Dropla mine countermeasures
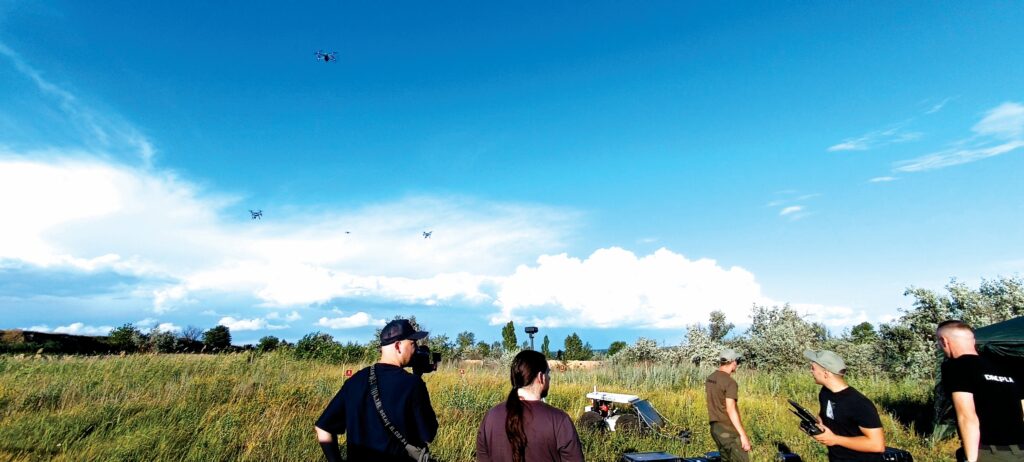
(All images courtesy of Dropla)
A world without mines
Rory Jackson examines a solution for the autonomous surveying, detection and clearance of landmines in Ukraine
In August 2023, much of the media surrounding the war in Ukraine was focused on an incipient counteroffensive, aimed at retaking occupied territories, including the Donetsk and Zaporizhzhia oblasts. By December, however, media and analysts judged the reprisal a failure, with only a handful of villages recaptured, and many noted how the Ukrainian troops seemed to advance far slower than predicted.
While Russian artillery, aviation and UAVs played a huge part in hindering Ukrainian advancements, the biggest culprit was landmines, which slowed them down, leaving them exposed.
Today, Ukraine is the most heavily landmined country on Earth: as of writing, around 131,000 km2 of its area (roughly the size of Greece, and slightly larger than the US state of Mississippi) is effectively inaccessible due to landmine contamination. This includes 26,000 km2 of non-occupied farmland, threatening Ukraine’s food security and prospects for post-war economic wellness.
Due to this problem, Ukraine established the 10-year National Mine Action Strategy, and it is also why V’yacheslav ‘Slava’ Shvaydak, a lieutenant in the armoured division, founded Dropla. Headquartered in Odense, Denmark, the company developed some of its technological IP as part of the Odense Robotics StartUp Fund and incubator, co-located with the Danish Technological Institute. It also has engineering facilities in Ukraine and the US.
Dropla has drawn worldwide attention for its multifaceted and highly tailored de-mining strategy, combining UAVs, UGVs, sensors, AI and augmented reality (AR) systems to realise its shared dream of not only a mine-free Ukraine, but potentially a whole world without landmines.
Now CEO of Dropla, Shvaydak tells us: “One might not think landmines should still be a problem in 2025 – in the age of AI, autonomous vehicles and high-speed signal processing – but detecting landmines remains an unsolved technical challenge, and I do believe it’s going to take quantum sensing and computing to tell safe land from unsafe land with 100% veracity.”
As of writing, Dropla is using remote sensing technologies, deployed on a fleet of UAVs for wide-area surveying, in an initial “detection” phase of operations, which forms a map of landmine locations and depths, with UGVs then being used for a second, ground-based, “confirmation” phase.
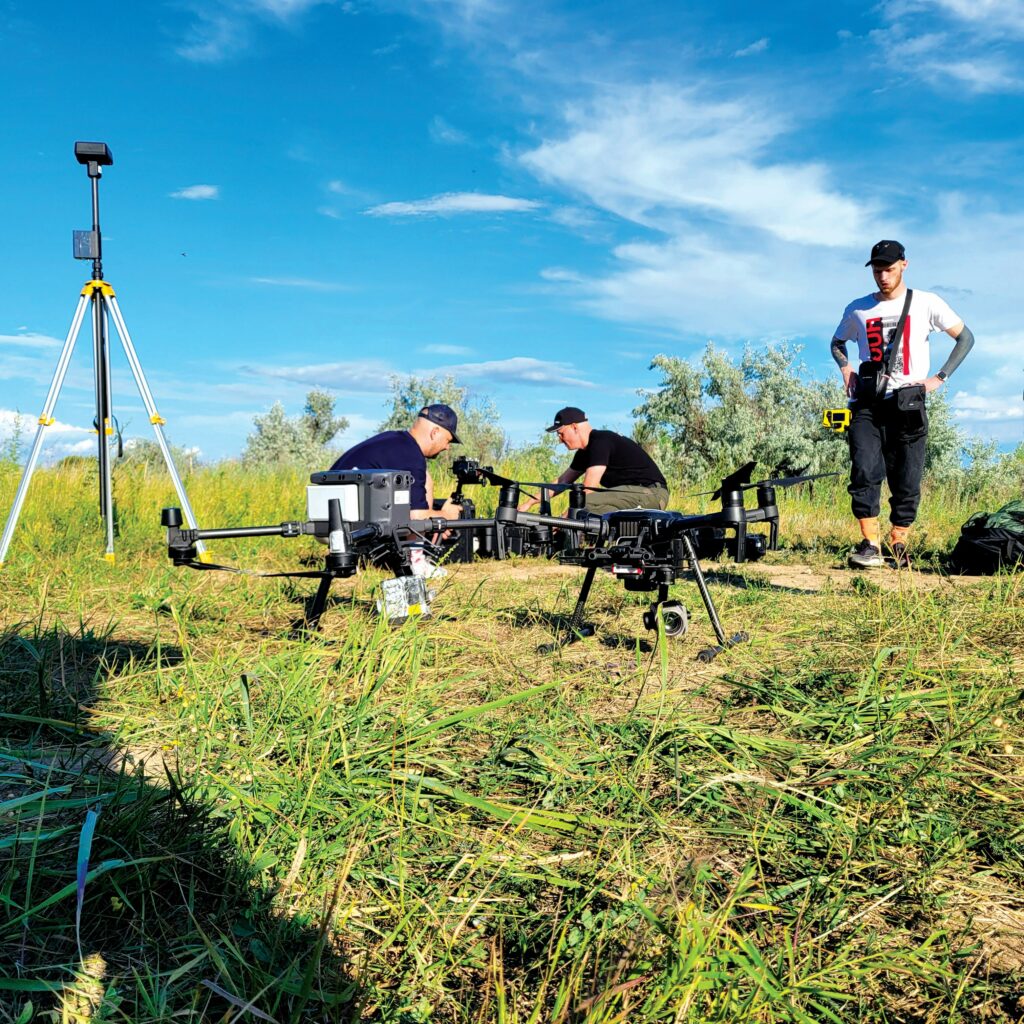
“Right now, our drones don’t communicate with each other or exchange position information. They each run their own separate mission, with only internal communications, purely to speed up data acquisition,” Shvaydak says.
“Scanning 50 hectares with seven sensors and one UAV will take a week; do it with six drones and you’ll be finished in a day. And, today, at our live testing ground in Ukraine, co-developed with an engineering regiment of the Ukrainian Army, we’re clocking 30 hectares per day, reaching operational excellence to perform the real contracts for technical surveying in 2025.”
He says the biggest effect of landmines stems not from their ordnance, but from the fear of encountering them: reports from international de-mining groups over the last 10 years estimate that just 2.5-5% of “suspected hazardous area [SHA]” will end up being actual “defined hazardous area [DHA]”, meaning dangerous land meriting direct technical intervention to remove landmines.
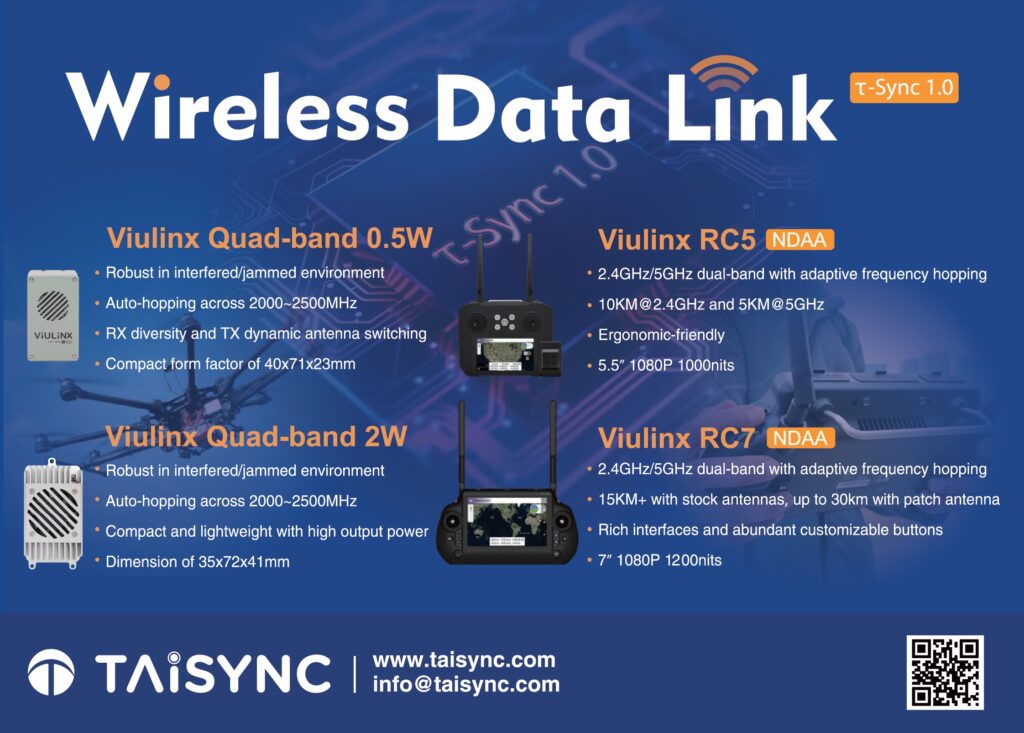
Furthermore, conventional de-mining is pricey: clearing one hectare (worth about €400 ($417) of annual profit to a farmer) costs $10,000-30,000 and, per the above rate of landmine incidence, 95% of those costs are wasted clearing ground where no landmines are present.
“So, you see the real systemic issue preventing worldwide de-mining: the ROI just isn’t there. Dropla’s first objective is to bring the price of de-mining down to 10 cents per square metre [$1030 per hectare] or lower; otherwise it’s really hard to make the financial case for de-mining,” Shvaydak says.
“Having brought the cost down, we can then focus on optimising our tech and methods to ensure confident detections and confirmations. Today, we can free 90% of denied land extremely quickly before any actual major de-mining takes place.
“Actual minesweepers weigh at least 600 kg and function alongside entire crews of trained sappers, so it’s important to note that what we do is not specifically the de-mining act, but doing area reduction. We take the amount of area to be physically de-mined down by 95%, and overall operational costs down by 90-97%.
“Even though the land swept by our flail-equipped UGV must be manually checked afterwards, the speed of the operation still increases by 80-200%. Safety skyrockets, as no human being will be able to physically trigger what hasn’t been triggered by a 600 kg flail hammering machine.”
Multi-sensor strategy
Dropla’s UAVs fly with three categories of sensors, broadly categorised as “optics”, “magnetics” and “electromagnetics” (EM).
Within “optics” are RGB cameras, multispectral cameras, thermal cameras and Lidar. The former two naturally serve well in daytime visual surveys for signs of minelaying, but they are limited when landmines are hidden by the presence of dense vegetation, being located underground, and similar factors.
“Thermal cameras can detect targets of substantial sizes hidden deep underground, such as anti-tank mines encased in metal, by measuring the signature of heat released over time; for instance, the temperature drop of an object between noon and just after sunset. If its temperature has dropped by a differential as small as 2 C, compared to the soil around it, that can be enough to confirm it as a potential landmine,” Shvaydak says.
The Lidar, meanwhile, serves more in feature extraction, including both the identification of soil disturbances typical of landmine placement (sapper work often leaving very precise signs that can be identified via Dropla’s Dropla.Vision analytics software during data processing) and the creation of a 3D map of the terrain the UGVs will use to navigate later on.
Within “magnetics” solutions are magnetic gradiometry sensors, which measure deviations in the Earth’s magnetic field caused by the presence of conductive objects (such as metals) in the ground.
“When working with magnetic gradiometry, however, you’re working with tensor fields, which follow the inverse square law of magnetics, which means a target of 10 kg lying 10 m deep will look just the same as a 1 kg target at 1 m depth,” Shvaydak explains.
“So you can’t run generalisation algorithms on their output data to determine whether it’s one or the other, but we do use localisation algorithms to calculate the probable exact centre of detected anomalies, which is still very helpful.”

Magnetic sensors are also limited by metal clutter contaminations, meaning, for instance, that a 50 kg piece of metal will be detected as an anomaly, spanning about 3-6 m in diameter, which could be hiding a second, smaller landmine within its radius. Hence, like the “optic” sensors, it cannot be used as a standalone mine detector.
The EM detection systems used are ground-penetrating radars (GPR) and pulse induction (PI) metal detectors. The former include highly regarded sensor technologies, such as synthetic aperture radar (SAR), but its accuracy reduces with the moisture content in the ground; very wet soil will back-scatter 95% of SAR’s EM radiation into the surrounding environment.
“We can’t rely on GPR if the ground’s moisture content exceeds 70%; it just renders the radar useless,” Shvaydak says. “There’s a very limited window of opportunity to use GPR and that’s when we have a warm, dry month, but in that window, GPR honestly becomes an amazing technology, capable of revealing the hardest targets of all: anti-personnel, plastic landmines. Those make up 80% of missed targets, simply because they don’t throw up a signature for any other sensors to use.
“Overall, the back-scattering of EM waves in highly non-homogenous environments remains an unsolved mathematical issue, although there is a multinational research group and open-source software developer called gprMax that is trying to resolve the problem by simulating that back-scatter specifically for landmine detection, as well as a few other pointed use-cases. Its progress will likely be hugely valuable in the fight against anti-personnel mines.”
PI metal detectors are well-established and widely used devices, which function by producing electromagnetic pulses via copper coils, but they suffer from a high rate of error – a ratio of around 100:1 false positives to actual metal targets. Therefore, other sensors are key to reducing ground clearance work.
With all these sensors combined (via real-time processing, post-processing and data fusion), the UAV-based sensing narrows surveyed SHAs down to the 5% of actually dangerous CHAs, where potential landmines lie. The other 95% is marked safe with an 80% confidence index (obviously, that 80% chance is insufficient for declaring such zones safe, but the second phase involving UGVs serves to provide 98% certainty, as will be explained later).
“The end result is that we can identify standard landmines with 100% certainty, and even things like plastic bags don’t just get discarded from the AI model because they could easily be improvised explosive devices [IEDs],” Shvaydak says.
“It’s well known that plastic bags can contain explosives linked to a cheap accelerometer, such that the vibration of nearby pacing will trigger a spring to push the bag to mid-air, where it will explode shrapnel across a 30 m radius. That’s why the second phase is called ‘confirmation’, because we confirm that we did not miss a potential landmine.”
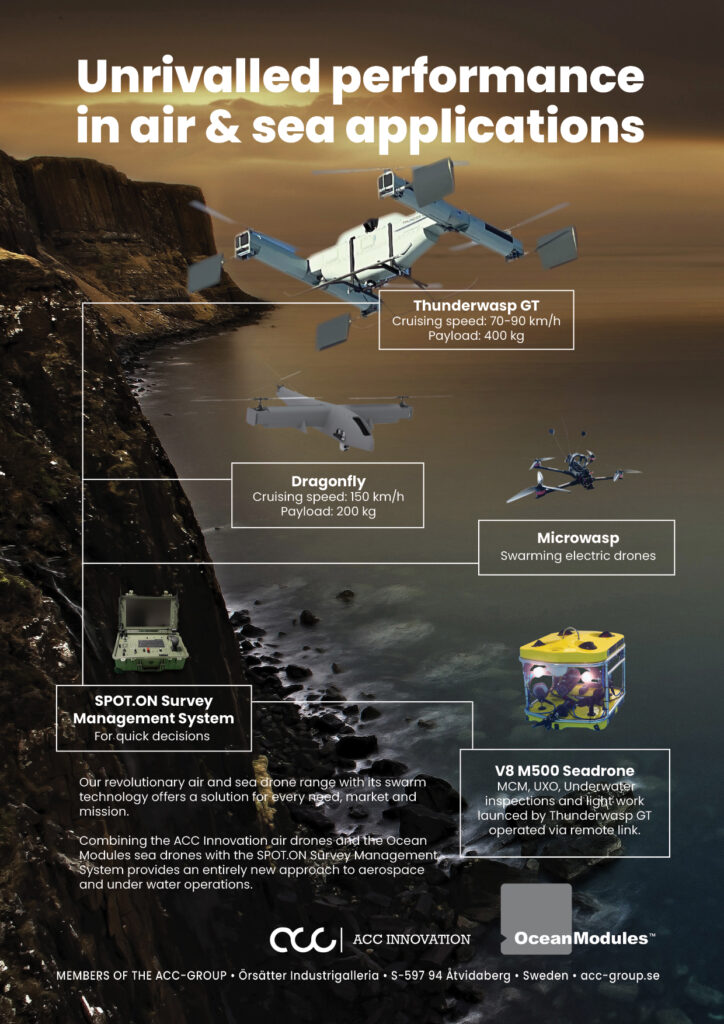
Therefore, while detections of false positives are permissible (as they won’t explode, and will get checked and confirmed as safe afterwards), false negatives (where an area deemed safe actually contains a landmine) cannot be allowed as people could be killed. And, while many different sensors can detect signs of mines in varying ways, no single standalone sensor can guarantee the prevention of false negatives.
Aircraft to aircraft
As of writing, Dropla has primarily flown using the DJI Matrice 350, having been an inexpensive and easily integrated solution. It was convenient to use during early r&d, particularly in flying preplanned, waypoint-based survey operations in controlled fleet formations in standard patterns over simulated SHAs at its test grounds.
“Mission planning and control has always gone smoothly, thanks to the C2 software of our partners, SPH Engineering, in Lithuania, but, of course, we can’t keep using a Chinese solution due to the coming import ban, so we’re also developing our own UAV and positioning system,” Shvaydak says.
While the Matrice 350 is a fully-electric, 9.2 kg drone, capable of 55 minutes of flight time on its battery, the upcoming Dropla UAV will feature a hybrid-electric powertrain, enabling 90 minutes of flight with payloads significantly higher than the M350’s 2.7 kg.
“Running the engine to recharge batteries mid-flight will produce high vibration, and that’ll be hell on the payload sensors, so a major focus of our UAV engineering is the vibration damping between engine and payload, which, frankly, will have to be at least as sophisticated as the rest of the UAV combined,” Shvaydak says.
“But the biggest focus of all is our navigational resilience, and that’ll be optimised using a combination of visual odometry – with a particular camera and Lidar fused to work in combination for pixel manipulation and depth extraction – and the sharing of INS data, facilitated via a mesh network based on STANAGs 5065 and 5066 for tactical data-link communications. That means swarm-based navigation, which will give a sufficient level of certainty, even in GNSS-denied environments. These are well-known, established navigation technologies, so there’s nothing too outlandish about being able to do that.”
Price of a mile
Once data from the UAVs and their sensors has been fused (via Dropla.Vision), the UGVs can be programmed to sweep the surveyed area in two key ways.
The first task required of Dropla’s UGVs is vegetation removal: 95% of professional sappers’ operational time is spent cutting grass with scissors to clear paths for large minesweeping vehicles and their crews to gain access to CHAs.
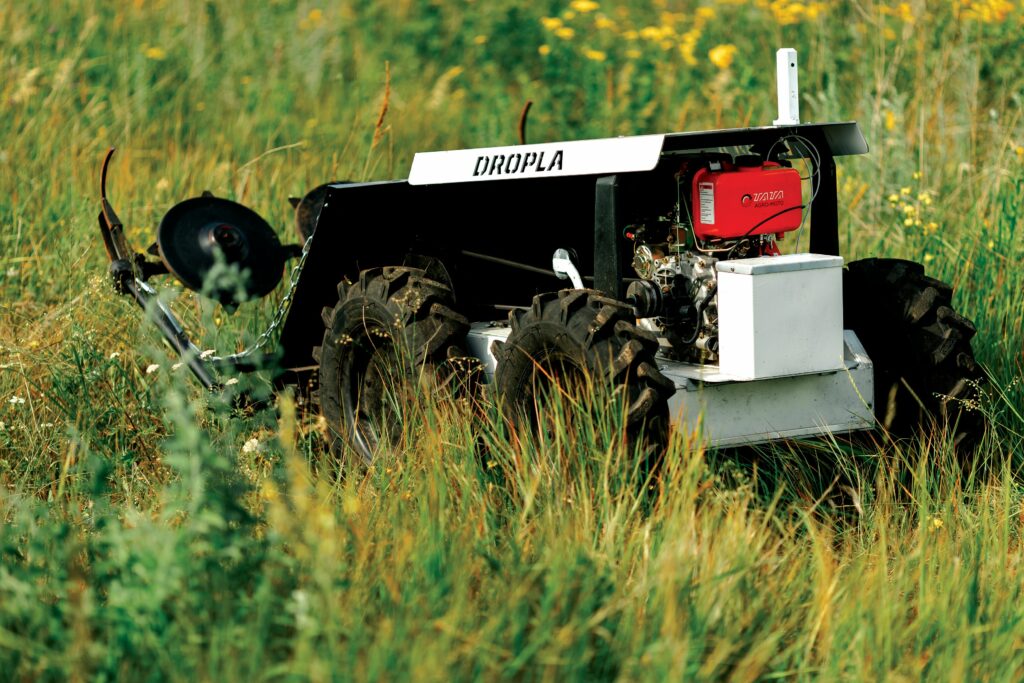
“Professional sappers, like those of Ukraine’s State Transport Special Service [STSS], who had cleared 3600 km2-plus of land as of May 2024, are highly trained individuals, but so arduous is the task of grass clearance that the first thing they asked me to deliver from Dropla was a low-cost and expendable system for automated vegetation removal,” Shvaydak says.
Currently, three UGV models are manufactured by Dropla, all costing $12,400-15,500. Its mowing solution (and the first typically deployed) is the Clover-1 UGV, a 350 kg vehicle measuring 2413 x 1310 x 1576 mm with its front mowing attachment, featuring three six-bladed rotors. It is capable of four hours of operation and speeds up to 10 kph, thanks to a 9 bhp diesel engine, which recharges a NMC battery from CATL.
Once the vegetation has been cut, another UGV model, the Mjølner-1, will then run in lawnmower-type patterns familiar to UAV survey operators, hammering the ground with flails and hammers to trigger or destroy any undetected mines. This 600 kg UGV measures 2900 x 1700 x 900 mm, and runs on its own 30 bhp hybrid-electric powertrain. Its frontal attachment is a milling system, which successfully triggers anti-personnel mines and similar small explosives, which can escape initial detection.
Mjølner-1 can withstand anti-personnel landmine detonations from models such as the PNM-2, PNM-4 and PFM-1, or from a larger device such as an unexploded artillery shell or an anti-tank mine of type TM-62, before suffering significant damage.
Dropla also produces a UGV called the UNI (meaning universal), which is identical to Mjølner-1, except that it comes without the frontal milling attachment. It can be fitted with either that or a mowing payload for users who prefer to work with a single system for both parts of the UGV-based phase.
One may contrast the price of these UGVs against typical de-mining machines; the latter can cost $1.54 m to $2.26 m, consume 300 litres of fuel per day, require an overhaul every 100 hours and clear just one hectare per day.
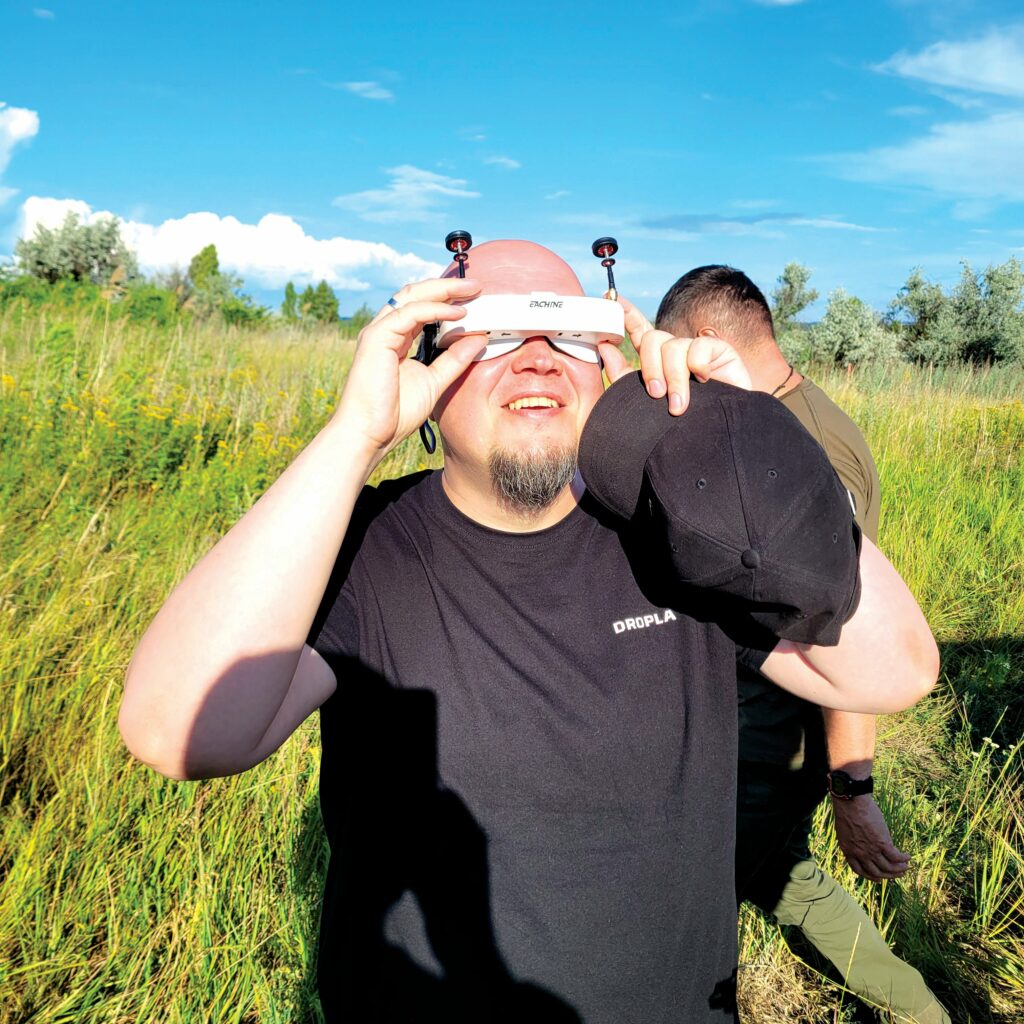
“Each of those costs $8253 per month in fuel and oil, and if one hits an anti-tank mine with 7.5 kg of explosives it stops, because the roller attachment at its front gets either damaged or bent, and needs replacing. Imagine the difficulties of withdrawing and repairing that system, and redeploying it only for it to hit another anti-tank mine after 30 minutes, and you understand the need for something with a far better operational efficiency per euro,” says Shvaydak.
“But, if our UGVs get blown up, fine. I spoke with a Ukrainian officer recently who had used a $412,900 specialised machine for vegetation removal. It got thrown up into the air in pieces after just four days of work. Our UGVs cost nothing like that.”
A major cost-saving comes from the “semi-autonomous” nature of the UGVs. This autonomy is limited to waypoint-following, with mission details automatically transmitted to the robots in real time from the user’s GCS, rather than needing to be stored and processed onboard.
“Full autonomy is extremely costly to develop, so the mission computations happen in the background, from the UGVs’ perspective, but we are developing a more expensive [$30,950 per unit] UGV that will have greater autonomous capabilities, most importantly the ability to safely navigate between waypoints while GNSS-jammed or -spoofed,” Shvaydak says.
Augmented reality
The last part of the solution is an augmented reality (AR) system, to be used by the de-mining teams once Dropla’s detection and confirmation work is complete. A highly georeferenced photogrammetric map of the environment, constructed using all of the sensor data, collected and fused, is displayed into the de-miners’ goggles, transmitted over wi-fi from a wagon-based C4 station.
“Building that map takes some time: if it’s a 30 hectare area, we can do the full circle of map generation in five hours,” Shvaydak says. “That encompasses checking the data, rechecking it, stitching it, and running it through 10 different neural networks we’ve developed thanks to our testing site, where ‘ground truth’ data with real live munitions buried under soil was available to train said networks.
“As for fusing the data together, there are maybe 18 types of sensor-fusion algorithms that work in this application. They each return a different operational picture, but we can run all of them through a sigmoid function to derive probabilities and confidences for each data set, giving a good, aggregated picture of the world, and potential landmines in it, in the end.”
The resulting map enables sappers to see not only where potential mines may lie – denoted, for instance, by yellow ‘medium threat’ zones or red ‘high threat’ zones (based on the probability of landmines and their explosive radii) – but also the paths the UGVs have taken, which are marked green because they have been physically confirmed as safe.
“There’s no cloud computing used to export data to the AR headsets. Cloud links aren’t efficient or particularly cyber-secure. So, we use a closed loop of edge and near-edge devices, with the wagon-based C4 station carrying the processed data and running on a 100 kWh battery pack when deployed in the field with sapper crews,” Shvaydak says.
“That wagon also features a 160 A charging outlet, from which any UGVs still operating can be recharged if necessary, given that they’re all hybrid-powered vehicles with batteries.”
In the long term, scalability of Dropla’s overall de-mining strategy depends on having more UAVs and UGVs working in tandem (with a rise in the uncrewed vehicle count linearly increasing the number of hectares that can be released per day). Up to 20 UAVs or UGVs can be managed from a single C4 station, as of writing.
Quantum future
In addition to all these technologies currently available, and the upcoming UAV being engineered in-house, Dropla is developing multi-domain swarming technologies to ensure continued co-ordination and effectiveness in GNSS-denied conditions.
This will involve the uncrewed systems communicating with each other, including sharing data from INSs and other navigation sensors, to ensure sub-centimetre precision of landmine detection, even amid jamming and spoofing. Dropla is developing its swarming and navigational technologies as part of a separate project, intended to form a bigger push for navigational resilience in humanitarian drone fleets.
“More than anything, we’re most looking forward to being able to incorporate quantum sensing technologies such as SQUIDs [superconducting quantum interference devices, which are highly-sensitive magnetometers, developed for measuring extremely weak magnetic fields] and integrate them into our stack,” Shvaydak says.
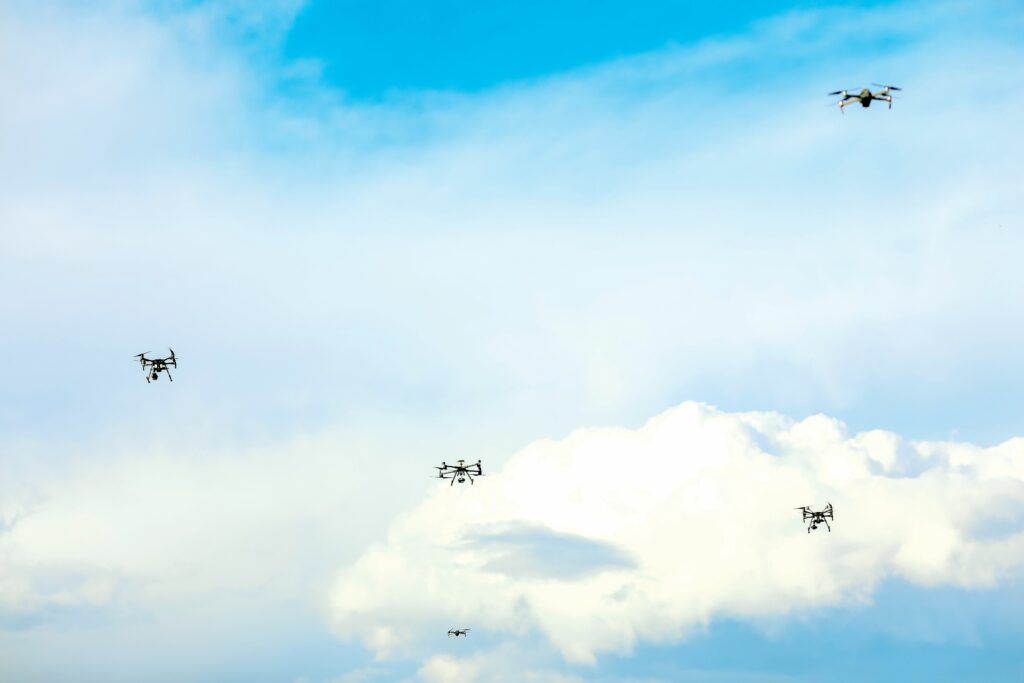
When combined with a viable quantum computer of 1000 qubits, quantum sensors could drastically increase the accuracy and confidence of Dropla’s landmine detections, and reduce the time taken across the envelope of operations.
Regular computers could process the signals coming in from SQUIDs and other quantum sensors, but as Shvaydak says: “They will not have the capabilities of quantum computers, such as those being made by companies such as IQM.
“Going forwards, we’ll look into other applications of our AI, quantum and swarm technologies. Our mesh network systems for swarming, for instance, are being designed to a NATO STANAG.
“Although de-mining is principally humanitarian work, there’s clear defence potential of our IP. The future of European warfare is uncrewed swarms forming a grand sword and shield to protect Europe’s people.
“Dropla is becoming an AI-powered shield, and if readers have additions or suggestions to the technologies described, or relevant experience in the field, I implore them to reach out and make this shield stronger.”
Key suppliers
UAVs: DJI
UAVs: Inspired Flight
Command and control software: SPH Engineering
C4 station development: UXV Technologies
Sensing solutions: Inertial Labs
Cameras: Sony
Magnetic radiometry sensors: Sensys
Quantum computing consultations: IQM
Batteries: CATL
UPCOMING EVENTS
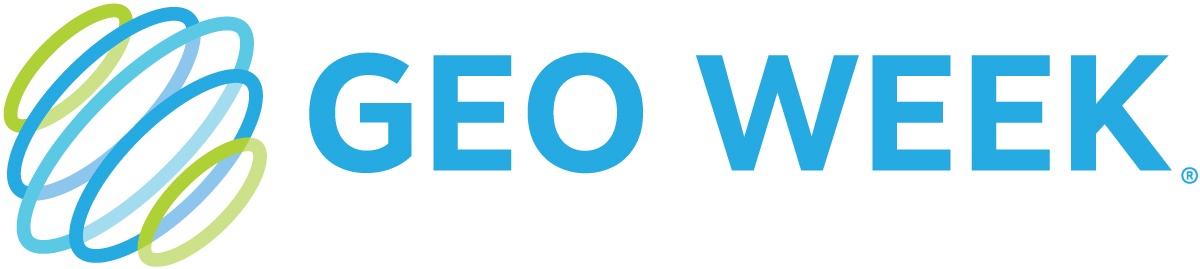
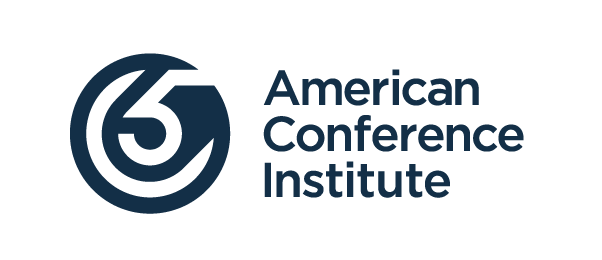
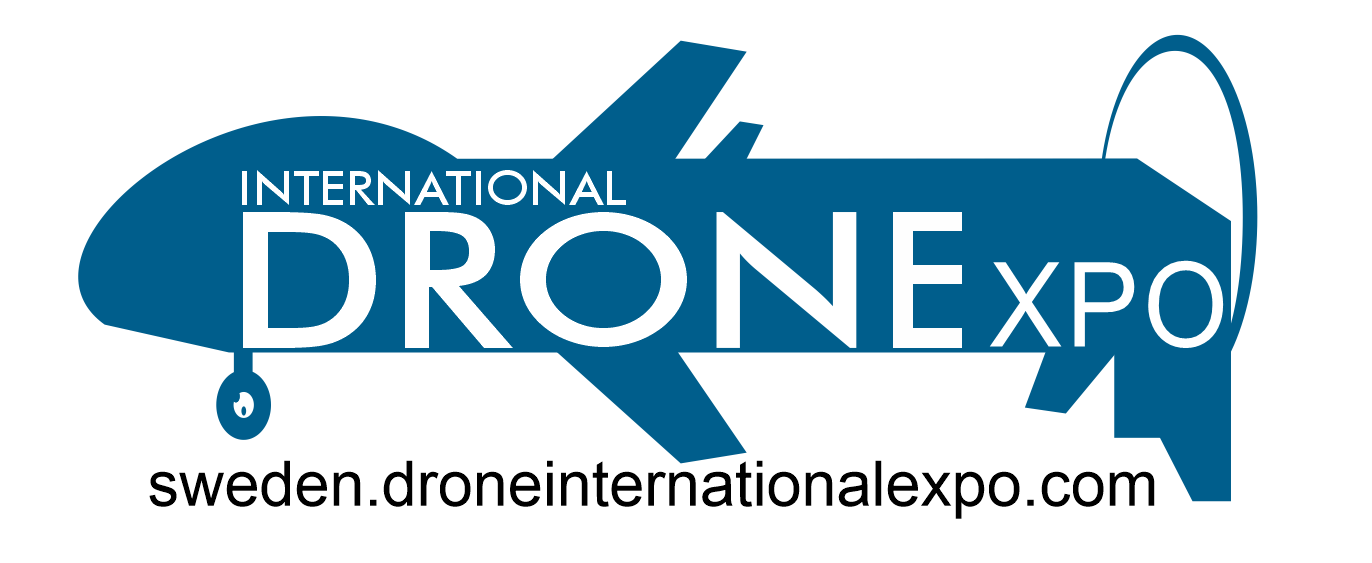
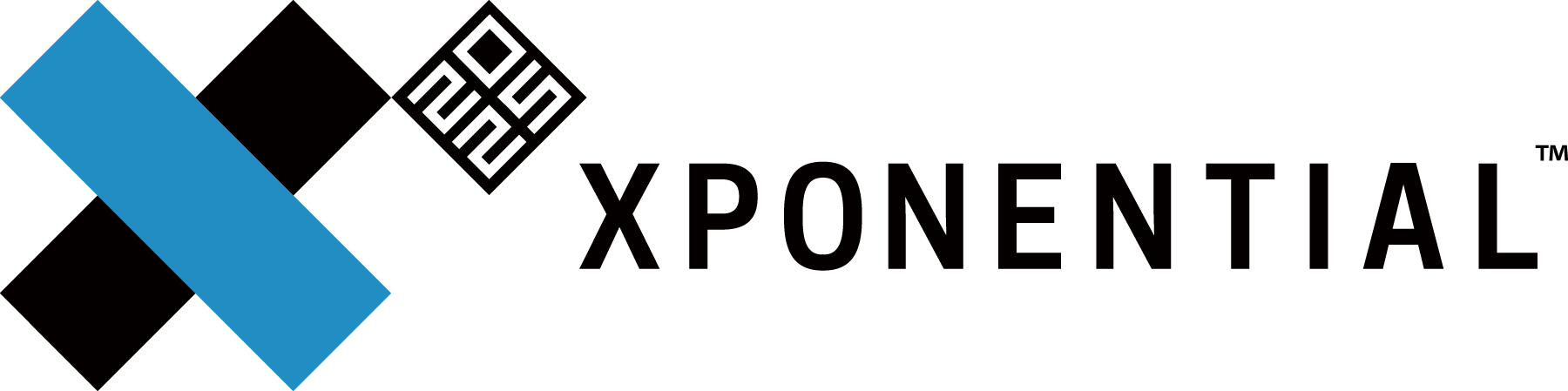
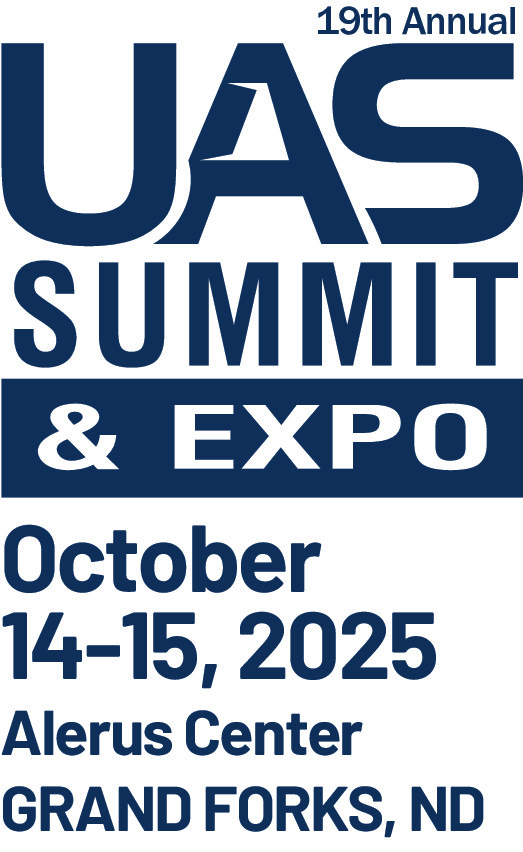

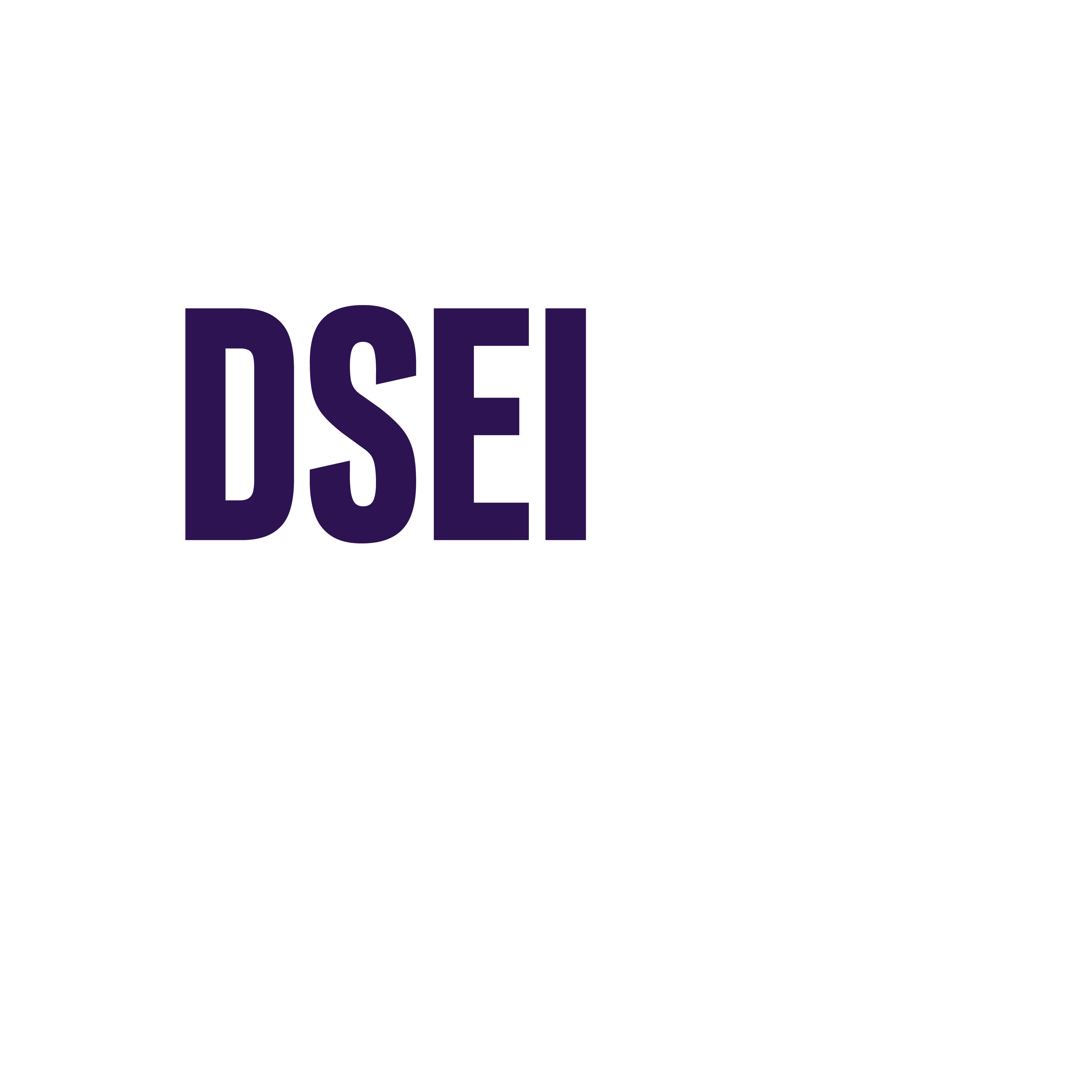
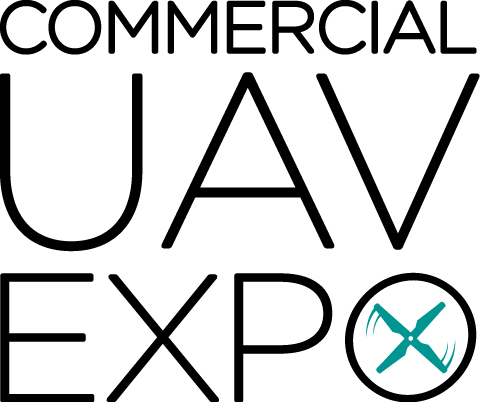
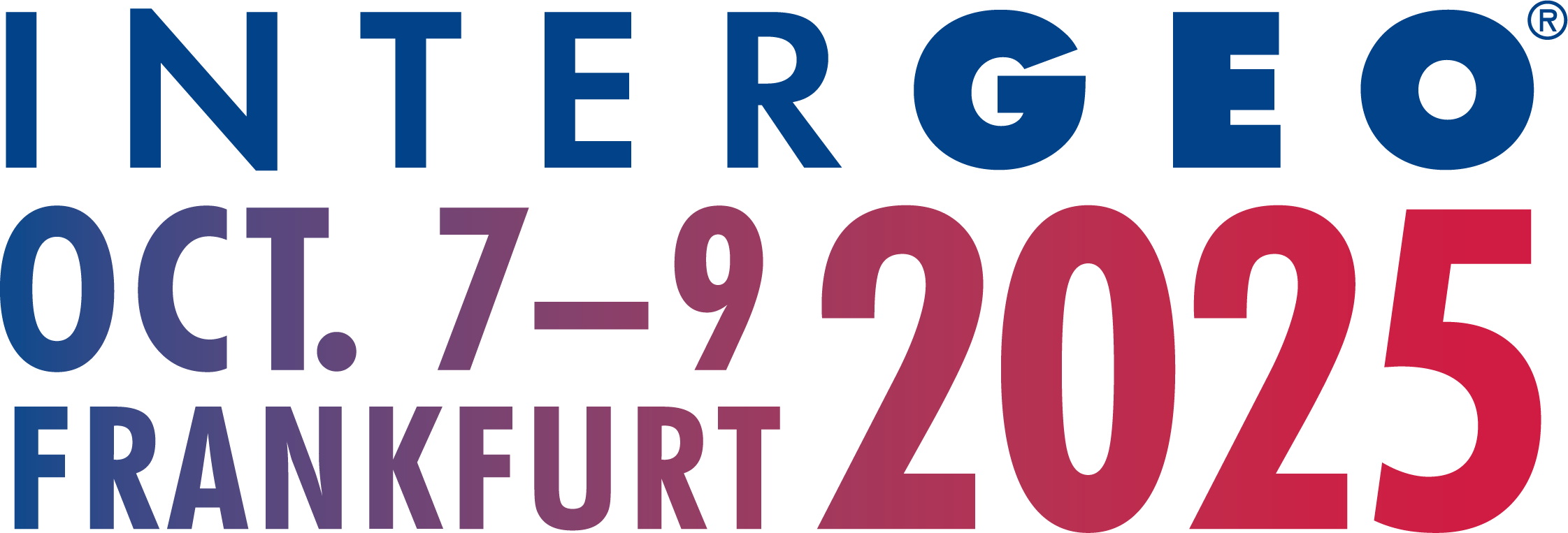
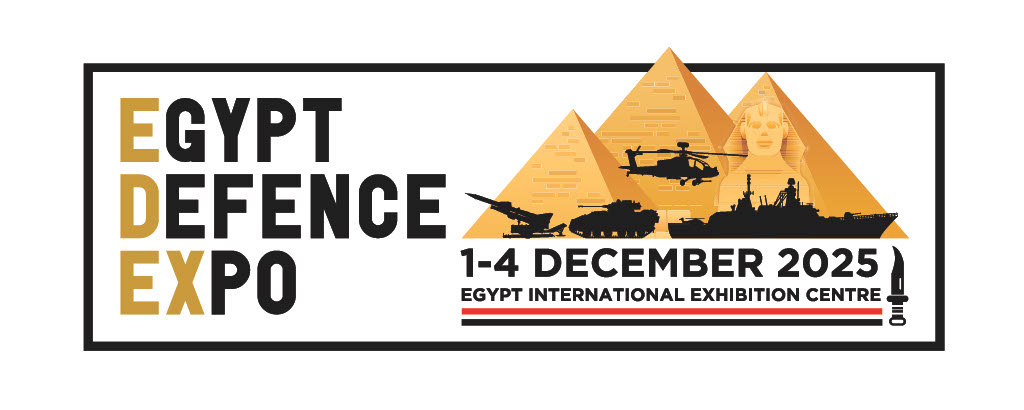
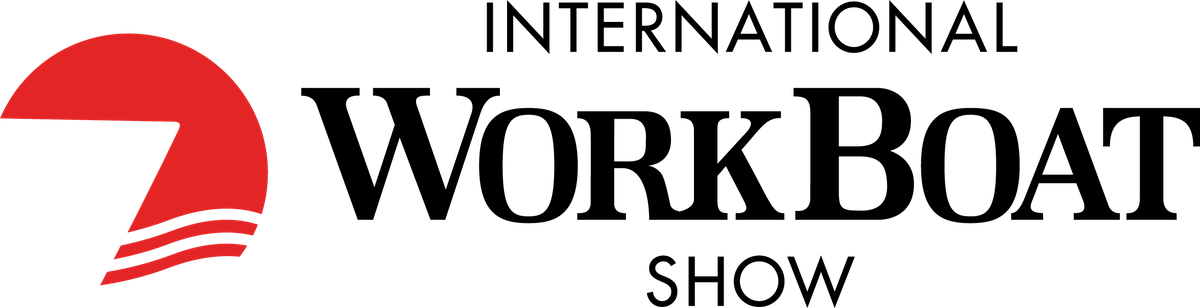