Fog-proof coating
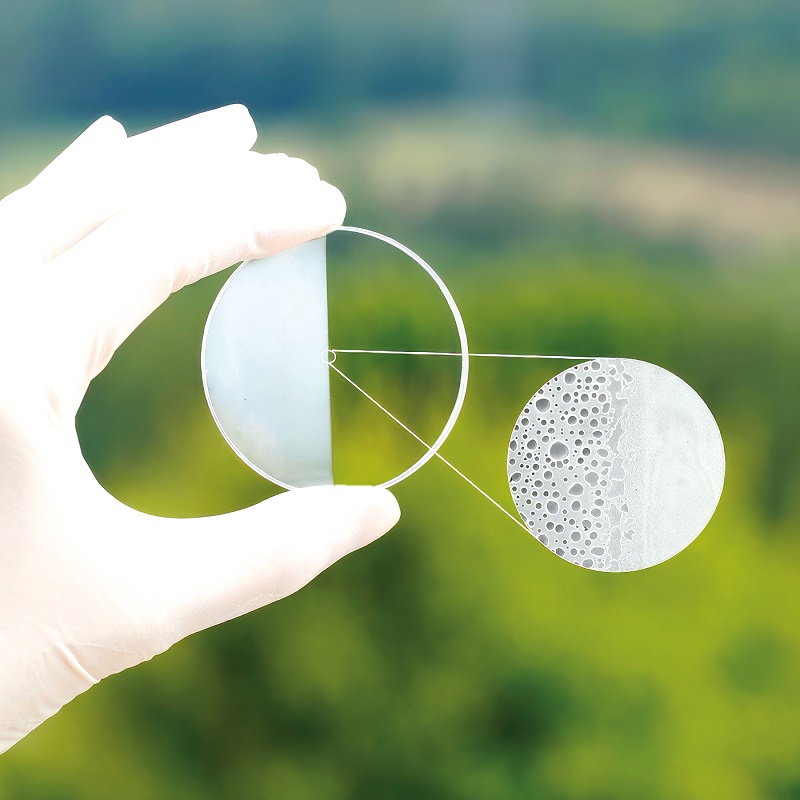
An optical coating that combines anti-fogging and anti-reflective properties to boost the performance of Lidar systems and image sensors has been unveiled (writes Nick Flaherty).
Researchers in Germany, at the Fraunhofer Institute for Applied Optics and Precision Engineering, and the Friedrich Schiller University Jena, say the coating prevents fogging by using porous silicon dioxide nanostructures that reduce reflections. It was designed for Lidar systems but can be tailored for other optical systems.
The coating was developed in response to a need identified by Leica Geosystems, which develops airborne Lidar measurement systems for terrain and city mapping. When there are extreme temperature differences between the environment and the measuring system, fogging sometimes occurs on the optical surfaces.
The polymer layer prevents fogging on an optical surface by acting as a water reservoir. However, differences in the refractive indices of the polymer material and the surrounding air leads to unwanted reflections and ghost light. To prevent the reflections, the researchers used very small structures, up to 320 nm high, to create an anti-reflective effect together with water permeability.
To make the coating, the researchers used an AR-plas2 plasma-ion-assisted coating machine developed at the Fraunhofer Institute for Applied Optics and Precision Engineering. It allows several nanostructures to be created on top of each other, etching a nanostructure into the anti-fog coating and then fabricating a second nanostructure on top.
That allows the refractive indices of the nanostructures to be adjusted to achieve very low reflections over the wide spectral range required by a Lidar sensor.
Samples manufactured with this new coating technology have already been used successfully for a year in several airborne Lidar prototypes operating in various climatic conditions around the world.
Because the structures are generated in a standard plasma system, the new approach can be easily incorporated into commercial manufacturing processes.
UPCOMING EVENTS
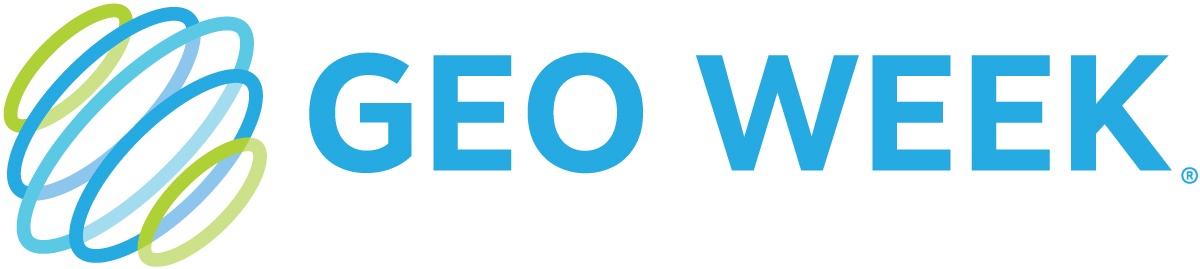
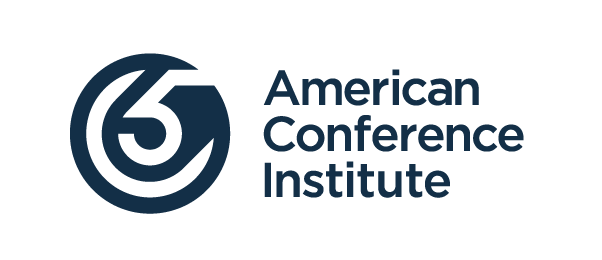
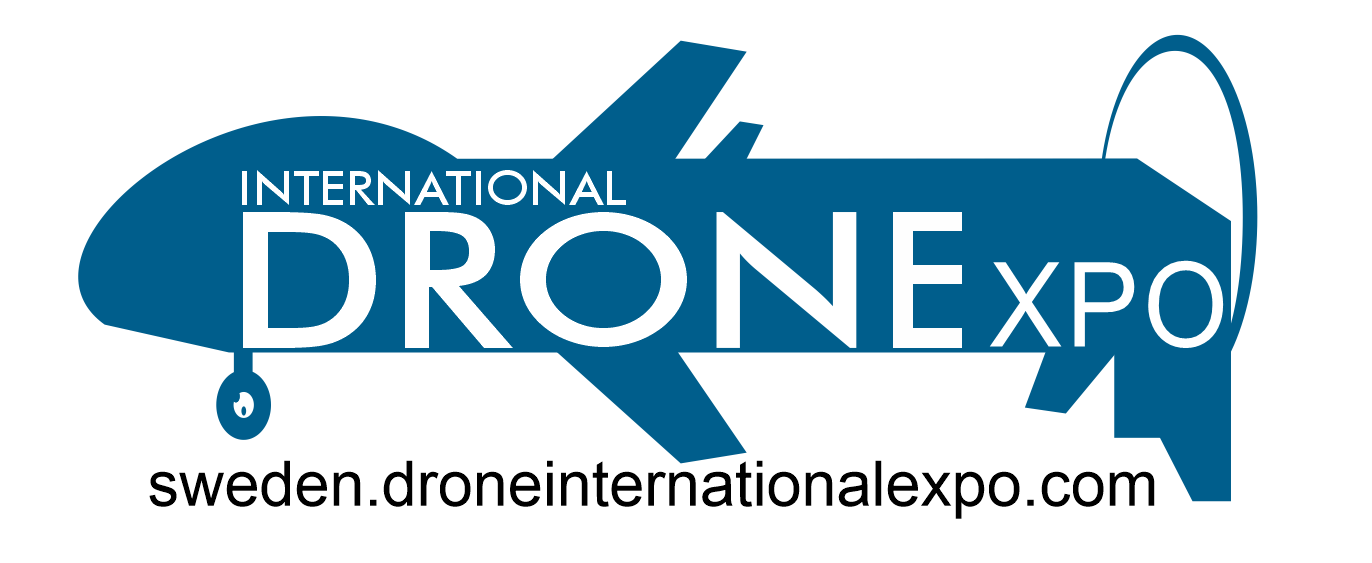
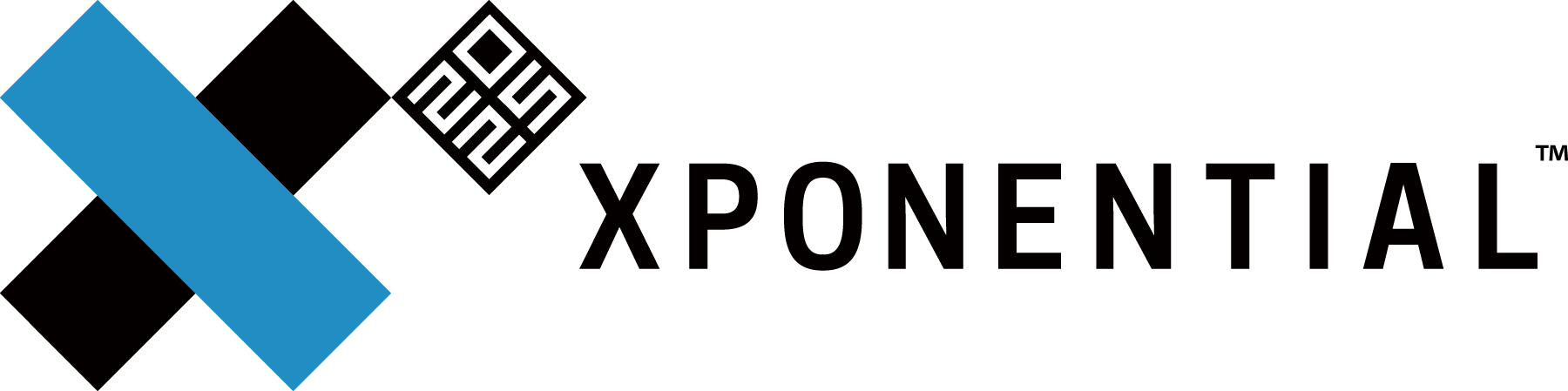
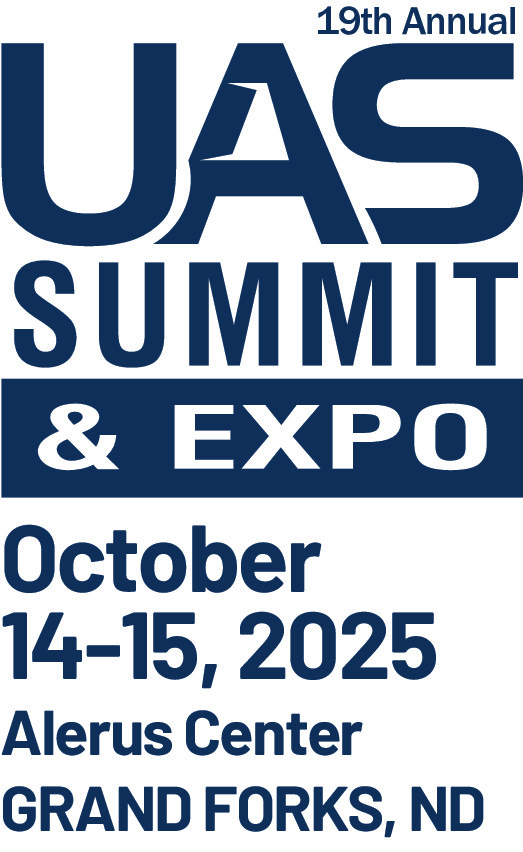

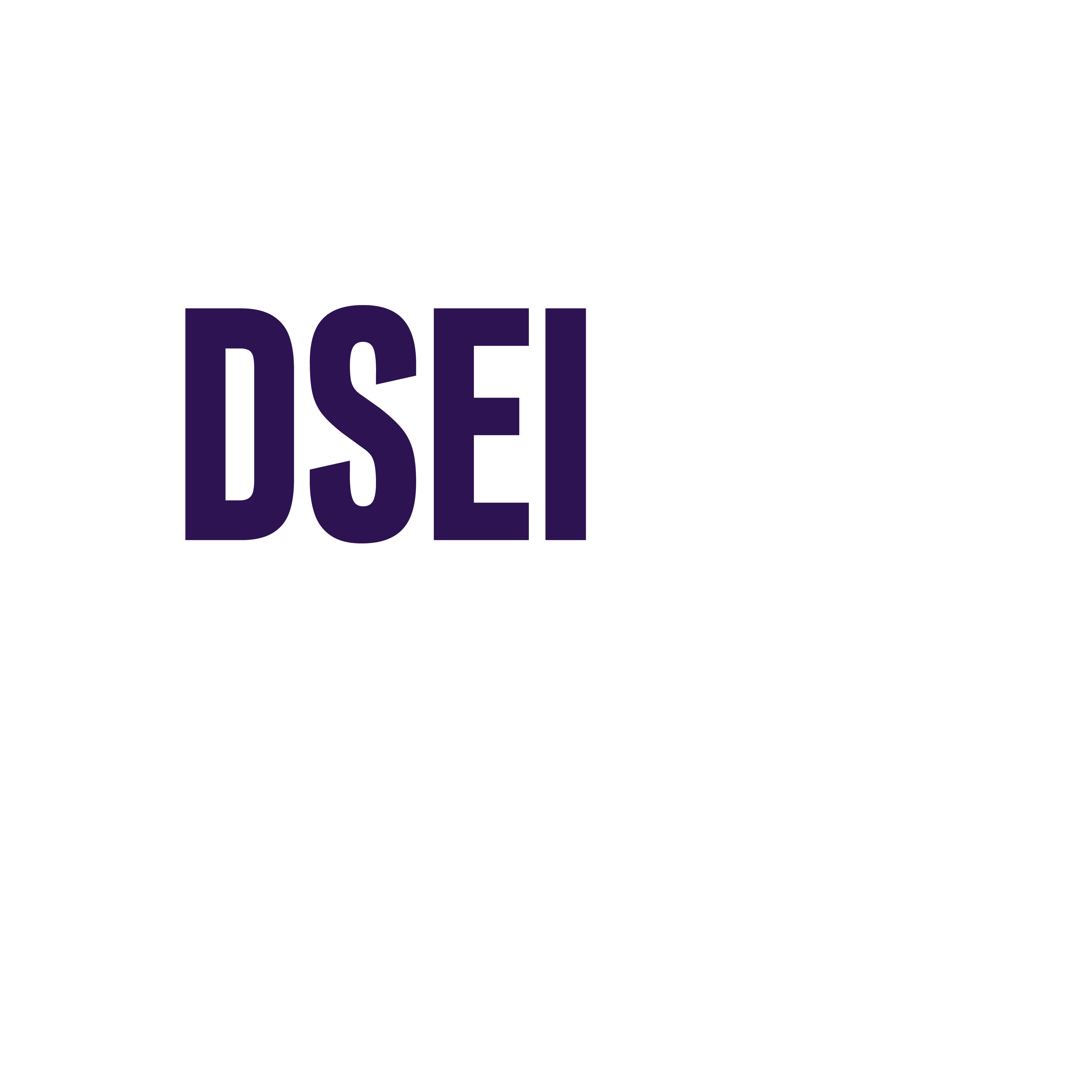
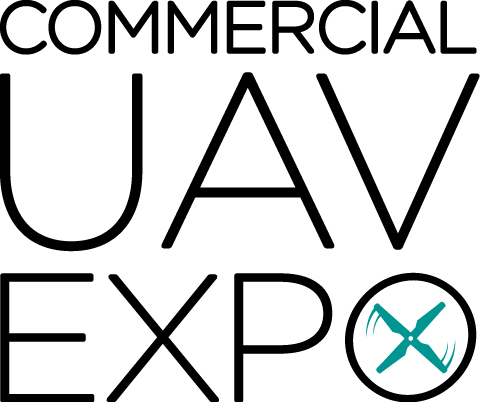
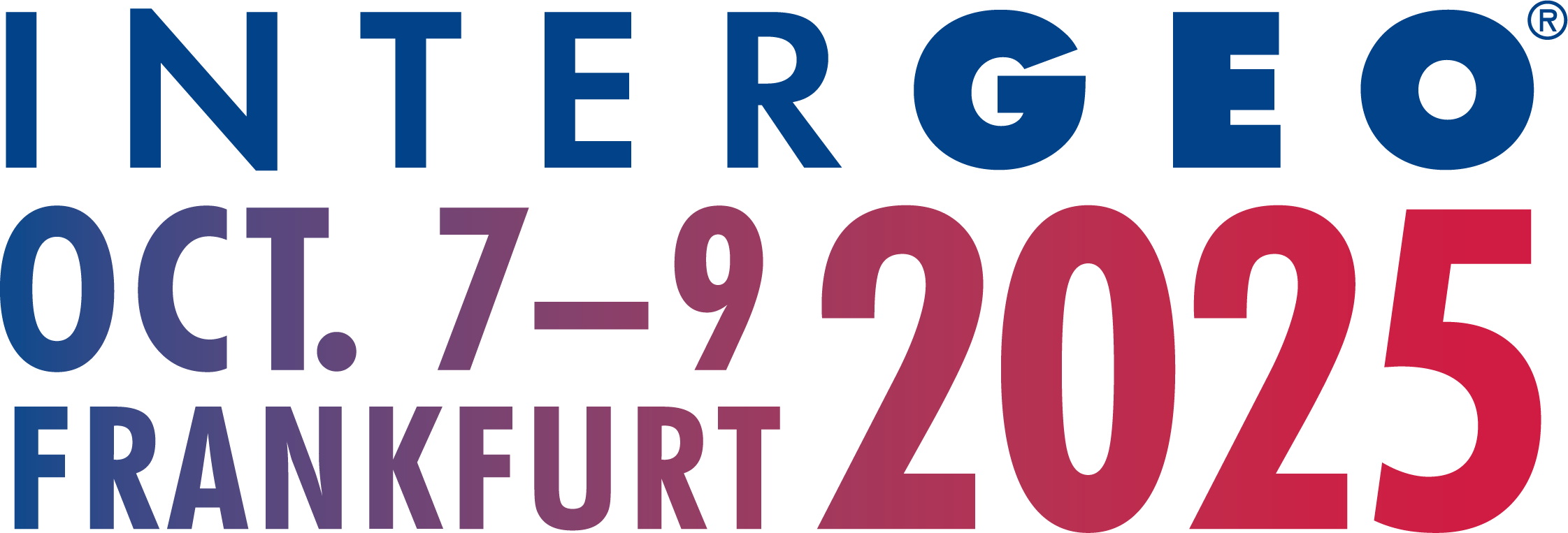
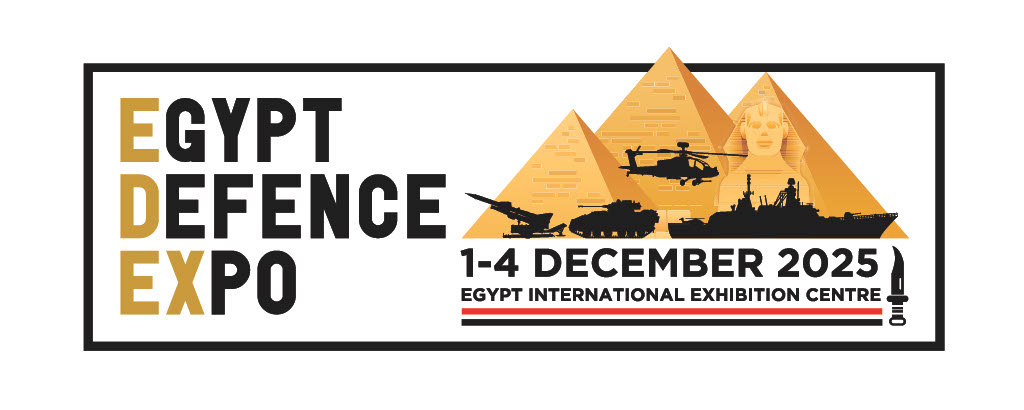
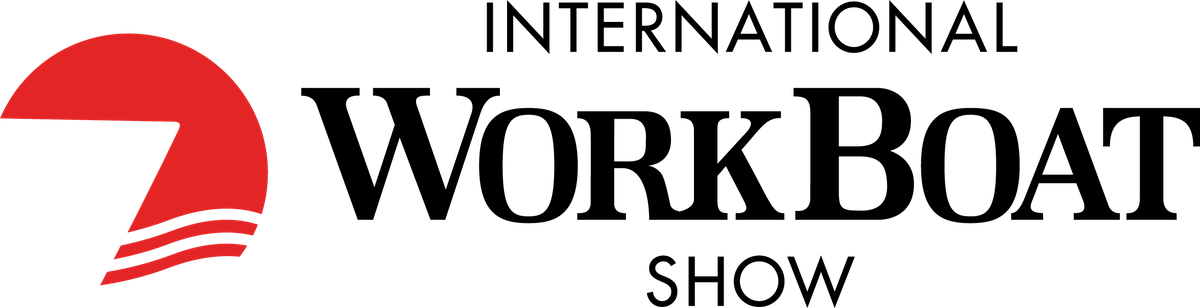