva notes. “This solution is meant to be autonomous. The software arranges for a last-known target position to be transmitted to the Goshawks, via the Nests’ antennas if necessary, and it’s the Goshawk that plans and recalculates its own routes, and adjusts its own gimballed HD camera to try and find the target visually.
“The monitoring technician can change the target mid-mission or cancel the engagement – for instance, if they’ve realised the target isn’t a hostile drone, or a drone at all. Radar sends false targets sometimes. They can then select other targets, maybe perform an inspection mission while they’re in the area of some important infrastructure or tell the UAV to return to its Nest.”
Robotican has also developed a digital simulation solution called Sphera, which is used to recreate and trial all of the company’s uncrewed vehicles within a virtual environment.
“In Sphera, we can simulate full scenarios within a 3D, photorealistic environment featuring high-fidelity dynamics, and naturally that includes twinning geographic locations with multiple Nests installed and multiple threats inbound,” Geva explains.
“The IMS software can be plugged into Sphera to train the monitoring crew. As operators’ interactions should be in a fully autonomous operation, there’s always going to be room for mistakes. So, the twinning software closely models the exact dynamics of the Goshawk and how it behaves in different weather conditions. As much as it was originally intended as a development tool, it has migrated to become a training solution too, which we now sell to other companies.”
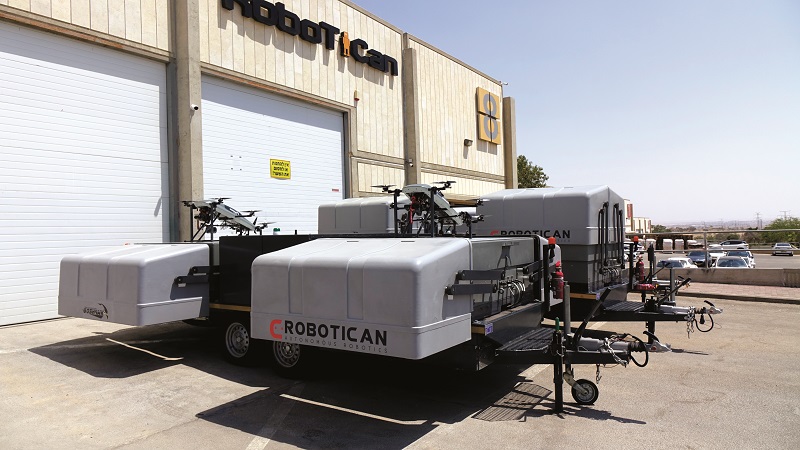
Threat detection and take-off
Once an end-user’s detection sensors and infrastructure have picked up a potential threat, the signal and location are sent to the central IMS network, which then selects the ideal UAV for the job, based on factors such as proximity, the absence of geofencing-related obstacles and flight-readiness, including health and battery energy.
Cameras inside each Nest look down at a set of health status and battery charge indicators on the Goshawk’s hull, which function as typical for industrial machinery status LEDs: particular flashing sequences or levels will indicate problems that the remote operator (or a technician in the field, if present) can address.
“But, obviously, the wireless radios in the Nest and UAV are working all the time, because the UAVs must always be kept warm for sudden take-off, so they can constantly communicate their health status to each other, with specific internal checklists running on the UAV persistently, covering all subsystems. The packs are kept at 100%, so the LEDs are just for the humans in-the-loop,” Geva says.
The Goshawk will tilt its gimbal upwards after a launch sequence has been triggered to confirm that its Nest’s doors have opened successfully (rather than relying on an open-loop of simply being told by the Nest that it has opened its doors, which could present a problem for the UAV if the Nest’s sensors are at fault).
“As security is an asymmetric problem these days, and the threat of swarming drone attacks is a looming concern for some, we work closely with customers to assess the smartest way to deploy Nests for each facility’s unique threat level,” Balshai says.
“For instance, some might feature multiple attacks at a certain portion of their site, and so maybe more than one Nest and Interceptor at that area is smart. On the other hand, the UAVs don’t always have to return to their Nest, or even to another nest – the Goshawk has carbon-fibre landing struts for touching down anywhere, and technicians can simply drive or walk over at the end of the day to collect them once the area is deemed safe.”
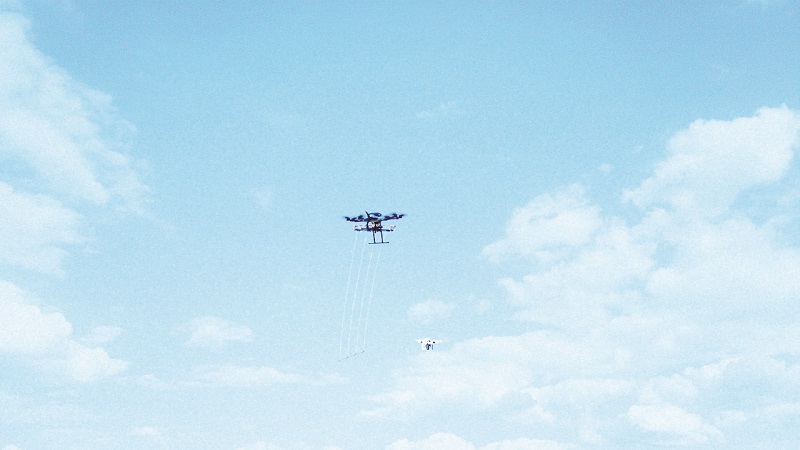
In pursuit
Such is the level of autonomy in the Goshawk and Smart Nest mission infrastructure that waypoints are not used in the path planning and guidance of the Goshawk, or at least none visible to the monitoring crew other than any pre-set preferential flight corridors which the UAVs opt into when flying through the affected areas.
“Although the operator can set such barriers, geofences and preferred path sections, and the Interceptor takes these into account, it’s the UAV that plans its own route to the target, constantly checking that path and if it still leads to the target, based on where the detection system or the UAV’s own camera say it is,” Geva says.
“We often expect that a hostile drone won’t be stationary; it’ll be manoeuvring, climbing, accelerating and so on, and so the Interceptor must be able to detect changes in where the target seems to be, relative to where its own GNSS and inertial system says it is, in order to keep homing in on the target until the capture stage can be initiated.”
Part of this is achieved by the Goshawk changing its search location in accordance with changes in the target’s location, as communicated by the end-user’s ground-based detection system.
To develop the Goshawk’s embedded software, Robotican made use of certain open-source frameworks, including choosing ROS 2 as its middleware. However, its capabilities in the detection, recognition and tracking of objects such as other drones were developed in-house through machine learning.
“We used tens of thousands of images of potential enemy drones with an artificial neural network to train the software to detect hostile UAVs, and we developed some very unique detector and tracker software modules that work together with the guidance algorithm to produce the homing intelligence by which the Interceptor closes in on its targets,” Geva says.
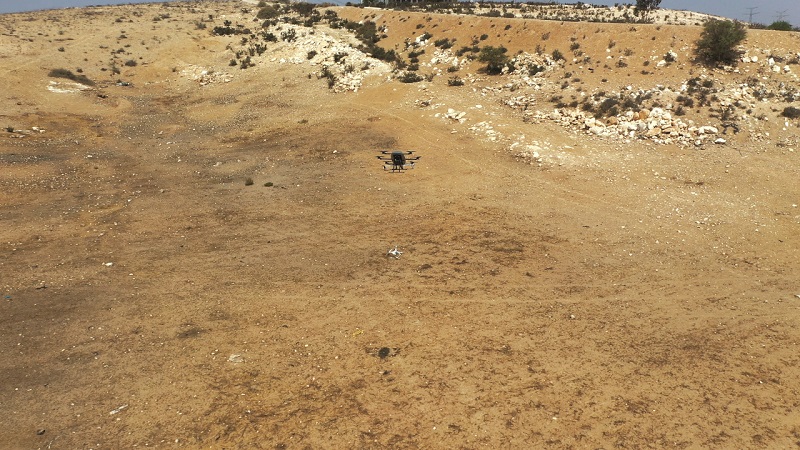
Capture and disposal
Notably, the capture mechanism in the Goshawk has not been designed for any firing of net- or water-based projectiles, or jamming signals, as sometimes seen in automated, remotely piloted or handheld C-UAS devices. Instead, a ‘net’, typically consisting of four cords, hangs from beneath the UAV like a curtain.
The net’s cords are linked together by a single rod at their lower end and from a long, rod-shaped magazine payload suspended just below the multirotor hub. These two structural rods ensure the Robotican’s unusual form of net doesn’t twist or tangle in the wind. In almost all instances, it hangs in the same direction, with the cords running along the breadth of the Goshawk.
Capture works by the Goshawk intercepting a target drone, releasing a net to unroll and hang below, and then flying such that the arms and propellers of the target become entangled (non-destructively, it is important to note) and its motors are jammed. The craft is hence arrested and carried securely by the Goshawk.
“The Interceptor will specifically aim to fly above the target to catch it in the net hanging below. That’s harder to do than just flying into the target, like I know some self-destructive C-UAS drones have been made to do, because the Interceptor doesn’t always have a clear view of the target from above,” Geva explains.
“It’s also much easier computationally than aiming and firing a net, for which you’d have to do a bunch of targeting calculations, as if you were firing ordnance. Those kinds of solutions also sometimes require that the UAV firing the net comes in a really specific direction relative to the target. They need really precise timing to pull off the shot exactly right, and they also often have to take greater account of the wind speed and direction than we do.”
The Goshawk’s algorithms pertaining to capture include some predictive measures in addition to the flight-path calculations being made post take-off, as it must consistently be able to capture potentially threatening moving targets, whether a head-to-head approach is taking place or a chase scenario in which the Interceptor must catch up to a drone and not allow it to escape.
“Luckily, the Goshawk is faster than most commercially available UAVs, to the point that it can perform captures from many different angles of attack, including coming up behind a target multirotor, and then quickly surpassing it, and doing a U-turn to capture it and drag it away from wherever it was headed, such as its intended target,” Geva says.
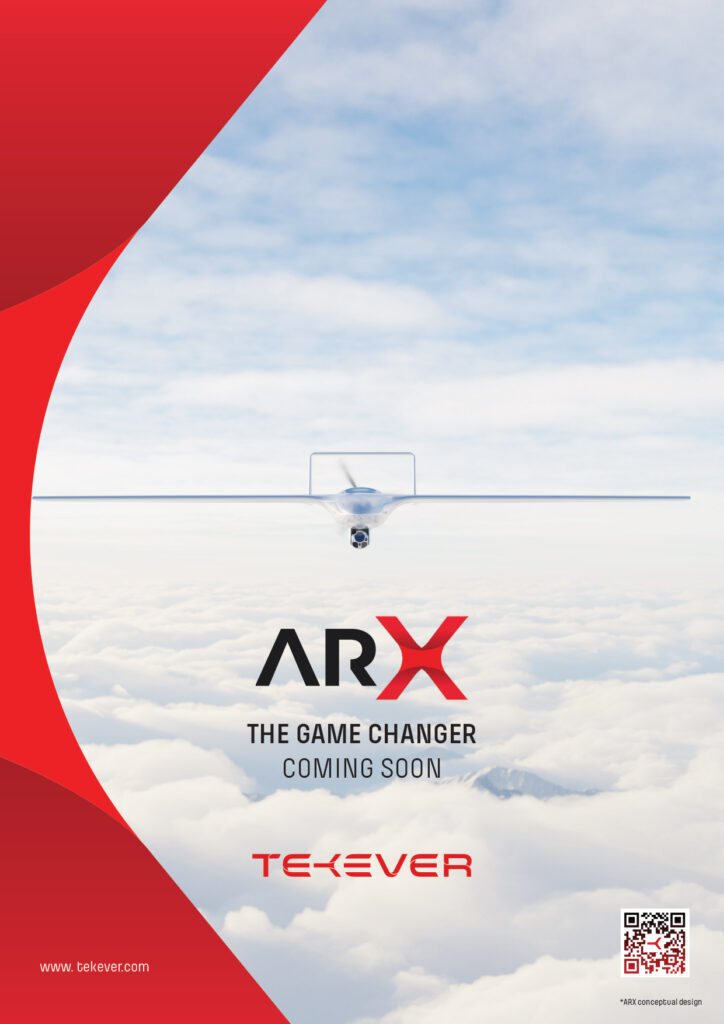
“The bracket holding the net before it is deployed isn’t a single-fire solution. Each Interceptor can carry a magazine stocked with multiple nets, and each net can be electromechanically detached from the UAV in order to dispose of the net and thereby drop the captured hostile drone in a place that the end-user chooses.”
Carrying multiple nets has benefits beyond swarming attack scenarios requiring multiple captures per flight. In some rare cases, the Goshawk may miscalculate its angle of attack and fail to capture its target, damaging its net on the target’s propellers or obstacles such as tree branches in the process. In such situations it is important that the UAV can discard the affected net to switch to one functioning optimally.
“Creating this net took a lot of trial and error. We tested a lot of different capturing solutions, including many inspired by other C-UAS drones, and although defence buyers tend to like the idea of shooting a net from a UAV-mounted cannon, in the end they need a solution that works consistently in capture and disposal, and doesn’t place too much computation burden on the Interceptor,” Balshai says.
The optimal disposal location depends entirely on the use-case and the security risk. Locations where attacking drones are suspected to carry ordnance (including improvised explosive devices) will require a highly isolated drop-off location, deserted of personnel and devoid of anything that could cause harmful shrapnel to fly far away.
“Although a mission should be fully autonomous, if the end-user wishes they can take control of the gimbal to pan down and look at the captured drone, to assess its model or view if it’s carrying anything of concern,” Geva notes.
Regardless of the location, dropping both the net and the offending drone there ensures the latter remains entangled and hence immobilised until a specialist team can arrive to take care of it, if necessary.
“Lowering the net and releasing it works via a combination of an electromechanical actuator that moves to first release the net, and an electro-motorised wheel for unrolling it, so it is suspended below the Goshawk. The actuator can then also detach the net once the Interceptor has captured its target and flown it over the disposal area, with quite a bit of r&d going into designing the ability to do both the deployment and release of the net with a single actuator,” Geva says.
“When you’re reloading nets into a magazine, the actuator and wheel help mechanise the installation and stowing of new nets, so we’re getting as much use as possible out of the electromechanical parts.
“But we don’t over-stress them at all; we want to be cost-effective. The wheel is very useful for lowering the net, but it doesn’t need to produce a lot of torque to do that – gravity does most of the work there.”
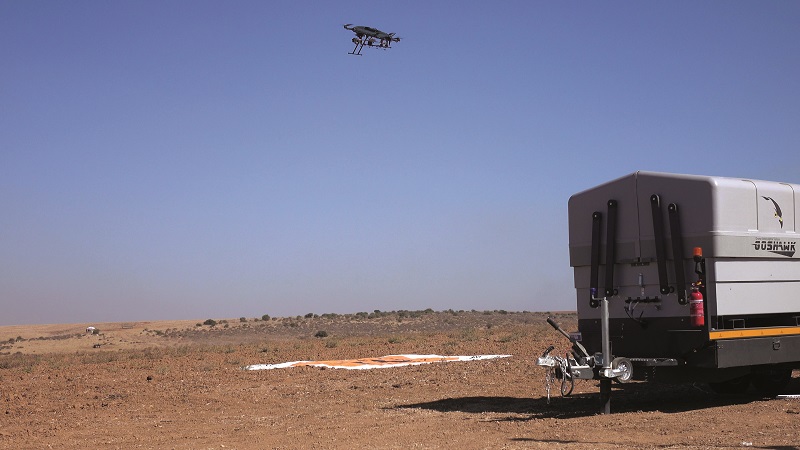
Return to roost
Once all of the hostile targets have been addressed, the Goshawk can return to its Smart Nest, or to another if the IMS determines a different one is available and no efficiency is lost by switching.
Wireless communications between the UAV and the Nest ensure the timely opening of the latter’s doors (and again, the UAV’s cameras and embedded AI can confirm the doors have opened, rather than risking a situation where they have jammed and the Nest has sent a false positive).
Once it has landed, conductive charging via connectors on the landing pad commences via the Goshawk’s struts, with the ensuing battery replenishment using the same power source and connection that kept the UAV fully charged and ready for action pre-take-off.
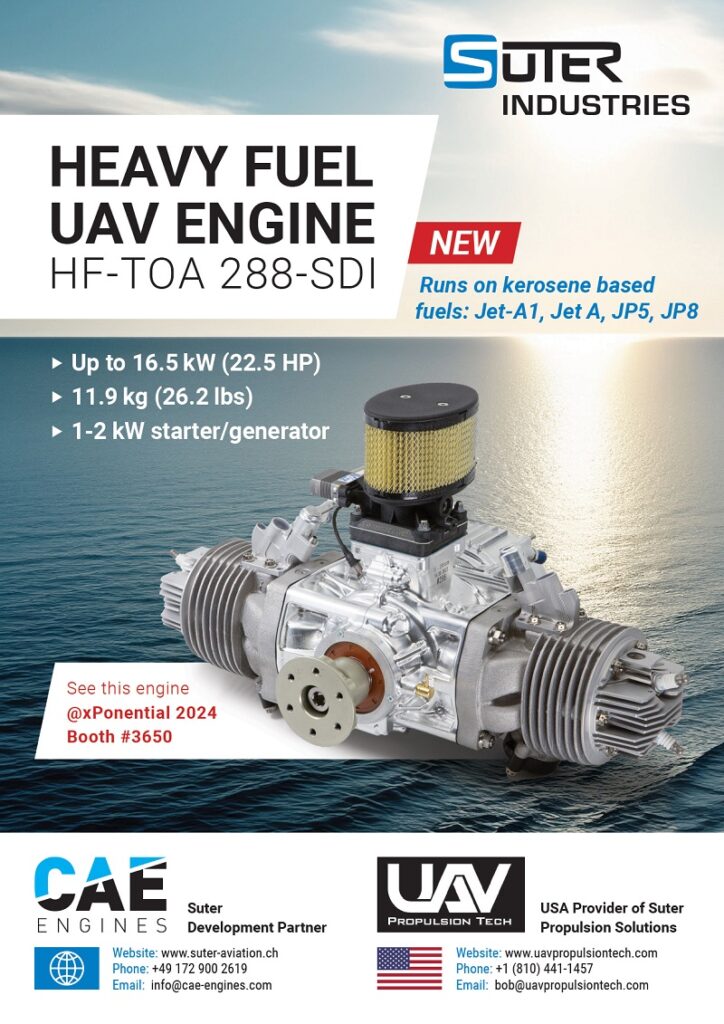
“Wireless charging is interesting, but at the charging rates and efficiencies currently possible with such technologies, the amount of power and time it would take to bring the Goshawk’s battery from empty to full is too much for our users. In defence, you want to do things as fast as possible, and be ready for the next mission as fast as possible,” Geva says.
“That’s why we also have the option to change packs by hand, which is even faster than fast charging. You just come to the Nest, click a button on the Interceptor to open its battery panel, replace the pack and it’s ready to go.”
Future flight
Over the forthcoming months, Robotican plans to continue working with its various customers in not only the defence sector but also in the energy sector, and others in the commercial world with vulnerable critical infrastructure.
As troubled as they may be by the increasing threat of autonomous drone attacks, more people are realising that autonomy can also be the solution to their problems, as Robotican’s systems are.
The company is also set to gradually announce some key partnerships over the next few years, while also working on ways to optimise and expand its technological offerings.
Such offerings include the unusual Rooster UAV. Just as the Goshawk was named after a raptor, for its job of capturing other flying creatures, the Rooster is designed to travel safely and energy efficiently along the ground, rolling around to conserve energy when obstacles are minimal and flying when there are many in the way.
Key specifications
- Goshawk
- Hexacopter
- Battery-electric
- Dimensions: 97 cm length, 110 cm width, 55 cm height
- Maximum take-off weight: 21 kg
- Minimum endurance between charges: 10 minutes
- Maximum airspeed: 108 kph
- Maximum carry capacity for captured drones: 7 kg
- Maximum combined thrust from motors: 6 kg
- Maximum battery energy capacity: 5 Ah
UPCOMING EVENTS
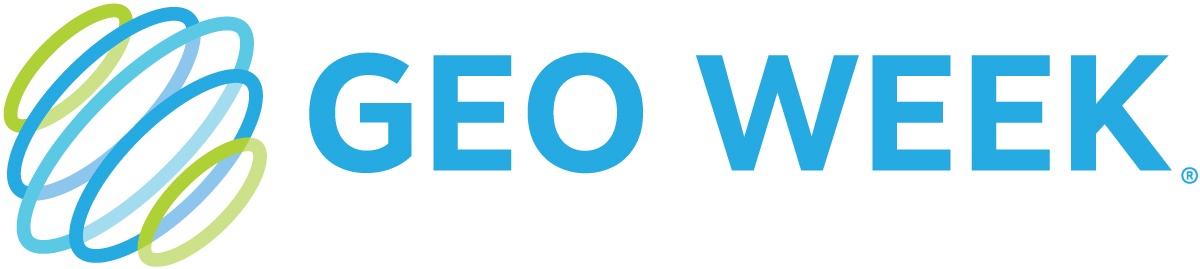
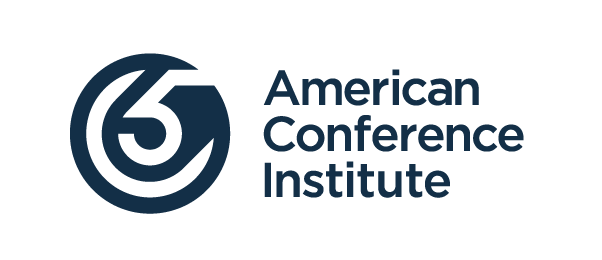
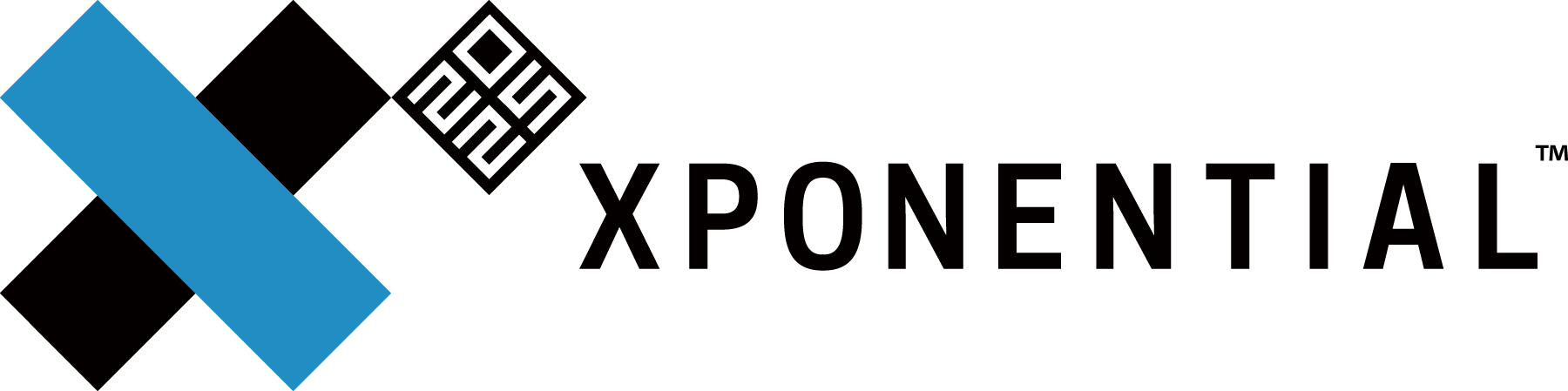
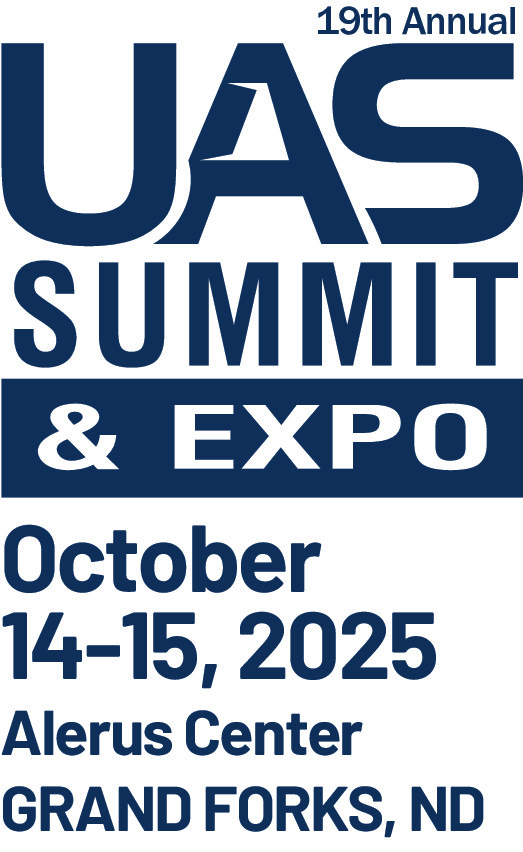
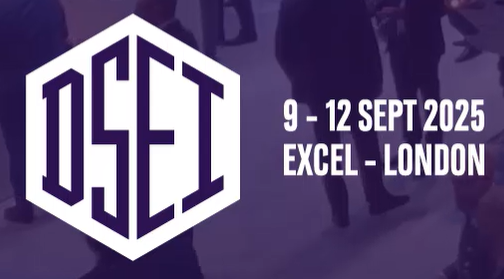
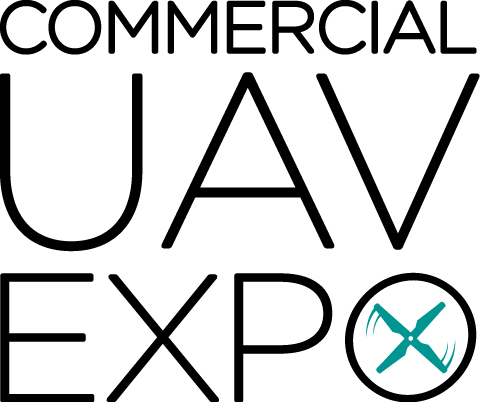
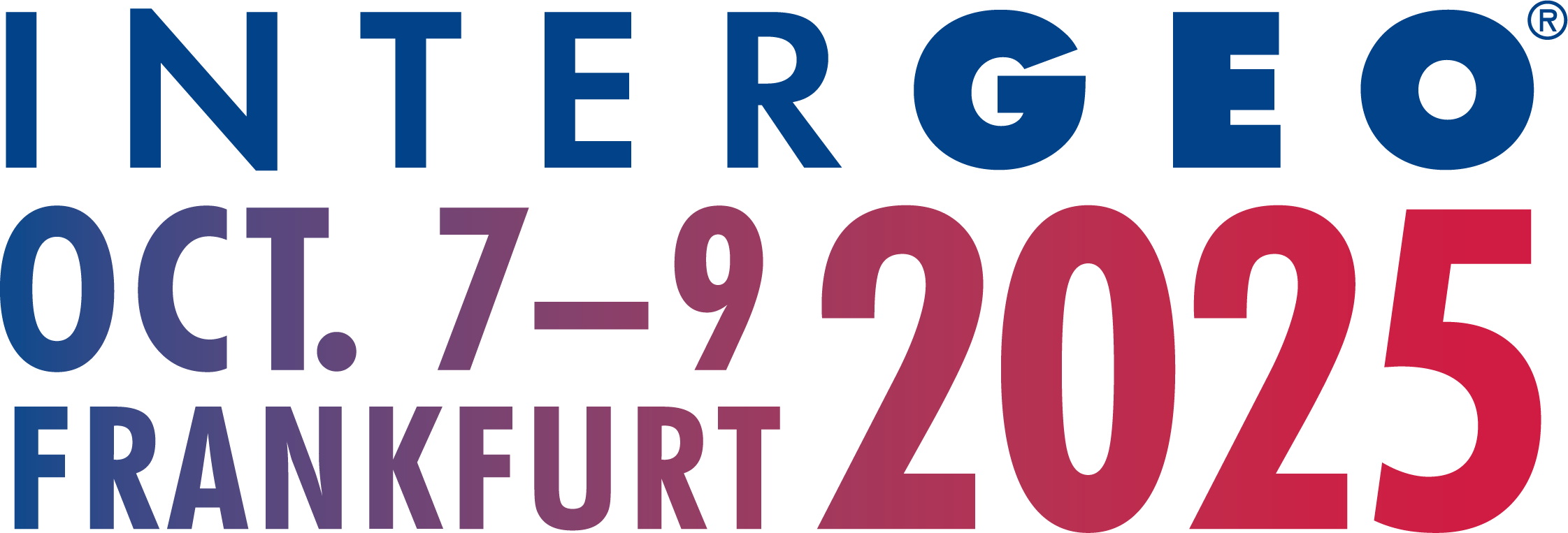
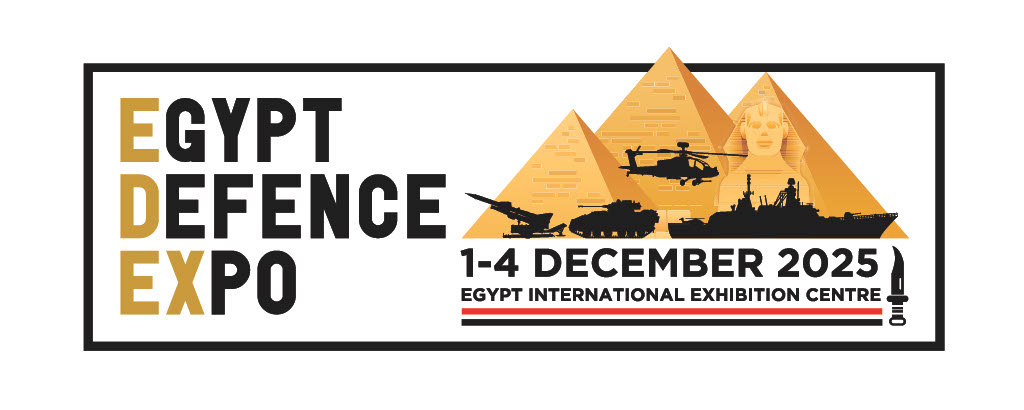
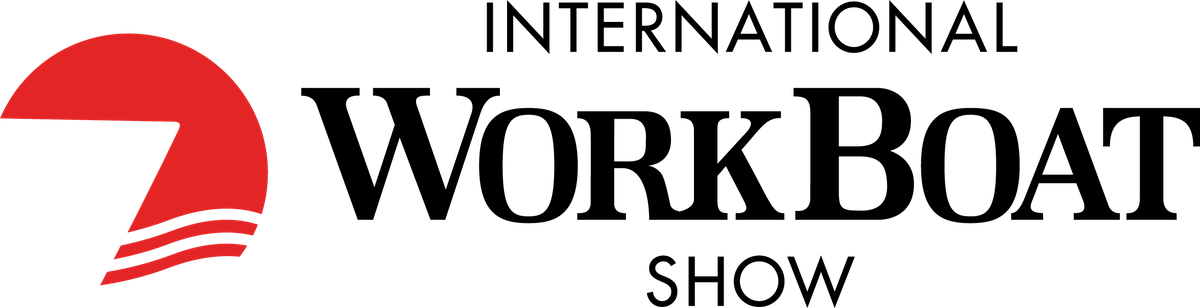
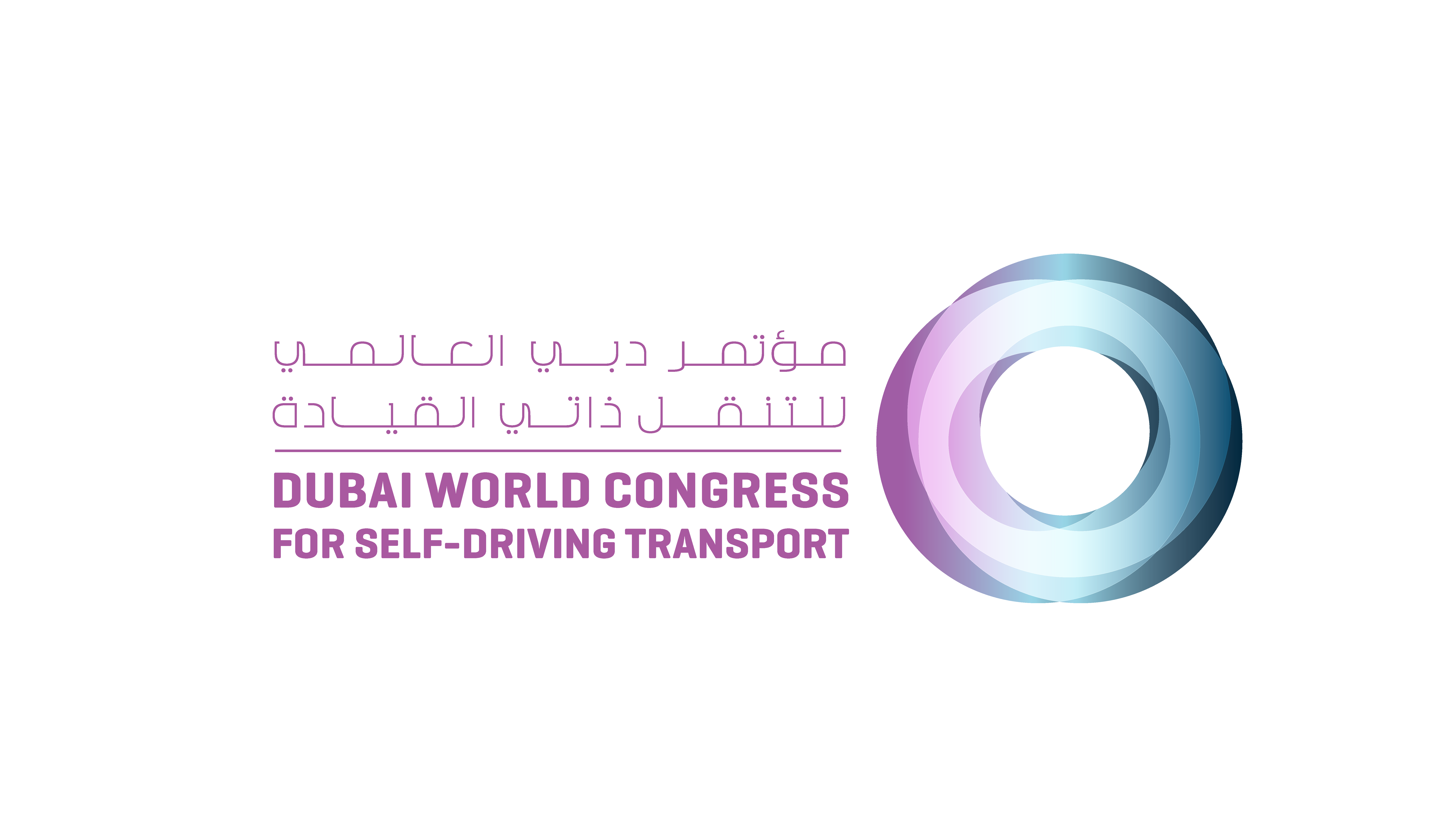
