Xponential 2023 part 2
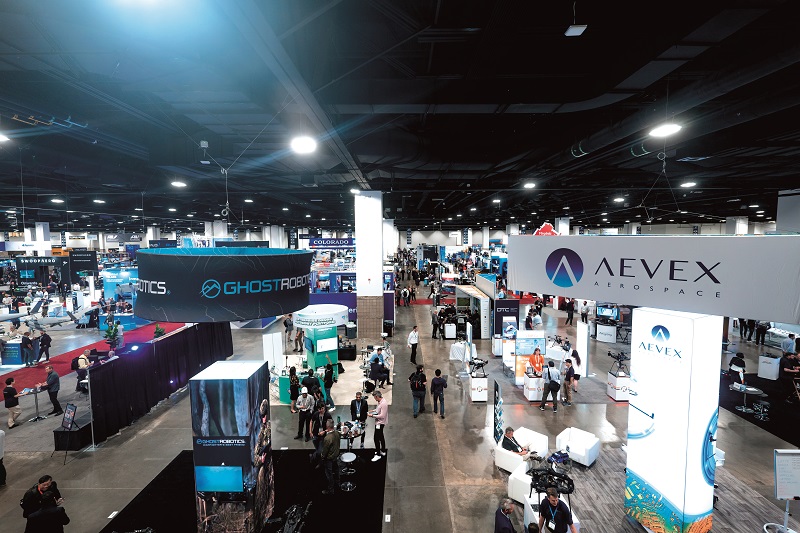
In the second part of our report on this show in Denver – the Mile-High City – Rory Jackson reports further on the uncrewed technologies that were on display
Going the extra mile
As many readers may recall, the Association for Uncrewed Vehicle Systems International (AUVSI) and Messe Dusseldorf North America (MDNA) jointly organised and produced the 50th anniversary edition of Xponential earlier this year in Denver from May 8 to 11.
The show was a grand return to scale and form following the impact of the Covid-19 pandemic on international trade shows and conferences. About 600 companies presented their latest products and services for autonomous and uncrewed vehicles across the expo floor, and around 7000 professionals engaged with the 3 days of the conference programme, the international attendance increasing by 65% compared with the 2022 show.
Such was the size of the exhibition and the number of solutions on display that we now bring you this second (and larger) part of our Xponential 2023 report, so that anyone who could not attend or could only briefly visit can catch up on some of the latest mission-critical updates from the uncrewed world.
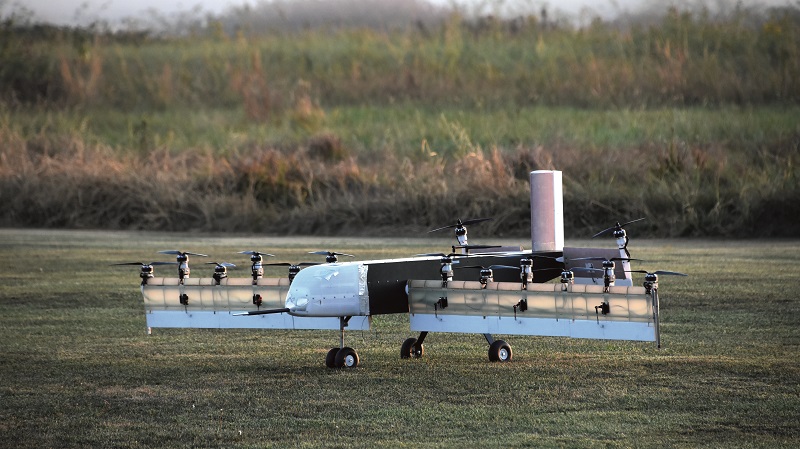
Although DARcorporation is not known for having a presence at trade expos, it attended Denver to show visitors its capabilities across propulsion system engineering, including propeller prototyping, acoustic optimisation, CFD analysis, structural FEA and vehicle design.
“One of our recent collaborations we’re discussing here is the Modular Air Vehicle Research Intelligent Kit [Mavrik], an SBIR project we did for NASA which wanted a modular aircraft that could be configured in many different ways but still be flown by the same autopilot controller,” explained Drew Darrah.
To that end, the company displayed its UAV demonstrator for that project at the show. In designing it, Darrah and his fellow engineers went with the most complicated configuration they could think of: a distributed propulsion arrangement with six electric propulsion motors on each wing and then two more on the tail, along with a tilting wing and tail VTOL-transition method reminiscent of the NASA Greased Lightning UAV demonstrator first flown in 2014.
“It has six control surfaces on the wing, three in the tail, and a nose gear, each of which has its own individual servo, then the tilting tail uses a linear actuator, and a car seat motor is used for the tilt wing, as that was the lightest, strongest option we could find,” Darrah noted.
The intended autopilot for the project did not arrive in time owing to a supplier-related delay, so to get the aircraft into flight testing, the team had to change to Ardupilot, which is not meant to be used with the Mavrik-type configuration. However, with some modifications, the team effectively ‘tricked’ the UAV into thinking and operating as if it had a quad-plane configuration.
“We’re now making our own custom flight controller to better optimise the in-depth design,” Darrah added. “We’ve just made a flying duct UAV for another project, and the key to that was creating a unique flight controller from a blank sheet, so that’s something we’re doing more and more.”
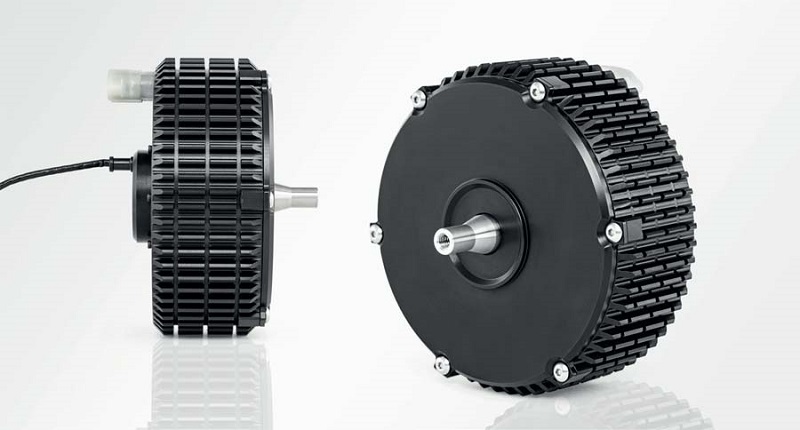
Plettenberg exhibited for the first time at Xponential, displaying a range of its electric motors, its Nova series of e-propulsion units attracting particular attention for potential integration in UAVs.
“There are eight motors in the Nova product line, starting from 1 kW for smaller UAVs and going up to about 50 kW for heavy UASs or advanced air mobility OEMs,” said Bastian Greiner.
“The Nova 15 is one of our top sellers, with 15-20 kW peak power depending on the length to which it is tailored,” he said. “We also have a close partnership with Mejzlik in supplying that system, which is critical because the efficiency of your UAV depends on the whole propulsion system – the right ESC matched to the right motor and the right propeller.”
The Novas are closed-housing inrunner BLDC motors, which Plettenberg noted are especially popular among UAS integrators for their ruggedness across different environments. Most of the motors are IP54-rated for dust protection and splash tolerance as a baseline, but the company customises its solutions for higher protection classes and other parameters on request.
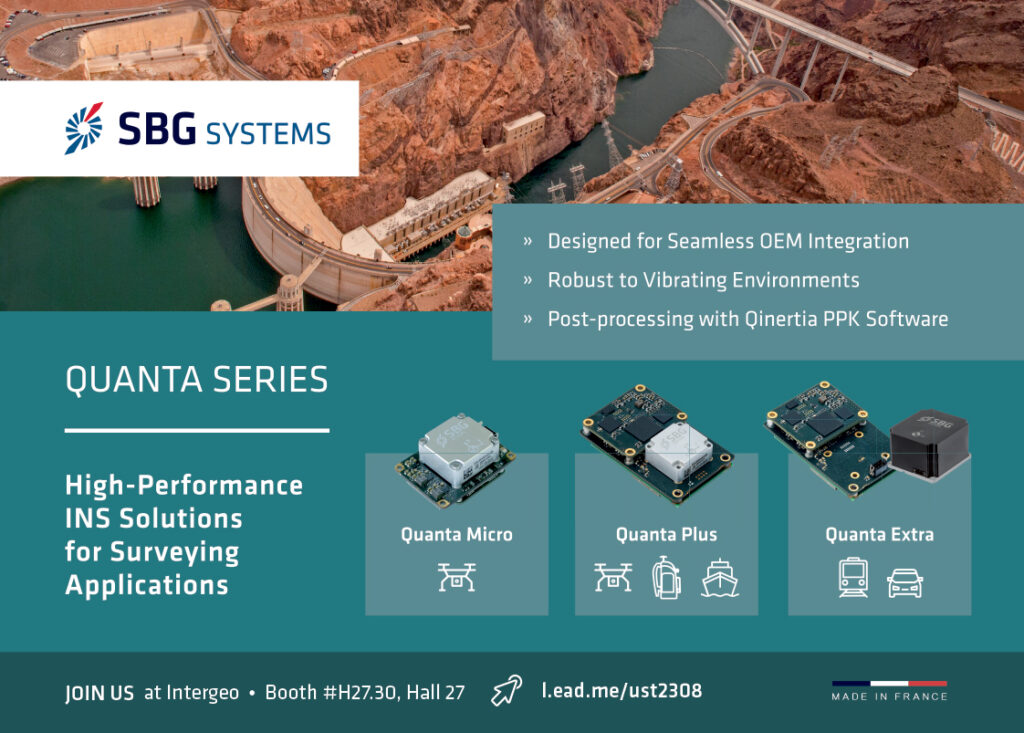
“As well as needing to cover different ranges and speeds, UAVs these days have all sorts of different battery voltages, hybrid systems, internal ambient temperatures and other upstream considerations that you need to look at in order to optimise the propulsion system,” Greiner noted. “With our tailored propulsion systems, we achieve the best trade-off for power to weight to robustness, while maximising efficiency over the entire load profile.”
Walking the aisles of the show was Armstrong Race Engineering (also known as Spintric Technologies), which specialises in fluid management systems. Although traditionally its customers have primarily been in motorsport, it has opened its doors to those in the uncrewed world, hence its presence at Xponential.
“We’ve been in racing for over 40 years, particularly making dry-sump oiling and fuel systems, and consequently aerospace integrators have been asking us increasingly over the past several years to design things like special pumps, de-aerators or air-oil separators for their engines or for hydraulics systems used in aircraft,” explained Gary Armstrong.
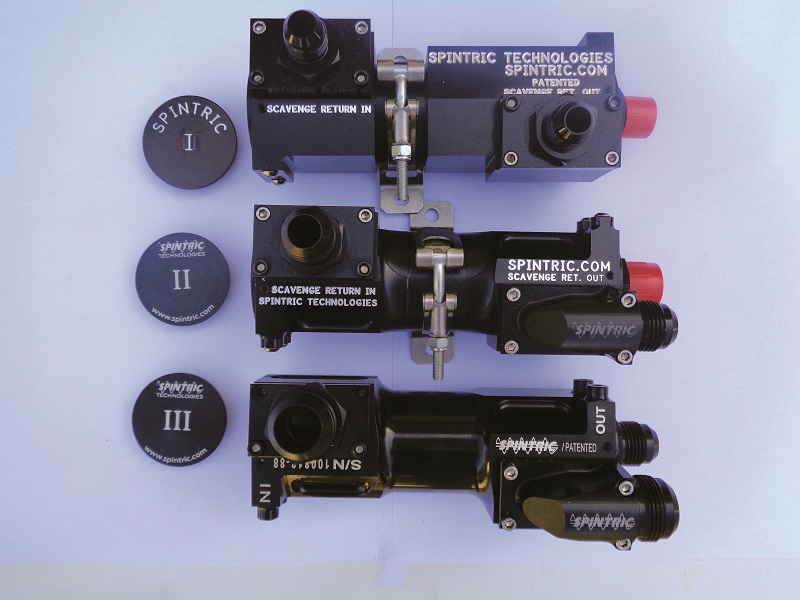
“There are a lot of similarities between race and UAV engines in terms of the power demands and duty cycles required of them and the safety needed from them, and we pretty much always do our custom work from blank sheets to produce an optimised solution from the ground up, so we anticipate being able to supply systems that fit UAVs’ tight constraints on things like weight, reliability and mechanical efficiency.”
As an example of this reliability, Spintric’s air-oil separator has no moving parts that might represent possible failure points. The separator works by way of internal centrifugal forces generated by the separator’s interior channel’s shape, cavities, port and undulating manifold, and relief ports, which force air out of the oil before it enters the tank. The separator can be integrated anywhere in the return line of the scavenge oil.
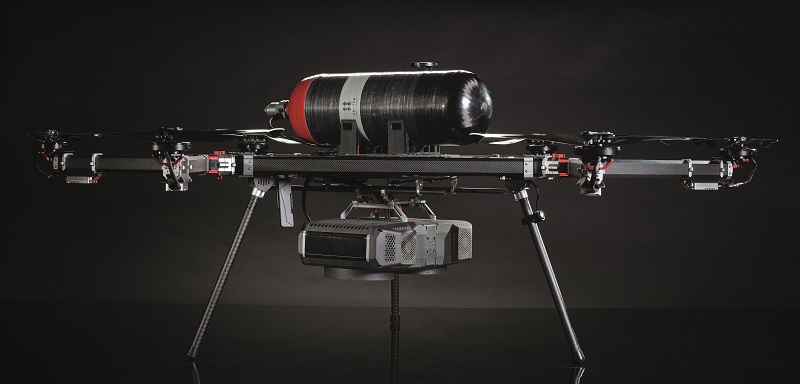
Intelligent Energy was on hand to discuss its ongoing work with Cyberhawk, a provider of UAV-based inspection services and data analytics for the supply of its hydrogen fuel cells to the latter’s UAV fleet.
“We have three products,” said Andy Kelly. “Our 800 W and 1.2 kW fuel cell units are typically meant for fixed-wing UAVs, and then our 2.4 kW cell is aimed at heavier commercial inspection UAVs, particularly multi-rotors carrying out linear inspections of power lines, pipelines and offshore wind, oil and gas.
“These applications are what Cyberhawk are targeting with their fuel cell drones. At present we have several hundred units in the field across our end-users.
“The extra endurance range enabled by the 2.4 kW fuel cell is key to their multi-rotors. If you only want to survey something a mile away, you don’t need a fuel cell, but if you’re surveying a
300 km pipeline, the capability of flying in the region of 150 km per flight is critical if you want to be able to survey pipelines with drones cost-effectively.”
Cyberhawk’s data collection typically comes from the use of state-of-the-art cameras and Lidars, both of which are normally heavier payloads than industry-standard ones, reducing flight time. Cyberhawk’s UAV has a 7 kg payload capacity enabled by the high power output from the fuel cell, which is critical to Cyberhawk’s commercial services. Kelly noted here that the low mass of hydrogen means enough fuel could typically be stored for flights lasting 2-3 hours with such payloads.
The 2.4 kW product is designated the IE-Soar 2.4. It weighs 4.8 kg, outputs power at between 50 and 70 V, operates in environmental temperatures between -5 and +40 oC, and at altitudes up to 3000 m (although this can be customised depending on an end-user’s power requirements).
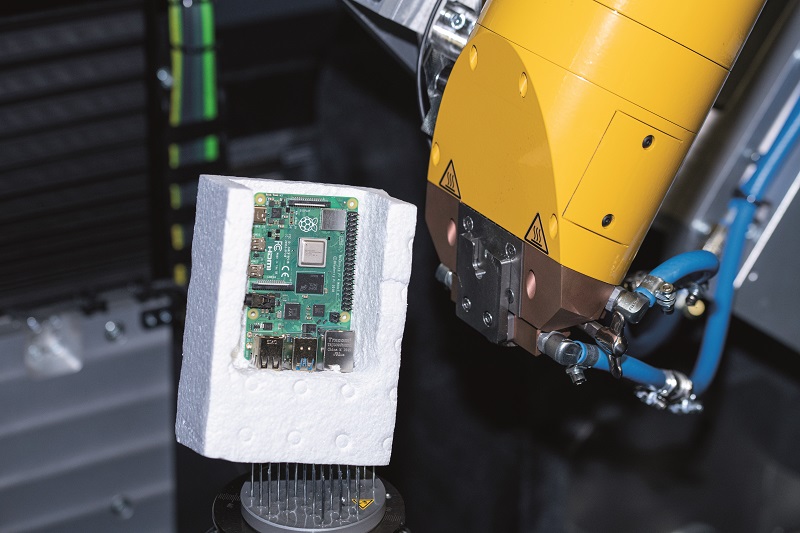
MaXerial has developed an AI-powered solution for maintenance and inspection of vehicle components by which fleet managers can track the health and lifespan of their platforms and components.
“We use X-ray computed tomography to scan through technical objects, taking about 2000 projections to reconstruct them with a quantitative volume in micrometre resolution,” explained Dr Roger Herger. “That allows you to measure minute things like crimp contacts, solder joint integrity, and ball grid arrays – or check their locations to see if the device has been assembled correctly.
“Our process is non-destructive, so if technicians take a subsystem from a UAV that failed during operations, they don’t necessarily have to disassemble the part to do a post-mortem on it.”
The display at maXerial’s stand showed a demonstration of an embedded computer being X-ray scanned and reconstructed, although Herger added that engine crankshafts, bearings, servo actuators, carbon composite hulls and many other parts can be checked using its X-ray tomography.
A high-quality scan is expected to take 30-60 minutes, but it be accelerated for quality assurance in production, including the use of the company’s own de-noising algorithm applied during post-processing for clearer reconstruction.
“Behind this is our AI product, the 1-click AI trainer, which we offer for AI engineers who need to retrain their image data analytics models,” Herger added. “With one click, end-users can apply our machine learning routines to their AI models. Our solution trains them, then runs tests with them and interprets if their quantitative analyses have improved.”
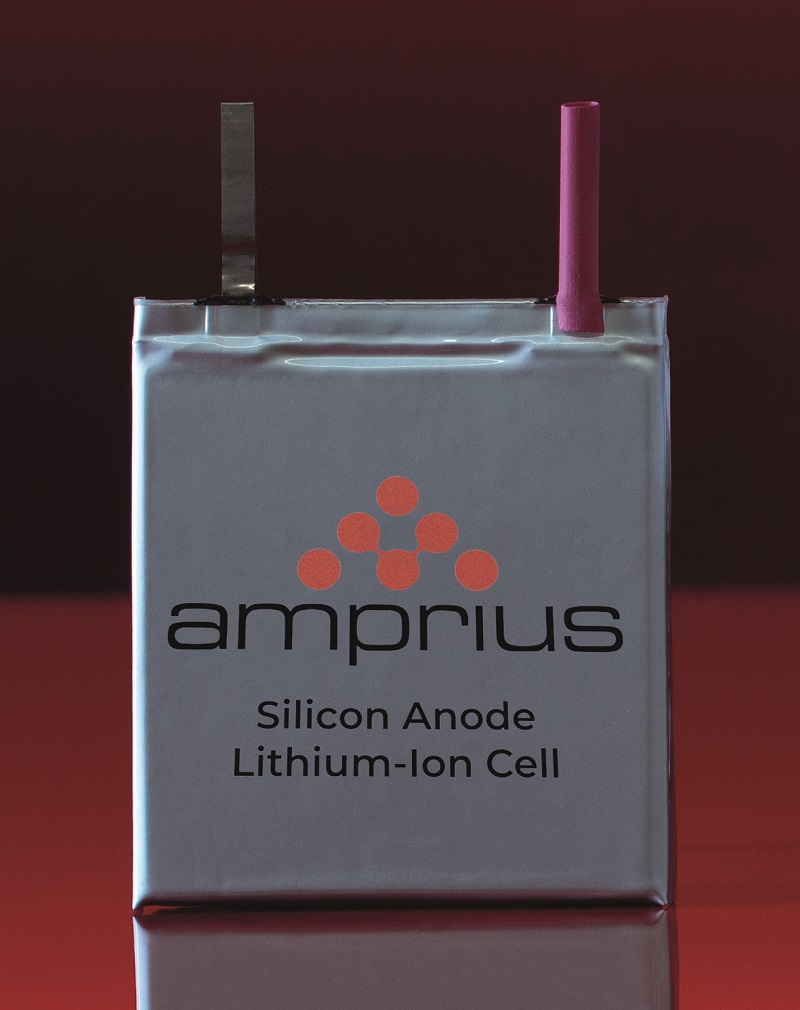
Amprius drew particular attention at the show for presenting its newest grade of lithium-ion batteries, one of which can store 500 Wh/kg. The cells, which have been validated by independent test lab Mobile Power Solutions, set a new bar for gravimetric energy density, Amprius said, and it is working with key customers to provide cell prototypes.
“That said, we’re able to manufacture and ship 450 Wh/kg cells at the moment,” said Erik Vaknine. “The key enabling technology behind our energy density is our silicon nanowire anode; the cathode and electrolyte are quite typical of lithium polymer and lithium-ion cells.”
The company customises its cells to maximise the energy density or power density for a particular application, and noted that the 500 Wh/kg cell will probably be supplied for integration in platforms where high discharge rates and long-cycle lifespans are not critical requirements.
“Although our technology is improving all the time, there are trade-offs depending on customer requirements. Someone wanting ultra-high energy density for example will need to be okay with sacrificing other characteristics, like discharge rates: you might need thicker electrode layers and other inert materials to enable higher power,” Vaknine said.
“As our roadmap progresses, we’ll continue to make advances in developing new platforms for high-power and high-energy cells that would surpass our current levels of performance.”
Unitree Robotics was performing demonstrations of its quadruped robot technologies, including its latest system, the B1, which is designed as an industrial-grade system for a range of routine or potentially dangerous applications.
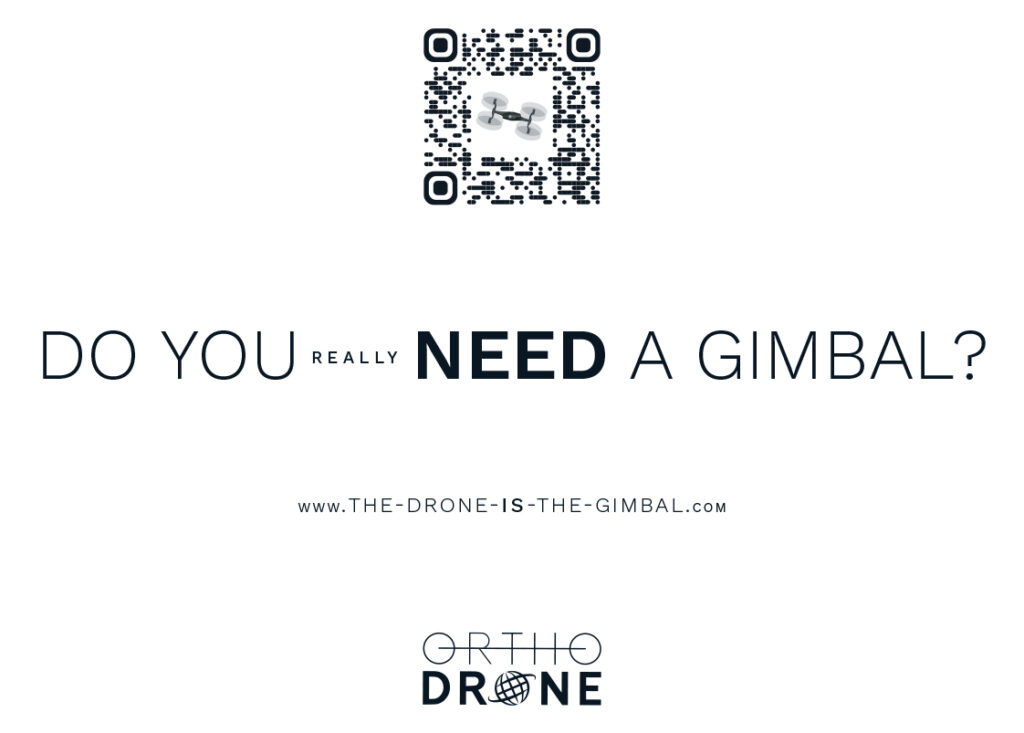
“Our company founder studied at Shanghai University, where he developed the Xdog1, a prototype which later became the first generation of our quadruped robots,” Tony Yang told us.
“In 2019, we started building the Aliengo, our first industrial-grade robot, then in 2020 came the A1 robot for educational and research purposes. Although that is now discontinued in favour of the much smaller Go1, which we launched in 2021; the B1 was also unveiled that year.”
The B1 measures 1126 x 467 x 636 mm when standing, and weighs 50 kg in total, including its battery pack (which weighs about 5 kg). It can carry up to 20 kg when walking, and technically up to 80 kg if only required to stand still. Its maximum endurance is 5 hours if it’s standing without a payload, or up to 2 hours with continuous walking.
“The B1 can do indoor inspections of industrial facilities like oil & gas installations or power stations,” Yang explained. “For this it can carry Lidars, robotic arms, thermal imagers, microphones and speakers.
“In addition, our AI-powered visual recognition camera can detect objects to collect data on them, and that data can be delivered to the local operations centre in real time. If needed, operators can also control the robotic arm remotely, if it’s integrated on the B, for emergency situations such as switching off a valve or other device.”
The robot B1 can also be deployed for fire safety and rescue operations, using sensors such as thermal imagers and gas detectors to scout around or get close to burning buildings, or go inside of buildings where a fire seems to have been quenched but not yet deemed safe for humans to enter. The B1 can hence survey for survivors, the presence of poisonous gases, fire or other problems that can determine whether human rescue workers can proceed.
The Go1 meanwhile comes in three versions, the Go1 Air, Pro, and Edu. The Go1 Air and Pro are consumer and retail-oriented solutions, capable of carrying 4 kg of payload each, but with much reduced programming capabilities than the Edu. This is the education and research variation, and has interfaces for scientific programming, Python coding, 2D or 3D radar, and 4G among other subsystems.
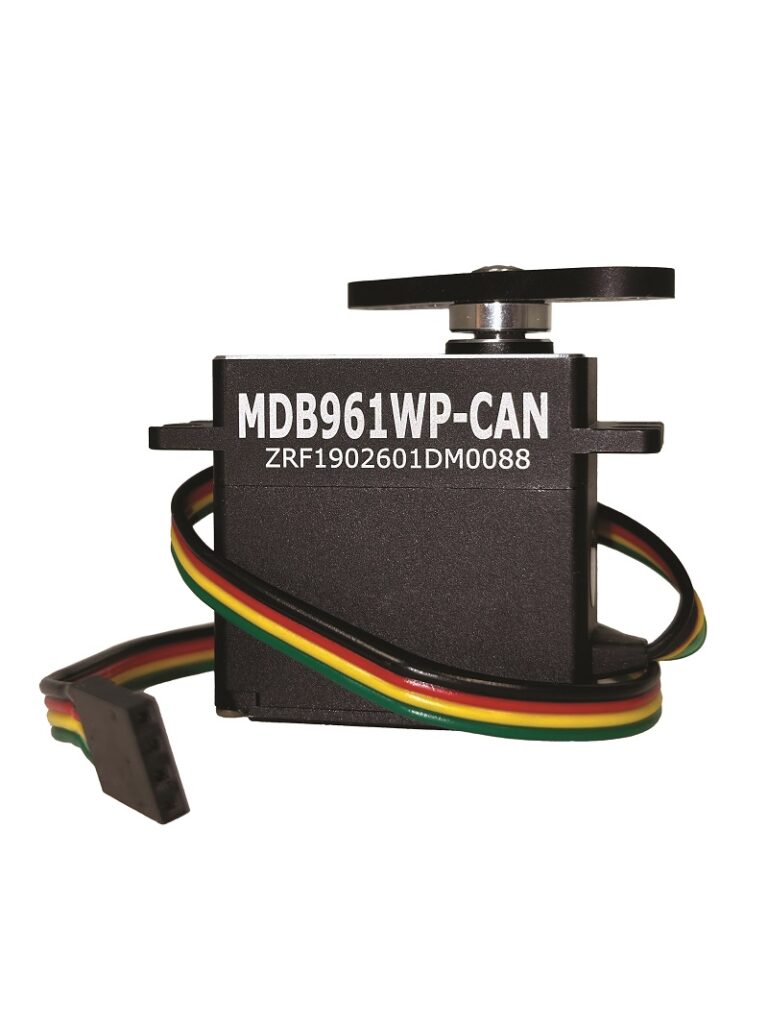
Hitec displayed several new servo actuators. First was its SG10BL-DroneCAN/CAN, which is part of the company’s SG series of industrial-grade actuators; at the time of writing, it was due to enter production shortly.
“The SG10BL runs on a CAN protocol to enable detailed feedback and real-time MTBF information, and is Mil-Spec rated for ruggedisation,” said Shawn Spiker. “It’ll be the smallest of the series but with similar long-life brushless DC motors and other components selected for durability, running on power inputs of up to 15 V DC.”
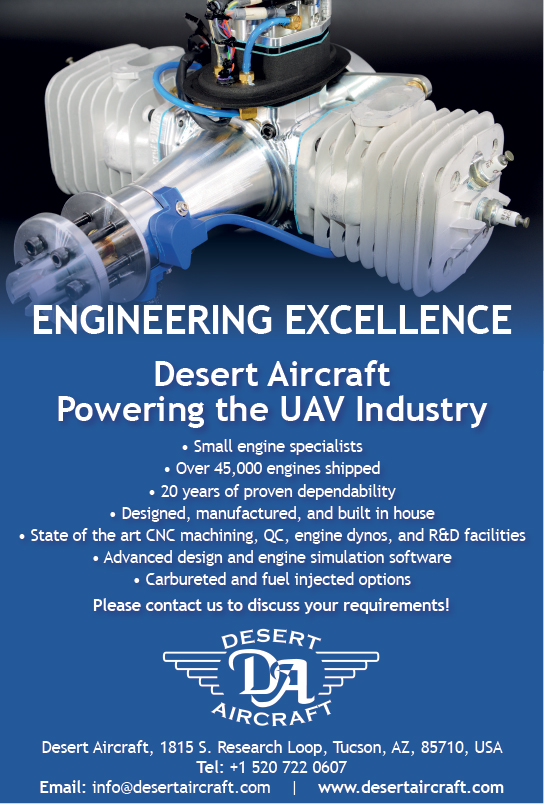
Also on display was the SG15BL-DroneCAN/CAN, the next size up in the series from the SG10BL, and already in production. The system runs using similar components, protocols and power input as the SG10BL, but has a 15 mm diameter, hence its product designation.
“Above that is the SG20,” Spiker added “Its 20 mm size is quite standard for hobby servos but it’s much more powerful than those, with an aluminium case and two versions, one running on 15 V DC, the other on 32 V DC.
“Lastly, our newest system on the market, the MDB961WP, is waterproof to IP67. It can run on 8-32 V, incorporate CAN or DroneCAN, and produce up to 60 kg of force per metre.
“It also has a new gear case design, with hardened steel gears, enabling the actuator to spread out its loads and withstand greater axial and radial forces, making for a much more durable and long-lasting servo than our past products.
“We’ve been testing it for 8 months, and some of our customers who are also running tests on it are getting up to 5000 hours of continuous operation out of them – over five times the lifespan of our previous generation of servos.”
The company also showcased low-profile versions of the MDB961WP, the MDB777 and MDB778. These also feature hardened steel gears, aluminium casings and IP67 ratings, with their MTBFs likely to be similarly close (although inevitably they will be slightly lower as a function of their smaller sizes).
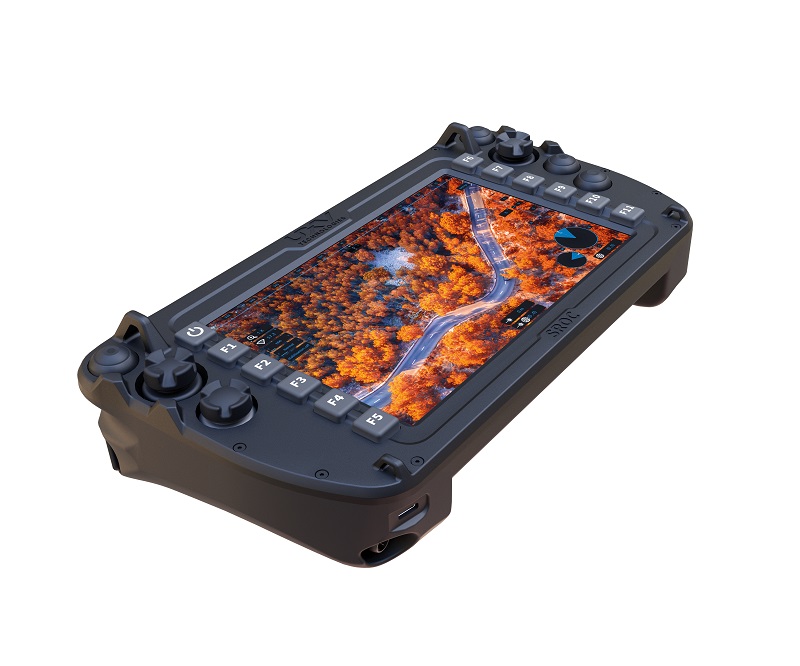
UXV Technologies showed the Soldier Robotic Controller (SRoC), its new GCS solution which has been BlueUAS-approved and designed to serve as a standard (non-customisable) handheld device for operators of uncrewed systems in defence operations.
“The SRoC is based around the Panasonic FZ-S1 tablet, so it’s an Android device, and we’re developing it in collaboration with other companies through a procurement by the US Defence Innovation Unit,” commented Simon Vestergaard.
“A key element of the SRoC is its compatibility with our Swappable Radio Modules [SRM] ecosystem. It is not limited to a single system, so you can swap SRM radios in and out of the SRoC in the field as desired using a simple tool-free click-fit into place.
“It also means the GCS works with almost any kind of radio, including those from Persistent Systems, Silvus, Microhard, Doodle Labs and TrellisWare.
“It used to be that, depending on whatever GCS you were using, you were forced to use the radio that came with it from the factory,” Vestergaard added. “With the SRM ecosystem you can easily change radios to get different frequencies, power outputs, modulations, encryptions and other parameters to suit your mission needs.”
The SRoC has a 7 in screen, weighs 950 g and measures 256 x 140 x 66 mm. Alongside the SRM dock, it includes a USB-C connector and one Nett Warrior connector. It also incorporates two swappable battery module docks, as well as an array of joysticks and buttons to prevent any mistakes from touchscreen use.
The standard GCS is available to buy now, and the first batch of SRoCs has already been shipped to customers.
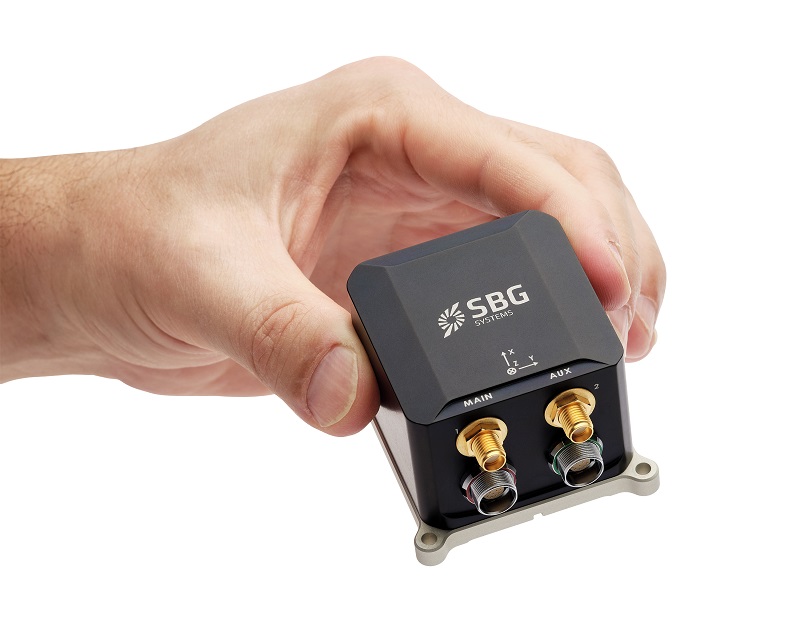
SBG Systems displayed its new Ekinox Micro INS for the first time, having announced the product only a week before the show. It comes with a tactical-grade IMU designed for a compact footprint, hence its name.
“The INS embeds a dual-antenna GNSS receiver, enabling its use even in low dynamic conditions, and making it optimal for navigation in large uncrewed systems,” said Yoann Plenet.
“It’s a rugged system, qualified to military-level standards such as Mil-Std 810 for shocks and vibration, Mil-Std 1275 for the power supply, and Mil-Std 461 for EMC and EMI protection, so it can be used with all kinds of carriers. But even with these military qualifications it’s still ITAR-free, so there are no restrictions on its import and export.”
The company has developed algorithms for enhanced detection and rejection of GNSS jamming and spoofing, enabling it to switch to use inertial readings instead of GNSS when the latter becomes hazardous to rely on.
Its navigation systems are also being updated for integrating wider selections of sensors such as pitot tubes, barometers, or magnetometers for mitigating magnetic influences on navigation data.
“The target with these extra integration capabilities is to help UAVs continue navigating for several minutes – and marine uncrewed systems for even longer because of their lower speed – without GNSS, such as in challenging or jammed environments,” Plenet explained.
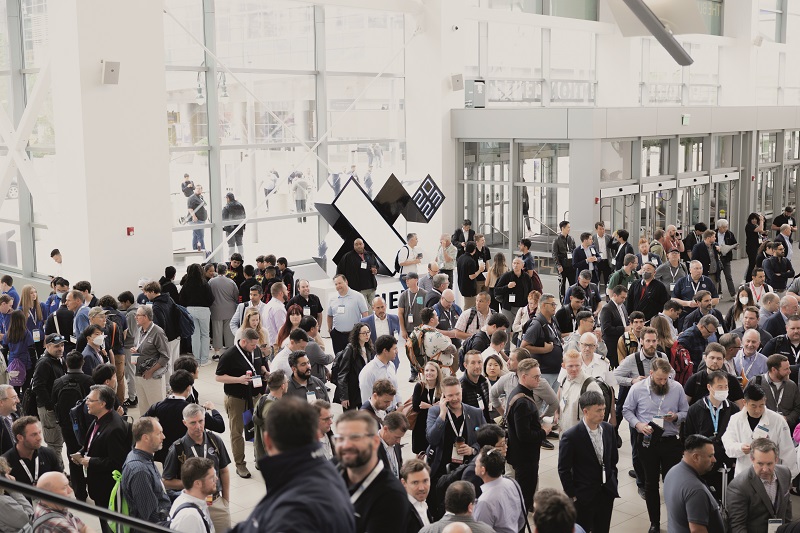
Spleenlab exhibited in Denver to promote its machine learning (ML) and AI solutions for use across different vehicles and platforms.
“We have shown good performance from our ML and AI products on board UAVs where there’s often a limited footprint for computer hardware and hence processing power,” said Jan Hartmann.
“Recent tests show that the functions of our Visionairy AI perception software require only 40-50% of the total computational power, which means there is a large margin to run many more embedded AI applications on the same system.”
Spleenlab is also partnering with companies including DroneUp, Quantum Systems, Apex.AI, Auterion and Blickfield, which are developing new hardware and software solutions that Spleenlab cites as ideal platforms for powering wider ranges of AI functions.
Visionairy can be used on autonomous aircraft or road vehicles for visual navigation, sensor fusion, 3D SLAM and functional safety,” Hartmann said. “For UAVs in particular it can enable gimbal tracking of moving targets under severe environmental conditions, real-time inspection analytics or safe flights without needing GNSS.”
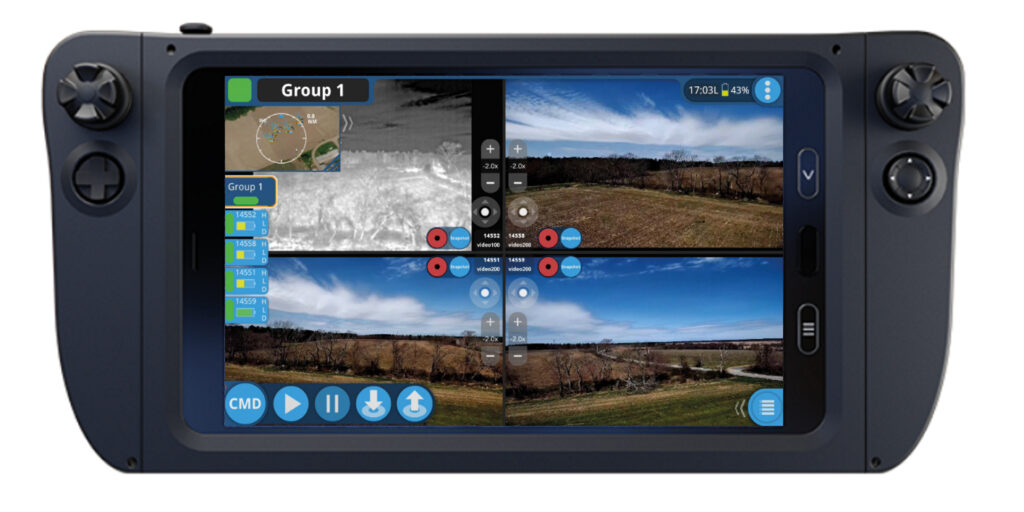
Autonodyne attended the expo to discuss the latest capabilities of its GCS software, developed to enable control of different autonomous vehicles simultaneously across varying domains by a single operator and console.
“Our solution allows an operator to draw a circle around five to 20 vehicles and give them a task to coordinate as a group, such as surveilling a target, rendering a building or following a vehicle,” explained Matthew Paddock.
“We can also go into more complex automated operations, for instance having vehicles change over when their batteries are low, or autonomously reinforcing each other in risky situations.”
The company focuses principally on software for GCSs rather than hardware. Its solutions can be run on Windows or Android devices, and are largely agnostic regarding computer hardware, data links and vehicle architectures.
“We do go through an integration process with new vehicles though, and we’re compatible with most key BlueUAS systems such as those from Skydio, Vantage, the Ascent AeroSystems Spirit and the Harris HX6,” Paddock added. “At the larger end, we’ve flown General Atomics MQ9s and MQ20s as well as Kratos’ XQ-58 in a pilot and safety-pilot interfacing capacity.
“We’re also exploring new integrations in the maritime domain. There are so many more USV manufacturers now than 5 years ago, so it’s exciting to see how maritime swarms can be shaped and engineered through our system.”
In addition, Autonodyne’s latest software release includes an AI-powered capability for rotating ISR, in which four uncrewed assets can sit on the ground near a target, taking it in turns to launch, observe and return to base when nearing energy depletion, to enable persistent surveillance. Through the GCS, the end-user can watch all four vehicles’ camera feeds at once, or just that of the active observer.
“We’re also now announcing a hand-off capability from one GCS to another, so that one operator can request control of a vehicle, and the other can approve or deny the transfer from their interface,” Paddock noted. “We’ve designed the algorithms for quick, low-latency comms and transfer, as that’s really important to teams working in the field.”
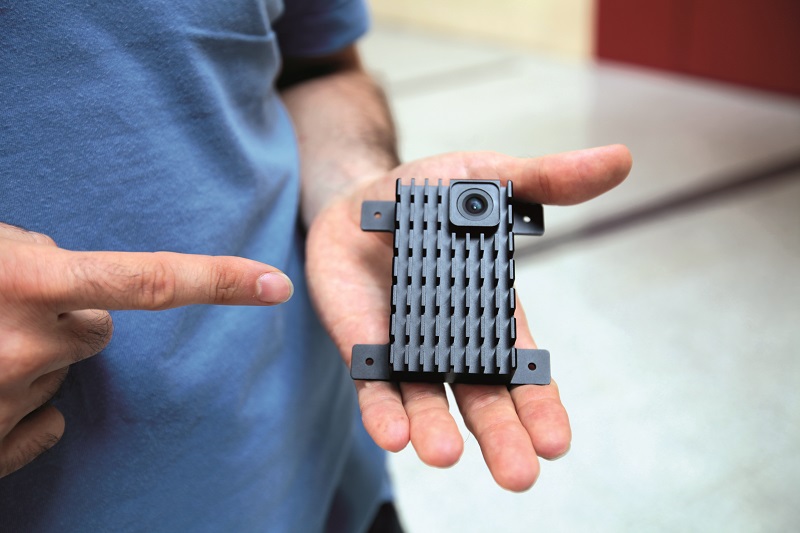
UAV Navigation-Grupo Oesia has continued work on its visual navigation system, the VNS01, which it last discussed with us in issue 32 (June/July 2020).
“We’ve been heavily focused on improving our GNSS-denied navigation capabilities,” said Carlos Lazaro. “Our Vector autopilot would theoretically experience drift at a rate of up to 35 m/minute without GNSS, but with the VNS product we can reduce that to almost zero.”
As its name suggests, the VNS01 is a vision-based navigation correction system. It weighs 100 g, features CAN 2.0, serial RS-232 and Ethernet interfaces, and consumes up to 5 W from a 12 V supply. Its configuration includes a camera pointed downwards from a UAV to identify specific points of terrain to use as visual flow references and hence a means of self-geolocation for the aircraft.
“That means that if the UAV’s GNSS is spoofed or jammed, it can use the visual markers and keep tracking its latitude and longitude with good accuracy,” Lazaro said.
“The VNS01 module is built around the most suitable camera for the necessary rate and resolution of image input, with embedded software for visual odometry and pattern recognition, and streamlined to minimise the necessary hardware. You integrate it into the underbelly of your UAV and connect it to the autopilot – it’s essentially plug and play.”
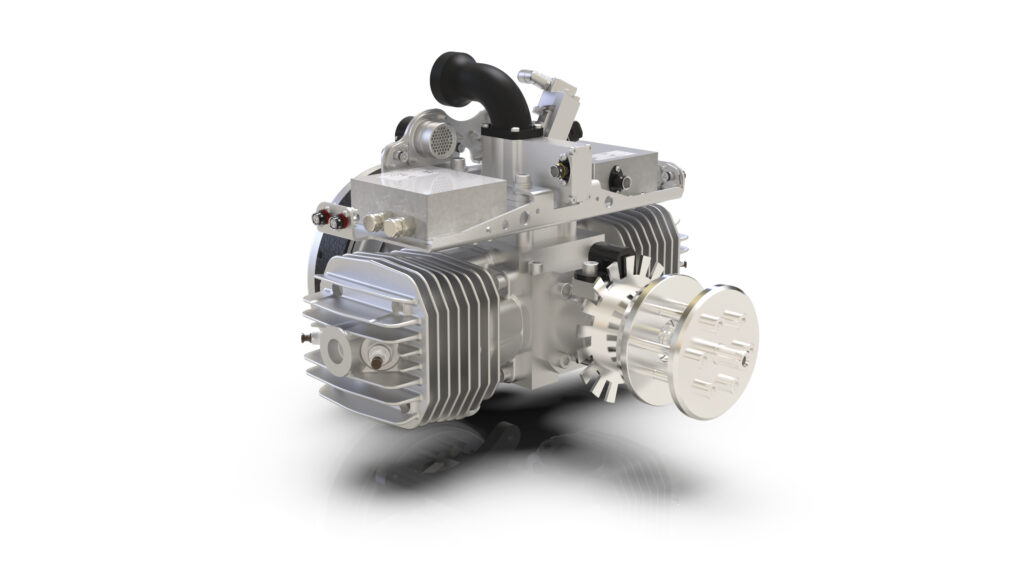
In addition to displaying its range of piston and Wankel engines, Sky Power announced that it has increased the power output of its SP-210 FI TS.
“We optimised the whole injection system without incurring any weight increase, paying particular attention to the throttle valve,” said Karsten Schudt. “We then completely changed the exhaust system to maintain back-pressure, and also did a complete re-mapping.
“We did the modifications on a broken-in engine unit, and increased the power from 11 kW to 14 kW at peak output. Given the scale of the increase, we’ll be applying the upgrade as prudently as possible across the rest of our engines, and look at how much we can recreate the power enhancement.”
The SP-210 FI TS is a two-cylinder, two-stroke boxer engine displacing 210 cc. It is air-cooled and naturally aspirated, and lubricated on 2% two-stroke oil pre-mixed with its fuel; its crankshaft runs in four ball bearings. The engine can also be fitted with a starter/generator.
Greenjets attended Xponential for the first time to exhibit and discuss its shrouded electric turbofan thrusters for UAV applications, in particular its first product the ipm5, which generates 5 kg of thrust.
“If you look across the UAV industry and its electric propulsion systems, it’s effectively all e-motors and propellers, but problems with propellers include the safety concerns of their exposed blades, and the noise from them and their tip speeds,” commented Darren James.
“Our propulsors are designed and optimised to be safe and quiet, as well as efficient. Fixed-pitch propellers are great for producing thrust at one condition, but our solution does so over a much wider speed range, with the duct, static structures and fan all optimised for thrust generation from take-off to cruise.”
The ipm5 weighs 750 g and is 200 mm in diameter. The company was spun out from Blue Bear Systems Research in 2022, with its staff coming largely from Rolls-Royce, Cosworth and other organisations with extensive experience and capabilities in CFD and turbomachinery.
“That experience went into the fine-tuning of geometric tolerances, materials and control of this solution, along with the larger products we have in development,” James added.
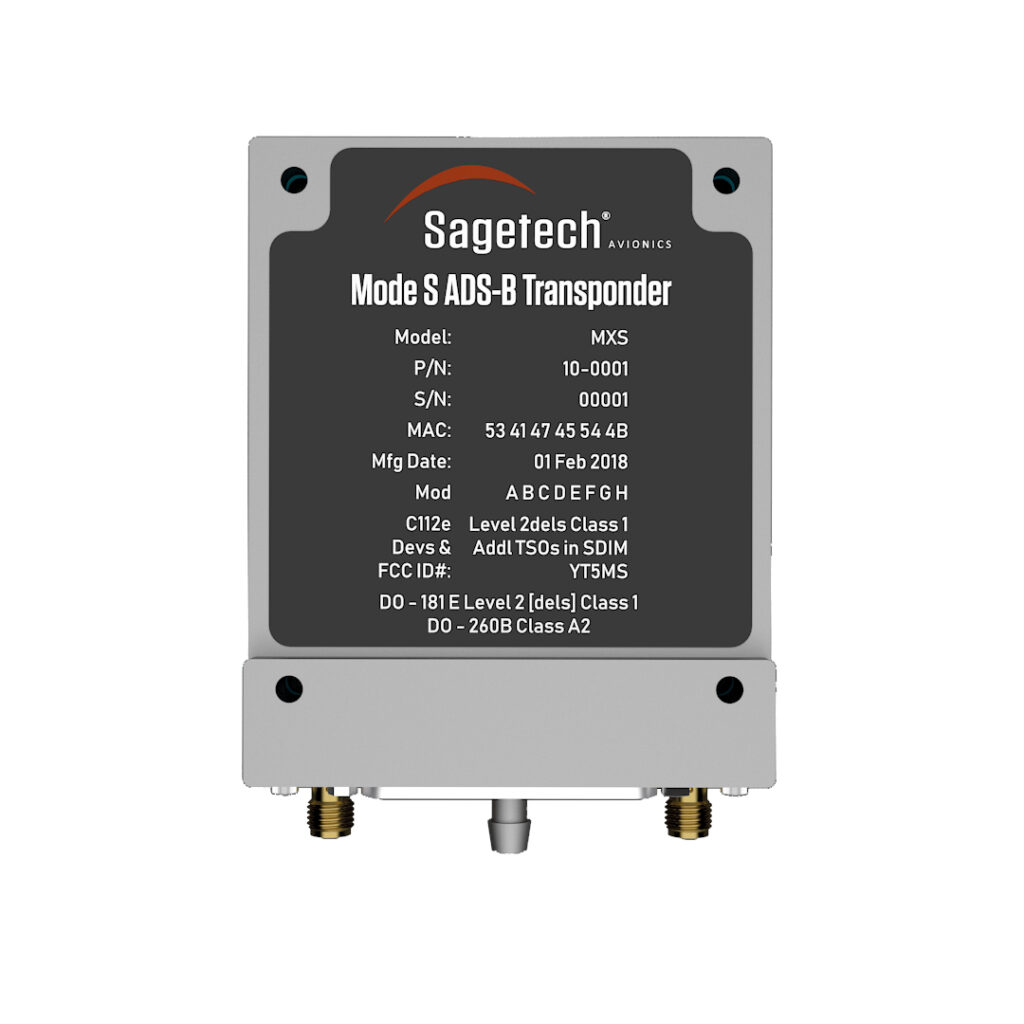
We caught up with Sagetech to discuss its transponder systems and the progress of its TCAS and ACAS programmes.
“The primary solutions we’re showcasing are our MXS civil transponder, which was TSO-authorised in May 2022, and our MX12B, which is the military variant of that transponder,” said Rudy Johnson.
“The MX12B has the same hardware footprint as the MXS – 190 g – and is DoD AIMS-approved for Mode 5 IFF functionality. Such is its small size that the encryption device can’t fit inside the housing. Normally you’d put that inside the transponder enclosure, but the MX12B’s enclosure is about the same size as the encryption system, so instead it just connects to it via a cable harness.”
The company also continues to build on its transponders to develop its collision avoidance and detect & avoid systems, in line with upcoming standards such as ACAS Xu for large fixed-wing systems, ACAS Xr for rotorcraft and ACAS SXu for small aircraft with MTOWs below 55 lb operating at altitudes of less than 500 ft.
“Our ACAS Xu and Xr-compliant systems are now being test flown and evaluated by some key customers to help us iterate and evolve them into mature products,” Johnson added.
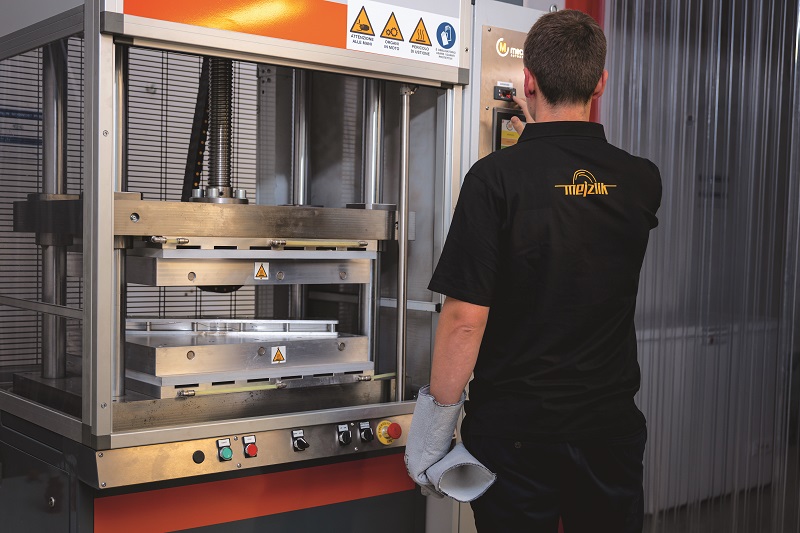
In its pursuit to supply ever greater quantities and customised variations of its propellers, Mejzlik has adopted a new hot-pressing approach in its manufacturing of prepreg carbon composite props.
“Until now, we used wet layups, but hot-pressing prepreg carbon gives us faster turnaround times and multiplies our production capacities,” explained Ambroz Both. “Where previously we could produce some hundreds of propellers per month, now we can make 2000 in the same time, and finish each batch in 2 weeks.
“A hot press contains a mould which gives you the exact same geometric layout across every part of every blade. That, plus using prepared, prepreg material, ensures you get really good consistency between units, so aerodynamic and structural performance stays the same across customers’ prop inventories.”
Also, the hot-press machine works using an aluminium mould, rather than a carbon or laminated mould, ensuring it will last far longer than the latter mould types and hence lower Mejzlik’s production costs per unit. After hot-pressing, each propeller is cut to its final shape and tolerances using CNC machining.
The company also showcased some of its new lines of folding propellers, which it says are gaining popularity for their easier transportability.
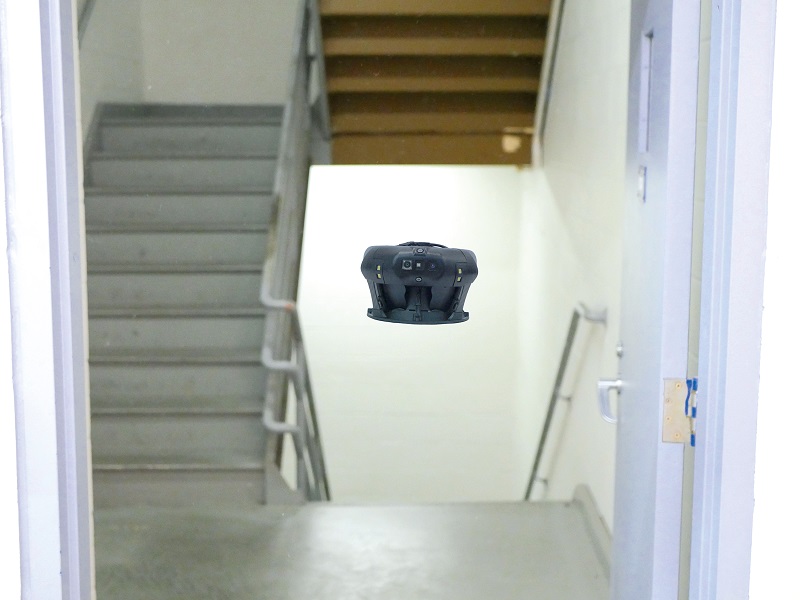
We previously examined Cleo Robotics’ Dronut X1 in detail for its unique flying duct configuration, which when combined with its Lidar and vision-based SLAM capabilities enable it to survey otherwise unsafe and GNSS-denied spaces such as air vents or active factory floors (issue 49, April/May 2023).
“Since then, we’ve been preparing for the upcoming commercial launch of the Dronut X1 Pro,” said Natalia Hoar.
“We’ll be unveiling a number of enhancements regarding the Dronut’s data intelligence and autonomous capabilities, including return to home, obstacle detection and avoidance, and increased flight time to enable more efficient and safer industrial inspection and data capture.”
The Dronut X1 Pro UAV is due to be available later this year.
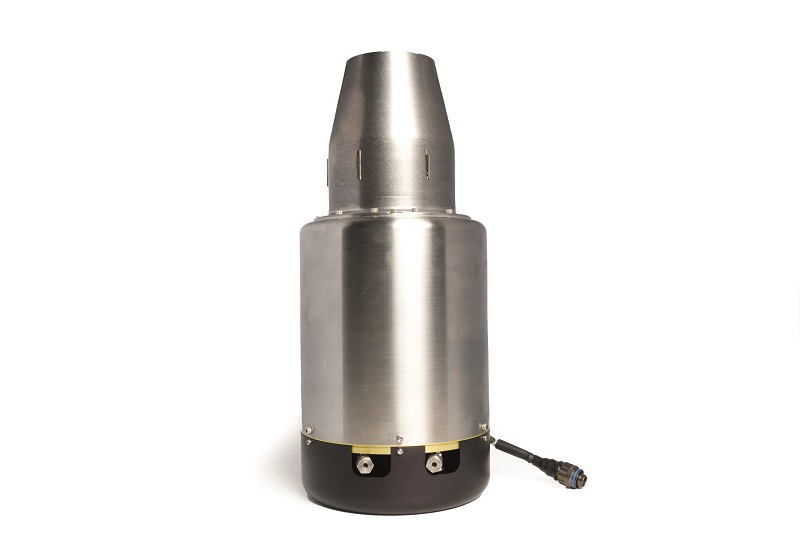
Acutronic showcased its newest microturbine engines for UAVs. The engines range from hobby-grade systems to robust professional and tactical-grade propulsion units.
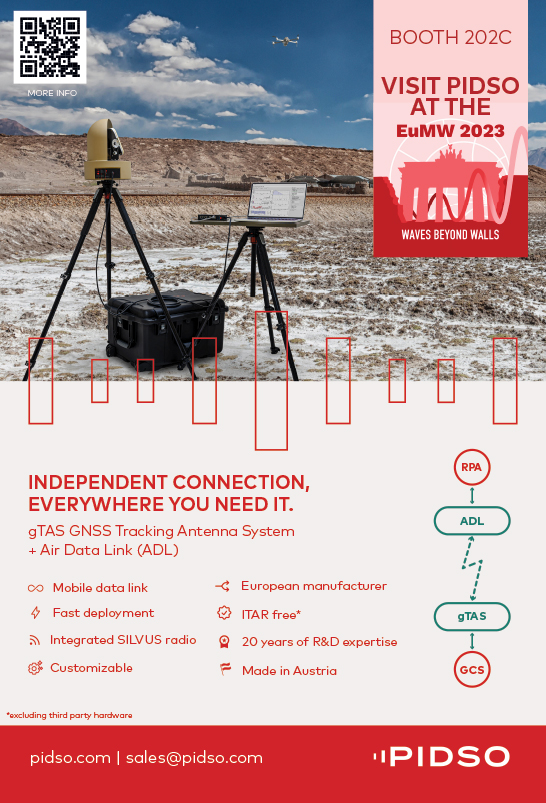
“Our ATI70 produces 310 N of thrust and is in a full operational testing phase and progressing towards full-rate production,” said Cody Fogwell. Acutronic’s engines include all system components (fuel pumps, valves, ignition and so on) and have electric power generation and rectification options.
“We also have turbogenerator systems in development,” he added. “They deliver electric power at a higher power-to-weight ratio than traditional diesel engines or battery packs. They are primarily bespoke solutions for specific customers but we’re developing offshoots for production as off-the-shelf systems.
“The ATI70 has the same form factor as another of our professional engines but with 8% more thrust and 8% better fuel efficiency. We’ve gone with targeted aerodynamics upgrades, a new combustion system and improved electronics.”
Further details about the ATI70 such as TBO and MTBF will be released in the future, pending additional testing.
Acutronic also displayed its range of servo actuators, such as the R0900 Acuflex, a rotary actuator family set to feature closed-loop motor control. They are qualified to Mil-Std 810G for shock, vibration and other challenging mechanical environments as well as Mil-Std 461G for EMC and EMI tolerance. The actuators’ MTBF is above 25,000 hours.
“All our control and depth health monitoring functions are designed in-house from a clean sheet, and are again aimed at tactical-grade platforms,” Fogwell added. “The Acuflex family will feature CAN bus as a standard, but we’ll be able to customise the interface for different end-user requirements.”
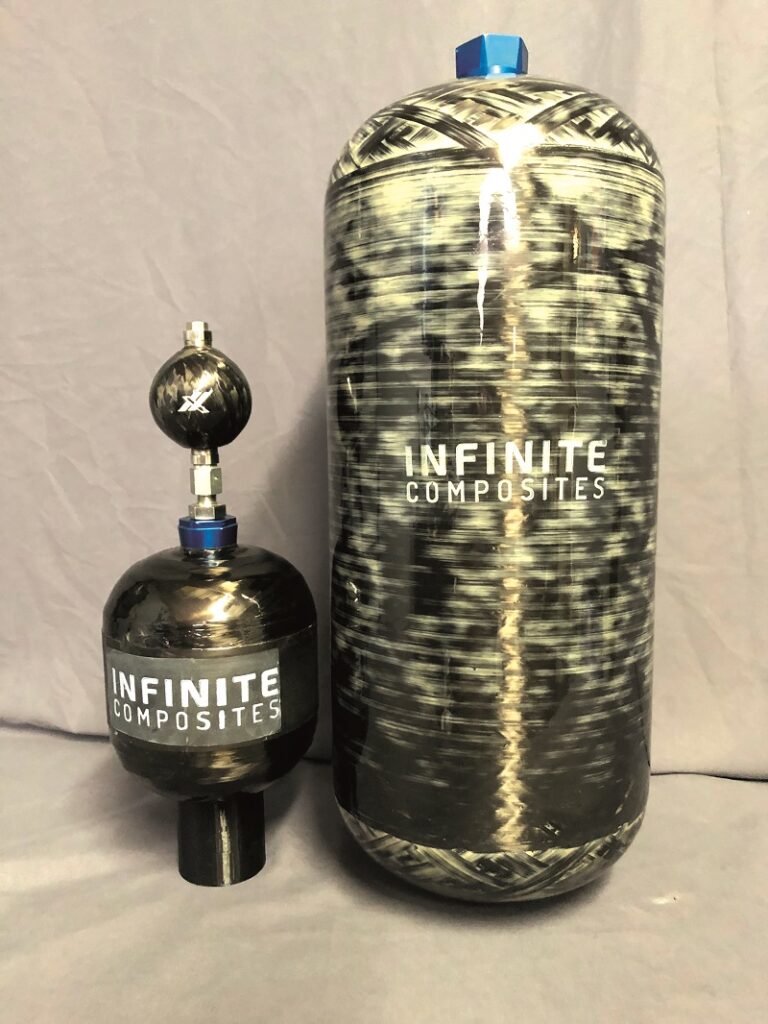
Infinite Composites displayed a unique new type of pressure vessel it said is ideal for applications such as hydrogen fuel storage. It is made from carbon fibre and the company’s own proprietary resin materials.
“Traditional pressure vessels are Type 3 or 4 systems, made using either a metal or plastic liner respectively, and completely overwrapped with carbon fibre in order to have the strength to contain the pressure inside the tank,” explained Michael Tate.
“However, other fibres can work too, such as fibreglass, aramid materials or even basalt fibres, technically speaking.
“What we’ve done is eliminate the need for that liner by having just a carbon fibre structure and an integrated resin-rich layer, which gives the systems integrator more internal storage volume and a lighter tank for the same external footprint, as well as faster lead times and typically lower costs than other aerospace pressure vessels.”
In most Type 3 tanks, the metal liner accounts for up to 10% of the mechanical loading, while in Type 4 vessels the plastic accounts for 0%,” Tate said. “These materials generally serve primarily as a mandrel for forming the carbon composite tank shape around them, and as a barrier to prevent fluids leaking into or out of the vessel.”
Infinite Composites has instead used a proprietary tooling system to form the tank structure and geometry. The tooling is then removed to leave the carbon fibre structure and a resin-rich layer, the latter serving as the permeation barrier without taking up the internal physical volume of the metal or plastic.
“We get the same or better permeation rates as a Type 4 tank, and very similar rates as a Type 3, while also passing all the industrial standards in terms of the performance and capability requirements from the DoT and other governing bodies,” Tate added.
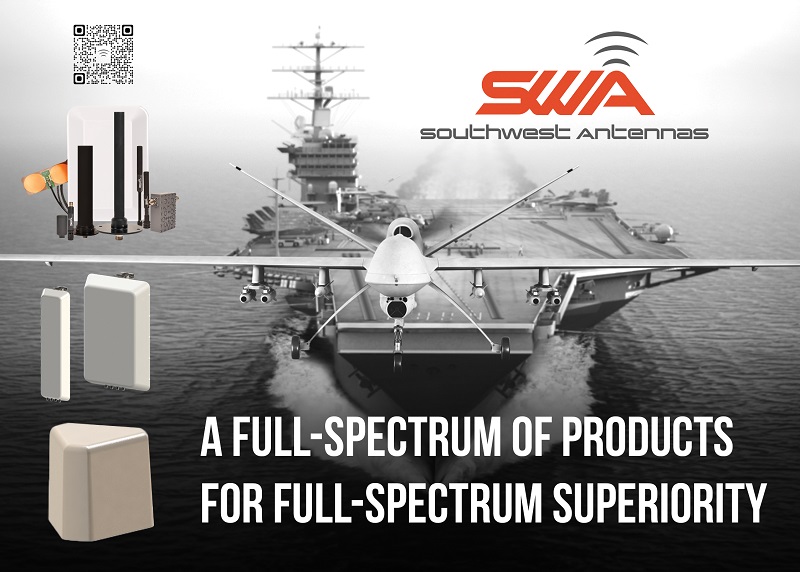
Advanced materials company Venture Aerospace attended the exhibition to show and discuss two new proprietary composite solutions.
“The first is called Melanyte, a carbon fibre alternative,” McKenzie Davis said. “It’s lighter, stronger and about two-thirds the price of traditional carbon composite, while also being more ductile.
“That means it won’t disintegrate or delaminate, like many carbons do when they hit their mechanical failure point. It’s also isotropic – strong in all directions – whereas carbon fibre is weak under compression, such that when you apply force in any direction other than the length of it, it will fail.
“It can also be shaped into various geometries and reshaped, such that a tubular rotor arm could be re-moulded into something else if needed.”
Davis attributes Melanyte’s original invention to Sasha Mela (formerly of Venture Aerospace), the inspiration having come from an ornithologist associate of Venture’s CEO who had cited toucan beaks as having one of the highest strength-to-weight ratios of any organic material.
“Melanyte therefore has essentially an expanding foam on the inside, and is cured with an unshrinkable skin on the outside, thereby mimicking the material in a toucan’s beak,” Davis said.
“Our second material, Lennoxite, follows a very different idea. It’s meant for protecting sensitive electronics against thermal and mechanical stresses. It has high conductivity and wicks heat away like a heat sink, but it’s non-metallic, so it won’t interfere with magnetics.
“So as well as using it to protect PCBs, you could use it in an e-motor. We’re working on a way to extrude it to envelope copper windings.”
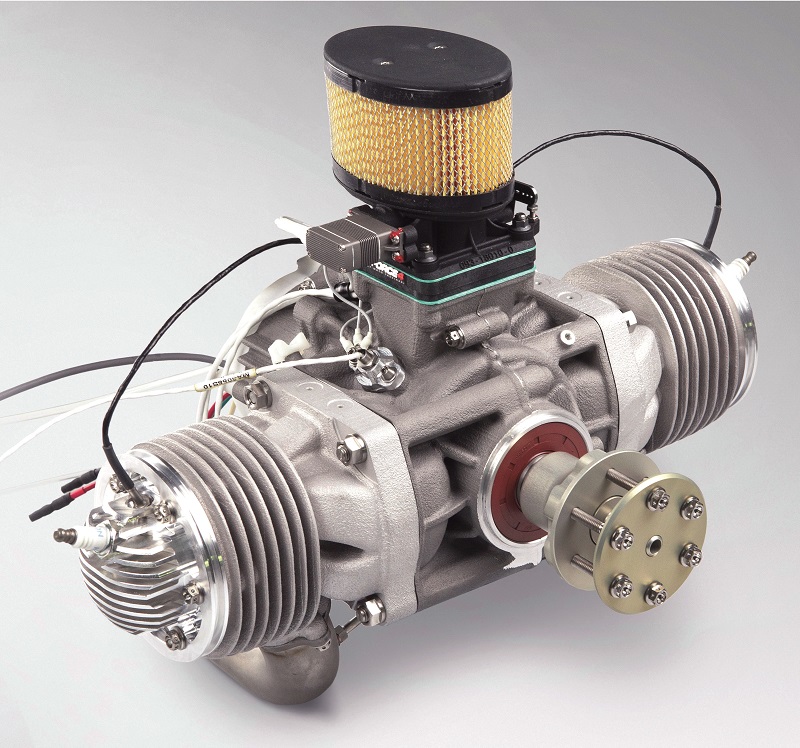
We last featured Suter Aviation in detail regarding its TOA-288 in issue 32 (June/July 2020). It’s a two-stroke, two-cylinder boxer, naturally aspirated and air-cooled, and rated to 14 kW continuous maximum power, up to peaks of 18 kW.
Development of the engine has continued since then. As the company told us at the expo, the 250-hour TBO noted in the previous article has been increased to 500 hours.
“The 250 hours is a safety margin as standard, but thanks to extensive testing with a partner company in Germany that specialises in cycling these sorts of engines, and which ran the engine 24/7 at length, we’ve proven its ability to run for 500 hours safely,” said Dietrich Kehe.
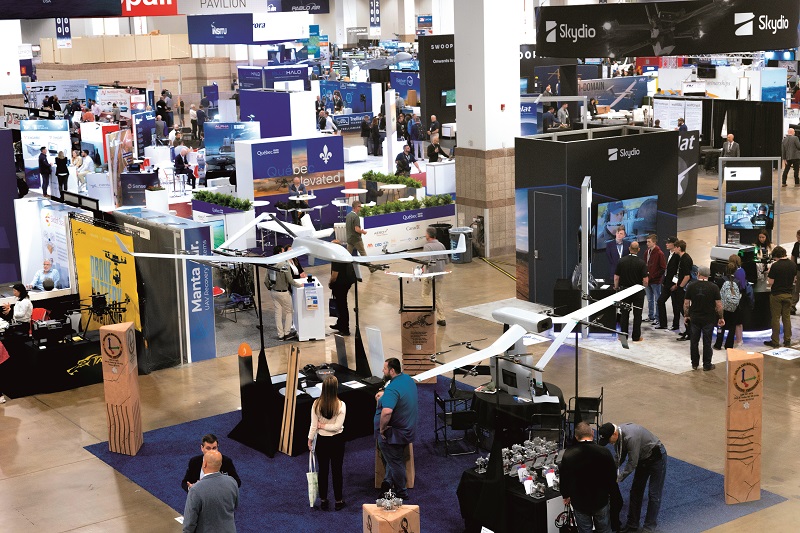
“We’ve also released a tuning kit for the TOA-288 that enables users to get another 2 kW out of it, meaning peaks of 20 kW are now possible at 6600 rpm,” he said. “The kit consists of some cylinder head and exhaust modifications as well as some ECU remapping.”
In addition to continuing to optimise the engine for its customers (such as Martin UAV), Suter is working on a larger engine, which Kehe described as another two-cylinder configuration but with a bigger displacement than the 288 cc TOA-288 – 330 cc was expected at the time of writing, hence its anticipated product name, the TOA-330.
Around 600 companies and 7000 professionals attended Xponential 2023 in Denver, to showcase new uncrewed products and services (Courtesy of AUVSI)
UPCOMING EVENTS
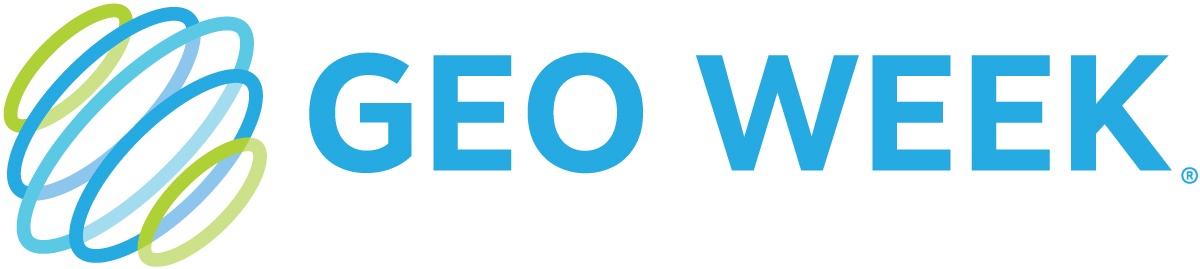
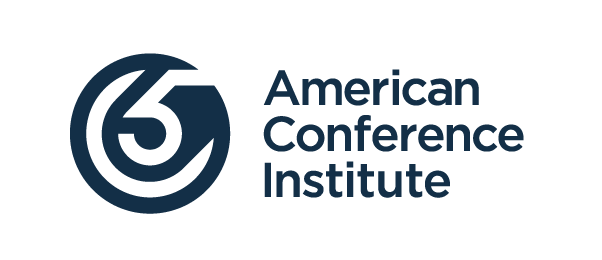
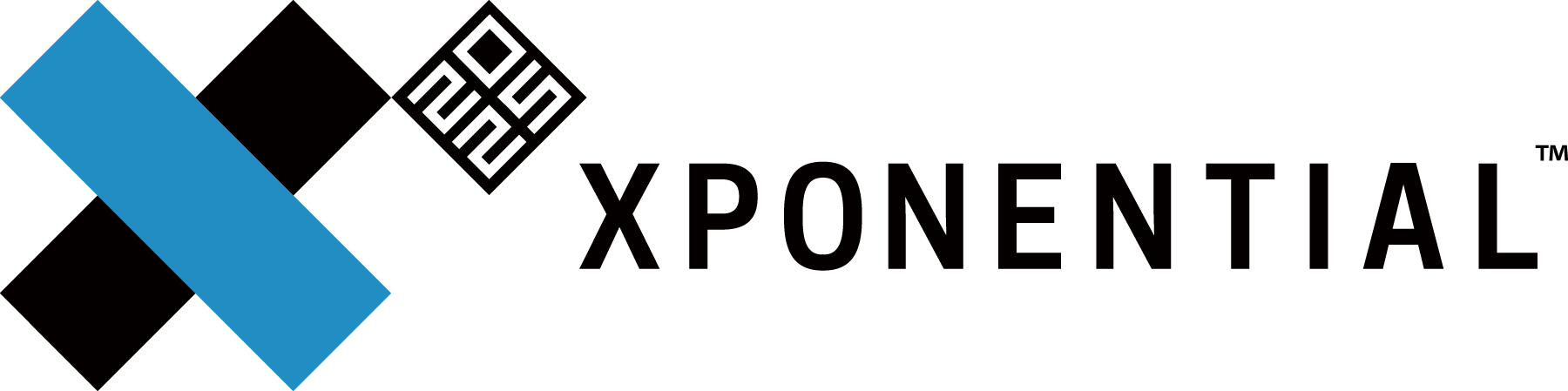
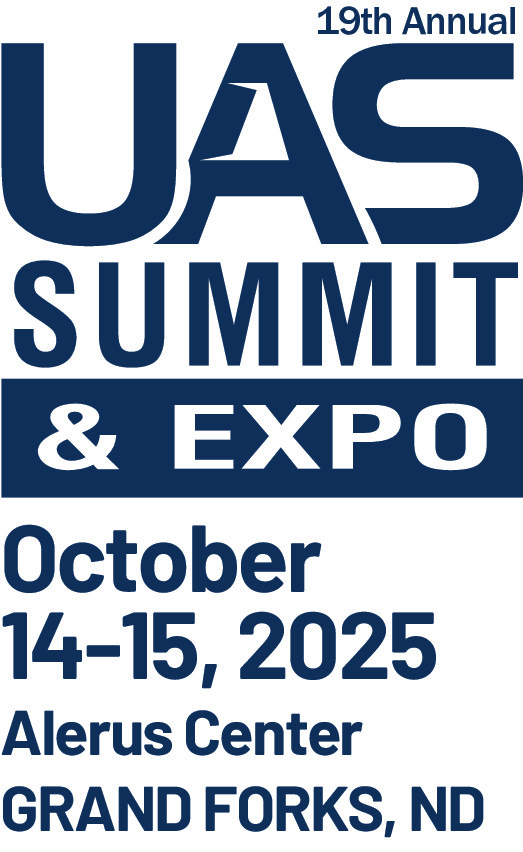
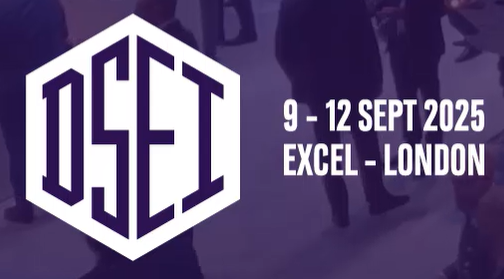
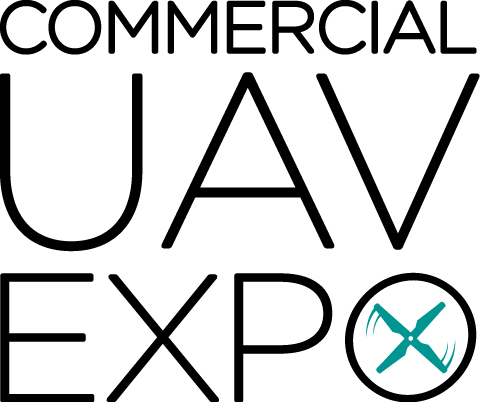
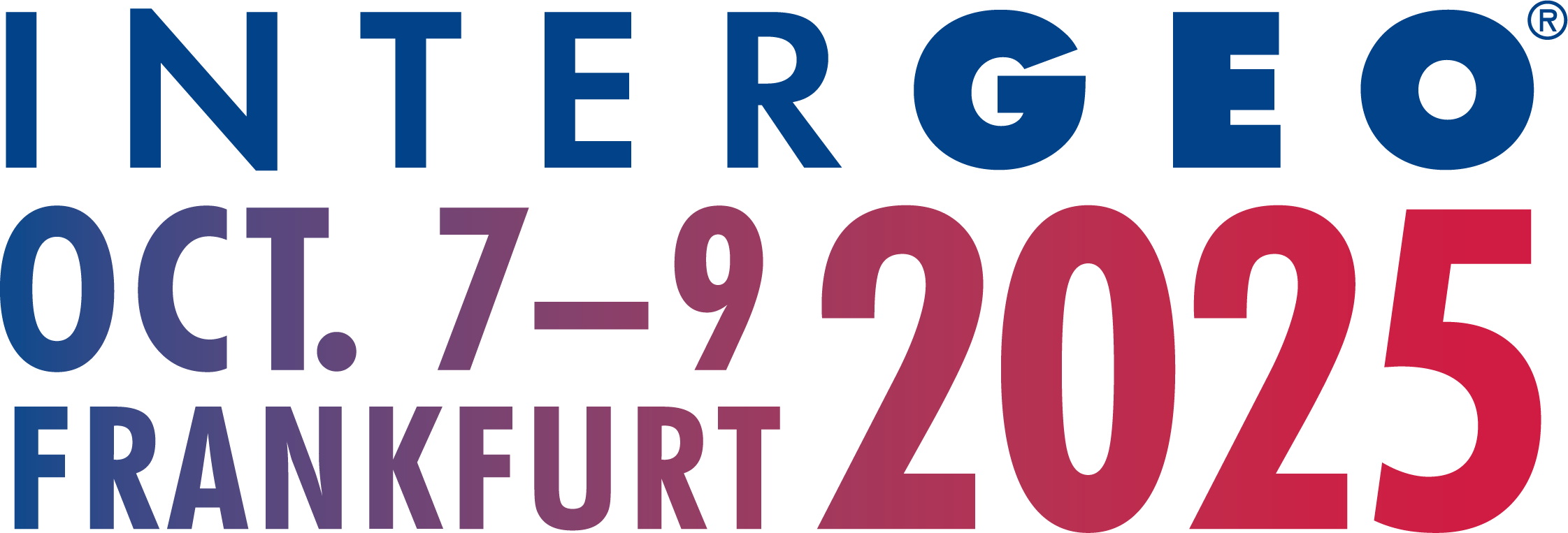
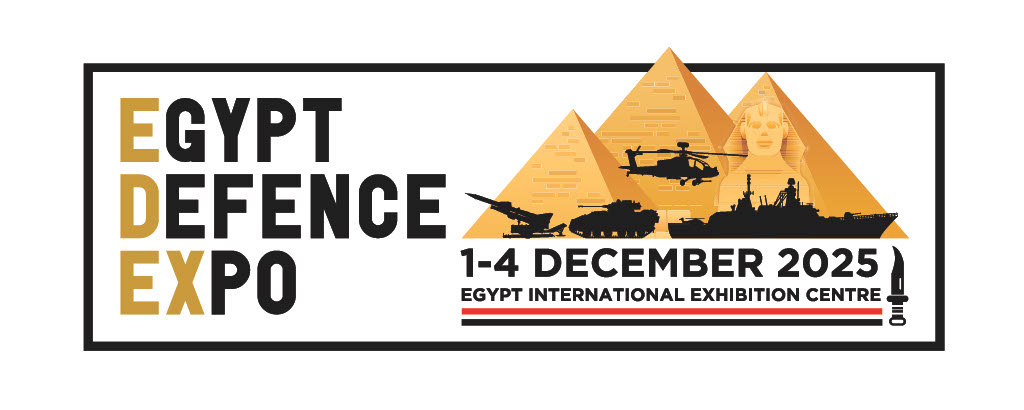
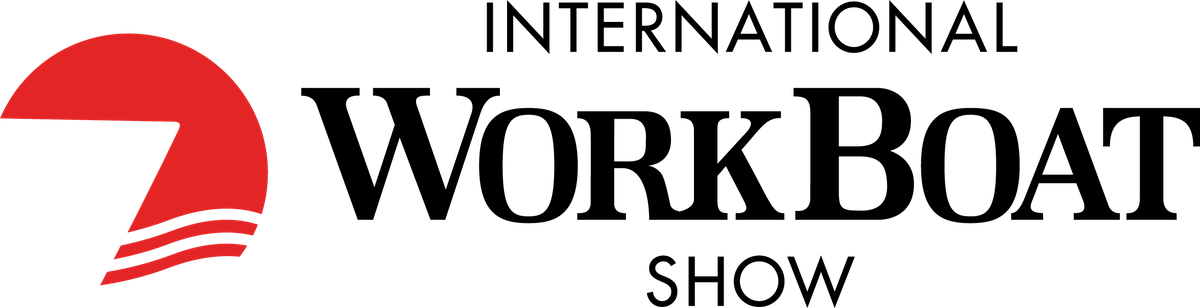
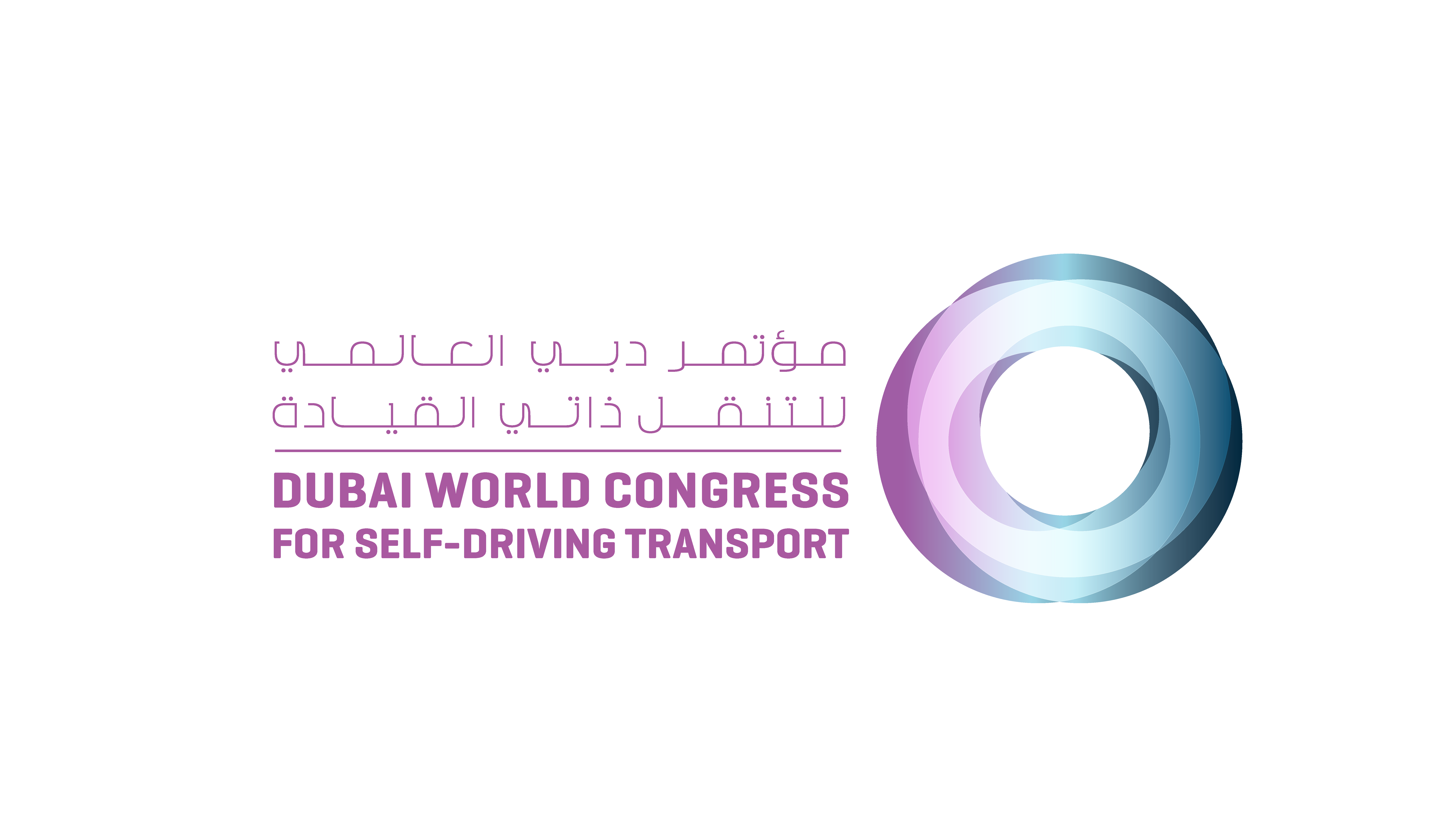
