USVs
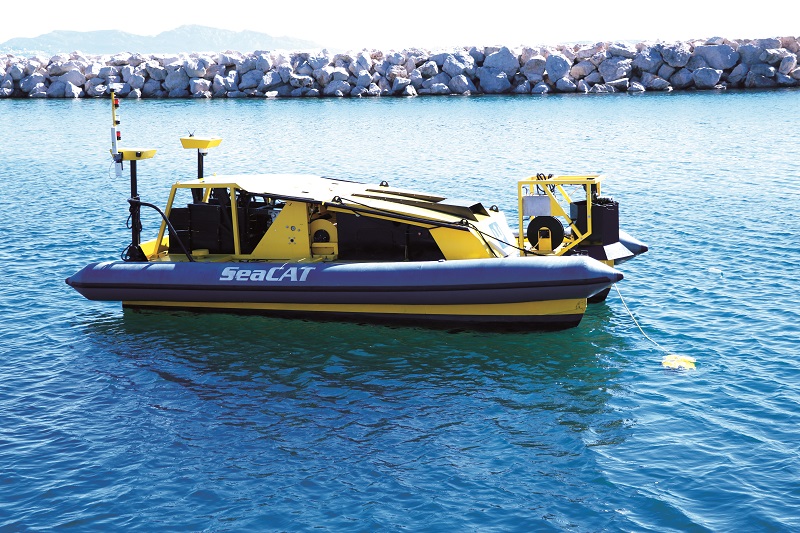
Rory Jackson looks at how some developers are meeting demands for uncrewed marine craft to carry out specialised tasks
Special editions
Autonomous vessels for marine applications continue to be developed and matured in a similar manner to that observed in UAVs over the past few years. That is, they are highly optimised and specialised, and are produced in batches of no more than a few hundred rather than, say, thousands of units, as might be seen elsewhere in the uncrewed systems market.
Where they might once have been purely hydrography and mine survey solutions though, USVs are now being used for increasingly complex and close-up work (rather than making observations at a distance) in a number of important contexts.
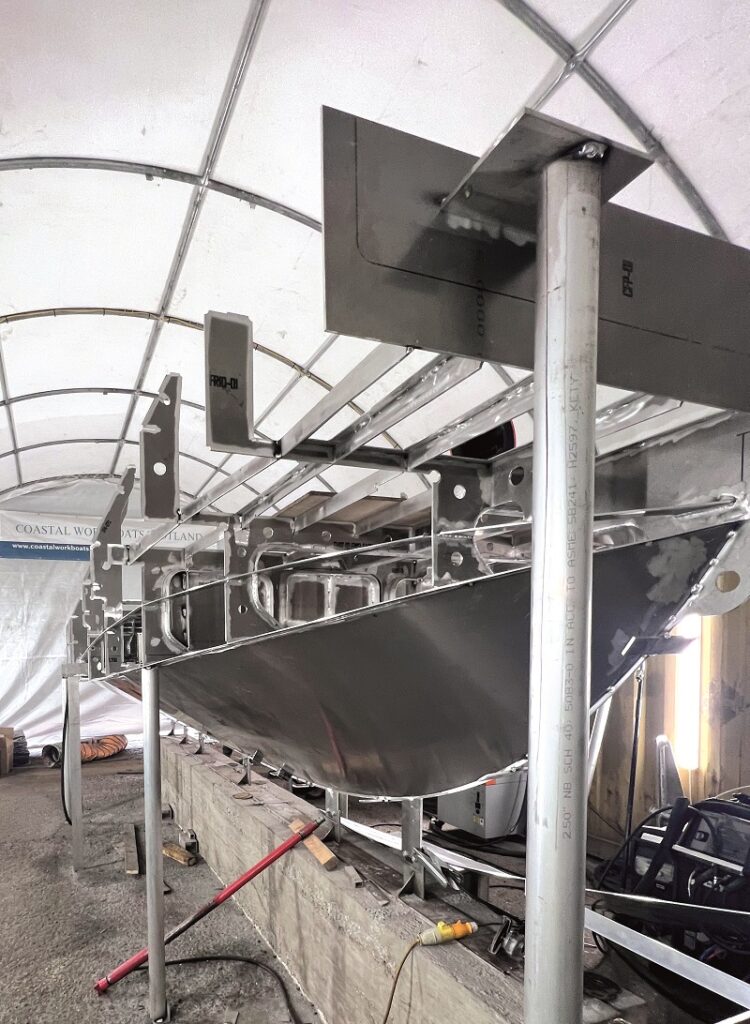
Environmental clean-ups
The world’s oceans are a major area of concern for environmentalists. Fortunately, more and more organisations are recognising that uncrewed vessels can mitigate the damage from marine waste.
For example, Subsea Tech was recently invited to take part in a Horizon 2020 project known as SeaClear (SEarch, identificAtion and Collection of marine Litter with Autonomous Robots), to gauge the extent to which the company’s solutions could detect and collect litter from the seabed.
“To that end, we developed our SeaCAT USV’s inter-deployment capabilities, and had it simultaneously stow and deploy two of our ROVs while in the water,” explains Yves Chardard, owner and CEO of Subsea Tech.
“The SeaCAT is a 6.8 m vessel and doesn’t have a huge amount of space, but we managed to deploy our Tortuga ROV from the stern, and our Mini Tortuga ROV from the bow. We then updated our autonomous navigation systems to make sure the ROVs could swim close enough to each other but without interfering with each other or the USV.”
The concept of operations (CONOPS) was for the Mini Tortuga to map the seafloor as well as identifying and geolocating litter, while the Tortuga would collect any litter and deliver it into a basket suspended from the SeaCAT.
“The automatic collection is done by mechanical grippers,” Chardard adds. “And the CONOPS for navigation is initially for a general back-and-forth lawnmower pattern across the area to be cleaned.
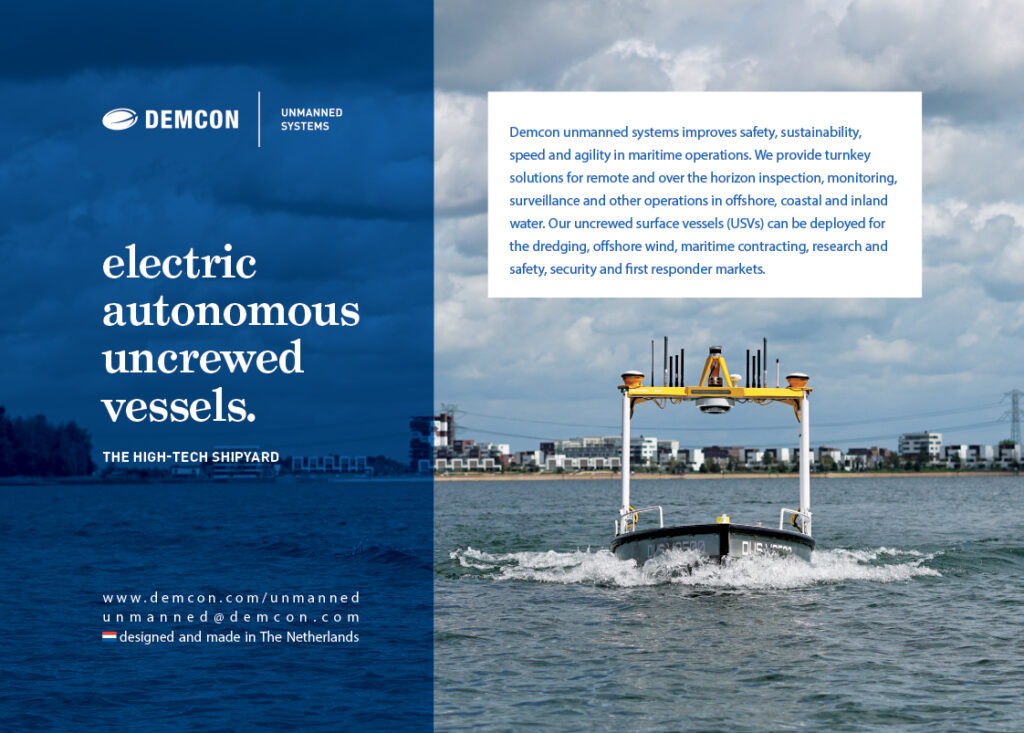
“The Mini Tortuga’s mapping and litter detection is delivered by umbilical tethers to the SeaCAT, so the mothership can deviate from waypoints to seek out and prioritise its collection.”
Subsea Tech intends that the Tortuga should move faster than the Mini Tortuga, so that the former can more easily dart about collecting litter while the latter maps and scans with a slower, more stable motion.
In situations where the density of litter is too much for the Tortuga to collect while keeping up with the SeaCAT and Mini Tortuga, it becomes the primary navigation arbitrator, and the other two systems slow to match the Tortuga’s pace.
As well as serving as the launch, storage and recovery platform for the ROVs, the SeaCAT is also their power source and the central ‘brain’ of the solution. All the control software for the ROVs is embedded in the SeaCAT’s computer, with commands transmitted down – and underwater sensor data transmitted up – via the tethers.
“We supervised all three vehicles over 5 GHz wi-fi from a shore station, but all the autonomy was inside the SeaCAT,” Chardard notes. “We deployed a UAV from the SeaCAT for aerial litter detection on the surface or through very clear waters, and also for long-distance navigational safety; it can see incoming ships much further away as well.”
The SeaCAT has an empty weight of 1075 kg and a 500 kg payload capacity. It is powered by a 12 kW diesel generator with up to 400 litres of fuel on board, and two unidirectional Aziprop electric thrusters for propulsion, enabling it to transit safely through sea states up to level 5.
A system of electrical winches and tilting baskets enabled the launch, recovery and storage of the ROVs, with up to 300 m deployment range for the Tortuga and Mini. A 40 m tether powered the UAV, a DJI Matrice M210 RTK.
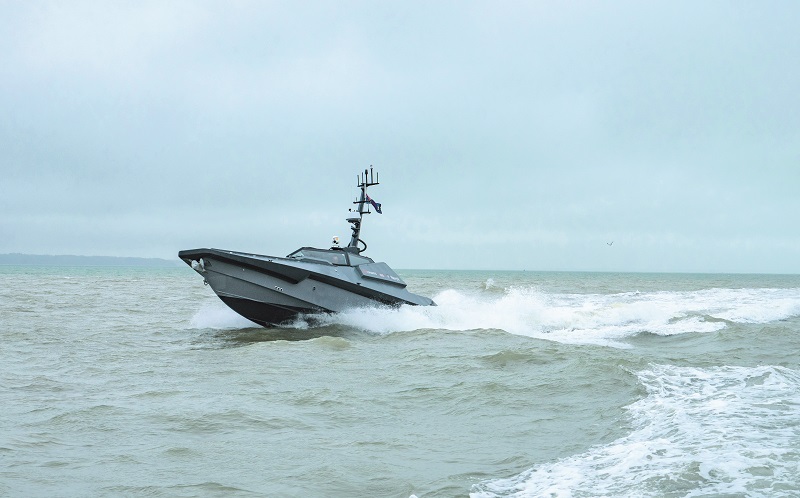
Search and rescue
Edinburgh-based Zelim is developing its Guardian USV to be the first uncrewed system capable of rescuing human casualties from water – including in dangerous high sea states. It will offer the flexibility of both crewed and uncrewed operation modes though, with both a remote and onboard helm.
There are several reasons why fully uncrewed rescuing of souls at sea is desirable. Rescue crew members are often killed in the line of duty, particularly during the launch and recovery of their fast rescue craft.
Also, the physical act of hauling casualties from the sea can injure the victim or the rescuers, the rescuers themselves can fall overboard, or they can end up suffering from PTSD, particularly in cases where casualties have already died.
Sam Mayall, CEO and founder of Zelim, was previously a career mariner with experience of these issues, so in 2017 he conceived an uncrewed fast rescue craft. At the time, there was scepticism that casualties could be safely lifted from the water by a totally uncrewed boat.
“In 2020 though, Sam had met with myself and others, and we built a full-scale prototype of the Guardian in the summer of that year,” recounts Doug Lothian, CTO of Zelim.
“That was 6.5 m long and based on a Royal Marines Rigid Raider. It had our Swift casualty recovery conveyor mechanism mounted in the front, and we demonstrated that it could lift a casualty from the water, albeit with a rescue crew operating on board.”
By December 2020, Zelim had developed the Guardian’s remote systems, upgraded its engines, hydraulics and electronics, and subsequently performed what it believes to be the world’s first uncrewed recovery of an incapacitated casualty.
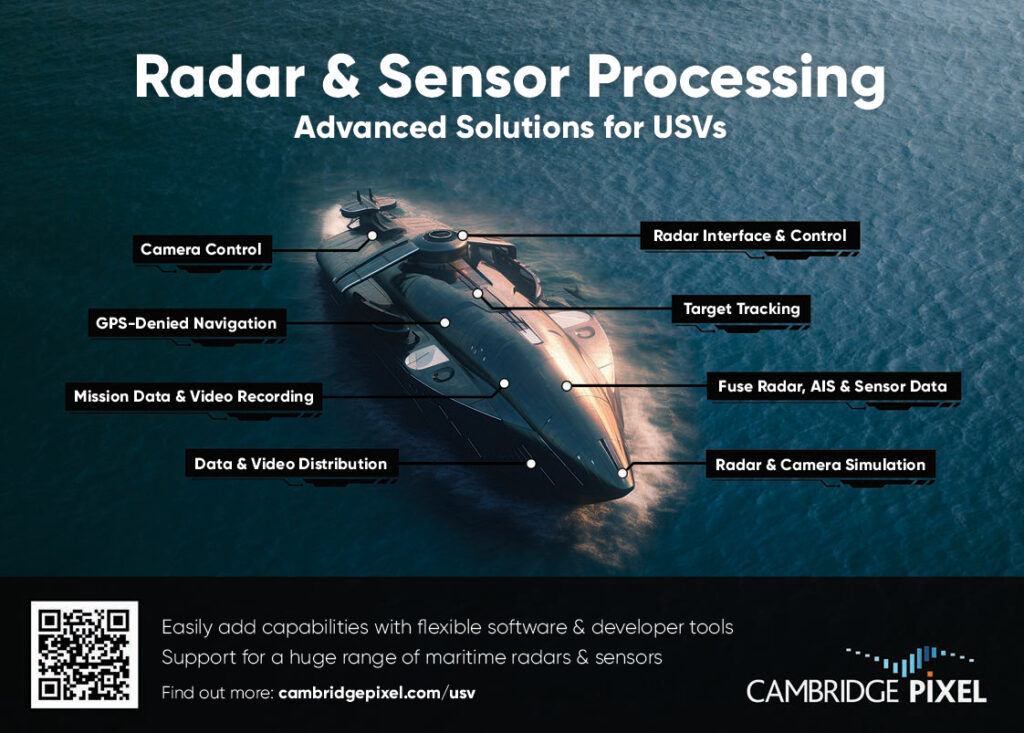
Interested partners and supporters of the project include Ocean Infinity, Chartwell Marine, InnovateUK and the Offshore Wind Growth Partnership, which represents the UK’s offshore wind farm industry. Working with these groups has provided advice and funding for the design, development and fabrication of the next Guardian prototype, which will be an OEM vessel rather than a modified Rigid Raider.
“There are more than 150 electronic components in the Guardian that need to be fully tested and integrated to support its self-righting capability, including things like closing and re-opening ventilation for the diesel engines – fuel power is necessary because of regulations on minimum endurance for rescue craft,” Lothian says.
“Many self-righting vessels will close those inlets automatically but not re-open automatically, so features like that had to be made from a blank sheet.
“By this July we’ll be testing that vessel on the water, and through the winter weather later in the year we’ll be able to put it through its paces. That will culminate in a validation trial with Northstar Shipping and Seacroft Marine Consultants.”
The Guardian is a high-speed planing craft with a frontal deep vee to cut through water, and appropriate buoyancy in the superstructure as well as ballast below to enable self-righting. Also, its GZ curve (the angle at which a vessel will roll over and self-right) has been calculated to work across different sea states.
A rescue conveyor called the Swift also provides a stabilising effect when deployed at the front of the Guardian. Its belt consists of a soft, gripping material that handles and orients casualties without causing or exacerbating injuries.
As a final measure, an inflating bag on the craft will expand to push it back upright. Meanwhile, AI survey and recognition of casualties is enabled by SARBox, the company’s proprietary and sensor-agnostic computer vision solution.
“We use Sea Machines’ SM300 as our onboard autonomy and control suite,” Lothian adds. “The big draw there was how closely they’ve sought to understand our vehicle and purpose.
“Instead of just delivering what we want, they delivered what we need. They made technical recommendations, corrections and fine-tuning to their offerings in order to make the Guardian smarter and more successful.”
Future developments include hybrid-electric powertrains (or even fully electric, given ongoing advances in marine batteries and e-thrusters) to decarbonise the Guardian without falling short of minimum endurance regulations.
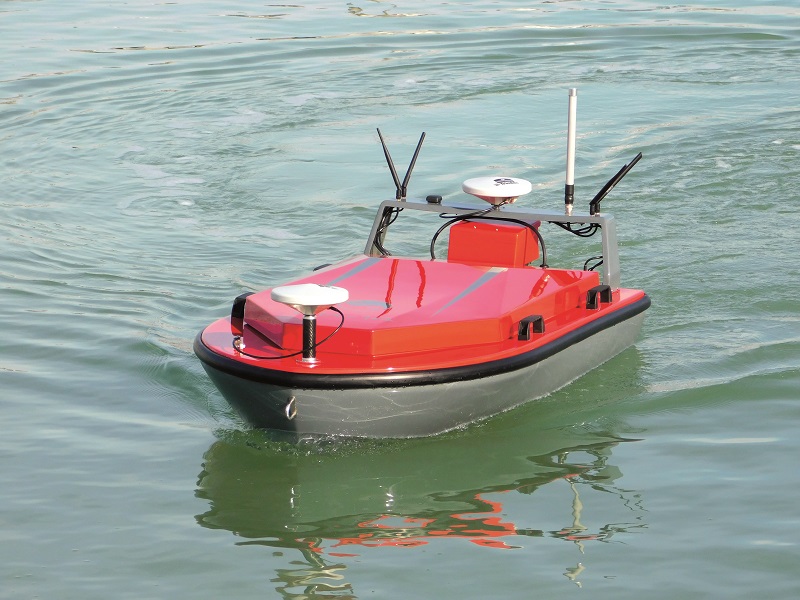
Defence
As conflicts and other border concerns around the world grow more severe, so are a growing number of countries turning to uncrewed systems as a force multiplier or gap filler for guarding strategic maritime resources.
Seeing that need, L3Harris’ portfolio of USVs (or ASVs, its preferred term) has grown significantly over the years, for defence as well as related applications. Most recently it has taken on defence-related missions in the Middle East, enabling it to optimise its uncrewed vessels through real-world trials and operational data.
“Our Shadowfox USV for instance is a 13 m aluminium vessel, which is an evolution of the MAST-13 platform,” explains James Cowles, senior business development manager with L3Harris, who works at the unit that produces its USVs.
“One MAST-13 unit is in service with the Royal Navy’s accelerator, NaxyX, while another is with Dstl [the UK government’s Defence Science and Technology Laboratory]. We also have an 11 m GRP platform operating with the [Royal Navy’s] Taskforce 59 in Bahrain.”
Although a lot of work goes into its USVs, L3Harris still considers the ASView control software as its core product. It has been developing it since 2008, and the eighth generation of it is due to be released soon.
“While some things, like sensor integrations into our autonomy software, have become simpler over the years as sensors have advanced, the big developments we’re looking at are around control – how the human interacts with our solution and how robust it is,” Cowles says. “To that end we’ve released a Sil-rated emergency stop system as part of ASView so that customers can be assured that, if all else fails, they have that as a back-up.
“That’s on top of our autonomy platform providing collision avoidance through radar, AIS and so on. We tend not to use Lidar, because in the defence sector and much else of the maritime world, we feel if something’s close enough for a Lidar to detect it, you’ve let it get too close.”
He adds that another major focus of the eighth-generation ASView is disaggregation of control – that is, the ability to have multiple control locations – and the construction of a sensible system for handing control from one GCS to another. That means programming logic into the solution
by which no-one can forcibly take control, or give control to someone else without prior consent or confirmation.
As USV developers increasingly integrate radars and cameras for obstacle detection and avoidance to augment their autonomous GNSS waypoint navigation, the ability to rapidly integrate new sensors becomes prized. On top of that, USV operators – particularly those in defence work – might want to quickly hot-swap radars in the field to suit different mission environments and objectives.
To that end, some USV manufacturers (including BAE Systems with its P24 craft) are using Cambridge Pixel’s software modules and HPx radar interface cards. These can enable smooth connectivity and the integration of radars from small commercial maritime units into high-end specialist surveillance sensors, such as those from Hensoldt, Sperry Marine, Raytheon, JRC and Terma.
Also, the company’s SPx Tracking Server application can enable radar-specific control panels for the GCS operator, with software displays of status information and controls for gain, sea and rain clutter, and range scale. And its SPx Camera Manager can direct gimballed cameras to point at radar, AIS or fused-sensor tracks for direct surveillance of targets.
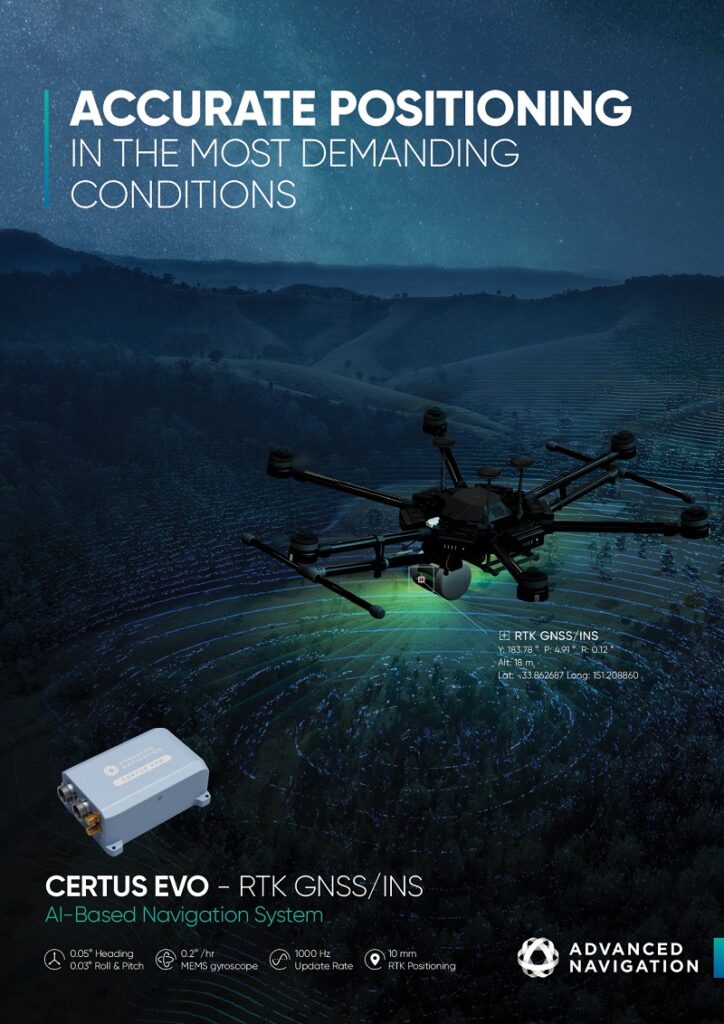
Shallows hydrography
Countries such as Italy, which is dotted with coastal and riverine assets, can benefit hugely from hydrographic surveys, and although rivers naturally need a craft to be narrow and nimble to avoid running aground, the more powerful sonars and other survey sensors are often too large and heavy to make small, light USVs a realistic option.
To resolve that, Codevintec has designed its CK-14 as a small USV, weighing just 15 kg when empty but also capable of carrying 40 kg of payload instruments. Heavier payloads are expected to be both possible and safe, pending further trials.
“That makes it one of the lightest USVs on the market for its payload capacity, with a very big moon pool,” says Giorgio Poli, product manager at Codevintec. “The moon pool measures 33 by 27 cm, and can host instruments like ADCPs as well as multi-beam, single-beam and sidescan sonars.
“It’s constructed from a resilient carbon-Kelvar material, which also contributes to the lightness, and is waterproofed by a gasket in the internal cover.”
The CK-14 measures 140 cm long, 90 cm wide and 45 cm with a roll bar installed. The system is powered by a 4S, 16 Ah lithium-polymer battery, with propulsion coming from two fully flooded brushless motors each producing 6.7 kg of thrust; their propellers also provide steering to avoid using a rudder, a potential point of failure.
“The USV is ideal for rivers, lakes and coasts, up to sea state 3,” Poli adds. “The data link from GCS to USV can run over a short-range RF link, a 5 km wi-fi link or LTE if users really want to operate or monitor it from a long distance away. We’re seeing particular interest in it from universities and research organisations, as well as government agencies.
“They are also interested in using our Sestante autopilot, which includes our smart controller and a 7 in display through which users can intelligently define a survey area they want to monitor.”
At the time of writing, Codevintec was looking for partners to distribute and promote the CK-14 overseas.
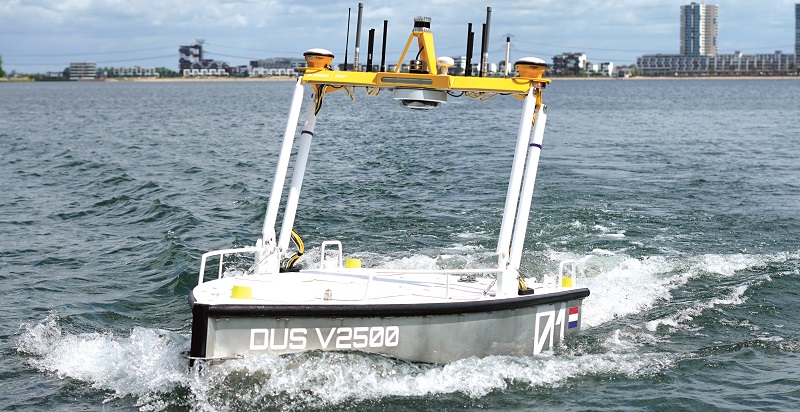
Dredging surveys
We last featured Netherlands-based Demcon Unmanned Systems (DUS) in UST 32 (June/July 2020) and its DUS-V USVs, which were being put through their paces as a solution for surveys in harbours and other inland dredging work sites.
Since then, Demcon has continued developing and growing its USV product and technology portfolio, and now offers a few other USVs, including its flagship, the V2500.
“The first prototype was a 2500 mm vessel – hence the name V2500 – which held all the survey equipment normally packed into an 8 m manned survey vessel, but since then we have increased its capacity and length over time,” says Fedor Ester, managing director of DUS. “It is now a 3 m vessel, but we kept the V2500 name since almost all the new builds have custom changes, which would have led to many name changes.
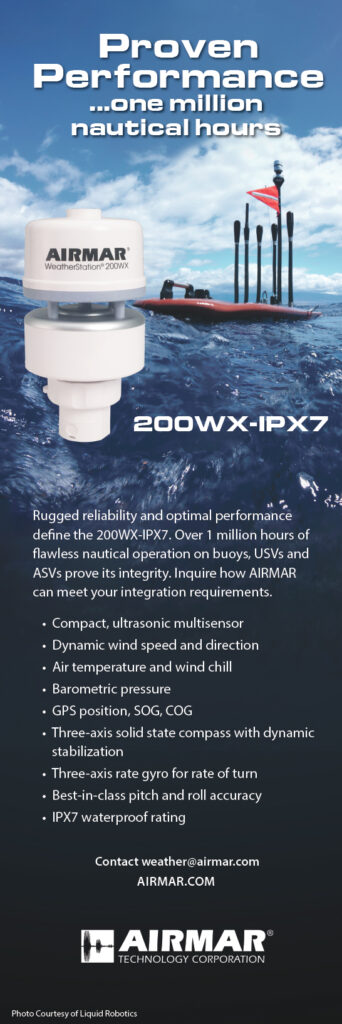
“This flexibility and modularity gave us more space inside, with a longer moon pool, making it easier to install different kinds of survey equipment. We also now have a double battery configuration that gives us an endurance of over 12 hours, or up to 52 km for surveying.”
A fast-charging system can enable the packs to be charged from empty to full in 4 hours, if an end-user wants to carry out additional surveys over a given period.
“We’re still working with Van Oord, the same dredging company we mentioned in 2020 [and now DUS’ strategic partner], where their first need was for custom solutions for inland waters,” Ester says. “After extending their V2500 fleet and gaining experience and confidence in the deployments, they broadened the deployments towards more near-shore operations.
“We were unsure about how the system would handle this different environment, in terms of the higher waves it would need to endure. To identify risks and validate performance, we first simulated the small V2500 design in our seakeeping, stability and flow simulation engine.
“We also validated payload sensor data performance through CFD modelling to verify if turbulent airflow could occur near the moon pool and so impact data quality in higher sea state conditions.
“The results were positive, and we only needed to make minor updates to the control model and path planning parameters to allow the real-time autopilot to cope with the displacement by certain waves. The V2500s are now being deployed in coastal projects globally.
“We’re also now building a 7 m vessel for offshore operations in conditions up to sea state 6. The first of those should be in the water at the end of summer this year.”
The 7 m USV from Demcon will be hybrid-electric, with the battery charged selectively so that the USV can venture into quiet areas. However, the onboard generators will be hydro-treated vegetable oil systems, so emissions will be negligible. These are expected to enable a mission runtime of somewhere around 2 weeks between refuelling depending on conditions.
Summary
It is worth noting that USVs seem to be coming in at larger and larger form factors. The smallest here has a 55 kg gross weight, a far cry from the 25 kg MTOW common among UAVs.
That makes perfect sense. USVs are not regulated to smaller sizes, as UAVs currently are, and they do not fight gravity to anywhere near the extent that UAVs do. Furthermore a larger, heavier USV means more space for sensors, enabling USVs such as the Saildrone Surveyor and the Mayflower (UST 42, February/March 2022) to carry out survey missions for dozens of organisations at once.
USVs will doubtless come in larger shapes in the future, as collision avoidance technology advances the safety case for such vehicles. So in addition to more autonomous ships for maritime freight, such as the Yara Birkeland autonomous container vessel emerging, it is likely that survey vessels of similar size to the Mayflower and the Saildrone Surveyor – or larger still – will become increasingly common sights on the high seas.
UPCOMING EVENTS
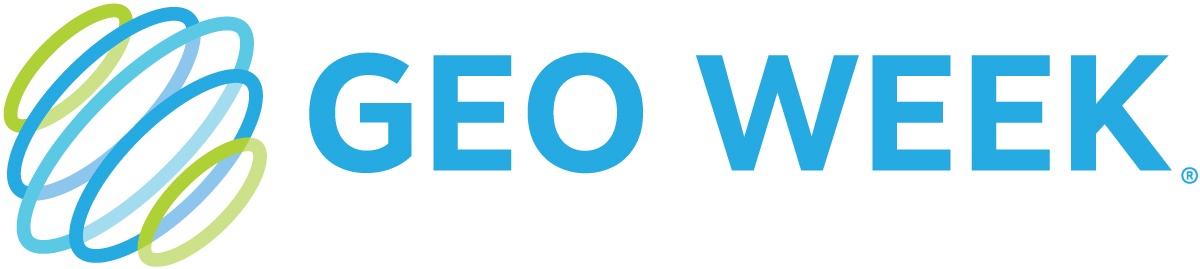
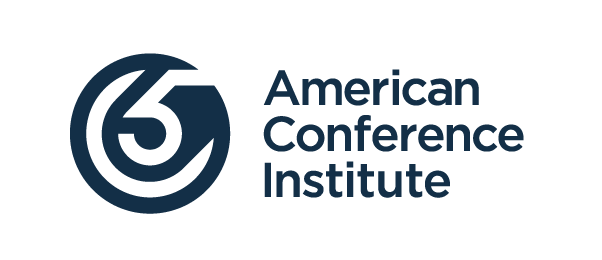
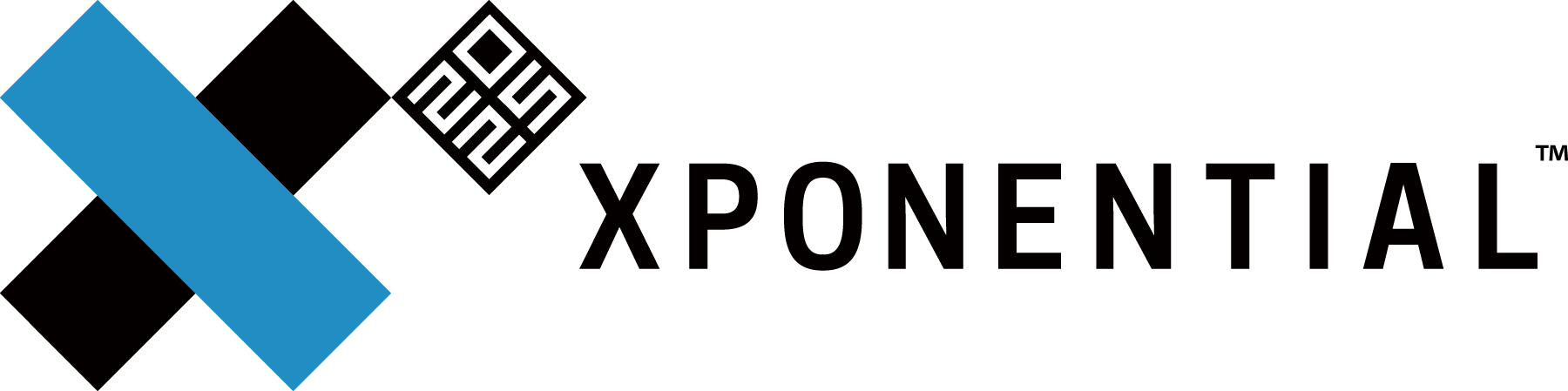
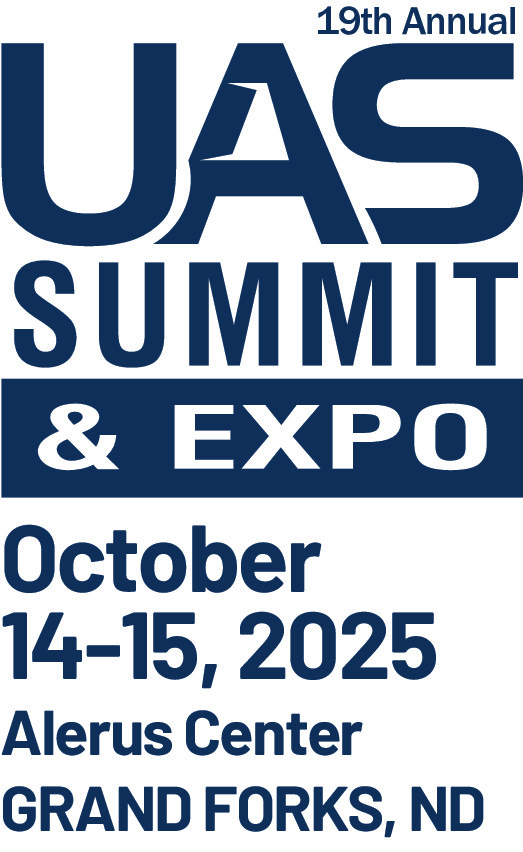
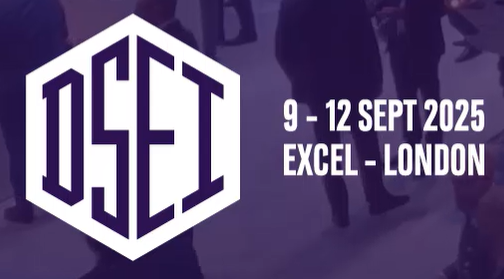
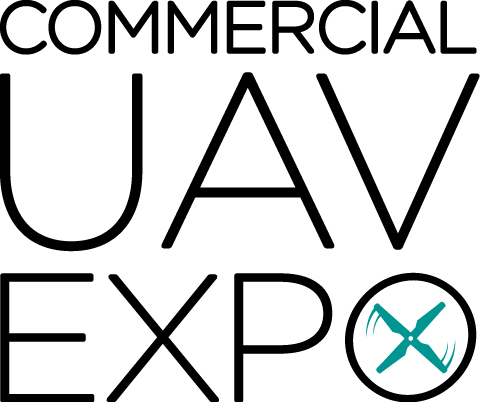
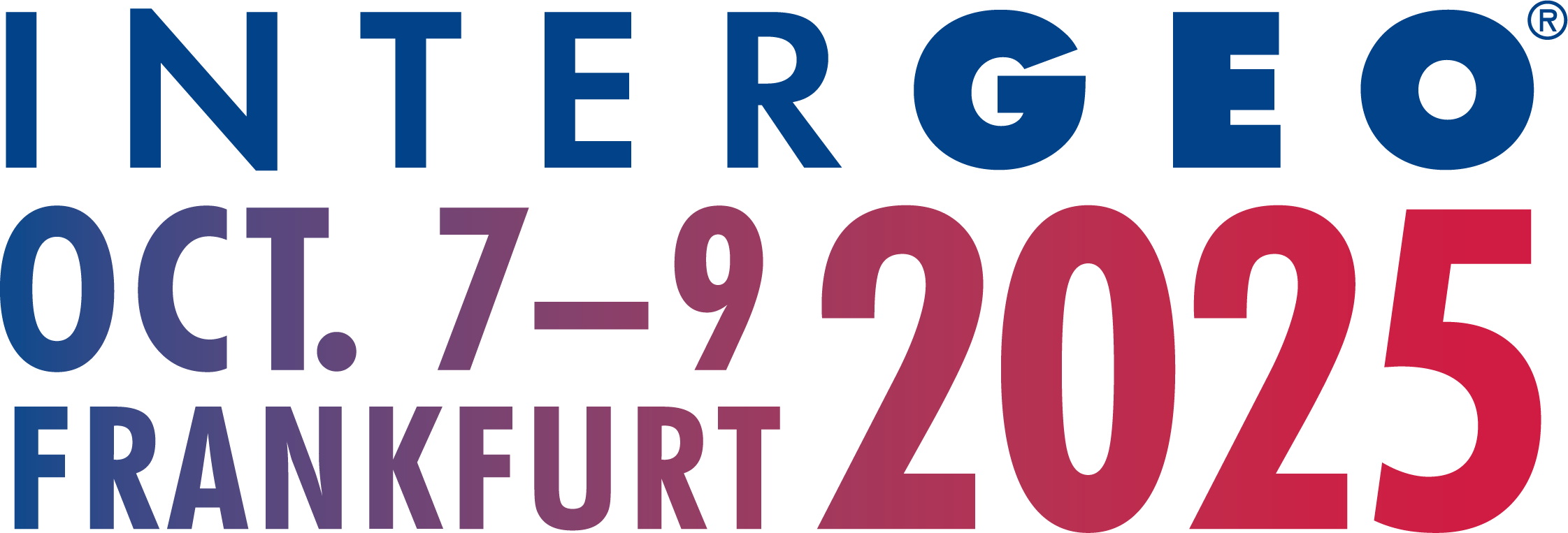
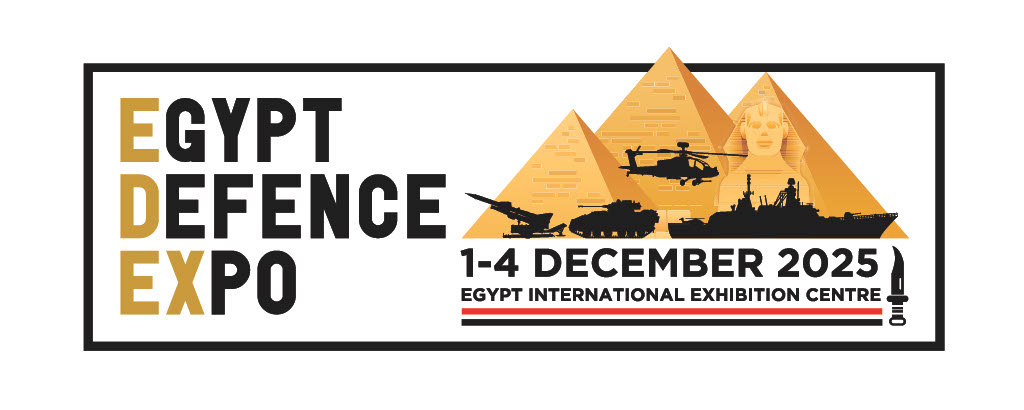
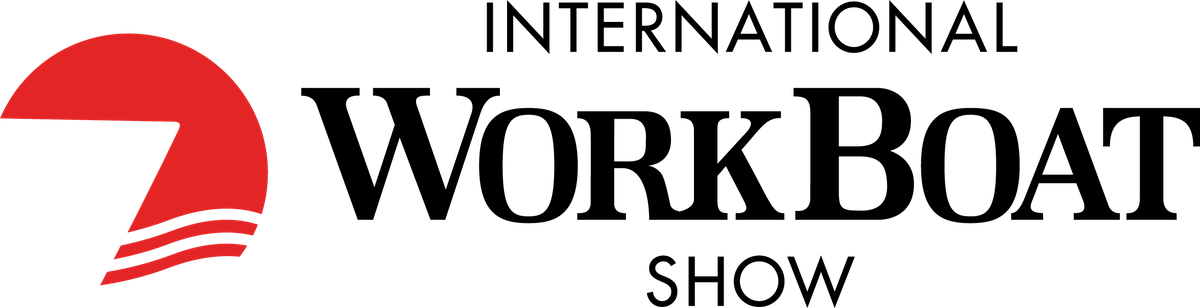
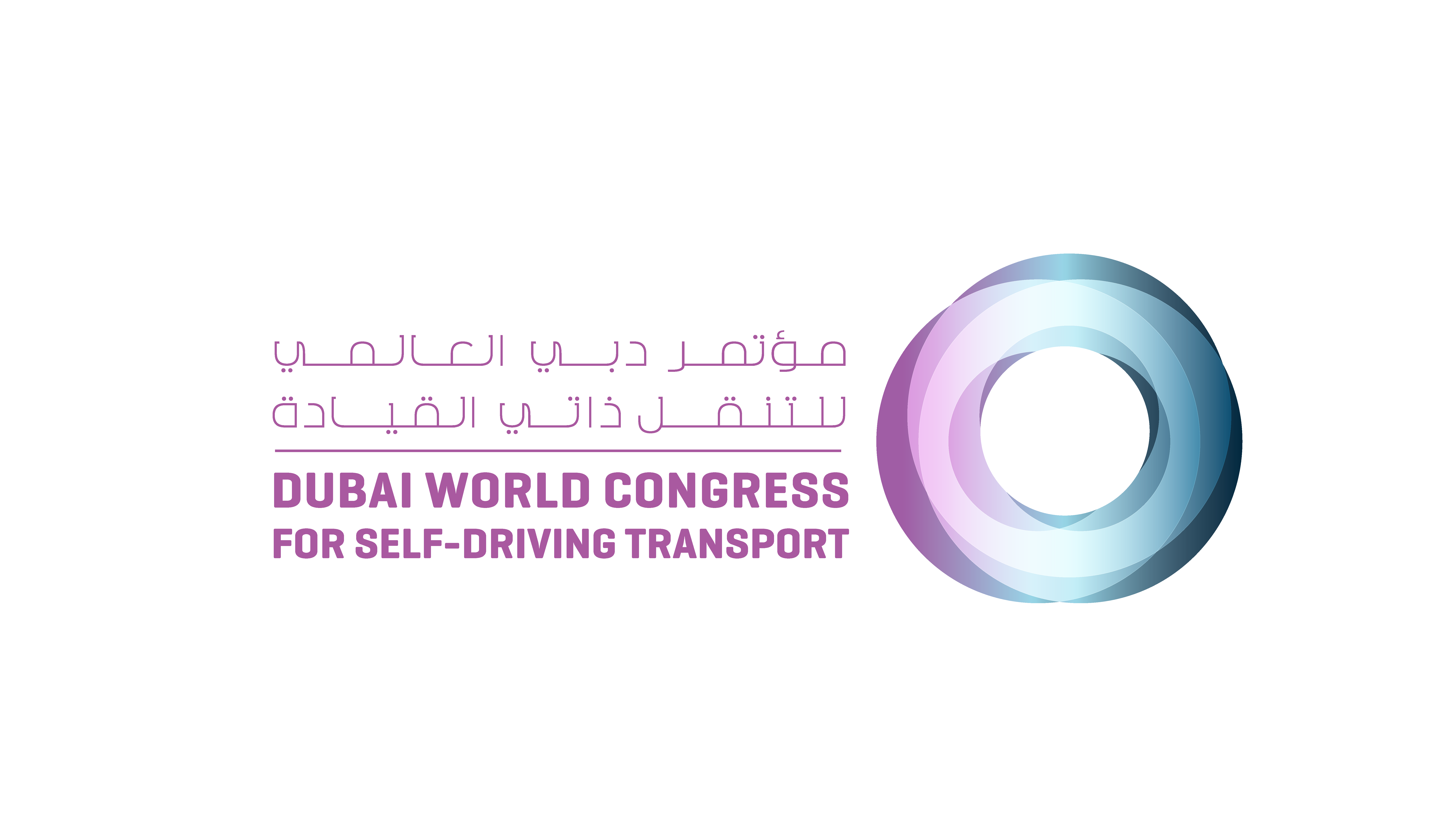
