Sonar systems
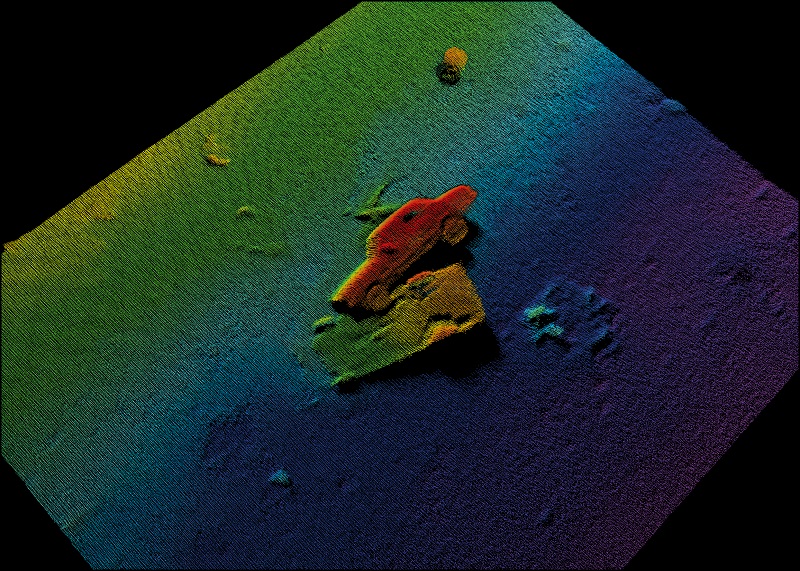
Returns on investment
Data gathered by sonar remains paramount for operators in the marine realm, and advances in the technology are offering new capabilities, writes Rory Jackson
In the world of autonomous vehicles, demand has arguably grown faster for marine systems than for any other vehicle type. Industries such as maritime asset security, ocean environmental research and offshore energy have become enthusiastic customers of USVs and UUVs, and with that has emerged a detailed understanding of what they want from their systems.
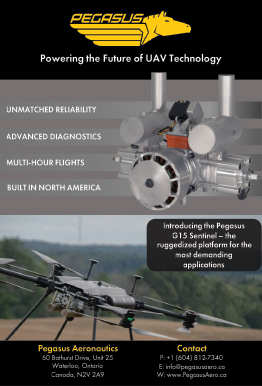
The bulk of their requirements can be summed up as ‘data’, in huge quantities and extremely fine resolutions. And although advances in underwater cameras and Lidars continue, there remains little real substitute for sonars when it comes to subsea mapping, monitoring and inspections.
Although the use of USVs along our coasts and rivers, as well as the more remote regions of the ocean, has become widespread for gathering data using sonar, the missions are usually straightforward, involving autonomous navigation along pre-planned routes and emitting pulses from their sonar payloads at a fairly constant rate throughout.
UUVs by contrast increasingly use their sonars in more active ways, given their innately autonomous nature by virtue of the fact that RF data links cannot effectively penetrate water. While UUVs can integrate many of the same subsea mapping and inspection solutions as USVs, there is a growing trend to deploy sonar for obstacle detection and avoidance, and in some cases even to achieve SLAM navigation.
Advances in forward-looking and imaging sonars are contributing hugely to this jump in UUVs’ AI capabilities, leading in turn to more USVs being developed to operate reactively to their sonar findings, such as backtracking to re-map an area where data lacked clarity or complete area coverage.
For both types of vehicle, there has been a huge growth in the range of sonar systems available, with considerable effort going into SWaP-C optimisation. This has been accompanied by a fast-growing availability of small, cost-effective UUVs (particularly micro-AUVs), as well as easily deployed USVs designed to integrate one small sonar payload, and very large USVs intended to travel for weeks or months at a time while packing as many survey instruments as possible into their hulls.
This boom in the supply of uncrewed marine vehicles has made ocean data more accessible than ever. At the same time, a lot of effort has gone into engineering sonars to provide cleaner, higher-resolution data without relying on excessively large arrays. While data quality can in theory be improved by carrying out more post-processing, the demand for data these days is such that customers can no longer wait for that to be carried out.
Enhancing sonars through a better understanding of acoustics, improved transducer and hydrophone designs, and the latest FPGAs and DSPs therefore provides more and better data, and greatly accelerates the speed and efficiency at which the oceans can be studied and modelled.
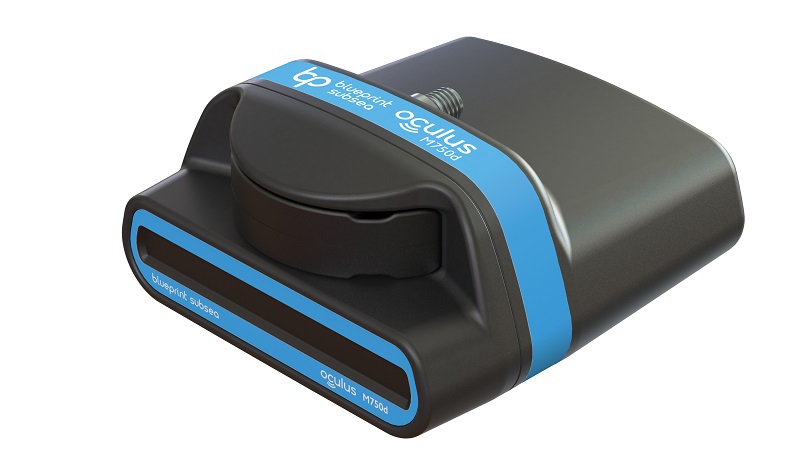
AI in bathymetry
Multi-beam echo sounders (MBEs) have grown in popularity compared with sidescan sonars among users of bathymetric surveys. That includes commercial customers building seafloor maps for construction or geophysical analysis, and defence users engaged in mine countermeasures or anti-submarine monitoring.
Reasons for this include the ability of MBEs to gather directional information from reflected soundwaves via beamforming, as well as the more complete mapping they provide (typically in a fan shape beneath the vehicle) than sidescan sonars, which in most configurations do not show what is directly beneath the vehicle.
Some newer sidescan sonars are designed to compensate for this mechanically, but developing a new sonar typically takes at least 5 years, making it hard for sonar engineers to react to market trends with newly optimised architectures of sonar products.
Being typically downward-facing, with no blind spots in acoustic measurements other than shadows created by objects on the seafloor, MBEs have been able to outpace advances in sidescan sonars to an extent by complementing their architectures with an array of new AI capabilities powered by advances in computing power and digital signal processing.
As mentioned, USVs are being engineered with greater reactivity to their sonar data. One new trend in some sonar designs that is helping to allow this is automated tracking and control via sonar readings, not only of the USV but of the sonar itself.
Traditionally, crewed survey vessels would use an online surveyor to track the health and telemetry readings of every payload sensor on board, all of which had to be constantly optimised, be it for power output, coverage, range, frequency or other parameters. However, the optimisations would rarely be based on the sonar (or other sensor data) results obtained, but on look-up tables instead.
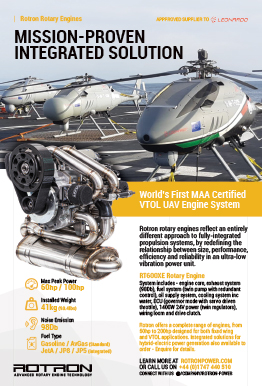
Given that the quality of real-time data from sonars has improved greatly over the past few years, some developers have recognised that this presents an opportunity for the sonars to control themselves. By examining their own acoustic pulse returns and seeing whether initial results indicate sufficient levels of detail for actionable 3D models for the end-user, the sonar can determine – by itself or using a companion computer on the USV – whether to alter the power it is using for scanning.
It can even do so digitally, which means for instance that it could calculate a precise figure for the optimal frequency based on its acoustic returns. For example, it could choose 217 kHz, whereas older analogue control systems on crewed survey vessels might have been limited to sliders preset to choose figures such as 210, 220, 230 kHz and so on.
That feature can be less important for UUVs, as they are not constrained to the ocean surface as USVs are. However, USVs remain a less expensive option for many users, and also come with operator benefits such as real-time monitoring and analysis of survey data as well as in-the-loop control if needed.
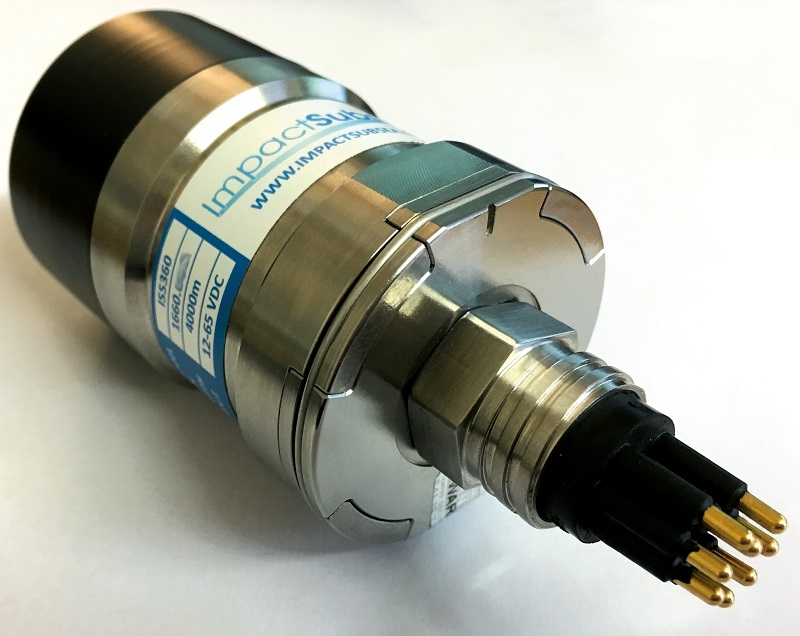
More interesting to UUVs are other AI-powered abilities intended to make better use of their close-up survey capabilities, such as automatic pipe detection and tracking. Advances in machine learning (ML) have accelerated the development of algorithms for UUV computers to recognise structures such as oil pipelines or similar structures that need regular high-resolution inspections in their 2D and 3D sonar imagery.
In addition, recognising a pipeline enables onboard processors to track along its length. While it might be assumed that surveying a pipeline is a simple matter of plugging waypoints with their approximate depths and coordinates into a UUV’s GCS planner, it actually leaves such surveys as open-loop operations with no real-time checking of whether the UUV is surveying the way its owner wants it to.
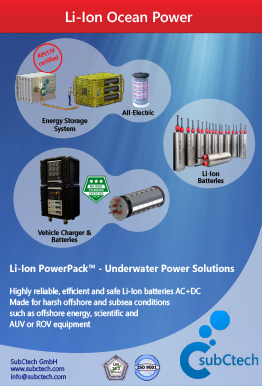
In reality, the acoustic waves from a sonar suffer reflections or distortions upon contact with many pipe surfaces, owing to the metals, concrete, plastics and resins used in their construction, which vary with the pipe’s inclines, twists or other directional and shape changes along its length. That introduces unclear details about pipeline inspection data, with sections of the pipe seeming to show blurring or otherwise erroneous imagery such as areas that are actually above, below or further along the pipe than the section being viewed.
One last area worth considering is the active stabilisation of sonars. Much as UAV camera gimbals need to be able to correct for vibration and movements of their platforms, sonars – particularly on large USVs – will be swayed to and fro by waves and currents, which will have an impact on how beam densities are distributed over survey targets if they are not corrected for.
Wind farm inspections in particular tend to have very strict survey specifications, often with a set number of ‘hits per cell’ or points per grid square of the area to be surveyed. If the action of waves is causing a vessel to heave, roll, pitch and yaw, the hits will naturally be excessive in some cells and insufficient in others.
Roll stabilisation is nothing new: when the INS reports that its USV has rolled 5o to port, the sonar can be commanded to alter its angle by 5o to starboard. Only more recently however have pitch and yaw stabilisation also been tackled by sonar developers, with greater understanding of how the transmit and receive arrays must be controlled in order to mitigate the effects of weather bucking the vessel in these axes.
Forward-looking sonar
The use of sonars in a forward-looking capacity, rather than the downward-looking integrations typical of bathymetric surveys, is traditionally tied more closely to autonomy and AI than actual mapping work, as their intended use case has been to scan ahead so that a USV or UUV can clearly see rocks, reefs, or other seabed features that represent a collision hazard.
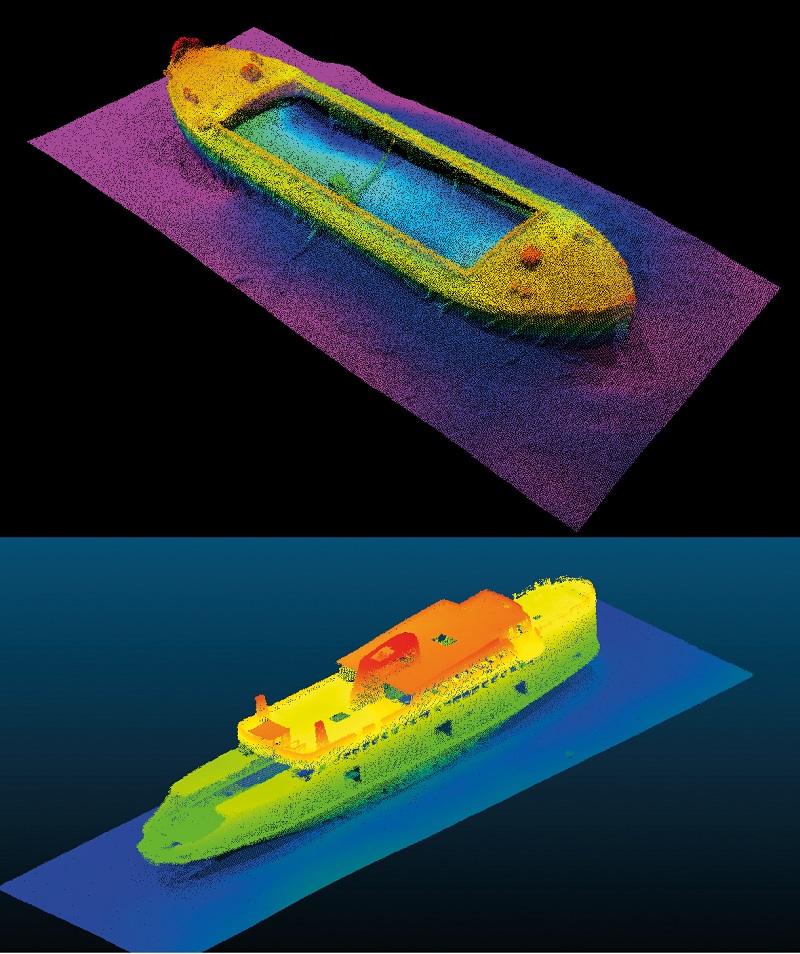
Naturally, this is more important for UUVs, as they operate closer to the seafloor than USVs, and are thus at greater risk of being lost through collisions with such obstacles. Nowadays however, most forward-looking sonars are less powerful and have a smaller form factor than those used in bathymetry.
Highly SWaP-optimised imaging sonars are used increasingly in 100-200 kg UUVs and 3-25 kg micro-AUVs alike, to enable real-time forward obstacle detection and avoidance as well as a limited degree of mapping in the water column in front of the UUV, particularly as it dives down to the seabed. That can provide actionable data for some users, on top of enabling the UUV to reactively plan out a survey or avoidance path of the seafloor ahead.
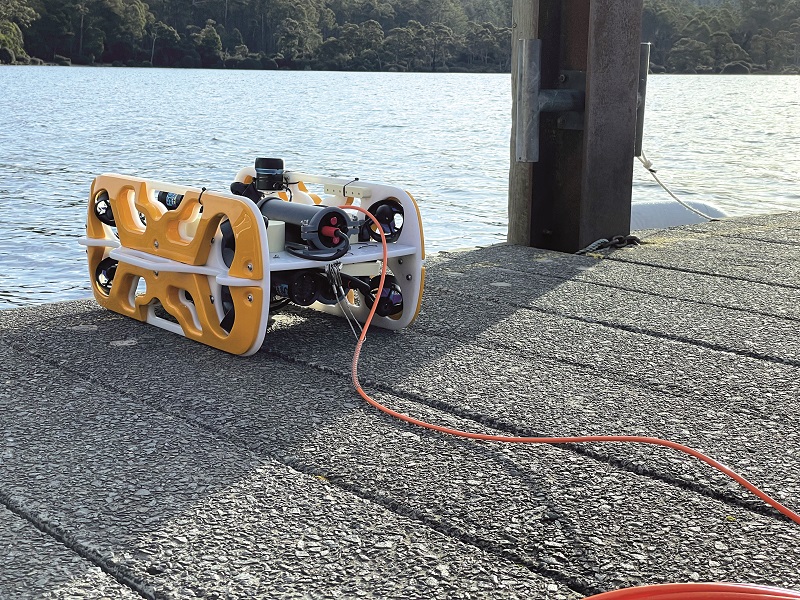
Imaging sonars used in this way are often around 100-200 mm in length and diameter, and consume about 20-30 W, to scan with 1o horizontal beam widths at frequencies of 400-900 kHz. Probably the smallest in the world at the moment weighs about 0.3 kg and consumes up to 240 mA at 24 V, and can operate at depths of 6000 m.
By contrast, the new breed of 3000-plus kg XLUUVs being built for upwards of 2000 km range might incorporate forward-looking sonars that are more than a metre in length and emit pulses at ultra-low frequencies in order to see objects almost a kilometre ahead. While higher frequencies would yield sharper images, long-range detection is critical for defence missions such as subsea border monitoring and asset protection, as well as for surveys in polar regions where icebergs or ice shelfs are unmapped and so represent critical safety hazards to vessels.
Some particularly advanced forward-looking sonars can even use a combination of interferometric and Vernier processing to map out the seabed terrain ahead of the UUV as it moves parallel with the seafloor. Real-time data outputs include vertical height discrimination of targets ahead of the sonar.
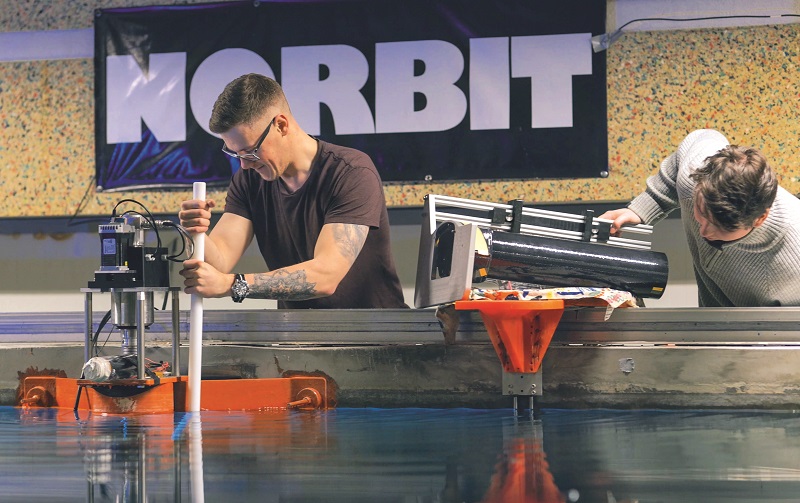
Such systems incorporate sub-arrays in configurations that allow switching between a 3D mode to enable bathymetric terrain mapping ahead of the uncrewed vehicle, and a 2D high-resolution imaging mode that can acoustically inspect features of interest in greater detail.
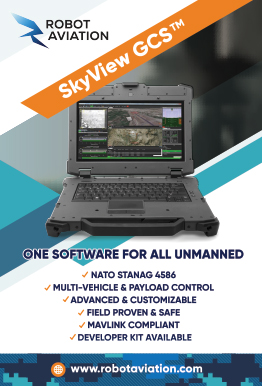
At the time of writing, military users were integrating this technology into their UUVs in order to perform simultaneous forward-looking obstacle avoidance and forward-looking terrain mapping, and the technology could soon be used to power high-level autonomous behaviours such as underwater SLAM.
A key area of further development of forward-looking sonars in the near future will be the application of ML for real-time object detection and classification, as is being done with some bathymetric sonars, for instance to better recognise objects such as mines, minerals or potentially hostile UUVs. Autonomous sonar survey missions could soon be regularly gathering thousands of terabytes of data per day though, which represents something of a bottleneck in terms of how best to process it in order to support decision-making by their operators.
ML will therefore be critical for designing computer-aided detection capabilities into marine autopilots (or sonar computers) so that uncrewed sonar platforms can zero in on items that are of interest to their operators. However, open-access sonar data libraries for training algorithms to enable such intelligence are scarce, so it falls to vehicle and sonar companies to amass and organise such data themselves in order to gain that next-level edge in forward-looking survey and inspection.
Sonar hardware
On top of these software enhancements, echo sounder architectures are improving to the point that beam widths as fine as 0.5o are commercially available in systems that are SWaP-optimised enough for integration into micro-AUVs and small USVs.
There is a demand for such ultra-high spatial resolutions from military as well commercial operators, although which customers prefer 0.5o beam widths over, say, 1o or 2o systems is unclear. In essence, however, the primary consequence of this higher resolution is an improved capability of target detection, by being able to distinguish between two or more objects at the 0.5o level.
For asset owners who need to inspect their pipelines, wind farm foundations and other critical infrastructure, such improvements in spatial resolution are vital to identifying microfractures, joint wear and similar signs of wear in potentially murky environments, particularly where biofouling and shadows could render even highly illuminated camera imagery and underwater Lidar effectively useless for spotting where maintenance and repairs are needed most.
Transducer design is a critical part of the continuing refinement of sonar hardware, as they are the systems by which electrical signals are transformed and emitted as sound waves, making them in many ways one half of the operative part of a sonar.
Advances in transducer engineering are particularly important for MBEs, which need transducers capable of ever-higher power levels and which can be precisely directed. The latter entails building a transducer to transmit pulses in a stable manner, so if the transmission is not robust enough to withstand being altered over ranges of temperature and pressure, it will inevitably fall short of the requirements of UUV and USV customers who increasingly want to be able to operate in environmental extremes such as 6000 m below sea level or in polar climates.
Transducers are only half of the equation for sonar mechanical design though; hydrophones are the other. As a hydrophone is essentially an underwater microphone, optimising it for sensitivity is the key to having it detect the specific sound waves and frequencies from the transducer, without interference from electrical or other sources disturbing the information in the received waves.
Some modern hydrophones can detect sounds that are quieter than those generated by a sea state of zero, where only thermal ‘noise’ (from Brownian motion of seawater particles) is present, as well as being able to detect across very broad bandwidths. Some for instance can be used to detect sound waves from just a few Hertz up to 100 kHz, while others can detect at more than 1 MHz.
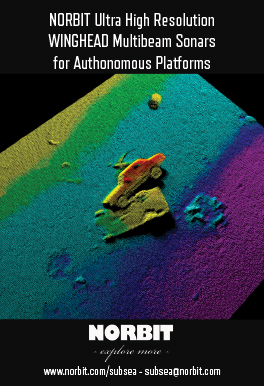
Although these two main components form the transmit and receive arrays of sonars, not all sonars are built as two-array systems. Some modern systems are able to use hydrophones to transmit as well as receive sound, while some more powerful architectures are increasingly key to enabling high-power transmissions while still sensing high densities of low-power wave returns on the receive side.
In addition to the core subsystems essential to any functional sonar, more and more solutions come packaged with other essential technologies for conventional geospatial surveys. For instance, some bathymetric echo sounders integrate GNSS and inertial systems, connected typically by just a single wet-mate link.
A crucial aspect here is the ongoing miniaturisation of INSs – that is, a fully packaged GNSS, IMU and processors – to enable them to fit inside a sonar package, dramatically improving the simplicity of integration.
Also, fitting an IMU directly on the sonar head, as opposed to standard integrations in USVs and some UUVs where the GNSS-IMU is installed some way away from the sonar, minimises the number and lengths of cables needed, and reduces the chances of error sources being introduced through separate integrations.
For instance, if an INS’ mount starts to come loose during a long-endurance mission, or if the two are installed at each end of a vehicle and experience different motions relative to a given target, these and similar issues could hamper the stitching and processing of sonar imagery.
Pre-planning and post-processing
The ongoing push by sonar developers for simplicity for end-users has driven some to work towards integrating sonar control software with that for configuring ancillaries such as GNSSs or INSs, to prevent errors in customers’ installation methods. That has helped smaller companies or research groups when they try to adopt autonomous hydrographic survey vehicles, as these will often lack specialist engineers for integrating their systems in-house.
On top of that, software tools are as important as ever for ensuring that the data is made available quickly and in high quality, easily accessible and actionable packages. Among these are lightweight data acquisition tool sets that generate easily digested displays of data, along with monitoring and tracking of survey information with vehicle and subsystem telemetry.
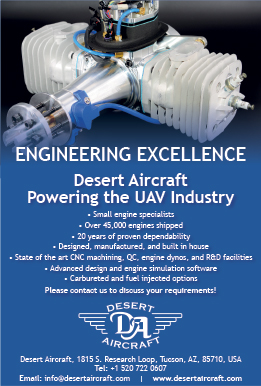
This blending of informational and control systems is expected to continue, with many open-source geospatial and hydrographic tools now being used to create portals for persistent data flows between ocean vehicle assets and surveyors’ offices.
By integrating autonomous sonar platforms with geospatial platforms and cloud servers, remote analysis of ocean data can be carried out in fine detail for each vehicle, wherever they are, even over very low bandwidth connections.
Conclusion
Accessibility and simplicity of marine data analytics is critical across all the supporting technologies for sonar, and companies who can achieve that will find no shortage of interested parties in the maritime sector.
UUVs are on the cusp of being widely deployed as resident systems in remote ocean assets, where they will periodically survey complex infrastructures such as subsea cables, energy installations and structural foundations, in constant exposure to harsh environmental conditions.
This will put sonars to the test in terms of reliability over time and mean times between failures, as they undergo operations at depth and over durations never before weathered by uncrewed vehicles in real-world conditions. Whichever sonar systems can operate for the longest before needing maintenance could prove themselves indispensable.
Acknowledgements
The author would like to thank Simon Barchard at Teledyne Marine, Tom Broomfield at Norbit, James Colebourn at Blueprint Subsea, Ben Grant at Impact Subsea and Rustom Jehangir at Blue Robotics for their help with researching this article.
Some examples of sonar system suppliers
AUSTRALIA
CEE Hydrosystems | +61 2 9482 5880 | www.ceehydrosystems.com |
Sonar Technologies | +61 2 9630 3533 | www.sonartechnologies.com |
CANADA
Aquatic Sensors | +1 800 894 2695 | www.aquaticsensors.com |
Aquacoustic Remote Tech | +1 604 730 8117 | www.aquacoustic.com |
Imagenex | +1 604 944 8248 | www.imagenex.com |
Nautel | +1 902 823 3900 | www.nautel.com |
Shark Marine Technologies | +1 905 687 6672 | Thales |
DENMARK
EIVA | +45 86 28 2011 | www.eiva.com |
Teledyne Marine | +45 47 38 0022 | www.teledynemarine.com |
FRANCE
ITER Systems | +33 9 72 45 73 30 | www.iter-systems.com |
RTSYS | +33 2 97 89 85 80 | www.rtsys.eu |
Thales | +33 4 75 79 85 11 | www.thalesgroup.com |
GERMANY
Atlas Elektronik | +49 421 457 02 | www.atlas-elektronik.com |
ELAC SONAR | – | www.elac-sonar.de |
Evologics | +49 30 4679 862 | www.evologics.de |
KOREA
Echologger | +82 2 3158 3178 | www.echologger.com |
INDONESIA
Sonar Nusantara | +62 821 1118 0598 | www.sonar-nusantara.co.id |
ITALY
Leonardo Electronics | +39 06 324 731 | www.electronics.leonardo.com |
ISRAEL
DSIT Solutions | +972 3 5313333 | www.dsit.co.il |
NORWAY
Kongsberg Maritime | +47 81 57 37 00 | www.kongsberg.com |
Maritime Robotics | +47 73 40 19 00 | www.maritimerobotics.com |
Norbit | +47 98 28 37 53 | www.norbit.com |
UK
Aquatec | +44 1256 416010 | www.aquatecgroup.com |
Blueprint Subsea | +44 1539 531536 | www.blueprintsubsea.com |
C-MAX | +44 1305 853005 | www.cmaxsonar.com |
Coda Octopus | +44 1315 531380 | www.codaoctopus.com |
Impact Subsea | +44 1224 460850 | www.impactsubsea.co.uk |
L3Harris | – | www.l3harris.com |
Neptune Sonar | +44 1262 490234 | www.neptune-sonar.co.uk |
Ocean Acoustic Developments | +44 1288 361652 | www.oadltd.com |
SEA | +44 1271 337500 | www.sea.co.uk |
Sonardyne International | +44 1252 872288 | www.sonardyne.com |
Tritech International | +44 1224 744111 | www.tritech.co.uk |
Ultra Maritime | +44 2088 134321 | www.ultra.group |
Wavefront Systems | – | www.wavefront.systems |
USA
Blue Robotics | – | www.bluerobotics.com |
Cerulean Sonar | – | www.ceruleansonar.com |
Chesapeake Technology | +1 650 967 2045 | www.chesapeaketech.com |
Edgetech Marine | +1 508 291 0057 | www.edgetech.com |
Falmouth Scientific | +1 508 564 7640 | www.falmouth.com |
Klein Marine Systems | +1 603 893 6131 | www.mind-technology.com/klein |
Kraken Robotics | +1 709 757 5757 | www.krakenrobotics.com |
Marine Sonic Technology | +1 804 693 9602 | www.marinesonic.com |
MASSA | +1 781 749 4800 | www.massa.com |
R2Sonic | +1 512 891 0000 | www.r2sonic.com |
Raytheon | +1 781 522 3000 | www.rtx.com |
Seafloor Systems | +1 530 677 1019 | www.seafloorsystems.com |
UPCOMING EVENTS
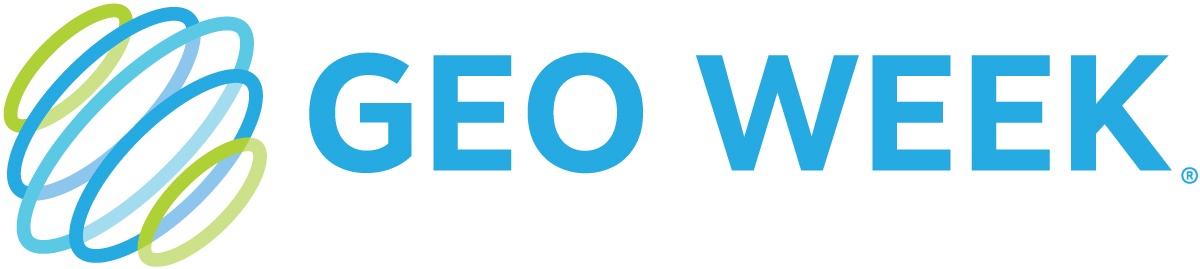
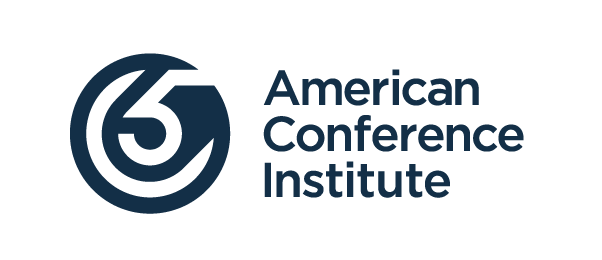
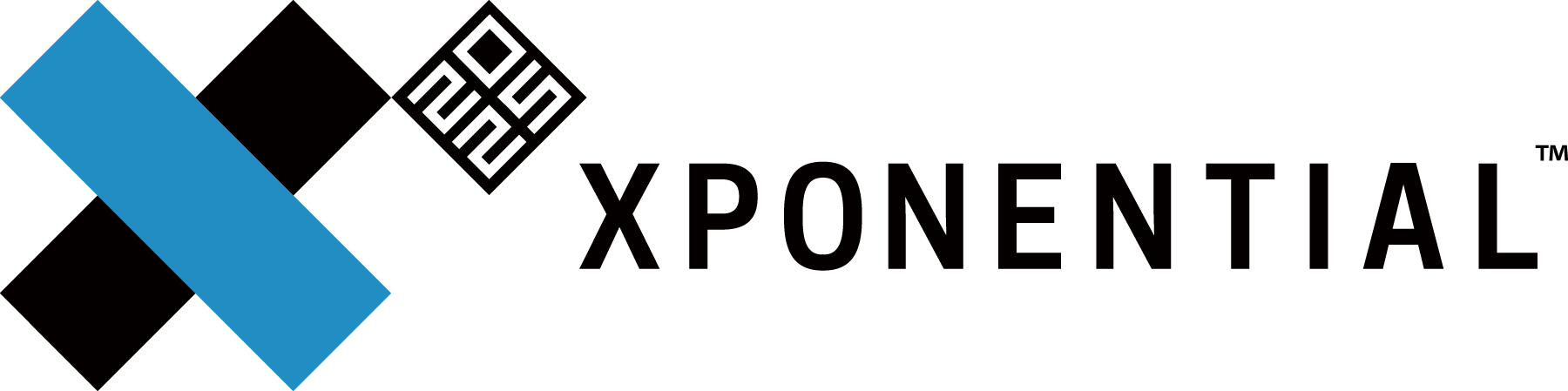
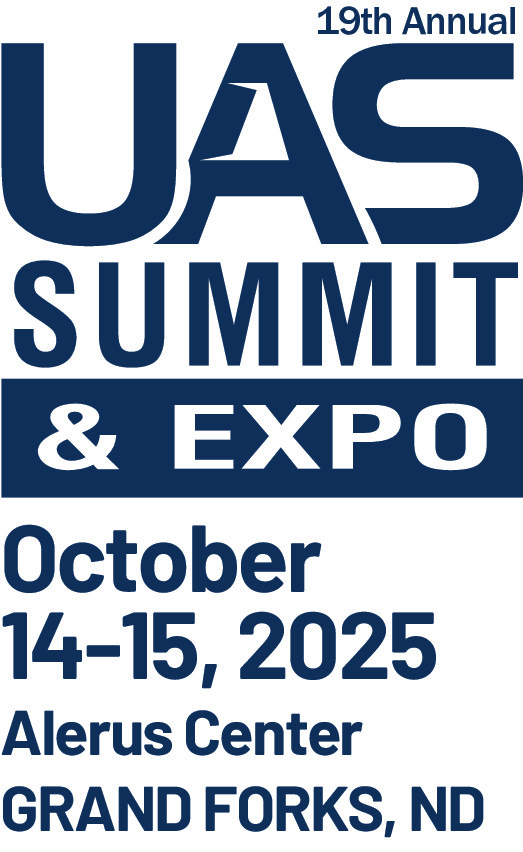
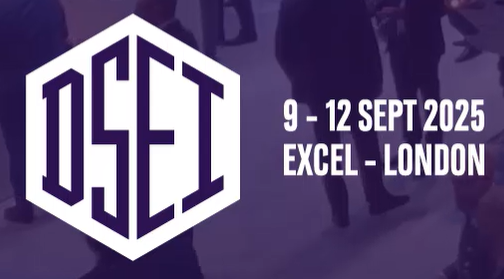
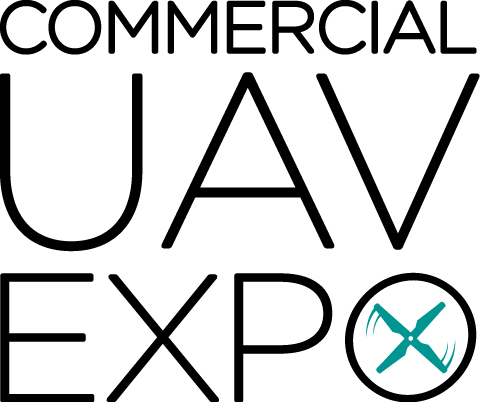
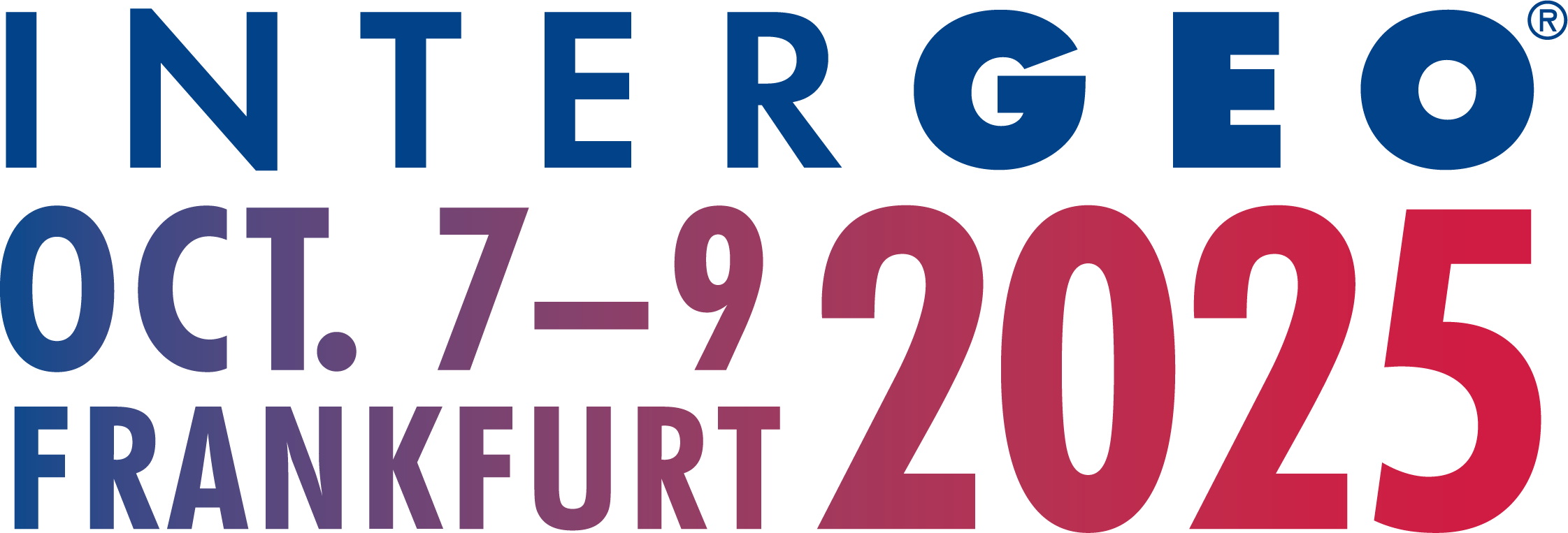
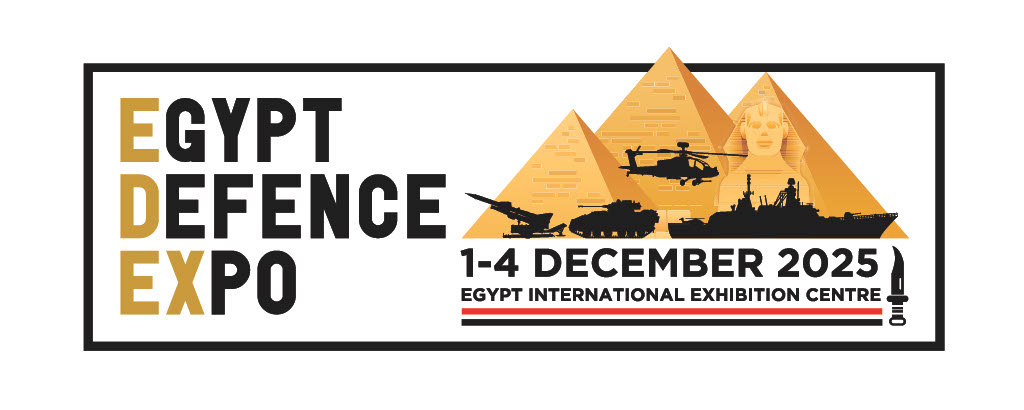
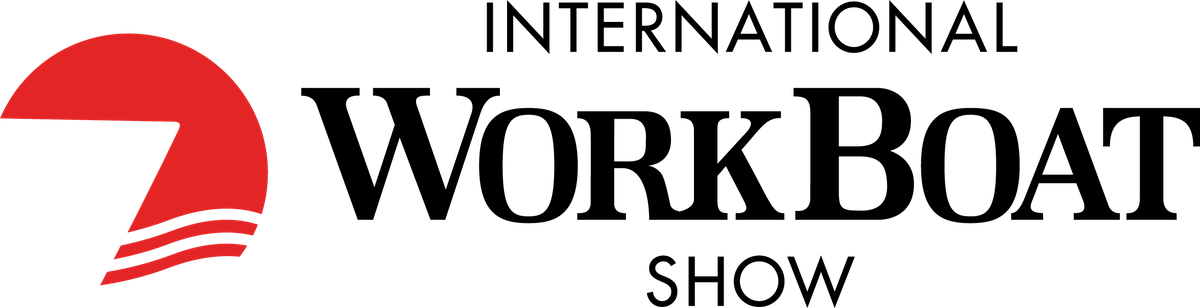
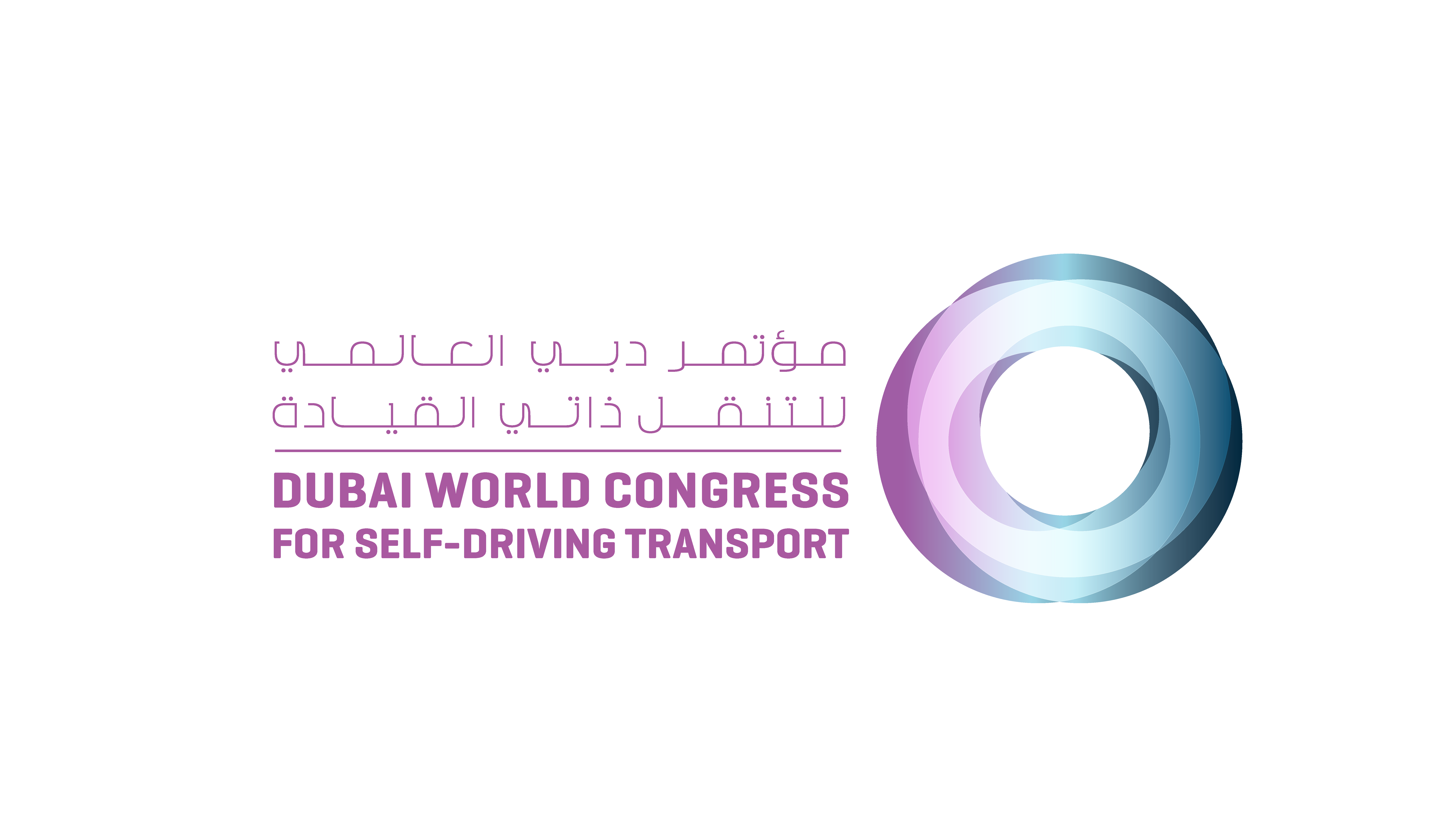
