Jakub Weglarz
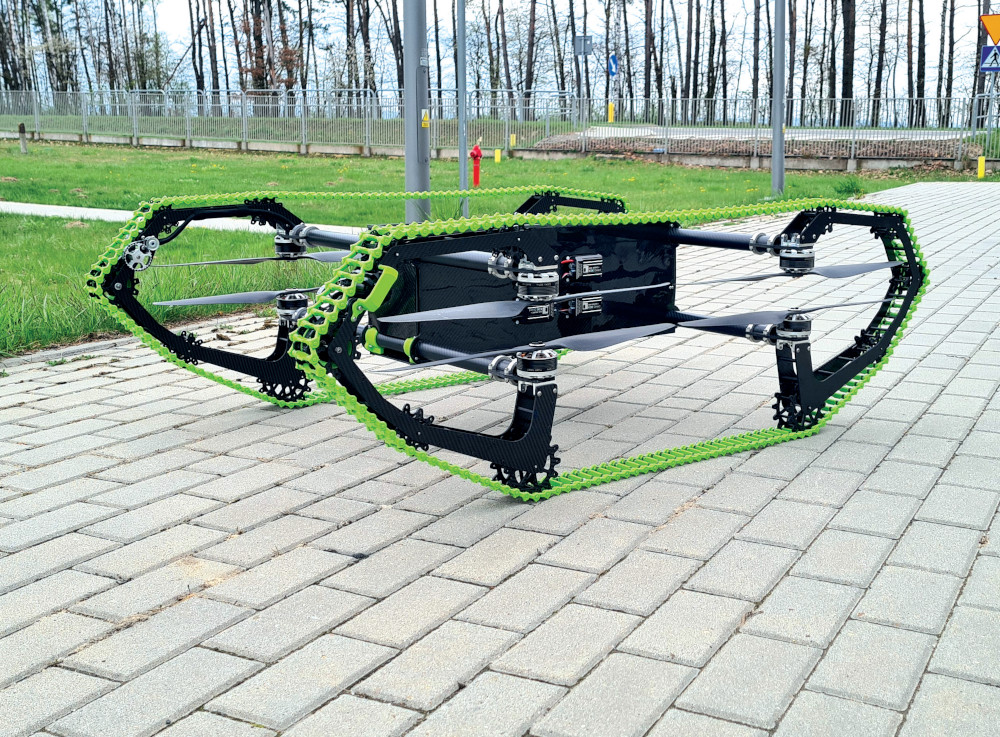
Fly-drive journey
DroneHub’s HUUVER project manager talks to Peter Donaldson about his involvement in developing this UGV-octocopter.
Hybrid vehicles that can operate in more than one medium are always tricky to develop. The demands of flight, to minimise weight for example, conflict with the requirements of a vehicle that can operate on the ground and successfully negotiate different types of terrain. These are some of the challenges faced by the developers of the HUUVER (the Hybrid UAV-UGV for Efficient Relocation of Vessels) which resembles a skeletal version of a WW1 British tank combined with an electric octocopter.
Funded by the EU under its Horizon 2020 initiative and by the European GNSS Agency, the HUUVER was conceived to perform missions under difficult conditions using capabilities including flight with VTOL, perching, driving and climbing, its ground movement ability allowing it to reach areas inaccessible from the air. An integrated Galileo GNSS receiver is the primary navigation sensor, backed up by Lidar and cameras, including thermal and visual cameras for its core search & rescue support mission.
The project team is led by DroneHub, known for its drone-in-a-box automated monitoring and data collection system, and includes Bladescape, Brimatech, Cervi Robotics, GINA, LUT University, NTT Data and Rectangle. In overall charge is project manager Jakub Weglarz of DroneHub.
“As long as I can remember I have been interested in past ages and how they influence the present day,” he says. “Political science and history complement each other, and if you know history you can forecast some sort of future,” he says.
At high school he attended meetings run by his history teacher, and was introduced to historical and technological issues that chimed with a growing enthusiasm for making model aircraft and tanks from kits, eventually building them from scratch.
“With every model I tried to learn something about its history and why it was designed the way it was,” he says.
The design of the Israeli Merkava main battle tank made a particular impression, with its storage of diesel fuel between layers of armour so that the entire hull becomes one big fuel tank. The design evens out weight distribution, makes it less likely that a hit will ignite all the fuel at once, and even adds some impact absorption capability, he notes.
Before joining DroneHub in 2021, Weglarz was involved in several uncrewed vehicle projects in the context of Poland’s cooperative industrial clusters. One of these was the development of an autonomous UGV to plant and tend grapevines. Others included developing UGVs for highway maintenance, maritime patrol and monitoring UAVs operating from ships, and a cooperative effort involving DroneHub in monitoring wind farms at sea.
Diverse projects
Working as a freelancer, he has been involved in more than 100 projects, including with local authorities on renewable energy and various Polish entities in areas such as optics and advanced materials. Working with his wife, he has raised more than e95 million in public funding for different programmes.
“I usually play the role of project manager, so I coordinate tasks, divide up work, coordinate schedules, prepare budgets, and research and write the periodic reports you have to submit when you receive public funding,” he says
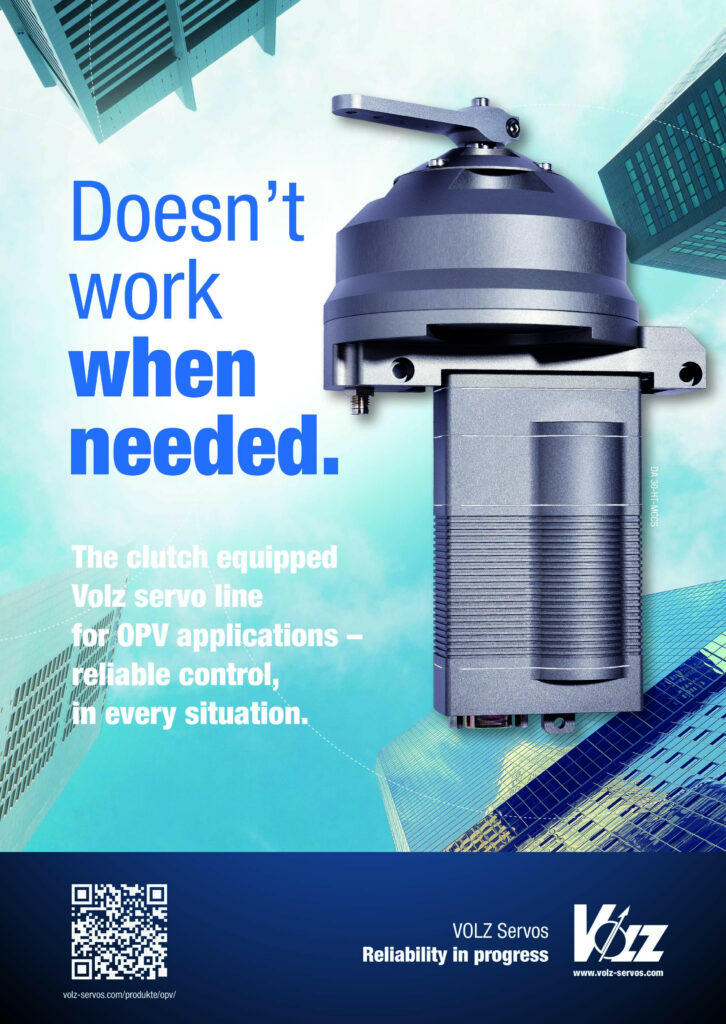
The job typically also includes troubleshooting, solving problems such as finding extra staff for a team, mediating in arguments and finding new components and materials to replace any that aren’t working well enough.
“We work in teams, and someone has to handle these issues,” he says. “Engineers bring me their wish lists and I deal with the realities of budgets, time and so on.”
Weglarz says he learns from all the technical team members he works with, but highlights brothers Lucjan and Maciej Gucma along with Rafal Gralak at the Szczecin Maritime Academy for special mention as mentors.
“The brothers are great engineers in navigation and mechanical systems. I call one of them every time I have some technical doubt on another project because their knowledge is so broad in different fields, and Rafal was really key in terms of augmented reality. Together they make a wonderful team for solving technical issues.”
Co-funded by the European GNSS Agency, which is part of the EUSPA space agency, the HUUVER project began at the end of 2019 and has completed its r&d phase. Around 40 people from seven organisations in five European countries contributed to its development, and are now focusing their efforts on technical improvements and getting it market-ready.
Tracks and rotors
The HUUVER has two tracks, each driven by its own electric motor through a belt drive system that provides two stages of reduction between the motor output shaft and the drive sprocket.
It has eight vertically mounted propellers that are also powered by individual motors, and all of them are off-the-shelf items. Even with 10 motors, this is a simpler and more robust arrangement than would be possible if the same motors, or a subset of them, were to drive the propellers and the tracks through an inevitably elaborate transmission system, Weglarz argues.
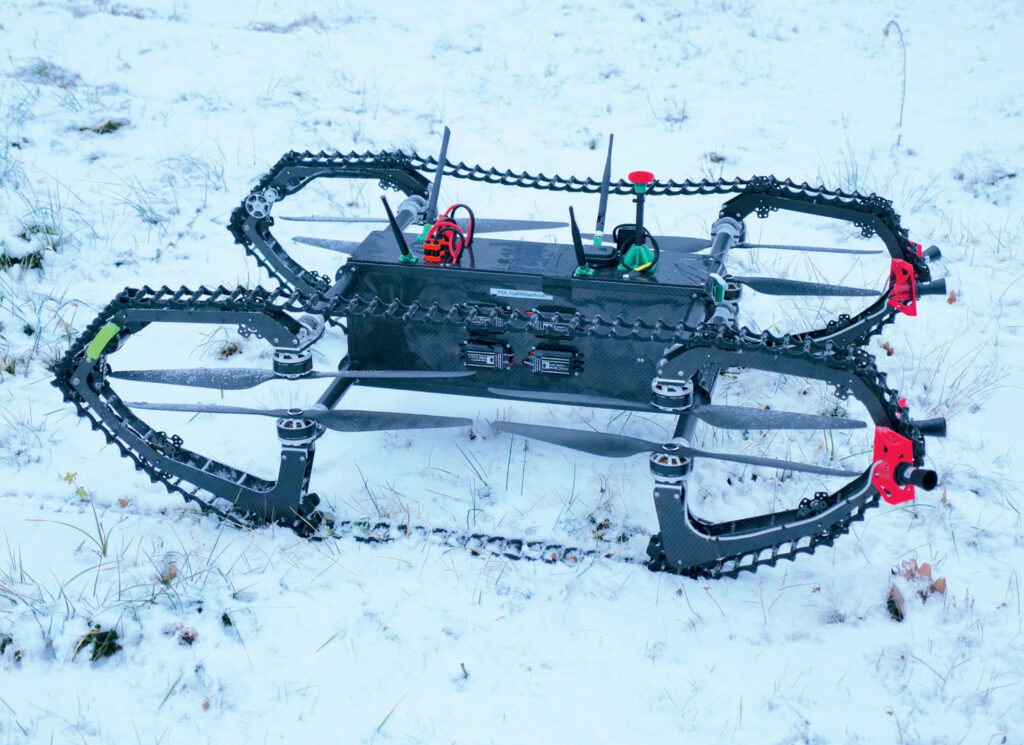
“A very complicated transmission is quite easy to damage, and that would bring trouble,” he says.
Closely coupled and counter-rotating, the propellers are mounted inside the tracks and are quite close to the fuselage, an arrangement that makes the aerodynamics complex, so tuning the
flight control algorithms to ensure good stability and control margins was a major task. Also, the control software has to both fly the vehicle and control it on the ground, Weglarz points out.
“One of the main engineering challenges was combining the drive and flight modes in one device and integrating it in software to provide the full set of operational abilities,” he says.
The flight control challenge centred on trimming the eight motors in all three rotational axes. The HUUVER can be seen flying on YouTube, displaying good stability and control, but achieving that was tricky. “The software took a lot of effort to trim the vehicle with enough precision to get that outcome,” he says.
Challenging trim
Much of the initial flight control work was done in simulation, which proved problematic in that good results predicted by the simulation were often not repeated in the tethered flight tests.
“In the end, we focused on tests in a warehouse, where we had the prototype plugged into a generator and tethered to a base so that we and the aircraft would be safe while the guys were trying to find the proper balance in trim,” he explains. “That way we could observe the vehicle’s behaviour while monitoring all the trim settings on the motors, then correct the control algorithms.”
Success in the tethered tests allowed the team to move on to free flight tests inside the warehouse before venturing into the outside world for airborne and ground work. The latter included driving in dusty conditions, on snow, sand, grass, tarmac roads and small piles of rubble.
“There is no connection between the flying and the driving that could affect controllability,” he emphasises.
Control on the ground is straightforward, as the HUUVER is a conventional tracked vehicle and behaves like one, with only two motors powering two shafts, while the rest of the mechanism passively tensions and retains the tracks.
Galileo integration
Integration with the Galileo system was crucial as well. The HUUVER uses the Precise Point Positioning (PPP) and authentication services provided by the system, supporting sub-metre accuracy for navigation and verification of GNSS information and of the sender for documentation purposes.
Effective for multiple navigation satellite constellations, PPP removes GNSS errors by sending the receiver satellite clock and orbit corrections generated by a network of continuously operating reference stations, according to the EUSPA. The corrections are distributed via satellite and over the internet.
As a result, the usual 3-5 m position error associated with GNSS is reduced to between 20 cm and 1 m when the receiver has an unobstructed view of the sky, and can reach sub-metre accuracy in under a minute, says the agency.
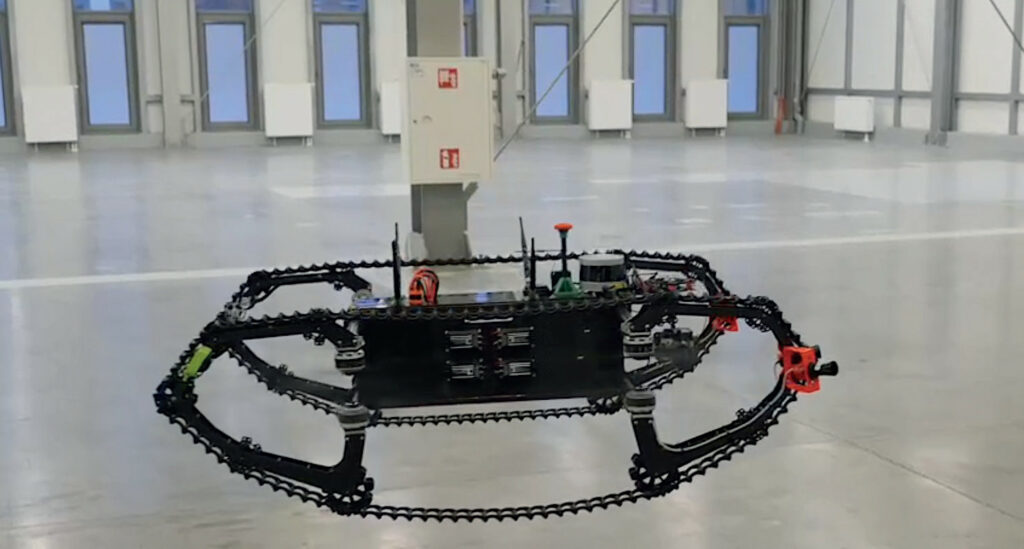
PPP is promoted as an alternative to other GNSS enhancement systems such as RTK, offering comparable accuracy without the need for a local base station. UAV tracking is one of the applications for which the service is intended, and accuracy is due to be improved to below 20 cm with the planned introduction of Galileo’s High Accuracy Service after 2024.
Galileo is also introducing its Open Source Message Authentication (OS-NMA) service that allows the receiver to verify that the GNSS information it is receiving is authentic and coming from a trusted source, reducing vulnerability to spoofing, for example. OS-NMA uses an intrinsic GNSS capability internal to the receiver, so no extra interfaces to the avionics are needed. It will also be free of charge and potentially available beginning this year or in 2023, says the EUSPA.
The final outcomes for controllability and Galileo integration were better than anticipated, Weglarz notes.
Server and app interface
The HMI and its software must make it easy to integrate the airborne and terrestrial portions of the mission from the operator’s point of view.
The HMI is embodied in a server based application for mission planning, management and navigation, and is complemented by a mobile app. The system enables a qualified operator to power the vehicle on and off, and to place waypoints and instruct the vehicle to follow them, specifying whether it must do so in the air or on the ground.
A typical mission plan might consist of a waypoint-defined flight route, a landing point, a waypoint-defined ground route, a take-off point and a flight route home. “It all happens automatically; you don’t have to switch anything from flight mode to ground mode manually,” Weglarz explains.
An extension of the server-based system, the mobile app is designed for a wider range of users, such as emergency service first responders. As such, users might not have specialised knowledge of UAV operations, and the mobile app provides fewer functions and less information than the primary mission management system, to which it will be connected by a dedicated API.
The mobile app will enable first responders to check the HUUVER’s availability, request a mission and track the vehicle’s position, movements and time of arrival at a scene. It will also provide information on the mission status and the system’s health. Plans call for the app to be available for download for Android as well as iOS devices.
Materials
As with any air vehicle, particularly one that’s a hybrid, weight is always a critical issue, and the HUUVER programme is no exception, with materials selection playing a central part.
“First, we started with some steel components for the main frame and some ABS plastic for the fuselage, but it was too heavy,” Weglarz explains. “So after some attempts to decrease its mass we changed materials, and at the moment the main frame is constructed from duralumin so it weighs much less than before. The fuselage is made from carbon fibre and aluminium, with only the axle shafts remaining steel.”
Duralumin is a 2000 series aluminium copper alloy commonly used in airframes.
Both the caterpillar tracks and the track wheels are 3D-printed polylactide (PLA) filament. Also known as polylactic acid, PLA is a thermoplastic polyester.
Unexpectedly, the track links proved to be one of the more difficult items of the propulsion system hardware to source.
They were simply not available with the combination of flexibility and durability to stand up to ground impacts and friction, for example, so the team decided to develop their own using a 3D printer fed with standard PLA filament. Initial efforts were disappointing in terms of quality, but the solution proved fairly straightforward.
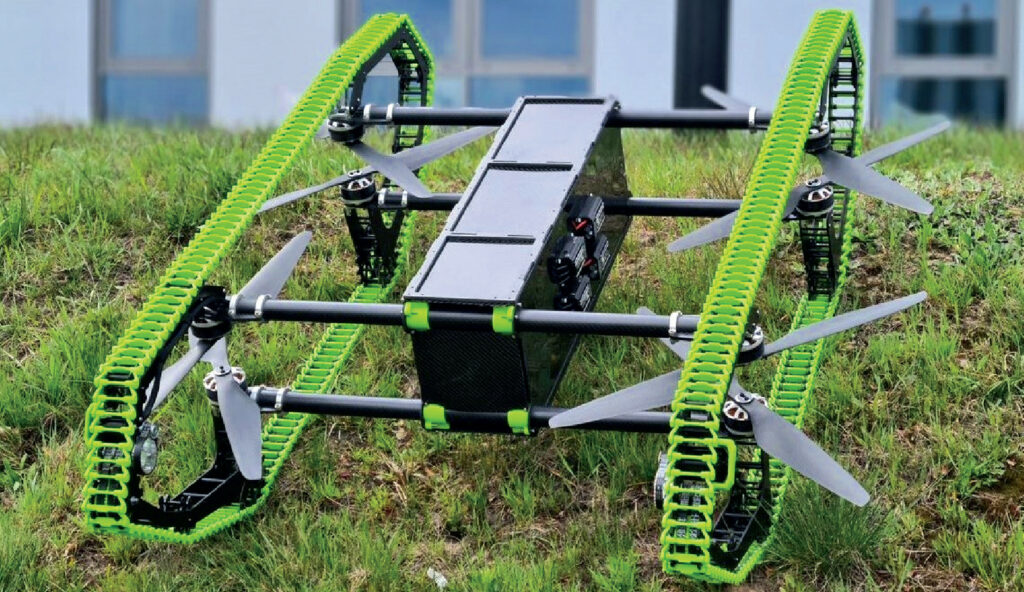
“One of my colleagues figured out that we could heat the filament more than recommended, so the material became more plastic,” Weglarz recalls. “At first we were a bit afraid that we would burn it, but that was not a problem and, after cooling down, the material becomes more durable. That led us to our new production process.”
Within the tracks are the frameworks that support the flight motors and propellers, the track motors, belt transmission, drive sprockets and idlers. The frameworks are assembled from carbon fibre-reinforced plastic plates and separators, and are attached to the central fuselage by carbon fibre tubes front and rear.
The HUUVER programme can now boast a fully operational prototype, but there are some small issues still to be resolved that are typical of the ‘childhood’ phase of product development. These include some refinement of the flight control system in the area of trim and some planned changes to the construction of the fuselage to improve water resistance.
“As with every prototype vehicle there are some aesthetic details that could be improved,” Weglarz says.
When these refinements are made, further testing will be required, while a production version is likely to embody other changes including weight reduction, which will require a whole test programme of its own, he adds.
The next step in bringing the HUUVER to market is a series of demonstrations for potential customers, including firefighters in the Czech Republic and border guards in Austria.
BIO – Jakub Weglarz
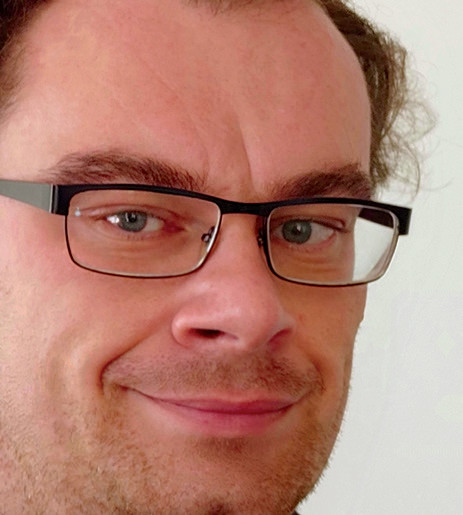
Although educated in the humanities, Jakub Weglarz, 34, developed a passion for engineering-related subjects as a child, constructing increasingly detailed models of military vehicles, and has built a career managing technology projects with a focus on uncrewed vehicles.
After qualifying in International Relations, Political Science and History at the Nicolaus Copernicus University in Torun, he studied International Economics at Cracow’s Economics University.
Starting out in project management, he was attracted to technical projects and worked on a number of them for both private and public organisations in areas including optics, IT and IoT, in addition to eight uncrewed systems efforts. These included UAVs, USVs and UGVs for monitoring, patrol and measurement missions, some developed privately and others with EU funding.
In 2021 he joined DroneHub, which was leading the multi-company consortium developing the HUUVER hybrid UAV/UGV, after which he took over as manager of the project.
UPCOMING EVENTS
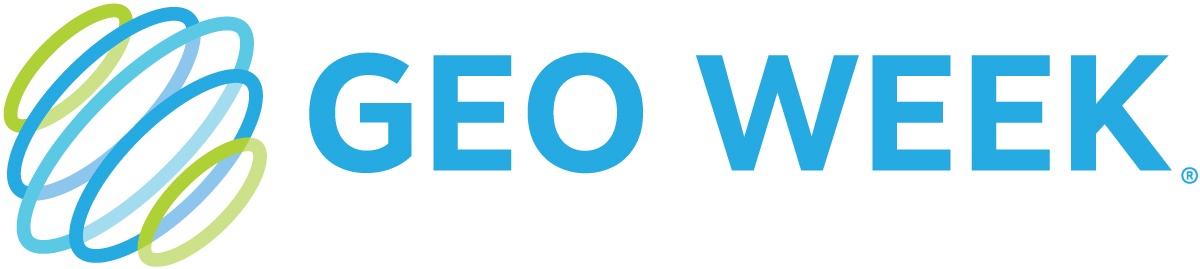
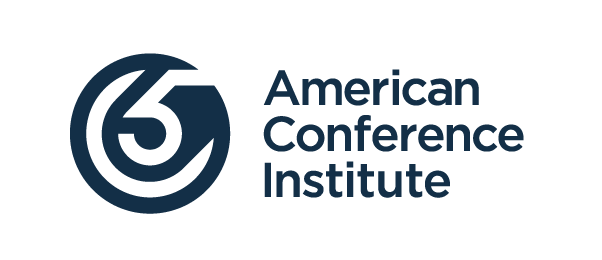
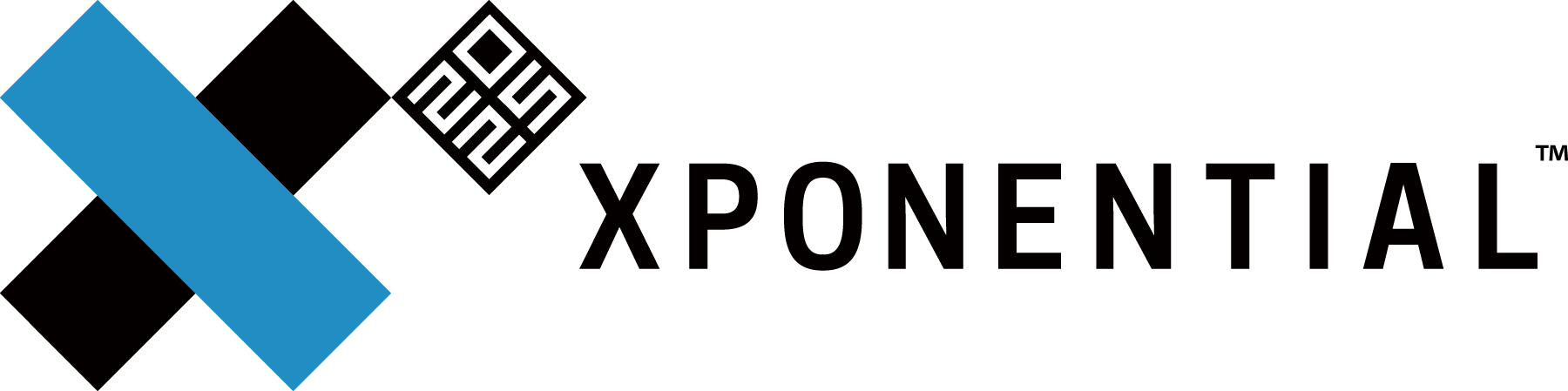
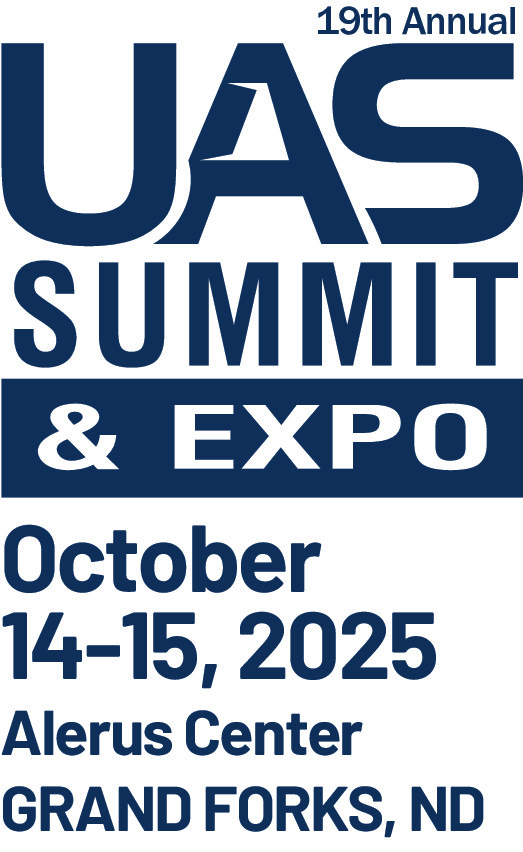
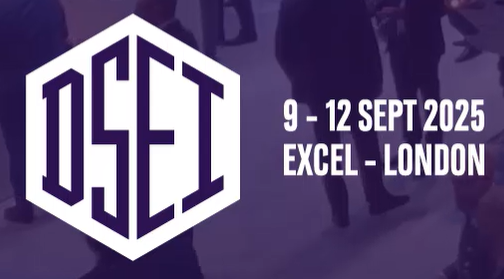
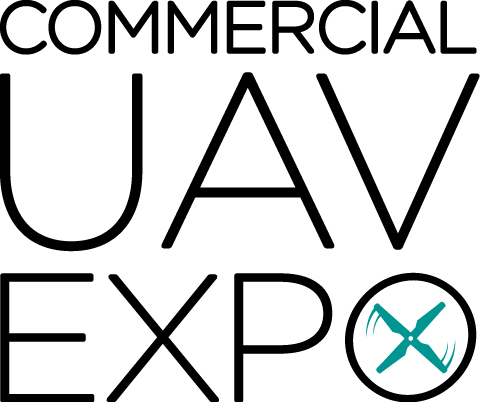
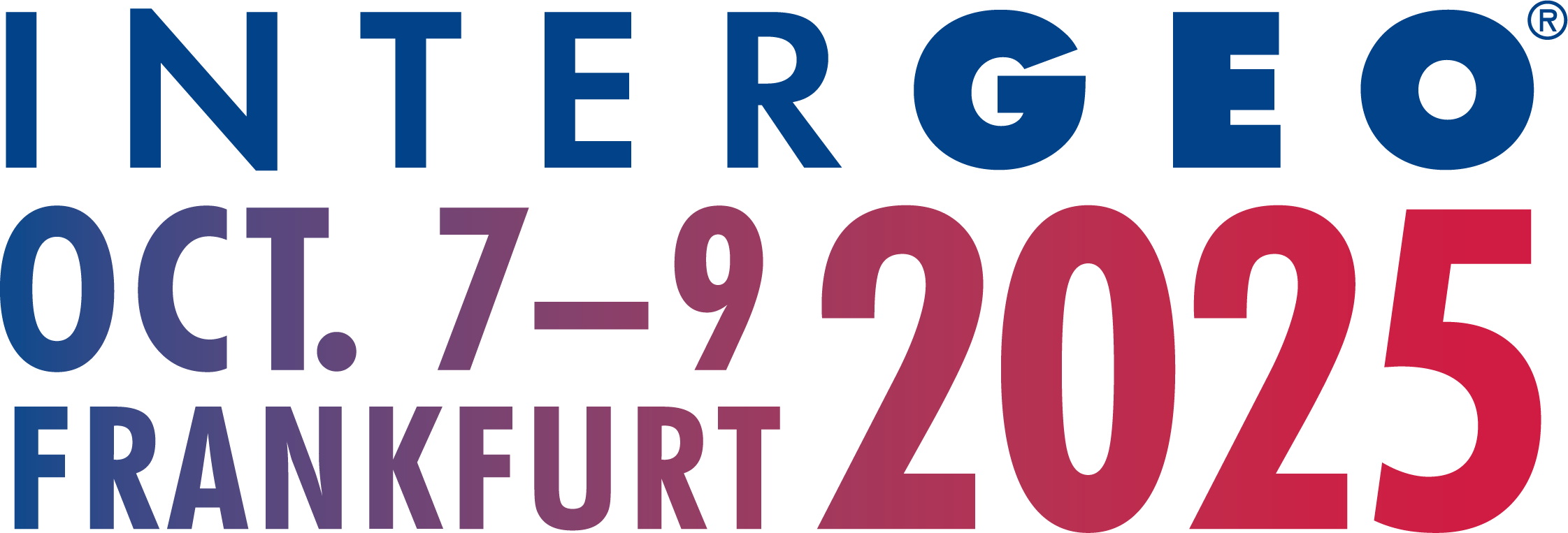
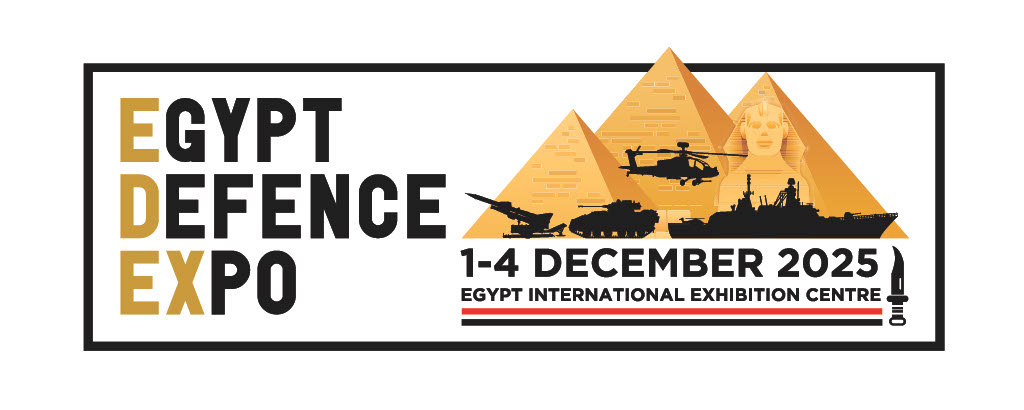
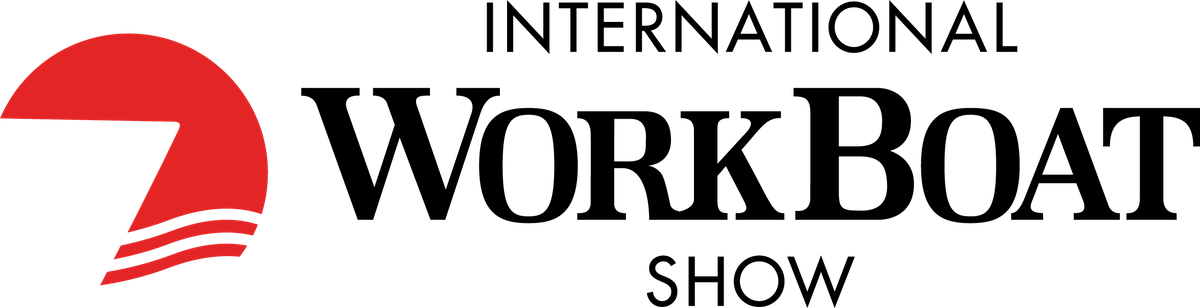
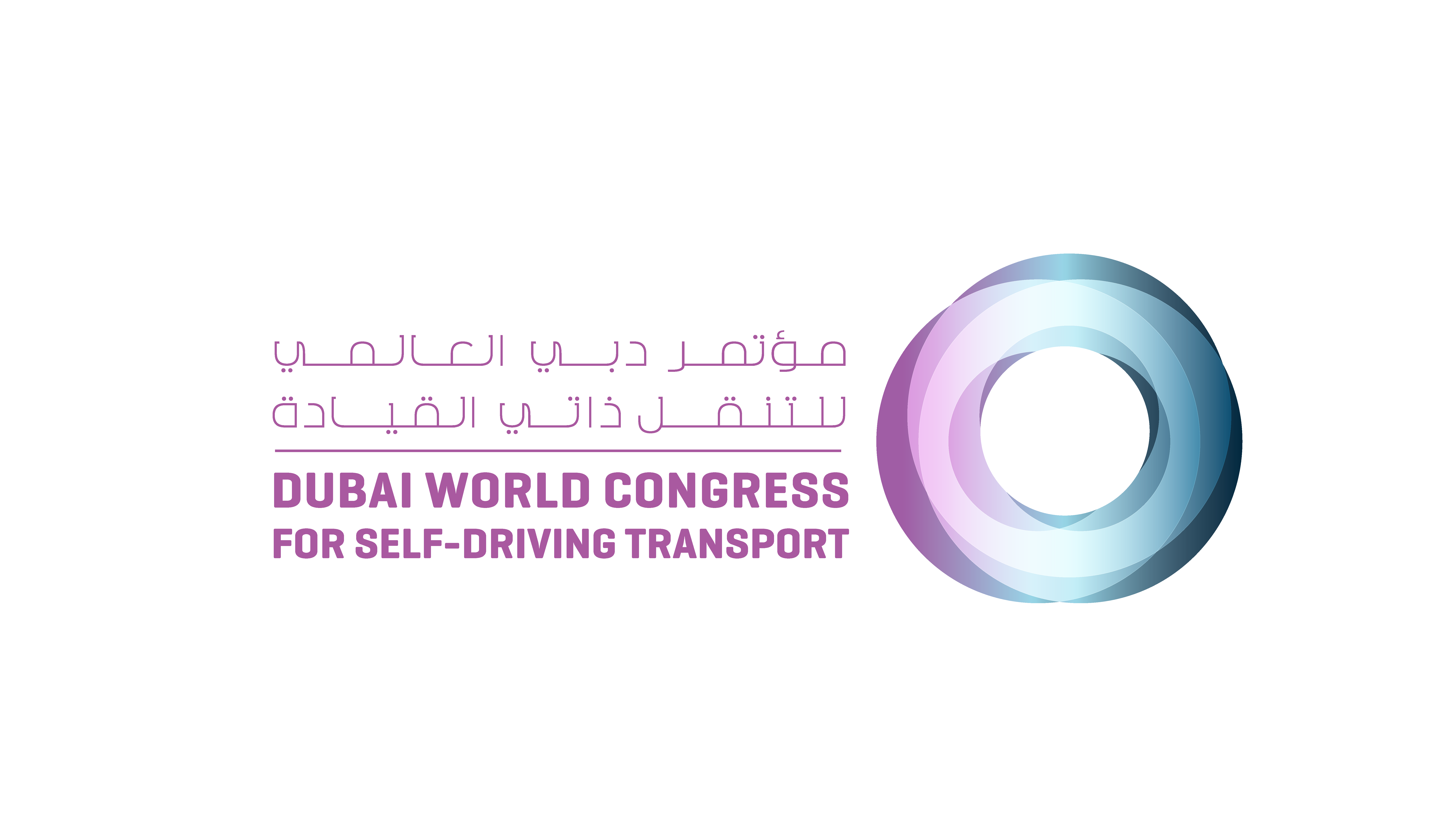
