Rheinmetall
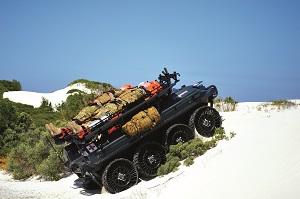
Rory Jackson discovers how intelligent UGVs are being used to rescue casualties in dangerous environments
Medical evacuations (or medevacs) in complex terrain present significant challenges to crewed vehicles, as drivers and pilots must negotiate tricky elevations, thickets, unstable ground and other hazards in their efforts to reach and then ferry casualties to safety.
It is often impossible for wheeled and even rotor-wing vehicles to access the locations of casualties, and in desperate situations rescue coordinators will resort to more feasible approaches, even if these present a greater risk to first-responder crews. The military, for example, are often left with no other option than to send four personnel on foot to carry a wounded soldier to an ambulance or rally point.
Lower-end uncrewed systems have recently been used in battlefield medevacs as teleoperated mules, carrying heavy equipment, ordnance and provisions for personnel in the field while being directed by a nearby operator using a ground control system (GCS), until the need arises to load a wounded comrade on to its back and direct it to safety.
Autonomy is the natural next step for such vehicles, freeing up personnel in the field or enabling them to safely take cover from dangerous conditions, while uncrewed ground vehicles (UGVs) serve as autonomous mules or all-terrain ambulances, returning the wounded and other key assets to a forward operating base.
These are the essential functions of Rheinmetall Canada’s Mission Master family of UGVs, three uncrewed, all-terrain (including amphibious) vehicles that the company demonstrated for interested armed forces across key exercises in Australia and Estonia in the second half of 2023.
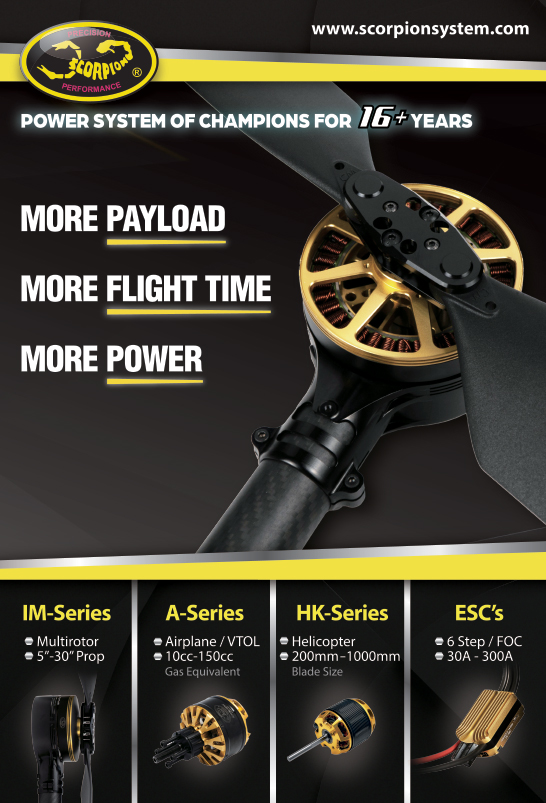
Mission Master trio
The three vehicles are, from the smallest to the largest, the Mission Master SP, the Mission Master CXT and the Mission Master XT.
The SP is a battery-electric vehicle, measuring 2.95 x 1.55 x 1.33 m. It runs on eight wheels with a ground clearance of 24 cm and a typical weight of 1100 kg, as well as a maximum payload of 600 kg (or 300 kg if the user aims to exercise its amphibious capabilities).
Its all-electric drivetrain of Li-ion batteries and a central electric motor drive is currently limited to a top speed of 30 kph, enabling an endurance of eight hours (at an operating speed of 10 kph) between charges and a maximum climbing angle of 40° on surfaces.
The CXT measures 3.16 x 2.25 x 1.53 m and runs on a hybrid diesel-electric powertrain, giving it an operating range of 450 km between refuellings. This larger powertrain and its increased size over the SP result in a base weight of 2200 kg, as well as a payload capacity of 1000 kg.
The XT, whose dimensions are 3.72 x 2.57 x 1.9 m, operates on a diesel engine with a hydrostatic transmission. Like the CXT, it has a 1000 kg payload capacity and a 2217 kg gross weight. Its powertrain and size give it 750 km of traversable distance between refuels.
Additionally, both the CXT and XT are designed to run at a top speed of 40 kph.
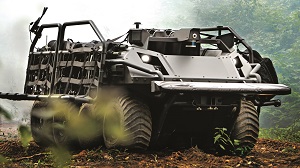
Intelligent self-driving
“All three are equipped with the Rheinmetall PATH autonomy kit [A-kit], a package of hardware and software that can be equipped on almost any ground vehicle to make it an intelligent, self-driving system – even logistics trucks and regular cars can use it. We’ve installed it on Ford Rangers and had them run together as a convoy,” says Eric Diniz, project management specialist at Rheinmetall Canada.
“Sensors differ between the vehicles because of their differing sizes and shapes. As a baseline, we use Lidar, radar and camera around the vehicles to navigate autonomously. But, for example, the XT is the largest, so it physically needs more sensors for full, 360o awareness, so that UGV has ultrasonic proximity sensors all around it that cover blind spots that Lidar and radar cannot see.”
Alain Tremblay, vice-president for business development and innovation at Rheinmetall Canada, says: “We don’t use any one model for Lidar, or cameras or radars – different military clients will have varying mission conditions and budgetary requirements, so we can go for lower- or higher-end sensor capabilities.
“If, for instance, they want a UGV in a very harsh, hot, dry environment prone to dust storms, or equally, a very icy environment with snowstorms, we’d go for very powerful sensor models to sense reliably through all that.
“But, even in those environments, clients will sometimes ask for somewhat low-power sensors because they want their Mission Masters to give off a minimal electromagnetic signature for stealth reasons, so the PATH A-kit really has to be modular for these types of applications.”
Development of the Mission Masters began from a blank sheet around the end of 2017, which Rheinmetall notes was a time when the UGV market specified little or no exact requirements as to how an uncrewed mule for logistics and Medevac should look, or what it should be capable of doing. There was also no indication that the UGV industry and market would later bloom in a similar way to how the UAV world was at the time.
By 2019, UGVs for autonomous last-mile resupply were in demand across the West (something Tremblay attributes particularly to Russia’s deployment of high-end, teleoperated, weaponised UGVs in Syria), which pushed Rheinmetall Canada to accelerate its development and optimisation of the Mission Master family.
Since 2021, defence customers have advanced their interest to specific subsystems and capabilities, including the use of UGVs as intelligence, surveillance and reconnaissance (ISR) vehicles, weapon platforms and intelligent, self-driving Medevac vehicles.
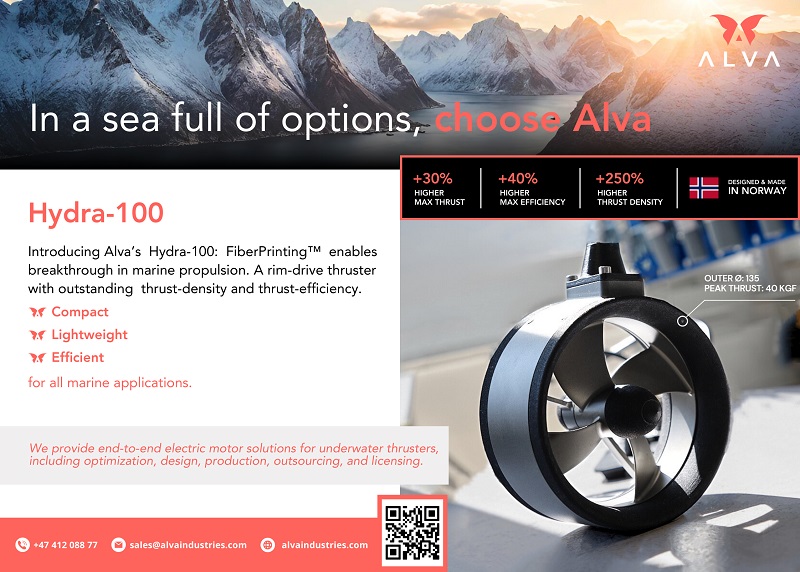
To the testing grounds
The Mission Master demonstrations, held in Estonia in June 2023, were part of the Unmanned Ground Vehicle Autonomy Trials event arranged by the Estonian Military Academy and the Estonian Defence Forces to test the limits of current autonomous technologies. The event was observed by military and civilian experts from numerous countries, with 11 companies (including Rheinmetall Canada) participating.
Meanwhile, the operations in Australia were part of Exercise Talisman Sabre 2023, a series of all-domain training activities aimed primarily at enabling US Marine Corps (USMC) forces to test new system capabilities, while improving the combat readiness and interoperability between Australian and US forces (and those of other allied countries). Notably, the USMC was among the observers of the UGV trials in Estonia.
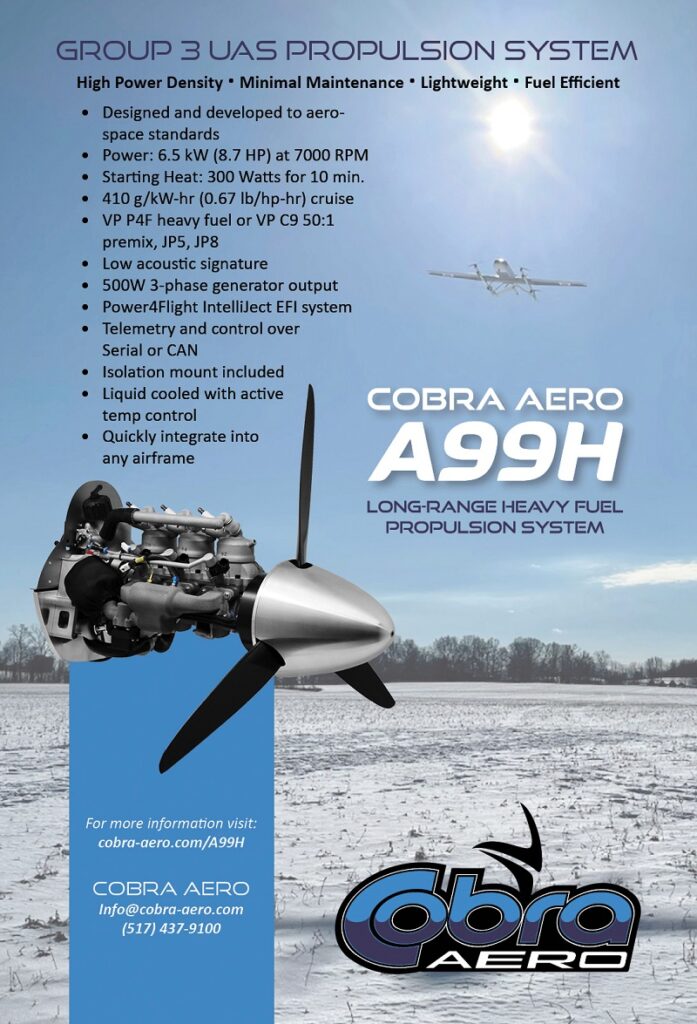
“Transporting the UGVs about the demonstration zones in Australia was straightforward, as the authorities gave us permission to operate them on civilian roads, so when moving from one tactical area to another, we just set them to autonomously follow a manually driven car or something, and off they went down the road without issue,” Tremblay says.
“That autonomous following capacity is something we’re ironing out in the Mission Masters so that the algorithm can one day be ported over to heavy logistics trucks. You could basically create a ‘virtual train’ of many self-driving trucks following in a line behind just one crewed truck at the front.”
Diniz notes that the autonomous convoy mode was similarly used in Estonia, enabling Rheinmetall Canada to arrive at the test zones significantly faster than companies relying on remote teleoperation of their UGVs.
The bulk of the activities in Australia and Estonia were focused on demonstrating and maturing the Mission Masters’ casualty evacuation applications.
Casualty evacuation
Preparations for these demonstrations were simple, as each Mission Master is programmed with self-diagnostic systems, such that any faults in mechanical, electrical, electronic or software systems are continually checked for. This effectively shortens the pre-deployment checklist down to operators merely eyeing the fuel level or battery state-of-charge to determine whether onboard energy is satisfactory for the mission range.
“We have deliberately designed the UGVs such that any necessary interactions are extremely simple for end-users; we can’t hand a system to soldiers if they need a MSc to operate it,” Tremblay says.
“But so long as they know how to operate smartphones or tablets, which all younger people today do, they can operate the Mission Masters. That is essentially what it’s like to operate the GCS, for which we use a custom, handheld computer from UXV Technologies.
“We had a custom safety architecture in mind, across both hardware and software, to bring the control system in line with the very difficult NATO standards for firing kinetic weapons over wireless networks.
“Some Mission Master customers wanted to be able to do that, so rather than give end-users two different GCSs and risk them taking the wrong one into the field, the standard-issue system needed to be NATO-compliant for wireless kinetic weapon triggering – and UXV Technologies was willing to engineer a GCS along those very unique lines.”
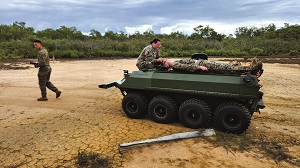
Outback and forest
A Medevac using a Mission Master will occur when a team of soldiers radios a base for a UGV to be sent out to collect a casualty from their position or when such a team already has a Mission Master on hand (typically functioning as a mule).
“The USMC trialled both modes in Australia: one where the UGV followed the soldiers autonomously and was then loaded with a marine playing the part of a casualty they came upon, and one where there was an assembly area where the UGVs were held in reserve,” Tremblay says.
“In the latter, troops in a forward position encountered a casualty actor as part of the exercise, and they radioed their rear echelon [the portion of a military force tasked with administrative and supply duties] to activate and program a UGV to go and meet them at their GNSS position.
“And there’s a third instance where a Mission Master has been left behind, say, for ISR purposes, as if to watch a given area for signs of enemy activity, where if you’re still within radio range of it, then you can requisition the UGV yourself to come and meet you.”
Tremblay adds that, from a technical point of view, performing Medevacs is not difficult so long as the UGV in use has a form factor and intelligence conducive to negotiating the types of obstacles to be encountered in a fully autonomous way.
For instance, if the mission environment is a devastated urban area, with heavy rubble and collapsed buildings, the CXT and XT UGVs are likely to be the best choice for their robust ability to push a pathway through to where casualties are located.
“One day, we might investigate the use of robotic arms to even pick up casualties and place them atop the flatbed of the UGVs in an autonomous way. It’s certainly possible. But that raises issues on how best to physically stabilise the wounded and related mechanical challenges, which will take time to solve,” he says.
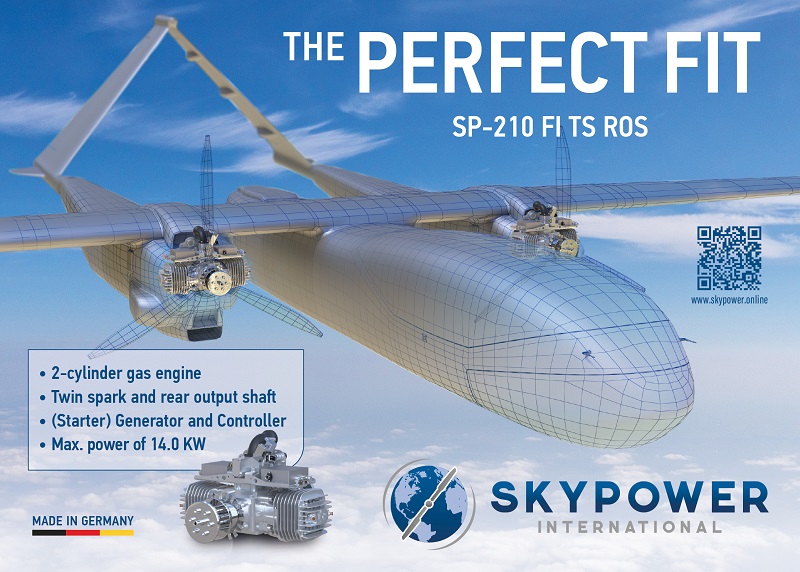
Preferred methods
In Australia, the USMC’s preferred method of using the Mission Master was to first have a medic on hand to stabilise the casualty, after which two or three soldiers would lift them on to the back of the UGV. Then the UGV would be ordered via GCS to find its way to a specified casualty collection point autonomously.
A seat would be installed for the medic to sit inside the vehicle and observe the casualties, and to perform first aid or other stabilising activities if the need arose. A hook for bags of intravenous fluid was also installed.

The activities of the Estonian authorities were similar, with the addition of testing the ability of the UGVs to travel through forested areas. This included the detection of overhanging branches and knowing whether the vehicle could drive safely under or through them without operator intervention, intelligently keeping to a dirt trail, and navigating through large fields of tall grass without losing its sense of direction.
“That’s another big reason [why] these sorts of trials are so valuable: we get to learn the edge-case limitations of our systems and refine our development roadmap,” Tremblay says. “We’ve been doing that continuously with the UK Ministry of Defence (MoD) for over three years now, with great interactions and feedback from them that have helped improve the systems a lot.”
Diniz adds: “We’re starting similar trials in Norway, where there’s a lot of very difficult terrain for autonomous systems to deal with, and our team is using the XT to compete with others there now. And in 2023, the Finnish MoD carried out trials in the Arctic Circle, where we were the only ones who accepted the challenge of working autonomously in that environment.”
Real and virtual worlds
The UGV is typically set to run no faster than 20 kph while carrying casualties to keep them physically stable and preserve their health (particularly when off-road), and also to ensure the autonomy software stack is never overwhelmed with sensory inputs faster than it can process them into logical steering, braking and speed commands.
However, Rheinmetall Canada reports that the current target for further optimisation of the autonomous Medevac capability is to increase the nominal speed at which casualties can be autonomously evacuated.
“This is something all UGV manufacturers interested in Medevac are struggling with,” Tremblay explains. “There are many platforms that can go up to 70 kph now, but not in a fully autonomous way. Computing power and AI today don’t guarantee that a UGV moving at 70 kph can still differentiate between a rock and a bush, or between a wall and a fence.”
Speed is of the essence
This is why Rheinmetall is focused on increasing the speed at which its vehicles can run fully autonomously, as are other UGV organisations, such as Team PoliMOVE of the Indy Autonomous Challenge – explored in depth in issue 46 (October/November 2022) – which has since broken autonomous land-speed records across the USA and Europe to create technology transferrable to autonomous commercial road vehicles.
“So, 20 kph was an ideal maximum for the Mission Master – not too slow for getting casualties to safety, and not so fast that it ever came close to making an error or failing to modulate its speed for worsening driving conditions. That was especially well trialled with the SP, which the USMC preferred for varying reasons,” Tremblay says.
“It also limited the degree of braking needed if the SP encountered something it couldn’t negotiate, like a huge anti-tank ditch. But, if we were running the XT or CXT, or something like a Polaris MRZR, a 4×4 military all-terrain vehicle (ATV), with no casualties onboard, we could go up to 50 kph off-road autonomously without too much difficulty.”
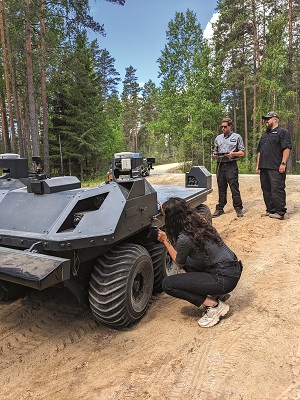
Simulating environments
Preparations for the operations in Australia and Estonia included visiting the environments to simulate them in synthetic situations, and designing profiles for the UGVs to run in the test tracks shared by Rheinmetall Canada and Rheinmetall Provectus Robotic Solutions; the latter is a Canada-based company last featured in issue 37 (April/May 2021), which was since acquired by Rheinmetall Canada for its capabilities in data-fusion that it developed for the autonomous driving market.
“If the right testing conditions aren’t available on our test tracks, we have plenty of wilderness space in Canada to use as real-world testing grounds, once the software testing is done in the lab and we want to see how it performs,” Diniz says.
“As well as Rheinmetall Provectus having a very good simulation software suite, we developed in 2023 a very good hardware-in-the-loop simulator, which consists of an A-kit computer in a Pelican case running Rheinmetall Provectus’ algorithms as if it were in a vehicle.
“Connected to that is one of UXV Technologies’ tablets with Rheinmetall’s C2 software, through which we can program an autonomous route and take control of a payload, all within a synthetic environment, so that, for instance, the Lidar will still detect obstacles, which the simulated vehicle needs to take navigation and avoidance decisions around.”
Tremblay adds that today’s Western defence clients want to holistically integrate all their assets across air, land and sea, uncrewed or otherwise, into whatever battle-management software they are using, “so our UGVs can’t be functioning as an orphan with their own software and their own GCS. Our software must integrate seamlessly with theirs.”
“Overall, I would say 70% of our development work today is on software, with 30% on hardware. The USMC even asked us at one point to integrate Starlink Communications on the Mission Master, which we did on-the-fly so that signals from the UGV operating in Australia could be monitored in real-time from California.”
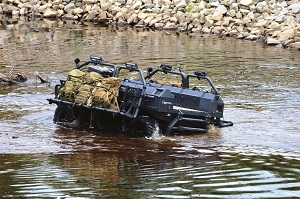
Passive navigation
Given apt worries among defence forces that casualties may be vulnerable en route to a collection point (whether transported by UGV or any other means), Rheinmetall Canada has integrated a ‘Blackout Mode’ in the Mission Masters.
In this mode, the Lidar stops transmitting to prevent detectable laser pulses being emitted, and the UGVs switch to what Tremblay and Diniz call “passive navigation”. This typically means using only the inertial navigation system, although other sensors such as electro-optical (EO) or infra-red (IR) cameras can be used for obstacle avoidance and localisation (by the UGVs recognising features such as specific trees, structures or geological features to triangulate their position) without significant risk of detection by hostile agents.
Passive navigation can also encompass uploading 2D or 3D maps into the Mission Master’s onboard memory. This can be critical for localisation in the event of GNSS denial (including jamming and spoofing attacks), which is an increasingly frequent concern among defence strategists, with the deliberate insertion of errors into GNSS feeds being a common tactic of some military forces.
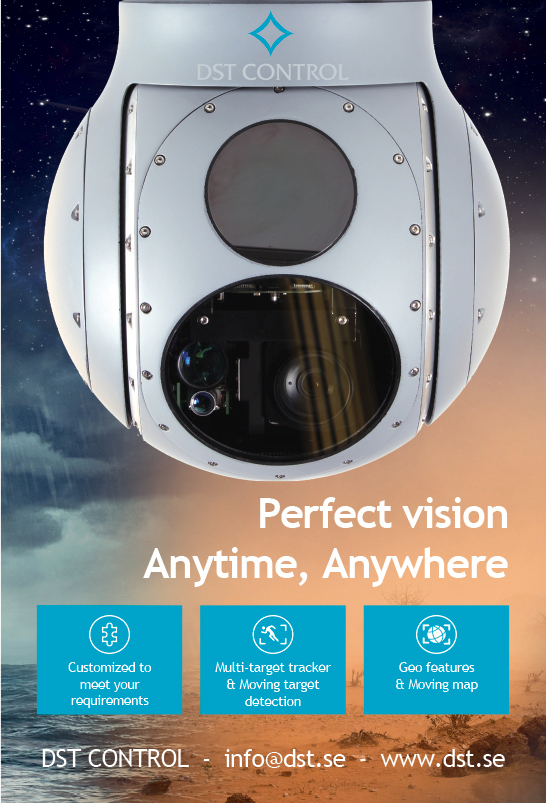
“Even without that, we’ve specifically chosen a very robust inertial measurement unit (IMU) system, such that the Mission Masters can go for quite long distances before distortions and degradations result in any noticeable drift during dead reckoning.
“But, again, the SLAM system we’ve developed and embedded means the UGVs can triangulate their positions and recalibrate their INSs if they visually recognise a particular landmark, so it’s even more unlikely they would reach any state of IMU drift,” Tremblay notes.
Diniz adds: “We’ve also tested the UGVs in a mine, where receiving GNSS is impossible, and there we used the Lidar to form a detailed map of the mine in real time. And because the UGVs can integrate mesh radios and form a mesh network, once the first UGV created that point cloud-based map, it communicated the information back to the others, so they could navigate and localise themselves while the leader continued to explore the mines and expand the map everyone was using.”
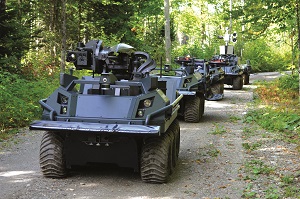
Damage downtime
When onboard energy runs low or signs of damage are visible, the UGV can be set to follow a soldier back to its base, or a return button on the GCS can be pressed that will trigger the vehicle to automatically backtrack all the way to its deployment point.
As with pre-deployment preparations, routine maintenance for the UGVs after and between missions tends to be minimal, even in cold climates where conditions ought to be detrimental to batteries and mechanical components. This is largely attributable to Rheinmetall Canada’s choice of powertrain.
“Batteries are expensive and don’t perform well at extremes of temperature, but we’ve worked around that to minimise downtime and the rate at which they need to be replaced,” Diniz says.
“The CXT can be left outside at -40 C overnight and will still start the next morning, primarily thanks to the liquid cooling and heating circuit, which enables the diesel engine to heat the batteries to their optimal temperature of 20-25 C.”
As the XT runs principally on diesel, it needs even less preheating and thermal management than the CXT. Additionally, ironic as it may sound (as one of the primary motivations of vehicle electrification is to reduce maintenance), Rheinmetall Canada reports that the absence of a battery pack contributes to easier maintenance for the XT than its smaller counterparts, as any standard garage can maintain or repair the diesel powertrain, and there is no large and expensive battery to repair or replace.
Tactically, the fully electric SP powertrain, CXT hybrid powertrain and all-diesel XT powertrain each have their own advantages. While the SP will take longer to recharge than the CXT and XT will take to refuel, it can naturally take electricity from a wide range of grid sources, and it is the stealthiest option – not only for its relatively small size, but also for its lack of emissions (exhaust, heat and noise included), making it harder to detect when carrying vulnerable casualties or being recharged in contested areas.
“With all three Mission Masters, downtime really is limited to recharging and refuelling, or changing flat tyres,” Tremblay says. “Unless you know for a fact that a critical system is damaged, you don’t need to perform any maintenance checks, as the self-diagnostic subroutine enables each Mission Master to keep checking itself; thus it can just be sent back out for another mission.”
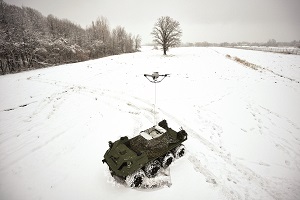
More missions to master
In addition to the ongoing development of its software (with safety certification to ISO 26262 and ASIL-D being end goals), Rheinmetall Canada is eyeing expansion into a number of key related technological areas, including wider capabilities across swarming to enable teams of UGVs to work together towards mission goals; these are likely to come before high-production outputs of the Mission Masters are prioritised.
“The UGV industry and market have come a long way over the past five years, but there isn’t huge requisitions of UGVs being placed yet, not in the way that companies today order 100 UAVs at a time for logistics, ISR or asset inspection,” Tremblay observes.
“But what we do see right now is a large and growing body of interested nations, who are exploring UGV technology and coming to understand what it is capable of. The first really large contracts for UGV orders will probably start happening between 2025 and 2027. That will likely be when nations have figured out what they want to do with UGVs and where they want to take them.
“For now, we can confirm that the USMC is very satisfied with the performance of the Mission Masters and their autonomous capabilities, such that they will be used in further exercises with the USMC, mainly in that Medevac capacity, although there will also be some ISR and weapon-platform testing too.”

Specifications
- Mission Master SP
- Battery-electric
- Eight wheeled
- Dimensions: 2.95 x 1.55 x 1.33 m
- Weight (without payload): 1000 kg
- Payload capacity: 600 kg
- Maximum endurance: eight hours
- Maximum ground speed: 30 kph
- Maximum amphibious speed: 5 kph
- Maximum climb angle: 40°
- Ground clearance: 24 cm
Mission Master CXT
- Hybrid diesel-electric
- Four wheeled
- Dimensions: 3.16 x 2.25 x 1.53 m
- Weight (without payload): 2200 kg
- Payload capacity: 1000 kg
- Maximum range: 450 km (50 km on battery alone)
- Maximum ground speed: 40 kph
- Maximum amphibious speed: 4 kph
- Maximum climb angle: 35°
- Ground clearance: 50 cm
Mission Master XT
- Diesel engine with hydrostatic transmission
- Four wheeled
- Dimensions: 3.72 x 2.57 x 1.9 m
- Weight (without payload): 2217 kg
- Payload capacity: 1000 kg
- Maximum range: 750 km
- Maximum ground speed: 40 kph
- Maximum amphibious speed: 5 kph
- Maximum climb angle: 35°
- Ground clearance: 50 cm
Some key suppliers
- Chassis and wheels (Mission Master SP): ODG
- Chassis and wheels (Mission Master XT): Zeal Motors
- Autonomy kit: Provectus Robotics Solutions
- GCS: UXV Technologies
UPCOMING EVENTS
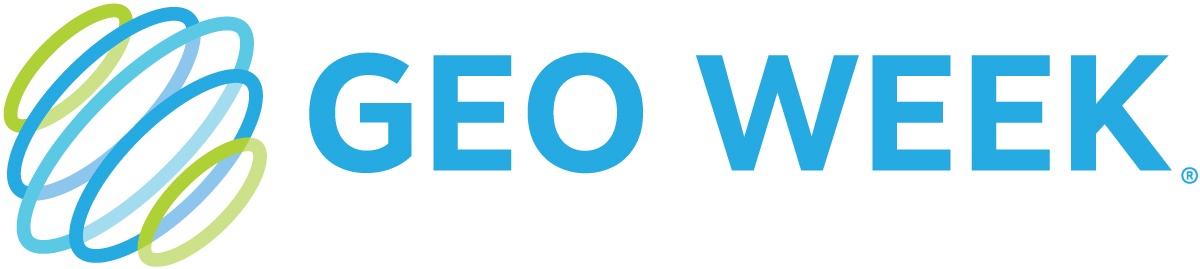
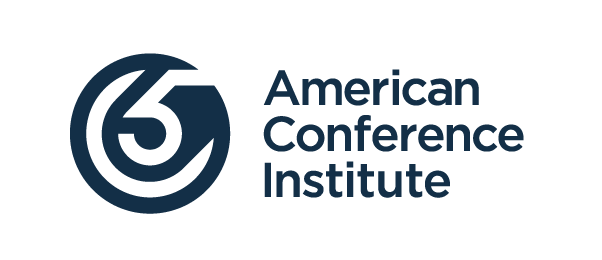
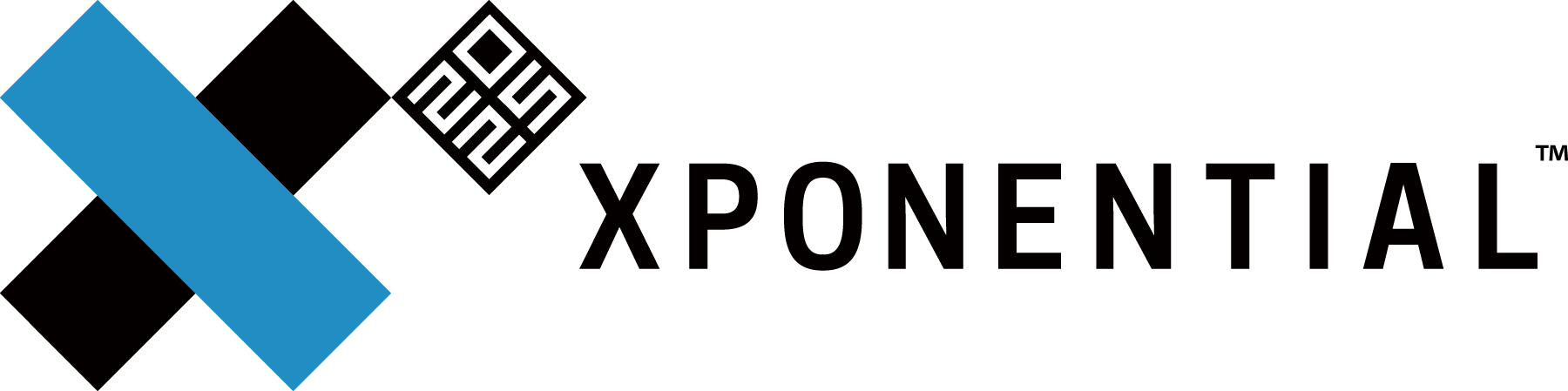
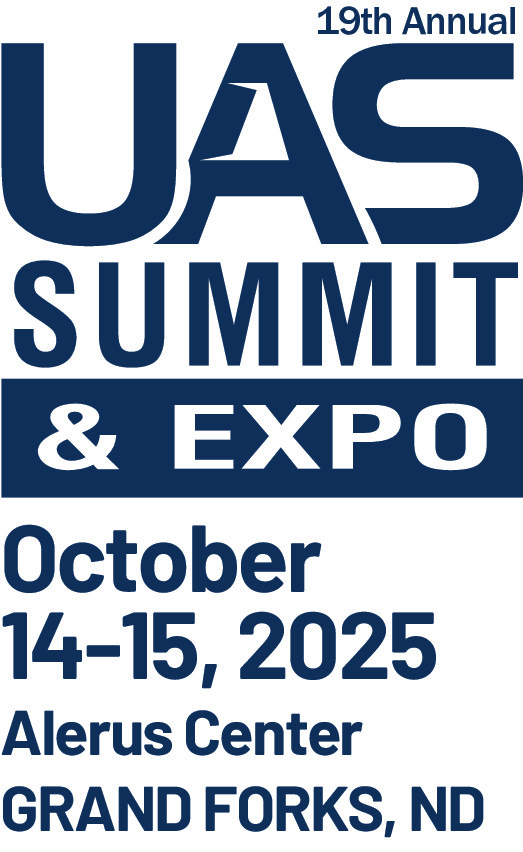
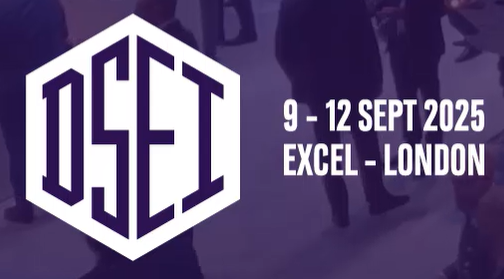
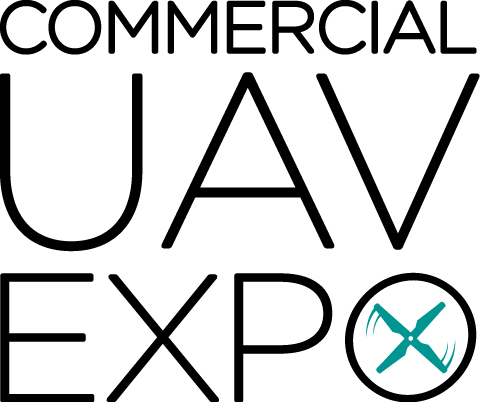
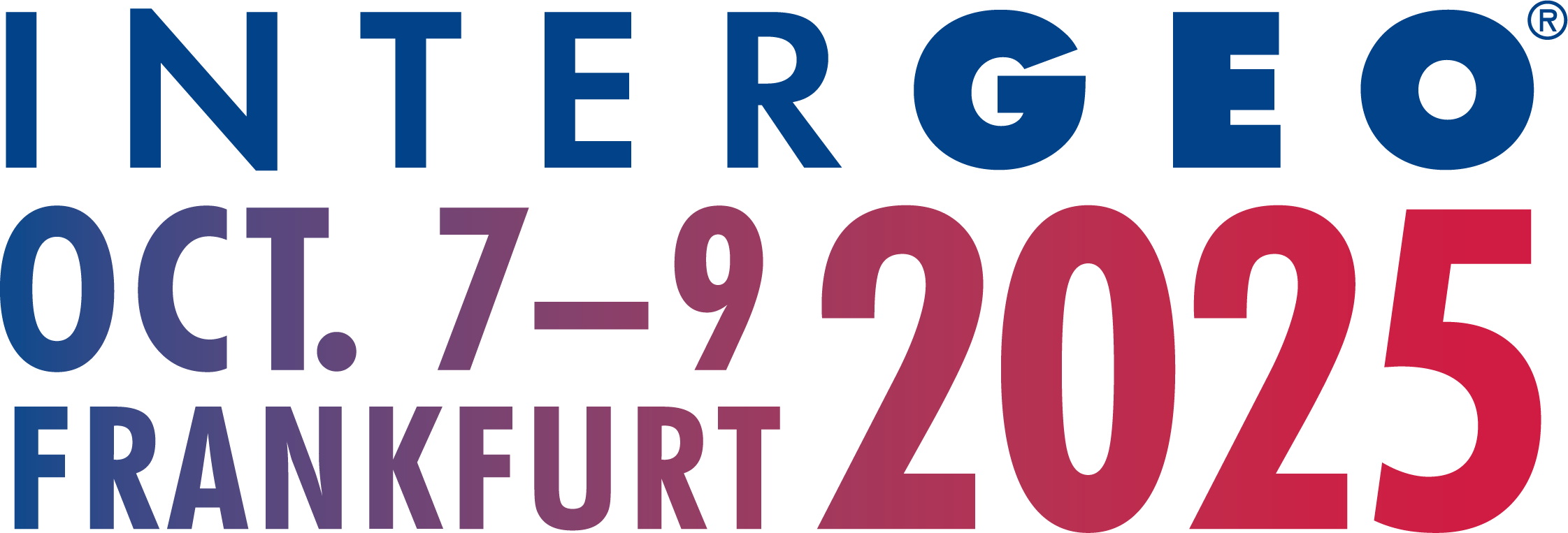
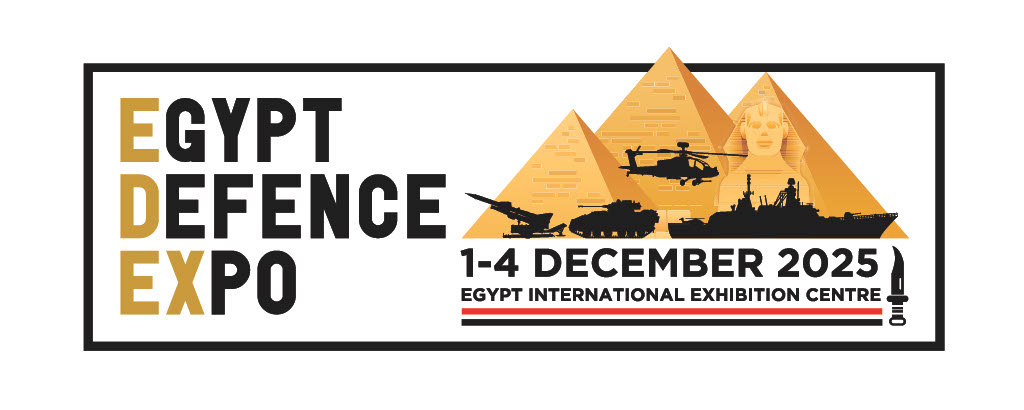
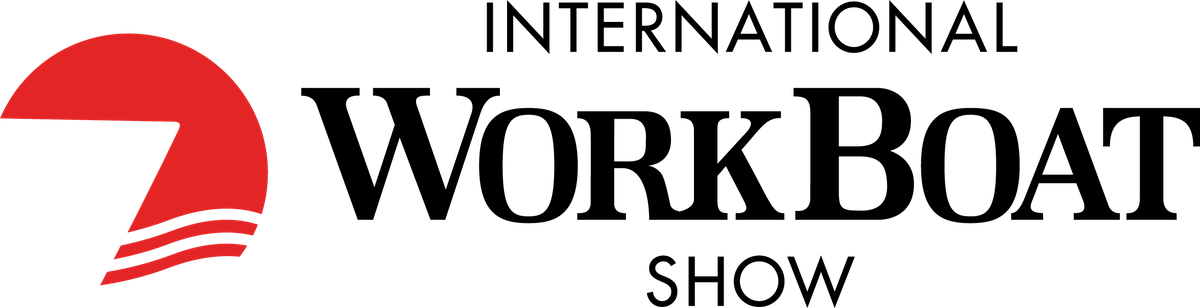
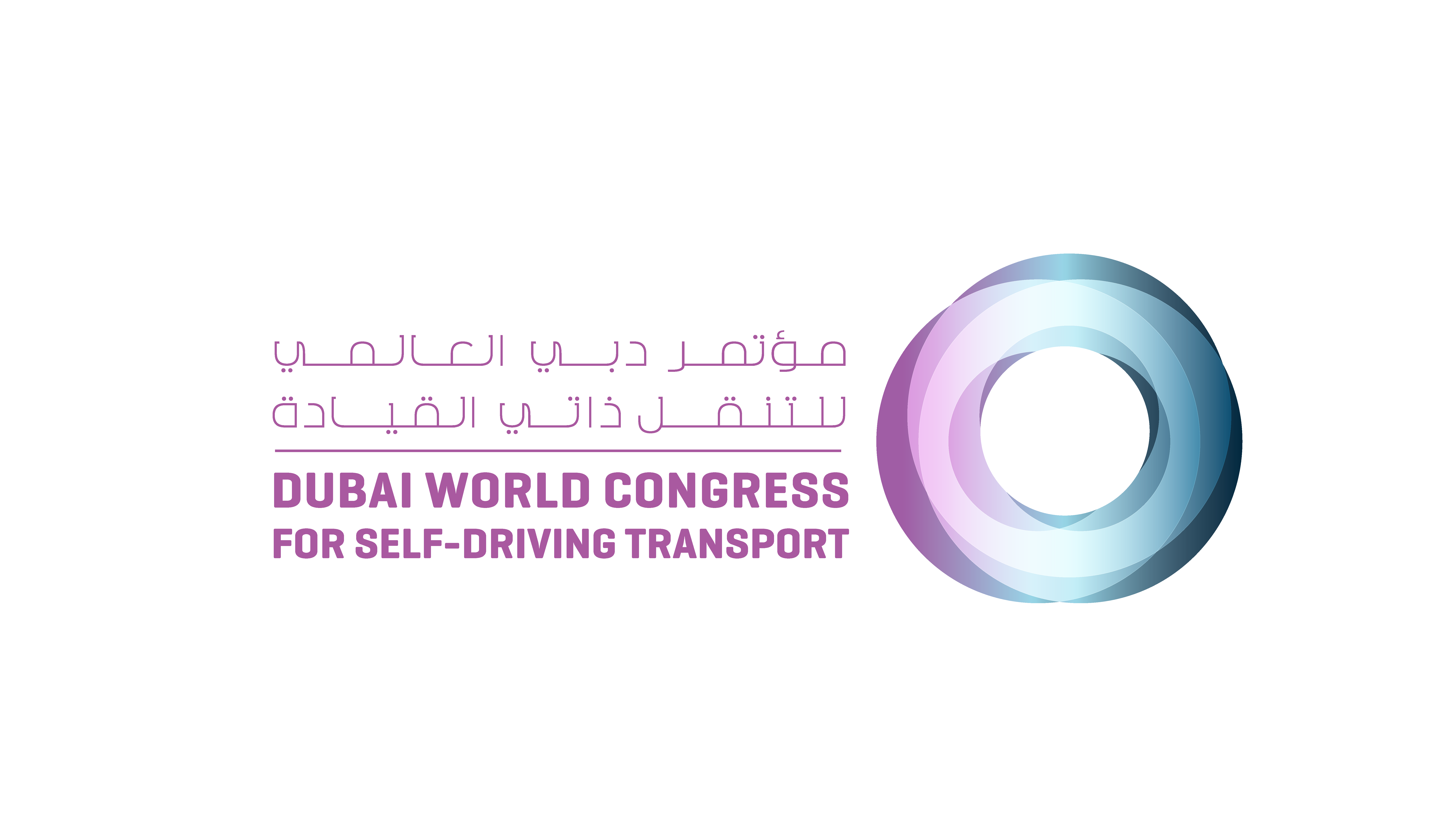
