CUAV Expo 2023
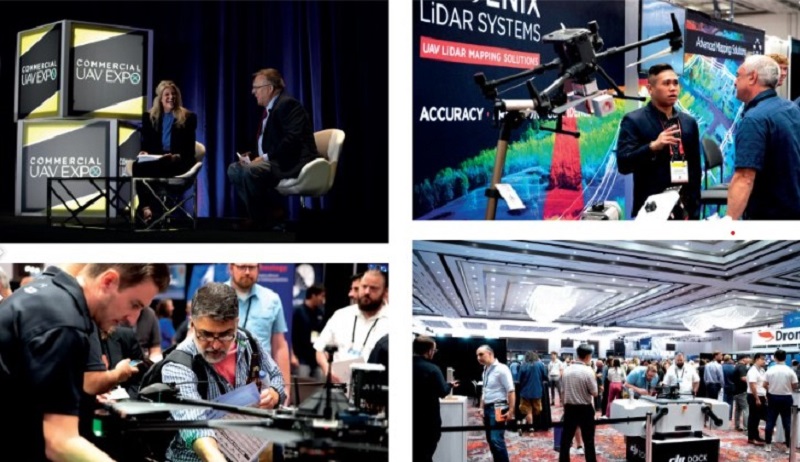
Rory Jackson presents an in-depth report on the huge range of uncrewed systems technologies that were on display at this year’s expo
UAS manufacturers, component suppliers and potential operators gathered in Caesars Forum in Las Vegas this year for the 9th annual Commercial UAV Expo. Running from September 5 to 7, the event played host to 206 exhibitors from 22 countries, along with nearly 3500 professional attendees out of the 4008 registered attendees, who came from across the US and 54 other countries.
As well as the diverse conference programme examining the future of UAVs and AI in many industries, as well as a vivid series of flight demonstrations, the expo hall once again featured a huge range of new technologies and innovations, thanks perhaps to the chance for detailed r&d as a consequence of the Covid pandemic.
Such was the sheer range of new systems on display therefore that we have produced this, our largest-ever report on the show.
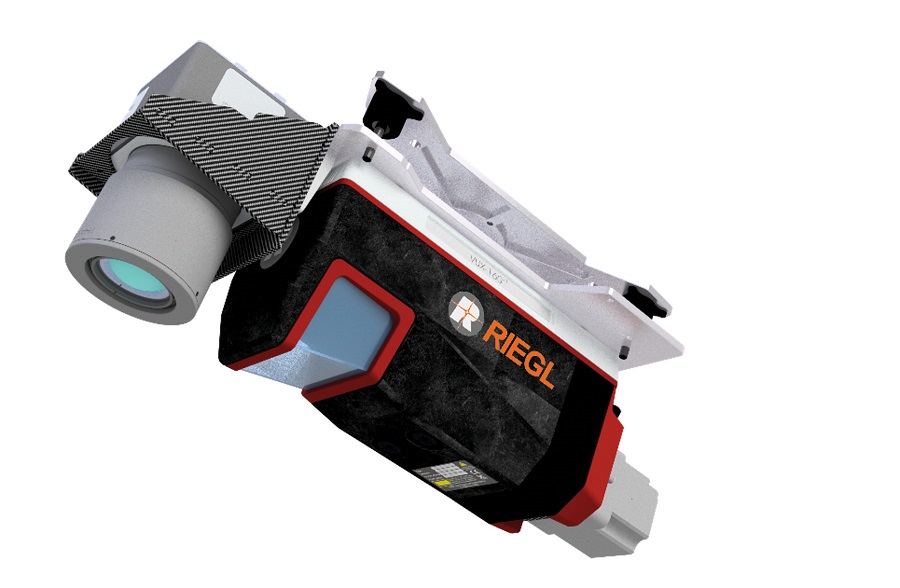
Riegl attended the show to exhibit and discuss its new Lidar systems and the missions they can undertake for industry. First was its newest laser scanner, the VUX-160²³, a more powerful version of its VUX-120²³.
“The more powerful laser in the VUX-160²³ means it has a longer range than the VUX-120²³, the trade-off being that it’s slightly heavier and larger, but that brings additional benefits such as an upgraded laser pulse repetition rate [PRR] of up to 2.4 MHz, with the same FoV of 100o,” said My-Linh Truong.
“It’s also constructed for NFB [nadir/forward/backward] scanning. With traditional airborne Lidar, most people understand the nadir orientation of points you get on the ground, but with NFB you get additional points and shots 10o ahead and 10o behind the UAV, which allows more detailed and higher quality 3D modelling of structures like transmission towers, power poles and building facades, as well as complex terrain across flight paths.
“And if an end-user has a flight path with overlaps in each pass, NFB really helps guarantee that they’re capturing complete and fine detail on the assets they’re looking to model.”
Operating at a maximum of 2.4 MHz PRR, the VUX-160²³ has a measuring range of up to 720 m and can measure up to five targets per pulse, although if the PRR is configured downwards, to the minimum of 300 kHz, these increase to up to 1800 m and 32 targets respectively. Its scanner functions using a rotating polygon mirror, with a scan speed of up to 400 lines/second and an angle measurement resolution of 0.001o.
“The VUX-160²³ also has five camera ports, so customers with large UAVs or crewed aircraft can integrate up to five cameras, potentially in nadir or oblique angles for added visual detail to overlay on the Lidar model,” Truong added.
“We can also integrate either Applanix’s AP+30 or +50 GNSS-IMU inside the housing, for additional accurate information on roll, pitch, heading and position in a compact package, with the total system weight coming up to 3.15 kg if the end-user goes for those. This configuration is ideal for high-performance VTOL UAV platforms.”
An Ethernet connection of 10, 100 or1 Gbit/s is suitable for interfacing with the system for scanning data outputs and configuration. The system is powered via an 18-34 V DC input and consumes 60 W in normal operations, with a typical weight of 2.65 kg; its enclosure measures 283 x 134 x 117 mm.
The company also talked about its VUX-120²³, which has a maximum range of up to 400 m and up to five targets per pulse when set for a 2.4 GHz PRR.
The scan parameters are the same as on the VUX-160²³, although the system consumes just 45 W in standard operation and weighs roughly 2.3 kg – 3 kg if the end-user chooses the optional integration of an Applanix APX-20 UAV GNSS-IMU, or 3.6 kg if either of the more powerful AP+30 or +50 units are selected. Up to two cameras can be integrated, as well as dual Ethernet interfaces if needed.
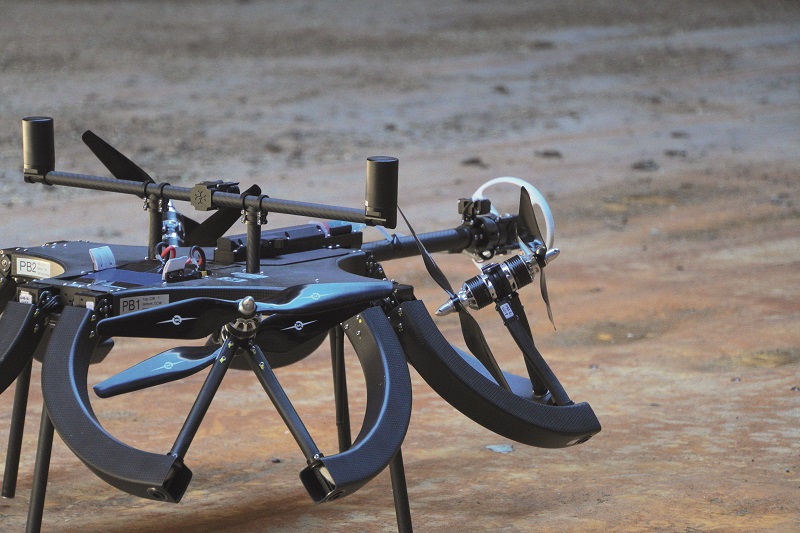
Skygauge Robotics debuted its Skygauge UAV, an X-8 octocopter in which each of the four coaxial rotor pairs are mounted on two passively hinged beams, the beams each linking to an arm on a rotary servo actuator. This arrangement enables each rotor pair to pitch and roll independently of the others, giving the UAV the ability to perform a range of tasks involving physical contact.
“The UAV’s four rotor pairs tilt as needed to keep the centre body stable and in place while flying. That stability turns it into a platform for contact instruments,” said Nikitia Iliushkin.
“Our first use case for that is ultrasonic inspection of infrastructure assets, such as refinery pipes and pressure vessels, or that can extend to bridges and wind farm blades. Any large metal structure needs ultrasonic testing, but that’s typically done using workers and scaffolding.”
The electric UAV is currently designed for an 8 minute optimal endurance (given the high number of motors and servos it operates during flight), and Iliushkin noted that the amount of work it can accomplish in that time would take a trained technician 1-2 hours if accounting for the movement of equipment and scaffolding.
In future, the company also plans to offer the UAV for other contact or near-contact work that typically relies on scaffolding, such as aerial painting, coating, pressure washing, scrubbing and sanding.
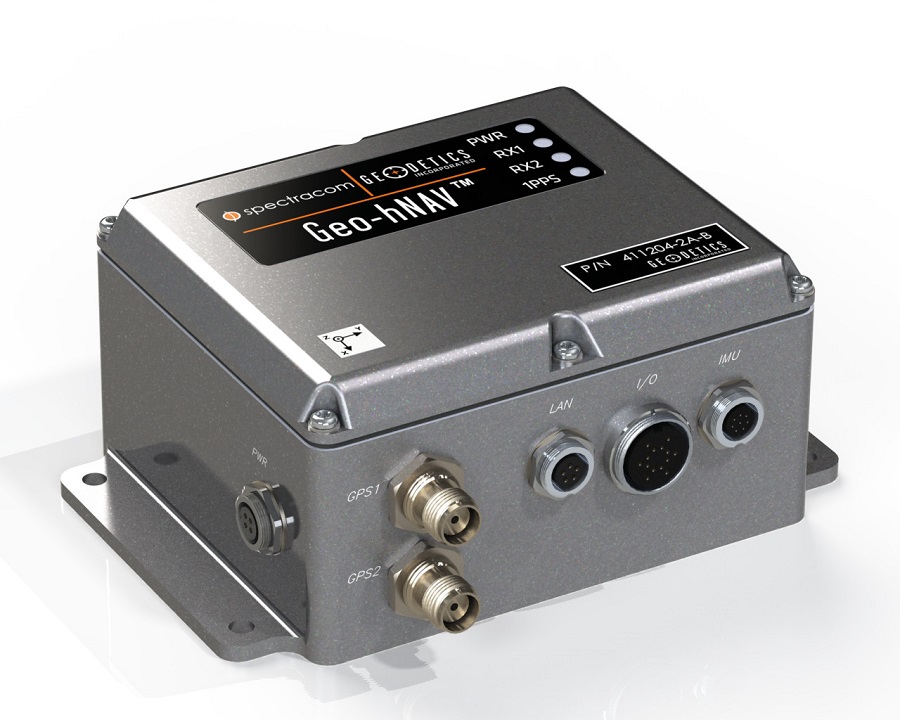
Aevex Aerospace had on display a range of its Assured PNT (positioning, navigation and timing) products, which are designed to sustain precise and resilient navigation in denied or constrained environments. Among them was its Geo-hNAV, a system consisting of two GPS receivers and one IMU with PNT capabilities packaged in a single enclosure.
“With the Geo-hNAV, which is suited to low-aerodynamic vehicles working in surveying or search locations, you’d ideally install the two GNSS antennas with a separation from 0.5 m to about 3 m,” said Mark Glover. “Our customers in the DoD find a lot of use for this capability as well.
“We provide commercial GPS receivers embedded inside the Geo-hNAV enclosure along with different IMU grades, from embedded MEMS IMUs to external, tactical or navigation-grade IMUs. We can also integrate a Selective Availability and Anti-Spoofing Module [SAASM], as well as the newer M-code, aimed at further enhancing anti-jamming and anti- spoofing of military GPS signals.”
The Geo-hNAV weighs 567 g and consumes 2 A during normal operations over a 10-30 VDC input. The output data rate is a function of the IMU type, and is up to 400 Hz over Ethernet or RS-232. Aevex’s system can support a range of IMUs including models from Honeywell and Northrop Grumman.
The Greene Rubber Company displayed some of its new thermal transfer materials aimed at removing heat from sensitive vehicle components.
“These can be silicone-loaded materials with a thermally conductive dispersion in them, or they can be graphite materials which transfer enormous amounts of heat rapidly to a heat sink or something else where the heat won’t do damage, as they might with electronics,” said Steven Holm.
“The key differentiator between them is weight. Graphite is a lot lighter, so in a UAV choosing the graphite over the silicone-loaded material would contribute to more air time.”
Suggested areas of integration include battery packs, board-mounted electronics, and IMUs. End-users’ CAD files can be used to understand the installation case, design graphite or silicone-loaded parts accordingly, and where necessary layer them with complementary materials such as electrical insulators if necessary.

Astrolabe Analytics is developing software for predictive battery maintenance capabilities it says are for users and manufacturers of batteries, UAVs and other uncrewed systems.
“A lot of our early traction was through SBIRs from the US DoD and Air Force, and their interest in eVTOL and UAV solutions. That initial funding enabled us to develop the different algorithms we’re using to forecast battery health and performance under different operating scenarios,” said Robert Masse.
The software, once complete, will be able to project the lifetime of batteries based on traditional lithium-ion chemistries, and Astrolabe intends to provide its software and services to that end for predictive battery maintenance in defence and aerospace applications. The company is also working on compatibility with other, less commercially mature chemistries that could become widespread in the future.
“There are nuances for each use case, but at the end of the day it all boils down to time, voltage, current and temperature data. We engineer different features and relationships from that data to inform usage and maintenance of each battery pack or module going forward,” Masse added.
“We have different ways to plug in our solution with OEMs or their partners, whether we’re on the BMS or interfacing with someone’s cloud-based UAV fleet management software.”
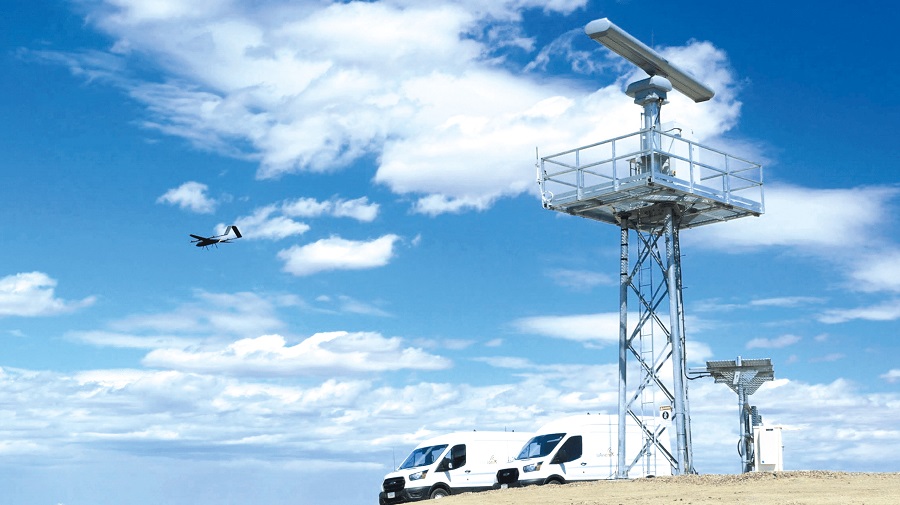
During the expo, uAvionix received an official FAA exemption that granted it the right to fly its Rapace in BVLOS flights on the North Dakota Vantis infrastructure that uses networked C2 and DAA systems. That has created the opportunity for other companies to fly BVLOS using uAvionix’s C2 products and its SkyLine cloud-based management system (for more details, see issue 46, October/November 2022).
“Basically, other companies can use our equipment and procedures to fly BVLOS,” said Joe Gibbs. “If they want to fly under FAA Part 91, they can reference this exemption in their safety case, using all the technologies named in it, and the FAA should then fast-track them for approval with minimal need for validation or additional risk analysis.
“It really makes performing commercial BVLOS missions a lot easier. We spent 18 months working for the exemption on behalf of our customers, and those piggybacking off our exemption should anticipate a much shorter timeline for theirs.”
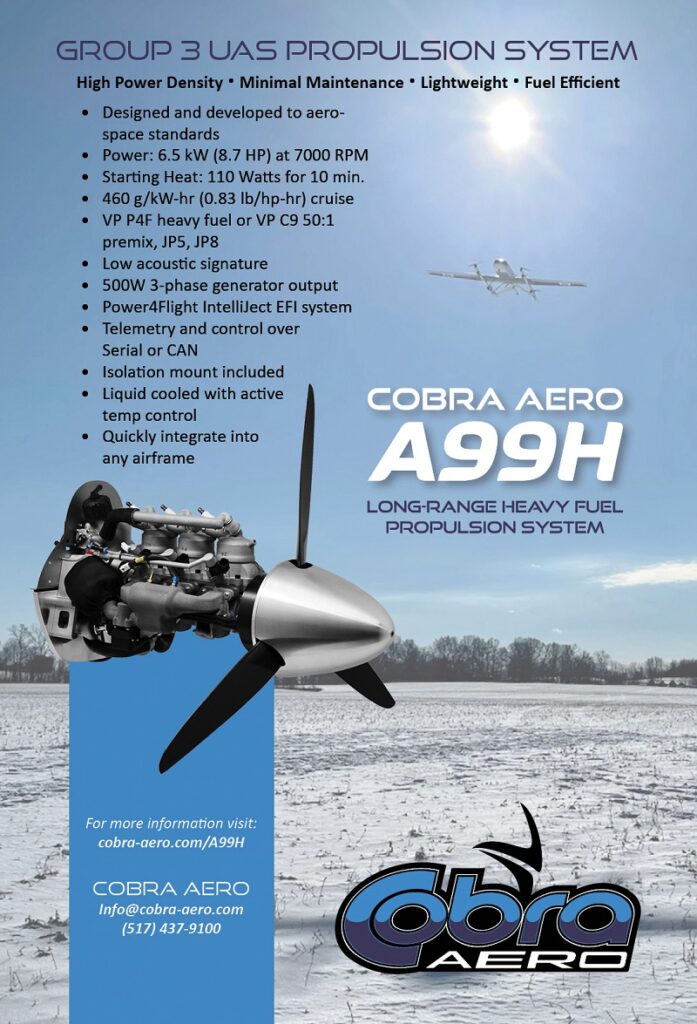
UAvionix added that UPS FlightForward, Phoenix Air and Zipline have also received exemptions.
Trimble Applanix showcased its new PX-1 RTX, a GNSS-IMU OEM positioning product supplied ‘as a service’ and specifically engineered for UAV delivery, providing roll, pitch and heading support for navigation, guidance and control, as well as real-time centimetre-accurate positioning for last-mile delivery.
“The fully integrated GNSS and IMU board is bundled with Trimble’s Centerpoint RTX, a global correction service derived from hundreds of survey-grade reference stations around the world, all constantly receiving signals from different GNSS constellations,” said Brad Schmidt.
“Centerpoint RTX uses this data to filter and correct for atmospheric errors, multi-path or other issues in the signals and then, via an L-band satellite or N-Trip internet connection, broadcasts these corrections to the receiver to archive centimetre-level accuracy anywhere in the world.”
In addition to providing centimetre-accurate positioning (within 0.03-0.06 m in real time, accounting for RMS errors), the PX-1 RTX provides heading data without influence from external magnetic fields.
As a result, delivery UAVs do not need their own ground infrastructure for positioning accuracy, and their trajectory can be tightly constrained to avoid exceeding the boundaries of what are likely to be strictly defined flight corridors, especially in urban areas, where they might be authorised to fly. It also aids with safety and security to bystanders by providing centimetre accuracy for package or cargo drop-off.
The GNSS-IMU board is included as part of a yearly subscription, and supports multiple frequency tracking of GPS, GLONASS, BeiDou and Galileo, as well as QZSS, SBAS and MSS L-band signals, delivering position, heading, pitch and roll at 100 Hz. It weighs 60 g, measures 67 x 60 x 15 mm, and consumes 3.5 W in normal operation over any connection from 9 to 30 V.
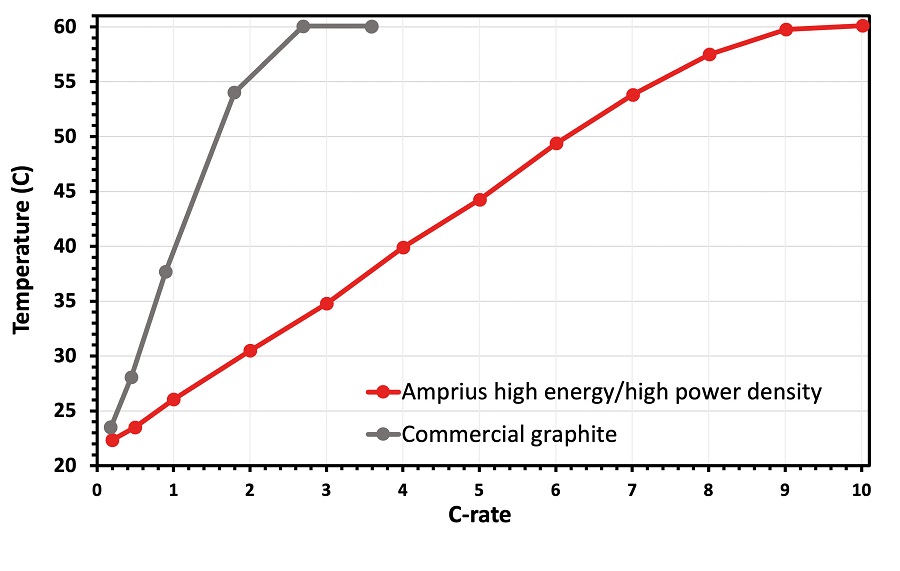
Sixdof Space showed its solution for ultra-fast optical tracking, which was originally developed for tracking head movements in VR and AR applications, although as of the expo it has been re-engineered for precise, targeted landings with UAVs.
“In a normal use case, our tech has infrared beacons placed on the landing spot, and our sensor is installed on a UAV,” said Mark Goldfarb. “The sensor sees only light – it’s not a camera – so instead of seeing the millions of pixels a camera sees, and needing to process all of that, it’s just a few thousand pixels. This is one of our tricks for reducing latency.”
On top of that, the company has a patented optical technology that compresses this light information into a single row of data, which can then be used to guide the UAV down for landings precise enough to work on boats being rocked by high sea states, or trucks moving fast on poor roads.
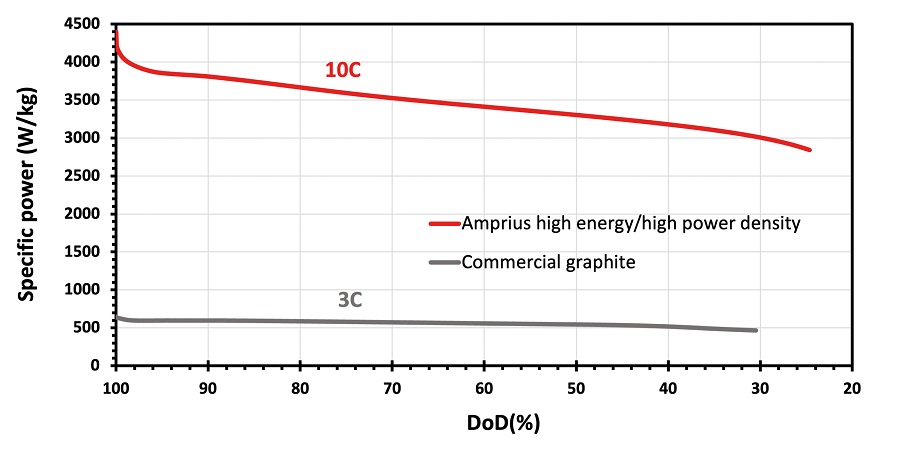
The technology provides readings in both altitude and orientation (hence the six degrees of freedom referenced in the company’s name), and the company has successfully tested the technology in both darkness and direct sunlight.
“Our system works at 400 Hz, enough to compensate for very dynamic conditions including winds and gusts, and it reconnects quickly amid fast-moving obscurants to keep on working mid-landing,” Goldfarb added. “The board weighs about 30 g, and the housing can be customised for end-users’ needs, or they can choose to integrate it into their own UAV’s hull.”
Although Amprius is best known for its 500 Wh/kg cell design it announced at AUVSI Xponential earlier this year, the company presented a new cell with a different use case at the expo.
Katie Maze explained, “This cell has been designed to deliver both high energy and ultra-high power. It has a gravimetric energy density of 400 Wh/kg, an optimal charge rate of 5C, and a maximum continuous discharge rate of 10C.
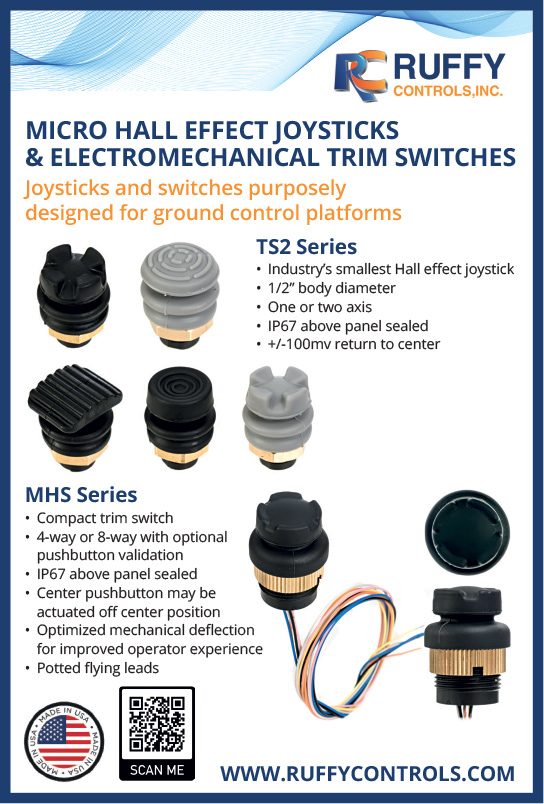
“What also sets this cell apart is its fast-charging capability. During charging, the charge rate can reach 10C, enabling a cell to charge from zero to 80% SoC in less than 6 minutes.”
Traditionally, battery cells have had to make trade-offs between power and energy. However, Amprius attributes the unique capabilities of this cell to its proprietary silicon nanowire anode technology. This highly conductive material is grown directly on the current collectors within pouch-type cells through a deposition process.
Maze said, “Our nanowire anode technology is 100% silicon, giving us very high energy density. There are no additives or non-active materials; it’s purely silicon. Also, the unique structural properties inside the anode mean our cells don’t swell any more than typical lithium-ion cells during use.
“The power delivery of this cell remains consistent even at lower depths of discharge, giving UAVs an extended usable battery capacity and the ability to withstand challenging conditions throughout a mission. In the growing industry of eVTOL aviation, rapid charging and reliable landing power are expected to be foundational elements.
“Lastly, we also generate less heat compared to graphite-anode cells, reducing the thermal management burden for pack manufacturers and UAV designers. This reduction translates into a lighter overall battery pack weight, freeing up more space for payloads.”
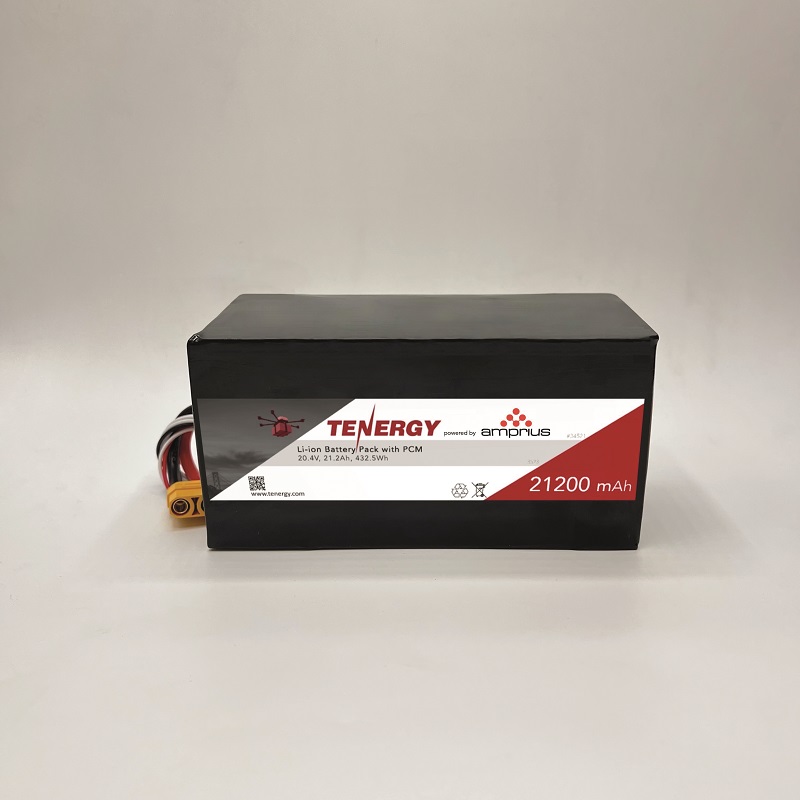
The company has also developed a range of UAS battery packs with Tenergy. Four versions are available, running from one to four strings of cells in parallel, each string composed of six cells connected in series.
The smallest pack is hence a 6S1P system weighing 627 g, with 10.6 Ah of energy capacity, 216.24 Wh of energy storage, and measuring 155 x 65 x 40 mm.
The largest is a 6S4P system that weighs 2508 g, with 42.4 Ah in capacity, 864.96 Wh of energy stored, and dimensions of 155 x 65 x 160 mm. All four systems have a nominal voltage of 20.4 V (with 2.5 V per cell) and can discharge at a rate of 4C.
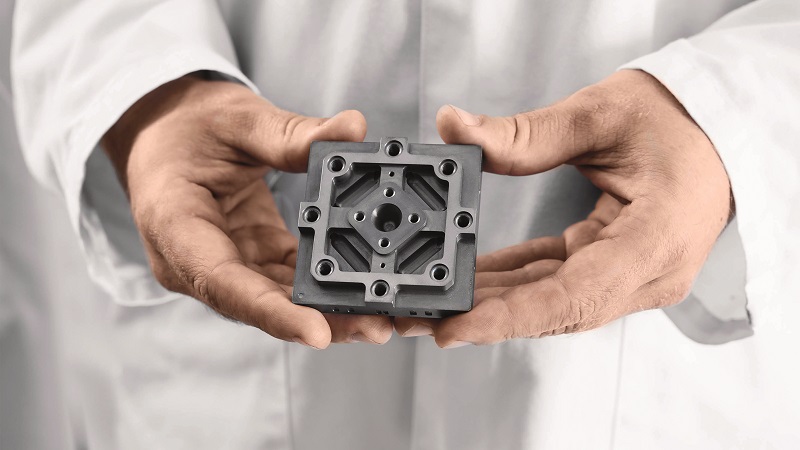
Sandvik Osprey exhibited at the expo for the first time to show its controlled expansion alloys and their effectiveness for use in components undergoing extreme temperature changes.
“They’re made from a binary aluminium-silicon alloy, and by changing the ratio of the metals we can change the thermal expansion degree of the alloy, tailoring it from anywhere between 5 and 17 ppm/K, with anything from 27% silicon up to 87% silicon,” said Dr Stuart Sillars.
“We can also vary it to match any material that has a CTE [coefficient of thermal expansion] of between 5 and 17, be they metal alloys, semiconductor wide-bandgap materials or even PCBs. Any assembly or component that is sensitive to a wide range of temperature changes, for example from room temperature to the Arctic, will need mounts with the same CTE.”
Typical CTE-matching materials tend to be far denser and heavier than Sandvik Osprey’s Al-Si alloys, for example molybdenum or tungsten-based materials such as copper-tungsten in space vehicles (with which the company’s Al-Si alloy has extremely close thermal conductivity, but with one-sixth the weight).
“Casting our alloys is rarely possible with more than 15% silicon, but we get around that by rapidly solidifying our material from its molten state to produce a material with a fine and homogeneous microstructure, and we can then make CNC or EDM components from the billet,” Dr Sillars added.
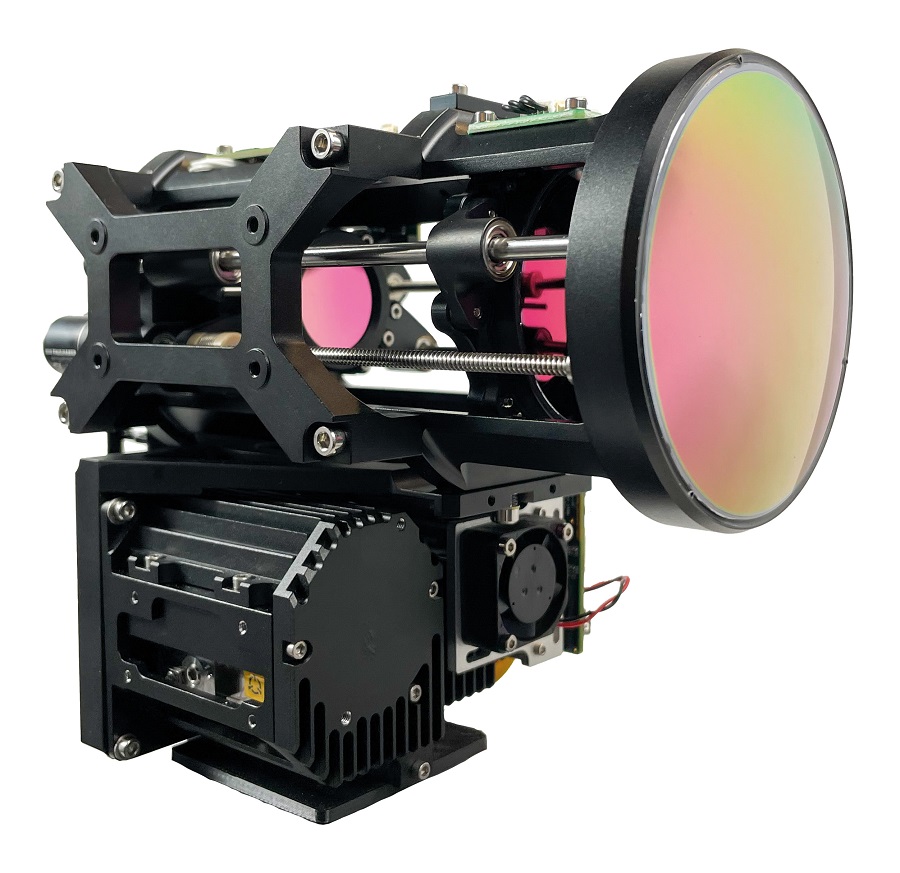
Sierra-Olympia Technologies discussed a range of new IR cameras supplied by it and the partner companies it represents. First was Jenoptik’s EVIDIR Alpha, designed as a small form factor, calibrated, radiometric microbolometer system for inspection-type UAV and other industrial applications requiring temperature readings.
“It’s a LWIR, 12-micron system with VGA at 640 x 480 resolution, and at the moment there are three available lens configurations. On top of that it can be configured for CMOS or CameraLink, and MIPI interfacing is expected in 2024,” said Chris Sculley.
“In addition, the latest release from Leonardo DRS – for whom we’re the North American master distributor – is the Tenum 640, a 10-micron VGA sensor with 640 x 512 resolution, and we’re also featuring the Tenum 1280 as a soft release, which also has a 10-micron pixel pitch but with 1280 x 1024 resolution, and is built on an uncooled microbolometer core.”
The Tenum 1280 measures 46 x 40 x 31 mm without its lens and nominally consumes 2.3 W in standard operation, up to a peak of 2.8 W. The Tenum 640 measures 31.3 x 28.8 x 27.2 mm with no lens and consumes up to 1.2 W nominal.
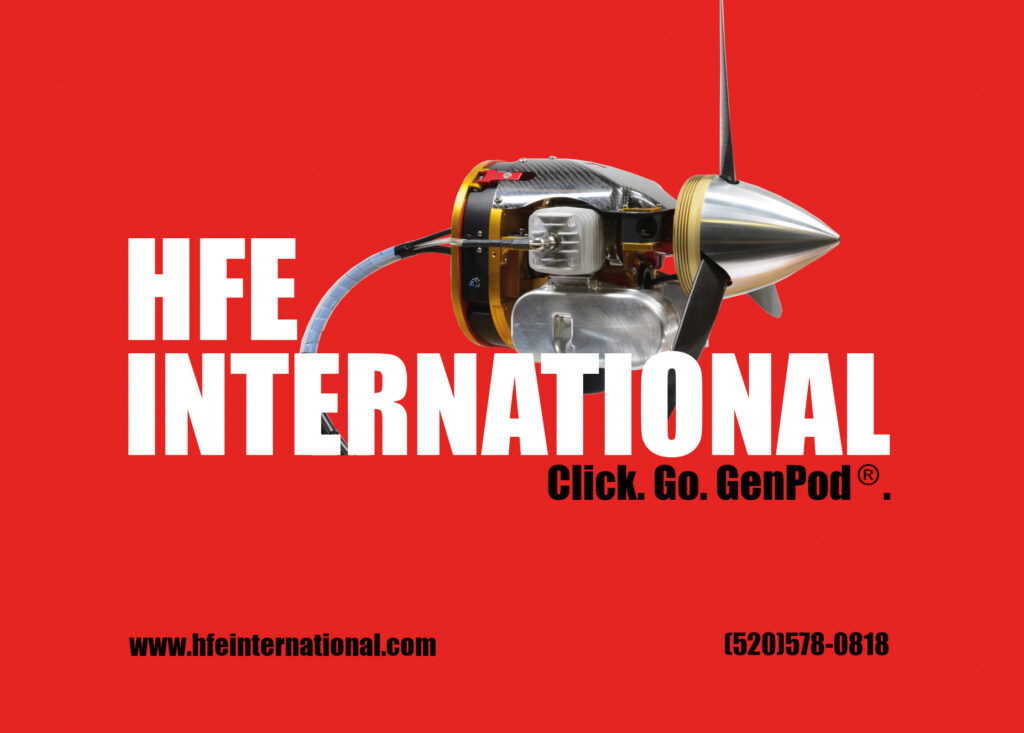
“We’re also showing our Ventus HD6, a new cooled MWIR series of cameras built around DRS’s HexaBlu cooled midwave core, with a really long lifetime – there are HexaBlus in labs right now that are still working after 3 years, sitting in temperature chamber tests of repeated cycles of start-up, runtime and cooldown; no failures as yet,” Sculley added.
“It has an extremely quiet motor with little to no vibration, and we’re pairing it with a range of zoom and fixed optics. We also offer an encoder board to integrate with it, to act as a lens controller and provide different interfaces for multiple applications.”
The Ventus HD6 has a 6-micron pixel pitch and a resolution of 1280 x 960, with a 30 Hz standard frame rate (up to a peak of 60 Hz). The HexaBlu core and Ventus HD6 are now commercially available, with three fixed focal length options and two zoom lenses, and one more to come in 2024.
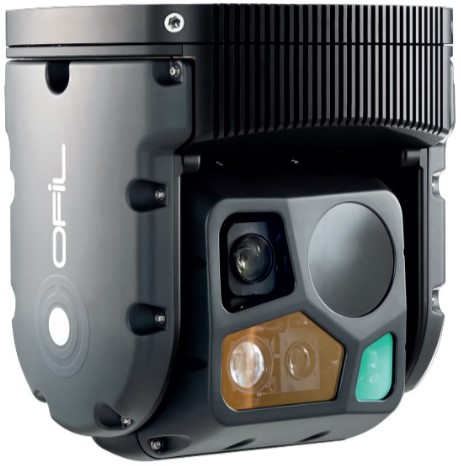
Ofil Systems showcased two large gimballed sensors for utility inspection, and the control stations for monitoring and operating them.
“Our technology incorporates a type of UV filter we call ‘solar-blind filters’, which allows us to track UV light even in daytime by filtering out everything except a very narrow band of UV,” explained Ray Hyland.
“If you look at our ROM HD gimbal, you’ll see we use a carbon fibre composite body, which allows us great robustness at low weight for integrating large, advanced sensors inside. Fully loaded, the gimbal weighs just 77 lb [35 kg], which is very light for this size of gimbal.”
The ROM HD typically integrates five sensors: a 1080p LWIR camera from InfraTec with a germanium lens, Ofil’s own 1080p DayCor UV sensor, a 4K Sony EO camera, a 61 MP Sony photo camera, and a laser rangefinder accurate to 5 km. A cooled MWIR sensor for detecting gas leaks is also available.
The company also showcased its ROMLite HD, which weighs 44 lb fully loaded, although it can be customised with lighter sensors down to 30 lb. Its standard sensors are the same as the ROM HD’s, but with room for four; the end-user simply chooses which they want.
“It’s all fibre-optic architecture internally, allowing us totally lossless data extraction from 1080p HD, IR and UV cameras without needing the data compression that traditional copper-wired gimbals have to embed somewhere,” Hyland added.
A single hybrid fibre-optic and copper cable carrying data and power runs from the back of the gimbal. Data is captured using the LineVision Desktop software from Remote Geosystems, a program and report generator well-known to geospatial and utility companies.
The main control station for the two gimbals is a computer with a 24 in touchscreen, which can be mounted inside any vehicle (including crewed aircraft). The live feed enables monitoring of visible sensor data including 1080p IR streams.
A hand controller is also supplied. Made from carbon fibre, it has a touchscreen and tactile controls, the latter being configurable for different users.
“Although the volume is of course still lowest with our small, 2 lb UV camera designed for smaller UAVs, these larger gimbal systems are designed for helicopters, airplanes and large UAVs,” said Hyland.
Taisync showcased its Viulinx DUO dual-band radio module, which incorporates 2.4 and 5.8 GHz data links.
“We’re manufacturing this modem using all Green UAS-approved components and certification. We can therefore work with UAV manufacturers to get NDAA compliance too,” said Yan Li.
“There is far less interference in the 5.8 GHz band almost everywhere. And as far as we know, it’s the only standalone link solution that supports frequency-hopping between this and the 2.4 GHz band.”
The Viulinx DUO measures 65 x 43 mm, consumes less than 6 W during standard operation, and transmits at 26 dBm at 2.4 GHz and 23 dBm at 5.8 GHz. It incorporates a number of interfaces including Ethernet for video connection, and serial ports for telemetry transmissions.
Taisync also showcased its VuiRC2.5, a 5.5 in (14 cm) Android-based handheld controller with the Viulinx DUO built in. It is intended as a low-cost, high-performance small GCS for UAV operators. The system is currently at the prototype stages, with production to follow.
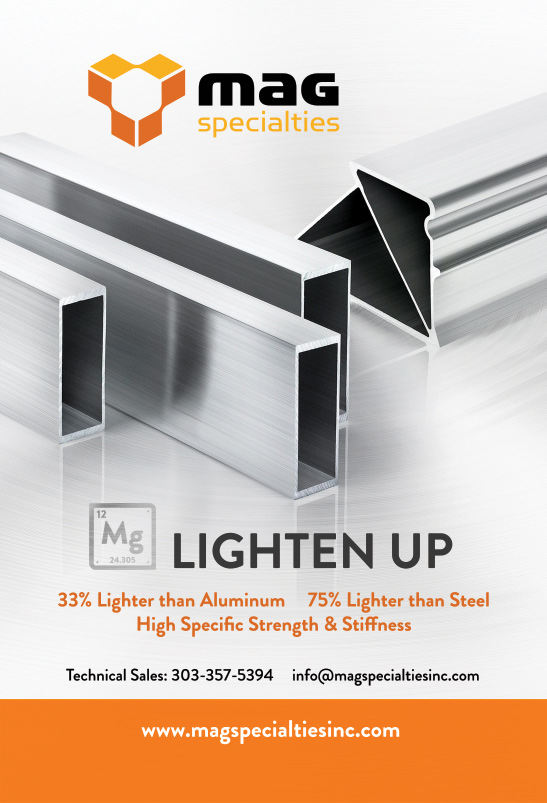
Freefly Systems discussed its new Pilot Pro handheld GCS with us, which has been designed and built around a Samsung Active Tab 3 Android tablet, and with other features around that.
“The system is ruggedised, has ultra-high brightness, and is entirely user-configurable so that integrators can install whatever applications or extensions they want for operating their uncrewed systems,” said Matt Isenbarger.
“It’s also designed to be upgradeable in the future, as the peripheral control hardware can be unplugged from the Samsung tablet and integrated with a different one as new models come out. We also have mounting locations on the sides, which are principally intended for users who have iOS or other non-Android systems they want in their GCS network, or if they want additional control buttons or knobs.
“A lot of our clients are in UAV cinematography, so we expect they’ll use those for focus wheels and similar camerawork tools that aren’t already available.”
The Pilot Pro’s factory-set peripherals include manual switches for altitude settings, following GNSS points, and tools for high-fidelity control in cinematography or inspection work such as ‘velocity clamps’ to adjust the speed and velocity (both vertically and horizontally) of the UAV and its gimbal.
It is also being designed with a radio interface on the back, which can accept either a Doodle Labs radio (currently NDAA-compliant) or a 2.4 GHz Herelink radio, although Isenbarger notes that Silvus, Persistent Systems and DTC radios will be compatible soon, following some development.
“We also have a number of interfaces for different power options, and USB-C which can be converted into HDMI,” Isenbarger added.
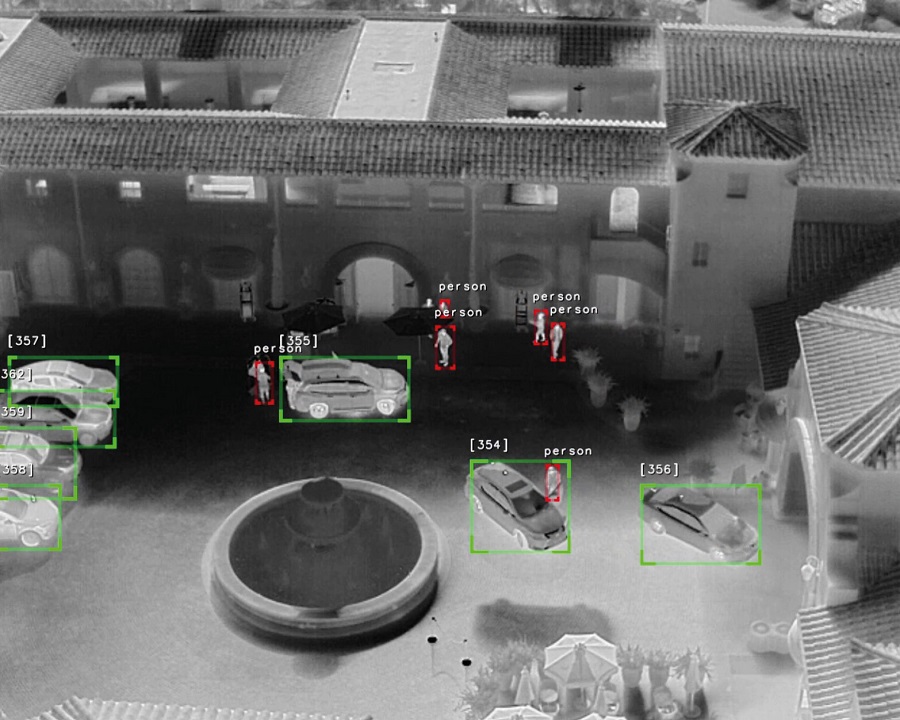
Teledyne FLIR showcased a number of its latest innovations for thermal sensing in autonomous applications. Among them was a perception software solution developed principally for advanced driving assistance systems (ADAS) but that can also be applied to uncrewed vehicles.
“It’s called Prism AI, and it’s a collection of software libraries that enable classification, object detection and object tracking that runs on low-power embedded processors,” said Arthur Stout. “It started in ADAS, where it was trained for visual and thermal recognition of traffic signs, pedestrians, bikes, motor vehicles and other things you’d see on the road, whether driving or driverless.
“We’re now using it for other missions. In UAV applications, doing things like air-to-ground target detection so that a UAV can classify people, vehicles, maritime targets and so on. In air-to-air, we have an interest in UAVs watching for other UAVs, as part of advanced security systems, to direct a gimballed camera that can pan, tilt and zoom to a moving object of interest.”
Prism AI has been developed with edge computing in mind. Teledyne FLIR is producing it with a set of libraries that customers will be able to install on their preferred GPU, although at the time of writing, they were compiled to run only on Qualcomm and Nvidia processors, particularly embedded applications such as the RB5 from the former and the Xavier and Orin from the latter.
FLIR also displayed its Boson+ thermal camera module, which has a 12 µm pixel pitch and a spectral band of 8 to 14 µm. It also comes with either 640 x 512 VGA resolution or 320 x 240 QVGA, and thermal sensitivities of less than or equal to 20 mK in its Industrial version or 30 mK in its Professional version.
Haskel International has developed a system for safely refuelling hydrogen gas tanks in UAVs and any other hydrogen-powered uncrewed systems.
“Our UAV RS AG-75 is essentially a unit that boosts the hydrogen delivery from common hydrogen bottles or an electrolyser into the fuel cell’s tank at 5000 psi, and we’ve engineered the solution to be portable so that it can be used anywhere; it also requires no electricity to work,” said Loy Reeder.
“Boosting hydrogen gas pressure is not as easy as you might think. To safely boost it to high pressure, the system needs to be heat, flame and spark-free, with no possibility of ignition sources, as hydrogen is explosive.
“That means it’s really hard to make it electric or electronic in any way, and the kinds of compressors you’d use for inert gases can’t be used with hydrogen.”
Haskel avoids these problems by having an entirely pneumatic booster, based on the technologies used in its larger gas refuelling systems for heavy industry. The UAV RS is also available in versions with nominal maximum delivery pressures of 1500, 3000 and 7250 psi.
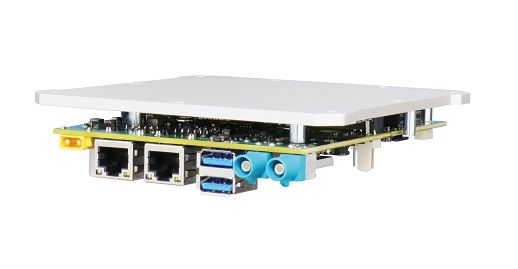
Rugged embedded system manufacturer Neousys Technology arrived from Taiwan to debut its FLYC-300 UAV mission computer at the expo. The system is powered by an Nvidia Jetson Orin NX system-on-module, and weighs 300 g, hence its name.
“For real intelligence, modern autonomous aircraft need eyes and a brain,” said Chris Ni. “The Orin NX serves as the brain, with 100 TOPS of operating power, enabling extensive real-time AI functions including image processing, object detection and environmental modelling.
“For eyes or other forms of sensing, the end-user can connect their sensors to the FLYC-300 by Ethernet, USB 3 or GMSL2 interfaces. GMSL2 is a serialised MIPI, which can use a thin cable to transmit MIPI signals.
“Through these interfaces we can support 2D, 3D, thermal or hyperspectral cameras as well as Lidar, to gauge depth, shape, colour and motion of objects, and distinguish near-identical objects from each other.”
For outputting command signals to the flight controller, the module features a port for UART, one for CAN 2.0, a USB 2.0 connector, an I2C and several GPIOs. All the ports for sensor inputs are at the opposite end from those for command signals, preventing avionics network designers from tangling the cabling for the flight controllers and sensors.
Also, one M.2 NVME interface is available for data storage. Overall, the FLYC-300 measures 124 x 123 x 32 mm and consumes 15 W in typical operation over a 12-60 V DC input. It can safely operate between -25 and +70 oC.
“We also have designed a space for installing 4G or 5G modules, so wireless and cloud connectivity is also possible with this system,” Ni added.
“And for UAV manufacturers who find the 300 g weight still too much, we can remove the enclosure and the weight drops by about half.”
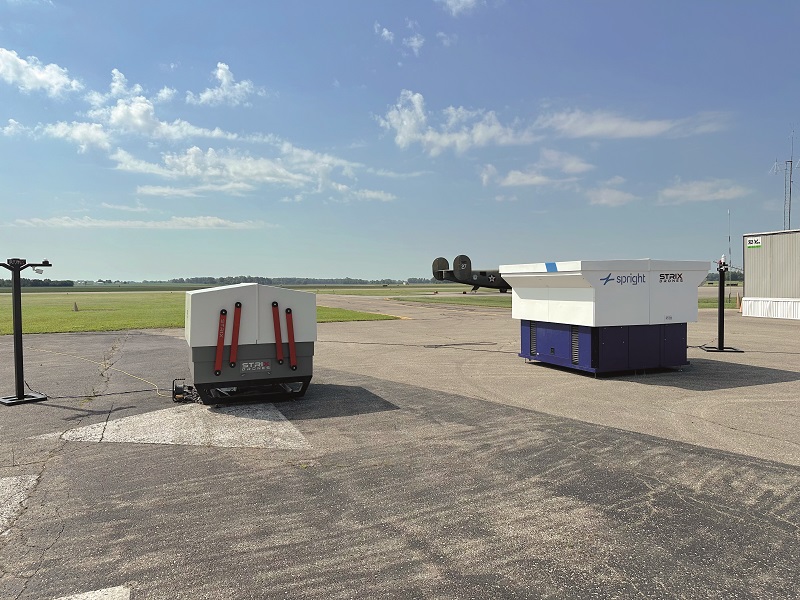
Strix Drones exhibited its range of UAV-agnostic docking, charging and housing stations, which currently consists of four models: the Strix 1100, 1600, 2100 and Strix Drone Drop.
“The Strix 2100 is our largest system, and the only docking station on the market big enough to host a fixed-wing eVTOL UAV,” said Niv Aharoni.
“One of our patented technologies in this system enables us to rotate the nose of the UAV to face the wind for take-off. Weather sensors are mounted and connected to the docking station, and a disc on the landing pad is rotated by our control computer based on the data from those sensors.”
When the 2100 is closed, its length is 15 ft (4.5 m), and its width is 7 ft. When its doors are opened, the clear area available for landing a UAV or eVTOL is 6.5 sq ft. After the UAV lands, the system closes and protects it from the weather.
“It’s ideal for any UAV measuring within 7 sq ft from rotor tip to rotor tip,” Aharoni added. “The Strix 1600 is more for mid-sized UAVs like the DJI M300, while the 1100 is more for UAVs less than 3 ft in size, like the Parrot Anafi.”
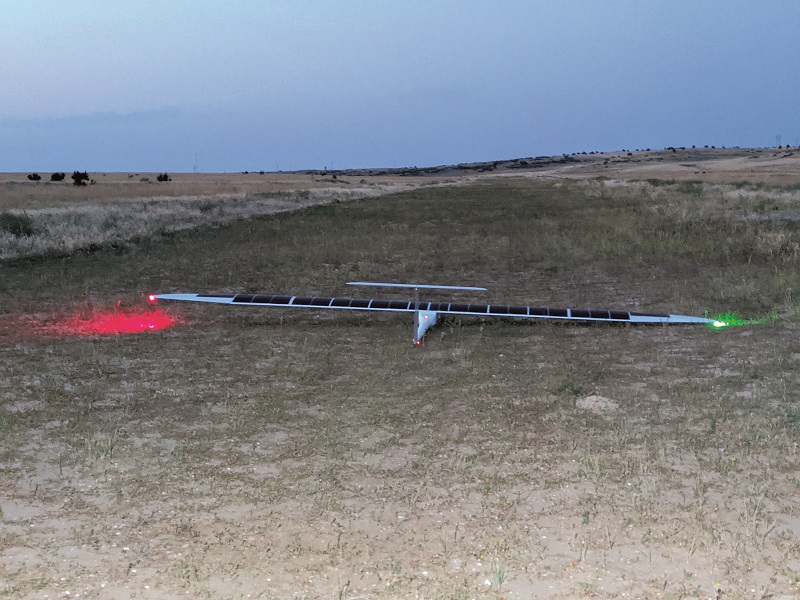
Astrium unveiled its solar-powered fixed-wing UAV platform, the Sunlink XD (SLXD), which has a 20 ft wingspan coated in a thin-film solar cell patented by Sunlight Aerospace, a company owned and operated by one of Astrium’s founders.
“They’ve been developing several versions of this UAV, and it’s been handed over to Astrium to market, operate, flight-test, modify and improve it,” said Ryan Osteroos. “We’ve been pushing it recently for more range, flight time, data and maturity.
“It has the ability to fly at 60,000-65,000 ft and perform long-endurance missions, particularly near the equator where there’s more sunlight. It was originally designed to act as a cell network comms relay in critical areas, as a single cell or in formations to cover more ground, but we’ve also been getting huge interest from airborne mapping customers and emergency services operators who want as much uptime as possible.”
The SLXD weighs 13 lb (5.9 kg) and has a MTOW of 55 lb, enabling considerable battery and payload capacity that can be traded off for balancing mission functionality against flight time. Its demonstrated flight endurance, proven during a cloudy day in August, is given by Astrium as 9.5 hours.
The craft is designed to be inherently stable in flight, with the qualities of a glider. It cruises at 6-7 m/s (21.6-25.2 kph), enabling a maximum straight-line range of 600 km.
As well as its development of the cells for the SLXD, Sunlight Aerospace also has developed its own stoichiometric single-step deposition processes, along with the formulation and structure of its thin-film multi-junction solar cells, to optimise the efficiency and specific power of its flexible PV modules for HALE UAV operations.
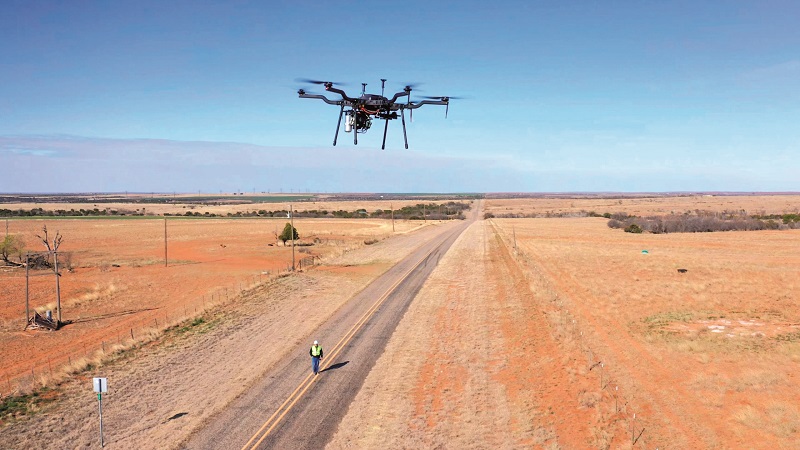
Harris Aerial displayed its H6 hexacopter UAV, which is offered in three varieties, each integrating a different type of powertrain for different mission requirements and fuel availability. The power units can be uninstalled and replaced with a counterpart in the field as needed.
The Carrier H6 Hybrid EFI is powered by the company’s H2400EFI generator, which provides 2.4 kW of continuous power. It is built around a Zenoah G320RC engine, a 32 cc two-stroke, spark-ignited unit running on gasoline, typically carburetted when issued as standard.
The Hybrid can fly for up to 2.5 hours with a 5 kg payload (its maximum carrying capacity), up to 2000 m above mean sea level (AMSL), although that can change depending on the payload.
The Carrier H6 Hydrone UAV meanwhile is a hydrogen-electric aircraft, integrating Intelligent Energy’s IE-SOAR 2.4 kW fuel cell power module (FCPM). The FCPM weighs 4.8 kg, can operate in temperatures from -5 to 40 oC, and has FCC and CE safety certifications as well as dual redundant power systems. It is capable of 8 kW of peak power (2.4 kW being its continuous maximum output), supplied over a DC-DC regulated 50-70 V bus.
The Hydrone can fly for 1.5 hours when carrying its 5 kg maximum payload weight, or up to 3 hours when empty, and can climb to 3658 m AMSL. During flight, the operator can monitor the FCPM’s hydrogen fuel levels and health parameters via a CAN interface between the fuel cell controller and autopilot.
Lastly, the Carrier H6 Electric integrates a 16 Ah lithium polymer battery system with a life cycle equivalent to 250 flights. This gives the battery-electric hexacopter a 48-minute maximum flight time (without any payload), and while flight times can vary, its payload capacity is given as 8 kg.
Whichever powertrain is integrated, the Carrier has a 25 kg MTOW, a maximum flight speed of 15 m/s and a maximum vertical ascent speed of 2.5 m/s. It also comes with dual-antenna RTK GNSS as standard, as well as dual-band comms with 2.4 GHz and 902-928 MHz data links, and a Cube Orange as autopilot.
The company offers the system and its configurations for missions in search & rescue, industrial surveys (including with Lidars and IR cameras), and testing and developing new or proprietary payload solutions.
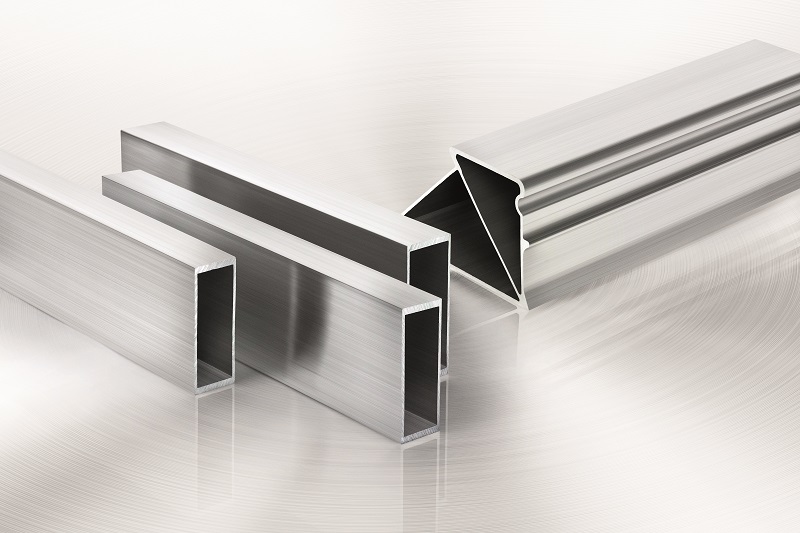
Mag Specialties displayed a range of its extruded magnesium components as part of a static demonstration of the uses of magnesium in UAV airframes.
“There are a lot of UAVs at this show with carbon tubes connecting their rotors to their main bodies, and everyone tells you the reason they choose carbon is because aluminium’s too heavy,” said Nes Abdulrahman. “But if you ask them why they aren’t using magnesium, they say they didn’t know it was an option.
“Magnesium is one-third lighter than aluminium, so it approaches the weight of carbon fibre composites but has comparable mechanical properties to 6000-series Al alloys and is far cheaper than carbon. Granted, carbon brings benefits like being able to lay the fibres in certain directions to maximise directional strength, but wherever the linear properties of magnesium are suitable, there’s huge potential for cost savings in uncrewed aircraft structures.”
The magnesium arrives at Mag Specialties’ facilities as a cylindrical billet. Extrusion begins with it being heated, after which it is pushed through a die, emerging from the other side in the shape defined by the die.
The company’s parts are therefore predominantly linear, structural parts, although Abdulrahman added that curved parts such as gimbal housings can be produced through die casting or a process known as thixomoulding on request. Extruded components tend to have a lead time of around 8 weeks.
“Magnesium also has field-repairability that you don’t get with carbon fibre,” Abdulrahman said. “If carbon cracks, it’s extremely difficult to patch, as essentially you’ve compromised it, but magnesium can be re-welded, patched or gradually bent if needed, much like aluminium.”
UPCOMING EVENTS
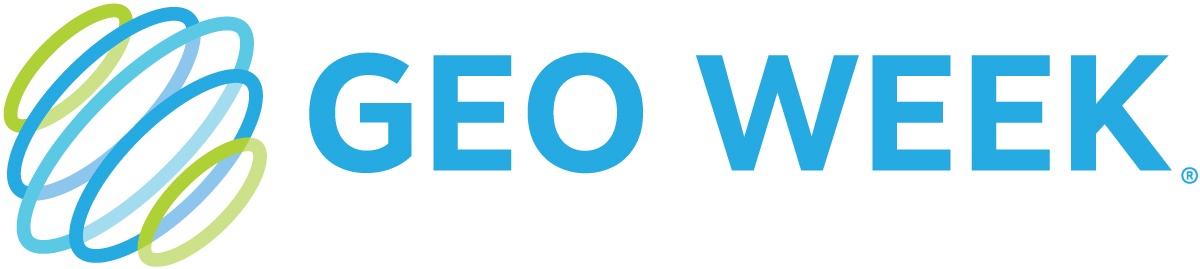
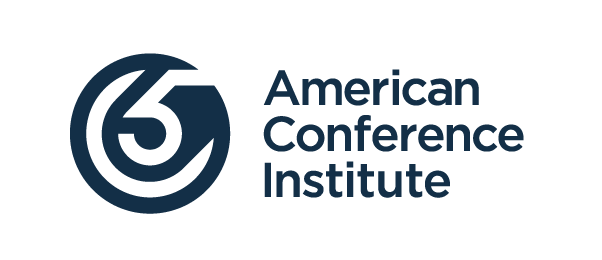
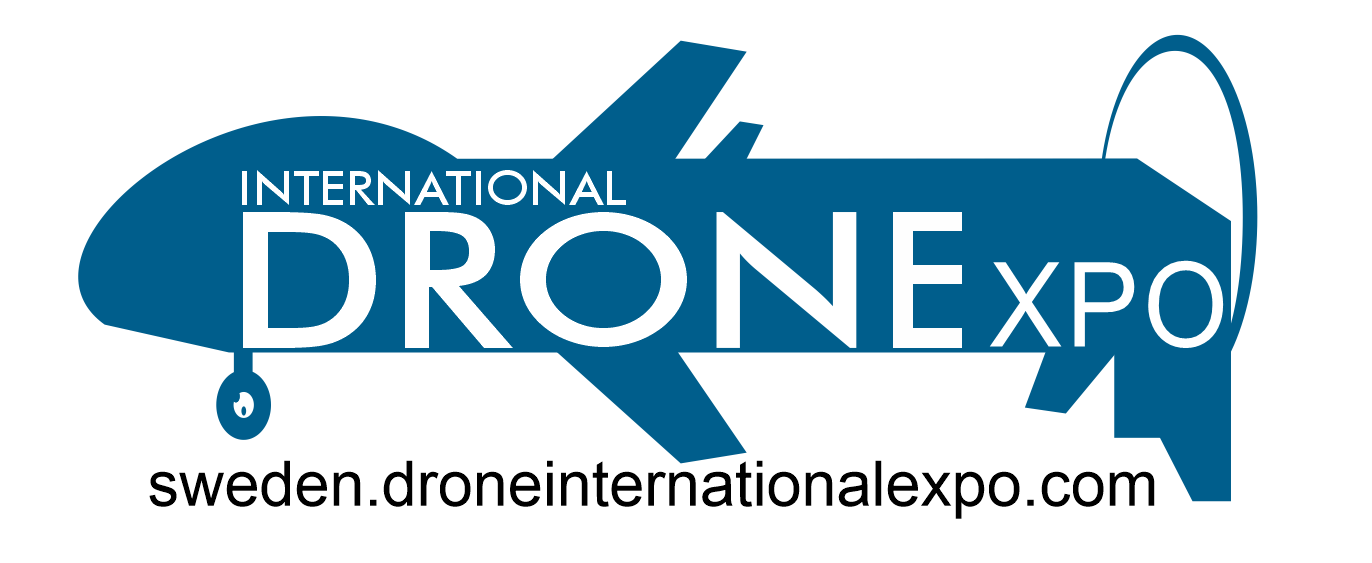
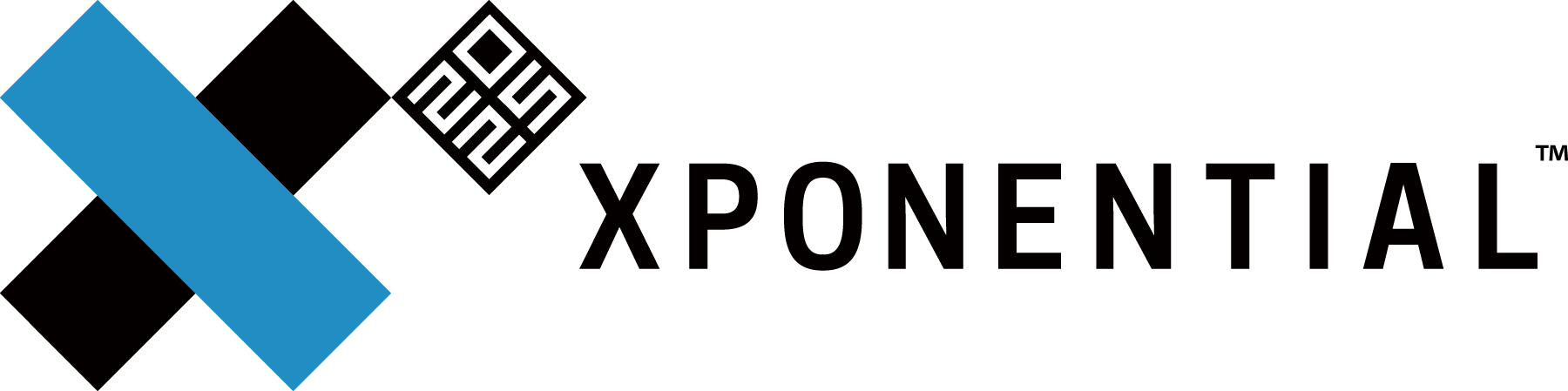
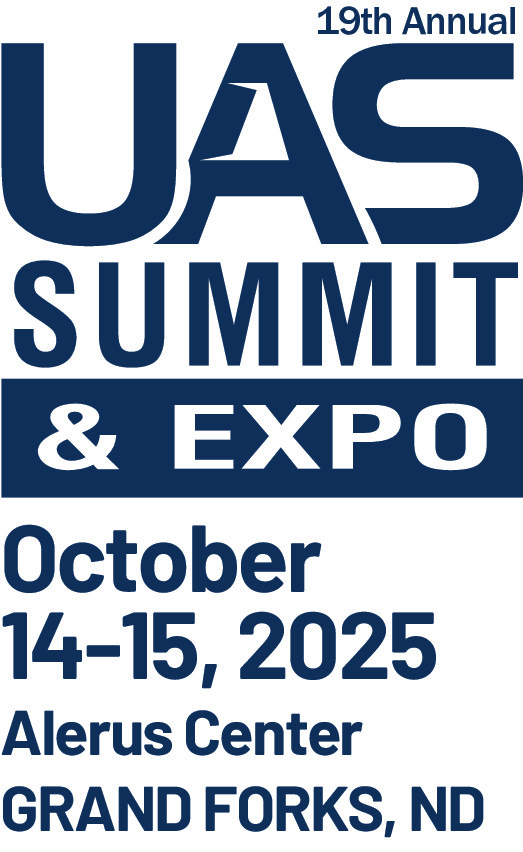

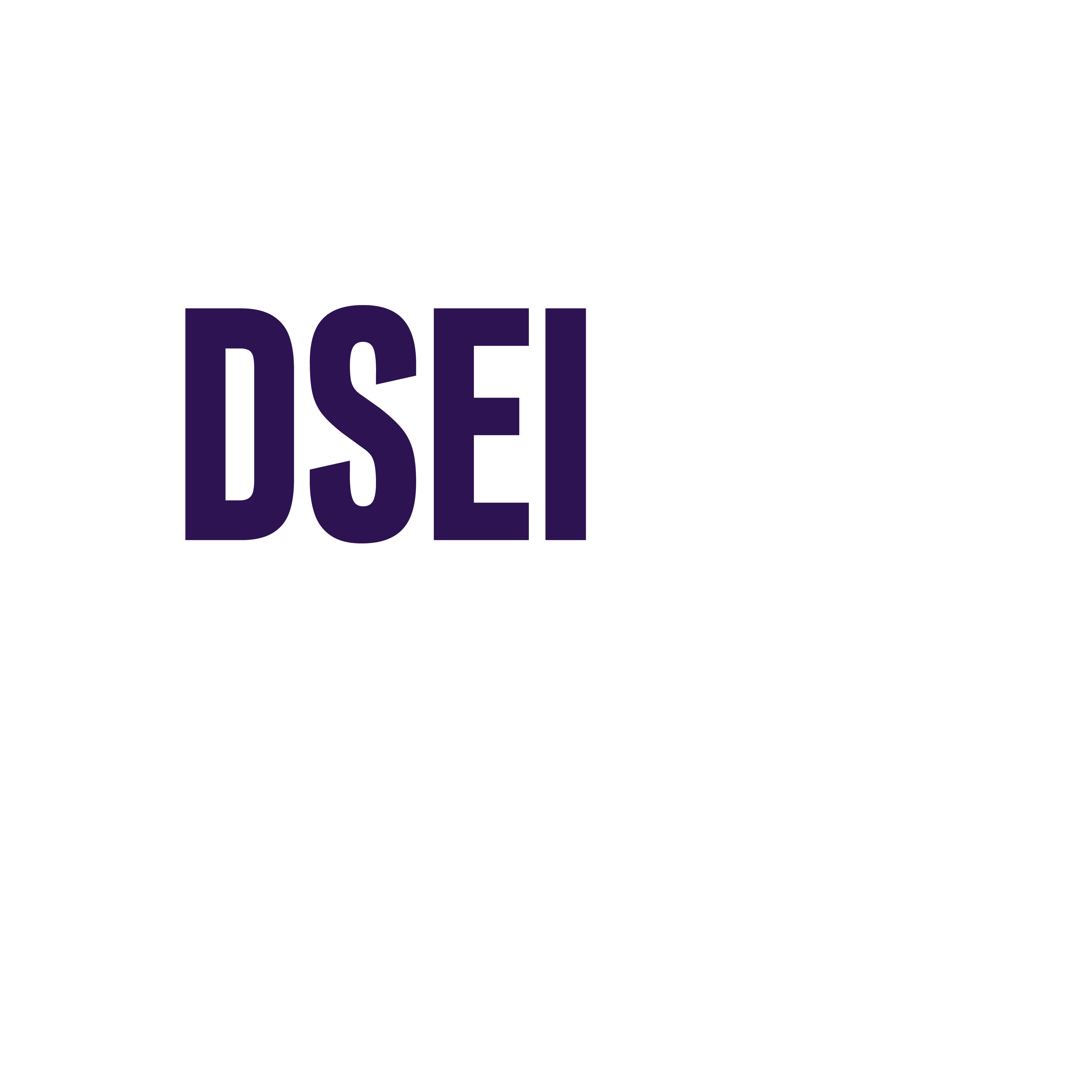
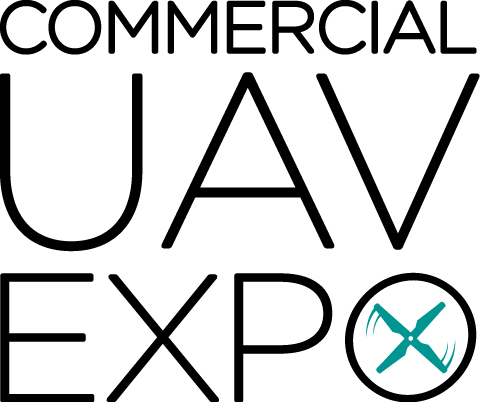
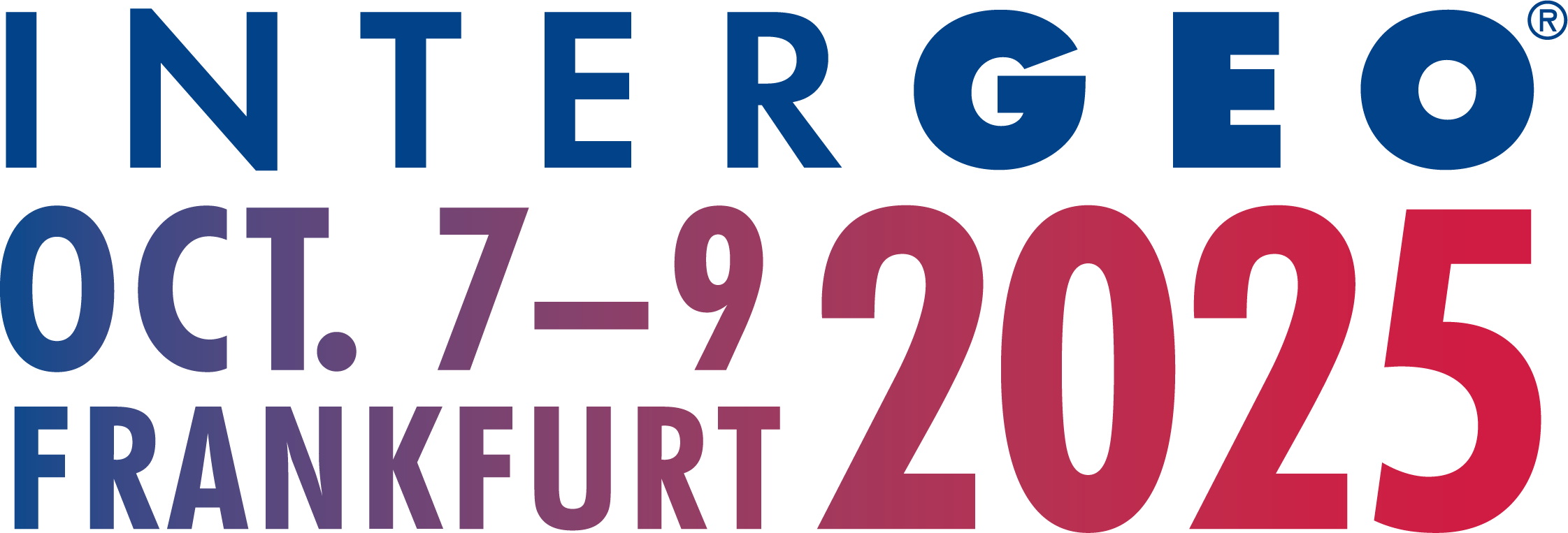
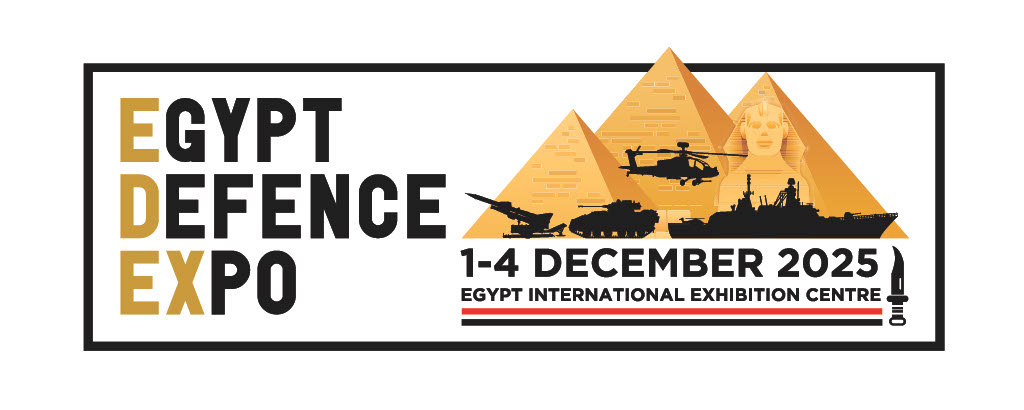
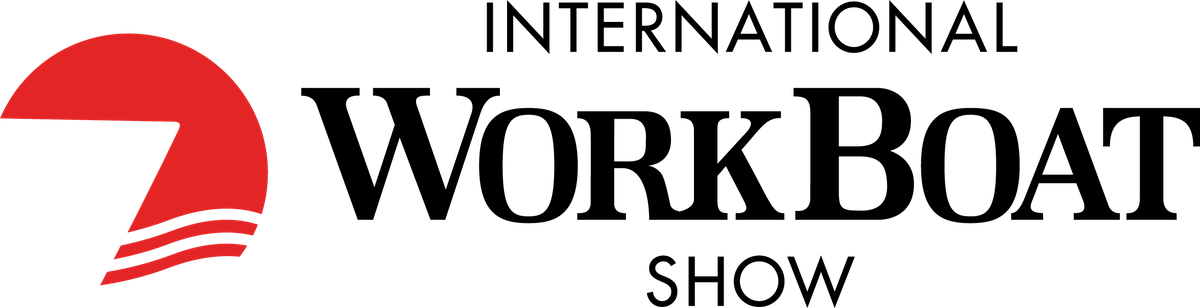