Ocean Business 2023
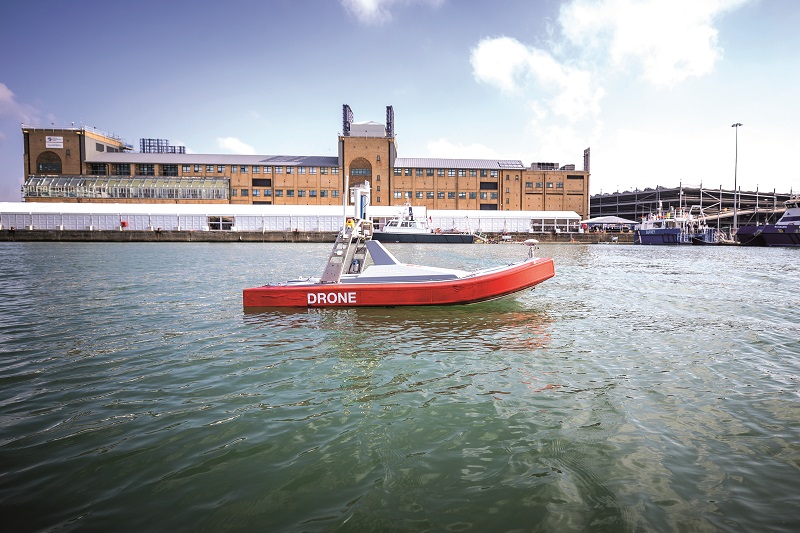
Rory Jackson reports from this maritime engineering exhibition and finds that the tide of autonomy is in full flood
Latest launches
In April 2023, ocean science and engineering experts from around the world converged in Southampton, England, for the largest edition yet of the Ocean Business exhibition and conference.
More than 5000 attendees from over 80 countries gathered at the National Oceanography Centre (NOC) for 3 days of innovations showcased by its 300 exhibitors, with new product launches and quayside demonstrations revealing the ongoing advances in maritime survey engineering.
These demos and unveilings were dominated by uncrewed systems, with marine autonomy taking centre stage for revolutionising the efficiency and safety of offshore infrastructure inspections, ocean mapping and other applications critical to maritime industry. We attended the show to witness the most important launches, a selection of which we present here.
Marine AI showcased the eighth and newest version of its Guardian AI suite of maritime control and autonomy software solutions.
“Guardian AI has three different levels,” explained Matthew Ratsey. “The first is Guardian Vision, which offers a computer vision solution, then there’s Guardian Crewed, which takes whatever level of sensors customers want – be it a camera, radar, AIS or others – and uses the information from them to offer smart recommendations to aid the boat operator.
“The third, Guardian Autonomy, implements those actions rather than just recommending them, on the basis of object detection, identification and analysis, as well as real-time risk assessment.”
Version 8 is set to bring new enhancements to Guardian AI’s sensor fusion layer, to further improve the intelligence and safety of USVs using the solution beyond the sometimes limited or vague definitions of COLREGs – particularly in edge cases such as when multiple vessels are detected within range, and the autonomous ship must simulate, select and navigate a safe path through them.
Ratsey noted that the version of Marine AI integrated on the Mayflower Autonomous Ship (issue 42, February/March 2022) was version 2.
He added that Marine AI can also integrate newer sensor types such as HD radars or Lidars, as well as interfacing with other onboard systems such as the engine throttle, where required.
EvoLogics’ Sonobot 5 USV (featured in issue 37, April/May 2021) is a tool for autonomous wide-area hydrographic surveys for use by groups including the police services to locate objects such as crashed cars or bicycles at the bottom of lakes through multi-beam sonar scanning.
To further advance the USV’s capabilities in acoustic surveys, EvoLogics has updated and re-released the Sonobot 5 (albeit with the same numbering) with a payload styled as ‘the EvoLogics echosounder powered by Norbit’, as the system is a multi-beam sonar integrating OEM boards, software and other components from Norbit.
As Dr Ilja Lange, head of underwater robotics development at EvoLogics told us, “It’s the smallest USV available with an integrated Norbit sonar. To develop it, we integrated their sonar interface unit in an OEM format, so without its typical housing but still with its Applanix IMU and I/Os as standard, into a watertight housing of our own that sits below the waterline, undisturbed by waves and cooled by the surrounding water.”
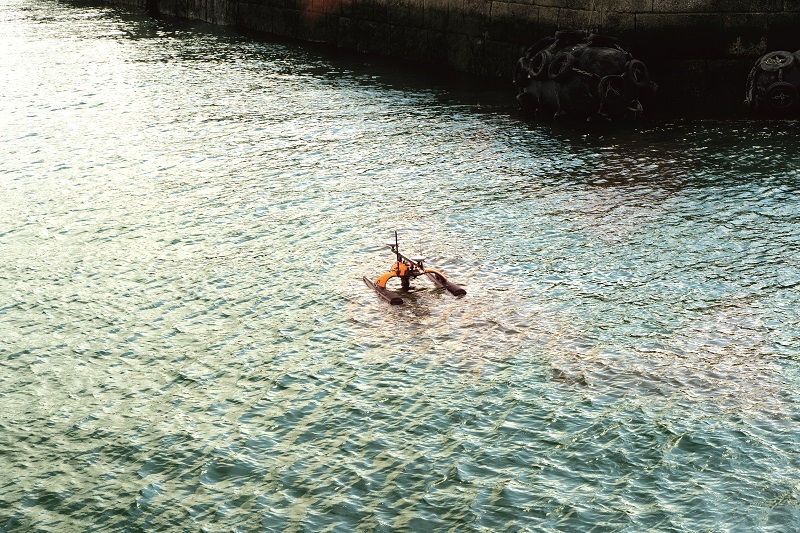
The payload housing attaches with a single cable and quick mechanical release for ease of maintenance and disassembly. In future, as Norbit plans to use a common interface for all its devices, other Norbit sonars could potentially be quickly installed onto the Sonobot using this mechanism.
Norbit’s DCT (Data Collection Tool) software is also installed on the Sonobot. This takes the survey data being collected and stored onboard and broadcasts key parts of it to the operator’s GCS, whether it is running EvoLogics’ software or Norbit’s.
“We see a wide spread of users being interested in this integration, because especially in Northern Europe and some areas of the south it’s becoming nearly mandatory to use multi-beam sonars,” Dr Lange said. “That’s because full seabed coverage is increasingly requested from surveyors, and you can’t achieve that anywhere near as easily with a single-beam or sidescan sonar.
“And although the weight of the sonar takes a bit away from the speed, without it the Sonobot is still the fastest survey USV out there, at 5 m/s top speed, which can be a critical asset for police, intelligence or defence work if you need to perform surveillance and then quickly escape an area.”
SubCtech was on hand to discuss one of the newest applications for its underwater battery technology, principally when stationary.
“We are providing a 2 MWh battery lithium-ion back-up system for an offshore subsea production system, at about 1500 m depth, with a total of up to 6 MWh potentially to be deployed there,” Soren Johannsen told us.
“The system, the 1 MWh Power Skid, contains 12 super-duplex steel canisters, each consisting of 14 SmartPowerBlocks [SPBs] that are also used in AUVs and other autonomous vehicles.
“It will be the first of its kind to come with full API17F and DNV certification, and it will be deployed later this year to achieve TRL6.”
Once the system is deployed, it is expected to be used with docking stations for AUVs to interface and charge themselves from the stationary batteries while running inspections of subsea facilities and infrastructure.
Each 7 kWh SBP can operate at temperatures from -20 to +60 oC, and can be housed in titanium to enable lifetime operations at 6000 m depths. 18650 cylindrical lithium-ion cells are used inside each module, chosen for their safety and are tested to UN- and Mil-Spec standards.
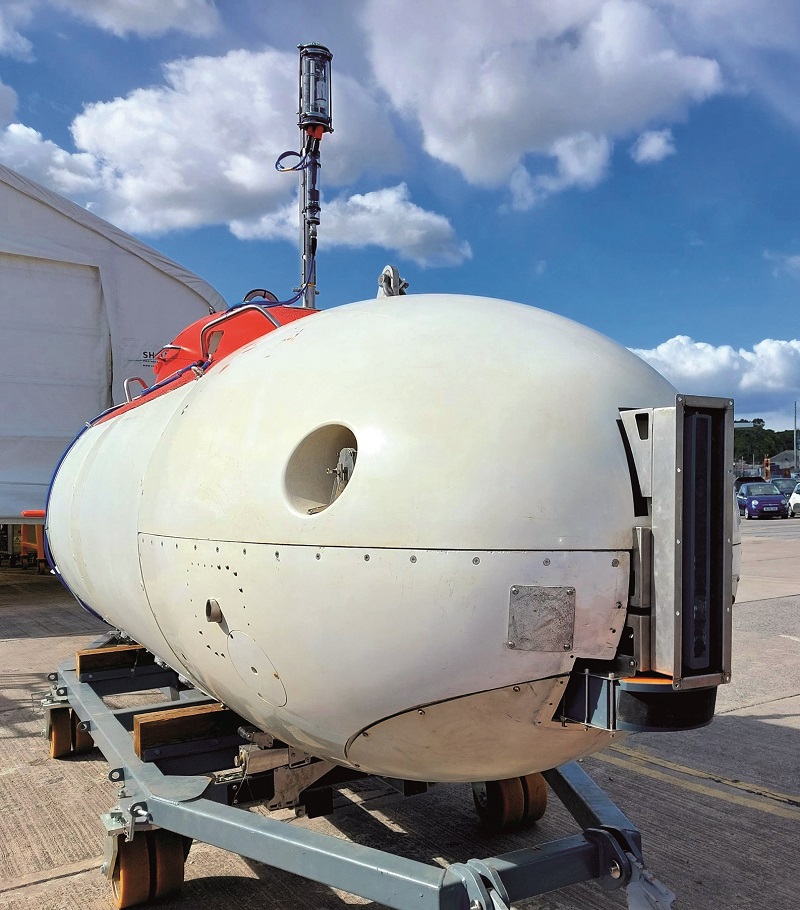
Wavefront Systems discussed its Vigilant series of forward-looking sonars, which the company noted is used on a number of large surface vessels as well as by MSubs and other AUV manufacturers for survey, navigation and obstacle avoidance applications.
“In particular they’ve trialled the use of our Vigilant 1000, which gives you a high-quality 3D sonar image of anything up to 600 m away, and reliable obstacle avoidance of anything up to 1000 m away,” Andy Covey said.
“Even for objects upwards of 900 m away, you still get solid detection of in-volume obstacles – whether it’s a shipping container, a marine mammal or another vehicle – with a range, bearing and position in the water column, along with determinations of whether you can navigate over, under or around it. Your uncrewed vehicle will therefore have time to take evasive action.”
The Vigilant 1000 has a 120o FoV, operates at a frequency of 70 kHz, and can be used at speeds of up to 25 knots and in temperatures from -2 C to +40 oC. It measures with an angular accuracy of 0.3o, has a roll and pitch stabilisation of ±20o, and consumes up to 150 W during operation.
Open Ocean Robotics had come from Canada to show the ongoing progress of its Data Xplorer USV, which is being used increasingly by customers interested in maritime domain awareness operations.
“We recently had a USV operating as part of the US-led Digital Horizon uncrewed and AI exercise in Bahrain,” said Julie Angus. “The Data Xplorer worked with other USVs over a mesh radio network, with AI providing and distributing information across the group on vessels detected and their activities.

“That kind of persistent maritime awareness could tackle many of the challenges associated with securing ocean borders against challenges like illegal fishing, drug trafficking and weapons trafficking.”
The Data Xplorer is designed to operate for 200-plus hours while moving at 2 knots, with a 10.5 kWh battery supplemented by power from deck-mounted solar cells, positioning it as a slow-moving, 360o scanning system (by way of EO/IR cameras, sonar or other integrated sensors).
Its design features a roll bar to enable self-righting amid turbulent waves, granting it added stability for clear, reliable survey readings even in high sea states, severe weather or traffic-congested waters.
“Because it uses buoyancy for self-righting instead of ballast, it is lightweight and has a shallow draught, making it well-suited to shallow waters,” Angus added. “And of course, that capability means it can be launched and operated in a range of conditions and it will continue gathering data.”
Prevco Subsea updated us on the latest offerings in its range of subsea pressure vessels and related accessories.
“We provide quite a lot of COTS aluminium 6061-T6 housings, the deepest-rated one being suitable for 2100 m; beyond that you’d need a different grade of material,” Stephen Ashley said.
“A company asked us about taking their UUV to 3000 m depths, and we suggested something along the lines of aluminium 7075, which is a stronger grade that many companies often take to 6000 m in short-term deployments, as long as there are inspections every 2 or 3 months to replace sacrificial anodes and check for scratches.”
He added that titanium would be the typical and (to some) obvious choice for such depths, and that Prevco Subsea does supply titanium housings but that aluminium 7075 is far less expensive than titanium. Titanium would however provide for a lighter in-water weight than many other materials, and lasts much longer than most, making it ideal for long-term deployments.
“Titanium isn’t very thermally conductive though, so if your internal electronics are generating a lot of heat, you might want to think about adding heat sink pipes or some other method of getting the heat out, although that might add too much weight,” Ashley added. “But it’s taken on a case-by-case basis, so we tend to work closely with customers in order to weigh up all the different factors and what the priorities are for the mission.”
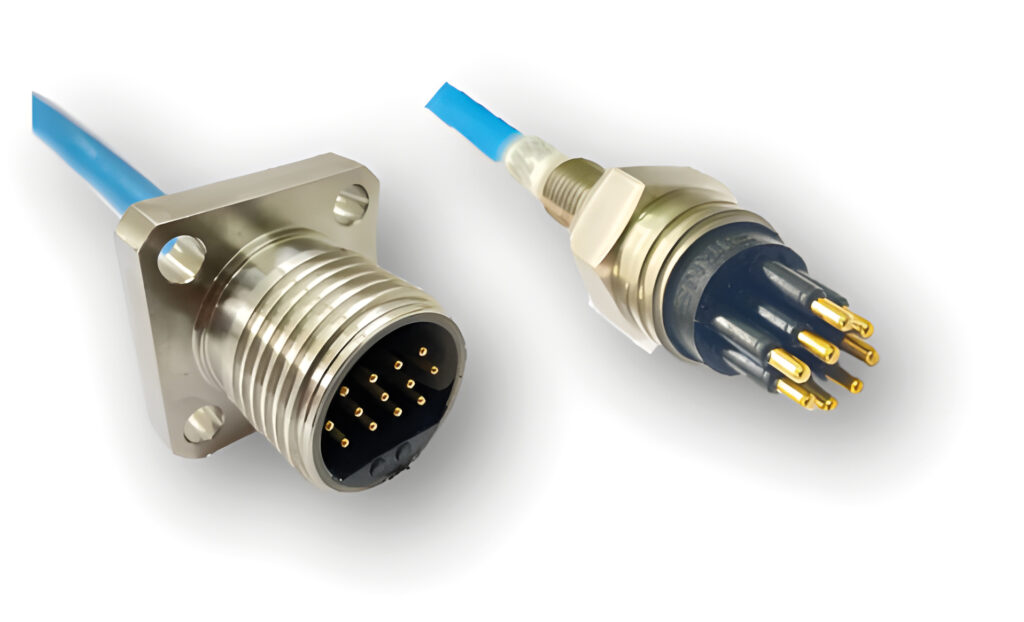
We met with Birns Aquamate, a US-based manufacturer of underwater connectors, and discussed its MC (Mini Connector) product series among others.
“While aerospace, comms and automotive connectors are governed by detailed industry standards, underwater connectors are not, so companies in the offshore technology industry have to deal with incompatibility of connectors often installed on the same systems,” said Eli Bar-Hai. “To help mitigate this problem, we’ve aimed to design all our products including the new MC series with a strong emphasis on compatibility.”
The MC units are designed as very small, volume-optimised circular units, and each has a locking sleeve that fastens against a step.
Bar-Hai said other manufacturers produce similar locking designs but make all the parts from rubber, which can cause the locking sleeve to pull off during operations. Birns has improved on that by adding a metal ring, which serves as a stronger base than rubber and prevents the sleeve from flexing and slipping off.
“Across our various connector designs, we opt for materials such as titanium, stainless steel, PEEK and aluminium-brass,” he added. “And of course, all our contacts are gold-plated and designed to Mil-Spec standards.
“We always have a large stock of those so that our lead times are as short as possible. In addition, we make our own contacts in-house on CNC machines so we can control both QC and inventory in the current challenging supply chain situation.”
The company also showcased new deep-submergence cable assemblies with data transfer rates of 9.4 (±0.1) Gbit/s for data transfer in advanced subsea vehicles. Performance testing has shown that data consistently transmits at this rate over a range of pressures from 0 to 8700 psi or 600 bar (6000 m equivalent depth).
The initial pin configuration in the 6000 m-rated Birns Millennium connector series tested for this capability is the Birns 3M-16, which features 12, 22 AWG data contacts, as well as four 16 AWG power contacts. Additional high data-rate configurations in the series are expected to be introduced soon.
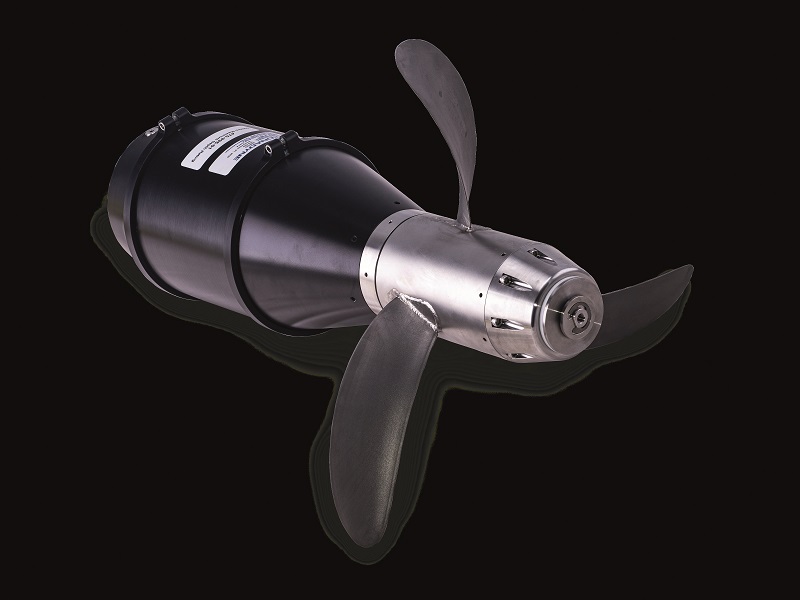
Tecnadyne attended the show to discuss its growing line of magnetically coupled thrusters for UUV systems. Its newest system in this series is the Model 2050, a direct drive thruster that was developed following requests by some customers to eliminate the noise created by the gearbox in their previous choices of thruster.
“This means that in this new system, the shaft from the motor goes directly to the propeller, eliminating all the noise,” Justin Leap said. “To have it perform appropriately without the gearbox, we had to make the motor a little larger to get more output torque out of it, but customers were happy with the trade-off.”
The Model 2050 weighs 11.4-14.5 kg in air depending on its configuration, measures 49.4 cm long, consumes 6.4 kW of input thrust (on a supply from 150 to 330 V DC) and outputs 63 kg of force at 10 knots or up to 113 kg at 5 knots. Among the customers for the 2050 thruster are Anduril Industries for its Dive-LD UUV (UST 37, April/May 2021).
“And while other companies have a shaft seal that goes all the way through, to connect the shaft to the propeller, on ours there’s an array of magnets on the driveshaft’s hub, and a set of opposing-polarity magnets on the propeller’s hub,” Leap added.
Applied Acoustics exhibited a wide range of acoustic navigation solutions for UUVs, and most notably showcased the Easytrak Pyxis, its new tracking system, which is a combined USBL and MEMS INS.
The solution calculates range accurate to 0.01 m resolution, with position accurate to 0.12% of slant range and 0.07o DRMS at greater than 20o depression angle, and operates over a range of up to 4000 m.
“We’ve also expanded our Easytrak Nexus 2 with a seven-element omnidirectional transducer, which gives us 0.25% accuracy of position,” said Ben Darling from AAE Technologies (parent company to Applied Acoustics).
“There are seven receive elements in the transducer head, which improves the bearing and depression angle calculations, and increases the accuracy and repeatability of the positions of the UUVs it’s tracking.”
Both Pyxis and Nexus 2 are capable of acoustically tracking up to 16 targets at once.
The company also showed its range of positioning beacons, which are provided in housings as standard but can be designed as OEM-style board sets for direct integration into AUV housings with connections to remote transducers.
These beacons can be SWaP-optimised for UUVs working at different depths and endurances. The smallest weighs 1-1.2 kg in air, is designed for 600 m depth limits and can be operated for up to 56 hours at a time, while the largest is meant for depths down to 4000 m, operating endurances of 400 hours, and weighs 22.8 kg in air.
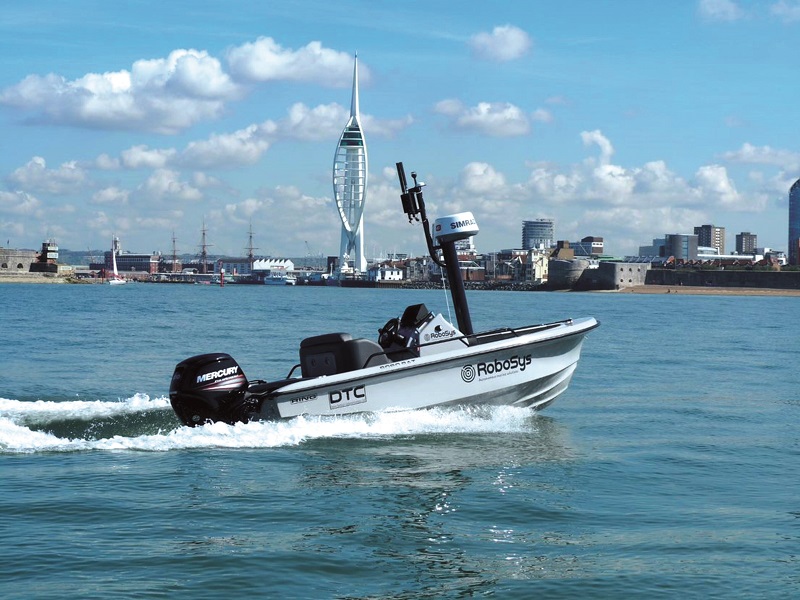
Imagenex showcased a range of its newest multi-beam sonars, intended particularly for UUV integrations.
“Our new DT360XI sonar for instance is aimed principally at robotic platforms performing tunnel inspections or similar surveys of narrow spaces,” said Doug Wilson. “It scans in 360o at five to eight shots per second, and sends 1440 beams per shot.”
The company also highlighted its Delta-T 837A forward-looking multi-beam sonar, which is suitable for integration on smaller UUVs such as those from the growing micro-AUV market.
“That’s always a challenge, because there are physics limitations on how much you can pare down the size and geometry of the transducers,” Wilson said. “However, power and weight are at a premium for AUVs, so optimising the sizes of those as well as our electronics are something we always try to focus on.”
The Delta-T 837A measures 240.3 mm by 69.9 mm, consumes just under 5 W at maximum performance (working on a 22-36 V DC supply), and emits a beam width of 12o x 10o.
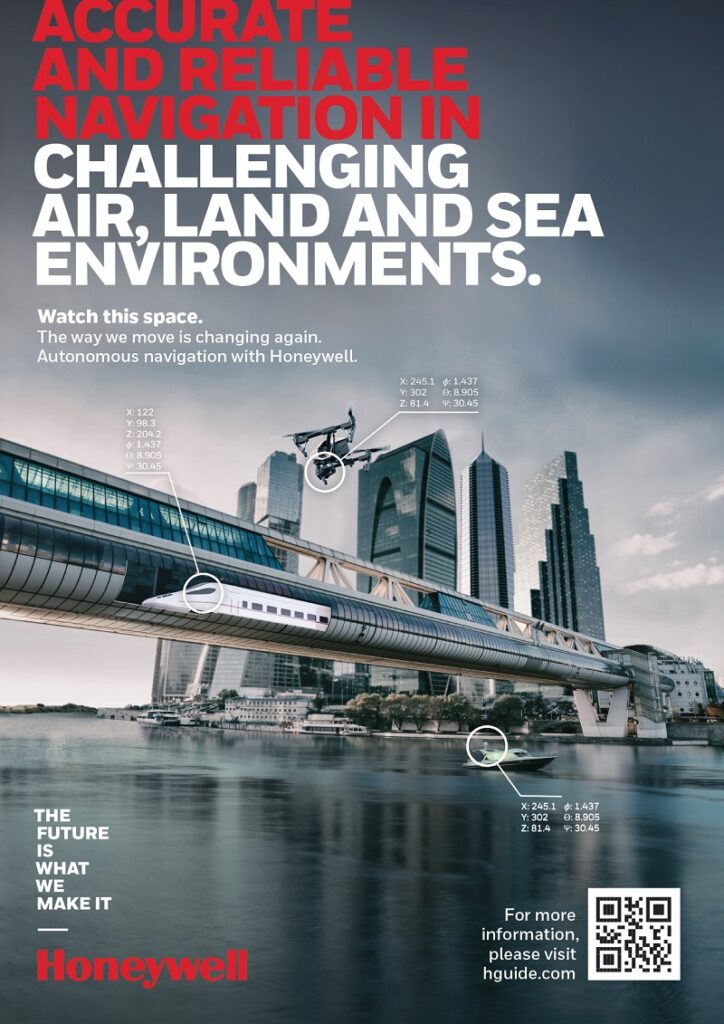
Robosys was on hand to talk to us about its marine autonomy software, which has been developed for compliance with the COLREGs governing how vessels must conduct themselves during avoidance manoeuvres.
“We’ve also developed a marine ‘intelligent’ autopilot software solution, the Voyager AI suite, and thus have a robust and proven architecture and algorithms for the safety of an uncrewed vessel,” Keith Henderson said.
“And during autonomous navigation and path planning, our software takes depths into account in real time using ENC S-57 charts, to ensure the planned track is a safe one.
“That minimises any risk of a USV or other autonomous ship type ending up on a sand bar or rocks.”
The Voyager AI software is compatible with a range of comms bearers including satcom, MANET radio, and 4G/LTE data links. In addition to the grounding avoidance it also comes with obstacle detection, collision avoidance and autonomous return-to-base capabilities in case all comms should be lost.
UPCOMING EVENTS
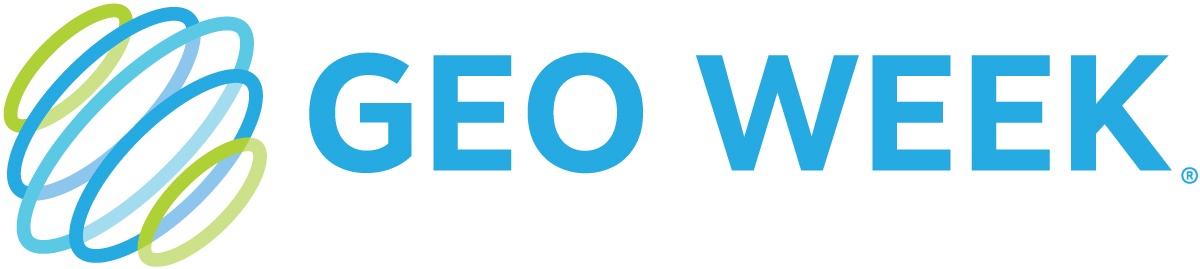
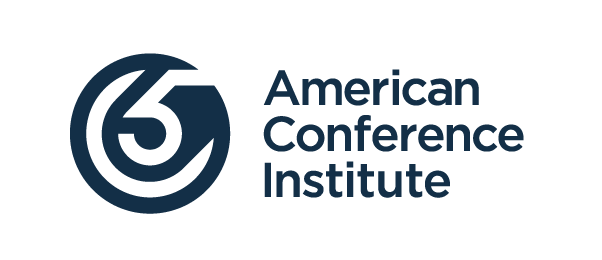
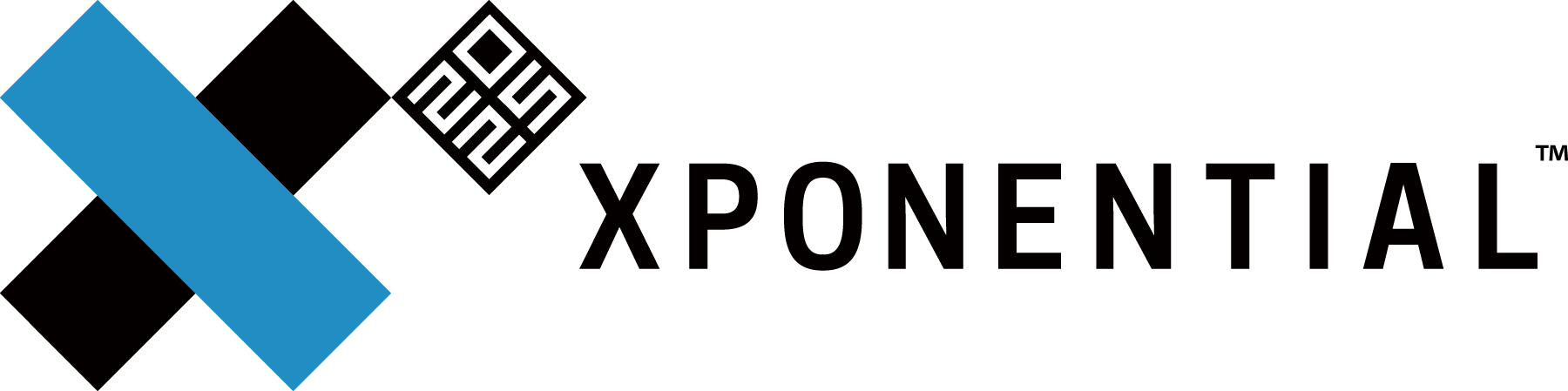
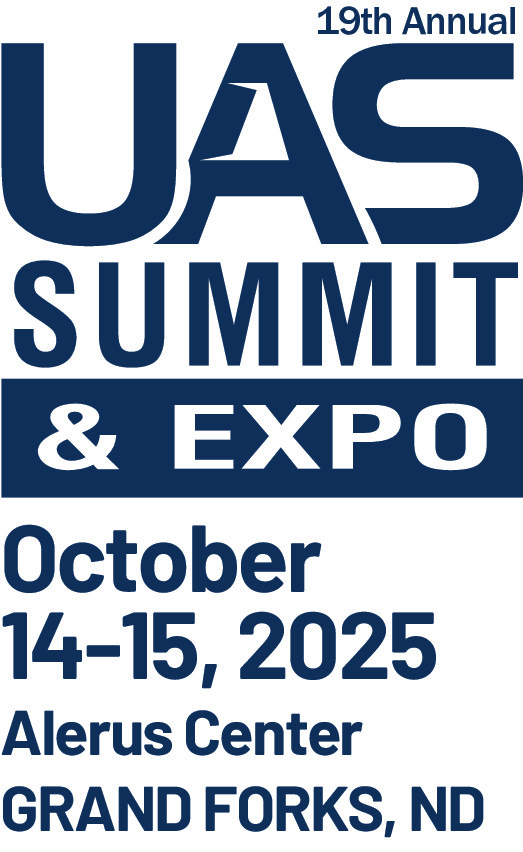
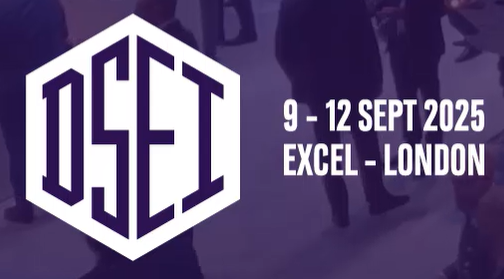
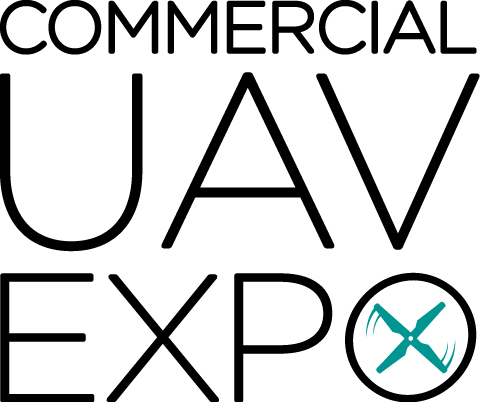
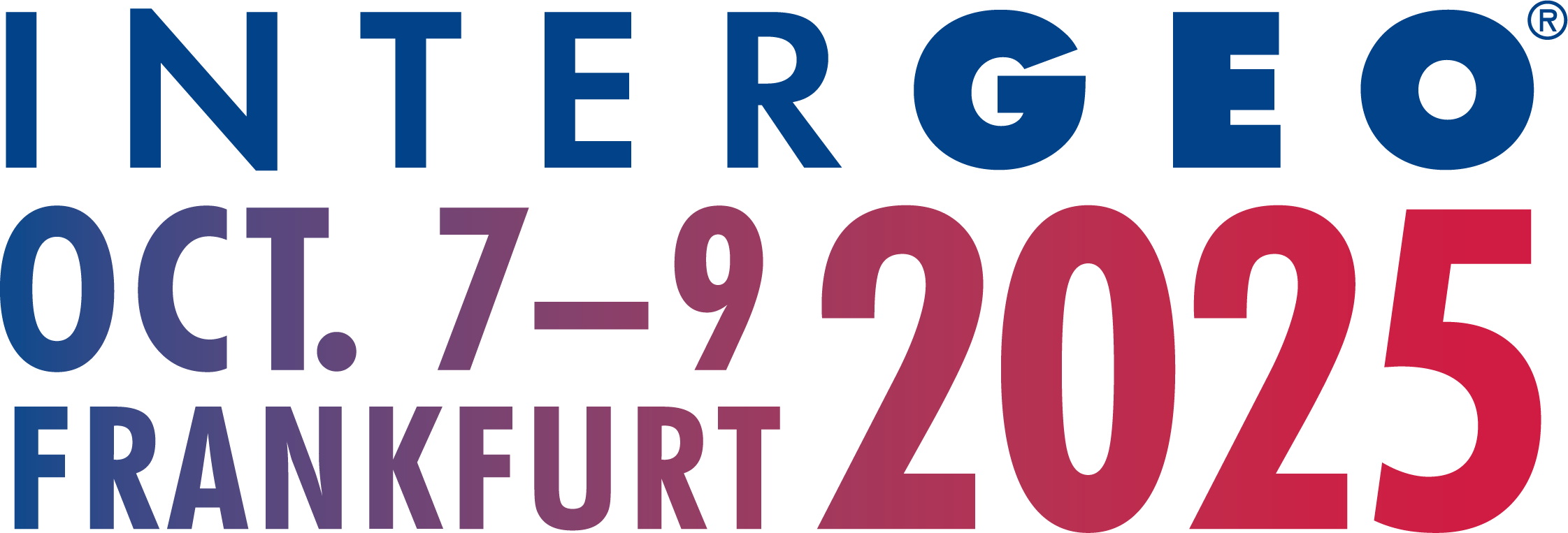
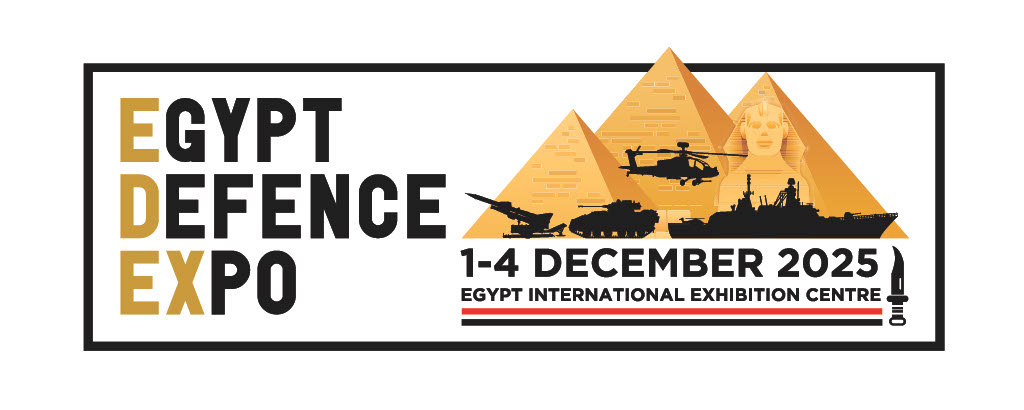
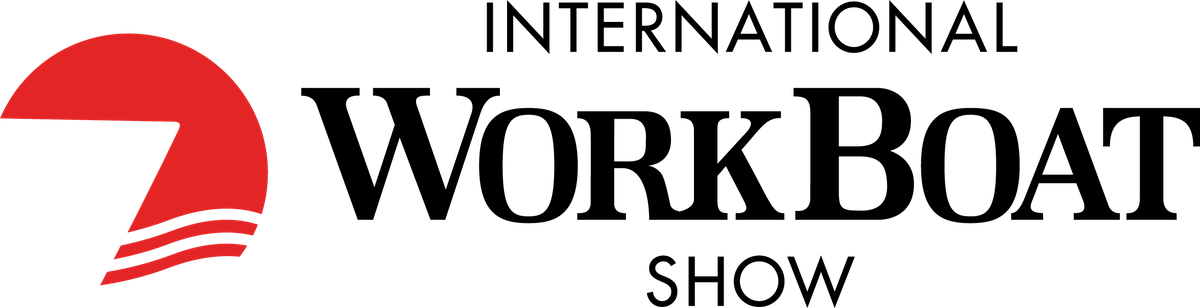
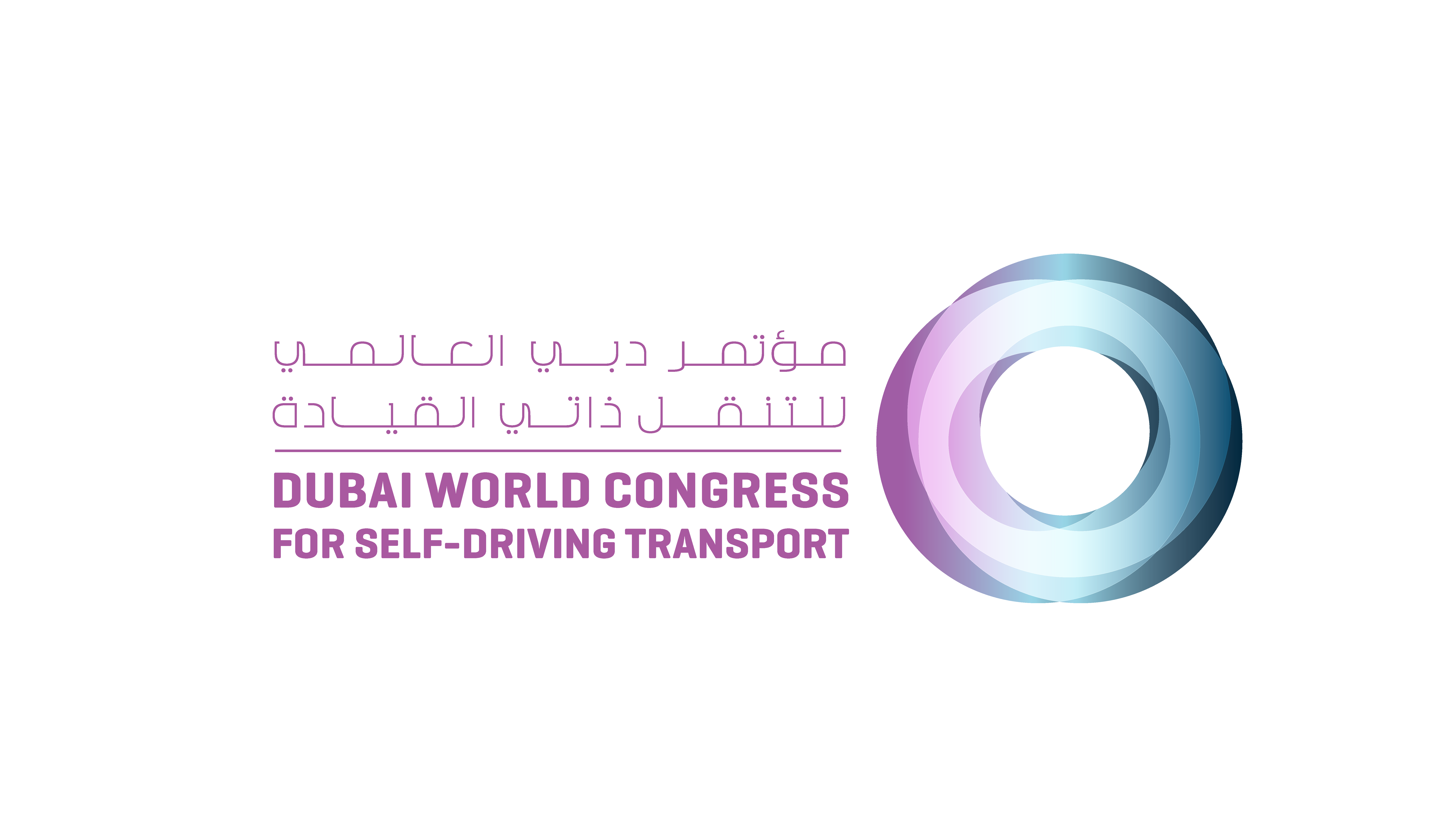
