Ground control stations
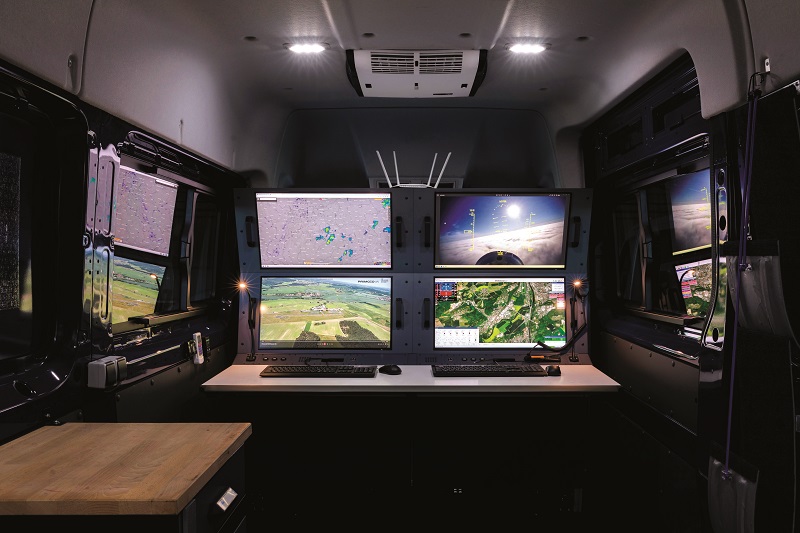
(Image courtesy of Primoco UAV and UAV Navigation-Grupo Oesia)
As GCSs go from small, bespoke batches to standardised units and sizeable production runs, Rory Jackson investigates the newest innovations and regulations influencing their design and engineering
A GCS must be an intuitive, tactile and multidimensional device, with varying arrangements of processors, control interfaces, screens, radios, protections and more. Such is the challenge of optimising these highly bespoke computer arrangements that it is not uncommon for a new GCS to arrive at its recipient, engineered precisely to their feedback on design, only for them to plug a common gaming controller into it as their preferred form of interaction.
With demand for quality, quantity, interoperability and capability growing in fleet and swarm management, it is worth considering all the different facets of GCS design plus the wider GCS industry to understand the evolution and standardisation occurring.
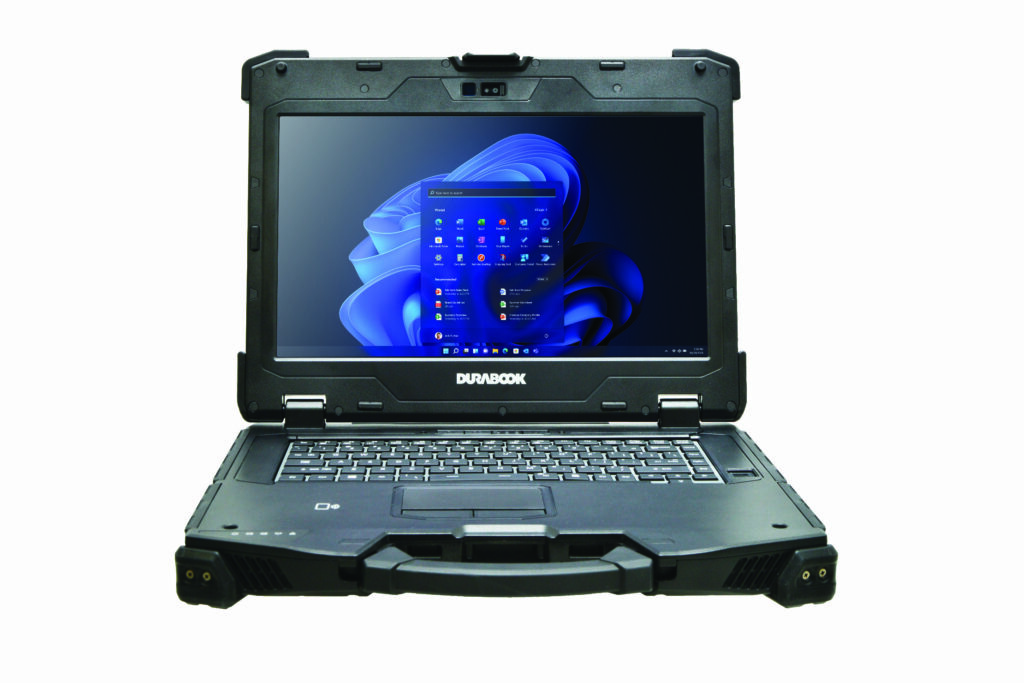
Software considerations
The system architecture of a GCS consists of a variety of components and arrangements, both in hardware and software terms. While one may traditionally think of such software being little more than a conventional map overlay with some surrounding digital buttons and menus, GCSs are increasingly software-defined solutions with much of their value coming from a plethora of useful advancements.
At the very least, it has become commonplace for GCS software to integrate a broader and deeper range of data flows from the aircraft, from real-time, high-resolution payload data streams for eager customers to the minutiae of subsystem performance and health data telemetry for vehicle maintenance teams to track.
It follows that specific tools for manual or automated analytics of such data are more often being integrated directly into GCS software packages, streamlining the production of actionable information reports (more so than the sometimes time-consuming process of porting data from the GCS to COTS analysis software).
Today, numerous features have become hallmarks of GCS software. For instance, software-in-the-loop simulators enable the execution of simulated missions while connected to GCS hardware, allowing their various facets to be tested, and enabling the flight team to gain familiarity and proficiency with the interface (or validate the parameters of an upcoming mission).
Additionally, software designed for multi-unit control is adapting to requests for greater numbers of vehicles to be managed per GCS, and for higher complexity of collaborative tasks that they may be triggered or preprogrammed to undertake. It is no longer unusual for discerning customers to ask for as many as 25 uncrewed vehicles to be rapidly set to a distributed patrol or search pattern within a predefined geofence, with the units intuitively taking each others’ place as battery or fuel stores run dry.
Additionally, mounting numbers of requests for multi-domain operations – with land, air, surface and underwater vehicles all managed at once – has required investigation and support of new protocols, sensors and payloads within high-end GCS software, as well as new forms of collaborative capabilities.
While achieving collaboration between different manufacturers’ vehicles – let alone those designed for varying domains – is challenging, companies presently engaged in engineering and demonstrating this are pursuing maturation and scaling of such capabilities in the years ahead.
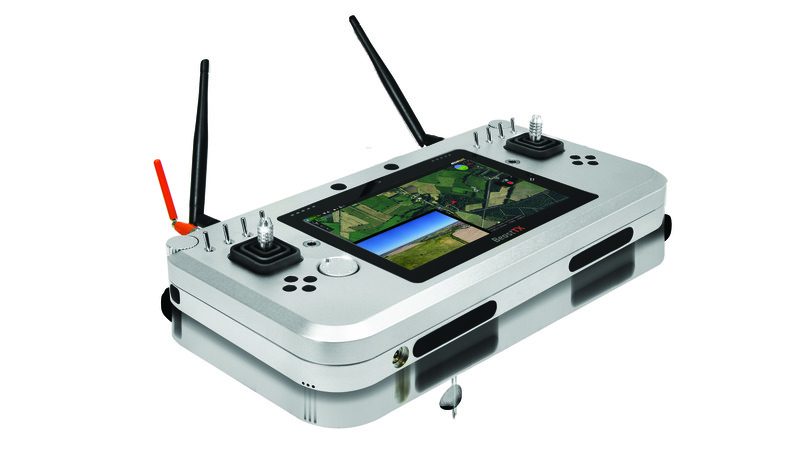
(Image courtesy of TM IT-Systemhaus)
Station to station
In many instances, UAS manufacturers and operators will suffice with some form of basic, ruggedised laptop or tablet (typically from Panasonic or Samsung) as their GCS station hardware. This can be enough in some instances, particularly for the sake of the familiarity that some users will feel with laptops over actual GCSs.
However, it has become more usual for professional, uncrewed vehicle operations to rely on more tactile, analogue control interfaces. These include joysticks, yokes, levers, toggle switches, large protruding buttons and other interfaces requiring deliberate, decisive movement to actuate, be it for the uncrewed vehicle or one or more of its payloads.
That may sound like an excessive effort compared with a laptop or tablet, but the need for extremely precise mission planning or even timely operator intervention in many uncrewed vehicle applications today (such as search-and-rescue, emergency services or defence missions) makes consumer electronics-type devices increasingly unsuitable for high-end users. Flat laptop keyboards can be fat-fingered, touchpads induce too many mistakes, and touchscreens are out in how many errors they can produce from even the most tenacious operator (especially in moving vehicles).
As a result, there exists four broad categories of what one might call ‘true’, dedicated GCSs in the hardware product sense.
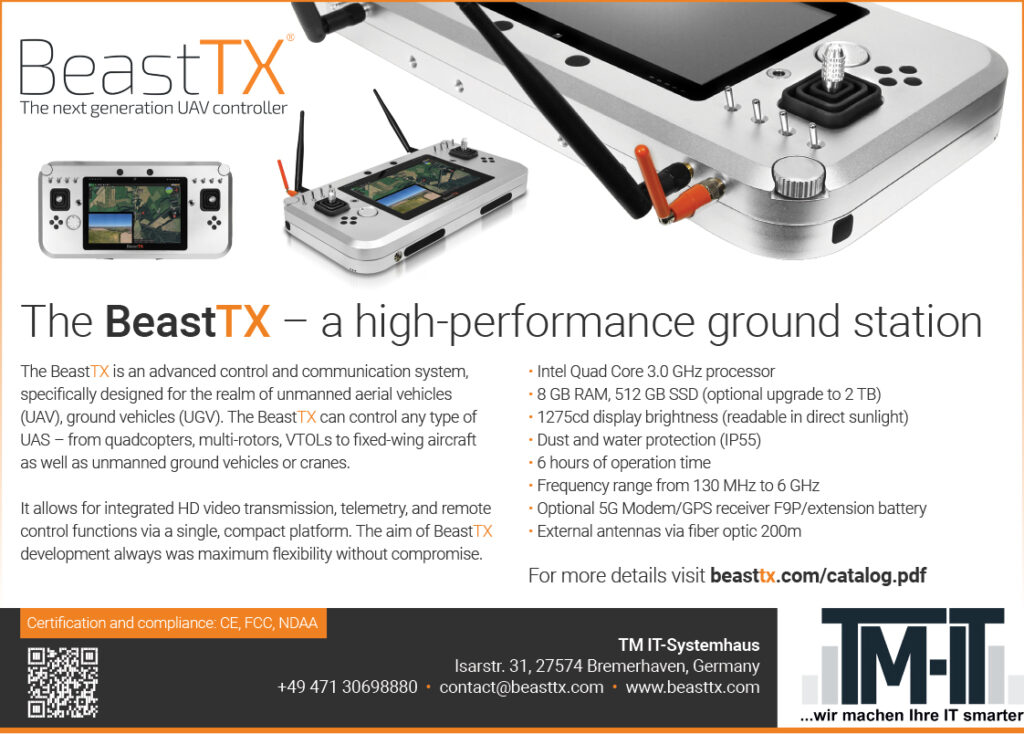
The lightest-duty are handheld tablet-type systems, designed with analogue interfaces constantly within reach of the holder’s thumbs, as well as highly SWaP-optimised batteries and radios to maximise system mobility while minimising weight (and operator fatigue).
The most heavy-duty are large, containerised or semi-containerised (with equipment arranged in crates, pallets or customised vans), remote command centres. These are typically tightly-integrated solutions, designed with more than two computers and a higher number of monitors for diverse information analysis. Naturally, they are also the least widespread, given the cost of mass-producing and delivering them, as well as their lack of mobility compared with other types, but they remain invaluable for serious users across defence, maritime and energy industries in particular.
Between these two extremes are case-type GCSs – highly turnkey solutions, often built into Pelican-style cases and integrating computers more powerful than tablets, as well as a plethora of controls, connectors, displays and features – and GCSs composed modularly of the user’s own choice of computer, monitor, controls, and so on.
The last of these four may sound an odd category to include among the more tangible other three, but some manufacturers are deliberately producing hub-type units that efficiently route and organise information traffic between PCs, analogue control peripherals and multiple critical industrial peripherals, such as radios, antennas and GNSS base stations.
The creation of such devices is motivated by the growing need for multiple GCS units to connect in a coordinated and simultaneous manner with multiple vehicles (aerial, maritime and terrestrial), and for such GCSs to integrate with crewed vehicles for Manned-Unmanned Teaming missions that require operating both uncrewed and crewed vehicles in formations or swarms.
As a result, a well-made GCS hub unit will include multiple physical and I/O ports, covering serial, Ethernet, CAN, GPIO and ADC systems, as well as ruggedisations to IP66, IP67 or similar ratings, as needed for the range of environments rich in dust, saltwater and precipitation.
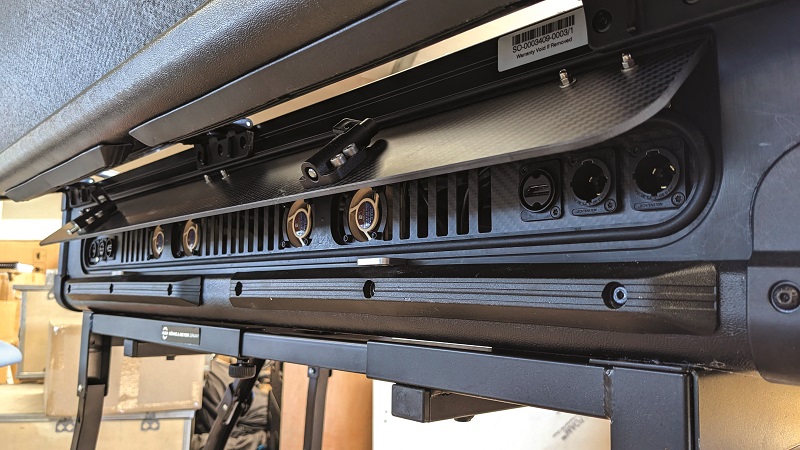
(Image courtesy of Worthington Sharpe)
Quality of life
Among the other GCS types, a variety of technical improvements have been achieved over the last year towards a number of key operating objectives revealed through the accumulated real-world mission hours of professional uncrewed vehicles.
With case-type GCSs, it has been found that COTS industry-standard cases do not make for the most hospitable environments for industrial computers to function in over the long term, particularly from a thermal-management perspective. They sometimes lack protection from specific environmental factors, such as dust ingress or water spray.
This is driving some GCS suppliers to design their own carry cases. While the extent of manufacturing facilities available in-house for such companies can vary, their custom cases can be design-validated and made by third parties. This can help to ensure the GCS-specific cases still have IP53 or IP54 protection ratings, as with standard cases, but with new features such as integrated vents for circulating cooling air through the cases while still keeping water from coming in contact with the electronics.
Additional quality-of-life improvements being realised through custom GCS case designs include running cabling through the case hinges to prevent exposure of cables to water and assembly panels that have been specifically chosen for improved strength-to-weight over the industry cases.
For handheld GCSs, ease of use and convenience are even more strongly emphasised, so the push for radio interoperability and hot-swappability is driving small manufacturers to continue updating their systems for mechanical compatibility and seamless interfacing with a wider range of radios.
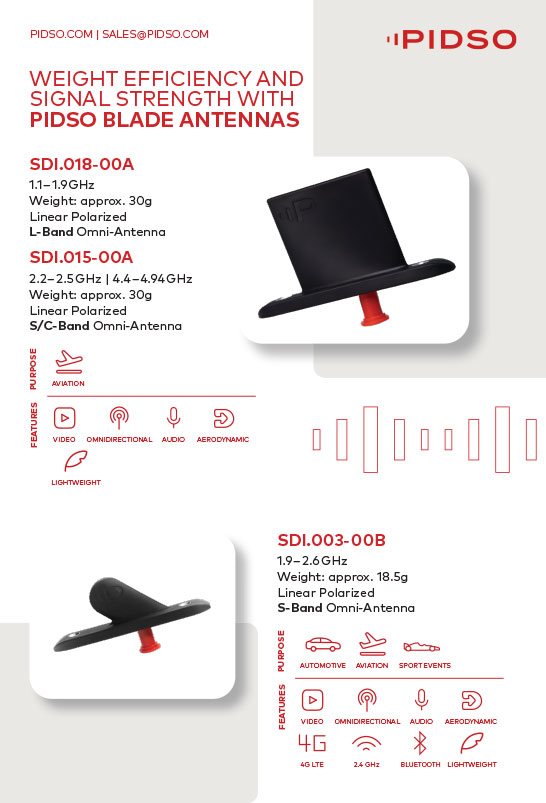
The advent of swappable radios has been acknowledged as the main hurdle towards the creation of true universal uncrewed system controllers. Designing and engineering an interface that multiple radios can use was not hugely difficult from a technical point of view; inspiration for the interface most commonly used today even took some minor inspiration from the Nintendo Game Boy.
Rather, jumping this said hurdle required intensive collaboration between radio manufacturers and GCS engineers to agree on connection and integration standards that everyone was willing to adopt and conform to, by which seamless radio interoperability and swappability could be achieved.
The end result was not something alien, but an idea that bridges the gap between the various existing radio connection standards, including compatibility with Nett Warrior. Engineering the system consisted broadly of designing the electrical interfaces (a close understanding of the contents of Nett Warrior connectors was vital) and optimising a mechanical form factor that would fit 99% of all radios.
Naturally, the latter was no mean feat, but this was eventually influenced by the near-universal use of MBITR-standard batteries among radios. Given that 99% of radios are designed to use that type of twist-on battery, it formed a critical guideline for a GCS design aiming to function as a handheld universal controller. Otherwise, the standard has been formed to specify as little as possible to avoid stifling creativity and customisability as some overly lengthy standard documents tend to.
Additionally, handheld GCSs must withstand environmental hazards, as well as case- and container-type GCSs, so advances in sealing are visible in such products. While this includes more robust gasket designs and selections, GCS engineers are learning that the best way to seal something is to not cut a hole into it to begin with (a simple measure, but not something always taught in universities), so designs are maturing accordingly.
Across the board, GCS manufacturers keep a close eye on the most powerful and cost-effective CPUs and GPUs available to account for the full spectrum of customer demands. Some end-users (particularly those new to industrial UAV survey work) still want a bare-bones, single-screen computer with 8 GB of RAM purely for managing aircraft waypoints; others seek something with a multi-core Intel i9 CPU and a non-integrated GPU, given the practical benefits of being able to output processed survey data from the GCS before leaving the survey location to analyse it and ascertain if additional flights are needed.
Given the speed at which new processors and embedded systems are released, the capacity for hub- and case-based GCSs to integrate with rack-mount computer cases designed for field surveys, and hence rapidly take advantage of new innovations in processing solutions, will become increasingly prized by high-end operators across industry and defence.
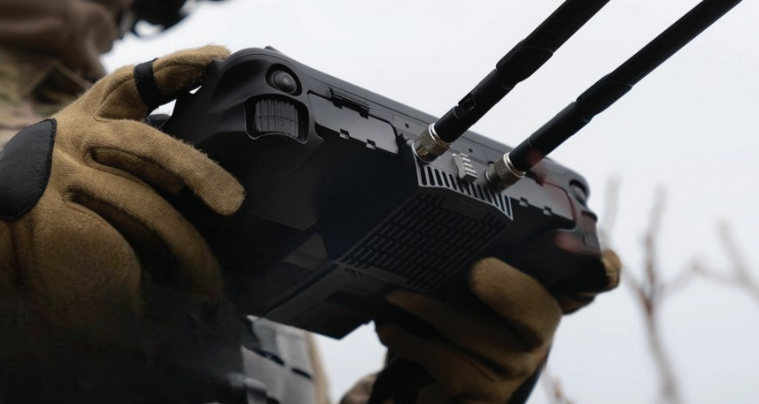
(Image courtesy of UXV Technologies)
Design standards
While GCSs remain highly bespoke systems in many quarters, with customisations needed for every end-user, mounting calls for connectivity and interoperability (as well as the need to reduce training when operators are forced to use a different GCS to their usual set-up) are influencing the emergence of new regulations aimed at organising and standardising designs, much as certifications can increase the price of a bespoke unit.
Several of these factors directly influence the GCS design process, depending on the operation type and level of certification required, and relate closely to the Specific Assurance and Integrity Level (SAIL) standards.
Those familiar with our most recent feature on autopilots (Issue 55) may recall that the SAILs were published by EASA (FAA equivalents to follow) and indicate levels of risk and hence the system robustness needed for an uncrewed vehicle mission to be certified via a Specific Operations Risk Assessment (SORA).
For GCSs being designed to SAIL III compliance, the primary standard is the Means of Compliance (MoC) listed under Operational Safety Objectives (OSO) #19-20. Those guidelines focus on human-machine interface (HMI) qualities and were released for public consultation in July; as of writing, they remain under review by EASA. The main standard affecting SAIL IV-compliant GCS designs is coded as MoC SC Light-UAS.2615. This is similarly HMI-oriented, was published a year ago, and is still under public consultation.
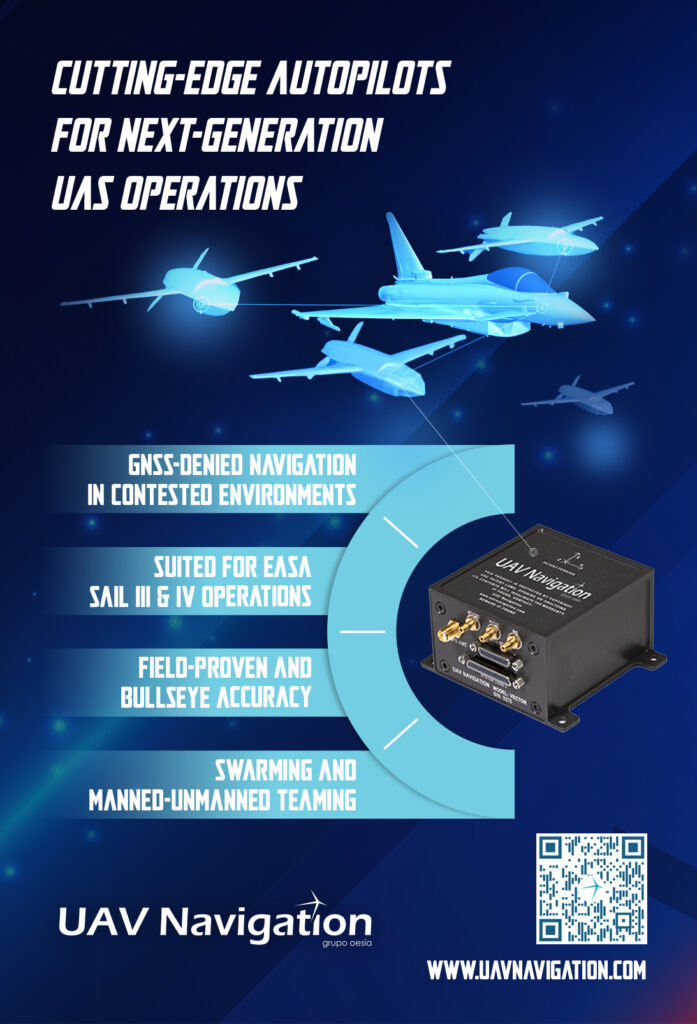
Other MoCs indirectly influencing GCS design, such as MoC OSO #5 for SAIL III and MoC SC Light-UAS.2510 for SAIL IV, do not directly address HMI aspects, but instead deal with safety issues such as redundancy or the probability of loss of control, which bear evaluating in the architecture of a new GCS (across hardware and software).
GCS and avionics manufacturers increasingly participate in the international working groups behind the development of these MoCs, while analysing their own design tools and adopting standards-compliant components wherever possible, to stay ahead of regulatory requirements and account for constructive feedback from testers and end-users.
Beyond these largely unfinished standards, the integration of electronics, racks, connectors and other components certified to relevant military, aerospace or other standards into GCSs can be a significant boon towards their usability in many operations.
Most notably, there is an emergent convergence in the number and arrangement of control interfaces across handheld GCSs, and towards certain Windows- and Android-based OSs, to aid in the aforementioned goal of increased familiarity and reduced training for soldiers who take a new GCS in hand.
Given the wide range of end-users’ requirements across the uncrewed space, capturing all relevant feedback in a dedicated data-management system can be vital for later identifying the pertinent design targets for a new GCS project, as can broader reviews or third-party consultations on advancements in core and peripheral components. Those help to ensure technology is up to date (without becoming too untried or untested for certifying bodies), including CPUs, GPUs, screens, operating systems, and design and programming tools.
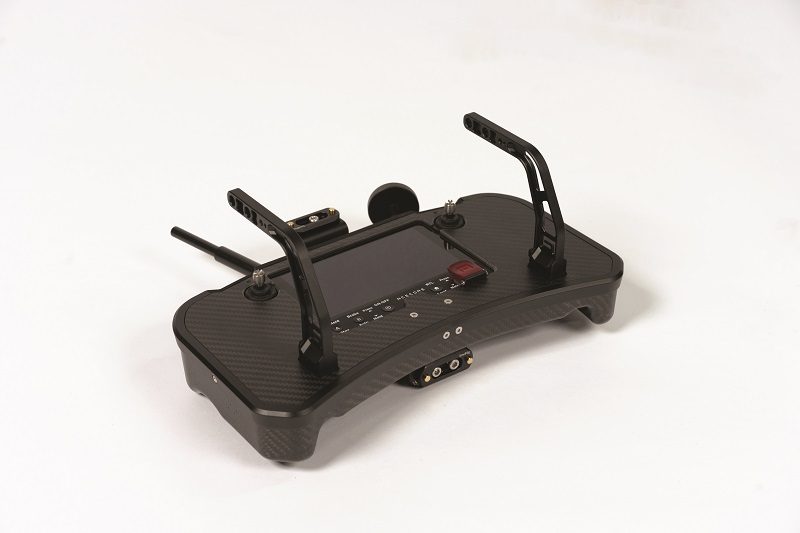
(Image courtesy of Acecore)
Iterate and simulate
Engaging in rolling feedback loops with customers can be crucial for GCS companies to incorporate lessons learned from previous iterations into the engineering process, and identify potential challenges or faults before they are unearthed through real-world testing (though this remains important for reliable GCS products).
Given the majority of GCSs sold today must unite a broad array of components within a single enclosure, and must survive being handled roughly, dropped or thrown by military personnel in extreme environments, taking a holistic approach to integration from the ground up is important to ensure all internal systems work together seamlessly.
A large part of this involves straightforward design and testing rigour to reveal and eliminate potential failure modes. Advancements in simulation software tools, however, are playing an ever-greater role in modelling and predicting GCS behaviour under varying operational scenarios.
For instance, simulating how a new GCS will handle or interact with different radios and antennas is vital to ensure the diversity of comms prized by today’s uncrewed systems market – particularly since different ports (including Ethernet, serial and CAN) must be provided for such peripherals, and some connectors are notably expensive and difficult to source.
Simulation for environmental or mechanical issues is similarly critical, given that GCSs must deal with ground-level temperatures, weather, salt spray, and so forth. Any components that may be exposed to sources of deterioration must be housed in metal, carbon composite or similarly protective materials, with treatments as needed to protect the electronics. Such enclosures must also account for the careful placement of connectors, wires and mounting brackets for hot-swappable radios or batteries.
Such simulations are critical for minimising the rounds of iteration and re-engineering needed for case-type and containerised GCSs, especially those slated for use in hot environments, where vents on multiple sides should be installed and optimised to enhance airflow, while preventing dust and moisture ingress, via custom-machined frames, seals, vent doors, variable-speed fans and other important parts.
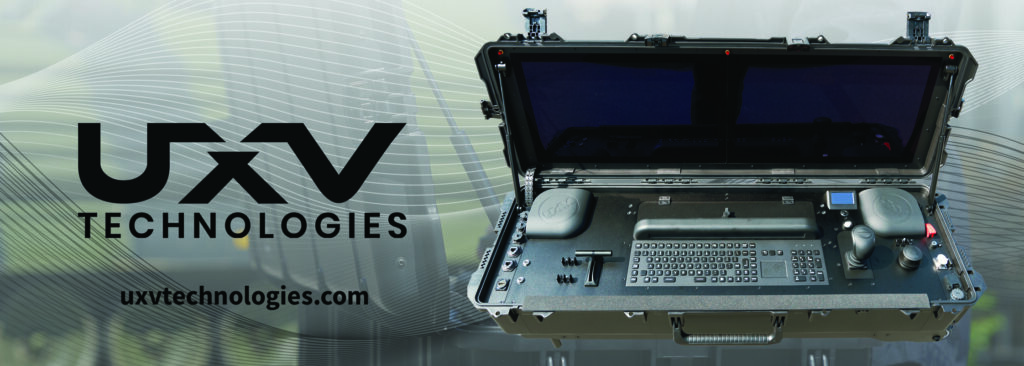
Manufacture and assembly
While custom designs still make up the majority of GCSs sold today, mounting wars and national security concerns have sparked a surge in demand from defence organisations for a GCS product that can be ordered COTS and is “just good enough” for purpose (delivery speed taking priority over design and performance optimisation for such customers).
Some military forces even consider contextually fast lead times of 10-12 weeks to be nine to 11 weeks too slow for their tastes, and this is spurring a move towards large-batch manufacturing of standardised, versatile GCS units to keep a ready stock of inventory that can be shipped within a week’s notice. As well as lowering per unit costs, standardised production lines are expected to achieve lead times of six weeks or less, with batch sizes of at least 1000 GCSs, within the next few years.
This shift towards standardised GCS batches is driving investment in automated assembly machines, as well as appropriate ISO ratings for efficiency, cleanliness and traceability among manufacturers to maximise consistency of the units produced.
Going forwards, some GCS makers will benefit from closer access to state-of-the-art factories where even circuit boards can be manufactured under strict quality controls, with high-end production lines outputting certified or certifiable components.
However, customisation is expected to remain in some aspects of even batch-manufactured GCSs with, for instance, minor external customisations to standard products, such as logo stamping, modifications to grips and brackets, or a means of customising the last 2% of a given design while still leveraging the cost- and time-saving benefits of a semi-automated production line.
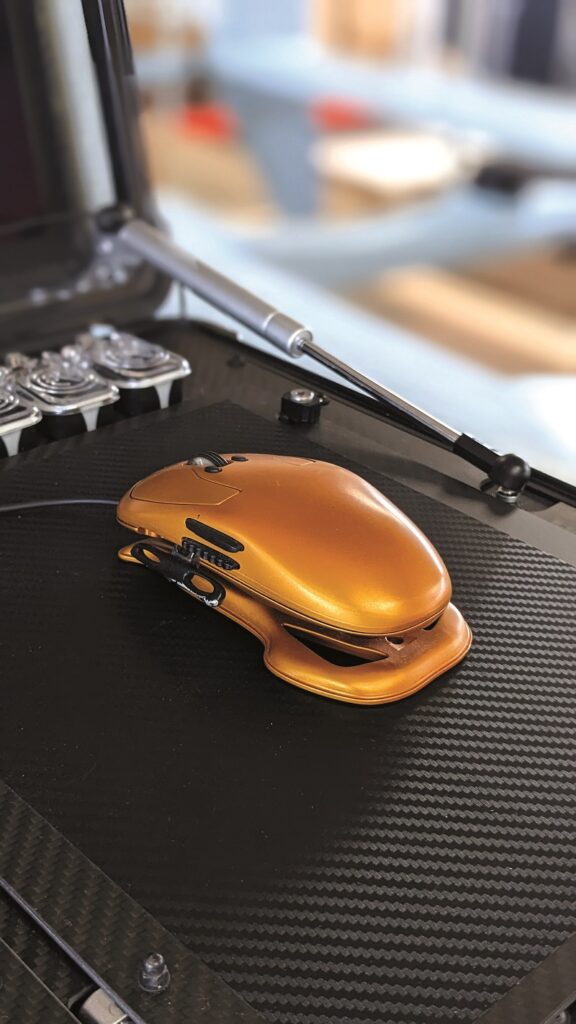
(Image courtesy of Worthington Sharpe)
Group tests
As with many avionics-related solutions, one can find two broad groups of tests that GCS producers undertake on their units: verification or validation tests conducted before a GCS design goes into production; and operational tests carried out on every unit that comes off the production line.
Among the former are well-known environmental, shock, vibration and other tests intended to define destructive limits and tolerances to mould, electrostatic discharges or impacts.
GCS prototypes that fail to pass these tests to established industry or military standards (depending on the intended market) must be redesigned, and then run through the tests again with varying levels of intensity until the testing standards are met and the prototype can become a solution approved for manufacturing.
Naturally, tests ascertaining the operating capabilities of GCSs from the production line are not so intensive and will not compromise the lifespan of units.
Additionally, stringent EMI testing protocols (in the engineering and production of GCSs) can help to ensure solutions meet industry standards for EMC, and minimise the chance of interference between GCS components, or from the GCS to its user’s peripherals or uncrewed vehicles when nearby.
With advancements in companies’ storage and management facilities, testing data can now be recorded and kept traceable via each unit’s serial number. This enables customers – and maintenance technicians in particular – to check their received GCSs were proven operational by the manufacturer, providing assurance that returns among the now thousands of these systems being produced for the uncrewed space will remain low in the years ahead.
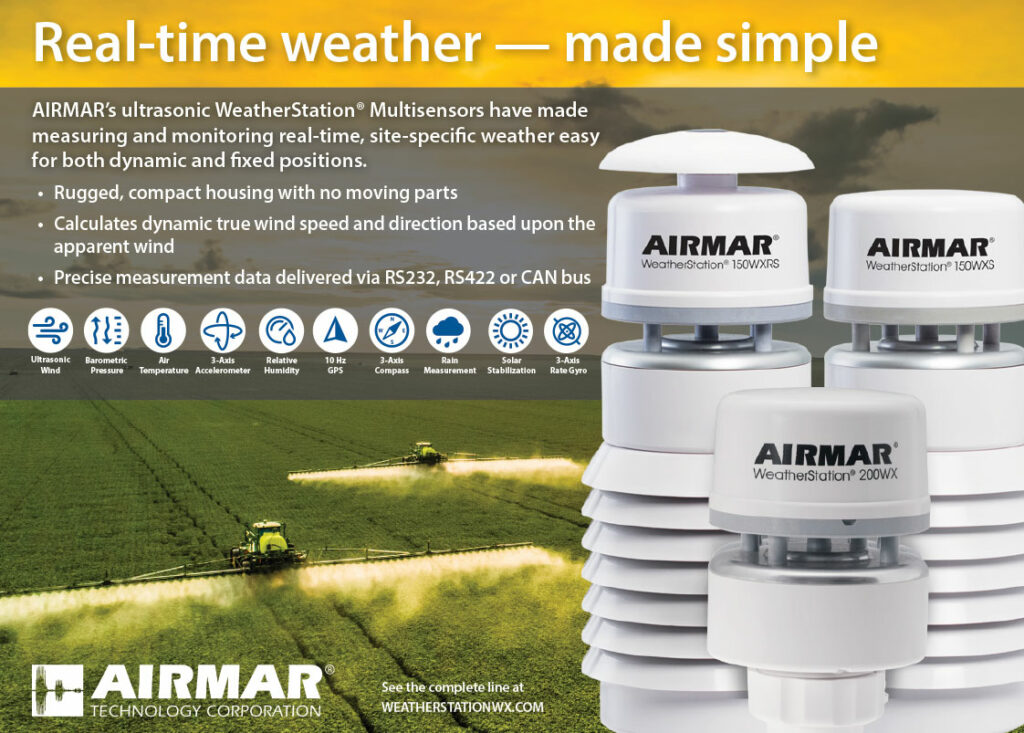
Tomorrow’s GCS
With high-end, uncrewed systems customers becoming more aware of their core requirements in a GCS, the evolution of mission-management and monitoring consoles will be increasingly steered towards improvements in usability, human/machine interaction, and the ability for greater numbers of vehicles to be managed smoothly and securely by fewer operators (from more locations).
Resilience to cyber attacks and other remote threats in myriad environments will also become paramount in control solutions, not only among defence users, but also civil and industrial ones, given the potential for damage and disruption that even one remotely seized UAV can cause.
Additionally, some GCS designers are questioning whether conventional control surfaces – including yokes, paddles, joysticks and other mainstays of crewed aircraft cockpits – are truly the best tools for the job when it comes to uncrewed operations management.
Future designs of GCS products can be expected to increasingly experiment with unusual (relative to present-day equipment) styles of control peripherals that blur the lines between joystick, toggle, PC, mouse and other well-known items, with the aim of creating new, as yet unnamed, devices.
More eye-catching contenders along these lines can be expected to be unveiled in the years ahead by companies aiming to create something more ergonomic, convenient and intuitive than their 20th-century predecessors – gaming controllers included.
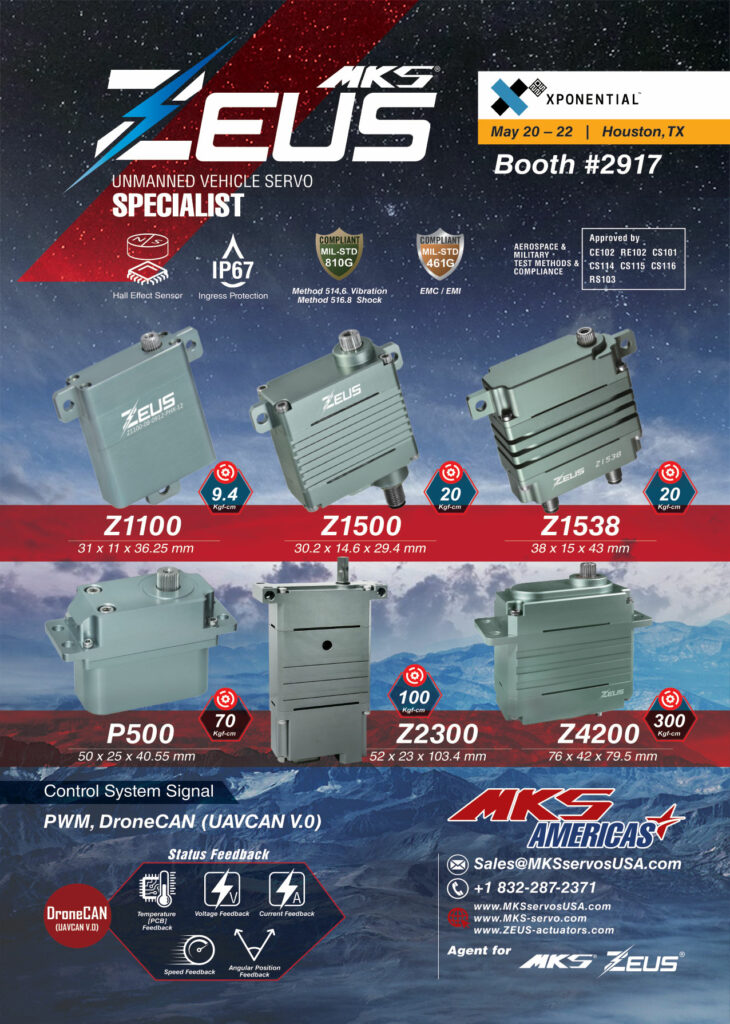
Acknowledgements
The author would like to thank Frank Severinsen and Frederik Bergenfelt Friis of UXV Technologies, Torsten Appelhagen of TM IT-Systemhaus, Sam Worthington of Worthington Sharpe, Matt Paddock of Autonodyne, Marvin Van Lith and Olaf Keijzers of Acecore Technologies, Howard Loewen of MicroPilot, Iwi Lin of Twinhead International Corporation, and Miguel Angel de Frutos of UAV Navigation-Grupo Oesia for their help in researching this article.
Some examples of ground control system manufacturers and suppliers
CANADA
MicroPilot | +1 204 344 5558 | www.micropilot.com |
DENMARK
UXV Technologies | +45 29 79 49 29 | www.uxvtechnologies.com |
ESTONIA
Threod Systems | +372 512 1154 | www.threod.com |
FRANCE
Aerodrones | +33 970 407 371 | www.aerodrones.com |
Cloudskeyes | – | www.cloudskeyes.fr |
GERMANY
TM IT-Systemhaus UG | +49 471 3069 888 0 | www.beasttx.com |
ISRAEL
BlueBird Aero Systems | +972 9 899 9335 | www.bluebird-uav.com |
Flying Production | +972 9 832 7061 | www.flying-production.com |
IAI | +972 3935 3111 | www.iai.co.il |
ITALY
Alex Sistemi | +39 02 90380626 | www.alex-sistemi.it |
JAPAN
Futaba | +81 3 4316 4811 | www.futaba.co.jp |
LATVIA
SPH Engineering | +371 25453422 | www.ugcs.com |
NETHERLANDS
Acecore Technologies | +31 6 18685736 | www.acecoretechnologies.com |
NORWAY
Robot Aviation | +47 906 52 502 | www.robotaviation.com |
POLAND
Aerobits | +48 500 501 305 | www.aerobits.pl |
SPAIN
Embention | +34 965 115 421 | www.embention.com |
UAV Navigation | +34 91 657 2723 | www.uavnavigation.com |
SWEDEN
UAS Europe | +46 13 560 22 40 | www.uas-europe.se |
TAIWAN
Twinhead International Corporation | +886 2 5589 9999 | www.durabook.com |
UK
Worthington Sharpe | +44 161 8830883 | www.worthingtonsharpe.com |
USA
AeroVironment | +1 805 581 2198 | www.avinc.com |
AlarisPro | +1 410 881 0800 | www.alarispro.com |
Aquiline Drones | +1 860 361 7958 | www.aquilinedrones.com |
Arcturus UAV | +1 707 206 9372 | www.arcturus-uav.com |
Autonodyne | – | www.autonodyne.com |
Bokam Engineering | +1 714 513 2200 | www.bokam.com |
CP North America | +1 800 787 4913 | www.cpnorthamerica.com |
Easy Aerial | +1 833 3279 828 | www.easyaerial.com |
Futaba Corporation of America | +1 847 884 1444 | www.futaba.com |
Lockheed Martin | +1 801 224 5713 | www.lockheedmartin.com |
RTX Corporation | +1 310 647 1000 | www.rtx.com |
Shield AI | +1 512 520 7170 | www.shield.ai |
Systems Integration Plus | +1 480 513 8979 | www.vme.com |
Textron Systems | +1 800 655 2616 | www.textronsystems.com |
UAV Solutions | +1 240 456 0195 | www.uav-solutions.com |
Vigilant Aerospace Systems | +1 405 445 7224 | www.vigilantaerospace.com |
UPCOMING EVENTS
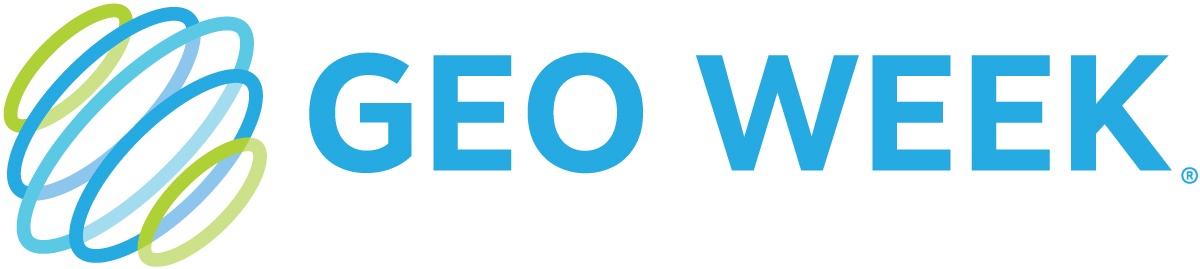
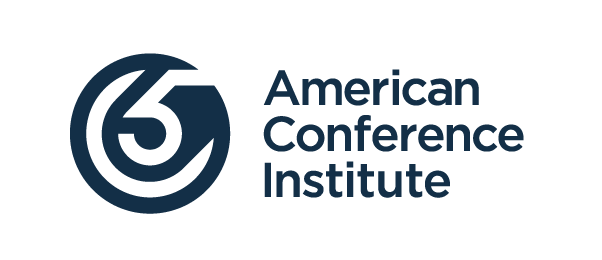
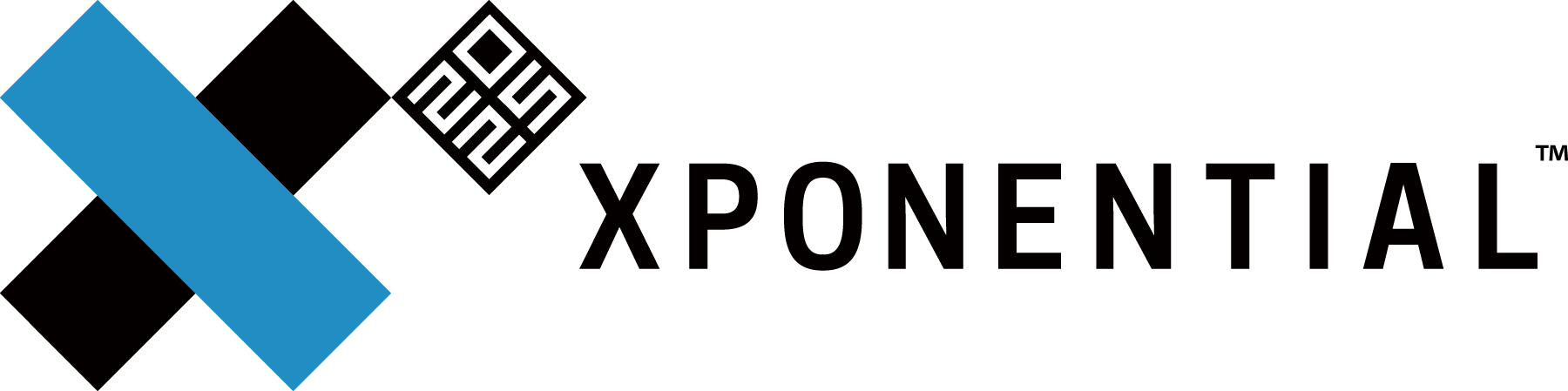
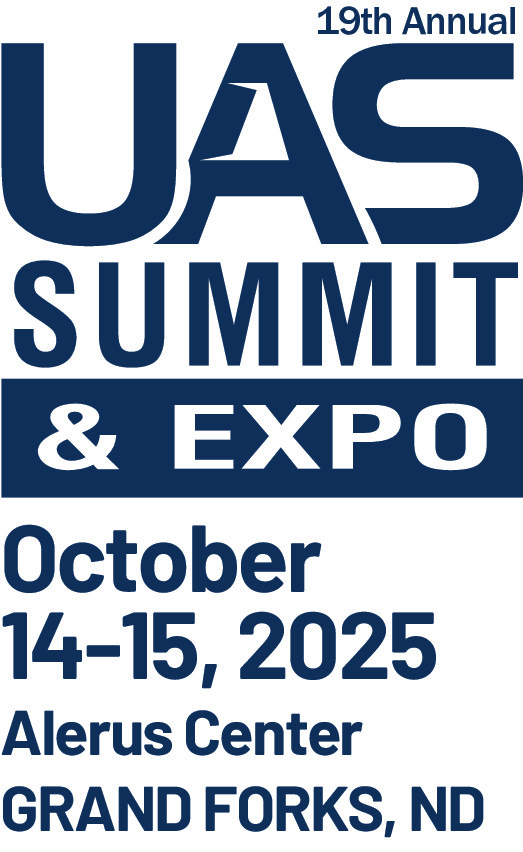
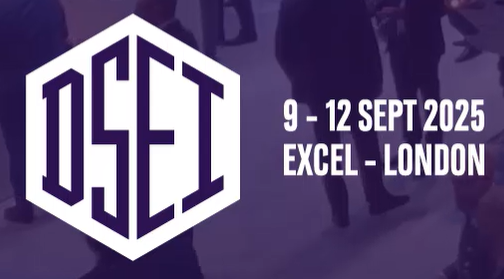
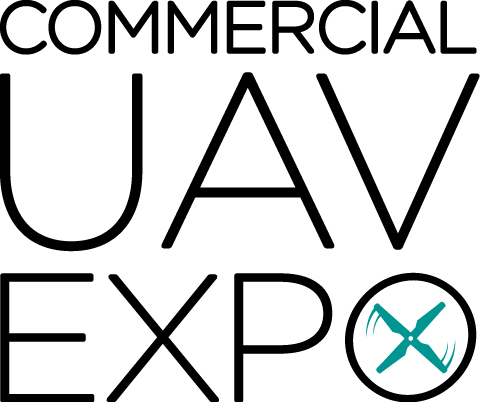
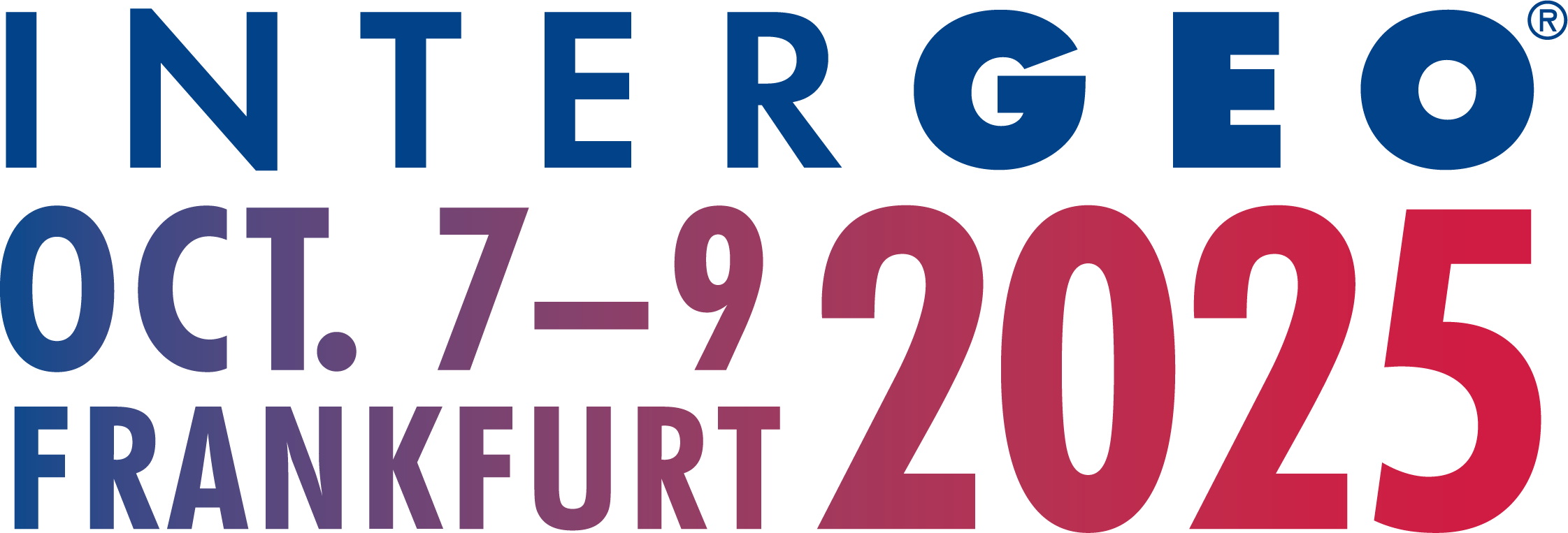
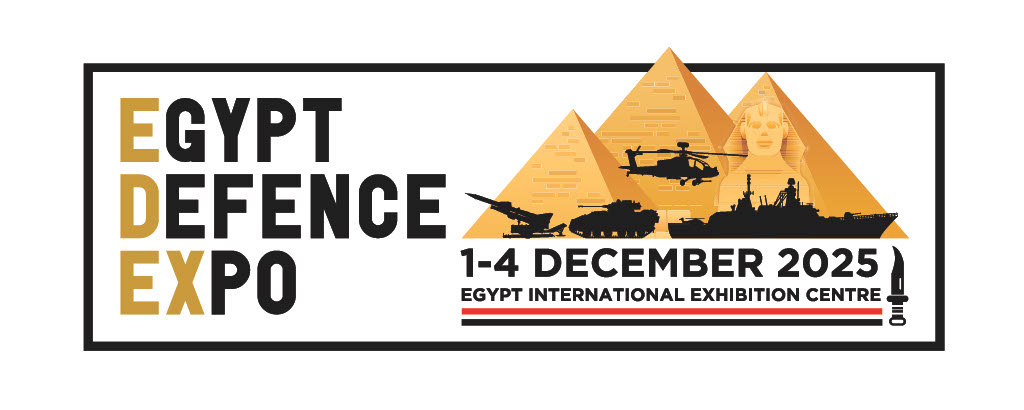
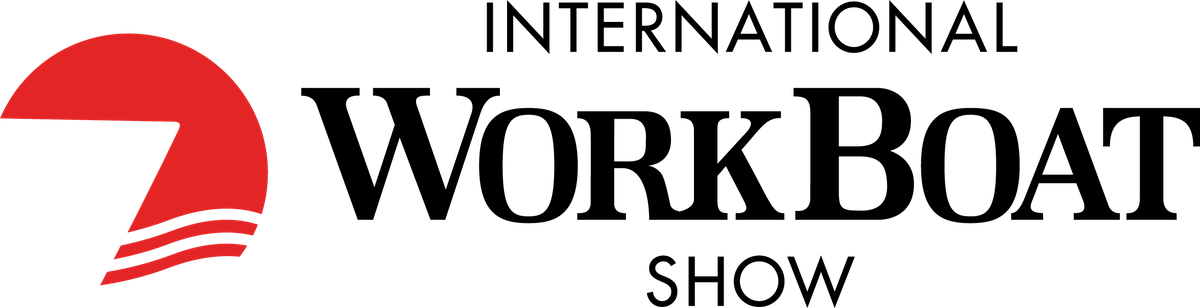
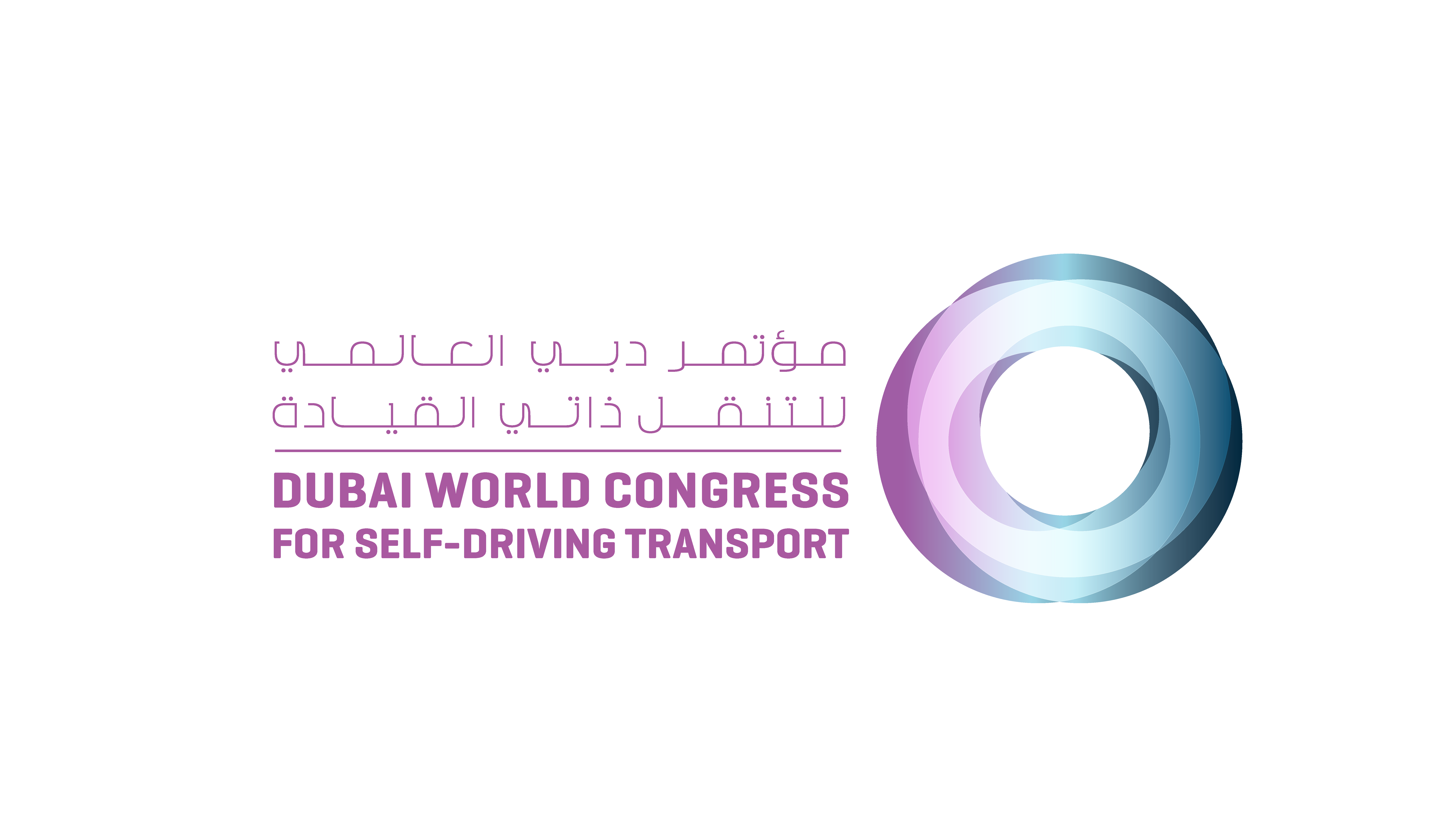

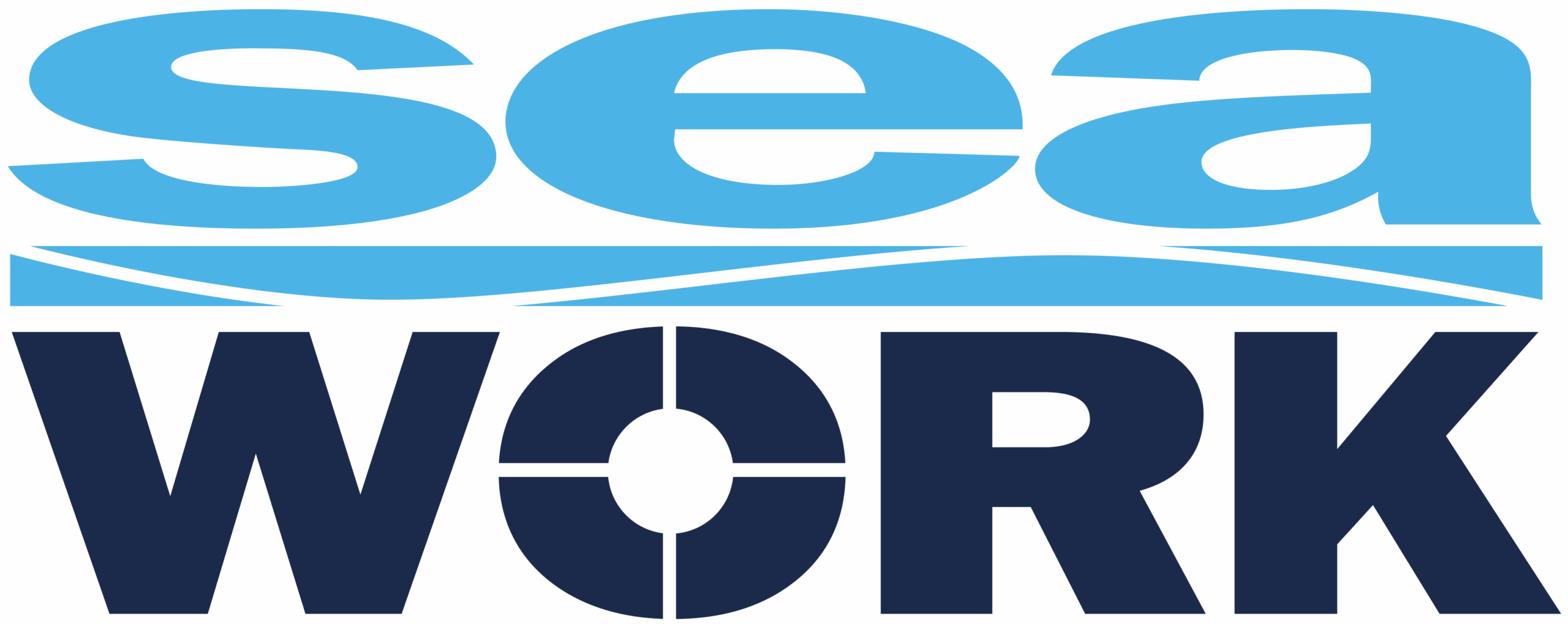