DroneWorks solar panel inspection
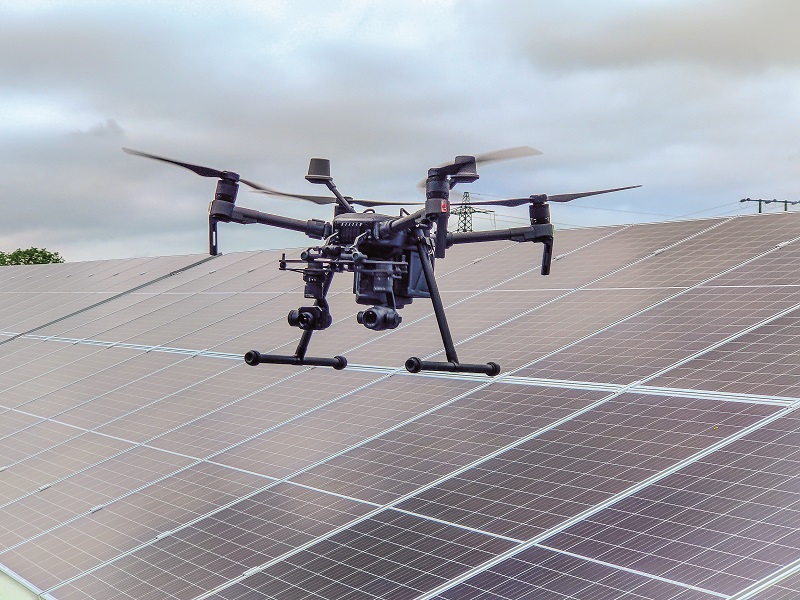
Sunlight duties
Peter Donaldson reports on how this company is using UAVs to carry out essential inspections of solar arrays safely and quickly
A small VTOL UAV fitted with a thermographic camera is a powerful tool for inspecting the integrity and energy efficiency of many kinds of installations that are difficult, time-consuming or dangerous to reach by methods that involve people working at height – and rooftop solar panels fit snugly into this category.
Turning this core capability into a professional business hinges on choosing the right equipment, developing safe operating procedures, reassuring the public and delivering the right information to customers, explains DroneWorks’ founder and director Jason Hinsley.
Thermography uses thermal imaging cameras to provide highly accurate temperature measurements throughout the image, which is enhanced with computer-generated false colour to provide an intuitive visualisation of temperature distribution within it to support the data. This is particularly valuable for quickly determining the condition of rooftop solar panels, the efficiency of which is critical to businesses and homes trying to reduce their carbon footprint, save money on electricity and benefit from selling energy back to the grid.
Follow the money
It was a sudden fall in income from the grid that first alerted the owners of Bleasdale Parish Hall, in Preston, northern England, that there might be something wrong with the building’s rooftop PV array, which was installed while the UK government was subsidising the technology. The hall is run as a charity and provides a venue for social, educational and business functions and events.
Besides its PV array, the hall has a wind turbine and a biomass boiler. In the summer of last year, its income from the grid fell by almost 50% over the previous comparable period, representing a loss of more than £1000. At that point, it called in DroneWorks.
The company is certified in the UK by the British Institute of Non-Destructive Testing as a Cat 1 provider of thermography services, able to collect infrared data to the required standards. Hinsley argues that, in addition to improving safety, UAVs collect that data more than 50 times faster than is possible with manual methods.
The company started its main aerial inspection business in April 2019, introducing thermography the following year, says Hinsley, who came from a software engineering background where he gained experience developing bespoke software to automate data processing and workflows.
“I feel the value is in the data, and drones with the right sensors are a very efficient method of collecting data at scale, safely and quickly,” he says. “With good data and the right software, there are numerous applications; the property and construction sector in particular can benefit from this in a big way.”
He adds that DroneWorks was set up to provide solutions to those sectors on the basis of fast and accurate collection of data and on exploiting software to deliver that data in a way that makes it easy to understand. “Ultimately, this saves the client time and money, and grants insights not previously possible,” he says.
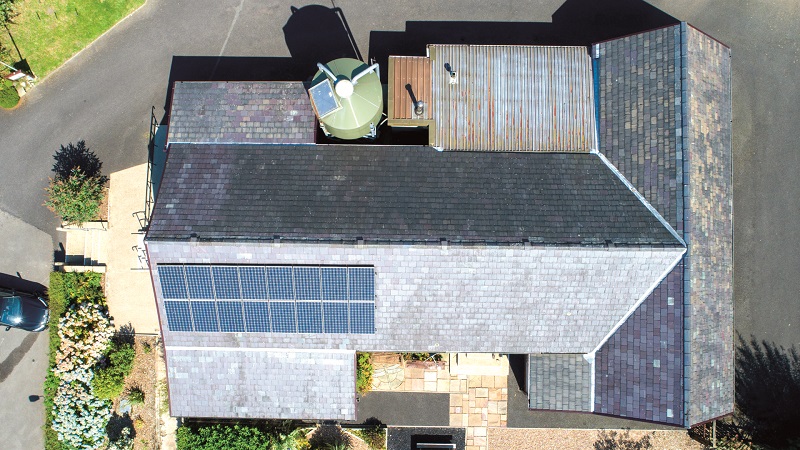
Tool for the job
The Bleasdale mission took place in August 2022, for which DroneWorks used a DJI M210 RTK v2, an electric quadcopter with a maximum take-off weight of 6.14 kg and a maximum payload of 1.72 kg, figures that include two 7660 mAh DJI TB55 batteries.
Hinsley describes the M210 as a flexible, robust platform with good flight times and multiple payloads and sensors, suiting it to many kinds of inspection and survey work. The facility to swap sensors in the field quickly to collect different types of data makes it versatile as well, he notes.
Aimed at commercial operations, it is reliable, has multiple safety features including geofencing, comes with ‘return home’ logic in case of a lost link and a separate front camera to help with navigation, he says. It is also larger than something like a Mavic 2 and carries a bright strobe, making it highly visible.
For the Bleasdale job, the M210 carried a dual-camera DJI Zenmuse XT2 sensor system. “This provides a radiometric IR image alongside a visual image to ensure we have as much information as possible to provide an accurate report to the client,” Hinsley says.
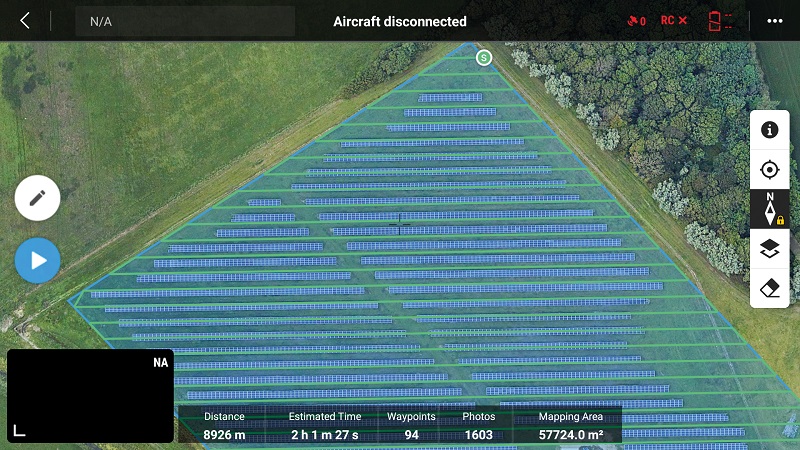
Radiometric sensor
The Zenmuse XT2 features an uncooled micro-bolometer radiometric sensor operating at wavelengths between 7.5 and 13.5 microns in the long-wave IR band. The core of the sensor is a 640 x 512 element vanadium oxide focal plane array detector with a pixel pitch of 17 microns.
In terms of sensitivity, it can resolve a noise-equivalent temperature difference of less than 50 mK, at an aperture of f1.0, while in terms of dynamic range it can make accurate measurements of scenes simultaneously containing temperatures from -25 oC to +135 oC at its highest gain setting, and -40 to +550 oC at its lowest.
The IR camera is paired with a colour camera operating in the visible spectrum. This is based on a 12 MP 1 x 1.7 in CMOS sensor and a prime lens, which is in focus from 8 mm to infinity. Both cameras also have a digital zoom.
Mission planning involved a site visit to scope out the building and its PV array installation, along with anything that might affect flight safety and the ability to complete the job while complying with aviation authority rules. This, Hinsley explains, is mainly about ensuring safe distances from people not involved in the job and staying clear of restricted areas such as the airspace near airports. While operating in such areas is possible, the required planning and liaison with the airport is more involved.
“Planning for Bleasdale was fairly straightforward due to the rural location,” he says. “The main consideration was the height of the roof and the direction and angle of the panels to ensure they were in direct sunlight during inspection.”
This stipulation is included in the standards set out by the IEC and in the UK by BS EN/ISO 62446 for inspecting PV panels.
“For thermography in particular, we need specific weather conditions,” Hinsley says. As well as being in direct sunlight, the panels must be subject to an irradiance level of greater than 600 W/m2 in low wind speeds and minimal cloud, he adds.
“Once on site, measurements of temperature, humidity, wind speed and irradiance are recorded and logged for use when processing the data. For PV panels in particular, we are looking for temperature anomalies at the cell and module levels. Certain faults will display a particular pattern, which helps to identify any issues causing the panels’ performance to be reduced.”
Camera mutuality
The cameras are used together so that each IR image has a corresponding visual image, while each IR picture is assessed in sequence to reveal thermal anomalies such as hotspots, dirt, damage, string errors, diode issues and faults in individual cells. The images are also paired in this way because it is quite easy to misinterpret an IR image, and the visible camera provides an alternative view that can be used for corroboration.
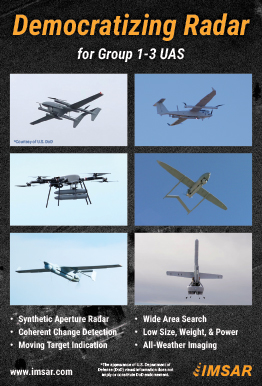
“On the visual image we can also check for dirt, bird droppings, debris or physical damage,” Hinsley explains. “For example, the IR image might show a large hotspot that could be diagnosed as a cell fault, but the visual image might reveal that this is due to bird droppings, and the panel simply needs cleaning.”
As it was relatively simple, the Bleasdale job was carried out by Hinsley alone, who operated both the UAV and the cameras. “We can have a second camera operator if required for a more complex environment,” he says.
As the Bleasdale job was also small, Hinsley flew it manually. For more complex missions, such as surveys of large solar farms, the DJI Pilot 2 software in the Android-based hand controller provides a powerful planning function.
“We can use Google Earth Pro to plan the flight and then import it into the controller,” he says “We tell the Pilot 2 software the camera we are using, the flight altitude and the level of detail we want to capture, and it can then plan the automated flight for us.”
In addition to the UAV and its GCS, the operator brings a package of support equipment to the job site. “We carry spare batteries, a generator and charging equipment, spare propellers and basic tools, plus a laptop and various cables so we can deal with any technical issues if they arise – and they usually do,” Hinsley says. “In addition, we carry signs, cones, a fire extinguisher and a first aid kit, just in case.”
At the hall, the owner granted DroneWorks access to the building, to enable it to check ancillary solar power system components such as the meter and the inverter. Readings from the latter showed that one string of PV panels was generating much less power than the other, Hinsley says, and interpretation of the UAV’s imagery would help to work out why.
Preparing the UAV for the mission involved allowing it to warm up and run through its pre-flight checks, while Hinsley set up instruments to collect the essential temperature, irradiance, humidity and other environmental information.
The flight itself took about 15 minutes and used up about half the battery capacity. The priority was to cover all the panels with both cameras, ensuring that they were all imaged both from high level to show overall patterns and in close-up to reveal small details.
“Both data collection and analysis rely on a knowledge of thermography,” Hinsley says. “The price of thermal imaging equipment is coming down, but you can easily capture images incorrectly and misinterpret them if you do not have the relevant training and experience.”
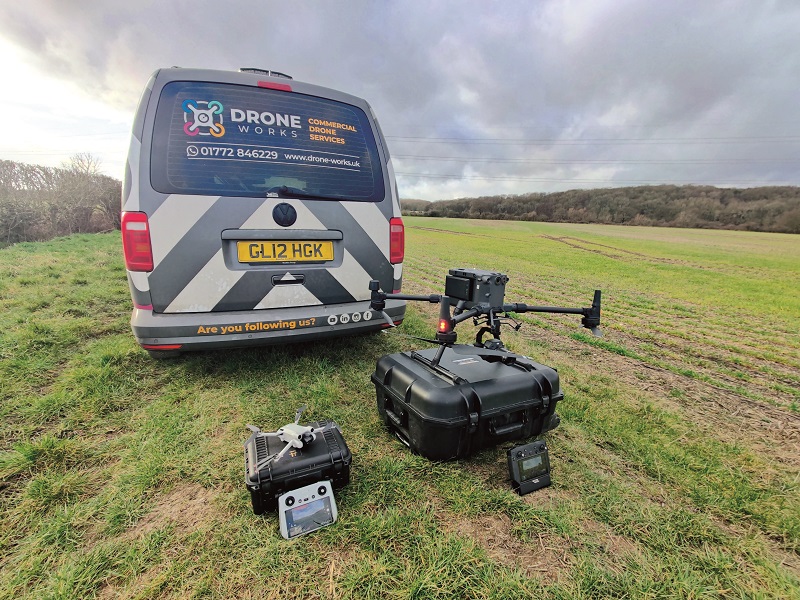
Post-flight processing
Alongside thermographic cameras, the associated image processing software is continually improving, with recent developments enhancing productivity, for example. “The ability to thermally tune and batch-process images is a big time-saver on larger sites,” Hinsley says.
DroneWorks used Teledyne FLIR’s Thermal Studio suite to assess the Bleasdale images. According to FLIR, the software supports any camera that generates images in radiometric JPEG format.
FLIR describes Thermal Studio as analysis and reporting software designed to help thermographers manage thousands of thermal and visual stills and videos, whether they were taken using handheld or UAV-mounted cameras, providing automation and processing capabilities to streamline the workflow.
Batch processing, for example, enables the user to prepare thousands of images at once, while the software’s image editing suite includes zoom and pan functions, colour palette changes, measurement tools, and automatic adjustment of temperature scales, annotations and so on.
Thermal Studio also helps with the creation of reports tailored to each customer by providing predefined and custom templates, with drag-and-drop functionality with which the user can add hundreds of images to the report with one action. It also exports reports in XPS spreadsheet or PDF format without the need for additional software such as Microsoft Office. Further, a video editing function allows inspection highlights to be shared.
However, there are still hardware/software compatibility issues that remain unresolved, Hinsley notes. “Software is dependent on the equipment used,” he says. “For example, an image taken with a FLIR camera cannot be used with Fluke software.”
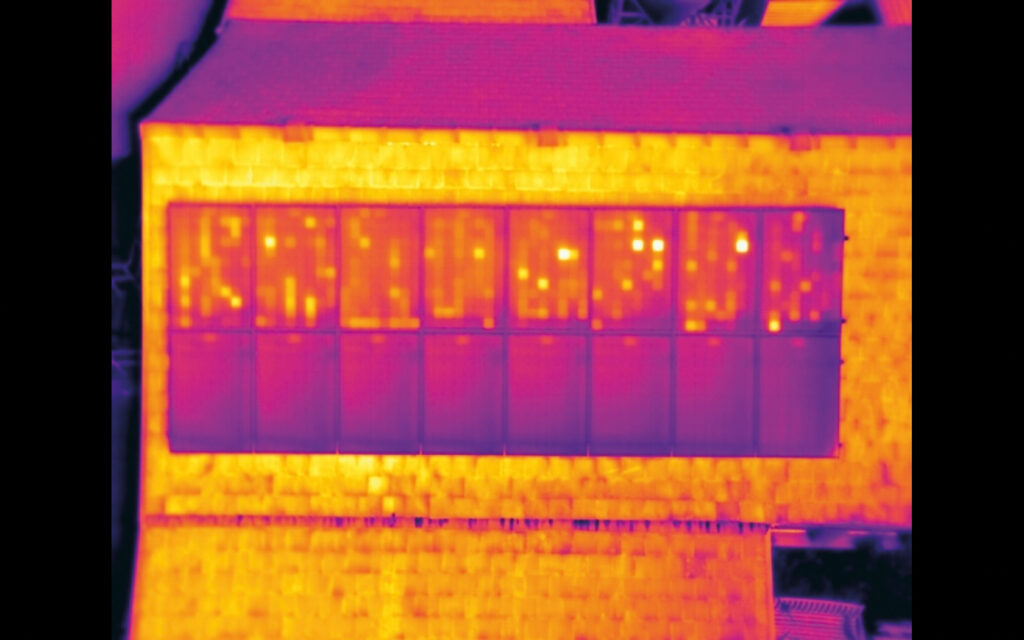
The UAV flight confirmed that the main problem at Bleasdale was that one whole string of modules – amounting to half the array – was faulty, causing a 50% loss in performance, Hinsley says.
Short-circuit chessboard
What the IR imagery revealed was a characteristic chessboard pattern of hot elements in the affected modules, indicating that they were in short-circuit. Probable causes include connector or wiring problems between the modules and the inverter or something more serious, such as potential-induced degradation (PID), he notes.
PID is caused by current leakage that develops over time from the PV cell through its encapsulant to the frame, resulting from a high negative potential difference (voltage) between them.
“We recommended starting with investigating the cheapest likely cause – the wiring and/or connectors – and working up to replacing the modules themselves, which would be the last resort,” Hinsley says.
DroneWorks emphasises that, if the schedule allows, data is analysed at the office on the day of the inspection, or the day after. The company likes to provide a quick turnaround because fast, accurate data collection is one of the key selling points that UAV inspection has over more conventional methods.
DroneWorks provided Bleasdale with a detailed report, along with the images, findings and comments, Hinsley says, to be used as a starting point for a PV installation company to investigate further. He adds that DroneWorks can also carry out more in-depth tests to pinpoint the issue if required.
Innovate or stagnate
In the 3 years since DroneWorks started its inspection business, the company’s equipment and software have evolved.
“For example, drone technology has advanced quickly,” Hinsley says. “We now cover more and larger sites, and provide more data, in higher quality than on day one.”
Naturally, that means DroneWorks is not wedded to one model of UAV, and since the Bleasdale job it has been using the newer DJI M300 RTK. It is a more capable family of vehicles, and replaces the now discontinued M200 series.
“With the correct sensor, the M300 can be tasked with covering most aspects of our work, such as large-area land surveys, high-resolution building inspections and creating digital twins,” Hinsley says.
The M300 RTK is a larger and more powerful electric quadcopter than the M210, with a maximum take-off weight of 9 kg, a payload of about 2.7 kg and a maximum flight time of 55 minutes. It comes with obstacle avoidance systems including time-of-flight lasers, and can support up to three payloads simultaneously.
Its primary payload is the Zenmuse H20T, a stabilised quad-sensor unit with a wide-angle camera, a zoom camera, a laser rangefinder and a radiometric thermal camera.
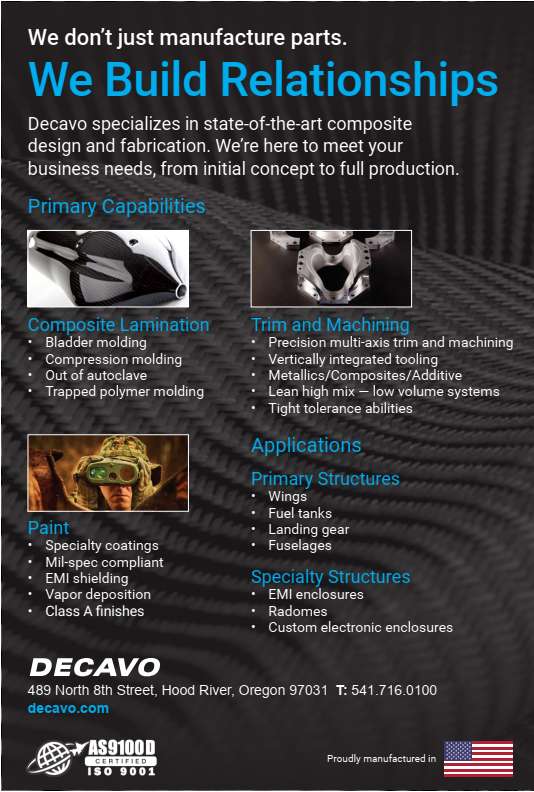
Local diplomacy
Carrying out this kind of inspection mission, particularly near people’s homes, often attracts interest, which sometimes requires some delicate diplomacy, Hinsley notes, but perceptions are changing. “Initially, the general public and industry perceived drones as toys, and were not aware of the solutions and services possible,” he says.
“Also, many people see drones in a negative light due to privacy concerns.
“I have had a handful of confrontations over the past few years, mainly where land or property owners believed we were ‘spying’ or doing something untoward. There is also a lack of knowledge of the rules and regulations, which occasionally leads to friction.
“However, as drones used as tools for commercial reasons become more common, most people we meet are genuinely interested in the things we can do with them once we have explained what we are actually doing.”
Looking to the future, he expects to build on the efficiency that using UAVs for thermography brings, covering larger sites more quickly than traditional thermography techniques allow.
“With that in mind, I expect to be inspecting more and larger commercial buildings and solar panel installations,” he says.
“With the current energy crisis, more and more businesses will be installing solar panels on their roofs, and it is recommended that they are inspected annually to ensure they are performing as expected.
“Doing that with drones is quick, safe and removes the need for costly scaffolding or cherry-pickers.”
UPCOMING EVENTS
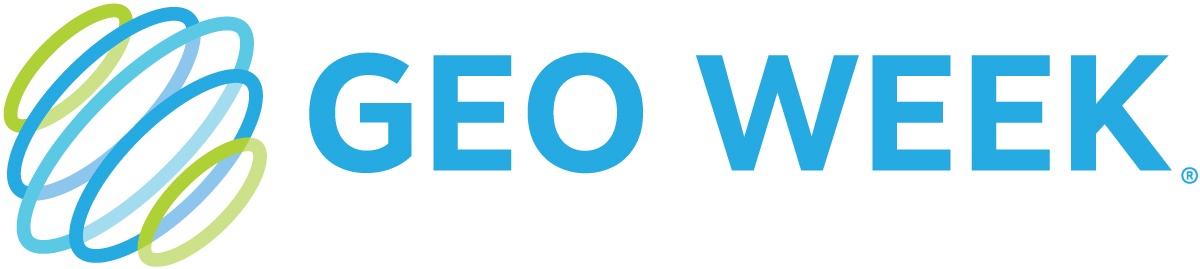
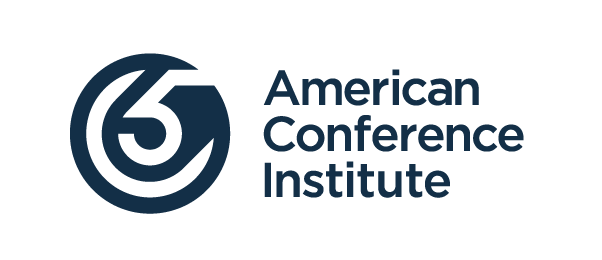
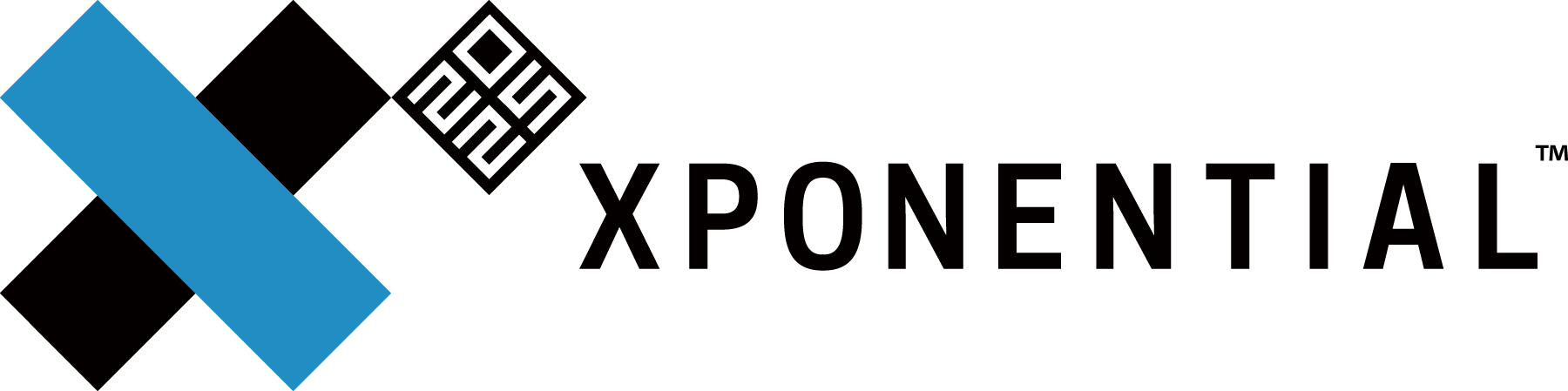
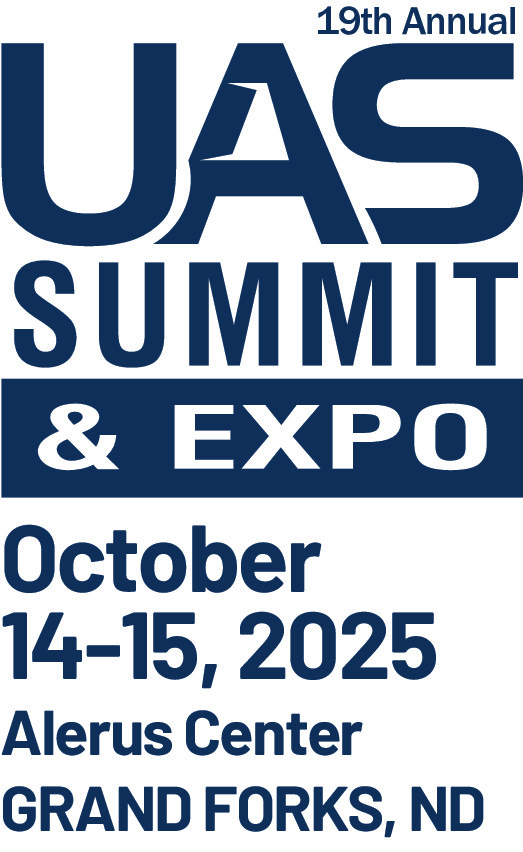
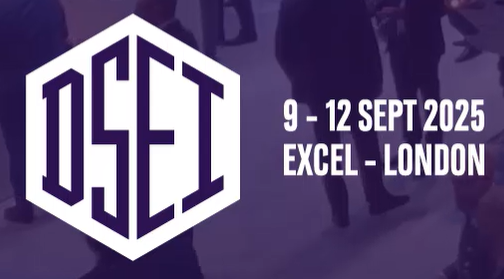
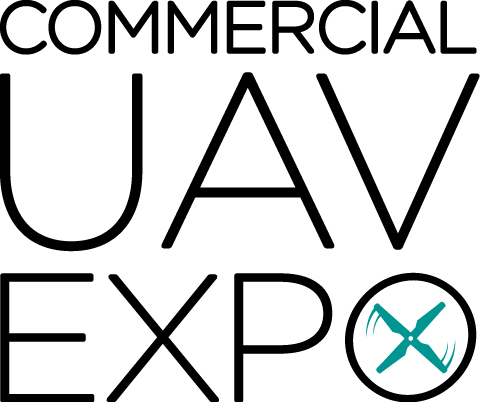
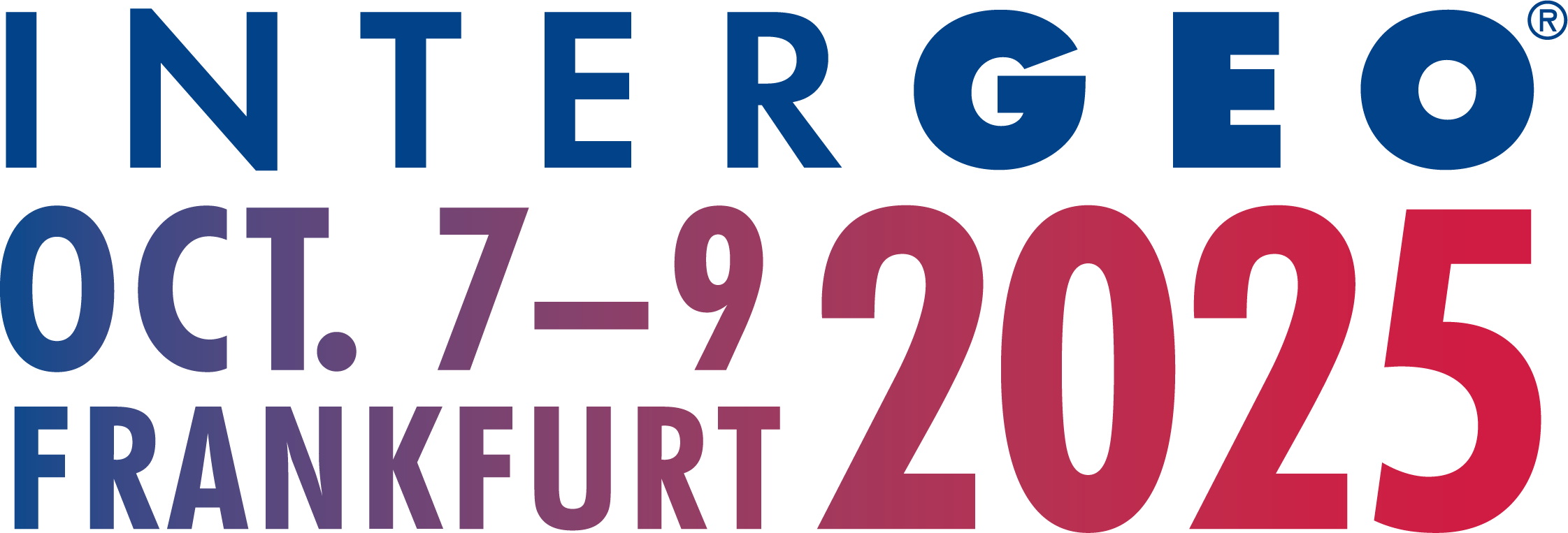
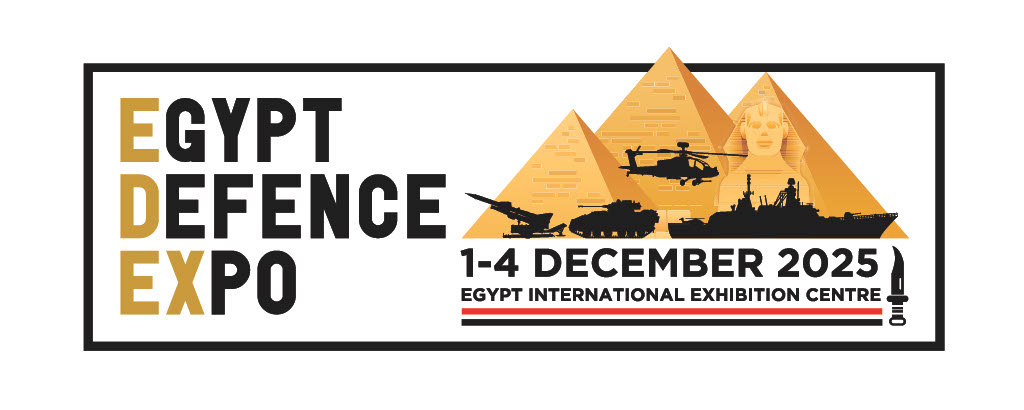
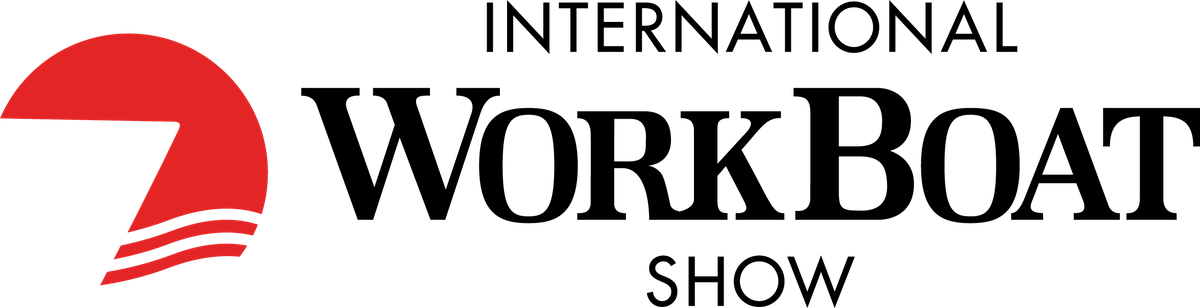
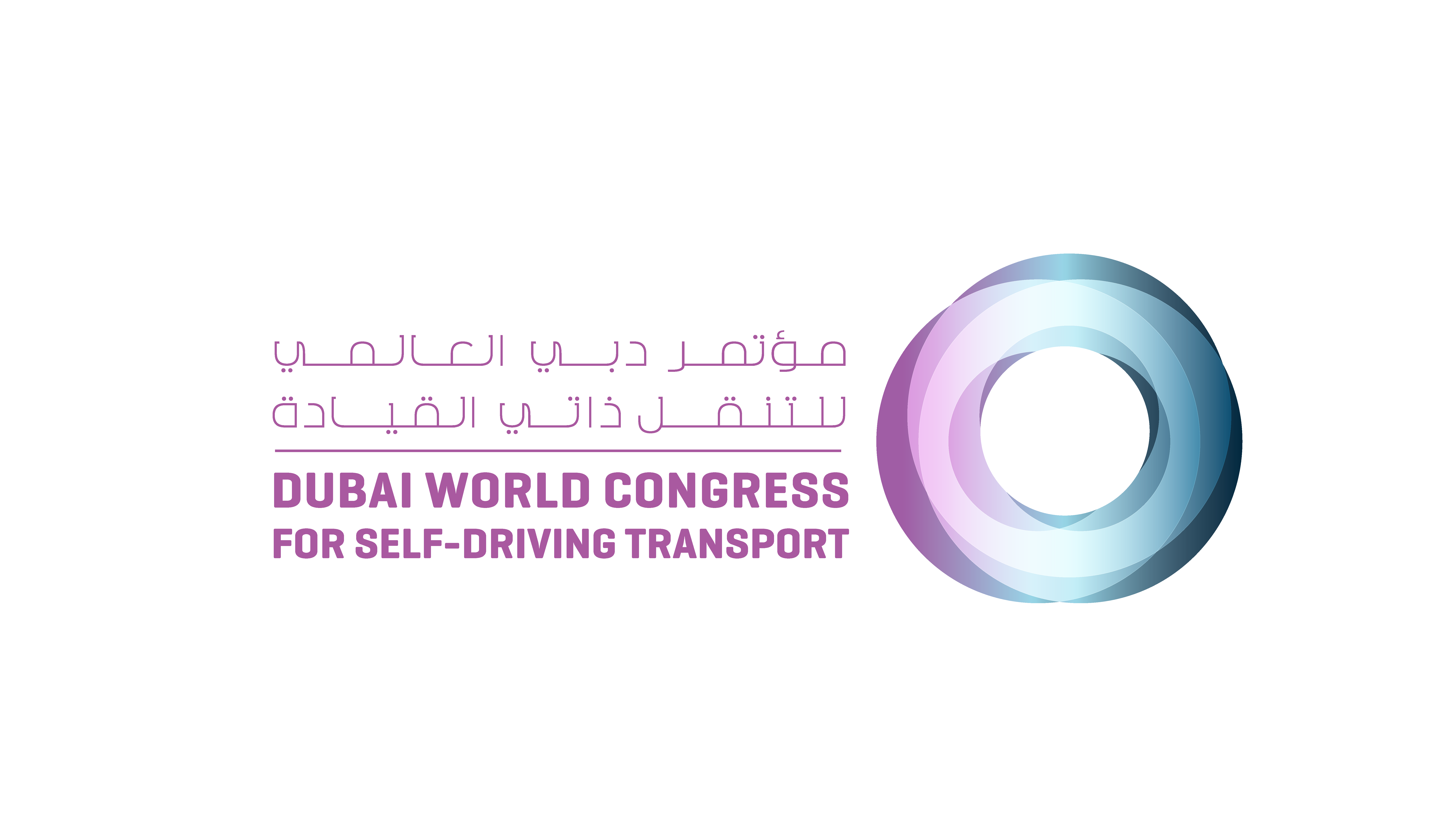
