Defence systems
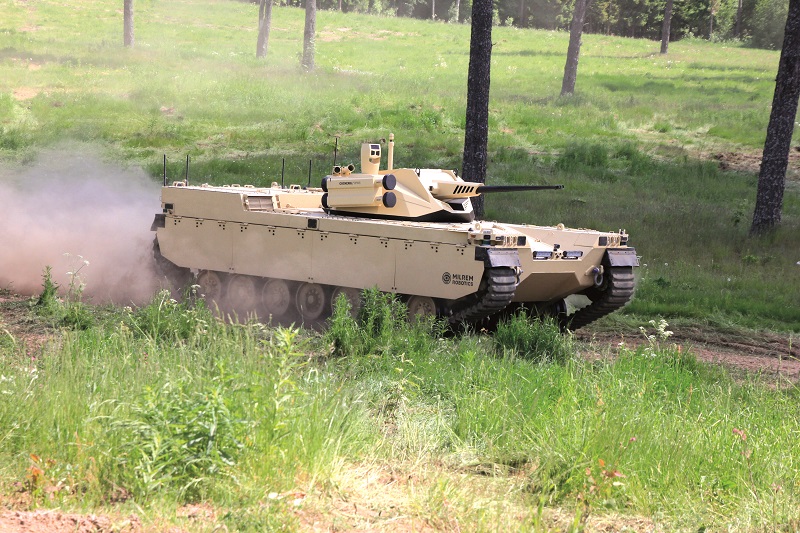
Defence uncrewed systems developers are tracking the changing nature of military conflicts. Rory Jackson reports on some of the direct results of that
Defence applications are arguably the longest running use cases for uncrewed systems, stretching back to World War I with the UK’s radio-controlled Aerial Target and the Kettering Bug aerial torpedo developed by the US. These days, more and more defence services are devising ways to substitute crewed missions for uncrewed ones to help keep personnel far from harm, and bolster an armed force’s effective fighting power.
And just as those forces develop new tactics and strategies, so too must engineers of defence-focused uncrewed systems develop new vehicle designs, capabilities and payloads so that uncrewed systems can tackle the niche requirements of air forces, navies and ground forces.
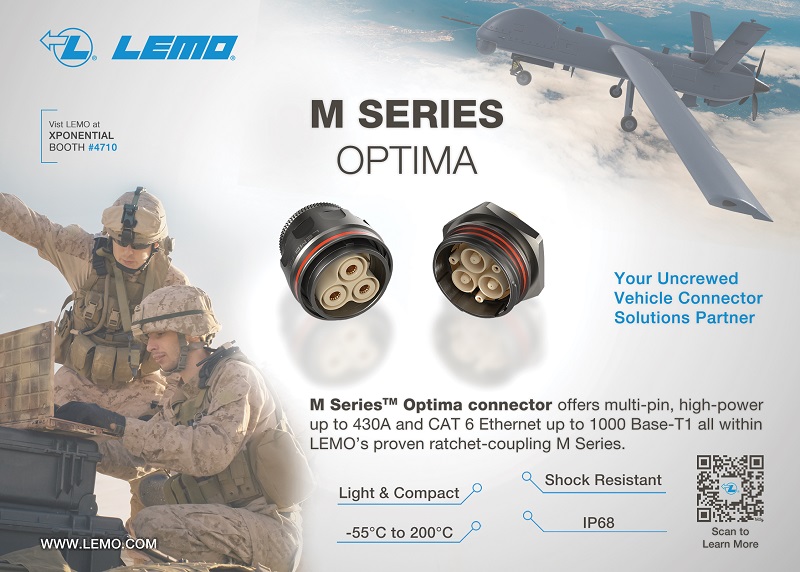
Ground fighting and ISR
In issue 23 (December 2018/January 2019), we investigated the Multiscope commercial ground robot from Milrem Robotics. This is a 1630 kg modular platform with 750 kg of payload capacity for firefighting, rescue, logistics and other operations.
Milrem is arguably best known for its defence UGVs however, and two of its platforms stand out in this regard. The best-known is the THeMIS, its most mature platform, with its engineers currently focused on enhancing its EOD (explosive ordnance disposal) capabilities.
“That means integrating hyperspectral cameras and similar sensing technologies to make sure customers can identify landmines, for example, and set up operations for removing them,” says Sverker Svardby, industrial partnership director at Milrem.
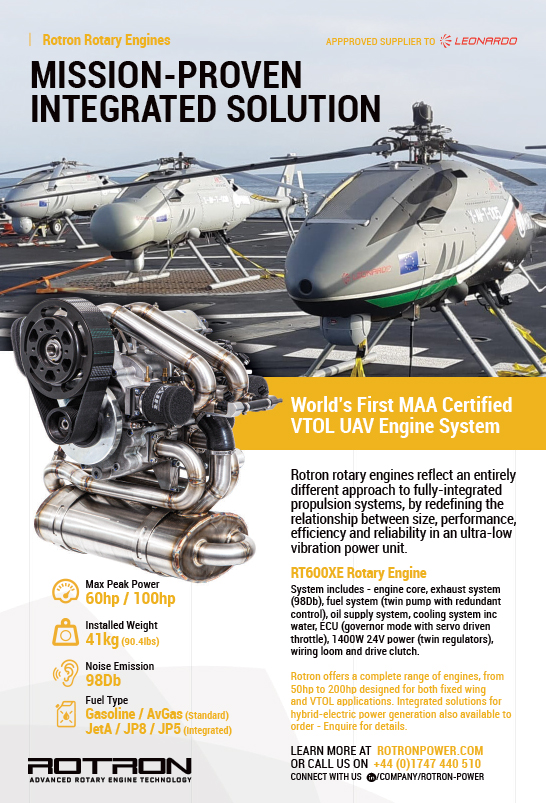
Further EOD payloads available for the 1630 kg hybrid-electric THeMIS are the Raytheon GroundEye sensing system for detecting, confirming and diagnosing explosive devices, and the Rocus (Route Clearance Unmanned System) from CNIM Systemes Industriels, which integrates a sweeper and a robotic arm capable of lifting 100 kg and with a reach of more than 4 m.
Also, Milrem’s Type-X robotic combat vehicle (RCV) is now production-ready, although as with the THeMIS the company continues to customise versions of the system for evolving defence customer requirements such as affordability and different terrain types.
The Type-X resembles a crewed infantry fighting vehicle, and is intended to function as a wingman or similar support RCV to main battle tanks and other mechanised units. It weighs 12,000 kg, measures 600 x 290 x 220 cm and runs on a hybrid diesel-electric drive, like the THeMIS, giving it a top speed of 80 kph on roads and 50 kph off-road.
It is certified to Stanag 4569 L4 for kinetic energy impacts (non-explosive projectile weapons such as bullets or mass drivers) and artillery protection, as well as Stanag L1 for mine protection. It can also be fitted with Kongsberg’s Protector weapons station as well as a multi-canister launcher for ordnance such as UVision’s Hero-120 and Hero-400EC loitering munitions systems.
“For customers seeking a lower-cost autonomous ground solution, we are continuing to develop our Milrem Intelligent Function Integration Kit [MIFIK],” Svardby adds. “This is an integrated kit with sensors for a vehicle to perceive its surroundings, and a computer running our algorithms to digest that perception data and process it into driving directions, movements and obstacle detection and avoidance.”
The MIFIK can be configured with location or event-based autonomous behaviours, including patrol loops, backtracking, return-home triggers and switching among multiple waypoints, routes and missions.
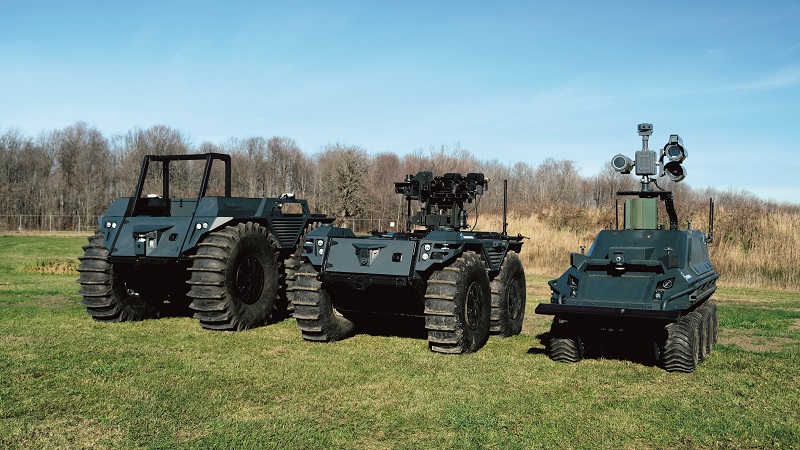
Ground medevac and logistics
As with many commercial entities, defence organisations have wide-reaching logistics requirements, and the closer these requirements are to areas of conflict, the more hazardous and urgent they become.
The development of autonomous ‘mules’ for carrying equipment, frontline resupply and even uncrewed medevac tasks is hence something a few defence technology firms have attempted over the past decade. Among such systems is the family of Mission Master vehicles from Rheinmetall, which have been trialled successfully in Australia during its summer, and Estonia and within the Arctic Circle during winter.
“We have three versions of the Mission Master UGV: the SP, the CXT and the XT,” explains Eric Diniz, project and system engineer at Rheinmetall. “The SP is a fully electric vehicle and can carry up to 600 kg of payload. The XT is the largest in the family; it can carry up to 1000 kg of payloads, runs on diesel and has a hydrostatic transmission.
“The CXT stands for ‘compact XT’, as its size is between the SP and XT. It has a hybrid drivetrain, with batteries and electric motors, and an engine that can recharge the batteries while running on diesel or JP-8, and it can carry a tonne of payload weight.”
The SP can operate for up to 8 hours at an average speed of 10 kph (its top speed being 30 kph), or for up to a week if sitting still and operating as a surveillance system.
The CXT has been tested to cover 50 km between charges of its battery pack, and up to 450 km between refills of its fuel tank, the hours of operation depending on the missions and terrains it is applied to. The XT has been tested to travel up to 750 km between refuelling, with the two larger Mission Masters both capable of up to 40 kph.
A platform on top of the vehicle can be configured with various payloads; Rheinmetall designs the platform with common mounting plates for bolting on or removing mission equipment within a few minutes. The payloads include pallets for carrying goods, soldiers’ equipment or wounded personnel, and the tests in Australia and Estonia have included trials and demonstrations of how medevac missions would be carried out in different weather conditions and terrains.
“All the Mission Masters are amphibious, enabling them to travel through water at up to 5 kph or up to 4 kph for the CXT,” Diniz adds. “Also, they all are equipped with the Path autonomy kit or A-kit, the hardware and software architecture powering the UGVs’ intelligence, which can be integrated in other vehicles for logistics or other purposes like personnel transports and autonomous convoys.”
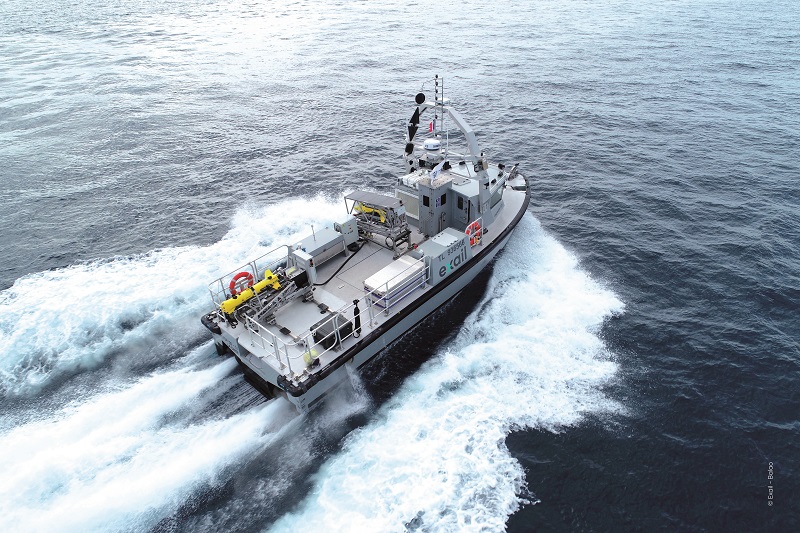
Maritime mine countermeasures
Uncrewed systems for naval customers continue to evolve towards faster, safer and more cost-effective operations. For mine countermeasures (MCM), this means configuring USVs and AUVs for an array of capabilities they can execute in parallel with each other, so that no matter the nature or size of the minefield, navy personnel and crewed ships can keep to a safe distance.
Exail has taken advantage of that need from naval integrators for parallelised solutions. “We have two USVs in our portfolio, the DriX, which is a pure civil design, and the Inspector 125, which is dedicated to MCM missions,” says Antony Penn, commercial director for maritime systems at Exail.
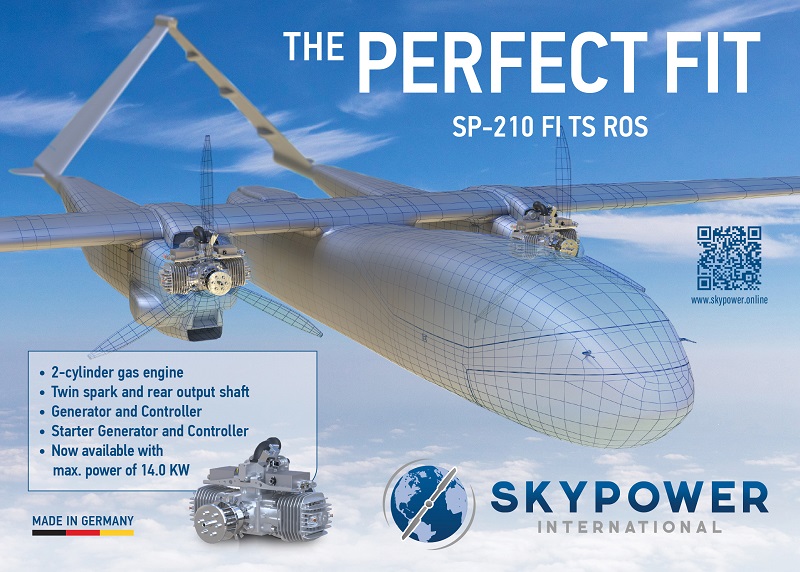
“The Inspector 125, when equipped with an Exail FLS 5 sonar, can perform the initial mine detection phase, before launching other uncrewed systems like our A18-M AUV, Seascan and K-Ster ROVs into the mined area so that the crewed ships can remain out of the danger zone.”
The Inspector 125 is a 12 m-long, 3.85 m beam-width vessel built largely from composite materials and positioned as a larger counterpart to the 9 m Inspector 90 (investigated in issue 6, February/March 2016).
It has been selected by the Belgian and Dutch navies as part of their next-generation MCM system, and is designed for a fully loaded weight of around 19 t, a 13.355 t empty weight, and for up to 2500 kg of payload on its main deck, which has a surface area of 23.6 m2.
The DriX (covered in issue 25, April/May 2019) was originally designed for commercial operations but has also been trialled in surface and seabed monitoring, for example. These took place during operations with Task Force 59, the US Navy’s lead group for testing and integrating uncrewed systems to enhance maritime defence capabilities, with a view towards developing a military version.
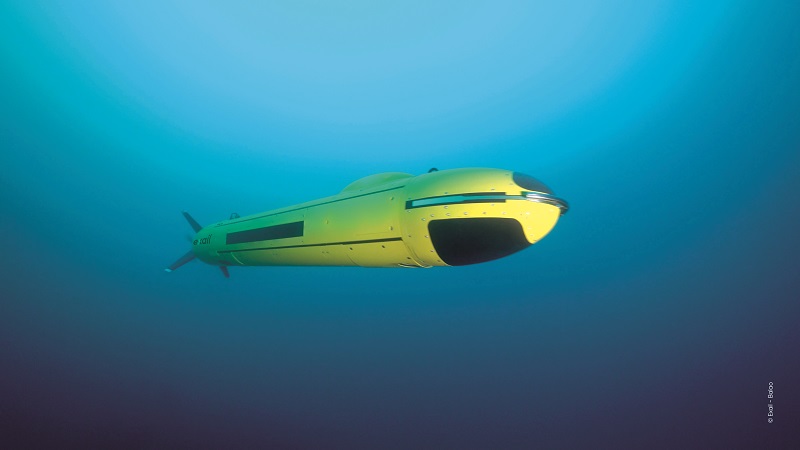
“In addition to the A18-Ms and the FLS5, the Inspector 125 can also pull a T18-M towed system equipped with Exail’s Umisas sonar, to cover large areas and provide real-time sonar data to MCM operators through the USV’s data link,” Penn notes.
Using AUVs can enable more covert and potentially closer surveys of mines than USVs, so the A18-M is designed for up to 24 hours of mission endurance at depths down to 300 m. The modular AUV weighs 442 kg and measures 4.5-5.5 m in length, integrating a 10.9 kWh battery pack.
Travelling at 3 knots nominally (up to a maximum of 6 knots), the A-18M can look for mines using the Umisas sonar as the T-18M towfish does, having been designed and built using much of the same technology as the T-18M.
While the T-18M is towed behind the 125, and deployed and recovered using a winch on the USV, the A-18M is lowered by the 125 into the water by cable and disengages a clamp on its nose to free itself from the cable. For recovery, it detects the cable, approaches it and re-captures it with its nose clamp so that the USV can reel it in.
The 125 is also equipped to launch and recover Exail’s SeaScan ROV. This is equipped with high-performance sonar and HD cameras to ensure identification and classification of the potential threat detected by previous systems.
Once the mines have been detected and classified, they can be neutralised using Exail’s K-Ster. This is a remotely operated expendable mine disposal vehicle, equipped with a rotating head containing a shaped charge, so that operators can launch it from a 125, navigate close to the detected mine before neutralising it with the charge.
“The USVs can also act as comms relays,” Penn adds. “If an AUV surfaces, it can immediately begin transmitting pre-processed survey snapshots and other data that the USV can then relay to the operators aboard their ships. From there, they can then start analysing and classifying what kinds of threats or other points of interest have been found.
“In addition to the work with the Belgian and Dutch navies on their MCM programme, where our uncrewed systems will be used alongside maritime UAVs like the Skeldar, we’re also carrying out a modernisation programme with the Latvian Navy.
“We’ve updated their traditional minehunting ships with various new subsystems, such as the A-18M, our Umisoft MCM mission control software and our Seascan and K-Ster ROVs. That means they too can perform long-distance stand-off MCM, without having to replace their ships,” Penn says.
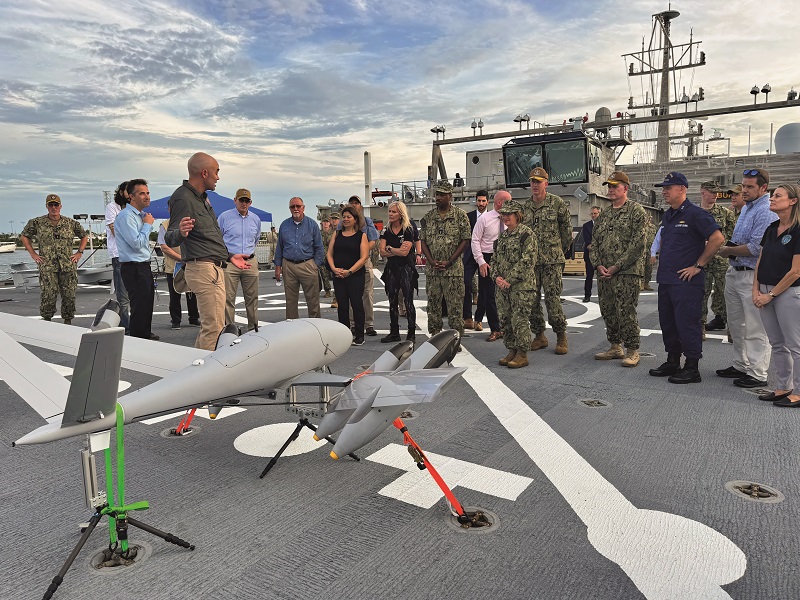
Ship-to-ship logistics
In addition to tasks like MCM, logistics from ship to ship, ship to shore and shore to ship are also being transformed through the use of uncrewed systems. The latest example of this was a demonstration at the US Naval Forces Southern Command/US 4th Fleet Hybrid Fleet Campaign Event (HFCE) in October 2023, where PteroDynamics performed its first ever ship-based test and demonstration flights.
There, the company carried out nine autonomous launches and recoveries of its Transwing UAVs (investigated in issue 41, December 2021/January 2022) from the USNS Burlington in Florida.
“Exercising our UAV and gathering data on potential ship-to-ship and ship-to-shore logistics, for missions like carrying critical repair cargo, was a key aim for us at the HFCE,” says Tim Whitehand, VP of engineering at PteroDynamics.
“Trialling autonomous precision take-offs and landings on moving ships with vision-based navigation were also critical. That’s key to actually working with the US Navy, because we’ll need to fly in GPS-degraded and denied conditions.”
The Transwing model flown in the demonstrations was the company’s 40 kg X-P4. This UAV’s transverse-folding wings enable a mechanically simple VTOL transition 10-12 seconds after take-off, and Whitehand notes that PteroDynamics is working to make the transition faster. The craft also performed demonstrations of autonomous climbs and dashes, and the company notes that in internal tests of these it has reached 3000 ft/minute and dash speeds of 90-100 knots.
To date, 12 X-P4s have been built, although Whitehand comments that the US Navy is most interested in the X-P5, a larger version of the X-P4 which is in development and is being designed for a 150 kg MTOW (the maximum weight in the UAV maintenance category) and a 27.2 kg payload capacity. The X-P4’s flights are hence aimed at proving the Transwing’s capabilities to the Navy, in advance of the larger production aircraft more suited to its preferred payload capacity.
Internally the X-P5 is also being designed by PteroDynamics as a modular platform for ISTAR-suited payloads such as EO/IR/laser rangefinder gimbals and COMINT devices, as well as different attachments for other defence missions and a range of commercial applications.
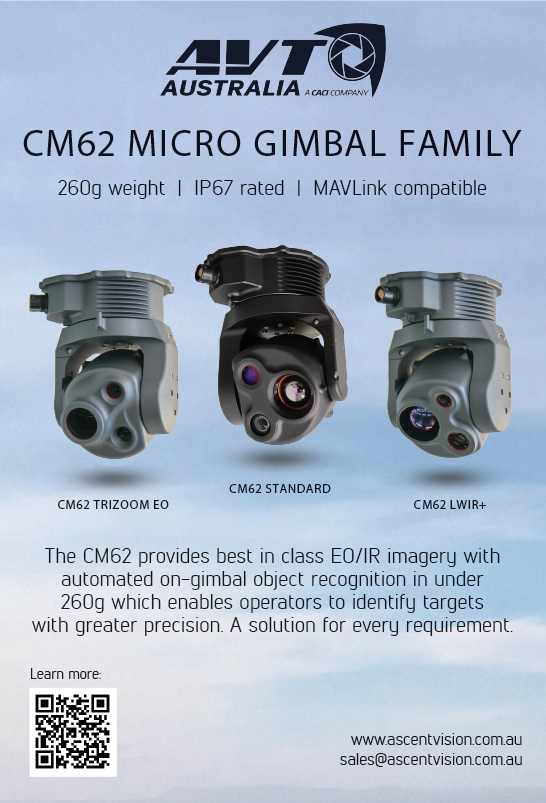
“We’ve also looked at several powertrain configurations, using multi-disciplinary engineering tools to design thousands of Transwing variants, including UAVs carrying different arrangements of propulsors tailored to customers’ technical and mission requirements,” Whitehand notes.
“Some of those have a series-hybrid or range extender engine in the fuselage, while others have one engine on a wing, and others have one or more pairs of engines split across the wings.”
Another version of the X-P5 is also being developed to target the requirements of DARPA’s AdvaNced airCraft Infrastructure-Less Launch And RecoverY (Ancillary) X-Plane programme. This is an ISTAR initiative aimed at producing a VTOL-transitioning aircraft with 12-16 hours of flight endurance, a flight range of at least 100 nautical miles from the launch and recovery location, and at least 80 knots cruising airspeed.
In terms of suitable powertrain configurations for PteroDynamics’ X-Plane project, Whitehand comments, “Top of our list are parallel hybrids, with energy and power-rich heavy-fuel IC engines driving the propshafts and motor/generators, maybe directly, to avoid the double conversion losses of a series hybrid.”
The X-Plane will also be expected to be launched and recovered in difficult weather conditions, without relying on any external infrastructure, and to operate safely in emissions control conditions when all radio transmissions must cease for safety or security.
PteroDynamics is also fleshing out concepts for an X-P6 and an X-P7, each of which will be progressively bigger – just shy of 600 kg and 1361-1814 kg MTOWs respectively – and Whitehand suggests that these heavy multi-role UAVs will need appropriately large powertrains such as recuperating turbo-generators, depending on end-user requirements and specific fuel consumption.
“That MTOW range for the X-P7 is targeted as a sweet spot for what we see our end-users needing in their future-generation UAVs,” he adds. “Internal studies on that have found a considerable crossover between the pragmatic scalability of the Transwing range and the multi-role UAS sizes and capabilities requested by our customers.
“For the time being though, we’ll continue demonstrating the X-P4 for the US Navy, including autonomous demonstrations of real-world ISTAR trial missions or simultaneous operations with multiple UAVs by using the data gained in Florida to improve our autonomy software and performance with useful naval ops in mind.”
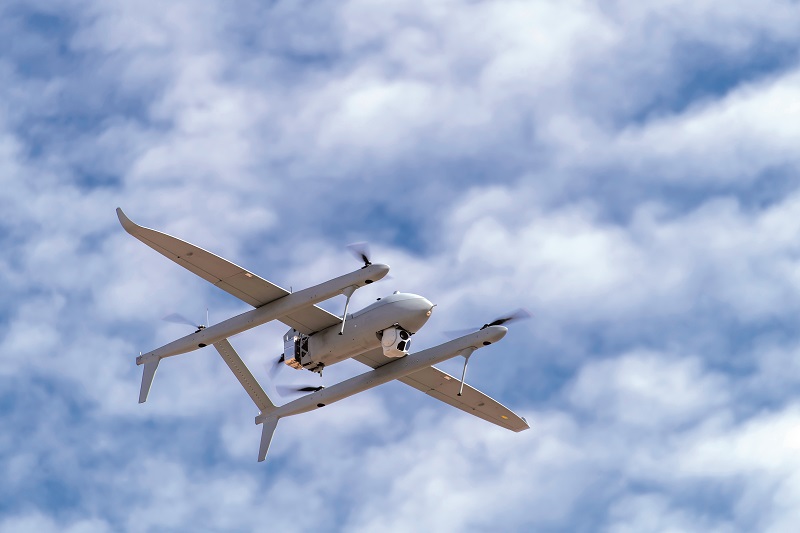
Future tactical UASs
The US Army’s Future Tactical UAS (FTUAS) programme is a competition-based effort to choose the ideal uncrewed aircraft design to replace its ageing RQ-7 Shadow. Key requirements from the US military for this next-generation UAV include significant modularity for installing different payloads, such as EO/IR gimbals, comms relay systems or SIGINT devices, and the ability to launch and land independently of runways.
As of September 2023, the competition field had narrowed, with Textron Systems among those having been selected to advance with their contender UAVs.
Textron Systems’ entry for the FTUAS is its Aerosonde Mk 4.8 Hybrid Quad (HQ), a VTOL-transitioning fixed-wing aircraft with four upward-facing rotors for vertical lift, landing and hover, by which it covers the US Army’s runway-independence requirement.
“It weighs 93 kg, and is a larger variant of our Mk 4.7 HQ,” says Jim Ryan, senior director at Textron Systems for air domain. “The Mk 4.7 was reviewed by the Army, and their feedback was that they liked the mobility and transportability but wanted more capacity for payloads, station time, higher altitudes and so on.
“So we took the Mk 4.7 and scaled it up to the new Army requirements. Disclosing full specifications of the Mk 4.8 is difficult right now because of the competition, but we can exceed 14 hours of endurance with 13.6 kg of payload.”
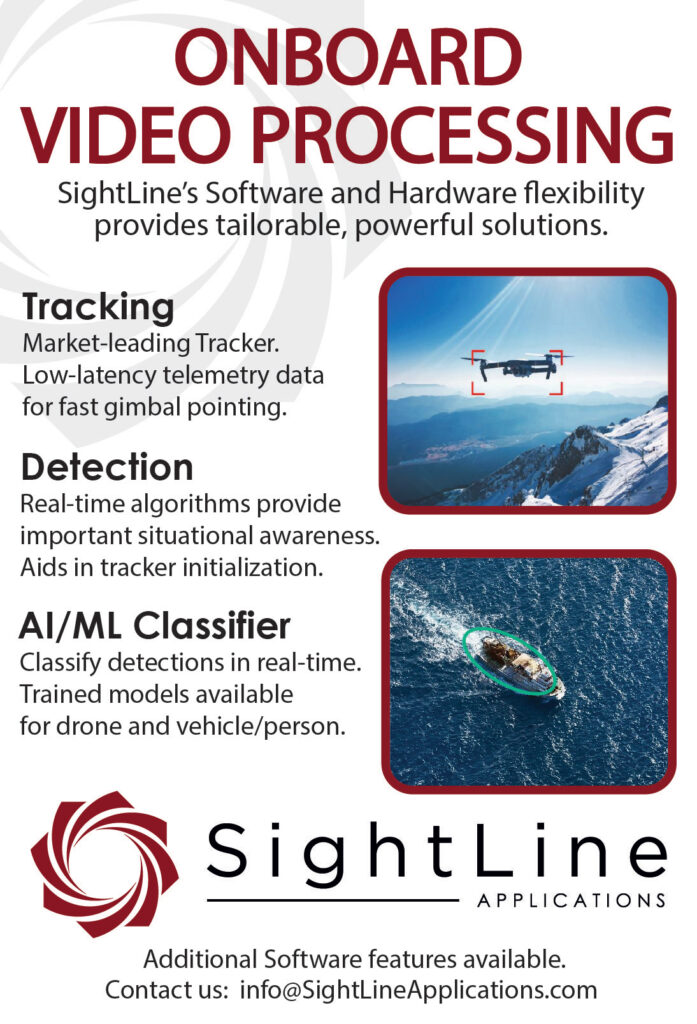
The Aerosondes are designed and built around a system of common flight and ground controllers, with each aircraft sized differently, running from 36 to 93 kg to cater for varying mission profiles. They include versions of the Mk 4.7 and 4.8 designed for catapult launching and recovery using a net, if preferable.
“The Mk 4.7 is powered by the EL-005 engine from Lycoming, our sister company, which has supplied the Aerosonde powertrain for many years,” Ryan adds. “It’s a 75 cc, 4.0 bhp engine running on JP8 or Jet A fuel, which we’ve been using since 2012, and the engine has now racked up 600,000 hours of operation and the data associated with it.”
To meet the higher power needs of the larger Mk 4.8, Textron has integrated Lycoming’s EL-010, a derivative of the EL-005. Whereas the 005 is a single-cylinder, two-stroke, spark-ignited engine with air cooling, the 010 is effectively a dual-cylinder version. This achieves higher horsepower as well as electrical power for payloads, along with improved balance owing to the two cylinders cancelling out much of each other’s first-order vibrations.
“An important feature of the EL-005 engine is its 1000 hour TBO,” Ryan notes. “We work for much of the time as a fee-for-service UAS operator as well as our core business of designing and building the UAVs. Powertrain TBO is a major cost-driver for UAS operations, which has really helped drive down our operating costs over the years.”
Cross-domain r&d has also played a major role. “Our UAV engineers aren’t pigeonholed into working only on aircraft,” he says. “For instance, they can work on our CUSV [Common USV] for minesweeping or ocean ISR, or our Ripsaw UGVs that we’ve submitted for the US Army’s RCV programme, and vice versa, each team learning from the others.
“And we’ve done exercises in which those uncrewed vehicles and their teams talked to each other and collaborated. That included extending the effective range of the CUSV by combining and launching an Aerosonde with it, and we’re looking to carry out more exercises where our different uncrewed systems work together.”
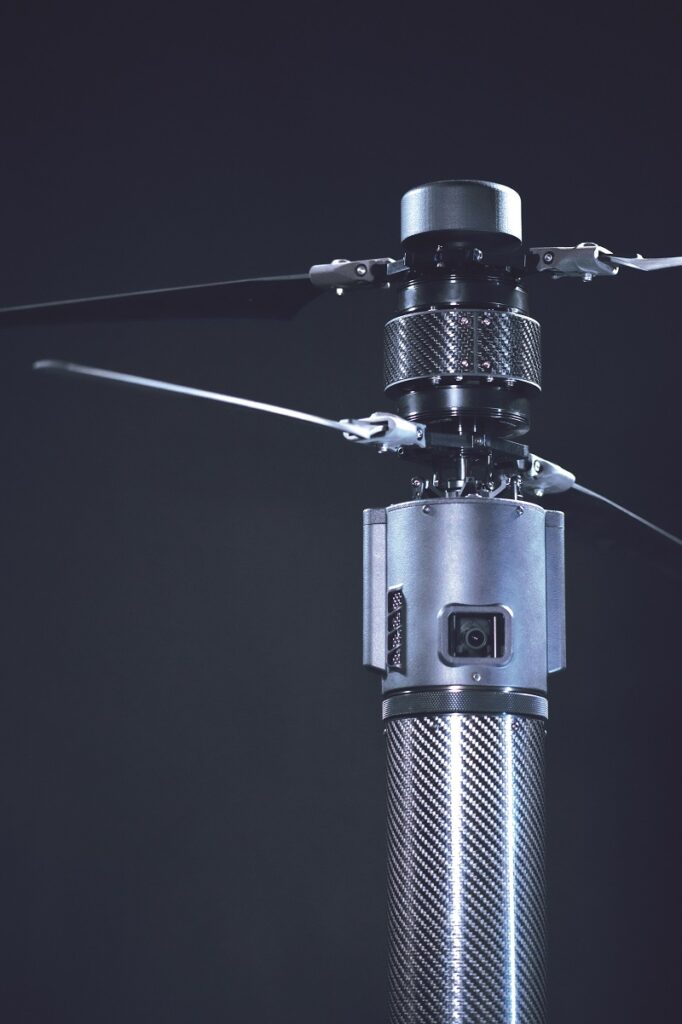
Airborne loitering missions
When designing UAVs as multi-role tools for military users, manufacturers must occasionally bear in mind that as well as serving as scouts and wingmen to crewed vehicles and human operators, they will sometimes need to function as a sacrificial member, as gathering crucial data on high-risk areas poses the possibility that a UAV will be destroyed while trying to find an enemy’s location.
A growing number of UAV manufacturers are taking this one step further by designing their aircraft as loitering munitions or precision strike UAVs. These first perform ISR and monitoring to look for an enemy asset, including UGVs and remote weapons stations, before approaching and using an ordnance payload to neutralise it.
Although some loitering munition ‘UAVs’ are little more than glorified cruise missiles, Overwatch Group’s multi-role Pholos UAV has been engineered to provide a static loitering capability using features such as a coaxial dual-rotor electric powertrain. The counter-rotating propellers are used to provide flight and hovering capabilities in as stable and quiet a manner as possible, while also optimising the craft’s tactical applications, portability and payload capacity.
“The Pholos is payload-agnostic, so it can serve in commercial or military operations,” says an Overwatch representative. “For the latter, the base of the tubular vehicle chassis can be fitted with interchangeable warheads.”
The Pholos has a 6.5 kg MTOW, with a 1.5 kg payload capacity. As standard, it also carries two cameras that are not included in the payload capacity. One faces forward for visual monitoring of the terrain and other features ahead, while the other faces downward for targeting or landing.
“The warhead is electronically enabled by a unique code, the operator bearing full responsibility for it, so the UAV can’t arm the warhead by itself,” the representative says.
“If a target isn’t found then it can be disarmed and the UAV triggered to return to base. This functionality also allows a mission to be cancelled even in the final descent.”
The Pholos can fly for up to 40 minutes on a full battery charge, its range limited only by the range of its data link or GNSS availability, although its modular architecture allows for the use of mesh radios that can extend its range significantly. Overwatch has tested the system at ranges of up to 10 km from its GCS operator.
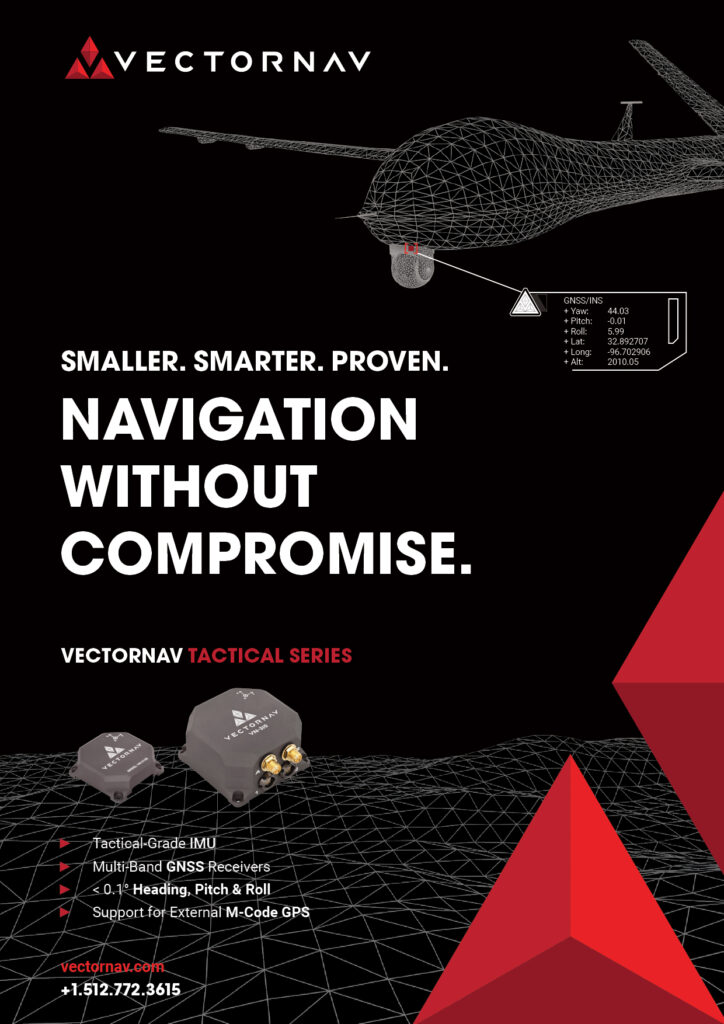
Summary
As these cases show, there is now a wide range of defence tasks for uncrewed systems. Logistics, medical and threat-countering missions will soon be the domain of autonomous vehicles, and as systems are better optimised for such capabilities, it begs the question of what the next generation of uncrewed defence vehicles might look like.
For instance, many UAVs used to be shaped very similarly to crewed aircraft, but are now being designed with more SWaP and aero-optimised shapes, and with nothing resembling a cockpit.
Hybrid and electric powertrains are becoming widespread on land, sea and in the air, for the stealth advantages of their low noise and thermal signatures as well as for meeting defence groups’ sustainability targets. Mitigating climate change is also a growing strategic imperative for military bodies involved in climate-driven conflicts in the future.
As an awareness of the importance of sustainability grows in the defence sector, other technologies could become of paramount importance. Recyclable batteries and composites, sustainable kerosenes, hydrogen powertrains and thin-film solar are a few examples of technologies that could be in strong demand from military integrators in the future.
And given the strategic importance of protecting vehicle comms from jamming, edge computing could take priority over cloud computing, pushing the development of more powerful, reduced-SWaP embedded computers.
UPCOMING EVENTS
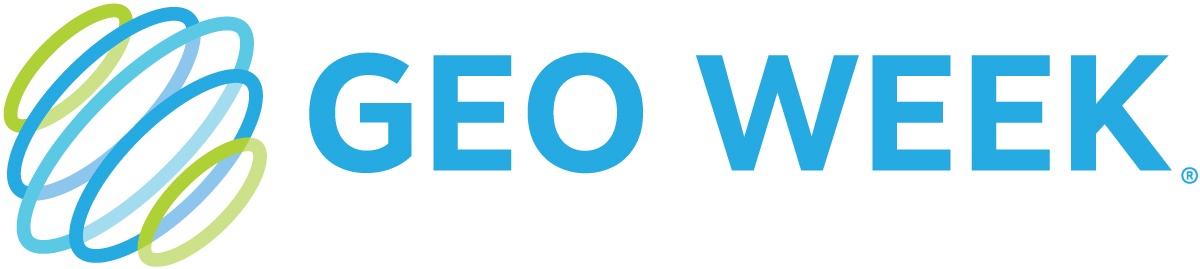
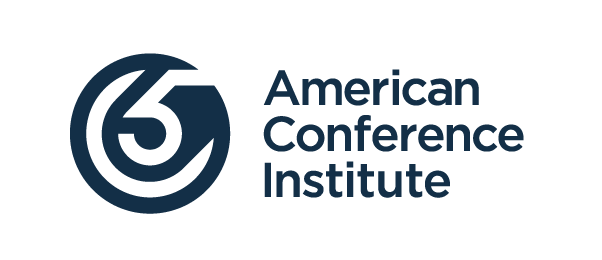
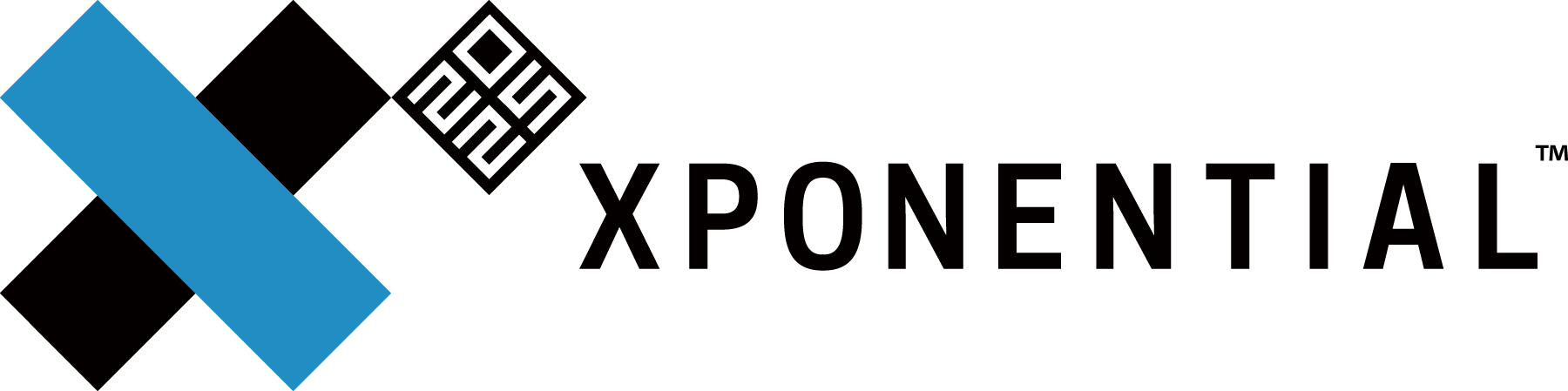
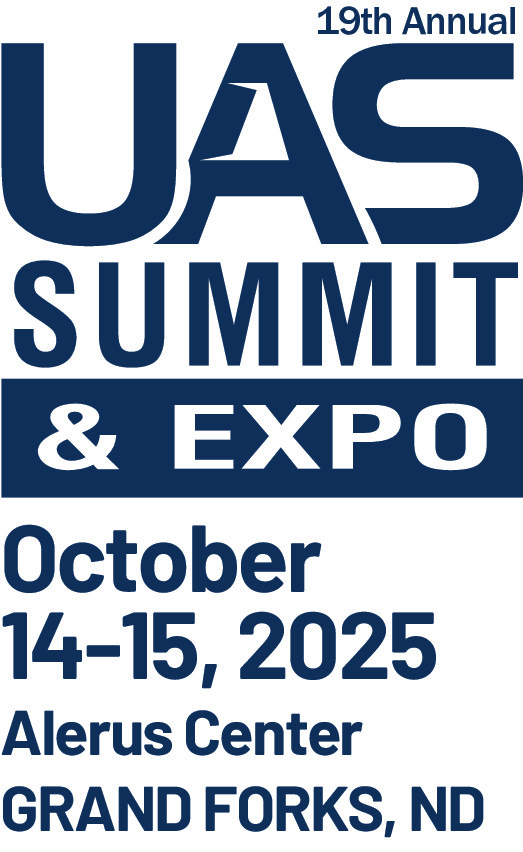
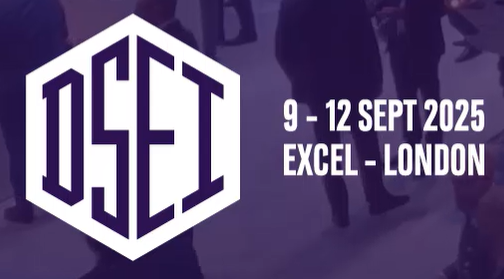
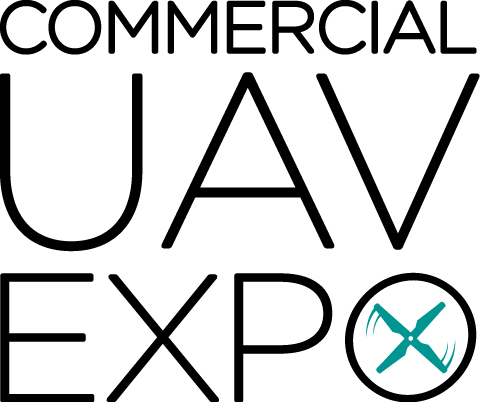
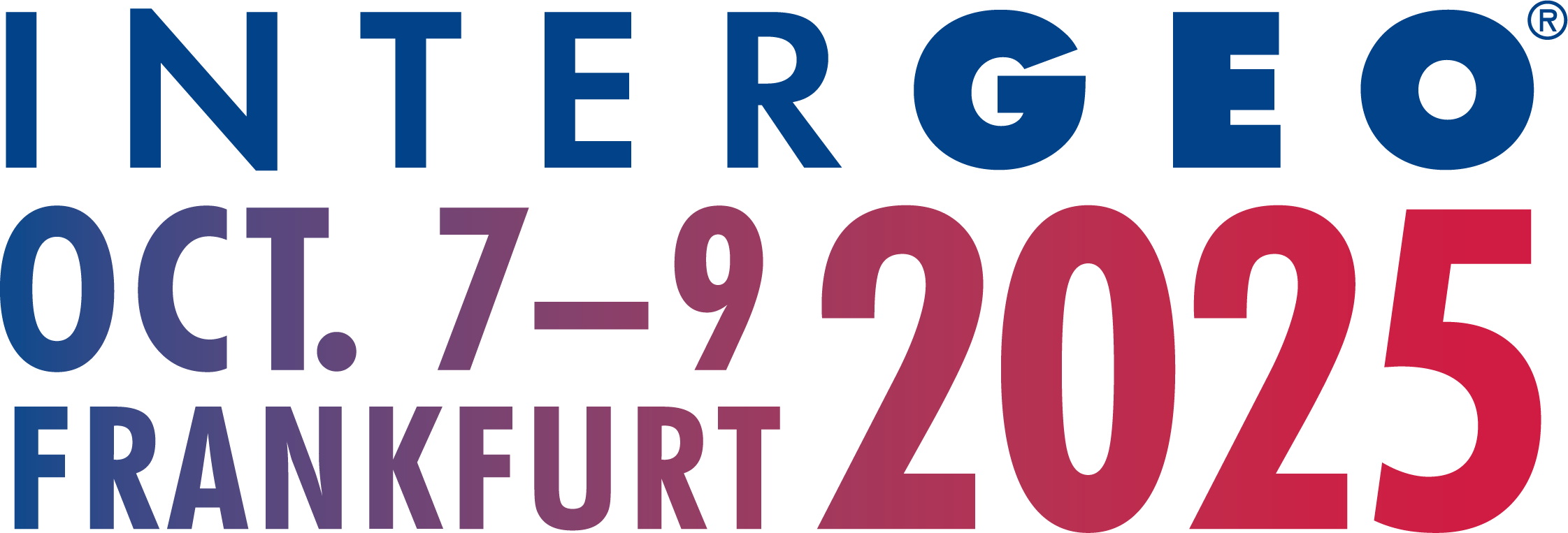
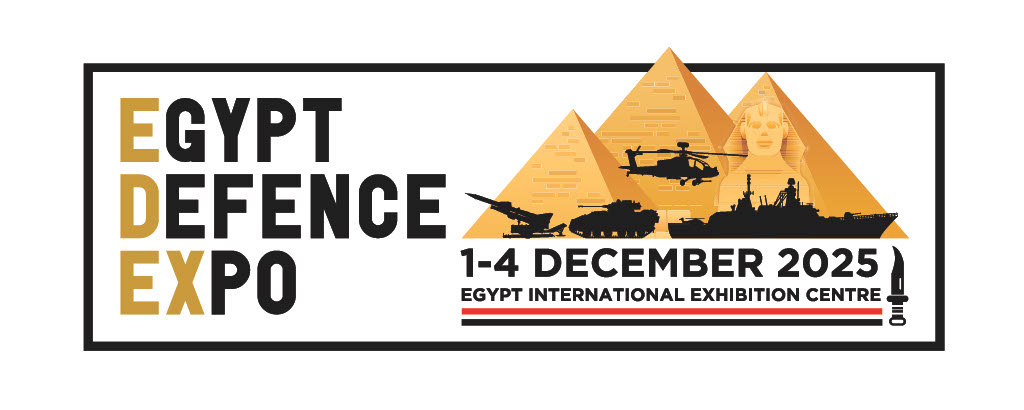
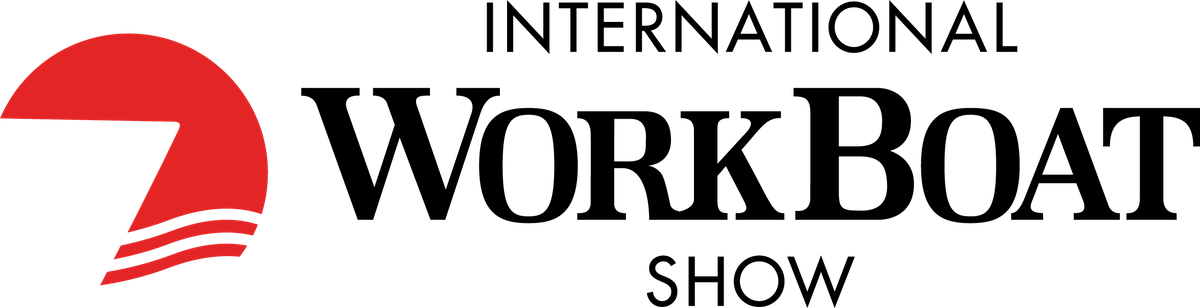
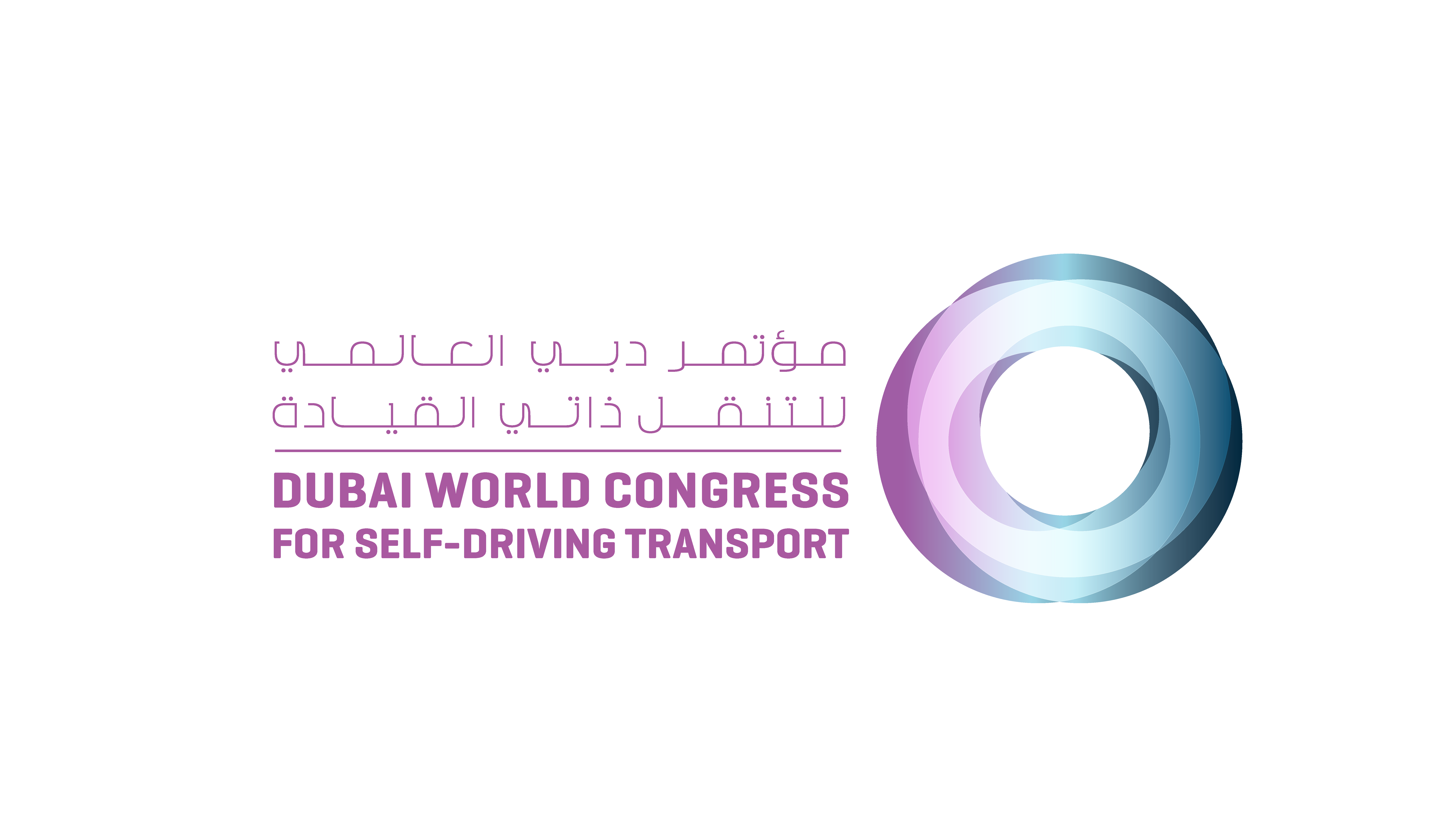
