AALTO Zephyr 8
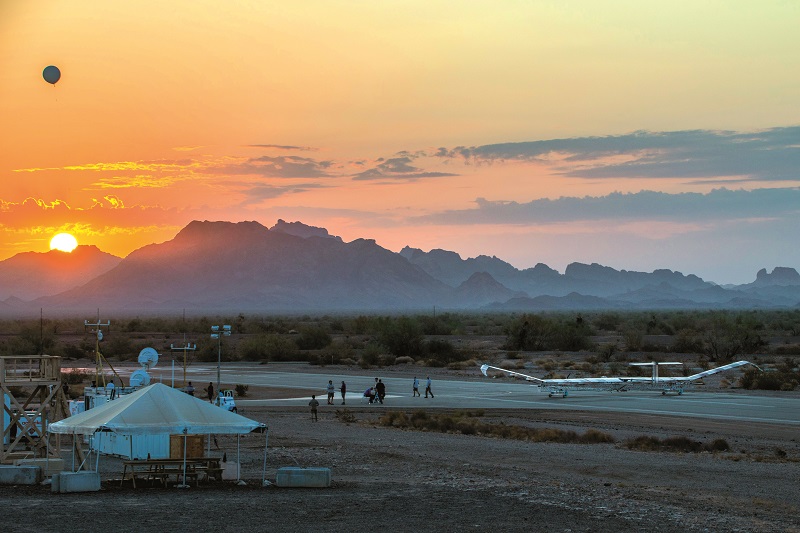
Rory Jackson traces the development of this solar-powered UAV designed to provide a range of services from the stratosphere
The stratosphere is the second-highest layer of the atmosphere, and over the past few decades it has hosted advanced UAVs for applications such as mapping, surveillance and comms relays that lend themselves particularly well to this environment.
Uncrewed aircraft flying in or above the stratosphere are increasingly referred to as HAPS – high altitude platform stations, or high altitude pseudo satellites. The term encompasses many types of vehicle configurations, and symbolises to many the last frontier of aircraft engineering.
While many HAPS projects have come and gone over the past 20 years, the Airbus Zephyr has not only survived but continued to mature. This large but lightweight solar UAV has changed ownership and design more than once since its conception, but it has nonetheless represented a constant for the UAV industry, setting new boundaries for UAV altitude and endurance.
The Zephyr has been developed in Farnborough, UK, for most of its history, with input from military users such as the UK’s MoD, a result partly of the craft’s origins within UK group QinetiQ.
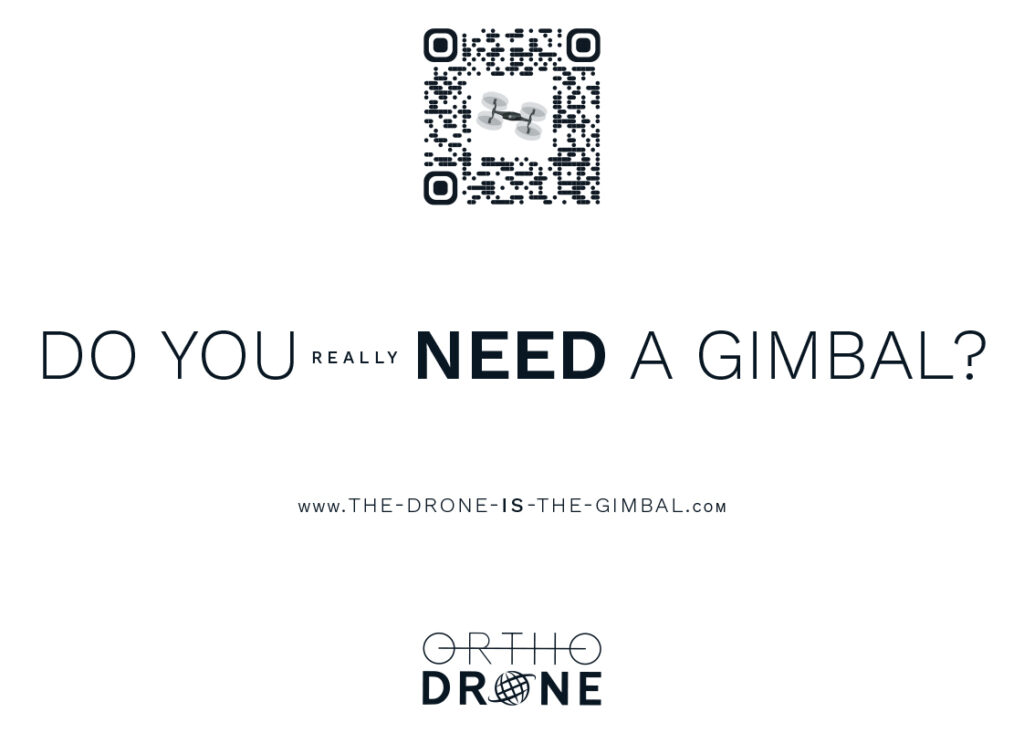
QinetiQ’s first Zephyr was the Zephyr 2, named for the aircraft built by the Royal Aircraft Establishment’s first flying club in Farnborough. The version we will look at here is the Zephyr 8 (Z8), once branded the Zephyr-S.
The Z8 was first launched in July 2018, before landing 25 days later in the August. That was a Guinness World Record at under 75 kg. Its empty weight comes to around 25-30 kg, making it lighter than most 1 m-diameter commercial multi-rotors.
A combination of structural design, aerodynamic optimisation and lightweight parts contribute to its size-to-weight ratio. In turn, at the time of writing its endurance had been tested over more than 64 days of continuous stratospheric flight – the current record for uncrewed stratospheric flight. Its engineering team aims to offer 200 days per flight of the Zephyr with essentially any variety of payloads up to 75,000 ft (22,860 m).
The Z8 is now being positioned for commercial activities. With 20 years of r&d behind it, Airbus and Zephyr’s engineers have agreed that the HAPS’ days as a research project are complete. This is why it has been decided to switch the Z8’s flights from science experiments to commercial offerings.
As a result, it is technically no longer the Airbus Zephyr: to transition it into a mission-ready platform, its team has spun out into AALTO HAPS (AALTO, derived from ‘Airbus, high ALTitude, zerO emissions’). It is an Airbus majority-owned but ultimately independent entity, its aim being to demonstrate its modularity, sustainability, technological maturity and very long endurance stratospheric flight for an array of missions.
Providing 5G connectivity for instance is a primary aim, although AALTO also sees the aircraft as being suited for wide-area mapping and surveillance, akin to satellite imaging but without the associated launch costs.
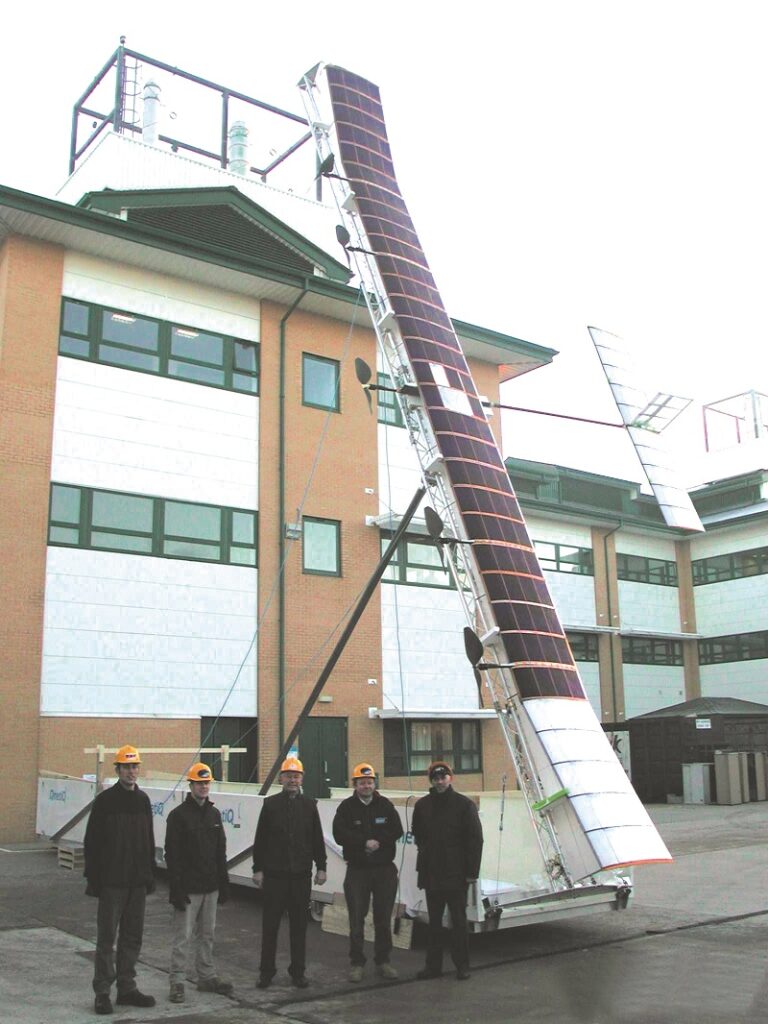
Early development history
The Zephyr 2 was the brainchild of Qinetiq’s Chris Kelleher. He had studied the first solar-electric UAV, the Sunrise 2, flown at NASA’s Langley/Dryden Flight Research Center in 1974, as well as numerous human-piloted solar flying machines such as the MacCready Gossamer Condor and the Gossamer Albatross.
“Materials have come a long way since then, but you can see architectural similarities to those in the Z8,” remarks Richard Tyler, VP of flight operations at AALTO.
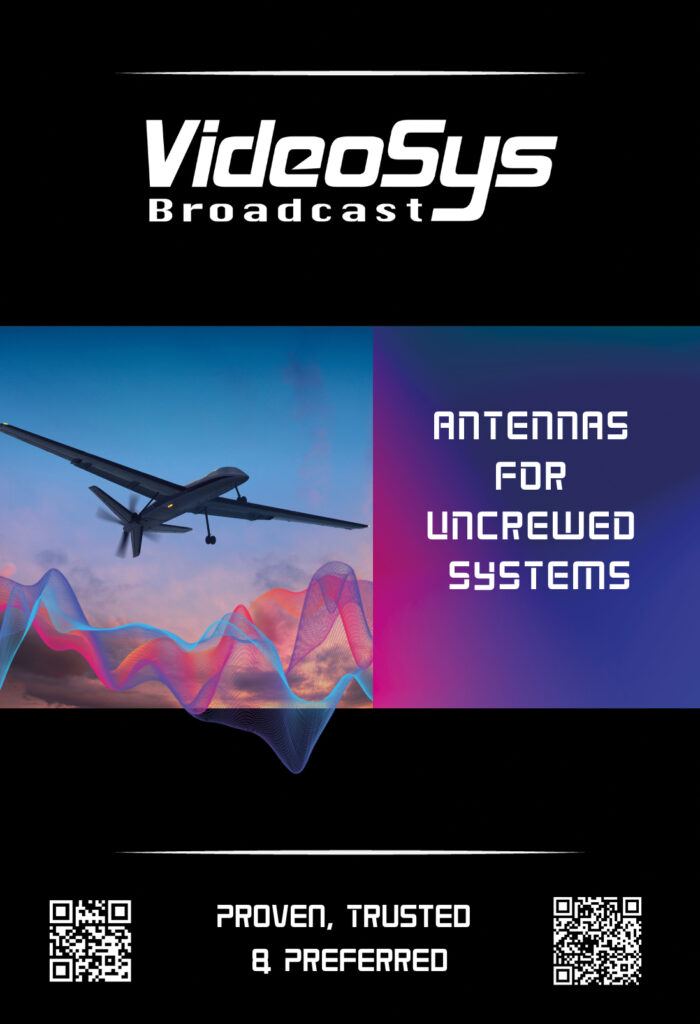
QinetiQ was founded in 2001, and to make a name for itself it planned to set an altitude record using a large, crewed balloon aircraft named the QinetiQ 1. To take live photos of the balloon in the stratosphere, Kelleher suggested using a solar-electric fixed-wing UAV, for which the Zephyr 2 was designed as a 50% scale demonstrator.
The full-scale aircraft was iterated in the Zephyr 3, a 12 m-wingspan UAV weighing 14.5 kg and integrating five motor-propellers. The team thought of tethering the Zephyr 3 to the Qinetiq 1 as the latter floated up to the stratosphere, where the UAV would spin up its propellers and fly around the balloon taking photos before the two descended together.
The QinetiQ 1 failed to launch though, and the Zephyr 3 never flew, but interest from the UK’s MoD and within QinetiQ drove continued r&d in the Z3, the company winning funding in 2004 to develop the Zephyr 4 as a prototype for stratospheric ISTAR. This was also to be balloon-launched and tethered, the tether breaking under tensile stress to release the UAV.
“That method was very quick, but controlling the Z4’s orientation during ascent was difficult, so in 2005 QinetiQ retired the launcher and switched to ground launching,” Tyler recounts. “They’d realised that the UAV was so light that it could actually be hand-launched by technicians spread across the wingspan.”
That concept was proven with the Z5 redesign, which operated from late 2005 to early 2006, flying for a cumulative total of 35 days and at up to 35,000 ft. This phase also marked the first use of a dedicated GCS, with multiple radios, computers and workspaces for the flight team.
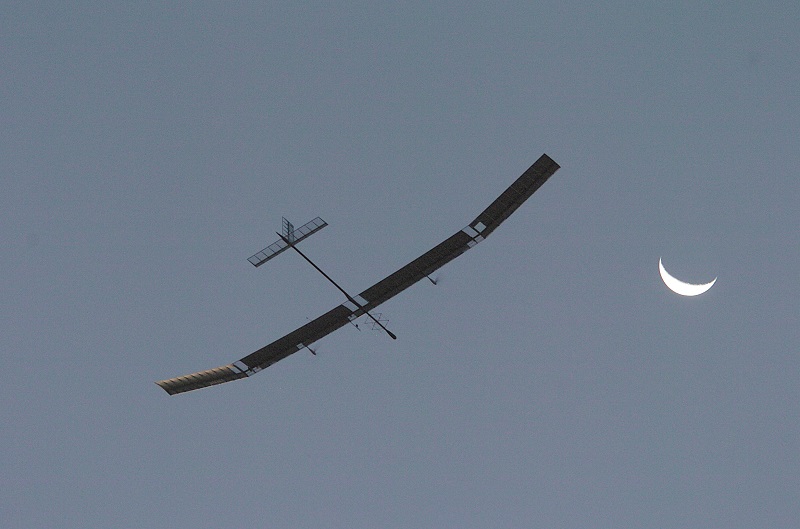
The Zephyr 6 followed in 2007, and was developed through to 2009. Five flights totalling 206 hours were carried out in those years, reaching a maximum altitude of 61,800 ft, with considerable redesign and improvement in the GCS architecture being done at the same time.
“The Z6 was really where we went from being a project to a programme – the MoD and QinetiQ directors all agreed that the Zephyr was viable, and we were making routine weight reductions and size increases using advances in materials and structural optimisation tools,” Tyler says.
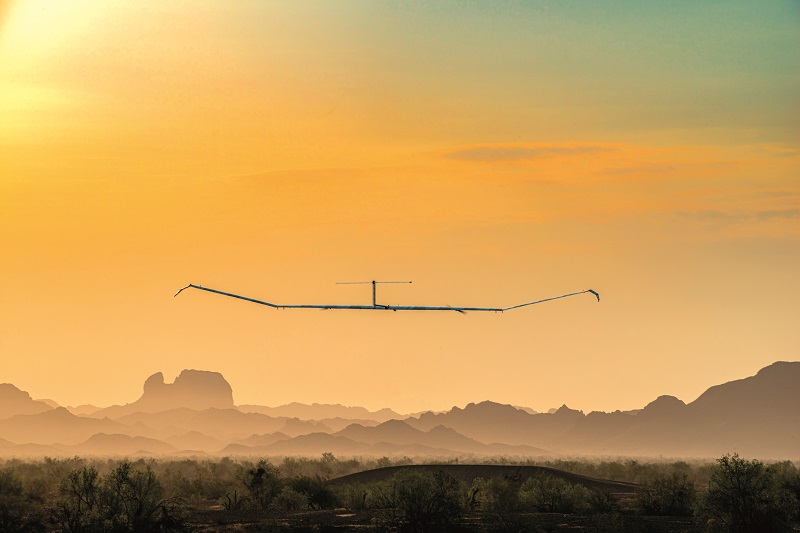
From QinetiQ to AALTO
The Zephyr 7 first flew in July 2010, with confidence in its ability to fly at a record 70,000 ft in daylight with minimal operator intervention (beyond the hand-launching). Its initial 14-day trial included a strategy to avoid a potentially catastrophic storm between days 4 and 6.
“Autonomy was always on the table, but it was with the Z7 that we really went from having our hands on the control sticks to taking our hands off and letting the mission run in an automated way,” Tyler says.
Six more flights followed through to 2014, over numerous sunlight-rich locations including the UAE, Ascension Islands and Arizona. This helped to show that the Zephyr could easily be dismantled, packed into a container and transported to a new launch point.
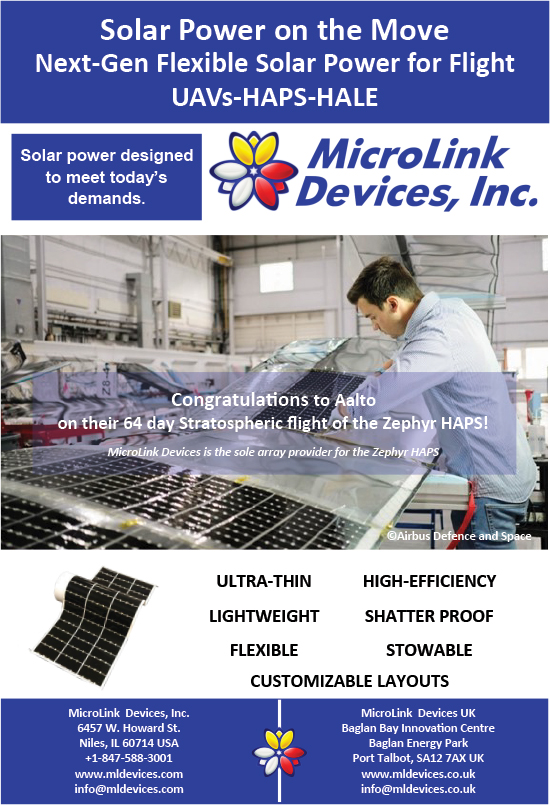
“But while we’d made a lot of advances with lighter composites, plastics, foams and other subsystems, what really held the Z7 back was its lack of battery capacity for maintaining altitude overnight,” Tyler recounts.
“The team looked at the design, reduced the dihedral angle to mitigate the Dutch roll resulting from the rarefied air in the stratosphere, and did things like changing cable harnesses and battery cells to increase our effective Wh/kg.”
In 2015, Airbus acquired the Zephyr from QinetiQ, and the developments above shortly fed into what became the Z8. This has remained the focus of the programme’s flights and r&d to date.
“At the beginning of 2022, we also spun out of Airbus as HAPS Connectivity Solutions, spending a lot of that year in a transitional state between being Airbus and being this new organisation, before officially becoming AALTO HAPS in January 2023,” Tyler says.
“As well as our technology now being mature, Airbus saw the business opportunity of stratospheric connectivity. But Airbus knows it isn’t a comms company, so spinning AALTO out gave us the freedom to research that industry and specialise in it.
“And although we’re still intrinsically linked with Airbus by things like shared IT, expertise and governance, we’re encouraged to form new partnerships, funding and so on at our will to become sustainable on our own.”
Much of the Zephyr’s intrinsic value relative to satellite-based comms and Earth observation comes from its superior latency. It is trialling payloads with latencies of 5-10 ms, meaning connectivity of an order of magnitude faster than LEO satellites, and faster still than GEO satellites (which have latencies upwards of 600 ms).
Both LEO and GEO satellites also require proprietary technology to function, meaning they are often restricted to connect only with satellite terminals. Conversely, the Zephyr’s payload agnosticism enables systems with direct-to-device (D2D) 5G connections, allowing high-bandwidth connectivity for smartphones and other personal devices wherever needed.
“Even when using existing satcom networks like Iridium, the connection quality is very poor, and you can’t work with it without buying really expensive equipment. Apple has made some strides in satellite-based texting, but it’s still really difficult to do live voice or video,” Tyler says.
“We can fill wide gaps in terrestrial infrastructure across the world for D2D connectivity. Even in the US, there are massive gaps in cellular coverage in rural, mountainous and other areas; a few steps off-highway can cut your phone connection.
“So we’re talking with the T-Mobiles and Deutsche Telekoms of the world. It’s probably not suitable to hire us to fly over a city, except maybe during a major sporting or entertainment event where hundreds of thousands gather in one place, and the local networks can’t handle everyone using their smartphones at once. But all the telecoms companies want to offer persistent, 5G, D2D connectivity to rural and mountain regions without the expenses and onerous project management needed for new satellites or base stations.”
The UAV’s Earth observation capabilities have also been promoted under the OPAZ (Optical Payloads for Airbus Zephyr) branding, with the HAPS offered as a much lower-cost means of providing live video from orbit than launching new video satellites, with any camera configurable to integrate in the aircraft so long as the 4-5 kg payload capacity is adhered to.
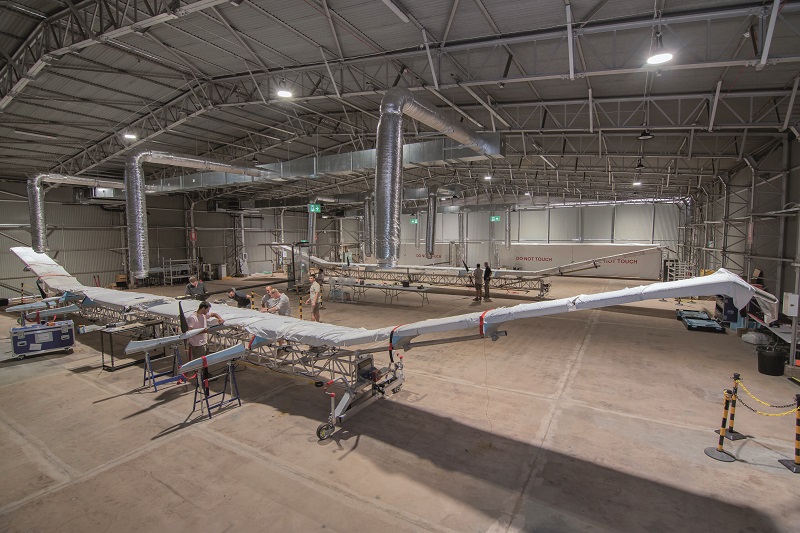
Zephyr 8 anatomy
At the time of writing, 12 Zephyr 8s had been produced and flown in eight flights, for over 3000 cumulative operating hours. The company estimates that the total flight time across all Zephyr models exceeds 4000 hours.
As mentioned, the Z8 was briefly re-designated the Zephyr-S, and promoted alongside a twin-tail version called the Zephyr-T, although the latter was internally named the Zephyr 9 (which to date has not been actively flown or optimised for commercial service). Those names did not catch on within Airbus or AALTO, so they have been discarded to avoid confusion.
Outwardly, the Zephyr’s shape looks little different from a conventional aircraft. It has two fixed wings that connect to a single fuselage, and each wing has a propulsion unit consisting of a motor and propeller, while a payload pod sits at the front of the fuselage and there is a tail at the back. The tail mounts a fin, an elevator and a rudder.
Unlike typical fixed-wing UAVs, however, the fuselage consists of a carbon tube and contains only cabling, with very few subsystems inside. Instead it serves primarily as a structural member, connecting the tail and the wings, with the bulk of subsystems mounted in the latter.
“Of course, there are quite a few other differences to a conventional fixed-wing UAS, such as our extensive use of solar power, and the fact that our aerostructure and propulsion system are optimised for flying in the stratosphere, not for the air densities and environmental conditions near ground level,” Tyler notes.
“On top of that, we have to design for really unusual thermodynamics throughout flight. I sometimes liken it to an astronaut doing a spacewalk: when the sun’s on one side of their spacesuit, it is practically on fire from the sheer heat, while the other side is below freezing.
“The Zephyr goes through a comparable cycle over each 24-hour period. The stratosphere can be -50 oC ambient during clear days but the sunlight shining down on the solar panels heats up all the topsides of our components really strongly. And it’s much worse on overcast days, because the sunlight reflects off the clouds below to cook the undersides of the wings and subsystems.
“In terms of our mechanical structure, we heavily span-load the wings with our componentry. We have no undercarriage, and every gram of weight installed and every milliwatt consumed must pay for itself in a net benefit to overall SWaP before being approved for use – 75 kg is our maximum all-up weight.
“Combine that with our 25-30 kg empty weight and 25 m wingspan, and you find we don’t actually fit into any definable group or category of UAV.”
Each wing consists of three sections – the main wing, which connects directly to the fuselage and sits at a 0o angle from it; the dihedral, which inclines upwards from the main wing; and the ogive, which extends briefly from the dihedral with a downward curve.
Although some subsystems can be moved around in the wings as needed, the satcom antennas are always installed in each wingtip, as far from each other as possible to prevent crosstalk. All the other systems must be spread out for an even distribution of weight and for the centres of gravity and balance.
Flight-critical systems such as the flight controller and its related avionics, FPV cameras and air data probes, as well as its angle-of-attack and sideslip vanes are typically mounted in the wing sections closest to the fuselage.
In the outer half of the main wing, there are the propulsor pods, one on either wing, comprising a propeller, an electric motor and an ESC, as well as three ‘large’ battery packs – hence six of them per Z8 – with up to three more pairs of ‘small’ battery packs typically sitting further out (AALTO declines to disclose the total onboard energy storage).
The ogive and wingtip sections host additional payload bays, along with cameras mounted conformally with the aerodynamic profile of the wings, and pointed back down the wings for remote operators to visually assess the condition of the aircraft during flight. Navigation lights and antennas are also mounted in these outer wing sections.
Tyler notes here that the payloads do not have to interface with or be operated by the flight controller. If for instance a potential customer is sensitive about their technical IP, data security or ownership, they can independently monitor and control the payload themselves, with the Zephyr serving solely as the platform and power source.
Regarding the fuselage, the rear half of its carbon tube mounts the GNSS antenna and an S-band antenna. Additional antennas for a UHF data link and a transponder system are installed nearby in the wing sections.
Phil Briggs, chief engineer for AALTO, adds, “We tend to position most of our subsystems in the leading edge of the wing. That helps a lot with keeping our CoG in the best position, as does spreading the weight across the wingspan, which also minimises any concentrated load point on the structure.
“The Z8’s total part count is somewhere in the very low thousands, which for an aircraft of this size indicates our focus on simplicity throughout its engineering.”
In addition to the UAV, the operation infrastructure includes AALTO’s GCS and its ‘rover’ mobile ground terminals. The latter are containerised workshops for pre-flight checks and analyses, as well as testing and validating systems on-site before a launch.
That can mean individual component tests such as cycling battery cells or electric motors. The company will also set up battery isolation and conditioning chambers on-site to monitor and prepare the packs for flight.
AALTO will also bring what it calls its low-level test article to launch sites. This is a 30% scale model of the Zephyr with the same Reynolds numbers as the Z8, albeit slightly different aeroelasticity. Nonetheless, it allows Tyler and his team to run ad hoc tests of the flight control system in the context of the HAPS’ aerodynamics.
“Also, before we take the aircraft to a launch site, we’ll have had to test every component with really long burn-in times, because for our operations to work, we need everything onboard to work non-stop for weeks or months at a time. We won’t launch for, say, a 60-day flight unless every component has been tested to function over 120 days,” Tyler adds.
The company’s testing systems include test benches for avionics, payload integration, and propulsion rigs. It also has a full ‘iron bird’ test rig for installing and validating payloads, to study how payloads can interact with the Zephyr’s avionics, electrical, structural, network and other aspects of the aircraft’s systems.
The company also owns two GCS simulators, for training its flight teams, some testing, and for assessing the design of its HMI, to determine for instance whether the crew finds the GCS layout intuitive or otherwise during routine or emergency situations.
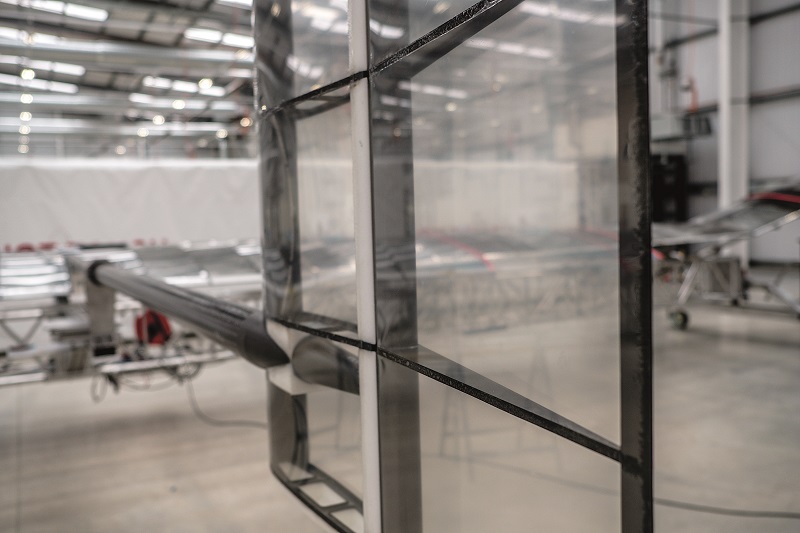
Construction
The Zephyr’s production facility is organised linearly, such that construction materials are received and stored at one end, with manufacturing of structural parts in the next room in its factory. Continuing through the factory, there are Zephyrs in various stages of assembly.
“The construction process starts with taking the carbon fibre ribs, spars and other airframe components, and placing them into our jigs, which are recognisable as aluminium structures around the workshop floor,” Briggs says.
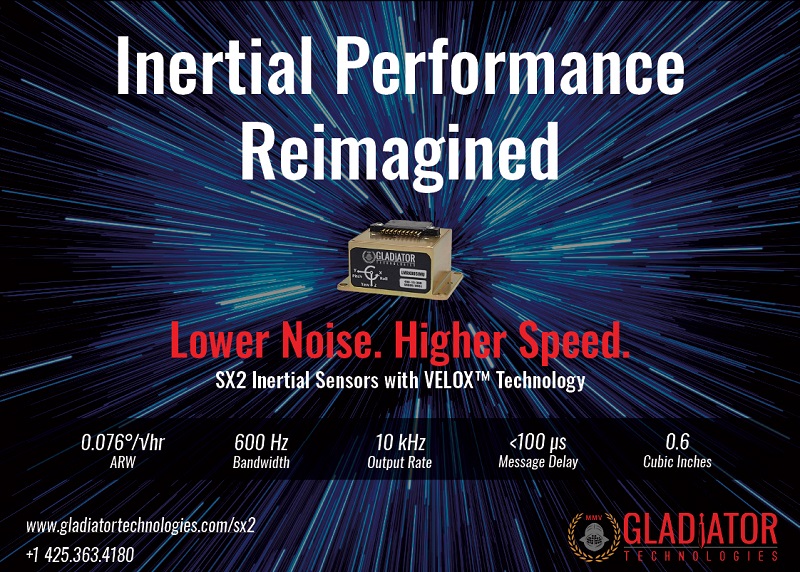
“Each jig is precisely controlled, and regularly checked and tested to see they’re still working within the tolerances we need for consistent manufacturing.”
Once the carbon parts are laid-up in the jigs and checked for correct placement, they can be glued together as an airframe. The completed airframes are then moved to the centre of the facility and load-tested to factors beyond the aircraft’s design limits for all-up-weight and g-forces. CFD and FEA simulations are also regularly run to support optimisations for bonding and structural design using newly gathered flight data.
“The load-testing measures not just the amount of deflection, but also checks that there are no sub-element failures resulting from the loads applied,” Briggs explains.
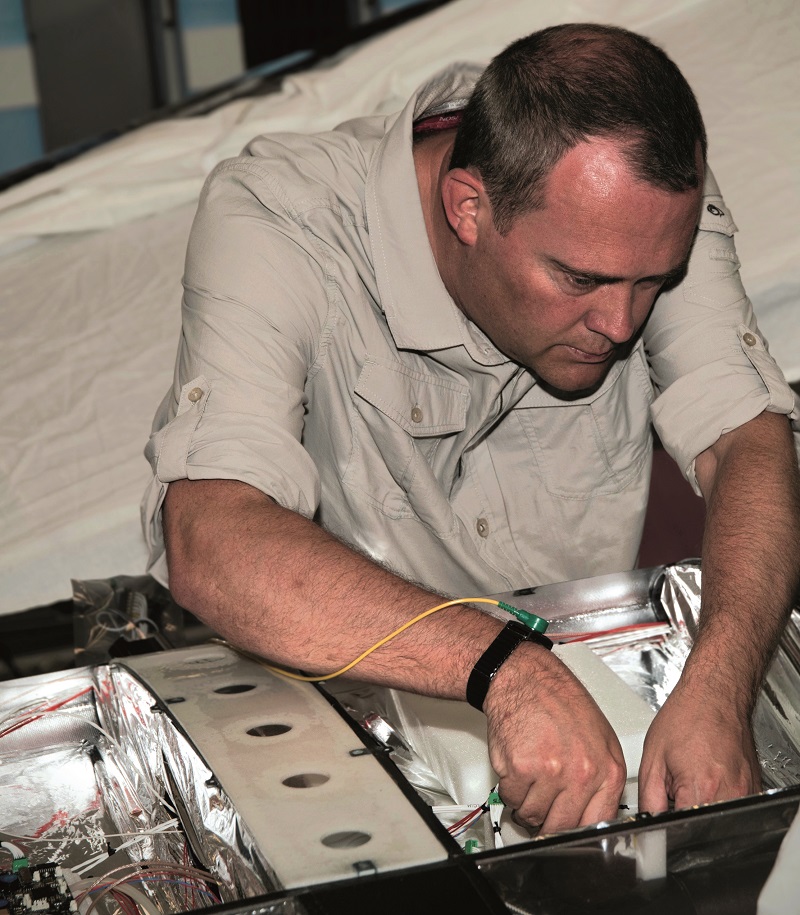
against the extremes of the cold of night and the heat of day
After passing those tests, the airframe moves down the production line into avionics integration. Most of the wire harnesses and principal components for flight control, navigation and comms are installed here, after which they are also test-cycled to verify their functionality. The same then follows for the payloads as well as the batteries, power distribution, motor control and propulsion systems.
“Before that though, we’ll have tested all those parts in our combined thermal and vacuum chamber, in which we can simulate and exceed the range of pressure and temperature conditions the stratosphere can expose our electrics and electronics to,” Tyler says.
Lastly, Mylar coverings are placed and glued around the mechanical, electrical and electronic systems to close them off from the environment. The solar array is glued on top of the Mylar on the wings, although future Zephyr designs could save weight by using the PV panels as housing members, forgoing some Mylar underneath.
“We want our final assembly lines formalised into something we can export and set up in different countries, so we’re not always building the whole aircraft here, or dealing with the costs or damage risks from shipping worldwide from Britain,” Tyler notes. “We could have components turn up and put together into a launch-ready aircraft anywhere.”
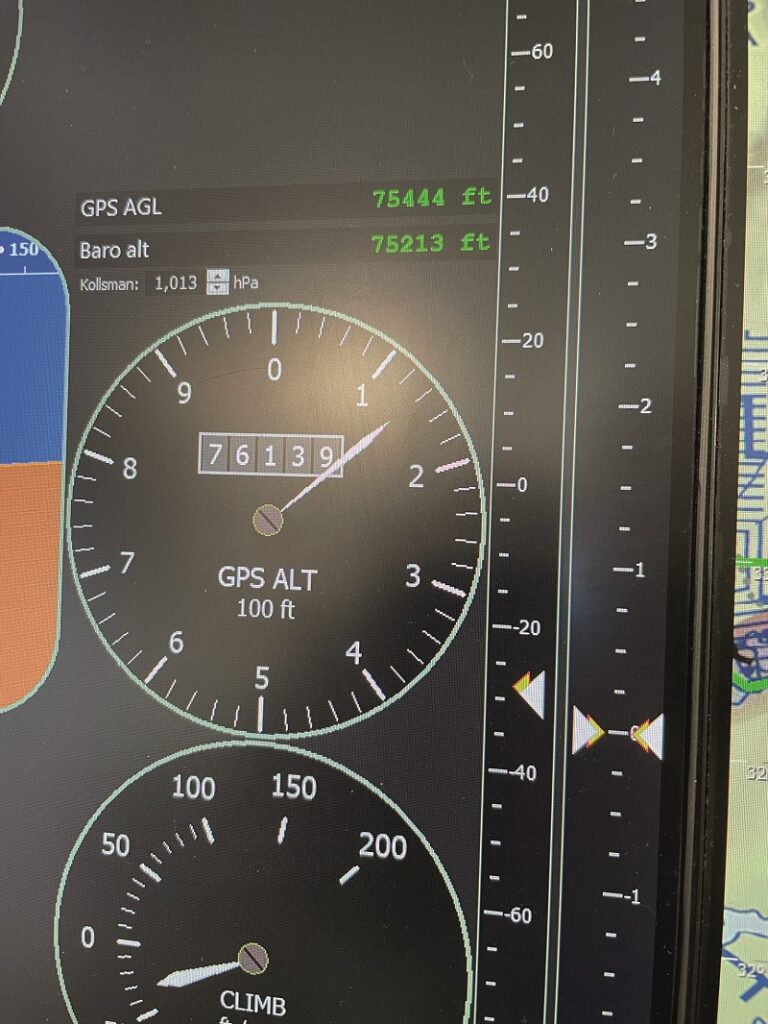
Airframe materials
The carbon fibre aerostructure is designed around a span-loaded wing with a single central spar and lattice ribs. Fairings and trailing edges are a lightweight open-cell foam, while as mentioned the skin is Mylar.
“Mylar is commonly used in this type of aircraft,” Briggs says. “It’s very lightweight and adds a lot of stiffness to the HAPS, and it was used on previous lightweight aircraft like the Gossamer Condor. It’s been improved since then to make it thinner and lighter.”
The open-cell foam provides similar weight and structural strength advantages, along with good thermal insulation properties for the batteries and electronics. It is also easily cut, sanded and shaped as needed for mounting avionics, batteries and other subsystems inside, as well as conforming to the shapes needed for the trailing edges.
In addition, a silver foil based on another type of Mylar is used throughout the wings for key subsystems, to provide extra thermal insulation against the extremes of cold during the night and heat during daytime.
Briggs adds, “Getting the insulation right so you can self-heat your batteries and electronics at night but not cook them during the day is a key balancing act.
“Onboard equipment needs constant thermal monitoring: there are around 50 thermistors installed in the wings, and then 80-100 in total if you include the sensors in the battery packs. Every single thermal sensor is tested for serviceability and range before being approved for launch.”
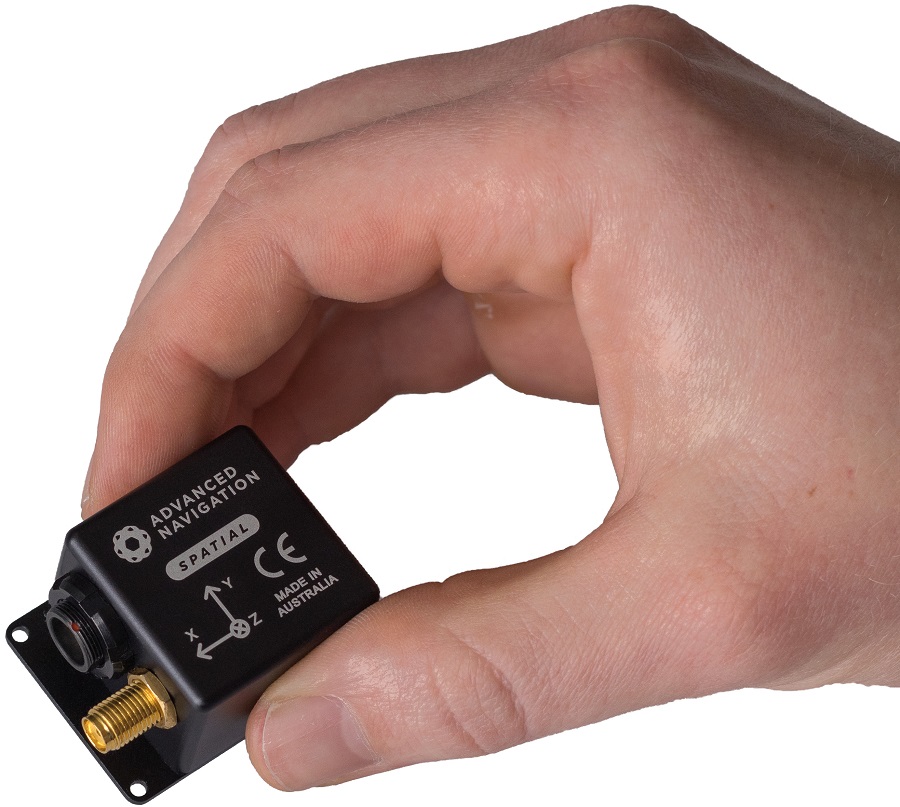
Structural design and loading considerations
Briggs estimates that there are around 250 separate carbon parts in the Z8. These flex and bend throughout flight, a necessary side-effect of AALTO using the lightest carbon composites it could find, although it helps to avoid structural stress and fatigue.
“Modelling loads across the aircraft is straightforward, but the tricky bit is dynamic simulations of the HAPS,” Briggs adds.
“Its flexibility means that at higher speeds, its wing will twist and change shape. Most modelling programs out there are designed for things like A320s, which are pretty stiff in their design and use of materials, but they don’t exactly come with a feature for a twisting wing.”
AALTO compensates for that by using its flight data, combined with further data such as that published by Google Loon, to simulate in-house the shapes the Zephyr takes at different speeds and within different permutations of the stratospheric environment. These are refined with each flight to further optimise and validate the HAPS’ structural design.
“Among the most important aspects of the primary structural design we look at is how to cope with torsional loads, which leads to the selection of materials and how they’re implemented in the design of the aircraft to counter those loads,” Briggs says.
“The hardest time for the aircraft is during the ascent to and descent from the stratosphere. The weight, thermal protections and load distributions are optimised for the stratosphere, whereas in ascent and descent it’s dealing with heavier air densities and higher temperatures than usual.”
In addition to the wing structures, the three carbon booms – the fuselage and the two motor booms – are sized to balance the CoG, with any further balance maintained by installing open-cell foam pieces and subsystems. That though does not necessarily require any major symmetry in system placements or cablings.
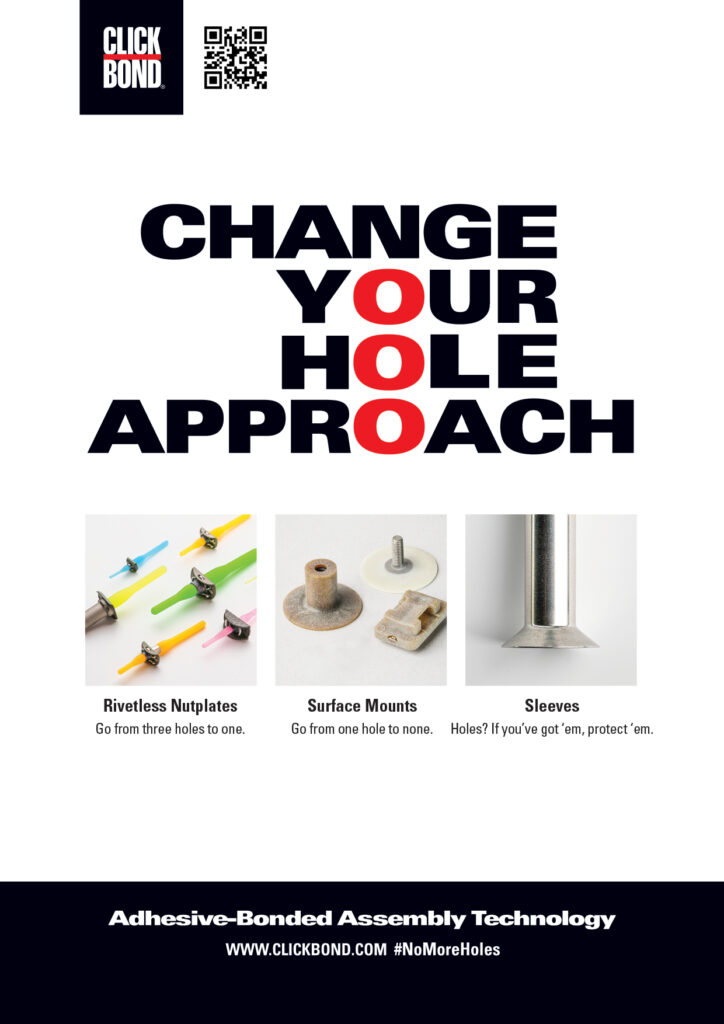
Flight management
Most COTS avionics products are unsuitable owing to the temperature ranges, altitudes and weight budget the Zephyr’s engineers must design for.
AALTO therefore assembles its flight controller and most other avionics in-house by taking delivery of COTS systems and stripping them down, often extracting individual chips and other PCB-level components and mounting them on its own weight and thermally optimised boards.
“For instance, the INS comes in a box about the size of a fist, and we remake it into something the size of a penny. Our pitot tube is remanufactured to about a quarter of its usual size, and our satcom radios and everything else are all stripped right back,” Tyler says.
“We use a proprietary master flight controller, to which most of the avionics are slaved. That controller is constructed with FPGAs around a primary CPU, with the FPGAs chosen to reduce overall power usage and processing power to just what our system architecture needs. Plus FPGAs can never get saturated, they just do their one job quickly and constantly, which is useful for avoiding faults.”
The Z8 can manage up to 1255 waypoints, spread out over 200 days or more. These can be time-bound or action-bound, for instance setting the aircraft to loiter at a given waypoint, where it might activate a 5G modem for a specified duration, check ADS-B data for traffic, or call a new GCS to attempt to hand over control. Alternatively, a waypoint can be set to expire based on the passage of time for example.
During lost comms, the aircraft can fly autonomously for up to 7 days without human input. This can be reduced depending on aviation regulators’ requirements, who may only allow for an hour or two of autonomous flight without a pilot in the loop.
The data bus from the flight controller to the navigation sensors and servos, along with the power bus, are proprietary, with SWaP optimisation being their key design focus.
“The aircraft is designed to be as aerodynamically stable as possible, which reduces the amount of on-the-fly work the flight controller needs to do,” Briggs adds. “That enables us to strip it and its network back to make them as light and low-power as possible.”
Although that right-sizing means the Z8 currently has limited processing capabilities, Tyler says he is interested in using AI at the edge in future, and forming collaborations to that end.
“We’re discovering entirely new phenomena in the stratosphere, like the behavioural patterns of gravity waves, and if onboard AI can use data from sensors capable of identifying those waves, the HAPS could intelligently avoid, study or take advantage of them depending on the mission requirements, just as we aim to in our pre-flight route planning for wind patterns.”
MEMS IMUs are taken from Advanced Navigation’s Spatial 37 g GNSS-INS and installed in the Z8’s avionics for inertial data. Briggs notes that the Zephyr’s movements and dynamics are quite slow during flight, so 1 Hz of GNSS updates is fast enough for the Zephyr’s safe flight calculations, let alone the 10 Hz typical of the Spatial product.
Different civilian and military customers are likely to have specific GNSS requirements, such as those for accuracy, robustness or security, in which case they will be integrated and redesigned where necessary. Other redesigns or supplier changes could be needed in the future to better enable certification of the Zephyr, which is challenging with the present, heavily bespoke engineering approach.
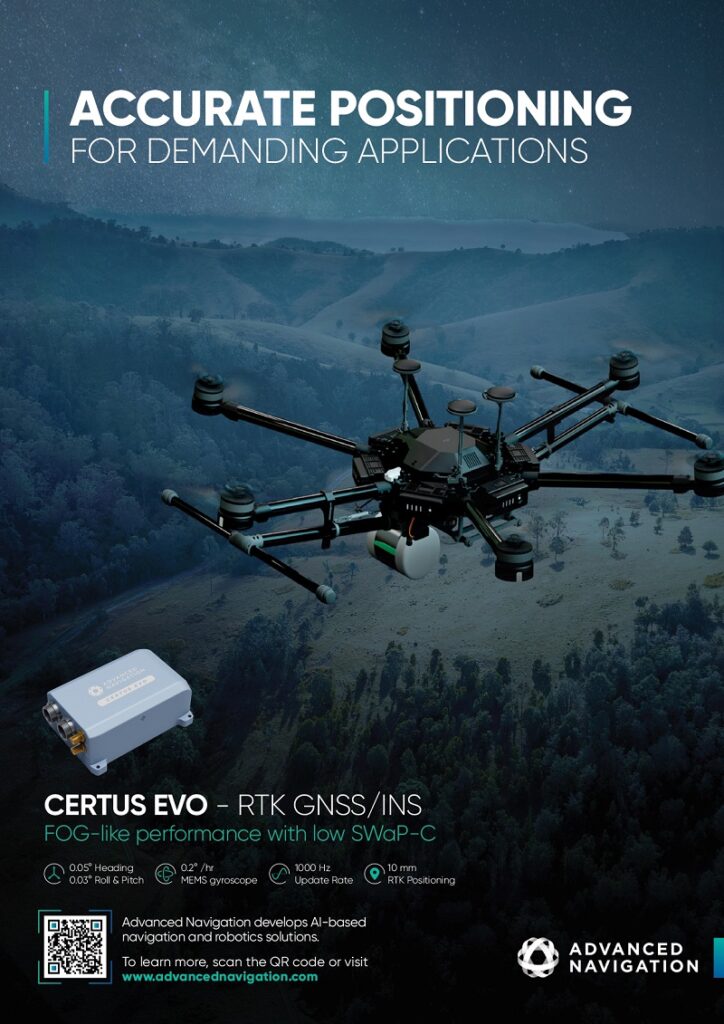
Servos
The Zephyr uses fewer control surfaces than most large, fixed-wing platforms – a rudder for yaw, an elevator for pitch and the variable thrust from the two propulsion motors for additional yaw.
Briggs and Tyler nickname the elevator a ‘stabilator’ (not to be confused with Piper Aircraft’s use of the ‘stabilator’ to describe ‘all-flying tailplane’ configurations in which the entire rear wing rotates around a shaft). While an elevator would only have one or two flaps moving within a horizontal tailplane, the Z8’s entire tailplane moves up and down.
“That means using two rotary servos, one in the rudder, the other in the stabilator, both above the tail fin,” Briggs says. “As well as keeping weight and power needs low, fewer servos means fewer points of mechanical failure. The stratosphere isn’t a kind environment, there are temperature extremes, radiation, ozone and other conditions that aren’t conducive to complex devices.”
While the servos’ power, size and weight requirements were met in a straightforward manner, the HAPS’ lengthy endurance requirements were more challenging; the Z8’s last flight exceeded 1500 hours, and future flights are aiming for 4800. The actuators are therefore tested in-house to multiple times their stated lifespan using a combination of accelerated and non-accelerated testing regimes before using them in flight.
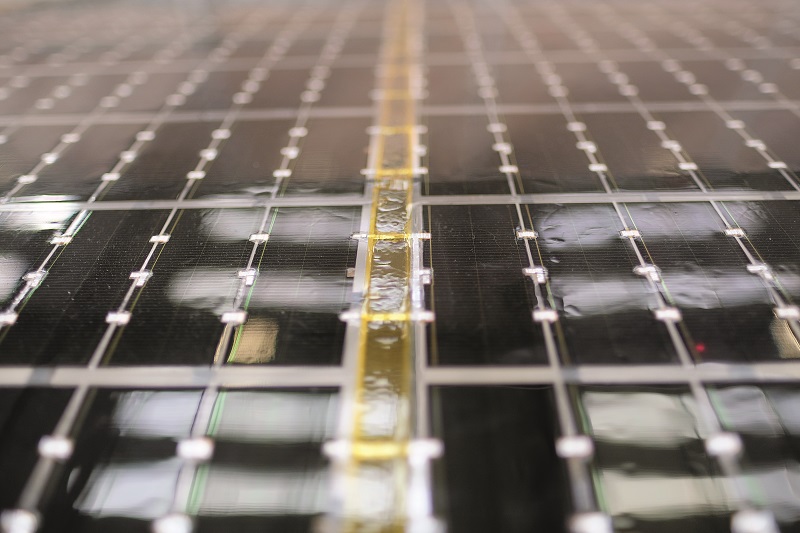
Solar power
The Zephyr’s solar panels are assembled from strings of Microlink Devices’ InGaAs triple-junction solar cell, partly for the high solar conversion efficiencies it provides at varying illumination levels and angles, which at the moment are up to 31% efficiency under AM1.5 illumination. They can absorb energy from UV, IR as well as visible light, and are just under 40 µm thick, with a mass density of below 250 g/m2. Potentially that gives just over 250 W/m2 and 1000 W/kg.
“It’s an expensive solar cell, but the panels we make from them consistently provide more energy than we need, so we don’t cover the whole wingspan with them – you can see from above that it’s only on part of the wing, shaped in strips to align with where the batteries and chargers are, and we’ll increase or decrease the solar panel area depending on where the aircraft is flying and what time of year it is,” Tyler says.
While the main wings provide the majority of power generation during the day, the dihedrals typically receive better solar coverage and hence generate more energy in the hours just after sunrise and just before sunset. The flight plan will often include specific patterns to ‘catch’ additional sunlight as the sun rises and sets.
“Flying specific, planned patterns captures more sunlight, and creates a curve of power to slowly replenish energy from one side of batteries to the other, increasing the lifespan of all the batteries,” Tyler notes.
An automated system manages the charging and discharging of the batteries – AALTO refers to this as its power system, rather than a battery management system. That includes the balancing of cells for currents, voltages and temperature, monitoring individual cells and their strings for health problems, and isolating cells and strings to pre-empt thermal runaways if necessary.
Most of the subsystems are powered by the main power bus, which can be supplied by the solar array or the batteries. The exceptions are the motors and ESCs, which are powered directly by the batteries at all times to ensure stable and consistent propulsion throughout flight.
Briggs notes, “We don’t get a lot of transients, thanks to the slow-changing nature of daylight and our onboard batteries smoothing out the power coming from the cells. The batteries are most important for moments like when we turn and face the sun, because otherwise we could suddenly get a big voltage spike from the array.”
Tyler adds, “Some careful programming and system architecture went into the ‘unlatching’ process by which we release the main bus from the batteries and attach it to the solar array, changing the flow of power. We’re able to see the sun through the clouds and the Earth’s curvature, so our ‘sunrise’ happens up to an hour before its expected time at ground level, giving the automated power system plenty of time to unlatch and start absorbing sunlight as soon as it’s available.”
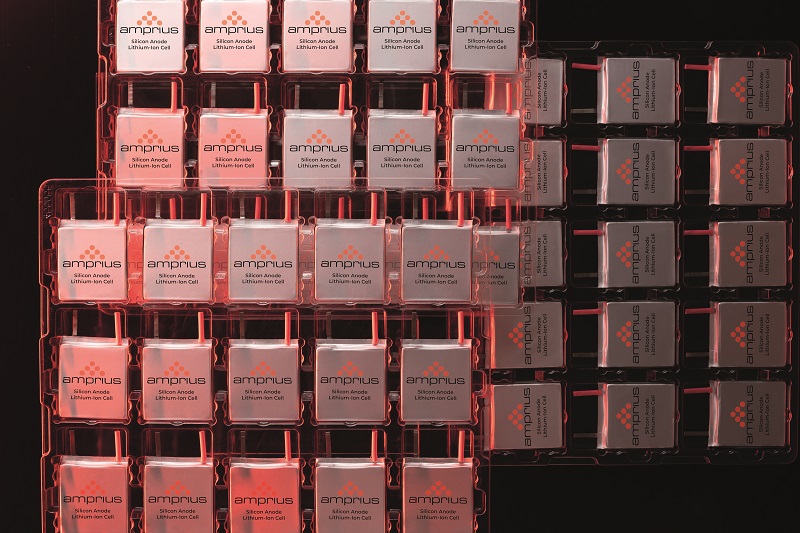
(Courtesy of Amprius)
Batteries
The batteries used in the Z8 are Amprius’ lithium-ion cells, based on the company’s proprietary silicon nanowire anode technology, to which it attributes its 400 Wh/kg specific energies. However, AALTO has announced plans to switch to the company’s 500 Wh/kg packs that were unveiled last year.
“We bond the cells using rubber bands, so as they go through their thermal profiles from day to night, they can expand and contract,” Tyler says.
“Compressing them that way is a key safety measure. Technically it also keeps them within a reasonable volume, but mass is far more of a concern for us than volume, which is why the high specific energy of the Amprius cells is important to us.”
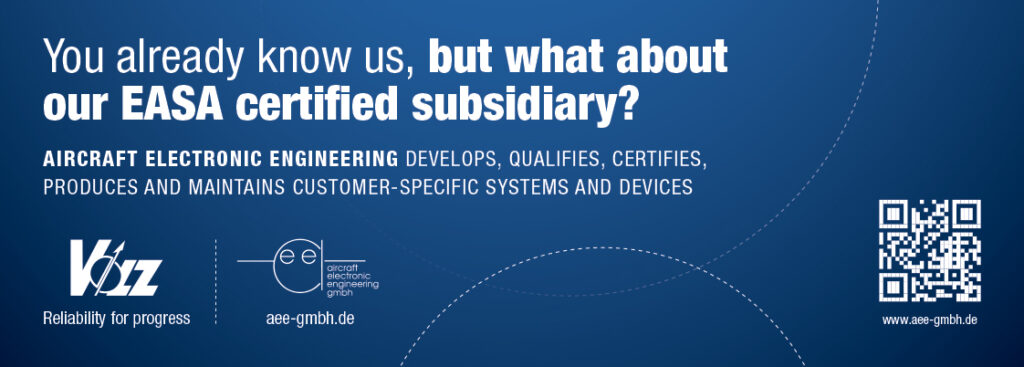
The cells are series-connected in strings, which are then connected in parallel, arranged as needed for each planned flight’s duration and the time of year.
“During the 64-day flight for instance, we had 60 strings spread across 10 packs,” Tyler explains. “We can go anywhere from eight to 12 packs, and we could have done that flight with only eight, but 10 gave us a bit more capacity and hence redundancy. If we’d had a sudden degradation in one pack, we would’ve been fine.”
Twelve packs means the highest weight penalty, so it’s a configuration reserved for missions with long night-time missions, such as providing 5G in Europe in winter. Naturally, capturing more sunlight for longer night flights will also require bigger solar panels.
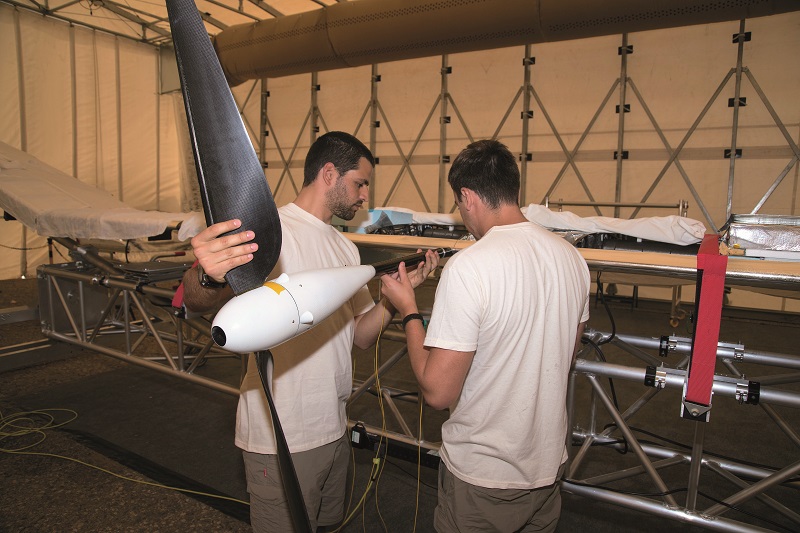
Motor drives
The electric motors resemble COTS products, but the rotors and stators are optimised for the Zephyr’s use case. Like the avionics, the ESCs are designed and assembled in-house.
“Consider that the original Zephyr designs date back to the early 2000s, to a time when the industry around electric motors for UAVs was nowhere near as mature as it is now, so you’ll understand why we’ve made our own ESCs and e-motors,” Briggs says.
“Even now though, it’s hard to imagine new suppliers who could make motors with the performance, efficiency and thermal stability we need to fly 200 days non-stop. The market for HAPS and other stratospheric platforms is not big enough for motor manufacturers to design and produce them in bulk.”
Tyler adds however, “At peak climb, the motors produce just under 1 kW, and at cruise they’re normally at half that – not much power for a 75 kg aircraft. In the stratosphere, It’s nice and cold for the e-motors, especially since they’re not getting anywhere near the solar exposure of the wings, and there’s no moisture or dust ingress. That makes engineering them a bit easier.”
The propellers are designed for flight in the low air densities of the stratosphere, so they have coarser pitches than most UAV props. Tyler comments that hand-launching the Zephyr to glide on its wings is necessary partly because launching it using propeller torque alone would be quite time-consuming, as it is not optimised for ground-level air densities.
At cruising heights, they are run at about 2000 rpm; near the ground they spin at just 500-600 rpm. Briggs notes that finding a carbon composite manufacturer capable of the geometric tolerances, stiffnesses and various other parameters needed for the props was extremely challenging.
“The process of manufacturing them is complex, and once they’re delivered you need to test every propeller to make sure they all perfectly match each other in performance,” he says.
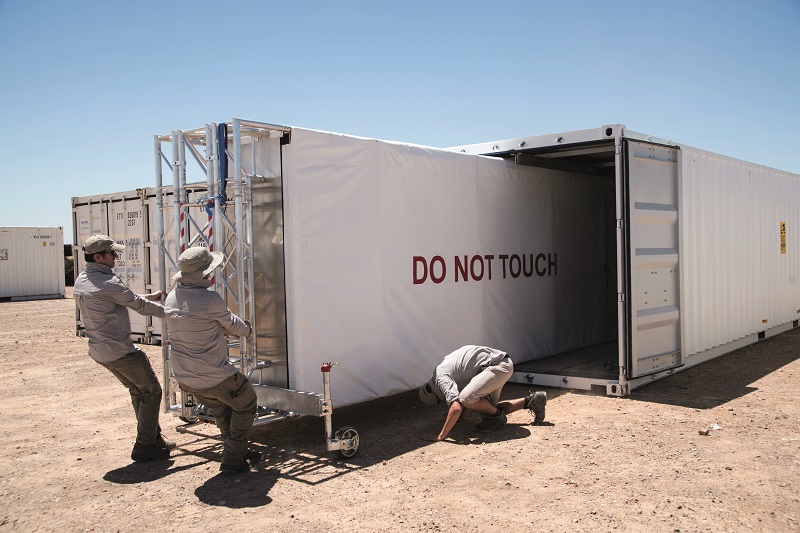
Launch
Confidence of a successful launching depends not only on tests in the factory and at launch sites, but also on preparatory steps such as in-depth meteorological checks aided by radiosondes.
“If we see something huge like a hurricane in a test flight’s area, we’ll leave and return in a couple of days – but obviously, we’re not going to consider taking away someone’s connectivity service when they need it most,” Tyler says.
“Flying above hurricanes will be key for that, so we’re working on some updates for slightly reduced weight, higher battery energy density and higher continuous altitudes.”
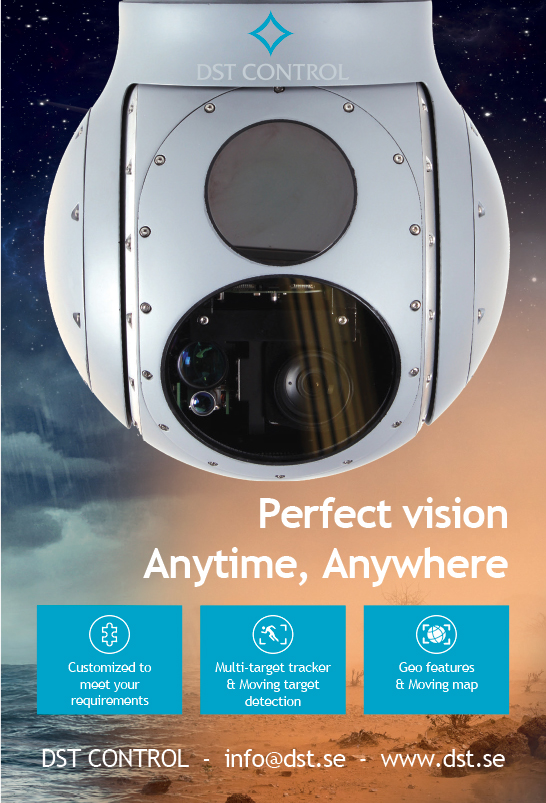
Two Z8 airframes can fit side by side in a standard 40 ft shipping container (each disassembled into a specialised holding frame designed in-house) that can be couriered to most locations around the world.
“The avionics and most of the subsystems will already be in the wings before loading the containers,” Briggs adds. “We’ll also ship our containerised ground station and usually another container full of spare parts and key ground support equipment.”
Once on site, the various components are unpacked, and the GCS, rovers and cells for testing and battery conditioning are connected to power. Although often dubbed a ‘solar-powered aircraft’, Tyler quips that since the Zephyr’s batteries are pre-charged using grid power, it is more accurate to call it ‘almost entirely’ solar-powered.
Once charged, the batteries are installed in the main wings and dihedrals, and the aircraft is bolted together. Tyler estimates that the HAPS will sit on the runway for an hour of pre-flight checks and orientation to face into the wind as much as possible.
Underneath the wings are several handles for five launch personnel to grip and hoist the aircraft. Once the motors are spinning, the crew takes around 10-12 paces before letting go. After it reaches a few metres/second, the wings generate lift, and for the motors and propellers initiate the climb.
“We’re working on a launch system for greater automation, but we have to consider the different environments they might be used in, to ensure they’ll operate from sea level up to 7000 ft. That mandates a wide range of launching speed and distances,” Tyler comments.
The ADS-B Out and In systems are vital for tracking and identifying other craft and their trajectories during ascent. In the event of data link congestion or losses, the flight controller will automatically toggle onboard radios to hop between frequencies.
To cover all air traffic requirements, the Z8 integrates the ping200X transponder from uAvionix as its Mode S transponder with extended squitter (and hence ADS-B Out) for transmitting its ID, GNSS position, altitude and velocity. ADS-B In receives data on the nearest targets, and issues any necessary avoidance manoeuvres during ascent or descent.
Links are also encrypted to guard against spoofing or replays of the Zephyr’s own data in comms or GNSS. Counters are designed into the flight controller to ensure the comms and navigation data from the multiple onboard sources all match up with each other, with no sign of anyone forcing a replay of a command the GCS crew might have sent, such as a 180o turn made to avoid an issue ahead.
“And we can fall back on IMU dead reckoning at times; we’ve tested that a lot,” Tyler muses.
“One of the joys of occasionally working on US military ranges is that they start trying to jam you. We’ve had situations before where we experienced periods of lost comms, and learned over the phone that ‘some guys were doing some testing’, but we were able to switch frequency to resolve the issue, but then rapidly lost comms again. That’s kept us on our toes and given plenty of opportunities to prove how the Zephyr can keep operating safely without us, if required.”
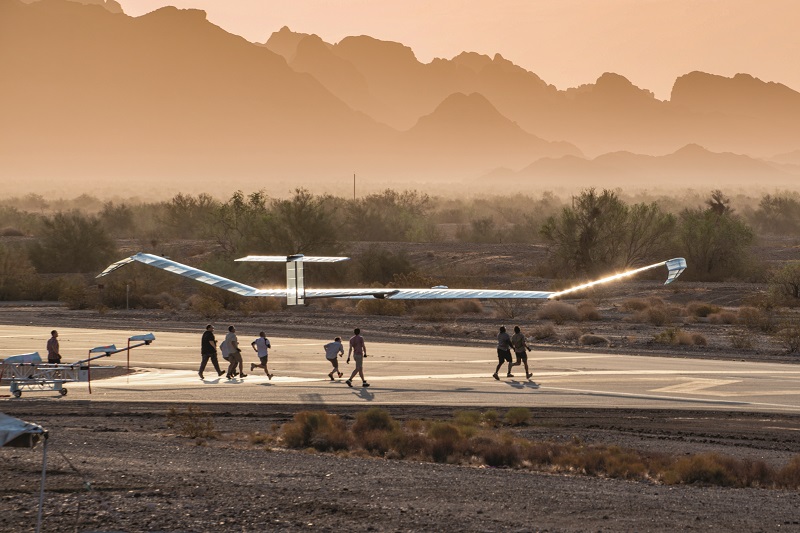
Flight operations
At the time of writing, 75,000 ft was the peak barometric altitude set by the Z8, with 76,149 ft being its peak measured GPS altitude. Indicated cruising airspeed during operations hovers around 16-17 knots, “That seems absurdly slow, but as we fly higher, our true airspeed increases relative to indicated airspeed, and as such, generally our ground speed increases too,” Tyler says.
“If there’s no wind, we’ll actually cruise at somewhere between 50 and 60 knots ground speed, which means we can cover 1200 miles per day. That’s how the aircraft managed to fly from Yuma in Arizona to Belize within the month of July 2022.”
For solar efficiency, most flights have been near the equator, although AALTO will serve other latitudes, the limiting factors being the shortness of the day and the length of the night.
The aforementioned surplus energy generation from the solar cells means that in daylight, the Zephyr climbs while charging its batteries.
At night, when the sun and solar recharging are absent, it draws power entirely from its battery stores and descends, reducing the power drawn by its motors and shifting some of the flight burden to its wing-generated lift.
The Zephyr can therefore operate wherever there is enough daytime to climb and charge for long enough for full coverage of the subsequent night-time energy needs.
Tyler points out however that most of the world’s population lives closer to the equator than the poles, and that the Zephyr does not need to launch precisely where it will be operating.
As it can cover nearly 2000 km each day, it can circumnavigate the Earth within 21 days, although as wind is used when maximising flight speeds, flying in a straight line from a launch point to a mission location will sometimes take more time than travelling in a physically longer route around the planet.
As mentioned, AALTO’s record is a 64-day (plus 17 hour and 43 minute) flight from June to August 2022, from Arizona to Belize. This was 3 hours shy of the world record for the longest flight of any aircraft, and beat the UAV’s previous endurance record by over 150%.
The flight accumulated a huge amount of engineering data and took over 4500 photos in a single day, until a large thunderstorm formed, covering the entire operating area for the Zephyr. That caused severe turbulence and led to the failure of a motor, rendering the aircraft unable to avoid the storm and maintain safe flight.
“The objective of the flight wasn’t to break records though, it was to demonstrate the platform and the payload capabilities to our customers, and to continue development and advance the maturity of our technology,” Tyler notes,
He adds that it was also the first of any HAPS in both the US National Airspace system and International
Class A airspace, commercial and military aircraft continuing to operate below the Z8 all the while.
Two GCSs monitored the flight from Yuma to Belize, tracking its navigational path. This steered clear of populated areas, as per regulators’ wishes and to ensure the craft could be brought back down or terminated safely in the event of a system failure, although safety manoeuvres such as loitering patterns were triggered in areas such as the Yucatan coast to avoid some tropical storms that were building nearby.
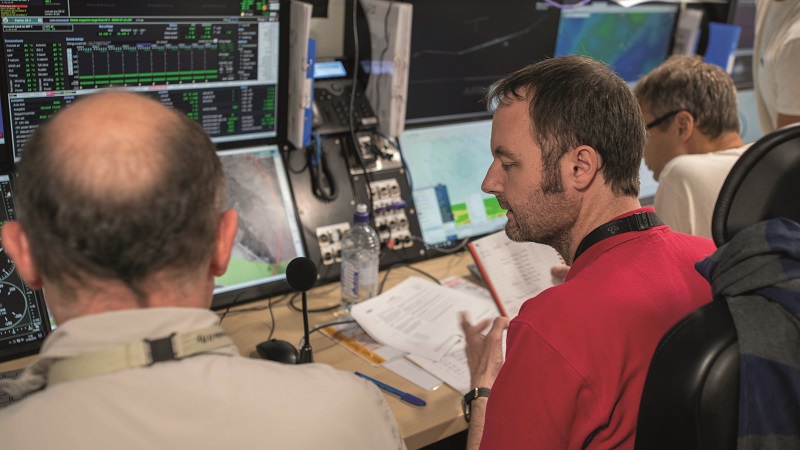
operating centres for monitoring and handing over Zephyr missions
From GCSs to SOCs
Inside the shipping container are two operator stations.
Both link independently to the aircraft via ground data terminals, each one being designed with the capability to control up to four UAVs at once, although tests so far have maxed out at controlling two Zephyrs simultaneously from a single terminal.
In practice, AALTO will not dedicate one GCS to more than four Zephyrs, to maintain full redundancy. If one operator station should break down, the other will be able to control all four aircraft.
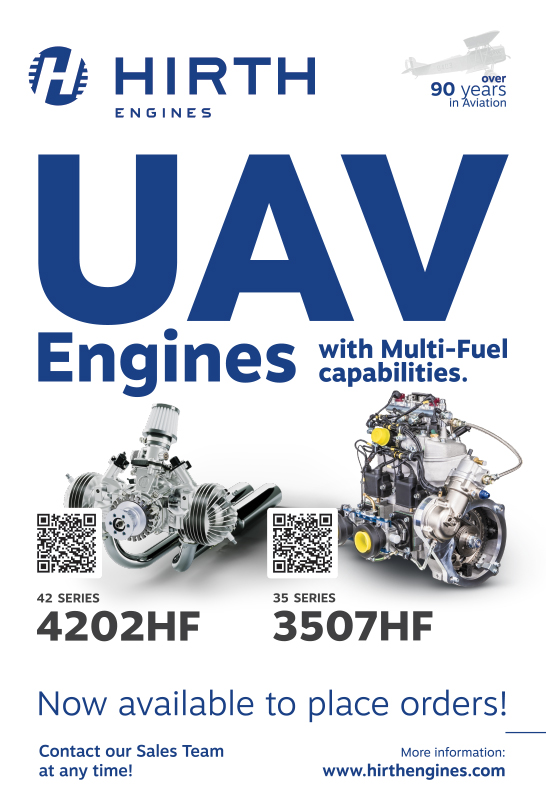
The GCS crews monitor air data, battery and power distribution data, along with video feeds from the wing cameras.
Any control signals are sent over satcom either as short-burst data messages or streaming calls if higher data rates of 2.4 kbit/s are needed. Data encoders in AALTO’s flight controller are key to compressing the commands and the system-wide telemetry.
Between the two operator stations is a mission planner console. While operators monitor and control the aircraft as needed in real time, the mission planner tracks and confers with the operators on parameters likely to affect the HAPS and mission in 3-7 days’ time.
“Our future GCSs will evolve into a network of Strategic Ops Centres [SOCs], from which we’ll initially carry out stratospheric operations only, but as mentioned we’re looking into automating launches and landings to perform those remotely too,” Tyler says.
“The SOCs will then be where we remotely monitor and hand over control of the Zephyrs, and we’ll set up SOCs in different time zones so that AALTO crews and interested parties can stay in their own time zones and work their regular shifts.”
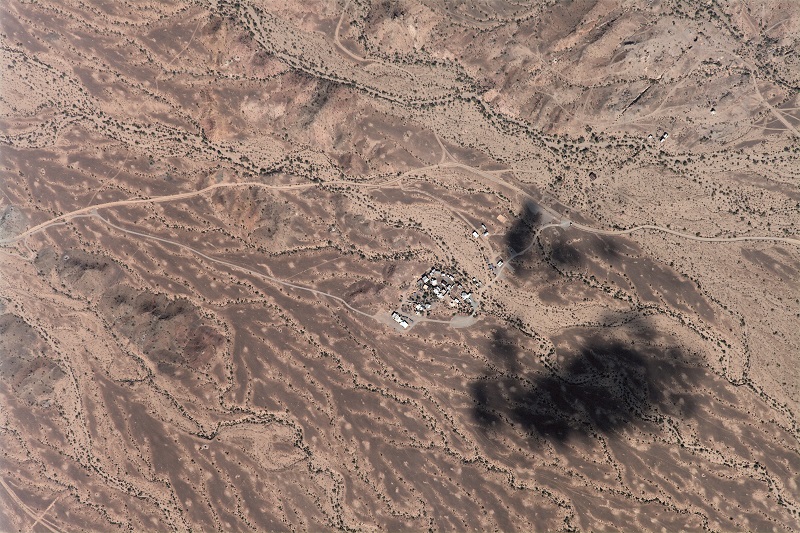
Payloads
A payload controller board installed among the avionics near the fuselage routes command signals and power to the payloads, although as mentioned customer payloads can be comms-independent. Hence they can connect just mechanically and electrically to the UAV, with separate data links from the Zephyr’s.
“Of course, you’ll generally want optical payloads in the nose, but things like comms relays could be mounted anywhere,” Tyler says.
Generally, Briggs adds, “Customers often get a bit worried when we give them a weight budget and their payload exceeds it. But we have ways of stripping the casings off payloads and adding lightweight insulation and heat transfer materials, along with other steps as part of our payload integration service.”
AALTO’s own in-house payloads include its previous OPAZ developments in live 4K video capture and streaming, as well as newer ones relating to connectivity. At the moment, the company’s payloads can capture EO imagery accurate to 18 cm/pixel and IR images at 70 cm/pixel at cruising height.
In addition to demonstrating D2D capabilities in the past – with the ability to cover 7500 km2 of ground while in flight, equating to 250 terrestrial towers – AALTO will be showcasing and demonstrating comms relay payloads as mature D2D solutions in flights over the next year.
“We’ve flown other payloads including IR cameras, Lidars, air-to-air optical comms systems as well as laser comms for air-to-air, air-to-ground, and air-to-orbit,” Tyler comments.
“Lasers present a huge opportunity in the future for high-bandwidth comms, and there are now good targeting systems for beaming directly from the ground to aircraft. Their full commercial readiness is still some way off, but we’re also starting to look at lasers for delivering energy and replenishing the Zephyr’s batteries.
“We’re not yet developing those in-house, but a year ago we weren’t even in the comms business. Since then, we’ve demonstrated airborne D2D radios – D2D being something even Starlink can’t do yet – so we’re interested in bringing in new ideas of what we could fly on the Zephyr one day.”
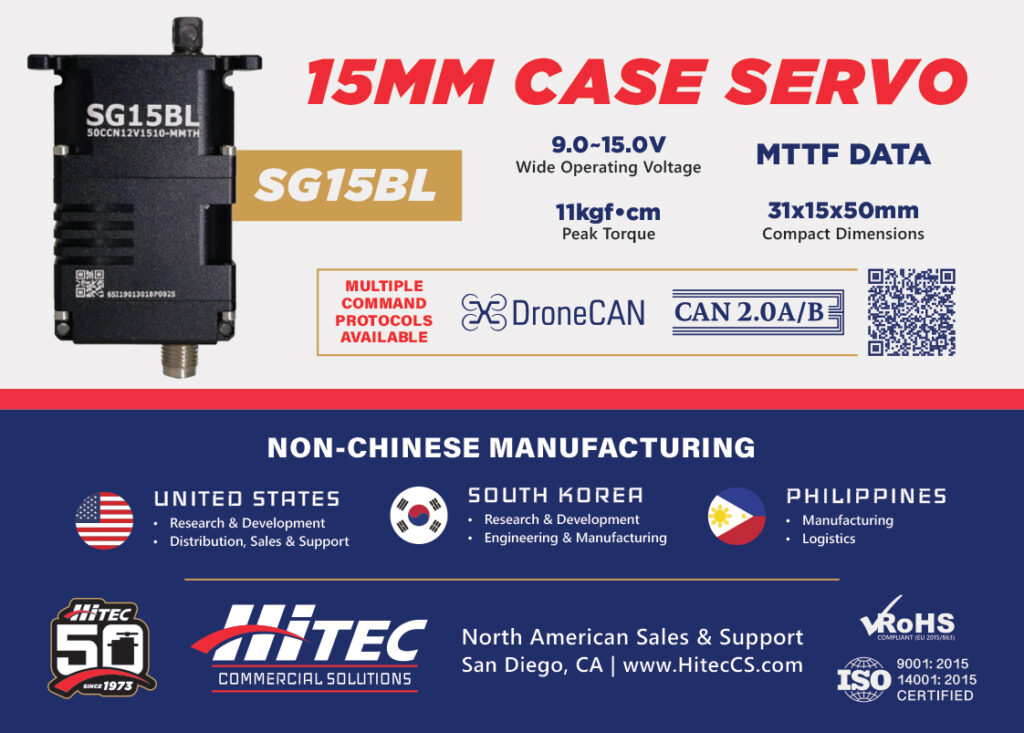
Landing
To end a mission, the Zephyr glides down to its recovery runway (tarmac is preferred but dirt is acceptable) and conducts an automated belly landing, stopping within 5-10 m of touchdown. Its lightness and low near-ground speed minimise its inertia, so a technician could stop the HAPS with one hand if needed.
Descent takes about 18 hours – a while longer than ascent – owing to the Zephyr’s gliding efficiency. Although this could be accelerated using extra servos to pitch harder, AALTO sees these as unnecessary weight as they would only be used for the final hours of a 200-day flight. This is also why Zephyr has no landing gear or wheels.
Once landed, the HAPS is hoisted from the ground onto a trolley, taken inside a containerised workshop, inspected and dismantled for shipping.
“As well as setting up SOCs, we’ll also have a worldwide network of ‘AALTOports’ in the future, with runways, personnel and facilities for all landing and post-recovery tasks,” Tyler says.
“Between SOCs and AALTOports, we’ll also plan out global ‘sanctuary areas’ away from airways and populations where we’ll terminate a HAPS if it suffers a fundamental issue or can’t re-establish a data link. And if we are coming down, we squawk 7400 to ATC from our transponder – that’s now globally accepted as the uncrewed aircraft issue code.”
If a fire breaks out at a GCS or AALTOport, and the crew does not have time to hand control to another team, the crew members can send it to a safety waypoint, and the craft can then set and follow up to over 200 further waypoints while waiting for its next order or landing clearance.
It also has numerous time-based safety actions, such as calling a specified back-up GCS and team after 30 minutes of losing a link with its operators to establish a new satcom link.
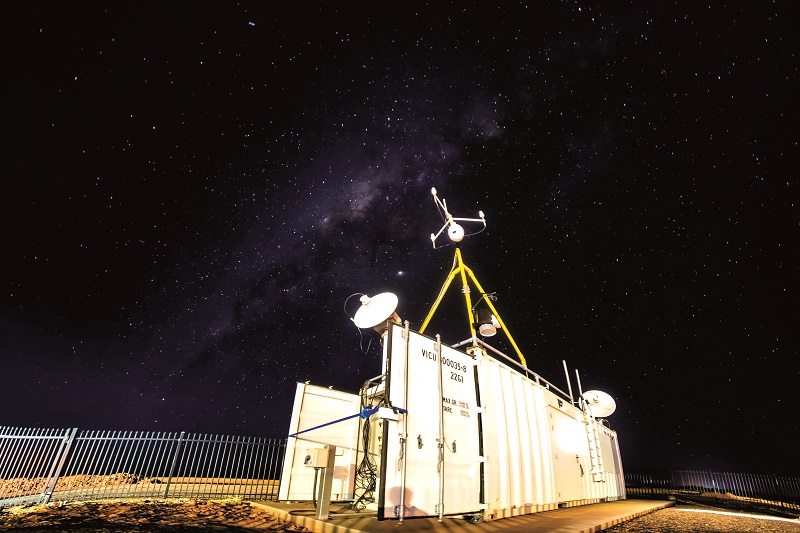
Data links
For LOS comms and telemetry including high-rate video streaming within a second of delay, the Z8 uses radios designed to operate at UHF (300 MHz to 3 GHz) and S-band (2 to 4 GHz). These work at around 10 Mbit/s until ranges of 150 km between the HAPS and GCS are exceeded.
“Our BVLOS and LOS links can be separated,” Tyler says. “We could monitor and occasionally control the aircraft BVLOS from Farnborough, even if it’s surveying over a remote disaster site or warzone and beaming live video down to somewhere nearby.
“Frequency approvals primarily define what radios and bands we won’t use. The S band is widely used commercially, which means we can easily find we’re coming within range of another vehicle or organisation using it and hence risking link loss or congestion. But as mentioned we have safety back-ups in place for that.”
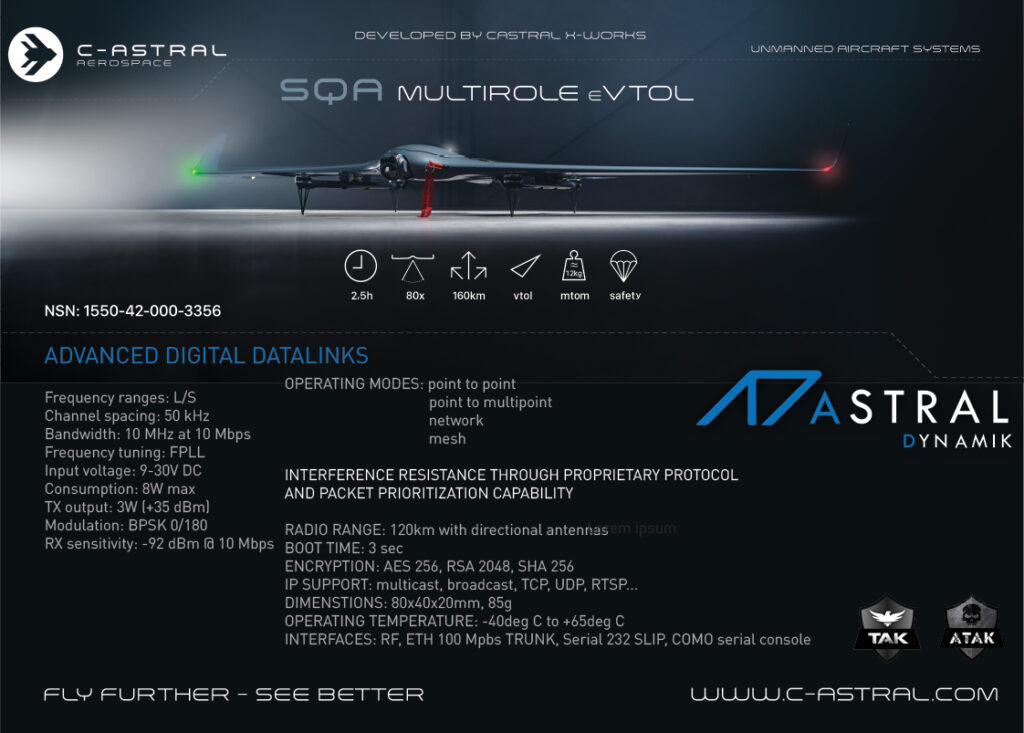
The UHF radios are able to hop between different frequencies within the band, and avoid specific ones depending on the mission profile. Tyler reports that AALTO was asked not to use three UHF frequencies in particular during a flight earlier in 2023.
“The overarching goal is to be able to beam high-rate data from anywhere on Earth, and we’re not far off from that, especially if we look into adopting mesh radios in the near future,” he adds.
“Meanwhile, the positioning of our S-band dipole on the fuselage tail means it generates no turbulence, and the UHF antenna sticks out of the trailing edge of the wing, also conforming aerodynamically, and with either omnidirectional antenna covering the others’ ‘null’ point for consistent GCS comms.”
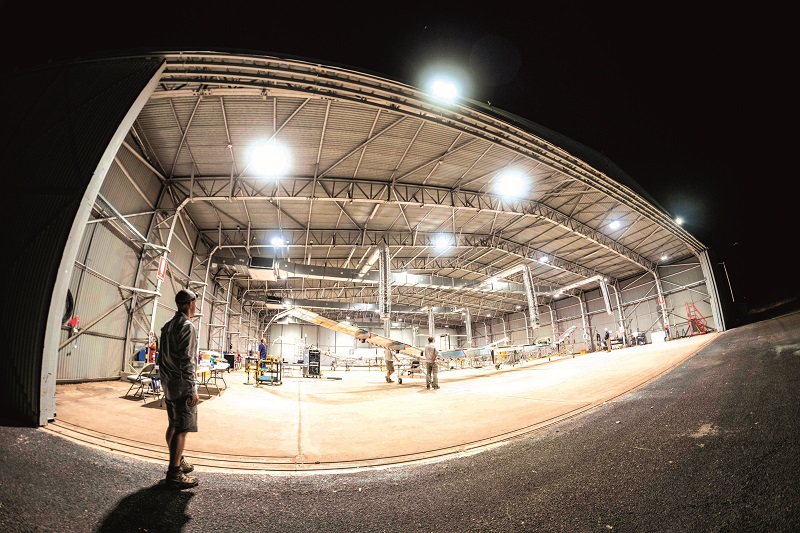
Type Certification, while keeping an eye out for new technology as it grows
Future plans
AALTO anticipates serving markets across Africa, the Middle East, India and South America, as well as Australia and North America, although it is also in talks with prospective users in Japan and elsewhere.
“Those include persistent and ad hoc connectivity for civil work such as disaster response and military applications like ISTAR,” Tyler comments.
“When Zephyrs aren’t actively working, they can loiter in the stratosphere for months at a time. They can then take over for others that are reaching their 200-day maintenance intervals or showing signs of faults, to sustain 5G coverage or persistent monitoring.”
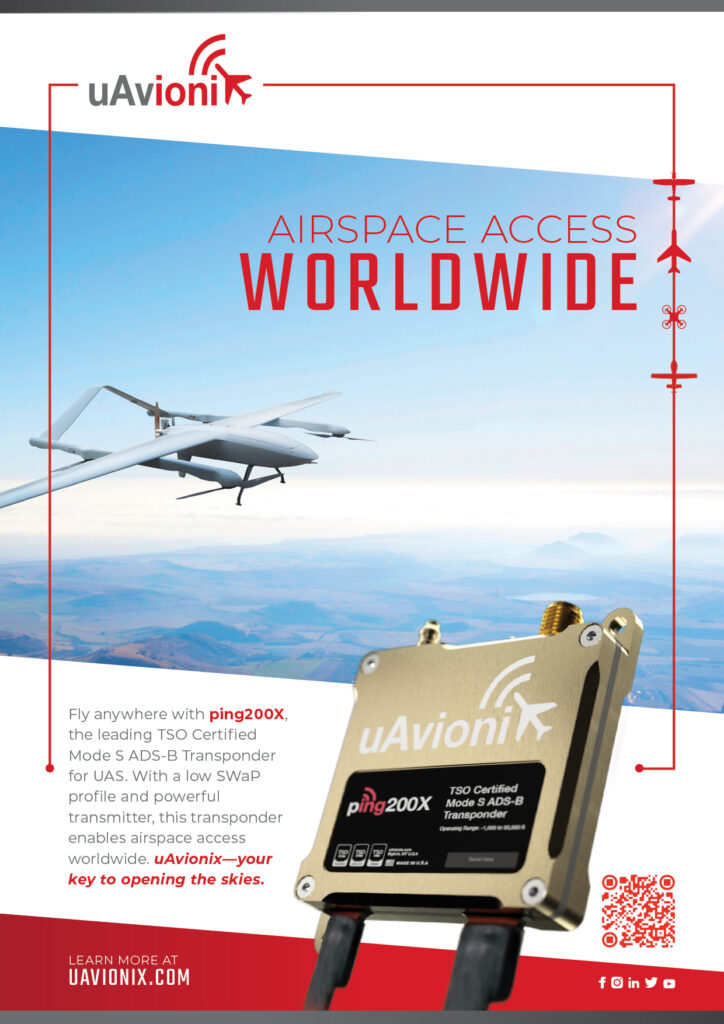
AALTO also remains aware that it has gathered a large and valuable body of stratospheric data, and is debating internally how best to offer it, and how the Zephyrs can gather more of it, to organisations such as NASA.
“We’re also working on the next version of the Zephyr, which will be designed more for manufacture,” Tyler says. “Our development roadmap has us freezing the configuration of the Zephyr next year for the next stage in the Type Certification process.
“We’re working closely with the UK CAA for the Type Certification, and as a new Type it’s going to come with a lot of new lessons for us all, particularly given how we just don’t fit into any existing category of uncrewed system.
“Thankfully though there’s a growing portion of industry starting to cater to the uncrewed HAPS industry, and that is bringing new kinds of electronics and batteries along together with other novel inventions that are very suitable for our purposes.”
Specifications
- AALTO Zephyr 8
- Fixed-wing UAV
- Solar-electric
- Wingspan: 25 m
- Length: 8.5 m
- MTOW: 75 kg
- Empty weight: 25-30 kg
- Payload capacity: 45-50 kg
- Endurance: 200 days (theoretically unlimited)
- Cruising speed: 50-60 knots
- Launch and landing speed: 4-6 knots
- Maximum barometric flight altitude: 75,000 ft (22,860 m)
Some key suppliers
- Solar cells: Microlink Devices
- Batteries: Amprius
- Transponders: uAvionix
- Carbon fibre: Formtech Composites
- Electric motors: Newcastle University
- GNSS-INS: Advanced Navigation
UPCOMING EVENTS
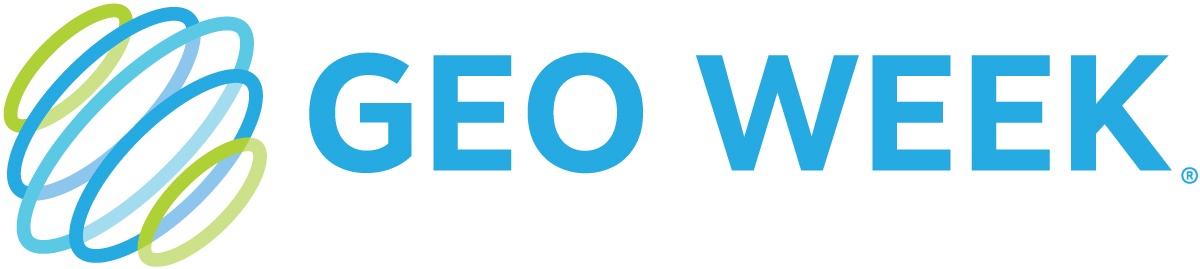
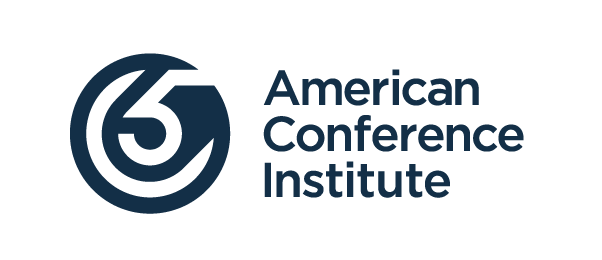
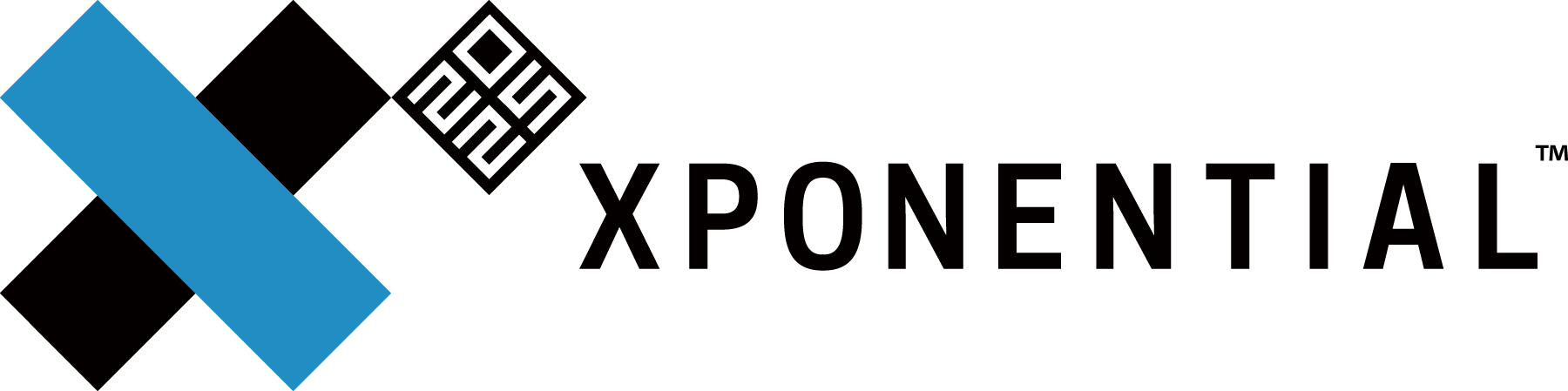
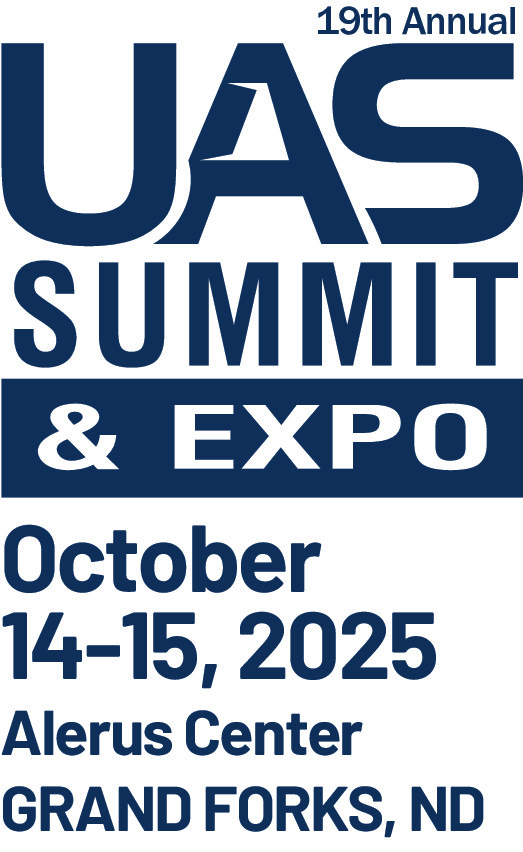
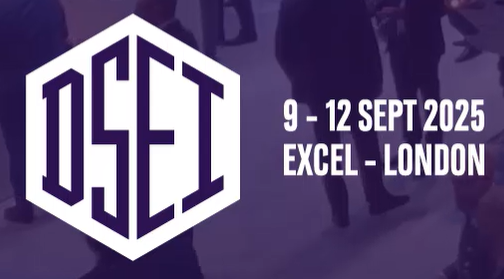
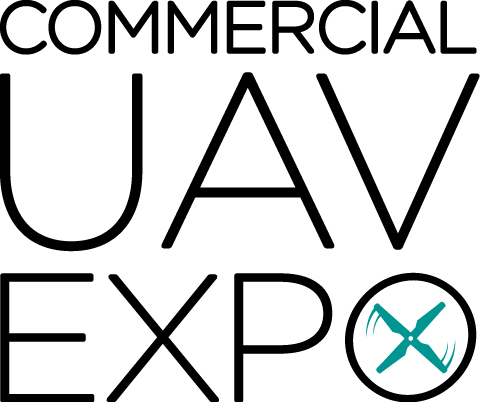
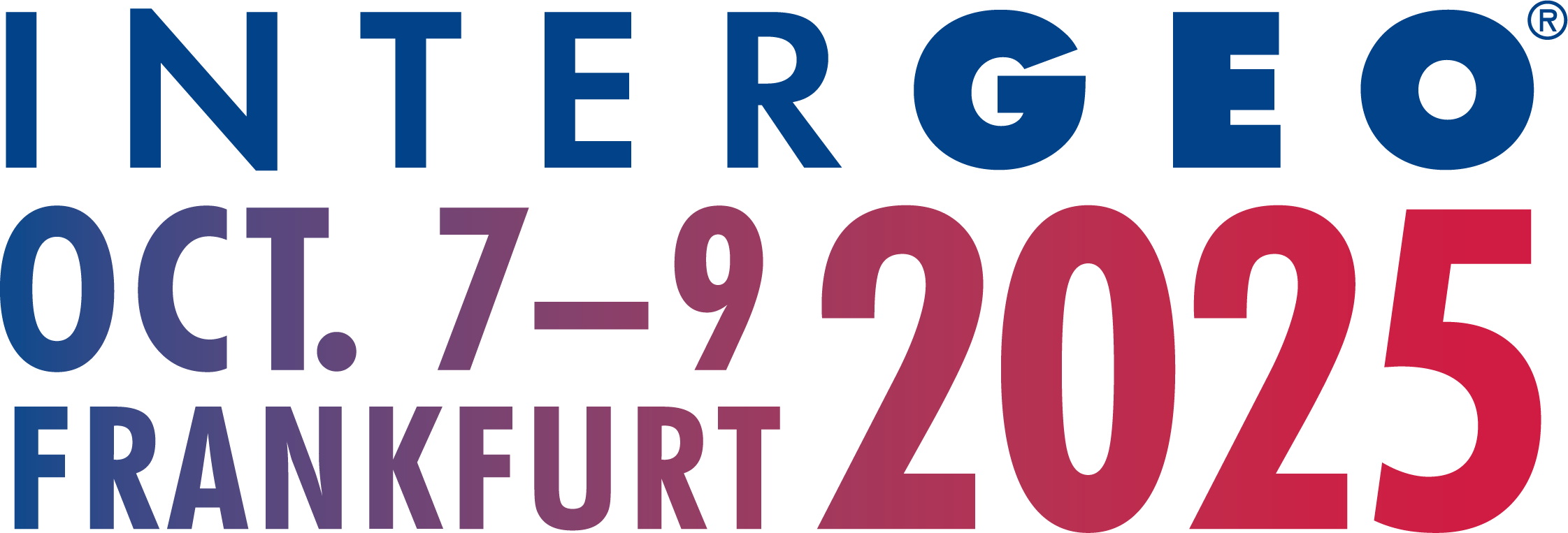
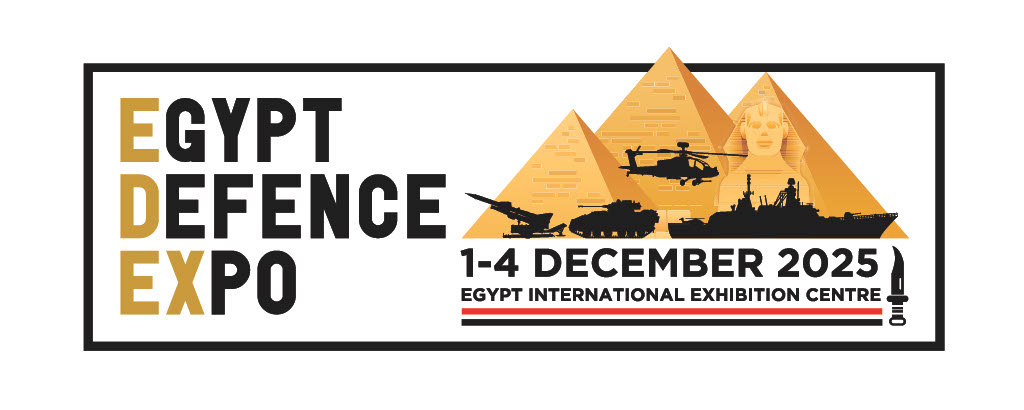
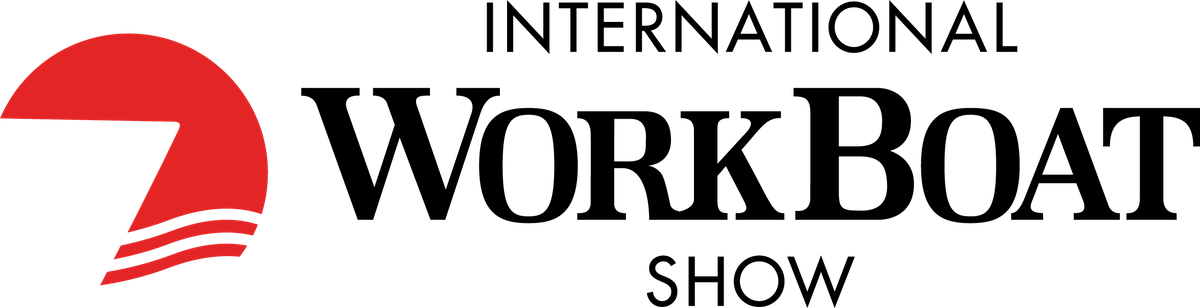
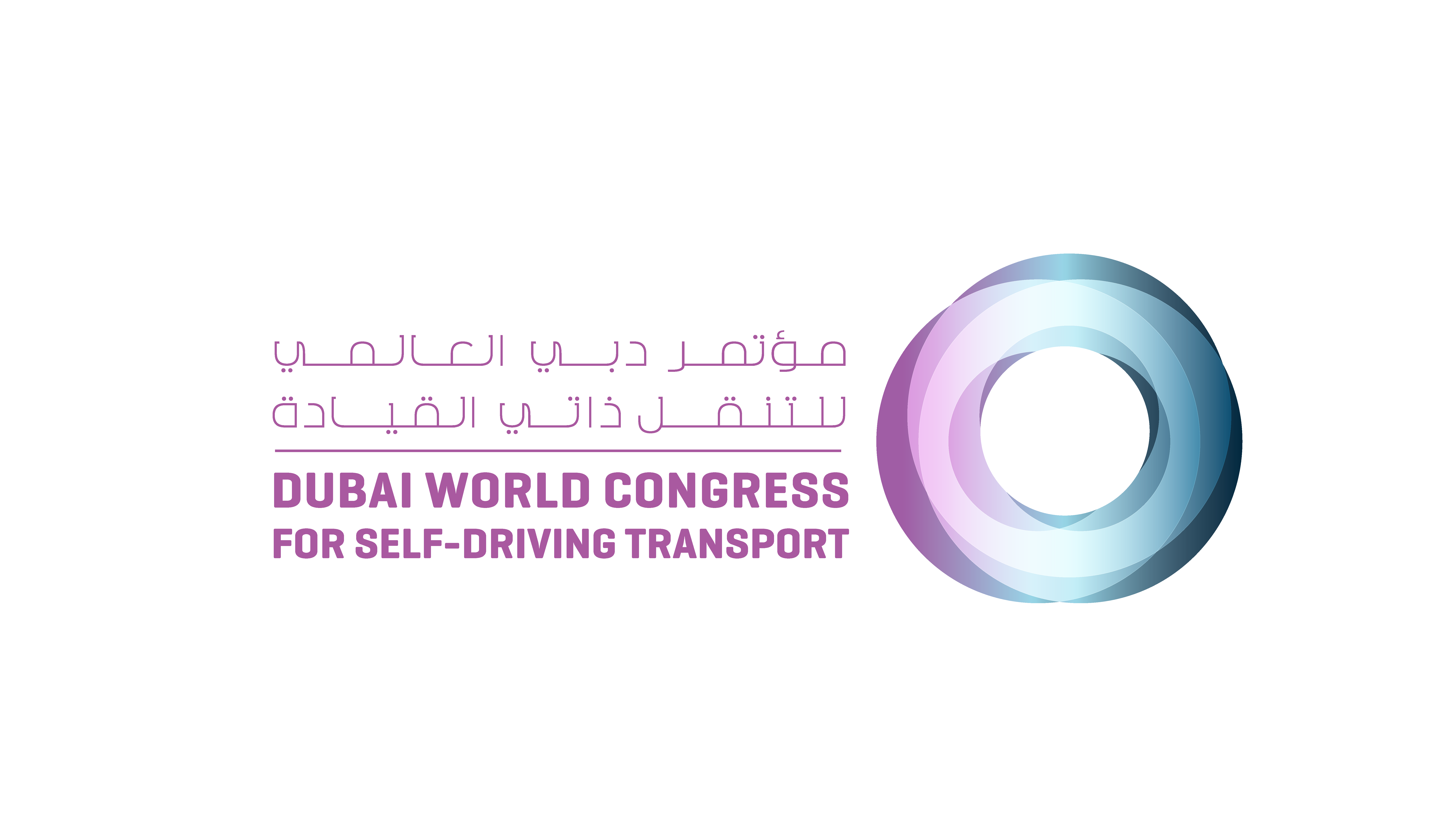
