Connectors
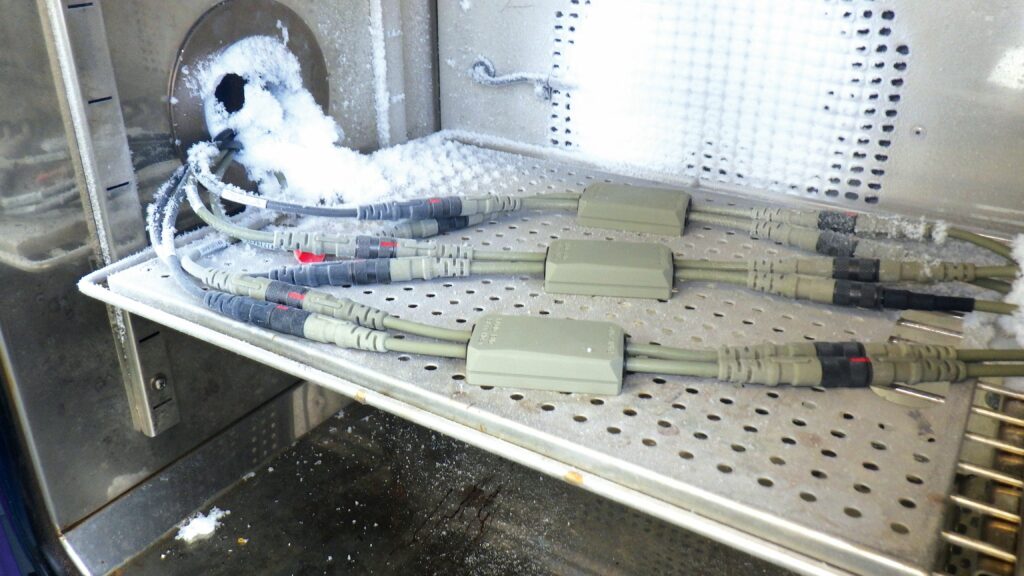
(Image courtesy of Fischer Connectors)
Smarter connections
Connector manufacturers are rethinking their approach amid rising demand, and evolving data management, AI and IoT systems, reports Rory Jackson
All around the world, connector manufacturers are building factories and hiring people to cope with booming demand for their products as uncrewed vehicles and other high-end vehicular and electronic systems are output in greater quantities.
Connector companies are also rethinking their approach to customers and new projects. The wide diversity of vehicle types, missions, environments (both inside and outside of vehicle bodies) now makes it beneficial for the connector supplier to become a partner or consultant to new integrators.
This is particularly important as today’s combinations of ‘big data’ management, Internet of Things (IoT) systems and electrification push expectations for information and power throughputs between connectors and cables. And customers often have their own, potentially misguided ideas on what they want, meriting diligent attention.
At the same time, data protocols and standards continue to evolve, pressing connector suppliers to update and refine their solutions from the ground up to ensure information can be transmitted properly. This has placed expertise in signal integrity, high-speed data transmission, EMC and other key concepts in hot demand among connector producers, particularly in comparison to five or six years ago amid the low speeds, signal bandwidths, and EMI for connectors working to USB 2.0 and RS-232 standards.
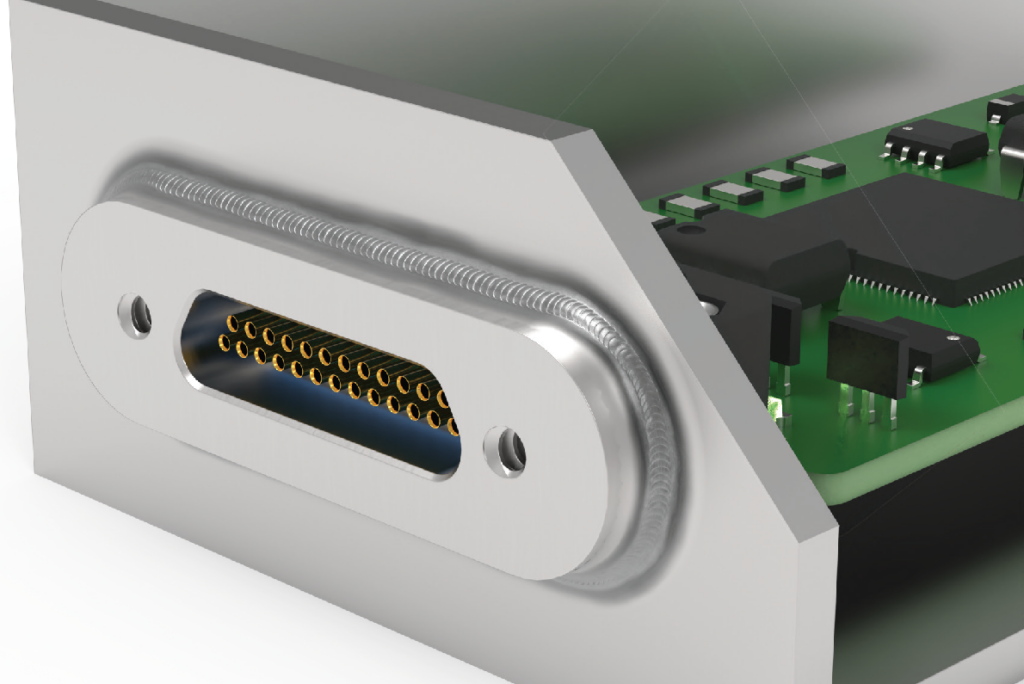
(Image courtesy of Omnetics)
In the interest of good service, connector companies are accruing an understanding of the ecosystems of different devices in need of connectivity in the markets they serve, through which they are able to adapt existing solutions or innovate new ones – going beyond connectors themselves to a range of related systems, as we will explore below.
Rugged and secure
As autonomous systems proceed to drive, fly and sail at faster speeds and in harsher conditions, so connector r&d teams are searching for new means of ruggedising the delicate signal and power links holding vehicle subsystems together, while saving on weight and cost where possible.
For particularly shock- and vibration-prone environments, chrome-plated brass remains a leading choice for ruggedised shell materials, while aluminium shells are also used as a more weight-optimised alternative (often nickel-plated for added robustness), particularly in aerospace, and some exploration of composite material shells is under way.
Additionally, certain plastics, such as PEEK and LCP, serve as highly temperature-resistant contact block materials, with various other plastics playing a key role in balancing ruggedness against cost (which can increase greatly when using metals).
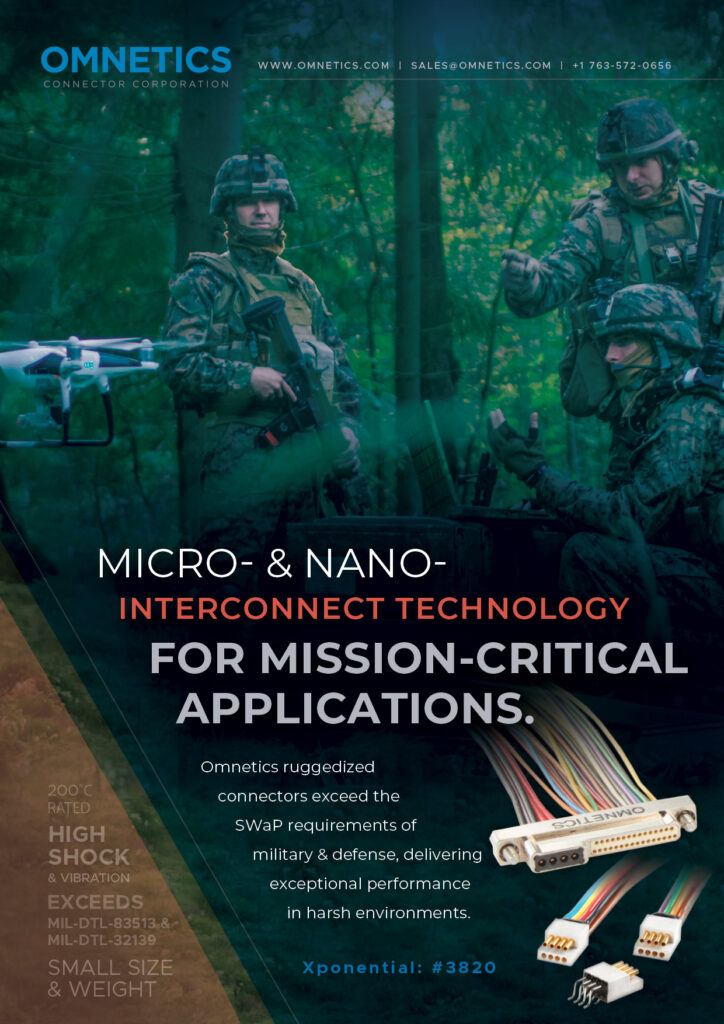
In the pursuit of effective plating methods, some manufacturers are stepping away from using hexavalent chrome plating for connector shell production and switching to trivalent chrome plating, which is more robust and consistent, as well as less energy intensive and environmentally polluting, while still being compliant with EU regulations on chrome bath processes.
An arguably greater quantity of r&d has gone into new locking mechanisms, with new launches over the past year including a new bayonet-style system using a ratchet to secure a locking pin from the male end into the female end. This type of approach serves as a compromise between legacy screw-type latches (which are satisfyingly tactile, but laborious to mate and unmate) and push-pull connectors that are insufficiently secure for certain harsh environments.
One such approach integrates a bright orange O-ring, which is visible to the handler until the connector is fully turned and locked, providing visual assurance that the system is secured. A key application has been in locking a COTS, high-speed, high-frequency, ruggedised USB-C connector, ensuring its data transmissions persist amid high vehicle velocities and vibrations.
That said, push-pull latching connectors remain widely popular simply due to the ease of engagement and disengagement, and in specific applications where vehicle downtime must be minimised, such as in search and rescue, or wildfire monitoring (and mitigation, now that UAVs capable of aerial firefighting are being supplied internationally). Time cannot be wasted in unscrewing or unsticking a cumbersome locking mechanism.
Hybrid connectors
Despite the significant costs involved in engineering hybrid connectors – those that can integrate power, signal and even coaxial pins together within shared connector housings – hybrid solutions have soared in demand over the past few years as customers request increased power throughput, data bandwidths and signal transmission speeds relative to the number of connections in their vehicles and subsystems.
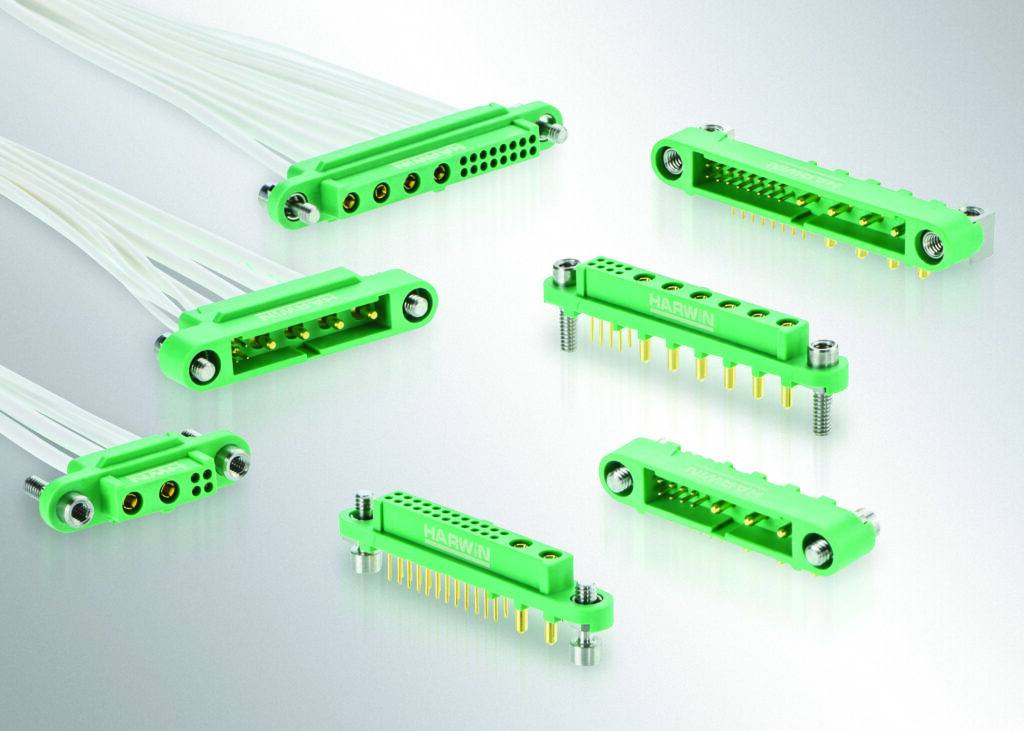
(Image courtesy of Harwin)
As part of this trend, larger and denser hybrid connector products are being released, some with up to 30 pins within a 15 mm plug, and some capable of integrating power pins alongside pins for fibre-optic connections (as well as those for data running on conventional copper wire). Some advanced hybrid connector designs are also making apt use of plastics instead of metals (or limiting the use of metals to select backshells) to bring down their typical cost disadvantage.
Integrating fibre optics into connectors and cable assemblies takes particular expertise, and can frustrate conventional manufacturers as optical fibre cannot be soldered. However, in certain contexts, particularly large vehicles such as next-generation naval USVs, fibre cables and connectors are a must-have due to the tendency of signals to degrade after travelling 20 m along copper wire. And, as 8K cameras start being integrated into UAV payloads, one should expect an exponential rise in demand for hybrid power-and-fibre connectors.
As they are challenging to ruggedise, suppliers of Mil-spec hybrid fibre connectors are limited to those with extensive know-how, and future innovations may extend to the use of specialised lenses rather than mere polished glass at the fibre faces for more scratch-resistant connections.
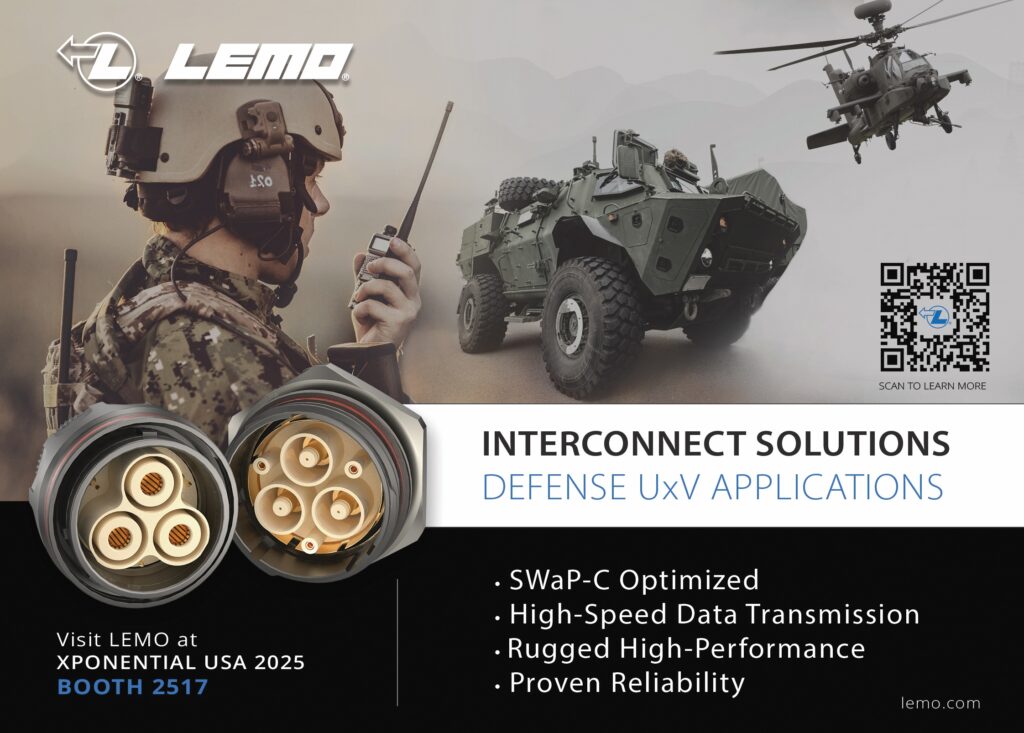
Meanwhile, slightly more conventional hybrid power and data connectors are being rapidly adapted and released for highly demanded newer data protocols, such as USB 3.2 and HDMI – a particular challenge given that HDMI is notorious for interfering with other proximate data transmissions, but one being tackled through judicious engineering.
Smart connectivity
The general idea behind smart connectors involves integrating microchips inside of contact blocks to give cable assemblies higher functionality – including compression, encryption or checking of transmitted data – thereby transforming them from ‘dumb’ electrical components into intelligent electronic systems.

vital for meeting today’s connector requirements
(Image courtesy of Nicomatic)
Smart connectors were posited as a theoretical future offering by several companies at least a few years ago, and while they are not yet widely available on the market (due to being highly application-specific in how they must be designed), a few pioneering projects in smart connectivity and cabling have been concluded for medical and defence-based land vehicle integrators.
Such projects have included the use of EEPROM (electrically erasable programmable read-only memory) microchips, integrated within connector housings, for simple tasks (in programming terms) such as counting how many times the connector is used, mated or unmated, and alerting whether the connector has been plugged into the correct or incorrect port.
In a similar vein, however, cable assembly markets are seeing a proliferation of other solutions using embedded electronics, not necessarily in the connectors themselves but in glands or tubes along the length of the cable. Chips integrated this way can serve as signal converters (for example, turning USB data into Ethernet or RS-232) or boosters; the latter being useful when stretches of cable exceed the ideal lengths for data integrity.
Developing smart connectors and cables takes multiple engineering disciplines; to prototype and supply them is far easier when connector manufacturers possess expertise on microelectronics, programming and plastic overmoulding in-house.
Also key is the interplay between suppliers and customers as a close understanding of end-users’ PCBs and data networks can closely inform how a smart connection must be architectured (particularly as many vehicle OEMs leave the connectors and cables as the last items to be considered, so the potential for mismatches and incompatibilities is high).
As some connector suppliers look beyond mere connectors and towards utilising their understanding of connectivity, certain security and defence markets are now being supplied with smart hubs or switches, which serve as wearable devices that can connect people’s power banks, handheld GCSs, radios, smartphones and even heart-rate trackers or emergency alert buttons for dangerous missions.
Such solutions require copious use of ruggedised and hybrid connectors to minimise the number of cables and the risk of accidental unmatings, as well as r&d in network and software engineering, such that advanced AI processes can start accounting for potential harm to connected systems or personnel.
Cable integration
As part of the push to provide better, holistic solutions to customers, some connector suppliers are making the jump to providing complete cable assemblies. This means saving the end integrator having to find the right cable, ensure any necessary twisting, shielding or other layout specifics to suit the connector and application, perform any testing or qualification of the assembly design, or successfully strip, crimp and solder cables to connectors in a consistent, quality-controlled manner.
Going from supplying boxes of connectors to batches of complete cable assemblies is more challenging than it sounds. While connectors are largely supplied as COTS, non-customised components, going into cable assemblies opens up a world of customisation, requiring specifics on length, how pairs are twisted, jacket materials, the need for splicing or breakouts, and other parameters.
In some cases, a customer will need one company’s connector on one end of the cable and an entirely different company’s connector on the other in order to connect two different subsystems, requiring considerable engineering expertise.
To pick the right cable (and supplier), a connector manufacturer must know the end-user’s desired data protocol, power throughput, voltage and environmental requirements; the latter including requirements on flexibility, and resistance to flame, chemicals, shear stress, temperature and other hazards.
Gathering and understanding all the necessary information can be challenging if contact between the connector supplier and vehicle OEM is limited to sales and procurement conversations. As with many subsystems, the best way to define comprehensive technical requirements and challenges is through engineer-to-engineer discussions, by which a connector designer and a UAV chief engineer, for instance, can methodically explore solutions from either perspective.
Fluid connectors
Just as different industry movements are driving innovations in power and signal connectivity, the proliferation of advanced UAV powertrains, including internal combustion, hybrid and electric engines, is spurring new approaches in fluid connectors or couplings for delivering fuel, oil and coolant.
Here, one can find a wide range of locking approaches. These include push-pull connectors, which, much like their electrical equivalents, push concentrically together to mate until a latching mechanism using balls, arc latches or snap wires engages. They can then be disconnected by pulling a sleeve on the coupler, releasing the latch quickly.
Alternately, threaded fluid connectors use independently-swivelling threaded components, preventing torsional loads on connecting hoses during attachment or detachment. The large bearing surfaces in these devices ensure reliable connections, even amid intense vibrations or high g-forces.
Bayonet-type locks are also used in fluid connectors, including some with hook-like receptacles, which require additional, deliberate movements for unmating, meaning greater security than typical bayonet latches.
In recent years, customer requests to resolve certain key issues have spurred innovative solutions in response. For instance, pressure drop – where liquid passing between an inlet and outlet suffers loss of pressure, possibly due to friction or other forces along the length of the channel – can render liquid cooling systems considerably less effective, and sap the efficiency of oil or fuel pumps.
Minimising pressure drop across connectors has therefore been a critical focus, motivating extensive CFD simulations in ANSYS to optimise internal flow paths, reducing turbulence, resistance and energy costs, and improving overall system efficiencies in high-performance fluid connectors.
The accuracy of CAD and CFD simulations in fluid connectors depends (like simulations across other devices) on copious data to enable designs to behave in digital environments just as they do in the real world. As such data is limited in open-source forums, fluid connector suppliers who engage in the most projects and prototyping each year will have the advantage in mitigating fluid-specific problems akin to pressure drop.
One design integrates a relief mechanism, by which over-pressurisation events driven by thermal expansion will trigger a controlled release of limited fluid, safely reducing pressure and preventing the coupling from being blown.
An even newer fuel-connection device that is useful in UAVs incorporates a pressure equalisation system, integrating two back-to-back check valves, each with distinct cracking pressures and flow paths. These effectively balance internal and external pressures: during climbing, when external pressure drops, a valve safely releases air or fuel to prevent an explosion.
In dives, a valve allows air to enter the tank, protecting it from collapsing. The system also prevents pressure build-ups stemming from thermal expansion, helping to reduce the risk of over-pressurisation events.
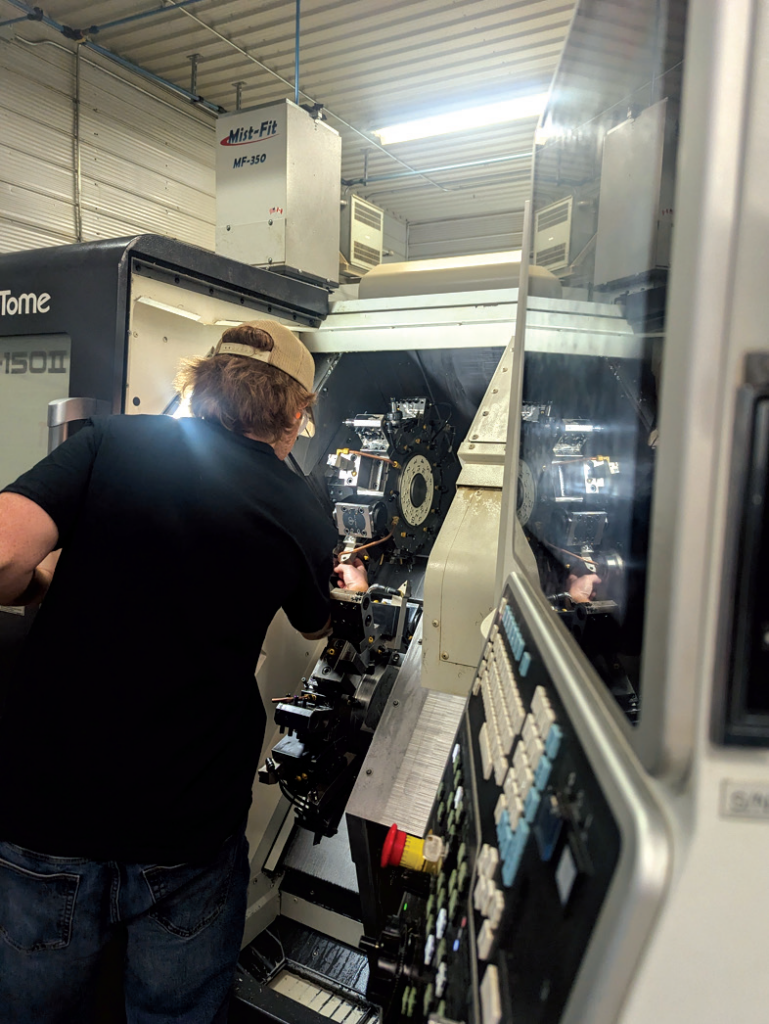
CNC machining to optimise for internal flow
(Image courtesy of Battlefield International)
Meanwhile, material innovations in this space include the use of various lightweight, high-strength alloys, as well as some aimed at functioning in cryogenic temperatures as low as -200 C to high temperatures exceeding 170 C – ideal for space exploration, advanced UAV cooling systems and next-generation propulsion technologies.
At least one US supplier is also sourcing domestically-traceable materials to comply with Defense Federal Acquisition Regulation (DFAR) requirements, and thus suit military and defence users.
Engineering
Prudent design of any new connector product often depends on close collaboration between multiple disciplines across manufacturing companies. With functionality paramount, the first step in defining a new system is to identify requirements, with product managers often gleaning these from the market and informing the designers accordingly.
Those designers must then work closely with mechanical engineers, as well as experts on electrical engineering and signal integrity, to begin concept work and simulations on a basis that ensures both power and data wind up flowing seamlessly through the resulting connector without interference, insertion losses or other issues.
Production experts ought to be included in the collaborative development process. Designing a connector that will perform is one thing, but the design must account for how the wires will be stripped, soldered or crimped to integrate the connector to the cable.
Subsequently, the design should account for how additional components such as shielding or bonding resins will be included in the integration process without causing problems like resin seeping under the shielding and amidst the wires.
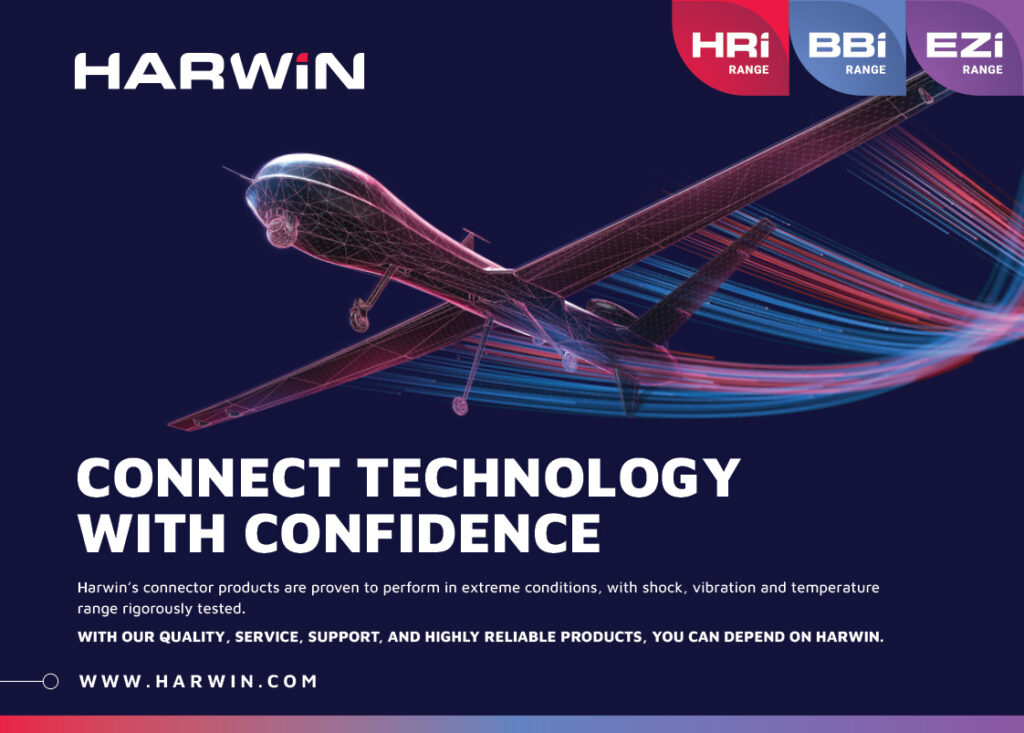
Throughout the design simulations and real-world tests that follow, it is increasingly common practice for connector manufacturers to analyse signal integrity to ease the end-user’s workload in creating a functional vehicle data network. As well as simulating for signal integrity, equipment such as vector-network analysers can be critical for affirming the amplitude and phase properties of signal transmissions through a new connector’s prototypes.
Signal integrity tests and in-depth analysis will become increasingly crucial aspects of cable assembly engineering as new high-speed data protocols, compression standards and levels of EMI inside uncrewed vehicles push connector designers towards new innovations and design techniques.
Qualifying new prototype connectors and cable assemblies (before handing their designs and all key information over to a production site) also depends on a much wider range of well-established tests. Among these can be a variety of methods for gauging physical durability, such as cable-bending tests, tensile strength tests, retention force tests, sealing tests in environmental and pressure chambers, and shock, impact and vibration testing.
Additionally, electrical analyses such as voltage and current capacity tests are vital steps towards the safety rating of connector and cable products; these can simultaneously test their thermal stability by deliberately driving up the current to induce heat in the copper towards a possible melting or breaking point in the surrounding material.
Lastly, as maintenance, repair and associated inventory requirements become more important prospects for uncrewed systems manufacturers aiming to offer a cost-effective product, automated test machinery for repeatedly mating and unmating connectors until a fault occurs are becoming indispensable for calculating and pushing the lifespan of new connectors.
Manufacturing
As mentioned, connector companies across the board are raising their manufacturing capacities, largely through expanding existing facilities or opening new factories in nearby locations, rather than trusting contract manufacturers or investments in faraway places that could become inaccessible in the event of a new pandemic or conflict.
Given the growing nature of the global autonomous and uncrewed vehicle industry, and how connector orders could rise exponentially with the number of professional uncrewed systems being signed for and delivered, a few suppliers are taking a distinctly modular approach to new facility layouts and development. Generally, this means model production layouts, which can be planned, built and then copied across structures or zones without needing to restructure the existing assets.
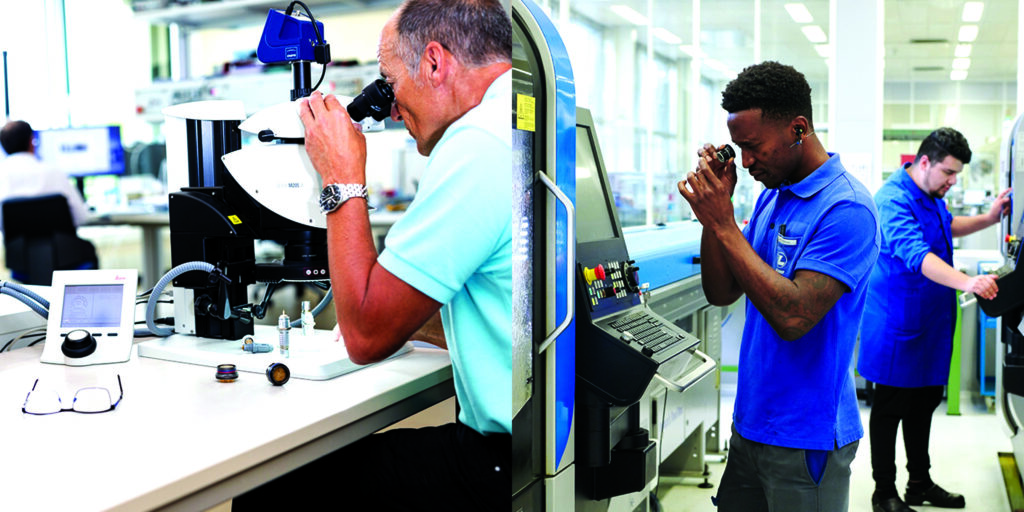
(Image courtesy of LEMO)
Such layouts typically begin with a tightly controlled inflow of parts orders. Quality control (QC) is critical, given the wide range of suppliers that pins, contact blocks, backshells, fasteners, O-rings, wires, cable jackets and other components may come from. It is also vital, because not all products are made to order; many connectors and cable assemblies are manufactured in excess of the ordered batches to facilitate future spot purchases, as the faster connector supplier will win the order (and a quality product is more likely to spark a follow-up purchase).
As more connector companies provide complete cable assemblies, factories are being built that are larger and more spacious to provide room for tasks such as stripping wires, gently twisting pairs, fitting heat shrinks and performing soldering or crimping as needed.
These processes are largely carried out by hand, although a small but growing proportion of crimping is automated via machine. However, it is typical, even in large-volume connector factories, for upwards of 95% of crimping to be done with standards-based hand tools, especially for military customers who may seek certifications such as the IPC Class 3 rating for highly reliable electronics, and for other customers who appreciate that good crimps take intuitive manual twisting of wires in specific ways, as well as visual checks of every contact.
Additionally, plastic overmoulding, which involves a controlled injection of rubber or plastic to seal, house and bond the connector with the cable, has long been performed by machines in a consistent way.
While most wire-related tasks are performed manually, connector-specific manufacturing can be automated, except when order volumes are too small to justify reprogramming the machinery. Otherwise, machines are used extensively for integrating pins into contact blocks, turning or bending metals into housings and backshells, and other processes.
Some companies anticipate using additive manufacturing (AM) in future batch-production approaches, particularly as AM machines become larger, to enable the printing of hundreds or potentially thousands of contact block or shell parts per print cycle.
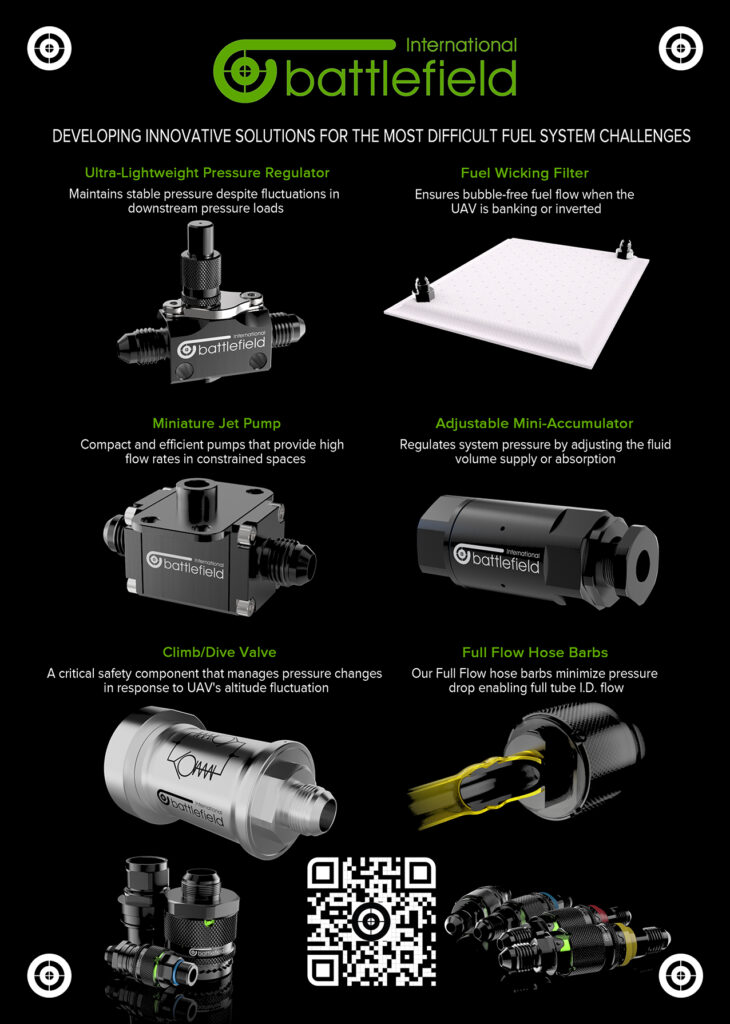
These, and other connector-manufacturing steps and machinery, must be arranged in a highly guided way, including controlled movement of parts between machines by automated guided vehicles or autonomous mobile robots to ensure dozens of different connector products can be made simultaneously and at scale every day (this also enables traceability and QC over where parts have been or are going).
Given the importance of QC to ensure identical batches of connectors, production lines typically close with end-of-line qualification-testing processes. These can include visual inspections of each unit by human officers, manual checks such as plugging in every connector’s male and female counterparts to affirm mateability (and that locking systems are functioning), and more detailed inspections such as electrical tests for ensuring pin-to-pin connections work correctly.
The latter types of tests can also measure electrical properties such as impedance or resistivity, particularly if the complexity of a product or its intended use-case merit doing so, or if the customer requests it, although these might be carried out on just one unit in 10, or one in 100, rather than every unit.
Transmitting forwards
It is well known that effectively zero connector companies supply solely to the uncrewed vehicle space; given the ubiquitous need for connectivity, manufacturers typically serve a wide range of applications, including medical, military, motorsport, marine and consumer electronics.
As a result, connector suppliers are particularly well-insulated against shocks affecting any one industry, and can draw from many types of partners and their perspectives, particularly for developing innovations that may carry over from one space to another.
Future connector architectures and standards for the uncrewed space are likely to be influenced by emerging successes among medical and marine robotics, as well as by how systems are miniaturised for the consumer market, ruggedised for the harshness of motorsport, and made workable even in dangerous and stressful environments for soldiers’ wearables, as they have been for years.
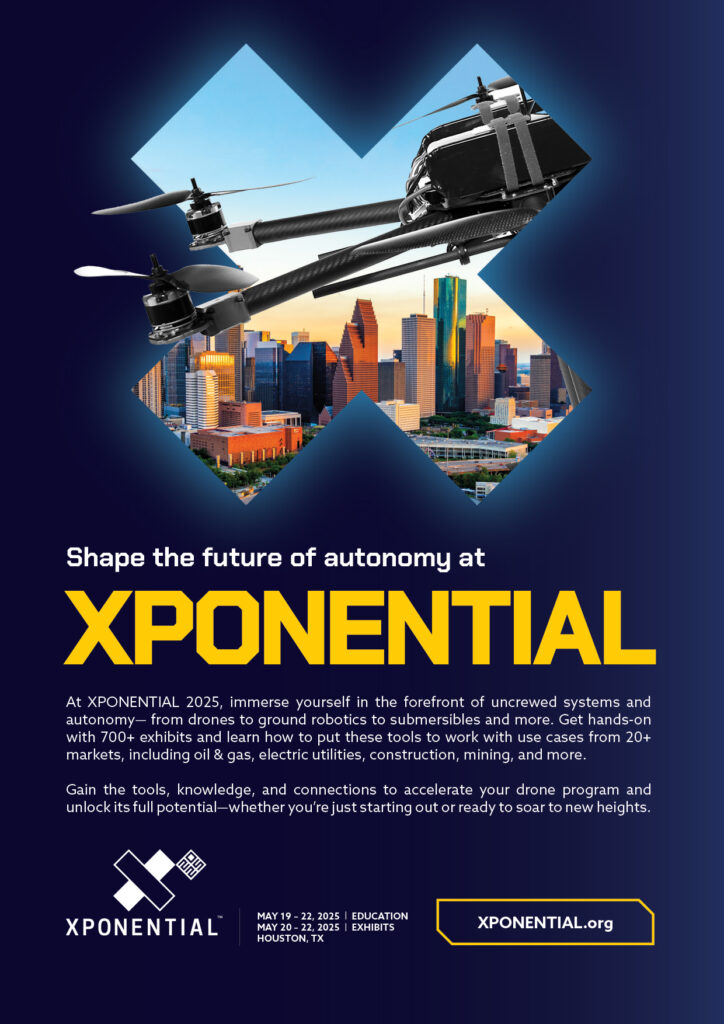
Going forwards, advancements in the IoT space, empowering connectivity to support emerging uses of 5G, AI and new cloud-computing applications can be expected to spur fresh waves of smart connectors, signal protocols, and intuitive design and testing tools. All of these innovations will serve to make connector customers and suppliers, as well as every stage of the production process, feel more closely connected.
Acknowledgements
The author would like to thank Andrea Coller of Fischer Connectors, Richard Johannes and Steven Lassen of LEMO, Ryan Smart of Harwin, Travis Neumann of Omnetics and Fadi Mishriky of Battlefield International for their help in researching this article.
Some examples of connector manufacturers
BELGIUM
SICK | +32 2 466 55 66 | www.sick.com |
DENMARK
MacArtney Underwater Technology | +45 7613 2000 | www.macartney.com |
FRANCE
Esterline Souriau | +33 1 30 84 77 99 | www.souriau.com |
Staubli | +33 4 50 65 67 97 | www.staubli.com |
GERMANY
GISMA Steckverbinder | +49 4321 983530 | www.gisma-connectors.de |
Wennmacher Electronic | +49 6022 62240 | www.wennmacher-electronic.de |
ITALY
AvioRace/Tecnoelettra Group | +39 059 77 0 0253 | www.aviorace.it |
SWITZERLAND
Fischer Connectors | +41 21 800 9595 | www.fischerconnectors.com |
Huber & Suhner | +41 71 353 4111 | www.huber-suhner.com |
LEMO | +41 21 695 16 00 | www.lemo.ch |
UK
AEF Solutions | +44 122 7711455 | www.aeiuk.com/aef-solutions |
CEEP Connectors | +44 1730 895785 | www.ceep.co.uk |
Cinch Connectors | +44 1245 342060 | www.belfuse.com/cinch |
FHS | +44 1753 513 080 | www.fhsracing.co.uk |
Harwin | +44 23 9231 4545 | www.harwin.com |
St Cross Electronics Ltd | +44 (0) 2380 227636 | www.st-cross-electronics.co.uk |
USA
Airborn | +1 512 863 5585 | www.airborn.com |
Air Electro | +1 818 407 5400 | www.airelectro.com |
Amphenol | +1 203 265 8900 | www.amphenol-aerospace.com |
Battlefield International | +1 905 772 3000 | www.battlefield.biz |
Binder USA | +1 805 437 9925 | www.binder-usa.com |
Cinch Connectors | +1 630 705 6000 | www.cinch.com |
E-Valucon | +1 949 450 0080 | www.evalucon.com |
FDH Electronics | +1 213 620 9950 | www.fdhaero.com |
Glenair | +1 818 247 6000 | www.glenair.com |
Harwin | +1 603 893 5376 | www.harwin.com |
HiRel Connectors | +1 909 626 1820 | www.hirelco.net |
ITT Cannon | +1 800 854 3028 | www.ittcannon.com |
LEMO | +1 707 578 8811 | www.lemo.com |
Meritec | +1 440 354 2100 | www.meritec.com |
Molex | +1 630 969 4550 | www.molex.com |
Nicomatic | +1 215 444 9580 | www.nicomatic.com |
ODU-USA | +1 805 484 0540 | www.odu-usa.com |
Omnetics | +1 763 572 0656 | www.omnetics.com |
PEI Genesis | +1 215 673 0400 | www.peigenesis.com |
PIC Wire & Cable | +1 262 246 0500 | www.picwire.com |
Positronic | +1 417 866 2322 | www.connectpositronic.com |
Smiths Connectors | + 913 342 5544 | www.smithsinterconnect.com |
TE Connectivity | +1 717 592 2339 | www.te.com |
Times Microwave Systems | +1 800 867 2629 | www.timesmicrowave.com |
UPCOMING EVENTS
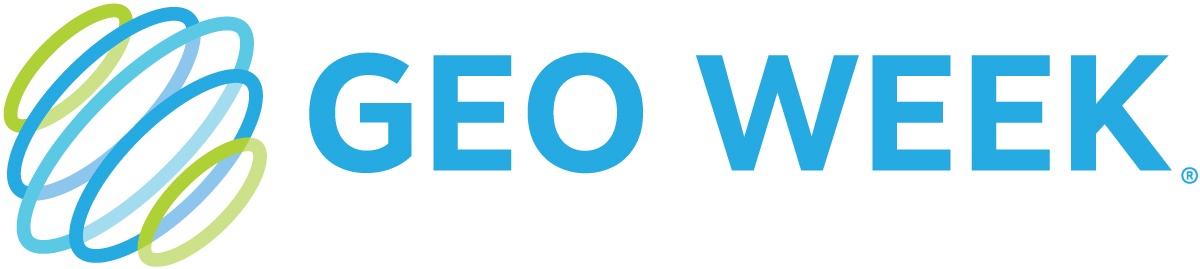
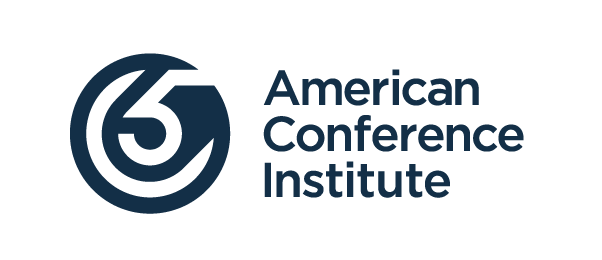
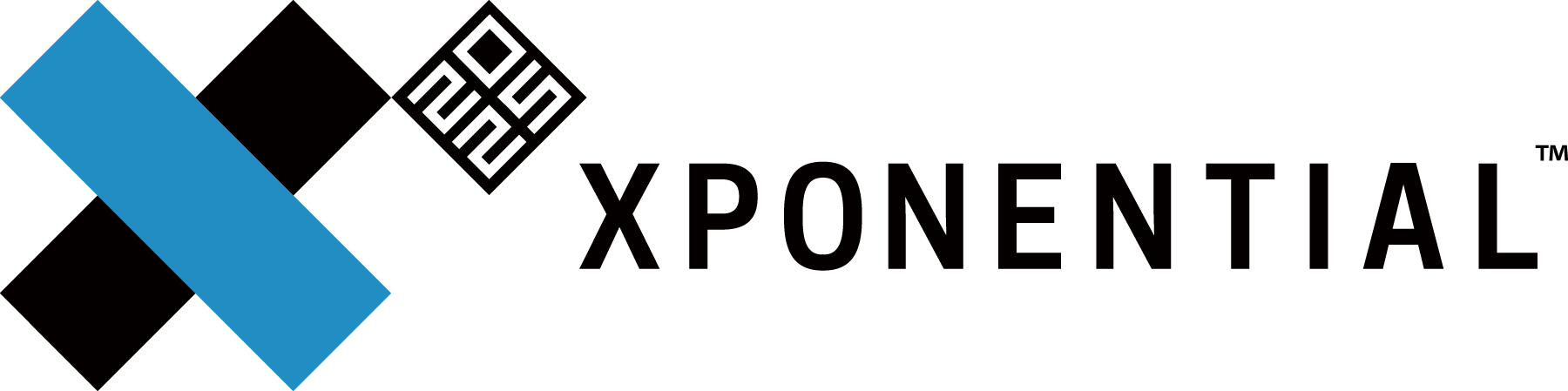
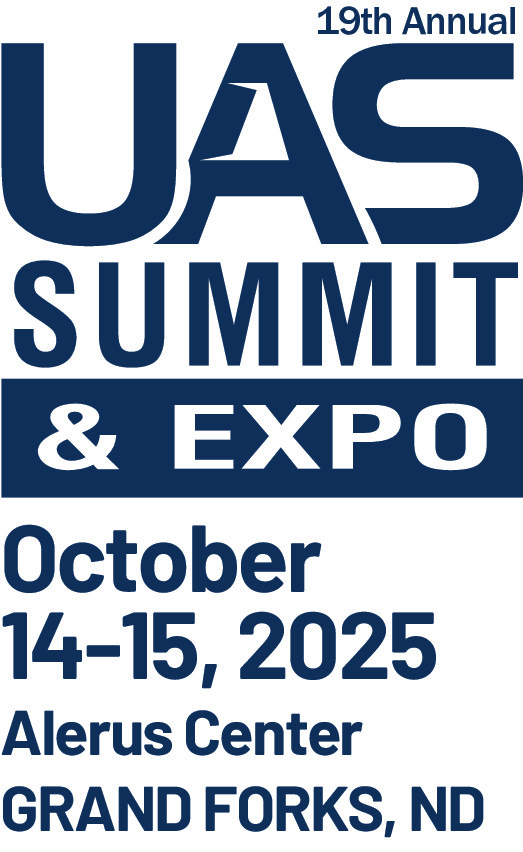
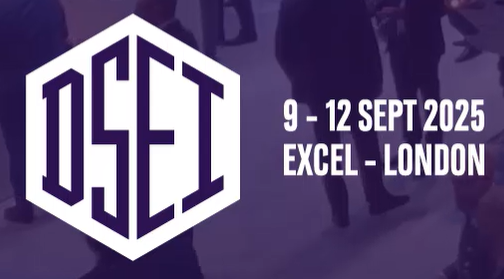
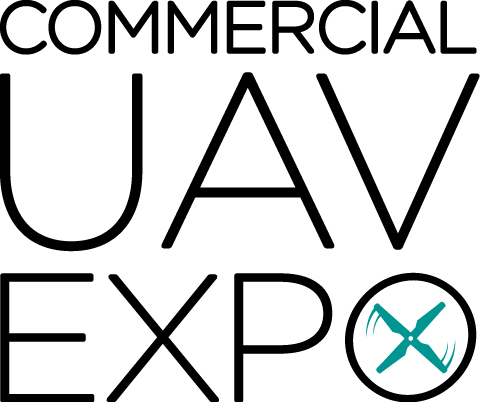
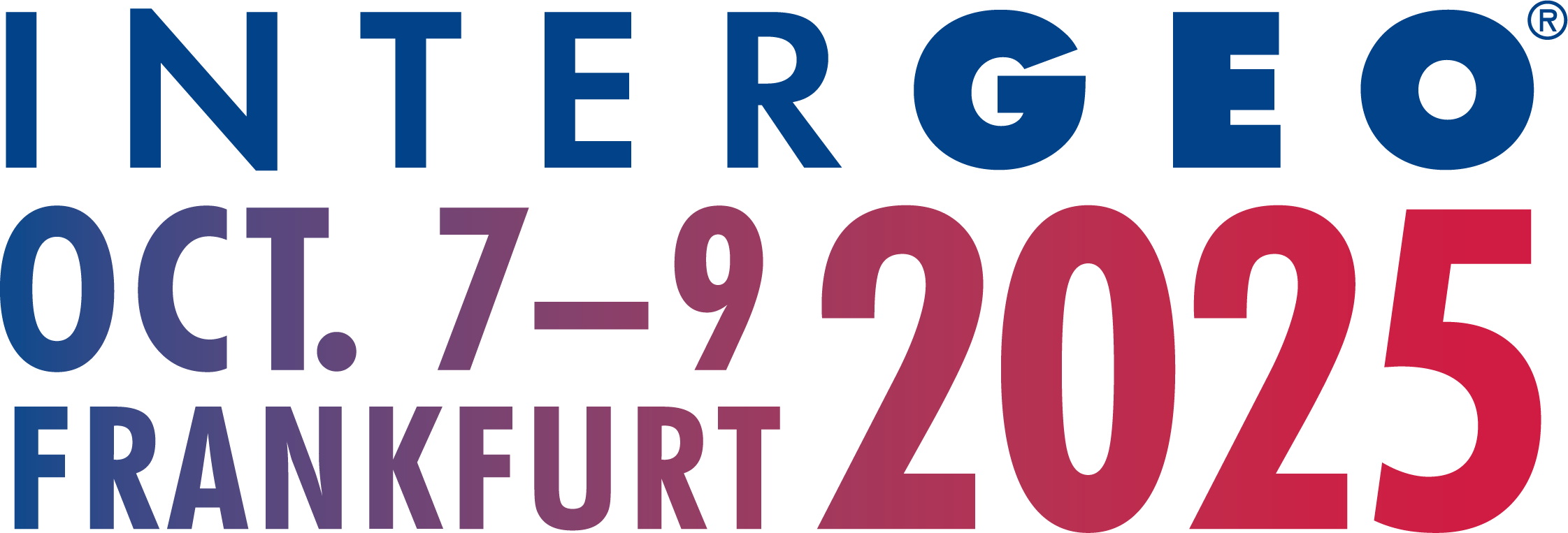
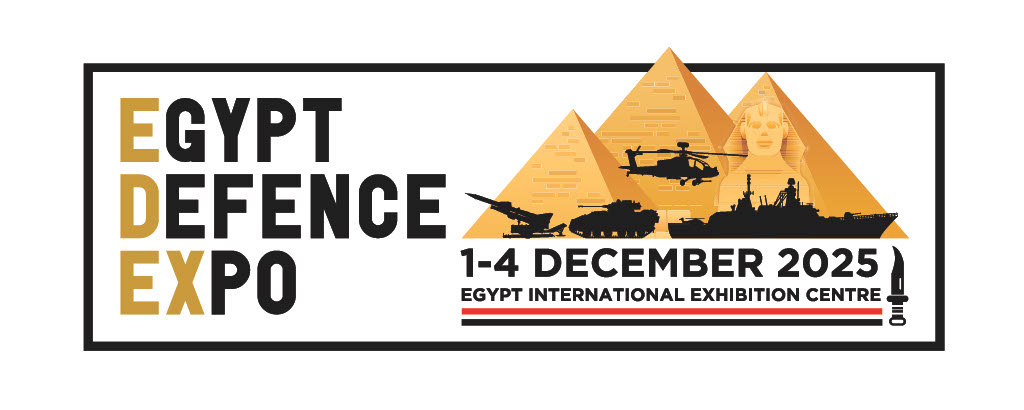
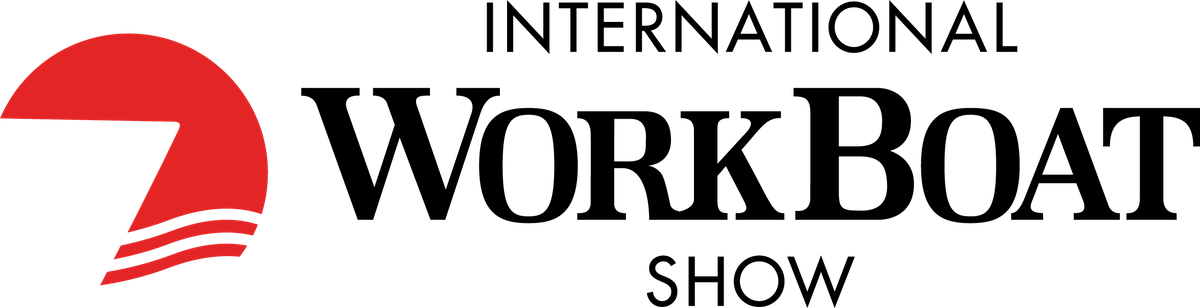
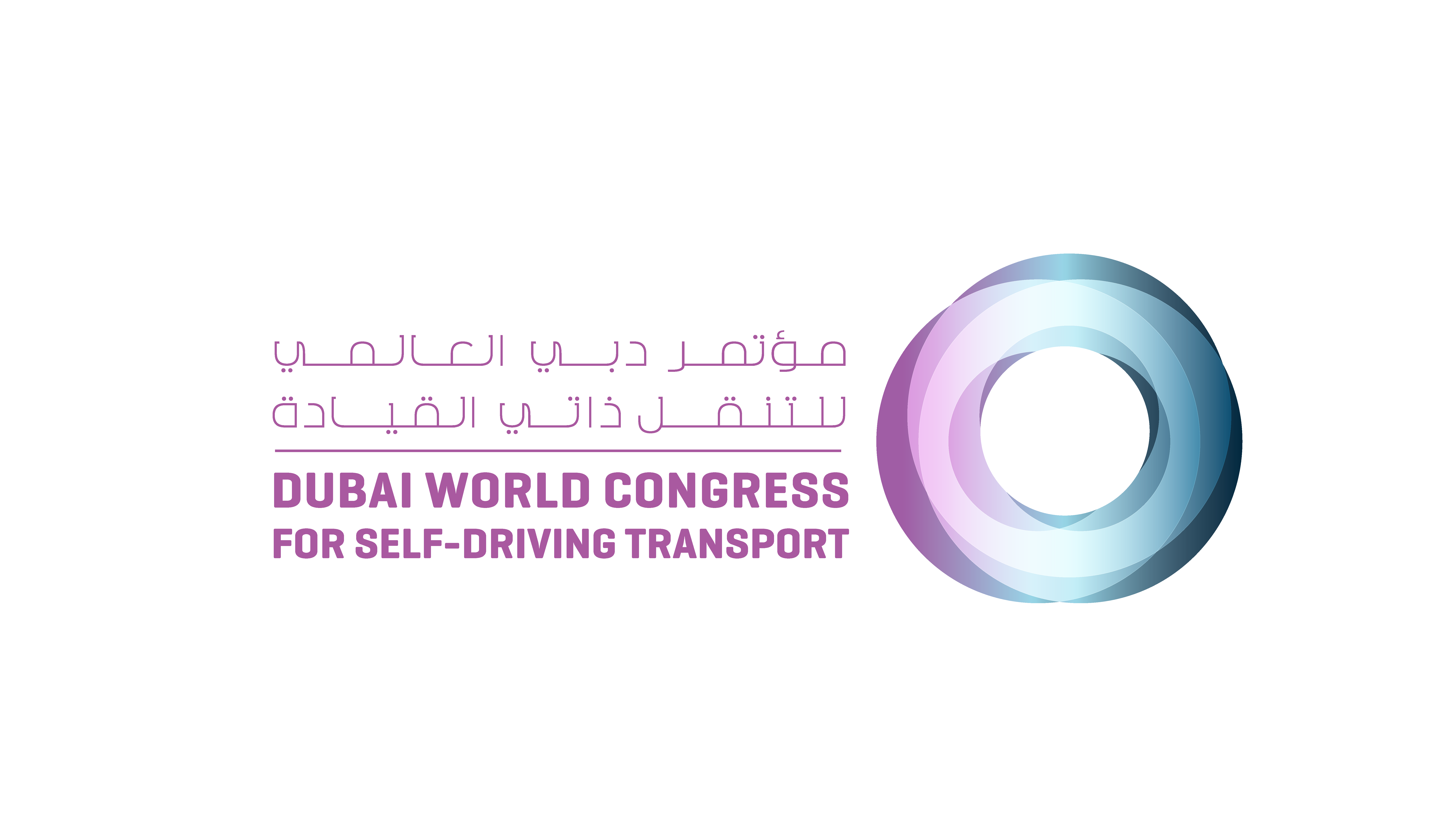
