Countdown starts for cells
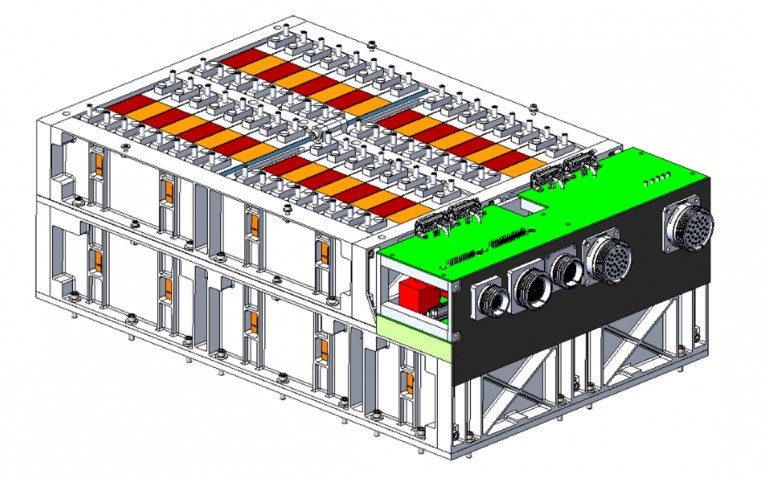
GS Yuasa Lithium Power (GYLP) is developing a small but scalable battery for space systems (writes Nick Flaherty).
The small form factor lithium-ion battery has completed the Preliminary Design Review and is now moving to the critical design phase.
GYLP’s design integrates the recently qualified LSE12x lithium-ion cell developed by GS Yuasa Technology. The flexible design accommodates 16 to 96 cells with a power of 720 to 4320 Wh and can be electrically configured to support both low- and high-voltage bus applications.
More autonomy and the use of neural network accelerators is driving up the power requirements in space systems. GS Yuasa has already flown 4.4 MWh of lithium-ion energy storage into space, and has also introduced a 12 Ah cell.
The smaller cells and batteries will be fully configuration controlled and built to AS9100 aerospace-quality standards with an auditable manufacturing and change record. This avoids the need to repeat the full qualification and life performance test for each new production lot. Developers can verify that the materials and processes used remain consistent from lot to lot, reducing programme testing costs.
The next stage will be the completion of the critical design review of a qualification model with a 72-cell configuration wired as an 8S9P battery. This has nine parallel groups of eight cells in series providing 108 Ah and 3240 Wh at 30 V.
The configuration incorporates all the manufacturing and inspection processes present on smaller and larger configurations. A full qualification test suite including environmental survivability is planned.
If a cell fails, each eight-cell string can be isolated in the battery through a commandable relay. Battery telemetry enables a satellite operator to detect the event and issue a command to clear or isolate the fault.
The design approach for the 72-cell battery aims to provide the smallest pack size with robust survivability for launching on a rocket. Thermally, the battery is designed to reject heat by conduction through a baseplate tied to the host vehicle’s thermal management system. The connector interface is flexible and can be tailored to match each vehicle’s specifications.
Battery monitoring and available telemetry will also be tailorable, with options for temperature monitoring points, individual cell or mid- and fullstack voltage reporting, as well as redundant heater options.
The battery design includes provisions to mitigate propagation of a thermal runaway event and to collect any material that comes out. GYLP has recently been awarded a US patent for systems and methods relating to effluent containment.
UPCOMING EVENTS
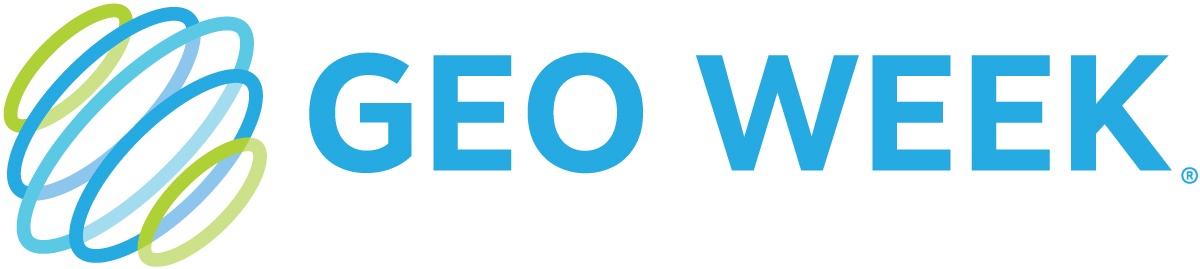
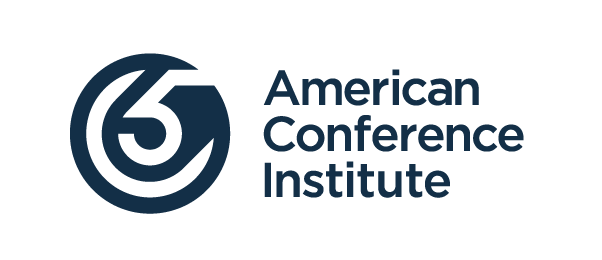
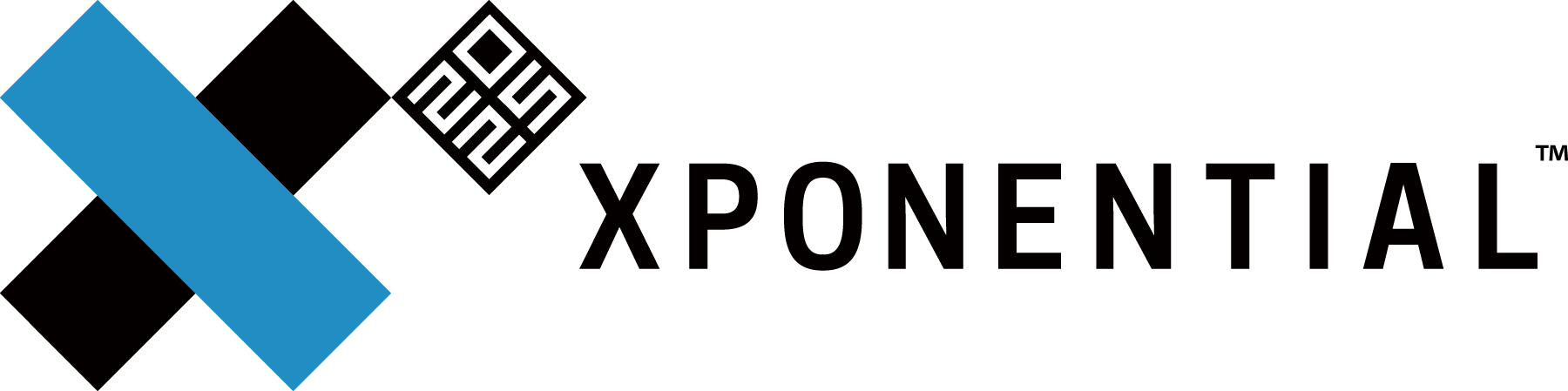
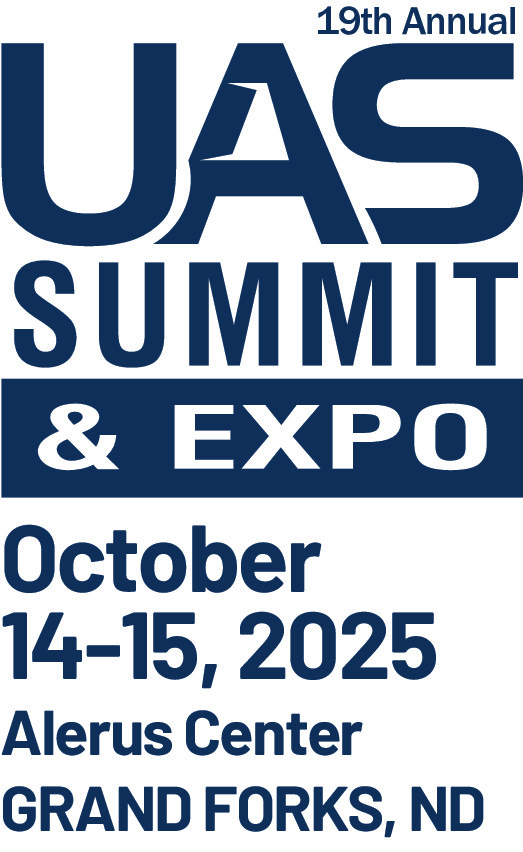
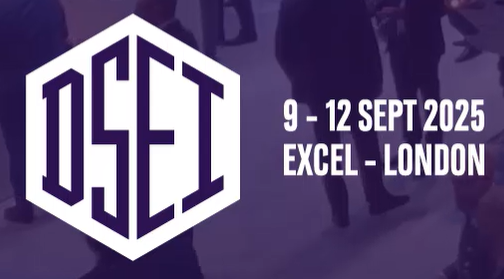
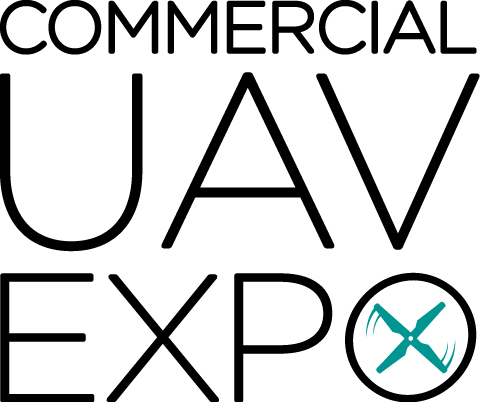
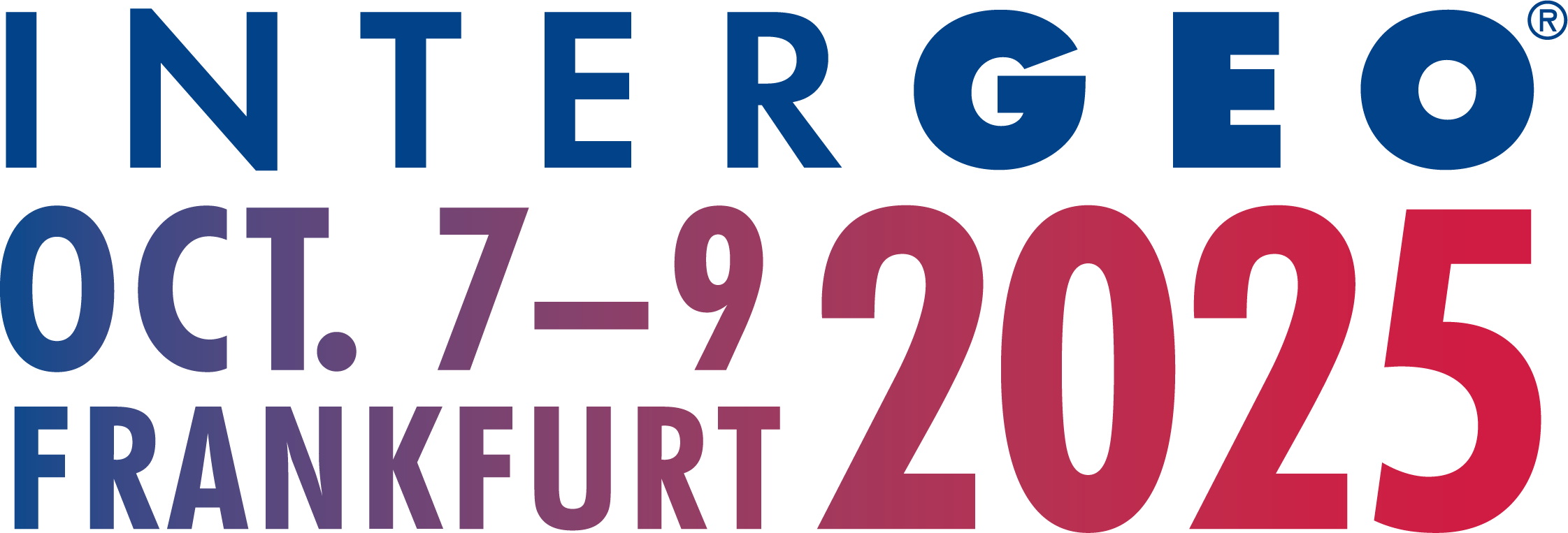
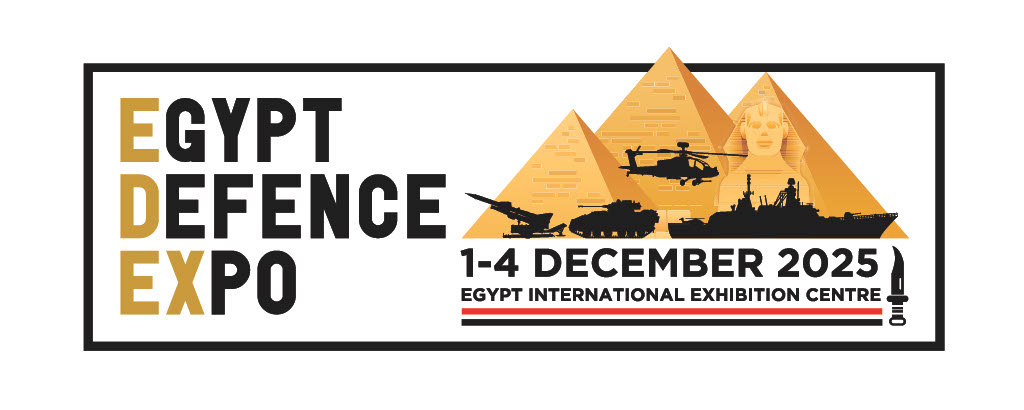
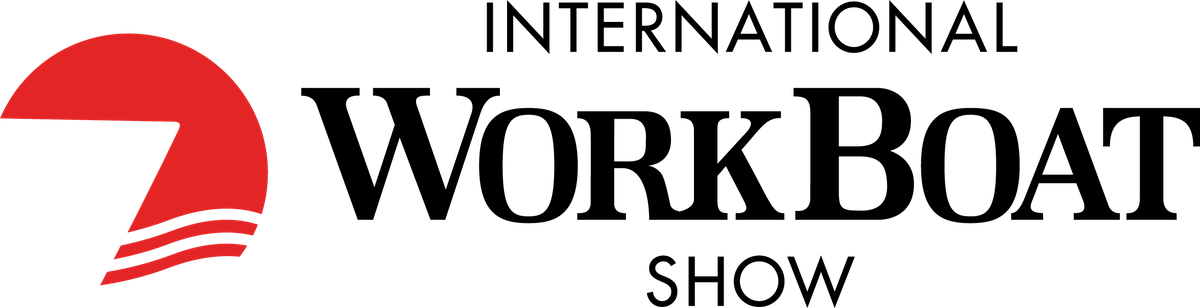
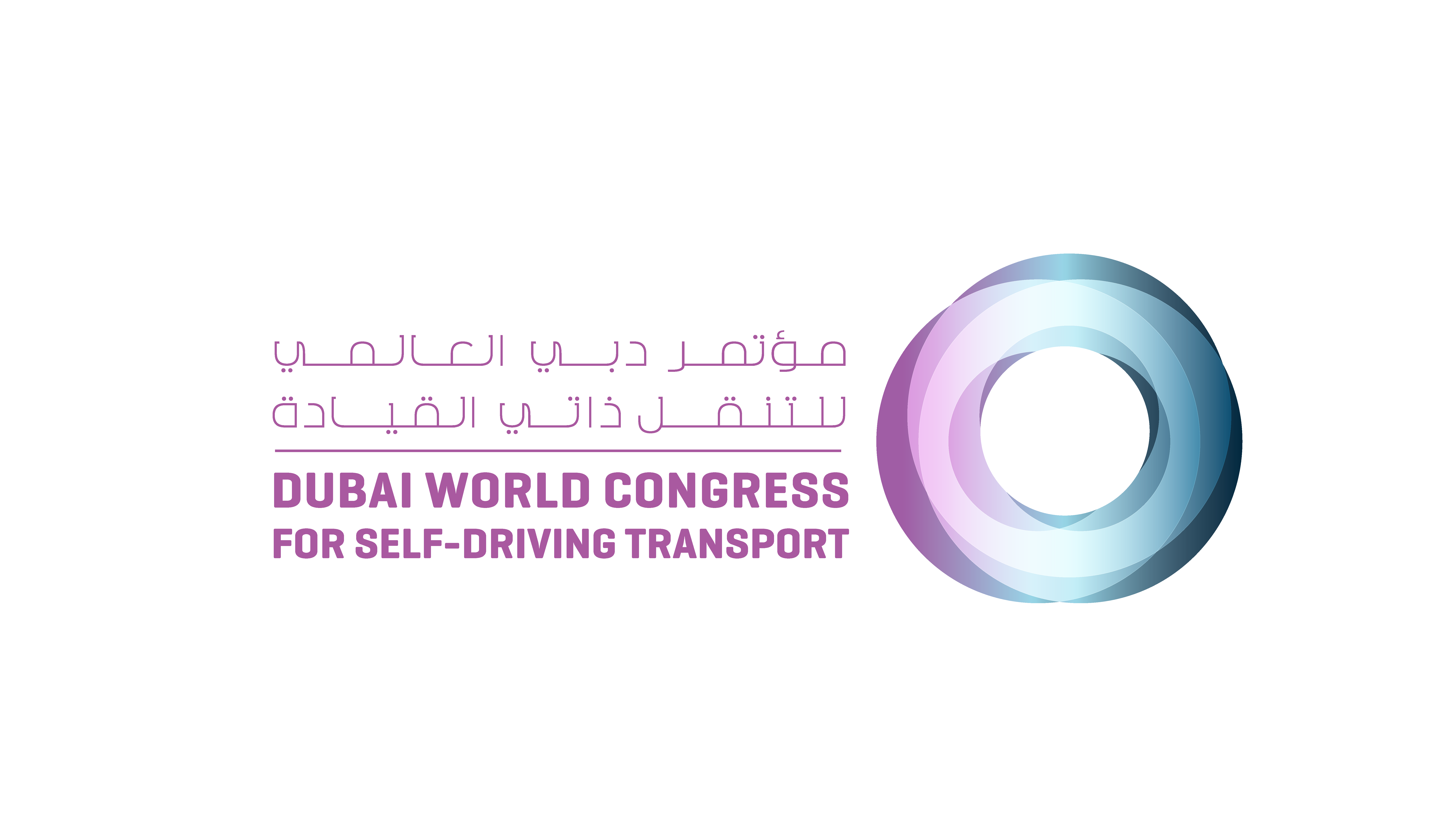
