Intergeo
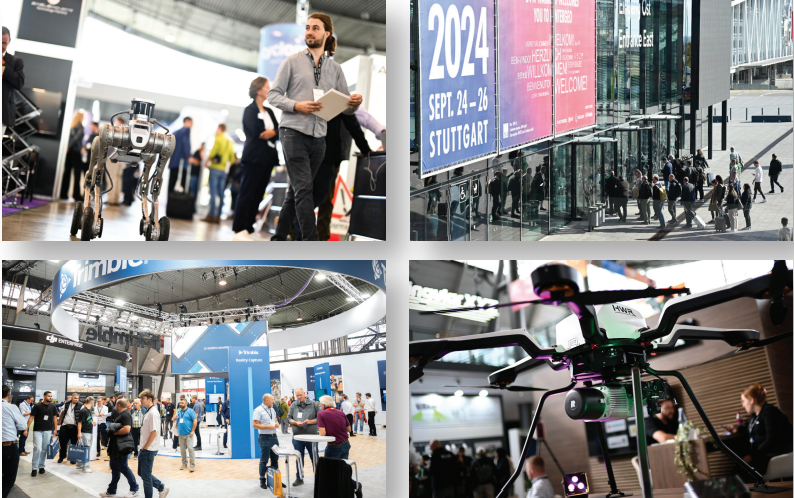
Geospatial update
Intergeo’s trio of expo halls played host to an array of new tech, as Rory Jackson reports
In September 2024, Intergeo continued its record of leading the way as a platform for new innovations and announcements in the world of all things geospatial, bringing together 579 exhibitors and more than 17,000 visitors from 121 countries across its expo floor. The conference, meanwhile, attracted an audience of about 800 people from 47 countries to discuss AI, digitalisation, Earth observation, and the ever-growing role of uncrewed systems in geospatial survey and inspection.
With the Messe Stuttgart playing host to this 2024 edition of the show, the three expo halls of Intergeo naturally housed hundreds of new products in GNSS, connectivity, photography, data processing and uncrewed vehicles, a selection of which are discussed below.
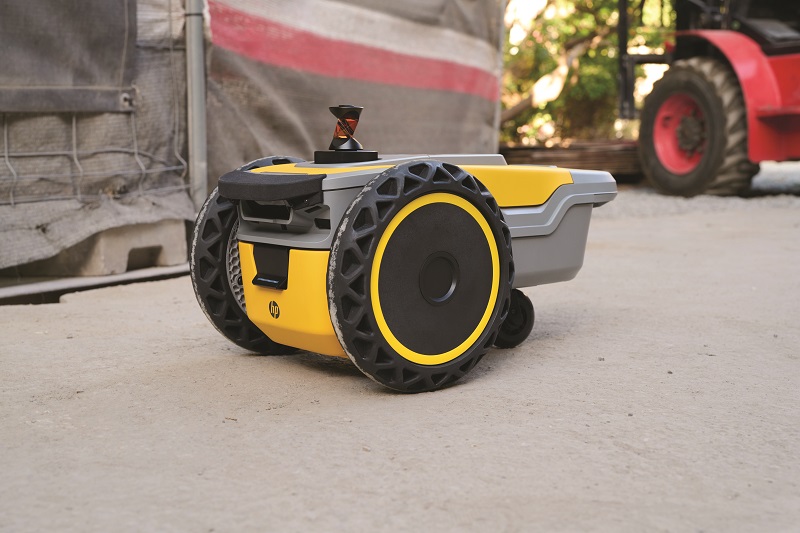
While HP is best known as a producer of computer, printer and related IT systems, the company attended Intergeo to demonstrate a small UGV it has developed for floor-layout line-printing of construction sites. HP SitePrint is a robotic solution that prints the most complex layouts with pinpoint accuracy, empowering construction professionals with significantly increased productivity over traditional, chalkline layouts.
“The robot HP SitePrint is developed by the company division, HP Construction Services,” said Sergi Gilabert.
“Barcelona is home to HP’s Large Format Printing headquarters, where we have a long history of printing for architects, engineers and other construction professionals. Around five years ago, we launched a project to investigate new niches and opportunities in the construction printing market, and that motivated us to consider the idea of, and then start prototyping, a robotic solution for autonomous layout in construction.”
Construction site layout is typically done manually, and is thus a time-consuming and physically onerous task. As the construction industry has failed to increase productivity over the last few decades, despite widespread stability and technological advancements, and the availability of surveyors has dwindled sharply recently, HP anticipates HP SitePrint to garner significant interest.
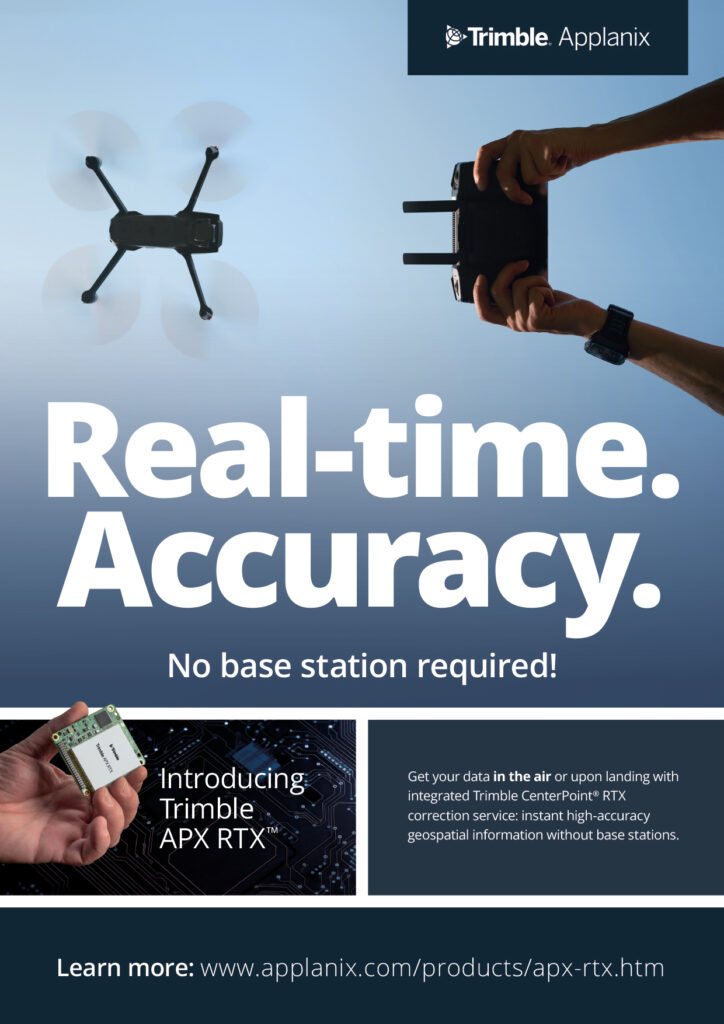
The HP SitePrint Robot operates with a Li-ion battery, enabling up to four hours of continuous operation (which can be quickly swapped for a fully charged battery to minimise downtime), as well as a 400 ml printer ink cartridge. It weighs 9 kg, measures 52.5 x 31.7 x 26.1 cm, and can move at speeds up to 2.52 kph, while printing up to 1.26 km of lines per hour.
TM IT-Systemhaus attended the expo to showcase its BeastTX GCS, for the growing industrial segment of geospatial specialists flying UAVs for their wide-area surveys, mappings and inspections.
The rectangular, handheld controller is CNC-machined from aluminium and weighs 1.5 kg. It sports a central, 7 in screen, multiple antenna ports, and dual sets of joysticks, buttons and flippers (for both left- and right-thumb interfacing), as well as rotary dials and a battery enabling up to six hours of operation.
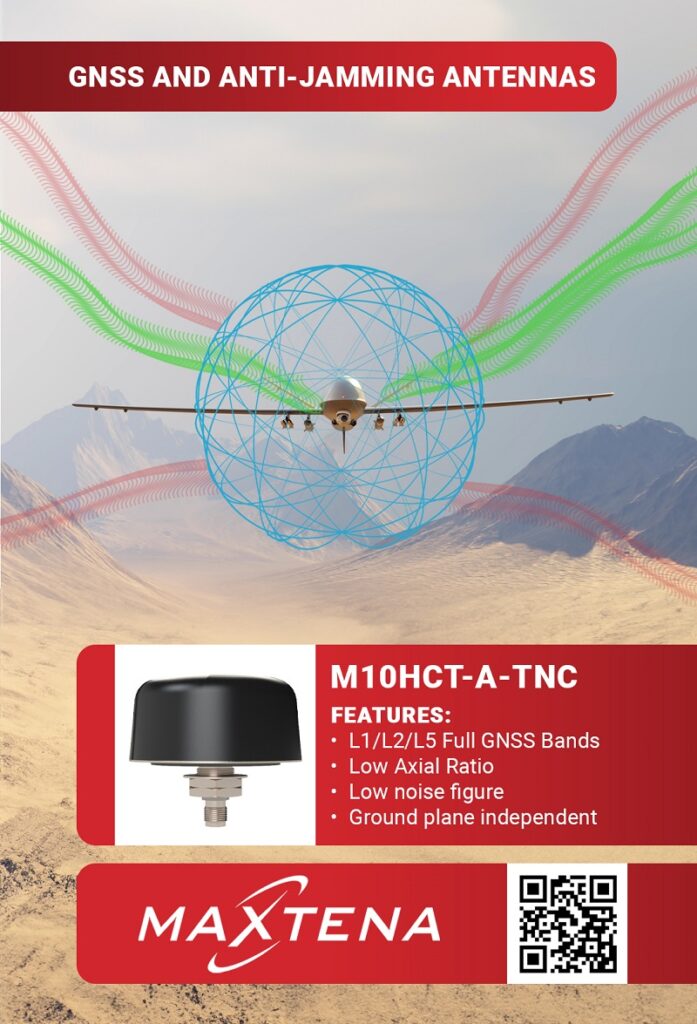
“The inventor of this product owns a fleet of agricultural survey UAVs, and was always quite frustrated that he had to carry around his own ‘GCS’ consisting of a laptop, ground antennas and many additional devices,” said Torsten Appelhagen.
“That complex arrangement merited a full car of equipment for every mapping job, so the general design for the BeastTX started more than 10 years ago, to create a GCS suited for our own purposes with all that equipment integrated into one lightweight device.”
Up to four data links can be integrated in the BeastTX, with any type that is compatible, including cabled connections to external radio systems if a must-have solution is too big for the housing of the handheld GCS.
Inside the GCS is a PCB, engineered to TM IT-Systemhaus’ own design, with a 500 GB SSD as standard (although up to 2 TB of space can be integrated) and a chipset chosen to accommodate the company’s embedded software requirements (and to avoid simply building around a third-party tablet).
“For now, we have an Intel x6425e quad-core CPU with up to 3 GHz processing speed, but soon we are switching to an even more modern Intel Atom CPU, which will give a great load of compute power for edge-processing real-world data in real time,” Appelhagen said. “That will mean end-users running UAS operations with the BeastTX won’t have to wait to get back to their offices to start making actionable information from their camera, Lidar or other data.”
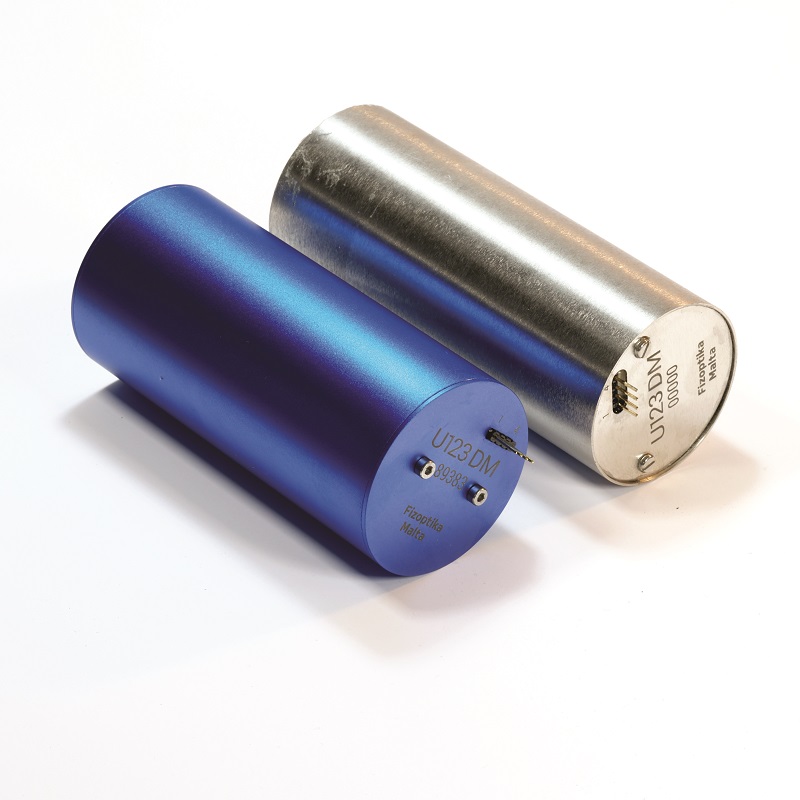
MostaTech has made a number of updates to its FOG IMU products, the first being some size reductions to the Maltese firm’s already SWaP-optimised systems and new advancements in its approach to magnetic shielding.
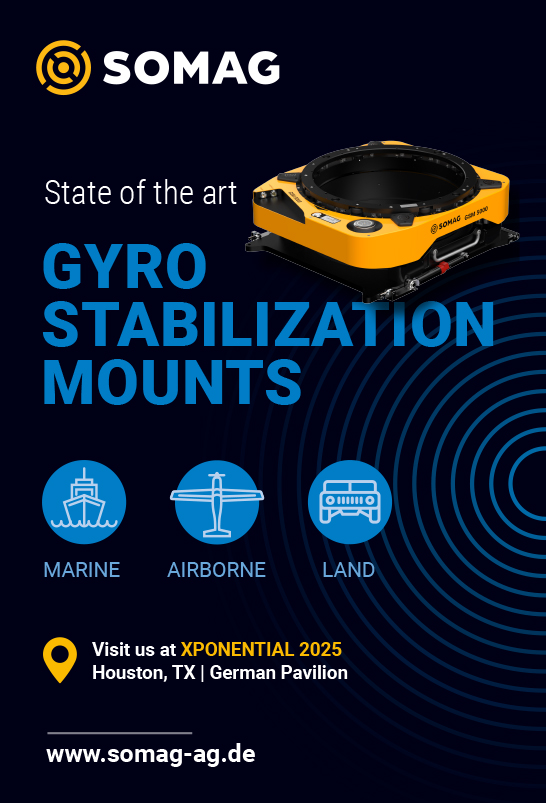
“Our U123D and U123DM FOG IMU products used to be 100 mm long. Now they’re only 90 mm long,” said Arthur Tua.
“Also, we’ve redesigned the product’s architecture from an external shielding to internal shielding, which makes for a lighter system as the external shield was quite heavy. It also makes the system easier to manufacture in terms of assembly being less cumbersome.”
In general, internal shielding features have much smaller, less problematic openings than external shields. In the U123 IMUs, each gyro is now individually magnetically shielded, with an aluminium housing encapsulating the product at system level.
Additionally, for clients with extreme shielding needs (such as those installing inertial systems close to large electric motors or other systems outputting high levels of EM radiation), the U123 IMUs can be supplied with both the internal and external shielding components, trading lightness for operational robustness.
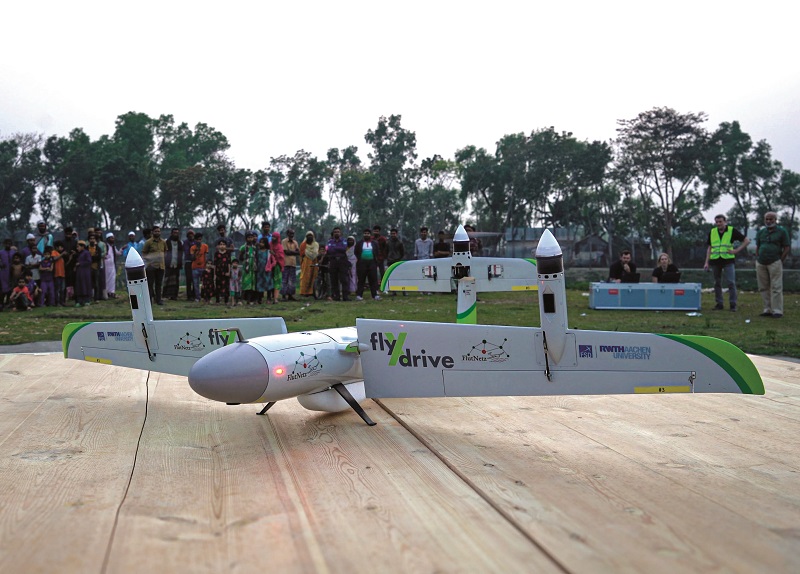
FlyXdrive, a spin-out from the Institute of Flight System Dynamics of Rheinisch-Westfälische Technische Hochschule (RWTH) Aachen University, exhibited to showcase the TW-Neo, its tilt-wing UAV that has successfully conducted demonstration flights for applications such as airborne medical logistics in various countries.
“The company was founded in 2017, principally for the manufacturing of its tilting-wing drone, the technology of which enables its VTOL flight system, and hence versatility in different services, among which are photographic and video survey for agricultural and other geospatial markets,” said Eva König.
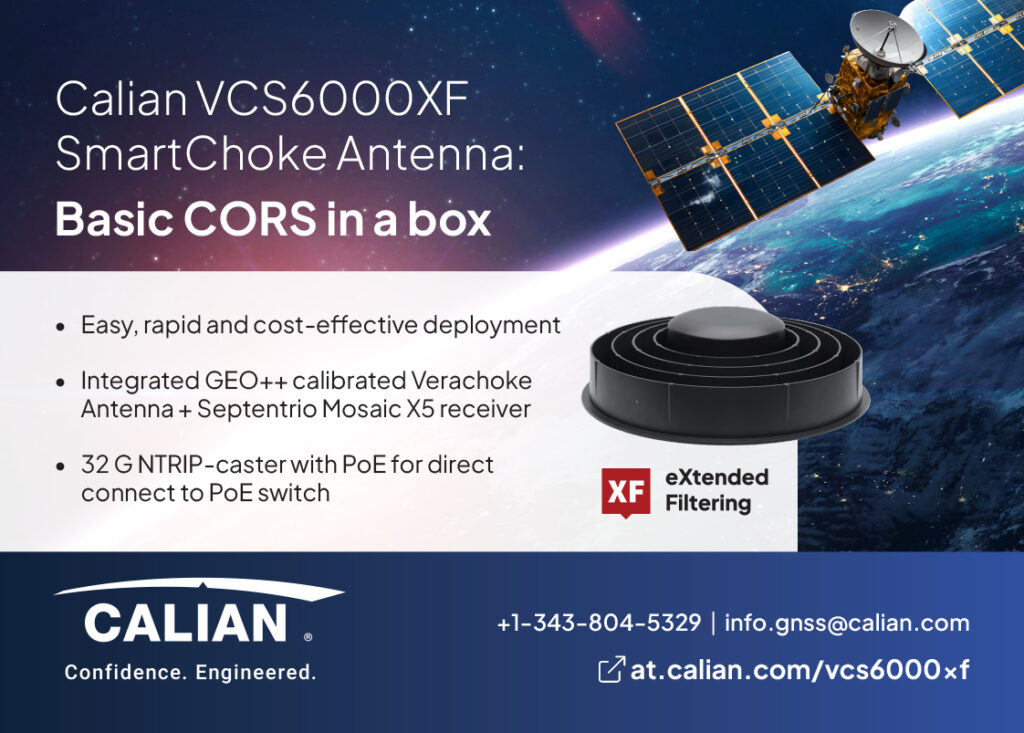
The TW-Neo UAV has a MTOW of 8 kg and a payload capacity of up to 2 kg. The aircraft is battery-electric and typically flies at airspeeds of 100-120 kph, with an average flight endurance of one hour.
To date, the craft’s (and company’s) most significant operation was a research project jointly conducted with the Institute of Flight System Dynamics, aimed at using the UAV to improve medical services in Bangladesh, particularly with reference to how that nation’s periodic flooding events make roads – and hence conventional medical aid logistics – impossible.
“Especially serious is that lots of people die from snake bites after flood events, because they can’t receive the life-saving anti-venoms in time, so in March 2024, we showed successfully that we could rapidly deliver those medications to victims in flooded areas,” König said.
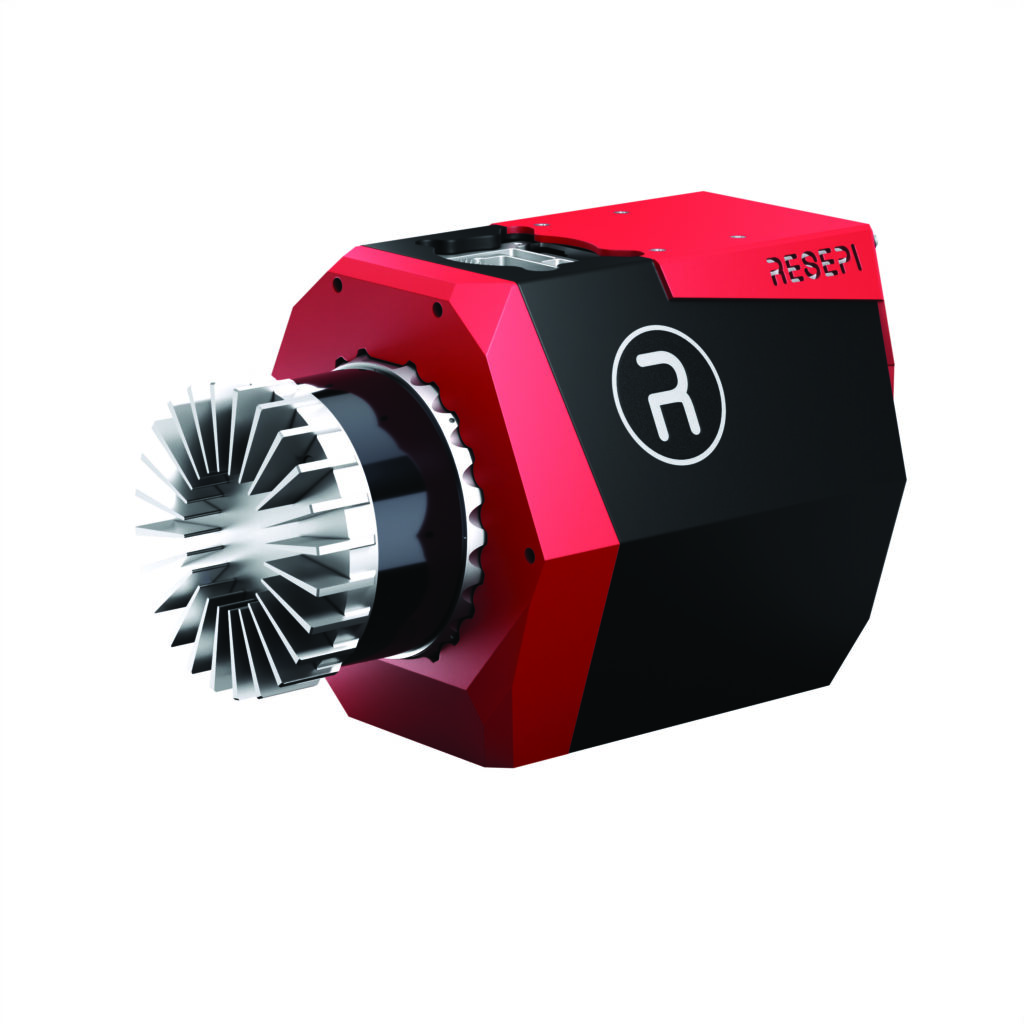
We met with Inertial Labs, which discussed the second-generation version of the RESEPI (remote sensing payload instrument) Lidar payload with us, the development of which was motivated by a combination of needing to update software and user experience features, and wanting to open up new markets for remote sensing.
“Traditionally, RESEPI has primarily been an airborne Lidar scanning system, and aerial users like to have some very particular features, like a real-time digitalised point cloud; that is, one that is interfacing back and forth with the UAV. And things like that required a CPU with an increased count of higher power cores to achieve the real-time computation of the point cloud,” said Will Dillingham.
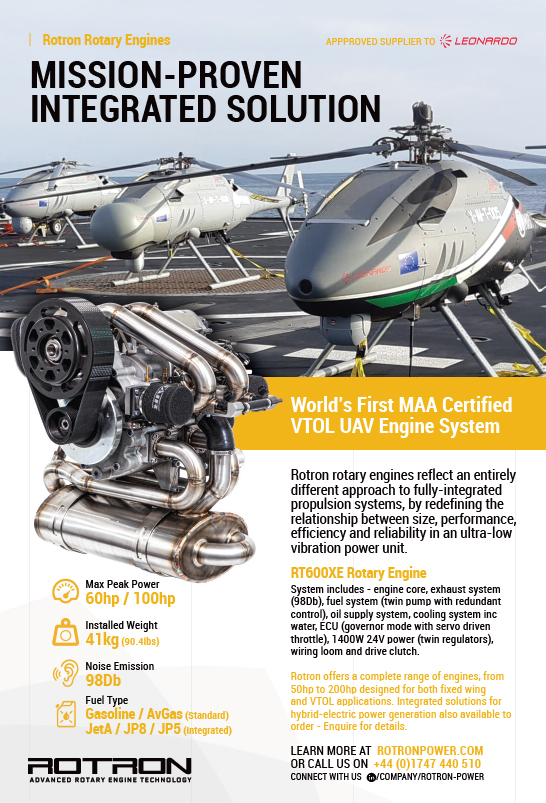
“It also required a lot more ports, both for electrical connections and signal interfacing, with not only DJIs but WISPRs, FreeFlys, Wingtras and all these other UAVs that businesses are flying, many of which have their own network languages and custom electrical interfacing.
“Making a single payload that can mount electrically and communicate smoothly with all of those isn’t easy, but it was maybe the most important reason behind making the RESEPI GEN-II.”
In addition to aerial survey, Inertial Labs is aiming the new RESEPI towards ground-based, mobile-mapping applications, which requires stronger IMUs, more electrical options for wheel-speed sensor integrations and more data ports (five-port Gigabit Ethernet is available, enabling arrangements such as 360o multi-sensor masts).
As with its predecessor’s general architecture, the RESEPI GEN-II features a front-mounted Lidar (this may be an Ouster product or a Hesai device) for point-cloud generation, and a downward-pointing camera (a RIEBO R2 or a Sony ILX-LR1) for overlaying colour and unlocking numerous intelligent features in the point cloud.
These mount on an enclosure that houses a six-core CPU from Variscite with 8 GB of DDR4 RAM and 16 GB of eMMC flash memory storage.
“Everything is CPU-based in RESEPI GEN-II, which is an important differentiator versus some other products. GPUs tend to be very power-hungry systems, and for UAVs, power consumption is flight time. There’s a crucial trade-off there, so limiting power usage by keeping everything CPU-based makes for a more viable product all-round,” Dillingham added.
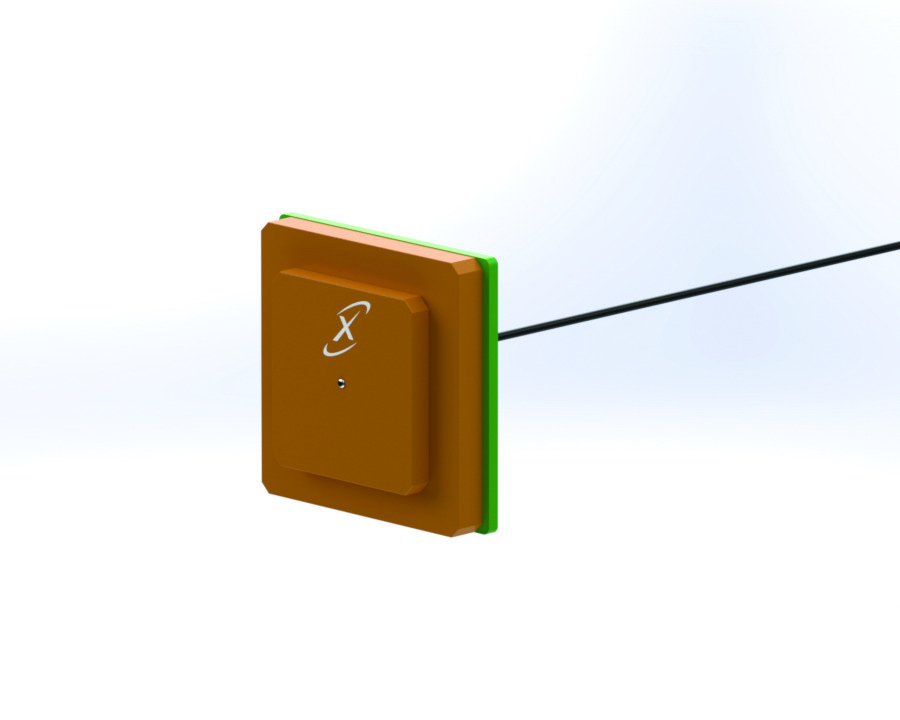
Maxtena launched its new dual-frequency band GPS patch antenna, the MIA-1227-1575A, so named for covering GPS L1 at 1575 MHz and L2 at 1227 MHz.
“It’s a ceramic, stacked, active patch in a 37 x 35 mm form factor; standard with a 240 mm cable and SMA connector, fully customisable for parameters like cable length and connector form factor,” said Arturo Proskauer.
“We’ve been working on this for a few months now and some of the top applications, given its light weight and small size and great performance, will be military missions, autonomous driving and high-precision robotic vehicles. It is designed and engineered onsite, and also tuned as needed for each specific application, depending on the device and environment of the antenna.”
A stacked patch antenna consists of multiple patch elements placed one over the other in descending order of size; two elements (corresponding to the two frequency bands) in the case of the MIA-1227-1575A. Active patches are those that embed circuitry and filtering within the antenna; in this instance via a PCB on the MIA-1227-1575A’s back side, with the low-noise amplifier (LNA) and front-end filtering protected behind a shield.
“Some customers may prefer a passive antenna, particularly if they want to control the design of the RF front end themselves. But the advantage with our active architecture is that we’ve designed, engineered and validated all these components to work very efficiently together within this form factor, which will save customers a lot of RF engineering work while also [being able to] perform in challenging environments and provide high accuracy,” Proskauer said.
“We designed the MIA-1227-1575A with efficiency and gain in mind, so it has a 50% efficiency and 32 dBi gain in both L1 and L2 frequency bands, which is not typical on these type of patches. Normally, you’d need a bigger patch that won’t perform as well, which will also translate into a heavier and more expensive UAV. We are also working on developing GPS-denied solutions for UAV and UGV applications.”
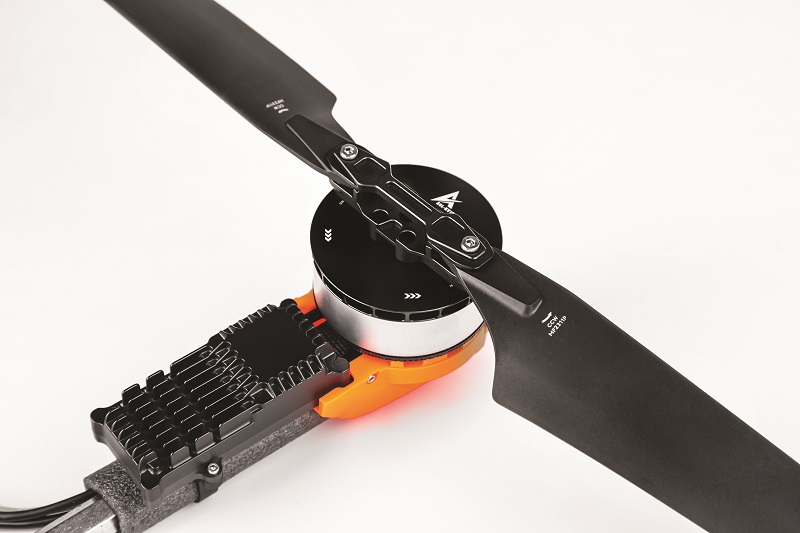
T-Motor showcased its new I7 products, which are its latest fully-integrated propulsion solutions for professional UAV manufacturers and integrators, consisting of electric motors, propellers and ESCs designed and pre-integrated onto a rotor arm.
By directly integrating the ESC into the motor, the design eliminates the need for a controller wiring harness and mechanical housing, enhancing space utilisation and energy density. The ESC also includes a risk-control function that performs self-checks before flight for common drone hazards, significantly improving flight safety.
“The ESCs built into these systems support two channels of communication: one is the traditional PWM and the other is a CAN bus interface,” said Travis Ma.
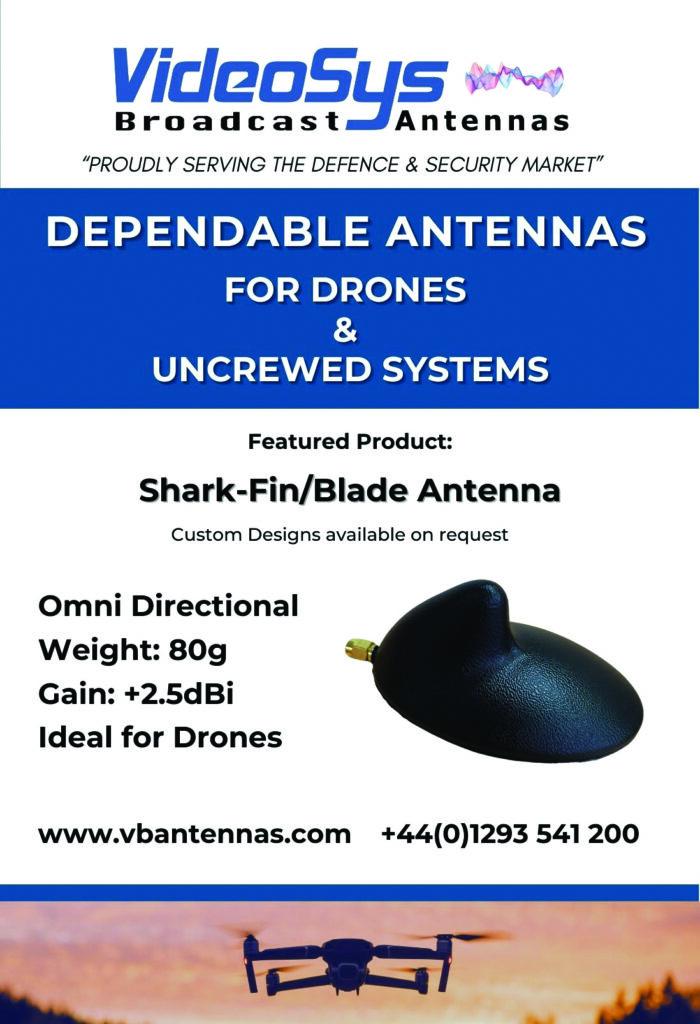
“Customers have been asking us for more CAN-compatible solutions, so with the I7, we’re releasing our first integrated propulsion units with the CAN protocol, as well as being our first products with both PWM and CAN. So UAV engineers can use whichever one they want, or perhaps use the simpler PWM during development and then switch to the more sophisticated CAN later on.”
The I7 series includes single-motor and dual coaxial motor designs, and it can be customised to user requirements. The I series propeller additionally features a quick-release design and advanced materials, which the company says reduces noise by about 15%, compared with standard propellers.
The company also exhibited its A Series modular propulsion systems, which mechanically and modularly combine motors and ESCs. They are initially slated for use in agricultural UAVs.
“Every product in the A Series has a high IP rating, so that means significant water and dust-proofing to help them work safely and consistently in fields, whether surveying or spraying very close to the ground,” Ma said.
“The A series is a new, modular power system for multi-rotor UAVs. There are 32 models – both coaxial and standard – from the A series, with a rated thrust range of 2-60 kg, and supporting 14S, 18S and 24S battery packs. It also scales for UAVs sized from 8-10 kg MTOWs, all the way up to very heavy, high-power multirotor aircraft carrying up to 70 L of agricultural chemicals per flight.”
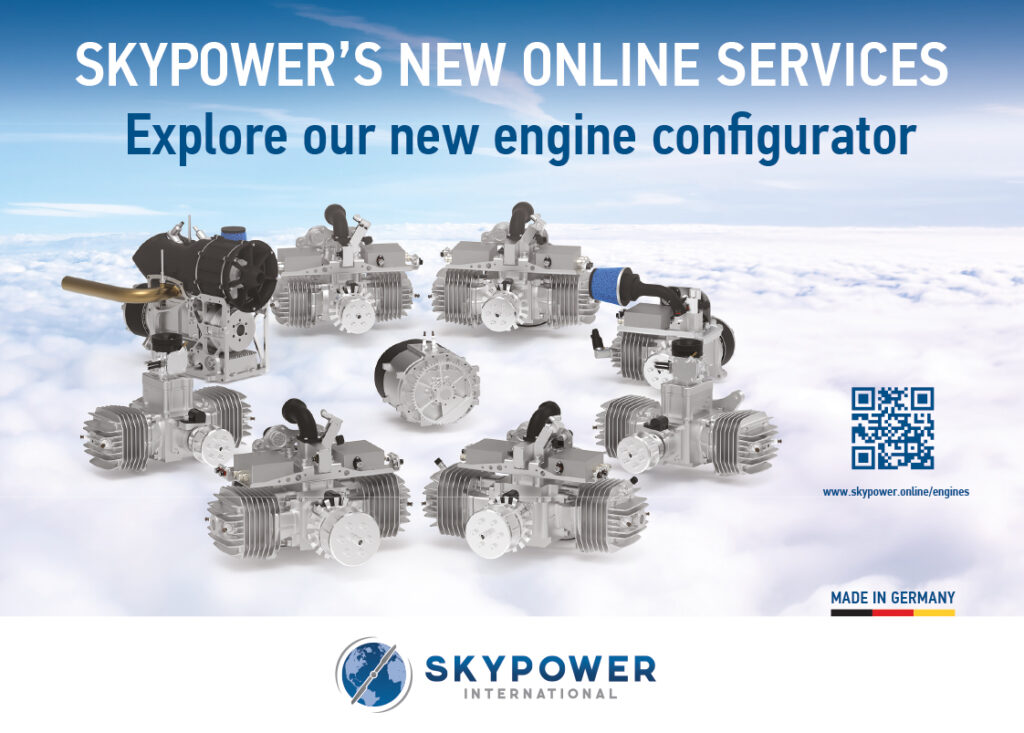
Netherlands-based UAS manufacturer Acecore Technologies showcased the latest version of its George GCS, a handheld tablet-type solution for mission planning and management for uncrewed vehicle operations.
“This is version two of our George controller, replacing the first version, as we’ve made changes to greatly improve the ergonomics. The GCS has a square-like shape for convenient storage and a much more comfortable hold, made from moulded carbon fibre rather than the square carbon plates in version one,” said Marvin van Lith.
“Additionally, the last version had an integrated battery in the case. This one makes use of a weather-sealed, V-Lock battery case on the back, which enables hot-swapping of any batteries with the V-Lock interface standard, so it’s way easier to keep constant power in the field. The back also mounts detachable harness holders for operators to suspend George from their necks using a harness, so they don’t have to constantly hold it or put it on the ground.”
In addition to its main screen (located between left/right thumb joysticks and several buttons), the GCS can come with an optional, detachable secondary tablet, pre-installed with mission-planning software for autonomous mapping flight-path generation, as well as simultaneous monitoring of FPV footage and payload camera footage.
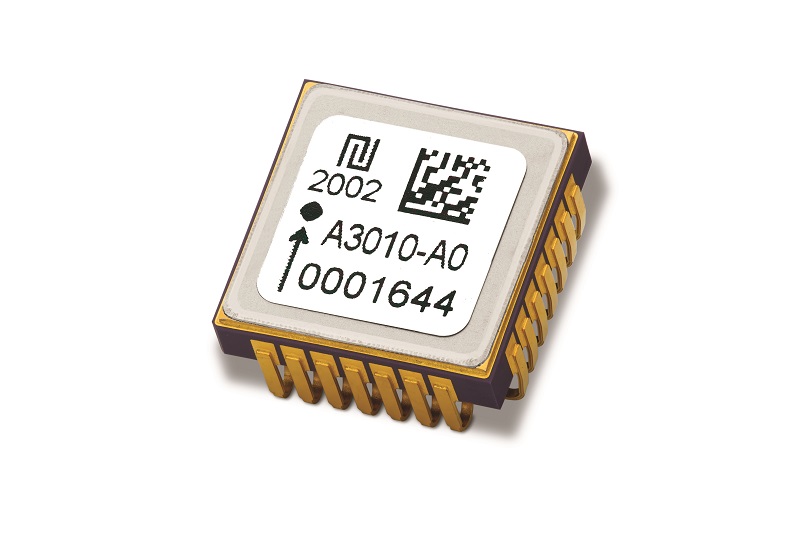
TDK Tronics discussed with us its AXO314, a closed-loop digital MEMS accelerometer for high-dynamics industrial applications.
“Uncrewed vehicles increasingly operate in harsh conditions with fast-changing temperatures, as well as high vibration, often due to combinations of fuel engines and electric VTOL motors,” said Pierre Gazull at Tronics Microsystems. “That means not only precision but also environmental robustness are crucial for maintaining stable inertial data output in such conditions.
“The AXO314 accelerometer has a 14 g measurement range, which works well for UAV and UGV dynamics, and the fact that it operates with a closed loop, with the internal MEMS element staying as stable as possible – which is common in gyroscopes, but rare in accelerometers – means it has a very high level of linearity, which brings very high vibration rejection.”
Almost all of Tronics’ MEMS devices are designed as closed-loop systems. The AXO314 in particular rejects vibrations as fine as 20 μg/g², and operates with a bias over temperature of 0.5 mg in noise densities of 15 μg/√Hz, and in temperature ranges of -40 C to 85 C.
“Also useful in the same applications is our AXO301, which has a reduced range compared with the AXO314, but higher resolution. Less dynamic, inclination- or stabilisation-type applications could hence benefit more from the AXO301,” Gazull said.
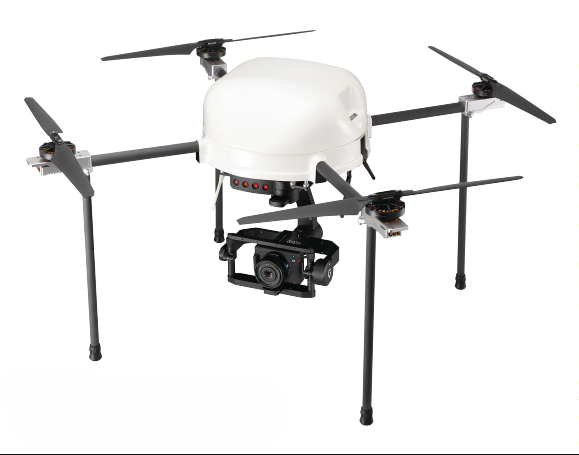
Sony exhibited at the event to showcase and discuss some of its foremost camera solutions for geospatial and other industrial UAV use cases.
“Quantum Systems has just contracted a large number of our latest bespoke drone camera, the ILX-LR1, which we released last year,” said Christie Patel.
“Units of the LR1 are already integrated by and in use with Quantum’s Trinity UAV, which is a fixed-wing system used in inspection, security monitoring and similar missions. It is a very lightweight camera, so it’s suited to the Trinity as a lightweight, VTOL-transitioning and easy-to-use sort of aircraft.”
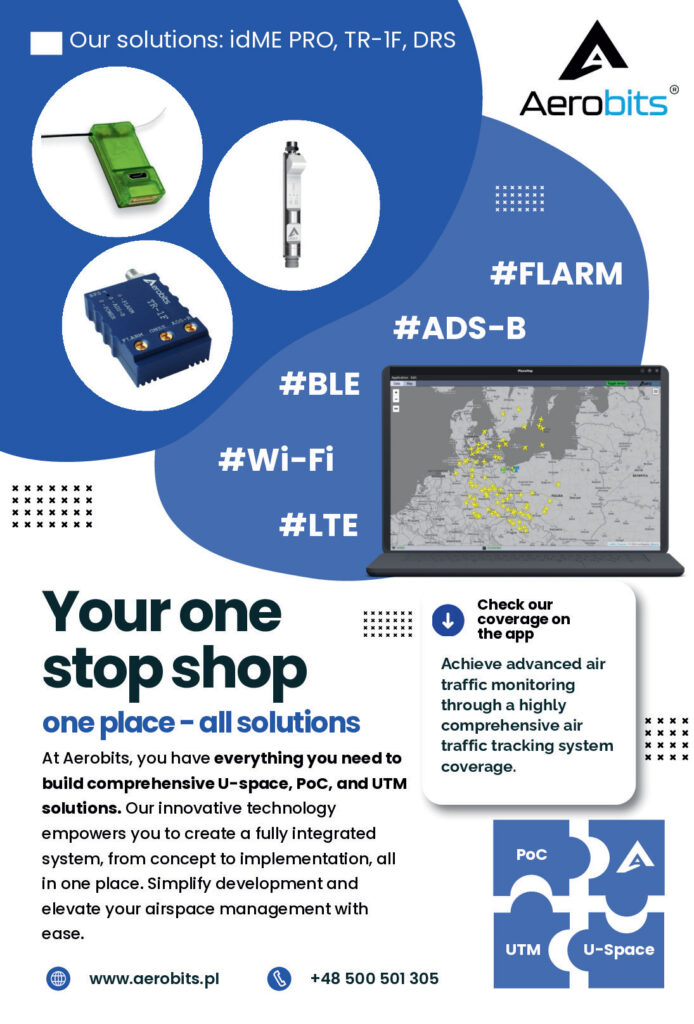
The LR1 weighs 243 g, integrates over a 10-18 V DC connection and consumes 3.8 W when streaming still imagery, or up to 6.5 W if used for streaming movies. Images can be output in raw, JPEG or HEIF formats, and videos can be compressed to H.264 or H.265 standards for streaming.
“Another customer, HHL, based in Hamburg, uses our a7R-IV camera to monitor and inspect transportation systems for the government, as well as inspecting piles of shipping containers with UAVs as a safer alternative to human inspectors climbing and inspecting them personally,” Patel continued.
“That camera is particularly high-resolution; hence why that customer uses it specifically to look for minute signs of damage in transport, and shipping infrastructure and equipment.
The a7R-IV weighs 665 g when equipped with a battery and a memory card, and consumes up to 6.2 W of power. It comes with an electronically controlled shutter for taking still images at speeds of 1/8000 s to 30 s (the LR1, meanwhile, can be supplied with either electronic shutter or mechanical shutter).
Calian GNSS recently unveiled the VCS6000XF, a new smart antenna aimed at high-precision GNSS base station applications. It integrates the company’s 3D Choke Ring technology, as well as a Septentrio Mosaic-X5 GNSS receiver (and hence support from Septentrio Rx Tools for monitoring and saving data from the unit).
“Its key feature is the choke ring, which gives a phase centre variation of roughly 0.5 mm, and it is fully calibrated by GEO++,” said Ken MacLeod. “It also comes with an integrated Septentrio Mosaic X5 GNSS receiver plus an optional radome, and we believe it is the first full-sized, high-precision, smart choke-ring antenna on the market worldwide.”
Choke rings are an antenna structure technology, originally developed at NASA JPL and optimised for mitigating multipath effects from ground bounce and reflections. Waves arriving at low elevation angles are suppressed by the choke ring’s high surface impedance, hence strongly attenuating multipath.
Augmenting the multipath mitigation effect is an antenna element designed for both strong gain at the zenith and weaker gain at the horizon. This ensures the base station’s radio-frequency GNSS signal is cleaner and stronger due to the reduction in multipath. The VCS6000XF has been designed with a Power-over-Ethernet (PoE) interface, so that customers can simply plug it into a PoE network node. A USB port is also present.
Additionally, a 32 GB flash drive is included for local storage of observation data, which can be accessed and transmitted over the network interface. The Septentrio Rx Tools suite supports conditional (password-protected) NTRIP (Networked Transport of RTCM via Internet Protocol) server access.
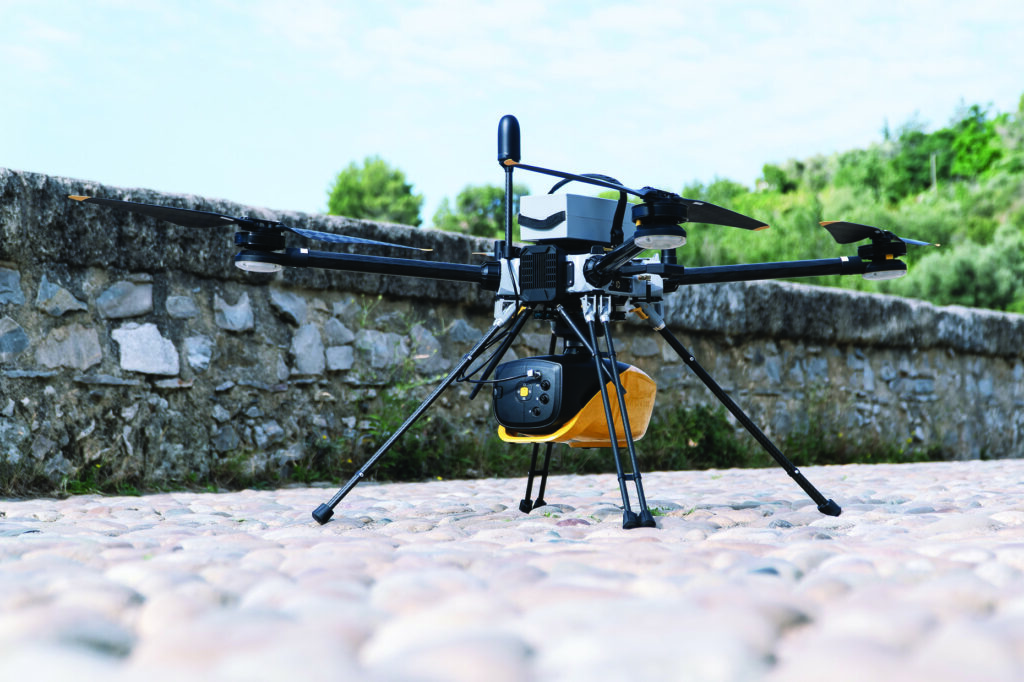
YellowScan showcased its Navigator, a green-light bathymetric laser scanner, designed to be lightweight and ahead of market requirements in such survey technologies, particularly as surveyors increasingly engage in UAV-based coastal-erosion studies and other vital environmental research.
“It weighs 3.8 kg, or 4.2 kg when equipped with a battery, making it significantly lighter than most other bathymetry Lidars, and it allows you to scan down to 2 Secchi depths – twice the depth that can be seen in the visible light spectrum,” said Morgane Selve.
“We researched and found this market is rich with heavy solutions for bathymetry, and given the prevalence of bathymetry UAVs, it was about time to design a new payload with reduced size and weight. This enables integrators to achieve longer mission flight times and, in many cases, seamlessly integrate the payload into their UAV platforms.”
As well as using a smaller IMU than in prior products, the Navigator’s other components were redesigned in-house to achieve its size and weight targets during development.
The Navigator integrates with YellowScan’s CloudStation for desktop-based Lidar data-processing and storage, with extensive configuration options, including auto-detection, visualisation and colourisation of strips (when combined with photo datasets), and the exporting of survey files in .LAS format for interfacing with all other end-user software tools.
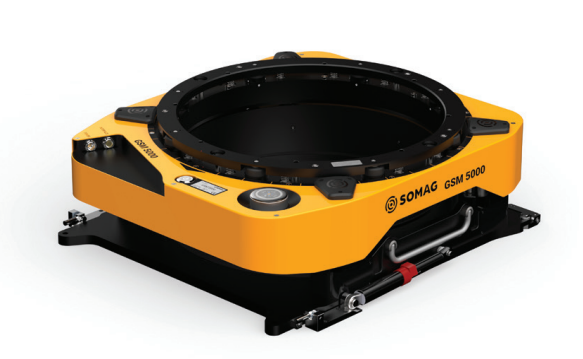
SOMAG unveiled the GSM 5000, its newest and largest gyro-stabilisation mount for sensors for airborne data acquisition. “Its predecessor, the GSM 4000, was released in 2014, and in the last two to three years we captured a lot of information from our clients on what we could improve,” said Sebastian Schreiber.
“Based on that feedback, we made this new product with an increased diameter of the mount, an increased movement range and a nicer interface with improved cabling, as well as removing the manual oil valving. Basically, a lot of small changes. But those add up to make a better overall product.”
The GSM 5000 has a 425 mm usable mount diameter (compared with the 4000’s 410 mm), while maintaining the same width of the overall product. The new system can pitch by 10.1° and roll by 8° to the 4000’s 8.8° pitch and 7° roll, meaning the 5000 has 33% more movement range in the horizontal plane and thus 33% more movement-compensation capacity than its predecessor.
“What really stands out is the drift range. Before, the drift was +/-25°, but now we can rotate the mount almost 360°, which gives a lot more opportunities for photogrammetric or Lidar modelling applications,” Schreiber said.
The pivot point of the mount has been relocated to the base plate, minimising displacement of the sensor system in the aircraft hatch during horizontal rotation and reducing the risk of collision. This design innovation can eliminate movement restrictions and enhances the FoV for the sensor system, provided the latter allows for deeper installation within the hatch and mount.
Pitch and roll movements of the GSM 5000 are achieved using hydraulic pistons and cylinders, while the drift is electromechanically actuated. Units of the product are available for pre-order, with deliveries beginning in spring 2025.
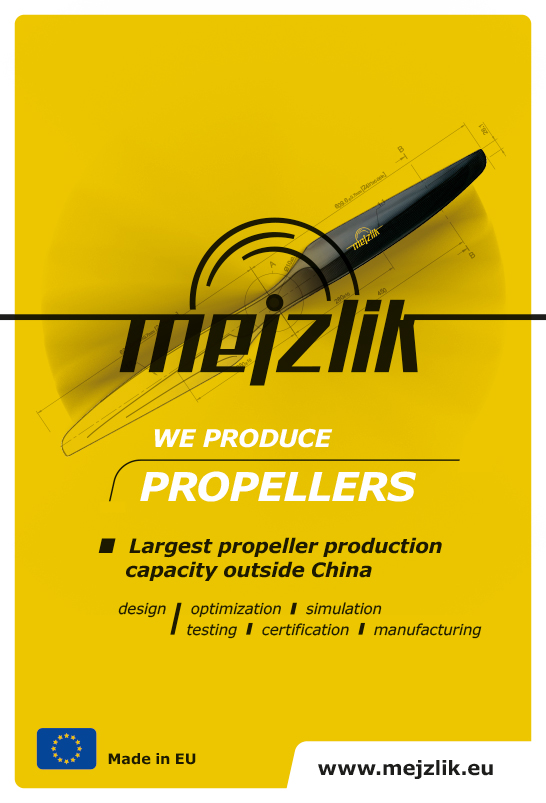
Advanced Navigation unveiled its new Certus Mini series of inertial systems, which has been designed and optimised to address several key areas of interest for integrators of the company’s navigation solutions (including both autonomous vehicle OEMs and operators).
“Higher-end users can still choose the rest of our full Certus product range up to the Certus Evo – meanwhile, the Certus Minis are engineered to forgo some features like Ethernet, onboard data logging, and ruggedisation, to make them as small, light, and low-cost as possible, while still having all core functional requirements, high positioning accuracy, and interference rejection for really lightweight vehicle applications,” said Advanced Navigation’s Alex Lloyd.
“That especially includes lightweight UAVs for all geospatial applications – but we do still have a few quite large and heavy vehicle integrators who are interested in the Certus Mini series – particularly the Certus Mini D, which is the dual antenna INS product in that range, and it can hence give heading data for a ground or hovering vehicle while it’s stationary.”
Along with the Certus Mini D, which weighs 55 g, two other products comprise the new product range, to cater for the different echelons of end-integrators. These are the Certus Mini N, a 43 g single antenna INS, and the Certus Mini A, which is a 38 g AHRS without an integrated GNSS solution.
The three products can be provided with housings, or in OEM forms to further reduce their size and mass (each system’s weight dropping by 30-40 g when its enclosure is omitted). They are also designed to use GPS L5 corrections, greatly boosting their capabilities amid multipathing or other local hazards, from both urban environments like cities, to sparse and rural environments such as agricultural and mining territories.
“What’s also important are all the software enhancements in our filter, which enable a platform to accept many different protocols,” Lloyd added. For more real world test results and contextual details key for those considering the Certus Mini series, a dedicated whitepaper is now available at www.advancednavigation.com
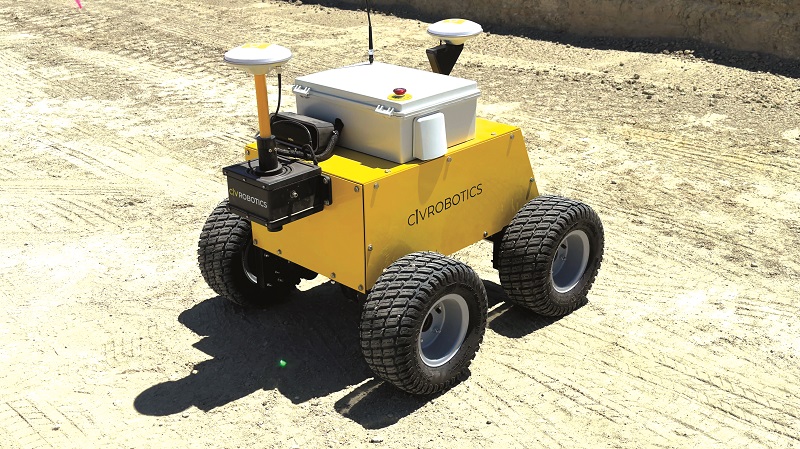
Civ Robotics exhibited its CivDot range of UGVs, designed around autonomous construction layout marking, particularly outdoor work, and engineered to suit varying capability requirements.
“Our robots are the CivDot, CivDot+ and CivDot Mini. Each model features dual-antenna RTK-GPS positioning to maintain precise marking accuracy despite weather, terrain and interference across construction sites as large as thousands of acres,” said Claire Gauthier.
“The UGVs can also be equipped with various tyre options to handle mud, snow and sand, and all three models are powered by Li-ion batteries.”
The CivDot is a 40 kg robot, and drives on four BLDC motors in an all-electric 4WD configuration, with a ground clearance of 10 in. It can place up to 3,000 layout markers per day, each with a marking accuracy within a 3 cm margin.
The CivDot+ is similar in design to the CivDot, but it is engineered for tighter precision in its placement. It marks up to 1,200 points per day with a margin of error within 0.8 cm. Both the CivDot and CivDot+ can operate for up to 8 hours between battery recharges.
Lastly, the CivDot Mini, unlike its two siblings, is intended specifically for road-lane marking. A three-wheeled vehicle, equipped with a spray-can payload, can paint up to 27.36 km (17 miles) of solid or dashed lines daily, with a marking accuracy within 2.54 cm (1 in).
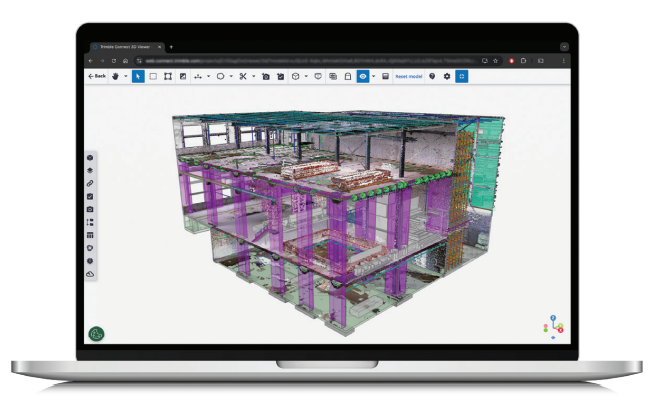
Trimble unveiled critical new innovations for professional attendees from across the geospatial (and other) industries, including solutions developed by both the data services side and the GNSS inertial products side of its company.
It has extended its Trimble Connect platform for easier sharing of and collaboration on geospatial data derived from UAV surveys.
“To that end, we’ve just released the Trimble Reality Capture platform service, which is a data service extension co-developed with Microsoft and designed to bring reality-capture datasets from 3D laser scanners, mobile mapping systems and UAV missions into Trimble Connect,” Gregor Willhauck said.
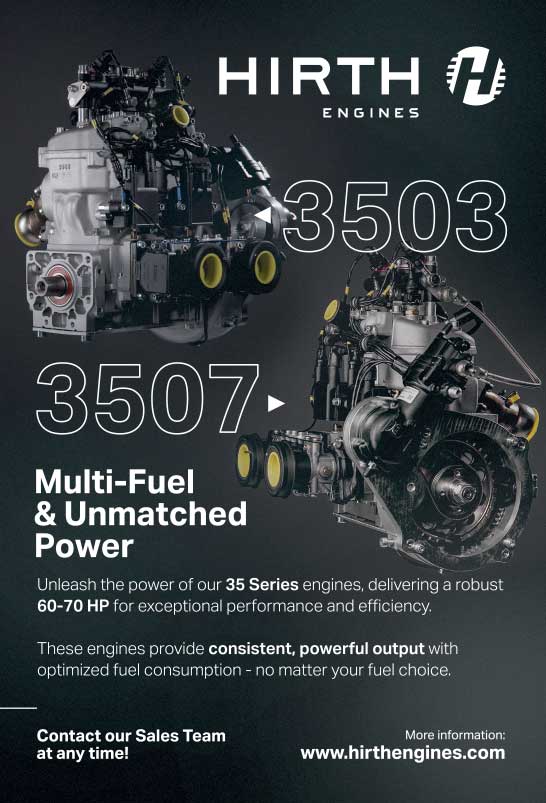
Trimble Reality Capture allows a surveyor or UAV operator to upload processed point clouds into Trimble Connect, for access and use by all types of project stakeholders, such as civil engineers, digital engineers or architects.
“One large customer of ours is working on a 10 km-long infrastructure project revolving around highway reconstruction. They beta-tested Trimble Reality Capture, as did four other organisations, and in working with them, around 700 active users were collaborating on the data,” Willhauck said.
“It really validated how this new innovation can enable surveyors to give access to vital data to a massive audience seeking tangible value and insights from it, without needing a PhD in photogrammetry to do it.”
Rather than streaming the processed data into Trimble Connect in a compressed way, or any other representation that loses the original format, Trimble’s engineers have focused on preserving the fidelity of the original so no details within the data are lost, such that engineers can go back and check subsections and fine details, even years down the line.
To develop the capacity for integrating reality-capture data into Trimble Connect, Microsoft provided copious expertise on handling large data quantities, along with ideal cloud services, formats and scaling approaches. Trimble itself brought the expertise on optimising around data formats, retaining data accuracy and surveyor-side considerations.
Trimble Connect today has 30 million users, with data stored via a multi-cloud approach: AWS provides the primary data hosting, with reality-capture data hosted on Azure. This multi-cloud approach involves data centres in North America, Europe, Asia and Australia, and it aims to optimise data security.
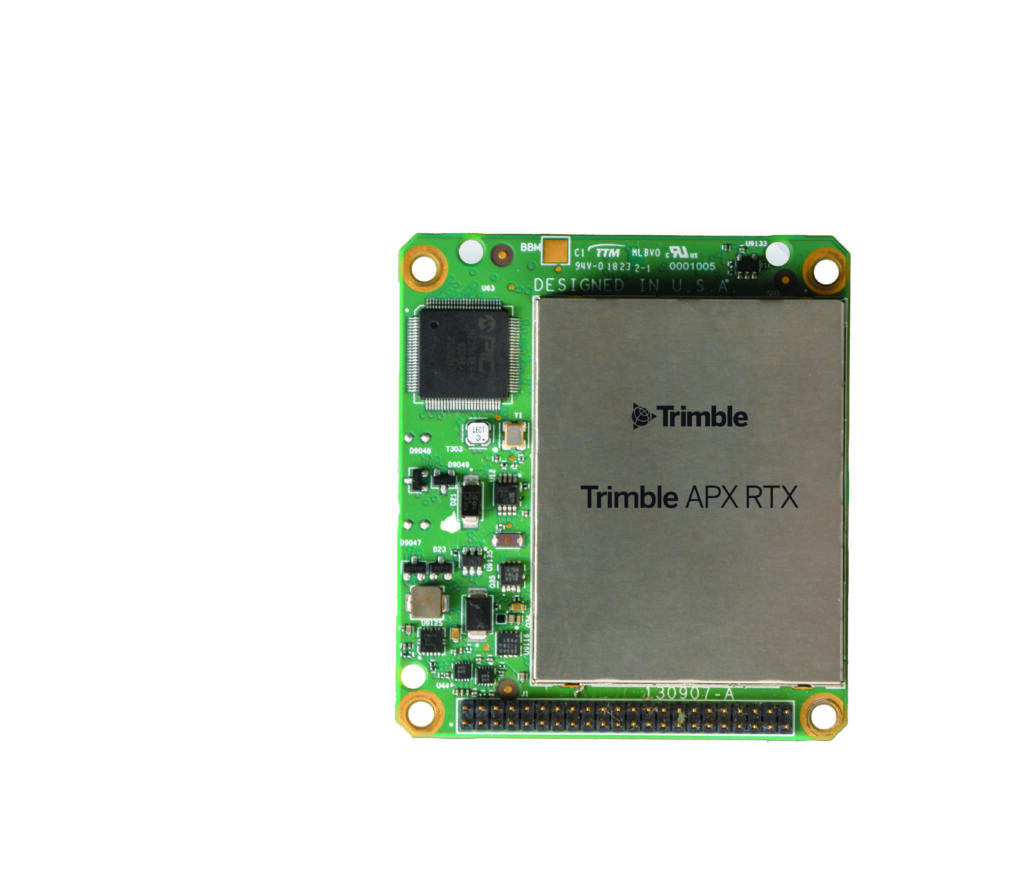
Meanwhile, Trimble Applanix launched its newest product for UAVs, the Trimble APX-RTX, which integrates its latest GNSS hardware and four different inertial sensors, as well as the Trimble RTX Centerpoint correction service, and a suite of real-time and post-processing software applications.
“It also comes with the Applanix SmartCal compensation technology for calibrating the sensors for things like lever arms and it offers the latest version of our IN-Fusion+ sensor-fusion technology,” said Steve Woolven. “That can integrate land odometry data, and with Lidar in a post-processed function to enable SLAM, with camera compatibility being worked on for the future too.
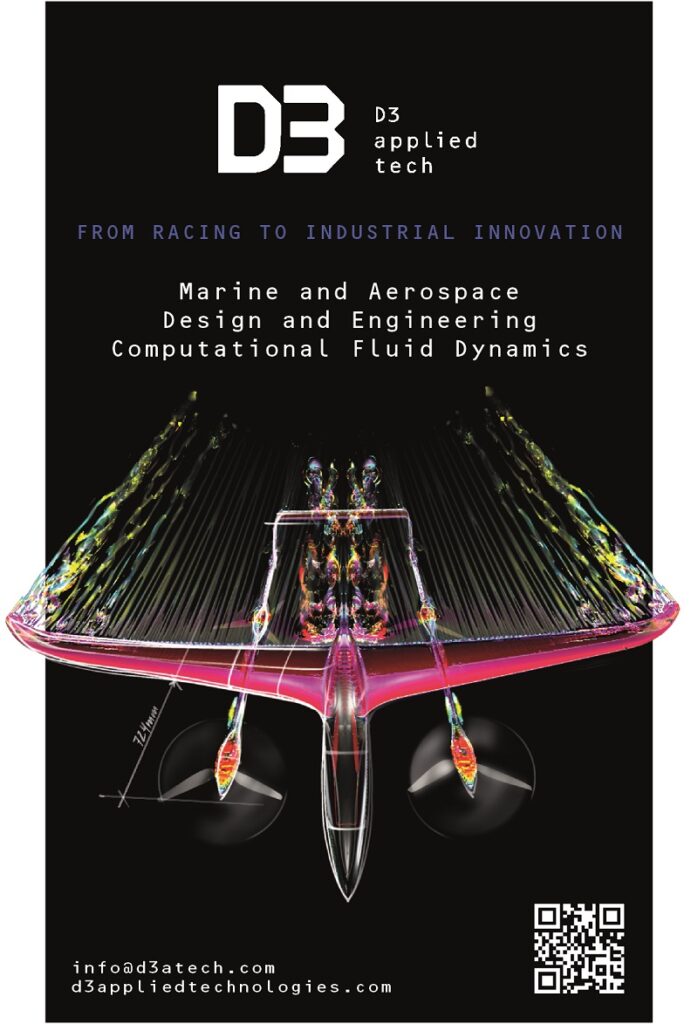
“As well as being designed with two onboard inertial sensors for covering Class 1 and Class 2 performance, we have two external IMUs that can be plugged in as needed to elevate performance; for instance, with higher flights or payload requirements that mandate finer inertial sensing.”
Those IMUs can include the company’s APX-15, APX-20, APX-30 and APX-50 – listed in order of precision, accuracy and noise rejection.
The APX-RTX weighs 56 g, operates using 336 GNSS channels (including GPS L5, Galileo E5 and BeiDou B2), and outputs position, pitch, roll and heading at 100 Hz. Additionally, the APX-RTX records all of its navigational telemetry onboard (such as raw IMU data, timing, position, attitude, performance metrics and velocity) for end-users to access, extract and use as needed for post-processing and other applications.
Key development targets for the new system included optimising for SWaP-C, to match such optimisations seen across autonomous systems industries, and enable more entry-level aircraft and payload integrators to use the APX-RTX.
Newer, smaller Lidar payloads informed much of the size and cost envelope that the APX-RTX had to fit into, as did the rising number of UAV manufacturers aiming for certification of their aircraft. The product is available for order now, in purchasing and subscription-based usage models, with shipping to begin before the year end.
UPCOMING EVENTS
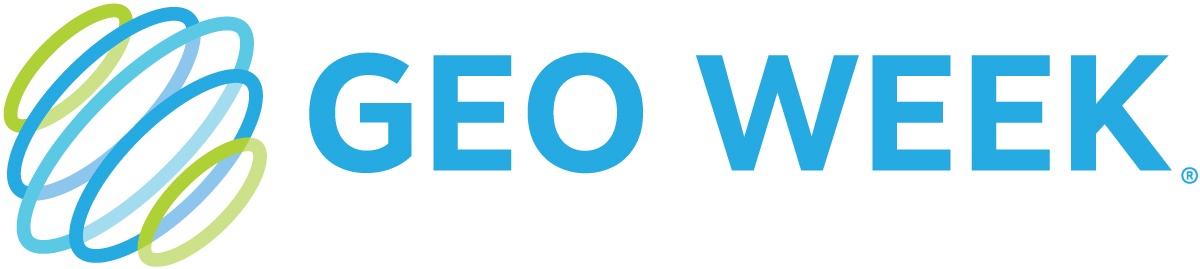
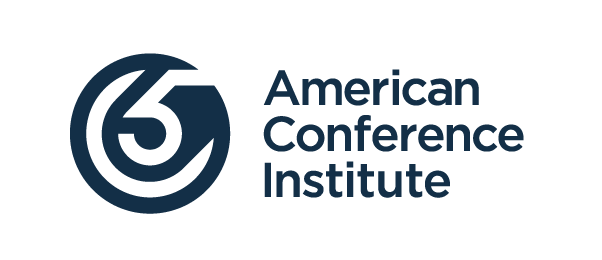
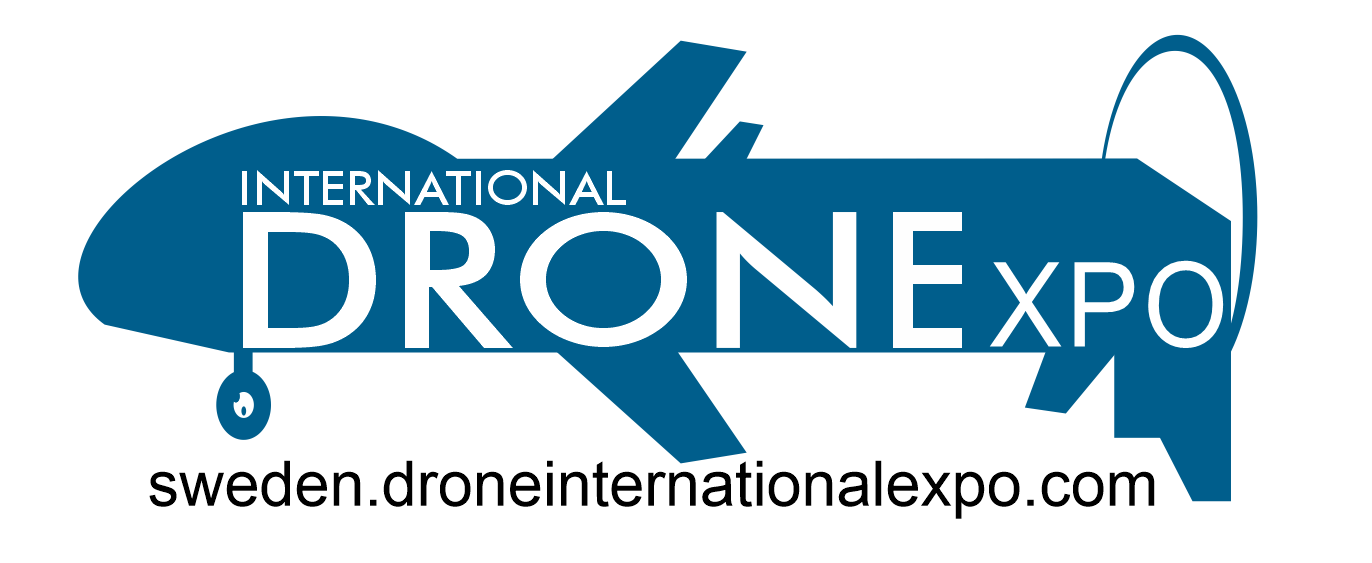
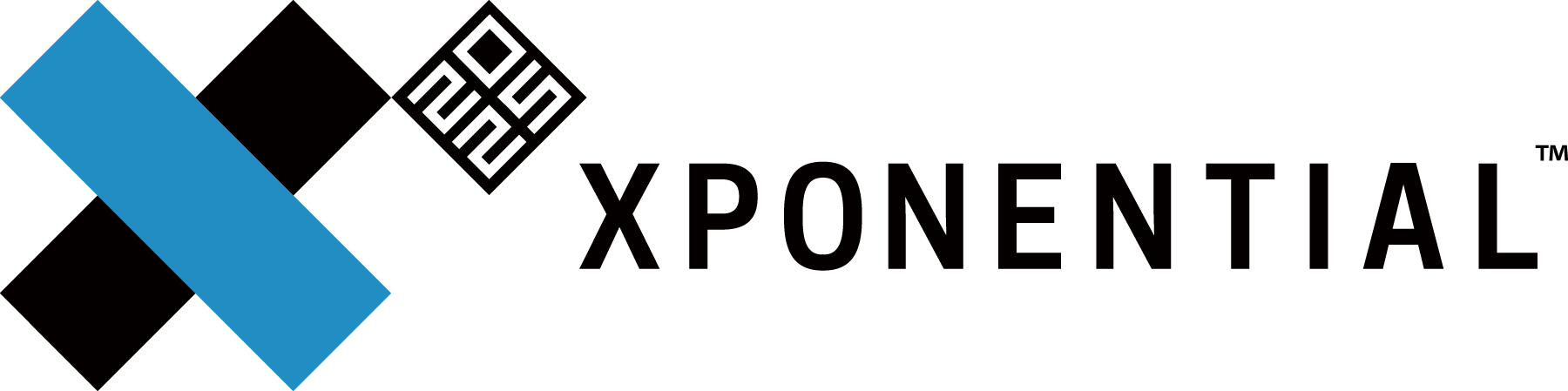
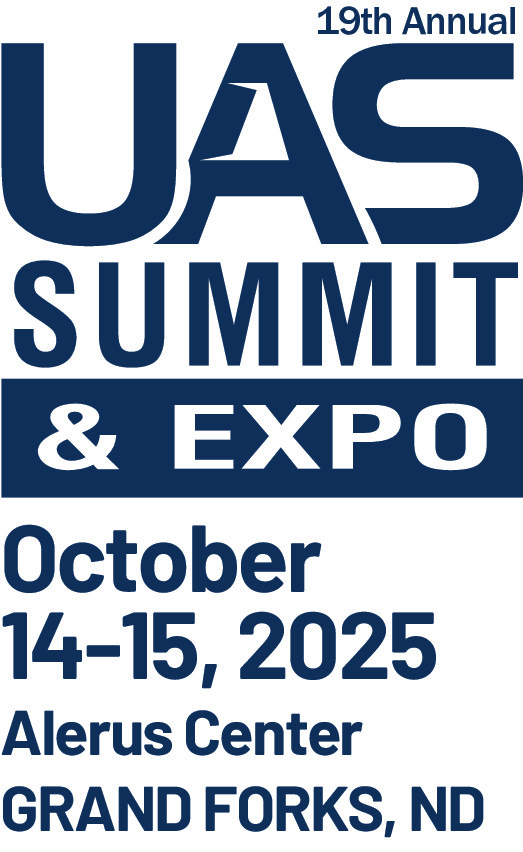

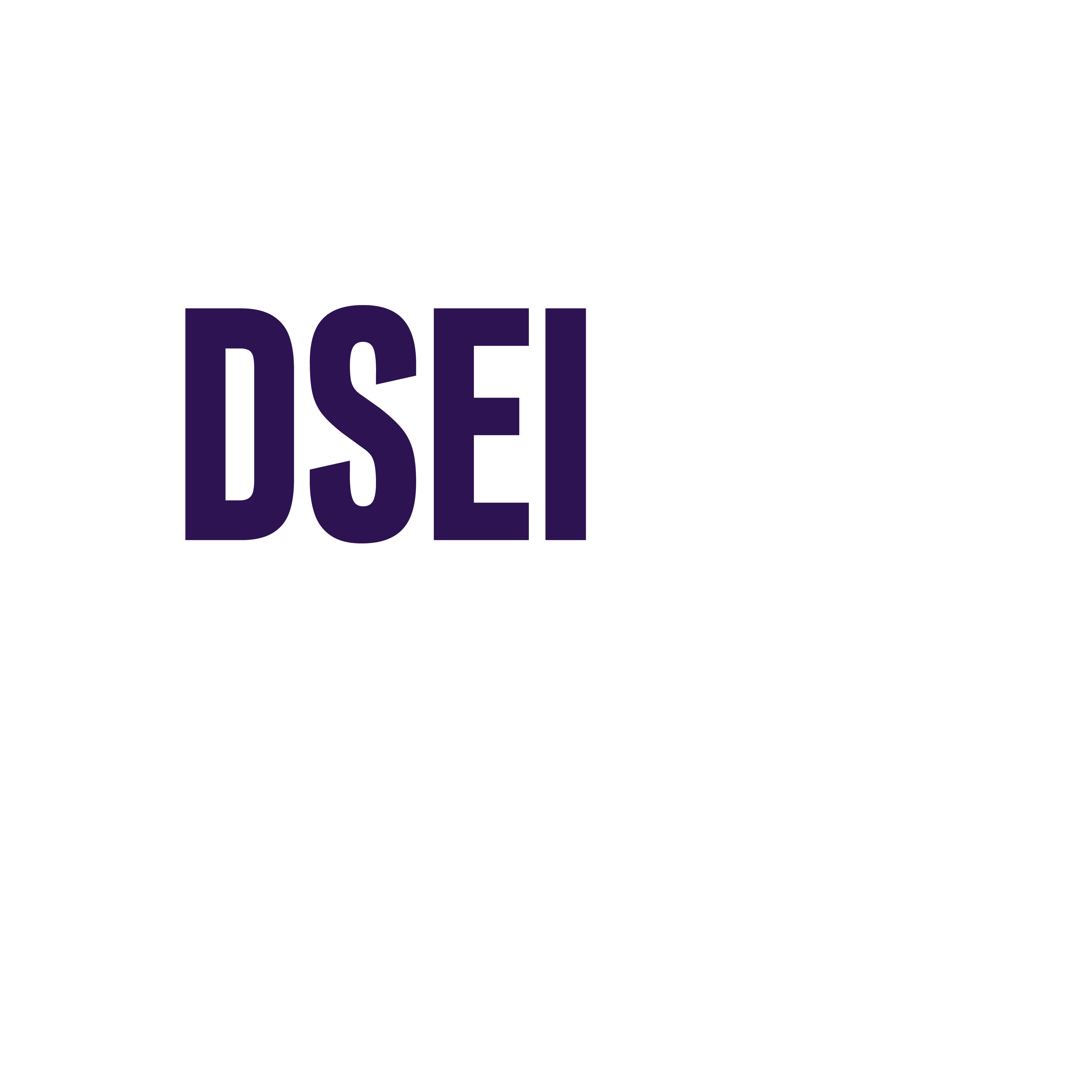
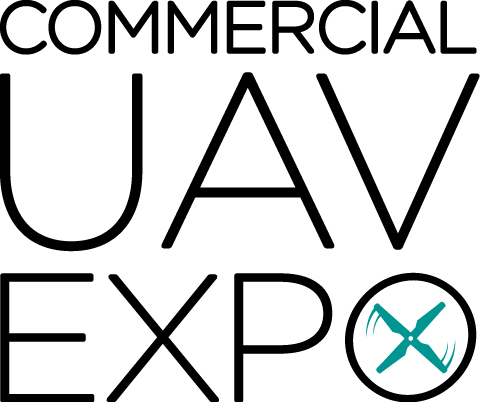
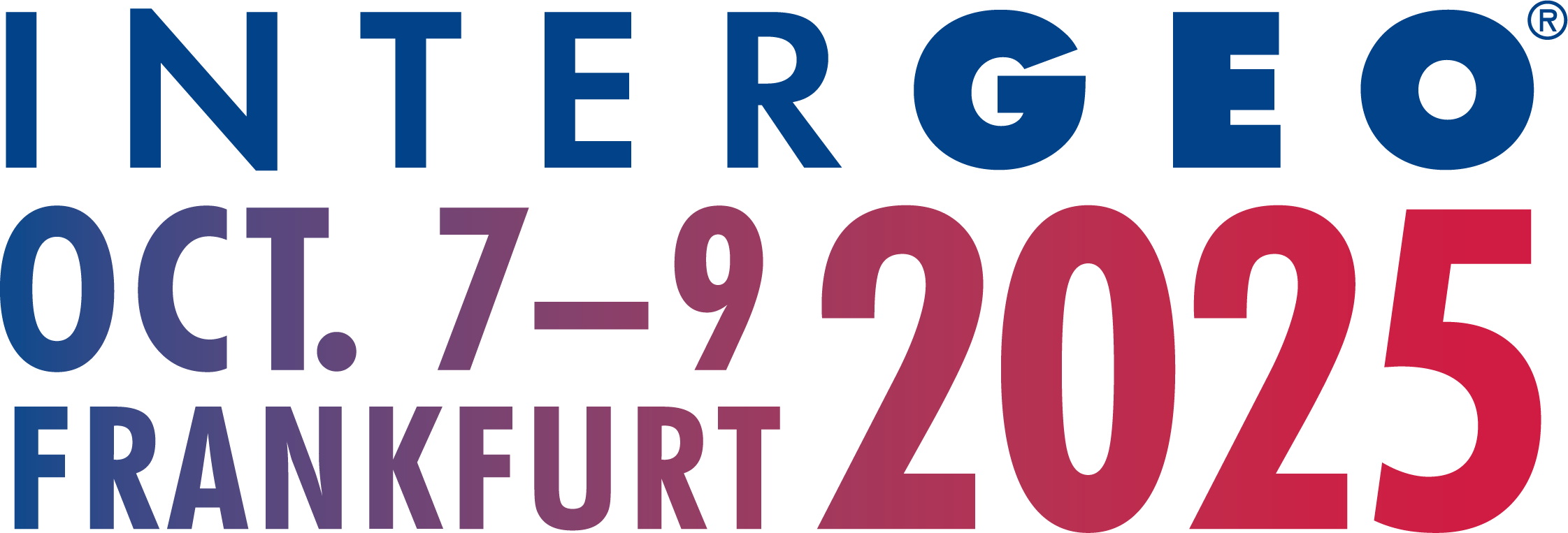
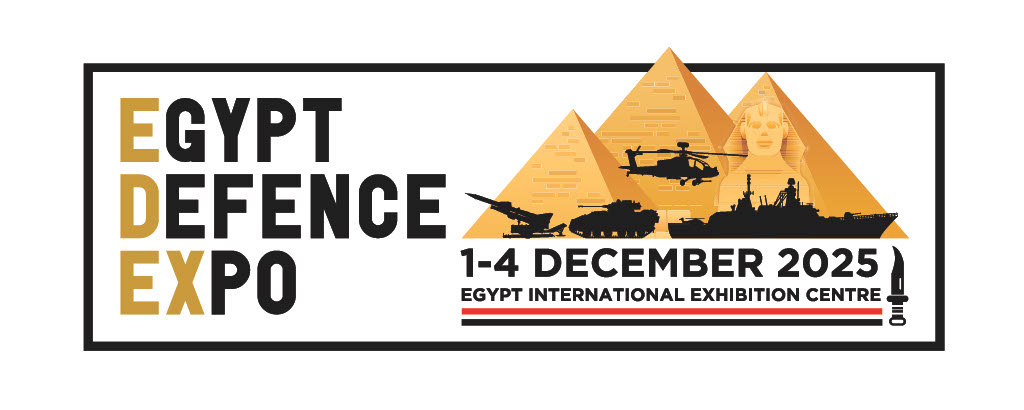
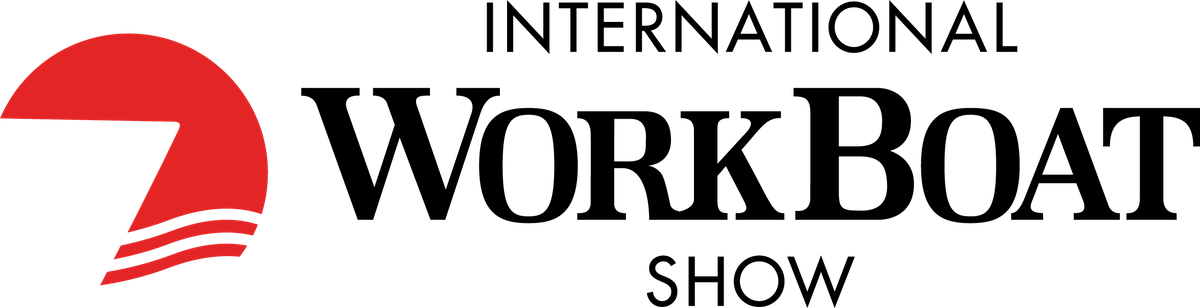