DroneX 2022
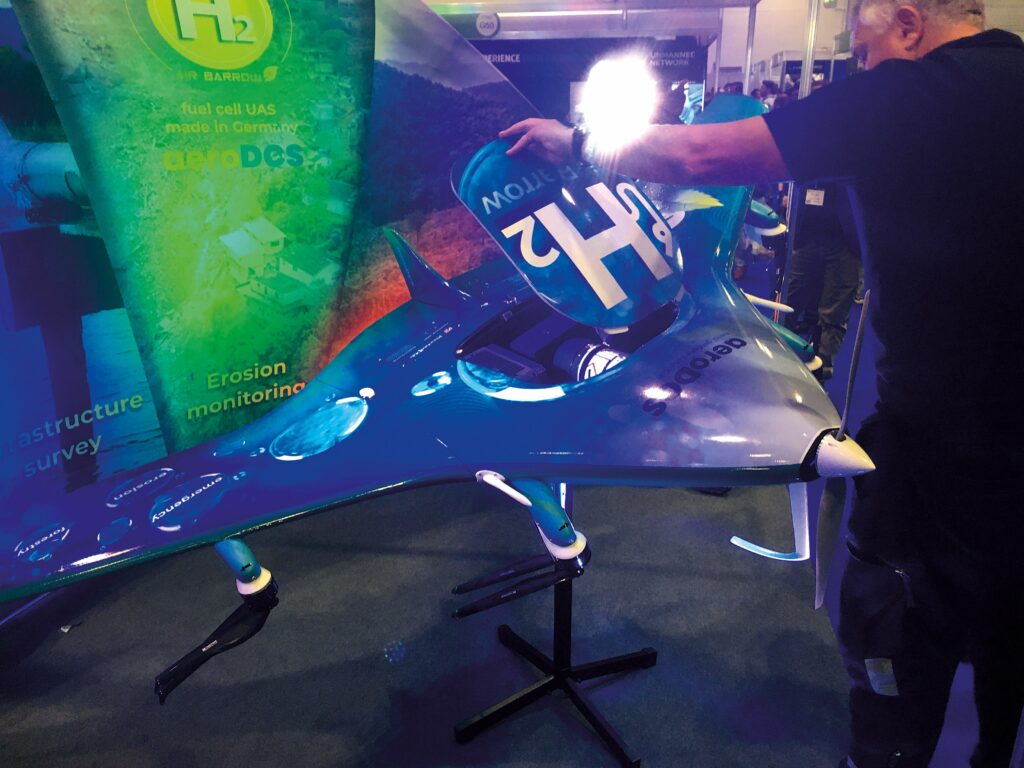
What’s the buzz?
Peter Donaldson reports with highlights from what is billed as the UK’s largest event dedicated to UAV products, parts, accessories and services
Advanced motor and sensor technologies, innovative propulsion concepts and flexible multi-vehicle control systems vied with UAV platforms for attention at DroneX 2022, held in London’s ExCel exhibition centre on September 7 and 8.
Alva Industries showed its electric motors that use Halbach rotors, FiberPrinting technology and quality assurance to produce powerful, compact and reliable electric propulsion systems for UAVs.
Anton Franzen said, “Two years ago, we decided to focus fully on the UAV industry as our beachhead market. We saw that performance is important but reliability is number one,” he said. “Our propulsion systems are designed for very long lifetimes and to be very robust; everyone wants something they can rely on and that works for a long time.”
Halbach rotors, he said, generate very strong magnetic fields using permanent magnets. In a Halbach array, the magnets are arranged with their poles out of phase to produce a field that is very strong on the side nearest the stator but near zero on the other. That allows the motor to generate more torque for a given size and weight.
Alva makes in-runner motors, in which the rotor is in the centre and the stator is around the rotor, which means they can be sealed from any harmful contaminants, he added.
“The stator does not have an iron core,” Franzen said. “That results in superior properties compared with more conventional motors, including higher efficiency, higher peak power capabilities and a more robust construction.”
The stator consists instead of filled epoxy with windings of fine copper filament in combination with structural fibres, all manufactured using Alva’s FiberPrinting process, helping the stator achieve a copper fill factor of up to 60%.
“Traditional iron-cored stators are not required in Alva motors, for three main reasons – the high copper fill factor in the stators, the very close proximity of the rotor magnets and stator windings, and the Halbach configuration’s concentration of the magnetic field where it is needed,” Franzen said.

The company focused on two UAV propulsion systems at the show: the single-motor Altus X60 Uno and the coaxial Altus X60 Duo. While the Uno system offers higher efficiency, the Duo makes the UAV more compact for a given number of motors and brings more redundancy to each motor position. Also on display was the larger X80 motor for heavy-lift UAVs, which the company plans to commercialise at the end of the year for single as well as coaxial configurations.
Autonodyne showed the latest iteration of its RCU (Rainbow Coloured Unicorn) multi-vehicle common control station software that Laura Aptowitz said sits at the nexus of the human-machine interface and autonomy.
“We use this software to enable control of multiple dissimilar platforms by a single operator,” she said. “Our main goals are to make the interface intuitive and easy to use, limit the time needed for training and reduce cognitive load on the operator to maximise mission effectiveness.”
Aptowitz said the RCU runs on Android smartphones and tablets, and desktops and laptops running Windows and Linux, for example. “We also remain agnostic in terms of the vehicles we integrate,” she added.
Autonodyne has implemented more than 11 message protocol formats including, for example, NATO’s STANAG 4586 standard for communicating with uncrewed systems.
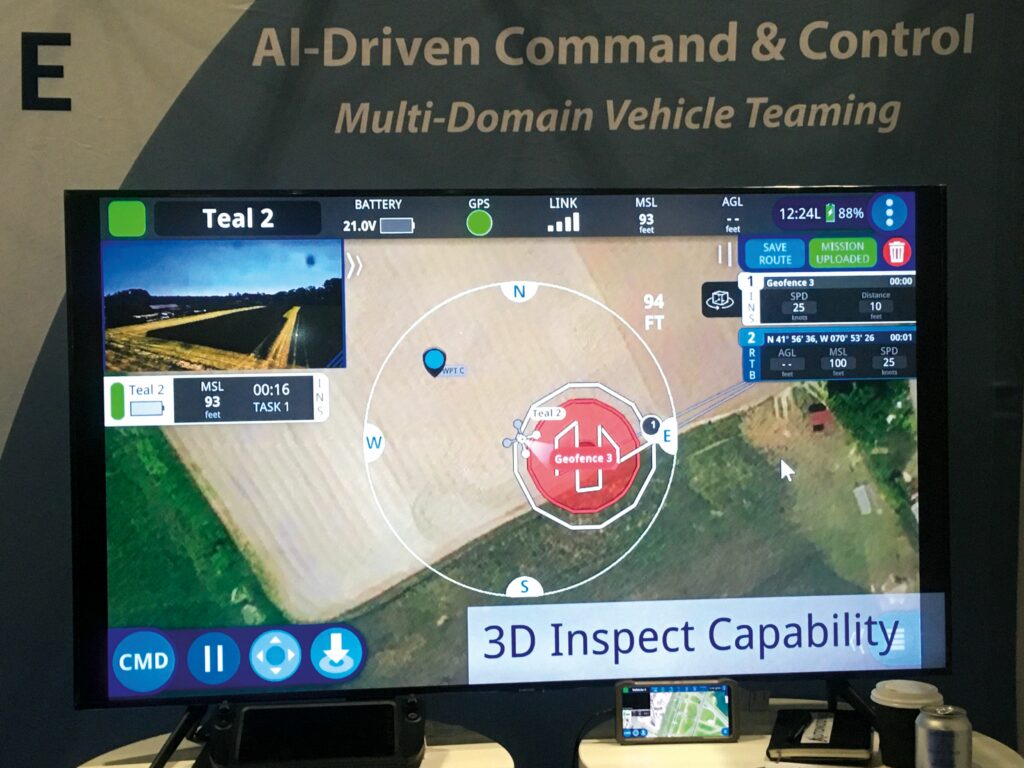
“When the software connects to a vehicle, it knows what its performance capabilities are, what its flight envelope is, what its maximum range is, what fail-safe battery parameters it has, and the RCU will build missions to ensure the vehicle is being commanded within its limits,” Aptowitz said.
To ease the workload of controlling multiple vehicles, the company has created more than 20 different autonomous behaviours that can be used with multiple groups of vehicles. “You can, say, circle your finger on the map, selecting the vehicles you want to use and then create a survey, for instance,” she said.
Having completed several contracts in the US with the Department of Defense and civil companies, Autonodyne said it is ready to sell RCU licences on the international market, and can provide solutions that are free of ITAR restrictions.
RCU is a tongue-in-cheek characterisation of a system created to meet so many operational needs at once.
CycloTech’s thrust vectoring cycloidal rotor propulsion system was a highlight of the show. The CycloRotor can generate thrust at 360º on a plane at right angles to the axis of rotation, enabling a UAV with four thrusters to hover, turn on the spot and move in any direction without tilting, decoupling the pitch and translational axes, Klemens Hofreither told us.
Each electrically driven rotor unit consists of five carbon fibre blades arranged in parallel around a central axis of rotation. Each blade also moves about its own pitch axis under the control of a mechanical pitch change system. This system consists of a set of rods connected to the blades and to a hub that surrounds the main axis of rotation but is free to move eccentrically in any direction around it, powered by dedicated servo motors.
Changing the pitch of the blades controls the thrust’s direction and magnitude, while the thruster maintains a constant speed and direction of rotation. “The need to alter the position of the hub enables only very rapid vectoring,” Hofreither said.
“We want to show in the autumn this year that we can decouple the flight path and the flight attitude of a UAV,” Hofreither said. “We want to demonstrate that it can take off and put itself at 30º in the air and it will hold still, for example.”
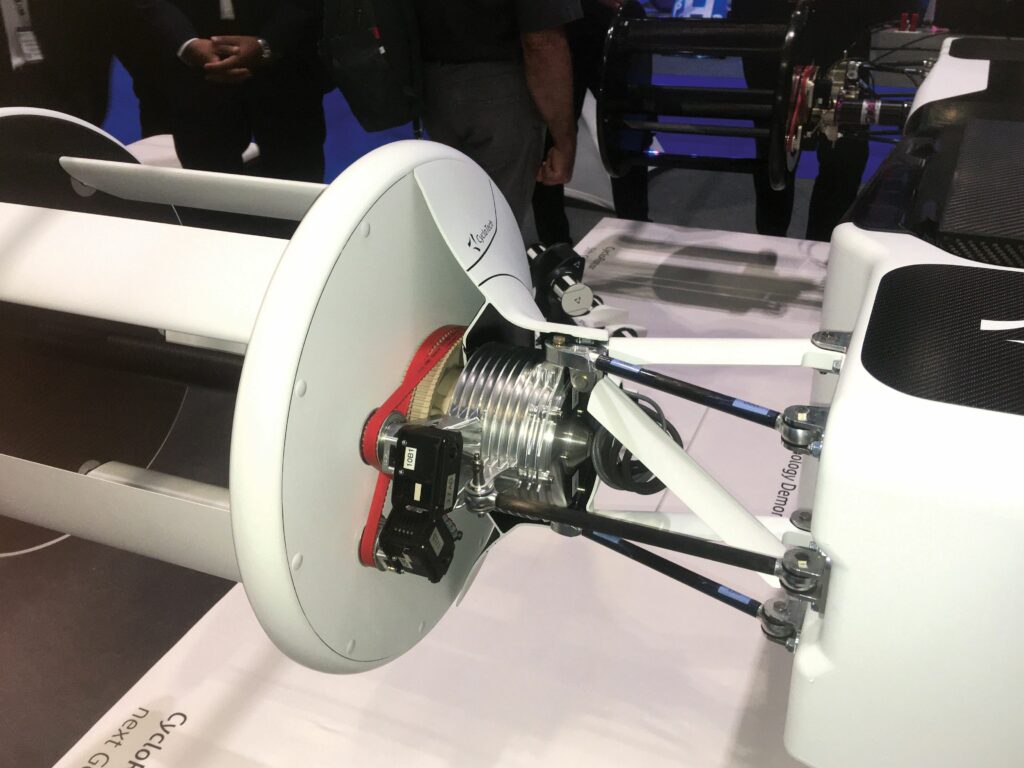
The system is designed for urban eVTOL platforms as well as UAVs, and rather than building its own aircraft, CycloTech intends to work with partners who want to use the system on theirs. Parcel delivery provider Yamato, for example, plans a UAV with six CycloRotors to enable it to counter gusts from any direction.
Hofreither said the flight control software is one of the biggest challenges the company is facing, because the working principle is very different from those of more familiar concepts.
“We had to develop our own flight control system from scratch, so the algorithm in the background is unique. We are working with the University of the Federal Armed Forces in Munich on the flight dynamics, and the project has been running for 2 years,” he added.
LightWare, a specialist in miniature Lidars for use in navigation, altitude measurement, simultaneous localisation and mapping, sense & avoid and position-holding functions, revealed a new landing Lidar designed as a lighter, less costly alternative to RGB camera-based systems.
“It’s a 3D Lidar, so it scans at 30º x 30º downward onto a landing zone, and can tell you if it is safe to land,” said Philip Constantine. “Some solutions use cameras, but you need a very expensive, powerful computer and multiple cameras to survey a landing zone using RGB.”
He explained that because Lidar is an active sensing technology it doesn’t need ambient light, and that the safety evaluation capability is built in. “All the processing happens on the unit, and it will evaluate a landing zone and give you a binary response – yes you can land; no you can’t,” he said.

LightWare offers Lidars priced at $280-1000, and has fielded around 50,000 units. The simplest are 1D sensors that measure the distance to a single point at a time, and have no moving parts, such as the company’s smallest Lidar, the thumb-sized SF000, which weighs 8.5 g and measures distances from 0.2 m to 50 m.
Then come the 2D sensors that scan a single beam through a 320º arc. “We do that in an oscillating manner with our SF45 so that it can be used for obstacle avoidance, detecting trees, buildings and power lines and so on, and at 56 g it is very light,” Constantine said.
Most capable of all are the 3D Lidars that cover the x, y and z axes and generate a 3D image from points at precisely measured distances from the sensor.
All the company’s Lidars meet Class 1M eye safety standards and use high-grade LEDs that emit light at 905 nm, carefully controlling the amplitude and pulse length to maintain both eye safety and range performance, Constantine said.
The other core components are the transmitting lens, the receiving lens and the avalanche photodiode detector, supported by other hardware such as optical filtering. “The optics are very important in terms of how the beam is shaped and focused,” he noted.
Next in line is the firmware that processes the signal. “Most of the magic happens in the firmware, where the algorithms discern what is noise and what is a real signal.”
The processed signal is then sent to the comms module for use by the autopilot. “We integrate directly with Cube and Pixhawk, and we have standard drivers for ArduPilot and PX4,” he said.
Edge Autonomy displayed its twin-boom, fixed-wing Penguin C VTOL and hinted at the capabilities of a new version that the company plans to offer within months.
Powered in horizontal flight by an in-house 56 cc fuel-injected piston engine with electronic fuel injection, the aircraft’s VTOL capability comes from four electrically driven rotors that draw power from lithium-ion batteries, all housed in extended tail booms of patented Aeroflow design. To minimise drag in forward flight, the two blade rotors automatically align themselves fore and aft when switched off, allowing covers to snap down over them and shield them from the airflow.
Konstantins Krivovs said the VTOL batteries can be swapped in under 2 minutes, and pointed out the aircraft’s rotating nose. “The nose is in the upwards position during take-off and landing, protecting the payload from any potential damage, and then rotates downwards during flight,” he said. “During operation, as the UAS banks and the nose remains aligned with the horizon, providing extra stability to the payload imagery.
“Also, the nose can be rapidly swapped by removing two screws, detaching the nose and replacing it with another containing a different sensor,” he said.
On the market for the past 2 years, this version of the Penguin C VTOL has an endurance of 14 hours and can operate at up to 180 km from base.
Born out of the merger between Jennings Aeronautics and UAV Factory in September 2021, Edge Autonomy added Michigan-based Adaptive Energy, designer and manufacturer of solid oxide fuel cells for back-up and portable power applications in August 2022.
LikeAbird had on show its new backpack UAV control station that integrates a battery management system, multiple radios, optional hands-on-throttle-and-stick (HOTAS) controls and a more conventional remote control pad. The idea behind the backpack is to create a modular system.
“The pack can be used with the HOTAS to control a UAV in real time, or as a relay station for data and video from a UAV over LTE or other comms devices, but you can also customise the system as you want,” said CTO Jarno Puff.
He noted that for direct first-person view piloting, the system can be used with video goggles from DJI, for example. He explained that the backpack system is divided into two main sections, one for power and the other for RF comms.
“In the power section we have two standard batteries that you can hot-swap. You can then use the same kind of battery with an adapter as a power bank to recharge your tablet or phone, and to power 12 V devices.”
The RF section can accept systems including IP radios, LTE cellular and satcom systems with power outputs of up to 10 W. “That is why we have two antenna poles, so that you can get the antennas far enough above your head that you don’t expose your brain to 10 W of 2.4 GHz radiation.”
Puff described the example on display as a fully working proof of concept, and said that LikeAbird is now working on the first production-standard unit.
Plettenberg was exhibiting at DroneX for the first time, and showed the newest member of its Nova series of electric propulsion motors, the Nova 15 LW, which was developed specifically for airborne uncrewed applications. The LW series is a redesign of the Nova in-runner brushless DC motor series featuring a lighter housing and other internal components enabling a 15% reduction in weight, while maintaining the ruggedness of the regular Nova series, according to the company.
“We can build new lightweight versions of all our Nova motors, and we are developing them now,” said Bastian Greiner.
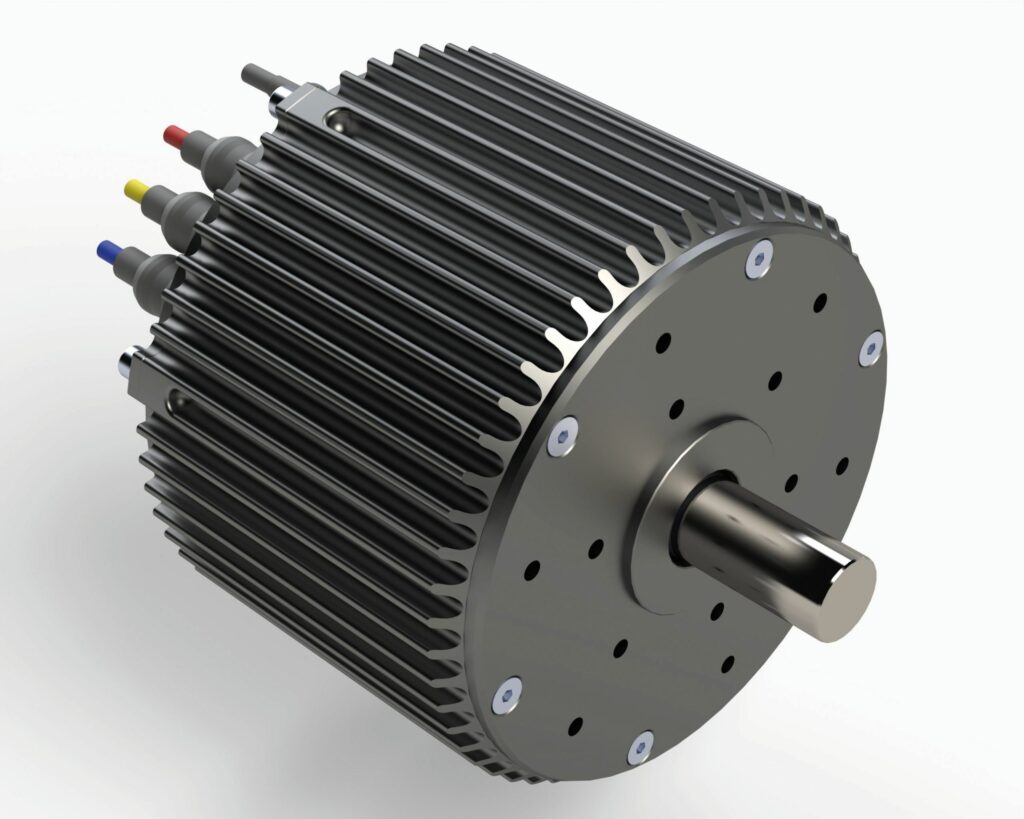
Greiner emphasised that Plettenberg custom-builds motors for uncrewed applications based on a modular design rather than offering standard motors, and can achieve 15-30% greater efficiency compared with off-the-shelf motors.
“That is part of our niche,” he said. “The second part is that we build enclosed rugged designs that can be used in very harsh environments, such as in deserts or at sea, and can be sealed to IP67.”
While the company can supply liquid-cooled motors, most UAV manufacturers choose air cooling, he noted. “Cooling can be a real challenge in many airborne uncrewed systems. What we can do in this case is run thermal simulations and, if required, build a duct housing for the motor with an active fan, or integrate a fan into the motor,” Greiner said.
UPCOMING EVENTS
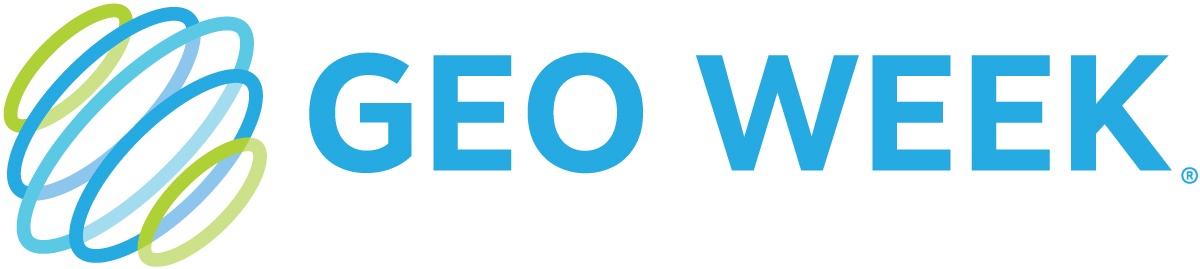
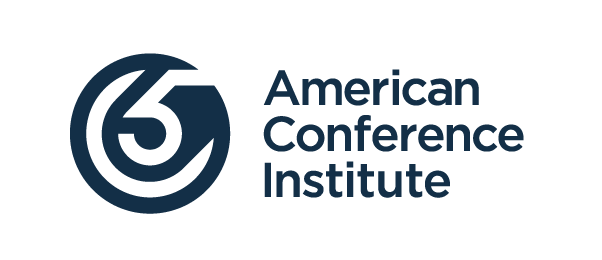
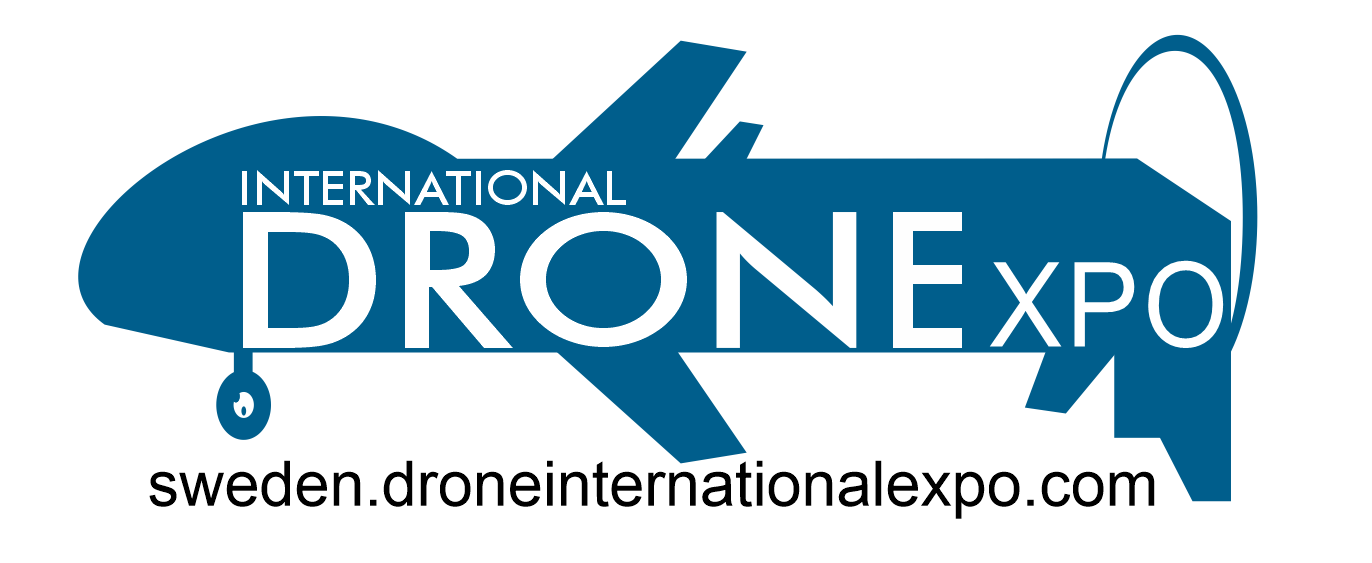
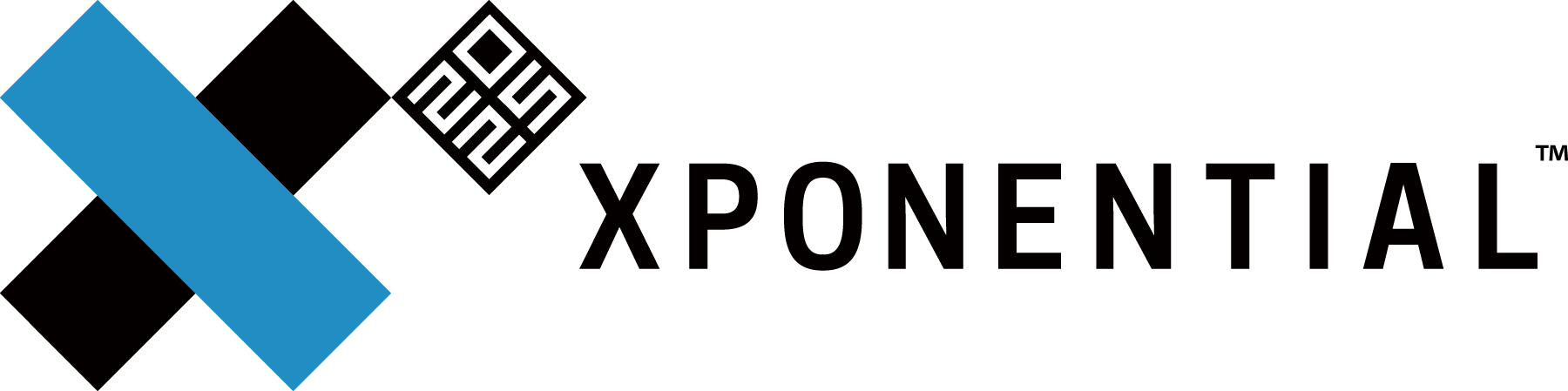
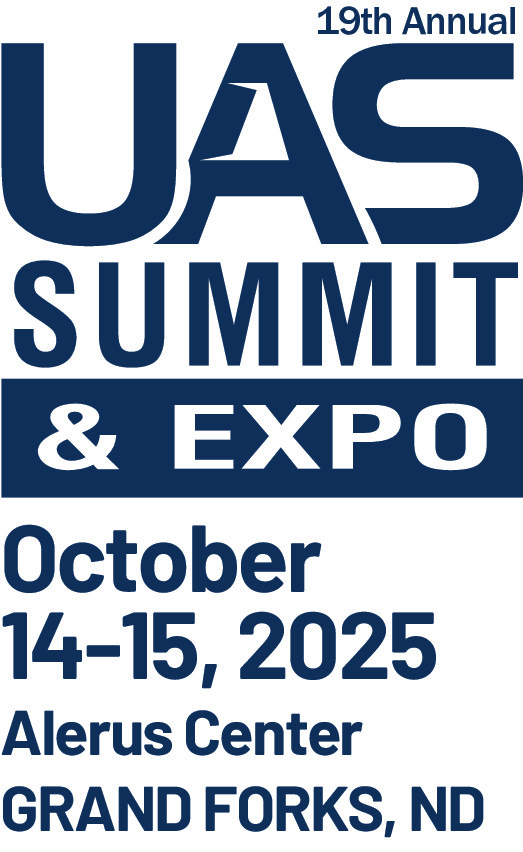

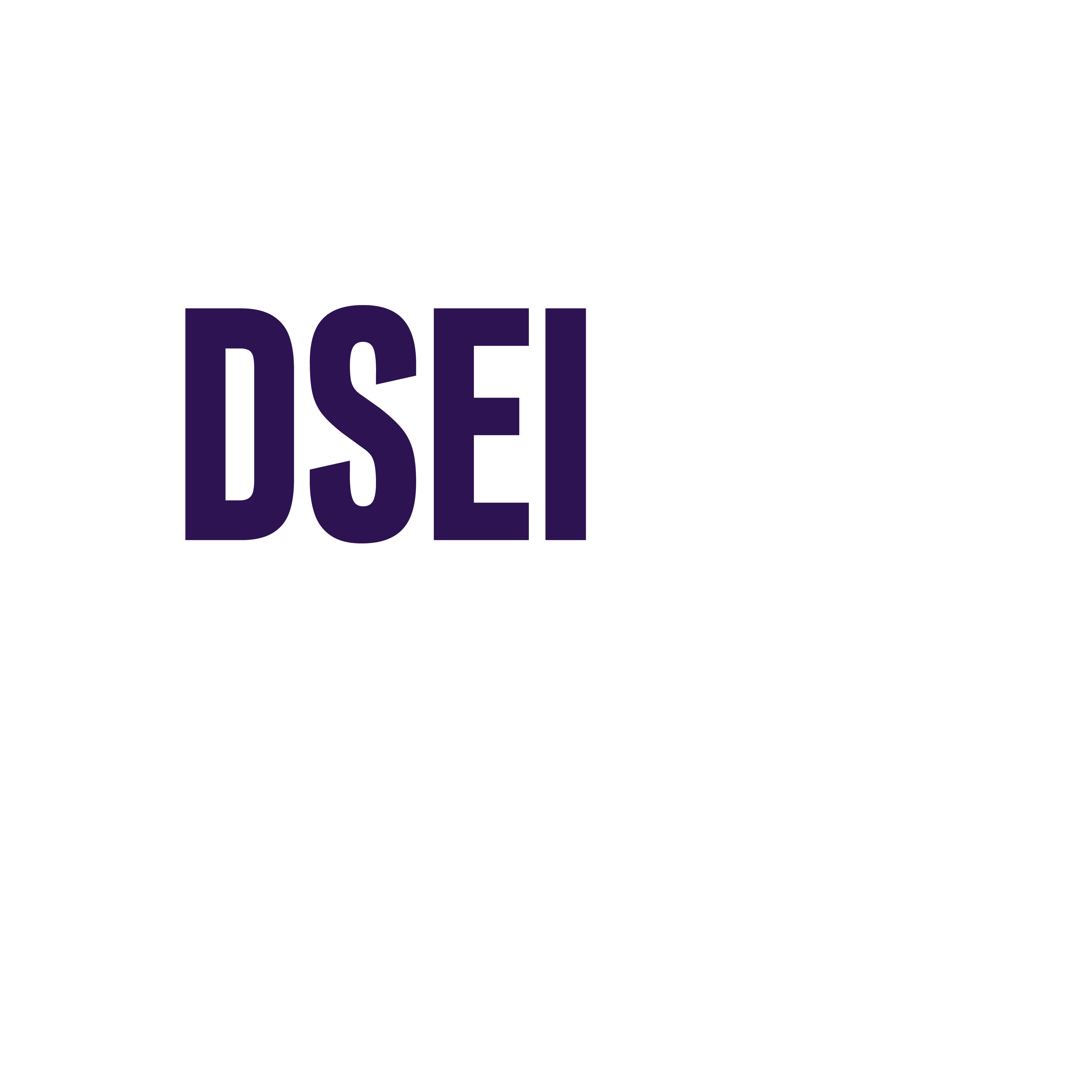
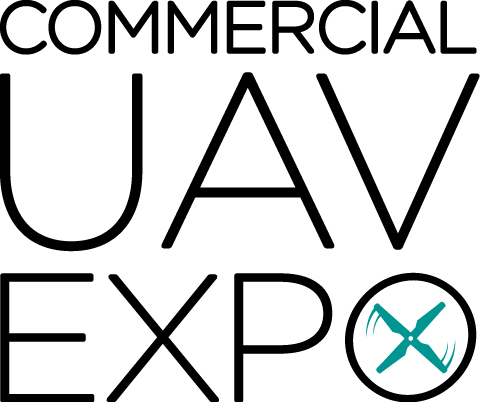
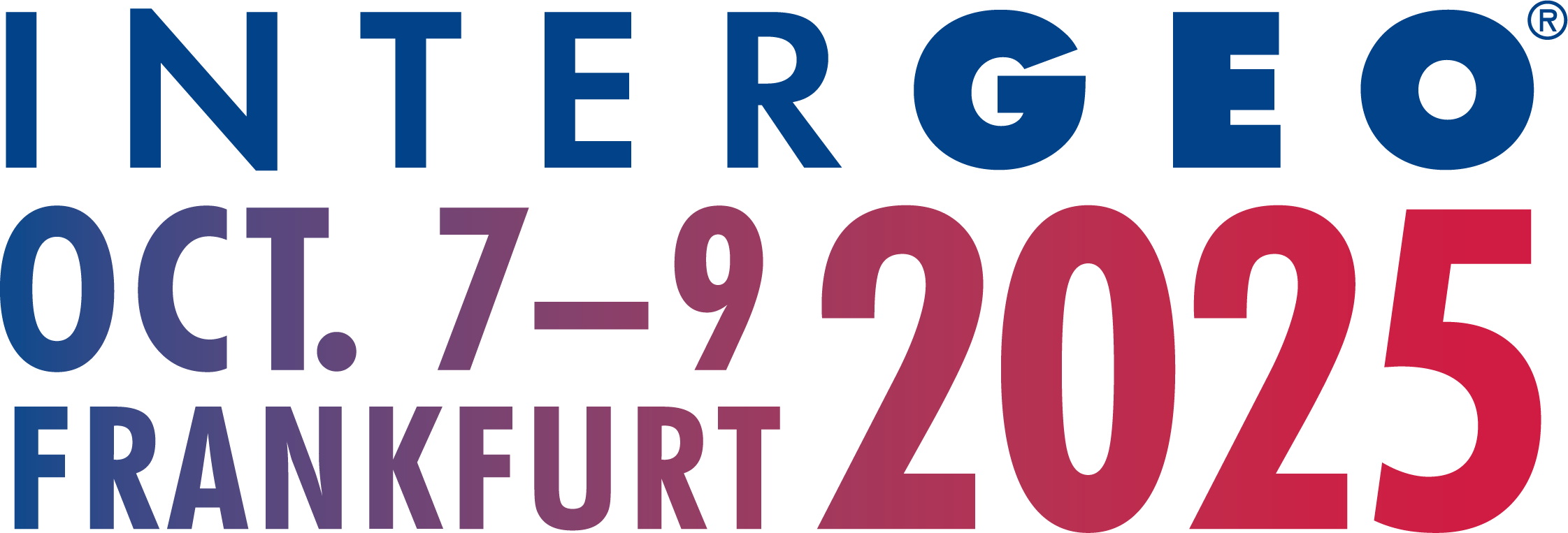
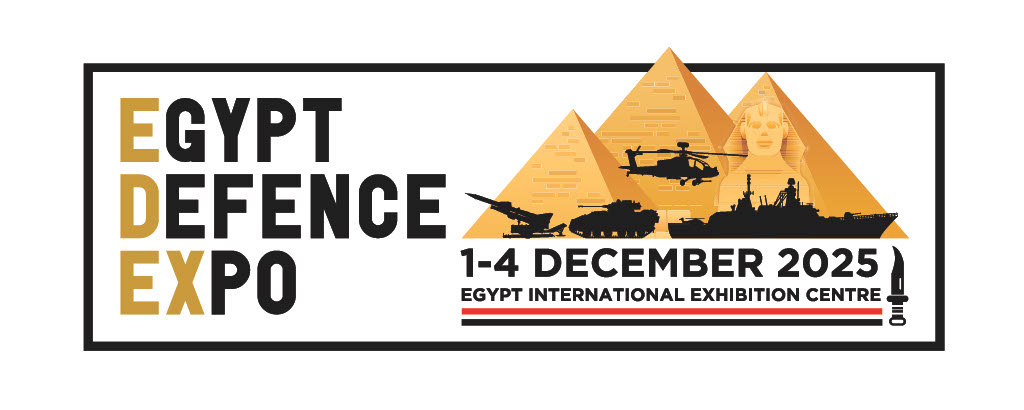
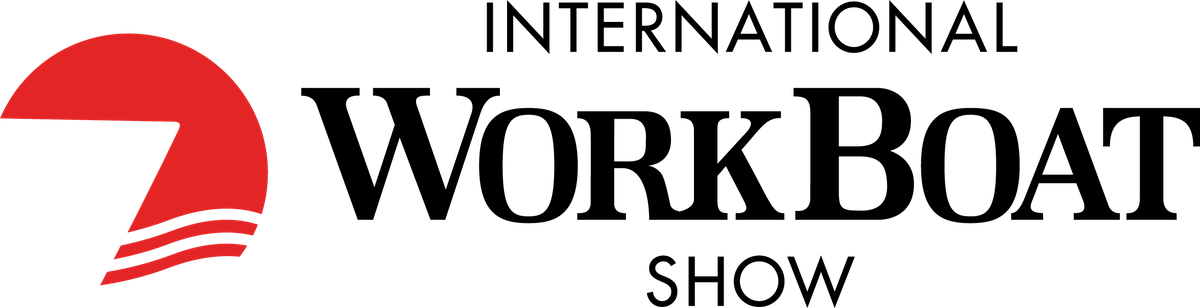