Eurosatory 2024
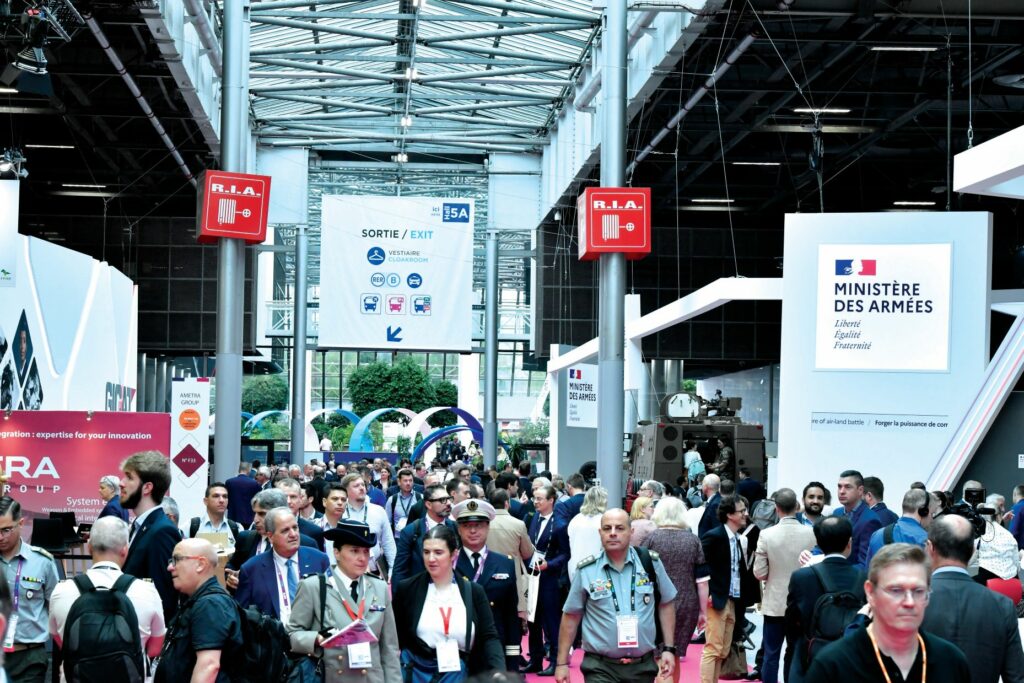
More than 2000 exhibitors and a record number of visitors inhabited the halls of the Parc des Expositions in Paris for Eurosatory 2024 (Image courtesy of Eurosatory Media)
Rory Jackson spotlights some innovations to boost military prowess on show in Paris
As conflicts continue to rage inside Europe’s borders and beyond, demand for uncrewed systems is surging to expand various nations’ military capabilities at a rate that is faster than the recruitment of soldiers and crews can provide.
At Eurosatory, Europe’s biggest land and air tech expo, countless new innovations in autonomous vehicle systems were showcased, including new means of boosting their intelligence, performance and connectivity capabilities, particularly on battlefields and in airspaces where GNSS spoofing, comms jamming and lethal strikes are a constant danger.
To understand how the changing face of war is bringing defence vehicle autonomy to new heights, and how both soldiers and civilians can be better safeguarded through innovations in uncrewed system technology, we investigated Eurosatory’s three vast exhibition halls at Parc des Expositions in Paris in June.
A selection of our findings follows.
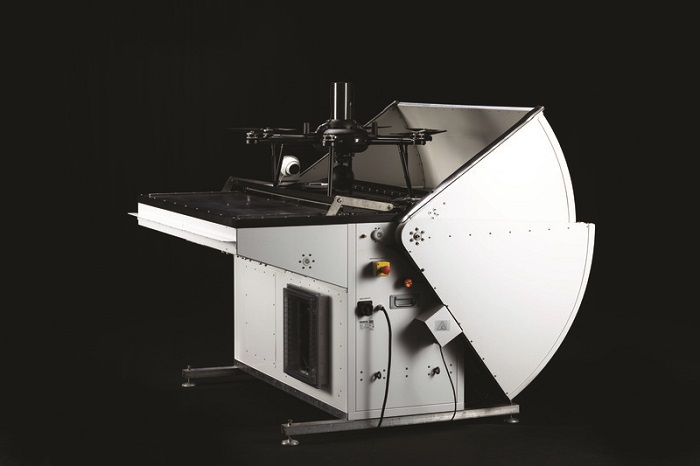
Nokia was exhibiting to showcase – in association with its 5G mobile network solutions – its Nokia Drone Networks drone-in-a-box system.
“Nokia Drone Networks is an end-to-end UAV system, which includes the drone itself, a dual camera gimbal with HD and thermal capabilities, docking station, ground control station, and all associated software and service components,” said Arnaud Legrand from Nokia.
The system uses both 4G/LTE and 5G connectivity to ensure higher bandwidth and lower latency for optimal data collection and processing, including high-bandwidth streaming of HD camera data and thermal camera data (its standard issue payload being an EO/IR gimbal) back to users’ GCSs or command stations in real time.
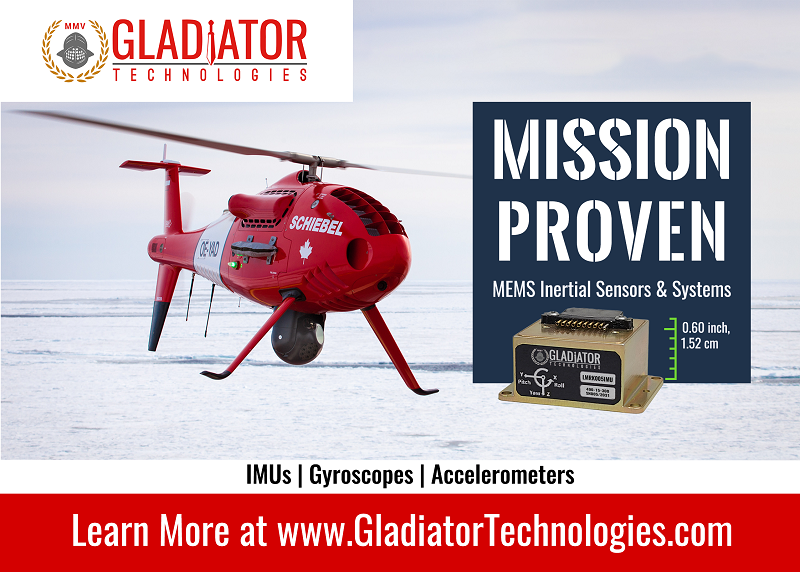
The docking station allows the crafts to take off repeatedly for autonomous missions and return for charging, even in remote locations.
Manufactured in Europe by Nokia, the Nokia Drone Networks solution is CE- and FCC-certified and commercially available. It is currently being deployed for nationwide use in Belgium (with deployment in Switzerland anticipated in the near future) for public safety use cases.
“The other benefit of 4G/LTE and 5G is that this connectivity enables flying beyond visual line of sight [BVLOS] as long as the drone stays within the range of the network. Additionally, what’s worth mentioning is that the system enables one pilot to control a fleet of drones from one remote operations centre,” Legrand added.
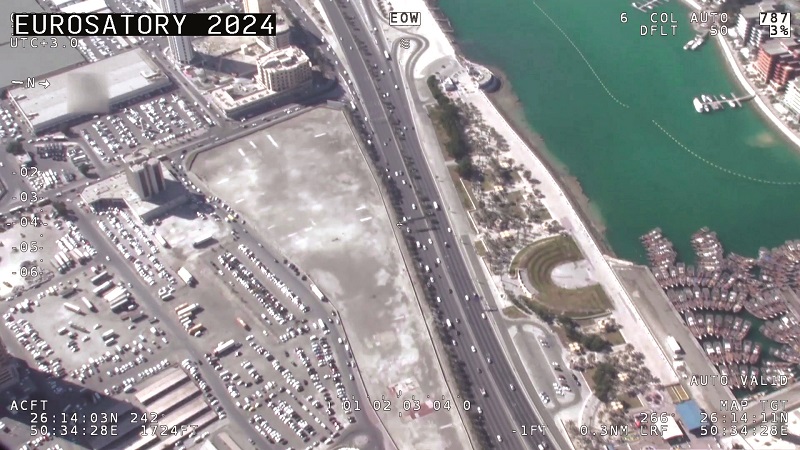
VITEC has launched an update for its embedded video-encoding platform, which adds an overlay feature that end-users can configure and limit as needed in their streamed data.
“As an embedded platform, we don’t use a huge CPU, as in a desktop computer, but the objective of this update was for end-users to be able to tag their video streams, so that if uncrewed vehicle operators have multiple streams coming in from assets on sea, in the air and underwater, all coming to the ground at once, then you can see at a glance which is which,” said Bruno Teissier.
“Engineers looking to qualify a new aircraft or sensor need to know which stream is coming from the new asset, perhaps to judge against an older or control stream for the test case. Also, some uncrewed vehicles in resident inspection applications will work simultaneously, so inspection personnel need to see at a glance which vehicle is streaming to which monitor in front of them, rather than go through complex settings to see that.”
The absence of a CPU puts significant constraints on how VITEC could develop the update; the exact details remain proprietary. However, the company said that with the latest version of its video-encoding solutions, the streaming bit rate can be changed seamlessly, autonomously and on the fly.
This means that when an end-user’s vehicle moves from a close distance relative to the GCS to a long distance, the bit rate can be automatically adjusted to suit the bandwidth to improve the overall quality of the video stream, preventing the need to stop and restart the stream with new parameters.
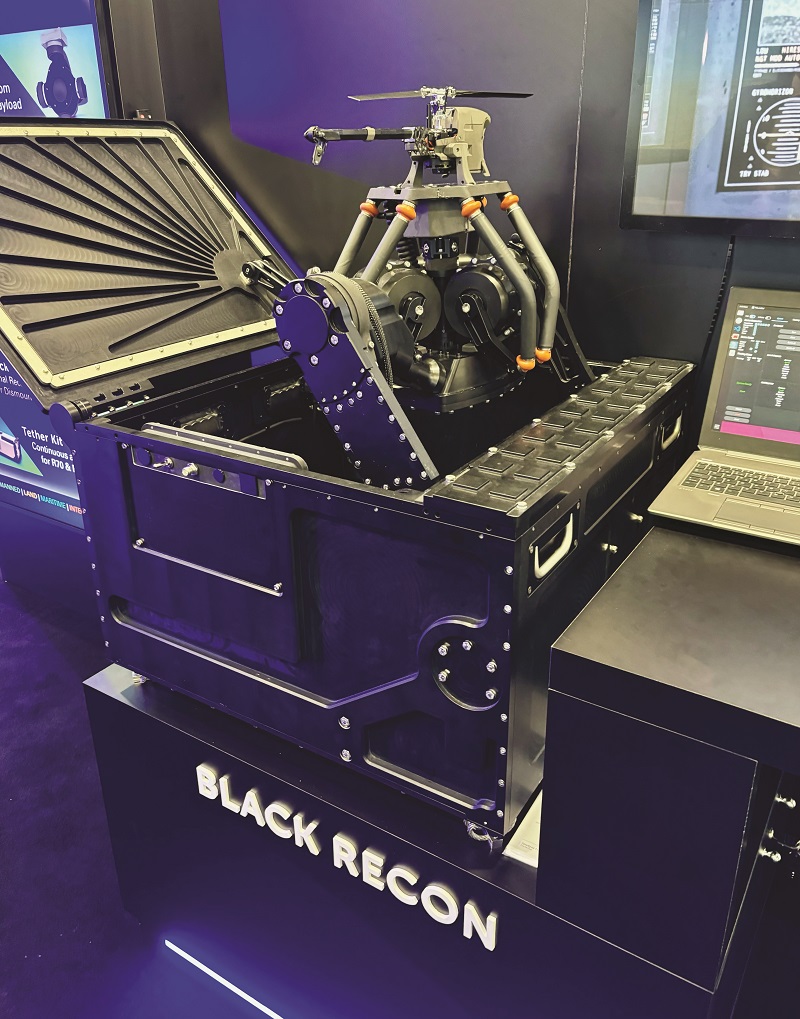
Teledyne FLIR Defense unveiled its Black Recon VRS (Vehicle Reconnaissance System) UAS, a combined solution of small-sized helicopter UAVs and a containerised Launch and Recovery box. It has been designed for mounting on armoured personnel carriers or battle tanks, and functioning as a larger complement to the company’s Black Hornet 4 micro-UAS.
The box contains three UAVs, each battery-powered and capable of over 45 minutes of flight endurance, with 5-6 km of data-link range.
As Teledyne FLIR’s Jakob Jakobsen explained: “By mounting the Launch and Recovery box on a military vehicle, the idea is that the UAVs will take turns between charging and flying to autonomously maintain a constant survey ahead of defence squads’ advancements.
“They will scan terrain for threats before they come within range, and stream back everything they see without the need for remote control, or even GNSS. Vehicle squads can then focus on preparing countermeasures for detected threats in advance of entering weapons range. That increases both general safety and advancement speeds for squads in the field.”
The Launch and Recovery box features a single camera that tracks each UAV as it comes in to land, and a motorised landing pad that self-adjusts using six rotary servo actuators to ‘catch’ the UAV safely while compensating for inclination by the vehicle below.
“The operator holds the decision over when UAVs come back to recharge or prepare for launch. Although we have constant radio comms between the box and the UAVs for both live streaming and command, users also have the option to operate in a radio-denied mode,” Jakobsen said.
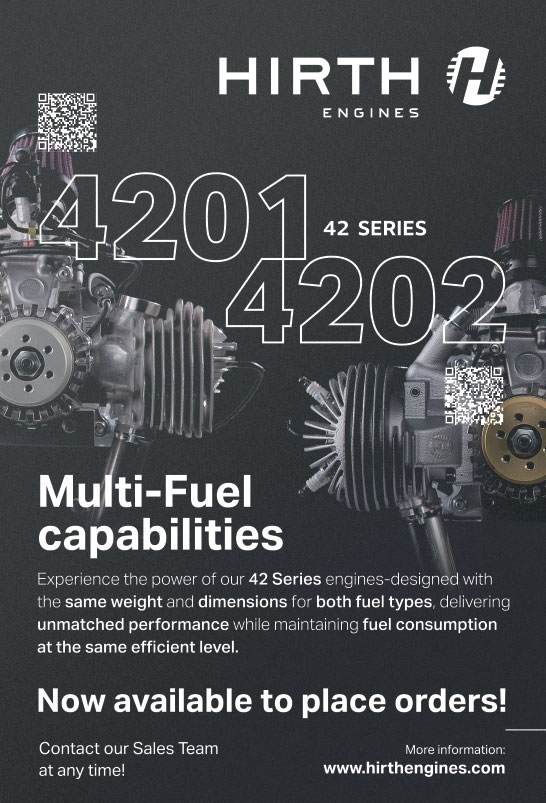
“The GNSS-denied navigation works using video, as it did on the Black Hornets 3 and 4, with the Black Recon picking up visual features and using them to triangulate its position and make navigational decisions.”
An update to the Black Recon will enable it to be soldier-mountable and function as a personal reconnaissance system (PRS) in the future.
Additionally, the Black Recon is interoperable with the smaller Black Hornet 4 UAS. Therefore, squads can use the same controllers and equipment to perform low-altitude surveys with the Black Hornet 4, while covering greater ground with the Black Recon by setting its UAVs to survey at higher altitudes.
Italy-headquartered M.E.Rin attended the show to exhibit its solutions and capabilities in fuel tanks for various applications, including its bladder fuel tanks, based on a technology formulated after (and remaining a standout since) World War II.
“When helicopters would undergo a low-speed drop during autorotation, the leading cause of injuries or deaths would be the fires that broke out after the crash, so we developed our bladder fuel tanks as a crash-resistant alternative to conventional tanks, such that they wouldn’t break and spill fuel outside of very high-velocity crashes,” said Andrea Maresca of M.E.Rin.
“Today, we still test every bladder tank design for crash resistance, typically by dropping a unit from 50 ft while it’s filled with water, to validate that no fluid is released from the system during or after impact.”
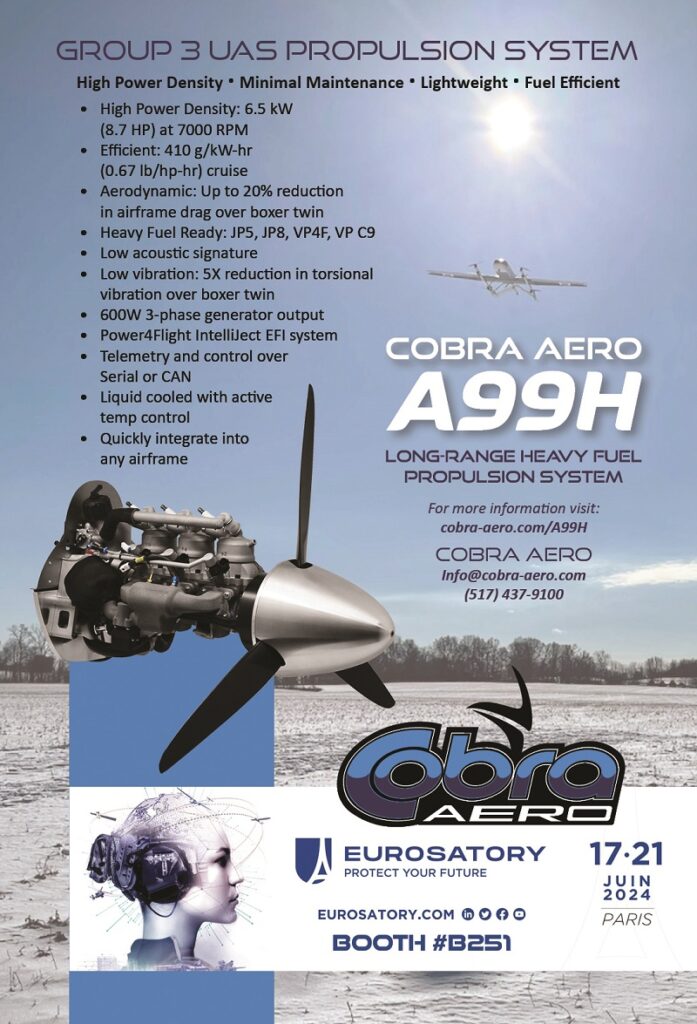
The flexibility of the company’s bladder tanks enables them to be installed inside airframes by folding them into compact shapes, and inserting them through maintenance hatches, payload bays and other openings. Once inside, they can be released, after which they naturally unfold into their regular shape, only filling the available space when fuelled.
“We’re seeing that this quality makes the bladder tanks especially demanded among UAVs, because easier replacement of the fuel tank is highly desired by maintenance technicians – that, and their lightness over solid tanks, is important for the value derived from uncrewed aircraft operations,” Maresca said.
“To make our bladder tanks, we start with a core of either cardboard or plaster, using that to lay one or more layers of fabric to achieve the shape and skin of the tank; somewhat like making a very high-quality dress. That fabric is a proprietary recipe, which gives very good resistance against many kinds of fuels and external atmospheric agents.
“The tank is then vulcanised in an autoclave, creating links throughout the structure of the rubber and making the whole thing behave more elastically. Afterwards, we apply water to extract the core via the tank openings; then we clean and inspect it for any defects before clearing the unit for shipping.”
Meanwhile, one of M.E.Rin’s newest product offerings is a self-sealing fuel tank, intended for military applications where weapon fire may be a present hazard. The walls of these tanks are constructed from two layers of rubber sandwiching a proprietary material layer, which reacts chemically to fuel exposure by expanding, and hence clamping shut any holes that would otherwise be left (depending on the calibre of the firearm).
“The self-sealing tanks are manufactured in much the same way as the bladder tanks, including the use of the same sorts of rubber, but with more layers of them and, of course, with the special expanding material as a core layer,” Maresca said.
“We tested them on shooting ranges in Italy and Germany, and the idea is that they will minimise fuel losses when shot and enable the aircraft to keep flying safely.”
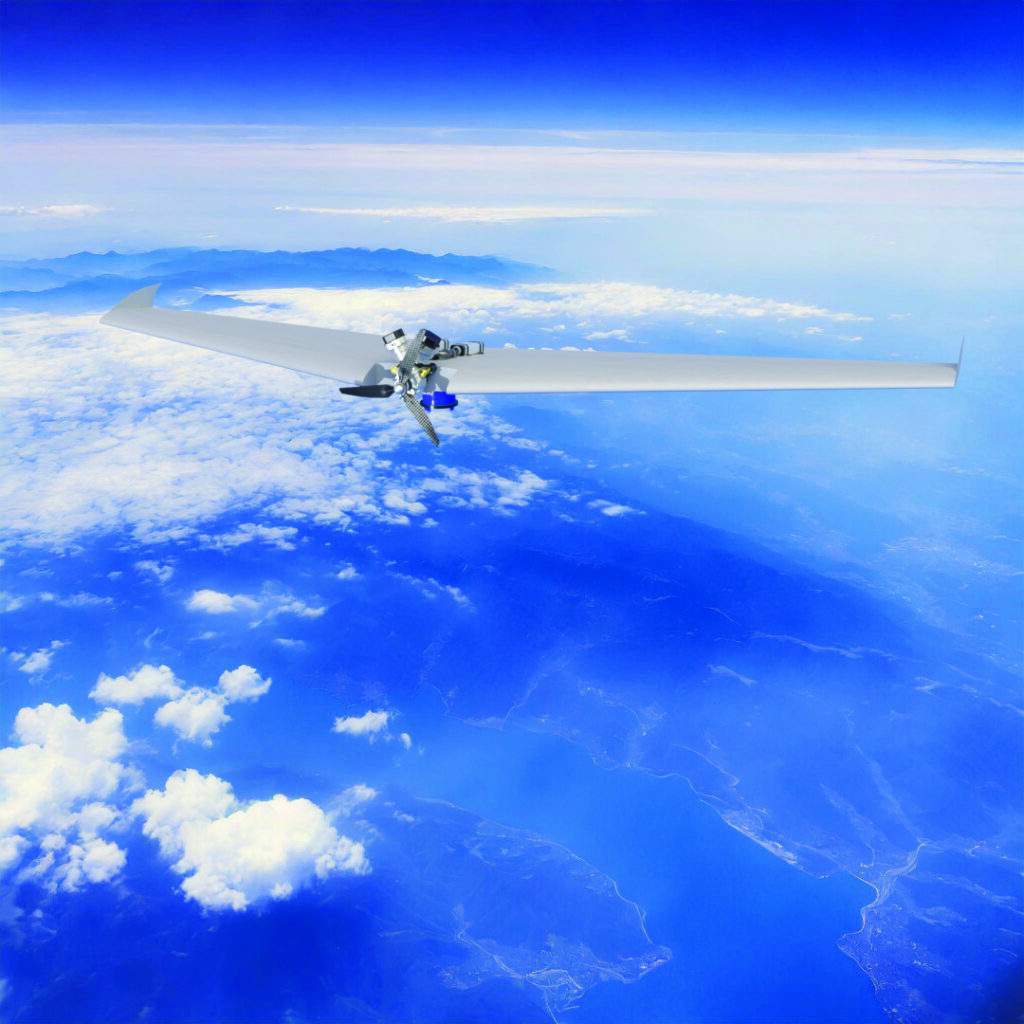
B&S Technology, a specialist manufacturer of aluminium solutions based in northern Germany, attended Eurosatory to display its Hitbird range of attritable UAVs for the defence market. The product range is made up of three flying, wing-shaped vessels, constructed almost entirely from aluminium.
“Our company owners are keen aviators and sought to design a cost-effective UAV that could be produced entirely using the machinery in our factory,” said Jens Sager.
“For example, manufacturing one unit of our HB [Hitbird] 700 aircraft takes just 12 hours, from cutting the first pieces of aluminium to assembling the completed UAV, and it comes with that short production time that the per unit cost is also quite low.
“We’re also fairly flexible and scalable. As a company of 50-60 people with one chief engineer, if a customer asks for something bespoke in a UAV, like a different payload, powertrain or airframe configuration, we just do it.”
The HB 700 is a 190 kg MTOW UAV, powered by a 60 bhp, two-stroke engine, capable of seven hours of flight endurance (and 1000 km of flight distance) when carrying 100 kg of payload and 30 kg of fuel. Its airframe features retractable landing gear, housed within a 700 m wingspan body (250 cm length).
The two smaller UAVs in the Hitbird range are the HB 350 and HB 175, similarly named for their wingspans, and powered by 20 bhp and 5 bhp engines, respectively. Either can be launched by catapult, although the former can be designed with landing gear if requested.
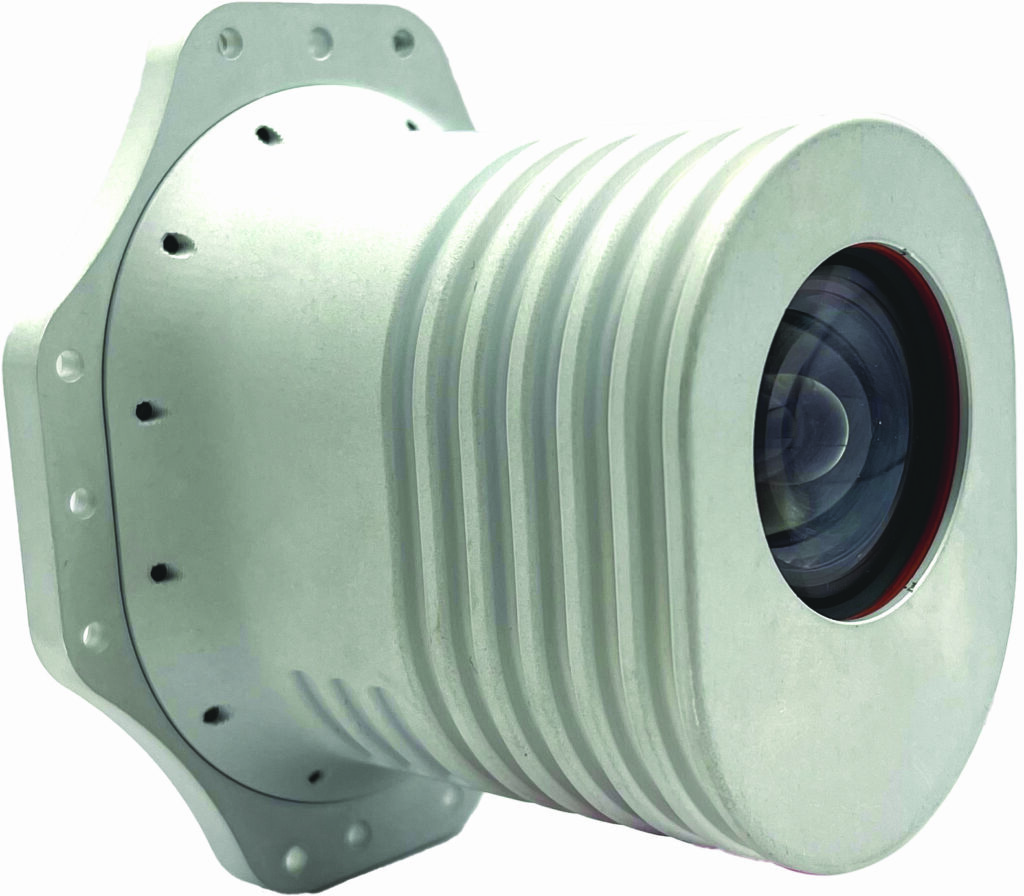
Inertial Labs told us about two new sources of aiding data that it has integrated into its ecosystem of solutions for GNSS-denied navigation.
“The latest version of our ecosystem will include the ability to utilise multiple different low-Earth orbit [LEO] satellite constellations for position, and to have those several different services incorporated into our INS’s extended Kalman filter as part of the standard package,” Jamie Marraccini said.
Also being incorporated is the ability to use map matching and map management to aid the company’s INS. This utilises many different collections of satellite maps and manages them based on various environmental factors. Map matching acts as an extremely accurate aiding data source for visual positioning solutions as the system will be able to cross-reference features identified in the live data with the database of mapping data in real-time.
“Additionally, following on from our previous release of a downward-facing camera for visual odometry, we’ve also begun deploying a stereo vision solution for low-flying and ground vehicle deployments, and we’re also enabling the prospect of additional computer vision suppliers,” Marraccini noted.
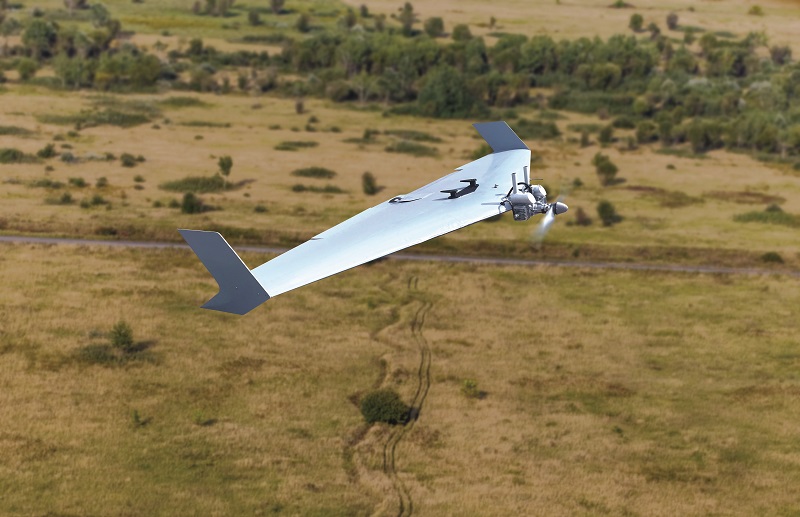
KrattWorks showcased its fixed– wing, aerial target uncrewed vessel, DART, a blended wing-body aircraft designed as an aerial target UAV for air-defence units, as well as practising C-UAS drills.
“We’ve engineered it to fly as a target for heavy machine guns, anti-aircraft cannons and heat-seeking missiles. For missile-shooting practice, we add IR flares to the aeroplane to generate sufficient heat signature,” said Martin Karmin at KrattWorks.
While most target UAVs are designed as sleek, narrow aircraft, KrattWorks created the DART with a wide, blended wing-body for greater visibility, improved aerodynamics and faster cruise speeds, thus increasing its utility to the end-user.
The 7 kg UAV has a wingspan of 2.2 m and length of 0.95 m. It flies at up to 50 m/s (180 kph) with a cruising speed of 30 m/s (108 kph), endurance of up to 40 minutes and an operating altitude ceiling of 4 km.
Propulsion comes from a front-mounted, two-cylinder, two-stroke engine, selected for cost-effectiveness and a high power-to-weight ratio compared with four-strokes. DART aerial target can also be mounted with various radar reflectors, and used for testing and exercises by air-surveillance radar units.
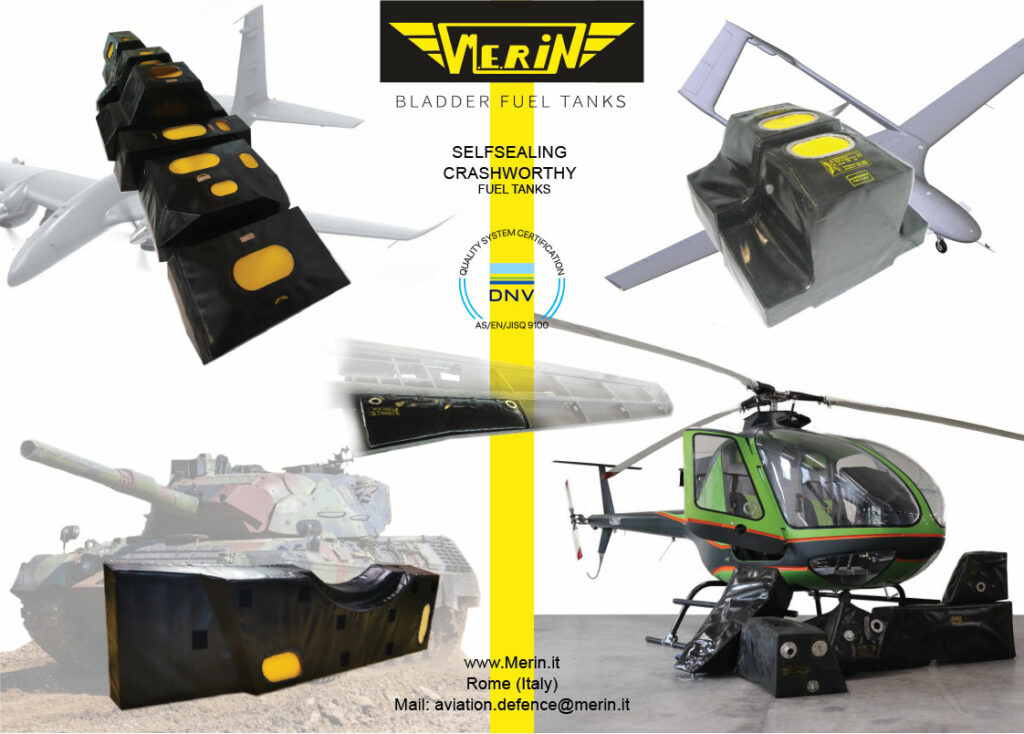
KrattWorks also discussed its reconnaissance multirotor uncrewed vehicle, ISR Ghost Dragon, which has been developed to resist electronic warfare jamming or GNSS spoofing. It uses a wide-frequency, range-hopping radio for jamming resistant video and telemetry links, and it also has GNSS-free navigation capabilities.
Hood Tech Vision exhibited a range of its payload solutions, including one of its latest gimbals, the 06 series EO/IR product.
“It’s a 6 in-diameter gimbal with four layers of stabilisation,” said Nolan Ohmart at Hood Tech Vision. “Gimbals of this size are challenging to stabilise with multiple layers, and two or three is common, but we’ve integrated four electric motors, two for pitch and two for yaw, to achieve optimal and closed-loop motion performance. We can also integrate a fifth layer for roll stabilisation depending on customer requirements.”
The 06 integrates a set of optics custom-designed by the company for the gimbal’s MWIR sensor, which optimises the packaging of the components surrounding the lens, and thus the product’s measurement and motion performance.
A laser target designator can also be installed, with fine target tracking aided by the gimbal’s aforementioned stabilisation architecture.
Hood Tech also showcased its ALTICAM 14 (AC-14), originally developed for the Insitu RQ-21 Blackjack (since restyled and developed as the Integrator, detailed in Issue 57).
Like the 06 series, the AC-14 integrates a MWIR sensor, along with an EO camera; the latter being capable of 280X zoom and the former 33X zoom.
It can additionally output three simultaneous, H.264-compressed video streams with embedded video-processing and AI, along with automated target tracking, video motion target indicators and automatic target recognition.
“One of the features that’s been key to the AC-14’s high performance, relative to its SWaP profile, is its lens, which we custom-designed into a form factor that other companies haven’t been able to achieve,” Ohmart added.
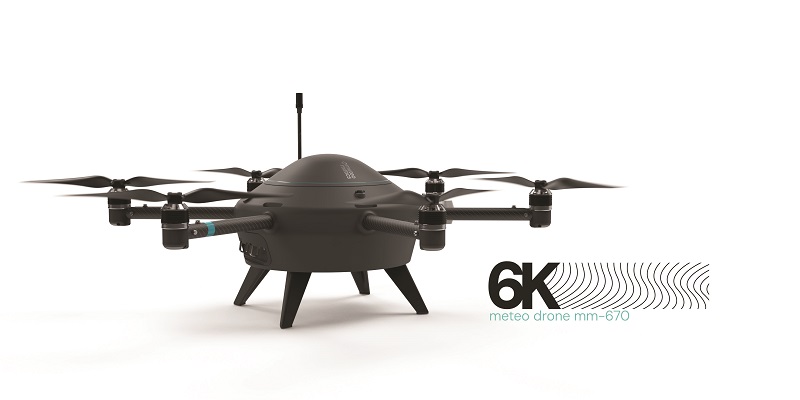
Meteomatics, a company specialising in high-accuracy weather information and intelligence technologies, has developed the Meteodrone MM-670, a UAV engineered for reliable and efficient capture of meteorology data.
“At the moment, meteorology in the middle and lower atmospheric layers consists basically of flying blindly, but more refined data is crucial if you want to improve fog, storm and other types of forecasts,” said Martin Fengler.
“With this UAV, our intention is to accumulate better weather data at altitudes of 6 km and below, and feed that into our proprietary, high-resolution weather model to generate more precise forecasts. We are manufacturing them in Switzerland, where we’re headquartered, and we have a BVLOS certification application to operate them in any European country.”
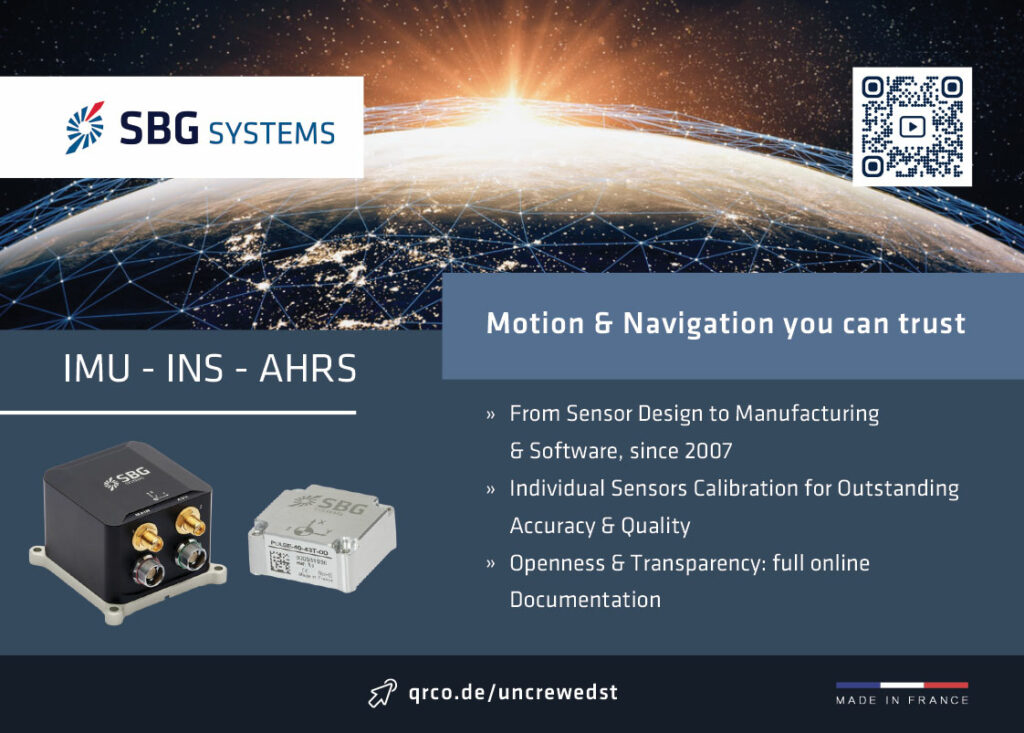
By default, the UAV integrates sensors for temperature, moisture and pressure, with wind speeds and directions computed using wind-induced changes in the aircraft’s attitude, as sensed by the onboard IMU.
Additionally, as well as the moisture sensor giving relative humidity data, that sensor combined with the pressure sensor can give dew-point calculations (this being the temperature to which a given body of air must cool to saturate with water vapour). End-users can, however, install their own meteorology instruments, if desired.
The Meteodrone MM-670 is a hexacopter, measuring 70 cm in diameter and weighing 5 kg. Battery powered with six brushless, DC electric motor-propeller drives, the craft’s typical flight endurance is 22 minutes, and it can operate in wind speeds of up to 90 kph. A safety parachute is installed and it is possible to include a propeller heating system.
The company is also developing a next-generation version of the Meteodrone, which will be able to fly at altitudes up to 10 km, with future versions able to go higher still. Such iterations will need to operate safely within civil air traffic, so transponder and potentially future detect-and-avoid technologies may be integrated (along with other key electronics for compliance with air-traffic regulations), as well as more powerful propulsion systems and possibly new means of de-icing or preventing icing.
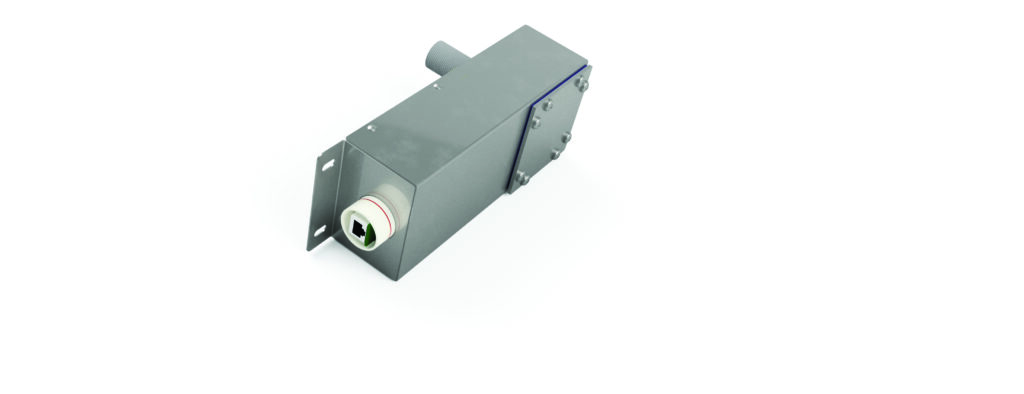
We also spoke with Total EMC Products, a UK-headquartered company specialising in the design, manufacture, modification and re-engineering of electrical or electronic systems to make them compliant with industry standards on EMC, such as DEF STAN 59-411 in the UK, MIL-Std 461 in the US, and DO-160.
“That includes integration of shielding, filtering or other components to enable EMC-compliance of subsystems going into uncrewed vehicles,” said Neil Harris of Total EMC Products.
“If a manufacturer needs to go further than that – for instance, hardening their UAV or UGV against anti-drone jamming, spoofing, high-altitude electromagnetic pulses or other sources of external EM waves – we can also do that to reduce their susceptibility to such interference.”
Systems that the company can assist with include embedded computers (both modification of new equipment and original equipment design consultation), servo actuators and alternators.
“EMC is a specialist area of engineering, with very few people able to help in the field, because so much of it comes from experience. There’s mathematics behind it, certainly, but they often miss out critical mechanical, packaging or cost effects stemming from what the numbers suggest you do for EM-compliance,” Harris said.
“What we do accounts not only for EMC, but also the holistic package around it, so that commercial and even defence users can end up with something both EMC-, SWaP- and vibration-optimised, as needs be.”
UPCOMING EVENTS
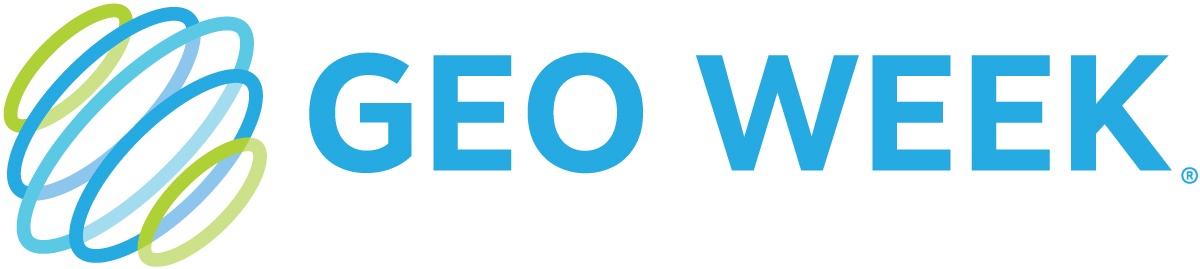
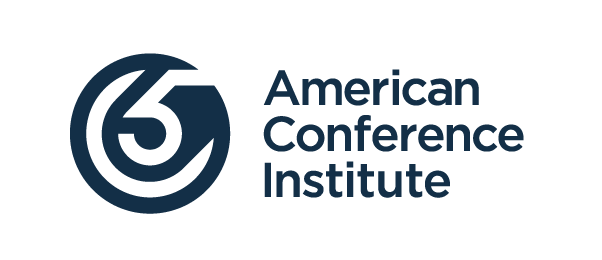
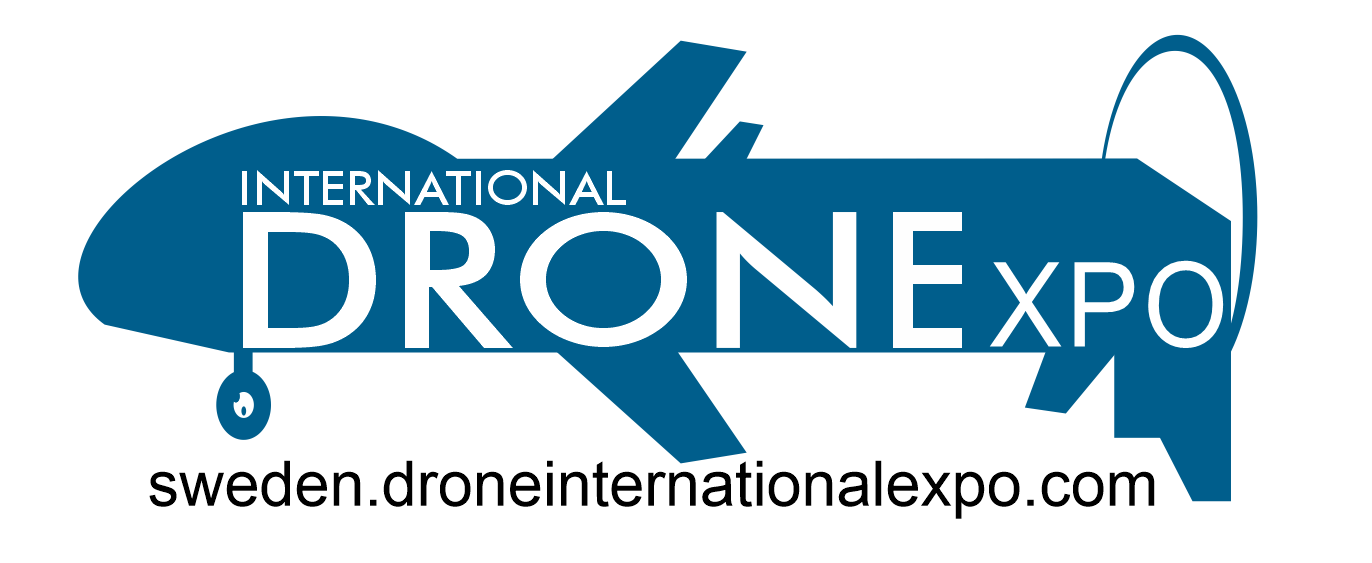
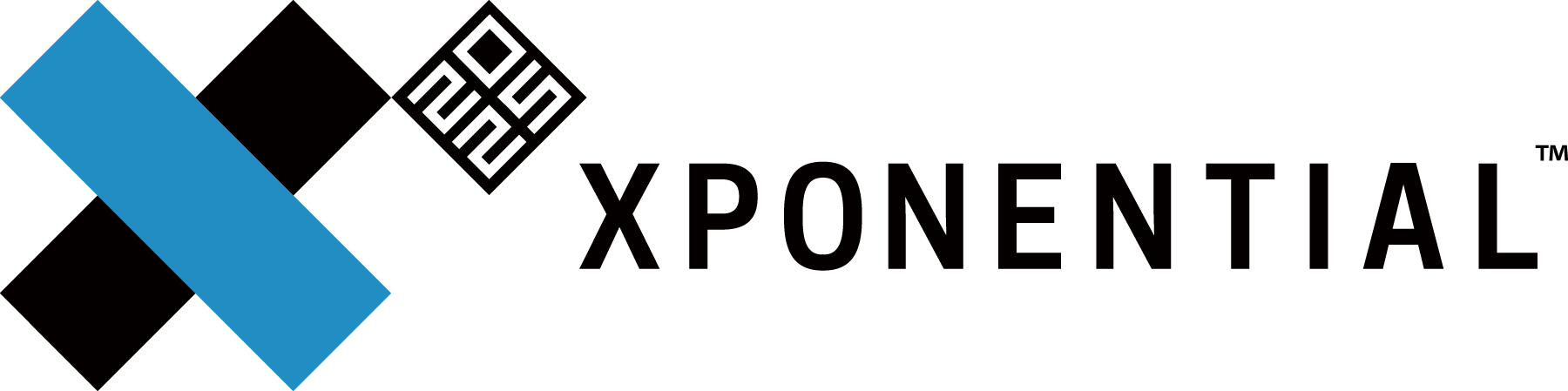
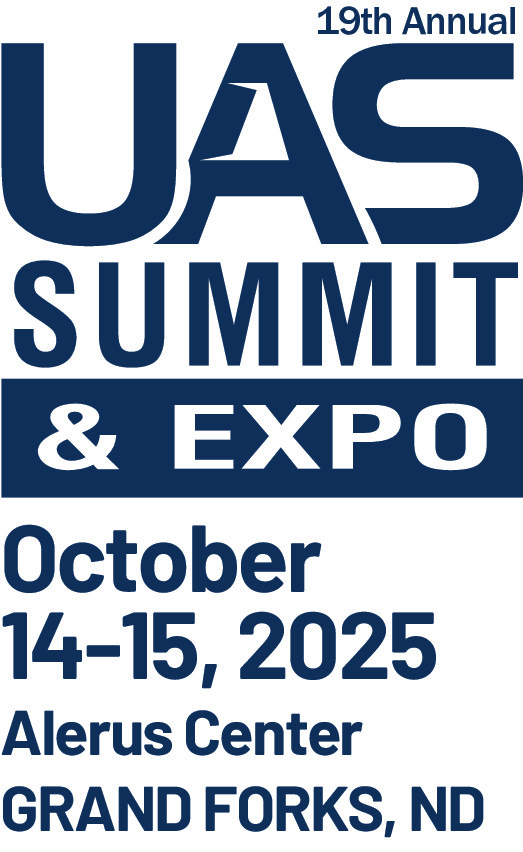

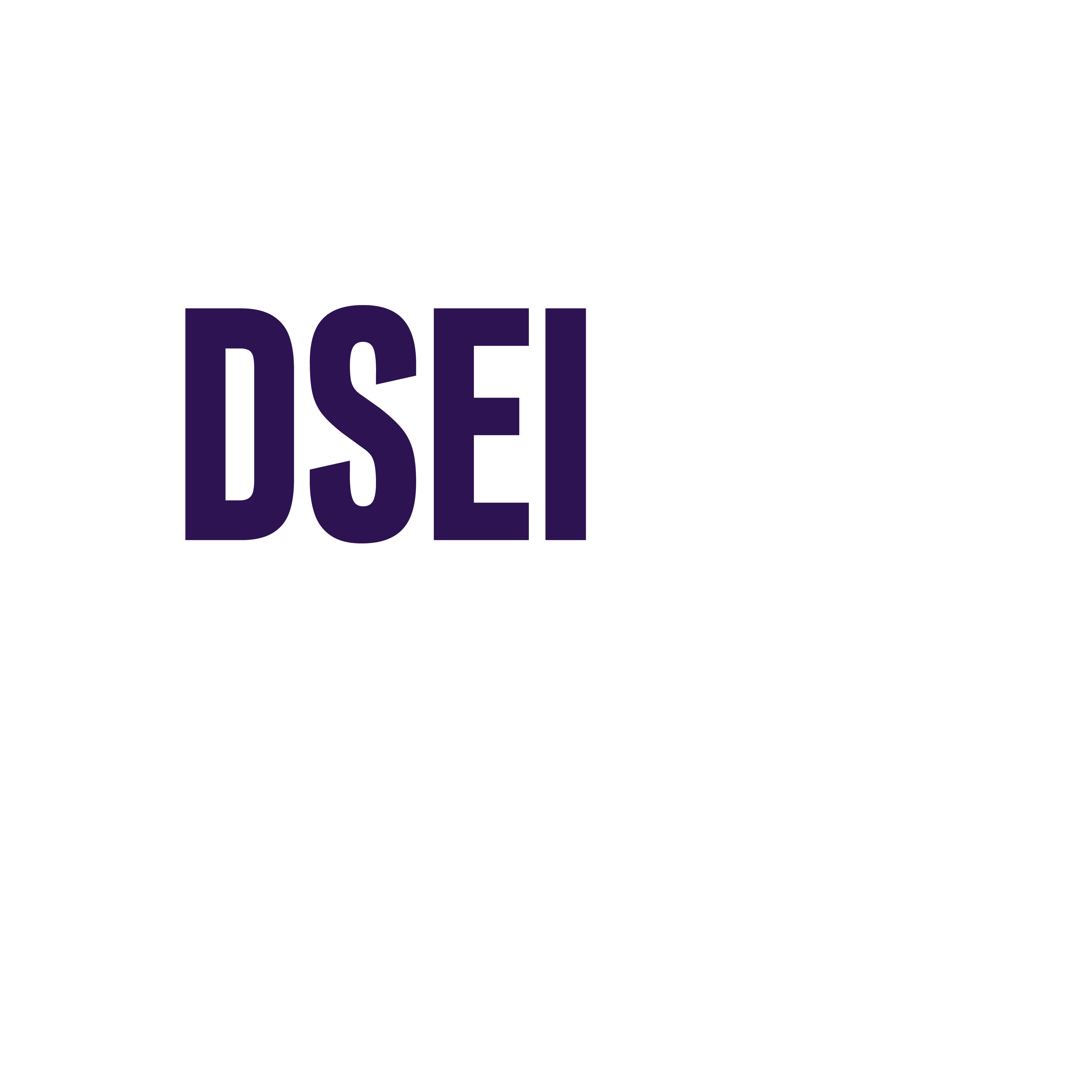
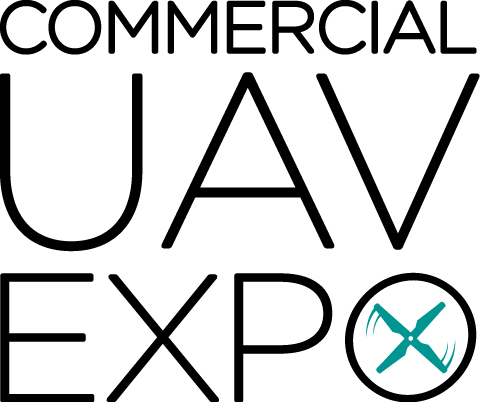
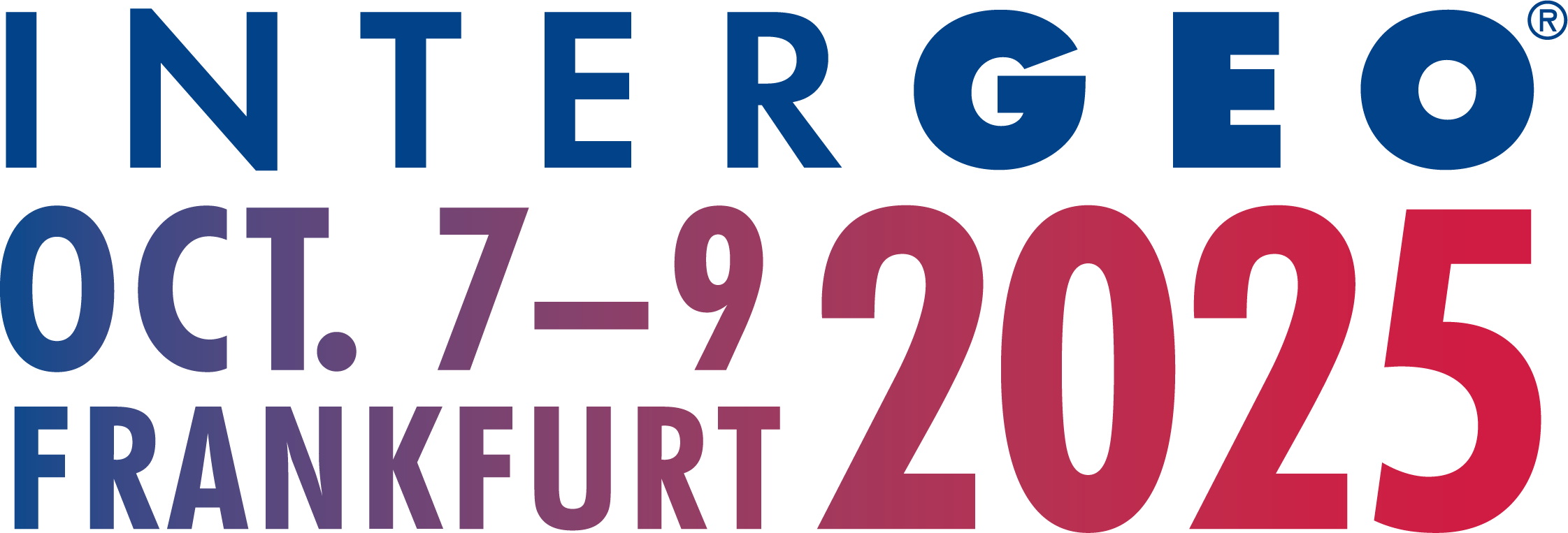
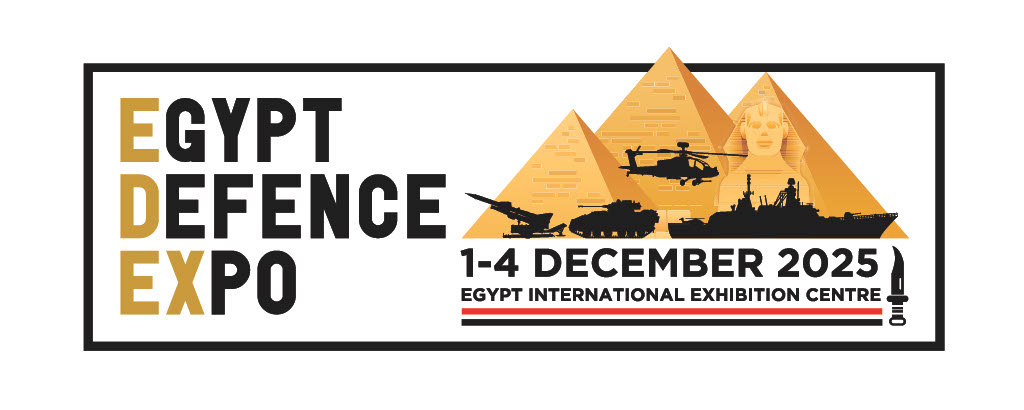
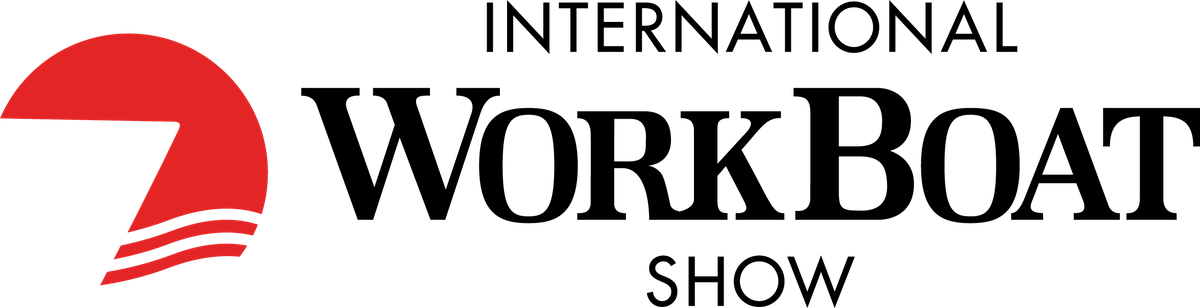