FIXAR 025
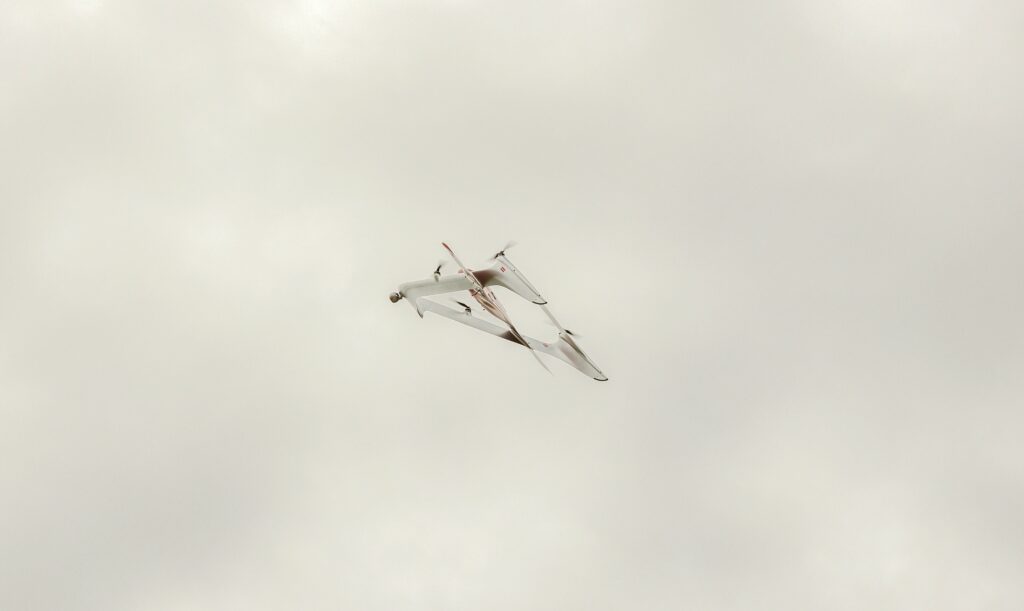
(Images courtesy of FIXAR)
Triangulate this
Rory Jackson investigates this established UAV manufacturer’s new flagship product, engineered with a unique form in pursuit of a fully maximised payload-to-weight ratio
The value of UAVs for mapping and inspection is directly linked to the efficiency with which they carry their sensor payloads. While this has been known for years, it is only recently that advances in modern design capabilities have enabled aerospace engineers to pursue alternatives to conventional aeroplane designs in pursuit of a fully maximised payload-to-weight ratio.
Latvia-headquartered FIXAR-AERO LLC is best known for its 007 UAV product, which resembles a conventional, twin-boom, quadrotor, fixed-wing UAV, but this was only ever intended to trial and introduce the company’s technology into real-world commercial applications.
However, the company’s newest UAV, the FIXAR 025, is the ultimate optimisation of its namesake FIXed Angle Rotor technology. It can simultaneously generate aerodynamic surface-lift forces (as in fixed-wing planes) and vertical-lift force (as in multirotors), and is engineered to maximise payload-carrying efficiency.
Through that technology, the 025 features a VTOL-transitioning capability, but with a rare configuration featuring a closed, triangular wing, wrapped around a blended-wing body.
This configuration maximises aerodynamic and weight efficiency relative to the UAV’s physical footprint (its wingspan is 2800 mm), principally by forgoing landing gear, struts, tiltrotors or servos, which do nothing to specifically generate lift and indeed serve no purpose for 99% of mission time.
It instead lands ‘backwards’ on the corners of its triangular wing, so every part of the craft contributes to producing lift. With the wing closed, this arguably reduces losses at the tips, compared with conventional reduction design techniques, such as adding winglets.
Overall, this gives the 25 kg, fixed-wing UAV a 10 kg payload capacity, as well as an endurance of 3.5 hours and a flight range of 300 km on its standard battery configuration. Additionally, the 025’s compact size means it can be disassembled into two small Pelican cases and transported by a single, small road vehicle.
While both the FIXAR 007 and 025 can VTOL-transition, neither does so quite like other VTOLs (be they tailsitters, tiltrotors or hybrid-quads), which must be exhaustively programmed to safely deal with the hazardous manoeuvring required to go from hovering into forward flight, and vice versa.
Nor do the company’s UAVs use tilting rotors. Instead, their rotors are integrated, such that they bear a non-vertical angle of attack (AoA) when landed or hovering: around 42° relative to the ground, rather than 90°. By angling the fixed rotors between the fully vertical and fully horizontal angles, the work needed by the autopilot and its programmers is minimised to a program that merges traditional quadcopter and aeroplane control system logic.
“It takes a few unique control loops, and some smart use of one’s navigation system, because it’s not a simple matter of switching between a ‘copter mode’ and an ‘aeroplane mode’ – it’s both of those modes combined in different permutations, depending on whether you’re looking at the lower- or higher-level logic,” says Vasilii Fainveits, CEO of FIXAR.
FIXAR started as a UAV engineering services company, carrying out design, development and validation of various systems and subsystems for different manufacturers. Development of the 007 – including its control loops, autopilot and navigation systems – began from a blank sheet in 2018, after Vasilii and his colleagues conceived the FIXAR technology during a customer’s project, thereafter introducing their first prototype for it (the client declined the unusual design and r&d it needed).
“We released that first UAV in 2020, using no open source code; it’s a very unique set of algorithms, not just for our proprietary approach to VTOL-transitioning, but for features like being able to navigate without a magnetometer or compass,” Fainveits says.
Development timeline
The 025’s development targets were steered to form a compromise between what FIXAR’s engineers wanted to accomplish and what customers seemed to want; the latter being uncovered via feedback on usage of the 007.
“That meant the 025’s key operating features, payload capacities, mission-planning interfaces and so on were engineered to directly cover what customers seemed to suggest were shortfalls in what the 7 kg 007 UAV could accomplish with its 60 km battery range, 59 minute flight time and 2 kg payload capacity,” Fainveits says.
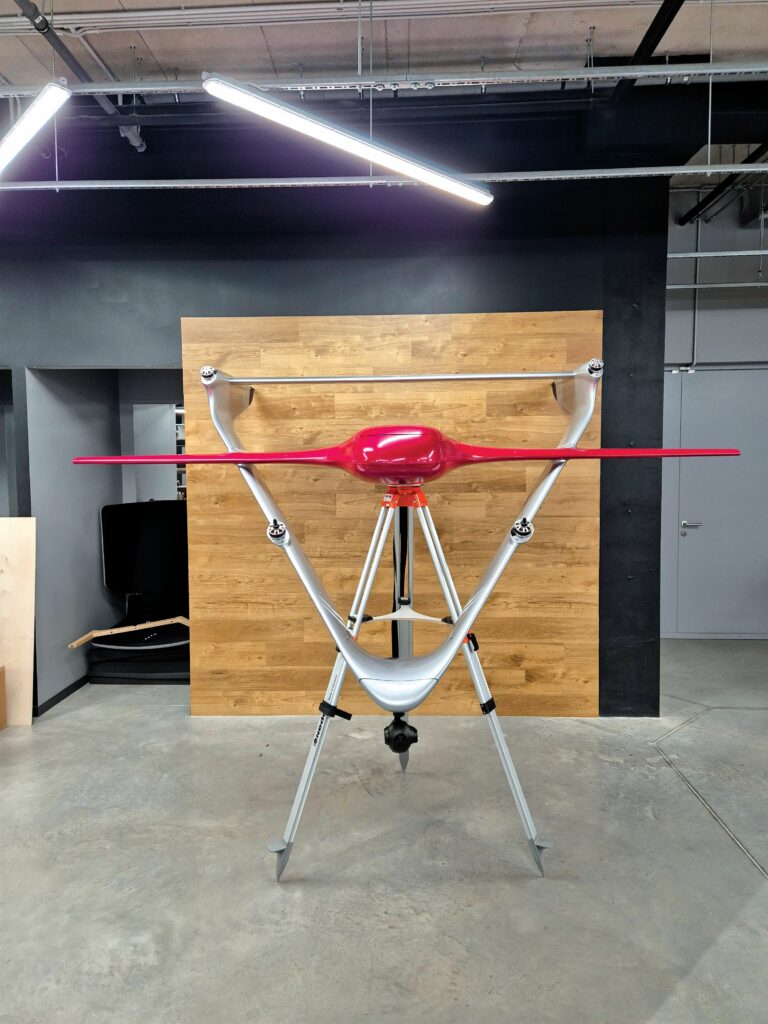
“We also received feedback on the main operational bottlenecks, and understood that the 025 had to be as easy as possible to set up and use, which fed into the design of the UAV, as well as training programmes. So our product engineers had significant freedom to be creative in how they shaped and iterated the 025, so long as they still addressed all these explicit market needs.”
Given that the 007 was always going to be a trial product, meant to inform a better successor, the first design document for the eventual 025 was drawn up immediately after the 007’s release in 2020.
Over the following year, FIXAR filled in that document to completion with feedback information from the 007’s customers, and it built the first scale prototype of the 025 concept over the next six months. Thus, in 2022, the company began flight trials with the first 025 prototype. Fainveits describes this prototype as having roughly the same total wing area as the 007, when both the triangular box wing and the fuselage’s blended wing body are aggregated.
“That meant it was smaller than the 007 in overall size, for both platforms to be equal in their aerodynamic surfaces, and so those trials were a major triggering point in terms of whether we would go with the unusual box-wing configuration or just make a scaled-up version of the 007 if the former architecture wasn’t successful,” Fainveits recounts.
Success, the company decided, meant at least a 15% improvement in efficiency. Hence, as well as controlling for wing area, FIXAR integrated the same batteries, motors, motor controllers, propellers and payload weight into the scale prototype as in the 007.
The scale prototype then flew roughly 12 minutes longer than the 007 (22% more flight time on the same powertrain and aero area), validating that the 025 design concept was significantly more aerodynamically efficient than the more conventionally designed 007.
“With the design validated, we then had to make a scale prototype, not just to validate full-scale performance but also to finalise our construction moulds,” Fainveits says.
“We build our production units using a wet lay-out composite technology in aluminium moulds. It’s quite expensive to produce the moulds with the correct shape and size, and really expensive to get them wrong, so while the common instinct in aerospace engineering is to always go as big as possible, because ‘bigger is better’, we had to remember that usability – and hence transportability – were important to our customers.”
To finalise the dimensions of the 025 and hence its construction moulds, FIXAR ran numbers to measure different UAV sizes and their associated revenues derived from expected mission-data gathering against the transport costs that could ensue for each aircraft size.
“There’s standard crate and pallet sizes used in transportation. By judging against the cost of using and moving those, we arrived at our wingspan of 2.8 m. But it would still have been risky to dive right into cutting moulds for a 2.8 m-wingspan aircraft, so we made another scale prototype with a 1 m wingspan and built from plastic moulds,” Fainveits says.
“By flight-testing that model, we saw several areas where the shape of the aircraft, and hence the moulds, needed to be adjusted. That’s been a running theme of our development, because we’re not dealing with traditional, 2D aerodynamics, where you have a wing with a top shell and bottom shell, and that’s all. We have a V-shaped nose, and a bunch of wings and angles all around that.
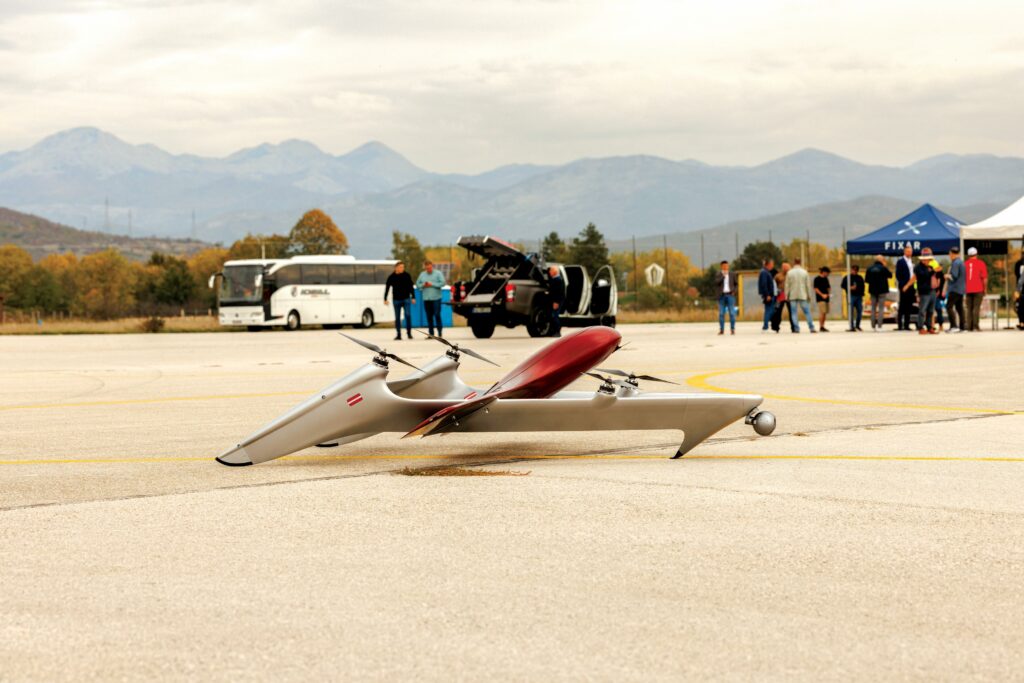
“Doing that 1 m wingspan prototype as an intermediary r&d step was incredibly valuable to subsequently getting the full-scale 025 and its aluminium moulds right. We validated that we’d achieved that via 500 hours of flight testing before introducing it to the market in October 2024 – something we’d also done with the 007 before releasing it.”
A point for every part
Such were the importance of payload and mission efficiency to the engineering of the 025 that its developers designed it with multiple payload hard points to ease the work of fitting 10 kg worth of sensors and other mission devices onboard.
“The nose and the bottom forward-most part of the triangular box wing are two of the primary payload-mounting points, from which cameras can get unobstructed views of terrain and surroundings without any part of the airframe interfering with their visual line of sight [VLOS],” Fainveits says.
“So, gimballed cameras, mapping cameras and multispectral cameras get installed at the nose, though gimballed cameras can also be installed behind the nose, and additional EO cameras can be installed inside the bottom corner of the box wing.”
A Lidar sensor typically weighing 7 kg is installed as standard in the lower rear of the fuselage to provide a 3D terrain-mapping and modelling function, and power the craft’s autonomous perception and obstacle avoidance (discussed below).
Additional mapping cameras can be installed between the nose and Lidar in the central part of the fuselage undercarriage. The UAV thus carries multiple different payload sensors per flight, enabling mapping, surveillance, laser scanning and, potentially, deliveries to take place concurrently within individual operations.
The 025’s batteries are mounted at the CoG, behind the nose. The autopilot, including the UAV’s two IMUs, sits very close by in the central part of the fuselage (to ensure the IMUs are as close to the CoG as possible for accurate inertial readings), placed directly under a top hatch for ease of access during maintenance.
The motor controllers are installed in the lower left and lower right bottom of the fuselage, with radiators for easy cooling via the air rush under the fuselage’s wings. These placements also enable unobstructed connection to the four motors: one sits at each of the box wing’s two upper corners, with the other two integrated roughly two-thirds of the way down the lower sides.
“The last important part is our communications set-up, because you can buy the best radio in the world and get nothing out of it if your antenna set-up is wrong,” Fainveits says. “You need both good quality and good placement of your antennas. So we install our comms antennas for C2 and payload data streaming under the fuselage, pointing downwards at an angle, while the GNSS antennas point upwards at an angle.”
Composite matters
These subsystems integrate across a body largely made from external fairings of fibreglass-Kevlar composite, sandwiching Herex honeycomb foam in places for an increased strength-to-weight ratio.
“We previously made the 007 mostly from carbon-Kevlar, but we found, through some users’ work in ISR that carbon may be too reflective for defence work – it’s very easily detected by any radio wave-based technology – so the 025 is fully radio-transparent,” Fainveits explains. “There’s some minimal use of carbon tubes, but not enough to present a significant radar signature.”
The composite and Herex honeycomb combination was key to achieving FIXAR’s weight goals (not exceeding 25 kg for regulatory approval) without sacrificing structural strength.
Before entering series production, the company built eight full-size 025 units, each made using a different supplier’s composites and manufacturing methods. These were then bench-tested for mechanical load handling by methods such as installing masses across their wings and bodies to analyse for wing flexing, vibration and similar undesirable properties.
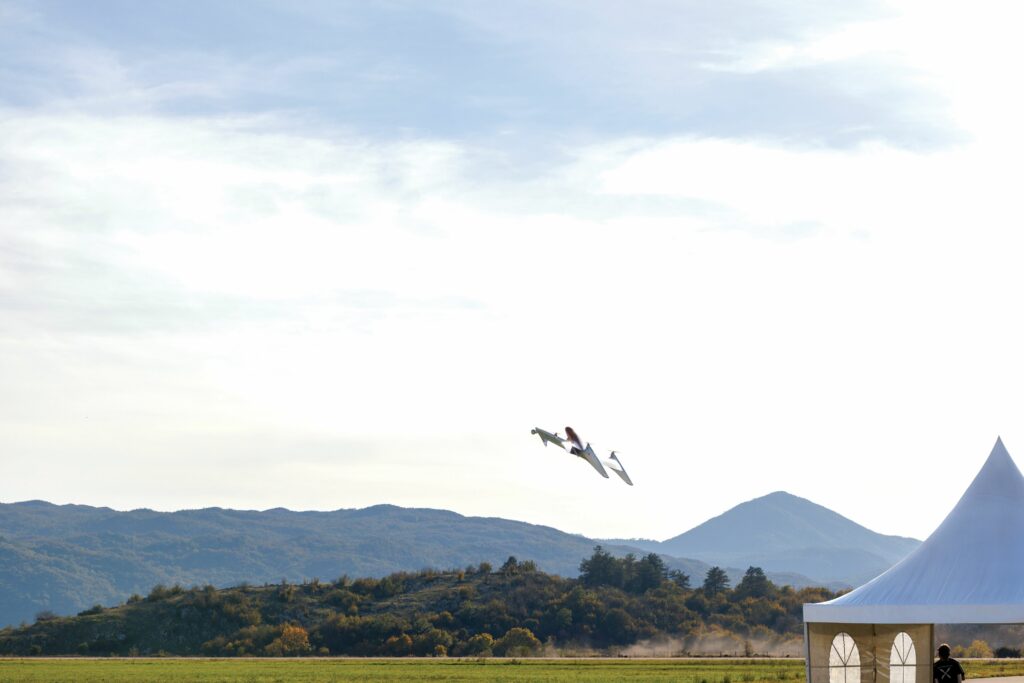
“From those results, we shortlisted the best three units, flight-tested them, and the one that performed the best became the unit which we put into series production,” Fainveits says.
“Its materials come from companies in Germany and the Czech Republic who we can’t name. That’s a trade secret for now, given how much time and work went into finding the best materials, as is the glue used for bonding the composite fairings together, since it was a real struggle finding one that gave the best balance between strength and flexibility, allowing the body to bend just a little bit to distribute the heavier loads.
“But we’ve historically found the best-quality materials come from Germany, with the Czech suppliers’ quality arguably becoming even better now. We also tested some Chinese materials, and while their prices were great, we found the quality wasn’t quite there yet.”
Optimising aerodynamics
Most of the modelling and simulations for informing the first scale prototype were performed in Matlab Simulink, particularly to enable FIXAR’s preferred hardware in-the-loop approach for developing the software logic and aerodynamics in tandem with one another.
These tasks were implemented in collaboration with the Riga Technical University, to which FIXAR is partnered. The company then advanced to wind-tunnel tests (at its labs) to develop and optimise the built models’ designs.
“We didn’t use Simulink at all during the practical development phases; everything there was established, traditional methodology, like analysing smoke movements around the scale model in the wind tunnel to optimise aerodynamics, and we also used such approaches to calibrate the airspeed sensors,” Fainveits says.
“We also built some specialised, automated test stands with tension sensors and servo motors to estimate the optimal AoA at which the rotors ought to be angled for this aircraft. From those, we measured lift and drag forces, with the servos changing the angles of the propulsion sets to see how each angle might change the aerodynamic efficiency.”
Given the plethora of payload hard points across the 025’s airframe, one of the biggest challenges in making the 025 function effectively was ensuring that, no matter the selection and arrangement of payloads integrated, the aircraft would fly with a consistent level of stability and hence controllability.
“Combining a closed wing of this shape with a conventional, blended wing body isn’t something we’ve seen anyone else do, so we’ve been dealing with an unusual set of 3D aerodynamics and hence a CoG that moves in all dimensions: move a payload to the nose and you move the CoG, while also creating a lever arm that generates instability in roll and pitch,” Fainveits says.
“Putting weight on the nose essentially means we need to put weight somewhere else higher up to make it easier for the autopilot and rotors to compensate. Fortunately, we wanted to target multi-mission applications from the outset, which meant we wanted to carry multiple payloads simultaneously; hence the many different integration hard points discussed earlier.”
There remained, however, many variables to account for across different missions, payload integration profiles and flight stages. For instance, the wing AoA is different during hover and horizontal flight, which means the CoG moves forwards when transitioning from takeoff into forward flight or into hovering (position hold) mode, thus increasing the frontal load to the front propulsion set.
“It was a huge challenge combining mechanical and software engineering to make sure the autopilot could account for those movements, and accordingly change the differential thrust across the rotors to maintain flight stability,” Fainveits says.
“We started with a simplified mathematical model of how the CoG might change throughout flight stages and different mission subsystem setups, which acted as a first stage towards calculating where the CoG was, and how it changed with more and more accuracy over our development time.”
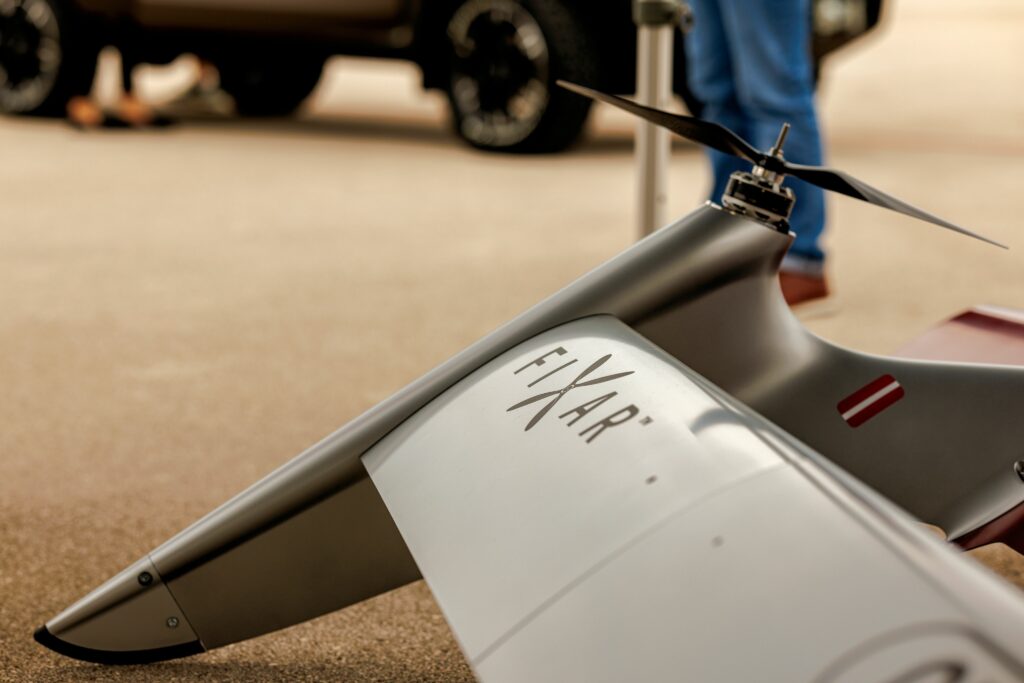
The overall result is that the 025’s software bears hugely different control loops to those of the 007, with the company describing the new flagship product’s consistent functionality – regardless of payload integrations differing (within reason) between missions – as “adaptive autonomy”.
Adaptive autonomy
The 025’s proprietary autopilot computer is built around an STM32 H7-series CPU, powered by an ARM Cortex-M7 chip at its core.
For navigation inputs, the 025 uses a u-blox GNSS receiver as standard, particularly the Swiss company’s F8N, or F9P, the former being reportedly the more accurate of the two, although the latter has the advantage in redundancy (and may be more certifiable). However, FIXAR will integrate most other suppliers’ GNSS products if customers have a preference, as this is increasingly happening in the uncrewed space.
The two IMUs installed with the autopilot are MEMS devices: one is an MTi-series system from XSens and the other is an MPU-series IMU from TDK InvenSense.
“The former is very high performance with very minimal drift; the latter isn’t so high performance and it drifts a little, but it’s very fast, so in essence the two cover each other’s weaknesses, and make for good state estimation algorithms and redundancy for navigation in flight together,” Fainveits says.
“Thanks to those estimation algorithms, the system can be GNSS-denied, and still remain capable of controlled flights and of completing most missions. We have also tested VectorNav’s inertial solutions and they present promising results, but we’d just need some further customisation and adjustments first.”
Those state estimation algorithms, as well as the 025’s aforementioned software-control loops, are key to how the UAV automatically senses and adjusts its control behaviours to account for changes in weight distribution – and hence changes in the CoG – derived from individual users’ different payload arrangements and changes in aircraft orientation during flight.
As Fainveits explains: “Having those adaptive characteristics is vital for going from ‘automatic’ to truly autonomous flight. Say, for example, you have a multicopter working in a delivery application carrying a parcel for someone as its payload, and it is controlled by some off-the-shelf autopilot running Pixhawk control software.
“When it’s carrying its package it has one specific PID [proportional-integral-derivative] controller setup; when it drops off its payload it must be triggered to shift into a different PID setup to account for the changes in weight, CoG and centre of balance.
“That’s a bottleneck of automated UAVs versus autonomous UAVs. If you don’t trigger that specific PID setup after the change in the CoG, then the UAV won’t be stabilising itself correctly and won’t fly safely. But, with the FIXAR 025, you put on your payloads, plan your mission waypoints and the system automatically adapts how it controls itself, with very quick reaction times to inertial data coming in at every flight stage.”
Payload integration itself takes some mechanical, electrical and software integration, including bridging PWM, TTL or UDP logic control between payloads and the autopilot, as well as API-to-API management (TTL, PWM and UDP is installed in the autopilot by default). This can take significant back-and-forth between FIXAR and payload vendors. Fainveits recalls one instance where a camera meant for gimbal pointing and target tracking repeatedly calculated targets’ coordinates incorrectly.
He recounts: “In summary, that happened because the camera was a two-axis system, trying to operate in a 3D mission. Fixing that is simple maths: ‘multiply it to the tangents of this angle’, we essentially said to the vendor. They did that, sent back an improved version, we tested it and found issues we didn’t catch the first time, they made fixes for it, and after two months we got the camera working nicely.
“But it hugely comes down to whether the vendor responds in good time, and is willing to either implement our changes, or let us make changes ourselves.”
Lidar
One more important feature, which brings autonomy, is the real-time surface-tracking system and autonomous altitude adjustment to the MOCA (minimal obstacles clearance altitude). As mentioned, a Lidar is installed under the fuselage to further the autonomy of the 025. The 3D Lidar measures terrain and objects below and around the airframe. One function of this system is to track the yaw and roll of the aircraft to aid the inertial sensors’ own measurements in informing the adaptive autonomy algorithms.
Its more important function, says Fainveits, is to track for surface objects such as trees and buildings ahead to undertake obstacle avoidance manoeuvres. BVLOS surveys of regions not recently or previously mapped will especially need such intelligent reactivity to avoid controlled flights into structures, trees or terrain, in the absence of pre-existing 3D map data to use during mission planning (FIXAR has been previously instructed that such information is not always available in a useable digital format).
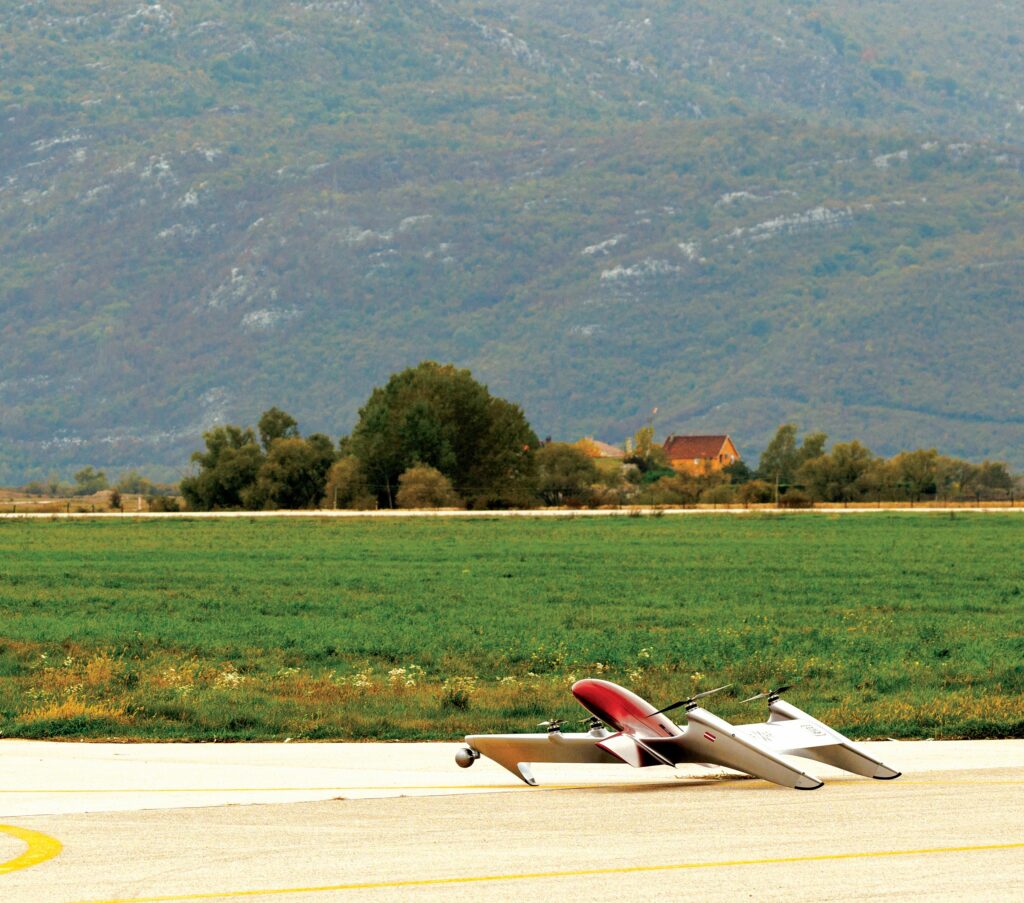
The Lidar sensor used for adaptive autonomy comes from LightWare LiDAR. Key factors for its selection include supply chain security and resilience, and more importantly, highly accurate and detailed measurements amid interference stemming from environmental factors.
FIXAR says the laser scanners of RIEGL, YellowScan and TopoDrone are used for laser scanning and mapping missions to generate 3D point clouds after some software processing. All onboard Lidar systems are installed in a way that maximises the width FoV, meaning close to zero occlusions from the body or airframe.
“As you know, the Latvian climate is very prone to snowy winters, and much of what we do is close to or over the shores of the Baltic Sea, which means it’s easy for us to test how optic-type sensors perform in environments where there’s a lot of reflections going on,” Feinveits says.
“When we speak about the most critical sensors, which are Lidar sensors, we put much attention to real conditions and operations of them. We tested many optical sensors and systems to see how they work in such winters. No-one should be building an uncrewed system that only works in good weather after all. So, we can confirm that LightWare’s Lidar still works very accurately in wintry conditions, and measures distance rather well in poor conditions too.”
Ground control
When 3D map data is available or can be estimated (including via 3D maps that FIXAR can create and host for users on its own server), it is visualised pre-mission in FIXAR’s XGround Control GCS software.
This is a proprietary, closed-source program, designed specifically to build, edit and operate flight missions for the 007 and 025 UAVs, and monitor them in real time.
Given the 3D nature of the 025’s control regime, 3D visualisation of mission areas was a key requirement in the GCS program’s development. The software is designed to pre-cache all 3D terrain data it is given access to, such that it can provide for planning waypoints in latitude, longitude and altitude without needing an internet connection.
“We have worked hard on making it easy to use. We’ve endeavoured to make it easier than most commercially available GCS solutions, and to be honest, a lot of that comes from having designed it only for FIXAR UAVs,” Fainveits says.
“Any GCS software meant as a universal tool for managing all sorts of different UAV models is naturally going to become complicated to make and use, because it needs to support a wide range of different platforms and hardware. With our system, a mission can be planned and started in less than two minutes, and with just nine mouse clicks.”
To further ease of use, the software can work on a wide range of operating systems, including Windows, iOS and MacOS, and others based on request.
Powertrain
A 54,000 mAh battery pack from Gens Ace in Germany provides the craft’s energy, and it is available either as a 50 V 12S2P configuration or four batteries split as per a 12S2P configuration (in some cases, the latter helps improve the CoG, payload placements and payload integrations). Upgrades to enable 60,000 mAh batteries are also in the works.
The four standard motors come from KDE Direct, chosen for their quality and performance relative to price, as well as a fast shipment time. Collectively, they provide a maximum thrust of just over 8 kW, with a combined average of 400-600 W in the UAV’s cruising speed (100-150 W per motor), and 2 kW in hovering mode and position hold, while 3.5 kW is typical for take-off power.
“The 025’s top airspeed before what could be called ‘self-disassembly’ is about 122 kph, but the autopilot will adaptively choose a speed that optimises energy efficiency for the sake of mission endurance, as well as safety, keeping in mind that the target cruise speed for survey and surveillance – including ISR – may be different,” Fainveits says.
“Many additional factors define the target cruising speed: the weight, type and number of payload, and the optical characteristics of the payload sensors, for example.
“Most often, it calculates 50-55 kph as the most effective speed, but it also dynamically changes that speed as it tracks its own energy consumption, and the optical sensors speed to avoid blurring, and it certainly won’t let users deliberately choose unsafe velocities.”
The seeming complexity of the control architecture is offset somewhat by the lack of servos to control. Altitude changes are achieved solely through differential rotor thrusting (the lack of servos also reduces maintenance costs, given that servos are one of the most frequently replaced UAV components).
KDE also provides the craft’s motor controllers, which eases integration with the motors. Propellers for the 025 are also supplied by KDE for now, although this may change in the future as FIXAR has designed a new propeller optimised for aerodynamic efficiency in the UAV’s angled-rotor flight and thrust, based on real-world testing data.
FIXAR plans to manufacture this new propeller in-house, and it anticipates that it will yield 20-25% greater efficiency and hence 40-50 minutes more flight time.
Communications
In pursuit of high-quality, cost-effective communications, FIXAR has chosen DTC as the sole supplier of all its data-link radios and most antennas (with some ground-based directional antennas coming from other suppliers such as PIDSO).
As well as the Australian company’s radios providing consistent latency and bandwidth, FIXAR reports agility and flexibility in DTC’s customer support and response; a critical aid given the challenge of integrating systems to work effectively in the 025’s 3D control regime (given wave polarisation, and what it means for how connection strength changes with banking and pitching).
“Radios are still a matter of customer choice, as each use-case will have different distances and terrains that their data link or mesh network needs to deal with, but DTC provides many different options for different ranges and prices,” Fainveits says.
“Transponders are, similarly, something we can install based on customer needs. We’re a global company now, so any number of transponder suppliers and protocols are fine by us. That can include DroneTag, beacons, ADS-B and so on.”
World future
With FIXAR satisfied that its aerospace technology has reached a key pinnacle in the 025 – one that can be scaled up or down to meet market demands on cost, payload capacity, endurance or transportability – its future plans for scaling up its business include licensing the production of UAVs to third parties.
This will include technology transfer to other countries, although partners will be responsible for their own payload integrations given the importance of quick turnaround in collaborating with vendors and fulfilling customer requests.
“That means partners can manufacture FIXAR UAVs locally, rather than us shipping them out. We’ve introduced this with one company in India already, with another in South Korea to follow, and we plan on both working with existing centres of excellence and helping create new ones, with models based on sharing revenues and scientific expertise,” Fainveits says.
“Licensing our technology will also mean building 3D map servers in partners’ countries to give functional safety and security in their customers’ ability to operate, and a degree of accountability and hence reliability that one can’t get when relying on open-source tech.”
In addition to partners in India and South Korea, FIXAR is working towards partnership agreements on manufacturing and r&d in Portugal (with environmental institutes and the University of Coimbra there). It has also signed an agreement with the Center of excellence for Unmanned Aerial Vehicle Research, Development and Education in Accra, Ghana, which is held as one of Africa’s foremost centres of UAV competency, through which FIXAR UAVs have already begun flying on behalf of companies and government ministries across Africa.
“Training and maintenance are already provided through that centre, customised and adapted for the expectations of African customers,” Fainveits says.
“They plan to become the leading centre of UAV excellence in Africa, and they’re led by Kofi Owusu-Adusei, who has founded and runs multiple UAV r&d and services companies. The UAV world needs people like him, so we’re very excited for what 2025 has in store for FIXAR and the industry as a whole.”
Key specifications
FIXAR 025
UAV
Blended wing body with additional, closed triangular wing
Battery-electric
Wingspan: 2800 mm
MTOW: 25 kg
Payload capacity: 10 kg
Maximum cruising speed: 85 kph
Operating speed: 50-55 kph
Endurance: 3.5 hours
Maximum flight distance: 300 km
Operating ceiling: 6000 m AMSL
Some key suppliers
GNSS: u-blox
Inertial systems: Xsens (subsidiary of Movella)
Inertial systems: TDK InvenSense
Cameras: Sony
Lidars: LightWare
Lidars: YellowScan
Lidars: RIEGL
Lidars: TopoDrone
Electric motors: KDE Direct
Radios: DTC
Antennas: PIDSO
UPCOMING EVENTS
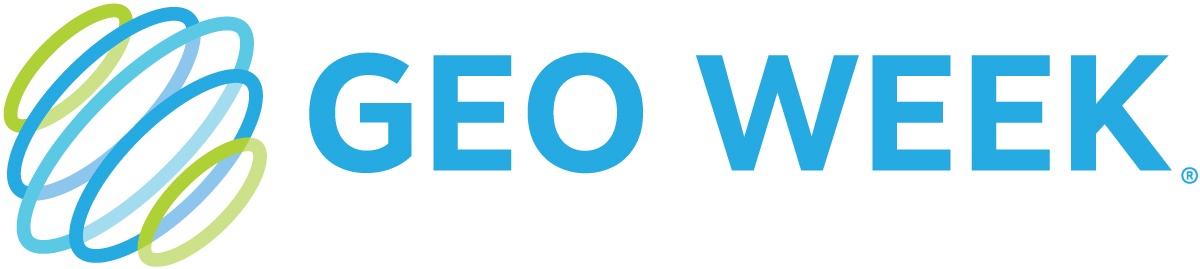
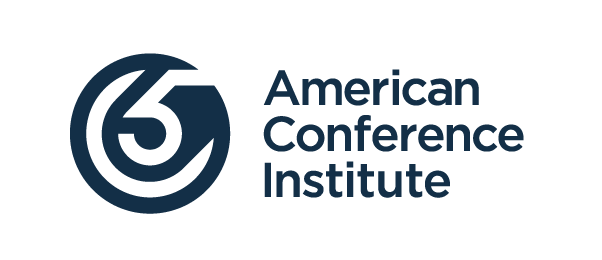
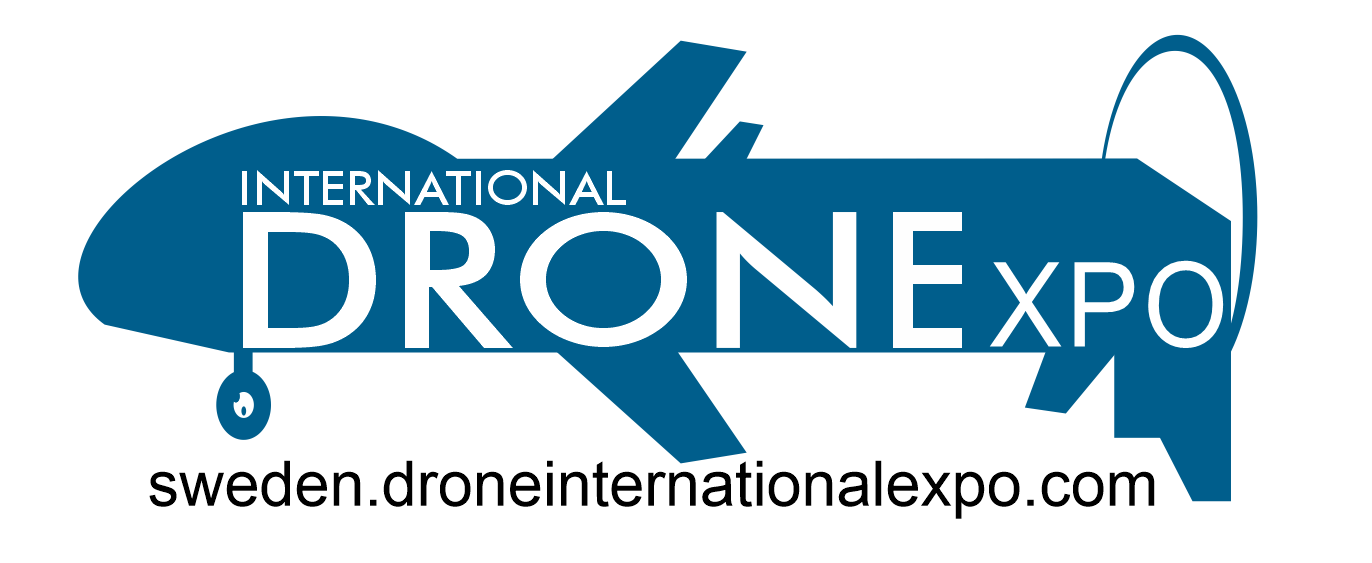
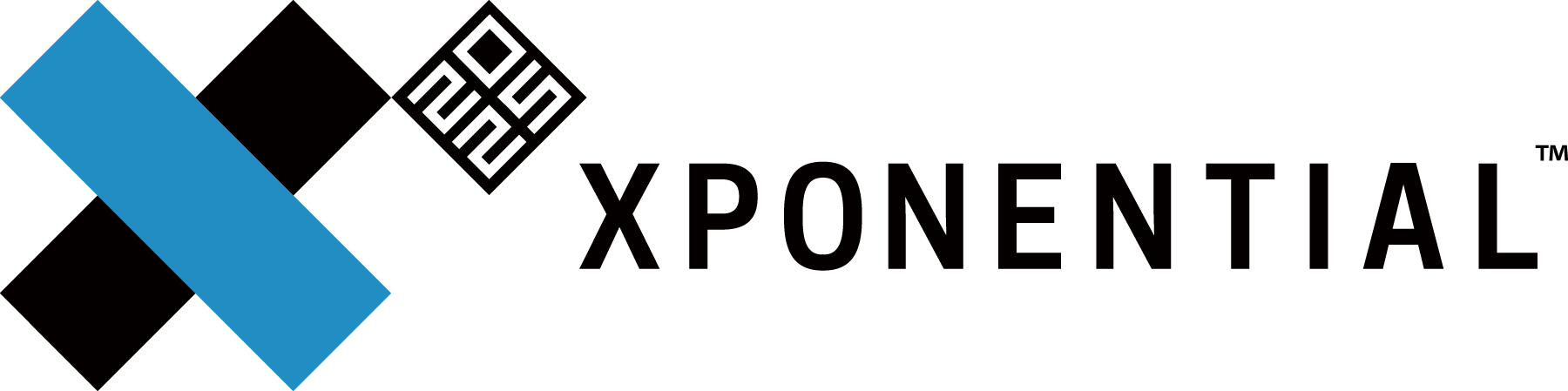
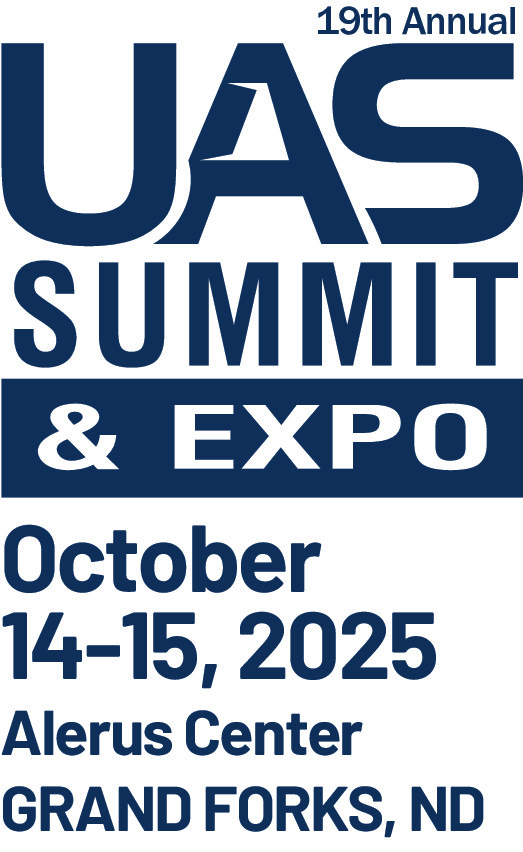

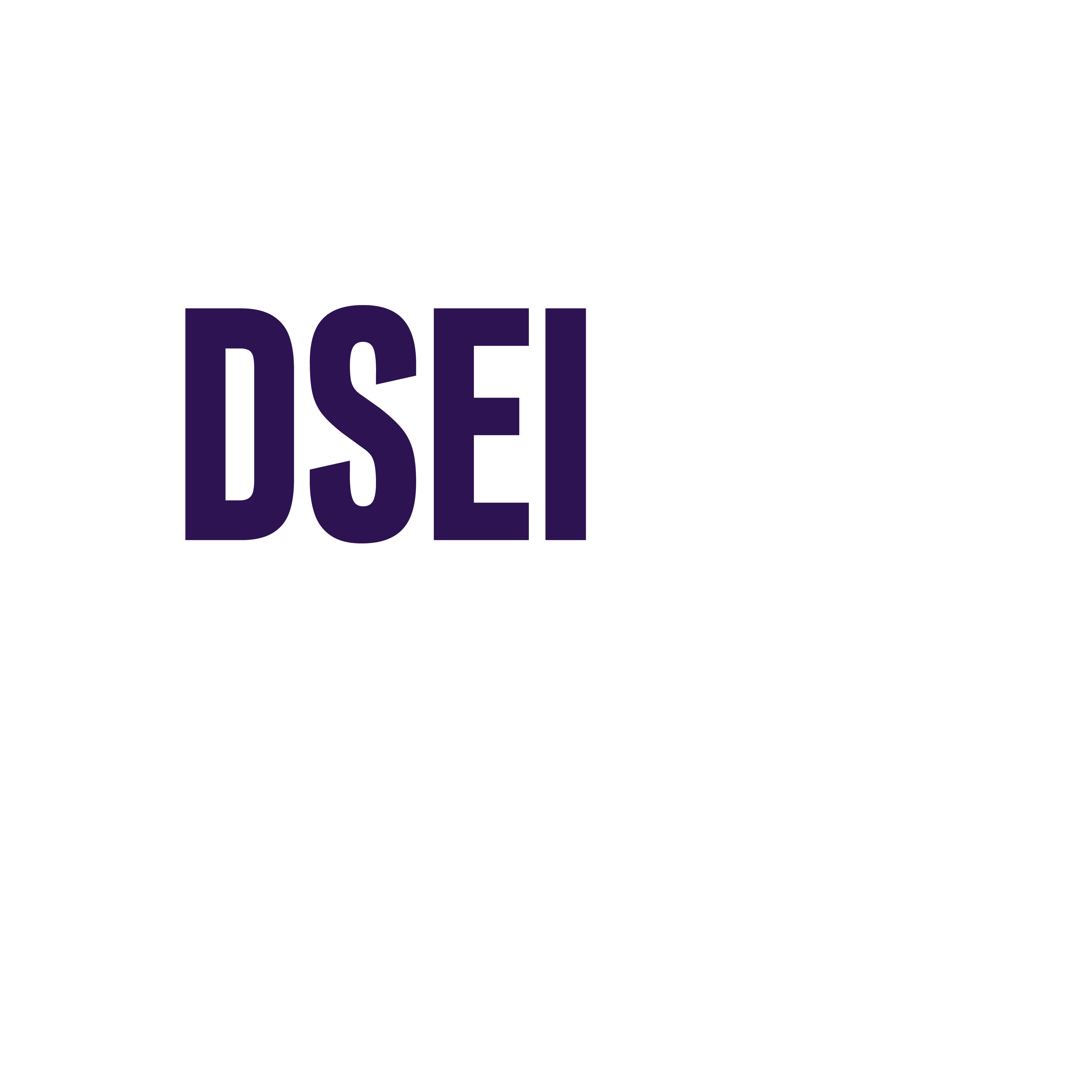
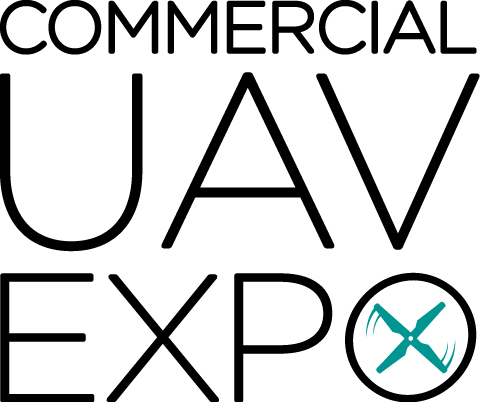
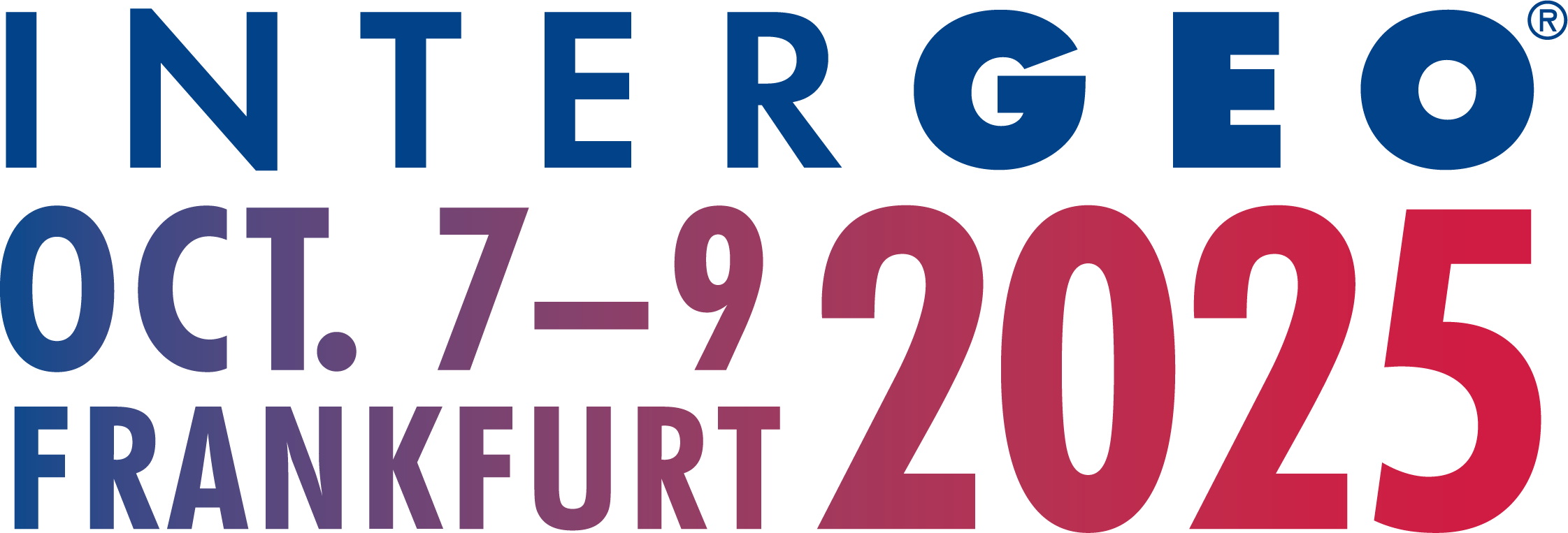
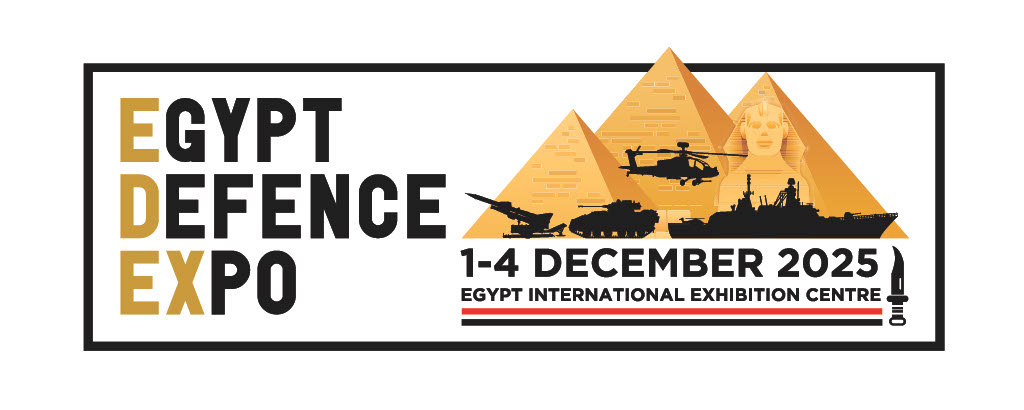
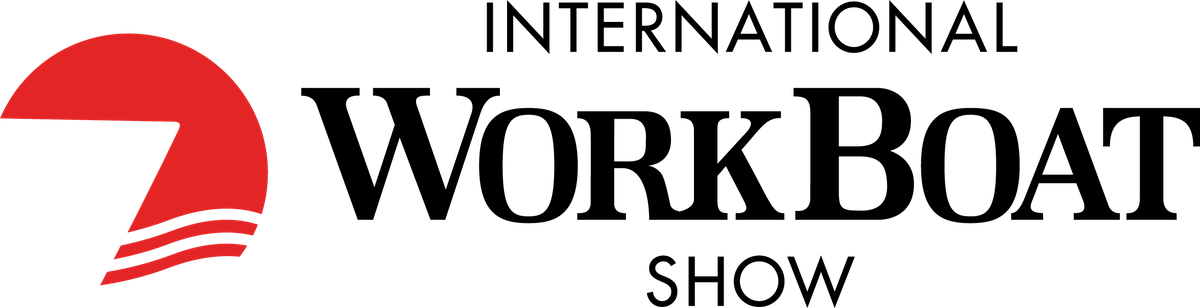