DroneX
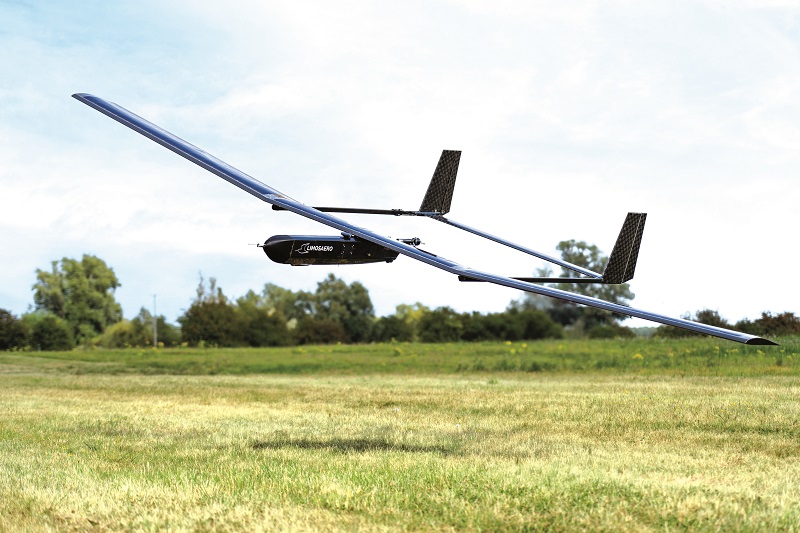
Deck the halls
Many companies showed off their innovations and services this year at ExCeL, as Rory Jackson reports
Once again, the DroneX trade show and conference made its way to the halls of London’s ExCeL in September 2024. There, many companies positioned across uncrewed aircraft manufacturing, operation and components took their places at their stands to show the fruits of their latest research and product development.
Among the new solutions on display were eye-catching innovations in aircraft engineering, autonomy systems, material production, sensors, data processing, and much more. Representatives of companies walked the aisles to discuss recent and upcoming product announcements with vital partners and prospective customers.
Limosaero is a UAV developer and manufacturer whose eponymous flagship product is a fully electric, fixed-wing aircraft sporting solar wings. It has been designed for low altitude, long endurance (LALE) applications, including remote sensing and atmospheric monitoring at minimised operating costs.
“Broadly, those remote-sensing applications are environmental monitoring and air-quality monitoring, including tracking of CO2 and methane fluxes, with longer-than-average flights and larger datasets per flight, enabled by its solar-electric powertrain,” said Hilary Costello of Limosaero.
“Our technical background originated in the high-altitude, solar aircraft space, meaning UAVs designed for 20 km operating altitudes. Since then, however, we’ve become more interested in making something more robust and adaptable for lower altitudes, wide payload remits [and] daytime flights, with the ultimate goal being something capable of multi-day flight endurance.”
The Limosaero solar UAV has a payload capacity of 5 kg, and a typical flight endurance of between five and 12 hours, with its airframe featuring a 5.5 m wingspan.
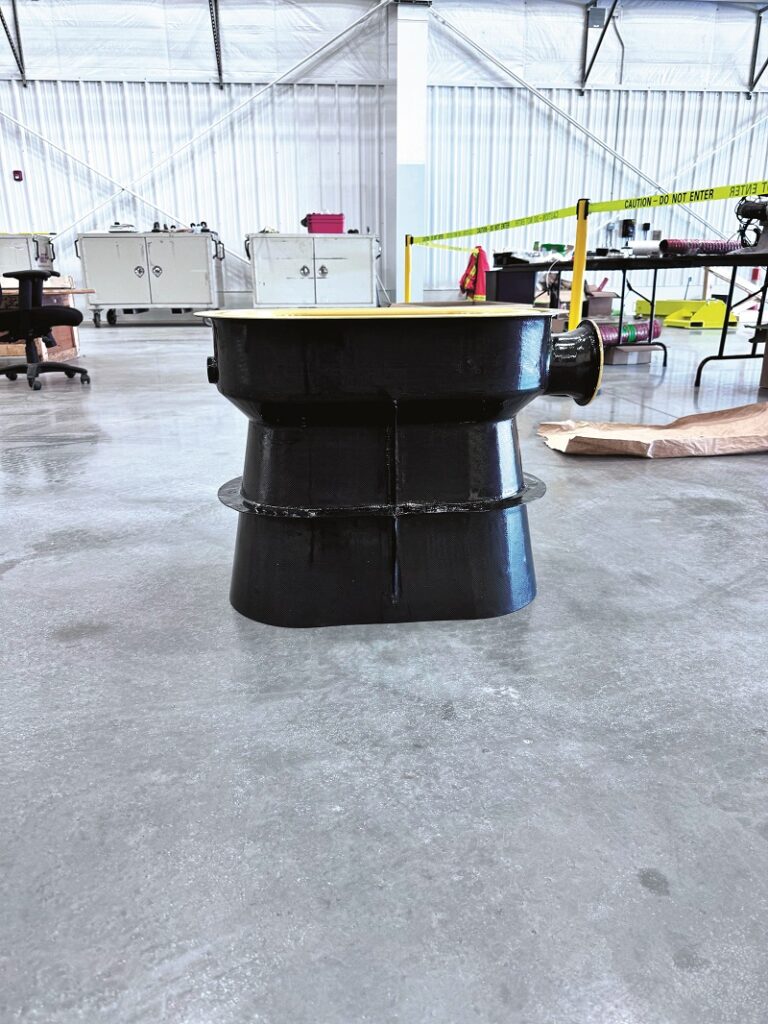
Jetoptera attended the expo to showcase a demonstrator for its J-500 UAV, developed in recent years with a prospective end-user in Dubai and anticipated for deployment next year.
“The maximum take-off weight of the aircraft is 500 lb, so about 226 kg, and we’re also announcing here at the show that our turbine engine, developed specifically for this system, has passed its critical design review,” said Dr Andrei T. Evulet at Jetoptera.
“Our FPS [Fluidic Propulsive System] propulsion technology has evolved a lot since we last spoke with you seven years ago. Today, it uses a turboshaft, driving an axial, two-stage turbocompressor, with highly optimised aero features and pressure ratio. The system is 90% manufactured via additive manufacturing and principally designed to burn jet fuel or sustainable aviation fuel, but we can switch to diesel if needed.”
The J-500 uses two 250 lbf (1000 N) FPS thrusters at the rear of its fuselage and smaller size, 75 lbf class (335 N) thrusters in the front. The rear thrusters are the highest-thrust version of Jetoptera’s proprietary FPS technology so far, and several versions have been successfully tested by the company.
“Two of those thrusters are installed at the front of our J-2000, which is to be our first crewed aircraft, a two-seater, so it has made sense for us to start at this engine size, and to do so in a UAV initially before moving up to bigger engines and to vehicles that can carry four or more people,” Evulet says.
“Along the way, we’ve developed and calibrated numerous unique r&d tools of our own for CFD, as well as probabilistic tools, statistical tools, manufacturability and other hugely valuable means of experimenting with and validating our prototype designs, which have proven indispensable towards engineering working turbomachinery and aircraft over the last couple of years. These now validated, unique tools are used for scaling up our technology to larger and larger scales and sizes.”
While 3DXR is best known as a specialist autopilot engineering consultancy and supplier of Cubepilot systems in the UK, we met with the company at DroneX to learn how its portfolio of supplied components has greatly expanded over the past few years.
As Ben Wilkinson of 3DXR told us: “While Cube Orange is still the most used autopilot we provide, we’re seeing growing interest in Cube Red, especially for its dual-redundancy. Since the Cube systems are modular, our customers can take any Cube, put it on virtually any board, old or new, and it works.”
In addition to autopilots, newer additions to 3DXR’s warehouse and distribution portfolio include telemetry radios, power-management units, voltage and current sensors, and Lidar models from companies such as LightWare, which are gaining popularity in the UAV space.
Wilkinson told us that 3DXR now stocks electric motors from T-Motor, Hobbywing and additional large manufacturers of propulsion solutions, including those providing batteries, servo actuators and propellers, for fast shipping worldwide from its UK location.
“What is particularly exciting in the industry right now is an influx of combined, motor-ESC units, available from small to big size and power ranges; those make for a tightly integrated and guaranteed, reliable electric-propulsion system, which is really helpful for engineers trying to build or modify a UAV in a smooth and tidy way,” he said.
“We now supply most of the sorts of parts used for building a custom UAV, from hobby users to commercial, civil and military organisations, kept in large stock for quick delivery to constructors who are under pressure of time to innovate something reliable quickly.”
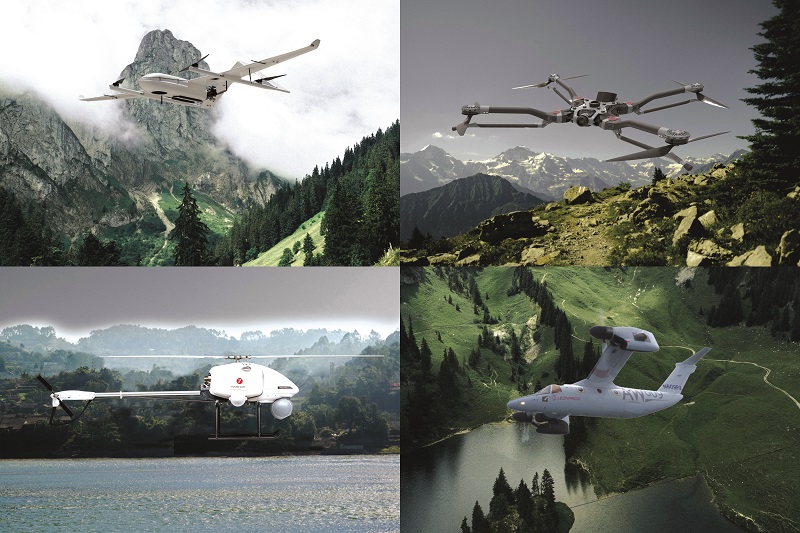
CRP Technology came from Italy to present its enhanced additive manufacturing services, using its proprietary Windform materials, developed to significantly improve the capabilities of selective laser sintering (SLS).
These innovations are centred around a range of advanced composite materials, specifically designed to elevate SLS applications for high-end markets, including components for UAVs, vehicles and satellite systems.
“For instance, we’ve been co-operating with Flying-Cam’s r&d teams to speed up their VTOL UAV development with parts additively manufactured from our Windform XT2.0 material,” said Laura Fabbi at CRP Group.
Flying-Cam specifically involved CRP Technology in the manufacturing of its tail-rotor gearbox housing, which attaches to the main tail boom.
“The choice of material has been very accurate as the part to be was conceived to withstand specific issues. It needed to clamp on the tail boom and also support a carbon plate used as ground protection for the tail rotor,” Fabbi added.
“For these reasons, good stress resistance was vital and Windform XT 2.0 achieved it, with a good ratio of weight-to-stress resistance.”
CRP Technology has also made enclosures for batteries and electronics, printing them using its Windform fibreglass composites to achieve high strength and insulative properties.
“We are one of the few companies that can print dielectric casings and enclosures; an expertise we gained by printing components for racing motorbikes and Formula One, where parts must be safe, very lightweight and strong enough to survive high vibrations,” Fabbi said.
While CRP Technology has largely specialised in making high-end materials for professional applications (from motorsport to industrial, aerospace and automotive), it also recently introduced nylon-based material as a lower-price alternative to its very high-performance thermoplastics and composites.
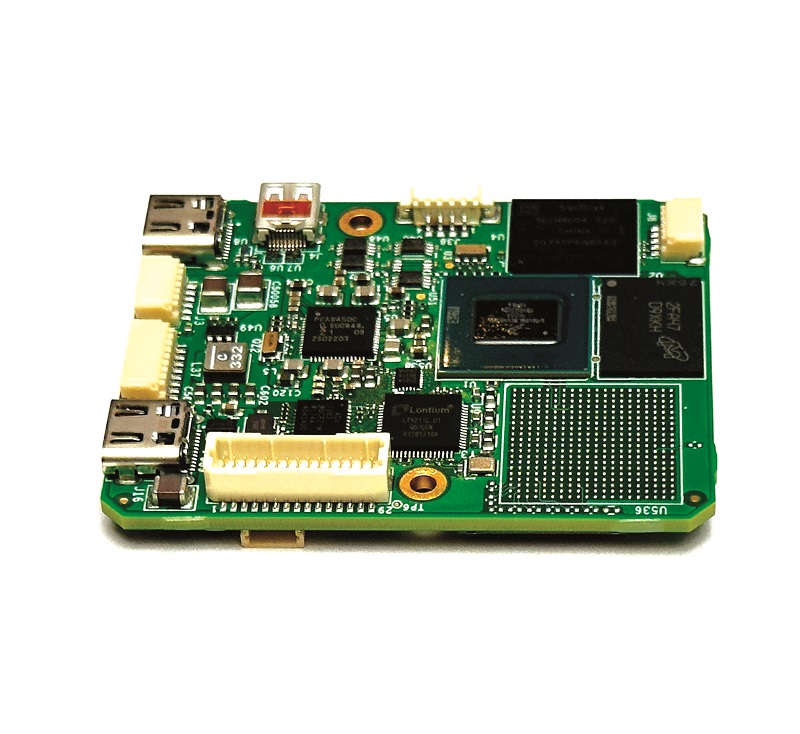
Antrica exhibited a number of its latest video-encoding and decoding systems, including several board-based, SWaP-optimised products that are suited to UAVs and other lightweight or uncrewed applications.
Key among the product range was the ANT-1776ZB, which weighs 22 g and measures 58.4 x 48.3 x 9.3 cm. It is intended to appeal to integrators seeking a SWaP-optimised solution, as well as one suited to multi-sensor operations, having been designed to accept up to three video inputs simultaneously.
“The ANT-1776ZB is designed to accept multiple video inputs and integrate with the Sony Zoom Block camera range, and we have recently introduced a lower, competitive price to make this an attractive option for installers,” said Carly Loke from Antrica.
In addition to integrating LVDS inputs, the encoder can interface with up to two extra inputs via CVBS, USB Type-C, SPI or CameraLink. Both H.265 and H.264 compression are also available in the ANT-1776ZB.
“Low latency is another key feature we’ve targeted with these products: achieving 100 ms of glass-to-glass latency is possible when used with the software decoder that is included with purchases of units in our ANT- 177X range,” Loke added. “In UAV applications, latency is critical, and our products are currently being used in real-world applications for their latency performance.”
As well as functioning as a video encoder, the ANT-1776ZB can be used as a miniature network video recorder, a transcoder or an AI learning solution. Antrica also continues to develop new features in the system firmware.
Inductive Power Projection (IPP) has developed a wireless, inductive charging solution aimed at transferring power bidirectionally between vehicles and charge stations, which it calls MHz-WPT (wireless power transfer).
“We use a much lower-weight coil on the vehicle and, overall, a lower-cost system than has been seen previously in inductive charging solutions, and, partly for that reason, we’re targeting UAVs as our first commercial application of MHz-WPT,” said Dr Mike Taylor of IPP.
“Conventional WPT technology uses copper coils, which are limited to maybe 85 kHz power-transmission frequencies due to skin effect, and while using increased turns of copper or ferrite cores can increase performance; they add weight and bulk, meaning diminishing returns. By contrast, our patented, metal/dielectric, hybrid-ring resonator technology can be constructed from a variety of materials.”
The company started its development using prototypes with copper-plated steel tubes and sintered ceramic dielectrics, and today it has incorporated a dielectric portion to achieve 13.6 MHz power-transmission frequencies, meaning charging rates of up to 2 kW.
The design of the MHz-WPT solution is additionally optimised to minimise power transmission to adjacent foreign bodies, lessening or removing the need for foreign object detection near the UAV and charging module.
It can also transfer power through water; the transmission rate is currently at kHz frequencies, but the resulting charge rate is still usable for USV, UUV and other marine applications.
IPP is also developing a sapphire-based design for future commercialisation, which should be capable of wireless charging rates up to 50 kW.
Kindhelm came to the show from Finland to showcase its technologies for sensor-fused navigation capabilities in uncrewed systems.
“We started with traditional GNSS-IMU systems, and today have integrated them with camera sensors – including compatibility with both stereo and mono cameras in various combinations – with visual positioning and odometry,” said Vesa Hölttä of Kindhelm.
For visual odometry, the Finnish company uses an algorithm that tracks features within video data, and references them in relation to the speed and rotation of the camera, measuring the distance travelled with positioning calculations accurate to 0.6%. Its visual positioning works by comparing a photogrammetric map with camera data.
“It’s AI, but we don’t need training data from the operating environment or annotating, as other solutions might. The algorithm simply finds features from images and then tracks them,” Hölttä said.
“We can use data from most cameras and GNSS-IMUs that end-users might want to use, though a wide-angle camera is naturally preferred for efficient mapping, and we make a lot of our own hardware in-house, along with the software, which we supply as products.”
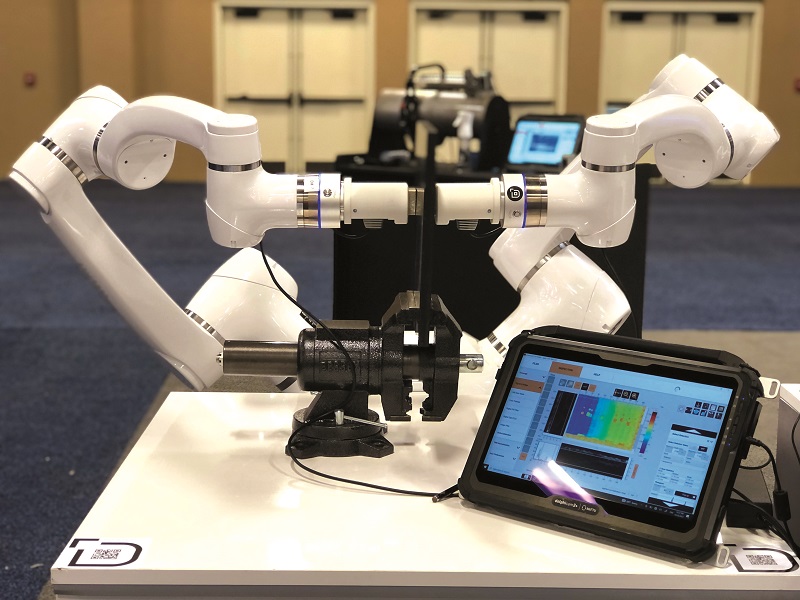
Dolphitech showcased its Dolphicam2 range of non-destructive testing solutions, which are based on its matrix array ultrasonic technology and intended for use by either manufacturers of composite parts, or inspectors of in-service parts, where validating for quality and safety is critical.
“Matrix array works by building up a picture of what materials look like on the inside, using a very data-rich method of generating ultrasonic signals, providing essentially a live C-scan,” said Matthew Day of Dolphitech.
“We can inspect down into composite materials from depths of half a millimetre to as deep as 50-60 mm. Limitations of physics still apply, so there will be nuances around the sizes and resolutions of defects that one can inspect, as there is with any ultrasonic testing.”
The Dolphicam2 uses electrodes to transmit ultrasound waves through material, resulting in 16,384 waves per 32 mm2 of scanned area at a frame rate of 11 fps. Traditional ultrasonic techniques, by comparison, transmit a single wave in and out of material at around 50 Hz. Larger areas can also be mapped, and Dolphitech produces 3D renders and volumetric assessments to give more understandable, actionable information about the integrity of a piece of material.
“We also have an onboard statistical tool that helps with understanding how manufacturing or other processes are affecting the quality of parts, enabling customers to understand where they might, for instance, be introducing porosity into their parts,” Day said.
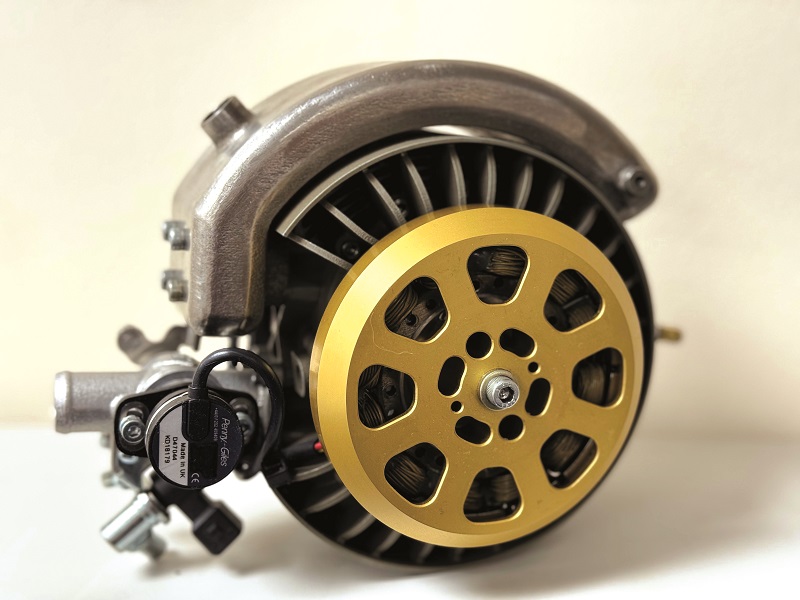
Advanced Innovative Engineering (AIE) exhibited its newest Wankel rotary engines, including its 40 ACS (air-cooled, compact SPARCS), which it described as the world’s first additively-manufactured (AM) Wankel, capable of 5 hp (or 3 kW) of continuous power output. It is now in an initial low rate of production.
“It’s a 40 cc engine, about 150 mm in diameter, has a 2 kg core weight and utilises SPARCS, our patented gas-cooling system for the internal parts of the engine, such as the rotor [explored in Issue 7], whereas the air cooling refers to how we thermally manage the external regions,” said AIE’s Nathan Bailey.
“Typically, our engines are externally liquid-cooled via a separate heat exchanger, but for this engine we were really aiming to make something simpler, lighter and more integrated.”
AM stood out as a means to print metal structures that are geometrically optimised for minimum weight versus structural strength and thermal stability. The latter includes maximising the external cooling surface and avoiding issues such as overheating during climbing or other high-power phases of mission cycles (to which air-cooled engines can be prone).
“When we started developing the engine, AM allowed us to change and iterate it very rapidly, including trying different designs for the heat exchange surfaces, and lattice-type structures to increase the surface area without adding significant weight,” Bailey said.
“We used a metal laser-sintering process and COTS AM machines. Our core goal was to use established tools and technologies where possible to minimise manufacturing risk, while allowing us to have maximum design freedom. All the major housing parts, like the end-plates, are printed using aluminium. The exhaust system is laser-sintered titanium and the rotor is laser-sintered steel.”
UPCOMING EVENTS
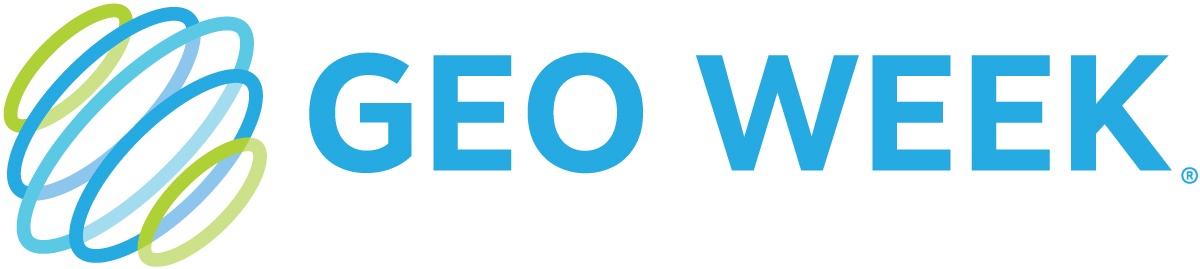
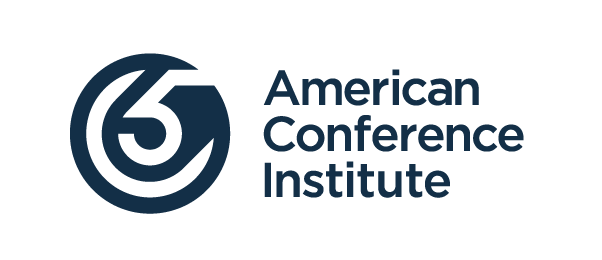
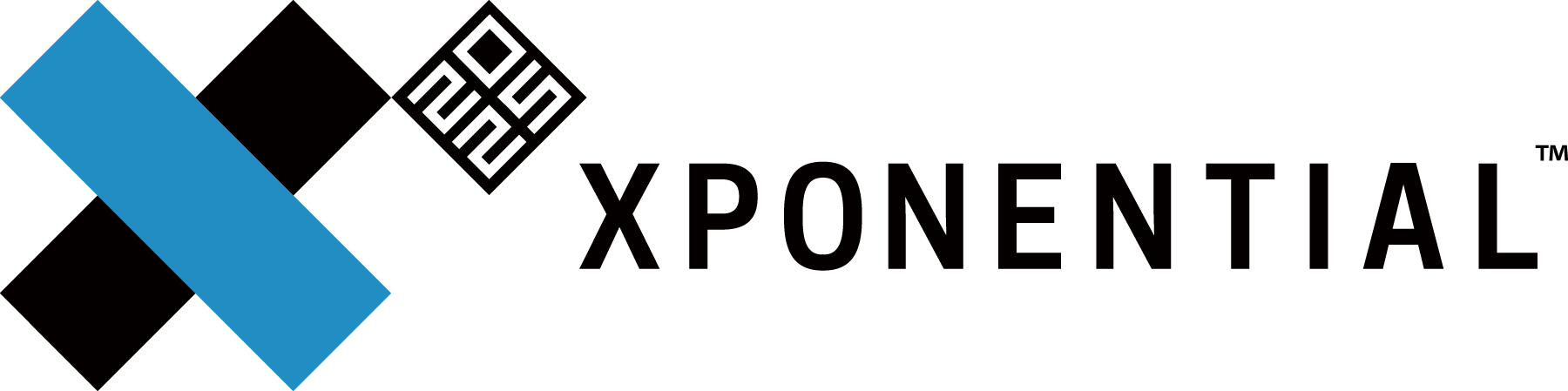
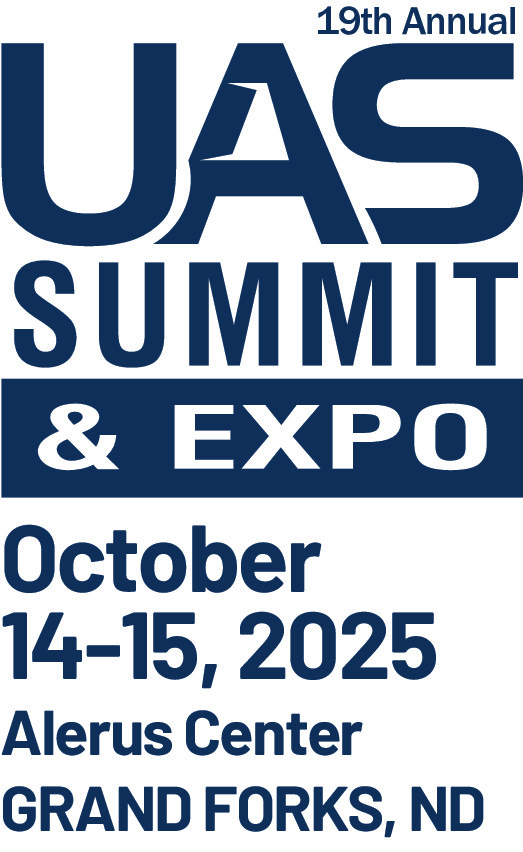
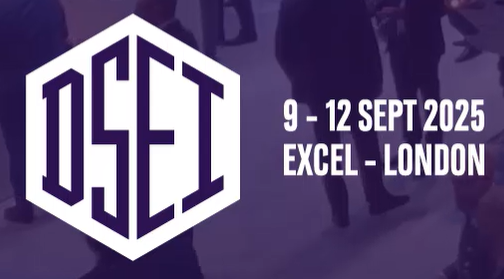
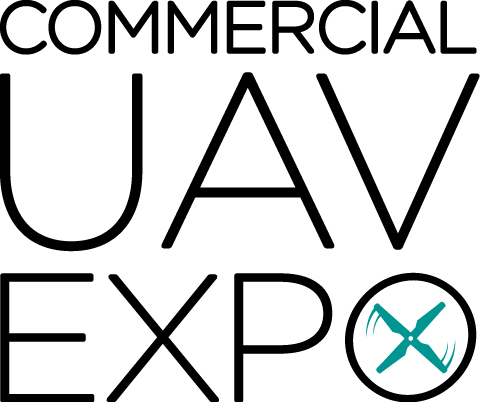
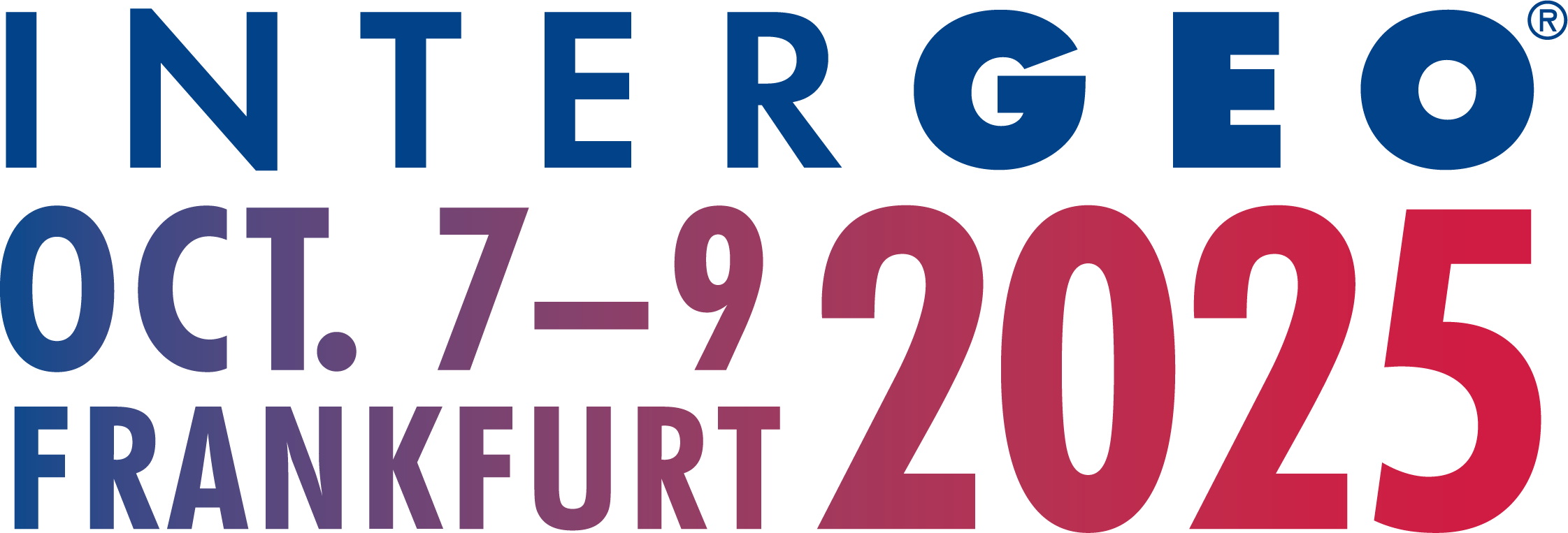
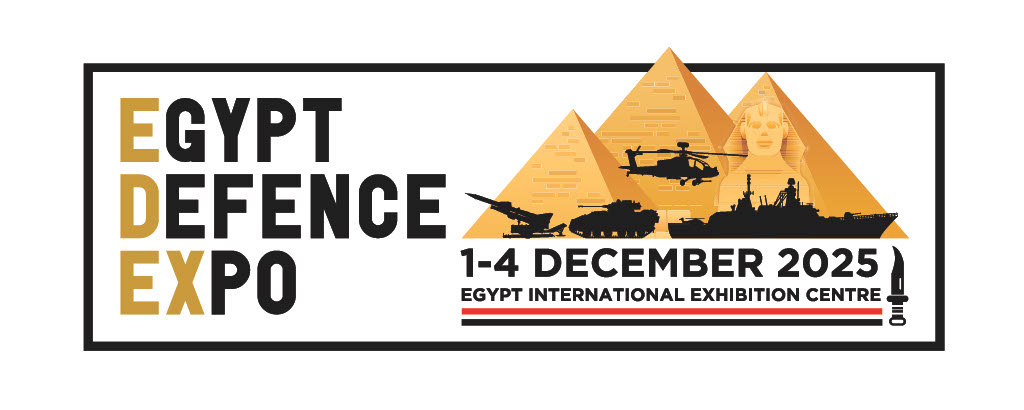
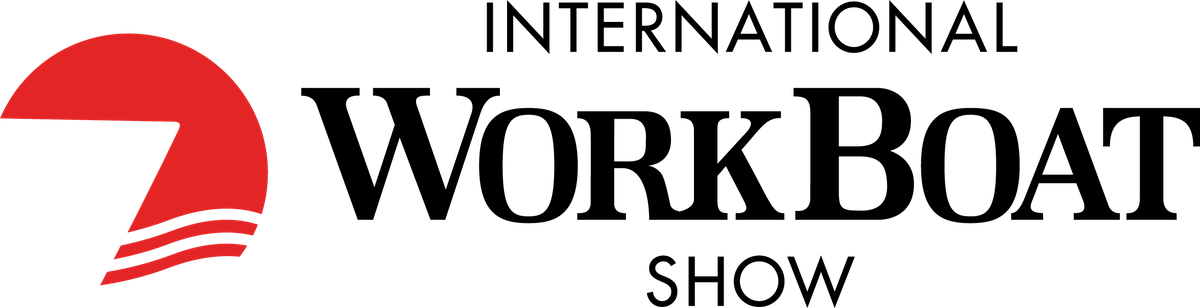
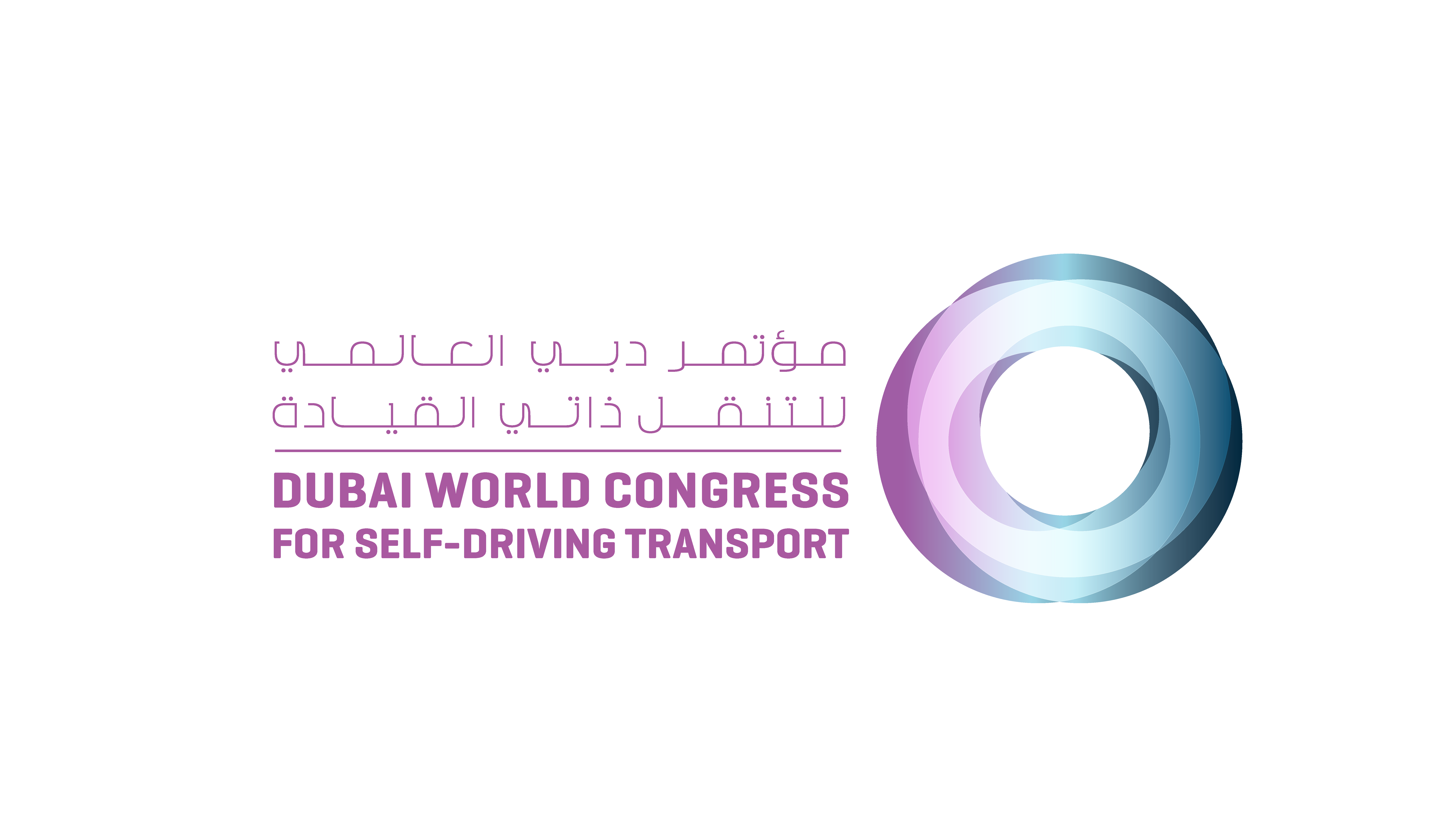
