Primoco One 150
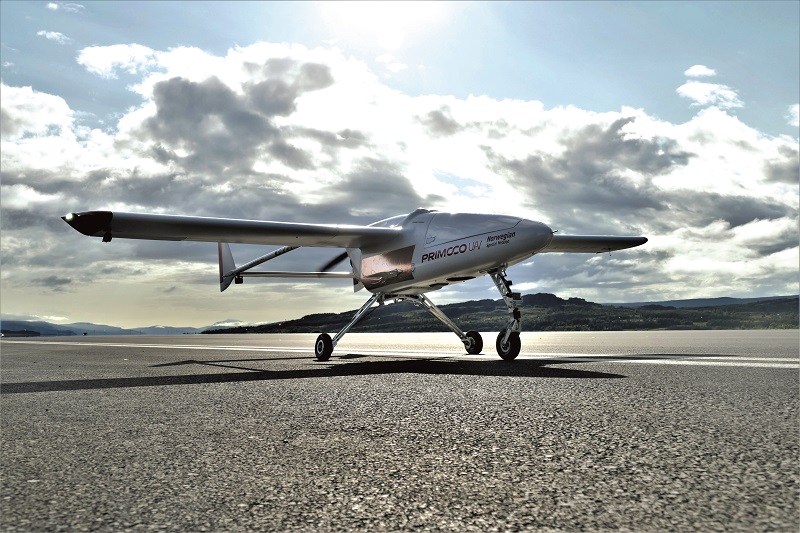
Rory Jackson looks at how making this UAV comply with a raft of NATO standards is paying dividends in its use for military missions
Cleared for take-off
To invest time and resources in developing a UAV weighing 150 kg purely out of a passion for aviation might seem like madness. To do so anyway, and make one of the most successful and highly certified autonomous aircraft flying some of the most dangerous missions on Earth might be branded as the madness of genius.
That though is what Czech entrepreneur and aviator Ladislav Semetkovsky has done since founding Primoco in 2015. He had previously been a private pilot but longed to design and produce an aircraft of his own.
Primoco principally targeted pipeline inspections as its entry market; many commented at the time that UAVs were bound to replace helicopters there. But as military and civil certifications soon became higher priorities, he and his team agreed that it made no sense to market a UAV unless flying it was not only legal but straightforward in terms of the authorisations required.
As Jakub Fojtik, VP of business development at Primoco, recounts, “It was originally planned as a 50 kg UAV, but the concept was iterated into bigger and bigger versions, until it reached the present 150 kg.”
Taking its name from its MTOW, the Primoco One 150 is a fixed-wing craft with a 4.85 m wingspan, a 30 kg payload capacity and up to 15 hours of flight. Its powertrain and aerodynamics enable a top speed of 150 kph, an operating range of 2000 km and a flight ceiling of 3300 m.
Fortuitously, when Primoco started engaging with military certification authorities in 2020, it discovered that 150 kg was in fact the maximum allowable weight in the NATO standard STANAG 4703 (the Type Certification for light UAS airworthiness most applicable to the One 150’s size and configuration).
“We were lucky that Ladislav didn’t try to make it heavier, or it would have needed a different STANAG meant for crewed aircraft – which would have driven our price way up,” Fojtik muses.
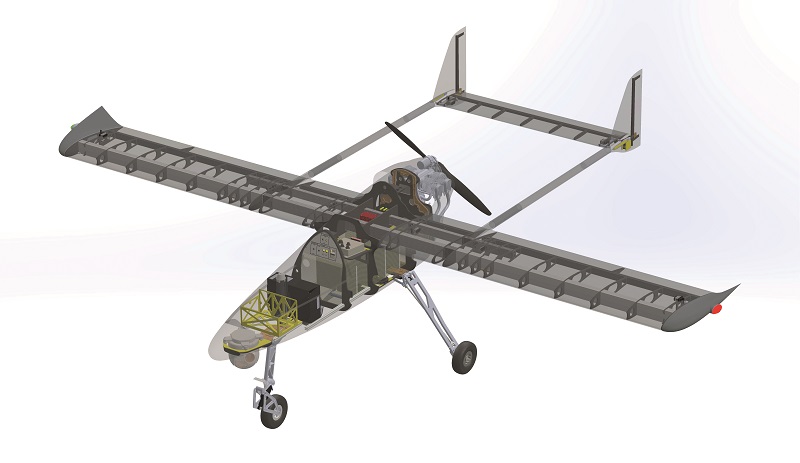
STANAG 4703
The One 150 is expected to receive STANAG 4703 certification soon, Primoco having made its design and production facilities and practices compliant with the European Military Airworthiness Requirement (EMAR) 21.
“The EMAR 21 certificates are a vital precursor to STANAG 4703,” Fojtik explains. “They set you apart in the defence market as a high-end UAV manufacturer.
“Complying with them forces you to remake your company from the ground up, to demonstrate to the standards authority that you have the proper engineering processes, proper tooling in the hands of properly trained people, flawless repeatability in production, all proven through seemingly endless testing.
“Overall, your factories must be as pristine as those of the world’s most successful aircraft OEMs. It required getting several associate professors of aeronautical sciences on the staff, but we’re certain that in 5 years it’ll be impossible to fly a military UAV in Europe without those certifications.”

Very few European UAS companies have been certified to EMAR 21 and STANAG 4703, with Sky Eye Systems’ Rapier X-25 (issue 40, October/November 2021) and the Thales Spy Ranger among them.
In 2022, Primoco also achieved its LUC (Light UAS Operator Certificate) for flying civilian operations in the EU, the first fixed-wing UAS manufacturer to do so. While most civilian UAV companies fly using a SORA (Specific Operational Risk Assessment) by declaring their mission intentions to aviation authorities, the application process is onerous and lengthy.
The LUC however allows Primoco to self-regulate its flights through internal paperwork and approvals, meaning civil tests and missions can be accomplished far quicker than under SORAs.
“I believe only six LUCs have been awarded across Europe, two of which are in Malta, where it’s relatively easy to get it due to strong government support for flight-testing UAVs in its ample clear airspace, and one of which is the Schiebel Camcopter,” Fojtik says. “Getting it also requires demonstrating very high levels of training, production testing and safety management – much like STANAG 4703.”
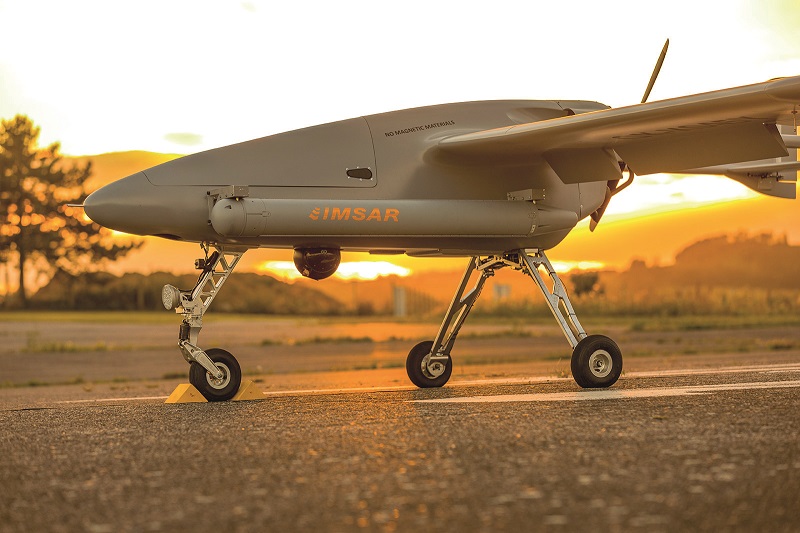
Testing for compliance
STANAG 4703 defines several thousand parameters regarding airworthiness for NATO military buyers. Validating these requires around 80 types of tests, including for EMC, power, performance and static strength, to demonstrate hard numbers on whether UAVs can handle extremely harsh use cases.
For instance, as Fojtik explains, “One test on airframe robustness had us lifting the tail by a chain with almost 200 kg of force, then yanking downward to the same degree, with the fuselage fastened in place to see how much bending force the twin booms could handle.
“If that much force actually happened in flight, no UAV could fly because the control surfaces would be smothered, but that’s just one of many ways the NATO regulators separate the wheat from the chaff. We’ve done countless other tests and broken several airframes along the way.”
While these tests have made pursuit of Type Certification long and costly, Primoco anticipates it will make getting European defence tenders easy in the long run, given that so few UAVs have such certification (and none have an MTOW close to Primoco’s). The options are few for any European NATO armed forces looking for a heavy UAS that can be deployed and operated without specific authorisation.
“In early 2022, we were asked by the German Army to perform a trial flight in non-segregated airspace over Ingolstadt Manching Airport, but they wanted us to do it under a civilian certification,” Fojtik recounts.
“We flew for several days using the LUC – we’d applied for a SORA, but our LUC came before it was processed – and that’s made our UAV the only one in its weight category to fly in Germany since civilian regulations came into effect.”
Just a few years ago, trying to fly in Germany using a Czech UAV with a Czech-granted certification would have been impossible, such is the scale of the change brought on by the LUC.
The One 150 captured a huge amount of test surveillance data, with extensive tracking of ground and air vehicles moving over Ingolstadt Manching (including a rare sighting of an Airbus Beluga in descent 10 km away), with 100% navigational accuracy.
“Although we flew on the LUC, most of our prospective customers are military-focused, particularly agencies responsible for border or coastal monitoring, intelligence and law enforcement, so the STANAG is still a primary focus,” Fojtik says.
As an indication of its capabilities, many units of the One 150 are currently flying in active war zones, the company having volunteered its assistance on a pro bono basis in at least one conflict. These are non-lethal operations including ISR and long-endurance missions through jammed and heavily contested airspace, and also over contested and occupied territories.
While the total number of One 150s in such service is classified, more than 100 units have been sold, including to customers in Europe and elsewhere.
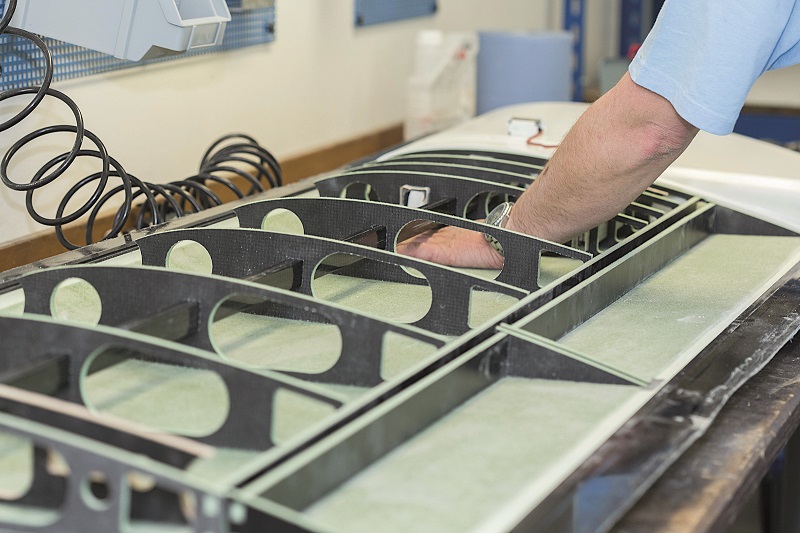
An almost-stealth aircraft
Fojtik describes the One 150’s engineering as “almost stealth aircraft” territory. Externally, the design looks conventional, with two high aspect-ratio fixed wings and a twin tail boom, both dimensioned with constant chord. It hence bears outward similarities to Baykar Tech’s Bayraktar TB2, and to the Leonardo Falco UAV (featured in issue 5, December 2015/January 2016) under Selex ES’ ownership.
The One 150 runs on the Primoco 340 engine, a 340 cc four-stroke, four cylinder, and is a notable departure in configuration, displacement and other respects from the Primoco 500 two-stroke we detailed in issue 17 (December 2017/January 2018).
The engine is integrated at the rear with a pusher propeller, with its exhaust routed into the propeller vortex so that hot gases are rapidly dissipated. That makes the UAV borderline undetectable to IR cameras, particularly when viewed from anywhere other than the rear.
“The four-stroke is also quieter than a two-stroke, so the acoustic signature is reduced compared to 2T-powered UAVs,” Fojtik adds.
The One 150’s small wingspan also makes its visual silhouette narrow enough that it cannot be seen with the naked eye from more than 1.5 km away.
Lastly, it is constructed from fibreglass composite, making it much harder to detect on radar than carbon composite. Combined, these properties give its operators enough confidence to fly over occupied or disputed territories in broad daylight.
In the front section of the fuselage, in order from front to back, are a payload bay for retractable gimbals, a recovery parachute enclosure, an electrical accumulator and power distribution box, as well as a second, more central payload bay. The middle section of the airframe has an avionics bay on top with the fuel tank underneath. The engine, alternator and propeller are mounted at the back, and the three landing gear arms and wheels integrate below the hull.
Payloads can also be installed on the fuselage’s sides – synthetic aperture radar (SAR) for instance must be side-mounted owing to its long, tubular shape – or mounted inside, with a balancing protocol in the autopilot software compensating if a particular integration upsets the centre of gravity (CoG).
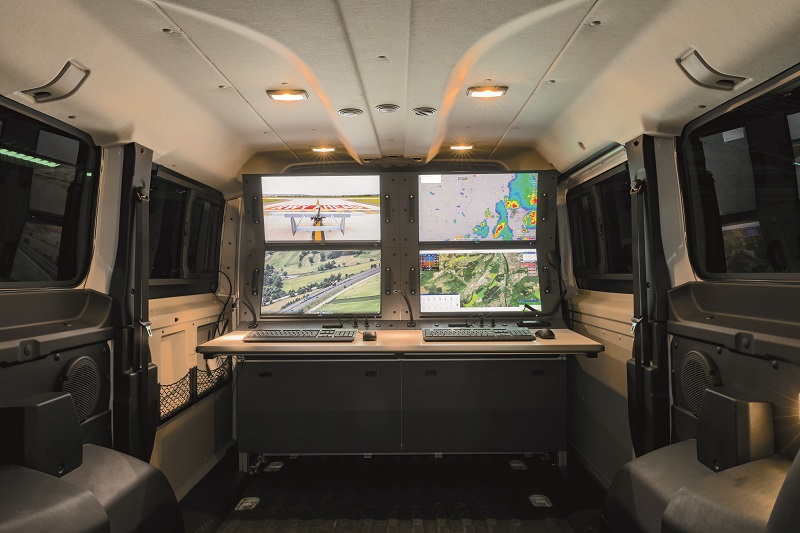
Special mission systems
Primoco is sensor-agnostic, enabling a variety of gimbals such as EO/IR with 4K HD, NIR, SWIR, MWIR and LWIR (with laser rangefinders and pointers) to be integrated.
“We’ve also integrated multi-spectral imagers that blend different IR spectra to find different parameters or targets over wide areas, for example by scanning thousands of square kilometres of open sea per hour for enemy ships,” Fojtik adds.
“You could use zoom cameras for that, but their narrow FoV makes multi-spectral imagers the more efficient option. And across all our different sensors, AI object recognition and detection enable us to identify credit card-sized objects from 2 km away.”
The UAV has also been able to integrate Lidars, radars (synthetic aperture and Ku band), and some military intelligence sensors including satcom interceptors, IMSI (international mobile subscriber identity) catchers, and VHF/UHF transmission directional finders and analysers.
“Sensors like those, combined with AI software and advanced systems like SAR, mean we can find enemies, casualties or missing persons through cloud cover, fog or forest canopies, or hiding in really dense crowds. Using the One 150 for something simple like agricultural survey in clear weather for example would be overkill,” Fojtik says.
Primoco has also flown with flight calibration instruments for certifying the navigation systems of a twin-engine Beechcraft to airworthiness standard tolerances. This was done in August 2021 in partnership with Norwegian Special Mission (one of Europe’s leading flight calibration providers) to prove that an uncrewed aircraft could perform such critical services for a crewed aircraft.
The size of the One 150 meant the Beechcraft’s antennas, computers and software were integrated without needing to miniaturise them (as is often done for UAVs) so the calibration was performed at a fraction of the usual cost. Primoco therefore anticipates making flight calibration a focus of its future commercial offerings.
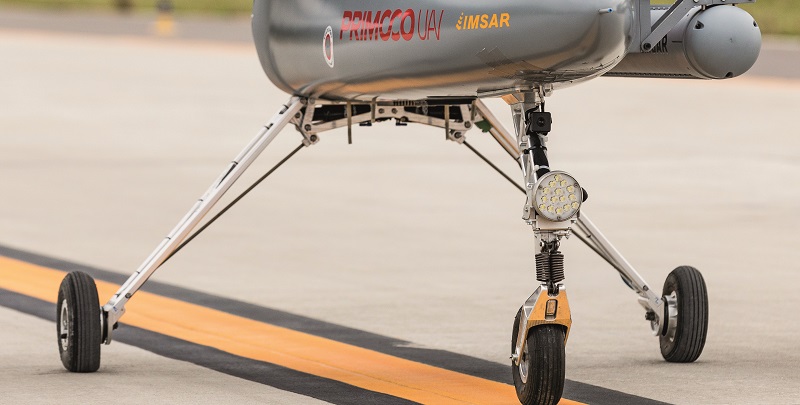
Structure and hull
Stealth is a major reason why the One 150 is fibreglass rather than carbon. Although it has a superb strength-to-weight ratio, carbon is easily detected by radar. Fibreglass is radar-transparent though, and allows Primoco to build its hulls using ‘out of autoclave’ manufacturing and to heat treat them using straightforward processes.
The material can also be repaired in the field, which is challenging with carbon layers. If a crack is found in a carbon part, an autoclave is often needed to re-bond the fibres and resins.
“We had fuselage damage on one occasion, and we re-baked and repaired it overnight in a military tent – not something you could do with carbon,” Fojtik says. “We could save lots of weight by switching to carbon, but the low radar cross-section and ease of manufacturing and repairs makes fibreglass more than worthwhile.”
For geometric strength, the One 150’s wing contains two beams – one main, one ancillary – running the internal length to maintain structural robustness, with about 12 ribs inside each wing along the lengths of the beams. The ribs are concentrated about the mounting points for each tail boom to reinforce them.
“It’s a stiff design; the maximum load factor is limited by the autopilot to 2 g, so with our MTOW of 150 kg you can’t technically exceed loads of 300 kg of force during flight; perhaps 600 kg if you account for gusts,” Fojtik explains.
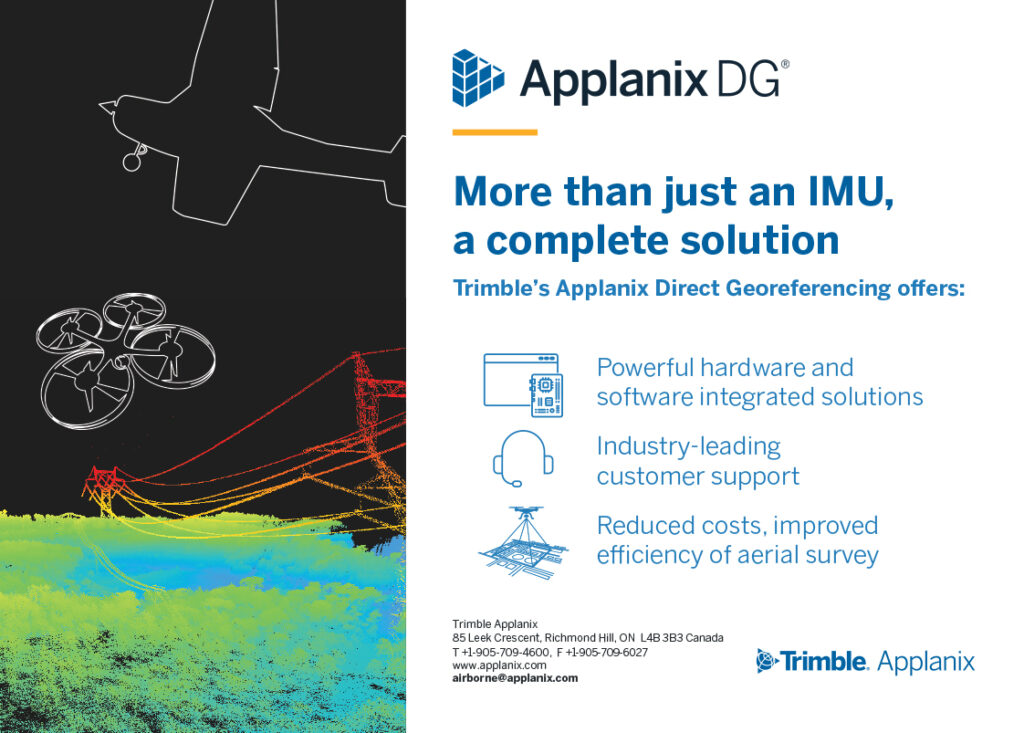
“But as per STANAG 4703, we’ve tested it to survive up to 1.5 t. Theoretically, we can adjust the autopilot’s load factor to allow freer flight and manoeuvring under severe conditions like high turbulence.”
Vector autopilot
A key rule in choosing the autopilot for the One 150 was that it could not be a development product but a mature solution, production-ready and field-proven.
Even so, it had to be tailorable for new capabilities and performance features on an ad hoc basis but remain reliable for controlling flight and subsystems. In addition, it should not be difficult to source.
These requirements led Primoco to select UAV Navigation’s Vector-600. Being manufactured and supported from Spain, EU licencing and easy importing were both a given, and Fojtik reports that UAV Navigation routinely provides quick turnarounds on new functions whenever requested.
For instance, UAV Navigation instituted audio warnings for issues such as engine problems or data losses, in case GCS operators fall asleep or lose concentration from the inevitable monotony of their shifts and warning lights alone are not enough.
Primoco’s in-house GCS hardware can be installed in a mid-sized van as a mobile command centre, reducing set-up overheads for field operations. It features four monitors (touchscreen if requested) and two pairs of keyboard and mouse for two operators in the loop simultaneously.
“That creates redundancy in case one computer fails, and the GCSs run UAV Navigation’s Visionair autopilot software, so updates at their end make a big difference in our GCS’s performance,” Fojtik explains.
Vector’s customisability has enabled close integration between it and the array of onboard sensors for airspeed, air pressure and other key inputs so that mission-specific functions such as autonomously following a target while staying within LOS range can be performed.
“If we’d made our own autopilot, or tried a totally new one from a newer company, we’d never have been able to prove out all bugs and failure modes on our flight hours alone,” Fojtik adds.
“UAV Navigation has many customers, so we know they go through terabytes of real-world data to optimise their platform. We don’t have to encounter a bug ourselves before it gets fixed – statistically, someone else is likely to encounter it, report it, and get it taken care of before it affects our missions.”
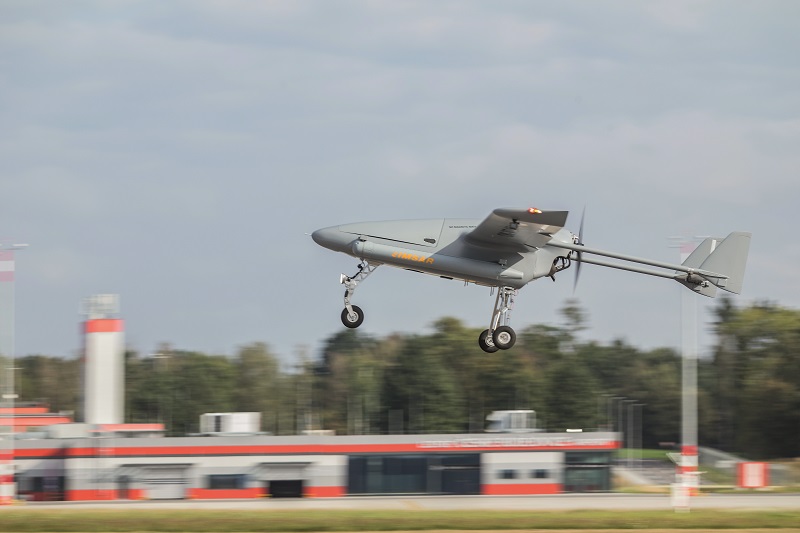
Control architecture
The onboard network has been designed to be as streamlined as possible while still incorporating two-way closed loops, such as each servo reporting back to the autopilot when a movement order has been executed. The Vector-600 is the master controller for commands and power distribution through the central box, being compatible with CAN, serial, PWM and analogue buses as standard.
Payloads are controlled via Ethernet, and through Visionair a protocol proprietary to UAV Navigation can securely stream data prioritised by the end-user. Cable harnesses are made in-house, with military-grade connectors bought from TENEO 3000.
The network makes the UAV fly-by-wire, each control surface being actuated by its own rotary servo, and electrically distributed and optimised for no friction or dust ingress. There are 10 flight control surfaces in total: two ailerons, four flaps (one inner flap and one outer per wing) and two rudders and elevators at the tail.
Primoco gauged the durability and consistency of the servos by building its own actuator test rigs and running millions of cycles on individual units to ensure each could last 1000-2000 hours of operation.
“And to reassure authorities, we limit each servo’s service life to 100 flight hours,” Fojtik comments. “It’s a huge safety margin, theoretically one-tenth or twentieth of their lifespan, and I don’t think we’ve even had one servo fail, but that’s necessary for flying defence missions safely.
“To minimise friction, we’ve used Teflon parts in places to avoid needing lubrication, and we laminate each control surface so there are no hinges. And we’ve validated the mechanical robustness of that lamination in material tests and fatigue tests.
“In flight, we continually monitor servo voltages, among other parameters, as overvoltages can be a sign of friction or failure at the component level. If that happens, an alarm pops up so that the GCS operator or autopilot can disengage the problematic servo.”
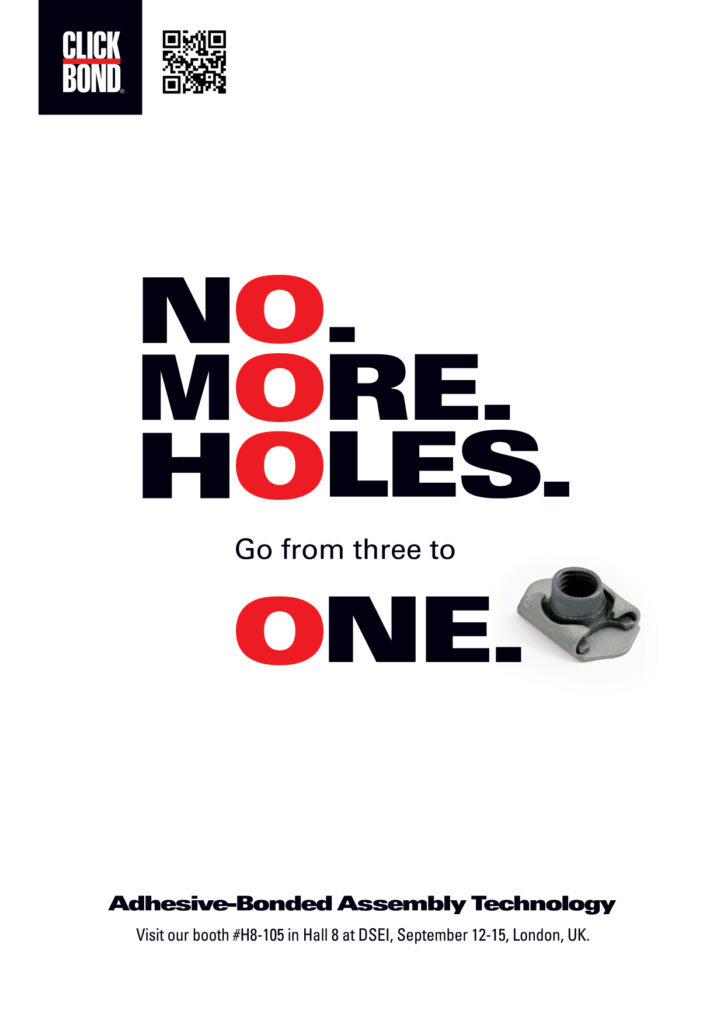
Primoco has also designed the One 150 to be positively stable about its CoG, with the balance and attitude-holding of a training aircraft rather than, say, a fighter jet (which is inherently unstable) such that it could fly with all its control surfaces trimmed.
Some aircraft can gain manoeuvrability by being designed as negatively stable, but the loss of just one navigation sensor input can make it nigh-on impossible for the autopilot to compensate and correct its flight, or make an emergency landing.
Fojtik says this was a specific requirement from one of its key defence customers. “Even STANAG 4703 doesn’t specify that. Although that certification is important to us, if all we did was design the UAV to STANAG 4703, it would meet only 50% of that customer’s needs. In war, as in all markets, listening to customers is key.”
Taxi, take-off and landing
For anti-collision and air traffic awareness, Primoco typically integrates Sagetech’s MX-Series of ADS-B In and Out systems. Through ADS-B In, the GCS can receive the positions of other aircraft and their IDs. However, the regulations are unclear on how to execute automatic course deviation, so Primoco has not implemented this yet, or autonomous taxiing to take-off points, although that is technologically achievable.
The frontal landing gear integrates a nose wheel servo for by-wire steering during taxiing; that, plus the engine throttle servo, makes 12 servos in total on the UAV. Pre-flight checks and take-off take around 2 minutes.
“The rear landing gear was originally designed as a banded metal structure, but after hitting the runway, the UAV would jump quite a bit,” Fojtik recalls. “So now we use telescoping structures that absorb the shocks of hard landings: the landing gear dissipates the impact energy by flexing and contracting.”
The telescopes are hydro-pneumatic systems installed on the upper part of the landing gear, and can be tuned for the anticipated landing terrain. The wheels integrate electromagnetic brakes for controlled slowdowns once the UAV has landed and stabilised. These, and around 25 other parts, comprise the landing gear.
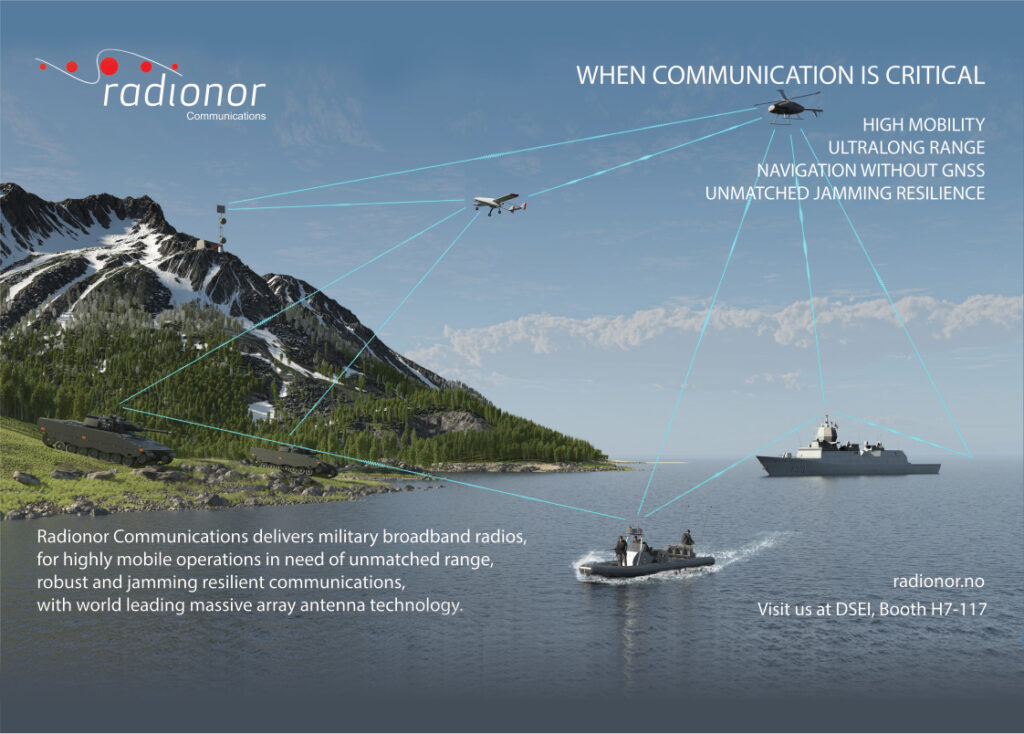
“The undercarriage was designed and calculated part for part in CAD for load distribution, and as per STANAG 4703 it’s been tested to hold 1 t of weight, as a safety margin for our 150 kg UAV in heavy loads or landings,” Fojtik says.
“And if loads are too much, usually just one part breaks, leaving the vast majority of the landing gears reusable, and they’re designed to be disassembled and put back together fairly easily.”
Safety during landing and jamming
A radar altimeter installed in the bottom of the craft feeds the autopilot with timely and precise updates on the terrain below the UAV, to ensure a controlled touchdown wherever possible.
“The vertical accuracy of GNSS, if it’s even provided, can be as high as 50 m,” Fojtik says “That’s a huge and potentially catastrophic margin of error, and even air pressure sensors can be thrown off by simple things like landing near a river or other body of water.
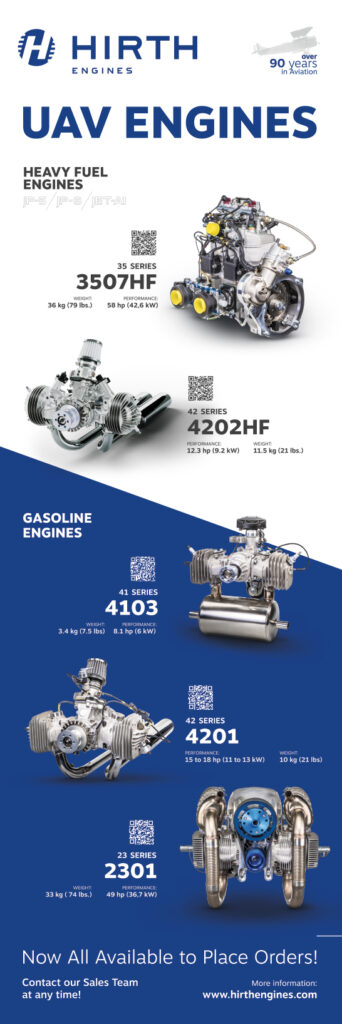
“That’s why we have our radar altimeter, which starts tracking from 200 m above ground level, and that’s how we’ve done the vast majority of our flights in a fully autonomous regime, without issuing the UAV with a single in-flight correction.”
Regarding how Primoco came to develop defences against jamming, Fojtik recounts, “One Middle East-based user had a real fear of their UAV assets being hit with jamming attacks while surveying oil infrastructure, but you can’t just shield the aircraft’s hull and network against jamming signals because you risk blocking your own data links or GNSS, so we engineered ways to fly under jammed conditions, and they worked.”
Since then, the company has honed its anti-jamming technologies, with the result that the One 150 is one of the few UAVs available to military customers today that can consistently and reliably fly in jammed environments.
Although it had prepared to do so in the context of oil infrastructure inspections, the UAV began proving its ISTAR abilities around the same time that Primoco gained its LUC. The company emphasises here that although it flies many defence missions in addition to its commercial and civilian applications, the One 150 is not a combat aircraft, and is never used to drop munitions of any kind.
However, the different design points of the UAV aimed at increasing its stealth capability have driven its demand to eclipse that of other successful uncrewed defence aircraft. A major part of this is Primoco’s aforementioned use of fibreglass throughout the hull and structure; most high-end UAVs are made from carbon fibre, which despite its strength-to-weight superiority is grievously easy to detect, causing carbon-built aircraft to “light up on radar like a chunk of metal” as Fojtik puts it.
As a result, other such UAVs are easily detected and destroyed in and around disputed airspaces, and so many other UASs being offered to customers involved in active conflicts are no longer being sought by discerning defence procurement officers.
By contrast, Primoco continues to operate directly and increasingly above combat zones without losses. Much of that is thanks to the company’s stealth and anti-jamming approaches.
A lot of the anti-jamming strategy revolves around the autopilot checking, cross-referencing and fusing data from a pitot tube on the nose, static barometric sensors on both sides of the fuselage (for when the UAV is in a banked turn), an IMU (with magnetometer) and a 72-channel, multi-constellation GNSS receiver with access to GPS, BeiDou, GLONASS and Galileo.
“The first consequence of jamming is often that GNSS readings for speed and altitude start changing too much and too quickly, but IMUs, barometers and pitot tubes work just fine amid jamming,” Fojtik adds. “So we’ve programmed alarms alerting operators to potential jamming when GNSS position and speed start conflicting with the inertial and pressure readings.
“Also, with many of our components we don’t go dual-redundant. Dual redundancy isn’t actually required in STANAG 4703, but the overall philosophy is the same: if one sensor isn’t enough for safety in flight or landing, another picks up the slack by tracking data in a different way.”
Protecting against jamming is often limited to a UAV integrating a GNSS that works across a wide spectrum, so that when one section of the spectrum is being jammed, the receiver switches to another section, which is often sufficient.
“The problem is that in some active war zones, there’s jamming across ultra-wide frequency bands, which is why we have so many countermeasures,” Fojtik says.
“We have one other navigation system, a proprietary technology that I can’t explain in detail, but even in a completely GNSS-denied or spoofed environment, we can fly and gimbal-track really precisely. That’s vital because if you find, say, a tank or artillery at some other target, and you lack reliable position data, the find is useless.
“This system is completely independent of inertial, GNSS and air data – all I can tell you is that it’s radio-based. It’s a big part of what’s allowed us to fly every day in jammed conditions.”
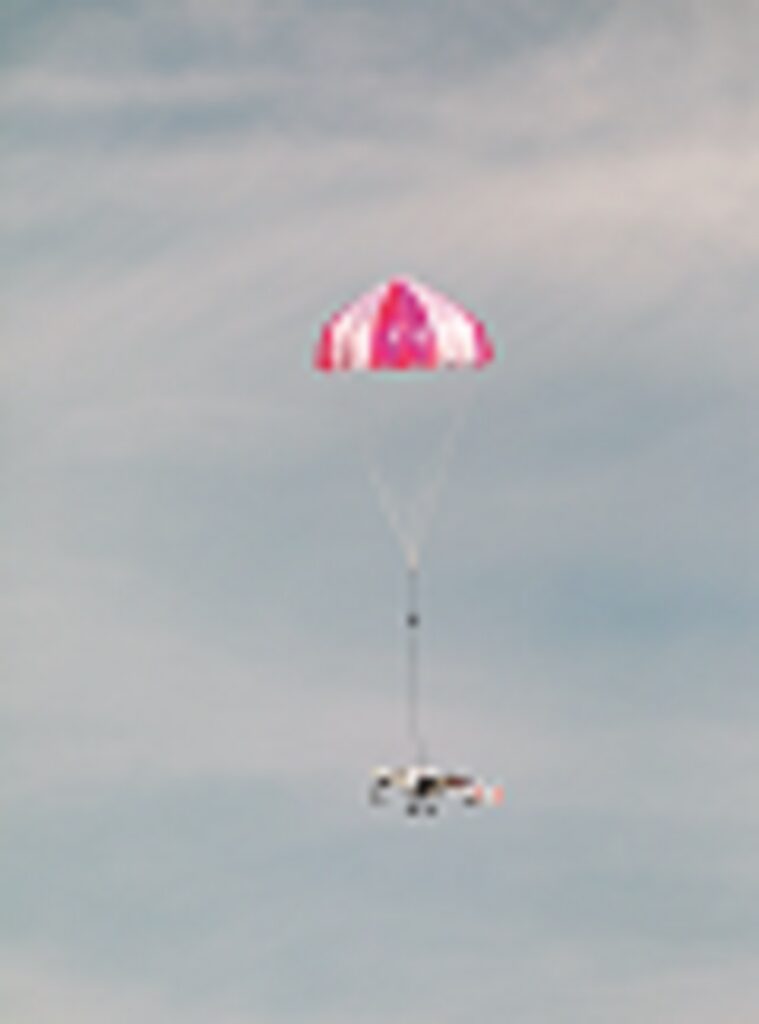
Parachute
If the landing gear should still fail, or damage makes standard landings impossible, the recovery parachute is deployed to enable a slow emergency landing.
When an emergency landing is triggered, a small ballistic rocket housed in a tube and tethered to the top of the parachute is launched upwards from the parachute box, tearing through the upper cover on the front of the fuselage and lifting it away from the rest of the aircraft.
The rocket hence pulls the parachute up quickly, allowing it to rapidly unravel and fill with air to begin slowing the UAV’s descent even at low altitudes.
As the One 150 falls, the parachute points the nose upwards, preventing payload sensors from being the first point of impact with the ground. The tail and landing gear point downwards, having been validated for load bearing and shock absorption such that the force of impact on touchdown is not transmitted to any of the electronics.
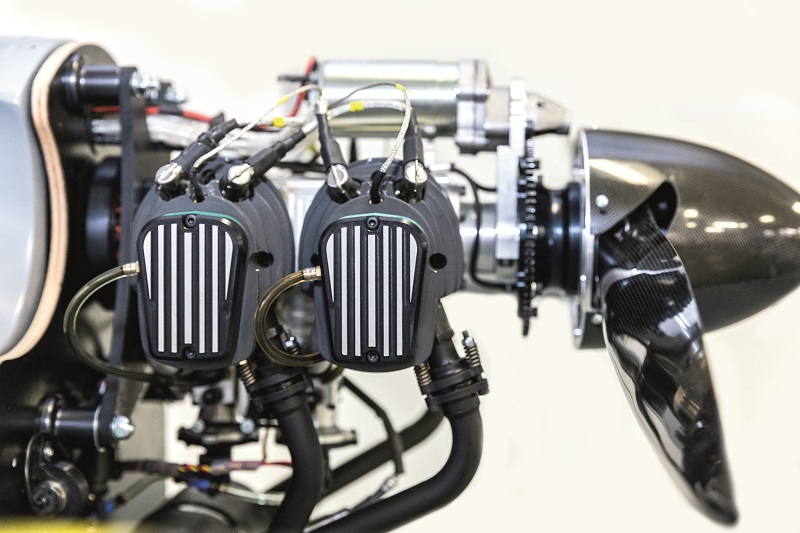
The Primoco 340 engine
The Primoco 340 is a four-stroke, four-cylinder boxer, producing 25 bhp at a maximum speed of 5000 rpm, and consuming between 3 and 4 litres/hour depending on the UAV’s carried weight.
It features dual EFI controls, dual spark plugs per cylinder, and dual injectors per row of cylinders. For added safety, the starter/generator is designed and programmed to perform in-flight emergency restarts, and electrical power for onboard systems is generated by an alternator mounted on the rear of the crankshaft.
“The alternator outputs 750-1000W continuously and feeds into the accumulator, which consists mostly of LFP cells, which as far as we’re concerned is the best chemistry for safe and stable energy storage,” Fojtik explains. “But the accumulator isn’t just a battery pack, it also buffers and balances the power going between systems, including storing AC power from the alternator or powering emergency restarts from the starter/generator.”
The accumulator is connected directly to the power distribution box, which integrates DC-DC converters to step the output voltage to 24, 12 and 7.5 V to cover the various requirements of the One 150’s electrical and electronic systems.
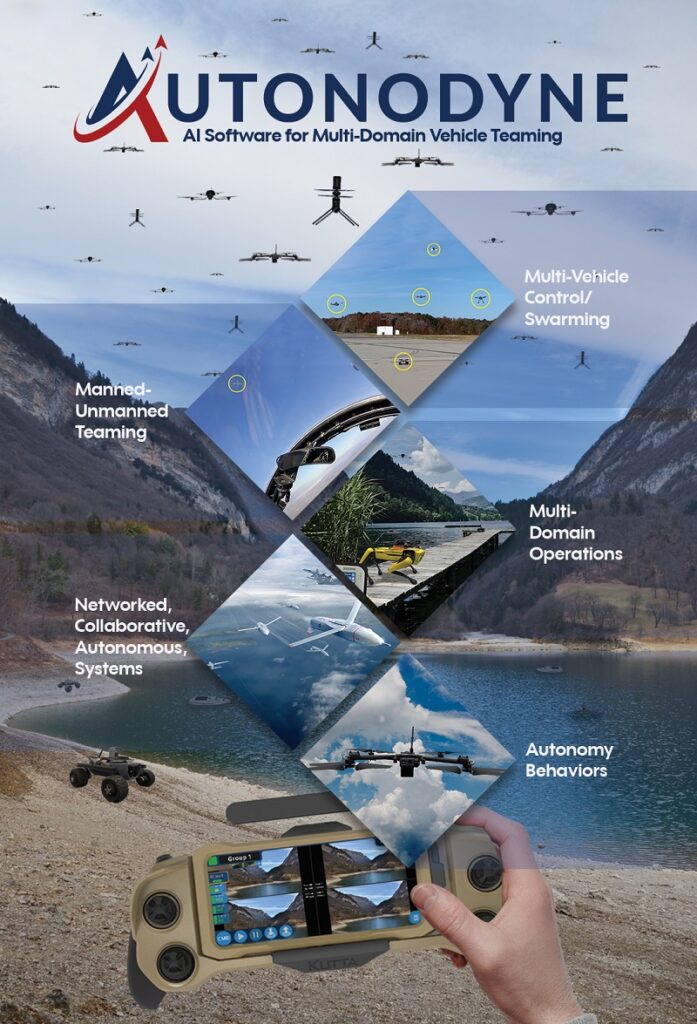
Plans for the engine began as soon as the One 150 started flying, as the company quickly realised that there were some safety issues with two-strokes that could not be overcome. For instance, the very exposed exhaust system could be a source of ruptures and hence compression ratio losses, which in a two-stroke means rapid loss of altitude. A four-stroke though can suffer exhaust ruptures and keep on flying, albeit with greater noise emissions and fuel consumption.
The company notes that the Primoco 500 had a superior power-to-weight ratio than the present 340, and that two-strokes in general will typically outperform four-strokes in this respect. However, this advantage was offset in practical terms by the 500’s much higher SFC, and the fact that it ran more optimally on heavy twin carburettors than on EFI, which brought risks of freezing (even without flying at particularly high altitudes) or vulnerability to gusts.
While the two-stroke’s development was outsourced to Czech subcontractors VM Motor and Motordesign, the four-stroke was developed from a blank sheet by a crew consisting of in-house, subcontracted and part-time specialists, with all the design, manufacturing, testing and tuning taking place under Primoco’s roof and brand.
The 340 is still being flight tested to validate key performance specs such as its TBO (which is estimated at between 200 and 400 hours for now, depending on fuel quality).
STANAG 4703 compliance tests are also being run to increase its guaranteed service life, with the eventual plan of redesigning it as a two-cylinder with greater displacement than 340 cc to increase power. At present, however, all-up weight comes to about 15 kg, and the system typically runs on widely available 95-100 octane unleaded gasoline.
“The ECU monitors performance and controls parameters electronically, so if there are discrepancies between any temperature, speed or voltage readings from the sensors and what we want them to be, the ECU implements whatever the mapping or embedded programming suggests is best to mitigate the issue,” Fojtik adds.
“As per STANAG 4703’s recommendations, the fuel lines are made from a special fuel-resistant, thermally resistant plastic that is non-flammable, and for further fire protection we’ve used specific aluminiums and other alloys around the engine bay for thermal distribution, compensating for the engine’s small size and the fact that it’s ram air-cooled. Also, the cables are all EM-shielded, as there’s huge potential for interference with data readings, especially if the SIGINT and ELINT-type payloads are installed.”
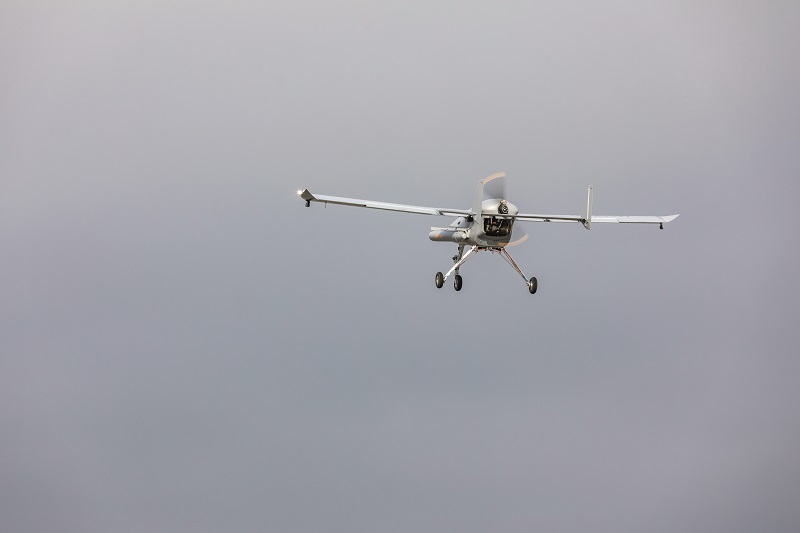
Data links
For stealth purposes, Primoco does not use omnidirectional antennas on the UAV during defence missions, instead opting for beamforming antennas.
Fojtik explains, “If you’re broadcasting everything everywhere, it becomes potentially quite easy to find the aircraft, whereas if you’re just transmitting in the narrow general direction of your GCS or another preferred receiver, it’s quite difficult to find us.”
While many tactical, MANET and mesh radios have been integrated and used with the One 150, Primoco prefers Radionor’s CRE2-179-UAV data link for tactical defence missions.
This is a phased array ad hoc network product consisting of a panel enclosure with integrated radio transceiver and antennas, and typically mounted horizontally beneath the One 150’s fuel tank on its underbelly.
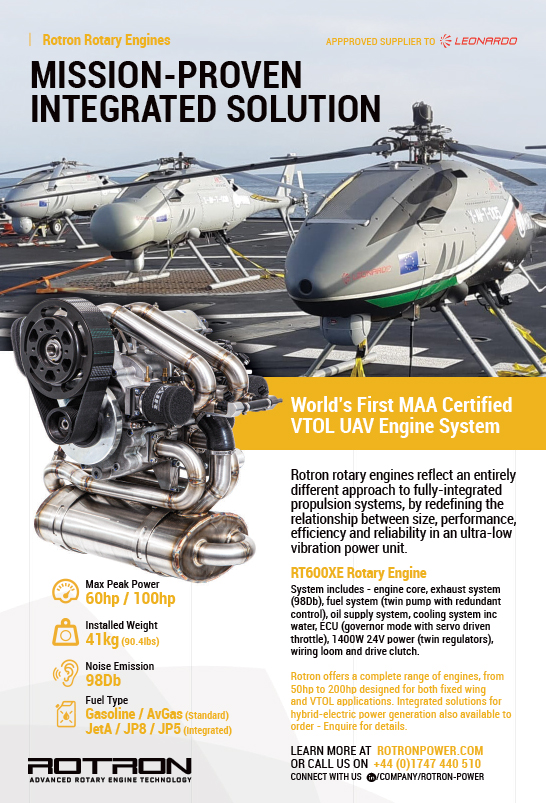
The system has a bandwidth of 15 Mbit/s within 200 km (although 7 Mbit/s can be achieved for some range beyond this) and embeds AES-256 encryption, covering all end-to-end comms to prevent remote takeover by hostile actors.
“It’s a super-large antenna for most UAVs, but it has really good bandwidth, encryption and beamforming,” Fojtik adds. “It’s good for meeting STANAG radio requirements, and it will probably always form the core of our comms in defence.”
And wherever possible, Primoco avoids installing separate, differently ranged data links for different systems, despite it being common practice in the UAV world to use one link for flight telemetry and another for real-time video streaming (with an SD card storing raw survey data on board).
Most of Primoco’s users do not want that difference in range. Up-to-the-millisecond streaming of everything the One 150 sees is vital, and enemy combatants cannot be allowed to seize the UAV’s data should they shoot it down.
The CRE2-179-UAV link therefore tends to be used by itself, with a ruggedised memory unit with self-erasing memory on board, and with the GCS van moving to keep the UAV and its operator within 200 km of each other.
Future plans
Primoco plans to expand its portfolio of offerings of the One 150, such as different wing types for different lift factors, as well as new sensor integrations across EO, SIGINT, electronic warfare and more defence and civilian applications.
On top of that, it plans to exploit AI increasingly to make the UAS easier to operate, for instance through real-time analytics to track, classify and prioritise targets autonomously.
All of this will however be done in compliance with STANAG 4703 and any other regulations the company thinks it is worth working towards.
“It can be overwhelming for companies to go through the painstaking efforts involved with this kind of certification, and we can foresee a tremendous shift towards newer, more agile entities in the UAV industry in the future, because many companies once considered leaders in this industry will find it hard to revamp
their operations to conform with EMAR 21 and hence STANAG 4703,” Fojtik says.
“For our part, we plan to progress to even higher levels of certification to allow us to fly over more populated areas.”
Specifications
- Primoco One 150 UAV
- Wingspan: 4.85 m
- Length: 3.65 m
- Height: 1.25 m
- Maximum take-off weight: 150 kg
- Payload: 30 kg
- Maximum LOS distance from GCS: 200 km
- Maximum flight distance: 2000 km
- Maximum endurance: 15 hours
- Maximum engine power: 25 bhp (18.6 kW)
- Cruising speed: 100-150 kph
- Endurance: 15 hours
- Maximum altitude: 3300 m (FL 100)
Some key suppliers
- Autopilot: UAV Navigation
- Cable harnesses: in-house
- Connectors: TENEO 3000
- Data links: Radionor
- Engine: in-house
- IMU: undisclosed
- Servo actuators: Graupner
- Synthetic aperture radar: IMSAR
- Transponders: Sagetech
UPCOMING EVENTS
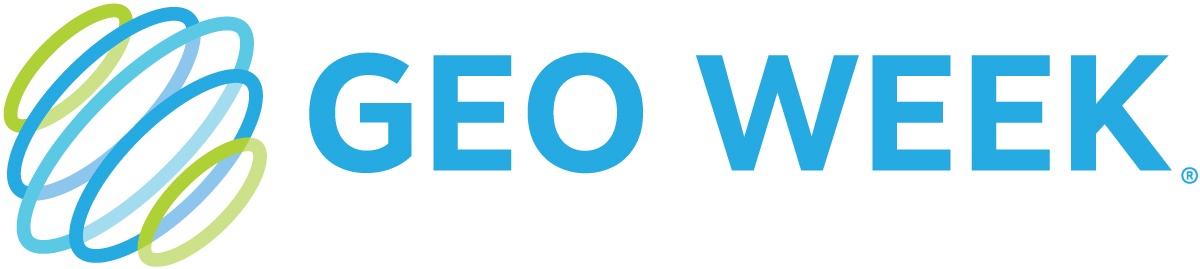
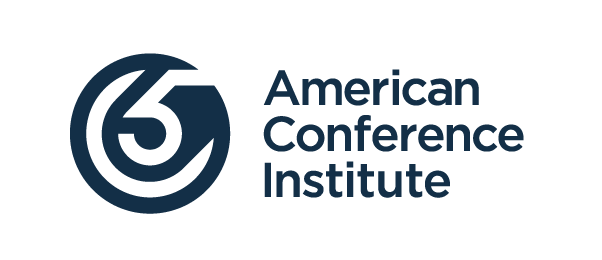
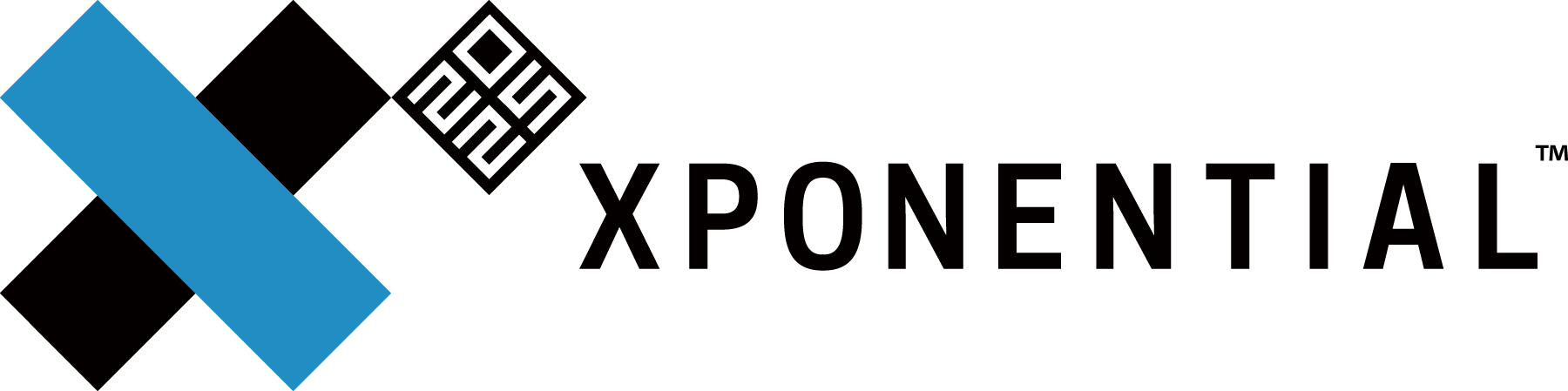
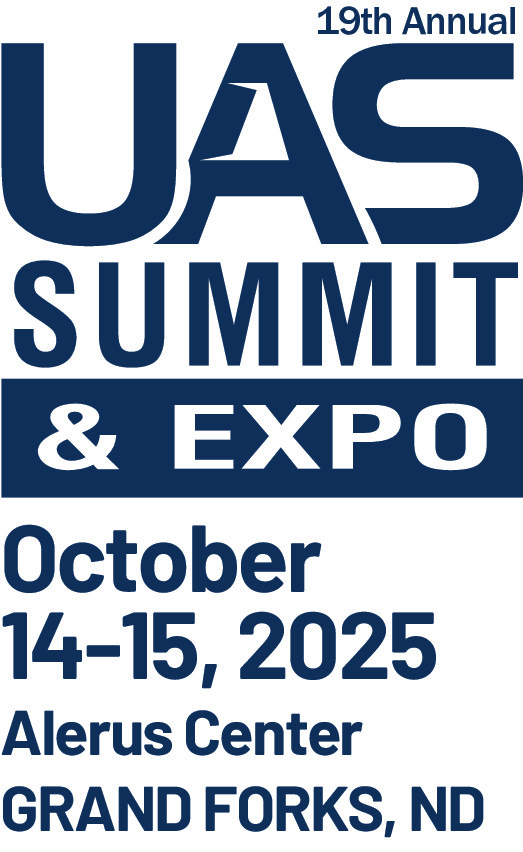
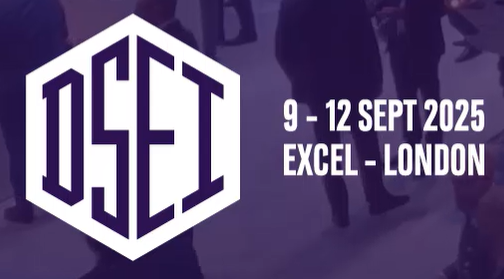
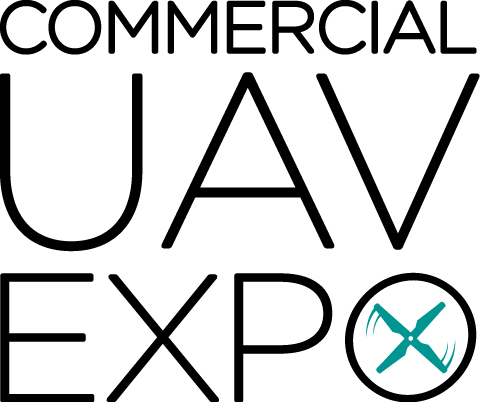
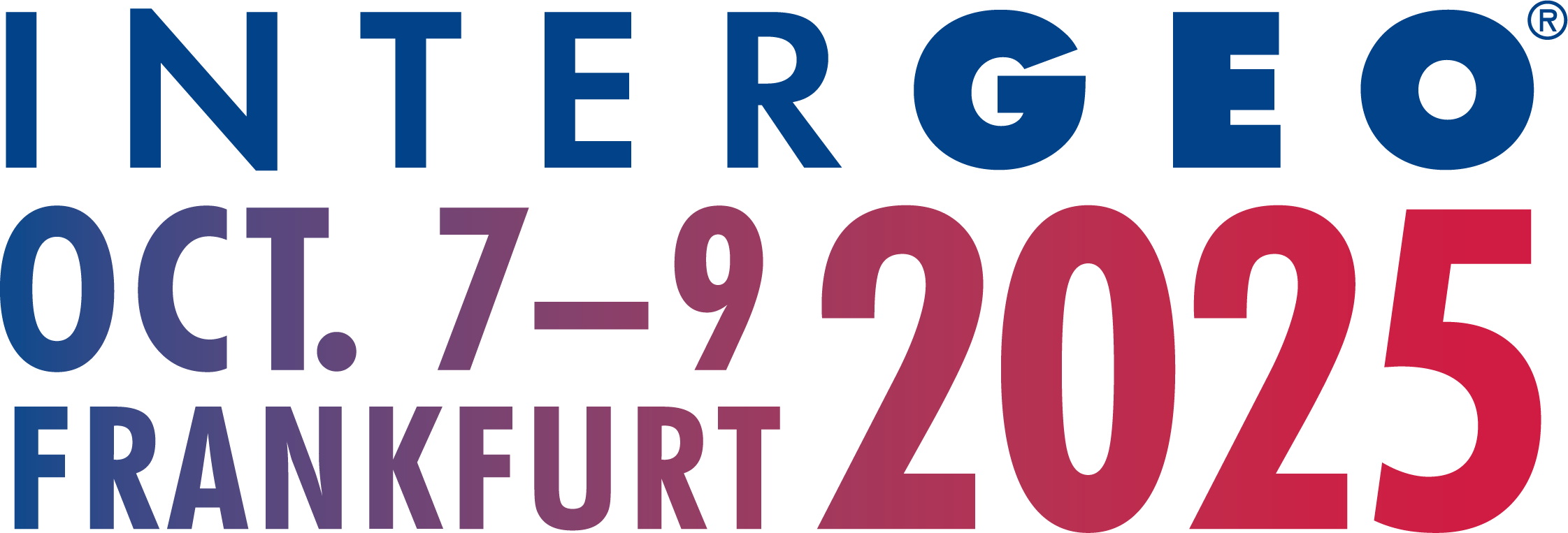
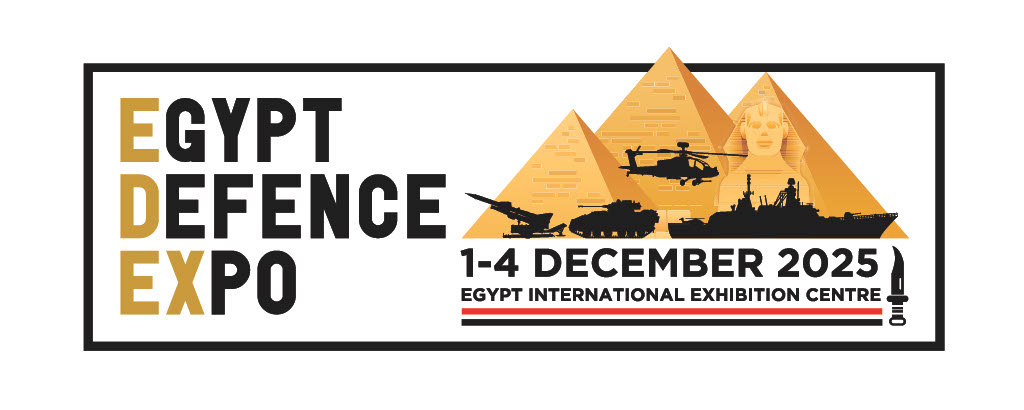
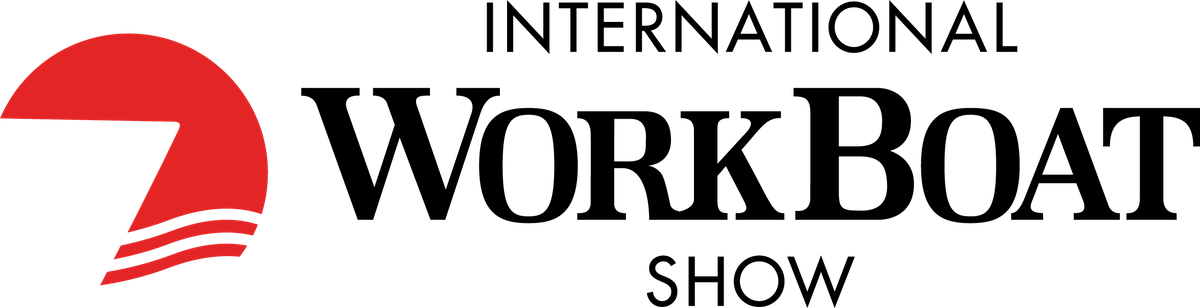
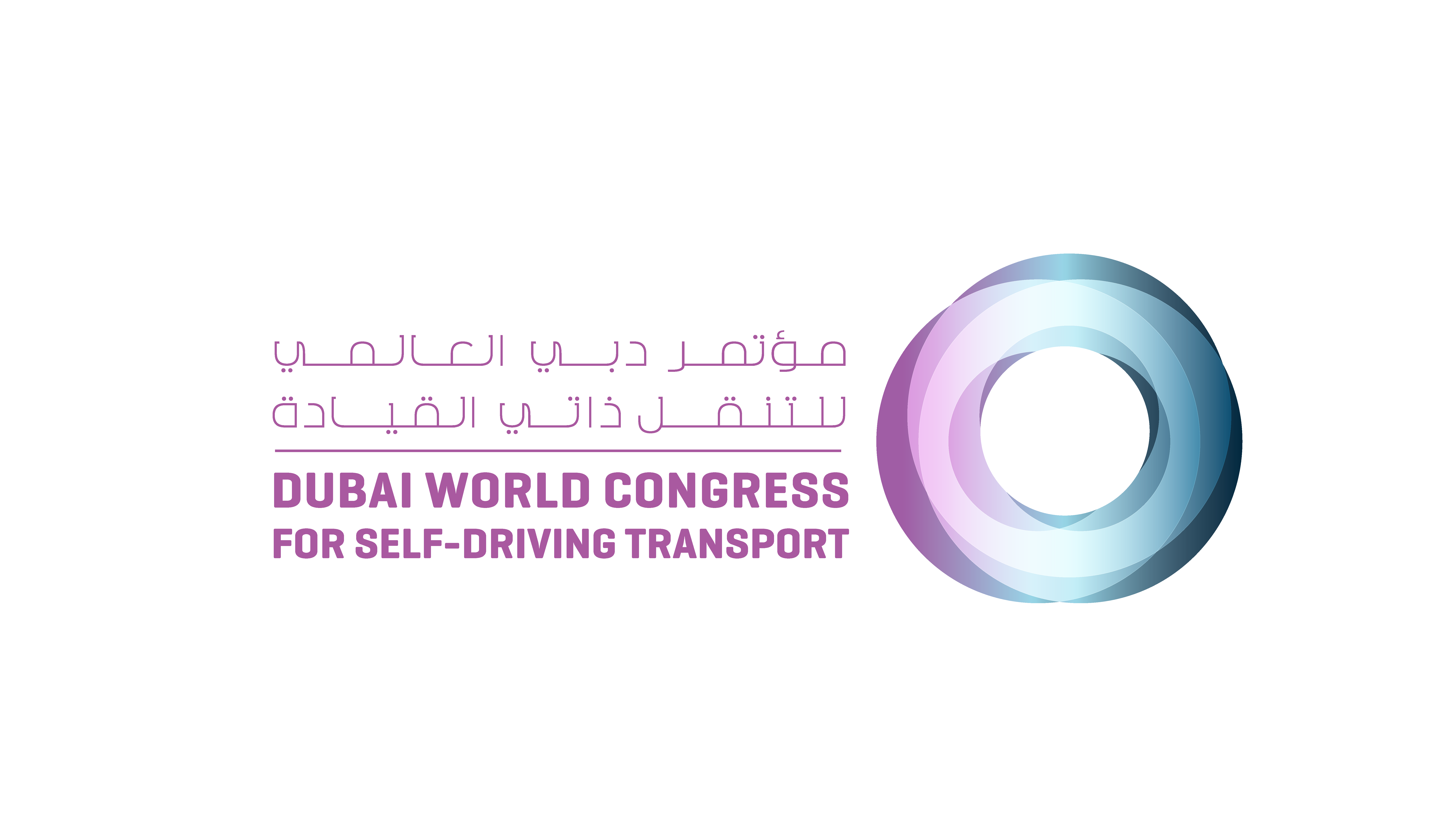
