Fuel systems
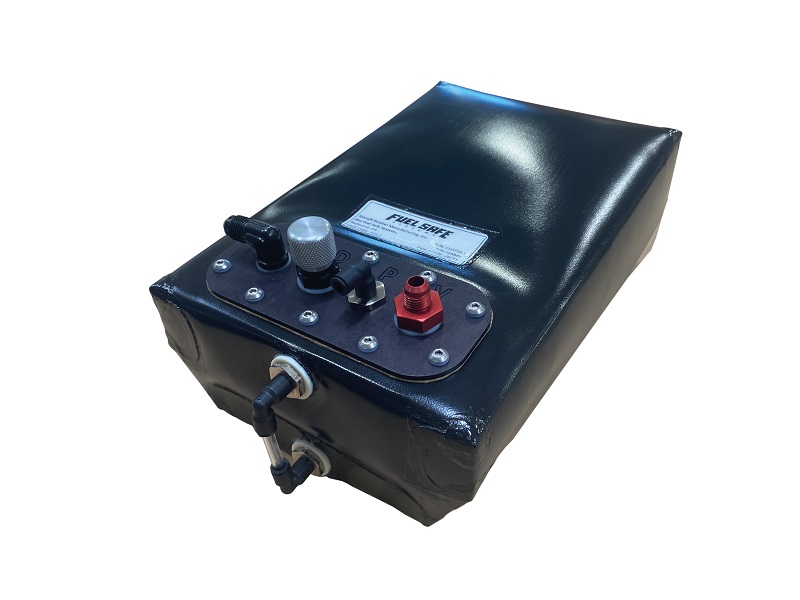
IC engines remain preferred for some types of UAVs but they face efficiency and emissions challenges – which fuel system suppliers are meeting. Rory Jackson reports
Burning issues
As discussed in our cover feature on page 24, the world of UAVs is converging around fuel-based powertrains. Countless organisations have outgrown their DJIs, Yuneecs and other semi-disposable ‘starter’ vehicles, and there is a now huge demand for uncrewed assets that can work longer, travel further and carry more weight than is possible using battery power alone.
Although battery technology continues to advance, the rate at which it is doing so has levelled out in recent years, particularly with respect to specific energy. Hydrocarbon fuels remain far superior in this respect, having around 60-80 times the specific energy of batteries, depending on the type of fuel. That makes their use pretty much unavoidable for powertrains in most high-end UAVs, which unlike autonomous cars and boats are fighting a constant battle against gravity to maintain endurance at altitude.
However, using fuels comes with the caveat of emissions and inferior energy efficiency compared to battery-electric designs, whether a conventional or hybridised fuel powertrain is used. The drive for greater endurance and performance is therefore hampered by emissions regulations, particularly for UAVs performing aerial logistics over cities or mapping around airports for instance.
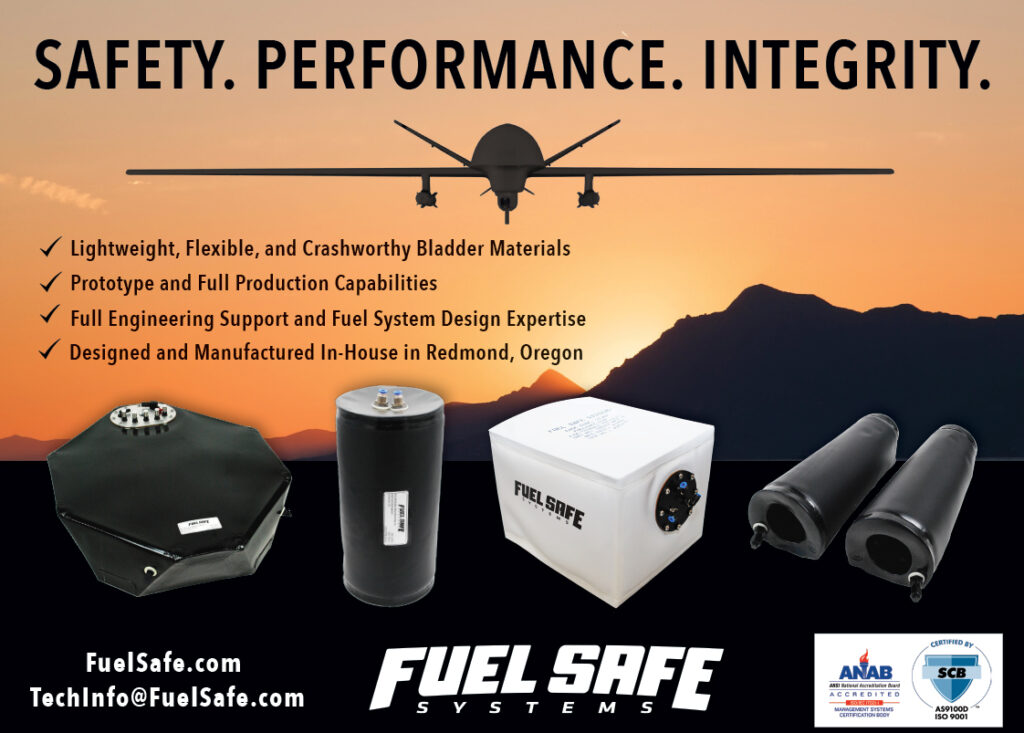
On top of that, the fact that IC engine powertrains inherently have more moving parts than battery-electric configurations means there are more potential points of failure, making their safety a paramount concern for those charged with the well-being of civilians below.
Aviation authorities’ regulations for UAVs are however still being finalised regarding how combustion-related components should be designed, quality controlled and tested in order to be certifiable. That means the guidelines are not 100% clear as to what kinds of parts UAV manufacturers should be selecting and integrating into their higher-endurance powertrains.
It therefore falls on UAV manufacturers to select components for the highest levels of fuel efficiency and safety assurance, while also somehow keeping their costs in check to make their aircraft affordable. Fortunately, the UAV industry has made considerable advances in storing fuel safely and efficiently, along with its delivery, monitoring and injection, which engineers are taking note of for the new generation of heavy-lifting UAVs as well as the emerging urban air mobility market.
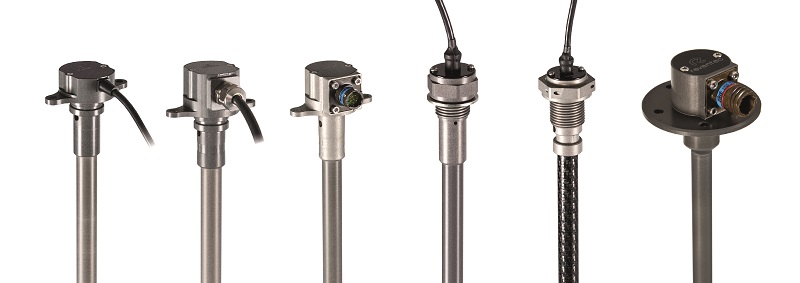
Fuel storage
One might not automatically think of fuel tanks and bladders as playing a major role in fuel efficiency, but great strides have been made in recent years in the design and manufacture of storage systems that are both lightweight and resistant to damage (and by extension to leaking), particularly thanks to innovations from motorsport making their way into the UAV world. The bladders can make aircraft lighter, reducing their required fuel consumption, and preventing leaks naturally reduces fuel expenses over the vehicle’s lifetime.

Bladders built from soft film materials make for light and flexible fuel storage, with some able to stretch by around 600% before failure and to compress by 50% depending on the geometry and the type of support foam used inside. Reinforced fabrics are better known as a bladder material than soft films, and offer better puncture strength and crash resistance, although as a trade-off they are around 30% heavier than films and less flexible.
However, in some new fuel bladders, soft films have been used as a primary construction material while incorporating reinforced fabrics in key areas where contact with sharp or harsh internal hull structural members is a concern. Taking the best of both worlds in this way optimises the weight and survivability of the bladders.
Both the film and fabric are often made from polyurethanes, particularly an ester or ether depending on whether the fuel is a diesel or heavy fuel versus a gasoline with a two-stroke oil mix. Coatings in the fabric bladders are often made from nylon or Dyneema.
These materials and their qualities can be traced back to motorsport’s governing body the Federation Internationale de l’Automobile, where standards for tensile tearing, punctures, seam strength and more have been specified for many years, although it is only in recent years that the benefits they could bring even to FAA-certified aircraft have started to be recognised.
As well as improving weight efficiency and ruggedness, flexible bladders can also be stitched into geometries that conform to a wide range of compartment shapes in UAVs, such as wings or bulkheads, and potentially even with structural rods or spars running through hollows in the bladder shape. Although tanks made from hard materials might do the same, flexible bladders are again at less risk of impacts, breaks or cracks.
Modern rigid tanks do however have some technological and operational advantages that make them worth considering for a fuel-powered UAV. One option is a tank made from a roto-moulded, cross-linked polyethylene, which is so strong that (as per military standards) it can be test-dropped from 20 m while fully fuelled with 60 US gallons (227.12 litres) onto a steel pad without losing any fuel. The tank might become deformed, but it will not crack.
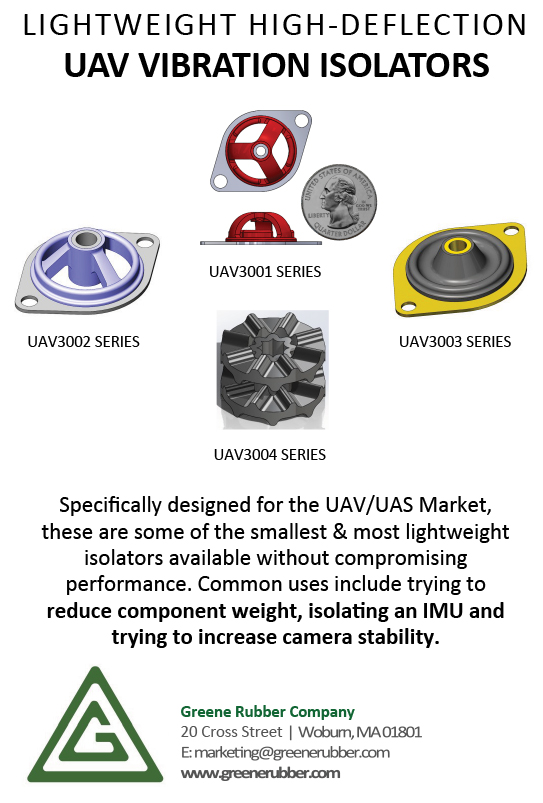
Its manufacture is highly repeatable and not very labour-intensive, making it a good option for bulk-produced UAVs for missions where crashing might be a major concern, such as defence forces, energy infrastructure monitoring or disaster relief applications.
Reinforced fabric bladders are often assembled by cutting their different components with tabs, which are then folded over each other and seamed.
Film bladders however can be produced using some newer approaches, such as having a cylindrical bladder with a single long tab for each flat surface on either end of the tube section. Having one long tab per end (rather than several, as in the usual method) reduces the number of potential leak paths and hence failure points.
A small number of fuel storage suppliers have even developed solutions for protection against ballistics impacts – clearly an ever-present concern for defence UAVs on front lines or those operating near potentially explosive industrial environments.
Rather than actually armouring the tanks, which would present a weight concern, the most promising technology is a self-sealing solution composed of a two-stage reactionary material. When a projectile penetrates the bladder, the rubber first ‘wants’ to mechanically return to its original shape, stretching inward towards the gap.
Second, a chemical reaction occurs as the fuel makes contact with the uncured rubber revealed by the ballistic wound. This reaction causes the uncured rubber to swell, and in the direction of the hole, thereby closing it.
First popularised in military aircraft and civilian armoured vehicles, this solution is not intended to clear a UAV (or other vehicle) for continued, uninterrupted operation but to prevent leaks and explosions of fuel, and potentially ensure that the vehicle can be approached and carried away, or launched to perform just a short flight to a safer location.
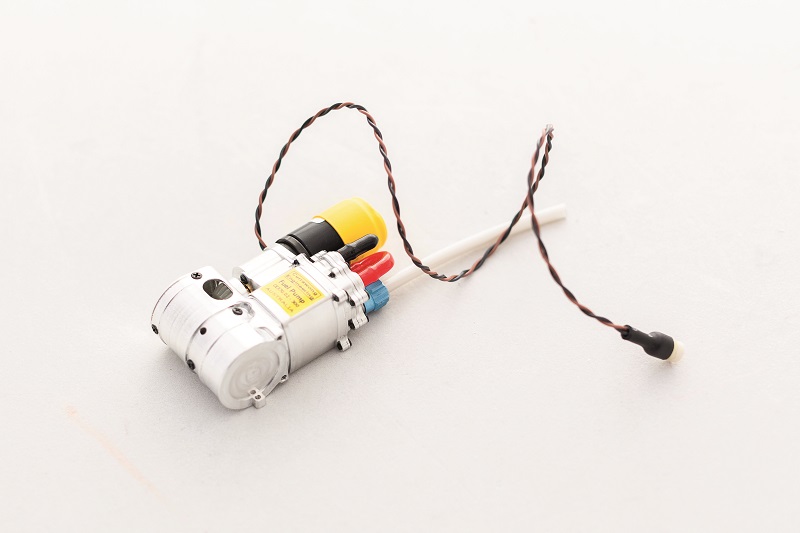
Fuel level sensors
A well-functioning fuel tank or bladder also depends on careful selection of the level sensors for tracking the availability of fuel, to gauge the remaining endurance or spot any problems with fuel storage.
There are a few different types of fuel level sensor, including ultrasonic, reed switch and resistive float sensors, and each has its drawbacks. Ultrasonic sensors for instance typically have a ‘dead band’ close to the sensor and can hence fail to measure liquid if it sloshes about. Reed switch sensors meanwhile tend to measure fuel levels with a poor, coarse resolution compared to others, and resistive float sensors are unsuitable for high-vibration applications.
Capacitive level sensors have overtaken the other types now though. They operate by measuring the energy stored in a capacitor formed by the probe’s geometry. The fluid forms the insulative dielectric, and the capacitance measured is therefore proportional to the fluid level in the probe.
They deliver a reliable and fine-resolution data output, which can be communicated over CAN, and in addition to being solid-state sensors and therefore suitable for high-vibration environments, in recent times they have been upgraded to enable their hardware to meet Mil-Std 461F for the control of EMI characteristics in subsystems.
That level of standards compliance will become a pressing need for many autonomous aircraft in the future, as engineers integrate more and more EM-emitting electronics for various purposes. The growing popularity of hybrid powertrains could add to the risk of EMI inside aircraft hulls as well.
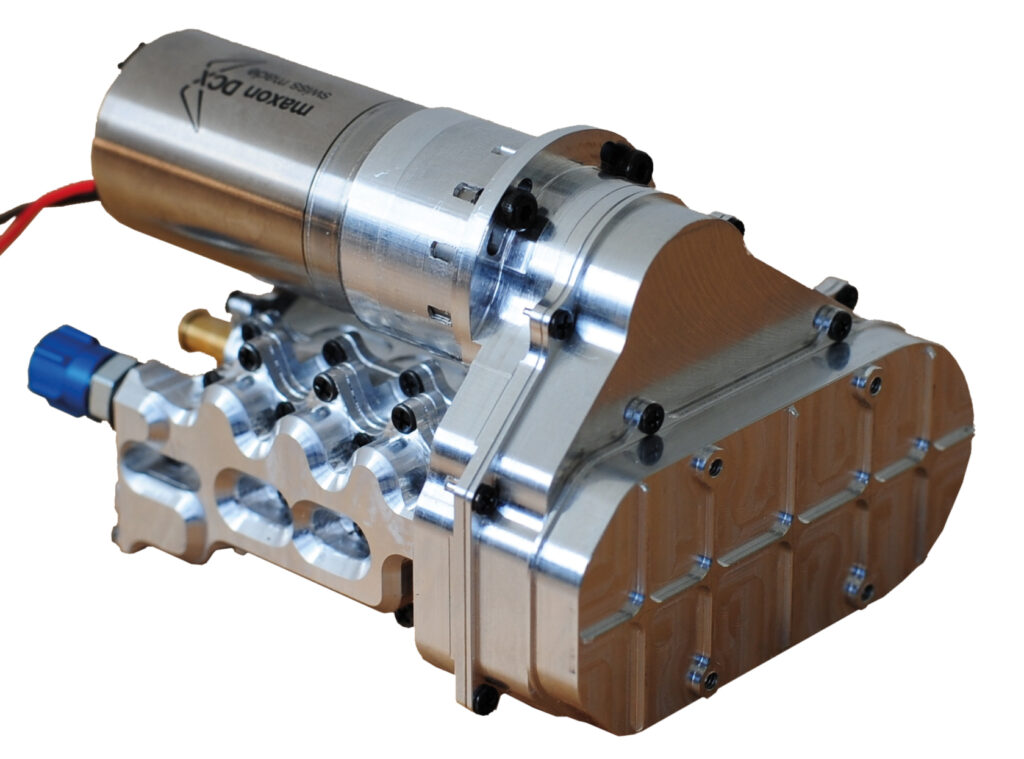
Fuel filters and lines
Transporting fuel to the engine depends on several key components. Filtering for instance is critical to keeping the fuel clear of sand, dust, metals or cleaning fluids for example.
Many fuel filtering systems are now standardised systems, but the range of filter types available run from sock-type pre-filters designed to catch anything over 30-60 microns in size, to inventions such as the Holly HydraMat, a 15-micron system that also serves to collect fuel bunching up at any corner of the tank.
Although this latter solution is currently only compatible with gasoline, it ensures that during hard cornering or other instances of high g-forces, the fuel does not slosh about or flow into the edges of the tank and out of reach of the collection nozzle, nor can any air bubbles force their way into the fuel and past the filter.
It can thus make collectors and check valves unnecessary to the continued supply of clean fuel to the engine. And once filtered, various industry-standard fuel hoses are available for the UAV market.
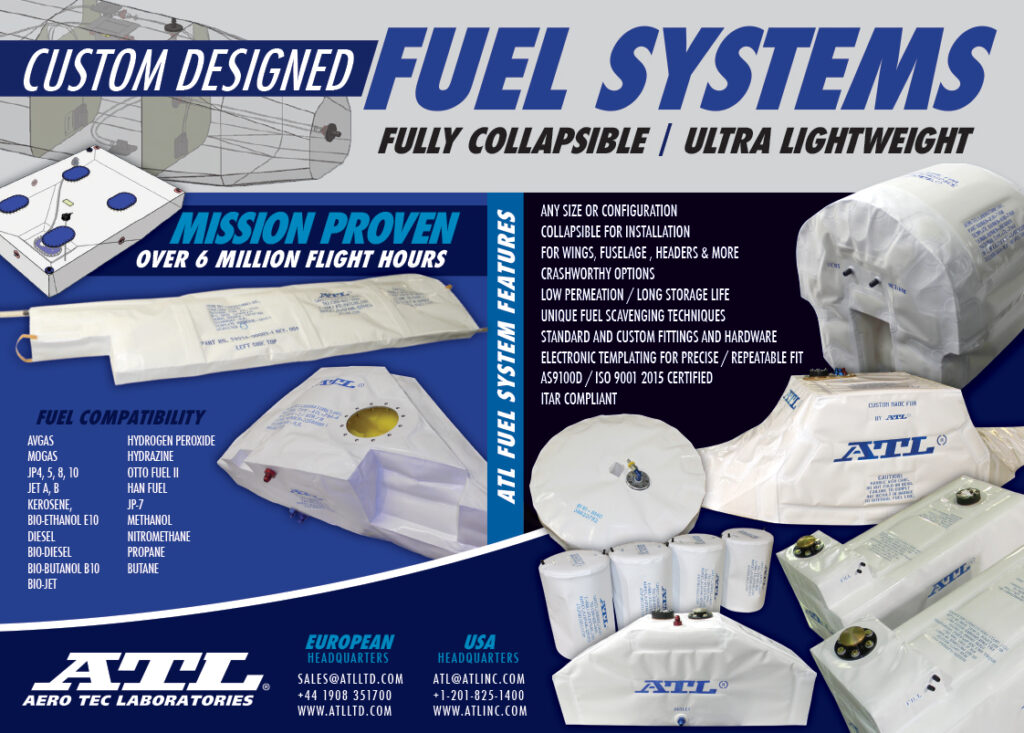
Fuel couplings and fittings provide safe, secure connections of fuel lines as well as overall weight saving and reduction of vibration resonances. Key design points to note in this regard lie in a few areas, one obvious one being careful to ensure couplings are well-matched to the chosen fuel hoses, with an optimised fit and which are grip-tested across different temperature, liquid, shock and vibration conditions.
On top of that, stretching the fuel tubing up the inside of the coupling’s hose barb – a cylindrical fluid connector component, typically featuring barb-like rings on the male part that allow an easy push connection of flexible plastic or rubber tubing. It can mitigate the flow restriction point needed by the internal barb fitting, and thus increase the nominal flow diameter. That enables the use of smaller and lighter tubing.
Fuel pumps
The UAV industry has not always had access to quality fuel pumps. Before 2000, many UAVs built by defence primes would crash because of poor choices of pumps, with few if any being tailored for the specific needs of UAVs.
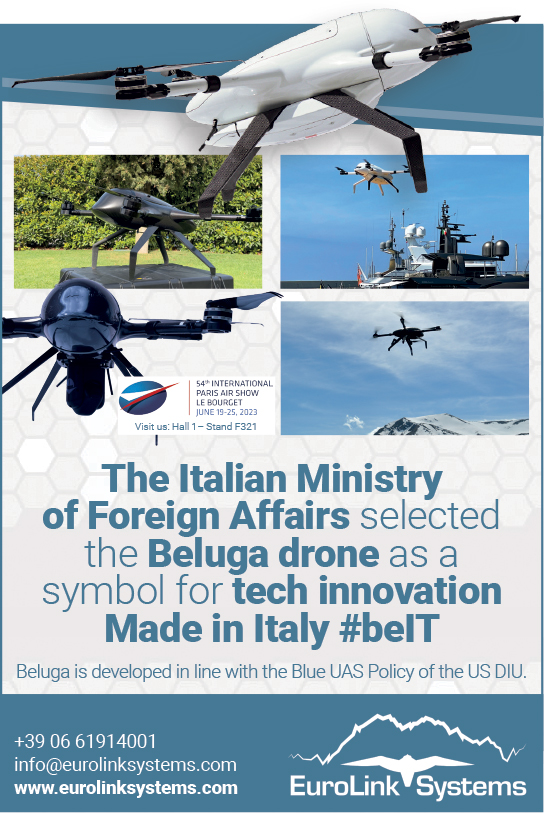
A conventional automotive EFI system uses a gerotor pump submerged in the fuel tank, sending fuel to a rail fitted with a pressure regulator; that in turn would have a bypass filter to send excess fuel back to the engine. In such a system, the gerotor would always be activated and pumping, the pressure regulator would always be open due to the quantity of fuel in constant circulation, and overall the system would be constantly pulling excessive electric power, making it rather energy-inefficient.
In UAVs though, constant fuel circulation is not only prohibitively inefficient but unsafe, as outgassing could occur owing to the smaller tank sizes (compared with those in cars) causing bubbling of their fuel.
Also, mechanical pumps such as gerotor or gear systems are difficult to scale down to sizes appropriate for UAVs (ideally less than 100 mm in length, width and height), largely because of the tight clearances needed. Even when well-designed, they can draw 10-20 W per pump, and UAVs in the late 1990s to early 2000s would rarely have had more than 60-90 W of electric power available, making such pumps a considerable burden.
UAVs therefore need dead-headed fuel pumps, driven by highly efficient electric motors regulated to control pressure, rather than by mechanical systems, and that in turn means having to use fuel pressure sensors. This efficiency helps to lower power consumption – a must-have for flight endurance as well as keeping running mission costs reasonable.
Positive-displacement pumps are among the most efficient designs. They have minimal leakage and strong self-priming. They are also often designed to run dry, as air can pass into the fuel line during moments of high or negative g-forces. Also, end-users will occasionally not refuel their UAVs completely before running their engines, which can break the pumps if dry running causes a failure mode.
This pump type can require a damper because of their pulsing manner of operation, similar to those sometimes used for the pulses caused by the pressure fluctuations from the injectors opening and closing.
A highly efficient UAV fuel pump will transfer around 45% of the electrical power it consumes into mechanical work, and it must tolerate the severe temperatures that can build up around UAV engines, as well as moments of low fuel pressures, down to the vapour pressure level, beyond which fuel can no longer be pumped.
Resilience to sand ingress is also vital; should a filter fail to block that, integrating meshes internally can be key here. With such robustness, a good fuel pump will last for 700-1500 hours in a UAV, rivalling the lifespan of a high-end UAV engine.
Some fuel pumps have been designed to be integrated somewhere below the fuel tank, with gravity providing assistive pressure to the fluid flow. This is of course unsuitable for UAV-bound pumps though, as not only will extended pitching and rolling interfere with the direction of gravity, but the fuel tank or bladder is often mounted at one of the lowermost sections of the airframe, making it impossible to mount the pump anywhere below the tank.
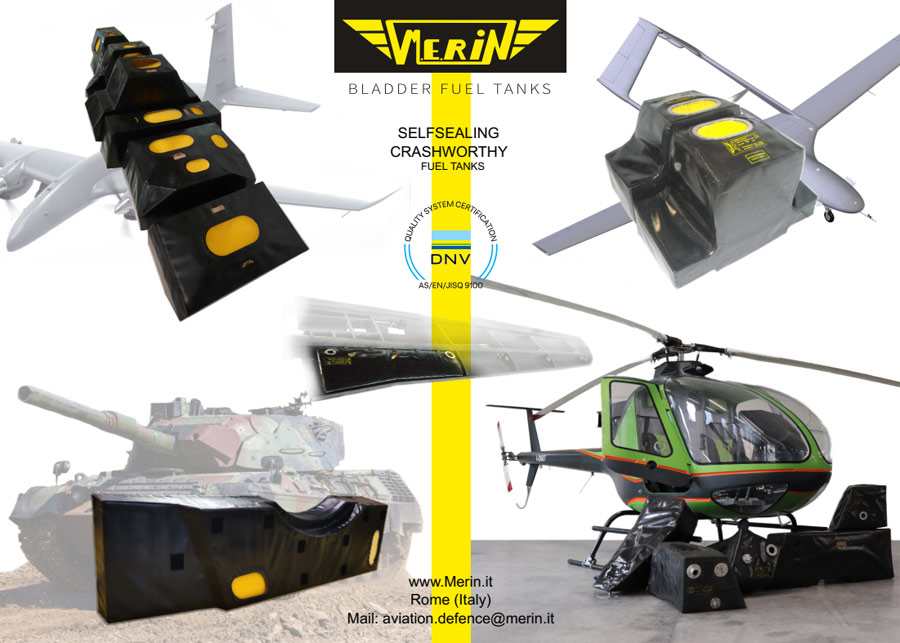
Higher-end UAV pumps are therefore engineered to function no matter where they are integrated relative to their tanks.
As heavy fuel becomes used to power more and more UAVs, demand for more rugged pumps designed to operate at up to 10 bar (with 8 bar being ideal for atomising such fuels) will grow. Positive-displacement pumps with a higher cylinder count and a stronger crankshaft than their gasoline-handling counterparts have a track record of meeting this need.
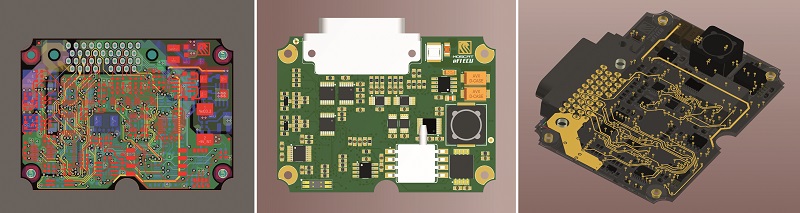
Fuel injection and EFI control
Some UAS suppliers opt for automotive fuel injectors, although it is recommended that they be modified for ensuring the appropriate flow rates for the 25-50 cc engines that are common among UAVs – changes would include replacing the director plates and drilling fresh sub-mm holes. Also, some note that injectors made for small, scooter-type vehicles often approximate closely to the ideal flow rates and efficiencies for UAS powertrains.
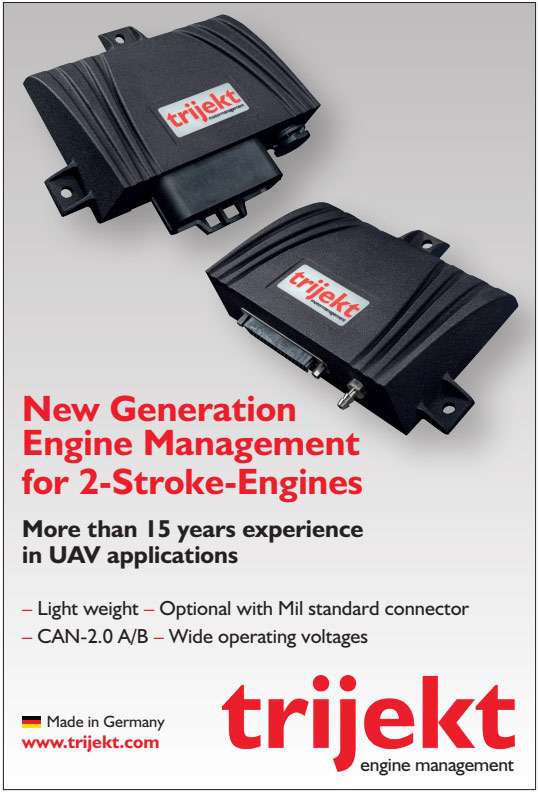
Sizing injectors accurately for gasoline two-strokes is especially critical owing to the very slim injection windows available at 8000 rpm. It follows that a very high flow rate can be extremely helpful in this regard.
Also helpful are some key innovations in EFI control systems produced for the UAV world. For instance, some more advanced EFI software modules now include programming for greater control over injection timings. In addition to assisting with finer gasoline injection times, this provides valuable opportunities for safety and efficiency in heavy-fuel operations, as is popular among defence and particularly maritime users.
During transients, for instance, injectors can be commanded to ‘skip’ injection rounds if heavy fuels are pooling too much inside cylinders owing to the vaporisation problems inherent in heavy fuels, to help regulate the richness of the fuel during the next combustion cycle.
Sensing such pools in real time is challenging, so accurate maps of pooling ‘probabilities’, as indicated by exhaust and performance readings, are very valuable for heavy-fuel engines. This technique can also be modified to compensate for projected fuel deficits, to build up a pool for when more fuel will be needed than can be typically injected in one go.
In general, air-assisted direct injection is still considered the best approach to heavy-fuel efficiency, by virtue of not short-circuiting fuel to the exhaust and hence substantially improving the specific fuel consumption (SFC).
However, they remain heavy and expensive. By reducing SFCs by around 20-25%, they can add 50% to powertrain mass as well as quite a few additional moving parts. The alternative approach of having a fine and flexible EFI control paired with indirect injection therefore stands to make a great difference for the value operators derive from their UAVs when preferring heavy fuel.
Although automotive injectors can work well for UAV applications, automotive EFI controllers can suffer issues such as mistaking altitude-related air pressures for errors or failures, unnecessarily triggering back-up measures, and can contain some unsuitable or proprietary modules that make them difficult to work with. By contrast, ECUs designed from (or mostly from) scratch for UAV applications can be tailored for the engines and aircraft unique to the industry.
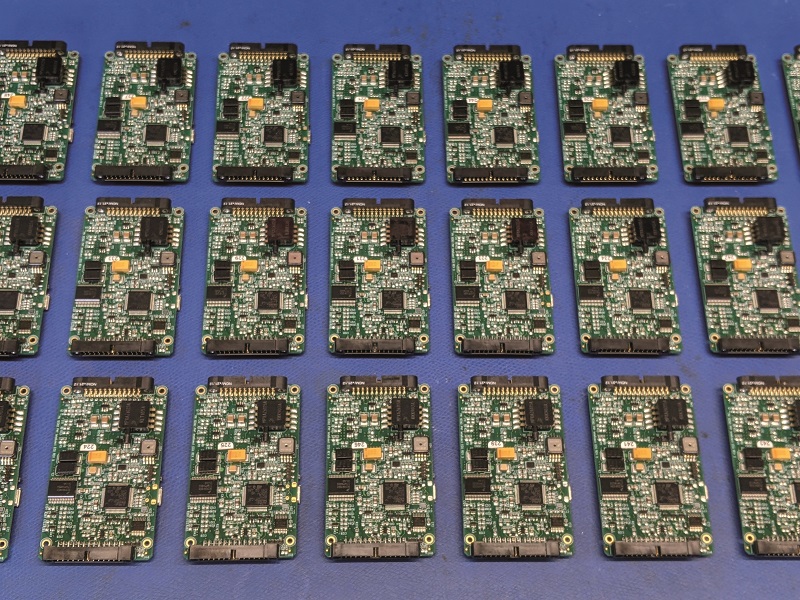
Future of fuel
Although IC engine powertrains retain an advantage of around 10x over batteries in terms of specific energy, it is generally agreed that batteries will eventually overtake fuel systems in that respect. However, advances in some key IC technologies will delay that.
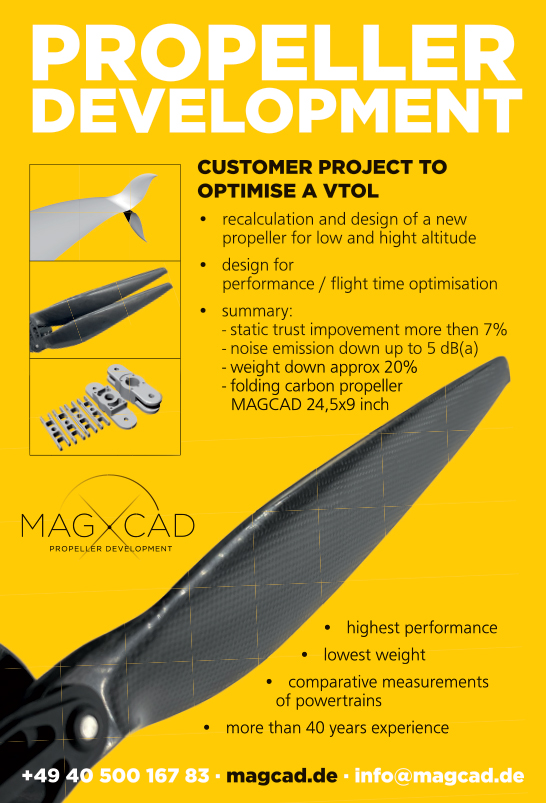
One of those is the use of alternative fuels to traditional gasoline, diesel and heavy fuels that can provide higher efficiencies and lower emissions. One obvious route is the mixing of biofuels into conventional fossil fuels, as some airlines already do, as well as using 100% biofuel (with Demcon already planning to do so with its upcoming 7 m USV – see page 62).
Synthetic fuels produced through captured carbon are also likely to become viable, with recent EU automotive legislations having enshrined the use of these ‘e-fuels’ in car engines beyond the 2030s.
Also, more engines are being designed to burn hydrogen. While not as efficient as using it to produce electricity via a PEM fuel cell, it still guarantees true zero carbon emissions shaft power. Whether hydrogen or biofuel is better environmentally depends on the source – ‘grey’ hydrogen for instance can be derived from processing fossil fuels, while ‘green’ hydrogen comes from electrolysers powered by solar and wind.
Similarly, biofuels can be carbon-negative when considering the CO2 capture and photosynthesis of the biomass from which they are produced, although any advantage there is cancelled out if rainforests for example have to be cleared for farming the biofuels. Determining the best fuel is therefore a matter of case-by-case calculation.
No matter the fuel though, hybridisation will be a major aspect of what the powertrains of the future will look like, as electric machines become more advanced and more widely available, and both series and parallel hybrids should be expected among hybridised aircraft.
That could play into the requirements of fuel systems, as the motor/generators in hybrid configurations will gradually come to be recognised as the focal point of aviation powertrains, and the prime mover in series hybrids. The roles of fuel injectors, lines, pumps, filters and bladders meanwhile will become gradually re-established around keeping the motor/generators working.
The smaller sizes of UAVs and their lack of onboard personnel compared with crewed aircraft will increasingly make them a vital test case and proving ground for what such future powertrains will look like.
Acknowledgements
The author would like to thank Dan Tynan and Trevor Hart at Fuel Safe Systems, Jack Birmingham and John Landells at Reventec, Sergio Moscat at Moscat Ingenieria, Gavin Brett and Brant Patford at Currawong Engineering and William Vaglienti at Power4Flight for their help with researching this article.
Some examples of fuel systems manufacturers
AUSTRALIA
Currawong Engineering | +61 3 6229 1973 | www.currawongeng.com |
CANADA
Battlefield International | +1 905 772 3000 | www.battlefield.biz |
GERMANY
CAE | +49 2402 1060 | www.de.cae.com |
P1 Performance Fuels | +49 30 2325 57010 | www.p1fuels.com |
SF Motorsporttechnik | +49 6253 238652 | www.sf-motorsporttechnik.de |
ITALY
MERIN | +39 06 9074 553 | www.merin.it |
SPAIN
Moscat Ingenieria | +34 914 91 02 36 | www.moscatingenieria.com |
UK
Aero Tec Laboratories | +44 1908 351700 | www.atlltd.com |
Atec Auto Technic | +44 1280 704525 | www.atec-autotechnik.com |
BMRS | +44 1753 545554 | www.bmrs.net |
Earls Performance Products | +44 1327 858221 | www.earls.co.uk |
KA Sensors | +44 1476 568057 | www.kasensors.com |
Premier Fuel Systems | +44 1332 850515 | www.premier-fuel-systems.com |
Protec Fuel Pumps | +44 1283 568407 | www.protecfuelpumps.com |
Reventec | +44 1725 510321 | www.reventec.com |
TetraBoost | +44 1869 227062 | www.tetraboost.com |
USA
Aero Tec Laboratories | +1 201 825 1400 | www.atlinc.com |
ARE Dry Sump Systems | +1 916 652 5282 | www.drysump.com |
BLP Racing Products | +1 407 422 0394 | www.blp.com |
Briggs & Stratton | +1 414 259 5333 | www.briggsandstratton.com |
Fuel Safe Systems | +1 800 433 6524 | www.fuelsafe.com |
Hank Thomas Performance | +1 800 848 4265 | www.hankthomasperformance.com |
No Limit Manufacturing | +1 715 384 4422 | www.nolimitmfg.com |
Power4Flight | +1 541 436 4299 | www.power4flight.com |
Rockett Brand Racing Fuel | +1 847 795 8400 | www.rockettbrand.com |
VP Racing Fuels | +1 210 635 7744 | www.vpracingfuels.com |
XRP | +1 562 861 4765 | www.xrp.com |
UPCOMING EVENTS
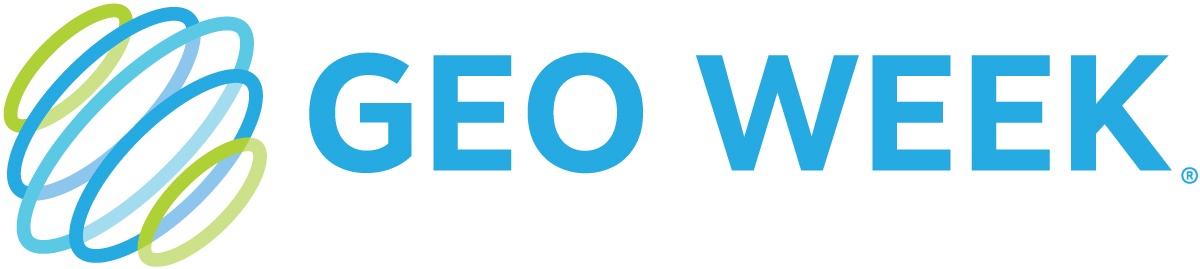
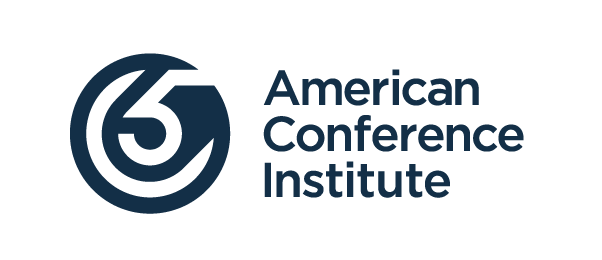
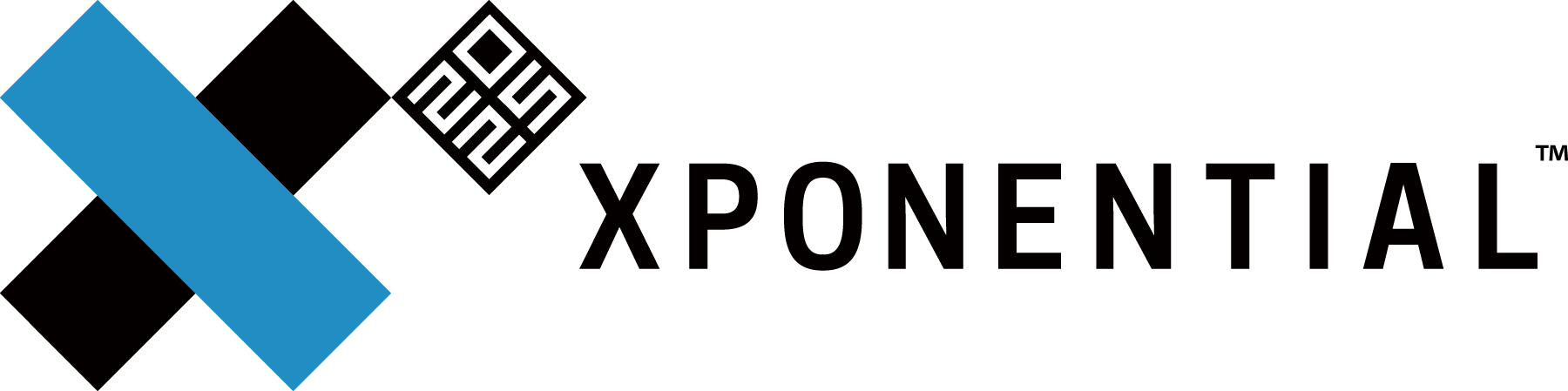
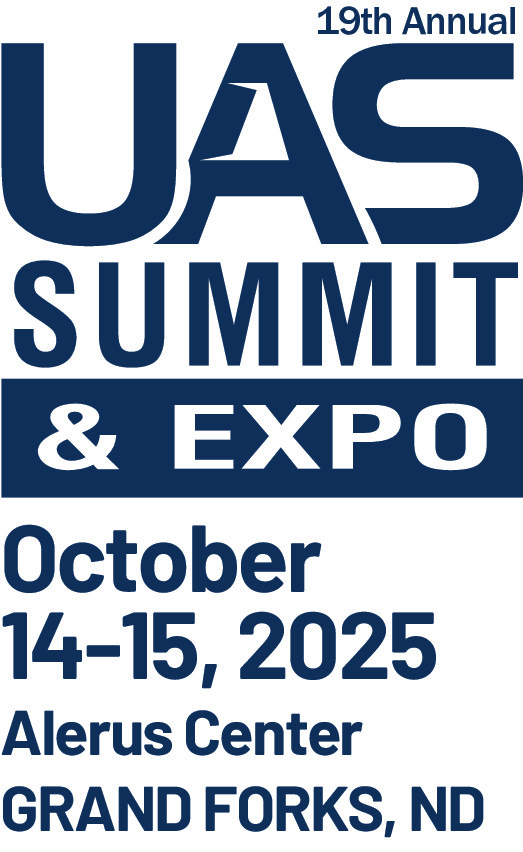
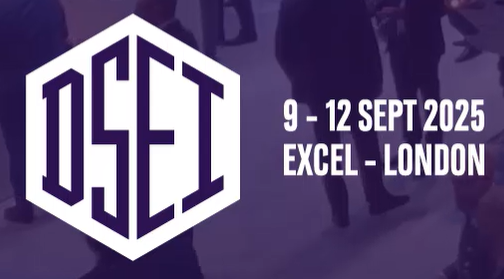
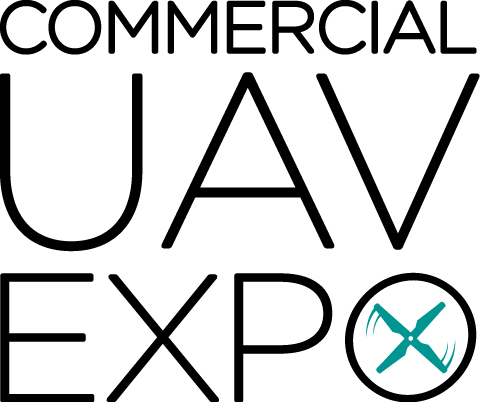
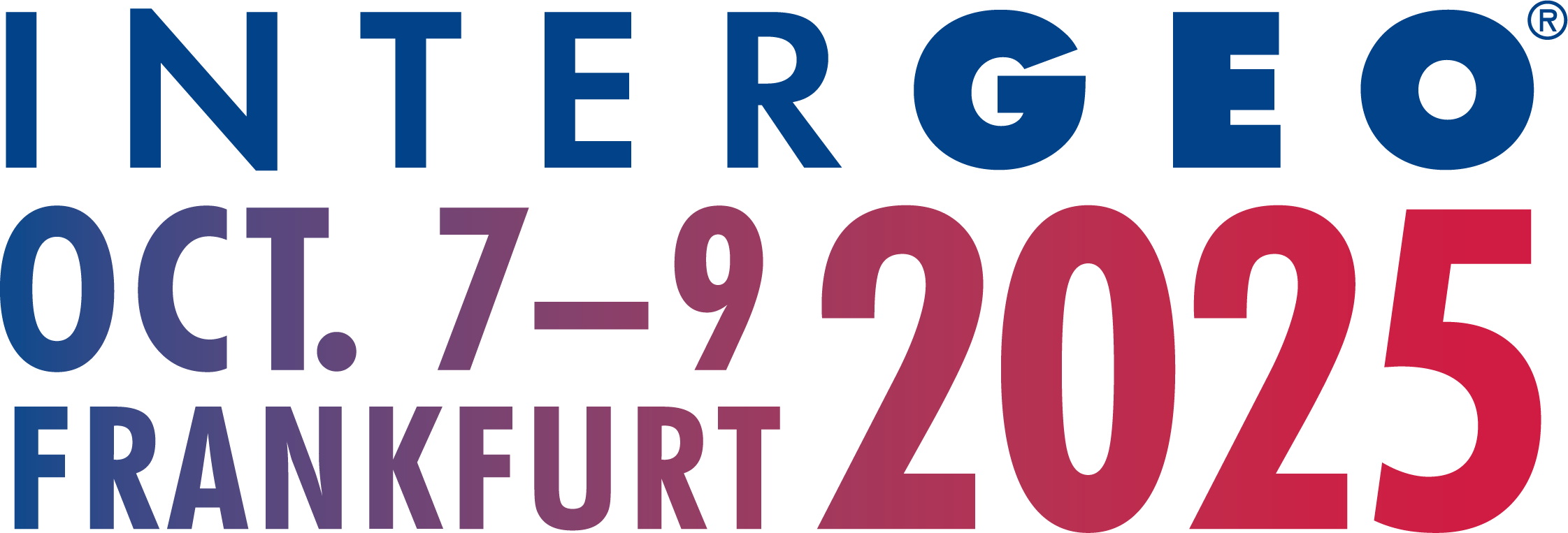
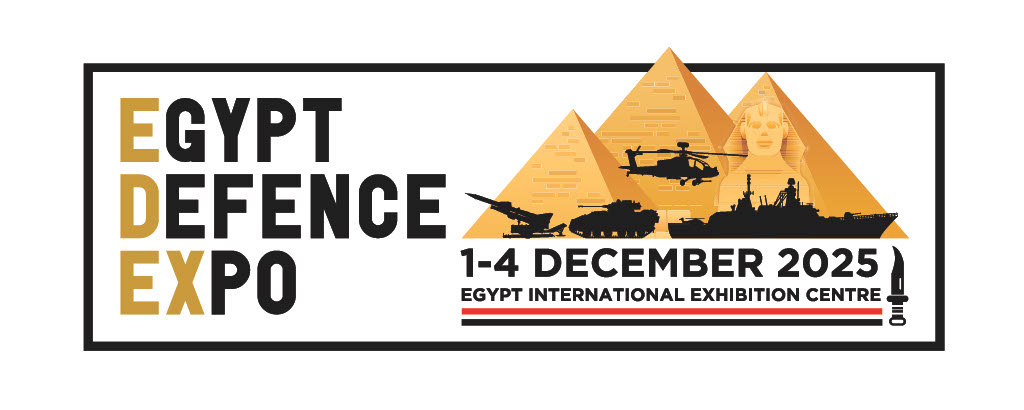
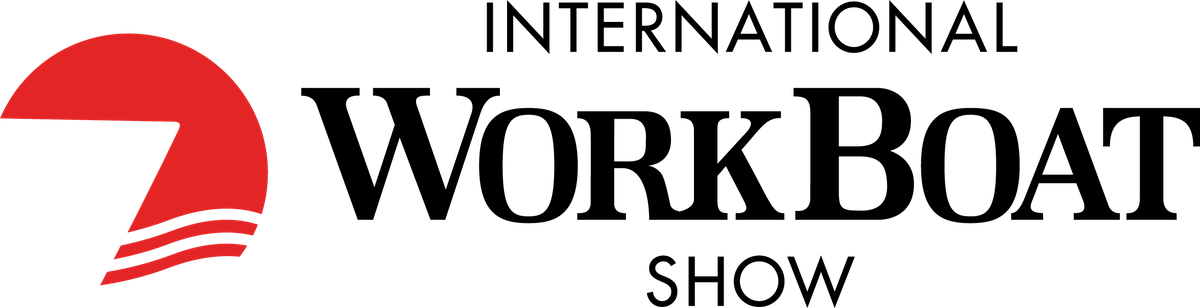
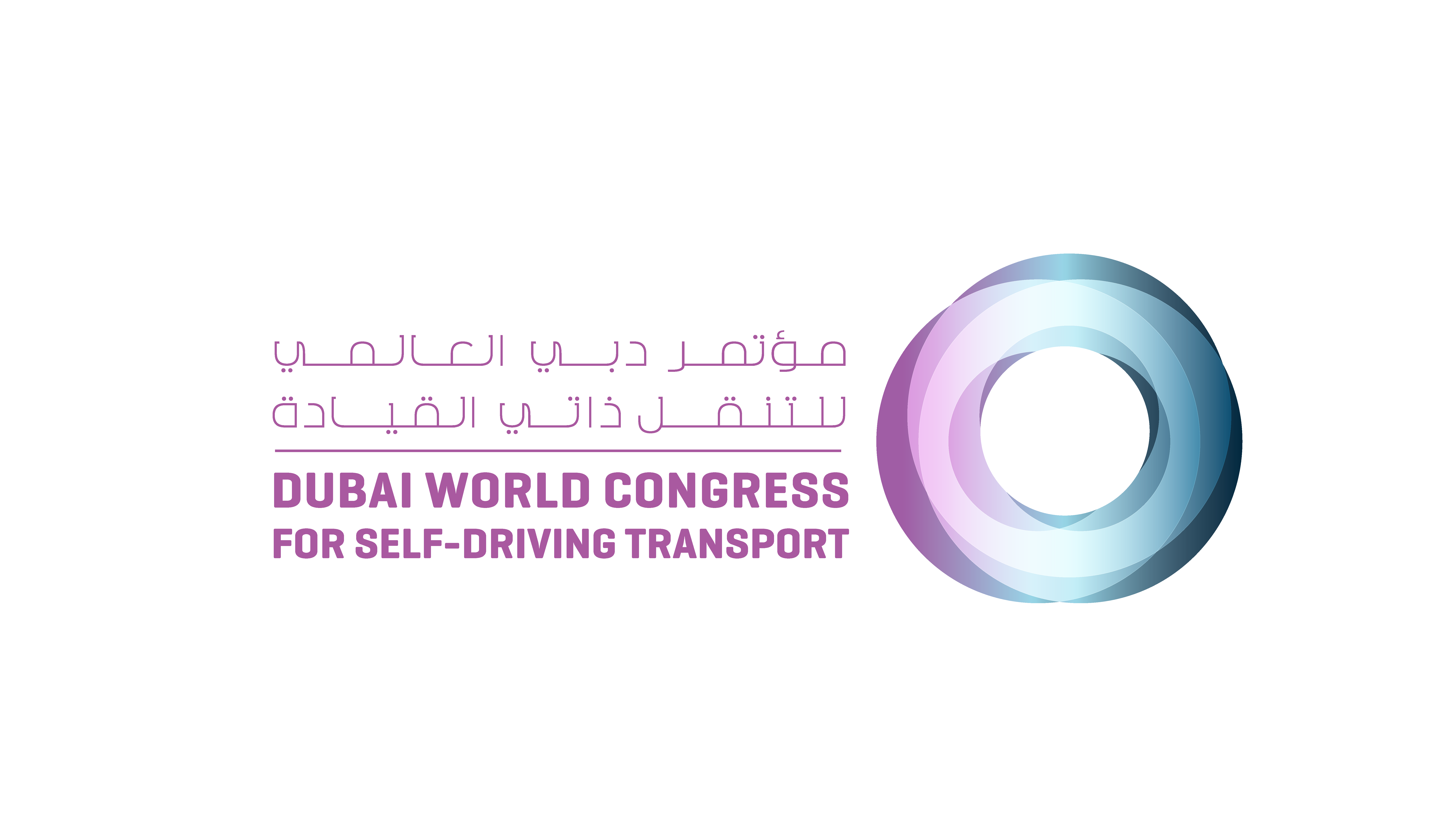
