Encoders for AGV designs
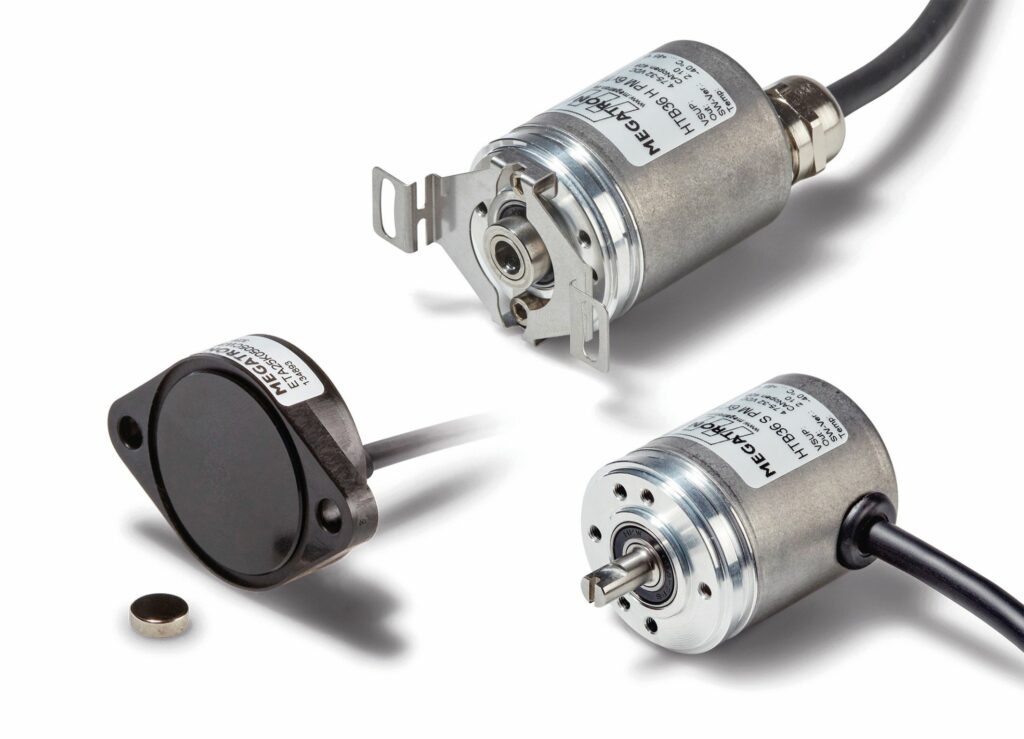
(Image courtesy of Megatron)
Megatron has developed two encoders for large autonomous ground vehicles such as forklift trucks, writes Nick Flaherty.
The encoders not only detect the steering angle but also the speed of automated guided vehicles (AGVs).
The kit encoders of the ETx25K series are particularly suitable for small AGVs because they require very little space with an installation height of only 8 mm. The single-turn or multi-turn versions have digital signal processing with magnetic gradient-based sensing. The encoders are available with a 12 bit analogue incremental or serial (SSI or SPI) interface.
A wide range of electronics for different power supplies and many electrical interfaces for data output allow the encoders to be integrated into the AGV design.
The robust HTx36 sensors can be used in larger AGVs such as autonomous forklifts. These encoders not only have a solid metal housing, but also incorporate a stainless steel shaft with double ball bearings, a durable bearing, and resistance to shock and vibration to withstand high axle loads and actuation speeds.
The absolute encoders operate with a resolution of 16 bits (single turn) or 43 bits (multi-turn) and are supplied with battery and gearless energy harvesting technology. This ensures that the encoders reliably detect the number of revolutions even when de-energised.
Digital communication interfaces such as CANopen, SAE J1939 and SSI also ensure optimum integration of the encoder into a design. The AGV manufacturer receives an encoder with a pre-programmed angular range that is precisely customised to the vehicle, saving costs in production and in programming the electronics.
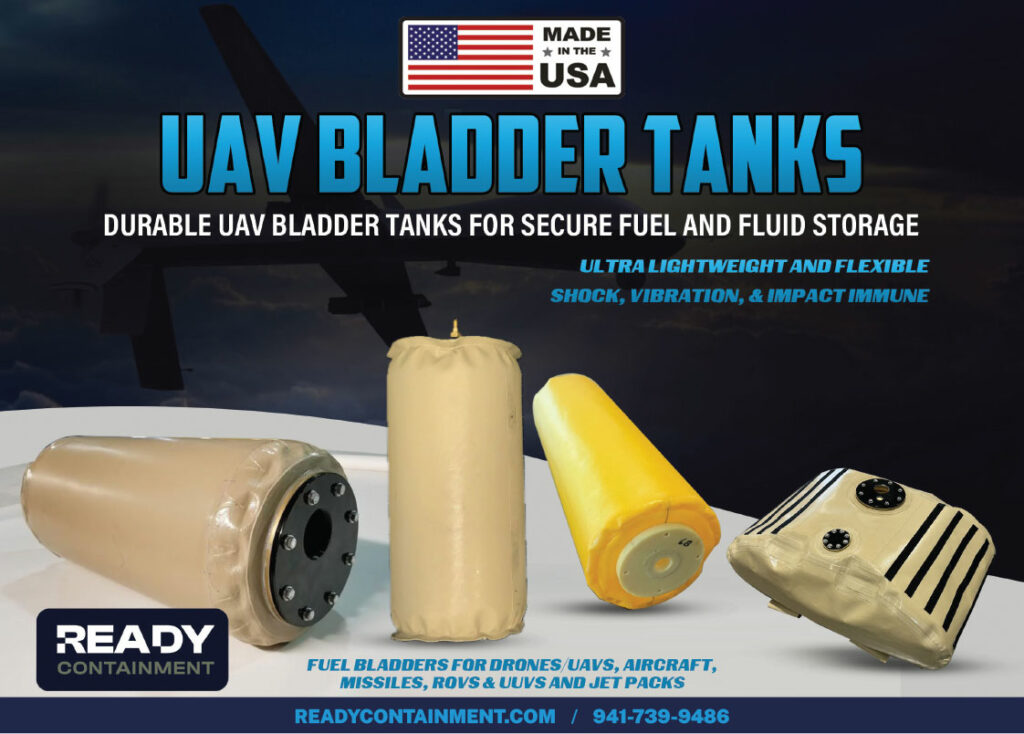
The CAN bus version also allows continuous monitoring of the encoder. For example, the encoder issues a warning if the shaft speed is exceeded, if the temperature range is exceeded, if there is a hardware defect (EEPROM) or if the CAN is overrun. High single- and multi-turn resolution ensures finely graded measurement results.
With the incremental version, the developer can select the number of pulses from 1 to 16,384 pulses per revolution in increments of 1, and set the index pulse to the desired position. The encoders are available with TTL or HTL output.
While the HTx36E encoders with the CAN bus offer various setting options in the LLS configuration mode, the HTx36PM absolute encoders with analogue output feature multi-turn electronics with a so-called teach-in function for flexibility in the field. This allows the user, for example, to set the start and end values of the output signal directly when installing the encoder using a simple programming device. This eliminates mechanical tolerances. However, the same encoder variant can be parameterised for different requirements, such as angular range, direction of rotation and power supply.
UPCOMING EVENTS
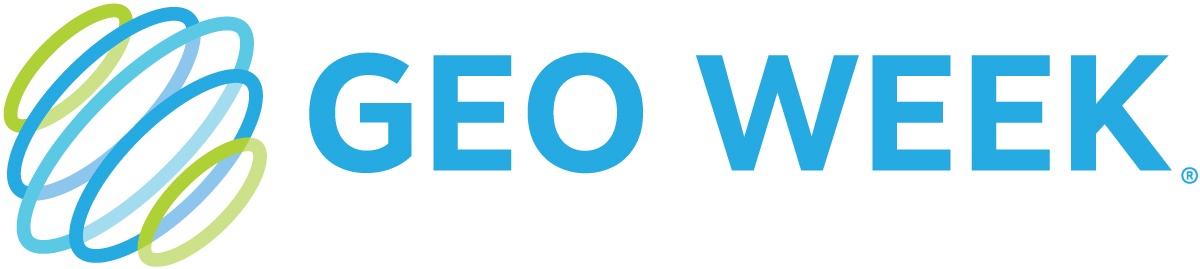
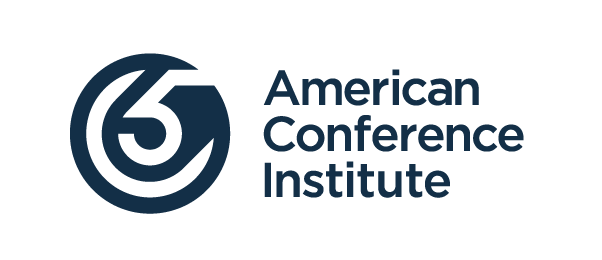
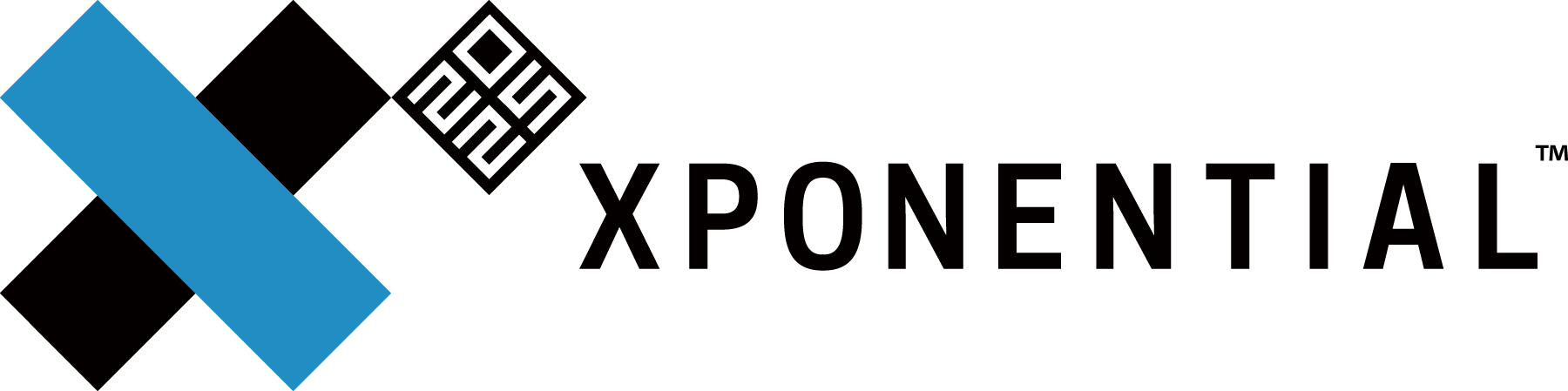
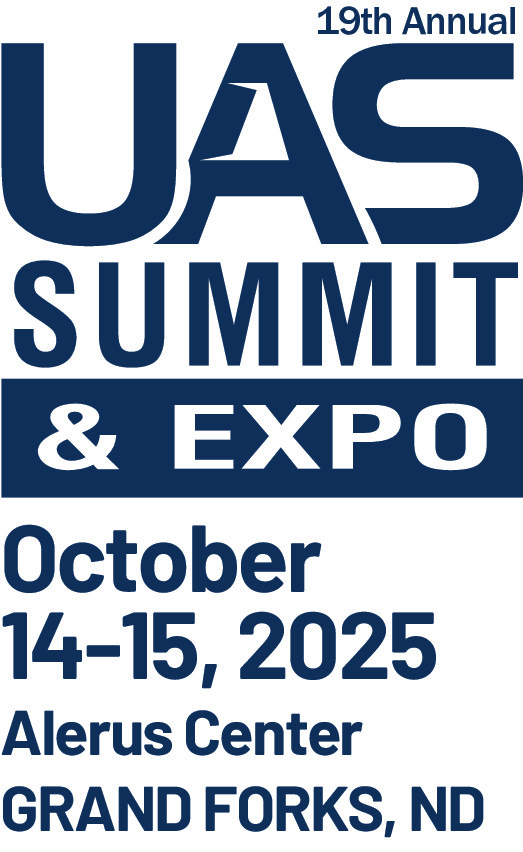
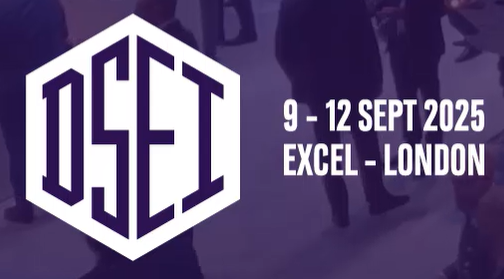
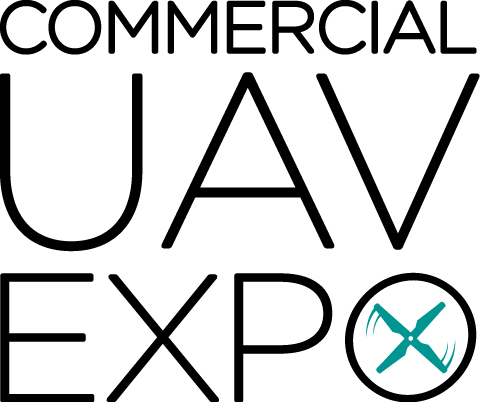
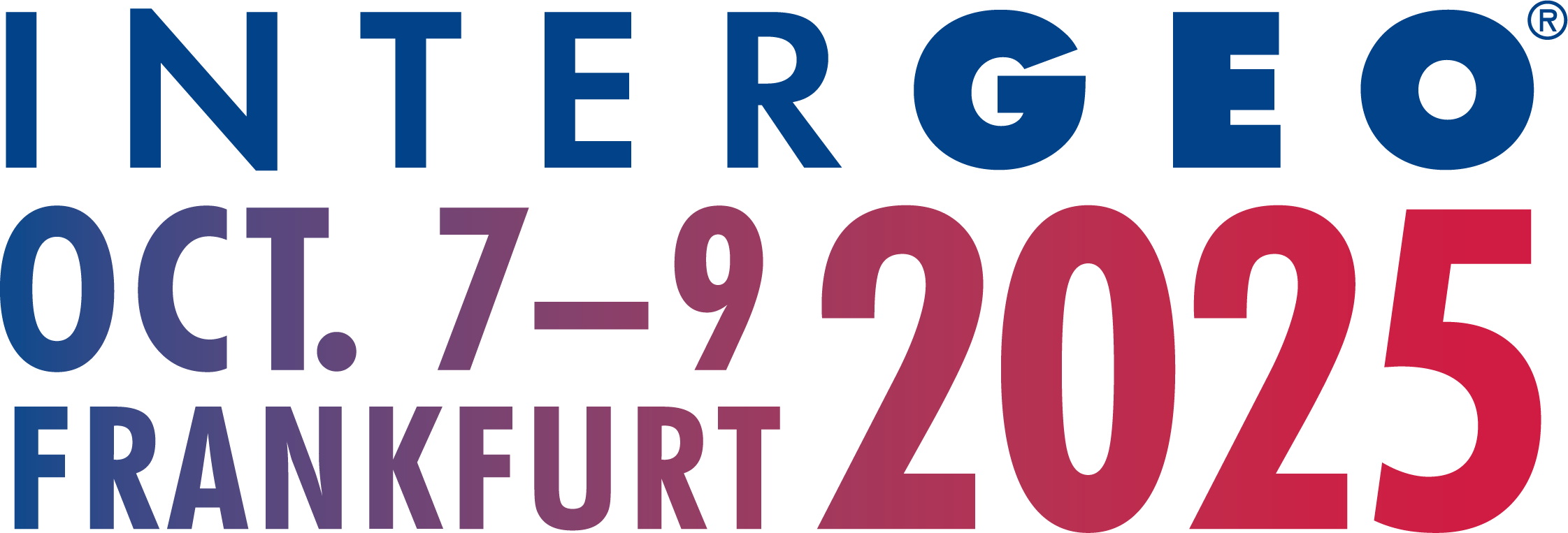
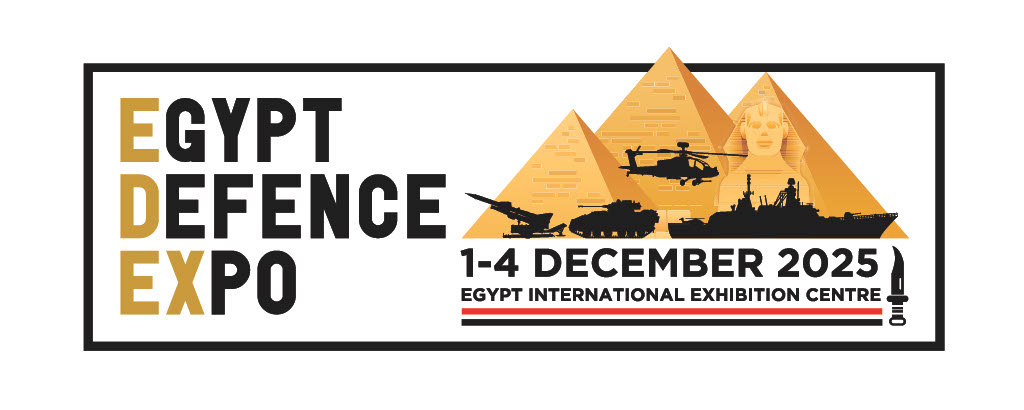
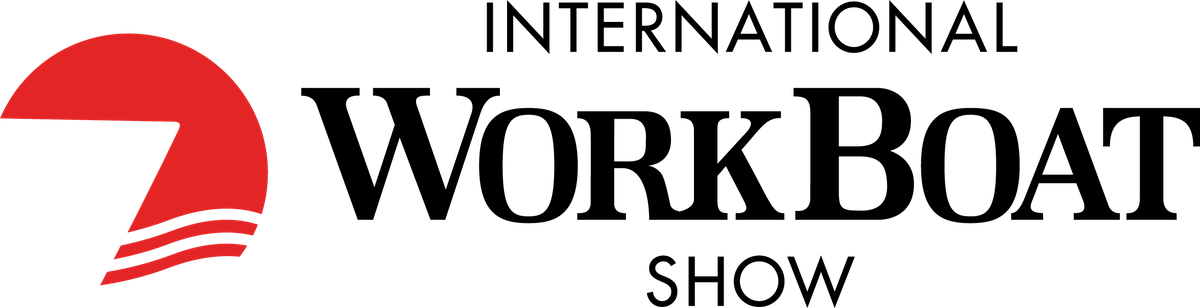
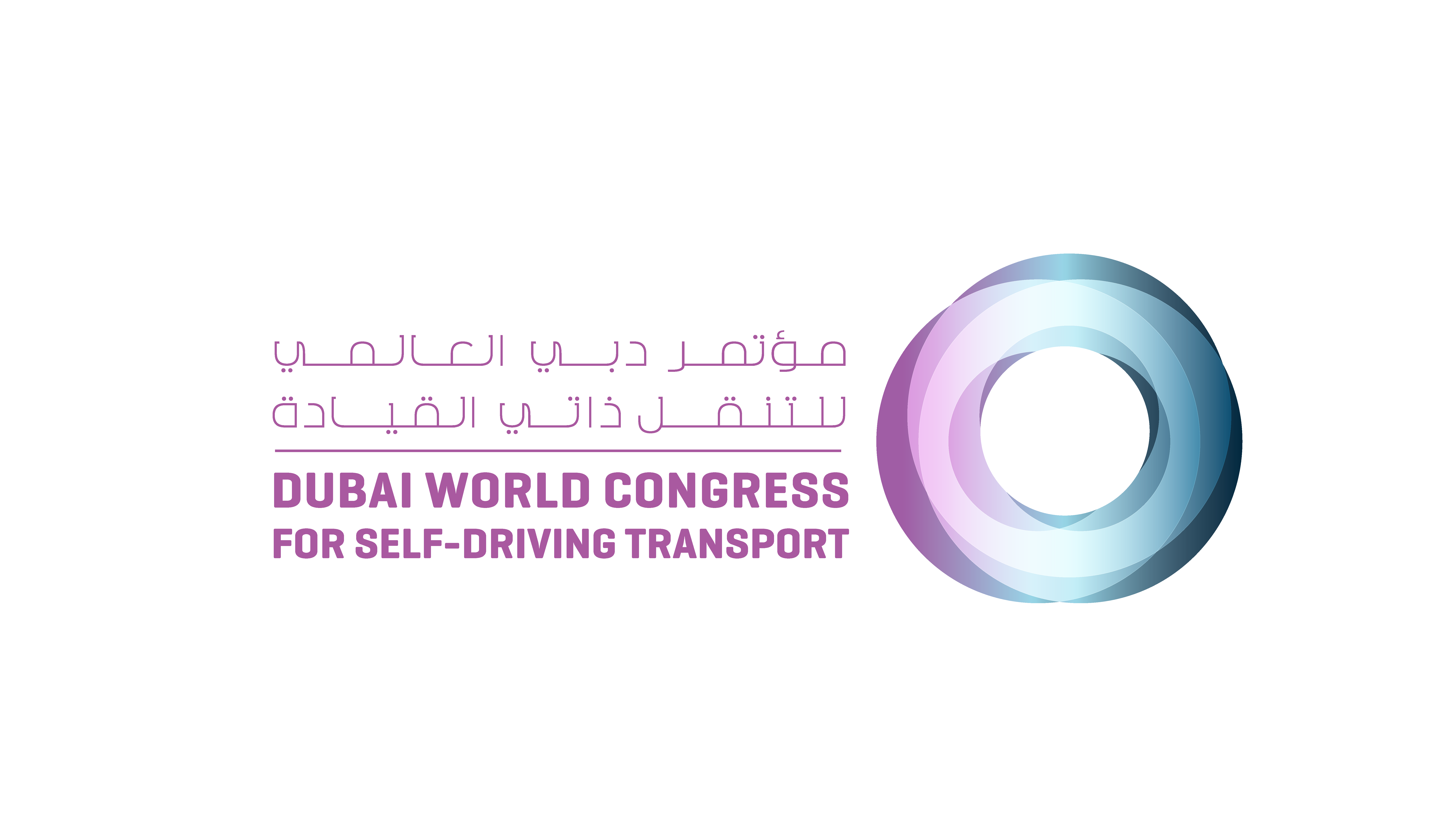
