Impossible Metals’ Eureka underwater miner
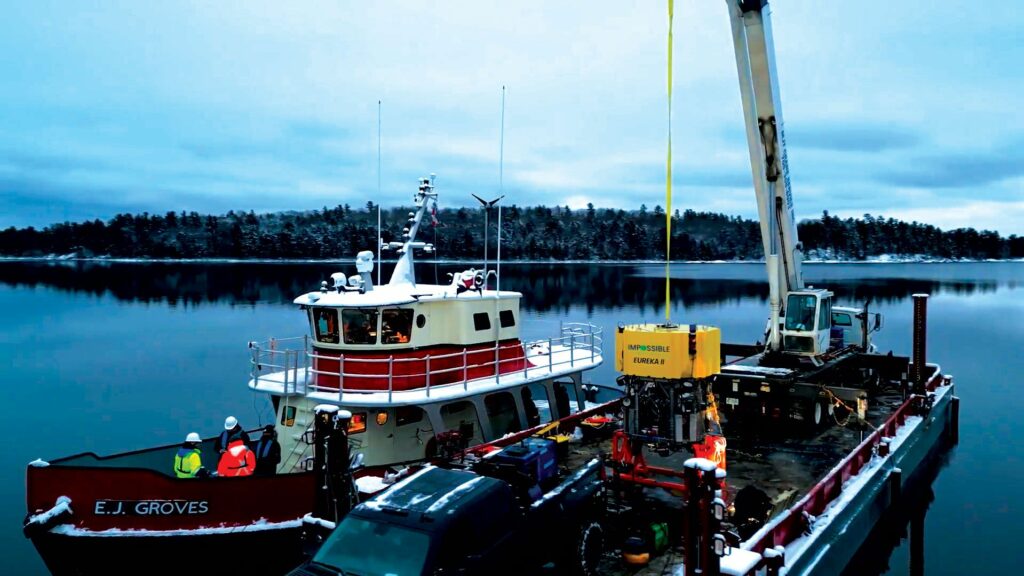
(All images courtesy of Impossible Metals)
Sunken treasures
Rory Jackson investigates how one company is leading the way toward a new age of sustainable, subsea mining
Ore nodules collected from the seafloor represent a potentially enormous and untapped source of raw minerals, which are key to the fast-growing sustainable mobility and power grid industries, and are sufficiently widespread that many countries could access them without the costs and environmental impacts associated with terrestrial mining.
Until recently, propositions for seafloor nodule extraction revolved around conventional dredging-style approaches, but these risk seafloor disturbance of the mined areas – including loss of biodiversity and ecosystem function – and climate-impacting carbon emissions from surface support vessels.
An alternative approach to deep-sea dredging, espoused by Impossible Metals, is a deep-sea ‘selective harvesting’ method. This utilises specially engineered AUVs that minimise harmful emissions, and combine machine vision and robotic arms to achieve nimble, fully autonomous collection of mineral nodules, without touching or harming seafloor fauna and flora, or throwing up pollutive sediment plumes.
Rather than consign such AUVs to theory, Impossible Metals spent several years in intensive r&d creating the necessary subsystems for autonomous deep-sea selective harvesting, before engaging in rapid vehicle prototyping and iteration.
The company achieved a critical concept-of-operations milestone in late 2024, demonstrating its Eureka II AUV at a special event in Collingwood, Ontario. The vehicle played through a practical representation of a nodule mining mission, executing most of the functions and stages needed for the commercialised, industrial-scale autonomous mining fleets that are poised to follow in the years ahead.
Eureka II
Eureka II is a tall, narrow vehicle, resemblant of some long-running ROV designs – although fully autonomous – having been designed for the practical purpose of demonstrating its subsystems, both individually and as part of a tightly integrated robotic system.
Those subsystems include its three key enabling technologies: a vision system for identifying mineral nodules and recognising (and avoiding touching) aquatic life forms, three sets of industrial pick-and-place robotic arms for grabbing and stowing nodules, and a buoyancy engine for ensuring stable altitude and movement over the seafloor – without which the arms would have a far harder job to do.
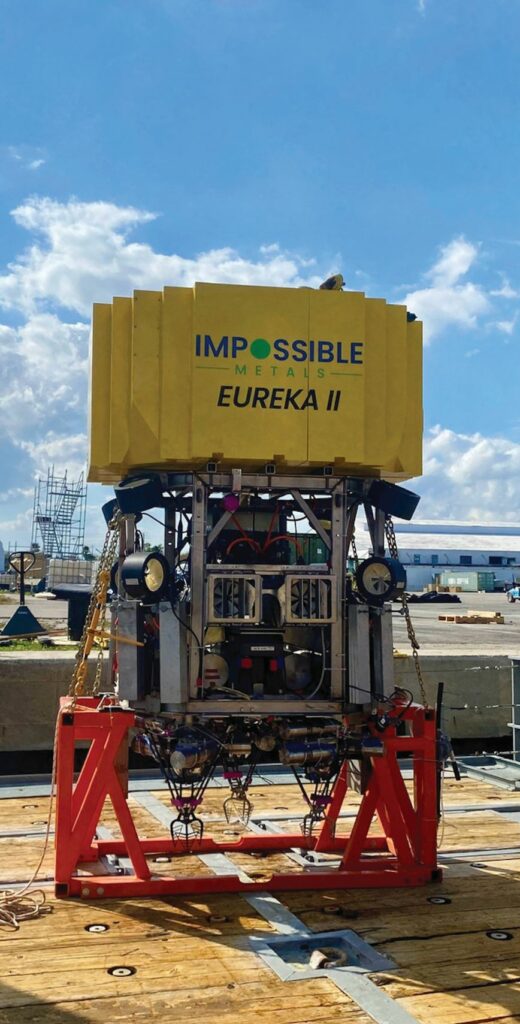
The AUV is engineered for depths of 6000 m, measures 3.2 x 1.95 x 1.93 m, and weighs 3950 kg in air, including the 14.4 kWh battery. An upper, closed section contains syntactic foam for buoyancy, with positioning and communication systems mounted (respectively) atop and on the side of this section. Meanwhile, a lower, open frame serves as a mounting structure for the propulsion, buoyancy, control, computing, battery, sensing and navigation systems, and for the robotic arms and material collection system, together with an emergency drop weight, to be released if all other means of returning to the surface are expended.
Altogether, the vehicle represents Impossible Metals’ final non-production prototype vehicle, and the final step before proceeding to the production vehicles, Eureka III and IV, which will be optimised for the economics of both vehicle manufacturing and mineral throughput.
As Jason Gillham, CTO and co-founder of Impossible Metals explains to us, “Unlike existing AUVs and underwater robotics, which are largely built for data collection, our systems are designed around maximising an economic throughput of material. It’s much more akin to running a factory under the ocean, because the bigger we build our AUVs, the better the economies of scale.”
Naturally, however, building bigger means bigger challenges in terms of startup capital, manufacturing approaches and vehicle optimisation, clearances and transportability. By constraining Eureka II to fit within a standard shipping container, it remains reasonably easy to build, modify and transport. Further ahead, the company plans to first produce commercial units of Eureka III from which it will learn how best to approach manufacturing and deployment of Eureka IV.
“There were two key drivers in how we engineered Eureka II: one was speed, because as a startup, we want to develop things quickly, learn quickly, even from mistakes and failures if necessary, and then iterate; I often use the expression, ‘test early, test often’, which has served us well in developing Eureka II and the Eureka I proof-of-concept that preceded it,” Gillham says.
Testing equipment at Impossible Metals’ location at Collingwood, Ontario, includes a 12 ft tall dunk tank for holistic system tests and buoyancy trimming, a 6.3 m gantry crane, a small, one degree-of-freedom tank for developing the robotic arms, and a larger tow tank for collectively testing and iterating the arm and vision systems.
“The second key driver was modularity,” Gillham continues. “That’s helped us swap subsystems in and out quickly as we test different iterations of the AUV, and it also allows us to take what works about Eureka II, and migrate it into our designs for Eureka III, thereby accelerating the latter’s development time.”
The delta robot arms (a type of robotic arm system, typically encompassing three arms connected to universal joints at the base, which keep a single end effector or claw consistently oriented) also benefited from rapid iteration and optimisation. Rather than use serial robotic arms, which are designed for high dexterity and manipulation, the parallel nature of delta robot arms provides Eureka with high-speed pick-and-place capabilities, and the quick development has compensated for some of the weaknesses of conventional delta arms, such as their lack of strength or range of motion, as the company would go on to prove at their demonstration at Collingwood, on November 13, 2024.
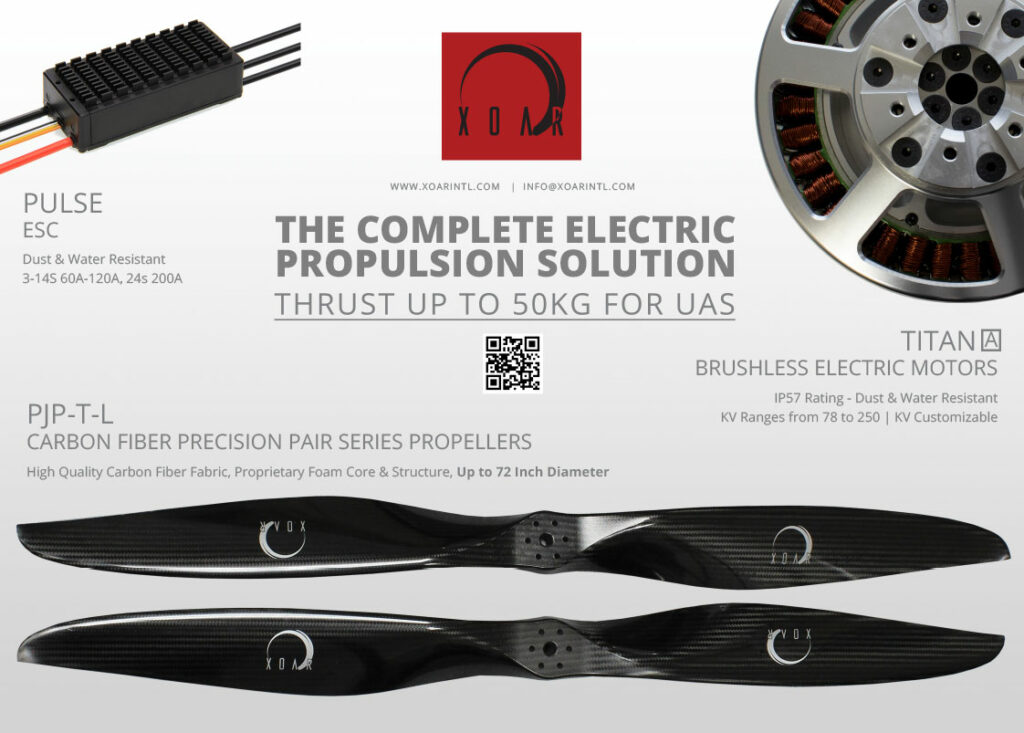
Yacht club
Local partners of Impossible Metals (specifically, the town of Collingwood and the Collingwood Yacht Club) made facilities available for its trial work, which meant that the pre-operational paperwork was a straightforward matter of communication.
The demonstration site at the Collingwood Yacht Club was established with a simulated nodule bed in the water, a homing camera for tracking the approximate location of Eureka II from the harbour, an observation camera for a wider view of the stretch of water involved in the demonstration and a mobile crane for AUV deployment.
“On an industrial ship, the deployment approach that we have used during our open-water testing is an A-frame crane system with a winch, which lowers the vehicle into the water and releases it for operations,” Gillham says.
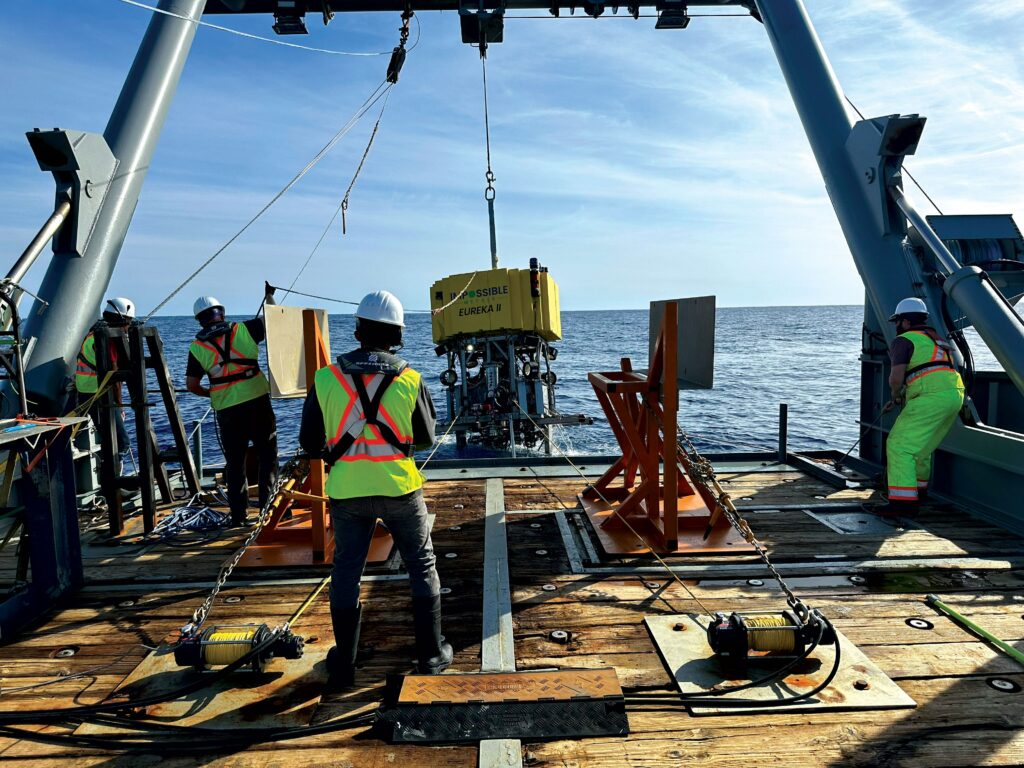
“When we do shoreside testing, we’re able to use a mobile crane for picking it up and deploying it; in both cases we use cranes, but very different cranes depending on the launch environment.”
Lastly, the operations team and the demo attendees monitored the AUV’s work and progress from a building at the opposite end of the marina. This was facilitated via four displays: a ‘Main UI’ containing extensive telemetry data from across the vehicle’s subsystems, an ‘Operator UI’ that displayed two top-down maps and a water column gauge for indicating the AUV’s real-time position (thanks to a live USBL feed aided by inertial data), an interface for onboard cameras showing the robotic arms’ activity (visible via a fibre optic link, otherwise unnecessary for autonomous operations), and a real-time feed of the marina-side observation camera.
Bobbing along
The demonstration of Eureka II’s autonomous nodule mining capability consisted of the AUV executing several runs across the set test area in which rocks closely analogous to nodules were distributed. Attendees viewed the underwater operations from their indoor location via the ongoing stream of UI and video feeds discussed above. A live feed from a separate ROV camera was also available, which produced video recordings of the demonstration.
The AUV’s movement across the water, between the deployment and recovery location and the nodule-filled area, relied on the aforementioned buoyancy engine (which, as discussed, would be important for keeping Eureka II hovering at a targeted average altitude above the nodules while the delta arms picked at them), as well as a series of shrouded electric thrusters.
Eureka II features eight hubless, rim-driven thrusters, supplied by Copenhagen Subsea: four vertically disposed units for ascent and descent, and four horizontally disposed ones for rotation and sideways movement.
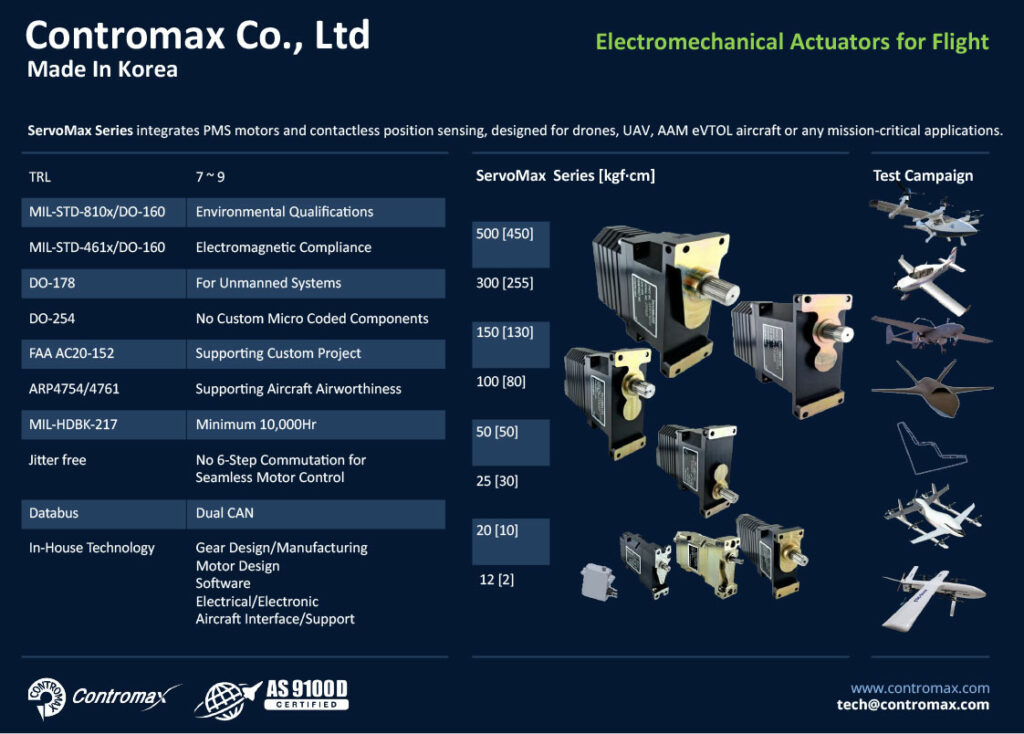
“Programming for tight motor control and response was important to some degree, but with any subsystem, you get different levels of responsiveness depending on what you’re trying to do,” Gillham says.
“To control our AUV, we needed the buoyancy engine for offsetting the weight of that 4 t vehicle, and enabling us to move up and down through the water column, but the buoyancy engine doesn’t actually have high response rates, so it can’t give precise control over altitude. The thrusters were henceforth key for minimising deviations, and they were very responsive systems, making them very effective for reacting to small undulations in the seabed and to disturbances caused by currents in the water, to maintain roughly the same altitude.”
Consequently, the AUV kept within a margin of +/-5 cm of Impossible Metals’ desired 1 m altitude delta from the seabed, while moving at 5–10 cm/s. The remaining distance and minor delta changes were then covered by the robotic arms, which adjusted their reach and angles with responsiveness similar to that of the thrusters, to ensure that their end effectors could be positioned as commanded by the onboard control stack to within a 1 mm margin of error, thereby picking nodules precisely, securely, and with minimal impact on any surrounding sediment or bio-organisms.
However, as mentioned, altitude management begins with the buoyancy engine, which was conceived and designed prior to Eureka I’s advent in May 2023, the company having identified the environmental and economic benefits of keeping their AUVs hovering over the seafloor during nodule harvesting.
“But as we were going to be collecting and adding mass to the AUV over the course of its operation, we needed something other than thrusters to first maintain that altitude, and then bring the nodules back up to the surface,” Gillham recounts.
“As we explored methods for achieving those, buoyancy engines became the clear optimal choice. But one of the challenges with existing buoyancy engines in deep-ocean operations is that they’re generally designed to use compressed air, releasing air into lift bag-type systems in order to displace internal water and generate lift.
“In those sorts of ‘fixed mass, variable volume’ solutions, where air is being exposed to the pressures of those depths, you don’t actually get a lot of lift, because the density of the air under such pressures starts to approach the density of the water itself.”
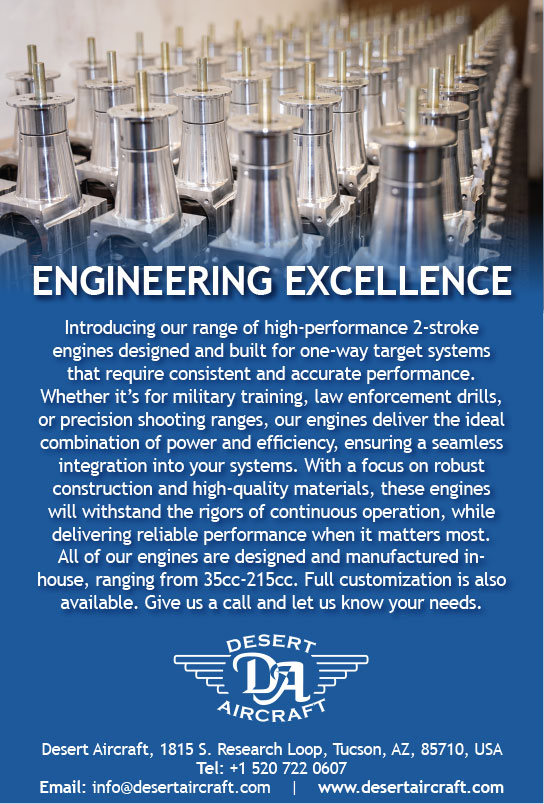
Therefore, Impossible Metals uses a ‘fixed volume, variable mass’ approach to buoyancy, pumping water in and out of tanks that are designed to resist high environmental pressure, thereby increasing or decreasing their mass (and that of the vehicle) by up to 50 kg to initiate descent or ascent, respectively.
The main engineering challenges were sourcing tanks strong enough to withstand the pressures (and changes therein), as well as finding sufficiently robust pumps. The latter was made more difficult owing to the small sizes of the pumps needed for Eureka I and II; the company anticipates that a wider range of commercially available pumps will be open to them to provide the higher flow rates needed for the buoyancy engines of Eureka III and IV.
Deep-sea prospector
A number of key navigational inputs were crucial to ensuring a robust, closed loop by which the buoyancy and thruster systems could control for position and hover. These included ring laser gyros for inertial sensing, which were co-located with Doppler velocity logs (DVLs) for altitude and velocity measurements, together with the aforementioned USBL for positioning data.
“We’ve been working closely with Exail, who provided the inertial system, and their partnership with Nortek was a strong source of support for us when it came to the DVL. We’ll continue looking to Nortek, especially for support and learning as we build the first version of Eureka II, particularly because they’ve expressed serious interest in working with us as we’re rapidly moving from single-unit production to supplying fleets of vehicles,” Gillham comments.
“There’ll be significant collaborative positioning benefits to be gained by having multiple nodule harvesting vehicles in a given region, because they communicate with each other and also the surface ships, which Nortek sees potential in. And lastly, we also have a forward-looking sonar for obstacle avoidance, which is provided by Imagenex in Canada.”
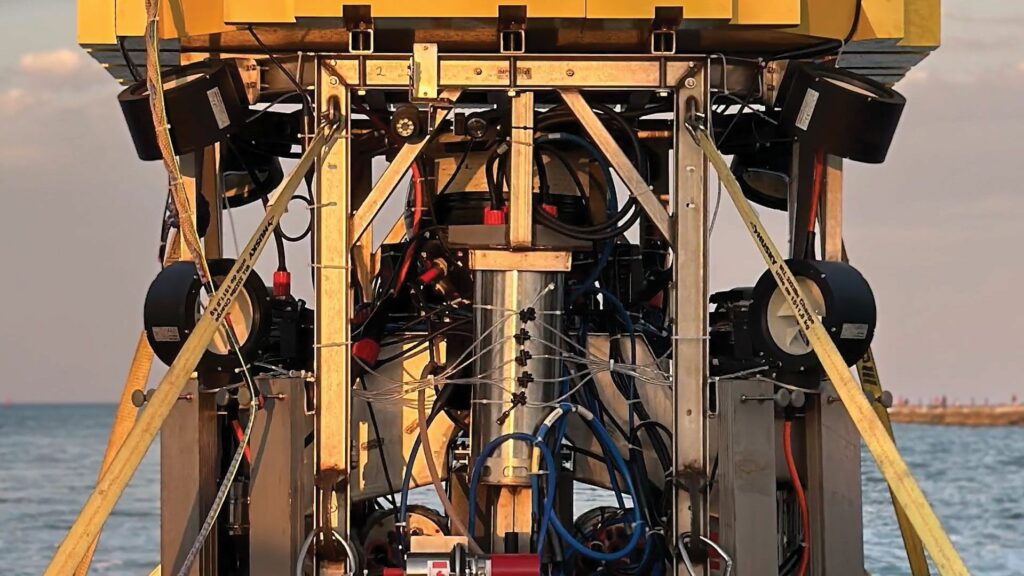
Processing these inputs to achieve apt commands for the control systems has rested on programming within the main computer to date, but is now being migrated outwards to the edge, within certain key sensors such as the vision system.
To ensure this type of distributed computing system will work effectively, Gillham and his team are focusing r&d effort into precise and tightly controlled timing, which is fundamental for reliable sensor fusion. That is spurring particular work into ensuring the AUV’s CAN bus is robustly engineered for minimal latency and to ensure smart prioritisation of mission-critical signals.
“I’ve seen other systems that have a hardware pulse-per-second time synchronisation; we don’t require that level of timing, but we absolutely need smart network distribution, where we have close understanding of what latencies exist between the different points of our AUV,” Gillham says.
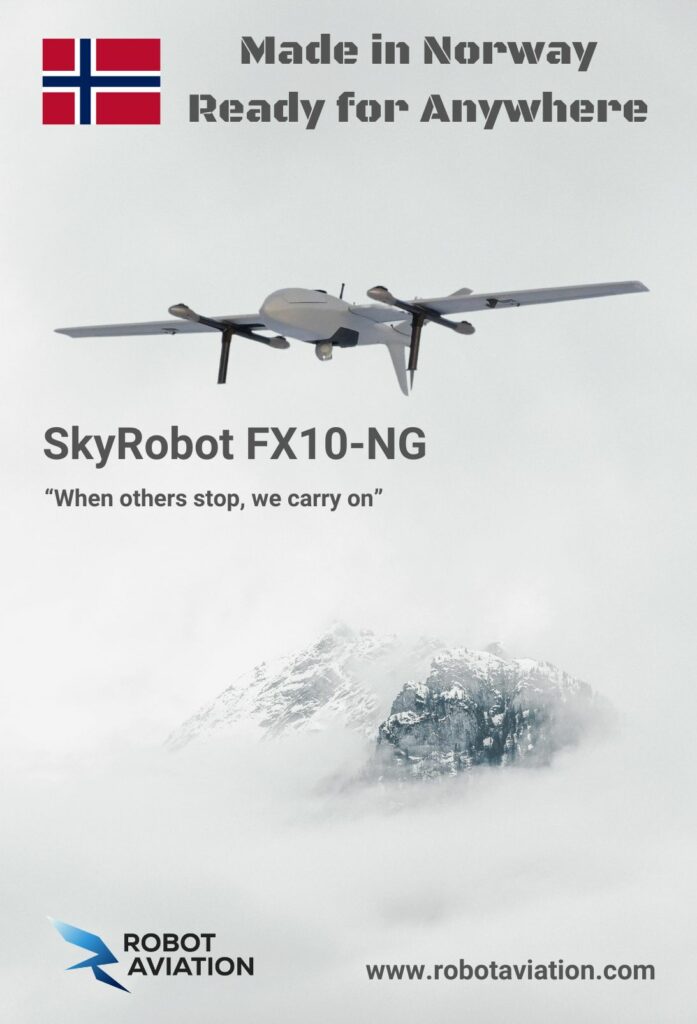
Once Eureka has navigated its way to a nodule bed, the vision system becomes key for recognising nodules to be harvested, assessing the surrounding sediment, and identifying fauna to be avoided. This system relies on a stereo camera assembled in-house, with Impossible Metals’ machine vision used for nodule identification, specific object avoidance and determining which of the three delta arms should reach for each nodule.
“The arms themselves have no idea of the selection process that’s going on; it’s entirely down to the vision system to decide which nodules get harvested, which are deemed too cumbersome to be worth it, and which arms are put to the task,” Gillham says.
“As well as engineering the stereo camera for our needs, and to enable freedom in the vision software engineering – there’s no natural light at the depths we’re operating at – the vision system also needed some powerful lights that provide as strong and even illumination as possible. As we learned through deep-ocean tests, water does a very good job at absorbing light, but fortunately we’ve engineered our system to operate very close to the seafloor, which meant we didn’t have to integrate especially massive LEDs, and there’s no dark edges in our images.”
To train the machine vision system, Impossible Metals first generated its own training imagery, using its tow tank filled with sand sediment, and then placing garden-type lava rocks inside as very close physical approximations of mineral nodules in terms of colour, shape and density.
Extensive studies of nodules to date indicate that they vary in size and shape as much as potatoes do, which has influenced the sizing and power of the delta arms to ensure secure grasping of nodules without energy-inefficient (and environmentally harmful) fumbling. It has especially guided Impossible Metals’ proprietary end effector design; for the Collingwood demonstration, this was constructed to grasp in a way that can secure objects from 3 to 10 cm in diameter. The end effectors on future vehicles will be further optimised for the specific requirements of nodules in different regions, as established across a wide range of available research.
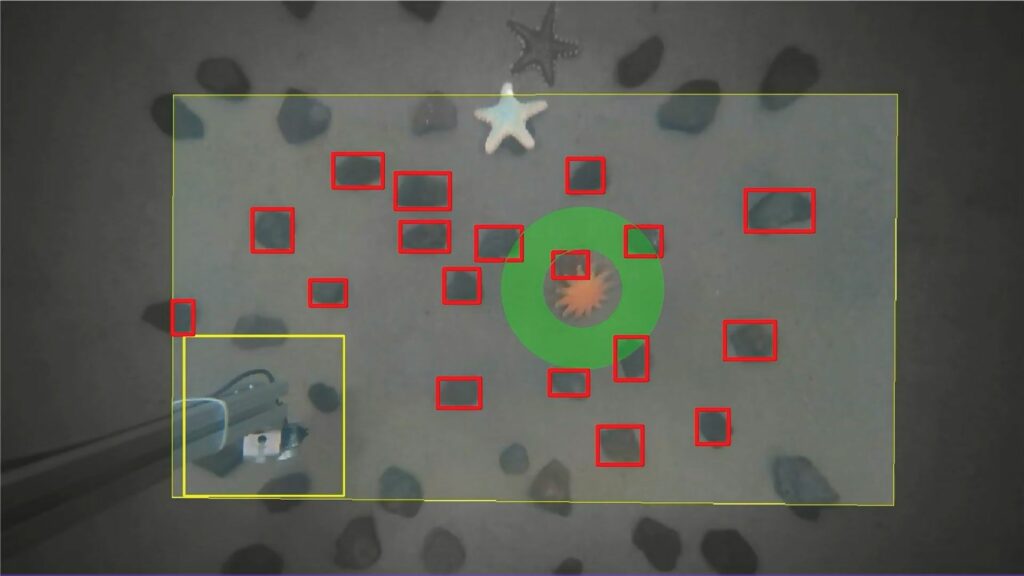
Thereafter, the team used modelling techniques to expand the generic nature of the machine vision, enabling it to function smoothly across different real-world environments, including continued training of the system with existing repositories of nodule footage.
“We then went through a similar development cycle for life detection, adding non-nodule features to simulated and recorded environments for training, which is how it’s able to class background elements as sediment, non-background items as objects, and objects as either nodules to be potentially collected or non-nodule items to be avoided,” Gillham says.
“And as we collect more footage in real-world operations, that’ll help us to be more discerning, in understanding things like which species of life are we looking at. That could enable different rules for harvesting or avoidance, depending on whether we’re looking at, say, an endangered species, a species of ‘least concern’, or an invasive pest.”
Hooked on a reel
The Eureka II was designed for 100 kg of nodule carrying capacity, which it filled in just under 30 minutes of active collection time (Eureka III is designed to carry 4000 kg).
As mentioned, the AUV was launched by mobile crane on the demo day (but it has been launched by an A-frame crane in sea trials). Recovery, however, poses a greater challenge than launching owing to the need to respond to how waves affect the distance and angle between the AUV and the crane. That relative dynamic motion needs to be accounted for or even cancelled.
“So, for recovery, we’ve developed – and demonstrated on that day at Collingwood – a novel recovery process for our AUVs, using what we call our ‘smart hook’,” Gillham says.
“This is a system with a crane that deploys a hook, which is lowered below the waves to engage with the AUV, and it holds it there in a stable and stationary way. Having secured it underwater, which is far easier than doing so above water, the winch can pull it back up above the surface.”
With the buoyancy engine and thrusters keeping Eureka stable (processes made easier by the AUV having been designed as very ‘bottom-heavy’ with a low CoG), the hook attaches to the top of the AUV using a proprietary mechanical auto-engagement device, which inserts into a cup atop the AUV’s syntactic foam body.
“Rather than lower the hook to precisely over the AUV’s cup, we used an ROV to ferry the hook over, using one of its own end effectors, which then enabled us to remotely mate the engagement devices to the AUV,” Gillham says.
“That was just a proof-of-concept, however, and we’re very much intending to develop the smart hook with a UUV that will be fully autonomous, with intelligence and cameras to empower it to swim over and engage with Eureka. That UUV’s tether will ultimately form the recovery cable by which the topside winch reels the deep-sea AUV and its nodule payload into port.”
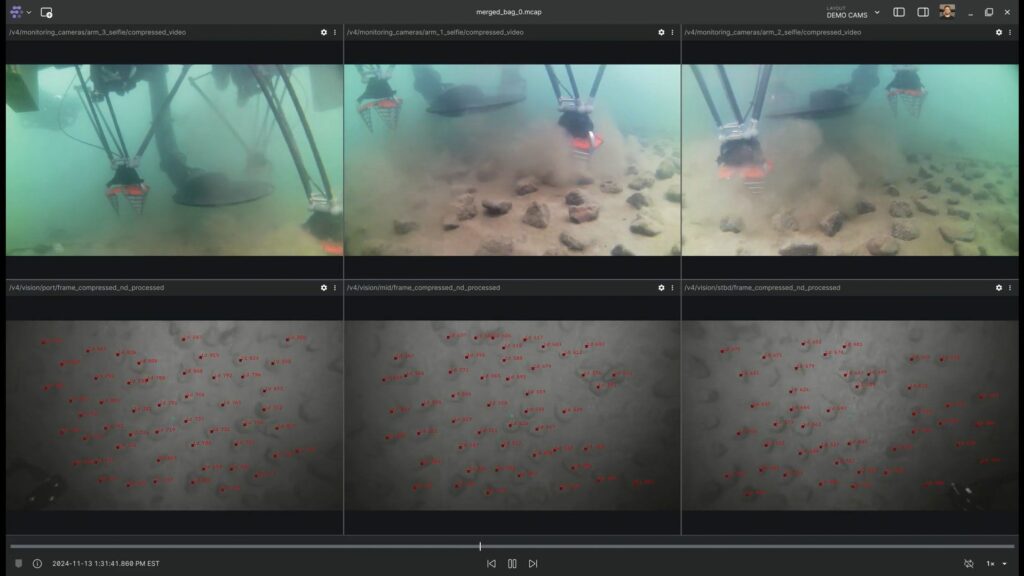
Future
As mentioned, the next phase of Impossible Metals’ plans is to develop Eureka III. It aims to prototype that commercial AUV over the course of this year, with 2026 as its target for the first ocean mining tests of the new system.
Based on current designs and analyses, Eureka III will weigh 4950 kg in air, feature 7–12 delta robot arms, run on 142 kWh of batteries, and measure 5.1 x 2.6 x 2.4 m. As discussed, it will be capable of carrying 4000 kg of nodules, operating down to depths of 6000 m (like Eureka II), and each vehicle is expected to cost $1.8 m to manufacture.
Although it might be some way off, Eureka IV’s design specification has it as an 11,950 kg (in air) AUV that is able to harvest 12,000 kg of nodules (with 15 harvesting arms), costing $3.2 million per unit.
“But as well as those main business and engineering objectives, we also keep in mind what happened after the Space Race: there were so many secondary uses of the technologies developed back then, and we’re already receiving interest in ways of modifying some of our subsystems to serve as commercial products in their own right,” Gillham adds.
“For instance, some like our buoyancy engine and smart hook for their potential to work as subsea docking machinery. Even our stereo camera, which might not seem unique, has received interest because of the unique underwater application we’ve tailored it to work within.
“Over this year and the next, it’s likely we will start to commercialise aspects of the systems we’ve developed for the underwater technology market as a whole, rather than just serving in our specific, albeit huge, niche.”
Key specifications
Eureka II
AUV
Dimensions: 3.2 x 1.95 x 1.93 m
Weight in air: 3950 kg
Battery energy: 14.4 kWh
Operating speed: 5–10 cm/s
Carrying capacity: 100 kg
Maximum depth: 6000 m
Some key suppliers
Inertial systems: Exail
DVLs: Nortek
Forward-looking sonars: Imagenex
Thrusters: Copenhagen Subsea
UPCOMING EVENTS
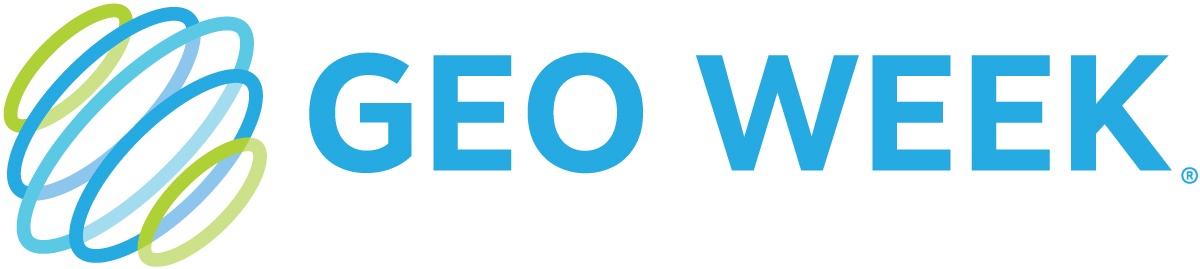
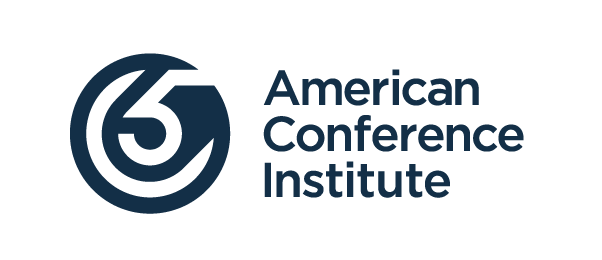
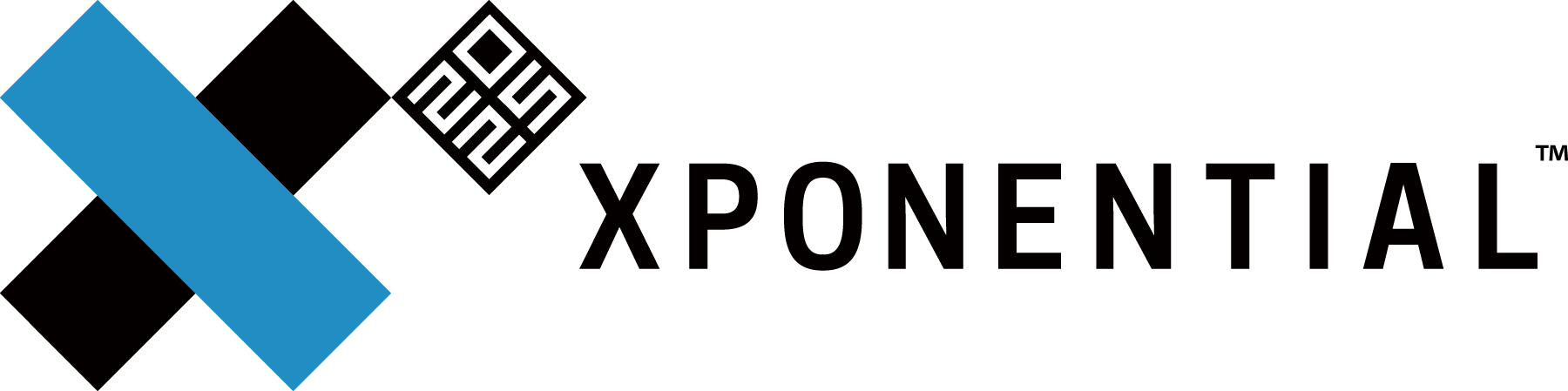
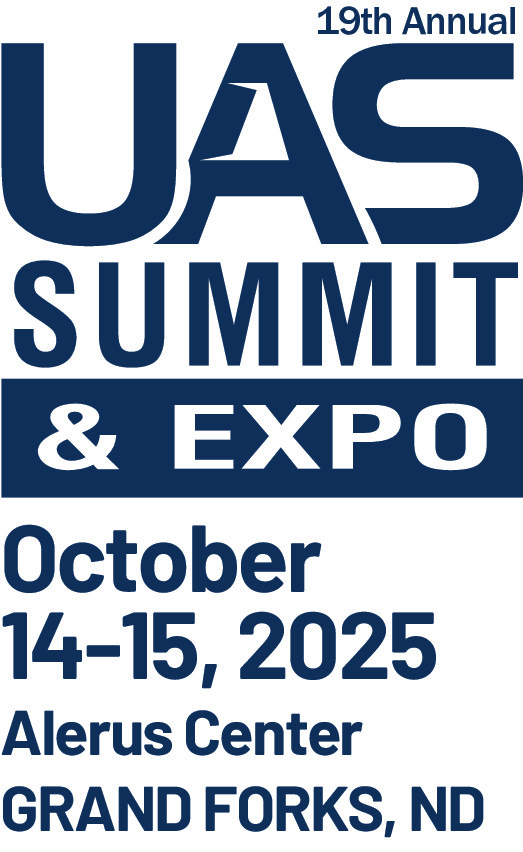
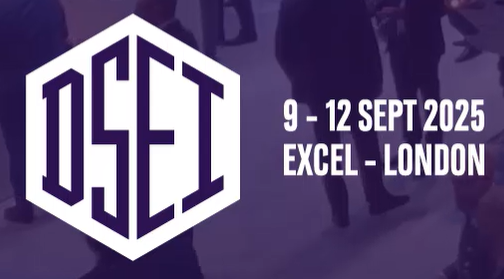
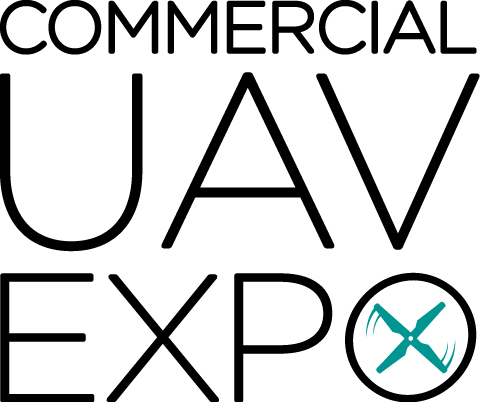
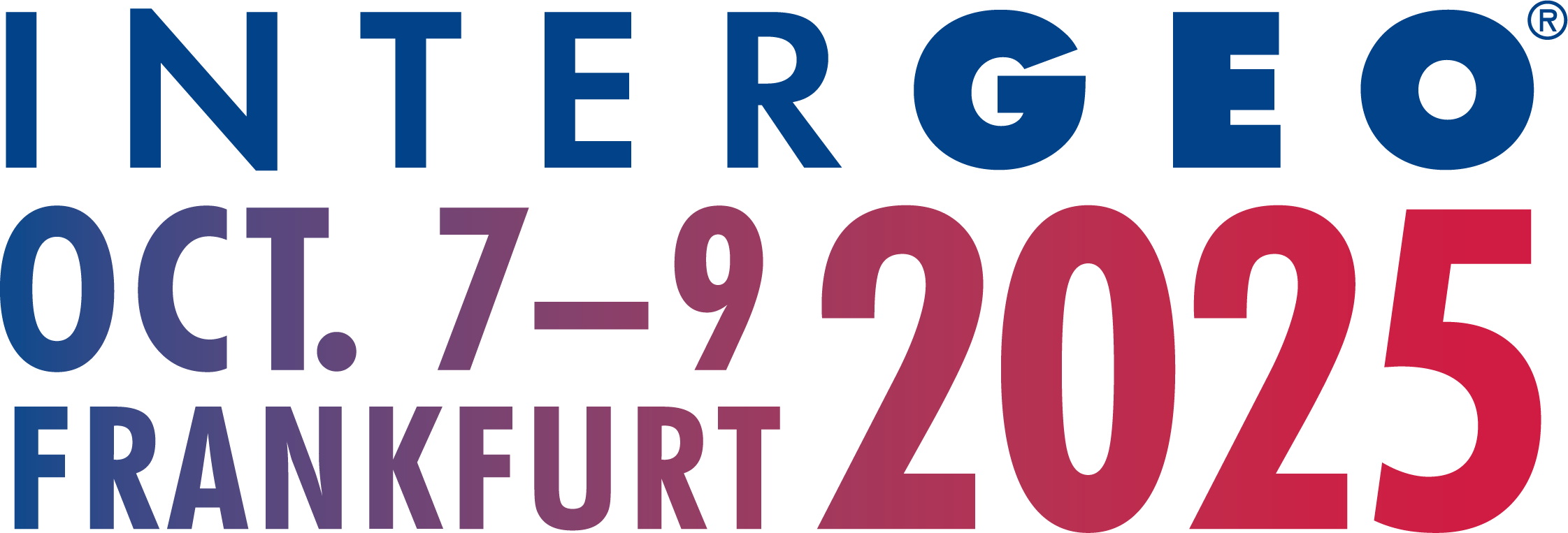
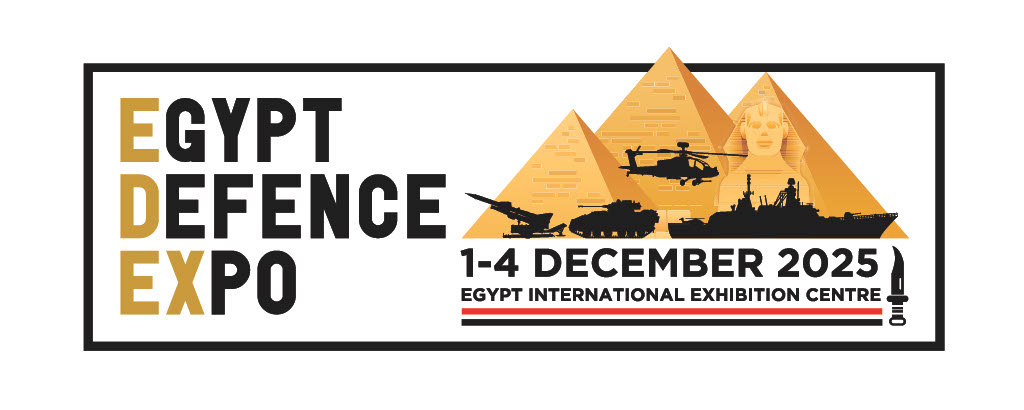
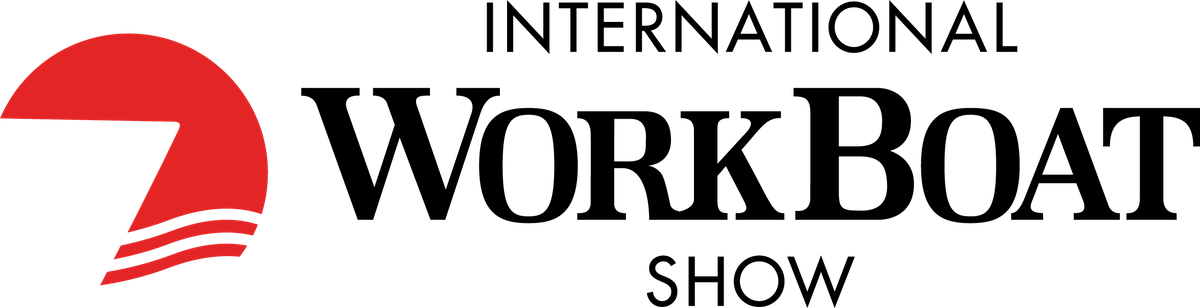
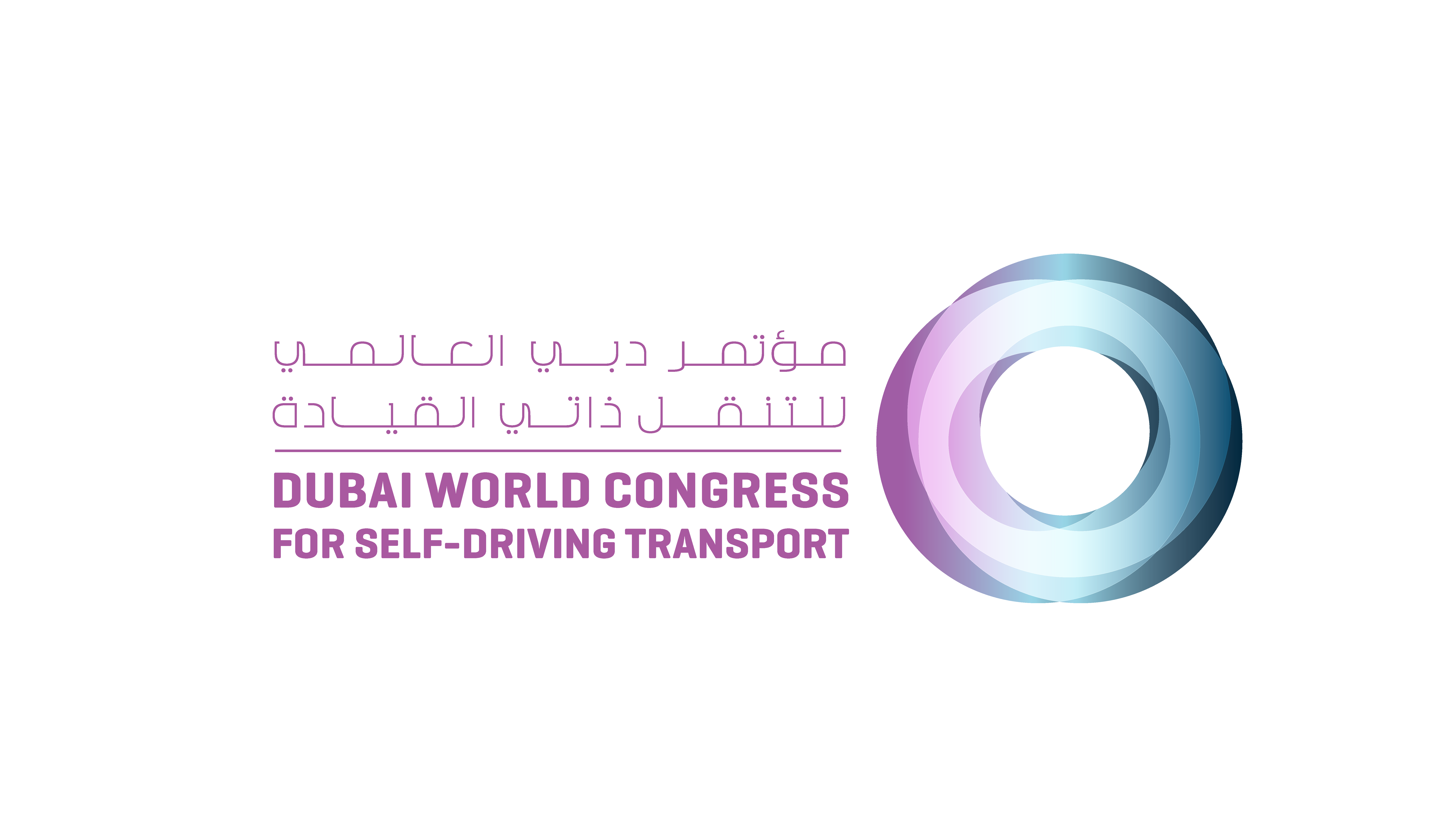

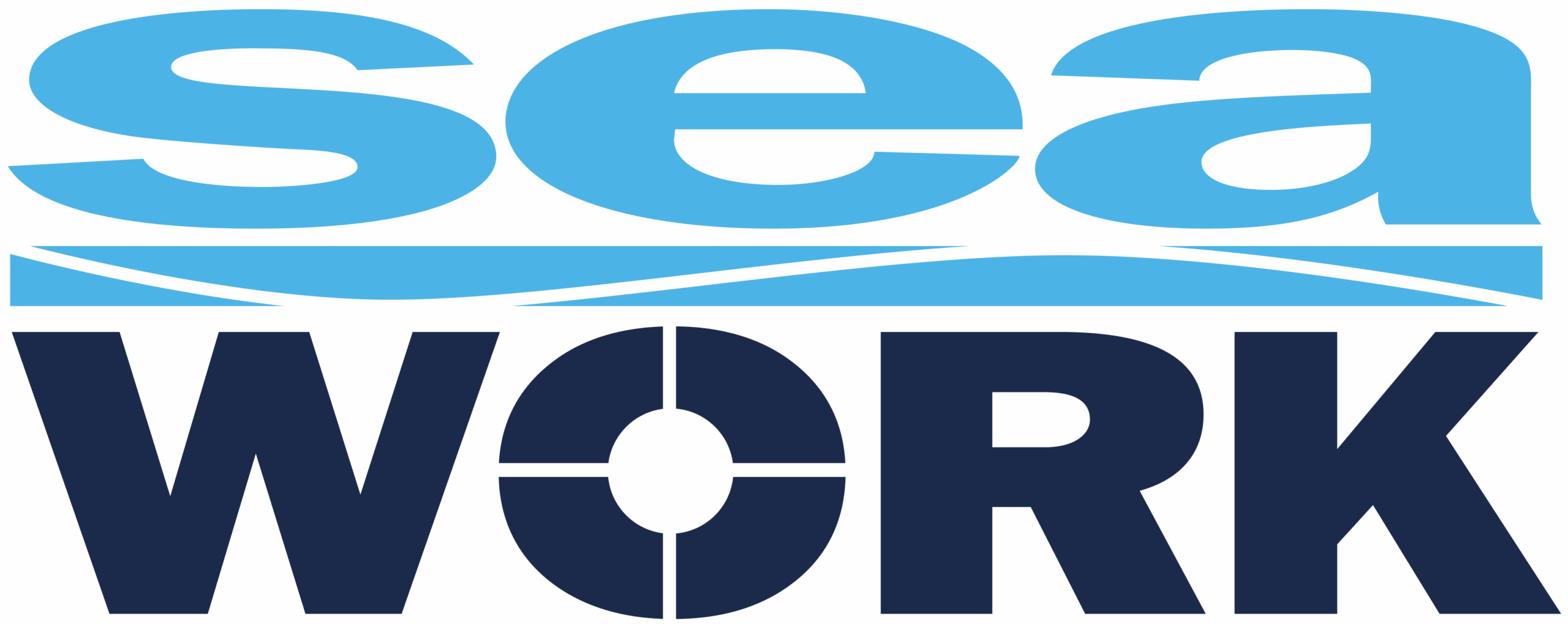