Elroy Air Chaparral
Going the middle mile
Although still at the prototype stage, this hybrid-electric VTOL-transitioning UAV is garnering a lot of interest for heavyweight deliveries, as Rory Jackson explains
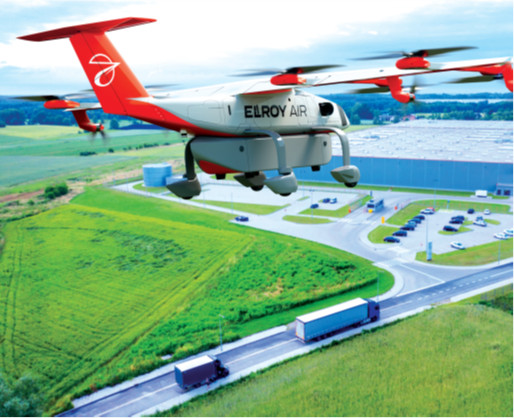
plans to launch test flights in 2023
(Images courtesy of Elroy Air)
Over the past few years, technological maturity among UAVs built for last mile logistics has spilled over into more complex aircraft systems designed for transporting heavier packages for aggregated middle mile deliveries.
One such system is being developed by Elroy Air, which was founded to provide large, uncrewed aerial courier services for shifting hundreds of kilos of cargo across hundreds of kilometres at great speed. Its core team includes experienced UAV developers with a common interest in pursuing what they saw as a growing variety of professional aircraft.
“We quickly received feedback that a large cargo drone would be valuable not just for express parcel logistics but also humanitarian aid, military resupply and more,” says David Merrill, Elroy Air’s CEO and co-founder. “The enthusiasm from our three major customer groups gave us confidence that developing our ideal aircraft was worth pursuing.”
Merrill and his team began exploring different configurations, including large multi-rotors and winged aircraft, as well as some studies into solutions for the technically similar urban air mobility (UAM) space. In 2019, the company’s r&d led to a test flight for an early prototype of what would become the Chaparral C1, Elroy Air’s pre-production version of its flagship Chaparral UAV.
“That early flight test campaign proved out several of the key technical directions that we’ve used and matured in the C1,” Merrill says. “Having confirmed our team’s ability to execute and validate several key technologies, we continued on towards the C1, developing the concept further – of a powerful and fast method of autonomous freight delivery that doesn’t depend on airports – then building it and validating systems internally along the way.”
Designing the Chaparral
The pre-production Chaparral was unveiled to the public in January, taking the form of a transitioning VTOL hybrid electric UAV that will ultimately carry 136- 227 kg of freight over more than 480 km in its mature form.
The system forgoes tilt-rotor mechanisms or tail-sitting behaviour; instead, it uses entirely fixed-pitch rotors
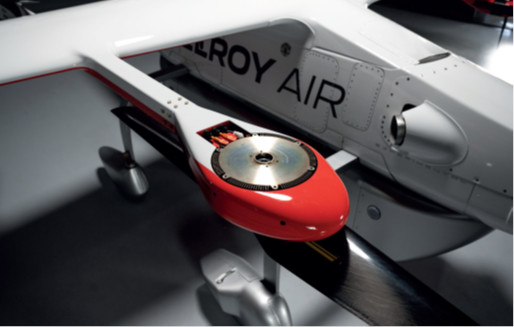
in a ‘lift-plus-cruise’ fixed-wing/multi-rotor hybrid configuration, although unlike most such UAVs we have featured previously, the Chaparral is shaped much like a traditional air cargo plane rather than a twin-boom aircraft. Its fuselage runs the entire 5.8 m length from the nose to the tail, with a straight (non-sweeping) and tapered 8 m span wing with a high aspect ratio.
At the upper rear sits a 2.2 m-high T-tail, and beneath the fuselage are landing gear with a wide stance that end in electrically motorised wheel pods for taxiing. The hull sections are carbon fibre to ensure a lightweight yet stiff construction for the powered wheel pods and its propulsors, 12 of which are distributed across the wings.
Four of the Chaparral’s propulsors are forward-facing electric motor drives mounted on pylons that hang below the wings, while the other eight are oriented vertically. Four of those eight point downwards on booms that extend forward from the wings, while the other four face upwards at the ends of booms protruding back from the wings. All 12 drive dual-blade carbon fibre props, with electric power from a turboshaft engine driving an electric generator.
“In many ways, the Chaparral resembles the kinds of eVTOL and UAM aircraft we’re seeing from our peers, such as Joby, Kittyhawk and so on, but the Chaparral has a few unique features that tailor it to the uncrewed air freight application,” Merrill says.
“One of those is the hybrid-electric powertrain, which enables a much longer range than a battery-electric vehicle and austere operations. That’s still fairly rare, even for this new generation of transitioning- VTOL aircraft,” he adds. “They’re difficult to engineer, and there are more parts that need inspecting and replacing, but the range and flexibility they enable are invaluable to our logistics customers.”
Another differentiator in the Chaparral is its automated cargo-handling robotics, which have been engineered to enable unattended taxiing, securing and release of cargo loads while it is on the ground. That is a critical factor in Elroy Air’s efforts to make much of the Chaparral’s operations autonomous.
“The big benefit of that autonomy in express air shipping is that the vehicle doesn’t need to wait around on the ground for ages to be loaded or unloaded,” Merrill says. “It can do all that by itself, leaving the workers on the ground free to focus on checking cargo manifests, moving pallets to where the aircraft taxis pick them up, and carrying out maintenance of the aircraft themselves when necessary.”
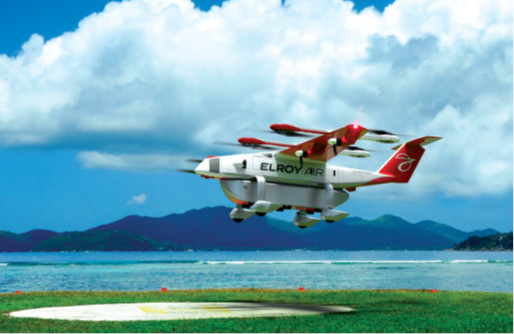
infrastructure, and avoid the maintenance costs and idle
times of helicopters and traditional air freight craft
The wing has a bearing that allows it to rotate 90º when necessary. This means that when it’s unfastened, the wing can be swivelled in line with the fuselage to give the airframe a footprint slender enough to fit inside a C130 Hercules for transport – particularly useful for the company’s potential military users.
“Enabling stowage without taking the whole aircraft apart is a significant saver in time and costs,” Merrill says. “Also, the tail is designed with a hinge to fold it back and down once it’s been unscrewed, to keep it out of the way of the rotating wing.
“These stowage factors also mean the Chaparral can be fitted inside a 40 ft standard shipping container, allowing our commercial and humanitarian customers to ship their vehicles anywhere in the world using standard transport, then rapidly set them up for flight.”
At the moment, those customers include AYR Logistics, which plans to order up to 100 Chaparrals to improve its transportation of humanitarian supplies around the world on behalf of organisations such as the UN, the World Food Programme and various governmental bodies and NGOs.
The US Air Force has also awarded Elroy Air a Tactical Funding Increase Award of $1.7 million in contract value alongside its existing Phase 3 SBIR contract. The new award is aimed at further developing the Chaparral’s deployment capabilities and CONOPS in collaboration with the USAF and Agility Prime, the USAF’s programme tasked with accelerating commercial eVTOL development.
Overall, more than 900 Chaparrals have been requested by customers. Elroy plans to produce several UAVs next year, 10-20 the following year, then dozens to hundreds in the years following.
Merrill comments, “It’s important to our production and scaling goals to remain largely a systems integrator, using COTS components wherever we can so that we don’t expend resources on reinventing the wheel for things like actuators, motors, engines and so on.”
Cargo pick-up
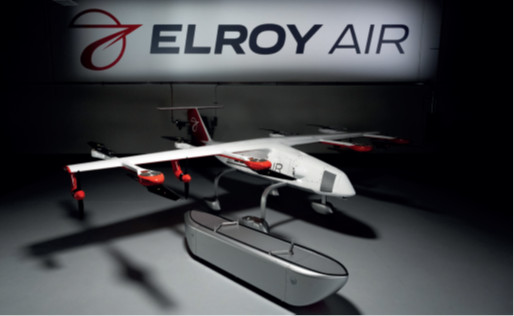
automated pick-ups and drop-offs
Elroy Air has developed several iterations of its cargo pod, as the Chaparral’s payload capabilities can be customised to meet the needs of different customer missions. The pod is a modular element of the Chaparral system, being designed for automated pick-up and drop-off by the vehicle, and to permit functional and aesthetic variations.
It currently has a canoe-like shape for the sake of aerodynamics. It is made from carbon fibre, like the Chaparral airframe, has a pallet base and is enclosed on all sides with a fairing to protect cargo from the elements on the ground and in flight.
Each pod also has four locator beacons on its approximate corners, to allow the Chaparral to align itself over the pods. It can detect the identity and location of a pod at up to several hundred metres.
“They are ultra-wideband RF beacons similar to Apple AirTags, and the Chaparrals have corresponding transponders to triangulate the pod positions relative to themselves without needing something more complex and subject to environmental variations like computer vision to recognise and approach them,” Merrill explains.
“Of course, we also use GNSS to tell the UAVs approximately where to navigate, for instance to the default pod pick-up location, but the beacons add the precision that enables a Chaparral to roll up and align its fuselage over its assigned cargo pod to within a couple of centimetres of accuracy – close enough that the automated grasping system can then pick up their container – all without needing RTK-GNSS.”
And when the Chaparral is taxiing to a cargo pod to pick it up, and afterwards taxiing to a take-off area, two automotive grade Lidars mounted at the front and rear are used for perception of ground objects to autonomously prevent collisions.
The company has also developed specialised robotic systems that work together to ensure that the physical act of cargo loading and unloading can be performed autonomously.
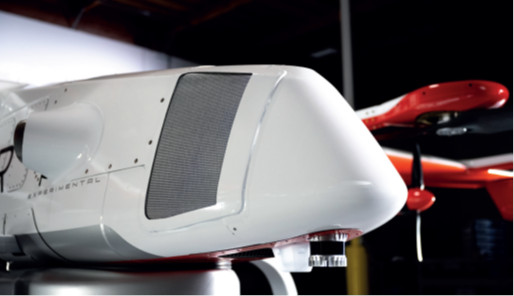
First, on the underside of the Chaparral is a ‘grasper’ mechanism hung from straps that winch it up and down. It’s a telescopic metal bar with linear actuators inside and open-receptacle ends, and can of course extend outwards and back.
The cargo container meanwhile has two V-shaped tracks, one at each end of its top side. Once the Chaparral has taxied over the container, the grasper is lowered from the undercarriage down to the height of the tracks, contracted at this point in order to fit easily between the connectors.
When it’s low enough, the actuators telescope the grasper outwards to seek the end of the tracks and keep a rigid hold on them while the grasper and pod are winched up snug to the undercarriage. Hasps at the corners of the pod are latched by mechanisms inside the fuselage, connecting the pod to the Chaparral’s hard points for the duration of the flight.
“At each end of the grasper is an open ‘fish mouth’ shape that is metal like the V-tracks and shaped to engage with, then slide along them easily,” Merrill says.
“The funnel-like shape of the V-tracks makes them tolerant of up to 15 cm position divergence, which is much wider than the beacons’ actual margin of error.
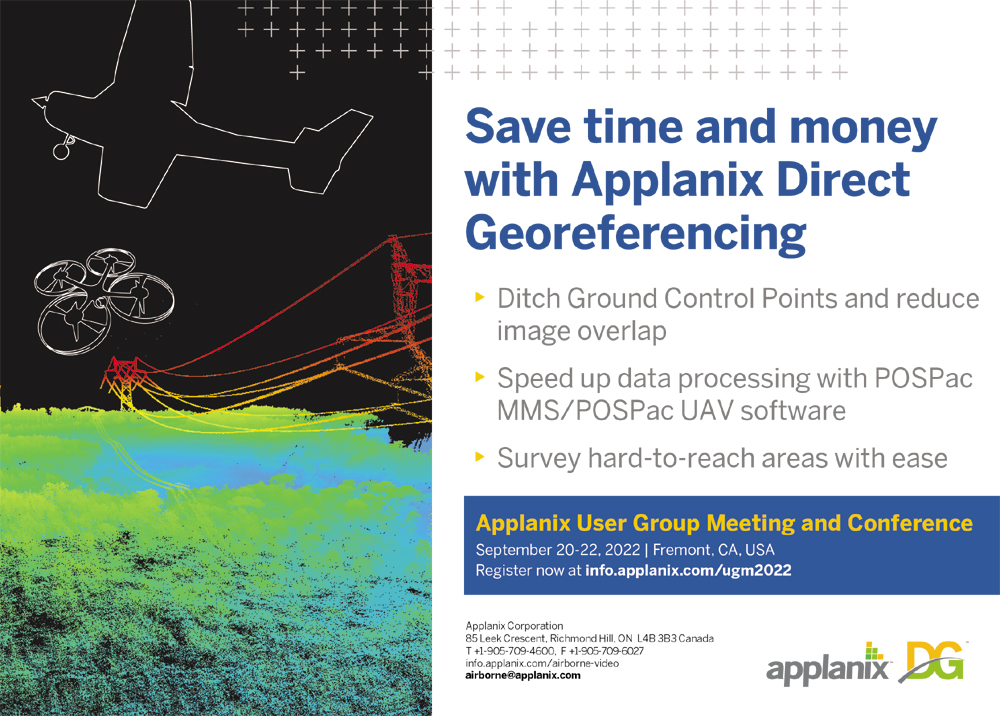
“Once the grasper winches the pod up to the UAV, a rubber gasket running along the upper edge of the pod helps to press and seal the container against the undercarriage.
“As this system was developed specifically for the Chaparral to automate its cargo handling, we have a unique test bench for constantly testing the mechanism under different conditions.”
Scheduled flights
Elroy Air anticipates that most of the Chaparral’s flights will be scheduled, regular deliveries, rather than ad hoc last-mile routes. For instance, earlier this year the company announced a partnership with US-based Mesa Airlines, which indicated its intention to order 150 Chaparral systems for its services in express parcel and healthcare logistics.
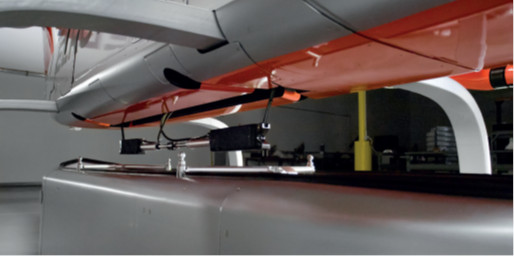
“We’ll be serving middle-mile B2B journeys such as airport-to-warehouse, warehouse-to-warehouse or warehouse to- retailer routes, which are mostly serviced at the moment using a combination of trucks and light aircraft,” Merrill says.
“Each Chaparral will run multiple missions per day, which is quite a bit different from how today’s feeder or regional air cargo are used. They often run just one flight out in the morning and then a return flight in the afternoon, with the asset sitting around the rest of the time.”
As an uncrewed system with lower operating costs and VTOL capability, the Chaparral will operate for long hours, flying multiple deliveries per day. Sometimes that will be in a hub-and spoke model, where a user has a central distribution centre with goods that go out to multiple places; at other times it will operate a milk run, where a single UAV makes multiple deliveries in a multi-leg circle on its way back to its origin.
“Broadly, we’ll be serving the need for express logistics that is stemming partially from a demand for shippers to meet the global growth in e-commerce, and also to differentiate themselves by offering faster and more flexible He adds that humanitarian users such as AYR would traditionally have used manned helicopters for carrying and landing aid pallets, but the expense of operating rotorcraft coupled with the risk that certain missions pose to pilots and crew make UAVs an appealing option.
Fleet maintenance and safety
As with its cargo latching mechanism, Elroy Air has developed other test benches in-house for proving the components selected for the Chaparral, particularly with respect to its powertrain.
“We built our thrust-test stand a few years ago to fully characterise, burn-in and measure the performance of electric motors, motor controllers and propellers,” Merrill says. “We took design inspiration from a stand NASA had built for similar purposes, and our tool allows us to run propulsors in excess of full mission operating parameters to benchmark rpm, thrusting force, torque, temperature, vibration, electrical current draw and more.
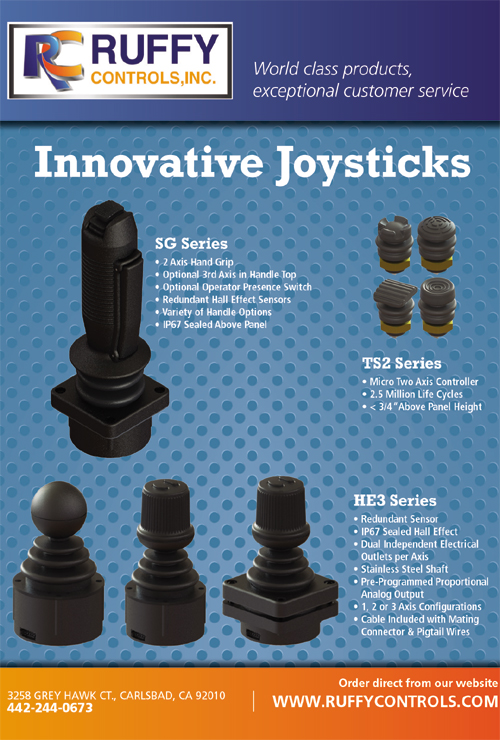
“We also have developed a full ‘iron bird’ test bench, encompassing the C1’s powerplant, propulsors and control surface actuators, on a trailer. That enables us to run full mission profiles to characterise and validate performance in advance of flight tests, so we can find and fix problems on the ground before they can happen in the air.”
At the time of writing, the iron bird contained the C1’s turboshaft engine and electrical generator, as well as fuel tanks, a battery pack, a power distribution box, four vertical flight motors and several control surface actuators. The system has enabled Elroy Air to run sustained powertrain performance tests to validate full mission power levels.
Connected assemblies of the Chaparral’s avionics are also set up in the company’s facility to run hardware-in-the- loop tests in tandem with its in-house simulation environment. Running its flight code and control laws in simulation with avionics operating against the simulated environment and data allows the team to find and eliminate comms bottlenecks or other faults that can crop up when hardware and software operate together.
The company anticipates that each vehicle will need perhaps 30 minutes of visual inspection each day, with onboard health monitoring systems expected to spot and flag up most potential issues.
“With the redundancy we have designed into the electric motors and power system, any Chaparral suffering a power fault or propulsor failure should always be able to complete its mission and transmit its need for maintenance ahead of landing – unlike traditional helicopters – reducing the urgency, length and regularity of inspections,” Merrill says.
“Typically, during take-off and landing, the high power demands of vertical flight mean we’ll have both the engine and battery delivering electrical power, but if the engine ever gives out completely the vehicle can make a safe landing on battery power,” he adds. “We deliberately kept the battery small to optimise aircraft weight, which helps any Chaparral with an engine failure to glide towards its intended landing coordinates and then bring itself down vertically to land.”
Future steps
The company is working with US government partners on certification, vehicle testing and operational concept development. Merrill cites a previous test flight campaign at the Naval Postgraduate School’s (NPS) test range at Camp Roberts in California as being representative of its productive ongoing partnership with NPS, and adds that the test flights were cleared in a very streamlined manner.
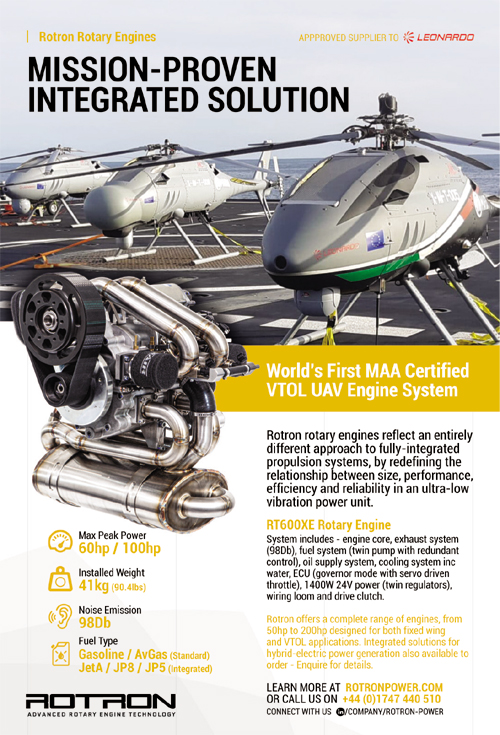
Full type certification for the Chaparral is expected to take a few years, given the nature of the process, so in the meantime Elroy Air plans to focus on setting up early commercial operations overseas, in places where civil aviation authorities can quickly approve aircraft for commercial service.
“That way, overseas humanitarian and commercial customers will be able to deploy the Chaparral while we’re working through FAA type certification,” Merrill says. “We have strong relationships with prospective customers in Africa, Australia and the Middle East for example, who want to carry packages, cargo and relief supplies using Chaparral systems.”
Elroy Air is also preparing for flight tests with the USAF, which are set to begin soon. At the time of writing, the final subsystem integrations and validations of the C1 prototypes were underway.
“Envelope expansion with the USAF will occupy the first and second C1 vehicles from now until the middle of next year, then in the back half of 2023 we’ll focus on demonstrating its capabilities with some commercial partnerships,” Merrill adds.
A key commercial partner is FedEx Express, which was announced in March. The parcel-logistics giant plans to test and observe how the Chaparral handles middle-mile shipments between its facilities, which could pave the way to larger operational deployments. Other partners are expected to be announced in the next few months.
Specifications
Elroy Air Chaparral
Hybrid-electric powerplant
All-electric propulsion
MTOW: 865 kg
Payload capacity: 136 kg (nominal) 227 kg (maximum)
Length x wingspan: 5.8 x 8 m
Maximum altitude: 18,000 ft
Maximum airspeed: 125 knots
Maximum flight endurance: 8.5 hours
Maximum propulsion power output: 250 kW
Nominal range: 482 km
UPCOMING EVENTS
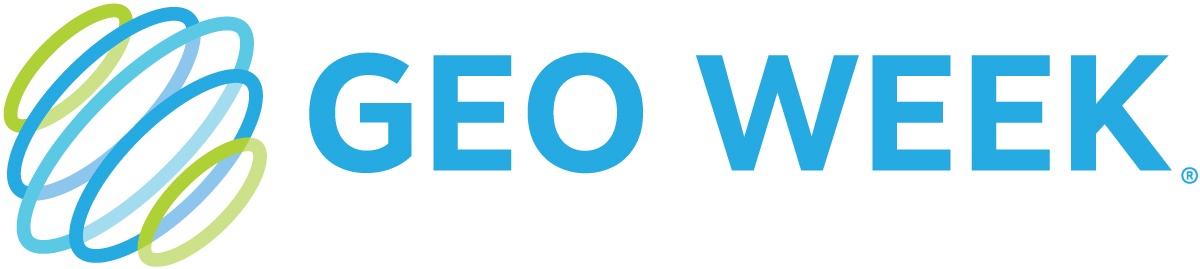
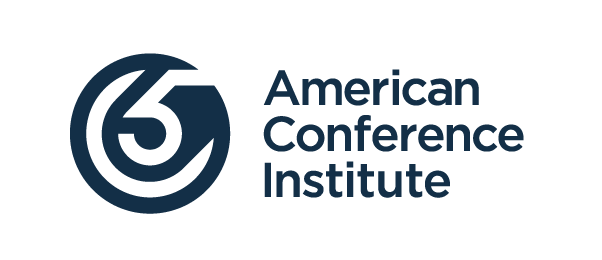
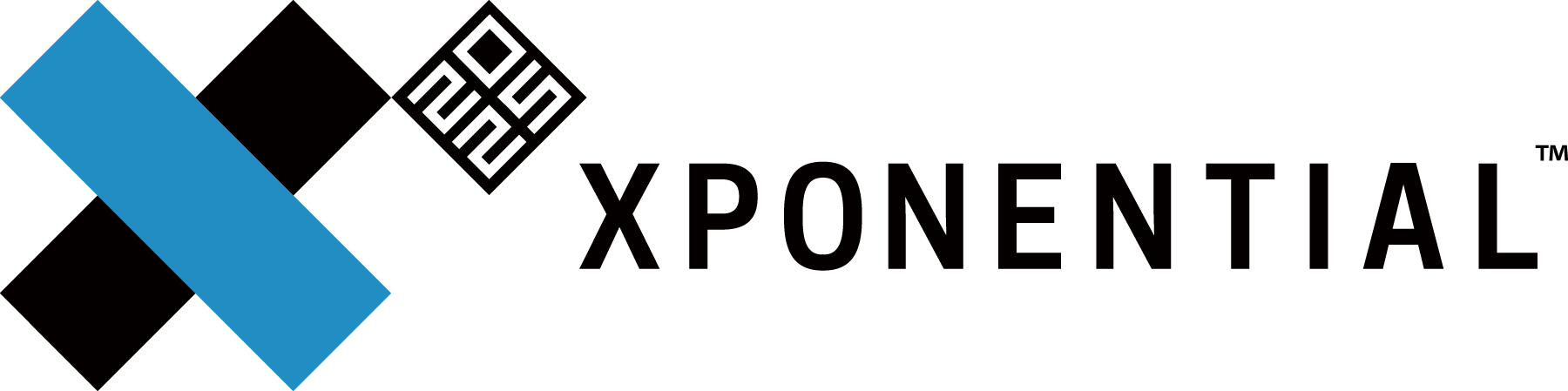
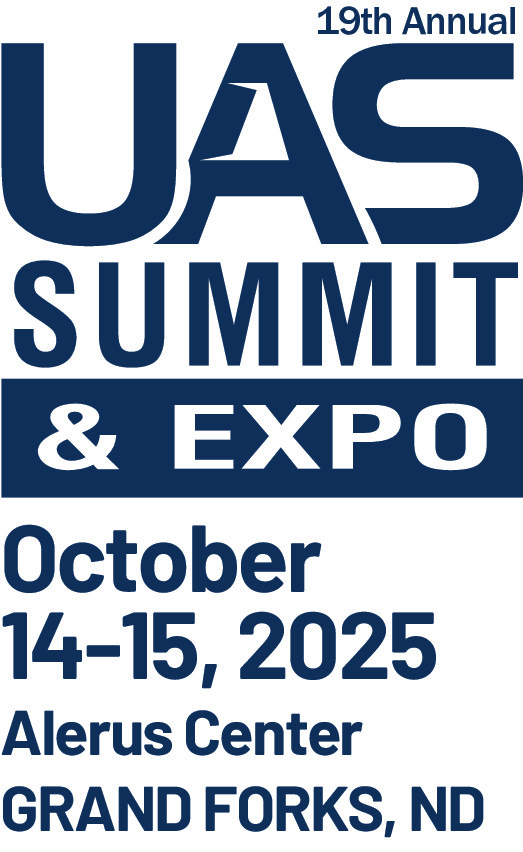
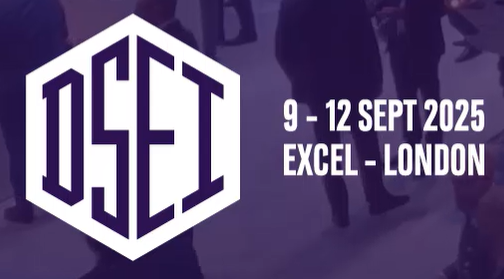
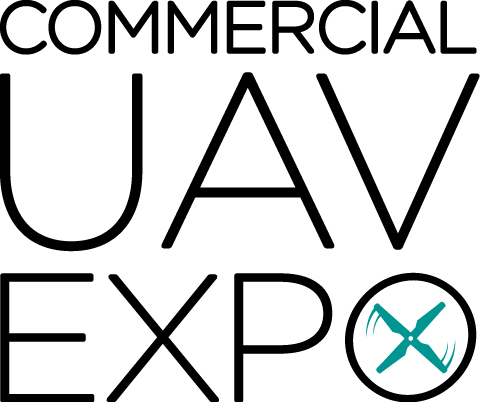
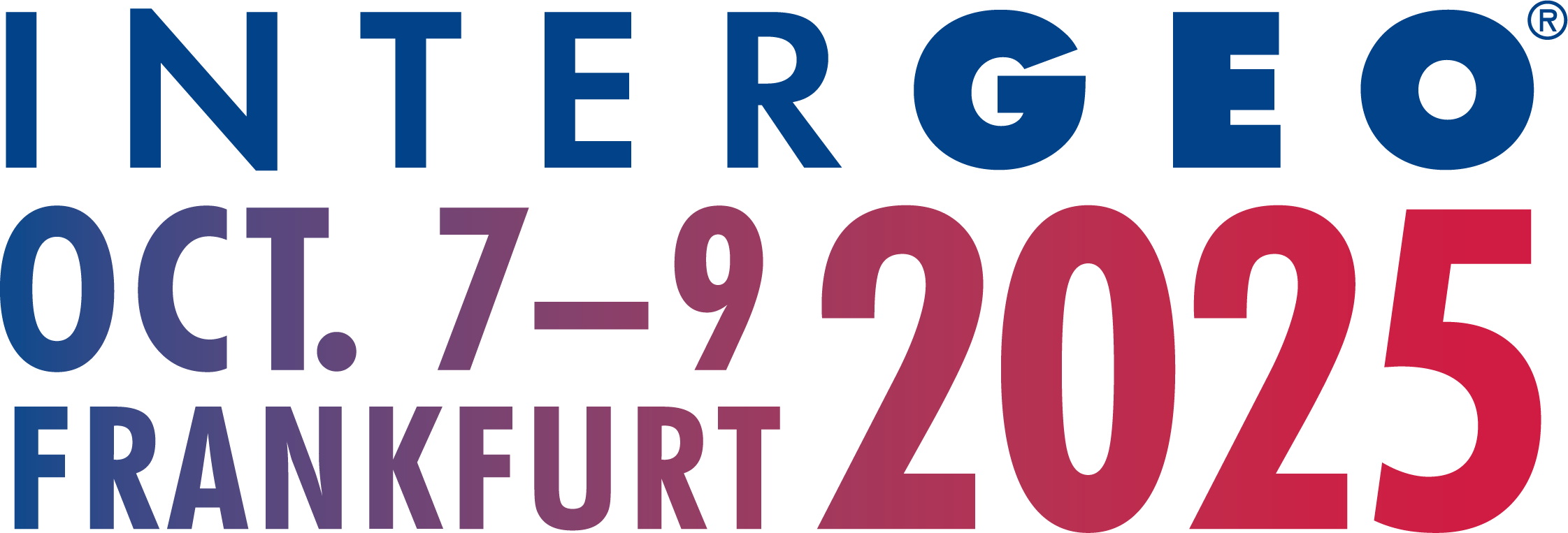
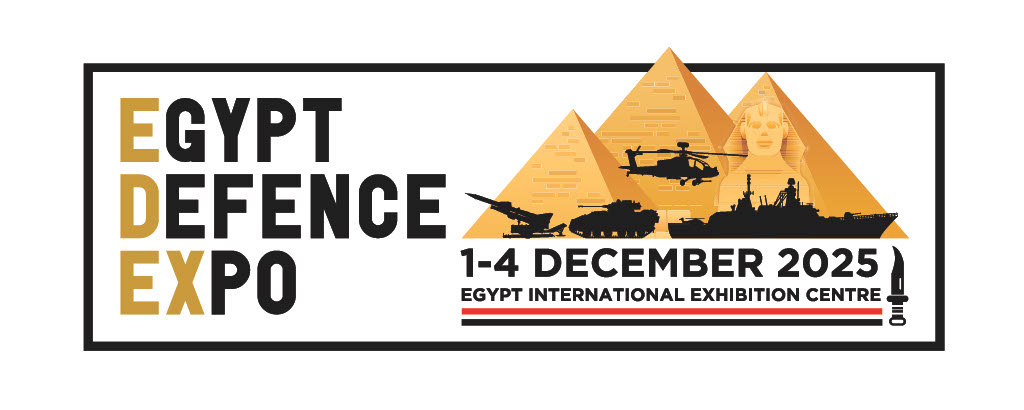
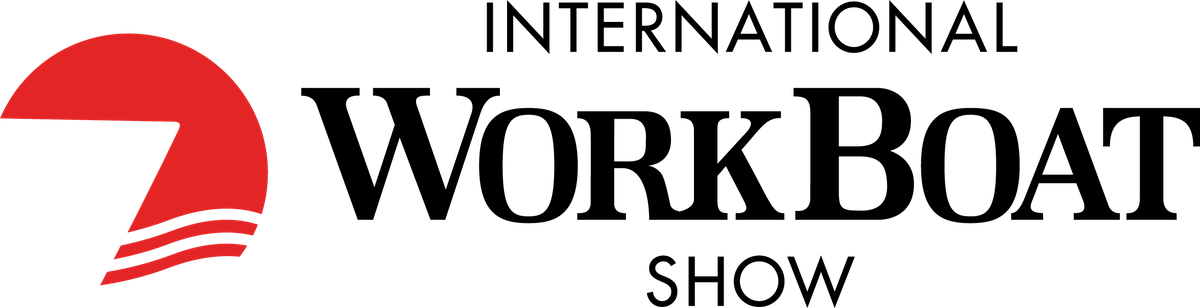
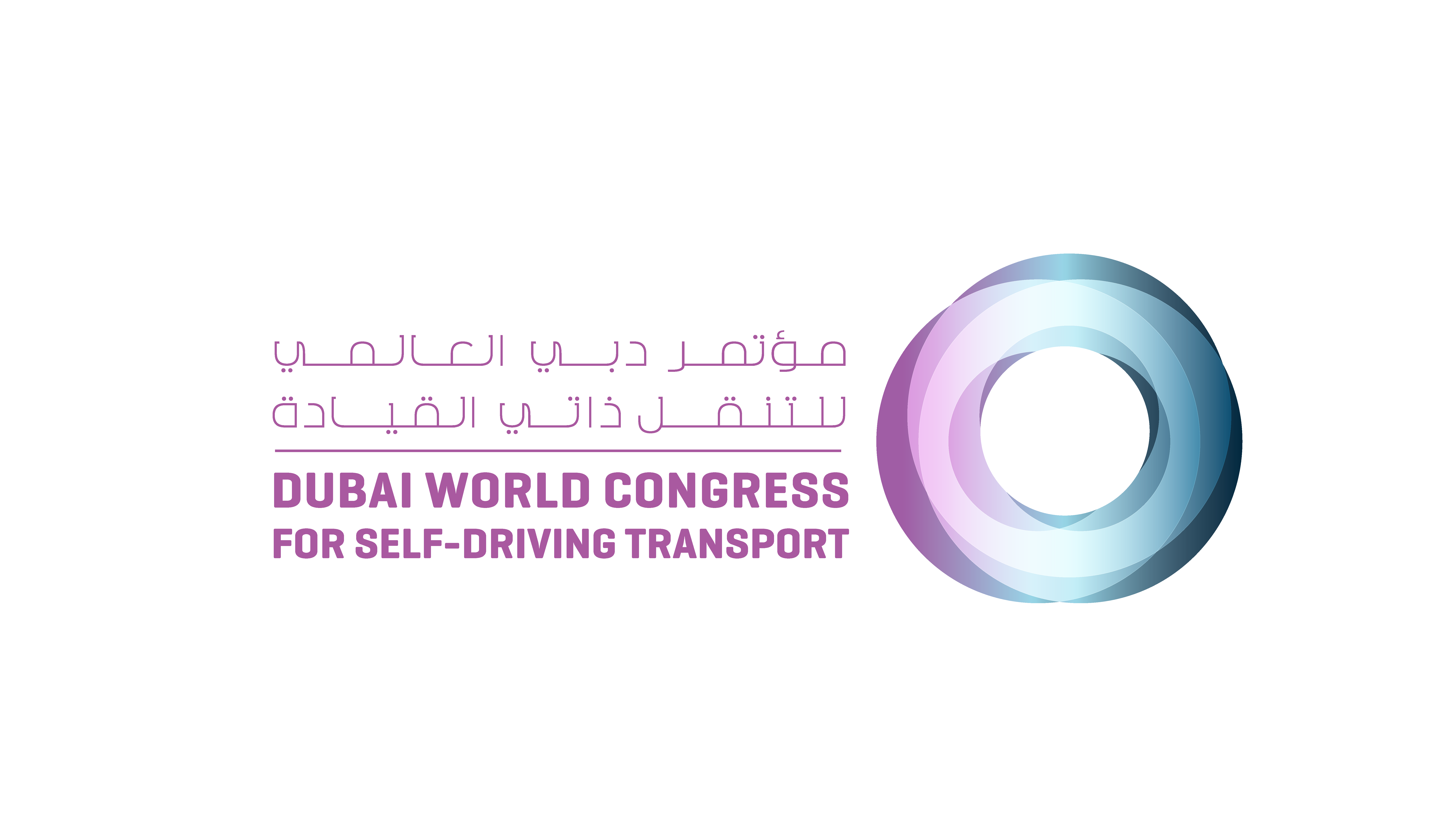
