Xponential 2023 part 1
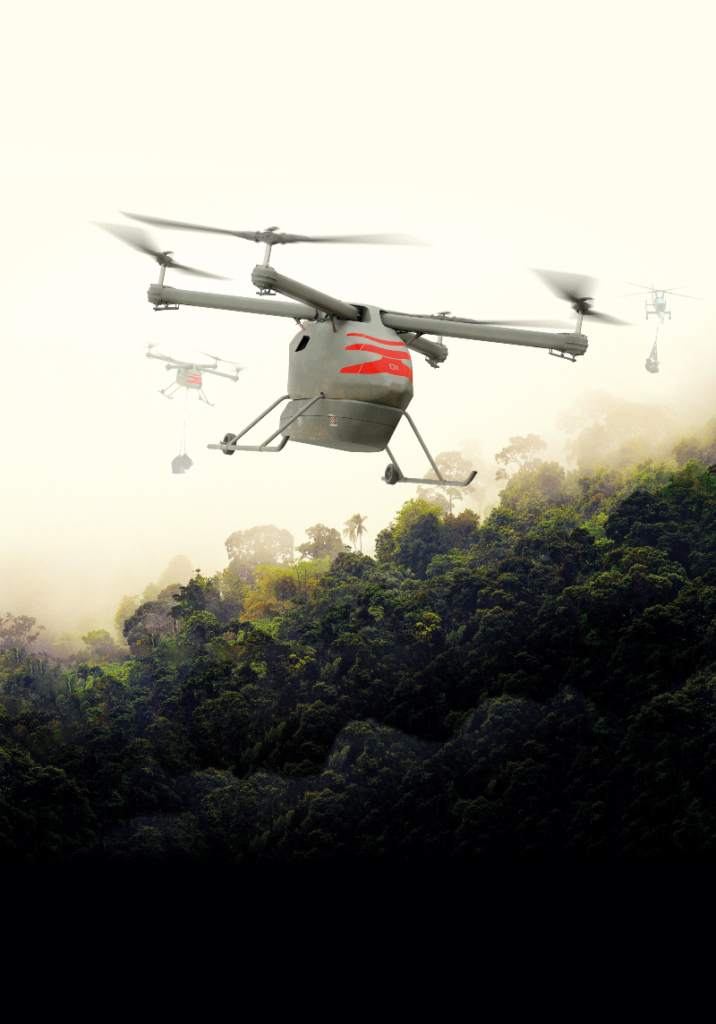
Rory Jackson presents highlights from this major uncrewed systems show, which this year paid a return visit to Denver
Notes from the Mile-High City
In May this year, AUVSI’s Xponential event returned to Denver for the first time in 5 years, the halls of its Colorado Convention Center playing host to hundreds of companies unveiling a fresh wave of innovations pushing the limits of uncrewed vehicles and technologies. Here is the first of our two-part selection of them.
Among the largest static vehicle displays in the expo hall was the Kargo UAV from Kaman Air Vehicles. Its primary mission is to provide military and commercial logistics support.
For military customers, the Kargo provides a low-cost, risk-worthy alternative to manned flight operations in contested environments. For commercial customers, it serves as an economical platform that can conduct cyclic, reduced-risk operations during bad weather or at night.
“Its total weight is about 2800 lb [1270 kg], and its cargo capacity makes up to 800 lb [362.87 kg] of that,” said Barry Maxwell. “The cargo system is configurable such that freight can be flown in a conformal pod or carried as an external sling load.”
While Kaman is focused on cargo operations, the Kargo’s large payload capacity can support a host of other mission-specific payloads. Its fuselage consists largely of a composite shell around a lightweight aluminium structure, with the pod fitted underneath between two landing skids. A gas turbine powers the UAV’s mechanical propulsion architecture, with the four rotors mounted above the fuselage on an X-shaped set of arms.
It is designed to carry a 90 kg payload for up to 390 nautical miles in 3.3 hours, or a 272 kg payload up to 143 nautical miles for 1.2 hours.
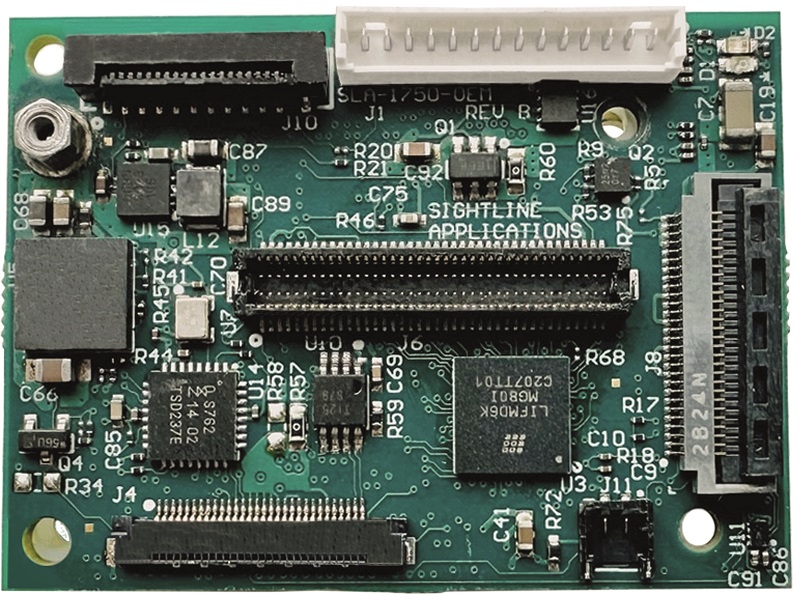
SightLine Applications announced updates aimed at expanding the use of its onboard video processing technologies. The first was its new 1750-OEM, which represents the next generation of its 1500 single-channel processor for advanced surveillance functionality and AI classification via small cameras.
“The 1750-OEM records 1080p30 video with H.265 encoding, whereas the 1500 just supports video quality up to 720p30 and encoding to H.264,” explained Danny Guerrero.
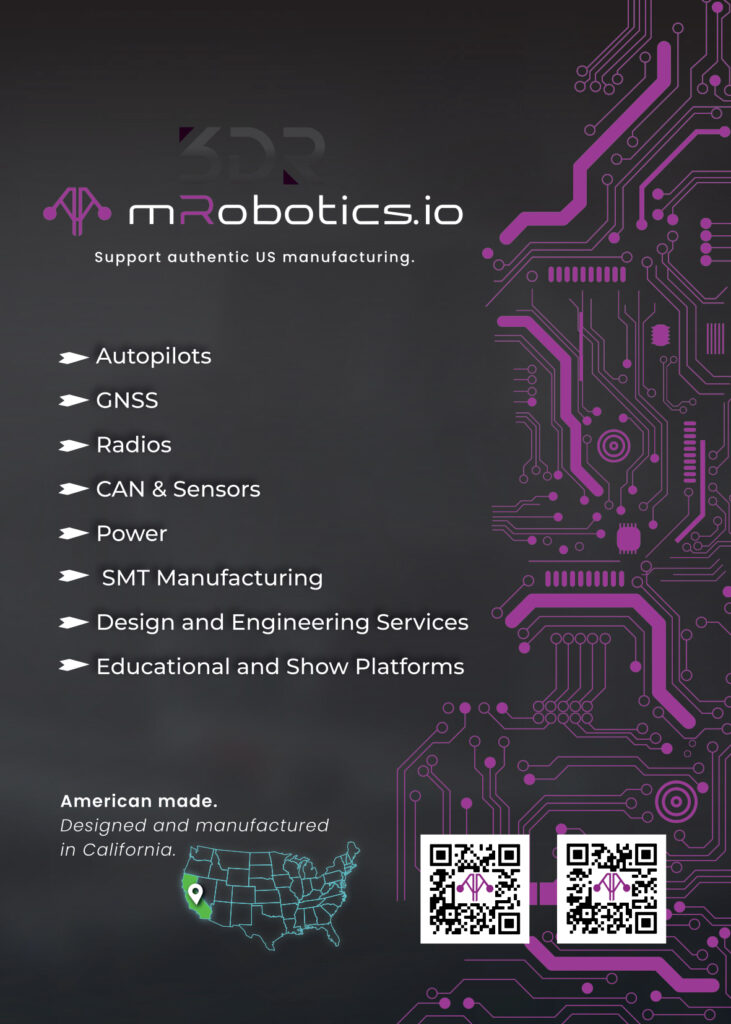
“It weighs 23 g and measures 33.3 x 45 mm, so as a low-SWaP system it’s meant for customers of the 1500 who want a similar footprint but with greater processing power and throughput, and probably those who just want one or two tailored pieces of our AI IP, such as tracking moving targets or some discrete object recognition.”
The company also showed its 4000-OEM, which supports three digital video inputs of up to 4k30, as well as around 100 different camera models, and comes with H.265 encoding. SightLine said the next generation of the 4000 is expected at the end of the year, and will result in additional, more powerful versions of what is at present the company’s most powerful solution.
The 1500 and 3000 processor boards meanwhile are still being supported for customers who use them, and will continue to be for the foreseeable future.
Lastly, SightLine announced that its full software suite can now be used on third-party ARM computing systems.
“Initially, our algorithms could only provide analysis functions on boards other than our own hardware products, like object detection, tracking, AI classification and provision of telemetry data,” Guerrero said. “But with our new 3.6.2 software release, we can now perform rendering functions, including encoding, enhancement, and KLV data on Nvidia Jetson hardware, for customers who want to continue using their current hardware.”
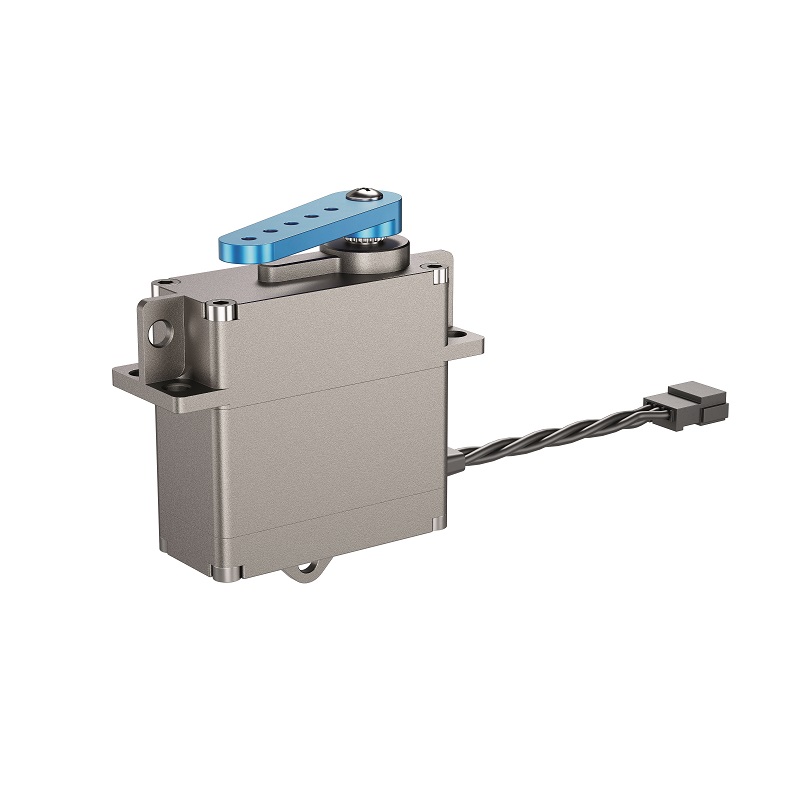
Volz has launched a new servo, the DA 14-N, aimed at filling the niche between its own high-end servos for professional vehicle OEMs and lower-end servos for hobby-grade aircraft or new entrants into the uncrewed industry.
“We’ve had a product called the DA 15-N for several years now, which is used on the AAI Aerosonde, Insitu ScanEagle, and Zipline’s Zip, be it through PWM, CAN, or RS-485 command interfaces,” said Mark Juhrig. “It has features such as a BLDC motor, brushless position sensor and an all-steel geartrain, with most customers flying it for a total of 2500 hours.
“We took those features and the associated components, and fitted them in a smaller case to make the DA 14-N. It’s a different concept to our other servos in that it’ll be a COTS product, with no customisability in terms of housings, and interfaces and so on. But it’ll have an MTBR of over 500 hours, a rating to IP64 for moisture ingress protection, and most important it’ll be a drop-in replacement for small hobby servos, but with a lifespan many times longer.”
Now in production, Volz anticipates the DA 14-N to be particularly attractive to lower-end uncrewed systems manufacturers and integrators who want a higher level of performance and cost-efficient long-term maintenance. It will therefore be available solely with a PWM-interface and 5-9 V operating voltage, as this is the most common type of interface for lower-end systems.
“It’ll be much closer to a hobby servo in price terms than any of our previous product lines –less than half the price of a DA 15-N – and because it’s COTS, customers will be able to receive it 2 weeks after ordering it,” Juhrig added.
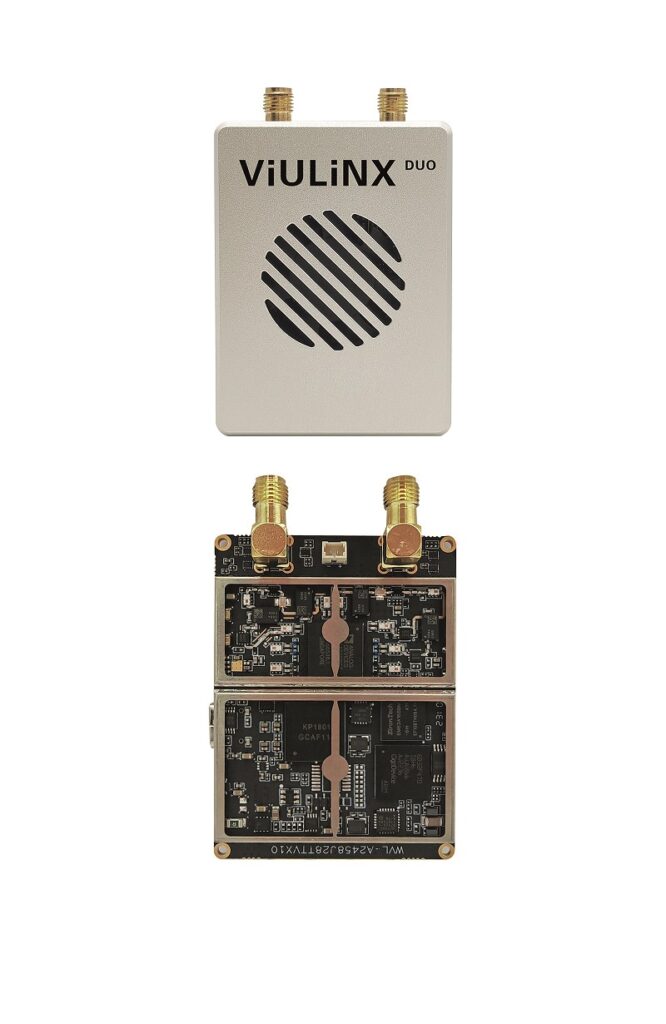
Taisync has released its Viulinx DUO, a new dual-band radio module for video, telemetry and RC data, which operates at 2.4 GHz and 5.8 GHz.
The system can be configured for bandwidths of 10 or 20 MHz, as well as a transmission power of 26 dBm at 2.4 GHz or 24 dBm at 5.8 GHz. It consumes 6 W in operation and communicates over a range of 10 km at 2.4 GHz or 5 km at 5.8 GHz; it can also provide transmission/reception diversity and dynamic frequency selection.
“We’re also releasing the ViuRC5, an Android-based GCS that has a 5.5 in touchscreen and a built-in dual-band radio link,” added Yan Li. “We’ve designed it as a low-cost solution to make it easier for UAV manufacturers to integrate.”
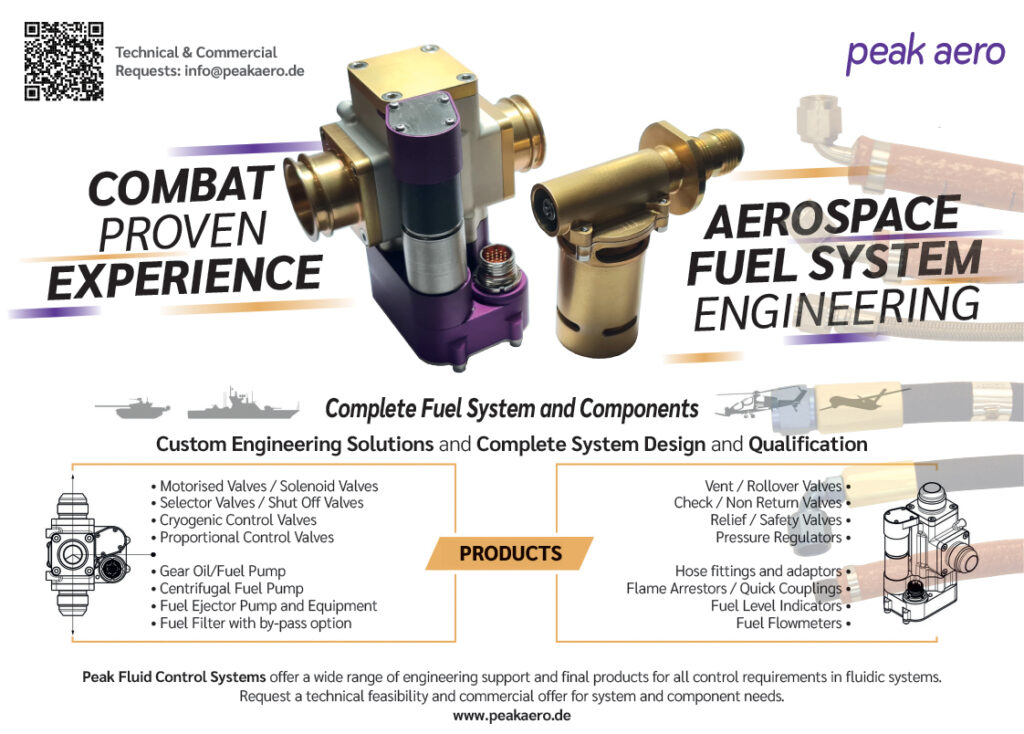
The handheld ViuRC5 weighs 793 g, is powered by 7800 mAh of batteries and runs for 6 hours between charges.
Microlink Devices spoke with us about a new form factor being used in the design of its thin-film solar cells.
“Our current solar cells are 20 cm2 rectangular cells, and when we cut those out of the circular semiconductor wafers we fabricate, we naturally end up with a lot of wasted material in the corners,” explained David Tyler. “That means we only get about 4.5 W per wafer, and the wafer is where most of the manufacturing cost is concentrated.
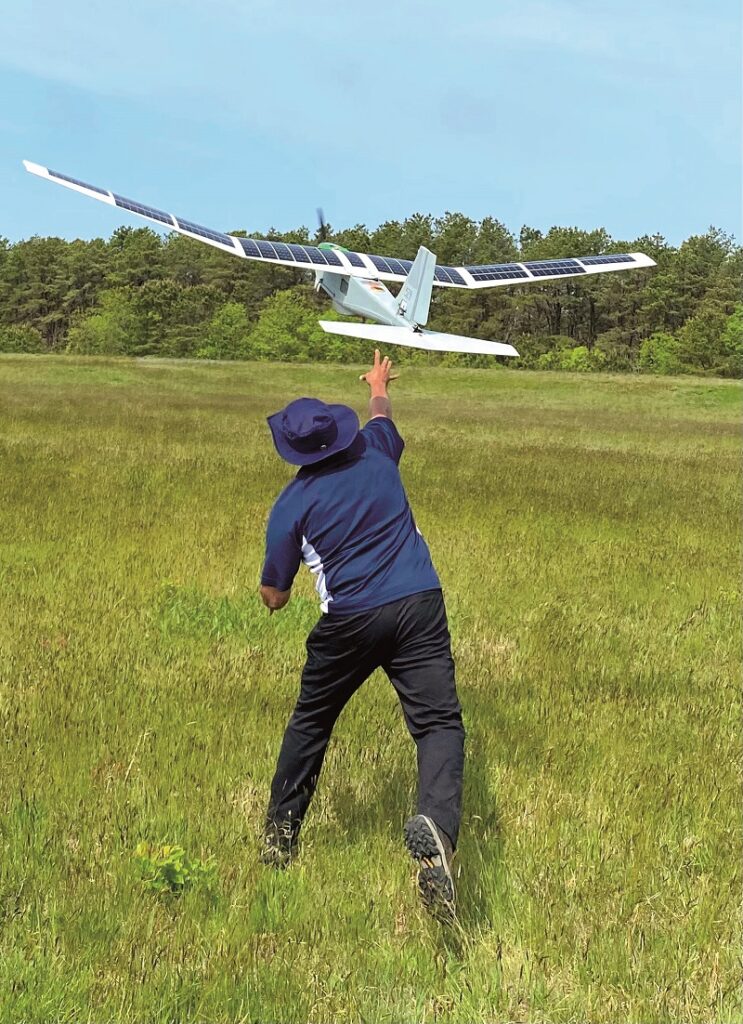
“But now we’re developing what we call a Quartex cell, which is shaped as a quarter of a circle, so when we cut those out, the area of wasted material is much less.”
The company expects this to increase the cost-effectiveness with which its solar panels are manufactured, particularly as the Quartex design uses the semiconductor material more efficiently, and requires fewer connectors and welds per unit area than the smaller rectangular cells.
“It’s generally a much neater cell than before, which also means you get far more power for the same area or mass of array,” Tyler added.
“And on top of improving our solar technology, our work with the AeroVironment Puma means we’re now getting interest from a couple of companies in retrofitting their own UAVs, particularly for defence and law enforcement operations in the US.”
Microlink is also becoming increasingly involved in the manufacture of heterojunction bipolar transistors, as a consequence of President Biden’s CHIPS Act. Further ahead, it is planning to build a new $100 million facility in Wisconsin for volume production of its solar cells in order to meet the demand for its technology.
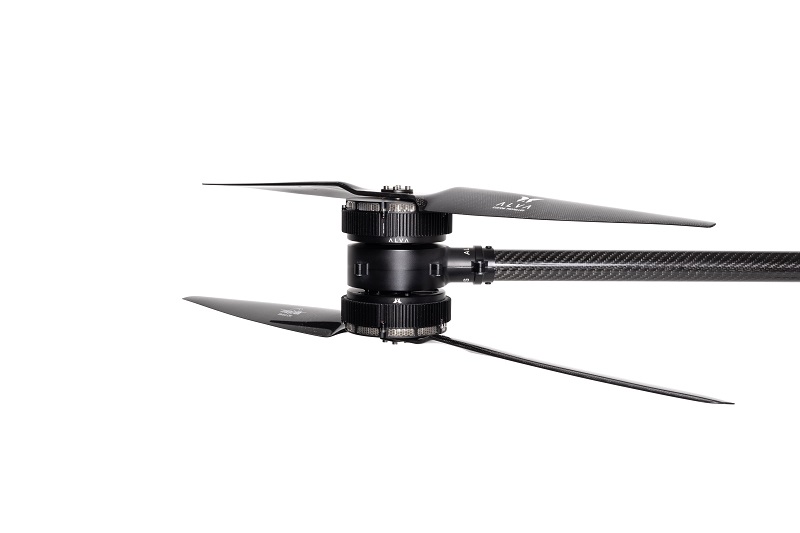
“Until now we’ve been principally a research company, but this year alone so far we’ve had a demand for over 30 kW of solar cells, and projections indicate we’ll be asked for 50-60 kW next year, and over 300 kW around 3 years down the line,” Tyler said.
With Remote ID now imperative for UAS operations across much of the world, uAvionix showcased its new pingRID (ping Remote ID), a retrofit broadcast unit designed for conformity with the relevant FAA regulations.
“In September this year, the FAA will start requiring drones to have Remote ID,” explained Brit Wanick. “It will come in two flavours: Standard Remote ID built directly into the core hardware of an UAV, or if it’s an older aircraft design it’ll need what’s called a Remote ID Broadcast module.
“The pingRID is our broadcast module that adheres to the FAA’s accepted Means of Compliance. Its operation is simple: turn it on and attach it to the UAV using the 3M lock-tape provided; it then acquires a GNSS reading, and it’s ready to fly. Once in flight, it broadcasts its platform’s take-off position and all subsequent GNSS positions of the aircraft during flight.”
That will allow law enforcement, ATC and UTM organisations to use scanning devices to track UAVs equipped with pingRID over Bluetooth. The unit weighs 21 g and has a battery that lasts for more than 2 hours, while also being USB-rechargeable between flights.
“There’s no app or device configuration required to install and use pingRID – users simply have to register a serial number with the FAA’s registration site, as they would for any remote ID device,” Wanick said.
The company also unveiled its truSky ADS-B validation system, which is designed to provide UAS operators and ATC confidence in the integrity and accuracy of ADS-B signals, and thereby verify whether the signal is truly coming from an aircraft with ADS-B or if it is being spoofed.
Alva Industries attended the 2023 expo to show its updated portfolio of production-ready electric motors, its engineers having moved beyond the design and concept phases and into scale production.
“First, we showed the propulsion system Altus X60 last year, but it’s progressed a lot since then,” said Anton Franzen. “We’ve carried out a lot of testing and flying, and therefore have several iterations of the design, and we now offer three configurations of it.
“The X60 Uno is a single-motor system for UAVs with one propeller, ESC and motor per arm, and it integrates an ESC inside its mounting hub for straightforward cooling.
The X60 Duo doubles up on that for a coaxial, two-rotor architecture, and the third iteration features a customisable, bulkier profile and interface on the drone arm, for things like mounting programmable LEDs that can serve as green or red warning lights.”
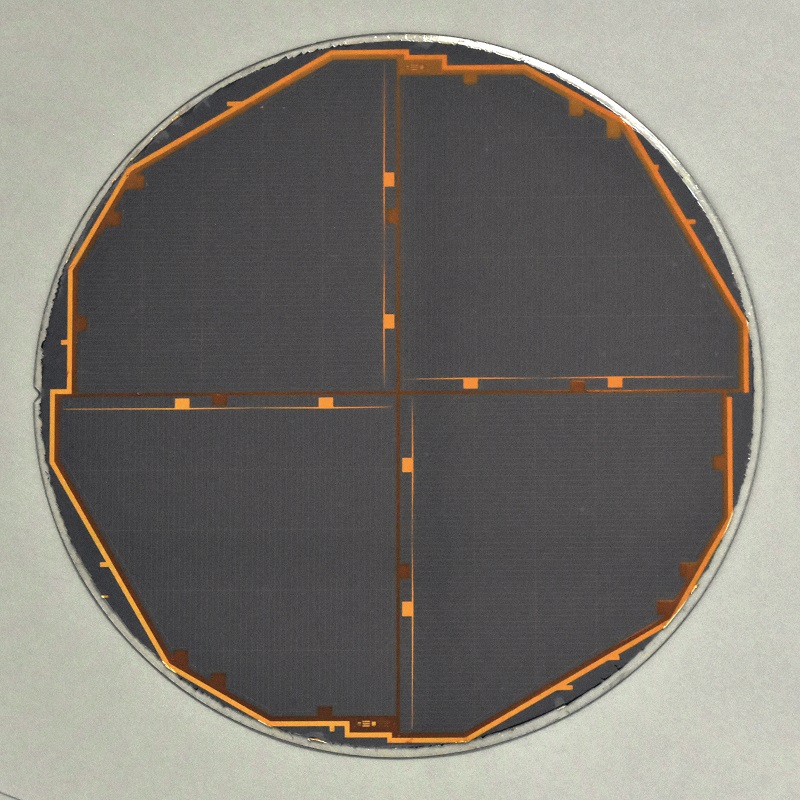
The X60 Uno weighs 685 g, outputs 8.2 kg of continuous thrust on a 44 V (12 S battery) input, and can support a20 kg MTOW quadrotor or a 30 kg MTOW hexacopter. The X60 Duo produces13.5 kg of continuous thrust and is designed for up to 30 kg MTOW X8 (four-armed) octocopters, with each Duo theoretically supporting 7.5 kg of MTOW.
Alva also showcased the X80 motor, which is designed for UAVs around 50% heavier than the X60’s users. It is still in r&d, with commercialisation to follow after further development and market research into ideal users, but it will produce up to 21.5 kg of thrust with a 32 in propeller, and ideally power a 30 kg MTOW quadcopter.
“And our FiberPrinting tech enables all these products to be the first slotless e-motors with high power density,” Franzen added. “We can design them as inrunners or outrunners, and they produce no torque cogging, with very good step response of the thrust output.”
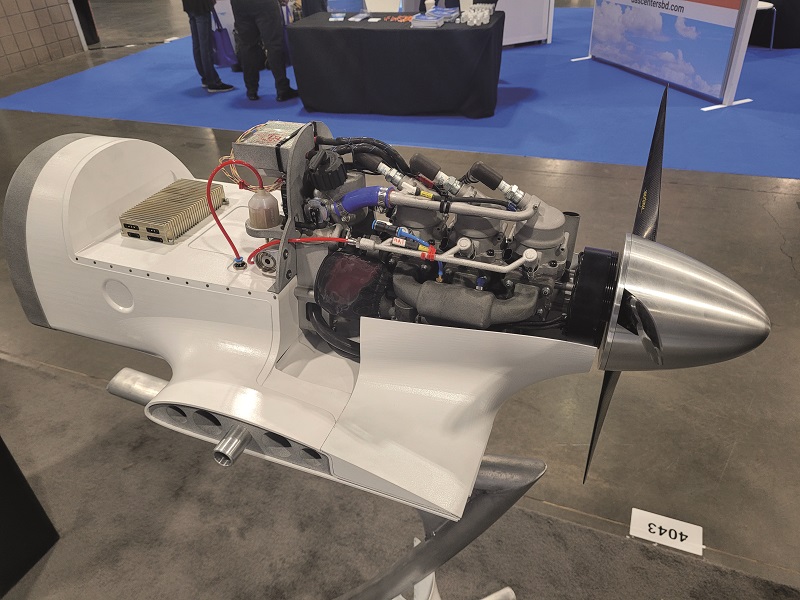
Custom battery manufacturer and charging system manufacturer Amicell came to the exhibition to showcase its mobile energy solutions for use in UAVs and robots.

Among the solutions Amicell presented were its Universal Battery Analyzers for small UAV battery packs, which in addition to recharging batteries will generate test reports on the conditions of packs.
“With these, UAV flight operators, maintenance technicians and manufacturers can test and closely track the health and performance levels of their batteries, for greater flight safety and maintenance cost-effectiveness,” said Amit Manor.
The company currently offers the UBA5, which handles packs with capacities from 10 Ah to 120 Ah and up to 2 A of load current per channel when analysing multiple fully charged batteries (or up to 3 A or 45 W from batteries being recharged), and the UBA5 which is compatible with batteries from 0.5 Ah to 120 Ah and up to 150 W per channel when analysing multiple fully-charged batteries (or up to 5A or 240 W from batteries being recharged).
Both systems are compatible with modern lithium-ion and lithium-polymer chemistries such as LFP, NiMH and Ni-Cd, and can handle battery voltages up to 70 V.
“We also have high energy density battery packs – 320 Wh/kg from our lithium-polymer pouch cells – which we can customise for dimensions and form factors, and fit into wings or even tails,” Manor added.
We last featured the Cobra Aero in issue 44 (June/July 2022) and its A99H two-stroke engine, which is designed as a spark-ignited, liquid-cooled I3 and optimised for running on heavy fuel. These days the engine is being integrated into a UAV being produced by L3Harris for the US military.
“The newest tech we’ve integrated into this platform is Power4Flight’s IntelliGen, which regulates the power from the A99H’s generator such that it can be stored in a HV battery, for instance in dedicated VTOL rotor packs, or delivered via a LV bus for payloads and avionics,” commented Sean Hilbert.
“IntelliGen can also preheat and start a heavy-fuel engine using HV lift battery packs; then, during warm-up, we can put that energy back into the battery. We’ve also installed some optimised air ducts underneath for tight integration of the cooling system. They’re much smaller, lower-drag ducts than you’d need for an air-cooled system, just to deliver air to our radiator.”
Cobra has also delivered the first unit of its A99S, a series-hybrid version of the A99H, to its alpha-tester customer. It is a 4.5 kW system (when running at 6500 rpm), with a future iteration planned that will run at 9000 rpm to produce 9 kW of shaft power, 8 kW of which the company estimates will be converted into an electric output.
“The subsequent development stage will focus on outputting power at higher voltages, going from 48-50 V right now to hundreds of volts within the next year,” Hilbert added.
The company also displayed a 7-14S battery pack called the Electron Canteen, produced by TWIG Power which Cobra spun out in 2019.
“That pack incorporates our aerospace BMS, which has ‘functional fail modes’ designed to deliver just enough energy to ensure an aircraft can limp home amid downstream failure modes that would cripple other aerospace powertrains,” Hilbert said.
“We also program it for tight temperature control around lift packs, balancing cells and keeping them ready for action. Many VTOL-transitioning UAVs let their lift packs get too cold when they’re not in VTOL mode, which could be dangerous when they need to descend from altitude and land. That’s why our BMS is optimised to maintain temperature and hence battery health.”
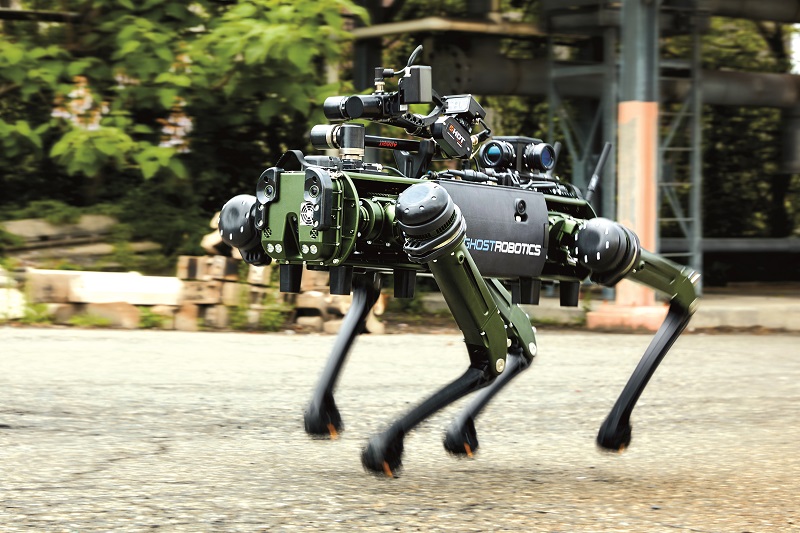
Ghost Robotics is continuing to develop its quadrupedal Vision 60 UGV (or Q-UGV), which is intended as a ruggedised system for operating in all weather conditions, and as an open platform for incorporating different sensors and other mission-critical payloads.
“We’re starting to scale up production, and not only carry out research but define how our manufacturing lines will be shaped in order to build more Q-UGVs,” explained Michael Subhan.”
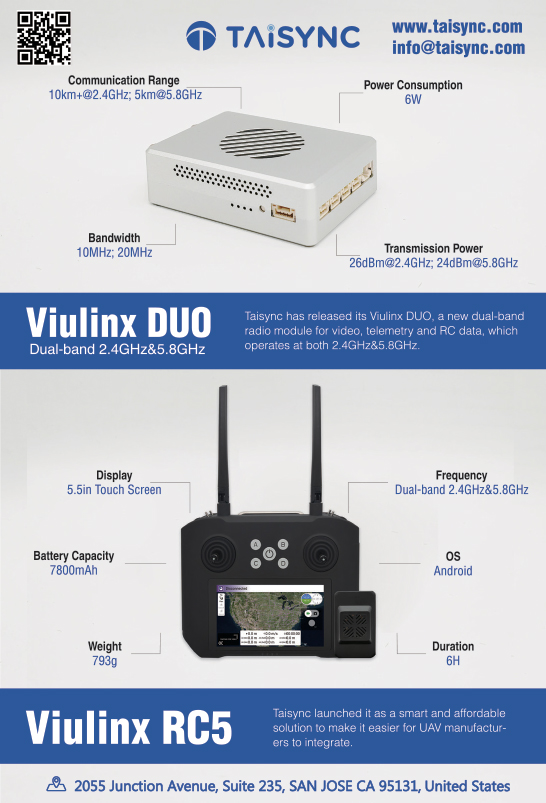
End-users currently include the US DoD as well as governments allied to the US. These comprise the bulk of Ghost Robotics’ customers, but the company is also branching out into enterprise and industrial applications with groups such as AT&T and Haskell Engineering.
The comms system in the Vision 60 is FirstNet (First Responder Network Authority) certified, so law enforcement can use it in the AT&T FirstNet network. It is also being operated as a walking cell tower in disaster relief and recovery missions: if the cellular service goes down during a natural disaster, the Q-UGV can be equipped with a comms relay to restore critical cellular activity.
Swoop Aero attended the expo to showcase its successes as both a UAV OEM and a logistics services provider.
“We operate as a business throughout Africa and the APAC regions,” explained Zac Kennedy. “In some cases, we operate our UAVs ourselves, in others we supply our UAV to other companies. Skyports in the UK for instance is a trusted partner and end-user of our Kite UAV.”
The Kite is an electric VTOL-transitioning fixed-wing aircraft with eight vertical lift rotors across twin booms. The rear end of each boom features an electric pusher-rotor and an inward-slanting tail fin with ruddervators.
It can fly for up to 175 km while carrying a 3 kg payload (primarily cargo, or survey payloads such as cameras or Lidars if required), at speeds of up to 200 kph. Swoop also estimates that up to 130 km can be achieved with the same payload in headwinds.
“It has a maximum payload capacity of 6 kg, and is modular to the extent that a user could do a medical supply delivery in one direction, then run an aerial video survey on the return flight,” Kennedy said.
“Our software stack allows us to fly 30 aircraft at once, for instance overseeing multiple individual delivery missions in the loop from a GCS, or overseeing a team or swarm of Kites working together to create an orthomosaic map of a large area.”
Also attending the show was mRobotics (also known as Mayan Robotics), which discussed its new Control Zero OEM board for highly SWaP-optimised flight control.
“It’s a 3.25 g flight controller, with triple-redundant IMUs and compatibility with Ardupilot, PX4 and most open-source solutions,” said Leonardo Garcia. “We have other carrier boards for it, or end-users can design their own, as we provide all the necessary documentation for OEMs to integrate the board into their systems.
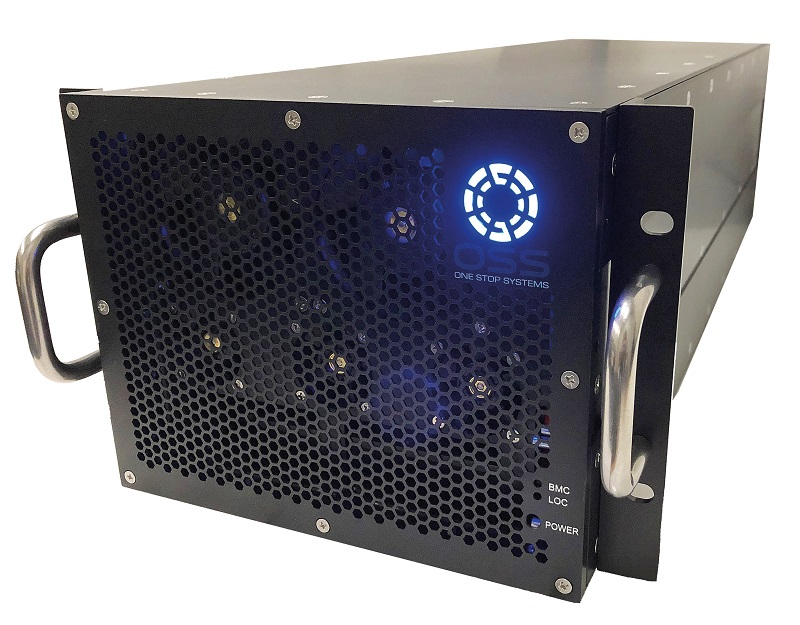
“We also have different package sizes to allow for different resonant frequencies, so for very complex airframes like tiltrotor VTOL-transitioning UAVs that have many actuators and hence complicated vibration profiles, you can filter those out with whatever configuration you want.
“One IMU is software-damped, while the others rely on mechanical damping, allowing you to get the best of both worlds in terms of arbitration between the three IMUs.”
A similar design philosophy has been applied to the company’s other products, including its recently unveiled Control One, which is targeted at uncrewed aircraft needing higher resilience. It incorporates a new sensor selection while keeping the same philosophy as the Zero, but each IMU has its own power domain, as does the MCU. In addition to keeping these systems isolated, it integrates 16 Mbytes of external flash memory, Garcia noting that flight controllers of its size and weight typically incorporate only 2 Mbytes.
The system will be officially released soon, at which time its other physical and performance specifications will be published.
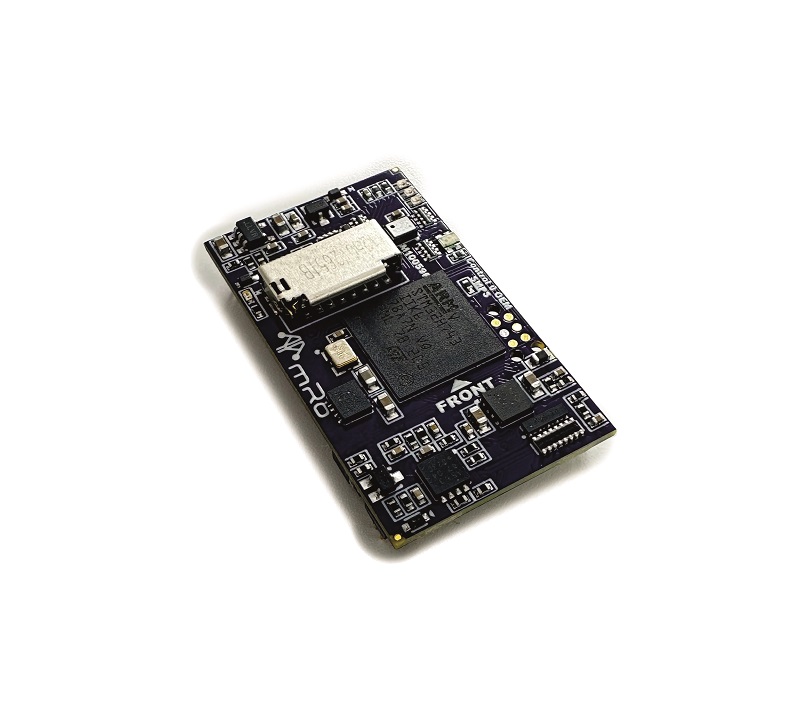
One Stop Systems (OSS) exhibited the latest in its range of ruggedised, high-performance edge computing systems, primarily for GPU computing or flash storage in harsh environments such as autonomous freight trucks or heavy industrial UAVs.
“Edge computers these days need to contain the same grades of hardware you’d find in a data centre, but also have very different power inputs, cooling systems, shock and vibration profiles and more,” explained Jaan Mannik.
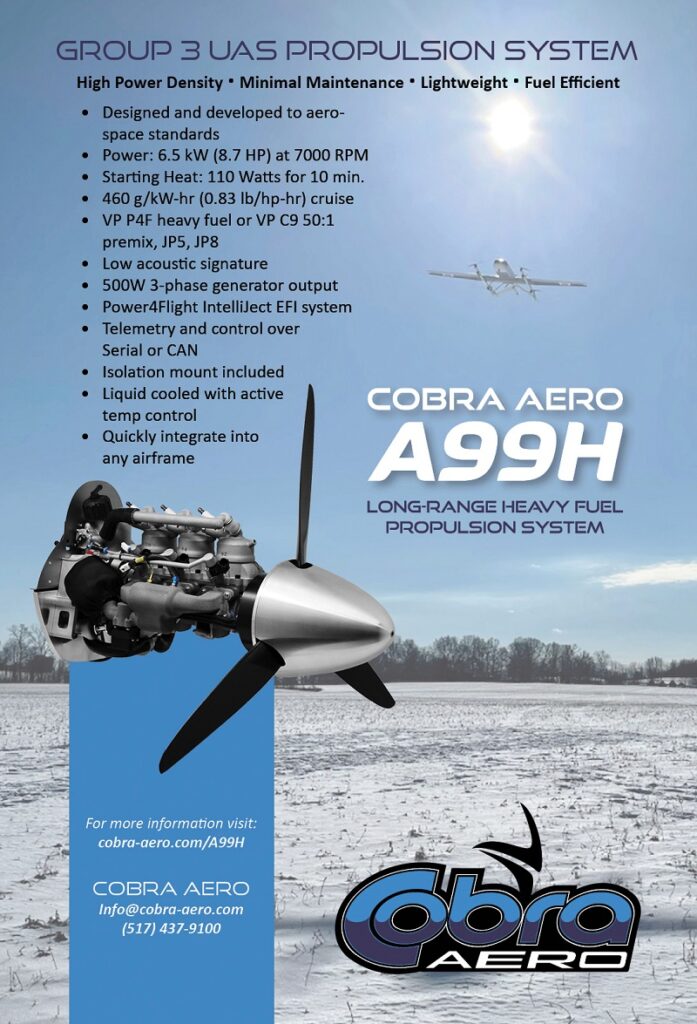
“From a GPU standpoint, our 4U Pro is a PCIe Gen 5 expansion accelerator that can support eight Nvidia A100 Tensor Core GPUs, or the new, more powerful H100 GPUs that can be connected seamlessly over PCI Express to an existing server. Any server that has a PCI Express slot can therefore now have up to eight GPUs connected, turning that one server into its own supercomputer, and up to four servers can be connected, with the system designed to accept 400 W cards.”
OSS also makes the EB4400, a half-rack version of the 4U Pro, for edge systems with very limited integration space. It is flange-mounted and has swappable power modules for supporting a variety of power inputs, from 48 V DC to 270 V AC. It is currently available in PCIe Gen 4, and will be available in PCIe Gen 5 later this year.
Lastly, the company exhibited its Rigel Edge Supercomputer, which it said is the highest performance-to-weight computer commercially available. The system features a GPU with a form factor called SXM, which is similar to the form factor of Nvidia’s PCIe GPUs such as the A100 but uses a P2P bus called Nvidia NVLink, which is 3-5x faster than PCIe.
“SXM is typically meant for data centres, and Nvidia and other companies sell SXM solutions as part of the DGX platform,” Mannik said. “We took the guts of DGX, shrunk it in half, and ruggedised it for an edge environment to Mil-Std 810G.
“That makes the Rigel half the size of systems of comparable power in data centres, and applicable to autonomous systems that need a huge amount of computing power.”
Rigel is Nvidia-certified, weighs 22.68 kg and integrates four A100 SXM GPUs for up to 24 Tbyte/s of total bandwidth, 320 Gbytes of GPU memory, an AMD EPYC 7003 CPU, and up to eight ECC DDR4 RDIMM/LRDIMM cards (with up to 128 Gbytes each).
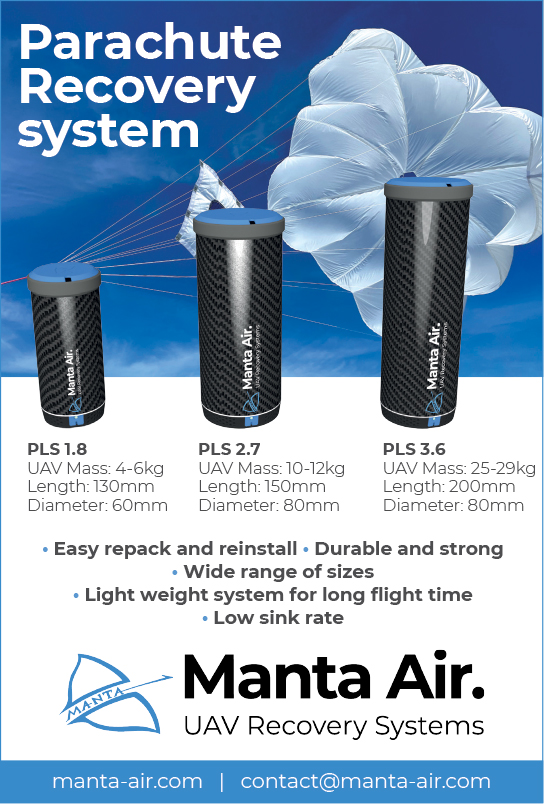
Although C-Astral is best known as a UAV manufacturer and systems integrator, for the past 5 years it has been covertly developing a digital data link, and disclosed details of it at the show to us.
“Historically we’ve been radio-agnostic – we integrate Silvus, Trellisware, Microhard, Commtact, you name it. But we’ve also specialised in RF-related activities like antenna design, analogue link design, shielding and link optimisation, and through that saw a need for a robust, tailor made and cost-effective digital data link,” explained Marko Peljhan.
“The first 30 units are shipping to experimental clients – mainly research organisations who we expect will give good, detailed feedback, one of which is also the Netherlands MoD.”
The products are to be marketed under the ASTRAL-DYNAMIK trademark and under the Dyn Series of radios, with DYN-23L and -S to be the first variants in that product line, both of these weighing 85 g and consuming up to 8 W.
They transmit securely over the L and S bands respectively, and although it is not designed to frequency-hop, they use a proprietary and highly customisable protocol that can be adapted for complex purposes. One user has tailored it for connecting mobile LTE base stations, and the system can be used for point-to-multipoint and mesh networking with packet prioritisation (an uncommon feature among other radio manufacturers).
“Packet prioritisation means that in very challenging RF environments – even jammed or other conflicted electromagnetic spaces – it reconfigures itself to get prioritised packets through first, such as the C2-specific packets or mission-critical intelligence data,” Peljhan said.

The company has also developed a modular ground control station architecture, which can contain an array of different links including C-Astral’s own new proprietary system just discussed.
“Also, our SQA eVTOL UAV is now in full production, with 50 units already manufactured, production capacity filled, and we’re now implementing new sensor packages to really flesh out its multi-role capability,” Peljhan added.
“It’s generated some good interest from first responders, law enforcement, the military and our more usual commercial clients seeking a more robust, capable and professional solution than their previous DJI-type systems.”
Honeywell exhibited a new GCS it calls its Ground Control System, which is aimed at providing a middle ground between large containerised GCSs and small handheld tablet devices.
“As more professional delivery and inspection vehicles become type-certified, there will be mounting expectations that GCSs will conform to a similar level of standards to ensure robust command, control, monitoring or supervision of multiple vehicles at a time,” said Sapan Shah.
“We’ve therefore designed this GCS to be certifiable, and although it will initially be configured for one vehicle per supervisor, it will be scalable to support many vehicles per supervisor over time.”
The GCS is a three-monitor desktop solution. At Xponential, one screen featured the state of vehicle subsystems such as the SoC of a UAV’s battery and the operating state of motors, comms, GNSS and so on. Another screen featured a top-down map with GNSS waypoints for the mission at hand, and the last screen featured a wider-area strategic map for managing multiple fleets and tracking other air traffic.
Honeywell also introduced its Versawave satcom solution with 5G capabilities. Given the expense of satcom, it anticipates being able to lower customer costs substantially by offering a 5G data link for when UAVs are flying at low altitudes.
“Versawave will manage the link automatically, so that when the quality of the 5G or 4G link degrades due to position, it’ll switch over to satcom seamlessly, with the IP address carrying over regardless,” Shah said. “The new product will start shipping in the summer this year.”
Honeywell also showcased its Resilient Navigation Solutions for GNSS-denied environments. This consists of a three-layer approach, made up of Infinidome’s GPSDome null-steering beam for mitigating GNSS jamming sources, onboard INS navigation solutions, and a radar for velocity-based drift correction.
Manta Air exhibited its latest UAV recovery and safety solutions, with a specific focus on developing and manufacturing parachutes and airbags for multi-rotors, VTOLs and fixed-wing systems without landing gear.
The company specialises in intricate development processes, using advanced methods and proven techniques through extensive field experiments and analyses, and also has in-house equipment for conducting experiments on newly developed parachutes and airbags.
“Our parachutes and airbags are reusable as long as they remain undamaged; we have UAV clients who have used our solutions multiple times for different missions,” said Olga Grab.
For fixed-wing UAVs, the company’s parachutes typically do not integrate launching systems. The airflow generated when the parachute housing doors open at high speeds swiftly and effortlessly inflates the parachute.
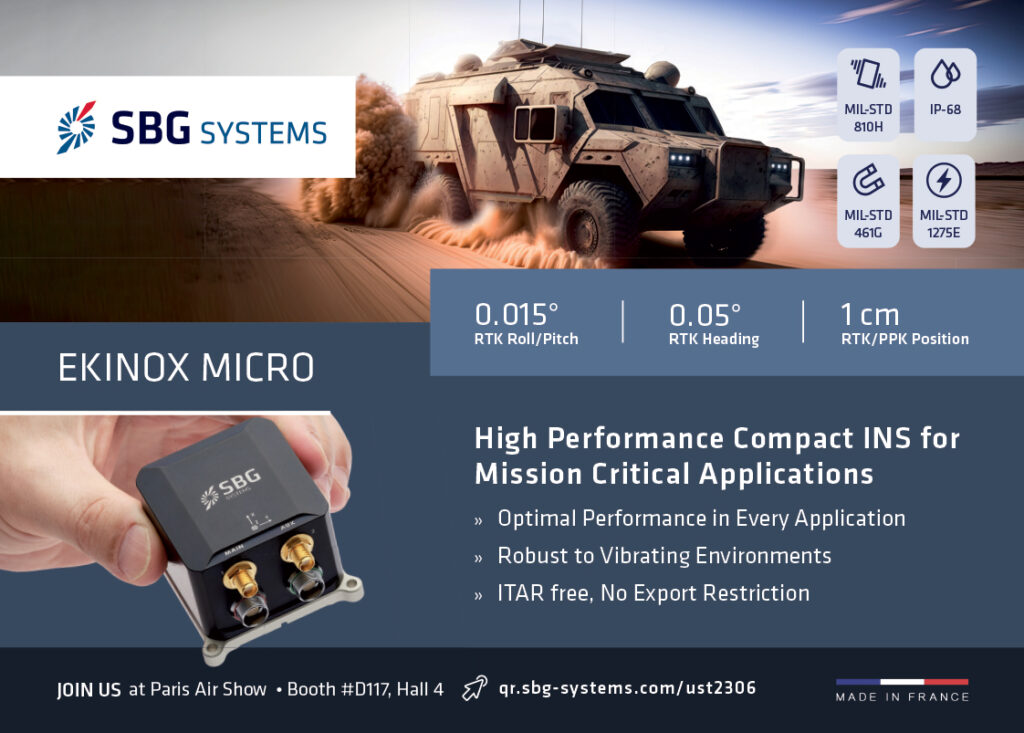
“However, for multi-rotors and VTOL-transitioning craft, we install active launching systems to rapidly deploy the parachute and decelerate the vehicle’s descent,” explained Grab. “Safety regulations increasingly demand back-up safety systems for VTOL drones in case of rotor failure, especially when flying over people. That’s where our solutions play a crucial role.”
Manta Air also offers advanced flotation devices for operations in marine environments. They are installed on aircraft flying over water. In the event of an emergency where the aircraft falls into the water, the flotation device is automatically activated upon contact. It inflates and enables the aircraft to float on the surface, preventing it from sinking.
Ultra Motion launched two new actuator products at the show, one of which was its first ever rotary actuator (the company having until now produced only linear actuators).
“The T3 Series is a rotary brushless DC servo, which incorporates features such as our integrated BLDC control electronics with CAN comms, contactless absolute feedback, D38999 connectors, and our shock and vibration-hardened design for withstanding harsh environments,” said Rob Koch.
The T3 Series actuator communicates over CAN 2.0B, RS-485, and RC PWM, and provides torque of up to 19.2 Nm with speeds up to 400 o/s.
The company also showcased its soon-to-be-released L2 Series of BLDC linear actuators, which are far smaller than the A-Series Servo Cylinder. It has the same comms interfaces and absolute position sensing as the Servo Cylinder and T3, and produces up to 362.87 kg of peak force with speeds up to 15.24 cm/s.
“The L2 is a single-motor design currently, but we’re planning to release a redundant version with two motors, two controllers and so on for higher reliability by the end of this year,” Koch added.
“We’re also showing our R Series linear actuators, which are our highest power density solution for applications like thrust vector control, and can deliver up to 567 kg of force,” he said.
UPCOMING EVENTS
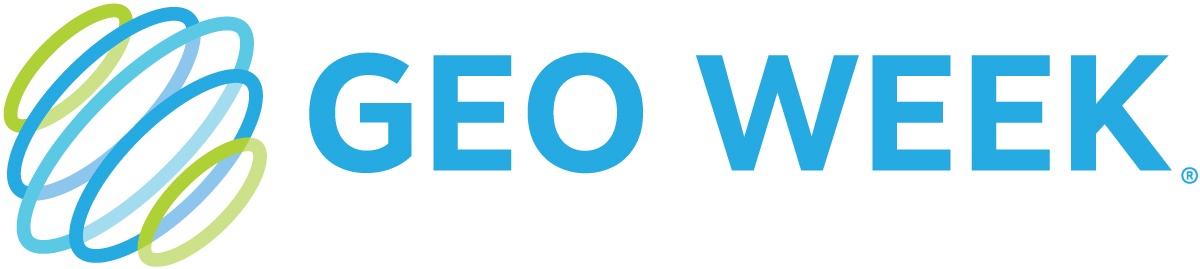
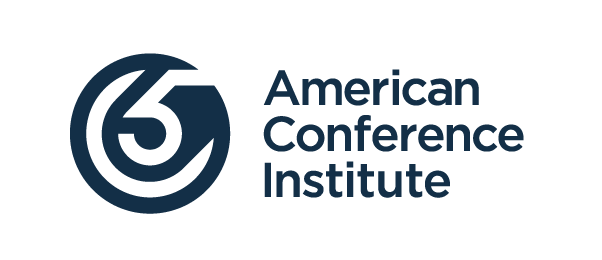
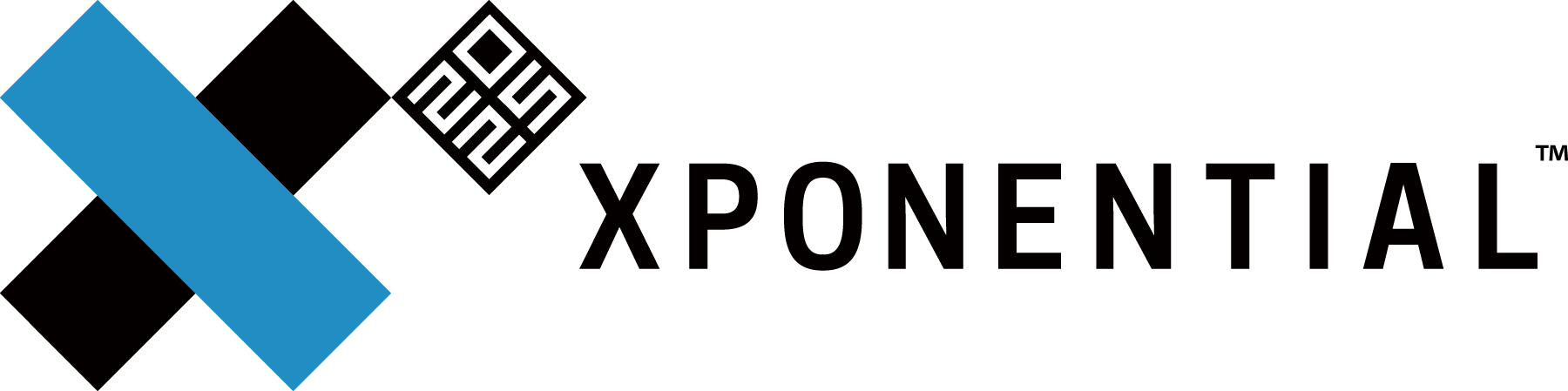
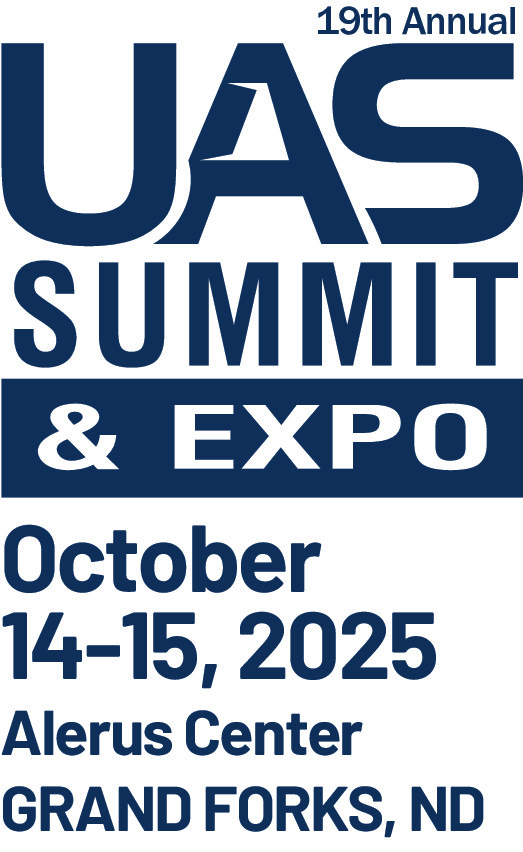
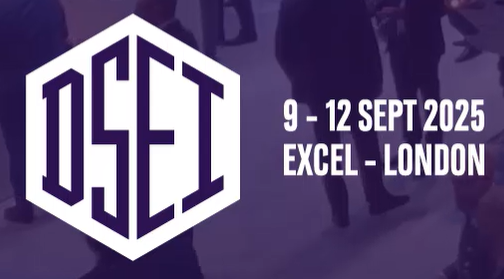
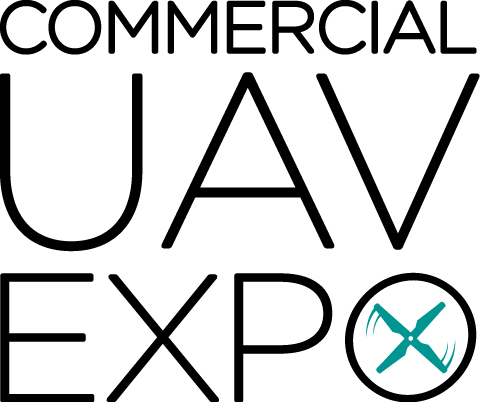
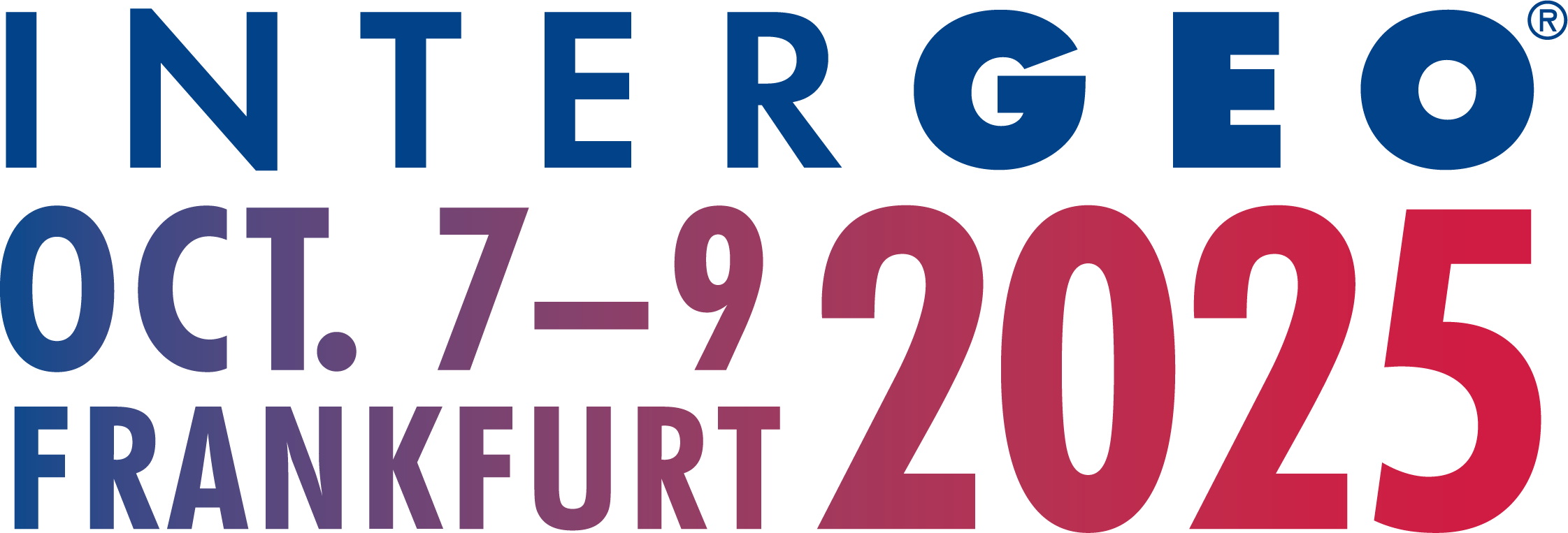
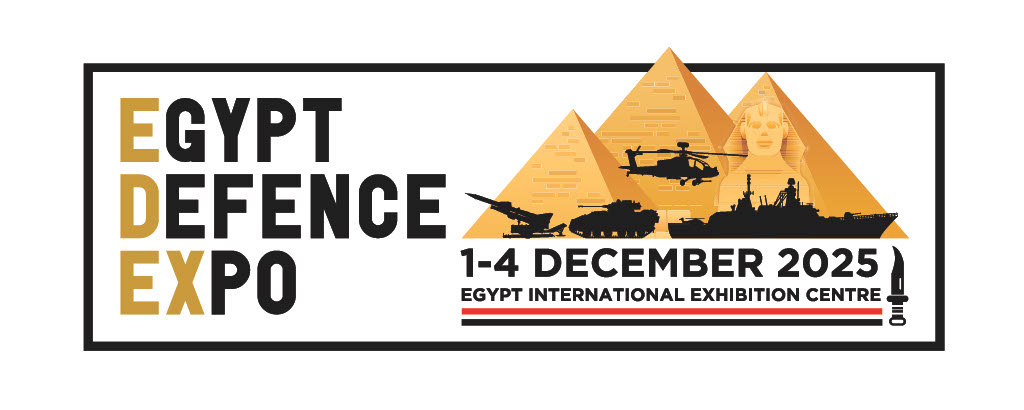
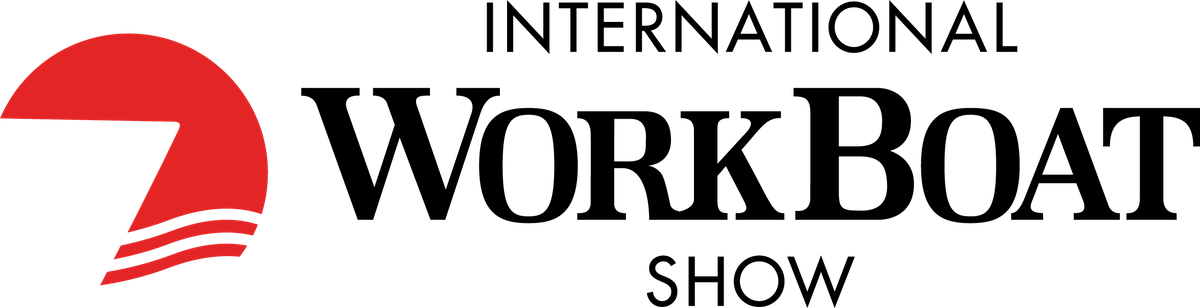
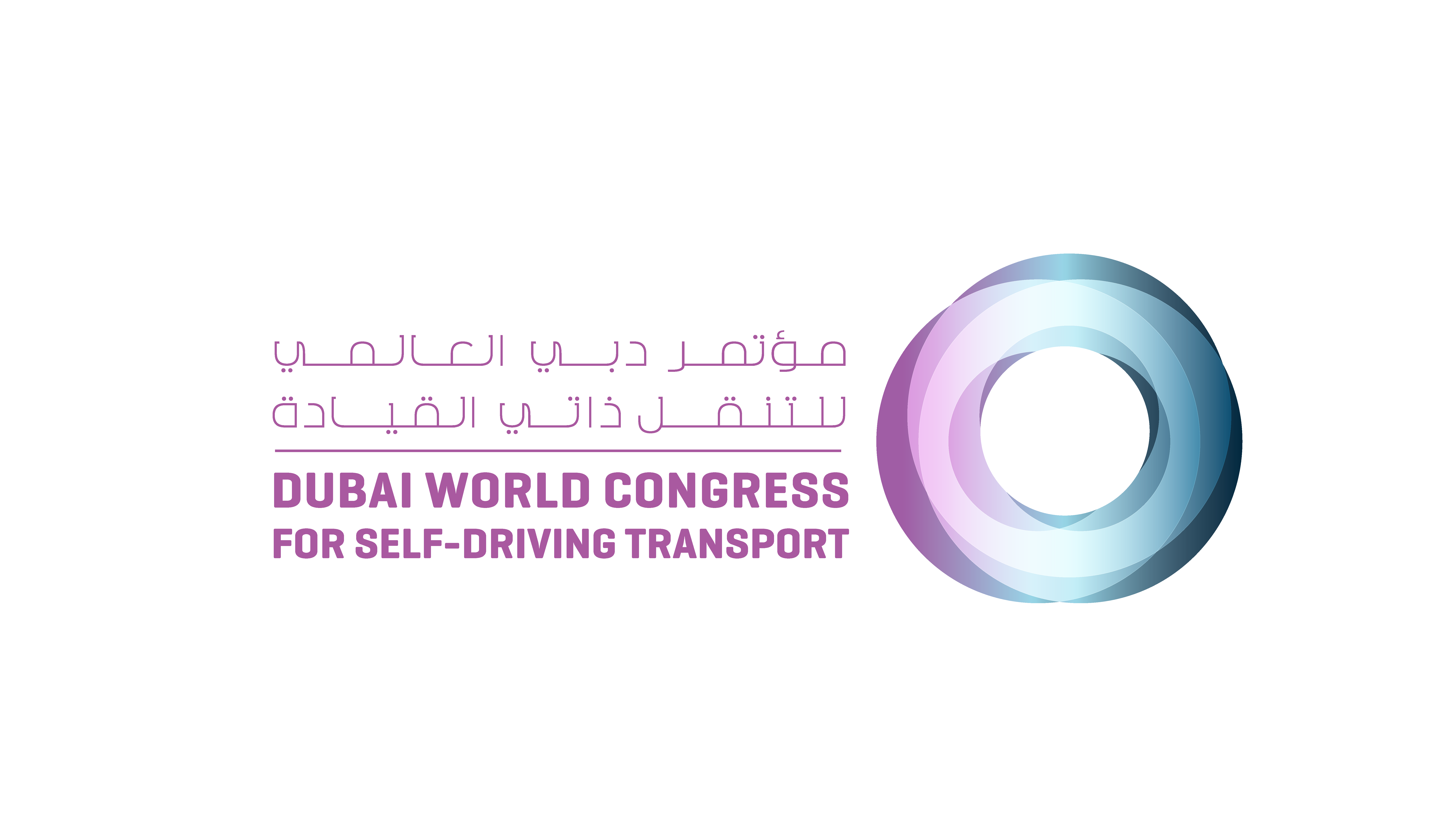
