SkyPower’s SP engines
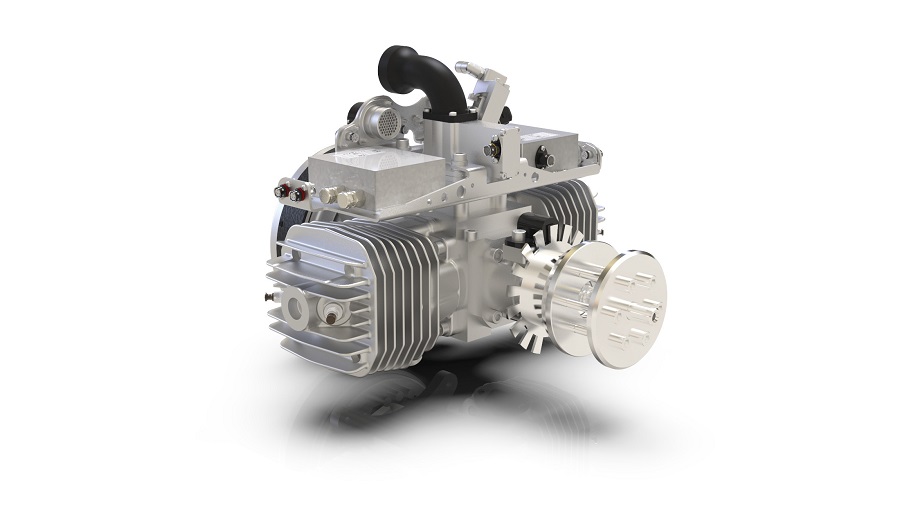
Rory Jackson finds out how this company is offering engines with common components to suit different UAV types
The UAV industry offers many types of aircraft configurations, from the tilt-wing system featured in our Dufour Aerospace digest (page 48) to tilt-rotors, multi-rotors, fixed-wing/quadrotor hybrids, tail-sitters, catapult-launched systems and so on.
Each comes with its own scaling and integration considerations for powertrains. For UAVs sized for small, two-stroke IC engines for example, a catapult-launched UAV’s engine will suffer far higher g-forces and mechanical loads than other types, whereas a multi-rotor will undergo minimal g-forces but need very high electrical output and active thermal management.
Systems integrators can therefore struggle to find their optimum powertrain configuration. Ideal figures for parameters such as the engine’s displacement, maximum continuous power output and weight can change depending on factors such as end-users’ MTOWs, mission CONOPS and the particulars of their airframe.
Naturally, those factors might also need to be altered for each customer, which could then alter the engine’s safety, fuel efficiency and many other performance parameters or integration considerations. That can mean choosing between running a sub-optimal engine or finding a new engine supplier.
Such a choice could be avoided however through modularity and commonality of engine parts. In theory, if an engine manufacturer offered common or easily interchanged components, UAV manufacturers and technicians could quickly reconfigure powertrains for different missions, instead of switching to an entirely different engine.
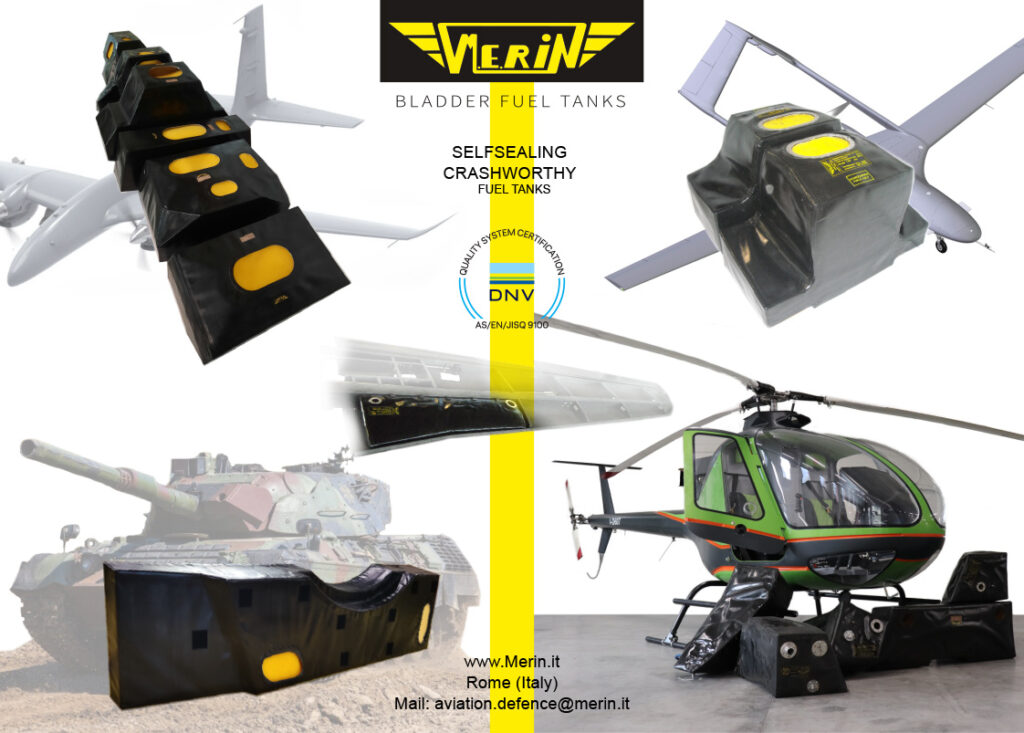
One UAV engine developer, Sky Power, has taken this approach, which has been applied to four of its engines – the SP-110, 170, 210 and 275. These share ancillary components and commonalities across their designs, such that any UAV using one of them could be swapped for one of the others.
“If the end-user isn’t 100% sure of their UAV’s MTOW, or of their other physical or performance parameters, or the exact kinds of missions they’ll be flying, we tell them to ‘go one engine bigger’,” says Karsten Schudt of Sky Power.
“Most customers just consider dry engine weight, rather than wet weight, and go a little too small. That means they could spend most flight hours operating between 90% and 100% of the engine’s load, so fuel consumption goes up and their TBO goes down.
“Picking an engine with a higher dry weight can mean a lower SFC for their required power output, hence less onboard fuel and a lower total wet weight than if they’d gone for an engine with a lower dry weight. Multiple engines can be optimal for a UAV in different ways.”
All four engines are spark-ignited two-strokes built as twin-cylinder boxers, air-cooled, lubricated by pre-mixing, and running on gasoline, with the designation for each coming from its total displacement in cubic centimetres.
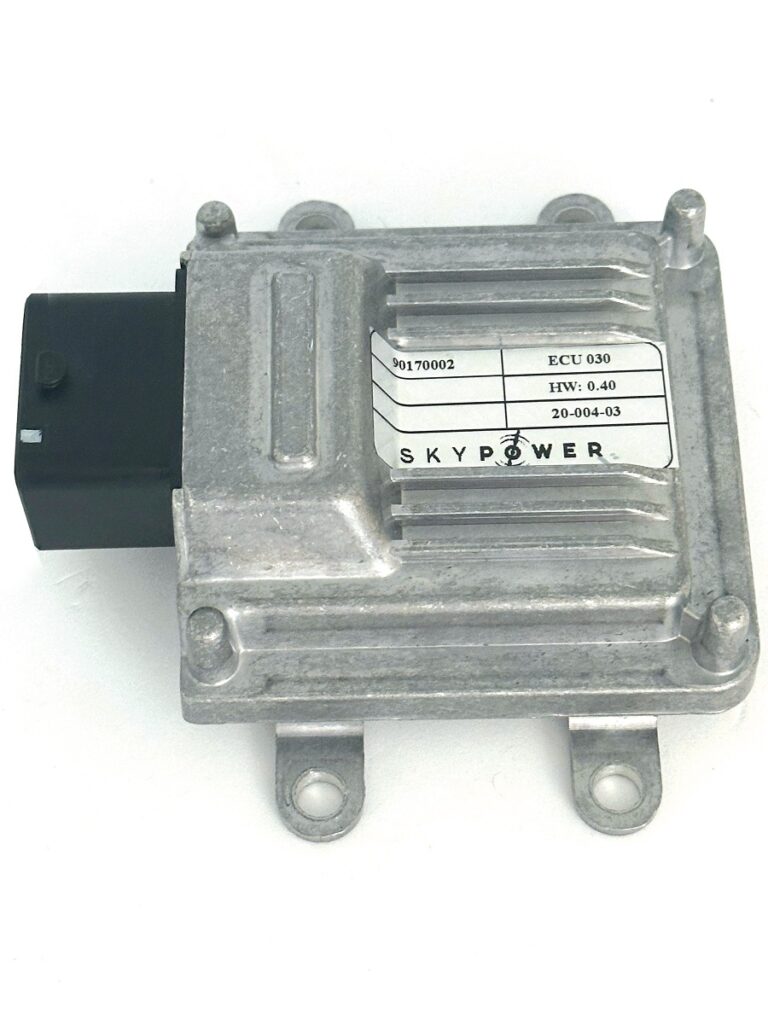
Ancillary engine systems
All four engines are managed via an ECU based on a 32-bit microprocessor with 512 kbytes of flash memory and 96 kbytes of RAM. Its IP50 housing measures 115.2 x 82.5 x 31.6 mm, which enables it to operate in temperatures from -45 C to +80 oC.
Its CAN bus has a baud rate of 500 kbit/s and enables persistent diagnostic feedback and monitoring of critical health-related parameters. These include crankshaft rpm, measured by a Hall or inductive sensor, throttle valve width as measured by a potentiometer, exhaust gas temperature, intake manifold air temperature, manifold absolute pressure, cylinder head temperature and generator temperature.
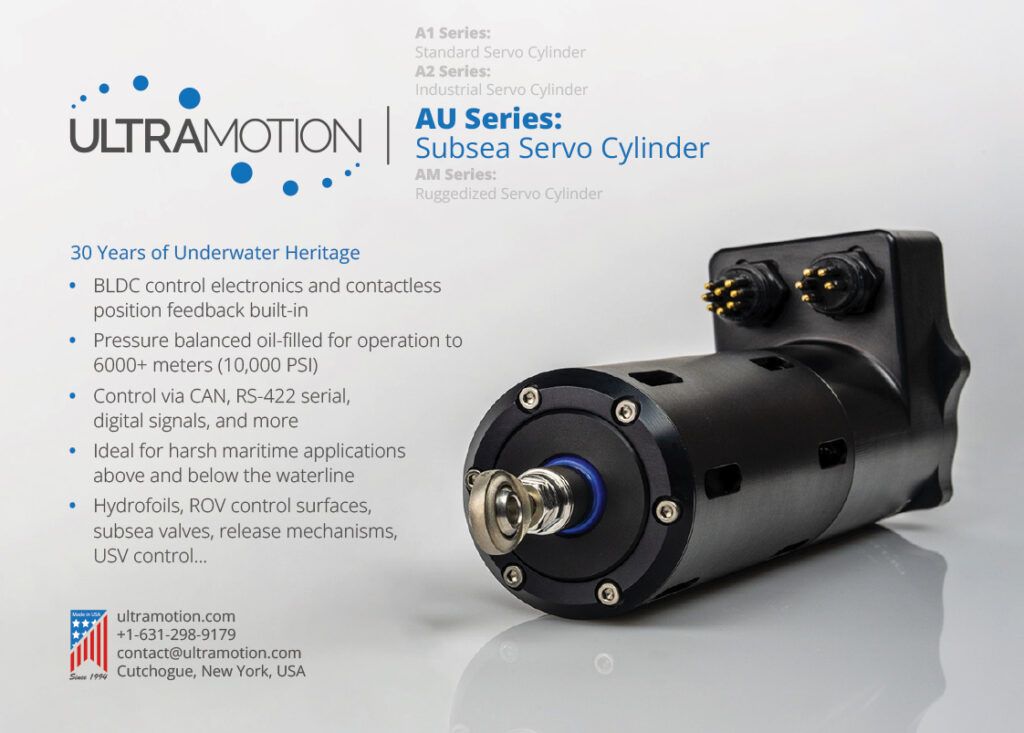
The ECU is also programmed for tracking parameters such as coolant water temperature or camshaft speed in Sky Power’s other engines.
“Having one ECU for all our engines means anyone with a fleet of different UAV models needs to program only the CAN comms between the autopilot and the ECU once. From then on they can swap the engines in an almost plug-and-play manner,” Schudt says.
The same models of throttle servos, fuel pumps and ignition plugs are used in all the engines, simplifying inventories and integration work compared with using different fuel and air components for each engine.
“We’ve also run tests with fuels of varying condition, to check for any mismatches between gasoline type or quality and the ECU mapping in terms of what power output you should get for the fuel you’re injecting – 95 octane won’t always be available where our users are operating,” Schudt says.
For fuel-oil mixing, Sky Power uses products from Aspen, particularly the pre-mixed Aspen 2 fuel solution at a 50:1 ratio. The Swedish company’s products are synthetic, alkylate fuel-oil mixtures, which it says are formulated in a proprietary manner to eliminate harmful components found in other fuel-oil mixtures to achieve a high purity and octane rating, as well a particularly clean burn, all useful qualities for small engines with a high power bandwidth.
Schudt adds that the engines exhibit the least carbon deposits inside the cylinder, on the piston and in the exhaust when running on Aspen’s fuel-oil mixtures, compared with any others the company has tried. That therefore contributes to all four engines having similar lifespan benefits from using the mixture; a 700-hour TBO is achieved when testing them with it.
Components and materials
Going deeper into the engines, differences between the engine parts begin to emerge, with crankshafts, cylinders and pistons being sized as appropriate for the various displacements and crankcase lengths of the four engines.
Looking closer, however, common metals and treatments can be found among these core parts of the engines. For instance, Sky Power points out that all the cylinders are coated internally with nickel silicon carbide, and the cooling fins surrounding them are designed to be as thin as possible – 1.6 mm thickness at absolute maximum – for optimal heat absorption and dissipation.
Each cylinder is cast from aluminium as a single piece with the head, with up to four transfer ports depending on factors such as fuel types, altitude and cost. Schudt notes that casting the complete cylinder as a single piece is a more complicated process than casting the head and body separately, but the result is a lower overall weight than if they were made separately and then attached with screws, as well as then needing gaskets between body and head.
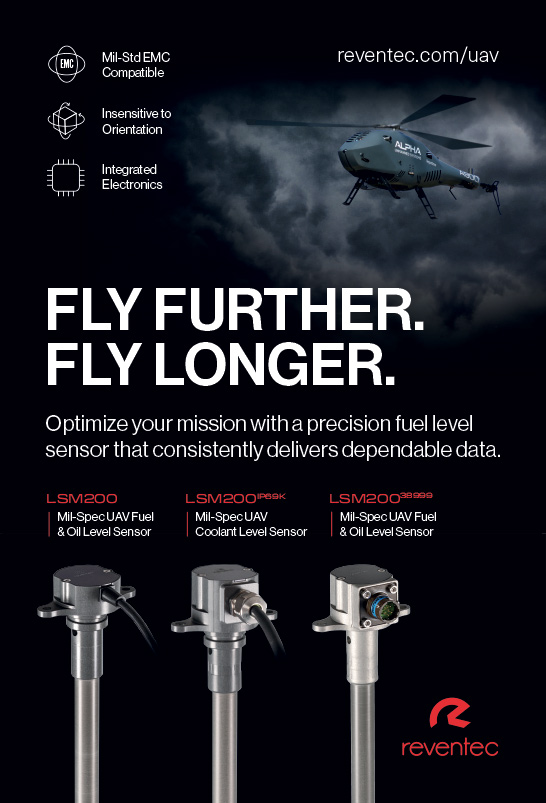
In addition, a heat transfer from head to body is faster and more complete, owing to the absence of any physical separation between top and bottom.
“It’s impossible to get the transfer ports through CNC machining for now. It would lead to really sharp edges instead of smooth channels, and airflow from the crankcase for efficient scavenging depends on that, while additive manufacturing comes with too many cost and optimisation problems for the time being,” Schudt notes.
The crankcases are CNC-machined from EN AW 5083 aluminium, and the reconfigurable nature of CNC machinery (unlike casting moulds) means end-users can have different customisations added, such as mounting points for gear or belt wheels to drive ancillaries.
Each crankshaft is forged from 1.5918 (15CrNi6) case-hardened 62 HRC steel as seven separate pieces (including the con rods) before being CNC-machined to their exact tolerances. After that, they are heat-treated, then pressed together into the complete shaft, with the single-piece con rods mounted on their crank pins.
The crank sits in four ball bearings (the only exception being the SP-275 TS CR, which has three ball bearings holding its crankshaft). The bearings are sealed, deep-groove designs to prevent fuel leaks or incomplete compression between sections of the crankcase.
The con rods are forged from the same case hardened steel as the crank, and run using needle bearings. Meanwhile, the pistons are cast from aluminium alloy JIS H5202, grade AC9A, with T6 tempering.
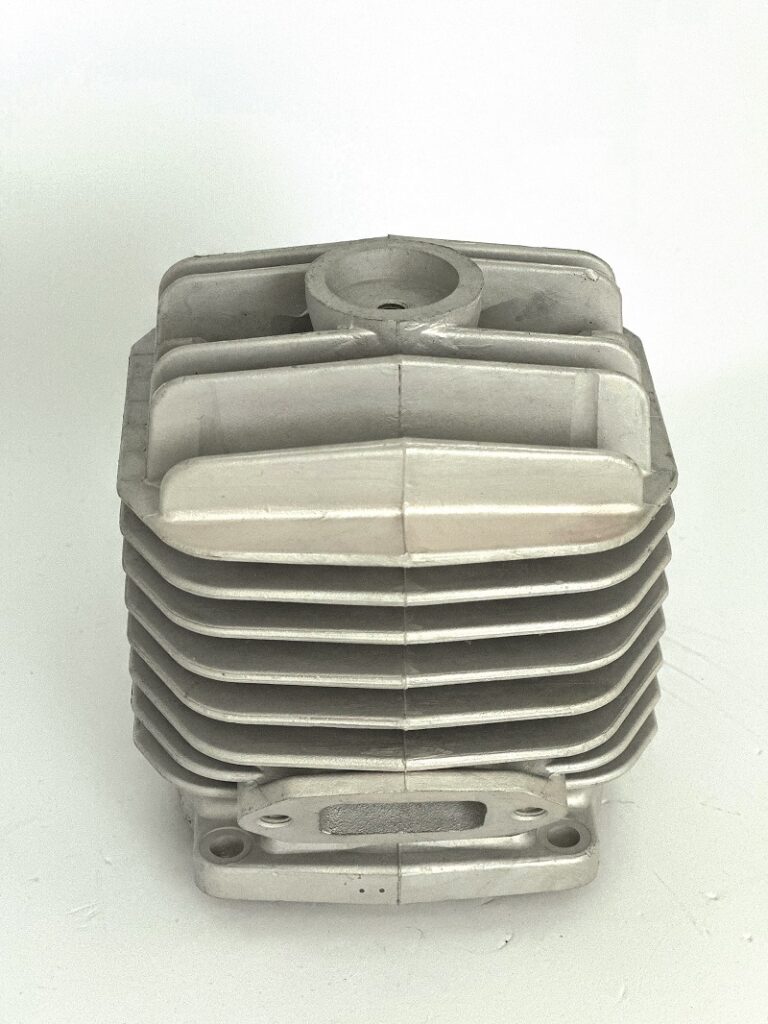
Hybridisation
Electrifying an engine line can be difficult to offer a commonality of parts for, as different UAVs and missions could theoretically need widely differing levels of electric power and sizes of motor/generator.
Sky Power’s approach however has been to develop what it sees as a one-size-fits-all (albeit customisable) set of hybrid components. It reasons that most UAV manufacturers want a growing amount of electric power from their powertrains, and those who don’t can scale what is effectively the regenerative braking of the starter/generator via its controller, the SGC-352.
The SGC-352 weighs 500 g, and can be set to operate in various modes depending on a UAV’s operational requirements. These include three modes for generating electric power, a battery charging mode for replenishing energy as quickly as possible, a battery current control mode, a phase current control mode, an rpm control mode, and naturally an engine starting mode.
In principle, the system operates as an ESC for the starter/generator (the SG151) via trapezoidal 120o block commutation, with Hall effect sensors for close position tracking and speed control. Its enclosure is IP64-rated, for sealing against dust ingress, and protection (if not fully sealing) from water spray in any direction. It enables the SGC to function in temperatures from -40 to +85 oC.
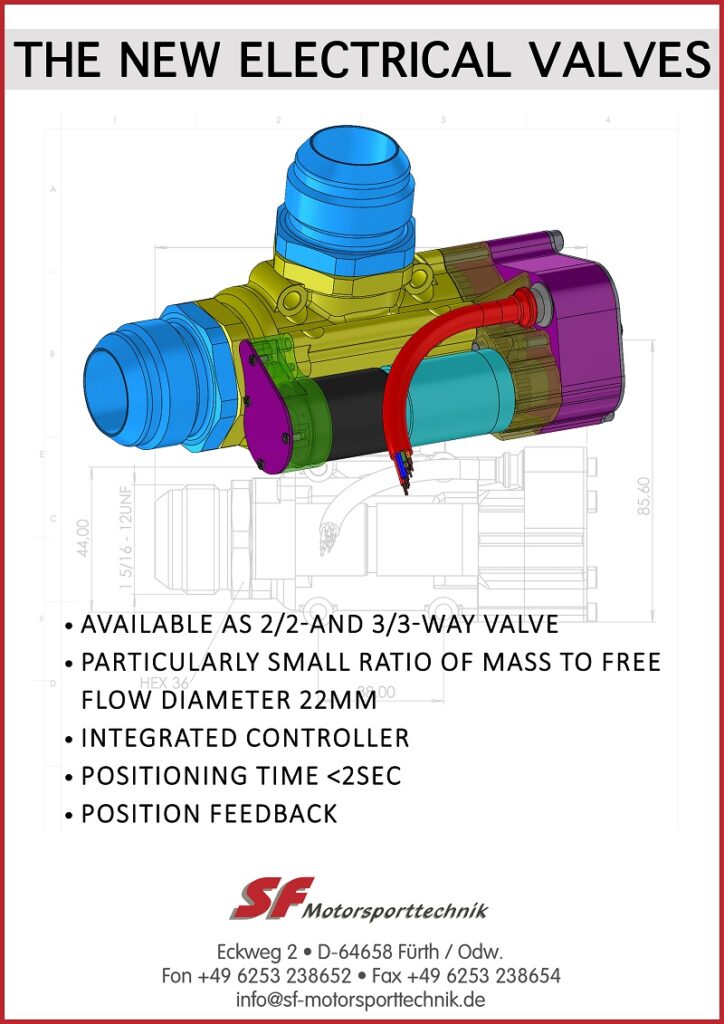
It produces power at a standard voltage of 48 V, although that can vary up to 75 V or down to 20 V. 100 A of phase current is typically produced, although peaks of up to 350 A are possible.
Upon receiving a specific starting trigger signal from the autopilot over the CAN bus, the ECU executes a start function that commands the SGC 352 to trigger a load in the starter/generator for drawing a control current (the exact values for that current being mapped in the SGC 352). Notably, the starting function can only be executed if the system is stopped – that is, if the rpm sensor reads the engine speed as zero.
“Starting electrically this way means there’s no accidental engine starting caused by, say, a maintenance technician accidentally grabbing or flipping a propeller blade,” Schudt adds.
Battery recharging is managed using a charge current map that induces current in the windings proportional to the crank speed and shaft power. The output current therefore matches whatever engine the SGC and SG151 are installed on without reconfiguring.
For example, when the SP-210 is running 3000 rpm and outputting 4 bhp of shaft power, the SG151 produces 1 kW of electric power and 20 A of current. At 4500 rpm and 7 bhp, 2.4 kW and 50 A are generated, these being the maximum continuous electricity outputs for safe recharging. The mapping can be changed for different requirements, although that might come with a risk of overcharging and damage to the batteries.
Also, a few thermal limiter functions are written into the controller to prevent damage to the engine or starter/generator from overheating. For instance, if the CHT sensor reads 180 oC or higher, the maximum allowed load in the battery will be reduced as needed, to scale back the burden on the engine from the generator and hence allow the cylinder head to cool.
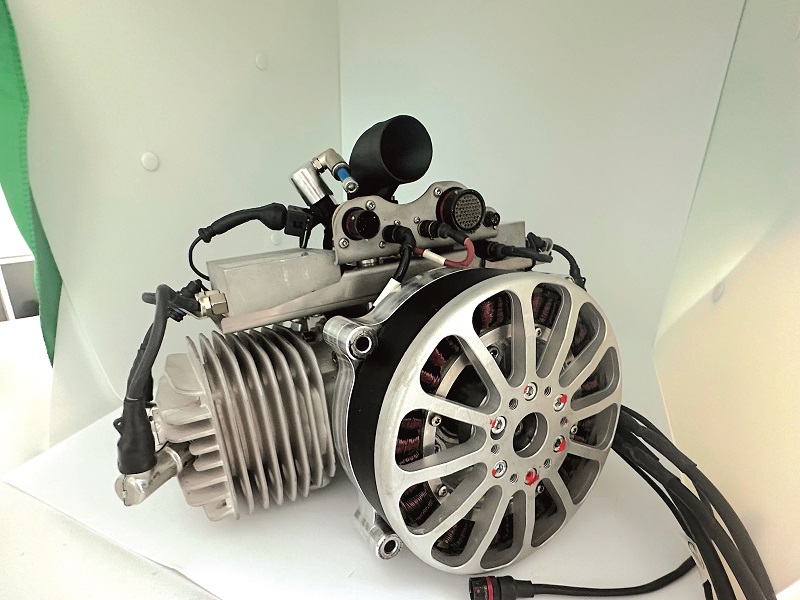
Integration
Despite all these commonalities, some limitations exist as to how far identical components can be designed or supplied for different UAVs. Sky Power says exhaust pipes and mounting brackets most often need to be tailored for the end-user’s airframe.
The exhaust system will be routed differently depending on the integrator’s preference for the routing and discharge of exhaust gases, and noise suppression around the hull, and depends particularly on the location of the engine.
Design of the mounting plate is dictated by a combination of CAD files of the UAV showing its engine bay and the downstream propeller selection, the latter having a strong impact on the momentum and vibration of the engine.
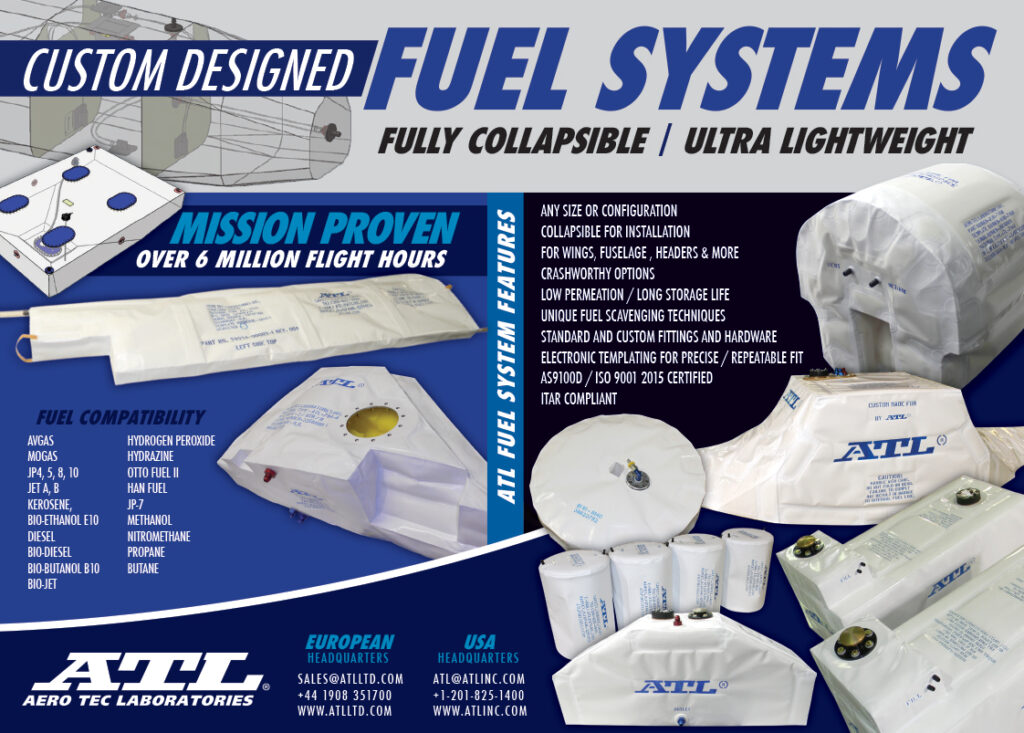
“Producing the mounting systems is a trade-off between strength, weight, cost and lead times. The brackets and dampers are always CNC-machined aluminium, which allows flexible design and adjustment to each engine and UAV,” Schudt says. “And the g-forces of a catapult-launched aircraft will typically imply the strongest, heaviest kind of bracket we make, with the highest number of connection points.
“Before that, we’ll additively print the design and perform initial integration and practical checks. We’ve found plenty of times that a bracket or plate that works great on paper is impossible to mount in practice, because of tiny details like a lack of space for inserting screws into the firewall.”
Summary
Limitations aside, Sky Power says parts commonality in engines brings benefits to UAV manufacturers and operators including fuel efficiency, inventory management, and maintenance.
That said, the question arises as to whether an engine company could exploit this sort of approach to components with engines more complex than two-strokes. Makers of four-strokes for instance, with their camshafts and valvetrains, or Wankels with their unique sealing and cooling considerations, might struggle with reducing the variations in these sorts of parts between engine sizes.
But with Sky Power also developing its SP-360 DRE (dual rotor engine) and SP-540 TRE (triple rotor engine) as modular expansions of the SP-180 SRE (featured in issue 25, April/May 2019), a precedent is being set for multiple ‘different’ Wankels using common rotors, apex seals and so on.
Naturally, Sky Power would also benefit from not complicating its manufacturing lines and inventories with new parts for new engines. And given the UAV industry’s tendency to order small batches of high-end subsystems, other engine manufacturers – and indeed of other components – can be expected to find ways of adopting this approach to its products.
UPCOMING EVENTS
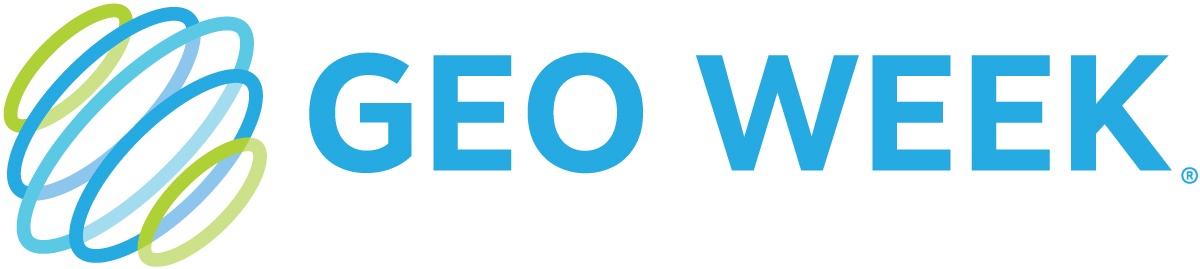
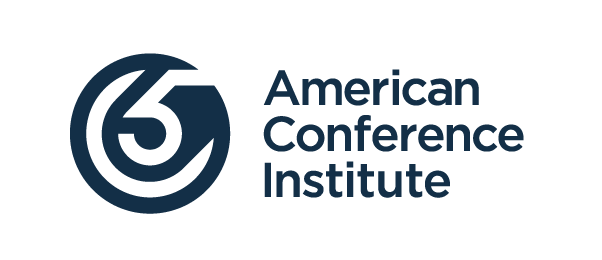
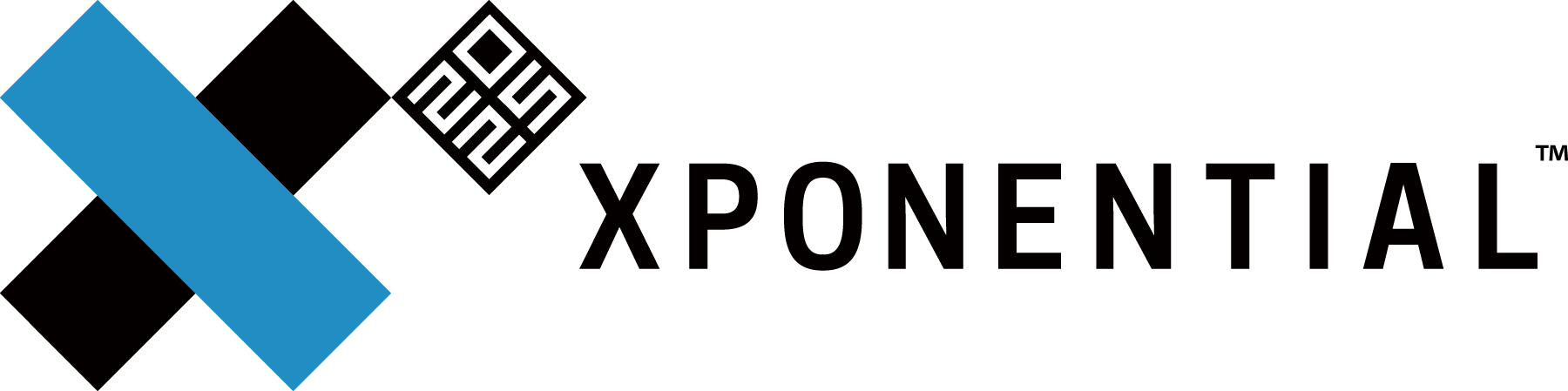
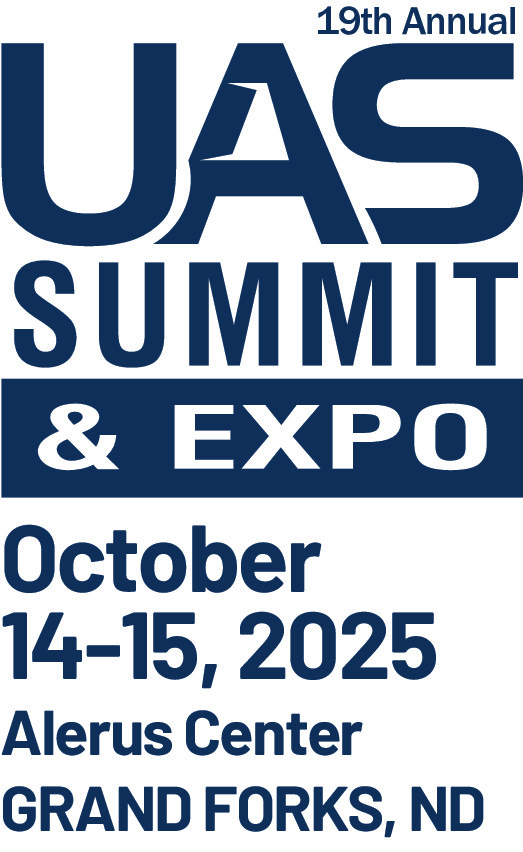
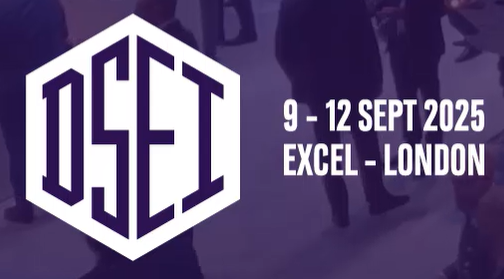
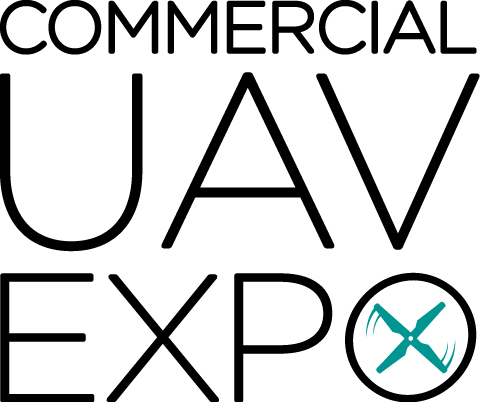
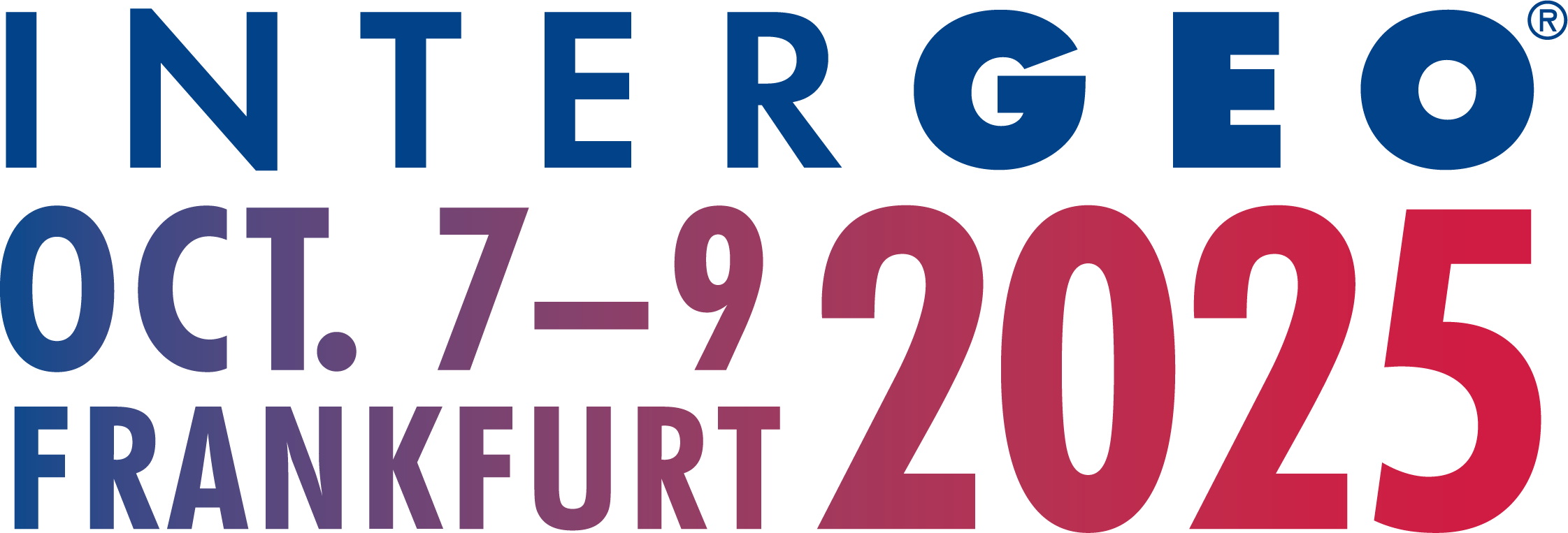
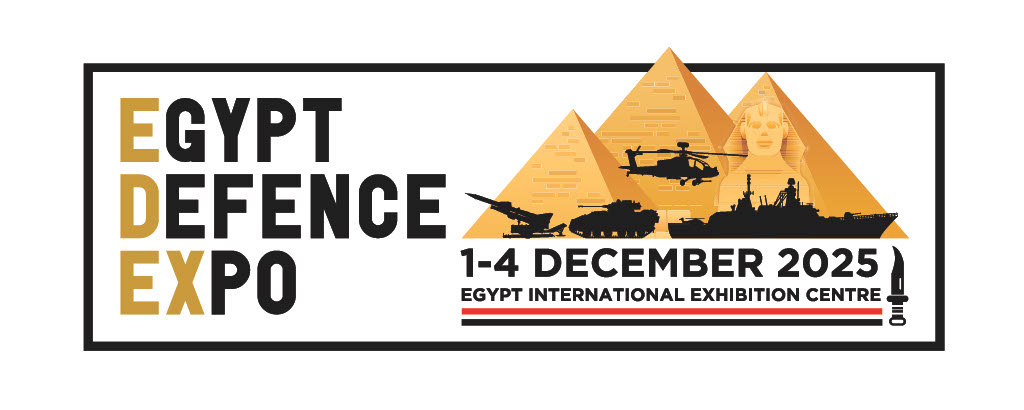
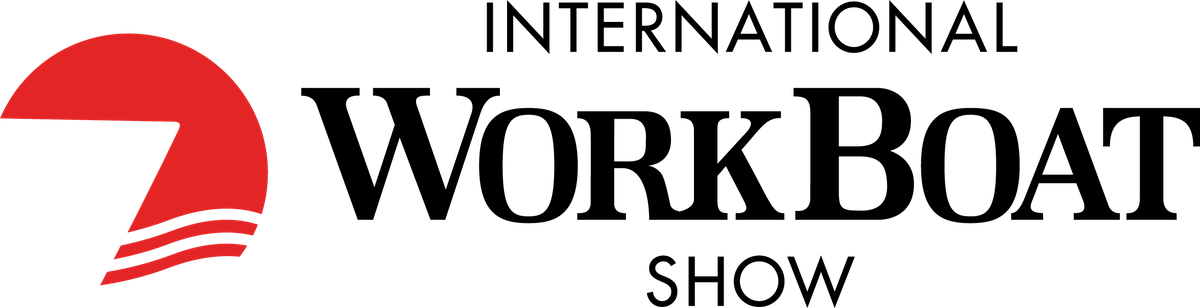
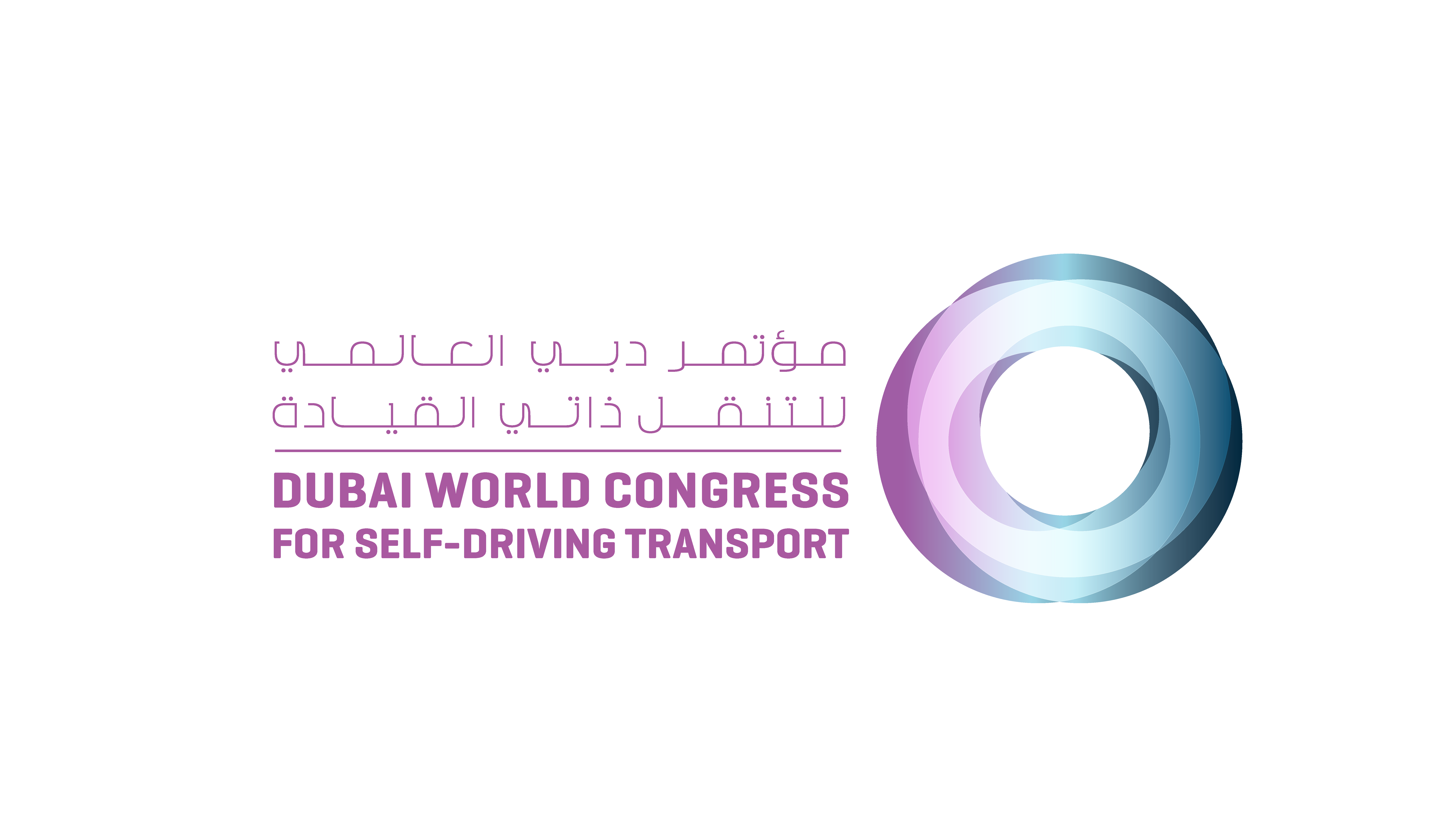
