Armach Robotics HSR
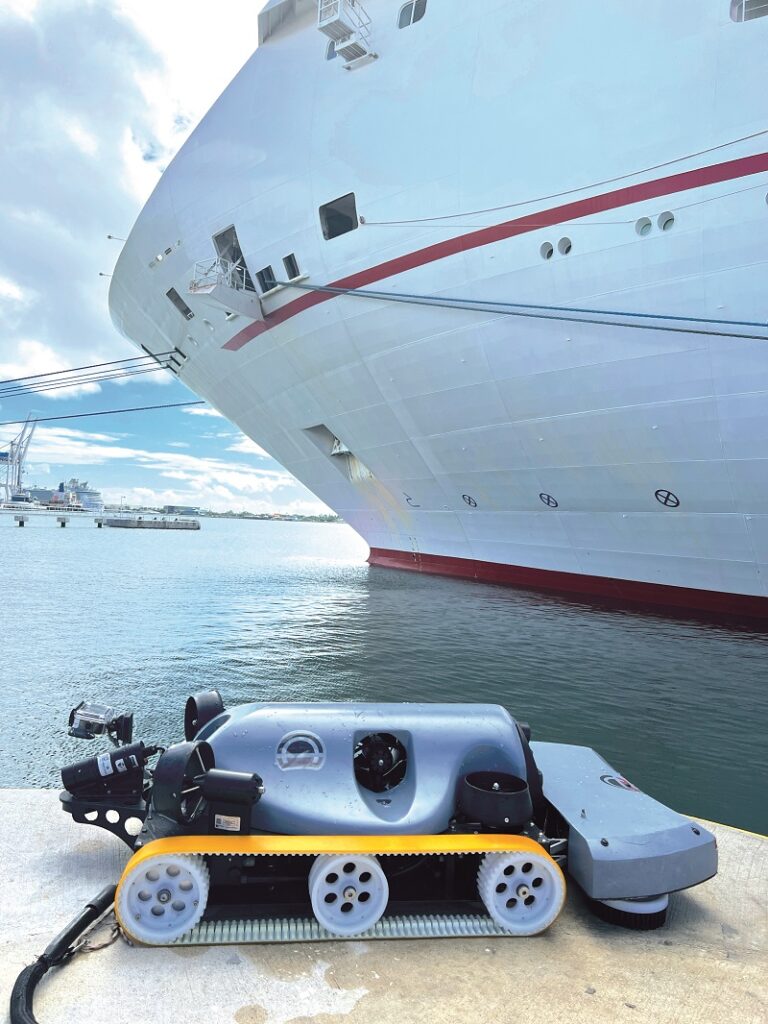
Demand for keeping ships’ hulls clear of fouling organisms is set to surge, says this developer of an uncrewed brushing system. Peter Donaldson reports
Smooth sailing
Marine life is notorious for attaching itself to any structure that people place in the sea, and a barnacle-encrusted hull is a sure sign of a neglected vessel that consequently suffers from increased hydrodynamic drag, fuel consumption and CO2 emissions. Barnacles, however, are looked on as macro-fouling – larger organisms that rely on ‘micro-fouling’ in the form of much smaller ones such as algae, bacteria and slimes to provide a base layer and initial food source.
Regularly brushing this micro-fouling off the hulls of a wide range of military and civilian vessels could become big business for the underwater robotics industry, so Armach Robotics, with its Hull Service Robot (HSR), is about to commercialise its EverClean service on a large scale. Rather than selling the robot systems though, Armach offers EverClean as a service to be delivered in port or with systems that live aboard a vessel.
Military roots
Karl Lander, director of regulatory compliance and outreach at Armach Robotics – a spin-off from Greensea Systems – recalls that the genesis of the idea was in a US Navy Office of Naval Research (ONR) project to develop an autonomous robot for cleaning hulls. Greensea impressed the ONR sufficiently that it awarded the company a Small Business Technology Transfer contract to advance the technology and provide a capability that could be delivered to the Navy.
With these contracts, the Navy is not looking for a military-only capability, for which it would have to cover all the development costs, so any technology must have a path to commercialisation in order to qualify, Lander explains. Cleaning commercial shipping provided that opportunity.
“By keeping a ship’s hull clean of bio-fouling, we can significantly improve fuel efficiency and reduce greenhouse gas emissions, as well as limit the potential of transfer of invasive species,” he says. “We do this in a way that is friendly to hull coating systems and can be completed in ways that avoid disrupting ship schedules.
“The idea of a crawler using low-pressure suction and rubber tracks to drive around on a surface, by itself, is not new to the industry,” he adds. “Other companies have done that with various small ROVs for inspecting inside large storage tanks, but the world of small marine robotics is constantly advancing, and we saw this specific need.”
Greensea began developing the navigation and autonomy technology in 2018, building on earlier subsea robotics work and leading to a proof-of-concept phase with support from the US Navy. Armach was formed in late 2021 to deliver the service, with Carnival Cruise Lines becoming an early adopter and service development partner.
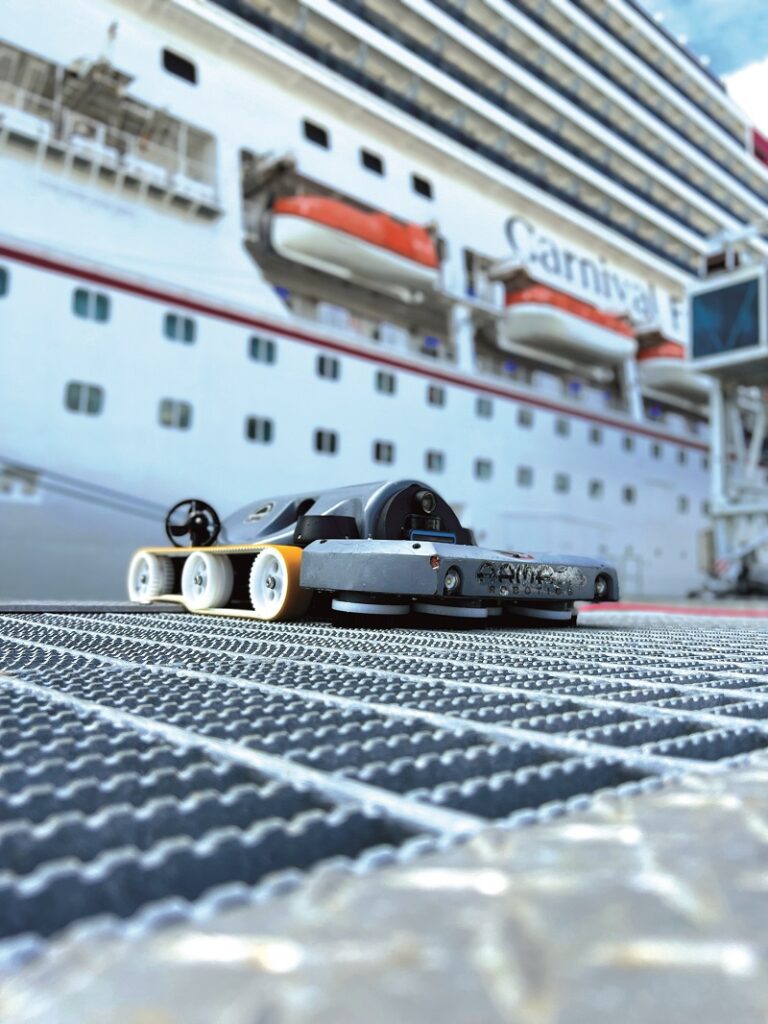
Proof of concept
For the proof-of-concept phase, Greensea’s early testing with existing systems proved unsatisfactory, Lander says, leading to the development of the HSR. Armach plans to improve it iteratively to increase efficiency and performance as the company learns more through operational experience and customer feedback.
The team worked on more than a dozen vessels of various sizes during the HSR’s development, carrying out test cleanings in ports in New England, Virginia, Florida and Texas. “The more complex the hull form and features, the more challenging they are to clean, but overall the degree of difficulty doesn’t change too much,” Lander notes.
The HSR has thrusters that allow it to be propelled manually like an ROV, and to attach itself to the hull using low-pressure suction. It then moves over the hull’s surface using its soft rubber tracks.
“We did a lot of testing with the Florida Institute of Technology [FIT], choosing appropriate track materials,” Lander recalls. “We want good traction, but we don’t want to damage the paint on the hull, and we don’t want the tracks to wear out too quickly. It took a lot of lab testing there to figure out the right balance and settle on a suitable rubber compound.”
Weighing around 30 kg and measuring about 86 cm long, the HSR is a small vehicle tasked with very large cleaning jobs. Lander explains that Armach wanted to keep it small so that it remains portable for one person, and can be launched and recovered without a crane or any other special equipment. “From there, it was a question of optimising the cleaning tool and robot speed to stay within that size limit,” he says.
Rather than using batteries, the vehicle draws power via its tether from a generator ashore or aboard the ship it is cleaning. The tether is also the robot’s comms link with Armach’s mobile operations centre.

Assessing the job
Before starting to clean any ship, the first task is to verify the condition of the hull coating and the level of fouling. As the robot can only clean micro-fouling, it is essential to be sure that the ship is in a suitable condition. Armach then works with the ship’s owner and agent to coordinate access to it.
“The HSR operates using supervised autonomy, so the pilot monitors its progress, while another member manages the tether,” Lander says. “In some locations, we can use a tether management system that reduces manpower needs. That capability will continue to evolve, making the evolution more efficient.
“On the day of cleaning, the team arrives at the pier with a mobile operations centre and two to four team members,” he says. “Once the approval is granted by the ship’s owner, the robots are manually launched and ‘flown’ into position. With the number of thrusters we have on the HSR, it’s easy to roll – the operator rolls it 90o, attaches it to the hull and switches it to crawler mode.
“The pilot will then do a quick survey to get an idea of the area we are trying to cover, and program that into the vehicle, essentially telling it to ‘drive around this area in this pattern’. The software will allow you to just select a pattern and then hit ‘Go’. At that point, the operator can put the controller down, sit back and watch to make sure the robot is doing its job and is not stuck in a corner.”
Watching the imagery on the Sidus Solutions forward-looking video camera, the operator can see what the HSR is coming up to next and assess the conditions. Any areas with no fouling, have macro-fouling that the robot is not designed to deal with or show damage to the coating, can be avoided. “With the software it is easy to set exclusion zones, and the robot has its own obstacle avoidance capability as well,” Lander says.
Almost SLAM
The main engineering challenges in the HSR’s development centred on the technology needed to navigate and operate autonomously in a GPS-denied environment that also has the ship’s hull rather than the Earth as its frame of reference, according to Lander. The HSR finds its way around the ship using a proprietary system the company calls hull-relative navigation, which uses sensors and software that provide capabilities close to those of simultaneous localisation and mapping (SLAM).
“It’s a slightly different approach, so we’re not calling it true SLAM, but that’s essentially what it is,” Lander says. The system creates a new coordinate frame based on the ship itself, and the vehicle uses a multi-sensor navigation system that includes odometry, inertial devices, and a Doppler Velocity Logger (DVL) from Water Linked, to find its way around, assisted by forward-looking sonar and camera imagery.
Including the DVL in the navigation system provides an independent set of motion cues derived from direct sensing of the environment immediately around the robot. “The DVL pings off the ship’s hull to give us another piece of information on how it is moving in relation to the hull,” Lander explains.
If the robot gets stuck but the tracks are still spinning, for example, or the tracks are stationary but the robot is sliding with the current, the odometry will not detect that but the DVL will. “It helps correlate what the robot’s other sensors are seeing,” he says.
The odometry system is integrated into the motors that drive the tracks, a solution engineered in-house.
“All the information from the robot’s sensors is fed through a Kalman filter to ensure it is using the best available information to give us its position,” Lander adds. “That information is coupled with sonar imagery collected in real time to build a map of the hull.”
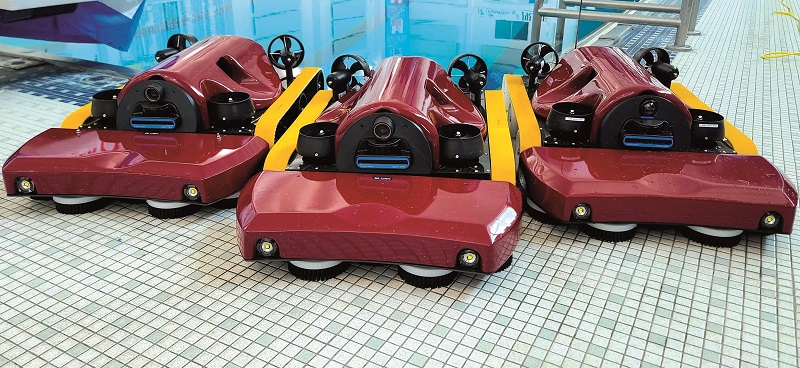
Building the map
Building the map starts with developing the hull-referenced coordinate frame. “When we pilot the robot in place to go to the hull, we then give it a new orientation – basically taking north, south, east and west and translating it into up, down, left and right, using gravity to reset that because gravity will always tell you where down is,” Lander explains.
The robot is then deemed to be located at a point on the hull where the equivalent of the equator and the Greenwich meridian cross, which becomes its datum point, from which its subsequent movements are tracked.
“As we build the picture, the sonar – we use a Blueprint Oculus – is providing feedback on what it sees,” Lander says. “It is accurate enough to identify weld beads on the hull, anodes, thruster gratings and so on.”
These items are in known positions on the hull, contributing to the navigation solution, as are markings such as the Plimsoll line and depth indicators that the cameras can read, each of which acts like a signpost for the robot. “When it sees it the next time it can calculate how far away it is from a series of points, like taking a fix for dead reckoning,” he says.
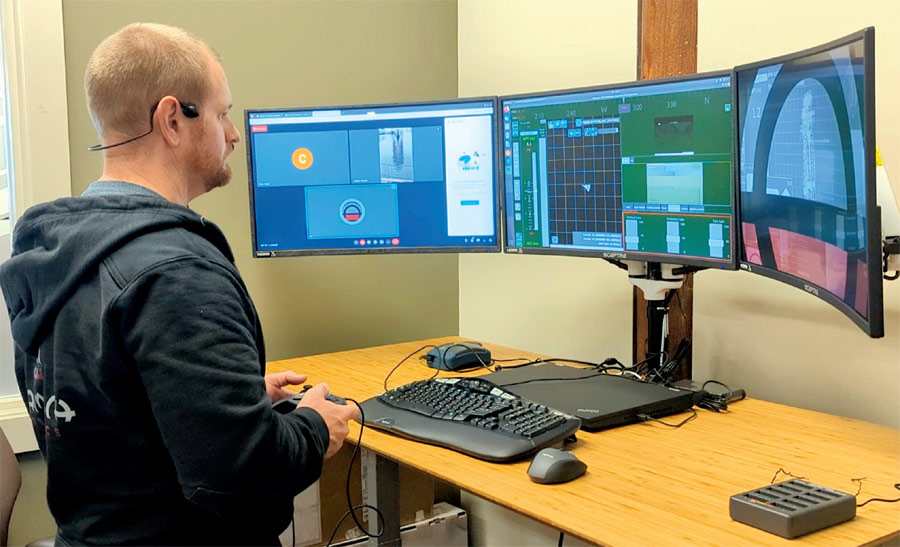
The HSR removes the micro-fouling using rotating brushes fitted with soft bristles, and is a purely mechanical process. Finding the best material for the brushes and optimising the design was an important part of the development effort, and is still subject to refinement. Much of that work was also done in cooperation with the FIT, Lander says.
“We developed our own design for the brush heads, focusing on how much independent movement they would need to adjust to the contours of the ship’s hull, and how much is reasonable to be able to build into a system to ensure good contact around a number of different surface shapes,” he says.
This involved finding the right combination of brush flexibility, head movement and number of brushes that work best on a robot of its size. “We have five brush heads on the vehicle, so each one has a bit of independent movement to handle some flex and curvature,” he says. “Since the vehicle is a metre long and two-thirds of a metre wide, there are complex shapes on a ship that we can’t yet crawl on, but for larger ships we can get onto probably 95-98% of the hull.”
Hull condition monitoring
The data on the hull’s condition is potentially as important for the ship’s operator as the cleaning, and consists mostly of location-referenced visual imagery, although sonar imagery is also collected. The imagery allows Armach to provide a detailed report documenting the pre- and post-cleaning conditions.
Processed using software developed in-house, the feedback data allows a variety of impending problems to be detected and identified before they become more serious and expensive to rectify. “We will be able to report on areas of excessive growth, coating failure, anode wear, and detect any other anomalies on the hull,” Lander says. “And we will be able to provide better comparisons between inspections.
“We also expect to add additional inspection capabilities to the HSR to allow for more detailed examinations that can support class inspections and help with pre-dry-dock maintenance planning.”
Efficiency drive
Efforts are continuing to improve the efficiency of the cleaning process and to make it faster, which are being embodied in a new and more easily manufacturable version of the HSR.
“We are going to have a slightly larger cleaning path, and the brush size has gone up a bit,” Lander says.
“We have been learning more about the relationship between brush size, bristle density and robot speed. There is a magic number of how many bristles should hit a spot per second, so even a 4 in difference in size on something that’s only 24 in wide makes it 15% faster, and that’s a big deal for the efficiency of a little robot on a big ship.”
Cleaning time is highly dependent on vessel size, but Armach aims to clean a 300 m cruise ship in 8 hours using multiple robots. Time in port is a major constraint for cleaning a cruise ship, he points out: “It’s only in for 8 hours and we don’t want to disrupt its schedule.”
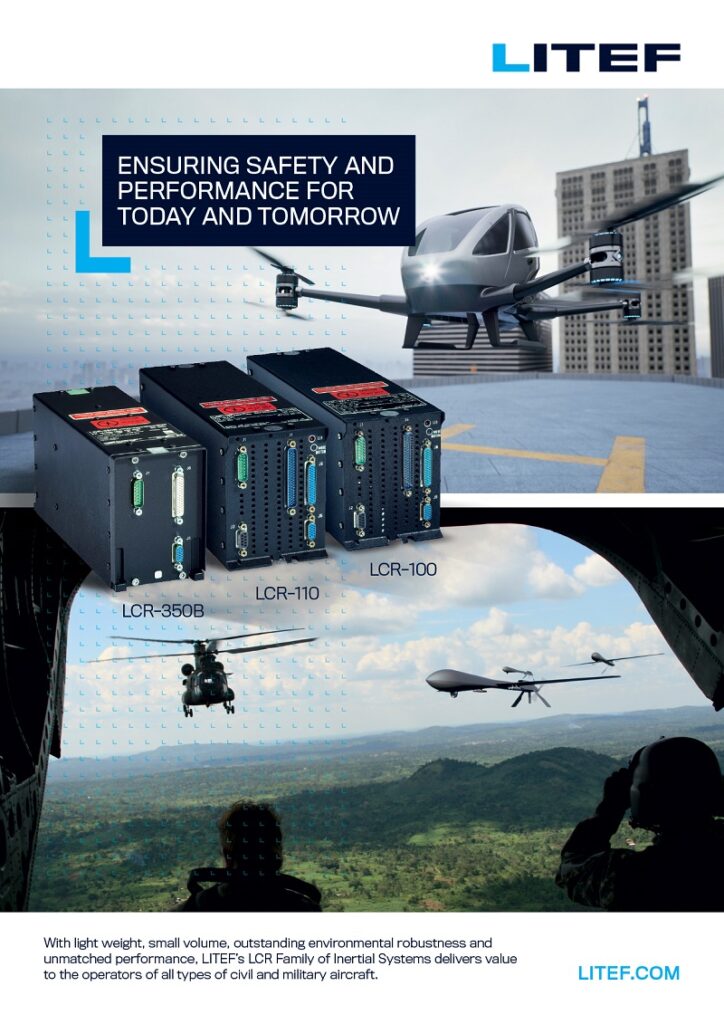
Frequency of cleaning is governed largely by a vessel’s operational profile, he notes. “Armach works with each vessel to determine the schedule in accordance with the vessel’s bio-fouling management plan.”
EverClean is offered as a subscription for an ‘always clean’ hull rather than single cleaning operations. “That said, costs are such that the fuel savings are more than enough to cover the costs,” Lander says.
While multiple robots can work on the same ship, it takes one or two people to operate each HSR. However, Lander says Armach is working towards allowing multiple robots to operate autonomously, with only one person providing oversight of them all.
Resident robots
Looking ahead, EverClean is moving towards installing HSRs aboard vessels as resident systems. They will need only minimal engagement from the ship’s crew, Lander says, as they will be overseen from a remote operations centre in the US.
“That will change the way we approach the operation, because it gives the robots more freedom to operate for longer periods. As we don’t face the issues that we would with a battery-powered robot, it’s not going to run out of power. Also, we can operate in the dark, so with a resident system and the vessel at anchor we can do the cleaning around the clock.”
This approach, he says, suits tankers and container ships, for example, that often sit at anchor for long periods waiting for a port to grant entry or for a pier space to become available.
Proactive cleaning is a big idea, Lander concludes. “Having clean ships sailing the ocean is a better long-term solution than allowing fouling to build up before cleaning them.”
Specifications
- Length: 1 m
- Width: about 66 cm
- Weight: 30 kg
- Propulsion through water: electric thrusters
- Propulsion on hull: electrically powered rubber tracks
- Power source: shoreside or shipboard generator through tether
- Control: manual ‘flying’ to hull and supervised autonomy Comms: 4G cellular or satellite link to Armach control centre
- Cleaning effectors: rotary brushes
Some key suppliers
- Autonomy and sensor data processing software: Greensea Systems
- Fibre optic gyro: Emcore (formerly KVH)
- Doppler Velocity Logger: Water Linked
- Multi-beam sonar: Blueprint
- Underwater camera: Sidus Solutions
UPCOMING EVENTS
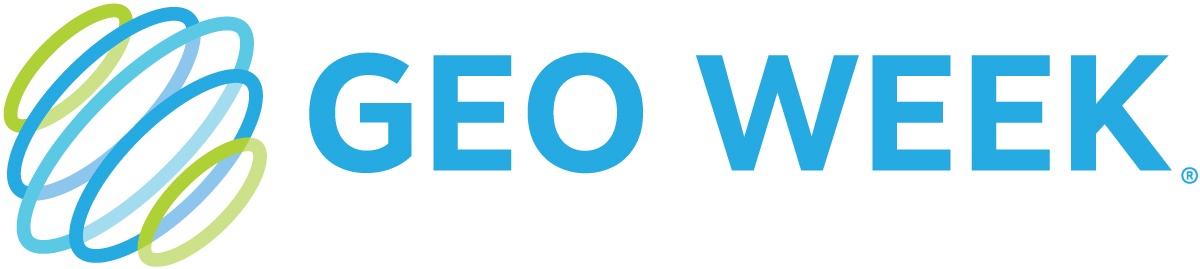
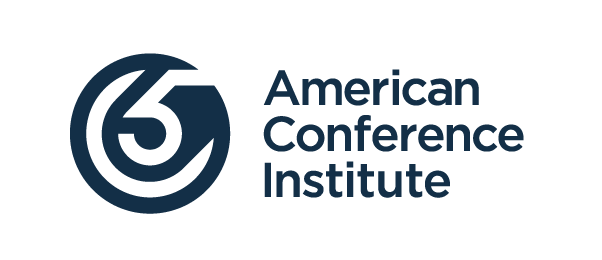
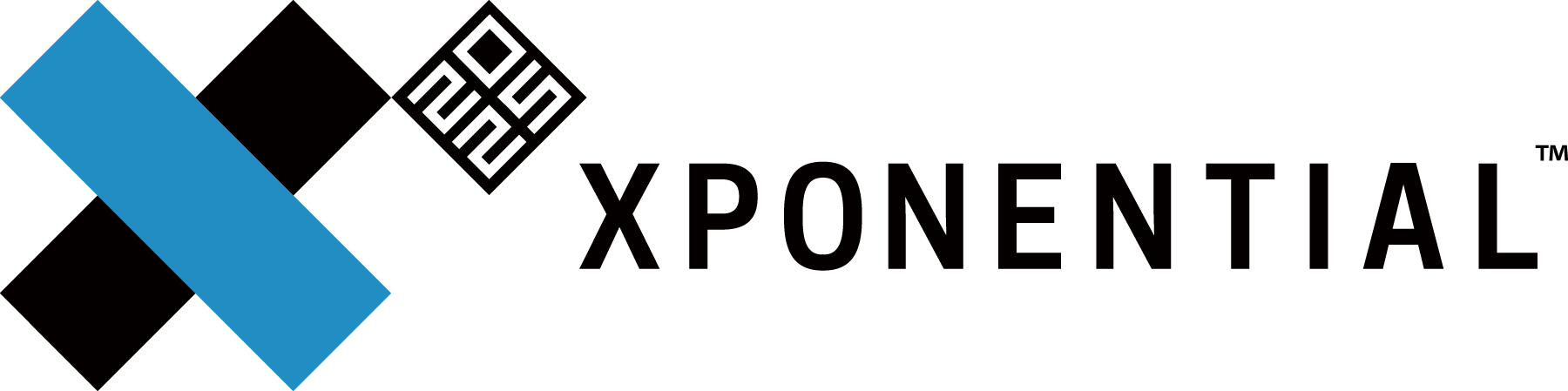
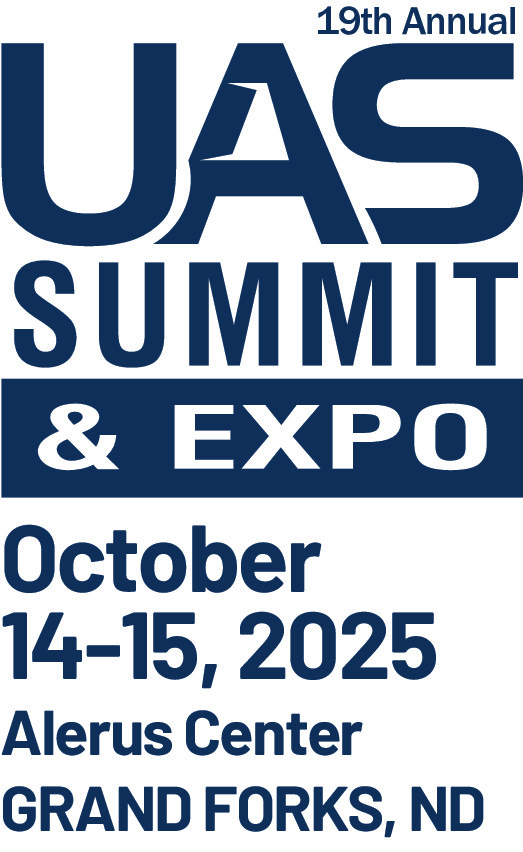
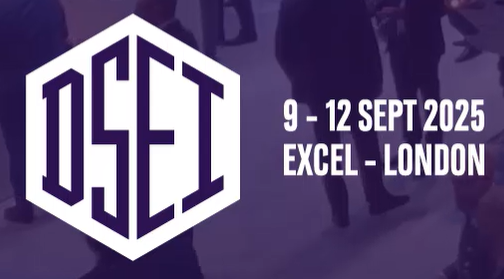
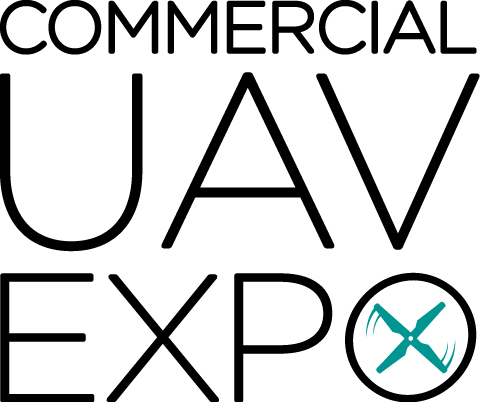
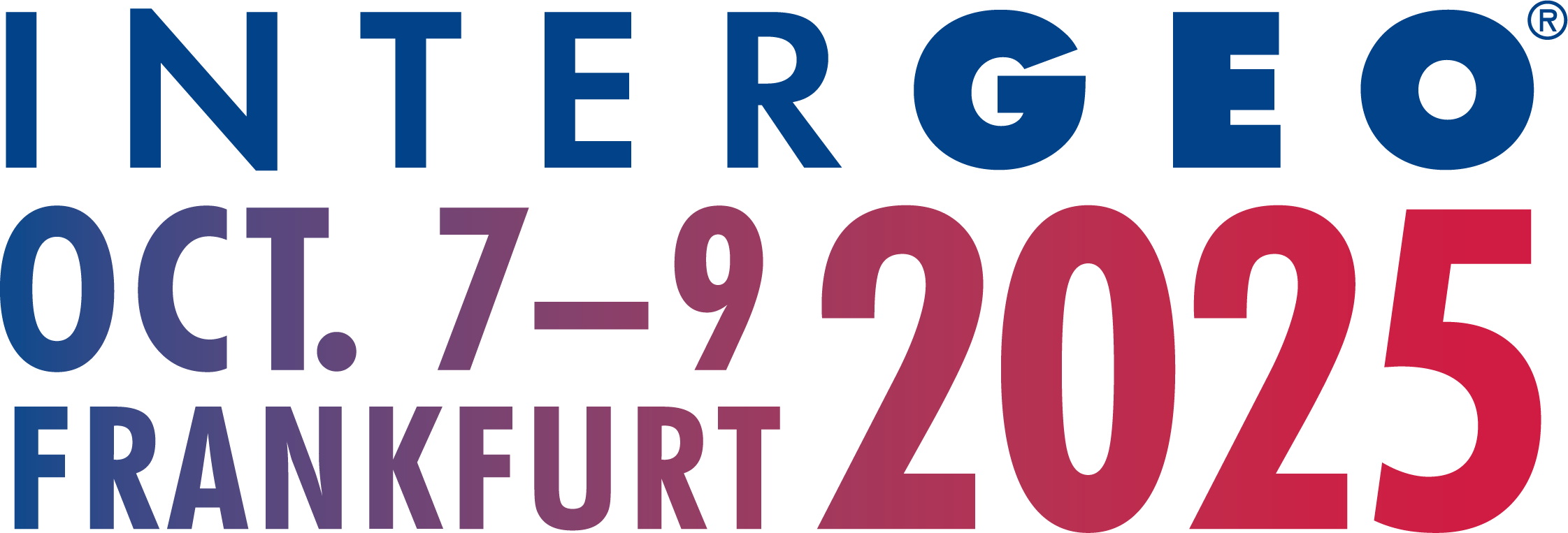
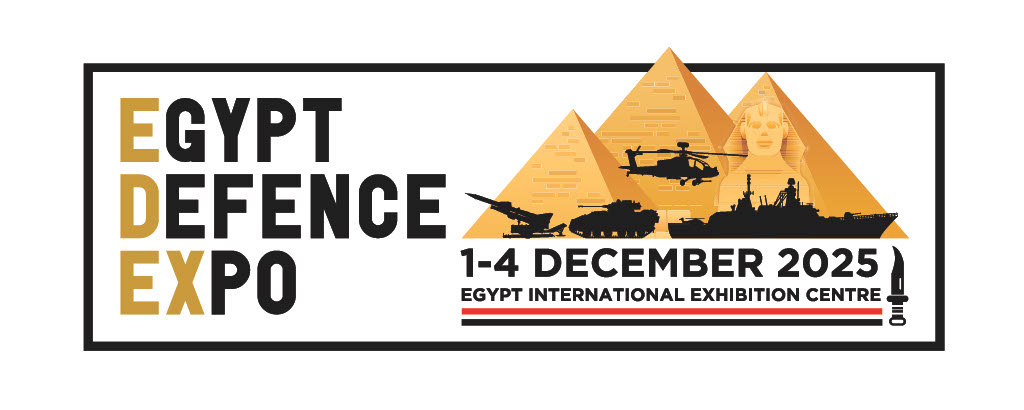
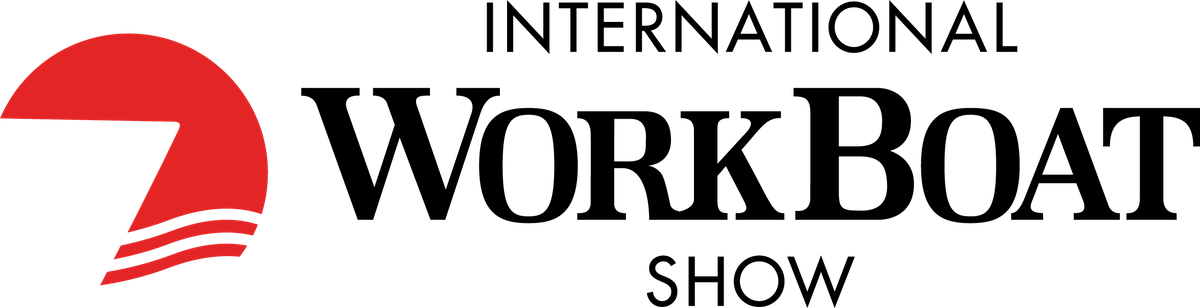
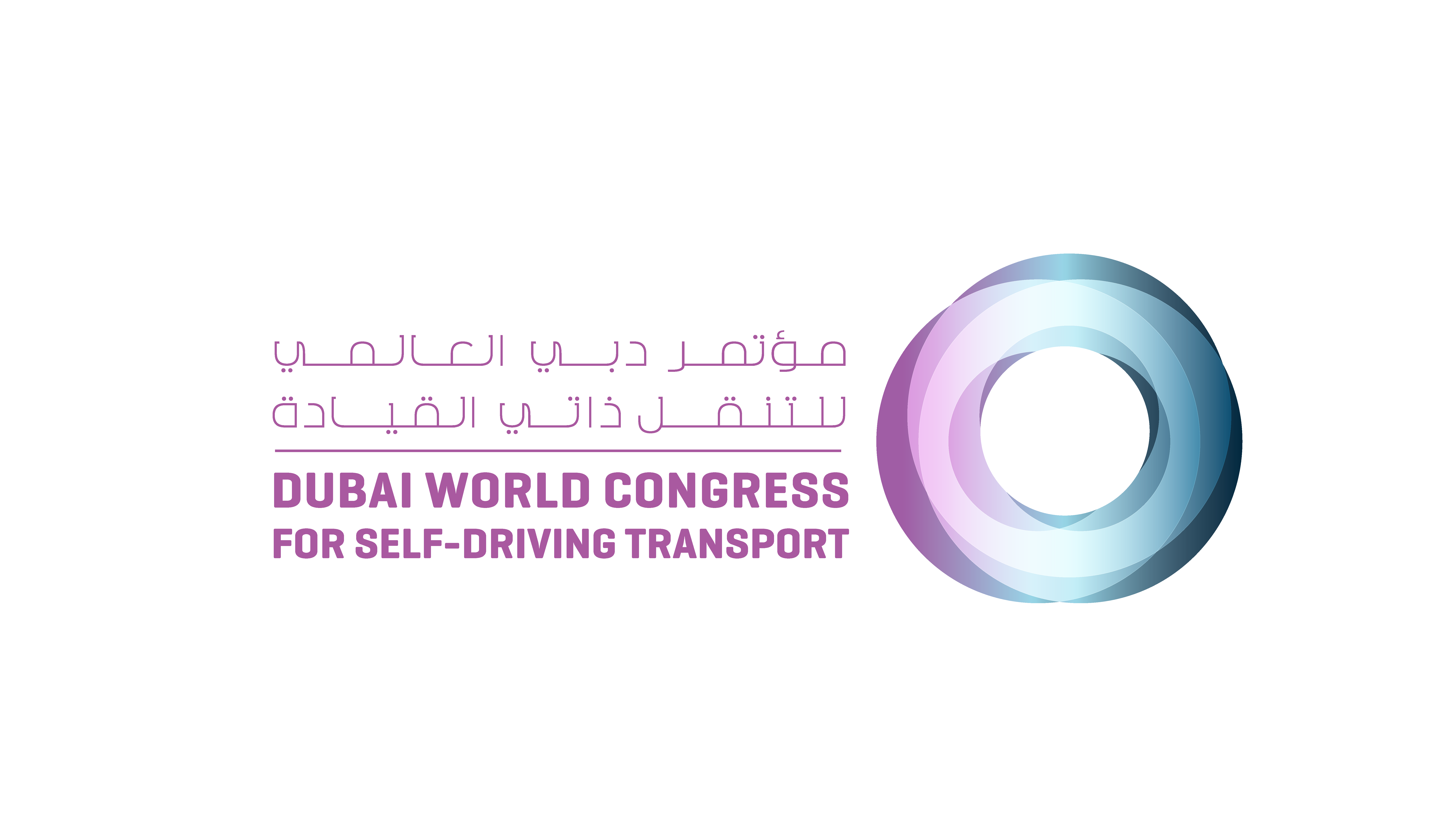
