Nauticus Robotics Aquanaut
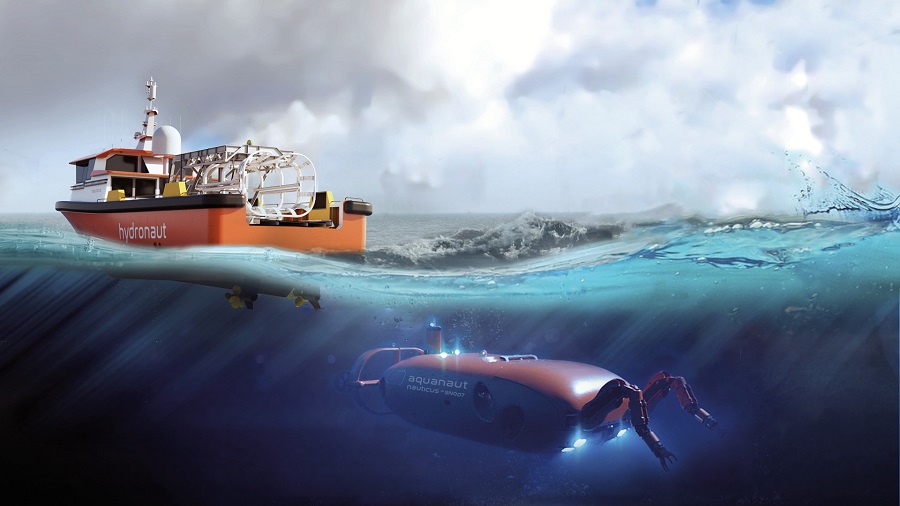
Peter Donaldson examines this AUV which, with its optionally crewed topside support vessel, provides a cheaper and cleaner way to inspect underwater equipment
Nauticus Robotics’ Aquanaut Mk2 is part of a system designed to reduce the cost of offshore underwater survey and intervention work by exploiting the happy consequences that flow from eliminating the need for a tether while operating as an ROV or an AUV.
The 4.2 t, 4.82 m-long, battery powered craft is now being introduced to the commercial market, principally the offshore wind, oil & gas sectors, along with a dedicated support vessel, an AI-based control system called ToolKITT and a suite of sensors and manipulation tools.
Rated to a depth of 3000 m, the Aquanaut has been developed in parallel with the Hydronaut, an optionally crewed topside support vessel that is much smaller than typical support ships, which have to be large to carry the heavy-duty winch and associated topside structure needed to manage the tether for a substantial ROV.
The company reckons this can save as much as 30-40% in operating costs and substantially reduce the environmental impact through lower emissions. Together, the Aquanaut and Hydronaut are called the Nauticus Fleet, of which Nauticus retains ownership and operational control, selling the services it provides.

The idea for the Aquanaut emerged from the combined experience of CEO Nic Radford and his team, who developed mobile manipulation systems at NASA. “There we deployed manipulators on various mobility platforms including two and four-wheeled bases, arachnoid-inspired legs, zero-gravity legs, and humanoid legs,” says vice-president of engineering at Nauticus, Jide Akinyode.
“Along with the hardware design, we spent a lot of time on software development, specifically how to operate these complex robotic platforms in remote locations across poor comms links to do useful work.”
From a design engineering standpoint, one of the biggest challenges came in packaging the required sensors, computers and manipulators to fit inside the vehicle while retaining a shape with the hydrodynamic efficiency to support long-range missions and retain enough energy to do the job and return to base.
Instead of the classic torpedo shape for an AUV, the Aquanaut has a broad, flattened body, and features an oval ring tail that supports the primary pair of propulsive thrusters. For manoeuvring and station-keeping, it has a set of tunnel thrusters – lateral and vertical, mounted front and rear – and an angled pair in the mid-body area.
Its lithium-ion battery pack has a capacity of more than 100 kWh, providing an average range of around 200 km, depending on the selected transit speed, which is typically between 3 and 6 knots.
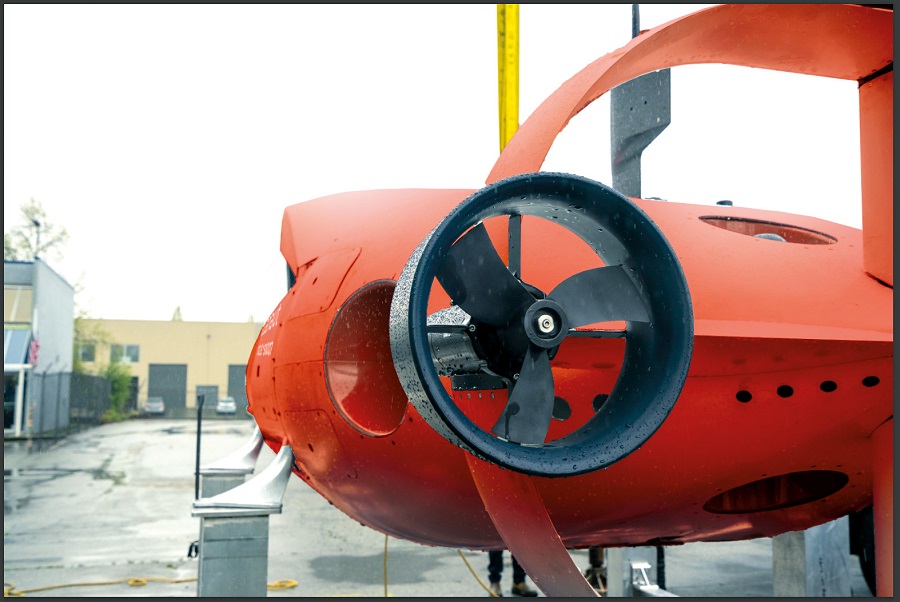
Sensing and perception
The Aquanaut has an array of perception sensors that include passive and active light systems as well as active sonar. By fusing the data from them, the Aquanaut builds a detailed model of its local environment. It then makes use of this model in deciding how to achieve the goals the operator has set for it.
The sensor suite is highly integrated with the Aquanaut’s semi-autonomous capabilities, and allows it to complete a wide range of tasks and objectives. This is one of the characteristics that distinguishes it from operations using traditional ROVs, in which specialised sensors are often swapped out for different tasks.
The sensors, individually and in combination, were selected to support semi-autonomous operation, a choice informed by years of testing and evaluation on test beds and engineering prototypes. Akinyode describes the resolution and accuracy of these sensors as “more than adequate” to support the requirements associated with customer tasks.
The 3D perception system makes use of multiple sensing systems. These include a Voyis Discovery 3D stereo camera with integrated Nova Mini lights, plus Nauticus’ own 3D structured light system. A structured light system projects a pattern, such as a set of stripes, onto an object, and the object’s 3D shape distorts the pattern in imagery captured by a 2D camera. Knowing the original pattern, the software measures the distortions and calculates the 3D shape that caused them.
This is complemented by a 2D Voyis Observer imaging system with Nova Micro lights, along with a Blueprint Oculus M1200d imaging sonar.
A Voyis Insight Pro laser scanner, a Coda Octopus Echoscope C500 real-time 3D sonar, and a Marine Sonic Sea Scan ARC Scout MkII sidescan sonar comprise the survey and mapping suite.
The Aquanaut also carries a set of subsea integrity tools that includes a cathodic protection probe to assess the condition of the corrosion protection systems on underwater hardware, a wall thickness measurement system and a cleaning brush.
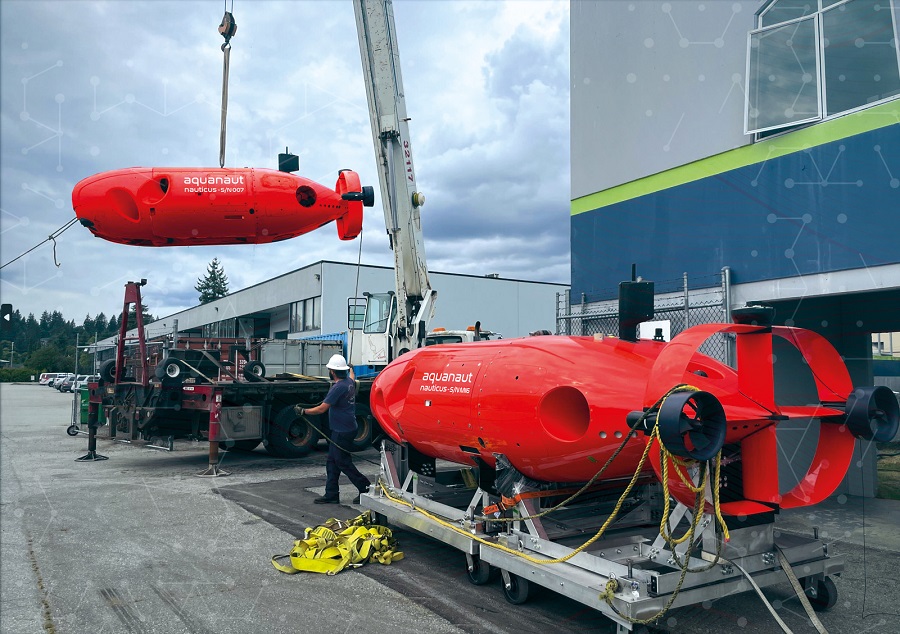
Navigation and comms
The navigation sensor package consists of an iXblue Phins 6000 fibre-optic gyro-based inertial navigation system, a Nortek DVL500 Doppler velocity log, an AML Oceanographic AML6 sound velocity, a conductivity and temperature sonde, and an Imaginex 837 AXi multi-beam obstacle avoidance sonar.
Positioning sensors include a Sonardyne Avtrak-6 tracking, comms and relocation transceiver, along with an increased instruction set GNSS and radio module.
The underwater comms system includes both acoustic and optical bearers. The acoustic element relies principally on two devices: an M25M series modem and Dolphin Comms’ ‘direct blast’ cancellation system that enables full duplex continuous telemetry without interference from signals from the transmitter to the local receiver. Optical comms are provided by a Hydromea Luma X 10 Mbit/s optical modem with a 50 m range.
In the Aquanaut’s normal operation, the assumption is that acoustic comms constraints apply, says Akinyode, but if optical communication is available, the comms system can take advantage of the greater bandwidth it provides to offload data gathered during recently executed tasks, for example.
Vice-president of operations Todd Newell says the Aquanaut is one of the first autonomous vehicles to offer both survey/inspection and intervention capabilities. For survey and inspection work using data collection and perception sensors, the vehicle is said to be in ‘excursion’ mode, while with a pair of robot arms fitted for physical manipulation of underwater hardware it is in ‘intervention’ mode.
Intelligent arms
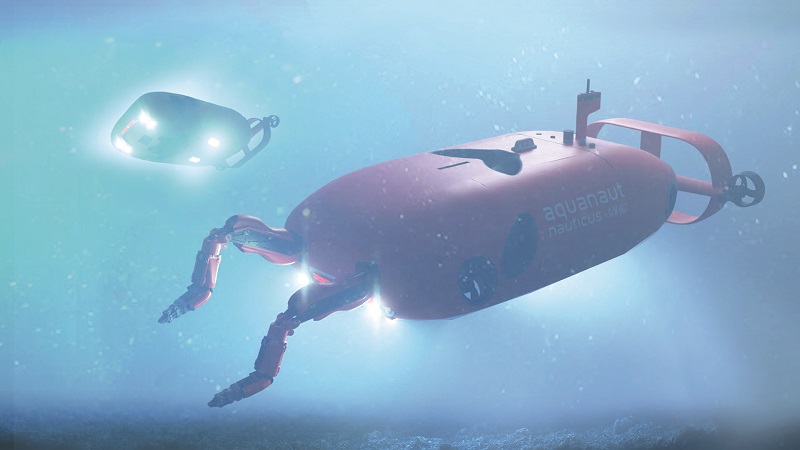
The manipulator arms are members of Nauticus Robotics’ Olympic Arm family, all of which are electrically powered and can be fitted with interchangeable tools.
The company says full electric operation makes the arm much more environmentally friendly than hydraulic alternatives, because there is no hydraulic oil to leak, while providing sufficient lifting power to handle tasks normally undertaken by divers. The Aquanaut carries extra tools in its front trunk (‘frunk’), and can change them itself underwater, Newell says.
The variant of the Olympic arm fitted to the Aquanaut can lift 60 kg at full extension and offers six degrees of freedom in motion, plus the gripper’s n x 360o of rotation and opening and closing movements. The gripper can exert a force of 454 kg, and includes a set of force-feedback sensors to allow some delicacy of operation to complement its power.
The arm itself weighs 109 kg in air or 73 kg in water, and measures 584.2 mm long, 266.7 mm wide and 977.9 mm high when stowed.
The Aquanaut’s sensors and manipulators are coordinated locally by onboard algorithms, Akinyode adds. Basic tasks such as station-keeping and manipulation tasks are controlled autonomously by the vehicle, while the operator has responsibility for high-level task direction of the platform.
Both the Aquanaut and the Olympic arms also feature the company’s Azimov system, which is designed to ensure safe operation near people, equipment and infrastructure.
Fine control of the manipulators is also the responsibility of the vehicle’s toolKITT onboard software, and manipulator accuracy is independent of the available comms bandwidth. The operator does not directly drive the manipulators; instead they specify goals for the platform to achieve, and the Aquanaut figures out the best way to achieve them. That is the essence of supervised autonomy.
Newell adds that while the robot can perform intervention tasks without human assistance, that is not Nauticus’ policy. “For quality and safety reasons we maintain the person in the loop, and the robot cannot take the next step in a sequence until the operator has authorised it, so a human is always checking what the robot is doing,” he says.
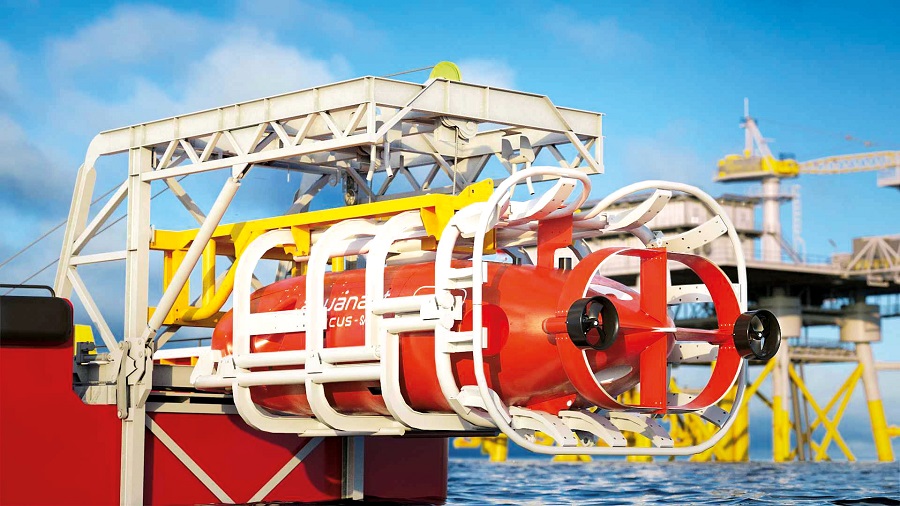
Supervised intervention
One of the most common underwater intervention tasks is opening and closing a valve in a pipeline. “First, the robot has to get within reach of the valve,” Newell says. “It knows in advance what kind of valve it is and which way it needs to turn it.
“Sometimes it will use a gripper to open the valve, other times it will use an onboard torque tool to turn it. The robot follows the same sequence as an ROV pilot. The robot would see the valve, position itself and then position the manipulator or gripper ready to turn it.
“Then the operator checks and says, ‘OK, I agree with you, you have positioned your manipulator correctly, and now I authorise you to take the very first inward motion.’ Then the next instruction might be, ‘OK, now you’re positioned correctly, close your gripper.’ Then you could say, ‘Take the first turn to the right by 15o.’ So you take the job one step at a time between the robot and the person. It’s like a dance.”
Management software
The control software for the Aquanaut and Nauticus’ other robotic platforms comes with a planning and oversight module called the Commander, a comms module known as Wavelink, a primary control module called the Helmsman, a modelling unit called Wayfinder and a data gathering and management module called Loggerhead.
The Commander enables the planning of autonomous missions and control of vehicles from the shore using web-based software, Nauticus says. It is designed for the direct command of operations as well as oversight of simple high-level commands and mission objectives. Platform telemetry, setpoints, commands and mission plans are sent to and from the Commander through Wavelink, which is Nauticus’ proprietary acoustic comms network.
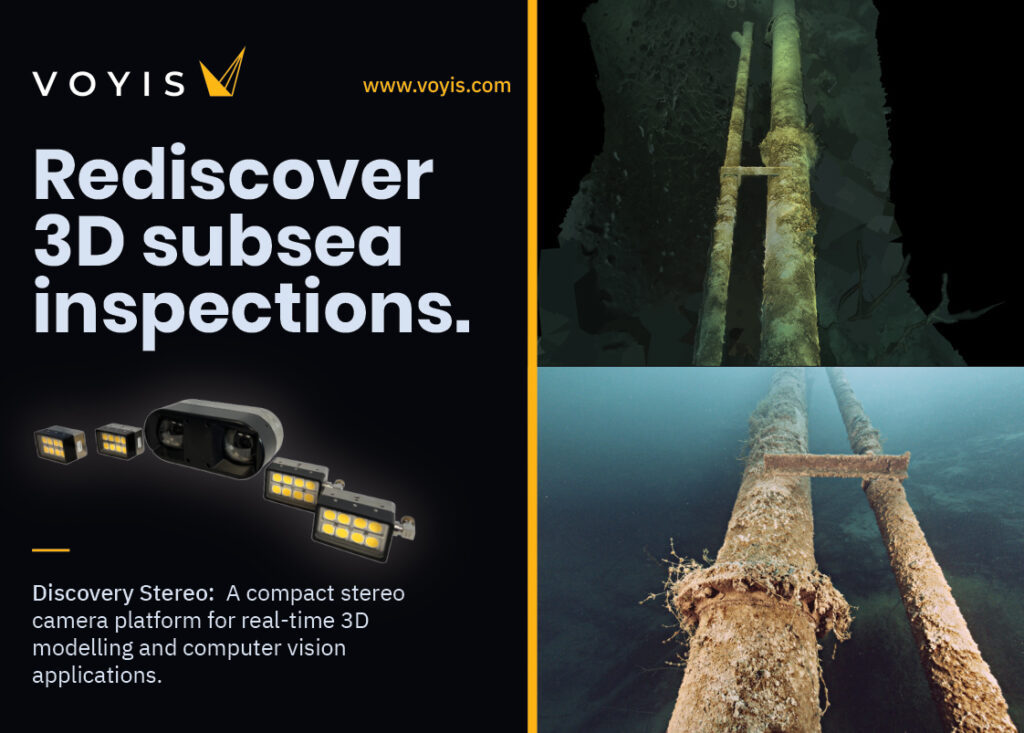
Bridging the air-water barrier between topside operators and subsea units, Wavelink uses a delay-tolerant network that selects the best channel from several comms modes that are available simultaneously.
The Commander’s Autonomy UI user interface provides an insight into the health and status of ongoing missions, and enables operator intervention if it is needed. At the same time, the Commander Companion interface uses platform telemetry and behaviour trees to carry out autonomy-related calculations, delivering the resulting command setpoints to the Helmsman, which handles all the primary control calculations for deployed robotic platforms.
Wayfinder supports mission planning and execution by modelling the subsea environment around the robot, interpreting sensor inputs and providing processed data to the Helmsman and Commander. Many of Wayfinder’s world-model calculations rely on information from onboard odometry from vehicles such as the Aquanaut and on state estimation by the Helmsman. Wayfinder is also an AI system, in that it uses neural network processing to help with cognitive tasks such as object recognition and pose estimation.
The job of the Loggerhead module is collection, visualisation and reporting of data such as runtime diagnostics and so on.
Launch & recovery
While the Aquanaut has traditional launch and recovery (L&R) interfaces so that it can be deployed from vessels of opportunity, the Hydronaut has a custom-built automated L&R system for the Aquanaut. It is designed to deploy and retrieve the underwater vehicle over the Hydronaut’s stern, and is certified to the DNVGL-ST-0378 standard. Its key mechanical components are a basket, a ‘cursor’ and an all-electric gantry crane, and a winch.
The basket is a semi-enclosed structure, open at the back, and designed to protect the vehicle and guide it to its L&R depth. The cursor is a horizontal frame that attaches to the basket to support and guide it, and features guide wheels, guide sheaves for the two lifting cables, and centring devices to align the basket.
The basket is fitted with bumpers to protect the vehicle, an integrated mechanical locking mechanism to secure the vehicle while it is inside, a ‘bullet’ to secure the basket and cursor in the crane’s hang-off lock, and interface points for a pair of lifting cables.
The basket structure is made in two parts that can be separated to provide access to the Aquanaut for maintenance. The system also includes integrated load, speed and length readouts, and is prepared for active heave compensation as well as remote operation, the company says.
The gantry crane transports the vehicle in its cage to and from the launch position over the stern. Driven by an electric motor, the crane travels back and forth on skid beams mounted on the Hydronaut’s deck.
The mechanism also includes routing sheaves for the two lifting cables, a hang-off fail-safe lock for the cursor and the basket, integrated vertical cursor rails, and electrically tiltable cursor rail extensions with end stops. When extended over the stern, the cursor has a 3.3 m range of vertical travel.
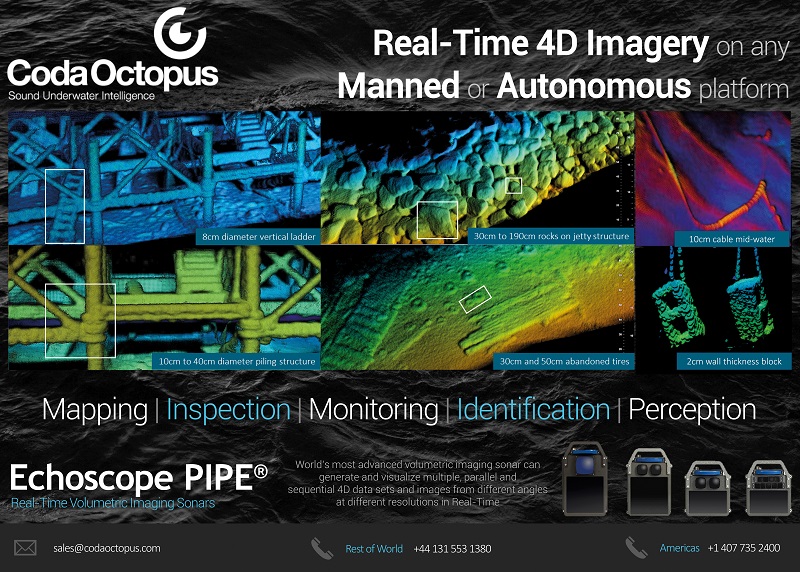
Early operations
The Aquanaut’s development started in earnest following the first round of investment funding that Nauticus received from strategic partners in 2018. Design work focused initially on the electric manipulators, followed by the rest of the vehicle.
The Aquanaut Mk2, as the designation suggests, is the second generation of the vehicle, three of which began commissioning exercises this April, followed by delivery to the North Sea and the Gulf of Mexico to support customer operations.
In June, Nauticus announced a contract with Brazilian oil & gas corporation Petrobras, under which the Aquanaut will use its supervised autonomy capabilities for inspection services in one of Petrobras’ deep water production fields. The vehicle is due to log about a month of subsea inspection time.
Although the main focus has been on the energy sector, some technologies derived from the Aquanaut, including its command and control software, have attracted interest from the defence industry.
In February 2022 for example, the US DoD’s Defense Innovation Unit commissioned Nauticus to convert an existing US Navy mine countermeasures platform into an untethered AUV under the Amphibious Autonomous Response Vehicle programme. The vehicle’s role is to identify and neutralise mines and other targets while keeping explosive ordnance disposal divers out of harm’s way.
Nauticus expects both immediate and long-term demand in the offshore wind, oil & gas and security and defence sectors that could lead to the deployment of more than 350 Aquanauts. The company also anticipates opportunities in markets including support of data centres, autonomous shipping, aquaculture, telecoms, subsea mining and biotechnology.
Specifications
- Nauticus Robotics Aquanaut
- Mk2 AUV
- Length: 4.82 m
- Width: 2.03 m
- Height: 1.71 m
- Weight (in air): 4200 kg
- Payload capacity: 90 kg
- Depth rating: 3000 m
- Cruise speed: 3 knots
- Maximum speed: 6 knots
- Environmental performance: station-keeping in up to 1.5 knot lateral current
- Typical range: 140 km
- Maximum range: 250 km
- Runtime: 30 to 70 hours
- Battery capacity: 101.1 kWh
Some key suppliers
- Inertial navigation system: iXblue
- Doppler velocity log: Nortek
- Water sensing system: AML Oceanographic
- Imaging sonar: Imaginex
- Location and tracking: Sonardyne
- Acoustic comms: Subnero
- Optical comms: Hydromea
- 3D perception: Voyis
- 3D perception: in-house
- 2D perception: Voyis, Blueprint Subsea
- Survey and mapping: Voyis, Coda Octopus, Marine Sonic Technology
UPCOMING EVENTS
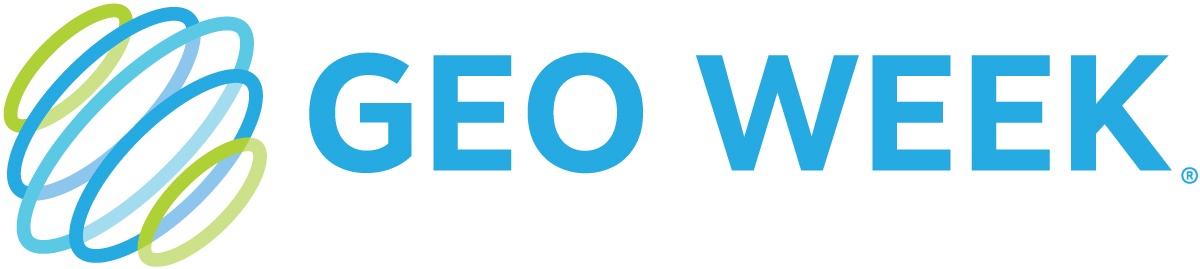
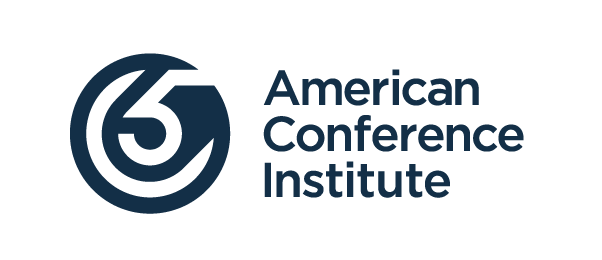
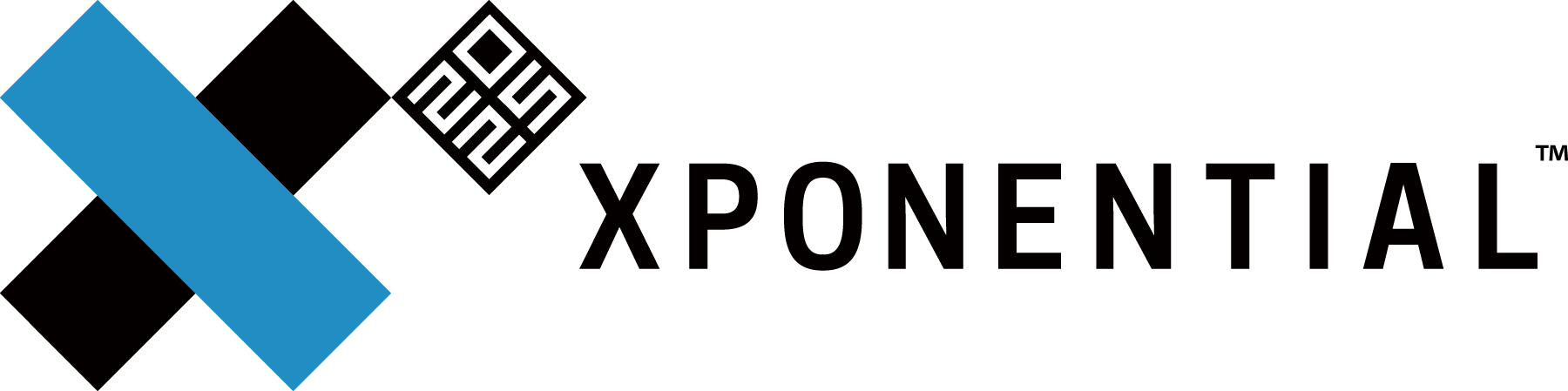
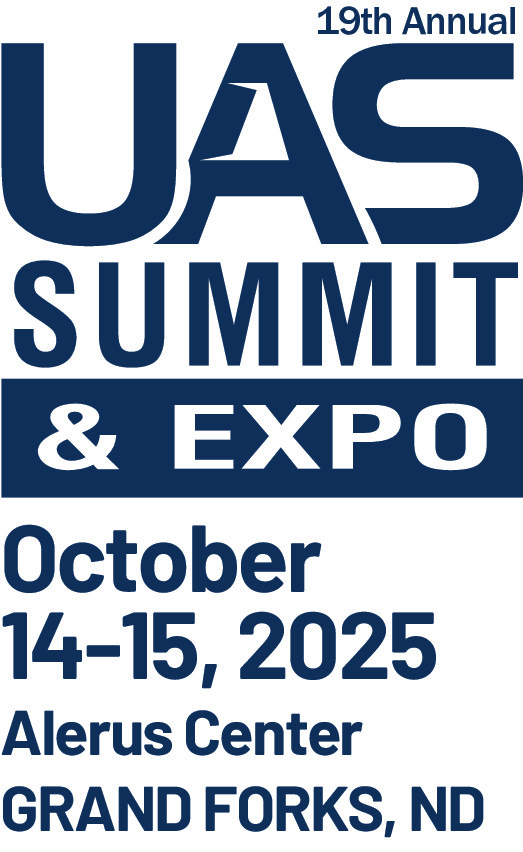
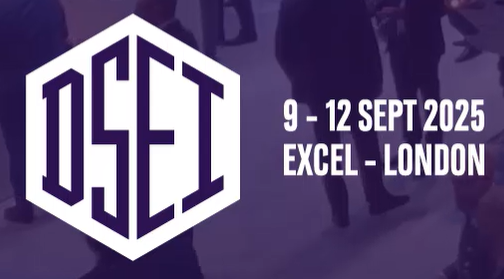
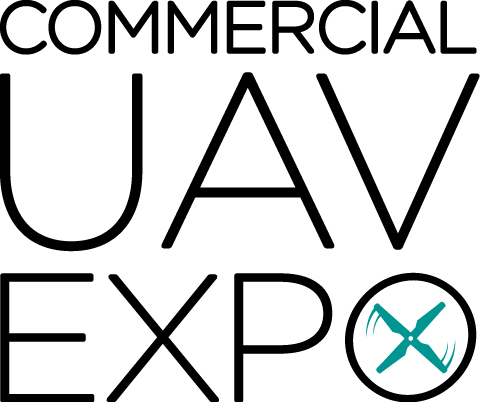
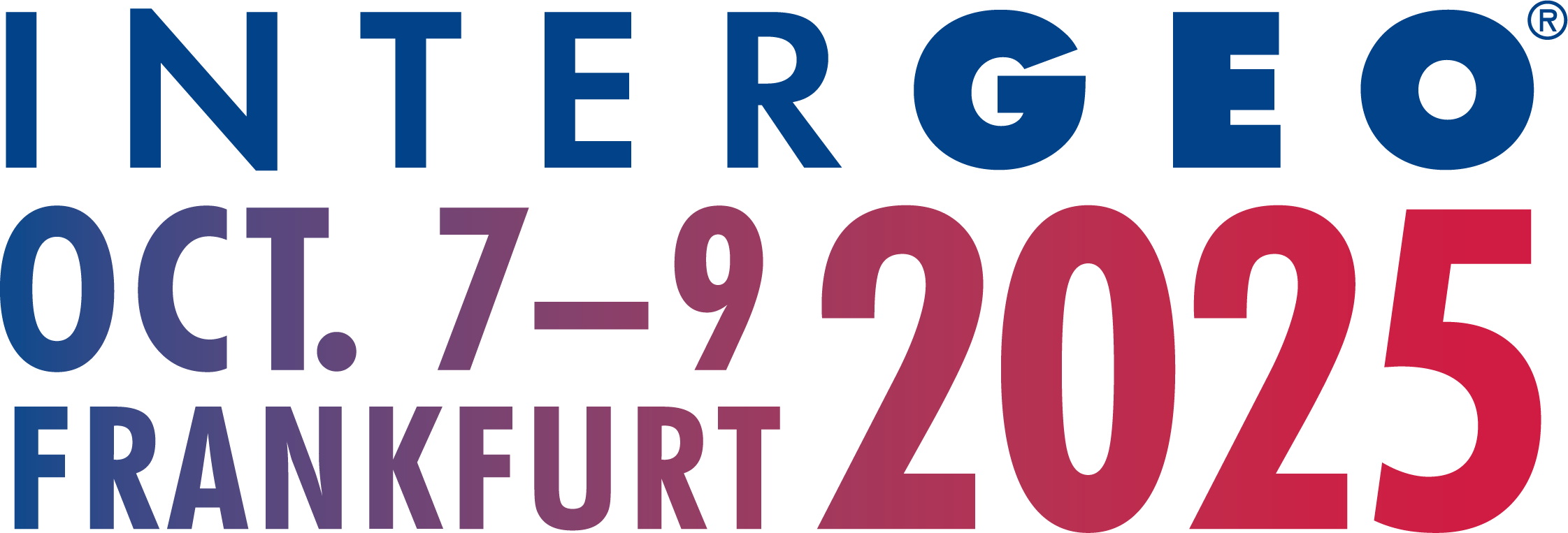
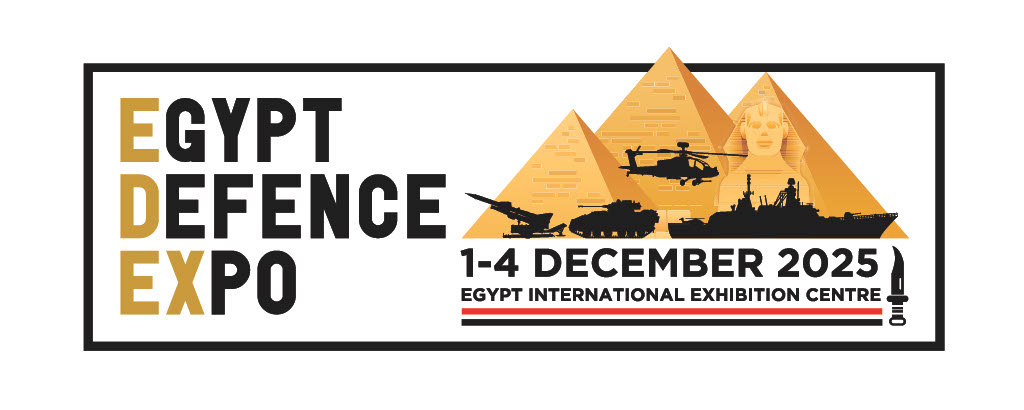
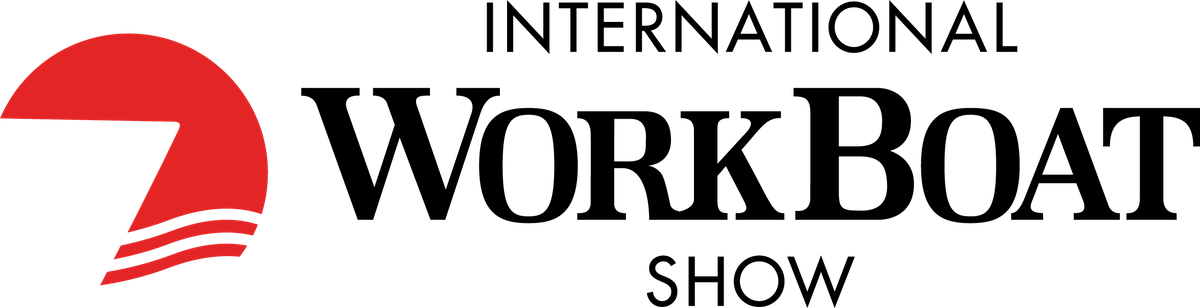
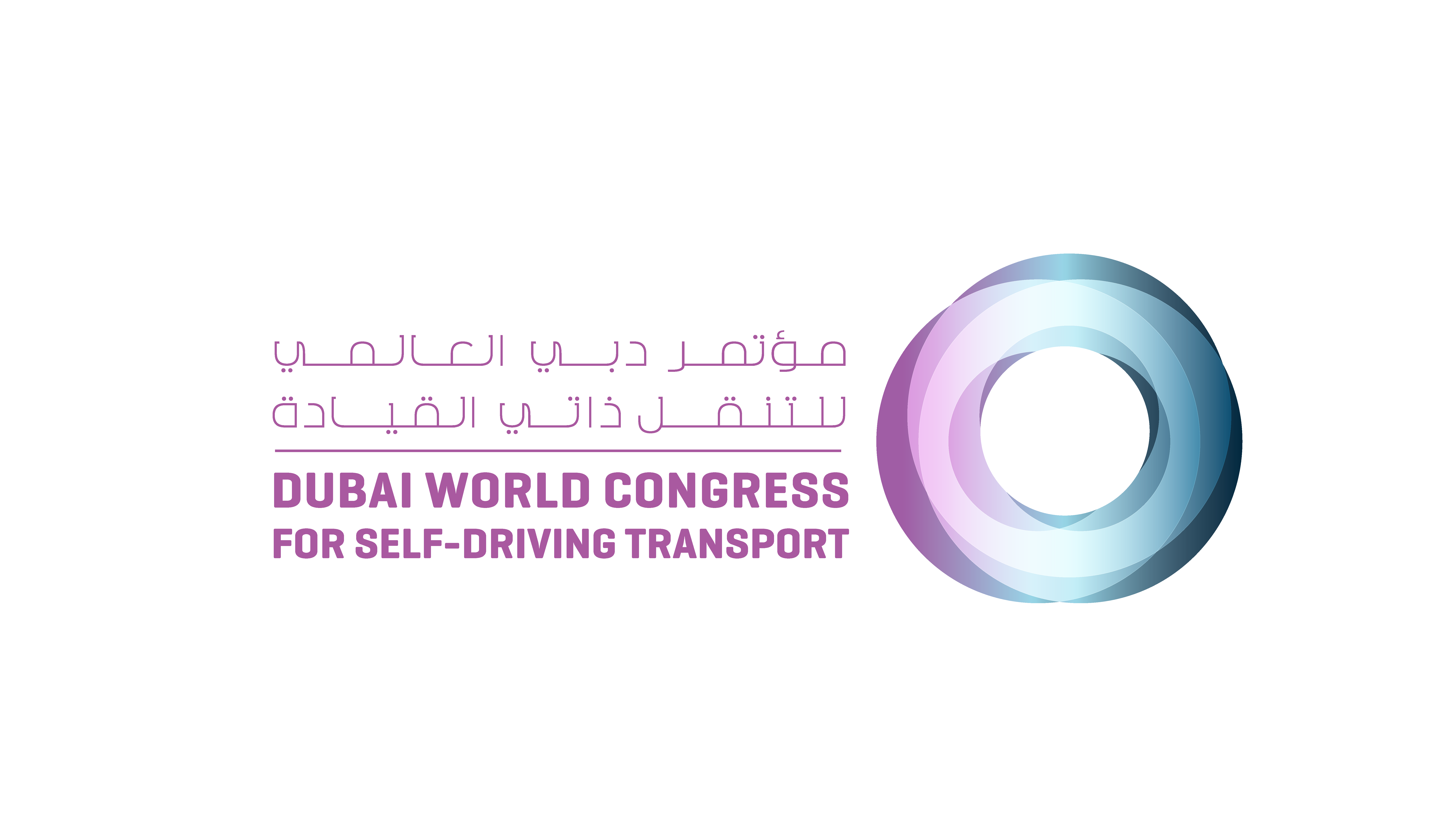
