Phoenix Wings Orca
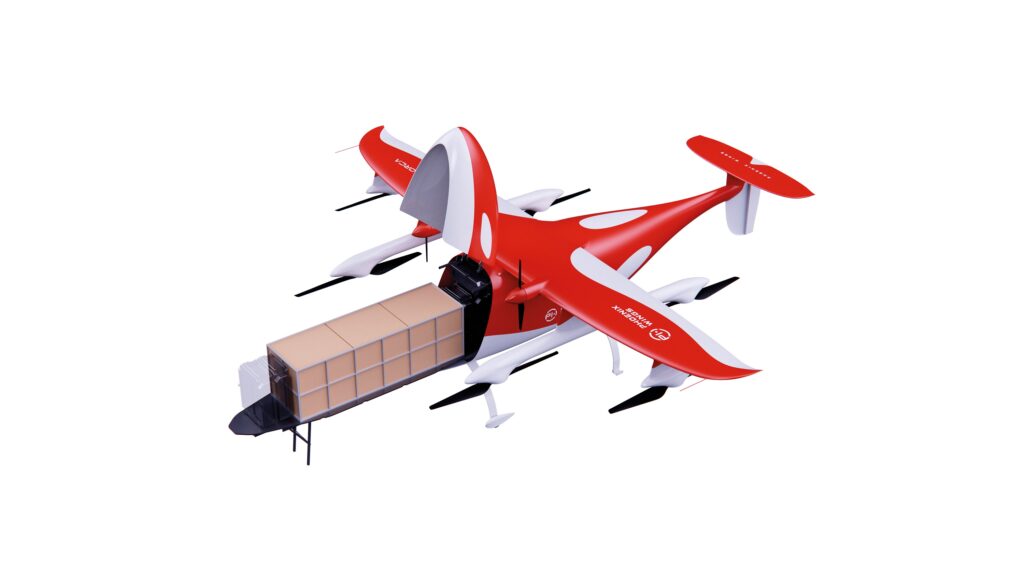
Killer application
Designing this UAV as a cargo carrier from the outset has allowed its developer to maximise its optimisation, writes Peter Donaldson
With its rounded yet sleek fuselage and large horizontal tail surface, Phoenix Wings’ Orca bears a strong resemblance to the charismatic cetacean after which it is named, an impression strengthened by the paint scheme. Many large manned cargo aircraft look rather whale-like, hinting at the Orca’s intended mission.
“We are focused on VTOL drones for cargo applications, and this is the debut of our new airframe, which has been designed from scratch to carry cargo,” the company’s CEO Jian ‘Jerry’ Wang says.
Flight test and operations engineer Robert Iordache adds that whereas the market for aerial imagery and survey is well-established, the UAV logistics sector is still in its infancy, implying that it therefore offers greater opportunities for new entrants.
Early on, it was decided to develop most of the vehicle in-house, including the airframe, flight control system, comms link and flight suite, which consists of a ground control application, a pad management app and a simulation environment for mission building.
The Orca carries a maximum payload of 15 kg within its 96 litre payload bay, with a range of up to 150 km – although not at the same time – cruising at up to 110 kph. Its 2.98 m wingspan puts it just within the EASA’s 3 m limit, while its speed and mass put it well within the 34 kJ kinetic energy limit.
“Our design tools optimise in this regard,” Iordache says. “The Orca flies fast, allowing a smaller wing surface area, resulting in a reasonable wing aspect ratio. Being a VTOL aircraft, you don’t have to deal with the slow-flying landing scenario.”
Profit-centred configuration
The Orca’s hybrid fixed-wing VTOL configuration combines greater speed and range than a multi-copter with the ability to take off and land almost anywhere with very little infrastructure. “This means more possible nodes in the delivery network, more jobs and more profit,” Iordache says.
Its VTOL capability is provided by six lifting rotors, and forward thrust by a pair of propellers, all spun by electric motors drawing power from lithium-ion batteries. It also features a blown flap high-lift system, which contributes to the Orca’s high payload for its wingspan.
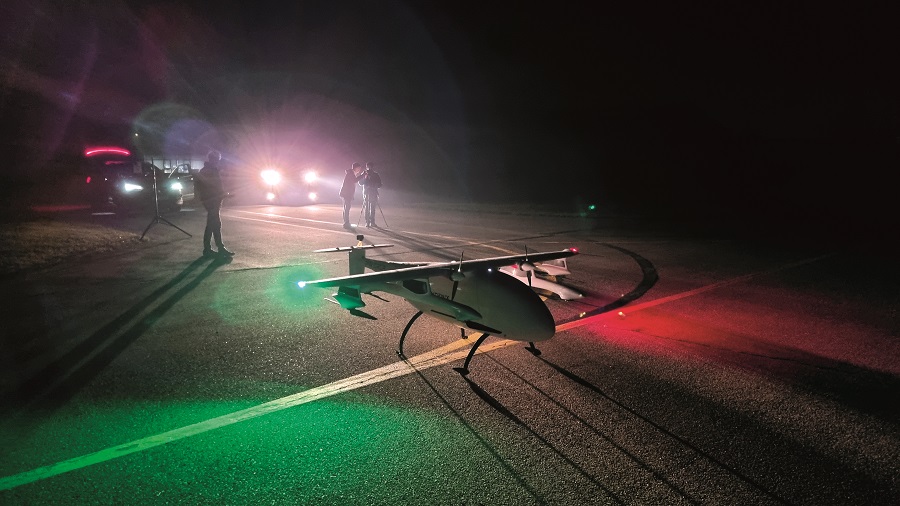
Another goal of the propulsion system design is low perceived noise, which Iordache notes is heavily influenced by the pitch of the sound. “We have also conducted this kind of study in the past with our PW Manta-Ray [now retired], and the Orca’s noise optimisation will start in February 2023.”
Wingspan broadly correlates with the mass of an aircraft, and relates to the risk it presents to people on the ground. Staying below that 3 m limit means the vehicle is subject to less paperwork and administrative costs, Iordache says.
This was one of several design limitations that the company respected when optimising the vehicle for its application. Another was the mandatory parachute, which is a ground safety measure deployed by the flight termination system (FTS), complemented by the ability to continue flying after powertrain or actuator failure.
The last of these was a stall speed of 22 m/s at MTOW, which Iordache explains is a reasonable speed that contributes to good handling and transition from hover to forward flight and back in short distances, ensuring that this happens within a legally mandated area on the ground.
To optimise the payload, Phoenix Wings created a large database of common payload geometries, obtaining the measurements of logistics companies’ standard boxes, medical supplies containers, tool boxes and so on. It correlated these with their mass, including their typical contents, to ensure that the volume and mass are well-matched by the Orca’s payload capacity, which Iordache refers to as “reasonable density”.
Combined with research on the required delivery ranges, this information enabled the company to judge how much of the existing market could be covered with the Orca.
The size and shape of the cargo bay, and the speed and convenience of access to it, are important for a safe and fast turnaround to minimise time on the ground and to maximise productivity, Iordache adds. Considering these factors led to the upward-pivoting nose section that provides unobstructed access.
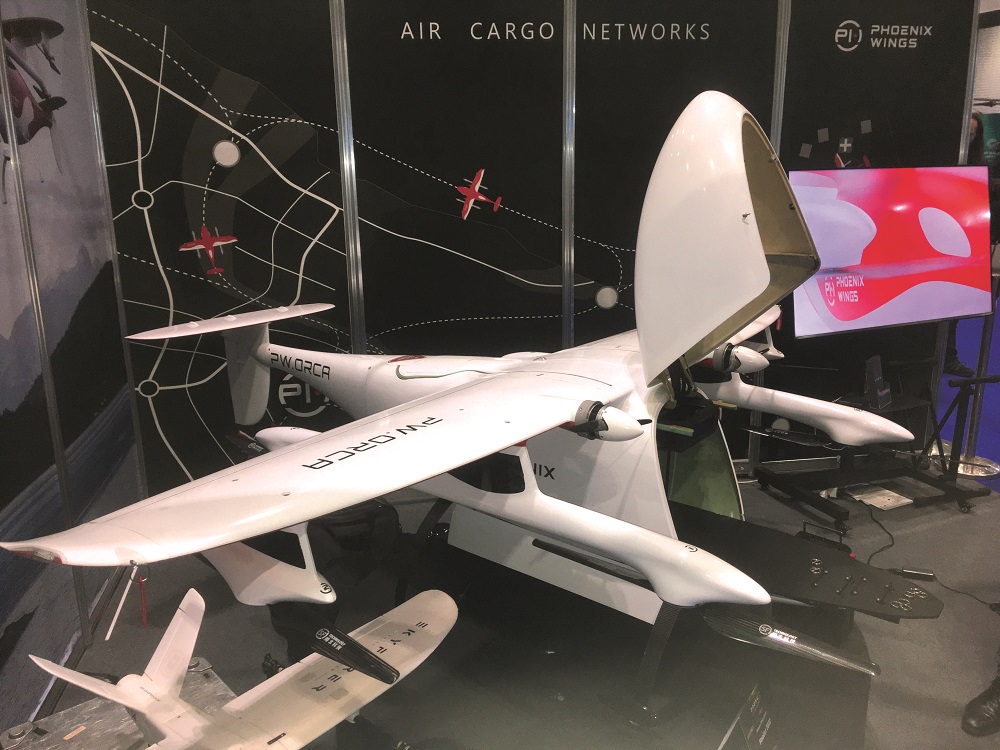
In addition, battery capacity can be adjusted to allow for longer ranges with less cargo, and to provide redundancy. Optimising the capacity led to the development of a modular concept that allows the use of different battery and cargo combinations, and Iordache explains that the range quoted above is for a one-way trip including take-off and landing, accounting for extended safety margins and moderate headwinds.
Optimisation tool
Overall, the optimisation process involved many engineering trade-offs. To help with these decisions the Phoenix Wings team used a numeric optimisation tool for complete aircraft design and mission simulation, basically optimising for cost per delivery, Iordache explains.
The tool was used for sizing the wing and tail surfaces, and for calculating lift, drag and stability, as well as for structural analysis and mass estimation. It also helped in selecting the powertrain components and batteries from databases, choosing the best locations for them on the airframe, and for calculating power consumption figures and ranges for different configurations, speeds and payload/range combinations.
Regarding the intended mission, the tool also helped to estimate operating costs, optimise airspeeds and calculate performance against headwinds to work out real-world ranges. It was even used to estimate the production and maintenance costs.
The most immediately visible result of this optimisation process is the hexagonal layout of the vertical rotors and the off-centre positioning of the twin cruise propellers. The latter had to be carefully designed to keep adverse yaw forces low enough to allow continued cruise flight on one engine, while providing a yaw moment large enough to maintain directional control after failure of one motor in the hover, Iordache explains.
The process also identified the optimum cruise speed to maximise the number of flights in a day. This, Iordache notes, keeps dominant cost drivers such as operator labour low for the same turnaround time.
In a hub-to-hub operation, for example, the process proved that carrying parcels in batches is more cost-effective for end-users, even though it requires more payload volume, because it allows the costs to be shared among more parcels.
Automated cargo handling
While cargo handling is manual initially, compatibility with automated cargo handling systems is planned. This can be seen in features including the powered nose door, automatic payload pallet locking and battery connection, and the belly doors.
“A winch will come later, but lightweight cargo drops will be possible without the winch or a dedicated release hook,” Iordache says. “It is also possible to drop the cargo onto the ground.”
A dolly for hauling the cargo and batteries between a preparation room and the aircraft is under development. Its use will ensure that the aircraft’s centre of gravity will be correct with the cargo aboard. “This will enable faster turnarounds, more convenience for ramp agents, and safer operations.”
Redundancy for reliability
A high level of redundancy is crucial for the reliability that express cargo customers require, he says. Also, Phoenix Wings aims to certify the Orca for operation in cities.
With these factors in mind, the company designed the Orca to continue its mission safely even after the failure of one of the cruise powertrains, one hover powertrain, one battery, any actuator, one control bus and one air data system.
Redundant comms
The comms system has access to multiple bearers for redundancy as well, including satcom and cellular systems and the PW Link, developed as mentioned in-house. The cellular system is 4G (LTE) capable with 3G and 2G fallback.
Operating at a frequency of 2.4 GHz, PW Link uses a proprietary protocol and custom radio hardware and software to form a mesh network, a topology that does not need a ‘master’ node. It provides a direct connection to the aircraft that is independent of the internet between ground stations and aircraft in the vicinity of landing pads, and also serves as an alternative to the cellular and satcom systems.
Iordache describes PW Link as a robust multi-point, synchronised system with frequency-hopping and spread-spectrum capabilities that enables multiple aircraft and ground systems to talk to each other within 7 to 10 km.
Those ranges are achieved with a 100 mW output through omnidirectional antennas, with greater range possible with an output of 1 W through directional antennas, although using the higher power transmissions often requires special permission from regulators.
PW Link is encrypted to the Transport Layer Security 1.2 standard. In addition, ‘bridges’ enable Phoenix Wings to open multiple ground-based comms bubbles that provide connections between PW Link and the internet.
“This allows us to build a comms network and, if needed, to cover an entire operational area,” Iordache says. “It also allows us to provide coverage in areas not reached by cellular or satcom signals, such as valleys.”
The system also lets air traffic control systems know where the Orca is through an ADS-B Out system, which at the moment can only be used in the UK.
The navigation system uses GPS and Galileo signals simultaneously, with extra redundancy provided by inertial dead-reckoning available for a few seconds after losing GNSS. Attitude, height above ground level and barometric pressure sensors can be used to control a hover descent, with a manual override available.
Proprietary flight control
Phoenix Wings developed the flight control system around an STM32 microcontroller from STMicroelectronics.
“Developing our own FCS allows us to have full control over the software stack,” Iordache explains. “It makes integration with customer systems easier and more customisable. Also, certification was an important consideration.”
In addition to following pre-programmed routes, the FCS can work with integrated transceiver-based in-flight collision avoidance systems such as FLARM, and with sensors to detect non-collaborative air traffic.
“At the moment, the flight control computer is the only component without redundancy, and a failure will result in an FTS activation,” Iordache explains.
“The upcoming release of our ground control application [GCA] will also plot a ground risk area, which will illustrate the areas that are at risk in the case of an FTS activation,” he explains. “Different regulatory bodies will ask for different mitigations, according to the situation, and a redundant FCS is planned for the future.”
Structure and materials
The Orca’s monocoque fuselage is made from a composite sandwich skin that takes most of the loads, supplemented by bulkheads for localised loads and to provide extra resistance to buckling.
The pallet rail system also plays a structural role, serving as a set of stringers to resist bending loads and providing reinforcement around the opening for the cargo doors in the belly.
In the prototype, the fuselage material is mostly fibreglass for its resistance to corrosion and transparency to radio signals, Iordache notes.
It is in the lifting surfaces where higher strength- and stiffness-to-weight ratios are essential, so these take the form of carbon fibre sandwich shells that take the torsional loads, bonded to carbon fibre composite spars that resist the bending loads.
The fibre is HT carbon, and parts are hand-laminated with an epoxy resin serving as the matrix for the composite, which is tempered at 50 ºC after its initial ambient temperature cure.
Aluminium alloy to 6061 grade or higher is used for powerplant interface components such as the 3D-printed cruise motor bulkheads (with integral cooling system) and the tilt angle adapters for the lift motors.
Powertrain components
The motors are MN705S KV260 units from T-Motor with custom-made electronic speed controllers. Phoenix Wings quotes a power draw of 8 kW in a static hover and 2.4 kW in cruising flight at 30 m/s, both at maximum take-off weight and 1000 m above mean sea level in international standard atmosphere +15 ºC.
The batteries that provide this power are 12S lithium-polymer units configured into 22 Ah modules, of which the Orca can use two, three or four. They are designed for quick swapping by one of two methods depending on the configuration of the battery system.
If they are mounted on the top rail in the cargo compartment, they are removed one after the other and replaced in the same way. They can also be mounted on the cargo pallet and replaced with the pallet in one go, Iordache explains.
Tracking down any faults quickly helps minimise downtime, and Phoenix Wings uses a number of diagnostic methods.
Analysis of logged data from the vehicle’s systems helps to spot trends that might indicate developing faults, and in-flight telemetry processed by the GCA is used to generate alerts to any anomalies in voltage, current temperature, rpm and other parameters that might arise. The company also uses several live debugging interfaces, and pre-flight checks are automated.
Access to systems that might need attention is enabled by hatches for the parachute and avionics, while the large cargo doors in the belly allow access to the cargo space.
All the major components are quickly removable for deeper maintenance and repairs, including the left and right main wing panels and wing tips, the tail boom, the vertical and horizontal tail surfaces, and the landing gear. Further, all the powertrain components including their wiring harnesses can be changed without having to solder anything, Iordache adds.
Flight testing
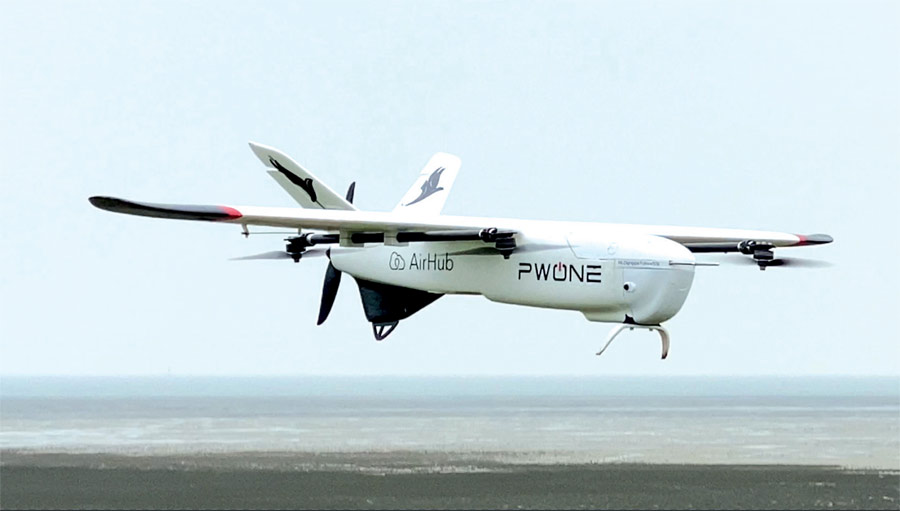
DroneX 2022 was the Orca’s public debut, and an intensive 3-month flight test campaign in Germany began immediately after the event, a smaller proof-of-concept vehicle called PW One being used to gather relevant flight test experience and the resulting data.
Wang explains that the PW One has the same core hardware as the Orca, and that the ecosystem of software is compatible with both vehicles, enabling the smaller machine to serve as a flight test vehicle and a means of proving the viability of proposed operations.
“We always test in simulation, including hardware-in-the-loop, and then we go to the small vehicle to test everything, especially emergency testing,” he said. “We use it to find out what happens in abnormal situations, and whether we can recover from unusual attitudes and so on, and then we can verify it on the bigger one.”
Iordache explains that using simulation in the development programme brought several benefits, including the ability to automate testing, run a large number of iterations and to run many different tests in parallel.
“We also provide the smaller drone as a proof-of-concept package to our partners, because that is a very cost-efficient way to do trials to prove the concepts of particular routes and potential business cases,” Wang says. “You can just take the PW One, put it in the back of a car and with one or two people at each end of the route you can run the proof-of-concept trials.”
At the moment, Phoenix Wings is focused on urgent deliveries, particularly of medical supplies, but it is also looking at offshore operations. “Offshore scenarios are interesting, because they actually have quite high demand in terms of cargo volumes,” Wang says. “Also, most routes can be planned to run over water, which is unpopulated of course, making it easier to get safety approval from local aviation authorities.”
That puts more demands on flight performance, he adds, for example on the ability to handle high winds. Tested in the Netherlands’ offshore environment, the PW One handled well in 50 kph winds, and the Orca is set to follow, Iordache notes.
The offshore environment also puts more demands on the level of ingress protection, with a particular need to keep out rain and salt spray, for example. “This is the kind of thing we are going to test more with our partners,” he says.
Iordache says the flight test programme is continuing, with further tests planned to assess performance, environmental factors, failure cases and longevity. “The Orca is designed as a modular, flexible platform that allows us to tailor it to different operational needs,” he says. “That might involve integrating camera systems, winches and hybrid propulsion – and of course we want warp drive!”
Specifications
- Wingspan: 2.98 m
- Length: 2.62 m
- MTOW: 52 kg
- Payload mass: 15 kg
- Payload volume: 96 litres
- Cruising speed: 110 kph
- Payload versus range: 15 kg to 60 km 1 kg to 160 km
Some key suppliers
- Batteries: Grepow Tattu
- Cellular comms module: Quectel
- Embedded computers and microcontrollers: STMicroelectronics
- Motors: T-Motor
- RC radio equipment: JETI
UPCOMING EVENTS
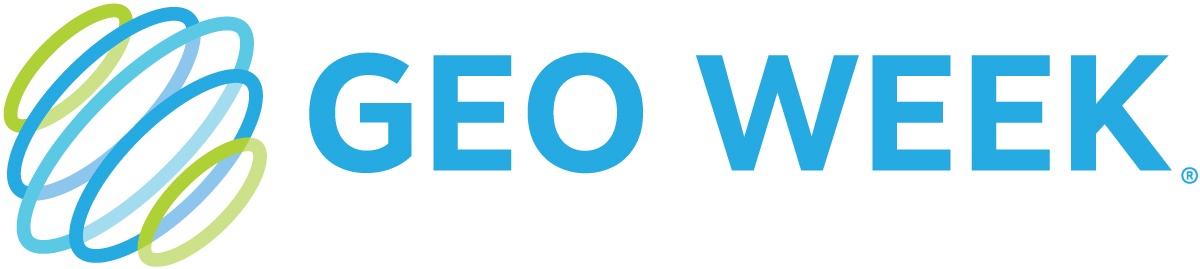
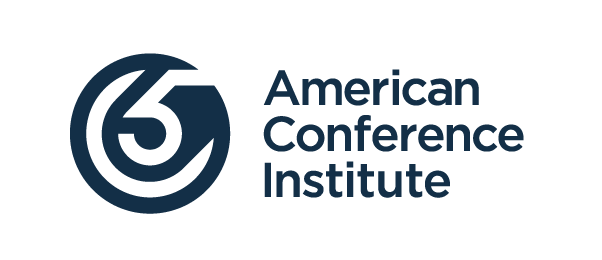
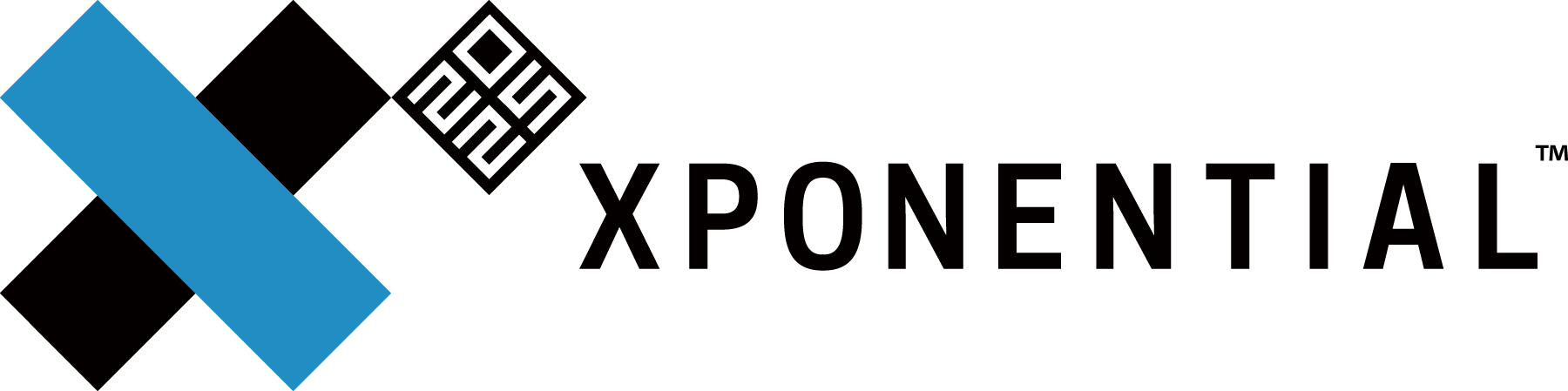
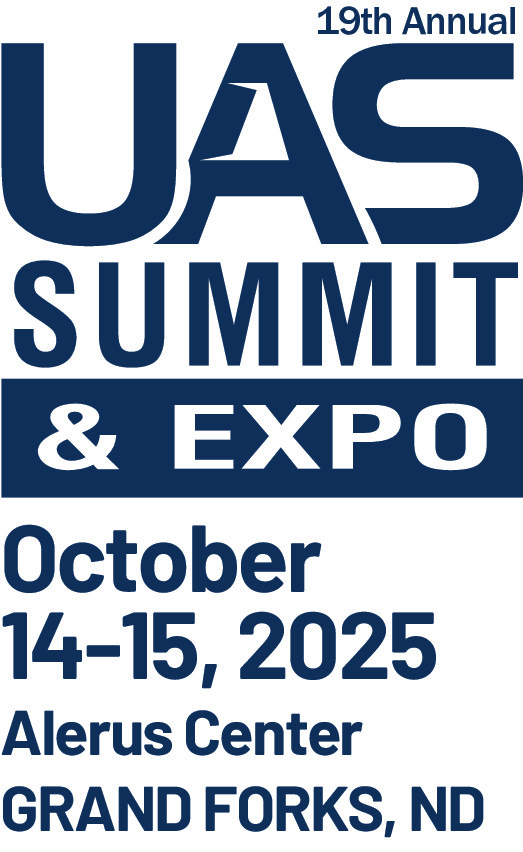
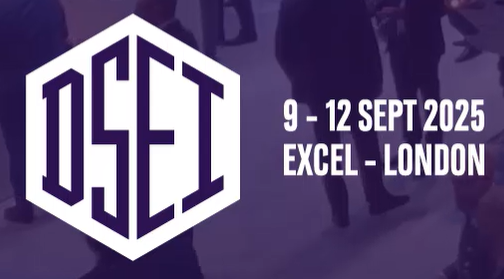
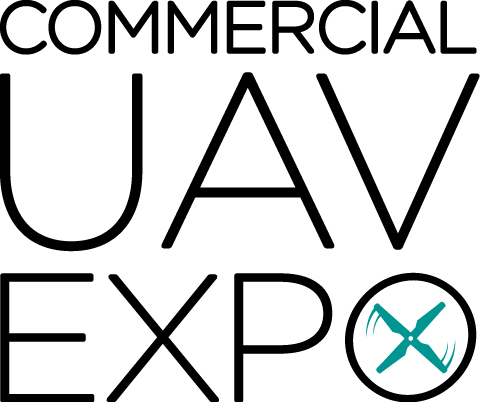
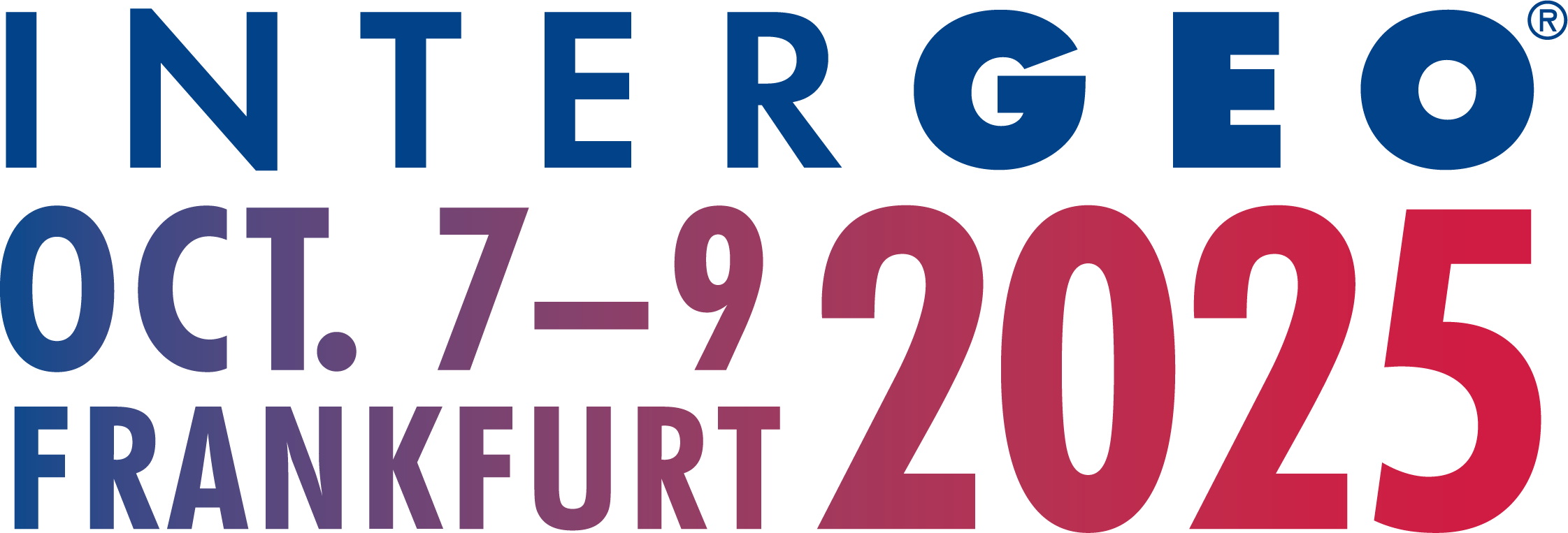
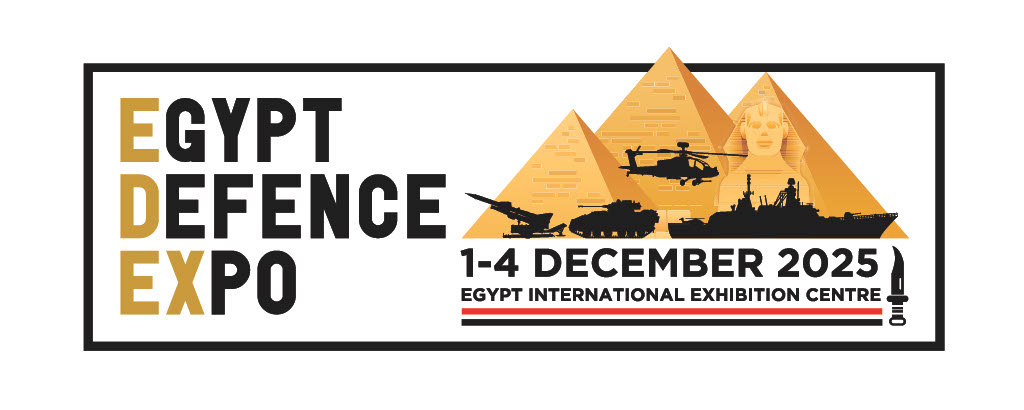
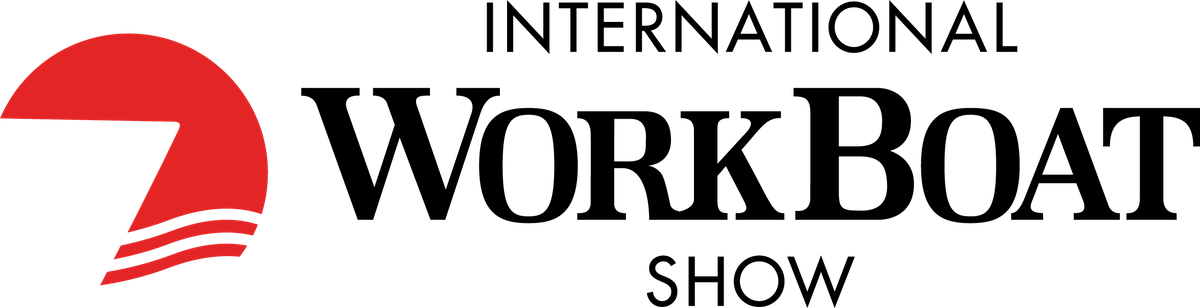
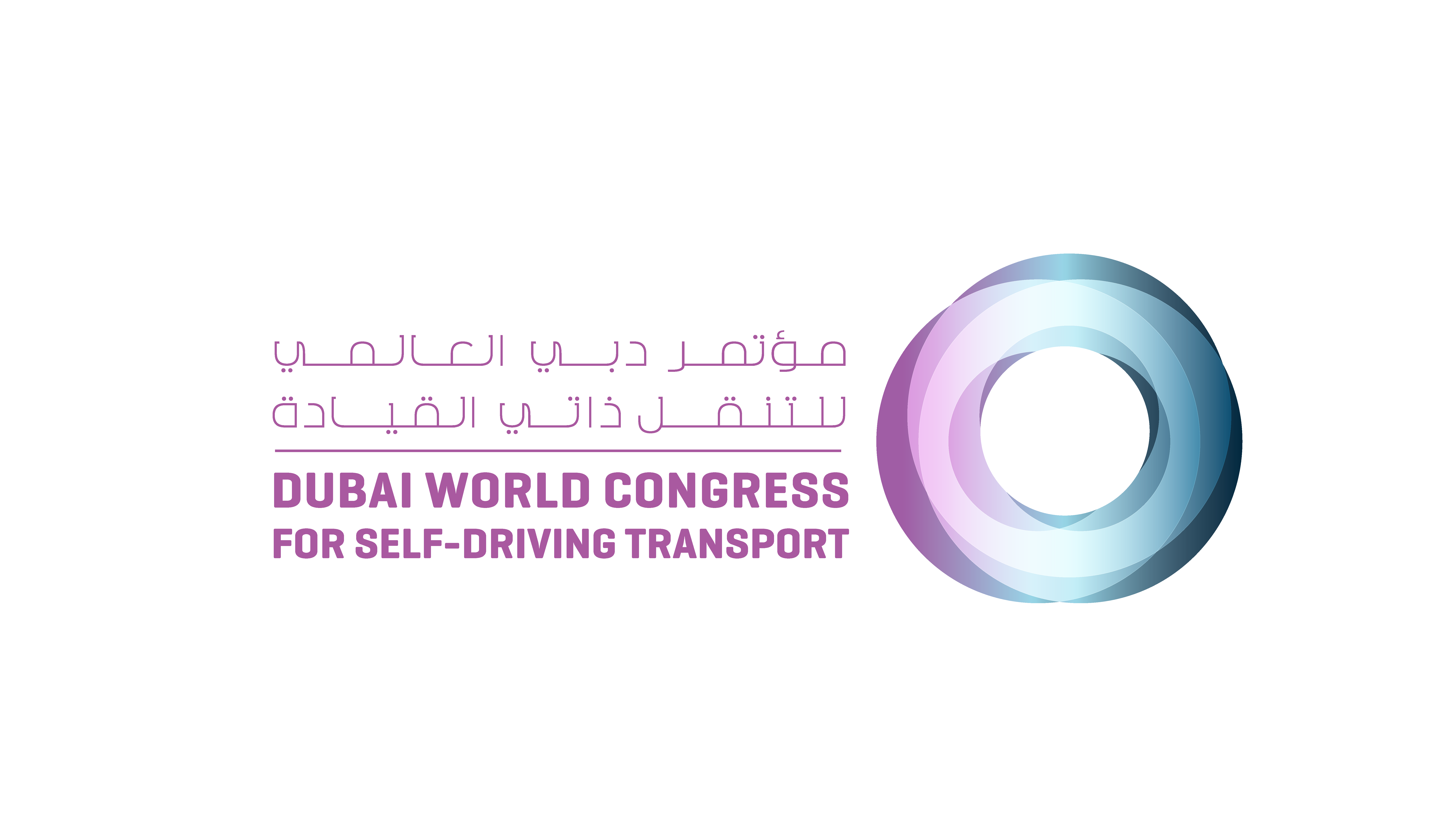
