UGVs
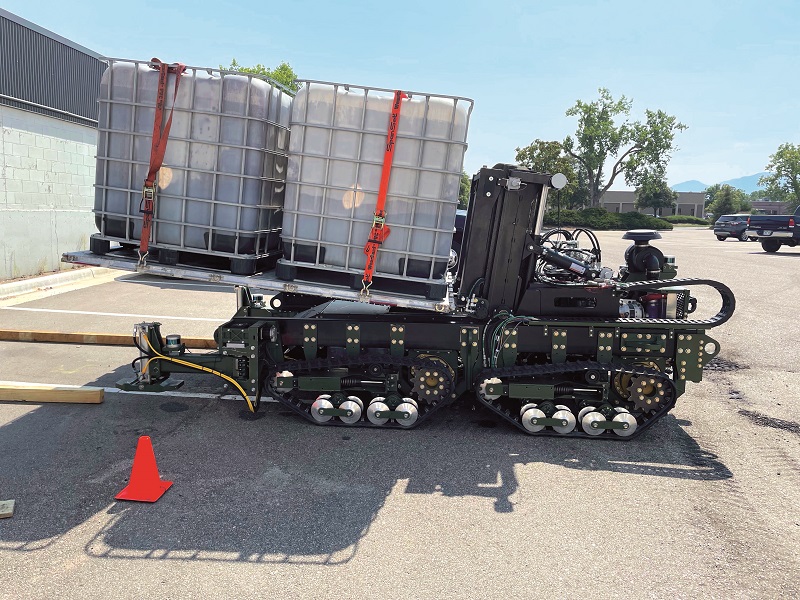
Danger zone
If there’s a job too dangerous or too dirty for people to carry out, there’s now a UGV designed to do it instead. Rory Jackson reports
Not so long ago, UGV developers were few and far between, but now there are hundreds of them, tailoring autonomous robotic solutions for organisations and markets of every stripe. And as with aerial and aquatic systems, they are particularly valued in applications regarded as highly dangerous, dirty or otherwise undesirable for people.
As a result, many UGVs are being engineered in uniquely intelligent ways, not as multi-purpose ‘Swiss army knife’ tools as multi-rotor UAVs often are, but as highly specialised systems for taking on some of the most heavy-duty jobs in the world.
Military logistics
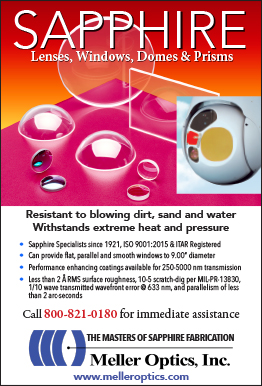
While logistics is often regarded as an enormous market for uncrewed systems, the term itself encompasses a huge variety of use cases and types of customer. In fact it is so large that UGVs are often designed for specific uses.
That often results in UGVs that look very different from each other. For instance, the Clevon 1 (UST 47, December 2022/January 2023), Kodiak’s Gen4 truck (UST 48, February/March 2023) and the Ottobot 2.0 from Ottonomy (see page 48) are all designed for ‘logistics’. However, the first is a 320 kg vehicle working mainly on city roads, the second is a giant highway-bound 18-wheeler that steers clear of cities, and the third is a 90 kg UGV that works principally in airport terminals or along sidewalks.
Another bespoke UGV is Stratom’s Autonomous Pallet Loader (APL), which has been developed largely for loading and unloading cargo from military as well as commercial aircraft and trailers.
Its design is similar to that of a forklift, but with four tracks rather than wheels, enabling tank steering for better manoeuvrability in confined spaces and over off-road terrain, as well as a proprietary system of powered rollers for easier autonomous transfer of cargo from its forks to racks. It is built for a 1:1 ratio between its empty weight and payload capacity, and currently weighs 10,000 lb (4535 kg).
“The current demand we see is based on the 10,000 lb payload capacity,” comments Mark Gordon, president and CEO at Stratom, on the decision to build the APL at that particular size. He adds that the platform will be adapted to different use cases as their cargo loading, unloading and transport needs evolve.
“One of its components for robust weight carrying is the patent-pending design of the outriggers, which allows the vehicle weight to be in parity with the payload capacity,” Gordon notes. “With this solution, customers can lift and transport heavy cargo without needing a counterweight or ballast on the back of the vehicle.”
The powered rollers meanwhile consist of a pair of removable, motorised and horizontally disposed conveyor belts (one immediately adjacent to each tine). Each belt consists of plates that grip the pallet and push it on top of the fork.
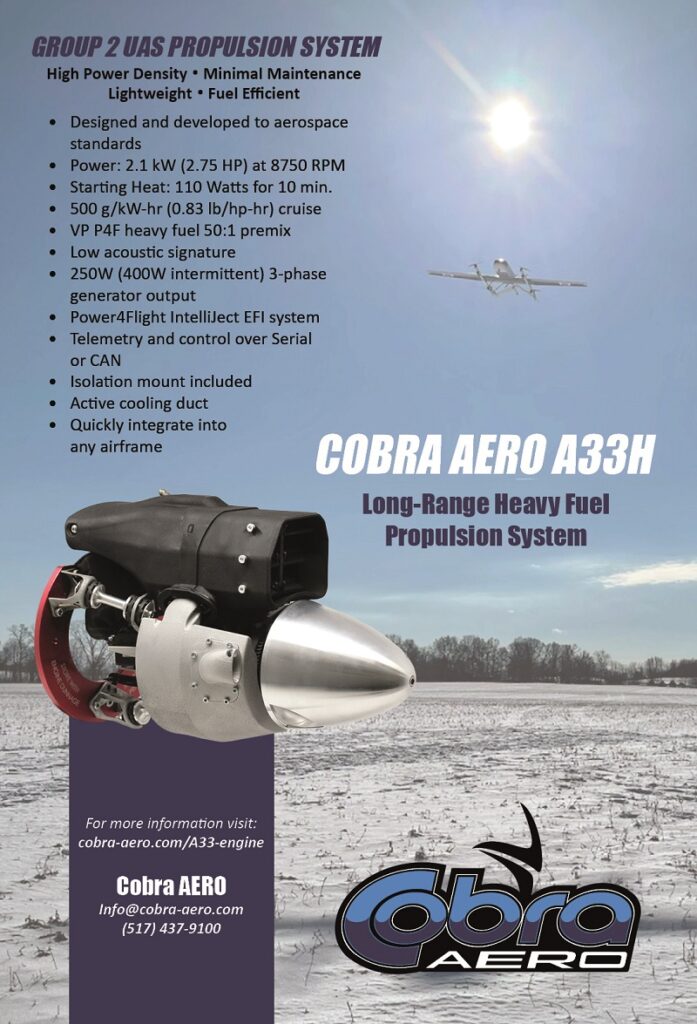
“Unlike traditional forklift-type assemblies, which require the cargo to be dropped off onto matting so that the forks can be removed from under the cargo pallet, the APL can be positioned next to a ramp or flat surface to automatically push the cargo onto the receiving surface or vehicle, reducing the time and effort required to load and unload it,” Gordon explains.
The APL is intended to be used autonomously in repetitive loading and unloading jobs, particularly in outdoor terrain or remote areas where manual work by people could be expensive or unsafe. Its autonomy is powered by Stratom’s Summit off-road software platform, which the company has developed to serve as a modularly configurable suite to enable straightforward autonomous operations across vehicle platforms from other OEMs.
Gordon adds that through Summit, Stratom is currently developing unique behaviours for the APL as well as integrating different sensors, cameras and other equipment to optimise its capabilities. In the long term, the APL will be updated with object detection capabilities for travelling across landing zones, between warehouses and across complex terrain.
Airports
Air freight and military logistics are of course not the only headache for workers and organisations. Commercial airliners often have to handle many tonnes’ worth of passenger luggage, all of which must be smoothly delivered between aircraft holds and airport terminals without damage or failure.
The routine and repetitive nature of commercial flight makes it ideal for the application of autonomous baggage handling systems. First, UGVs can be pre-programmed to travel in an automated fashion from their garages to planes on the ground, and then to baggage claim with a payload of luggage, before moving on to pick up luggage deposited in check-in zones for delivery to their planes before take-off.
On top of that, fusion of sensor data from real-time perception systems can ensure they intelligently avoid or navigate around obstacles such as shuttles, technicians or flocks of birds that can appear without prior warning.
Aurrigo International knows this only too well. Following its success in using autonomous shuttle buses to allow Covid-safe passenger transport at the 2020 ISPS Handa Wales Open golf tournament (UST 36, February/March 2021), it has gone on to develop other autonomous ground vehicle solutions, including two for airport loading and unloading.
Its Auto-Dolly and Auto-DollyTug use Lidar, cameras and GNSS to achieve full autonomy and prevent collisions when navigating through outdoor zones in airports as well as indoor areas such as warehouses and baggage loading or unloading ports.
The Auto-Dolly can carry up to 1.5 tons in a ULD (unit load device, an industry-standard luggage container) on its flatbed, while the Auto-DollyTug can carry up to 1.7 tons and tow up to four additional dollies, each loaded with a 1.5 ton ULD, giving a total carrying capacity of 7.7 tons.
The company began working with Changi Airport Group (CAG), in Singapore, in October 2022 to trial and jointly develop the UGVs to meet CAG’s aim of automating its baggage tractor operations, which had been suffering from labour shortages (a problem faced by airports worldwide).
In a notable contrast with other autonomous airport tractor solutions, the Auto-Dolly and Auto-DollyTug have been successfully used at Changi to unload their ULDs themselves onto their subsequent loading systems, known as Skyloaders. That has eliminated the need for intermediate machinery and workers typically used to move ULDs between baggage tractors and the Skyloaders.
Also, as both UGVs are fully battery-powered, they are viewed by CAG as ideal for its long-term goals regarding sustainable aviation.
CAG’s approval of these trials was such that in February 2023, it signed a deal with Aurrigo for continued joint development and testing of the UGVs as well as the company’s simulation software AutoSim, which allows the scheduling and planning of specific airport operations to be tested.
The trials so far have been carried out with safety operators present; the next stages are expected to be performed without them. Data and observations from these will be combined with the AutoSim 3D airport digital twin, to update and refine the operation of the Auto-Dolly and Auto-DollyTug for seamless crewed-uncrewed air hub tasks.
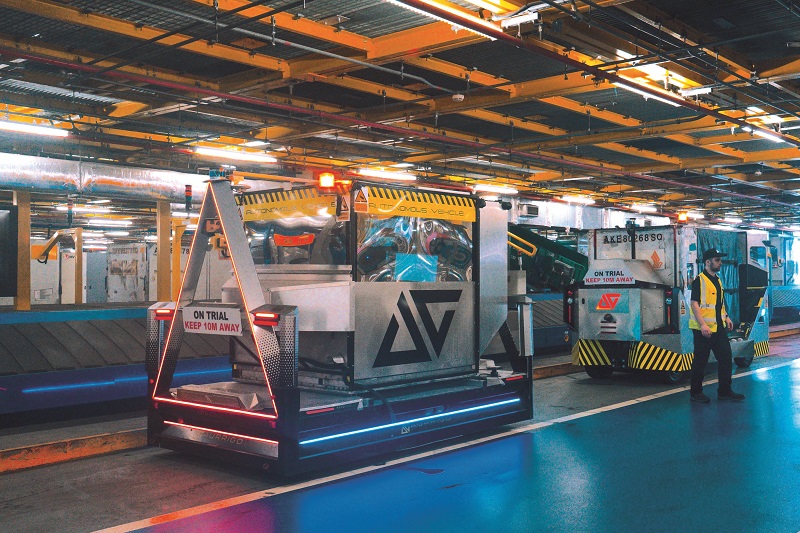
Sanitation
When considering particularly arduous or dirty jobs, cleaning work in various locations often springs to mind. For instance, industrial spaces such as warehouses and factories must constantly be kept spotless and free of any contaminants that could affect the products in them.
Meanwhile, civic spaces such as car parks need to be kept clean for the sake of pedestrians and customers, not to mention safety from potential accidents and injuries.
As well as cleaning floors, any debris also has to be removed, typically by ‘pre-sweeping’. Floors littered with wood scraps, leaves and so on can leave scratches or smears on the floors, making them hazardous for people or autonomous vehicles, be they logistics robots or parking valet UGVs such as the Stan from Stanley Robotics (UST 44, June/July 2022).
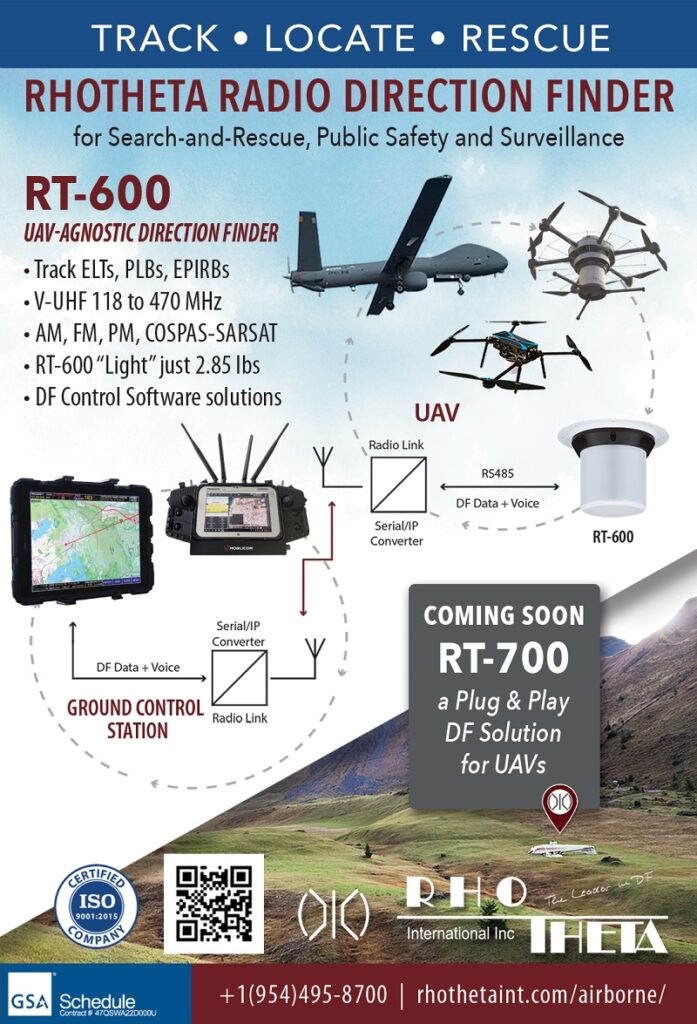
To that end, the R12 Rex CS (Cylindrical Scrubbing) UGV from LionsBot, which was unveiled in early 2023, is aimed at taking over these arduous jobs from labour-starved sectors, and shortening them by performing them simultaneously.
For pre-sweeping, the UGV features two cylindrical Nylon carbide-coated brushes, each one 77 cm in diameter, one positioned behind the other, mounted on the undercarriage to sweep debris from its path of travel. Also, each front corner has a conventional spinning broom-type brush that brings its total sweeping width to 127 cm.
Scrubbing is carried out by an onboard de-foaming and chemical dousing system whose chemicals are stored in 140 and 5 litre tanks respectively, and which are distributed behind the brushes after the appropriate mixing. A 95 cm-wide squeegee is mounted at the back for then scrubbing with the cleaning fluid, applying 95 kg of downward pressure for a thorough wipe – doing away with the ‘elbow grease’ gap that some potential customers have cited as a barrier to automating cleaning work.
The R12 Rex CS measures about 1715 x 938 x 1473 mm and weighs 748 kg when full of cleaning fluids or 585 kg when emptied for transport. It is powered by a 250 Ah battery and runs for up to 4.5 hours between charges, with 3.5 hours as an estimated minimum, its maximum cleaning speed being 5 kph.
Although a manual override is available, the UGV typically cleans and navigates autonomously, with onboard 3D SLAM powered by a Lidar with a 200 m range to enable real-time path planning, obstacle avoidance and localisation without needing GNSS (given its indoor operating environment).
As a further aid to autonomy, LionsBot can provide an automated battery charging and cleaning fluid refill station, with an automatic return function to enable the R12 to navigate to its station at the end of each cleaning cycle (with charging taking about 8 hours). Batteries can also be manually swapped via a tray at the base of the vehicle.
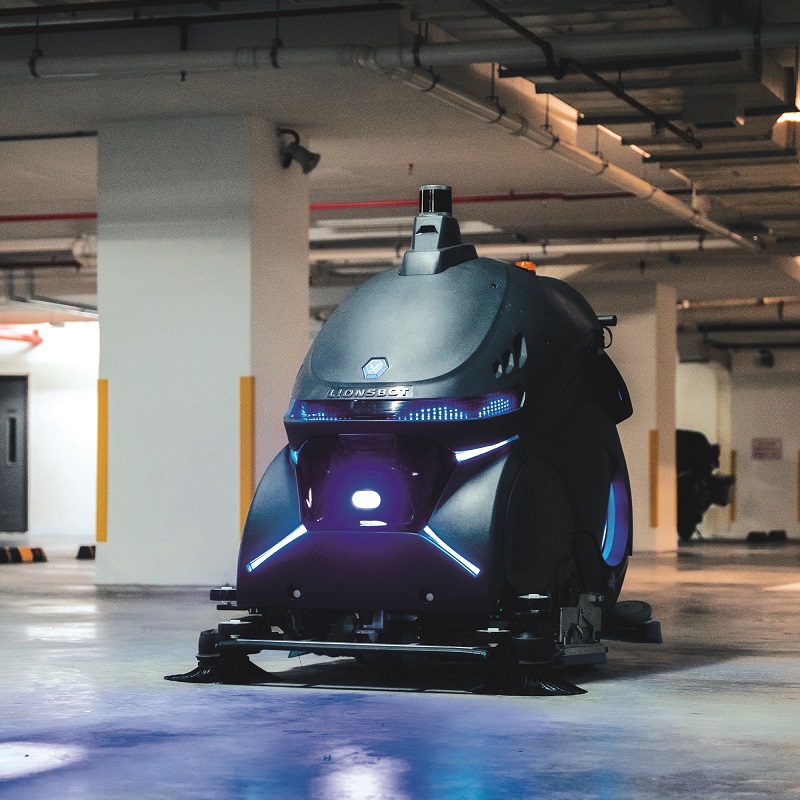
Security operations
Eurolink Systems has a history of developing and providing UGVs for security purposes, with its Leopardo wheeled and tracked UGVs having been supplied to the Italian army for counter-IED operations in Afghanistan about 8 years ago.
“Around 2014, the Italian military approached us quite unexpectedly with a list of capability requirements for a UGV,” says Pietro Lapiana, president of Eurolink Systems. “We were nonplussed but we agreed and began work from a blank sheet, and around 9 months later we delivered the first units.”
More recently, the company has begun delving into more advanced robotics, also for security users. Specifically, it has been supplying its Doberbot UGV to Italian private security forces to enhance their capabilities in a number of ways. To do so it has analysed police requirements and used the data from that to inform the development of its algorithms.
The Doberbot is a four-legged UGV incorporating 12 servo actuators to achieve locomotion, as well as two HD depth cameras for sensing and navigation, a Lidar for environmental mapping, and an Intel CPU as its main computer. The system is capable of operating at 5.4 kph and running at up to 7 kph, as well as walking up or down stairs and rubble.
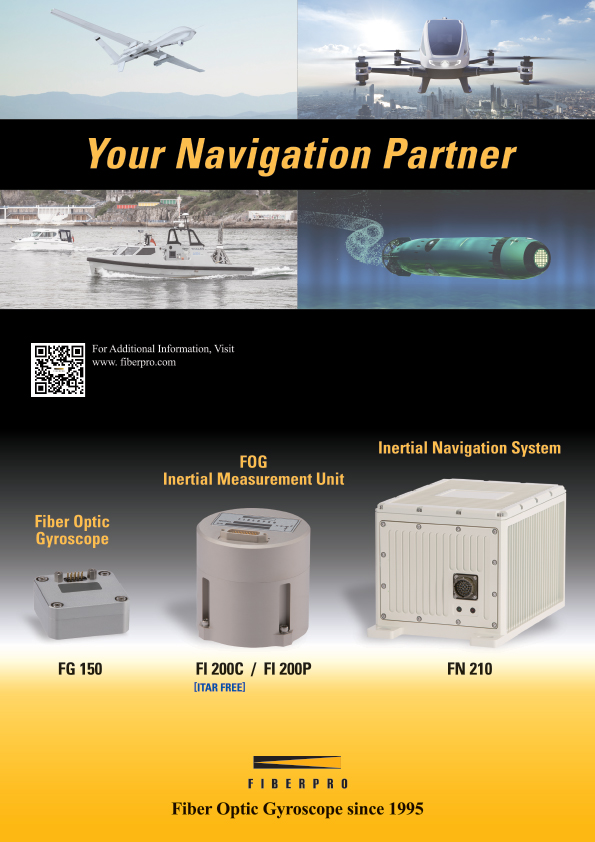
“Customers in Italy asked us to configure the Doberbot to act as a companion system to officers, principally out of a fear that if a police officer were to become embroiled in a fight with violent offenders and die, no-one would know, because no-one would see,” explains Lapiana.
“To that end, we engineered our computer vision algorithms for some abilities beyond just obstacle avoidance. It can now recognise things in the visual data that the Doberbot would capture, such as if there’s a gun, or if people are standing up or on the ground.
“And if firearms or potentially wounded people are identified, it can transmit an emergency alert to the police command & control centre, to notify them that an officer has a problem.”
The system can also be trained to recognise voice or hand commands for situations outside autonomous following, where operating a GCS is unsafe or cumbersome, and this can be paired with a facial recognition system to ensure the Doberbot obeys its ‘master’.
“For unsafe operations where a Doberbot might need to scout ahead intelligently through a building, we’ve also trained its computer vision to recognise doors and whether they are open or shut, as well as recognising when something has changed in a scene it has previously surveyed,” says Enrico Remiddi, Eurolink’s chief strategy officer.
“For example, if it revisits a room where there was a computer, and the computer has been removed, it will form a box around the space where it was to highlight it for operators and analysts watching its feed.”
Although the Doberbot is not a wholly original design – it uses an AlienGo quadrupedal robot from Unitree Robotics as its substrate – its AI algorithms have been largely replaced with Eurolink’s, with only the locomotion algorithms for the ESCs in the legs being retained.
That means its AI can also be migrated to other quadrupedal UGVs on request, such as Boston Dynamics’ Spot, Ghost Robotics’ Vision 60, or ANYbotics’ ANYmal (UST 40, October/November 2021).
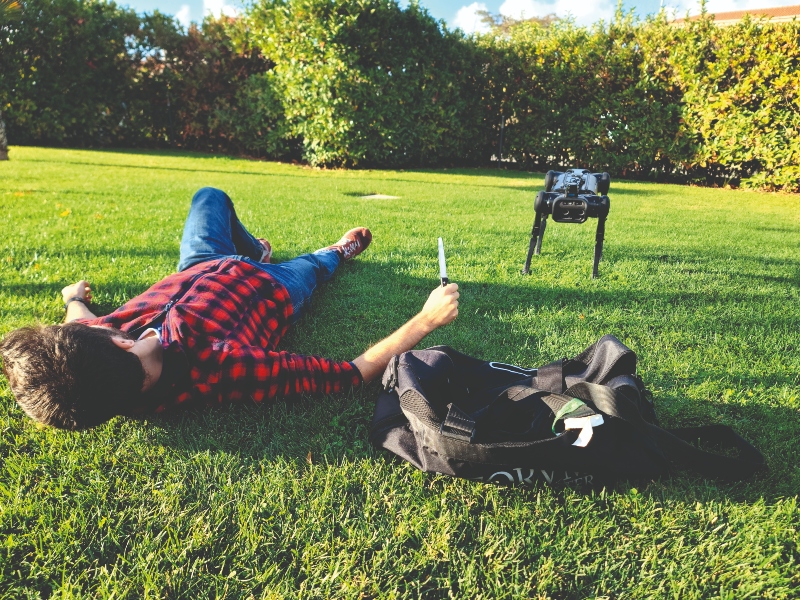
Firefighting
While none of the applications discussed so far are easy work, if removing people from dangerous jobs is the main motivator for UGV developers, then most new UGVs ought to be aimed at firefighting.
Being a firefighter remains one of the most hazardous occupations in the world. For example, one recent study found it to be the most dangerous job in the UK, with more than 47,000 injuries suffered by British firefighters from 2018 to 2023.
At the time of writing, the FFBOTS Industrial Robots Assembling Company in the UAE was the latest organisation to develop a UGV for mitigating the high rate of firefighter injuries and fatalities. Its FFB-FW8000 has a top-mounted extinguisher cannon that can be configured for spraying water at a nominal rate of 4800 or 7800 litres/minute, up to a peak of 8000 litres/minute.
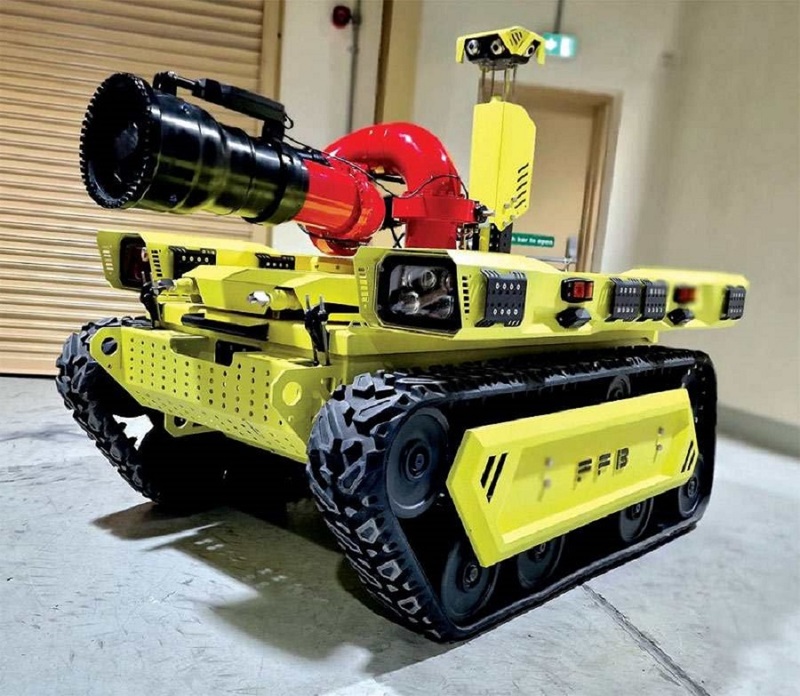
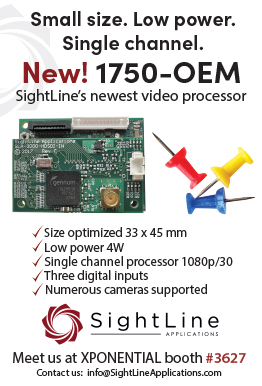
It has a total weight of 1000 kg and a payload capacity of 200 kg, along with four apertures for connecting water hoses at its rear. It has a top speed of 3 kph, torque being more important than speed, and can climb stairs at an incline of up to 30o. It operates on a pair of tracks powered by 3 kW motors.
Architecturally it bears similarities to firefighting UGVs such as the Tecdron TC800-FF (UST 26, June/July 2019) and the Thermite RS3 from Textron subsidiary Howe & Howe (UST 35, December 2020/January 2021). Like these vehicles, it has a largely metallic body for robustness against the harsh environments it needs to be used in, and features a winch on its lower front for added utility.
The company advises using the FFB-FW8000 in a range of particularly dangerous scenarios such as ammunition store explosions, nuclear reactor fires, and burning buildings which are close to collapse.
Accordingly, the range of its control and telemetry link is 1000 m, and for situations where human firefighters are normally limited to spraying water from a distance, it can go in, deliver close-up, real-time intelligence via a 360o visual array of six cameras around its body, and try to extinguish the flames directly at their source.
At the moment, the FFB-FW8000 is designed and built in Dubai, although the company plans to open a second location in Saudi Arabia.
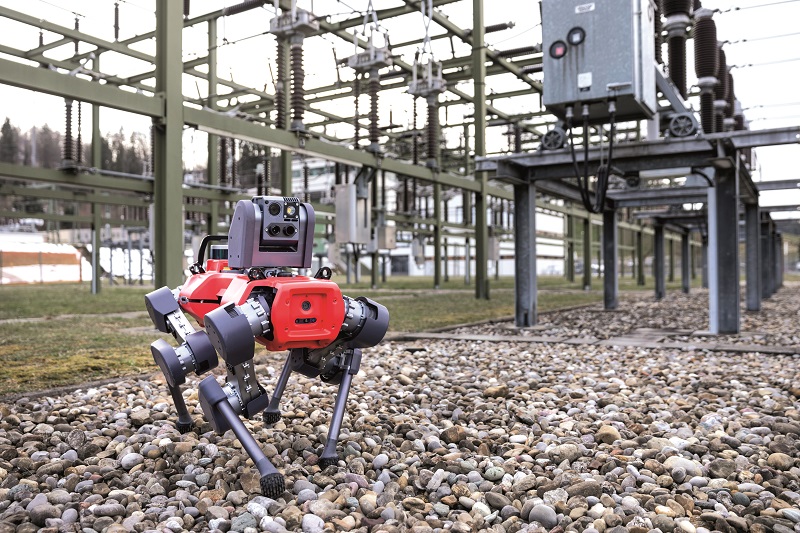
Industrial inspection
Returning to the ANYmal from ANYbotics mentioned above, this four-legged UGV is capable of walking through hallways and up and down stairs as any human inspector would, while carrying out the visual, audio and thermal inspections of machines, cables and tanks that form the more onerous and repetitive as well as less valuable parts of an inspector’s routine.
Although a lot of ANYbot’s work to date has been for oil & gas companies such as Petronas, its latest customer, RTE, is a fellow European entity. RTE is responsible for the operation, maintenance and development of France’s electricity transmission systems, and is therefore responsible for assets that include 105,000 km of power lines – the largest single transmission system in Europe.
The ANYmal was deployed at three replica installations at Campus Transfo, RTE’s technological and industrial laboratory, to gauge its mobility, navigation and data-collection capabilities.
The ANYmal’s 3D SLAM enabled it to navigate through established facilities, so no structural changes were required for it to start carrying out simulated inspections.
Thermal surveys of electrical shelves and visual sweeps of liquid levels, gauges and levers were performed, with the UGV’s auto diagnostics analysing data in real time for any irregularities that would warrant preventative maintenance.
A range of indoor and outdoor deployments were performed during the trials. Each mission lasted about 20 minutes and included up to 35 points of inspection, as well as numerous en-route tests of autonomous functions including obstacle avoidance, operating in the dark, and conditions where water was being sprayed.
Having judged the trials a success, RTE now intends to investigate how well the ANYmal carries out autonomous inspections in its electric substations in urban and offshore environments, as well as in its high-voltage DC power substations.
Conclusion
The growing competencies in optimising UGVs and their supporting technologies for unsafe and challenging applications are likely to open up new applications for autonomy across heavy-duty missions.
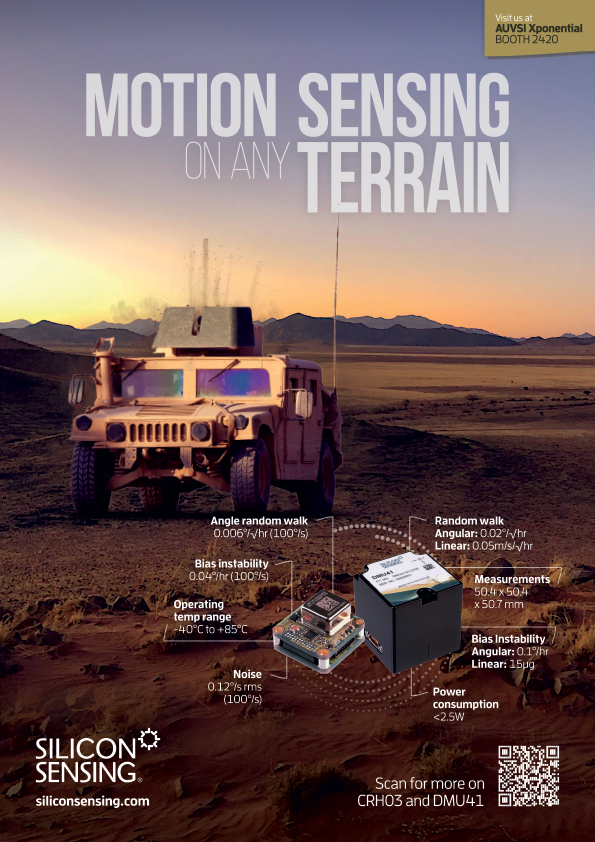
Just as we have recently begun to see many uncrewed systems weighing many tonnes each, the decade ahead might lead to evolutions that result in competing autonomous fire trucks, mining haul trucks, battle tanks and bulldozers.
In addition, the ongoing successes of the Doberbots, ANYmals and other four-legged UGVs could drive demand for even more dexterous solutions. Given that theoretically nothing ought to be a better substitute for people, it might however not be long before bipedal, humanoid robots become a sought-after solution in hands-on civilian and military tasks where humans might otherwise have been irreplaceable.
UPCOMING EVENTS
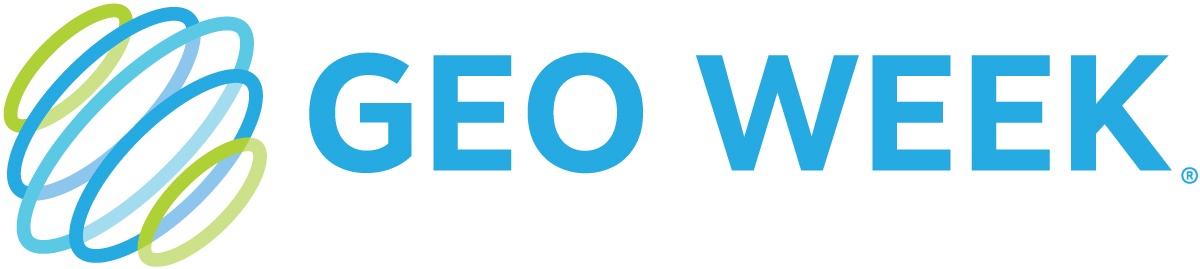
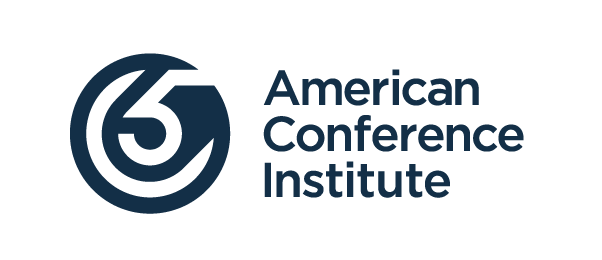
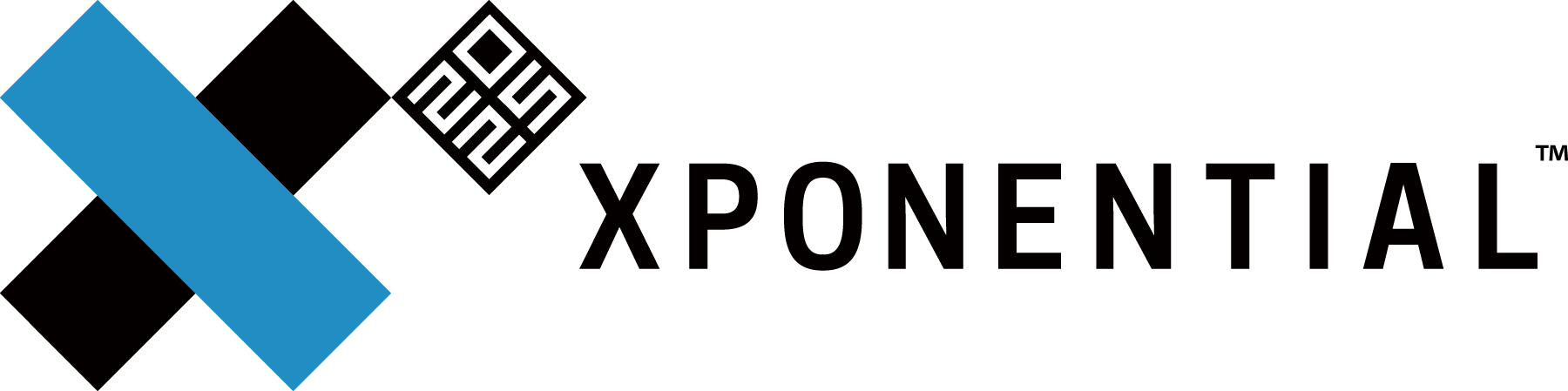
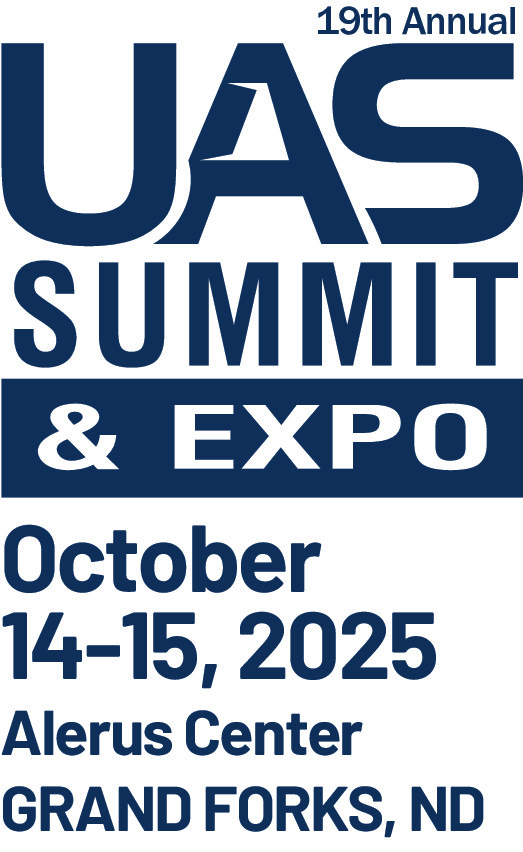
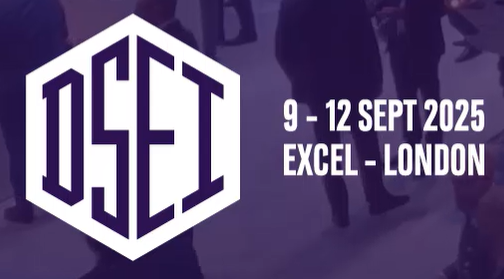
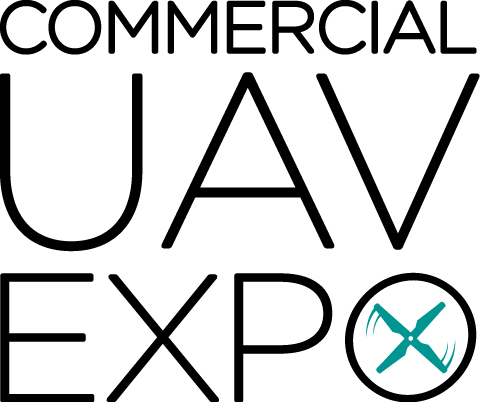
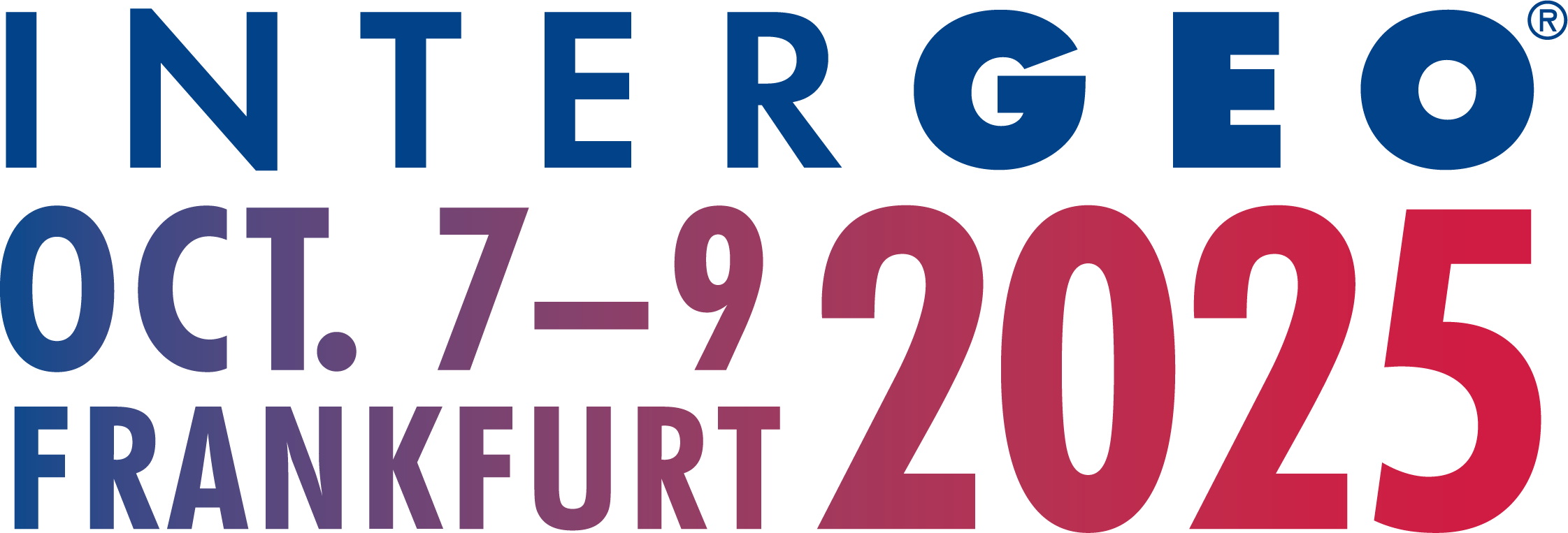
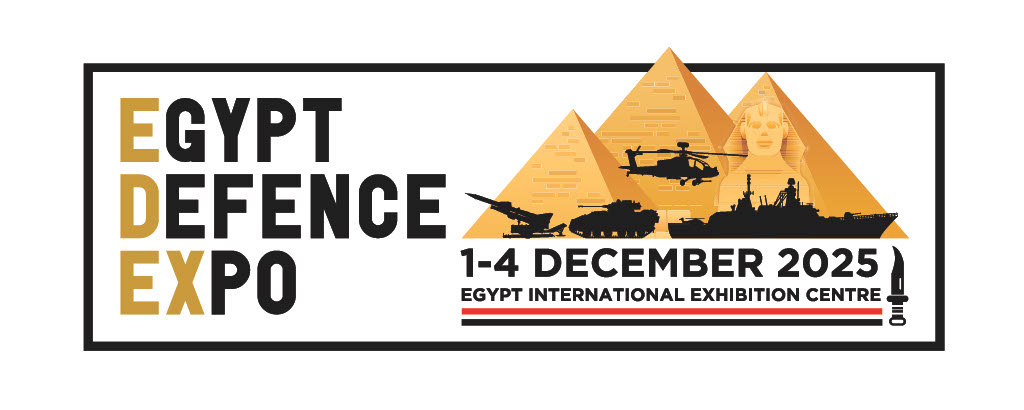
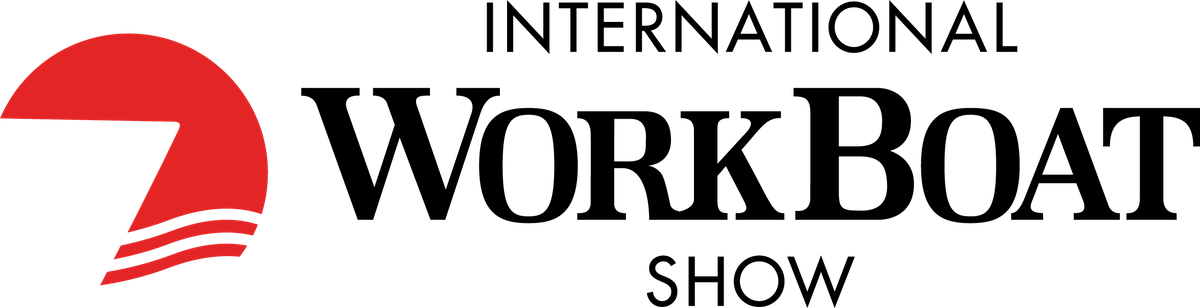
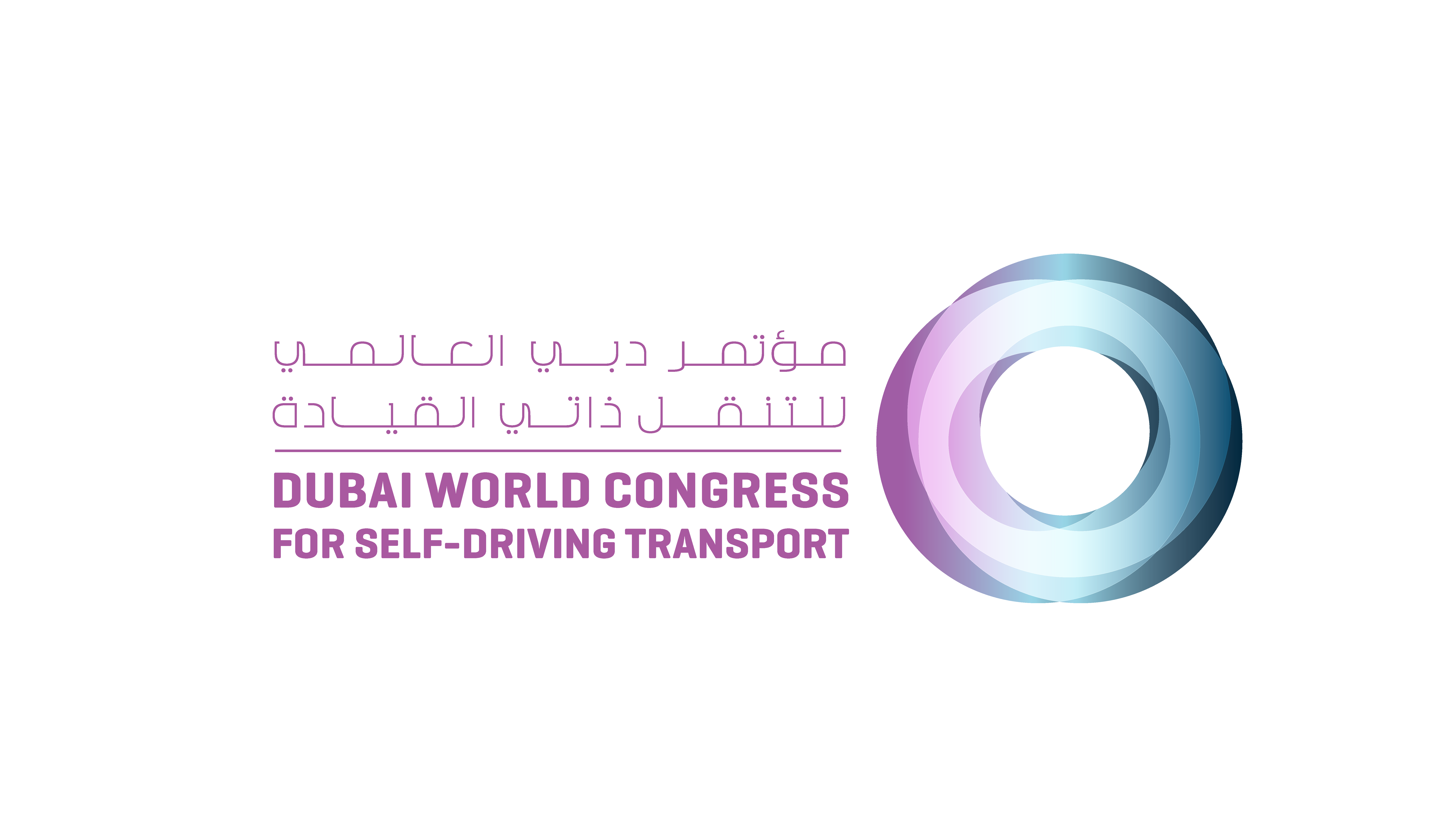
