IM Solutions Monodrone IM 3000 Mk2
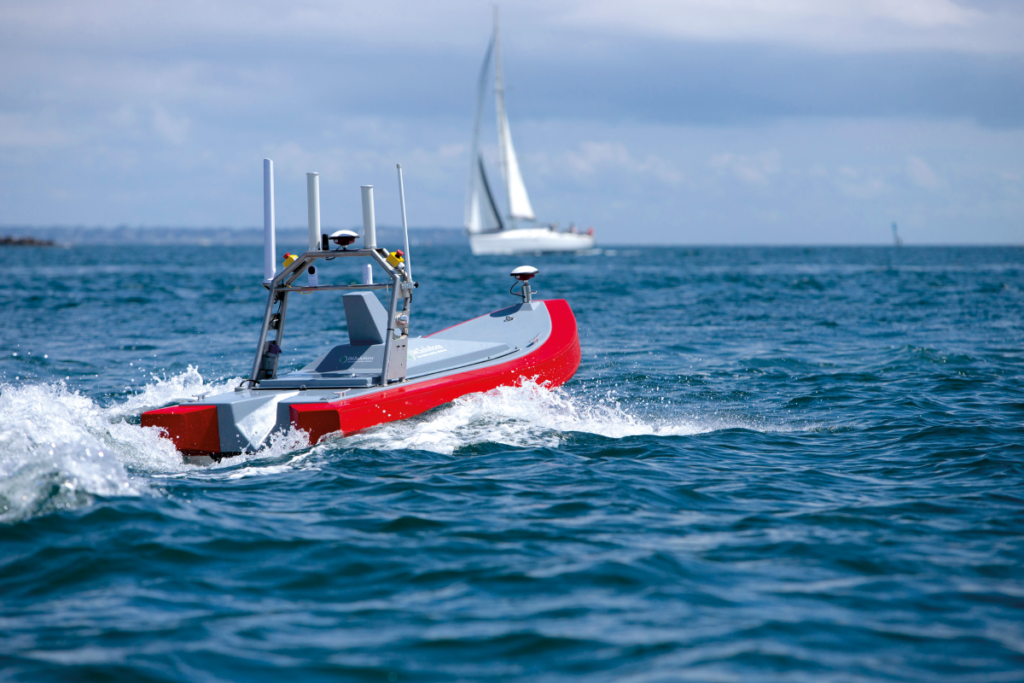
(Courtesy of IM Solutions/Christophe Le Potier)
Fitting right in
Peter Donaldson reports on how a customer’s request for an intermediate-sized survey vessel prompted one developer to add this USV to its range
Sebastien Manigot, operations manager at USV developer IM Solutions, describes the company’s new Monodrone IM 3000 Mk2 as a gap-filler in its range of vessels, which also includes 1.3, 1.8 and 7 m craft.
The rigid-hull boat was developed at the request of some of the company’s customers for a platform of intermediate size with good sea-keeping capabilities and a useful range and payload. The numbers that emerged from that requirement was a length of 3 m, the ability to operate in up to sea state 3, an endurance of 12 hours at survey speed and a payload of 65 kg, Manigot says.
Shallow water missions
Designed for operation in shallow water in coastal as well as open ocean areas, the electrically propelled IM 3000 is intended for a variety of survey missions, including bathymetry using a high-resolution multi-beam echo sounder (MBES), and debris surveys with interferometric sonars such as the Kongsberg 2040 and the EdgeTech 6205s.
Manigot adds that the USV is also suitable for harbour monitoring tasks, as it can be equipped with a high-resolution camera or a Lidar on the bow, and water column analysis using a high-end acoustic Doppler current profiler. A winch with 100 m of cable supports water column analysis, sound velocity sensor (SVS) profiling and conductivity, temperature and depth (CTD) measurements.
The vessel is also equipped with a situational awareness payload that monitors the area immediately around it and warns the operator of any collision risks. The collision avoidance suite is a new option on the Mk2, he says.
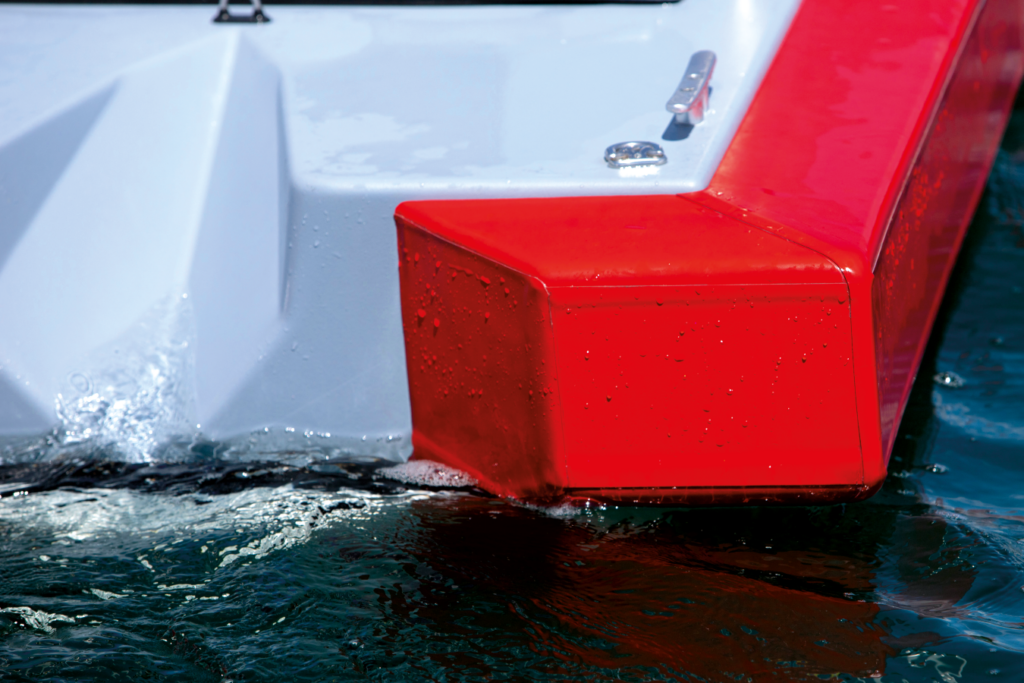
(Courtesy of IM Solutions/Christophe Le Potier)
He explains that the vessel’s mission computer runs open platform client software that enables any kind of sensor to be installed, automatic identification system (AIS) and software-defined radio (SDR) receivers being typical of the kinds of other systems operators add.
In addition to the open computer platform, payload support facilities include a dedicated payload bay, power supply and a telemetry link supporting multiple bearers.
Supplementing the internal bay are several other options for payload mounting and deployment, including a 300 mm2 moon pool that provides access to the water through the hull, an antenna mounting frame and a reinforced deck at the bow.
The telemetry link works with the comms suite, which can choose the best bearer for any given situation, switching automatically between satcom, LTE cellular comms and wi-fi, Manigot notes.
While the comms range using wi-fi is limited to around 2 km, it is practically unlimited when connected to an LTE network or using its VSAT satcom installation, he says.
Running at its survey speed of 2 knots, the IM 3000 can extend its 12-hour mission endurance to 16 hours with an extra battery pack, although naturally with less payload. Manigot quotes a top speed for the vessel of 14 knots.
Daughter vessel
While designed primarily for shore-based shallow water bathymetry and debris survey, it can also serve as a daughter vessel for a conventional survey ship, Manigot says.
For example, one client is using it for an offshore cable debris survey in the Baltic, in an operation that includes both bathymetric work and water column imaging. Manigot explains that the USV is used in the tide zone, where the crewed mother ship cannot go. “The USV is operated from the beach while the survey vessel does the offshore part, so productivity is increased and transit times are optimised,” he says.
Manigot describes the IM 3000 first shown at Oceanology International earlier this year as the ruggedised Mk2 version, which incorporates improvements based on operational experience with the Mk1.
“We had a lot of interesting client feedback on the Mk1, and we took that into account when designing the Mk2. The first version was a semi-rigid vessel with an outboard motor, and lacked a winch for SVS or CTD sensors; battery charging was tricky as well,” he says.
“The Mk2 is completely waterproof and includes an onboard charger, so there is no need to open a hatch and therefore no risk of water ingress during charging. That is particularly useful during charging on the survey vessel’s deck.”
Mounting the motors inboard allowed IM Solutions to put a winch at the stern, along with a new aluminium A-frame, to ease deployment and recovery of cable-mounted sensors. “We also fitted ruggedised fenders that allow it to stand up to harsh contact or rough handling, so the Mk2 version is designed for real-world survey operations.”
The hull structure is moulded from glass fibre-reinforced plastic (GRP), while the fenders are made from tough closed-cell foam and the mast from inox (French for stainless steel).
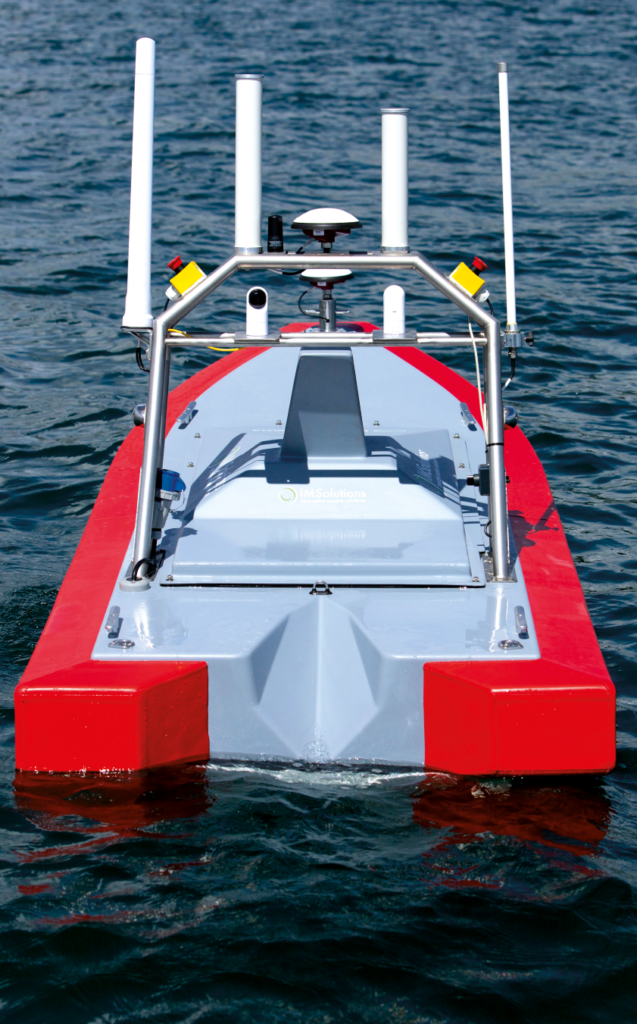
(Courtesy IM Solutions/Christophe Le Potier)
For the electric powertrain, IM Solutions chose a single solution including batteries, power management, motors and propellers from Torqeedo, Manigot says, citing their reliability and ease of integration.
With a boat that has to work well in shallow inshore waters as well as the open sea, hull design was one of the key challenges, he explains, because both stability and manoeuvrability are crucial and conflict with one another.
“For open water work, having a stable platform – particularly in heave – is very important for data quality. The IM 3000 has excellent sea-keeping capabilities thanks to its length-to-width ratio.”
Manoeuvrability is the most crucial aspect of shallow water operations, so in these environments USVs have to be able to avoid beaching and to complete surveys in confined areas. One of the keys to this is the pair of independently controllable electric motors, he says.
The motors are housed in pods, and drive high-efficiency, fixed-pitch, three-blade propellers through planetary gearsets.
The launch of the Mk2 in March this year followed a trials programme, and the vehicle went into commercial service in the summer. Since then it has been working mainly in debris and bathymetric survey missions, using Norbit, EdgeTech and Kongsberg sensors.
Multiple sensor options
The vessel displayed at Oceanology International was fitted with an EdgeTech 6205 S2 wide-swathe bathymetry and dual-frequency sidescan sonar. EdgeTech says the 6205 S2 overcomes the limitations of MBES and interferometric sensors in shallow water through the use of the company’s multi-phase echo sounder (MPES) technology.
IM Solutions describes MPES as a hybrid approach that uses multiple receive arrays and combines beam-forming and phase-differencing techniques in each sounding. That, it says, results in a clean 200º swathe as well as faster and safer surveys.
It also uses EdgeTech’s version of compressed high-intensity radiated pulse technology that transmits pulses which change in frequency with time, exploiting the returns from multiple frequencies within the pulse to generate more information. That enables the sonar to exceed widely recognised standards for feature detection bathymetric data point uncertainty, the company says.
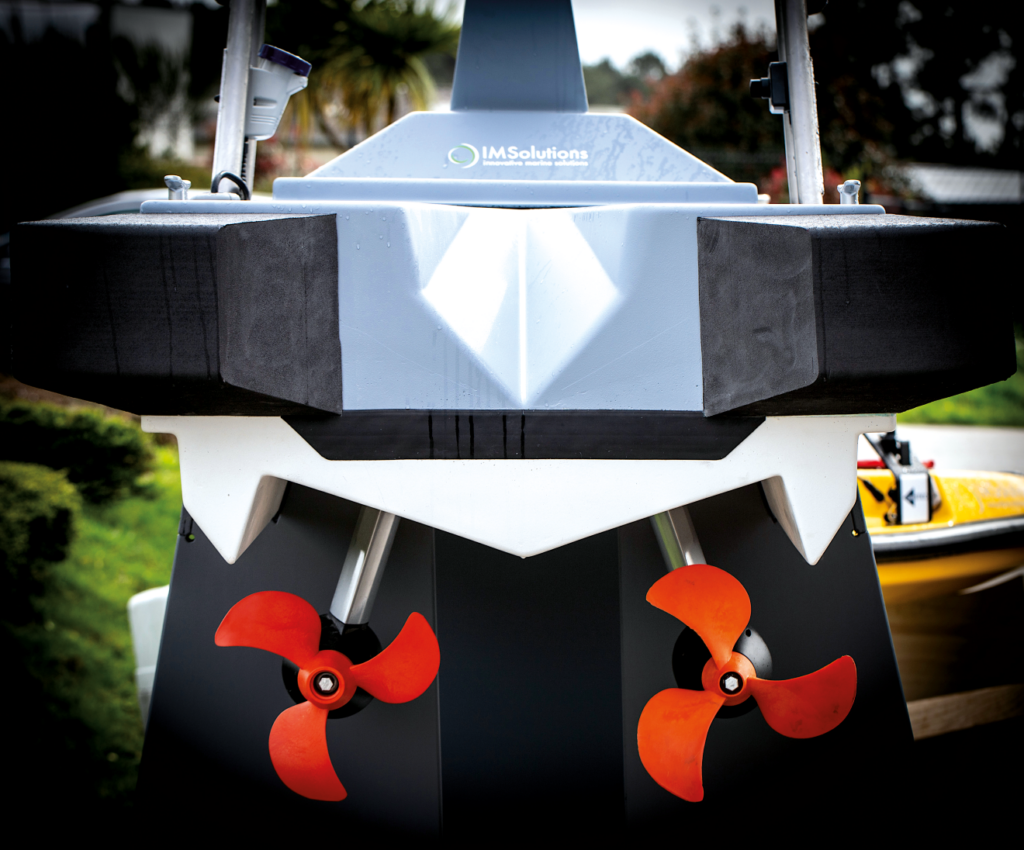
(Courtesy of IM Solutions/Christophe Le Potier)
For bathymetry, it can operate at frequencies centred on 520 and 850 kHz, while for sidescan imaging operations it can use frequencies centred on 230, 520, 850 and 1600 kHz.
Weighing 21.4 kg, the ‘ultra-lightweight’ version of the sonar measures 77 cm long, 33 cm wide and 34 cm high. The company also works with Norbit, which offers a range of light and compact wideband multi-beam sonar (WBMS) systems for bathymetry from USVs in shallow water.
Its iWBMSh, for example, is a high-end turnkey system designed to operate in all conditions, including rough seas and under bridges. It features an integrated IMU and an NRTP client, which is a means of communicating differential GPS corrections to a GPS receiver.
It features an 80 kHz bandwidth over a frequency range from 200 to 700 kHz and a nominal operating frequency of 400 kHz. Software capabilities include processing frequency modulated and continuous wave signals, several backscatter modes and a multi-detect capability that enables real-time detection of objects in the water column as well as on the seafloor. It also has an integrated sound velocity probe.
With a sensor head assembly measuring 348 mm long, 227 mm high and 236 mm wide, the sonar provides swathe widths from 5º to 210º, along with a range resolution of better than 10 mm and between 256 and 512 beams.
The EM 2040 is an established family of MBES sensors from Kongsberg, with the EM 2040P MkII for example representing the latest standard demonstrated on USV platforms. Available as a 200-700 kHz system, it enables the operator to choose the best frequency for the application, according to Kongsberg, such as 300 kHz near the bottom, 200 kHz for deeper waters and 400-700 kHz for very high resolution inspection.
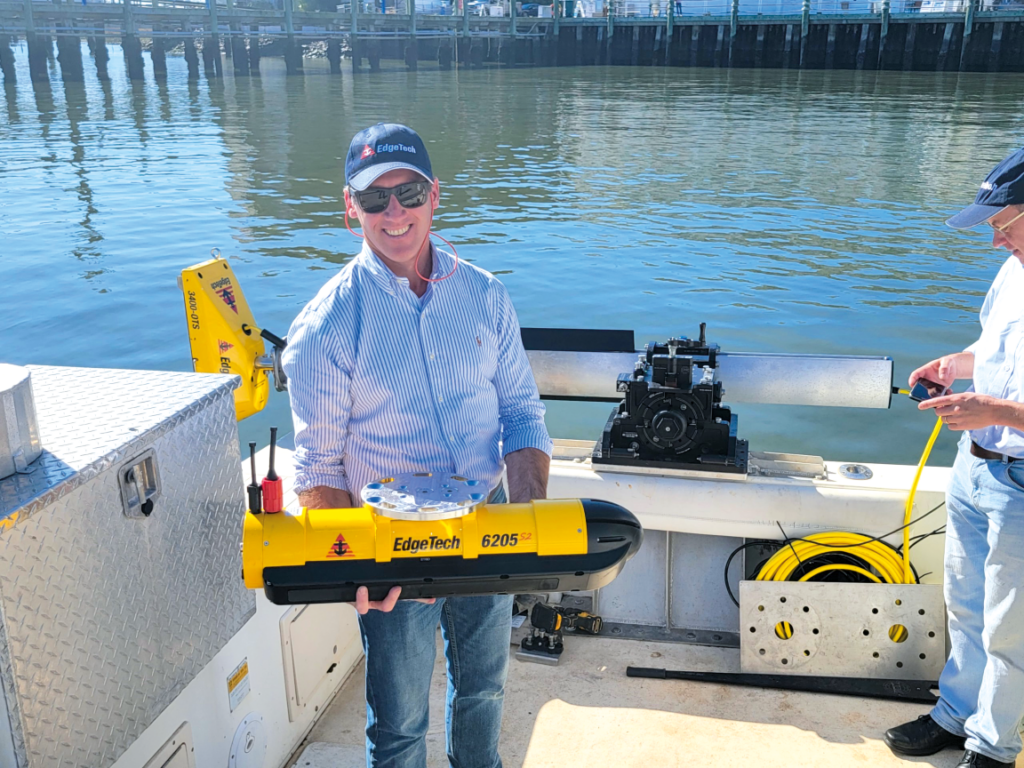
(Courtesy of EdgeTech)
It also offers a 600 kHz wide area mapping mode in which it can achieve a swath width from 100º to 120º, while 700 kHz provides the sonar’s highest resolution within a swathe width of 30º, the company says.
It can also generate multi-frequency backscatter to improve characterisation of the seafloor. By changing frequency modes as it scans, it can provide backscatter from up to five frequencies in a single pass, Kongsberg says.
Its large bandwidth enables a sample rate of up to 60 kHz, the company adds, and its ability to use very short pulses improves range resolution. For its shortest pulse, which lasts just 14 µs, Kongsberg quotes a raw range resolution of 10.5 mm. In terms of angular coverage in the 200-300 kHz range, the company gives a figure of up to 170º.
Accurate water temperature measurement is critical to the interpretation of sonar data, and RBR, which makes thermistor strings, is another of the sensor companies with which IM Solutions works closely. Thermistors are semiconductor devices with a negative temperature coefficient, meaning their electrical resistance falls as their temperature rises.
With between 12 and 24 thermistors in a string deployed vertically in the water column, the RBRconcerto Tx system for example can be set for sampling periods of between 3 seconds and 24 hours, and can resolve temperature changes as small as 0.00005 ºC over a measurable range of -5 ºC to +35 ºC.
Above-surface sensors include Lidars from Velodyne for high-resolution 3D imaging of structures in harbours and so on.
While an increasing number of sensors come with integrated IMUs, the IM 3000 can be equipped with units from SBG Systems such as those from the Ekinox family, to provide a common stable reference for the whole sensor suite.
Mission preparation
Making the USV ready for a mission has been kept very simple, Manigot says.
“We provide a full parameter checklist in order to prepare the mission, so just a few steps are needed – switch the power on, check the battery level and GNSS reception, perform a basic motor check, then download the mission path. With that done, the client can start a survey.”
Missions are planned on widely used survey software, such as those from Beamworx and Hypack, and downloaded to the autopilot.
Launch & recovery remain among the most challenging aspects of USV missions, Manigot notes, adding that the company has designed a dedicated trailer to make that operation easier and is working on an autonomous docking system to reduce workload further. For launch & recovery from ships at sea, the USV is fitted with a three-point lifting system that hooks up to a crane.
So far, the IM 3000 has not been certified to any set of maritime regulations, but work on that is under way. “We are working on a gap analysis to look at what we have developed and what the maritime regulation is requesting, and we will bridge that gap in the Mk3 version,” Manigot says.
In the meantime, the vessel operates under special permissions granted on a case-by-case basis, obeying the COLREGs, which are the recognised ‘rules of the road’ at sea.
Automating collision avoidance
IM Solutions offers several options for situational awareness and collision avoidance. Its basic system relies on a set of cameras that provide a video feed, allowing operators to follow normal COLREGs, while a more sophisticated optional package includes AIS and radar to increase the range at which potential threats can be detected.
However, in the near future the company intends to offer what Manigot calls a complete system that will incorporate fusion and AI to provide a semi-autonomous collision avoidance capability.
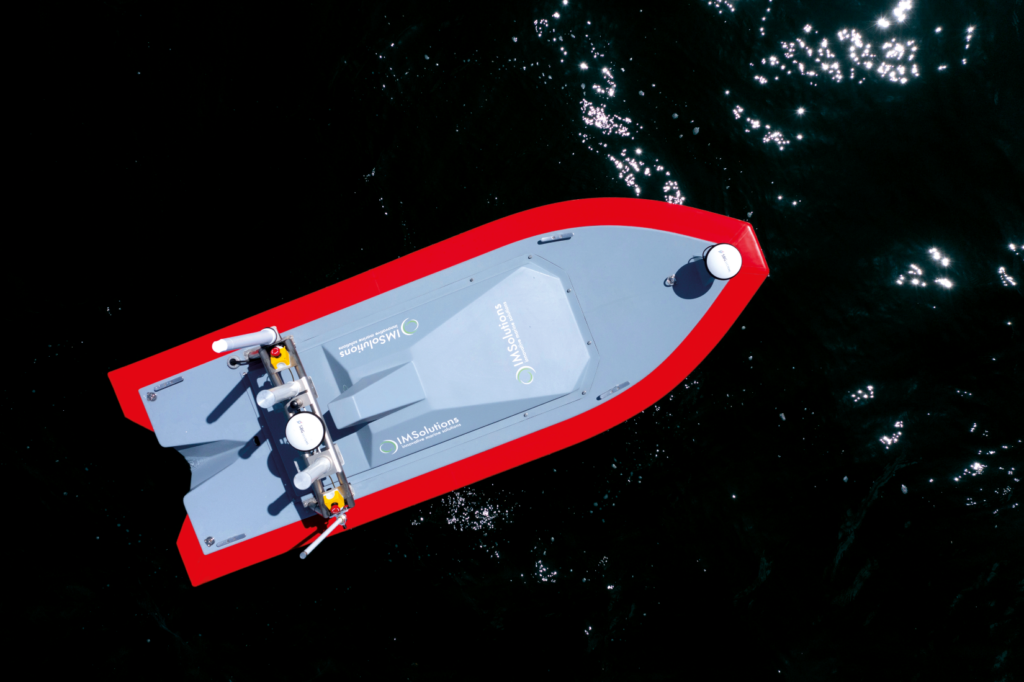
(Courtesy of IM Solutions/Christophe Le Potier)
As with most survey USVs, the normal operational team is two people: one to monitor and pilot the vessel, and watch the feeds from the situational awareness cameras; and a qualified surveyor whose main responsibility is to check the quality of the data the sensors are generating.
The operators can communicate with the IM 3000 over any of the bearers, but to conserve bandwidth only sensor quality control data and a remote desktop showing the map and basic vehicle data are normally displayed, along with the feed from the situational awareness cameras. However, targets generated by the AIS can be plotted on the survey software. The bulk of the sensor data is stored on board the vessel to be downloaded at the end of the mission over the wi-fi link.
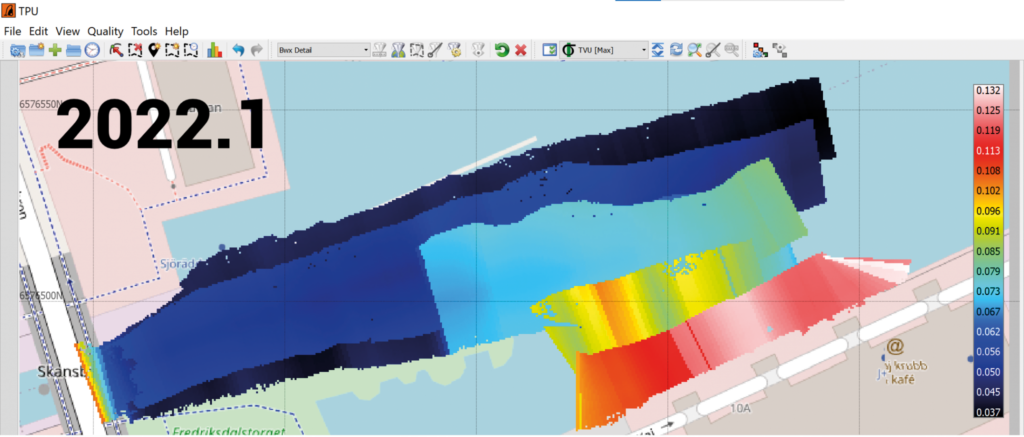
(Courtesy of Beamworx)
Manigot notes that there is minimal interaction between the USV and the operator during a mission, as the IM 3000 normally operates on autopilot to follow the waypoints that define its survey line or pattern. “Operator action is only needed if a dangerous situation begins to develop, such as a potential collision for example,” he says. That, he adds, makes it possible to operate several IM 3000s simultaneously from a single control station.
While the IM 3000 is not equipped to launch and recover smaller uncrewed vehicles, it is a capability that IM Solutions’ r&d department is studying, and one that will probably be implemented in the Mk3 version, he says.
Care and maintenance
Routine maintenance of the vessel between missions is designed to be simple and require minimal tooling, the main points being tightness checks on the propellers and a few other components, as well as careful washing down after use to stave off corrosion.
Even though changing the batteries is not normally required, the process is designed to be easy; as such, they are accessed through a wide hatch. However, the batteries are 48 V items that weigh 45 kg each, so they normally remain in place and are replenished by the onboard charger.
The moon pool gives easy access to subsea sensor payloads, Manigot notes. “A complete survey set-up, including INS and MBES installation, can be completed in less than a day,” he says.
In the near future, IM Solutions plans to extend the sensor suite, adding the ability to tow a small sidescan sonar, a sub-bottom profiler and a magnetometer to offer a full survey portfolio.
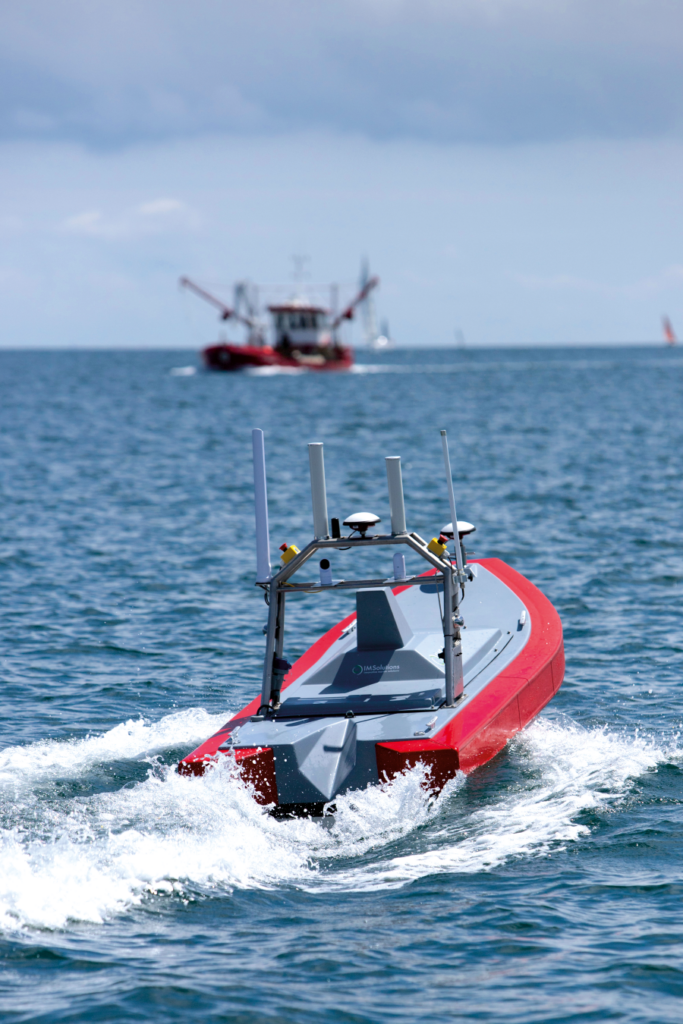
(Courtesy of IM Solutions/Christophe Le Potier)
Specifications
Length: 3 m
Survey speed: 2 knots
Maximum speed: 14 knots
Payload: 65 kg
Comms range: 2 km (wi-fi), unlimited (satcom, LTE cellular)
Endurance: 12 hours standard, 16 hours with extra battery pack
Launch & recovery: dedicated trailer or three-point lift for crane
Some key suppliers
Acoustic survey software: Beamworx
Acoustic survey software: Hypack
Sonar systems: EdgeTech
Sonar systems: Kongsberg
Sonar systems: Norbit
Lidar: Velodyne
Inertial navigation system: SBG Systems
Thermistor string: RBR
Battery pack and electric powertrain: Torqeedo
UPCOMING EVENTS
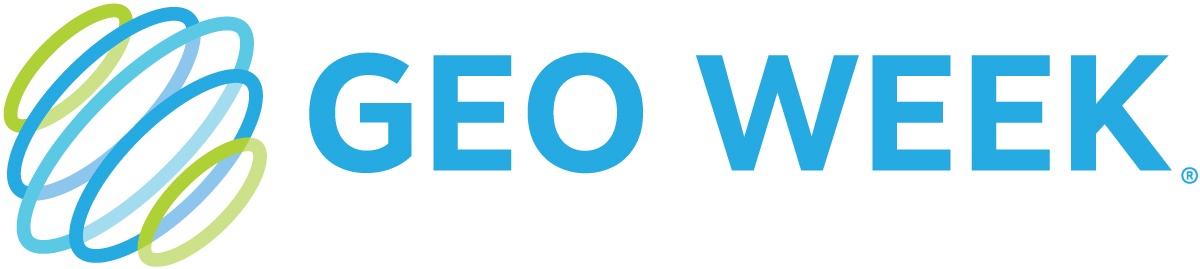
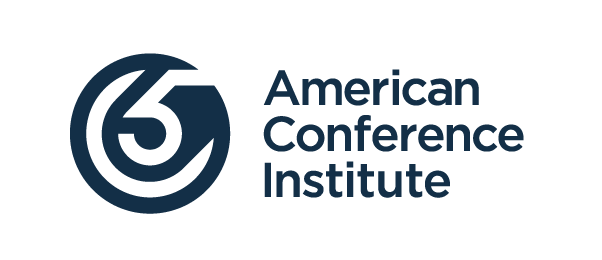
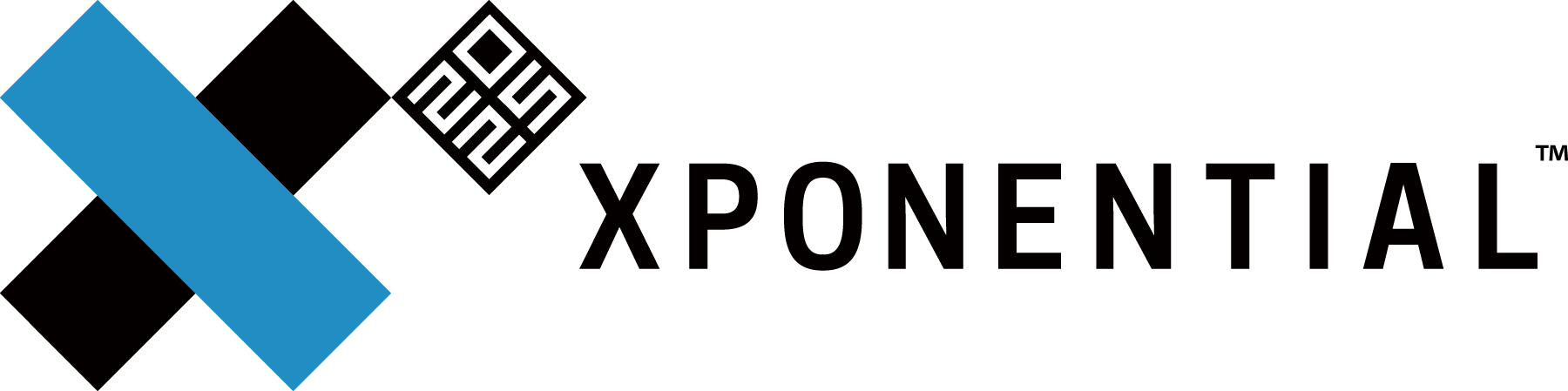
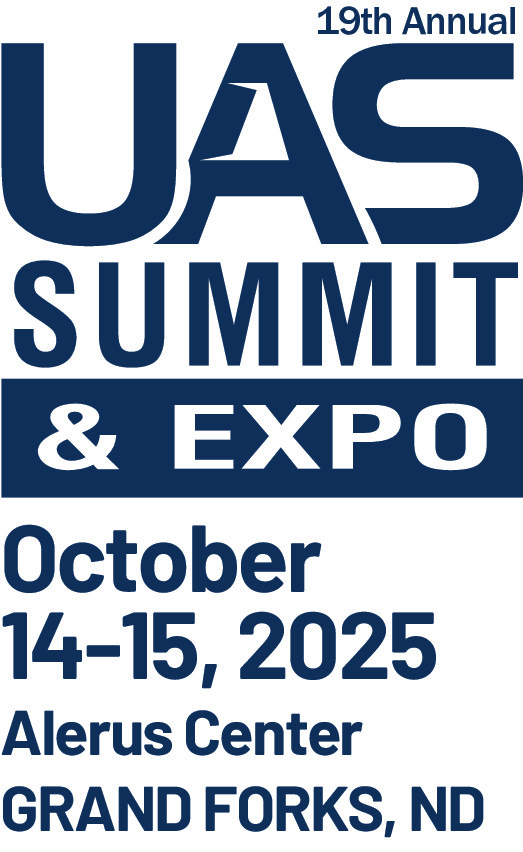
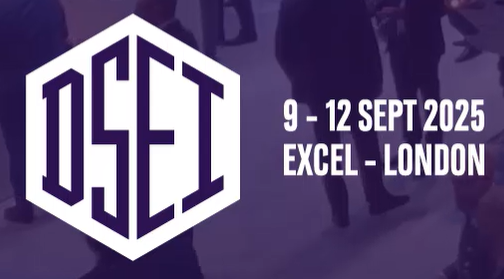
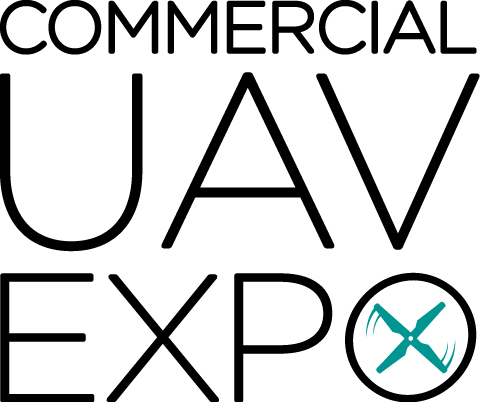
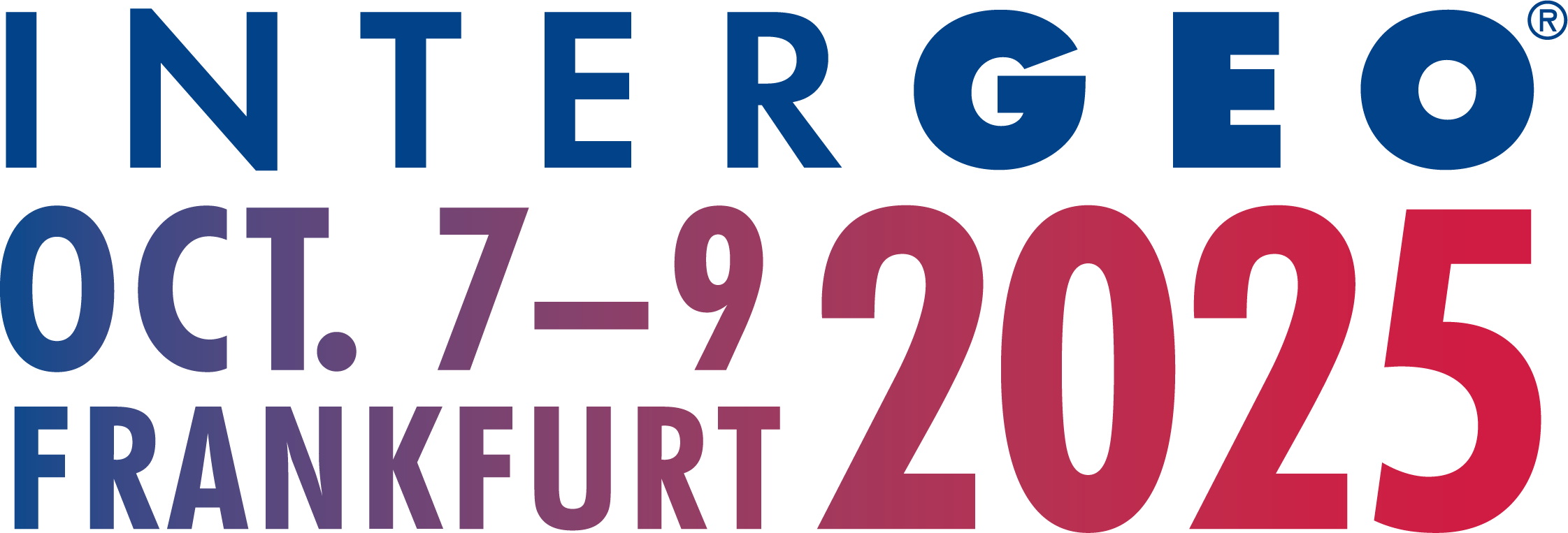
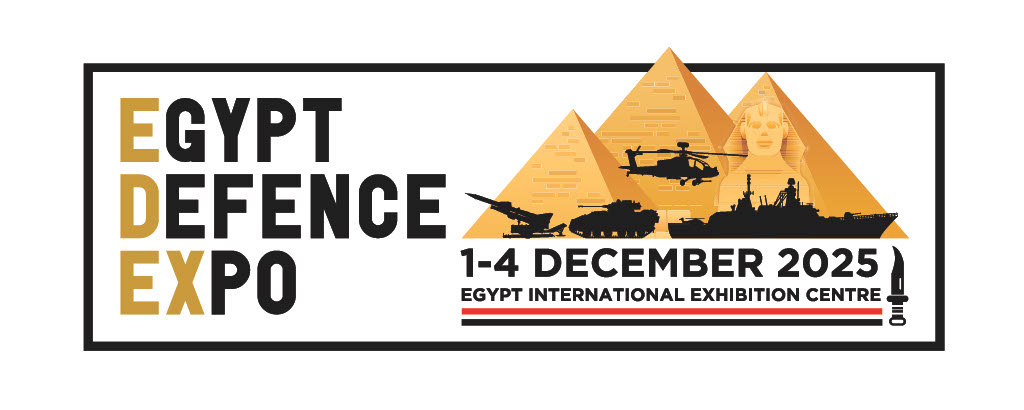
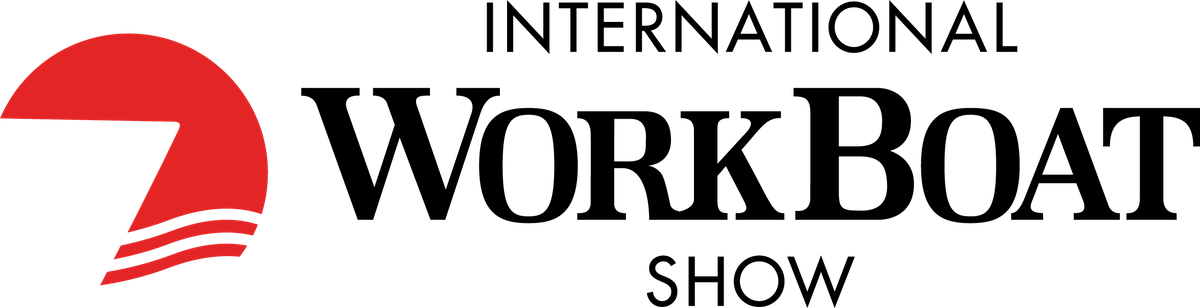
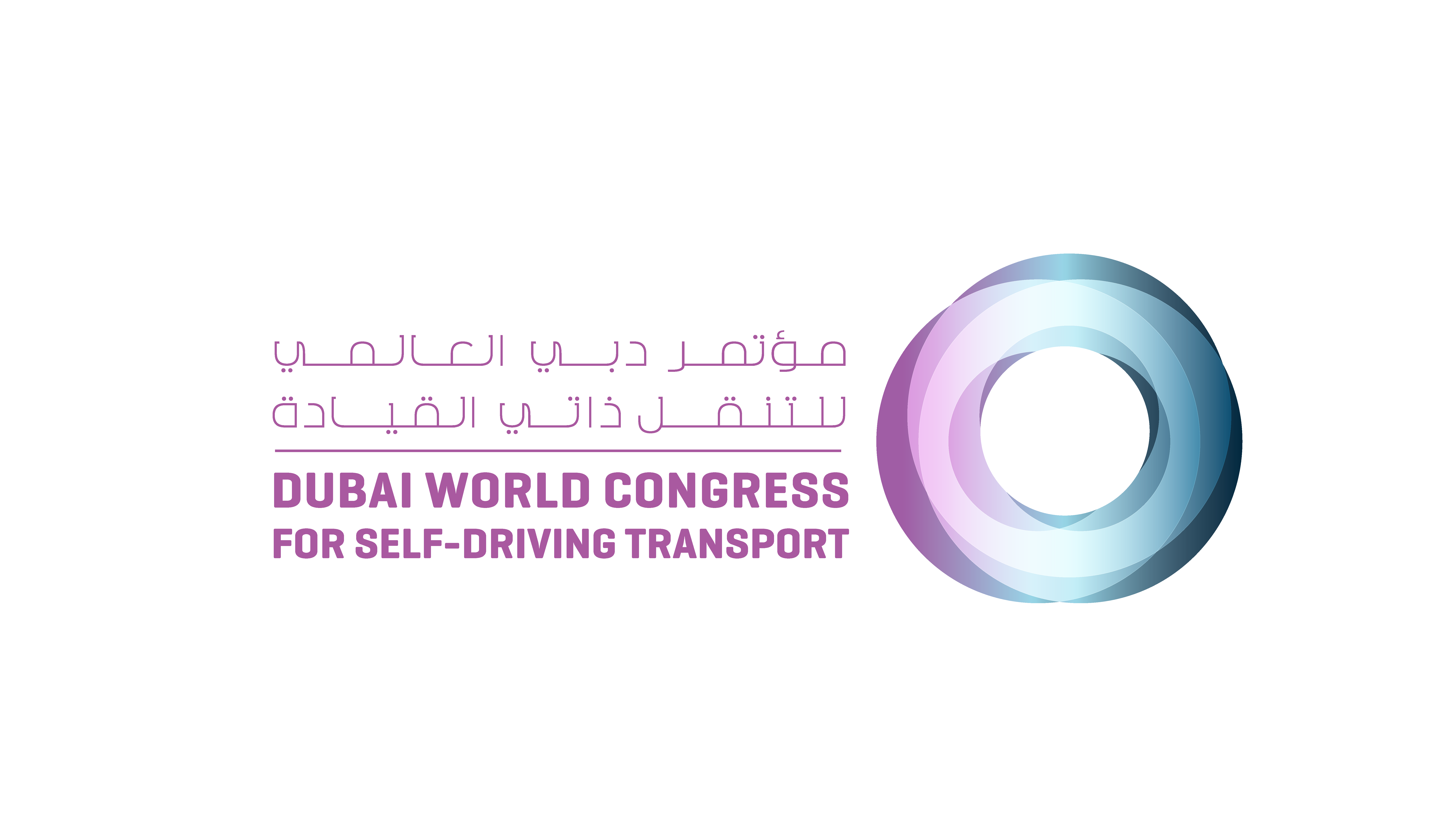
