Event 38 E455
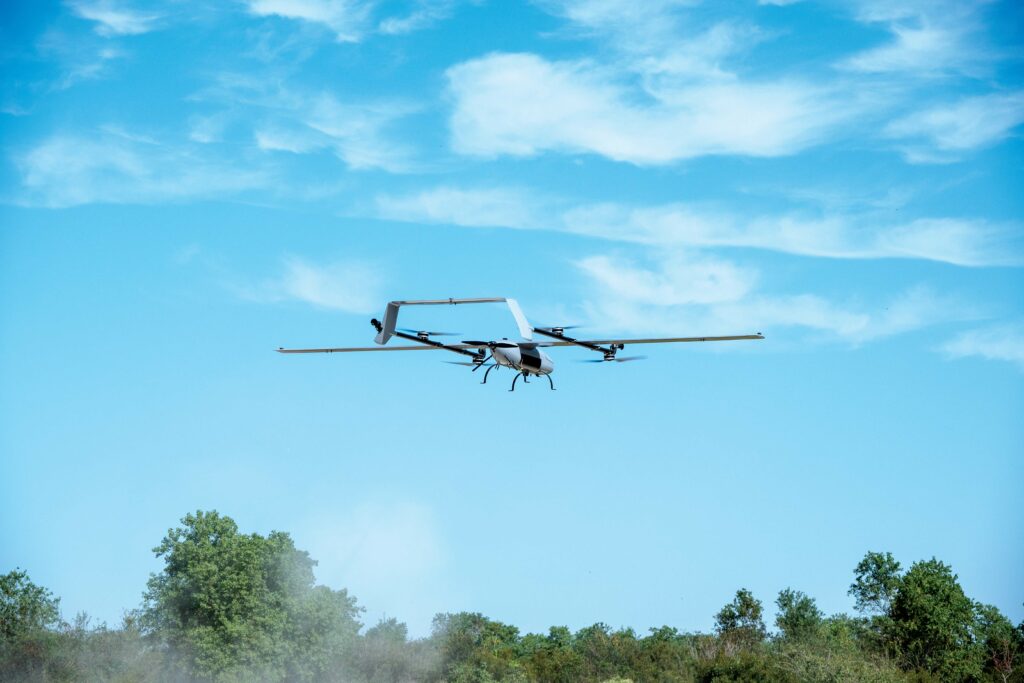
PAU patrol
Peter Donaldson gets the measure of a record-breaking pipeline survey by US-based, Event 38’s E455 fixed-wing VTOL aircraft
Experienced commercial UAV operator Phoenix Air Unmanned (PAU) announced in early January that it had used a single Event 38 E455 fixed-wing VTOL aircraft to complete a 320 mile pipeline patrol in just 7.6 flight hours for Shell Pipeline Company.
Conducted under a beyond visual line of sight (BVLOS) waiver, the operation exceeded the project goal of proving that 300 miles of pipeline can be effectively patrolled by a single UAS in one day.
Founded in 2014, PAU is affiliated with the Part 135 air carrier Phoenix Air Group, which is recognised for its deep-rooted commitment to safety in crewed aviation. Specialising in utility inspection services, PAU has a track record of conducting more than 16,000 miles of uncrewed linear infrastructure inspections. Their extensive BVLOS operational experience, coupled with comprehensive US Federal Aviation Administration (FAA) authorisations and waiver expertise, and robust project management capabilities, contributed to PAU becoming the first registered operator to achieve the International Standards for Business Aircraft Operations (IS-BAO) Stage 1 for remotely piloted aircraft systems in 2021.
William Wheeler, director of operations at PAU, and Jeff Taylor, founder and president of Event 38 Unmanned Systems, developer of the E455, take us through how they prepared for and conducted the record-breaking mission, and provide insights into the capabilities of the vehicle and its equipment suite.
Wheeler explains that PAU holds a Part 107 BVLOS waiver for two aircraft, including the E455. “PAU’s waiver is nationwide and not limited to the section of pipeline chosen for this inspection project.”
With such a long flightpath, airspace deconfliction and coordination is potentially a complex problem. However, it was made simpler with the use of infrastructure shielding as the primary means of risk mitigation, Wheeler notes.
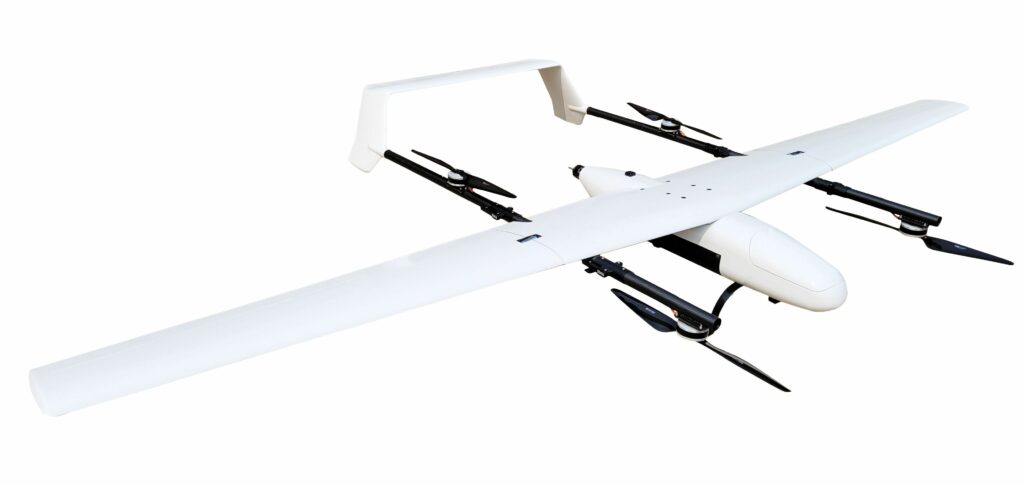
A shielded operation is one in which the UAS has right of way in a volume of airspace “that includes 100 ft above the vertical extent of an object or critical infrastructure and is within 100 ft of the same obstacle or critical infrastructure,” according to the US FAA.
In the Shell pipeline mission, PAU flew the E455 at 250 ft above ground level (AGL). The aircraft also had an Iris Casia three-camera system, with video live streaming back to the company’s electronic observer (EO) station. “This allows ground control to see the airspace around the drone in real time,” Wheeler says.
He emphasises PAU’s commitment to extensive mission planning, averaging a 4:1 ratio of planning hours to flight hours. The company’s planning process includes careful selection of launch and recovery sites, a risk mitigation strategy, review of command and control link coverage maps, and BVLOS waiver compliance verification. “For this particular mission, PAU also spent considerable time planning the logistics and routing for their operations support vehicles for a cumulative 700 miles of driving. Customer GIS data were used for aircraft route verification.”
The waiver stipulates that the ground crew should include a minimum of two pilots and two EOs. It was the latter who conducted pre- and post-flight data analysis while, at various times throughout the mission, additional crew members, technical advisors and observers provided support.
During the mission, the data transfer process consisted of a live video feed over an LTE cellular connection. Wheeler explains that the integration of the Elsight Halo allowed ground crews to control the NextVision DragonEye camera and verify data quality visually in real time.
Elsight’s Halo is a connectivity platform designed for BVLOS operations in particular, aggregating multiple communications links including cellular (LTE/5G), satcom and other RF systems to provide reliable and robust connections. The Halo system aboard the E455 is part of a bonded radio solution designed to maintain ground control through seamless connectivity at all times—a solution that includes a Silvus point-to-point connection alongside the Elsight LTE connection. The system automatically defaults to the strongest connection at any given moment.
“PAU executed one hand-off per flight,” Wheeler says. “This generally occurred fairly early in the flight, ensuring better continuity by having one crew monitoring the flight for as long as possible.”
The NextVision DragonEye is a stabilised dual-sensor EO/IR zoom camera weighing 125 g and measuring 40 × 40 × 65 mm. For this mission, video from the camera was reviewed in the field, Wheeler says, explaining that—under the terms of its BVLOS waiver—PAU is authorised to pilot the aircraft remotely from an off-site location, and to control on-board cameras and review incoming data remotely. The visible-light camera provided images with resolution of 1280 × 720 pixels, whereas the resolution of the thermal camera images was 640 × 480 pixels. Event 38 and PAU selected the DragonEye for its lightweight design, crucial for missions carrying significant onboard equipment, and its proven capability to detect targets relevant to right-of-way inspections.
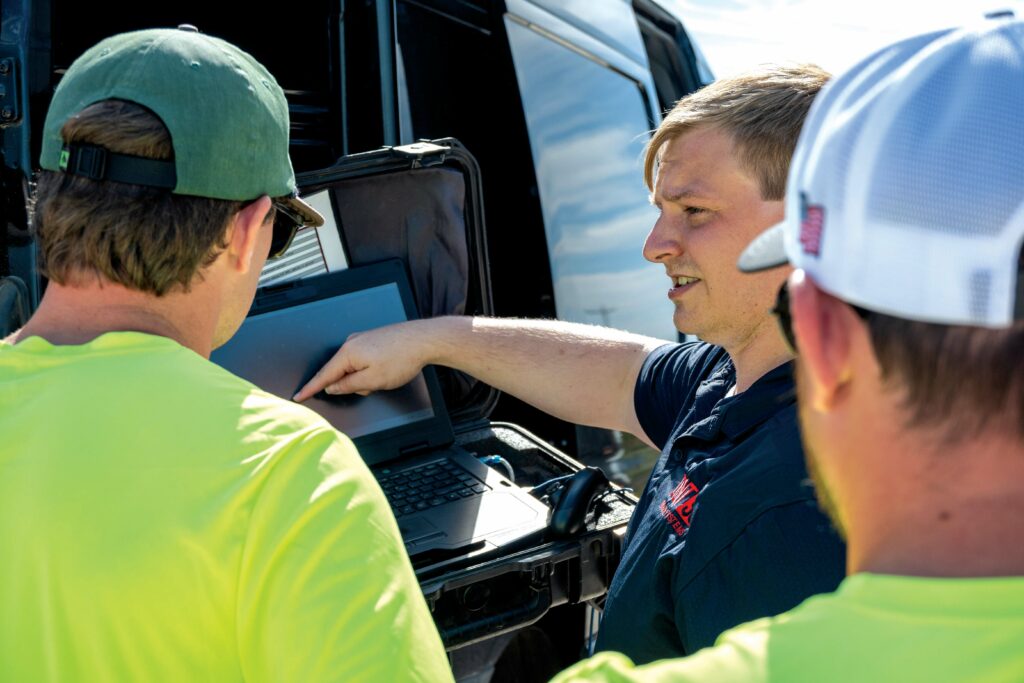
“One of the challenges of a mission this large is planning around airspace classes, where BVLOS flight is not authorised,” Wheeler notes. “Visual line of sight (VLOS) must be maintained in these areas, which requires ground control crews to stay close to the aircraft. PAU recorded key observations that will allow for optimised vehicle placement to ensure seamless operations when falling back to VLOS flight capacity and improving efficiency during future missions.”
Mapping the pipeline right of way and integrating it into the flight planning software was a key part of PAU’s preparation for the mission, a process eased by Event 38’s flight control software that allows the import of a KML file containing the flight path. “The software takes in the minimum and maximum operational altitude above ground level, then uses digital terrain elevation data along the flight path, together with known climb and descent rates, to plan the mission autonomously,” Wheeler explains. “Missions can then be exported as KML files for verification in external software.” The E455 flies using a custom version of ArduPlane, while ground control stations utilise a custom version of QGroundControl. Both software platforms were developed in-house by the Event 38 software team.
Although the mission was conducted in a single day with one E455, the aircraft made a total of 18 flights including functional tests, morning tests, and mission flights, adding up to a total of just under 8 hours flight time. Over that time, the aircraft’s average speed was 22 m/s, and its average altitude was 240 ft AGL.
The E455 can safely conduct 50 miles of right-of-way inspections per flight. However, Wheeler notes that individual flight legs of this mission were limited by waiver provisions and airspace proximity and restrictions. The average flight was 29 minutes long and covered 20.65 miles, with the largest single flight covering 45 miles, he reports. “The wind conditions were extremely favourable and calm during the mission, and the E455 responded beautifully.” The aircraft can operate in temperatures ranging from 5 to 110 F, with wind limits of 21 knots for take-off and landing and approximately 30 knots while in flight.
Event 38’s Jeff Taylor recalls that logistics were the biggest challenge leading up to the mission. On the 700 mile drive across the state of Louisiana, the team carried numerous items of mobile ground infrastructure. “Even basic logistics, such as transportation and housing of crew, are challenging when conducting a mission of this scale,” he says. “Thanks to many years of operational experience, PAU was able to develop a successful plan, and with the E455, they were able to accomplish six times more flying than is usually possible in a similar timetable.”
Wheeler notes that access to controlled areas with long, groomed runways was extremely limited. More often, the crew was operating out of small service areas, many with gravel parking areas. He praises the E455’s VTOL capabilities, emphasising that they enabled smooth take-offs and landings from virtually any space, improving the accessibility and efficiency of the mission by eliminating the need to locate spacious launch and recovery points for every leg of the mission.
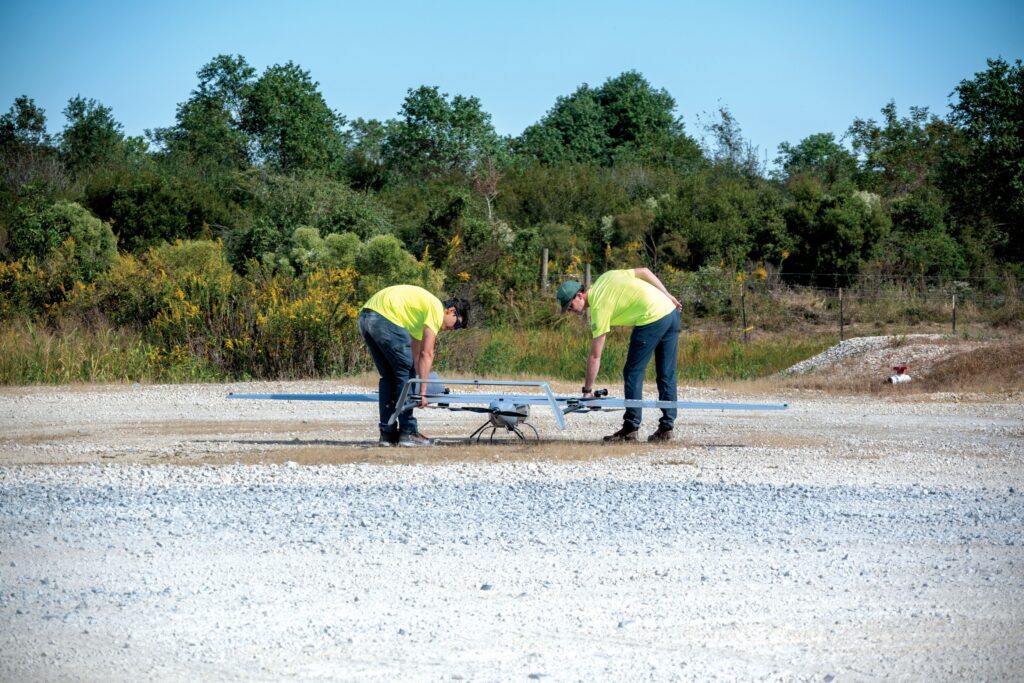
The E455 has a high-aspect-ratio wing mounted on top of the fuselage and between two slim composite booms, each of which supports a pair of vertically mounted motors and two-blade propellers, together with the two vertical tail surfaces joined at their upper ends by a single horizontal surface. A pusher propeller is mounted at the rear of the fuselage. Landing gear consists of a pair of fixed half hoops under the fuselage. The aircraft can carry a payload of up to 15 lb (7 kg), but this is limited to 5 lb to keep the gross weight within the 55 lb (25 kg) regulatory limit, although it can take off with a payload of up to 65 lb (29 kg), Event 38 says. While payloads typically consist of sensors, it can also carry small amounts of cargo.
In addition to the sensor package carried for the Shell mission, the aircraft provides the option for other systems including Lidar sensors, edge computing, electronic warfare and signals intelligence payloads, hyperspectral cameras and magnetometers etc.
Among the Lidar-based systems the E455 can support is Inertial Labs’ modular Remote Sensing Payload Instrument (RESEPI) centred on an XT-32 Lidar from Hesai. Designed to achieve “best-in-class” data accuracy, good detection range, high point density, and versatility, RESEPI is described as a sensor fusion platform that supports the XT-32 with the combination of a high-performance GPS-aided inertial navigation system with a high-accuracy single or dual-antenna GNSS receiver, integrated with a Linux-based processing core and data-logging software. Another option is a RESEPI system with an Ouster OS1-64 Lidar.
In addition to the Lidar and supporting precise positioning system, the RESEPI installation also comes with all the required cables and mounting brackets and a vibration isolator, together with Lidar calibration, bore-sighting, and post-processing kinematic and point cloud software services.
Event 38 offers to integrate payloads with the flight controller and ground control system software such that the EO can control the payload remotely or the payload can control the aircraft directly.
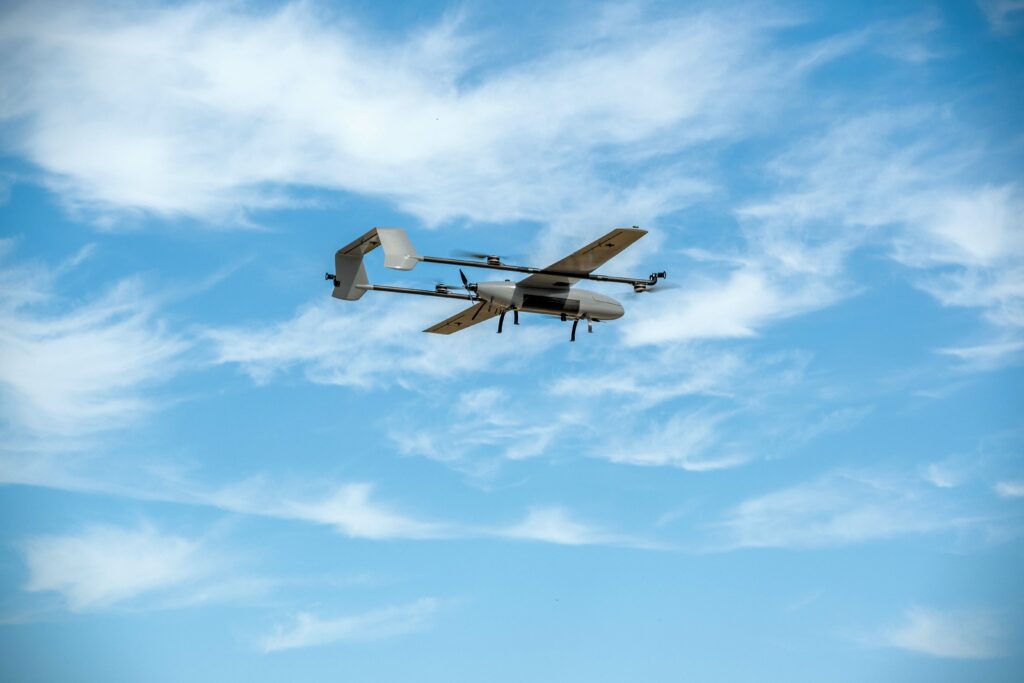
While the machine used for the Shell mission is all electric, Event 38 is developing other propulsion methods for missions requiring additional power, payload or endurance. The aircraft originated in a research partnership between the company, the Ohio Federal Research Network and a university team, which explored the integration of a fuel cell into a fixed-wing VTOL UAV. The idea was to capitalise on the combination of quietness and endurance that a fuel cell brings to surveillance missions, particularly long ones.
Because fuel cells have relatively small power outputs compared with other sources such as batteries or engines and are generally insufficient for take-off, the research team developed an electrical power distribution model that integrates and balances battery and fuel cell power to realise the benefits of both.
Designed for BVLOS
“The E455 was conceived from the ground up to meet the demanding requirements of long-endurance BVLOS missions, particularly in critical infrastructure inspection,” Taylor says, elaborating on the philosophy behind its development. He highlights the fact that Event 38 manufactures the system entirely in-house at their facility in Richfield, Ohio. “This vertical integration provides us with complete control over the design and manufacturing process, allowing us to tailor the aircraft to specific customer needs without being constrained by off-the-shelf airframes purchased overseas.” This capability allows for accommodation of specialised sensors, housing additional radios for redundancy, and modifications to virtually every specification of the aircraft.
The airframe is constructed from carbon fibre, a material chosen for its exceptional strength-to-weight ratio. “Carbon fibre’s lightweight nature enables the E455 to achieve relatively slow flight speeds even at its maximum weight, which is crucial for long endurance and collection of the accurate data required on surveying and inspection flights,” Taylor explains. “Simultaneously, its stiffness and strength allow the aircraft to withstand higher air loads at high speeds, resulting in a wide flight envelope spanning from 17.5 to 28 m/s.”
Furthermore, the E455’s thin (approximately 1 mm) carbon fibre skin maximises the internal volume. “This generous carrying capacity is particularly valuable for BVLOS operations, which necessitate the integration of substantial onboard equipment including redundant radios, detect and avoid systems, the primary sensor and processing units,” Taylor adds.
Regarding aircraft care, Taylor notes that the shortest maintenance interval for the E455 is 100 flight hours, at which point the servos should be replaced. Flight batteries have a replacement interval of 200 flight hours, and motors after 400 flight hours. All other components are replaced based on their condition and observed wear and tear. The E455 used in this mission had flown fewer than 100 hours and did not require any maintenance.
The E455 is an electric aircraft, rendering it “almost inaudible at 250 feet,” according to Taylor. Even at close range, the motor noise is low enough for operators to converse easily.
Integration for situational awareness
The success of the 320 mile patrol relied heavily on seamless integration and performance of several key onboard technologies. The primary detect and avoid system was the Iris Casia system. Developed by Iris Automation, this system comprises two forward-facing cameras with an overlapping field of view (FoV), providing a wide 170° forward FoV, and a rear-facing camera with a 90° FoV.
Casia feeds the output from these cameras to AI algorithms that scan the airspace for other aircraft and are capable of differentiating between various types of aircraft including UAVs, helicopters and fixed-wing aeroplanes. Based on the detected threat and its predicted path, the system can autonomously command its host UAV to execute pre-programmed avoidance manoeuvres, such as altering its altitude or lateral trajectory, to maintain a safe separation distance.
The heart of the system is its central processing unit, an NVIDIA Xavier AGX system-on-module that runs the computer vision and machine learning algorithms responsible for object detection, classification, tracking and avoidance planning. Ruggedised for UAV use, it includes interfaces for connecting to the cameras, autopilot and other aircraft systems. It links with the autopilot via UART or other serial communication protocols to receive flight data and send commands for autonomous manoeuvres. The system incorporates intelligent avoidance logic that determines the most appropriate and safe manoeuvre to avoid a collision, taking into account the intruder’s trajectory, the UAV’s capabilities and the regulatory requirements.
Iris claims an average detection range for non-cooperative targets of approximately 1.3 km, with the maximum range potentially exceeding 2 km, depending on aircraft type and environmental conditions.
Wheeler reports that while several objects were detected during the mission, there were no “loss of well-clear” events, and the E455’s flight path never needed to be adjusted. No specific calibration of the Casia system was required for the pipeline inspection.
Redundant radio links were crucial for maintaining continuous command and control. The system incorporated Silvus 2.4 GHz radios for point-to-point communication, achieving a range of approximately five miles during this demonstration; however, the potential range can vary significantly based on environmental conditions, terrain, antenna configuration and data transfer rate.
Complementing this was the Elsight Halo 4G cellular radio. Wheeler explains that as long as the radio remains within range of a cell tower, virtually unlimited range is achievable, especially with the aircraft operating at a significant altitude above ground level, minimising signal obstructions. The Halo employs AES-256 encryption and delivers data to the ground control system via secure VPN tunnelling, while the Silvus radio also utilises AES-256 encryption, ensuring a high level of cybersecurity for data transmission and control systems. The LTE Halo uses L-Com antennas designed for cellular radios. PAU typically uses Silvus antennas mounted on pneumatic masts on the ground for enhanced connectivity; however, the LTE signal strength was consistently robust throughout the Shell mission, rendering the mast-mounted antennas unnecessary.
ADS-B in data was directly integrated with the flight controller, providing ground control with real-time information on the position, speed, and heading of any potential intruder aircraft equipped with ADS-B transponders.
The onboard GPS/GNSS system was a custom unit developed by mRobotics (now 3DR Inc.) based on the u-blox M9N chipset and featuring an external antenna. Taylor explains that the E455’s carbon fibre airframe can block GPS signals, necessitating the external antenna to ensure a strong and consistent signal for precise navigation and maintaining connection with ground control.
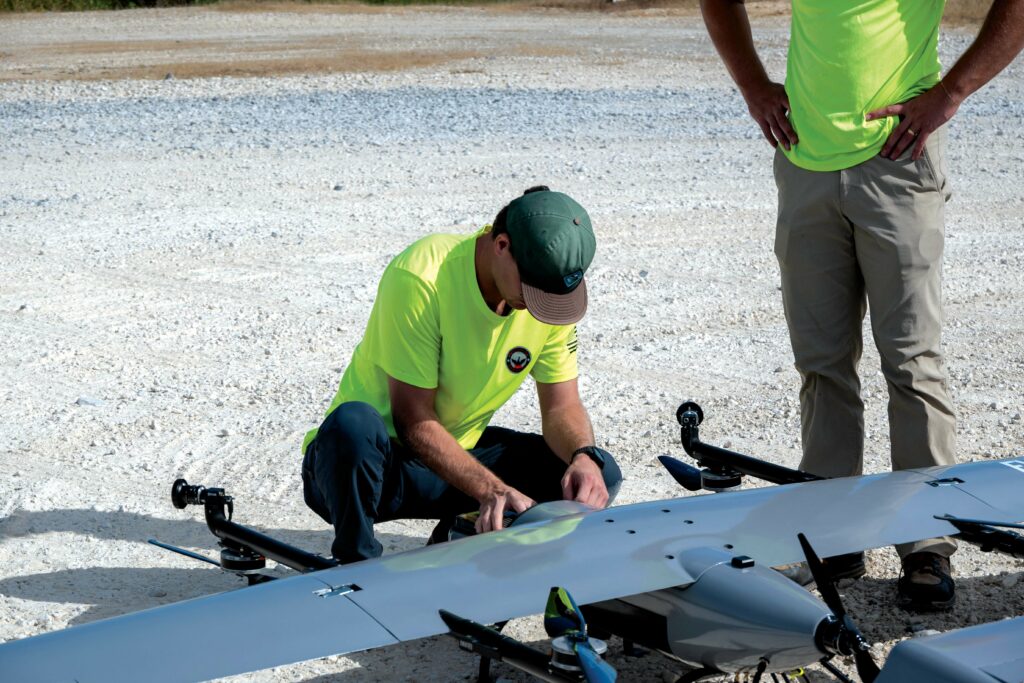
The live video feed from the onboard cameras was transmitted using H.264 encoding (also known as advanced video coding) over the bonded radio solution. Wheeler confirms that the video quality met Shell’s requirements, providing enhanced data compared with traditional patrol methods. The transfer rate was sufficient to support the livestream video, enabling real-time analysis by the ground crew.
Taylor emphasises the rigorous testing that all Event 38 aircraft and systems undergo at their manufacturing facility, including bench testing, pre-flight ground testing, and in-flight testing. The specific E455 and associated equipment used for this Shell mission underwent an additional week of testing with PAU, including BVLOS flights with hand-offs between ground control vans prior to the actual pipeline patrol.
Wheeler adds that waiver compliance and risk mitigation were central to the mission’s planning and execution. The E455 was selected partly because Event 38 could integrate their drone into PAU’s existing BVLOS infrastructure, which had supported previous approvals.
Data handling and future applications
During the proof-of-concept demonstration, right-of-way agents from Shell were present and conducted data verification in real time. The primary focus of the demo was to assess the feasibility of conducting such long-range pipeline patrols at scale. Because the analysis of the incoming data occurred live, and Shell’s immediate data requirements were met, no post-processing of the collected data was needed for this demonstration. Therefore, no issues around post-processing software, onboard processing limitations (because real-time streaming was prioritised), or data archiving and storage arose in this phase of the project. Information regarding the types of anomalies detected and how the data were correlated with existing pipeline infrastructure data remains confidential. The payload bay of the E455 for this mission primarily housed the NextVision camera and required minimal customisation, with other equipment such as the radios mounted elsewhere in the aircraft.
Looking to the future, Wheeler says, “Our long-term goal is to execute this type of mission at scale and explore further applications for uncrewed aerial systems in the pipeline industry.”
Key specifications
MTOW: 55 lb (25 kg) regulated, 65 lb (29.5 kg) max.
Payload: 5 to 15 lb (2.27 to 6.8 kg)
Range: approx. 81 miles (131 km)
Endurance: 2.5 hours on batteries
Speed: 39 to 49 mph (63 to 79 kph) cruise, 56 mph (90 kph) dash
Wingspan: 14.2 ft (4.3 m)
Length: 7 ft (2.1 m)
Some key suppliers
EO/IR camera: Nextvision
Detect and avoid system: Iris Automation
Radios: Silvus
Autopilot: Cube FC running Pixhawk software
4g radios: Elsight Halo
UPCOMING EVENTS
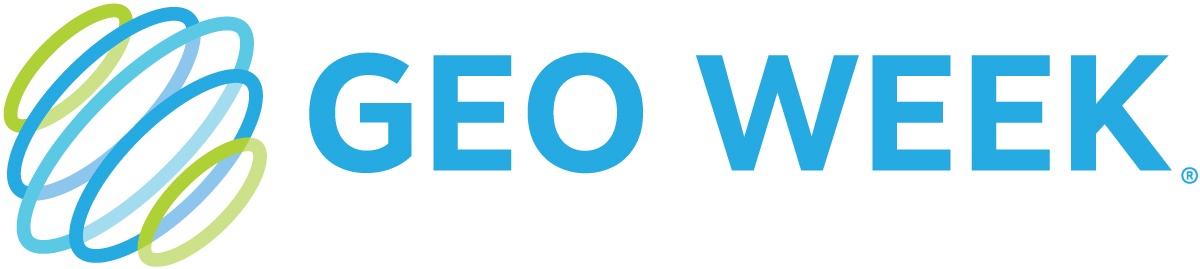
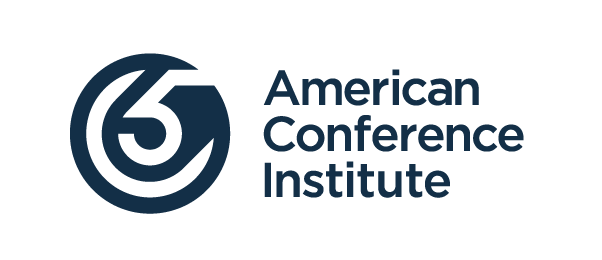
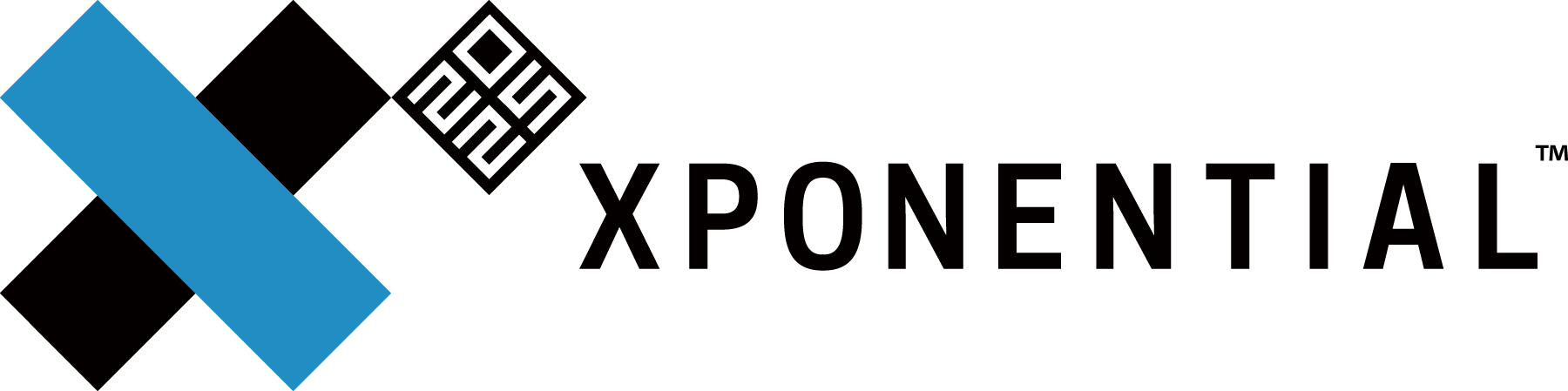
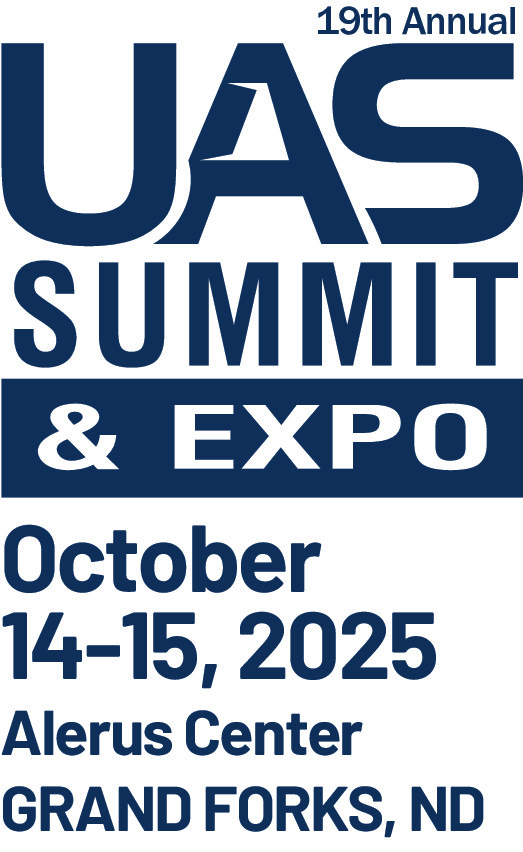
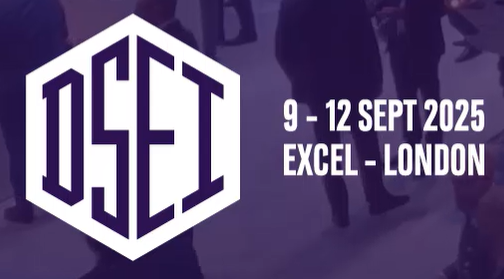
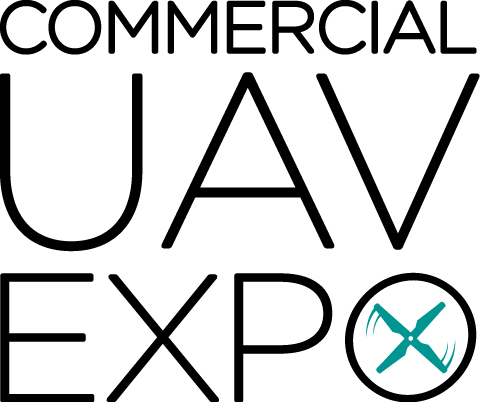
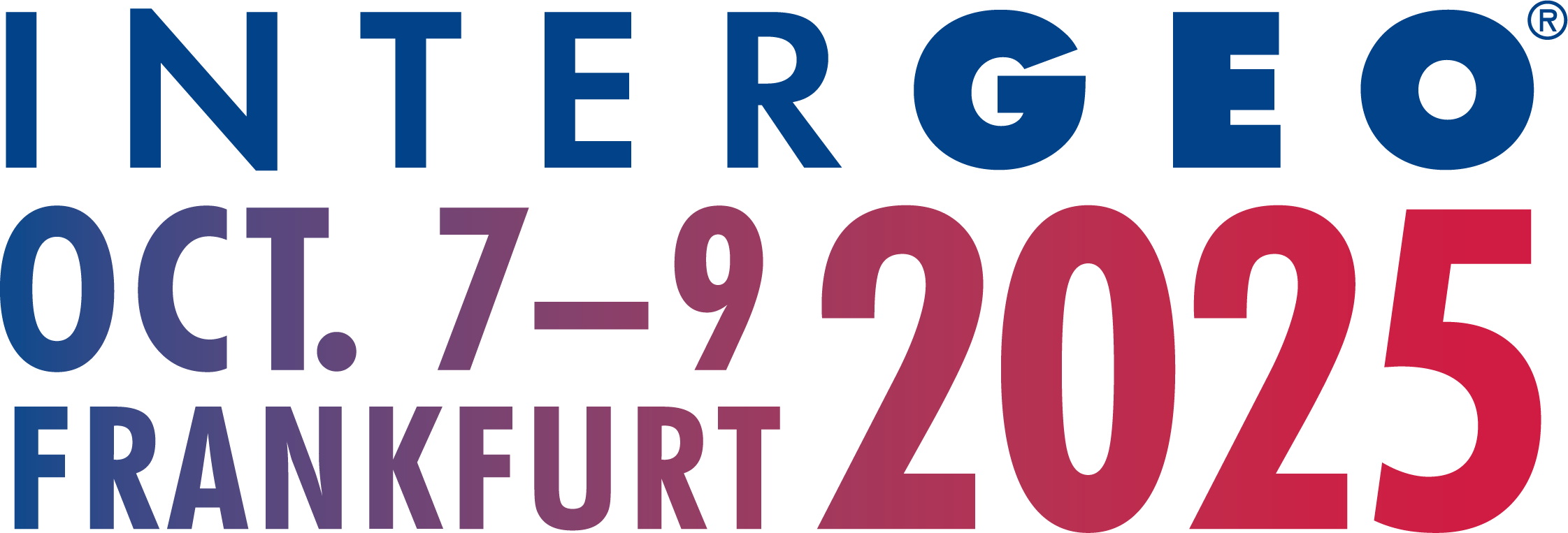
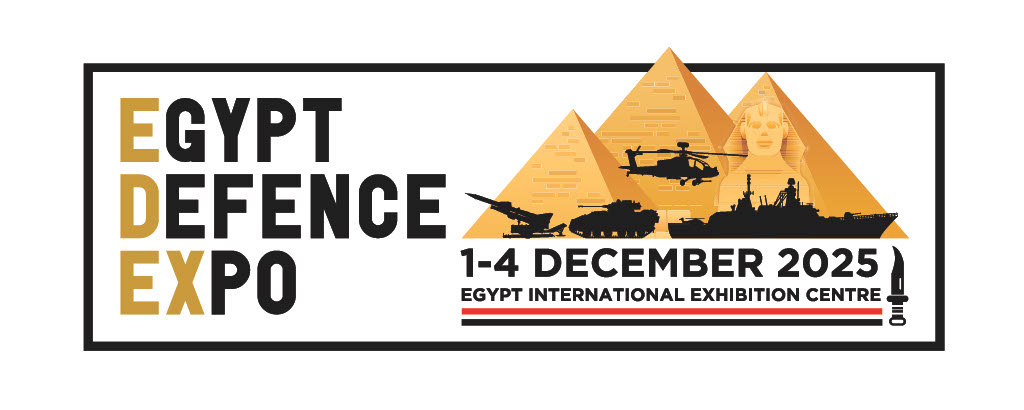
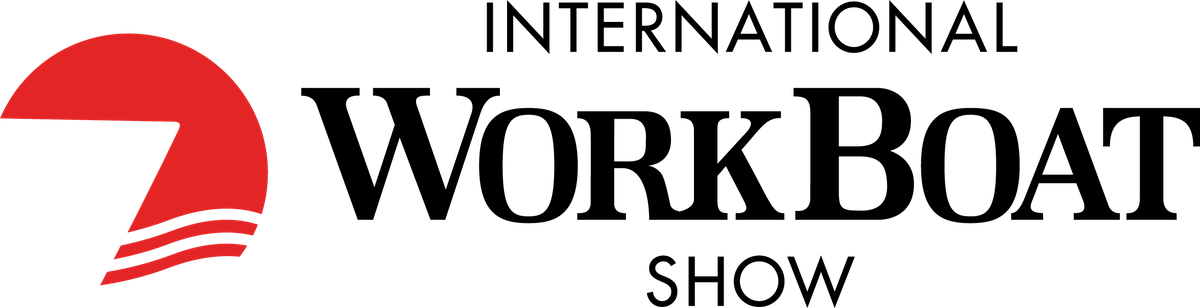
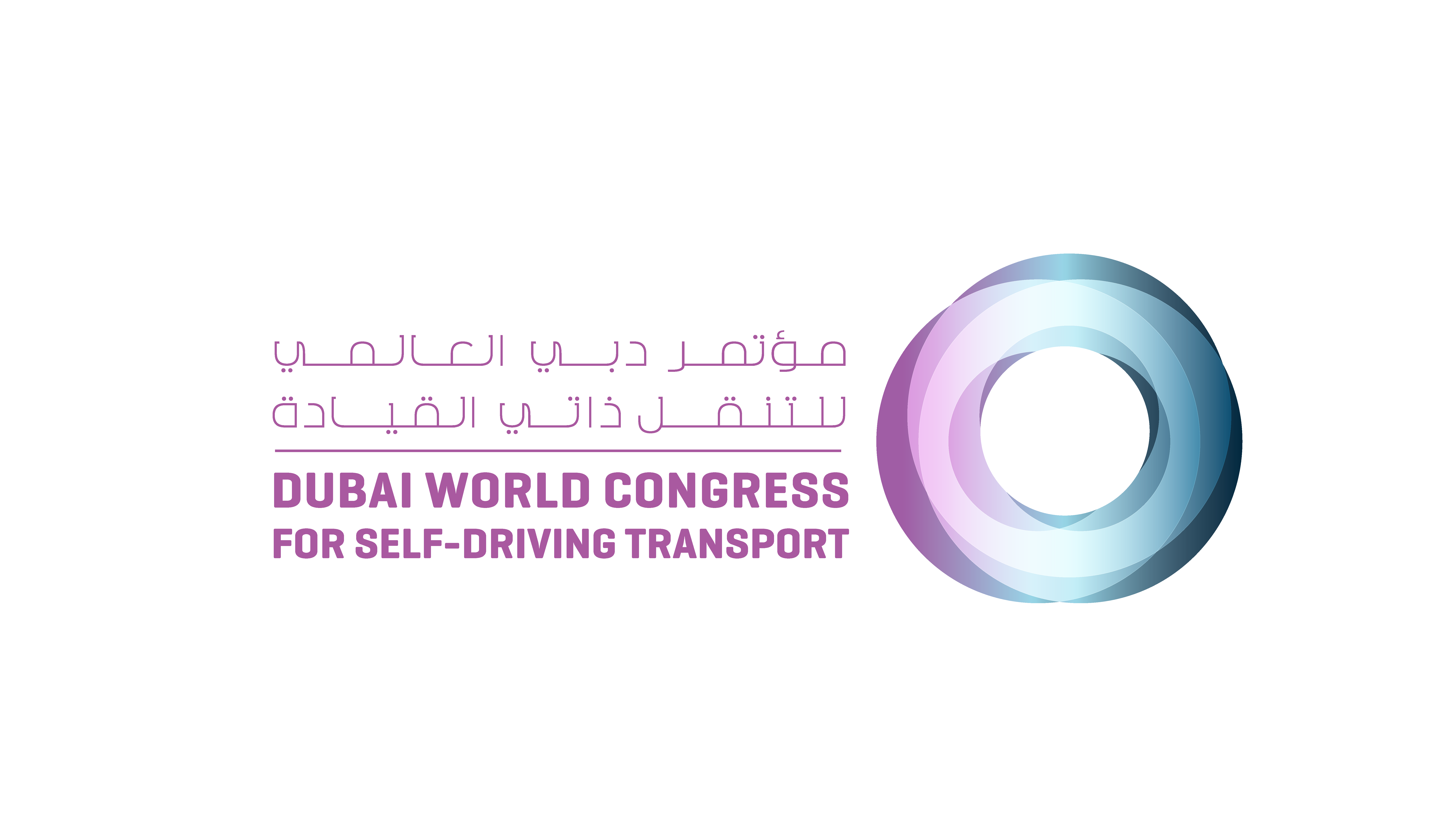
