IDV Robotics Viking UGV
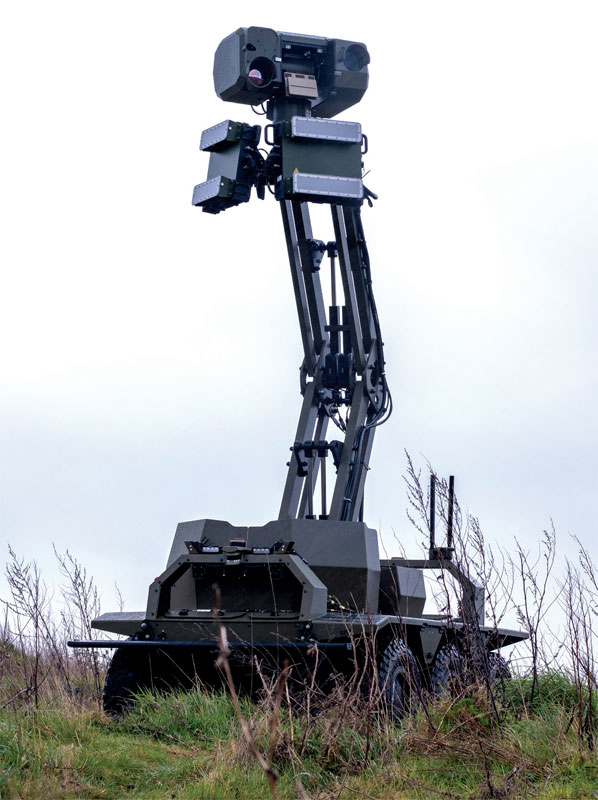
Rory Jackson finds out what the UK’s sole domestic supplier of military UGV tech is working on
IDV Robotics (IDV-R) is a company at the veritable heart of the UK’s UGV development pipeline for defence applications. Formerly part of Horiba MIRA (a UK-based automotive engineering, test and development consultancy), IDV-R has been innovating UGV technologies for over 15 years, much of which has involved working with the UK MoD in pursuit of robust UGV operations in harsh environments. Today, under new ownership with Iveco Defence Vehicles (IDV), the company is expanding its reach into Europe and beyond.
It was in 2008 that the organisation first stepped onto the stage of uncrewed systems by entering a UK MoD grand challenge with a prototype robotic platform on an autonomous mapping and threat-detection course at Copehill Down, the MoD’s urban warfare training facility.
Inspired by successes there, the team’s ongoing development culminated in the Viking, an all-terrain, multirole, six-wheeled diesel-electric hybrid UGV.
“Armies around the world increasingly want first enemy contact to be with a robot, rather than a soldier, or they need machines to perform mission-critical tasks in contested environments,” says Dr Geoff Davis, managing director of IDV-R.
To tackle such evolving tasks and environments, Viking is built for a variety of defence applications, including ISTAR, casualty evacuation (CASEVAC), logistics resupply, CRBNE (chemical, biological, radiological, nuclear and explosive) reconnaissance and survey, and remote weapon-station combat roles.
As an offroad military UGV, the Viking has a gross vehicle weight of 2 t, measures 3 m x 1.8 m x 0.9 m, and can carry up to 750 kg of payload mass (with a payload mounting area of 2.2 m x 1.8 m available atop the vehicle). While this vehicle originated under Horiba MIRA, the technology and team behind it was recently acquired by IDV, based in Bolzano, Italy; now IDV-R, it continues to develop and manufacture the Viking UGV and uncrewed technologies in the UK.
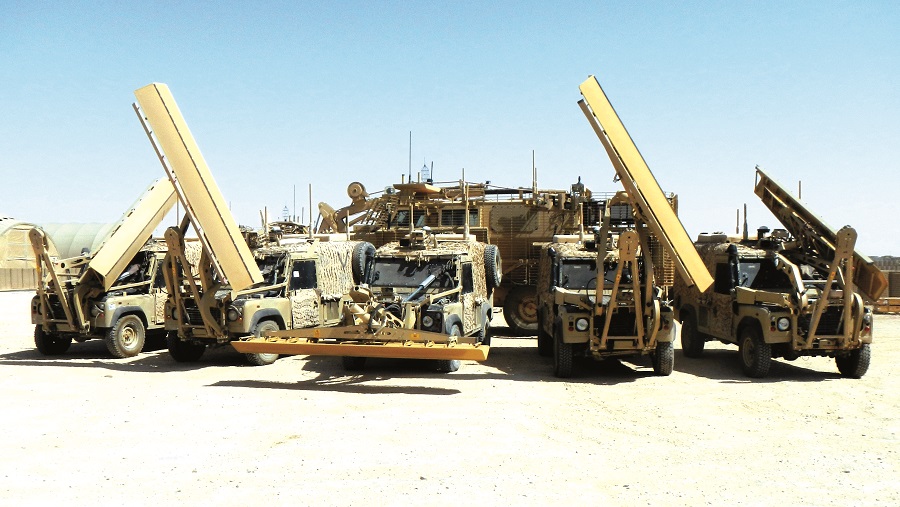
Viking ancestry
The first real-world application of the team’s UGV engineering was as a convoy protection system in Afghanistan, where the constant threat of roadside bombs and improvised explosive devices (IEDs) merited an uncrewed autonomous vehicle that could detect explosive threats ahead of convoys, which would be dealt with by explosive ordnance disposal (EOD) personnel and machinery in the convoy.
The system, known as PANAMA, was based on converting Snatch Land Rovers into autonomous systems, removing their seats and steering wheels (to remove the temptation to drive them), and adding an autonomy kit, ground-penetrating radar, cameras and other sensors.
Around 20 units were built, delivered and supported by the team, and served the British Army in Afghanistan from 2011 to 2015, with plans to make them a core capability after the conflict.
“But it was decided instead that after the withdrawal, UK forces did not plan to return to that kind of IED-rich environment, so that system went on the backburner,” says Andrew Maloney, head of technology and chief engineer at IDV-Robotics.
“We came out of that campaign with a great deal of field-proven UGV engineering know-how and were looking for ways to apply it. At that time, computer vision and other AI-based technologies were becoming available that we hadn’t had access to before, so that’s really when development of Viking started.”
Per its predecessor, the Viking was developed as a highly desert-capable system, meaning its developers wanted it to be able to climb steep sand dunes with a large and heavy payload. This drove them to design it as a 6×6 vehicle, with low ground pressure, and equip it with a high-performance, high-voltage, hybrid powertrain, enabling it to take soft sand slopes with a 60% gradient (or ‘grade’ in American English), equivalent to an approximately 31° angle, and achieve speeds of up to 45 kph.
“The high-voltage powertrain was chosen to maximise its efficiency, and reduce losses due to high current in the wiring, especially in high power manoeuvres; something like a low voltage 48 V system could be dissipating hundreds of watts in the wiring when delivering high torque,” Maloney notes.
To aid efficiency, IDV-R equipped Viking with several thermal conditioning systems, particularly for cooling the battery in hot desert environments or heating it in cold places. The MIRA Technology Park in Nuneaton provided key testing facilities to iterate and validate thermal performance, including climatic chambers with dynamometers for cycling the powertrain in very cold or hot climates, including simulating environments with over 50 C ambient heat and intense solar loading on the UGV body panels.
The advent of an autonomous last-mile resupply programme from the UK MoD soon drove the team to begin developing offroad autonomy technologies, including advanced terrain perception and ATLAS, its GNSS-denied navigation solution, as a means towards guidance and localisation via a combination of perception sensors, AI and embedded maps.
“We decided to install our new autonomy technologies and ATLAS first on the Viking, and trial it with DSTL [Defence Science and Technology Laboratory] on Salisbury Plain during the Army Warfighting Experiment 2018, which saw it successfully resupply troops across the range of scenarios that DSTL designed for the programme,” Davis says.
Since then, IDV-R has gone on to participate in numerous national and joint defence programmes on autonomous resupply, CASEVAC and other applications, with Vikings being controlled in groups alongside other uncrewed systems, and through those it has continued optimising them in the UK and in overseas trials – along with its navigation, computer and powertrain systems – to date.
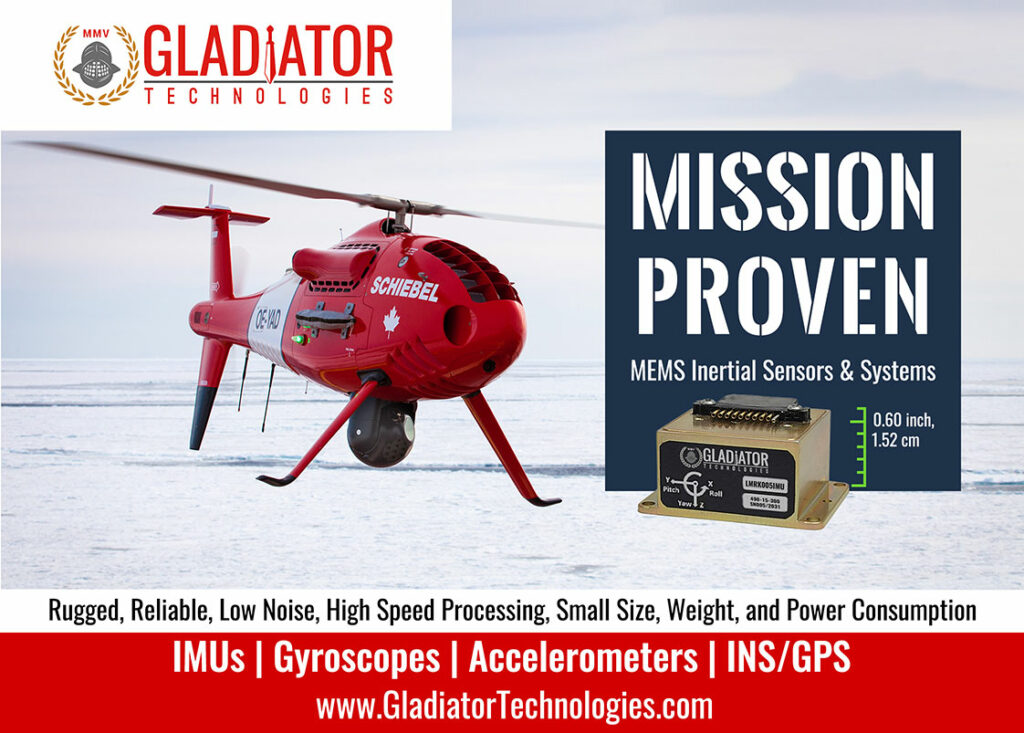
Modular architecture
As a multirole defence UGV, modularity is inherent to the Viking’s subsystem layout: payload, sensor and comms integrations may change between missions, and maximising payload area and capacity were key targets from its earliest, blank-sheet design stages. Standard military power and data interfaces are also installed to aid this, and the control software is programmed to ‘discover’ payloads as they are integrated, and open new pages in the GCS accordingly to manage those payloads once fitted.
“Those could be CBRN, ISTAR or other payloads, and we’ve also targeted a payload swapping time of less than one hour with the open payload bed, as customers are envisaging buying one family of UGVs and rerolling their platforms as requirements change in the field,” Davis says.
Viking’s systems mount on a tubular-frame chassis, designed by IDV-R and manufactured by Safety Devices, a nearby specialist in chassis and roll cages. This allows different body panels to be mounted, as defence organisations vary as to how much armour they want on their UGVs. Those prioritising weight savings can opt for aluminium body panels, and those wanting more protection can cycle up through the established classes of armoured vehicle protections for their desired types and thicknesses of body material.
Davis continues: “The vehicle is low-profile, at 0.9 m height to the payload bed, so it’s hard to spot, compared to most vehicles. Combine that with its ability to run silently on electric power and to navigate without Lidar – or anything else actively sending out signals – and it’s stealthy enough that you don’t always need to protect it.
“But if it’s going to be used for critical intelligence or ordnance, you don’t want it to be taken out, so allocating some of the 750 kg payload capacity to armour can be a good idea sometimes.”
The UGV is assembled in-house at IDV-R’s workshop in Nuneaton, where the company can manufacture some tens of units per year, although an industrialisation process is underway (with considerable practical expertise on the matter coming from the new parent company, IDV) to make the Viking faster and less costly to produce.
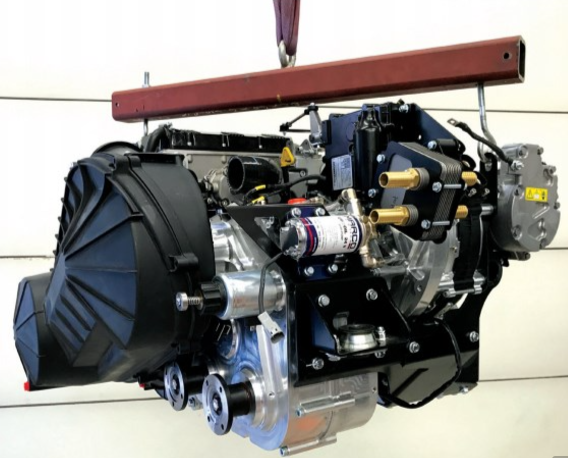
Hybrid 6×6 powertrain
The Viking’s engineers wanted a vehicle with high mobility without resorting to tracks, as that would have reduced reliability, maintainability, and the speed of on- and off-road operations. This was a critical factor in choosing the six-wheel configuration, as was a shared desire for maximum gap crossing and soft ground capabilities.
“Six-wheel-drive means very low ground pressure, and with the right power-to-weight ratio, enables climbing sand dunes,” Maloney says. “We’ve also chosen an independent, double wishbone suspension with dual-rate coil springs around adjustable dampers – both for mobility and to not shake payloads to pieces when we’re crossing very rough terrain. If something like a CBRN payload or remote weapons station fails when you need it, because it has suffered too much shock and vibration, it can be catastrophic.”
The platform is designed with Ackermann steering, as IDV-R finds that skid-steering, the more popular choice among similar-sized defence UGVs, often results in excessive friction on tarmac or other grippy surfaces. When 750-1000 kg payloads are added atop the mix, problems such as tracks coming off or burst tyres can ensue.
“For added manoeuvrability, we’ve got four-wheel steer, which we switch to at 20 kph for tighter turning radii, with the Ackermann two-wheel steering at higher speeds, so it’s not too twitchy,” Maloney says.
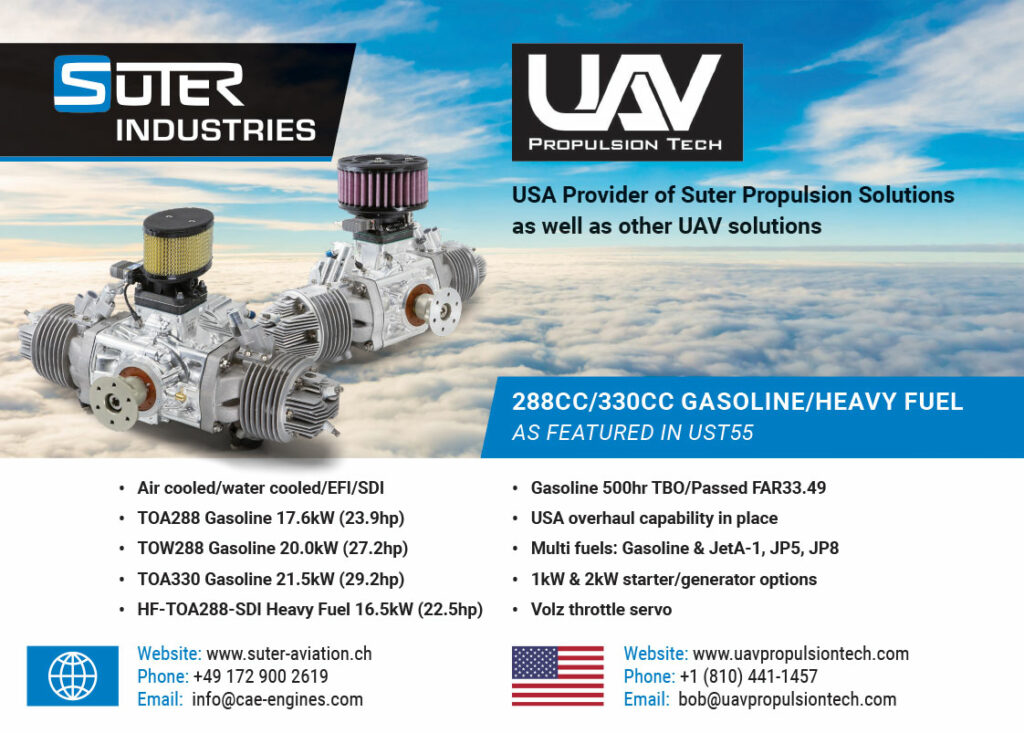
The four-wheel steer mode’s turning circle is 7 m kerb to kerb, while the two-wheel steer’s is 12 m. The parallel-hybrid powertrain occupies most of the space inside the chassis, with a 20 kW Kohler diesel engine at the back, a 120 kW Yasa axial-flux, electric-motor generator mounted forward of the engine via a transfer gearbox, and a 400 V battery pack at the front, which is designed and assembled in-house.
By making the pack in-house, IDV-R can select different cells for different advantages. Nickel manganese cobalt chemistry cells are often chosen where energy density is prioritised, while lithium-titanate oxide cells are increasingly picked when safety takes precedence, including situations where the UGV’s battery must be trusted to sit safely after rough treatment (that is, with minimal chance of combustion).
The system can run for just over 20 km on battery power alone, with 250 km endurance in hybrid mode when accounting for the current diesel fuel tank.
Having a parallel-hybrid configuration allows the Viking to run in all-electric mode for stealth, in diesel-and-electric hybrid mode for maximum range, or a series-style charging mode for energy and range security. Power can also be run offboard, using the Viking as a generator for powering or recharging soldiers’ equipment and other devices.
“The diesel engine and electric motor connect via a custom transfer box from Compact Orbital Gears in Wales,” Maloney says. “The high-performance, axial-flux motor is especially useful for getting a lot of power either into the battery or into the wheels. Yasa’s technology packs a lot of power and torque into a very small form factor, and uses a very unique oil-cooling system to achieve that. Since we have been using them, they’ve been bought by Mercedes because of their leading design.”
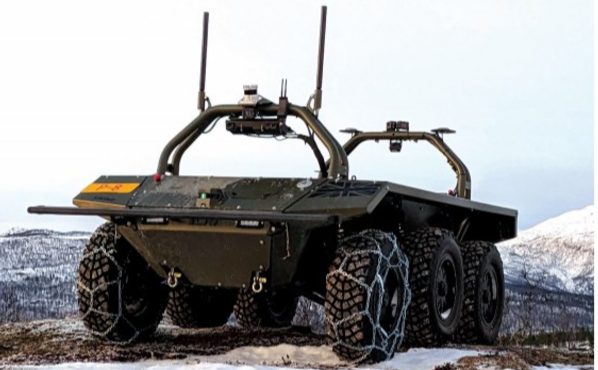
Cooling
As the Viking is designed to operate in not only hot desert environments, but also in cold tundra or Arctic conditions (a couple of units having been recently supplied to the Norwegian Defence Research Establishment), engineering a thermal management system that was capable of thoroughly cooling or heating the temperature-sensitive lithium-ion battery pack was critical. Managing the battery temperature helps to get the best performance from it.
“At the back of the vehicle we have a cooling pack with a high-temperature radiator for the diesel engine and a low-temperature radiator for the autonomy electronics, battery pack, inverter and motor. We also integrate chillers and heaters into the liquid cooling loop, depending on the customer’s environment, to manage the battery via refrigerating or warming the water-glycol coolant,” Maloney says.
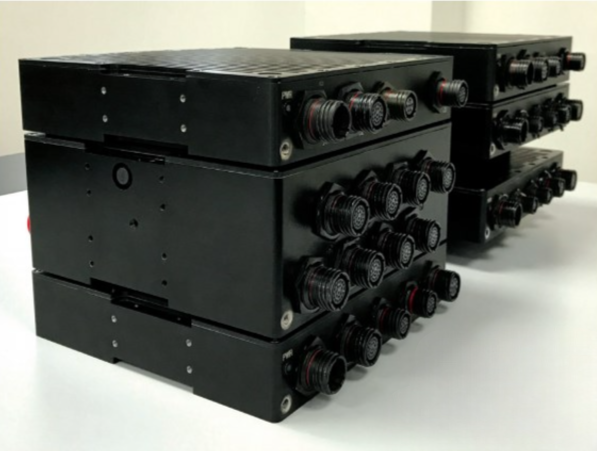
Autonomy sensors
While the Viking can be remotely controlled and teleoperated (the former mode intended for when the UGV is in close line-of-sight and the latter adding a low-latency video feed for a GCS operator to see where they are going), full autonomy has been developed since the early days of the project.
“Autonomy for us includes modes for following routes, and for intelligently following a person or a vehicle, like in a convoy, as well as a mode for searching or mapping independently across routes and areas,” Davis says.
To execute each of these modes, the Viking integrates a central stereo camera at the front for 3D perception ahead of the UGV, as well as Lidar mounted similarly at the front. Lidar is an active system and can risk giving away the Viking’s position in some situations, but it has advantages in range, accuracy at range and night-time functionality over stereo vision that make it valuable.
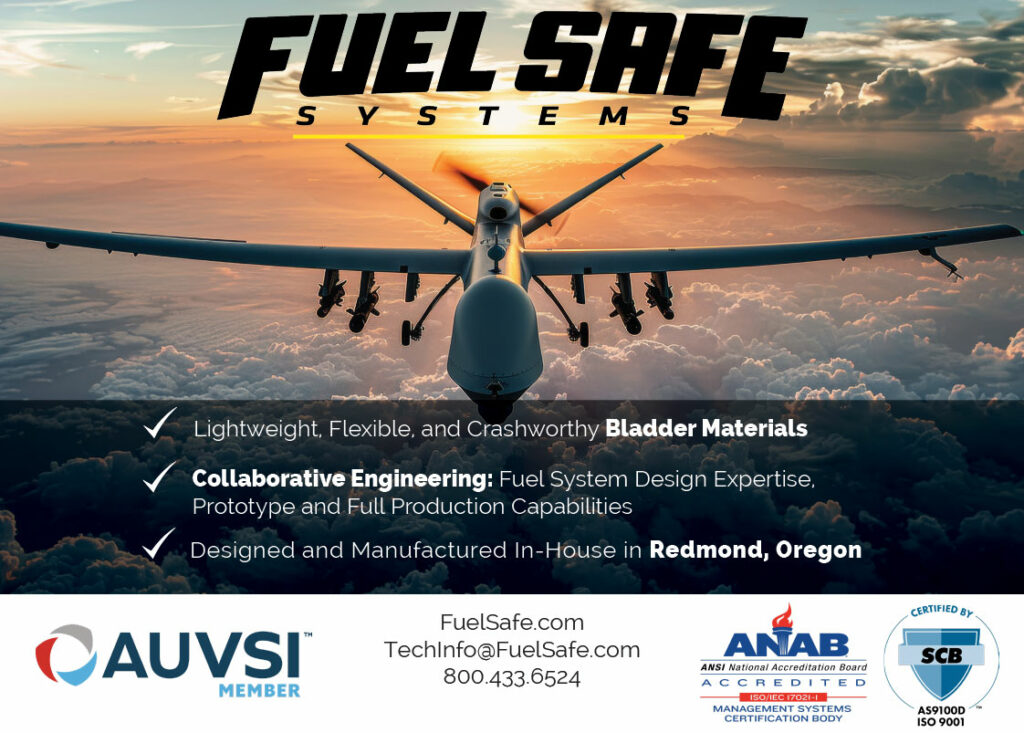
“And then we have a range of different perception cameras we can install, including EO daylight cameras, thermal cameras, and additional stereo cameras or Lidars for the level of situational awareness the mission requires, and its budget and performance targets,” Maloney says.
“Wherever possible, we have gone for sensors with the maximum field of view, resolution and update rates we could find, but there’s rarely hard performance requirements from the customer on those. It is currently dictated by autonomy performance requirements and cost.”
IDV-R can install different grades of IMU and GNSS receiver, including when end-users want a civil receiver or full military GNSS capability.
Around the centre of the vehicle sits the modular autonomous control equipment (MACE), including the main autonomy computer, which IDV-R has designed and engineered in-house to meet military standards on ruggedness and power conditioning. MACE can be configured in various form factors for each vehicle integration, but is likely to be standardised in future with a two-box configuration, with one computer executing basic functions and the other carrying out more complex, autonomy related processing.
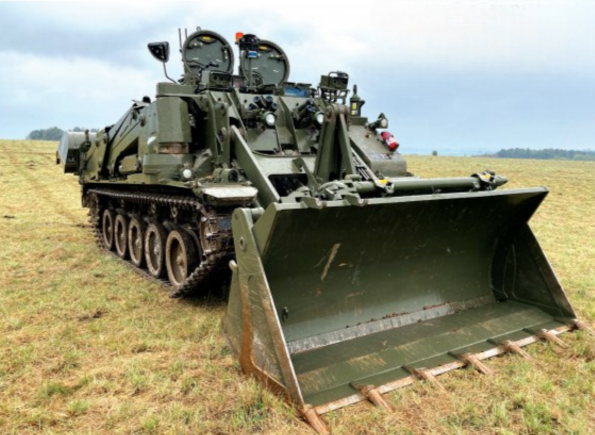
Passive GNSS-denied navigation
Each of the sensors discussed also plays a part in IDV-R’s ATLAS system for GNSS-denied navigation. The frequent problem of trees and buildings near the UGV hampering its satellite reception from GNSS constellations, combined with the ever-increasing threat of electronic warfare, jamming and spoofing, motivated the creation of ATLAS.
“We decided in 2016 that we ought to try using computer vision on the UGV to observe landmarks and compare them with an onboard map database to get our solution,” Maloney says. “We started using a probabilistic filter to try and match up landmark observations with the map database to figure out where the UGV was, to navigate just like a soldier would.”
The team won funding from the UK Defence and Security Accelerator to pursue a proof-of-concept, and it so happened that the first generations of NVidia Jetson embedded-AI computers were being released. These provided the ideal computing power and architecture for training Viking to recognise landmarks using a neural network.
ATLAS has since progressed through several phases and trials with the UK MoD and British Army. Last year, it was tested on the Cultana range in the Australian outback, with Viking under real GNSS jamming conditions as part of the Aukus Trusted Operation of Robotic Vehicles in Contested Environments programme.
“For training the neural networks, we do image gathering and annotation twice: the first round is done from above, using aerial or satellite systems to collect imagery, in which we label anything that could be used as a landmark and train the networks. Once the aerial network is trained, we can run it across new aerial imagery, creating a map database that Viking can leverage. We also vectorise it and make it semantic, so it’s small and efficient for fitting onboard the vehicle’s data storage,” Maloney says.
IDV-R also supplies map tools, so that when customers go somewhere new, they can source their own imagery and create the map databases for ATLAS and strategic route planning.
“Then, the UGV observes landmarks in the field, and uses AI to classify anything it sees that qualifies as a landmark; for example, the edge of a track, a road, tree or building. It can then compare the range and bearing to those with the map database’s spatial information. With a good few landmarks around, the system can localise itself with accuracy approaching 10 cm, which is good enough for autonomous guidance,” Maloney adds.
During movement, the UGV continuously performs visual measurements with the stereo camera (and Lidar if the situation allows), using that data to update the particles of its probabilistic filter and localise itself, combining that localisation analysis with attitude and heading information from its IMU and odometry, resulting in a probability distribution of where the UGV thinks it is.
“We also use AI for real-time terrain perception, looking ahead and recognising optimal routes for getting between waypoints; for instance, having the AI decide where it’s best to drive, and avoiding obstacles within constraints around a planned route from the user or global/strategic planner,” Maloney says.
“The mission itself, global or strategic route, is usually planned by an operator using our Base Station software. The map database we use can currently be used to generate routes to an objective. The operator can set waypoints and a range of preferences, and the algorithms will work out a route.”
The map data and control software are installed on standard SSDs for secure storage against shock and vibration, with some work having gone into cybersecurity and remote purging for military users who want to keep their tech out of hostile hands.
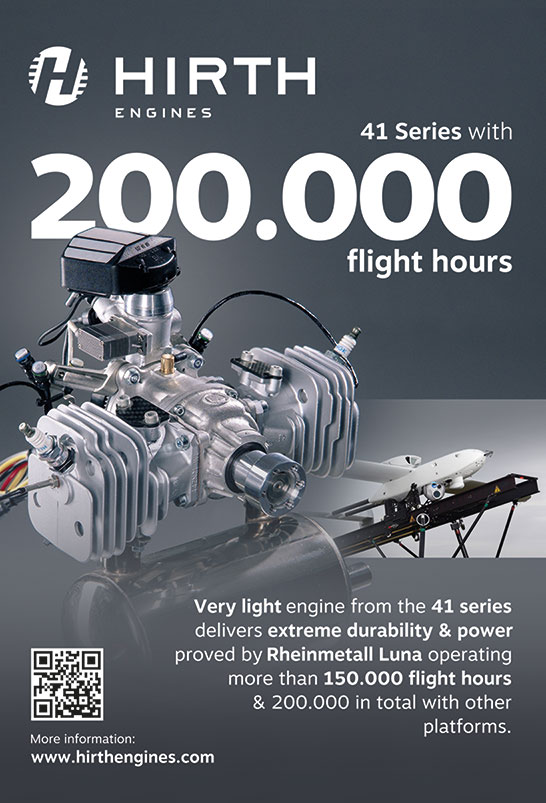
Communication systems
Through ATLAS and its autonomy software, Viking is designed with the potential to navigate and complete missions without any communication from its operator – important for operations in contested environments. The system is largely agnostic to communication systems, typically integrating IP mesh radios, and either recommending or fitting in with any system already in use with the defence users.
Maloney points to Domo Tactical Communications’ software-defined radios, Persistent Systems’ MPU-5, and Silvus Technologies’ StreamCaster MIMO radios as being frequently chosen for use with the Viking. “Given that we’re going to be integrating into a customer’s network of crewed and uncrewed nodes, we need to be agnostic to use whatever they prefer. You can even replace the comms link with an Ethernet cable for interfacing with Viking over a wired link and it will work.”
The IDV-R portfolio
Most of the systems discussed on Viking can also be installed to convert crewed vehicles into autonomous ones. These have included very large defence systems, such as Mastiff protected patrol vehicles, and infantry fighting vehicles for uncrewed operations and crewed/uncrewed teams. The Terrier Combat Engineering Vehicle and a tracked loader have also been converted for autonomous obstacle construction and obstacle clearance in support of infantry and mechanised brigades.
“The Terrier weighs about 40 t, and it’s the UK MoD’s only in-service, drive-by-wire, heavy tracked platform, so the concept came from Army HQ that we might convert it easily, relative to non-by-wire platforms, during a two-year programme. We put MACE, ATLAS and some other systems on it, and five two-week blocks of integration trials and improvements followed, resulting in it driving autonomously using just computer vision and AI,” Maloney recounts.
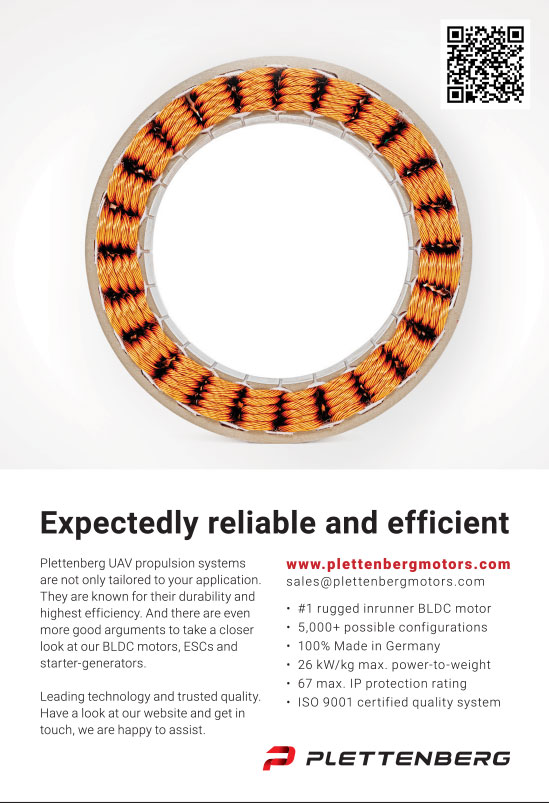
“We’ve also used our simulation systems for training the AI for autonomous ISTAR in MUM-T [Manned-Unmanned Teaming] trials. The UGV with ISTAR payload would detect and recognise tanks, despite never actually having seen real tanks before. The ability to use computer-generated and automatically labelled images to train neural networks is improving all the time, as imagery from simulation engines becomes more realistic.”
Recently working with DSTL in the UK, Viking was converted to perform autonomous CBRN reconnaissance to find safe routes through contaminated areas, and CBRN surveys to accurately delineate the geographical extent and severity of CBRN threats across an area. This required IDV-R to develop a new payload with mass spectrometers, nuclear spectrometers and other sensors, tied together with software supporting new autonomous behaviours, and interfacing with MACE and ATLAS.
With all these capabilities in hand, one can expect to see Vikings continue to travel far and wide the world over.
Specifications
- Viking UGV
- 6×6 wheels
- Diesel-electric, parallel hybrid
- Dimensions: 3 m x 1.8 m x 0.9 m
- Gross vehicle weight: 2 t
- Payload capacity: 750 kg
- Payload area: 2.2 m x 1.8 m
- Maximum power output: 140 kW (187 hp)
- Maximum speed: 45 kph
- Maximum range: 250 km
- Maximum range (electric only): 20 km
- Maximum gradient: 60%
Some key suppliers:
- Chassis: Safety Devices
- Autonomy computer: NVidia
- Diesel engine: Kohler Engines
- Transfer box: Compact Orbital Gears
- Electric motor: YASA
- Wiring harnesses: Rockford
- Data links: Domo Tactical Communications
- Data links: Persistent Systems
- Data links: Silvus Technologies
UPCOMING EVENTS
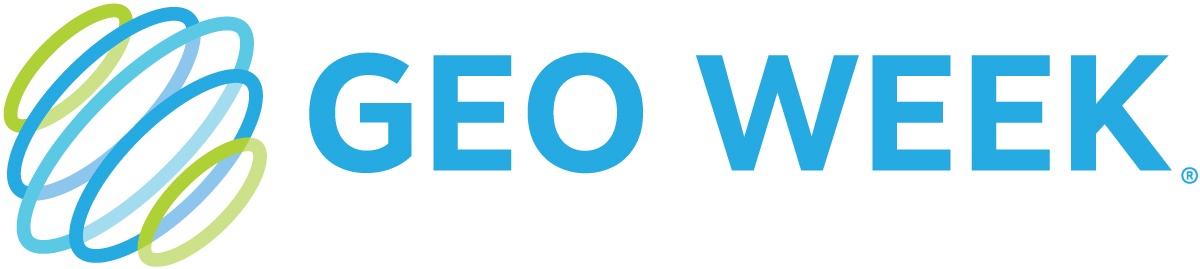
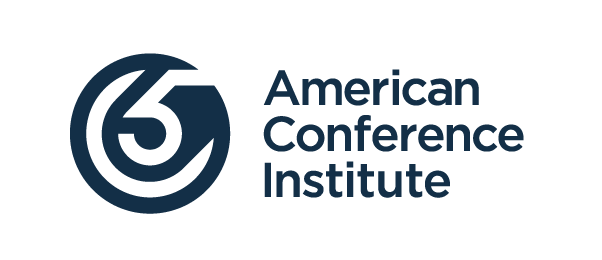
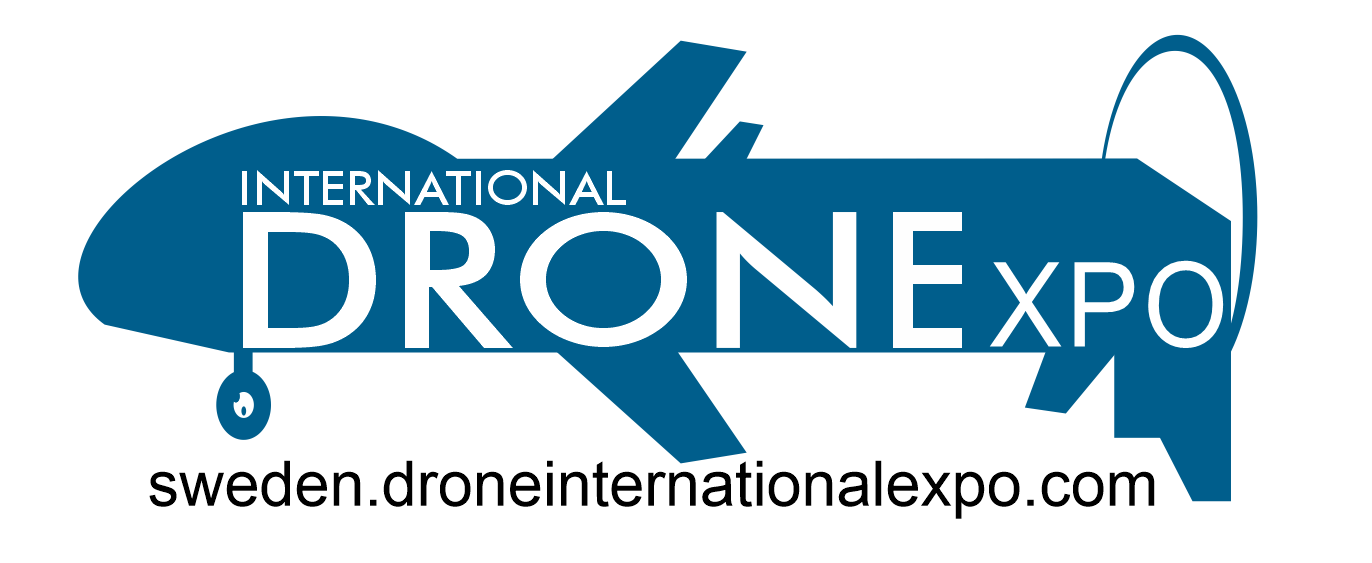
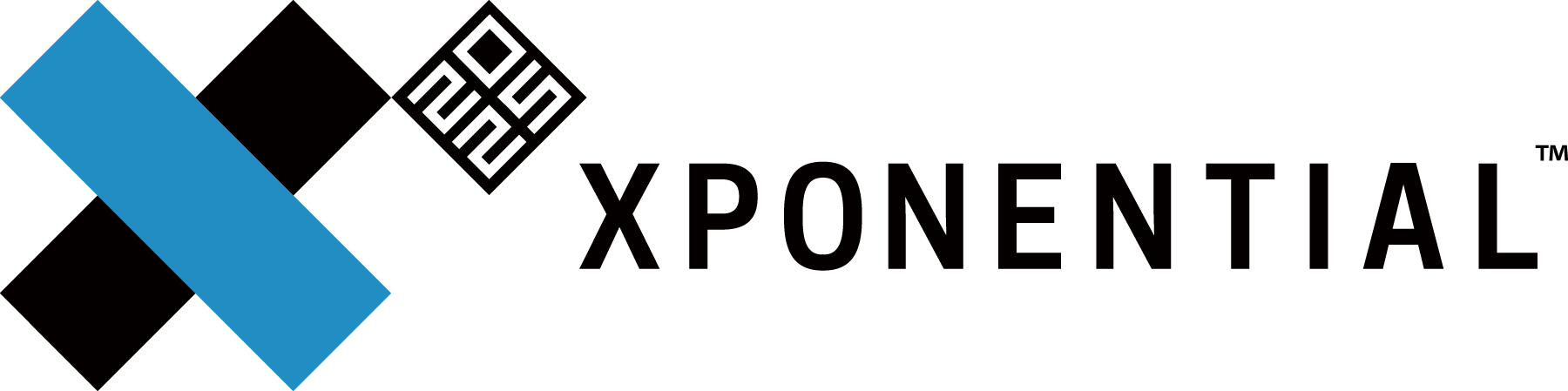
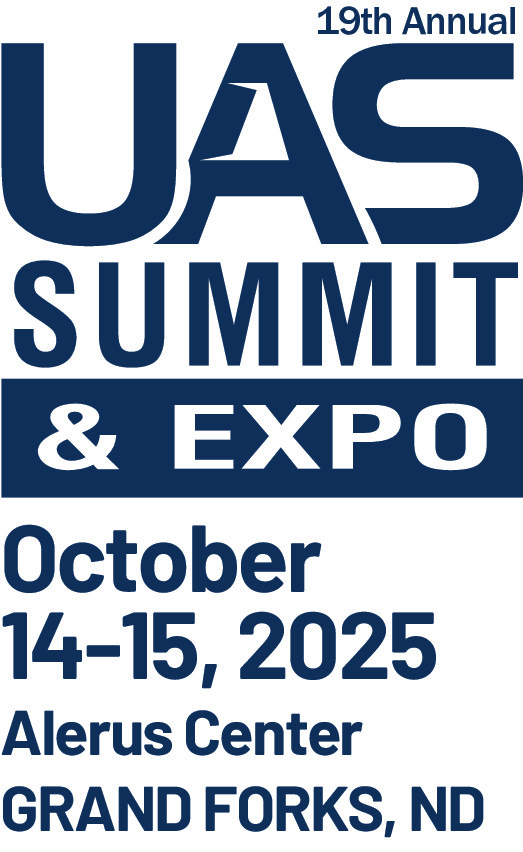

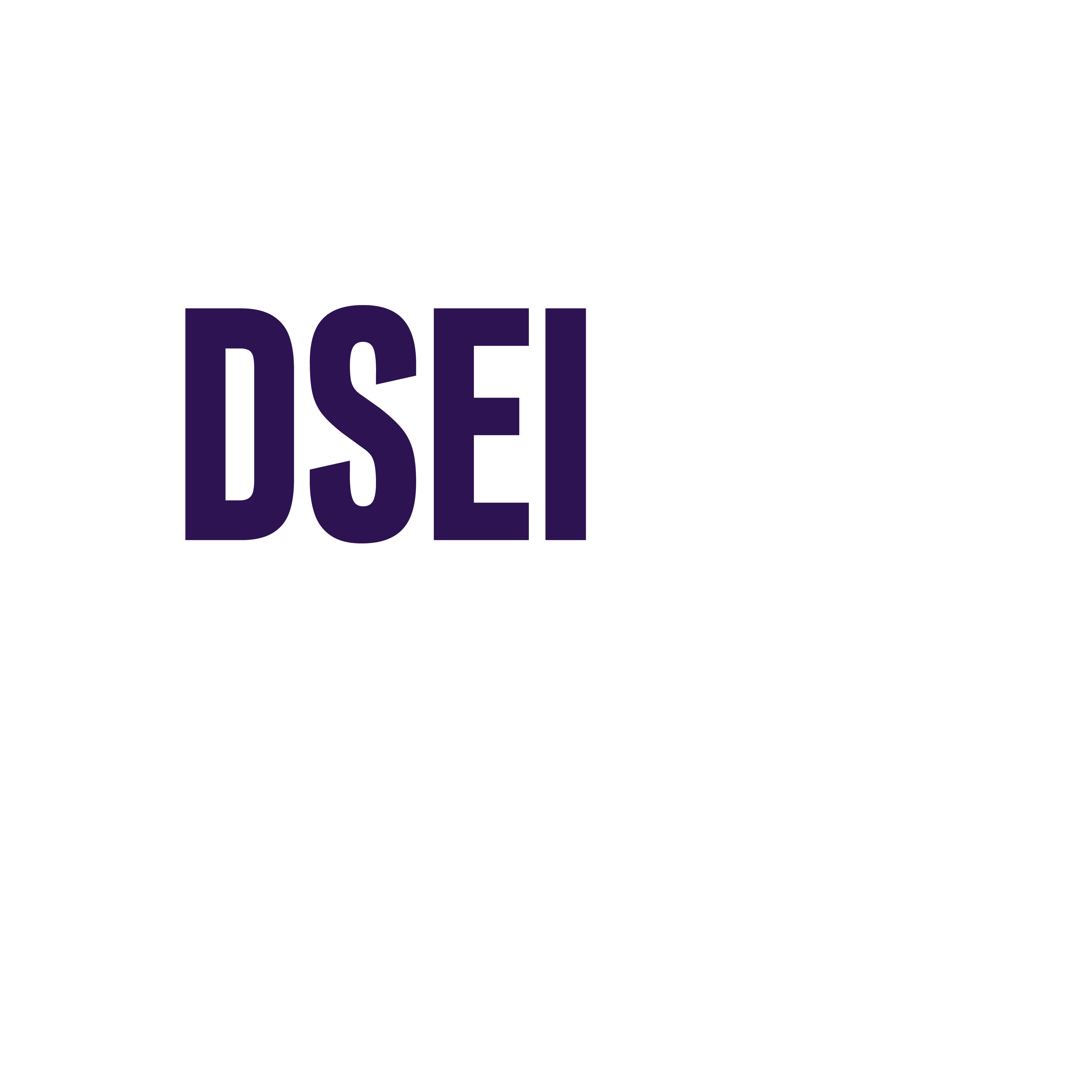
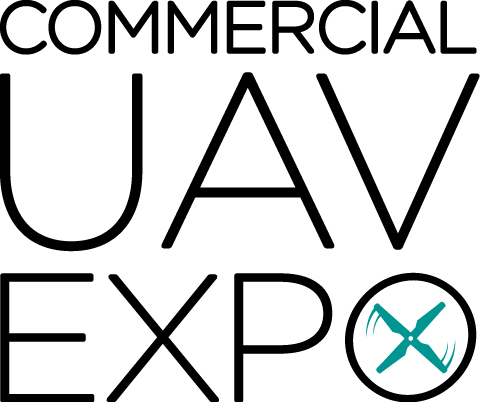
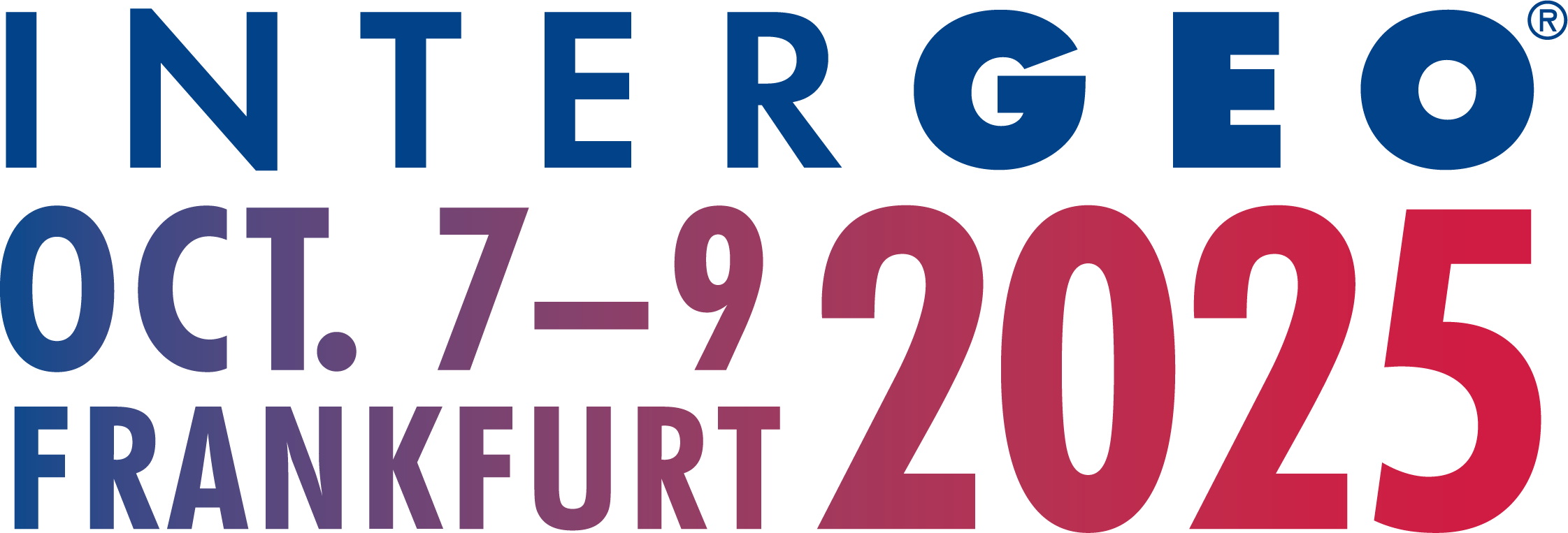
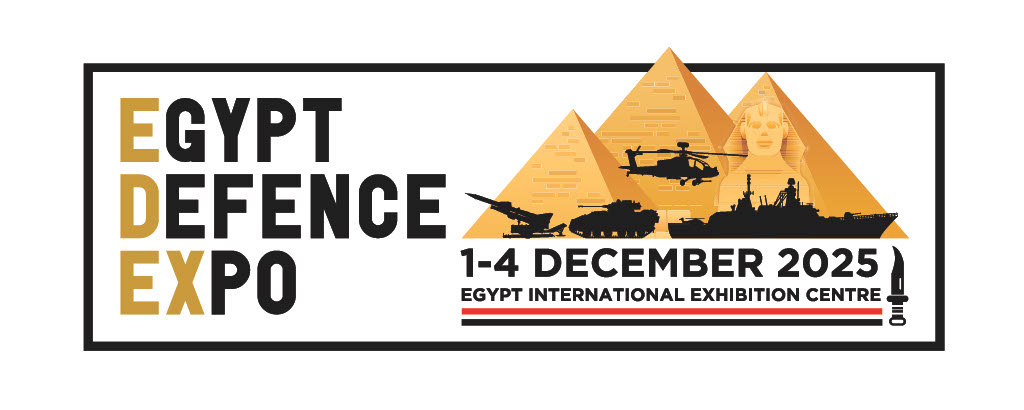
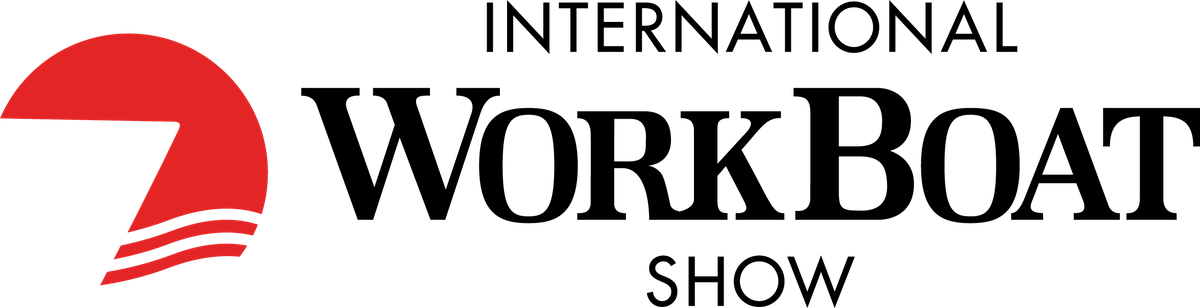