CUAV Expo Americas 2022
Back with a bang
Rory Jackson picks out some highlights from this show, which after its pandemic-enforced hiatus drew record attendances
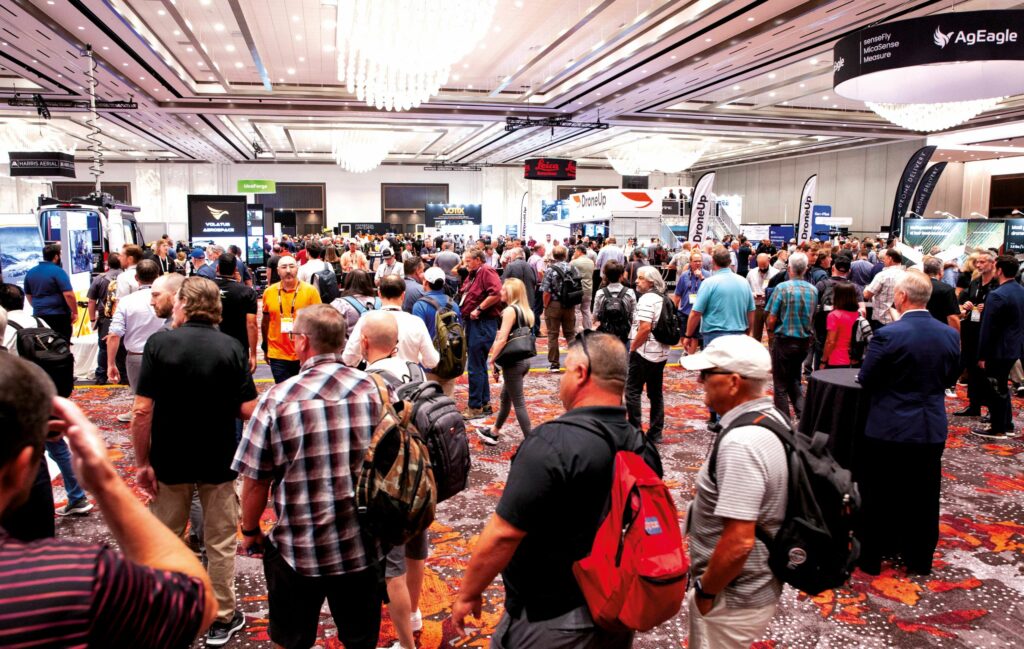
After three years of being kept away by the coronavirus pandemic, Uncrewed Systems Technology returned to Las Vegas for the Commercial UAV Expo Americas from September 6 to 8.
This year’s show set new records. It hosted 232 exhibitors and 3405 verified professionals, as well as more than 4100 registrants from 60 countries and 48 US states – a hefty increase over pre-Covid attendance figures.
Eager to show their r&d from the past few years, exhibitors and attendees alike pitched and discussed a plethora of new uncrewed systems and subsystems across the show floor at Caesar’s Forum, a selection of which follows here.
Flyability showcased its Elios 3, the latest iteration of its cage-protected indoor inspection multi-rotor. The system was unveiled earlier this year, is available for pre-order, and is expected to start shipping within the next few months.
“The third-gen system has a few noticeable differences versus the older Elios 2,” said Zacc Dukowitz. “The biggest thing is that it now has a Lidar mounted, an Ouster OS0-32, which allows 3D modelling.
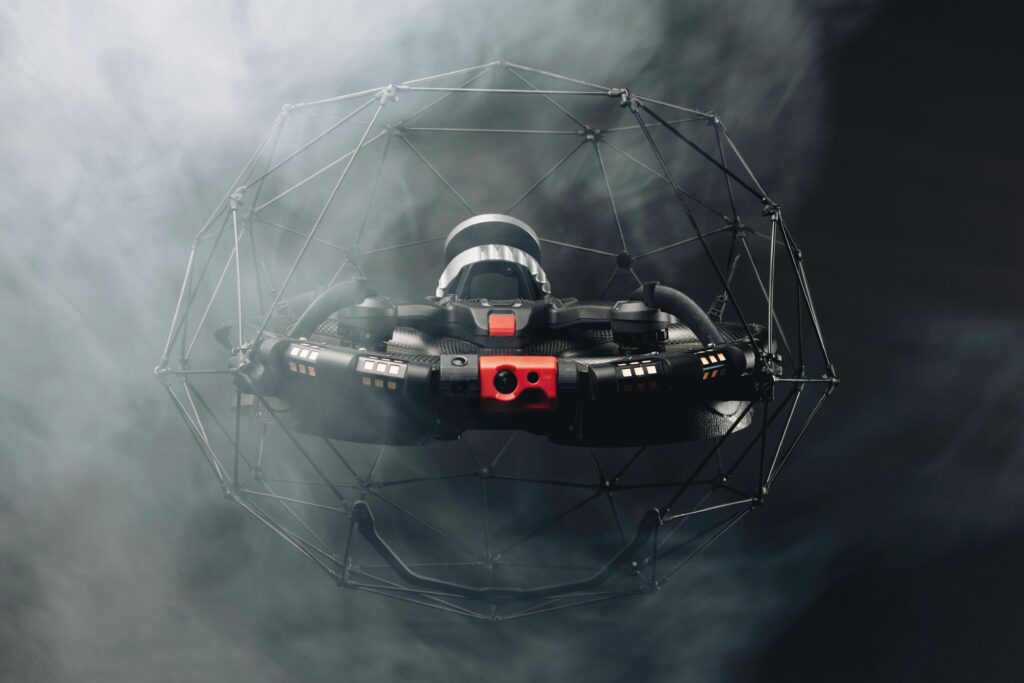
“The UAV is flown using Flyaware, a proprietary SLAM engine, so it uses the Lidar data to navigate and sit still with better stability than our previous aircraft. That also means the 3D world model is being constructed in real time, visible to the GCS and enabling operators to locate the UAV no matter where it is in the asset they’re inspecting or mapping.”
The Lidar data can also be post-processed for survey-grade analytics via GeoSLAM Connect.
The Elios 3 has an MTOW of 2.5 kg and a flight time of just over 9 minutes with the Lidar payload installed. It runs on an Nvidia Xavier NX computer running a Linux OS, and is powered by a 6S, 99.2 Wh lithium-polymer battery.
“And while the carbon-Kevlar cage has been kept mainly the same, the propellers are now ducted, which helps direct dust through and away from the fans,” Dukowitz added. “The Elios 2 would create something of a dust cloud in some of the industrial facilities it was used for surveying in.”
Riegl attended to showcase a variety of its latest high-power Lidar solutions, including the miniVUX-3UAV, VQ-840-G and the VUX-120.
“The miniVUX-3UAV is Riegl’s most robust, compact, cost-effective, miniaturised Lidar sensor for UAV integrations. It has a maximum pulse repetition rate [PRR] of 300 kHz, which is effective for a field of view [FoV] of 120º,” said Abby Clark. “The operator can also reduce the PRR to 100 kHz to expand the FoV to 360º.
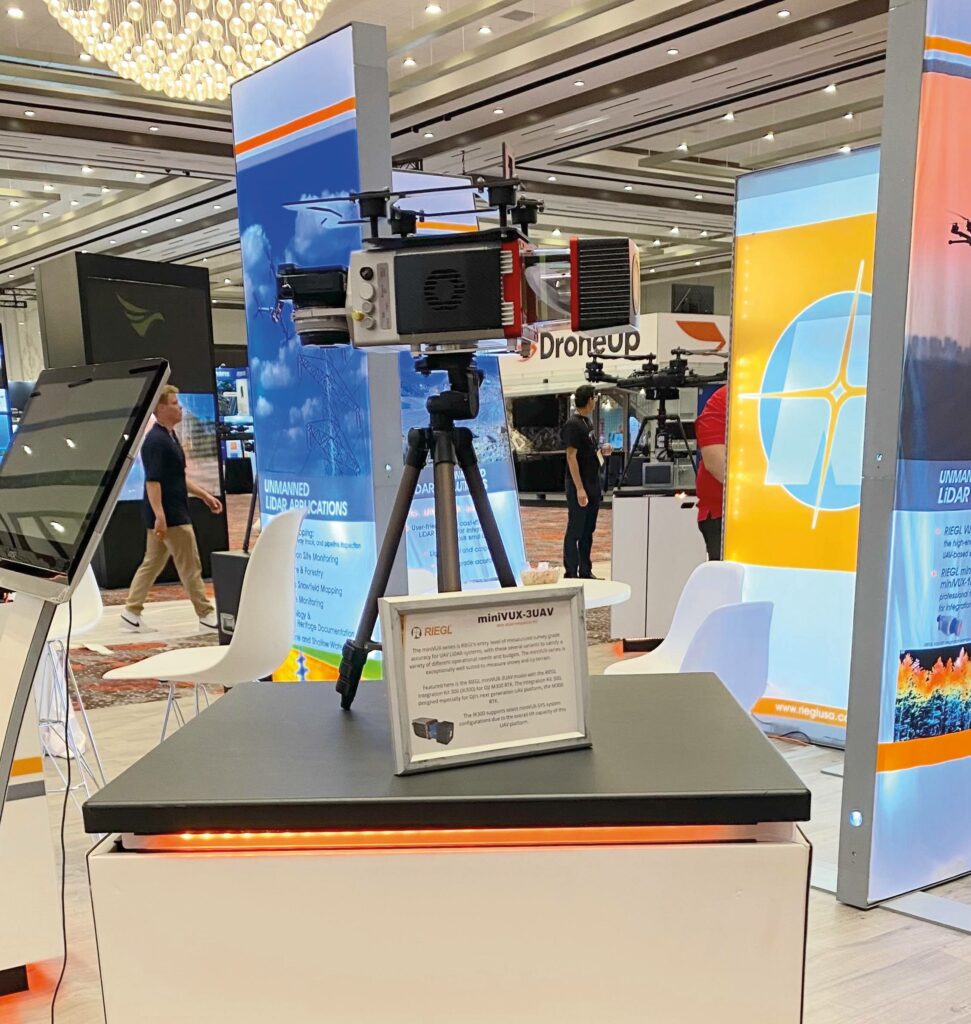
“The VQ-840-G is on display at the show fitted to the Harris Aerial H6-HL heavy-lift UAV platform, as Riegl’s compact topo-bathymetric Lidar system for larger UAVs and helicopter integrations. Its green-channel laser wavelength of 532 nm is key for penetrating water and measuring submerged objects, down to depths of 2.5 secchi [a measure of water transparency].”
The smaller miniVUX-3UAV weighs 1.6 kg and consumes 18 W when performing 100 scans per second. The VQ-840-G weighs 12 kg in standard configuration, or 15 kg if the optional GNSS-IMU as well as camera (or IR rangefinder) modules are selected, and consumes up to 220 W.
uAvionix presented its new muLTElink solution, which is a data link manager with a built-in LTE radio for UAV command and control (C2).
“It is designed to integrate seamlessly with, and intelligently switch between, multiple C2 radios simultaneously,” said Cyriel Kronenburg. “By that we mean it will effectively determine from all the open links available which is the most optimal and safety-reliable that should be used for controlling or monitoring a UAV.
“The LTE radio is network-agnostic: it uses an eSIM so it will work with any LTE network. It keeps that LTE link on permanently at the same time as any C2 link it has selected.”
The system simplifies and automates the process of radio selection for improved comms autonomy in uncrewed systems, a process that is otherwise usually a very manual and burdensome one for mission operators.
Commaris attended the expo to exhibit its flagship Seeker UAV, a VTOL-transitioning craft with fixed twin-boom mounted quadrotors and control surfaces mounted on its wings and an inverted vee-tail.
It has been designed around missions requiring long endurance with relatively light payloads, such as mapping, surveys and surveillance,” said Jason Daub. “It can fly for more than 3 hours, up to 16,000 ft above sea level, and from -40 ºC to +60 ºC.
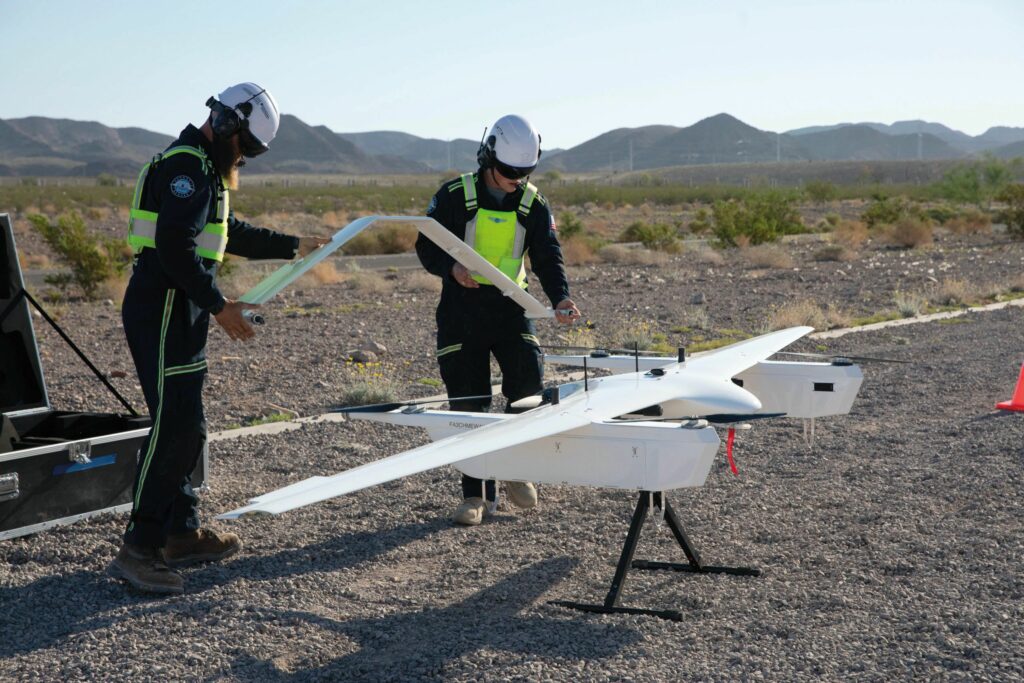
“We also demonstrated a new device called the Lifeseeker earlier this week, which is a small cellular repeater to allow search & rescue authorities to identify and find victims lost in remote regions via their cell phones.”
The system runs on HV batteries (4.35 V per cell) with larger nacelles than traditional airframes for storing packs close to the electric lift motors. Up to 4.5 kg of payload or additional batteries can be carried, and its maximum onboard energy capacity is 32 Ah.
“As well as having the body blended with the 4.5 m wingspan for better aerodynamics during take-off, there’s a slight cant to the lift motors that further helps with aero and stability during launch and cruise,” Daub added.
Skyfish, a US-based producer of multi-rotor UAVs and 3D photogrammetry software, discussed its M4 and M6 aircraft with us, which it had on display at the show.
The M4 is our quadcopter solution for high-level, engineering-grade 3D mapping and modelling,” said Joey Libin. “While other systems can carry the Sony A7R IV camera, we worked closely with Sony to integrate that along with full control of it in our Windows-based C1 remote controller GCS.
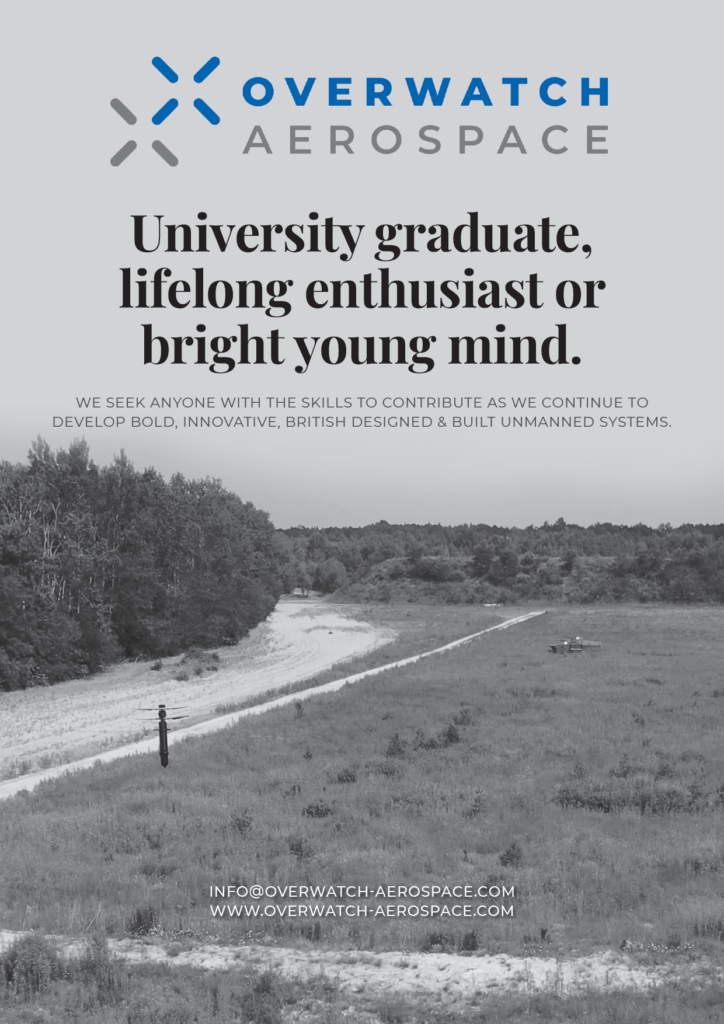
“The M6 meanwhile is our hexacopter, which can carry about 5.4 kg compared with the M4’s 2.7 kg. They both integrate the HD Sony camera, but the M6 gives the option of carrying an additional Lidar, thermal or gas sensor. We can integrate a wide range of systems using MAVLink or open source protocols.
We also have RTK capabilities on both aircraft, which can use wi-fi hotspots to gain a remote correction source, or an RTK base station supplied by us can be placed at job sites for a shorter baseline.”
In addition to in-house flight computer and software development, the company offers cloud processing of data through Skyportal, which takes the collected UAV data (aerial images) and processes them into very high resolution 3D models. These display granular details of inspected targets, such as individual threads on bolts, cotter pins and pipe thicknesses.
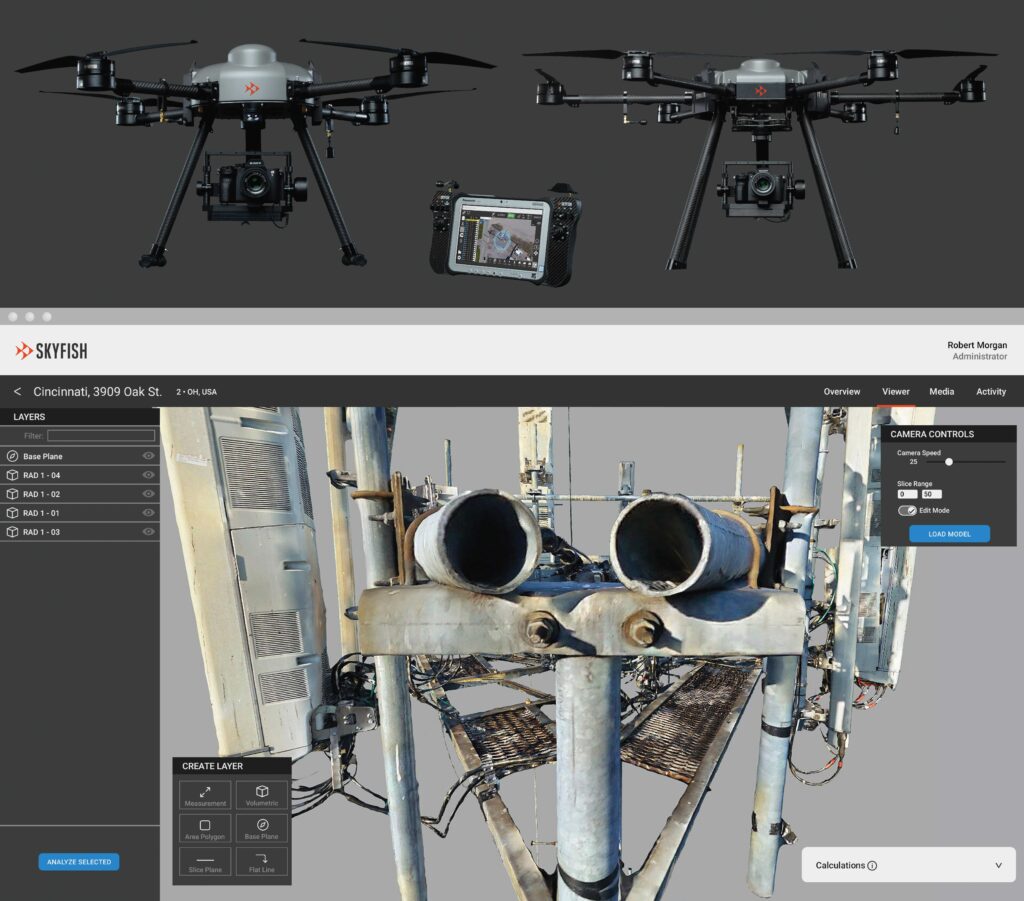
That saves end-users such as telecoms companies time by not having to manually go up and down their poles so many times,” Libin noted. “We get much better data and measurements on infrastructure far quicker than is possible with most software packages.”
Also in attendance was allocortech, which displayed its range of solutions for autonomous systems propulsion, flight control, sensing and power.
Regarding brushless motor control systems, we’re partnered with PteroDynamics [see UST 41, December/January 2022], to help with the position control of their electromechanical folding wing system,” said Brian Viele. “Their prototype designs used COTS ESCs, but they couldn’t customise them for working at different accelerations and maximum speeds, or for things like thermal management inside the controller.
Our ESCs have a whole software framework wrapped around a motor control library on a microcontroller, so we can bring in temperature sensors, run closed-loop controllers, and just customise so much for whatever a UAV needs, no matter how unique. And PteroDynamics will be able to tune that baseline software for whatever additional features or robustness they want.”
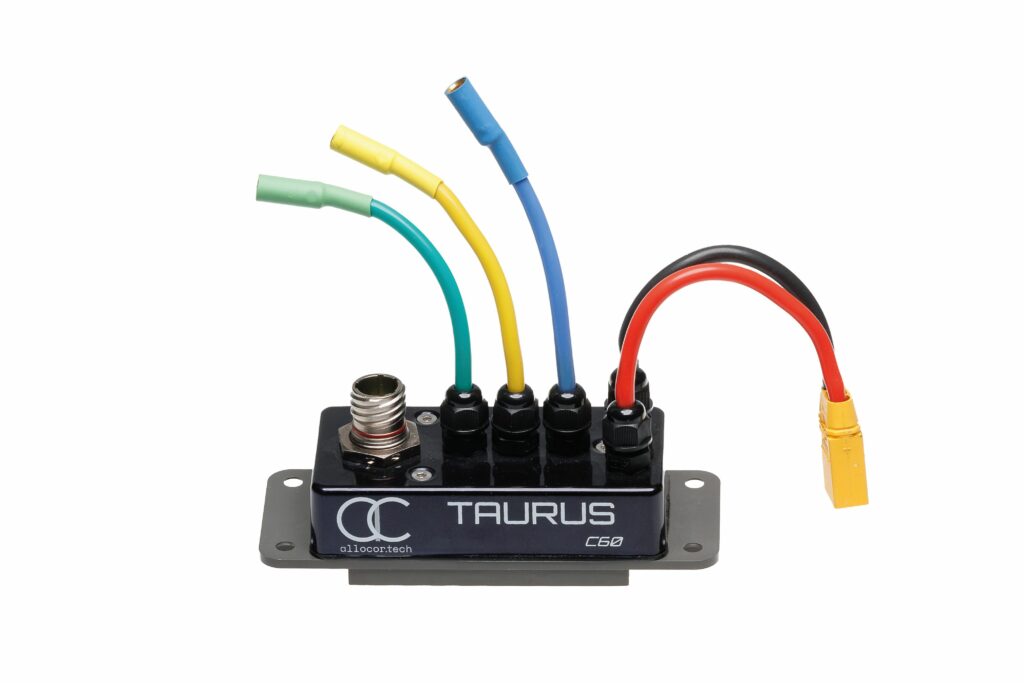
The company’s standard-issue ESC is the Taurus C60, which implements four-quadrant field-oriented control through space vector PWM, and supports overmodulation to maximise the peak power output of the motor drive. It weighs 276 g, can work on inputs from 10 to 60 V and can operate to upwards of 6 kW peak and at 4 kW sustained power.
The C60 sits in an IP67-rated housing and can be interfaced with via CAN and RS-485. It can also be custom-shaped to fit into different booms, winglets and other aircraft sections.
“Our most popular product though is probably the Clio Series B, a general-purpose computing platform with a large number of I/Os – two Ethernet ports, 11 CAN buses, 14 RS-485 ports, current monitored and e-fused load channels – and it’s a really flexible system that can be configured for many different embedded applications,” Viele added.
Using the allocore open SDK, end-users can write their own software applications on the Clio to suit their needs. “We assumed people would install it in their UAVs’ wings to interface with sensors and actuators, and connect it to their flight controllers via Ethernet or CAN, but because it has a very powerful processor we’ve actually seen a lot of customers use it as the central flight computer.”
The Clio has a 400 MHz ARM Cortex-M7 based main processor and is paired with an FPGA for flexible I/O processing. It weighs 325 g in its standard aluminium housing, although there is a composite housing option that would make the system 40 g lighter.
Sony Electronics showcased numerous UAV components produced in-house for UAS manufacturers, which had been largely developed around its Airpeak S1 UAS that was on display in the centre of its pavilion.
“We are the largest sensor manufacturer in the world, across the automotive, smartphone and other industries, so when we designed the Airpeak we did it with in-depth integration with all our sensors, processing systems and the knowledge from our robotics division, adding with that some newer r&d to create the propellers, propulsion motors and the flight controllers,” said El-Deane Naude.
The Airpeak quadrotor weighs about 3 kg and has a top speed of 25 m/s. As well as being issued with a customised Gremsy T3 gimbal that is compatible with the Sony Alpha series cameras, it has stereoscopic cameras on each of its four sides as well as downwards for visual and depth awareness of any obstacles that might come its way.
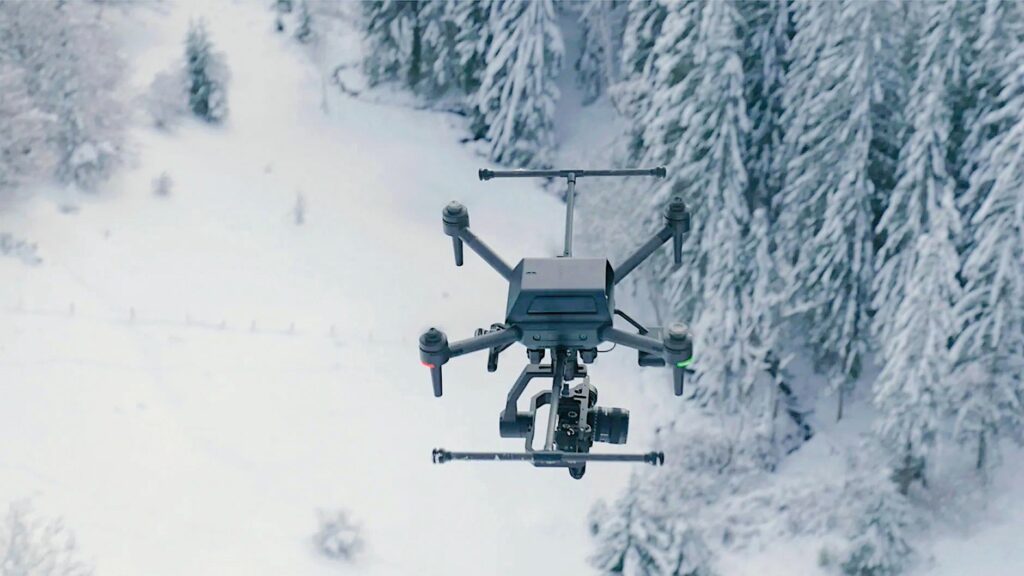
It’s ideal for survey or other hi-res work in cinematic, industrial or agricultural applications, as it integrates smoothly with any number of our Alpha cameras, including our 50 MP Alpha 1, the 61 MP Alpha 7R IV, the 12 MP Alpha 7S III, and the 30 MP Alpha 7 IV, depending on whether their application needs really hi-res 8K or 4K video, or maybe more still photo-focused optimisation,” Naude said.
In August we released a huge firmware update that greatly improves flight control and autonomy. The only part we don’t make ourselves is the gimbal, which Gremsy built to work via a single-cable connection with our system.”
Sony also announced its RTK system at the show, in which two antennas are installed on the Airpeak along with a small control module and a base station, together enabling centimetric accuracy for mapping and surveying. It also unveiled an extended-life battery with 50% more capacity and 35% more flight time for the UAV than its previous battery, as well as a battery charging station that can hold 10 packs and fast-charge four at a time.
FT Technologies exhibited its FT742-SM (Surface Mount) sensors for ultrasonic wind sensing. “We use acoustic resonance technology to build up a strong standing wave inside the cavity of our sensor, which gives us a really high signal-to-noise ratio,” said Phil Richardson. “As a result, our sensors maintain really high data availability, even in incredibly high vibration environments, which is great for any moving platform like a UAV.”
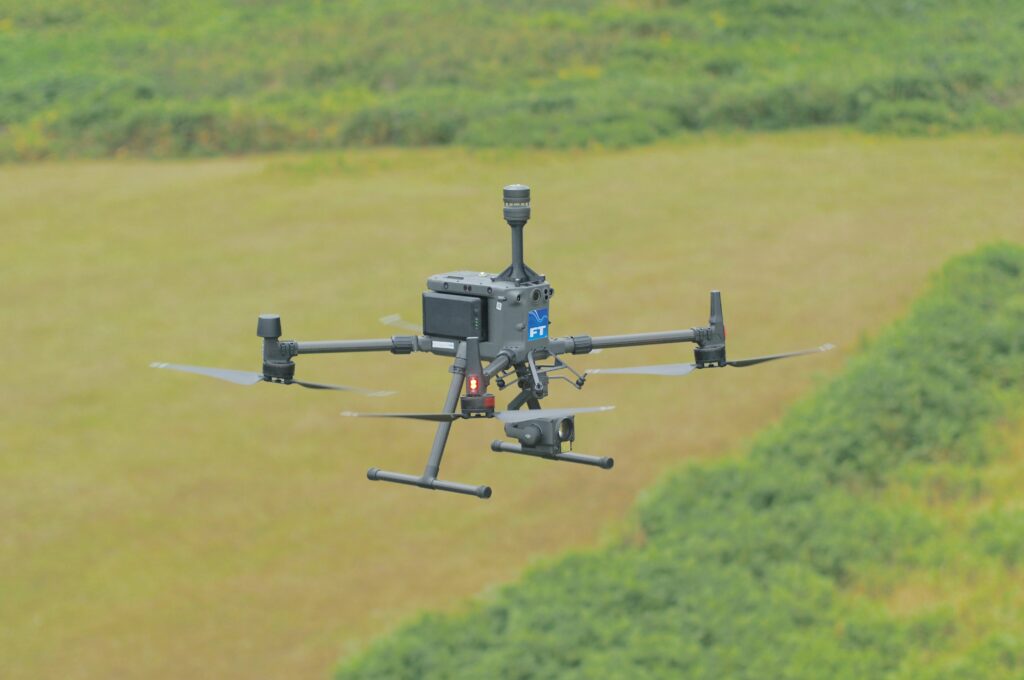
As well as being useful for fine flight control, the company notes that a range of commercial, civil and scientific applications – including atmospheric monitoring, leak detection and wildfire monitoring – could interest potential end-users. The FT742-SM weighs 252 g, is 71.2 mm in height and can measure wind speeds up to 75 m/s.
Singapore-headquartered composites company AirGo Design was also walking the aisles of the show to discuss some of the unique processes it uses in its hull and structural parts manufacturing for uncrewed systems
“Our roots are in aerospace – we made the world’s first all-carbon fibre aircraft seat to be awarded FAA approval using Atlas, our proprietary AI-assisted optimisation program,” said Patrick Muglia. “Atlas is up to 1000 times faster than conventional, homogenisation field theory-based techniques.
“Using Atlas we can predict the behaviour of discontinuous carbon fibre composites faster, more accurately and without the need for expensive material testing. When combined with our suite of design tools we can control fibre placement, and optimise weld location and resin flow throughout the mould.
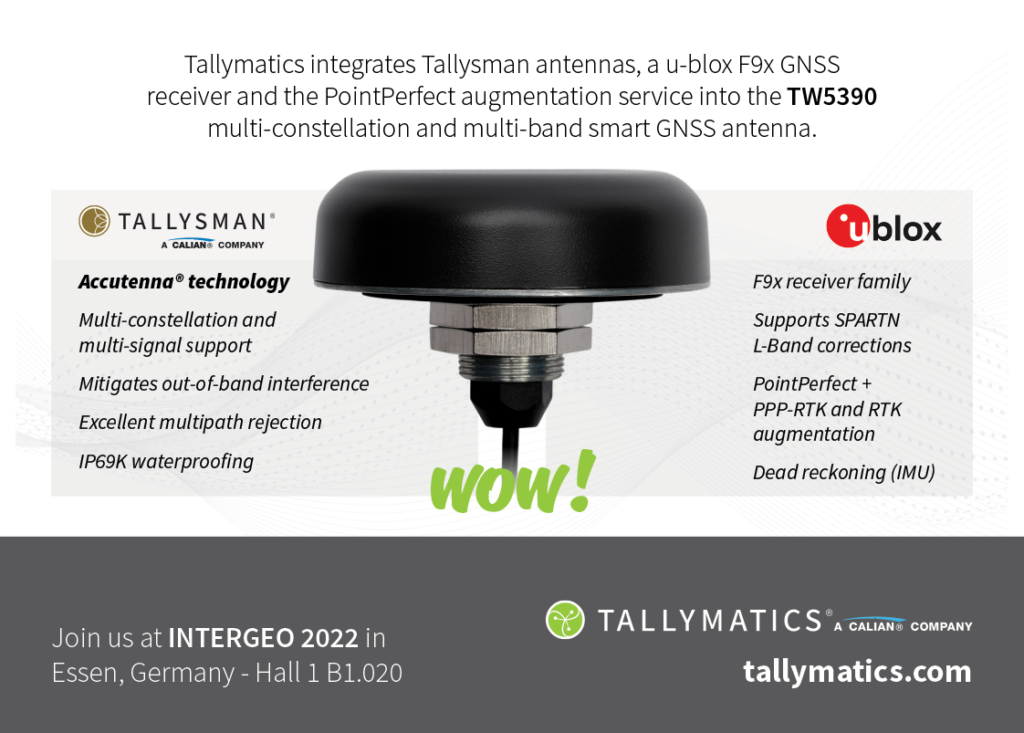
“The result is a three to four times increase in mechanical properties versus traditional random fibre injection- moulded plastic parts. We are achieving full fibre alignment with our injection moulding system, which opens the door for weight savings of up to 50% and increasing stiffness to degrees that nearly match the properties of traditional carbon-epoxy composites.
“AirGo carbon thermoplastics are much easier and faster to process than carbon epoxies, which means we can produce carbon fibre components that perform close to carbon fibre epoxy parts but at a production rate of one part every 60 seconds with one mould, as opposed to one or two parts per shift.”
He added that the toughness of the carbon-thermoplastic composites and the advantages of the company’s injection-moulding process make it easy to replace metal fittings as well as produce larger and more complex parts at lower cost compared with carbon-epoxy composites.
By supplying larger, monocoque carbon-thermoplastic components rather than multiple small carbon-epoxy assemblies, the number of metal fasteners and hence overall part count and total weight per airframe – as well as assembly time – can be reduced significantly.
FIXAR attended the show to exhibit its flagship FIXAR 007 UAV, an electric VTOL-transitioning system with a unique take-off and landing technique.
“FIXAR stands for ‘Fixed Angle Rotors’, and the ‘007’ refers to the craft’s MTOW in kilos,” explained Ronald Schultz. “It’s a 5 kg UAV with a payload capacity of 2 kg and a 1.6 m wingspan, which is possible partly because of the lightweight and durable airframe made from carbon, fibreglass and Kevlar.
“Also, the rotors are fixed at an angle to enable the craft to lift-off at a 45º angle, and quickly transition into horizontal flight by tilting itself instead of the rotors. Tiltrotors break far too often, making them a safety hazard and expensive to replace, so we wanted a system that is as simple and robust as possible.
“So, our design and the FIXAR technology forgoes tilting servos and uses the same motor-propeller drives for VTOL as for flight, which is key to our high ratio of payload to empty weight. In addition to manufacturing the UAV, we also make the autopilot and mission planning software.”
Also on display was a half-scale prototype of the FIXAR 025, which is planned to use the same fixed-angle rotors with a 2.8 m wingspan in order to carry a 10 kg payload over 300 km within a 3.5 hour flight time between charges.
“The 007 is ideal for photography and mapping work, while the 025’s capacity will be more suited to last- or middle-mile deliveries as well as more heavy-duty surveys, such as carrying a 5 kg Lidar with additional sensors, computers or batteries as support, or flying payloads at altitudes of up to 5 km,” Schultz added.
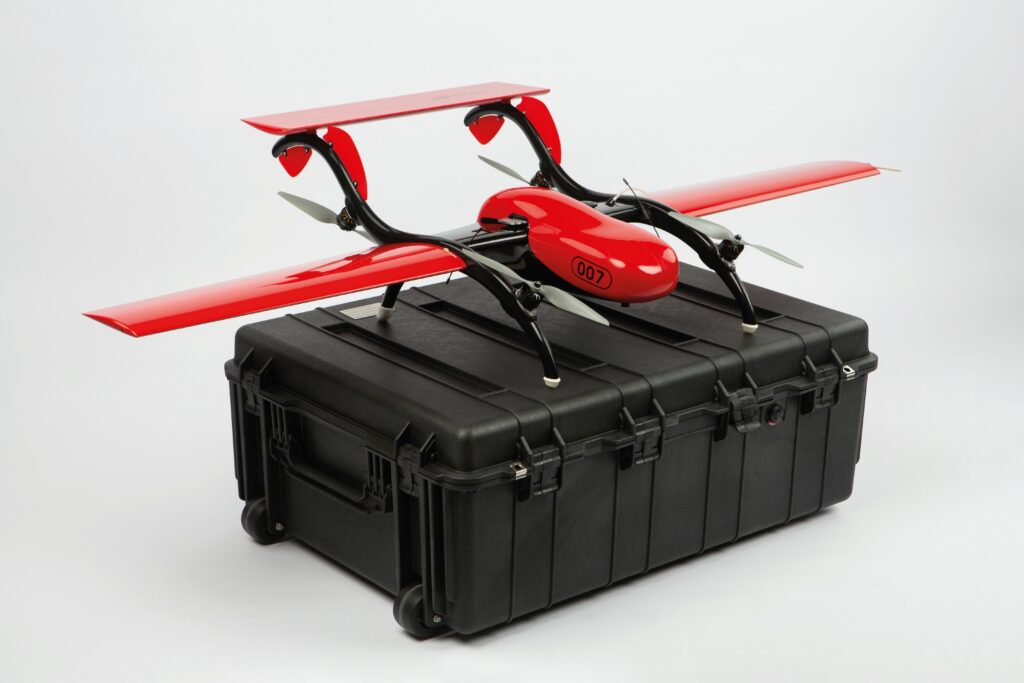
“And since the 025 also takes-off and lands at 45º, we’ve designed it with a unique triangular wing shape to maximise its lift in a narrower space than conventionally designed aircraft.”
We caught up with Gremsy to discuss its latest gimbals for UAV applications.
“The Duo features a dual camera interface for connecting IR and EO sensors in a single enclosure, which is useful for mapping and security missions, or anything else where visual and thermal signatures need to be tracked,” said Chu Nguyen.
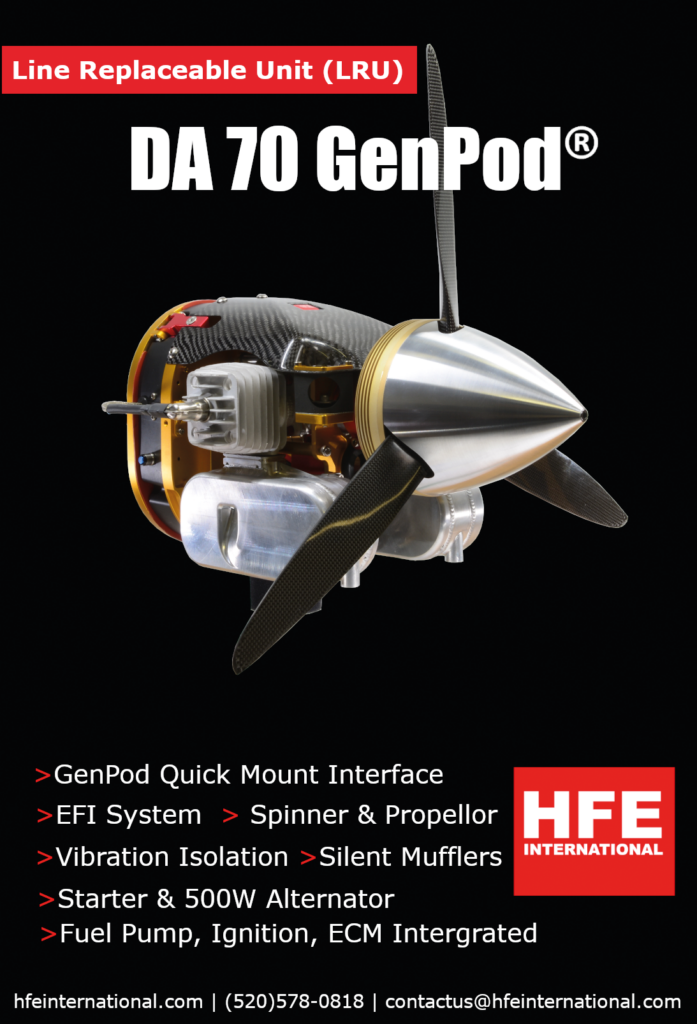
“We make the software for all our gimbals, which is embedded on an onboard AI chip, although the cameras are high-end systems sourced from third parties. The Duo uses the Sony Block 4K and FLIR’s Vue Pro R as its daytime and thermal cameras respectively.”
The Duo weighs 750 g with cameras installed, and interfaces over USB 2.0, CAN, UART, S-bus, and PPM, as well as Bluetooth 4.0 remotely.
The company also showcased its new Pixy S, a mapping gimbal integrating Sony’s A7R IV camera and designed for use with MAVLink-based UAVs (those flying using PX4- and Ardupilot-based autopilots. The system weighs 540 g, and is compatible with 28, 35 and 55 mm lenses.
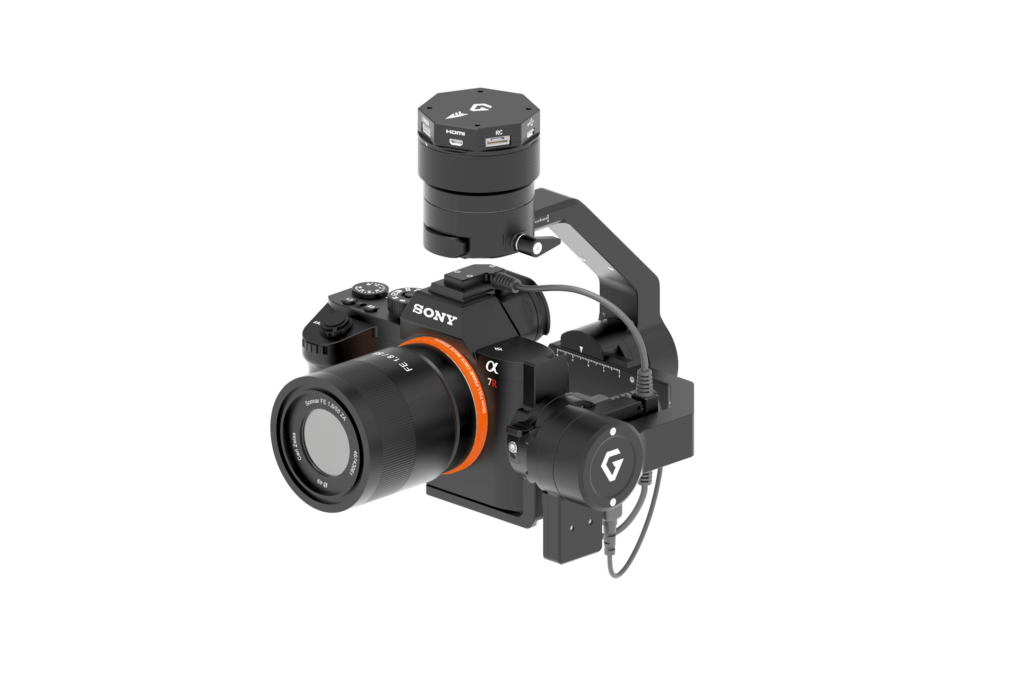
Drone Delivery Canada exhibited static models of its UAVs, which are designed and built to support its commercial logistics operations in North America and elsewhere.
“The Condor helicopter UAV is our largest, and probably the largest on display in this hall,” Armen Keuleyan said. “It has a payload capacity of about 180 kg [400 lb], and a range of around 200 km [125 miles].
“There are stringent flight regulations that we must abide by in Canada, however we have a tremendous number of rural communities that are secluded from the bigger and more populated cities, and hence need a swift, cost-effective solution to serve them that doesn’t rely on roads. Aside from parcel delivery, industries like mining, oil & gas and healthcare will benefit from cargo packages of equipment and supplies that our UAV can deliver.”
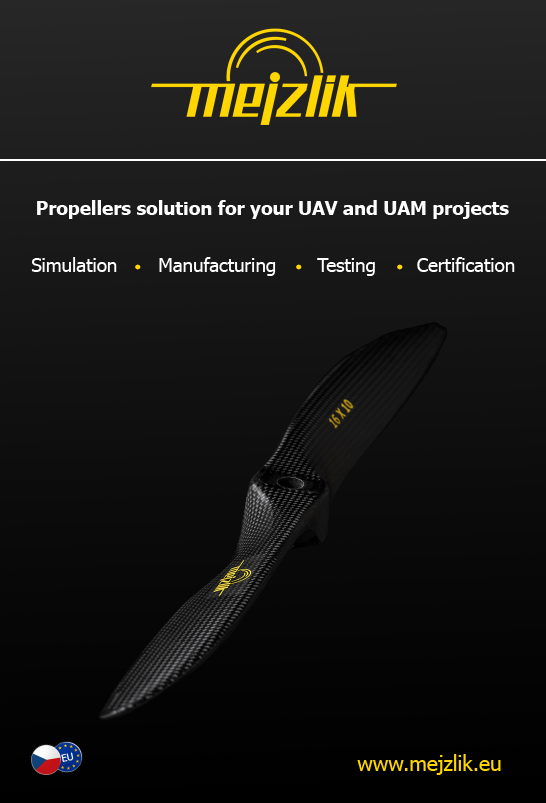
The Condor has an MTOW of 476 kg and runs on a two-stroke gasoline engine, and has a maximum speed of 120 kph.
Drone Delivery Canada also showcased its Sparrow and Canary UAVs, which are X-8 multi-rotors with MTOWs of 24.5 and 25 kg respectively, and 4 kg payload capacities on both platforms. The Canary is designed for a higher top speed of 80 kph to the Sparrow’s 60 kph.
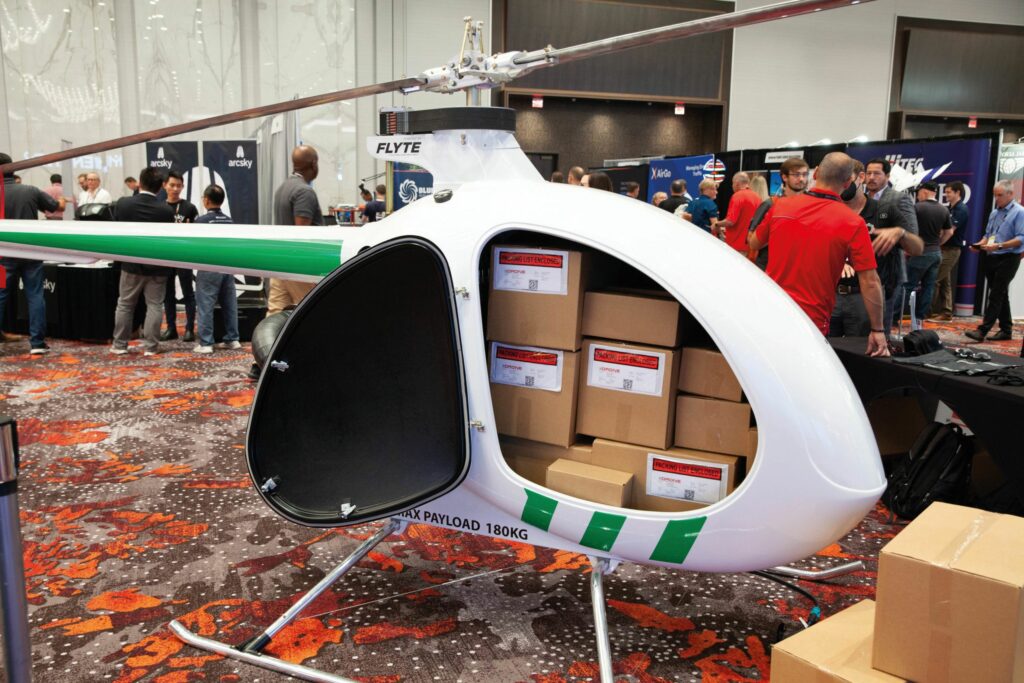
We spoke with Drone Geosciences about some of its work and the sensors it deploys for UAV-powered geophysical research.
“Our sensors effectively see into the subsurface of the Earth while being flown from a UAV, usually from 1 to 30 m above the ground,” said Ron Bell. “One is a magnetometer, two are electromagnetic systems – a metal detector and an earth conductivity meter – and all are commercially available.
“We are also talking with a company developing a semi-airborne EM system capable of imaging the Earth to depths of 1000 m or more. The system is applicable for subsurface geological mapping for environmental studies and resource exploration. All these systems are available in the US, and we are looking to take them overseas in the near future.”
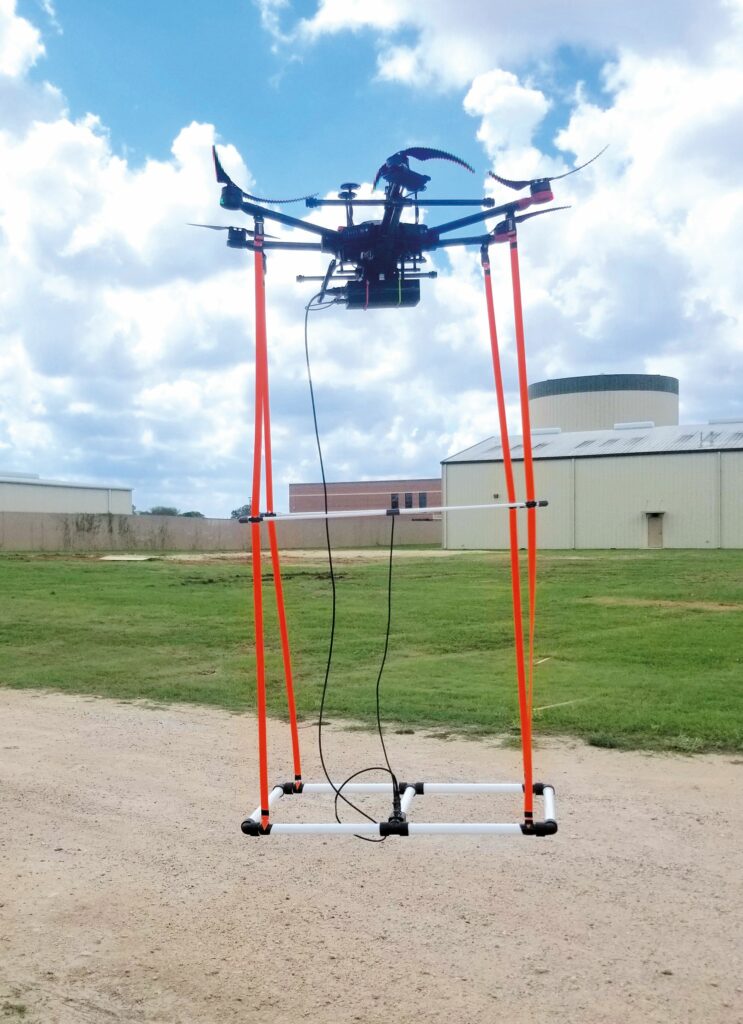
The company’s magnetometer is the caesium vapour MagArrow from California-based Geometrics, which has been designed for use on multi-rotors. It weighs 1 kg, includes an internal IMU and GNSS, has no sensor dead zone and is powered by a hot-swappable lithium-polymer battery for continuous data collection that is independent of the UAV’s power and positioning systems.
The metal detector is the EM61-Lite from Canadian company Geonics, while the EM conductivity meter is known as the GEM2 UAV manufactured by Geophex, in North Carolina. A D230A gamma-ray spectrometer from Terraplus is also part of Drone Geosciences’ sensors inventory. It provides a quantitative measure of gamma radiation resulting from radioactive element decay to quantify the amount of potassium, uranium and thorium in soil and rock outcrops.
We work on a range of projects for different industries, from locating legacy oil & gas wells and pipelines to exploring for hidden pools of groundwater and deposits of copper, gold and silver, to detecting unexploded ordnance or buried cars,” Bell added. “We even conducted a drone magnetic survey as part of a scientific study of what is thought to be an impact crater from a meteor.
“Further down the line, there will be new geophysical sensors and variations on existing ones that will enable missions like seismic surveys and gravity-based geophysical sensing, and there’s huge potential for applying machine learning and AI techniques to the drone’s geophysical data volumes to quickly extract more information about the subsurface. The overarching purpose of drone geophysics is to better understand the content and make-up of what’s in the ground below our feet.”
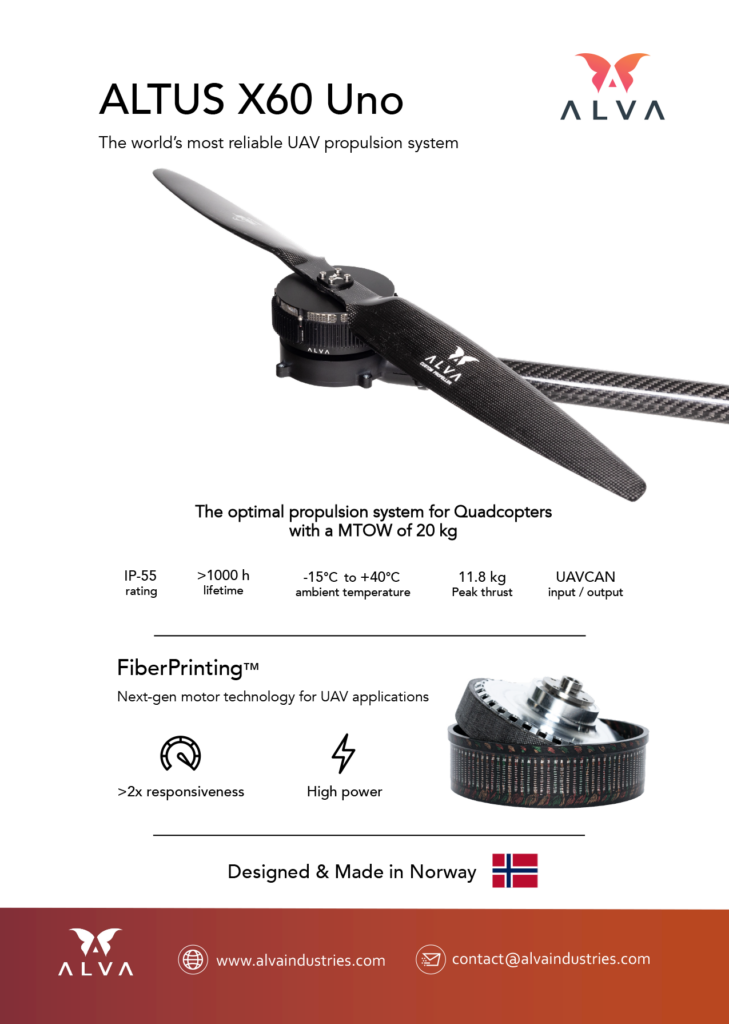
Hesai Lidar attended the show to display its range of laser sensing solutions, in particular the XT32 3D Lidar.
“It’s about twice as precise as any other commercial 3D Lidar available right now,” said Frank Bertini. “It will capture points in its surroundings to about 0.5 cm of range precision, making it ideal for UAVs and ground vehicles such as self-driving cars and trucks.
“It also measures range accurate to ±1 cm, and all this is possible through our custom-designed, proprietary ASICs. The XT series are our first products using those, and we’re getting positive feedback in terms of the 3D model quality they enable, not just for autonomous driving but pipeline inspection, powerline inspection and more.”
The XT32 consumes up to 10 W and is 103 mm in diameter at its base (where it is widest) and 76 mm tall. It measures with a vertical FoV of 31º and out to a maximum range of 120 m, with up to 640,000 data points captured per second (with a single return per pulse).
UPCOMING EVENTS
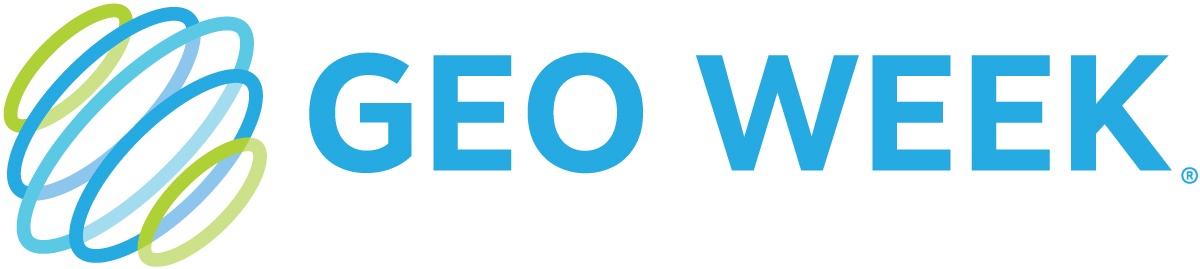
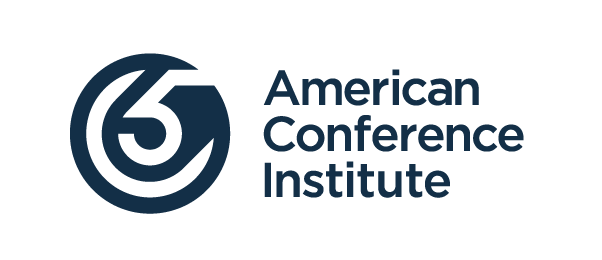
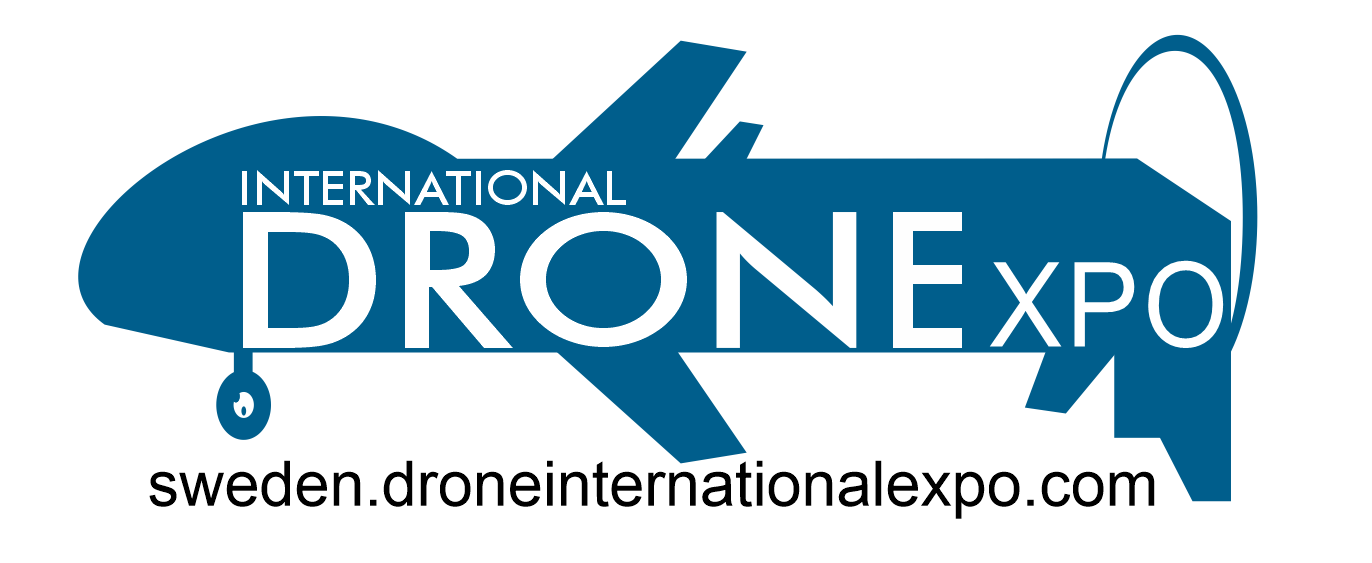
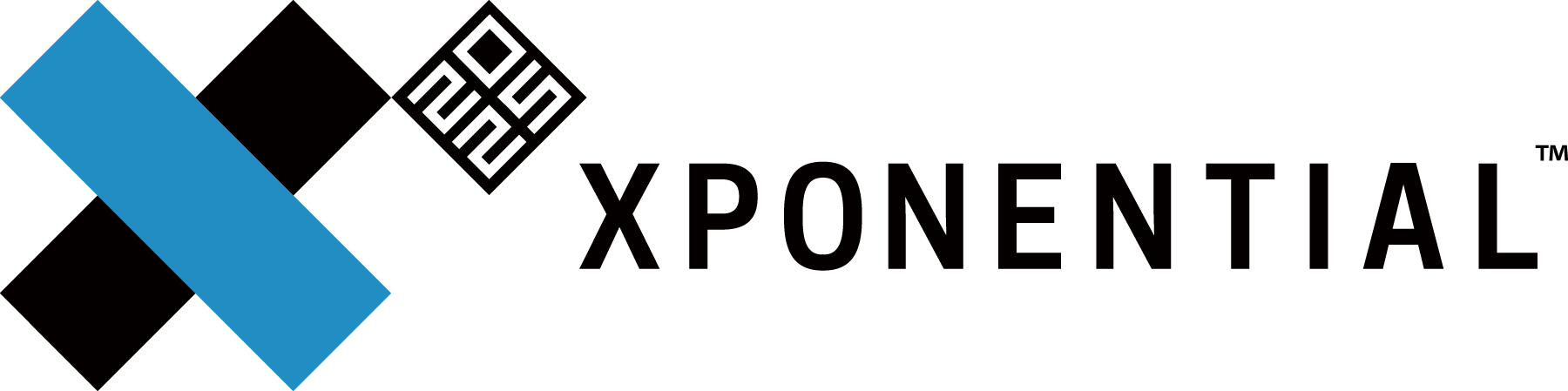
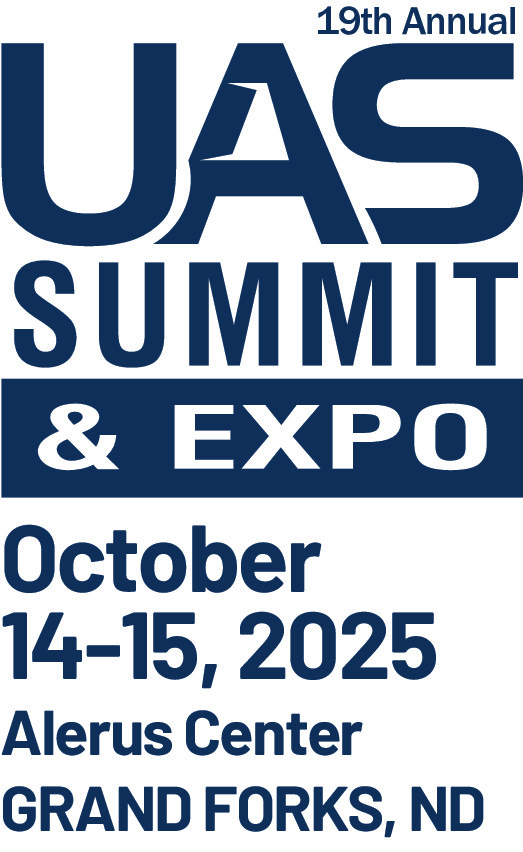

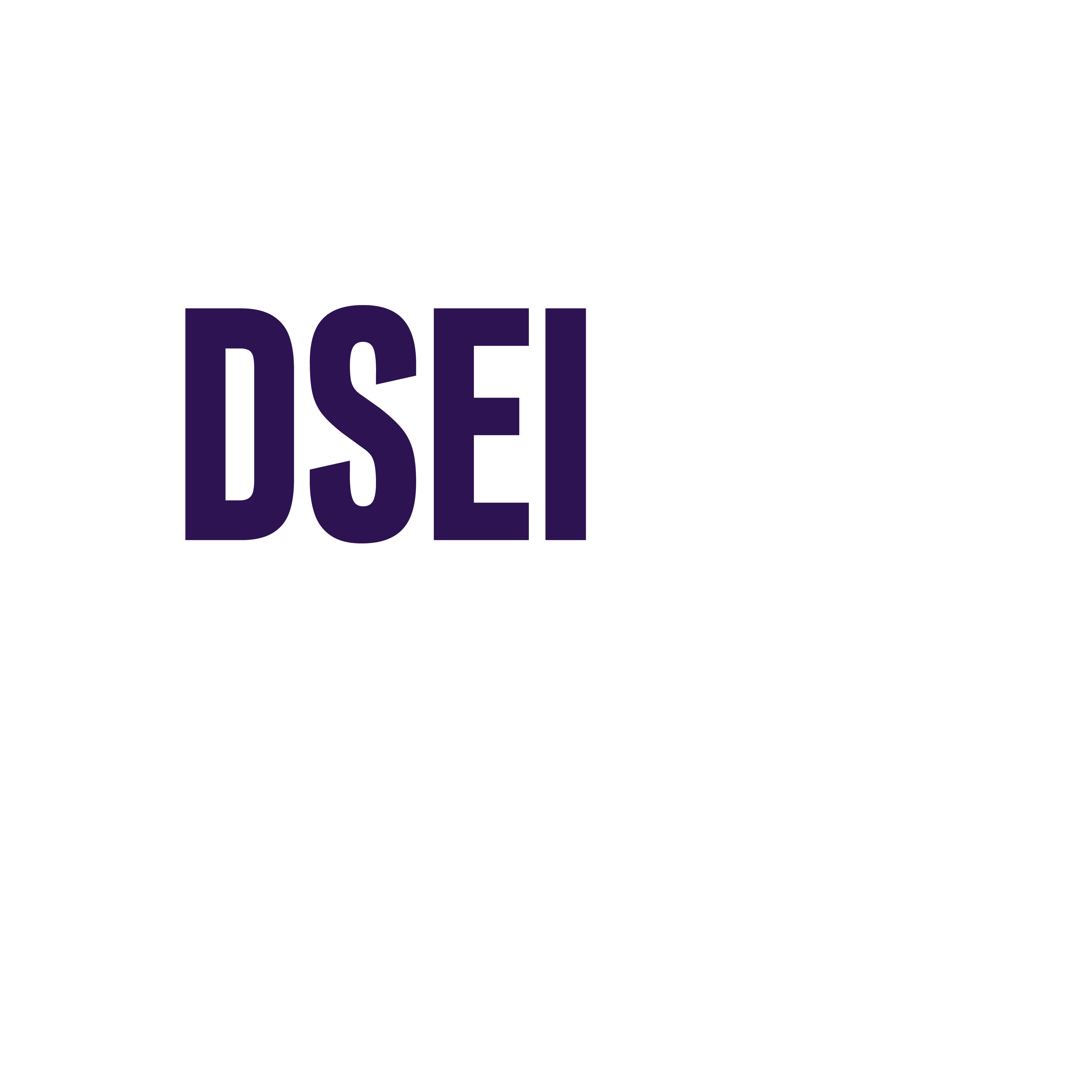
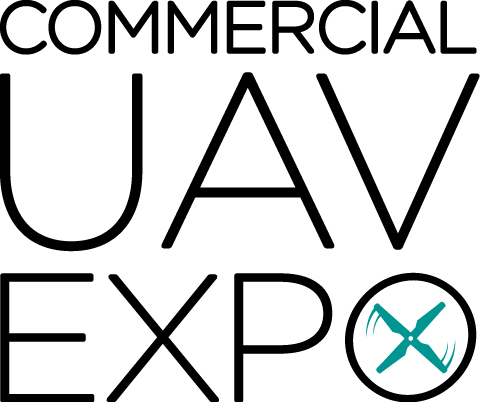
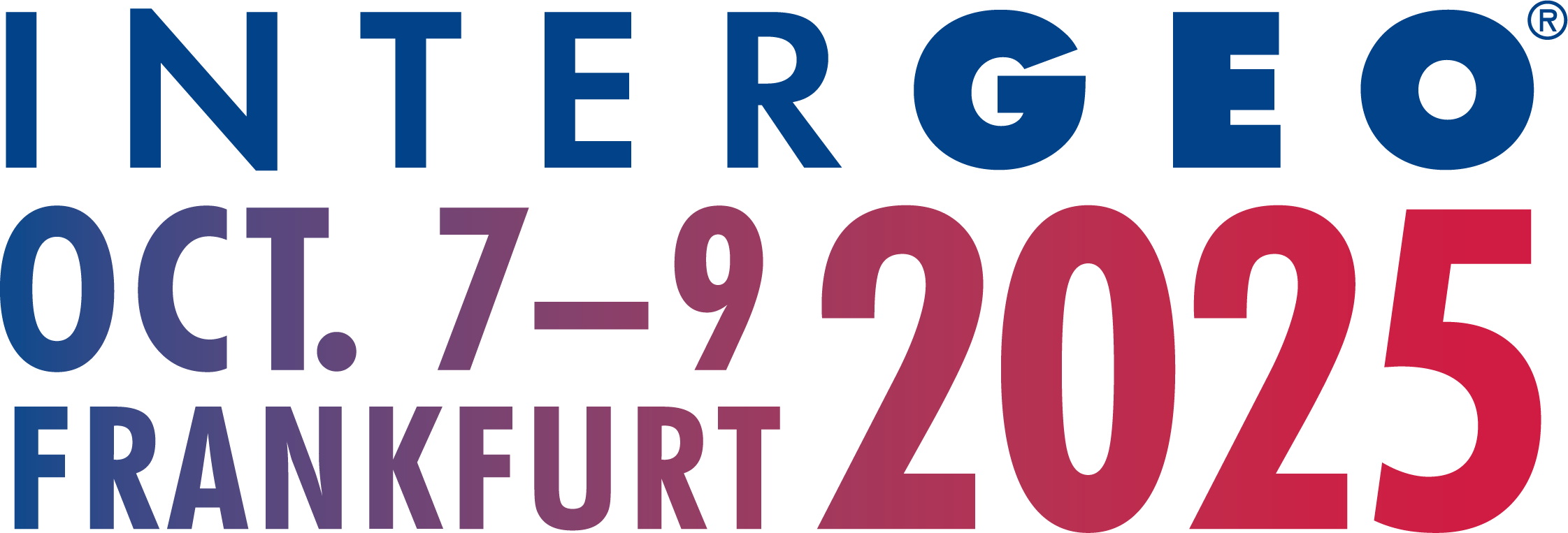
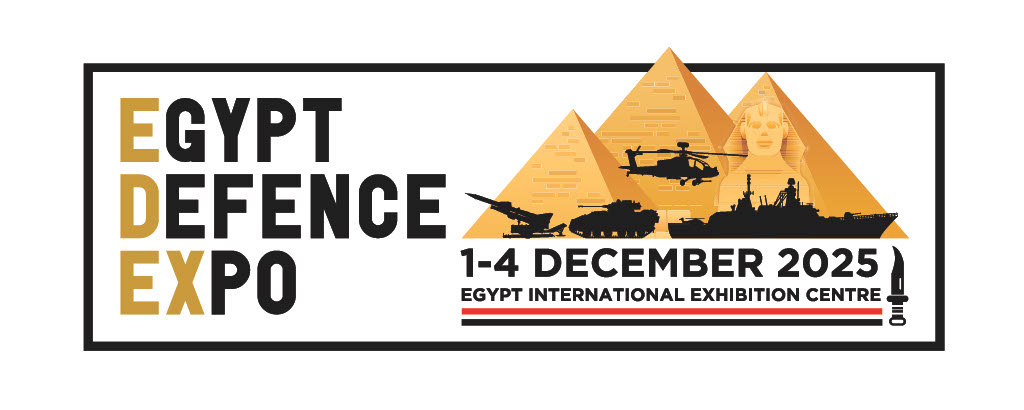
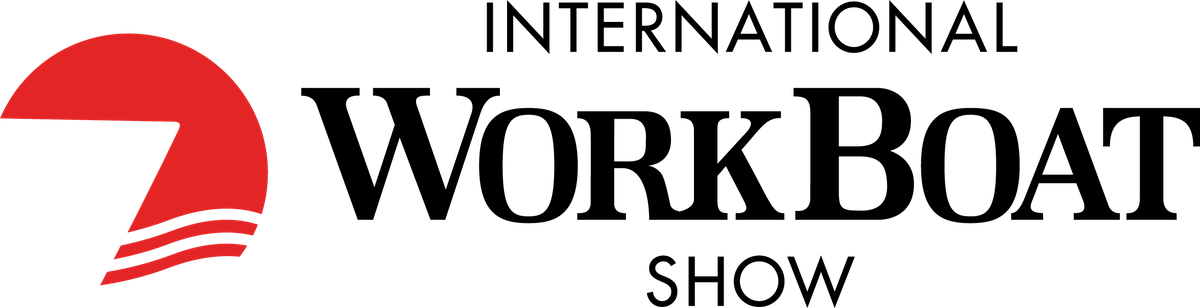