Connectors
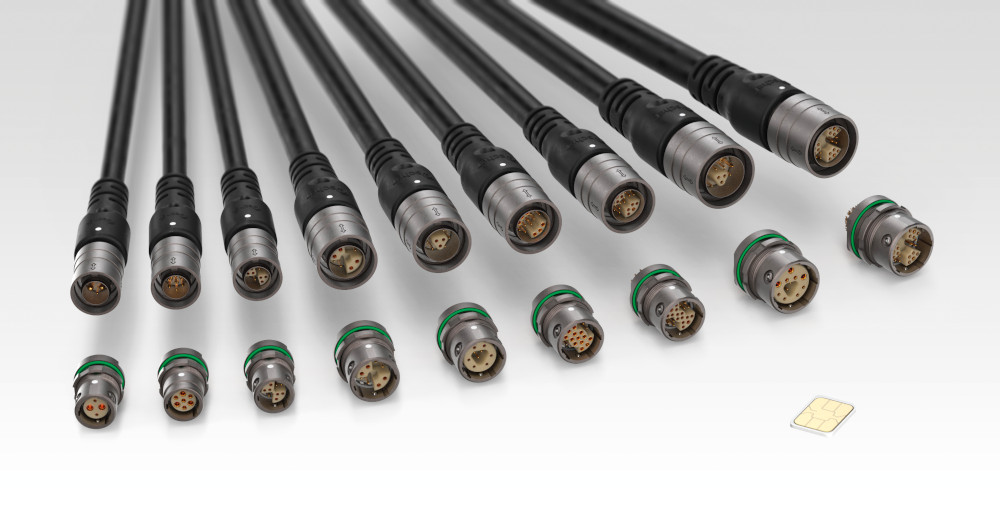
(Courtesy of Fischer)
Secure in the knowledge
Uncrewed vehicles have particular needs regarding their internal connections, which suppliers are now meeting. Rory Jackson reports…
The number of connections needed in an uncrewed vehicle for power and comms means that connector designs often reflect the nature of the vehicle itself. Lighter connectors help to make it less heavy, for example, while more rugged ones help it to better withstand turbulence and accidental impacts, and less costly ones contribute to bringing down its price point.
It should come as no surprise then that as the autonomous world becomes more sophisticated and right-sized for users in various markets, connector designs are showing improvements in a range of capabilities.
For instance, some now have usage lifetimes of up to 10,000 mating cycles, enabling reductions in costs associated with part turnover and storage, and others are being designed with ever smaller sizes to suit more compact vehicles. Others still can handle far higher power than is typical for the industry, to better serve the hybrid electric and long-endurance vehicles designed for long-range logistics and survey missions.
This evolution is due in no small part to a growing number of connector manufacturers involving their engineers with uncrewed systems OEMs early in the design cycles of new products. That has yielded greater information on the OEMs’ engineering and operational goals, as qualities and parameters of the connectors throughout their architectures will affect such goals dramatically. As such, connectors can be swiftly designed and developed for an exact purpose, whether it be size, weight, power, cost and so on.
Marine connectors
Among our previous articles investigating connectors (UST 24, February/March 2019, for example) much of the discussion has centred on ways to make them more suitable for UAVs – that is, ways of making them lighter and in some cases smaller.
And while the UAV industry continues to grow, in many ways the pace of growth in the maritime world has outpaced that in the airborne sector, hence a considerable number of innovations in marine connectors have appeared over the past few years.
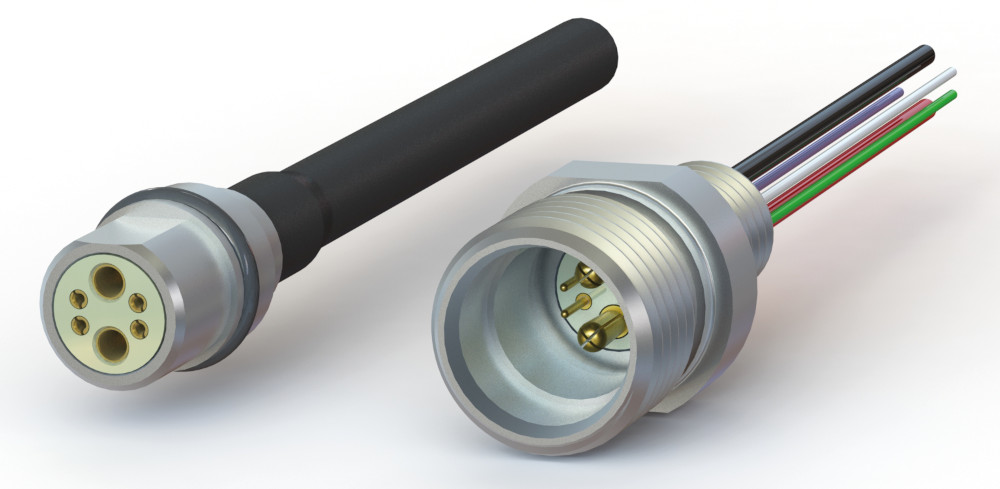
(Courtesy of Blue Trail Engineering)
UUV connectors are particularly challenging to engineer well. While weight is less of a problem for underwater vehicles than for aircraft, the pressure and corrosiveness of seawater mean that connectors running through the flooded hulls of large and extra large UUVs often have to consist of wet-mateable, rubber-moulded or epoxypotted plugs. These are highly effective, but as is the case with pretty much any kind of moulding or potting, producing them is time-intensive and is a tightly controlled and costly process.
That has driven a few manufacturers aiming at the marine market to seek ways of producing a safe, secure underwater connector that requires no potting or over-moulding. One of the most notable new solutions in this regard is a press-fit connector, which is built using a stainless steel shell with a PEEK (polyether ether ketone) insulator base holding the pins in place once they are pressed into the plastic. Although they have not yet been tested to their absolute limit, they have so far been proven to 600 m depth, making them suitable for missions in the riverine and littoral operations increasingly dominated by micro-AUVs.
That suitability is reinforced by the fact that they can be produced around 10 times faster than their conventional moulded equivalents – a critical improvement given that standard marine connector lead times are often around 12-18 weeks – and cost around half as much. This is further aided by the use of a barbed connection sleeve around the back end of their housings, which cable harness jackets can slide around and griponto for a watertight seal, accelerating the production process of complete cable and- plug systems for marine vehicles.
While these connectors are not wet-mateable, they remain ideal for manufacturers of UUVs that are unlikely to require their connections to be unplugged and reconnected underwater. And many vehicles are now designed to have slightly reduced capabilities than the high-end UUVs for the defence and petrochemicals industries in exchange for enormously lower production costs, making these sorts of connectors an ideal match.
Another notable innovation in this vein is a compression gland cable penetrator, which seals cables to a depth of 950 m. While not the traditional type of connector that uses male and female pin contacts, penetrators nonetheless allow users to add removable cable connections to an enclosure.
Potted penetrators have grown enormously in popularity over the past several years, but have weaknesses in terms of reliability and robustness. The compression gland penetrator design combines a rubber seal with a carefully designed internal geometry to achieve high-pressure performance without the use of potting materials, and they can be installed in just a few seconds.
Products such as these are helping to drive the boom in micro-AUVs for global environmental research and inspecting tight spaces inside sewers, storage tanks and so on. For long-endurance XLUUVs travelling down to 6000 m depths however (perhaps the second-fastest growing portion of the UUV industry), much stronger and more rugged designs are needed.
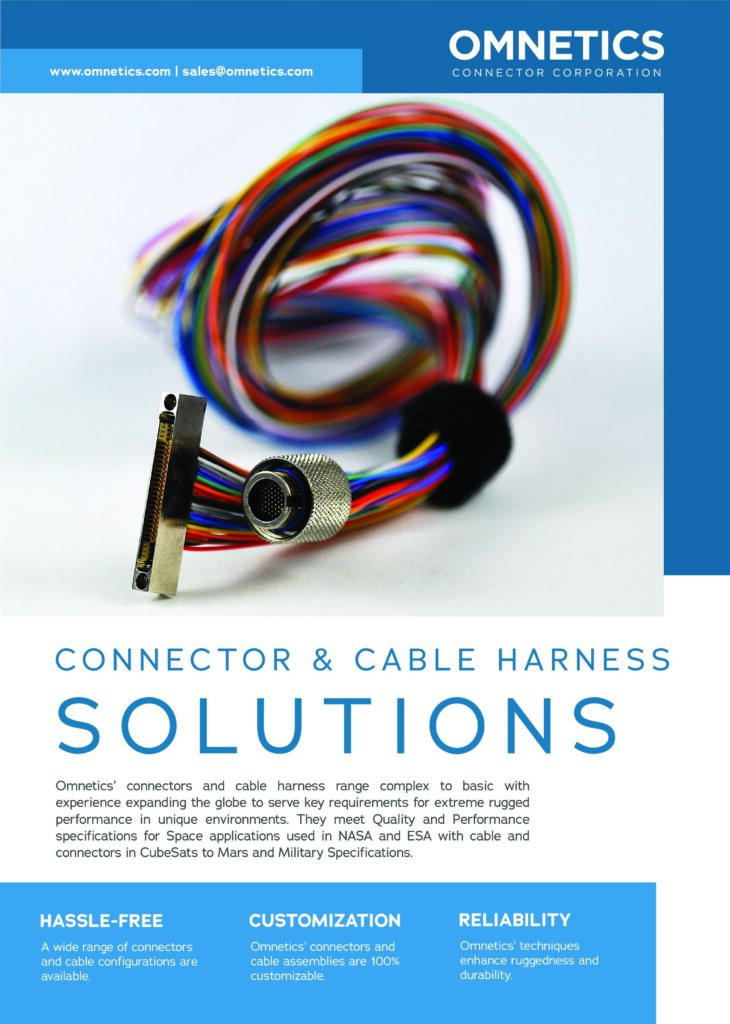
A certain measure of ruggedisation makes a connector ideal for use in the air as well as at sea. For instance, some circular connector developers design their products for IP68 rating, which means they can safely be submerged in different chemicals and solutions. That can make such designs useful for a USV or micro-AUV with plugs that might need to be submerged in up to 20 m of water for 2 hours, or for data or power connections around an aircraft engine where oil, fuel or coolant could spill.
And the use of such connectors goes beyond cable harnesses. Highly ruggedised flash drives have been popular for some time in motorsport for exporting car telemetry to a removable, physical device that will not be damaged by severe vibration, heat or splashing from race fuel or oil, and can be quickly removed and replaced during pit stops.
USB drives with ruggedised connectors that can be quickly un-mated could be
vital for many autonomous applications.
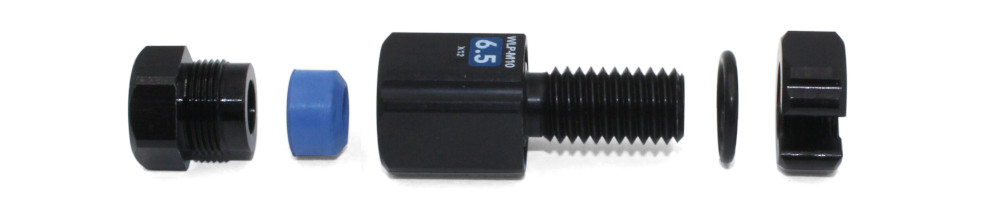
(Courtesy of Blue Robotics)
For example, UAVs that need to make quick and repeated mappings of an area – for instance in wildfire monitoring, warfare or disaster relief planning – could quickly dump their mapping and other mission data for post-processing on the ground before taking off again. The same goes for UUVs conducting back-to-back missions to find crashed airliners on the deep seabed, or critical leaks in subsea cables or oil pipelines.
The connectors of such devices can of course also be designed with unique keys to prevent unauthorised access to their data.
Design
The biggest factor steering new connector designs is probably volume. OEMs need connectors (as well as wiring harnesses) to take up less and less space in their vehicles, to be able to make them lighter, with less drag and with more free space for payload volume. As this directly contrasts with the increased need for ruggedisation, a few significant design innovations are gaining traction.
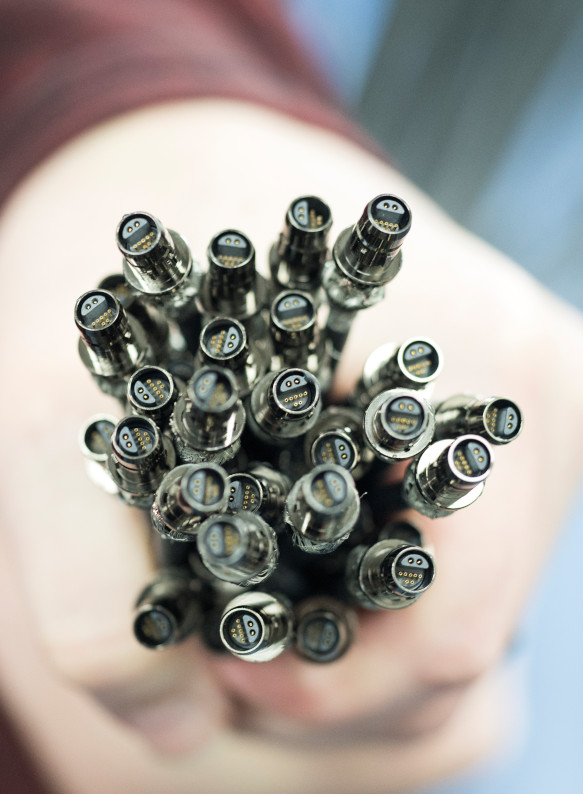
(Courtesy of Omnetics)
Some of these are ‘hybrid’ products that combine power and signal links within single connectors and harnesses. Designing these successfully depends hugely on close collaboration between the connector maker and the vehicle OEM, because an accurate understanding of the end-user’s voltage and current requirements is key for correctly sizing, spacing and insulating the pins, otherwise signal safety and integrity will suffer.
Similarly, as UAVs get larger and the line with the growing eVTOL taxi market becomes blurred, OEMs are requiring higher and higher power throughput in their connectors without making them prohibitively large. What started as new demands for 50 A, 100 V connectors a few years ago has since evolved into a market seeking up to 300 A at far higher voltages.
Designing and prototyping these takes skill and knowledge regarding conventional high-end connector design.
Any soldering for instance requires a heat sink, or else the quantity of solder material risks melting the wires or contacts. Alternatively, for crimping to work with the hefty gauge of the sorts of wires needed to conduct hundreds of amps at once, such large connections should be crimped before the pins are loaded into the connector housing and epoxied in place.
In the further pursuit of improving ruggedisation versus size, some developers have taken the step of combining male and female pins in individual plugs.
The reason why this helps with size reduction is that the back end of each contact typically needs more space than the top end, so all-male connector plugs need more clearance than their female counterparts. These ‘hermaphroditic’ plugs therefore make far better use of space and bring down the overall form factor of the connectors.
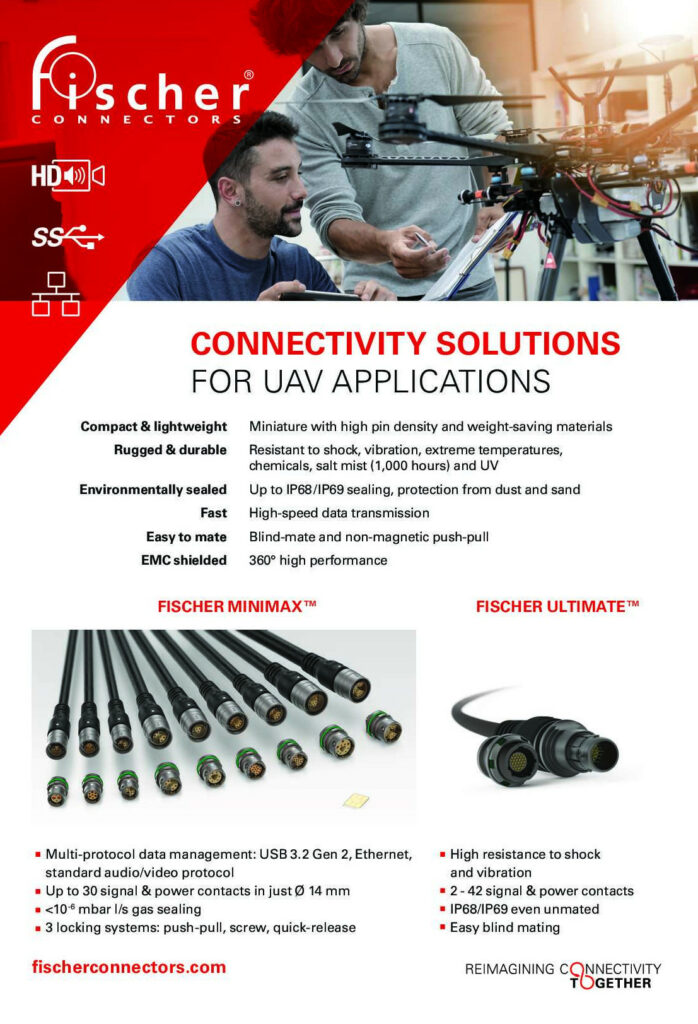
Such connectors can, however, be extremely challenging to engineer correctly with the right pin clearances and geometries to ensure that end-users can mate and un-mate them as smoothly as with conventional plugs. Considerable design lab resources must accordingly be devoted to them, as extensive trial and error is often needed to qualify the micrometre accuracy of their designs before investing in moulds and tooling to make the final prototypes.
And even once their design has been qualified in-house, hermaphroditic connectors remain less tried and tested than the typical male-and-female pairings. It is therefore not uncommon for prototypes to be sent to potential customers for beta testing, to ensure they can work in the various areas and operating conditions of their intended application before investing in tooling for series production.
To a lesser extent this is also useful for checking that connectors have not been made too small. One might instinctively reply that such a thing is impossible in the autonomous vehicle world, but given that field technicians at airfields often work with gloves and in a range of outdoor conditions, very small connectors could become highly frustrating to mate and un-mate.
In all cases, simulation software such as Dassault’s SolidWorks, Ansys’ High Frequency Structure Simulator and similar are critical to any company looking to design the latest generations of connectors, not only for new highpower connections but high-frequency ones as well, for reliable transmission of RF and Gigabit Ethernet data without losses. Real-world testing can then validate new designs to satisfy the demand for these parameters.
Testing
For high-end rugged connectors, every unit might be tested before shipping from its factory. Just as an engine might be cycled at all its crank speeds and across its power band in different conditions to assess its safety and reliability, so data can be run through connectors and cable assembles at different bandwidths on rate tables and in environmental chambers to certify that it can weather severe harshness and continue communicating critical information and commands throughout its intended vehicle.
Such testing is increasingly enhanced by connector companies taking OEMs’ own subsystems and vehicles, and running the connector tests while integrated with the systems. After all, what better way to model how a connector will perform in the field than running performance tests on the equipment to be fielded?
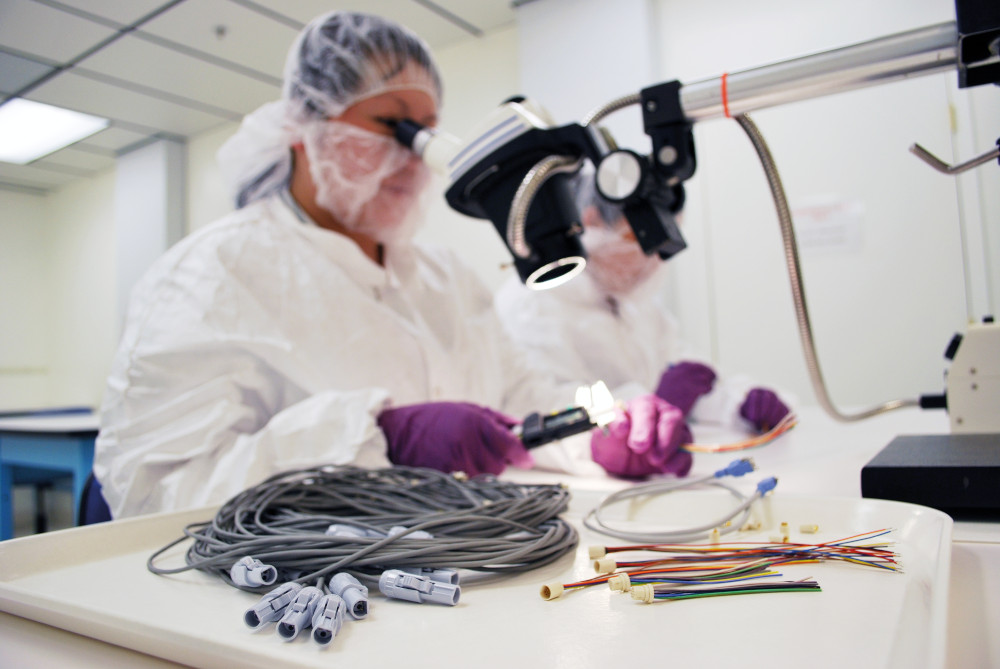
(Courtesy of Omnetics)
That also helps guarantee that different protocols are transmitted and received correctly, regardless of differences in signal or encryption type. It ensures that connector developers can serve commercial as well as military interests, rather than specialising in the protocols more often used by one or the other.
Also especially helpful in this regard is the growing practice of running tests and inspections for quality control on each part of every connector as they progress through the manufacturing line.
The sooner a mistake or defect is caught, the easier it is to fix, preventing leaks or short-circuits in the completed and delivered cable assembly.
Once fully assembled, the kinds of tests that can be run are largely conventional and well-understood. For instance, submergence tests can identify whether a better O-ring is needed for effective sealing against fluid ingress.
Vibration tests on rate tables will reveal the quality of latching or interference fit in the design relative to whether it will be mated on a stable surface or on a high-shock surface such as an engine or e-motor. And a wide range of electrical, radio and optical devices are available for measuring and analysing the ability of copper, coaxial and fibre connectors respectively to ensure the energy efficiency, data fidelity and overall integrity of each unit.
Increasingly though, end-users are specifying levels of testing they need performed on their connectors that go quite far above what might be called conventional. These can include measuring how resistance changes over extreme temperature cycling, longer and higher pressure salt spray tests, severe durability testing, and many others that suppliers cannot disclose.
As a result, more and more connector companies are building or expanding their own internal testing labs to cater for an end-user base whose testing requirements seem to be on an unwaveringly upward trajectory.
One marine connector company has gone as far as developing a pressure test chamber capable of automatically cycling pressure hundreds of times, while incorporating refrigeration and heating systems to simulate cold and hot conditions. That was in response to internal studies that found connector material failures to be more common in warm, tropical environments than in very cold waters.
Housing materials and parts
To provide a base level of contact protection against environmental variations, a wide variety of metals and plastics for connector shells are available.
Their choice depends mainly on the cost and weight constraints that OEMs are dealing with, and knowledge of these is well-established throughout the industry. Of them, it is worth mentioning that PEEK has gained considerable prominence thanks to its chemical resistance, temperature range and low cost, and Ultem is also widely used for its easy machinability.
Additive manufacturing has also helped considerably in prototyping plastic as well as metal housings that outwardly take the same form factor as older connector products while fitting more pins or hybrid combinations of power and data contacts inside. These technologies are also well-understood now by connector designers looking to fulfil a request, and customers looking to present one for mass production.
Less familiar to many is the wide array of new backshells that connectors can come with. These can provide critical protection against the ingress of dirt, liquids and, most importantly for new generations of autonomous vehicles, EMI.
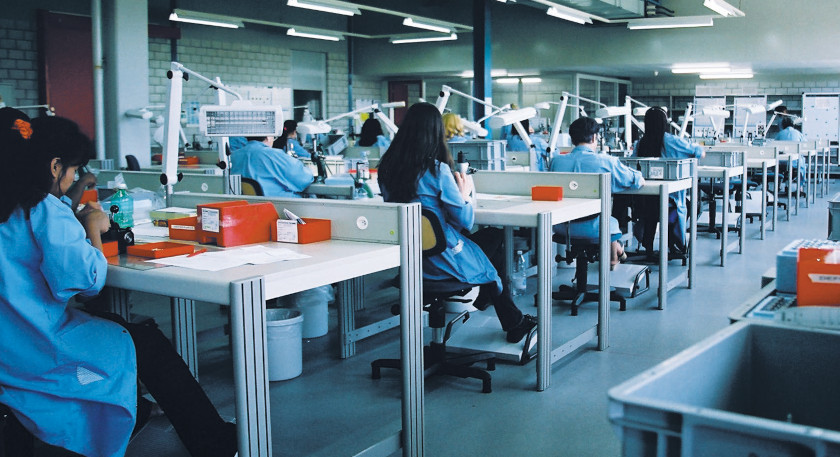
(Courtesy of LEMO)
While system integrators typically have a good understanding of the kind of shielding they should have in their cable jackets – for instance, EMI protection has long been critical for safeguarding PWM links running between ESCs and electric motors – they may not understand so well how their new electrical connector designs might be susceptible to (or generate) EMI.
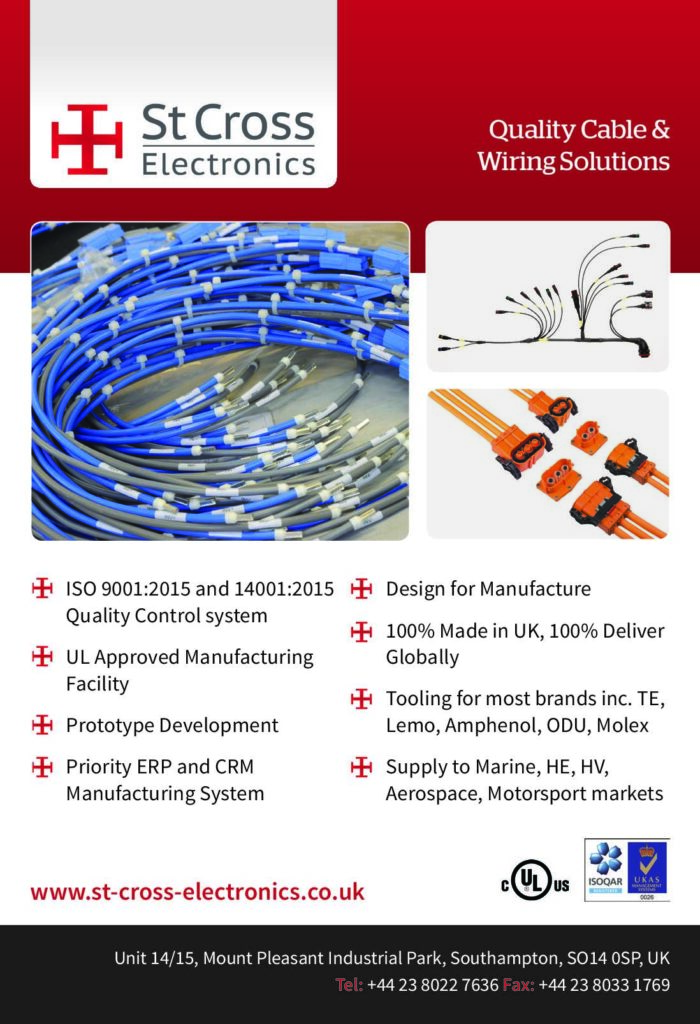
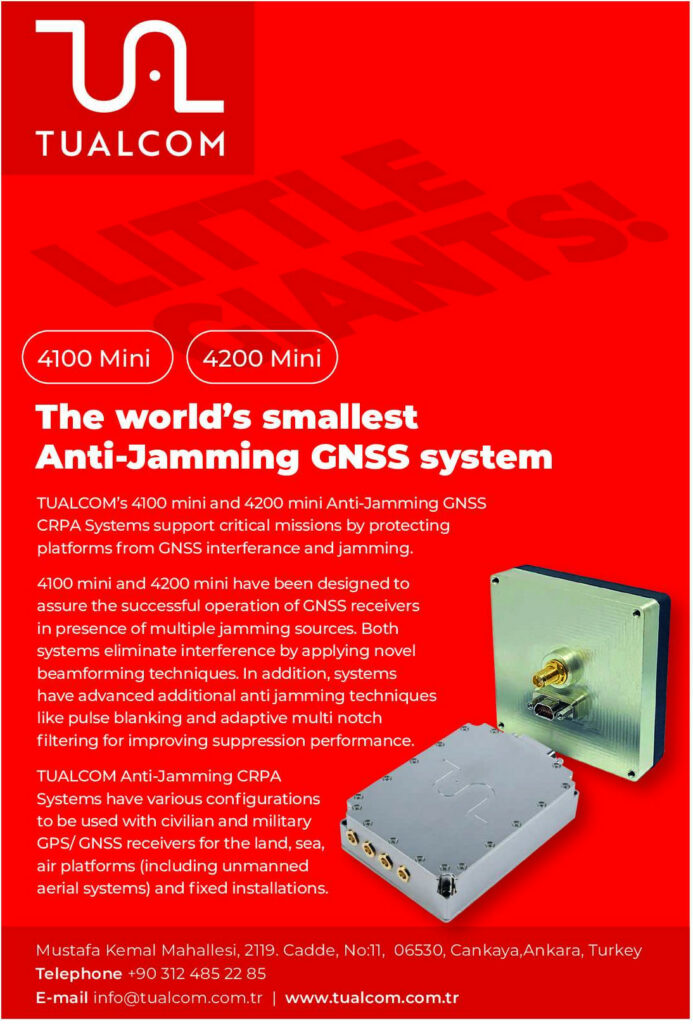
Backshells made from combinations of aluminium and steel, with mixtures of elastomers or composites for additional environmental robustness, could be critical add-ons for the new wave of high-current connectors, or for any sensitive data connections sitting near them.
In addition, an ever-wider variety of latching methods are available for ensuring mating is secured against shock and vibration. For example, screwlocking enables what is effectively a lengthy interference fit through an outer sleeve on one plug that mates circularly into or around the other. Alternatively, some connectors can be designed with an integral safety locking ring to prevent unauthorised or accidental release.
As well as these, many traditional approaches are still available that work well for most applications. For instance, circular connectors are often selected with the familiar push-pull locking. This works by the plug having an outer sleeve with bevelled forward edges that, during mating, catch and are secured in a locking groove inside its receptacle.
For some applications, however, excessive mating security can actually be problematic: defence operations where a UAV being recharged or repaired must be quickly redeployed are an example here. For such situations, connectors can instead be designed with breakaway latches that separate when a certain threshold of direct manual pulling force is applied, unlike screw locks that must first be unscrewed and push-pull locks that must be squeezed.
Manufacturing innovations
As demand for connectors across the autonomous vehicle industry grows, connector manufacturers are constantly looking to upgrade their manufacturing lines with newer and better machinery to enhance the productivity, quality control or complexity of units that can be assembled.
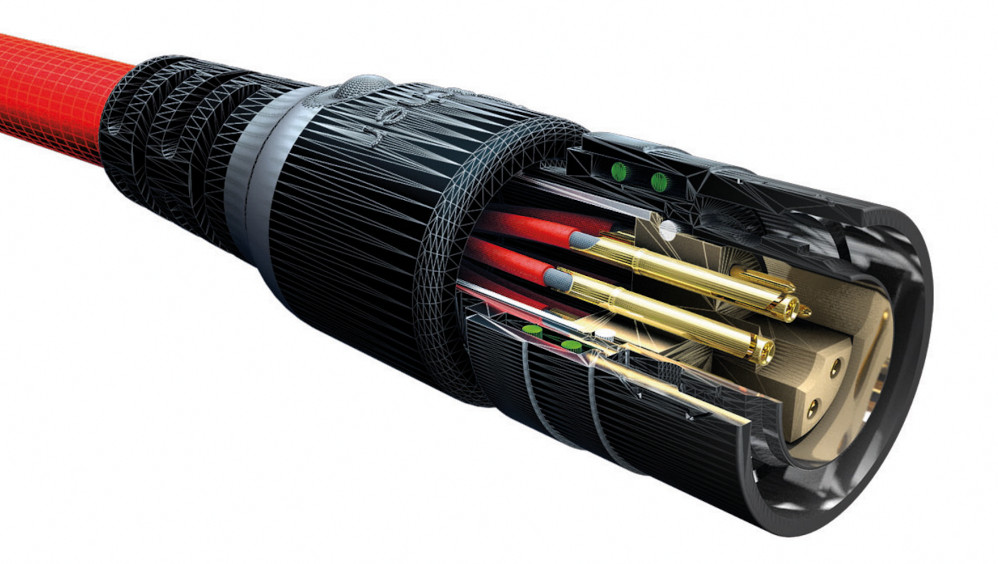
(Courtesy of Fischer)
While retaining manual production of some aspects can be critical to providing the customisations that uncrewed vehicle makers request, automation provides too much consistency and reduction of man-hours per unit for connector manufacturers not to have viewed it as an upgrade worth investing in for the past several years.
Among these are CNC-cutting machines with automated mechanisms for loading pin contacts into their housings. Robotic insertions are far less labour intensive and often faster than manual loading or ‘swaging’, where contacts are pushed by hand into their through-holes and then cooled. Such machinery can also be quality controlled in an automated fashion using laser or camera scanning of the pins and housings.
When it comes to mating wires to pins, although crimping remains the most popular approach and automated crimp machines are becoming more and more widespread, major advances have been made in the designs and techniques related to soldering. Some connector manufacturers now solder 90% of their connections and crimp the other 10%.
These often relate directly to advances being demanded in high-end autonomous vehicle connectors. For instance, in very small circular connector designs, which can now feature up to 30 contacts in 14 mm-diameter connectors, it can be difficult to get a close fit using crimping tools.
One solution is to design solder cup terminals – arrangements of pin backends intended to ease the process of precisely applying the molten solder – in a ‘Christmas tree’ configuration. Here, the central contact is longest and hence sticks out further than those around it, while the contacts become progressively shorter in concentric circles away from it.
That allows engineers to solder from the centre, moving outwards for a generally straightforward and easy termination process. This is essential for vehicle manufacturing and assembly suppliers, who need to be able to terminate their conductors in-house, as even the best connector in the world will find little demand if it is too time consuming and difficult to work with.
Comms protocols
The reach and rate of advances in the uncrewed vehicles industry are also driving the adoption – and in some cases, creation – of entirely new comms protocols in order to ensure that data is transmitted and received at ever higher bandwidths, speed, fidelity and more.
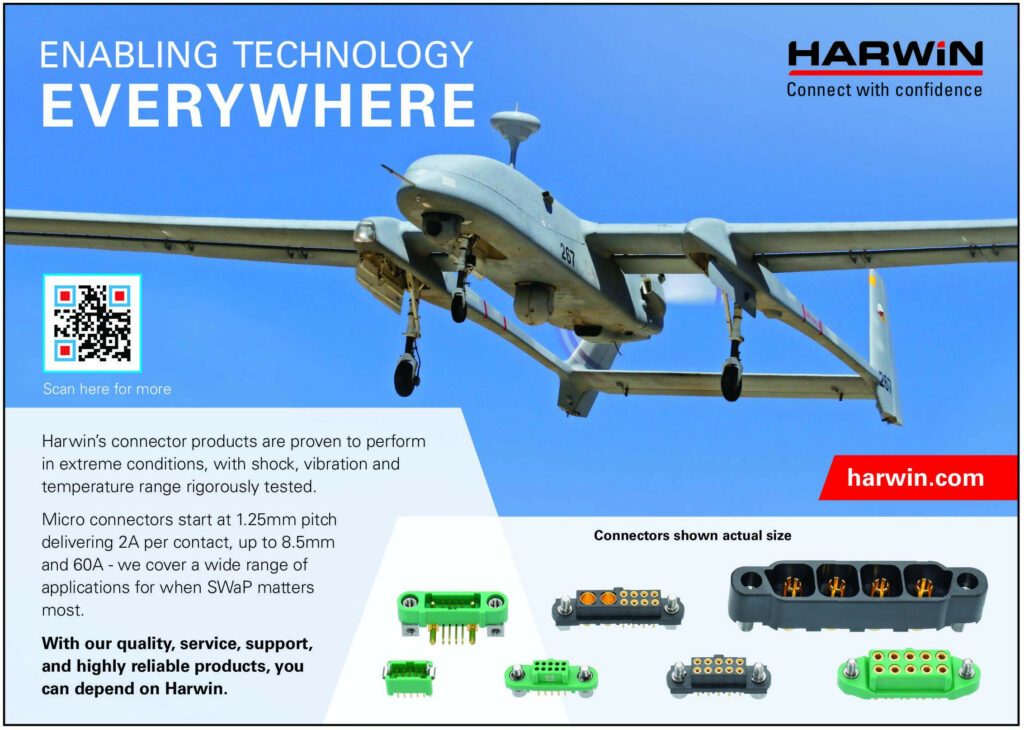
For instance, different standards for USB 3.2 and a number of newer types of CAN bus are among those published in the past several years that are likely to see growing interest for uncrewed air, sea and land vehicles in the years to come.
Meanwhile, Gigabit Ethernet has seen widespread uptake for the data speeds and bandwidths it enables, and the new industrial standard SPE (Single Pair Ethernet) is being adopted by military and medical users, as well as across IoT systems.
In order to ensure that companies’ inventories of connectors are not rendered obsolete every few years by the advent of new comms standards, connector developers keep track of certain key parameters to help futureproof their designs so that they can still carry more and more advanced and complex protocols.
‘Clearance’ and ‘creepage’ are of paramount importance among these. While the former has been explained above, creepage refers to the minimum distance between pins as measured when running along the physical surface of the insulating material (as opposed to straight-line distance).
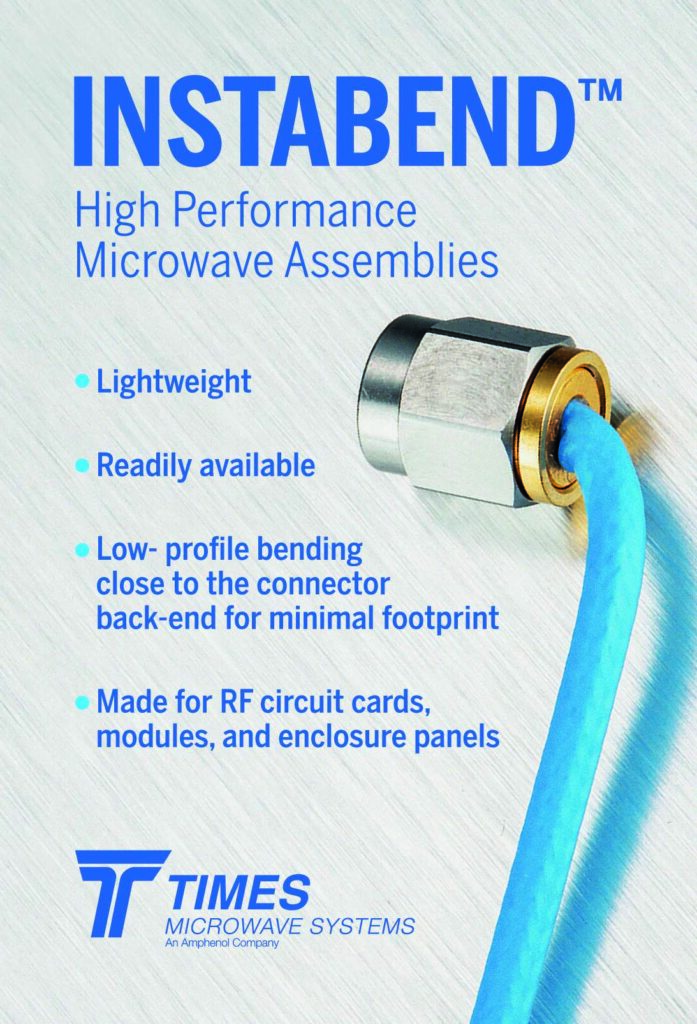
Minimising these means squeezing pins closer together and potentially fitting more connections into a given space. However, enough space and dielectric material such as PEEK must exist between each contact to ensure arcing does not occur, otherwise connection failures or even fires can occur. And increasingly, new kinds of inserts must be designed and produced to ensure sufficient space and arrangements between contacts to pass protocol standards.
Signal integrity engineers continue to experiment with different approaches to optimise pin spacings, material choices and contact types for new data configurations. They are also combining them with more established technologies such as the aforementioned latches, backshells and new solder terminals to better specialise in what the uncrewed sector needs.
Conclusion
Just as UAVs cannot run well on engines taken from chainsaws or lawnmowers, plugs from existing high-power or high frequency applications are rarely optimal for use in autonomous vehicles. The connectors industry is therefore growing and innovating fast to match the pace of the world of uncrewed systems. With innovations emerging across the board, it is worth keeping a close eye on new products coming out in the years ahead.
Acknowledgements
The author would like to thank David Ptacek at Fischer Connectors, Derek Hunt and Travis Neumann at Omnetics, Steven Lassen at LEMO, Damon McMillan at Blue Trail Engineering, and Rustom Jehangir at Blue Robotics for their help with researching this article.
Examples of connector manufacturers and suppliers
BELGIUM
SICK +32 2 466 55 66 www.sick.com
DENMARK
MacArtney Underwater Technology +45 7613 2000 www.macartney.com
FRANCE
Esterline Souriau +33 1 30 84 77 99 www.souriau.com
Staubli +33 4 50 65 67 97 www.staubli.com
GERMANY
GISMA Steckverbinder +49 4321 983530 www.gisma-connectors.de
Wennmacher Electronic +49 6022 62240 www.wennmacher-electronic.de
ITALY
AvioRace/Tecnoelettra Group +39 059 77 0 0253 www.aviorace.it
SWITZERLAND
Fischer Connectors +41 21 800 9595 www.fischerconnectors.com
Huber & Suhner +41 71 353 4111 www.huber-suhner.com
LEMO +41 21 695 16 00 www.lemo.ch
UK
AEF Solutions +44 122 7711455 www.aeiuk.com/aef-solutions
CEEP Connectors +44 1730 895785 www.ceep.co.uk
Cinch Connectors +44 114 478 9351 www.belfuse.com/cinch
FHS +44 1753 513 080 www.fhsracing.co.uk
Harwin +44 23 9231 4545 www.harwin.com
USA
Airborn +1 512 863 5585 www.airborn.com
Air Electro +1 818 407 5400 www.airelectro.com
Amphenol +1 203 265 8900 www.amphenol-aerospace.com
Battlefield International +1 905 772 3000 www.battlefield.biz
Binder USA +1 805 437 9925 www.binder-usa.com
Blue Trail Engineering +1 720 526 6388 www.bluetrailengineering.com
BTC Electronics +1 919 556 8900 www.btcelectronics.com
Carlisle Interconnect Technologies +1 904 829 5600 www.carlisleit.com
Cinch Connectors +1 630 705 6000 www.cinch.com
E-Valucon +1 949 450 0080 www.evalucon.com
Glenair +1 818 247 6000 www.glenair.com
Harwin +1 603 893 5376 www.harwin.com
HiRel Connectors +1 909 626 1820 www.hirel.net
Intro Corp +1 321 757 6330 www.introcorp.com
ITT Cannon +1 800 854 3028 www.ittcannon.com
LEMO +1 707 206 3776 www.lemo.com
Meritec +1 440 354 2100 www.meritec.com
Molex +1 630 969 4550 www.molex.com
Nicomatic +1 215 444 9580 www.nicomatic.com
ODU-USA +1 805 484 0540 www.odu-usa.com
Omnetics +1 763 572 0656 www.omnetics.com
PEI Genesis +1 215 673 0400 www.peigenesis.com
PIC Wire & Cable +1 262 246 0500 www.picwire.com
Positronic +1 417 866 2322 www.connectpositronic.com
Smiths Connectors +1 913 233 5123 www.smithsinterconnect.com
Stealth Aerospace +1 818 716 5696 www.stealthaerospace.com
TE Connectivity +1 717 592 2339 www.te.com
Times Microwave Systems +1 800 867 2629 www.timesmicrowave.com
Ulti-Mate Connector +1 714 637 7099 www.umi-c.com
UPCOMING EVENTS
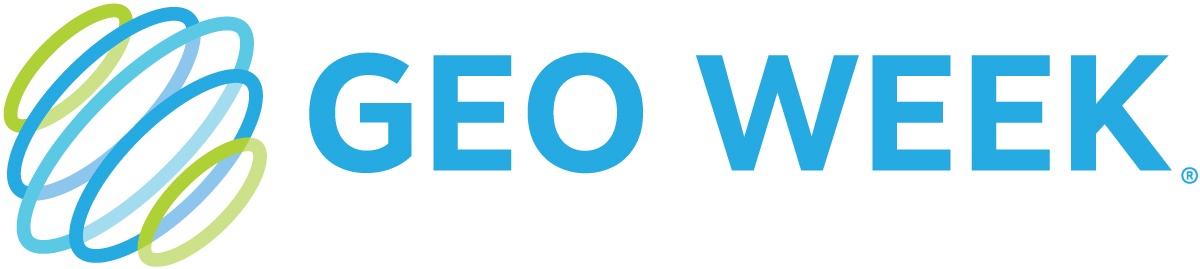
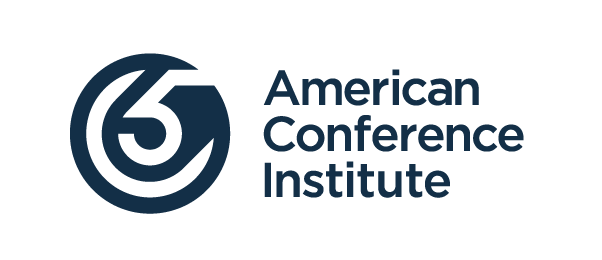
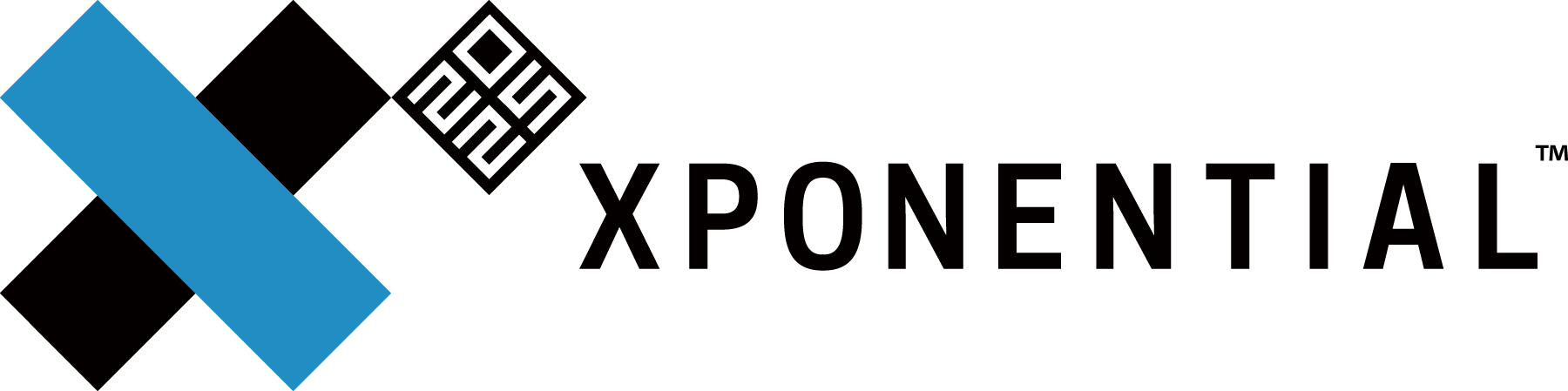
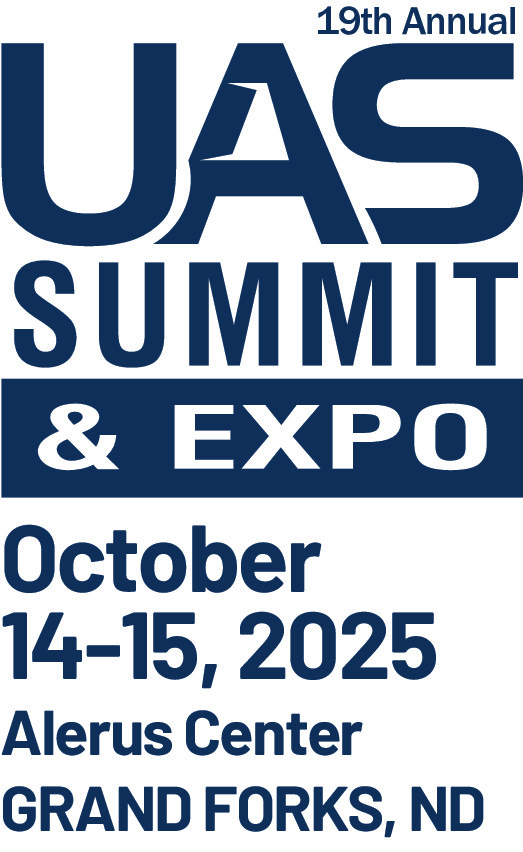
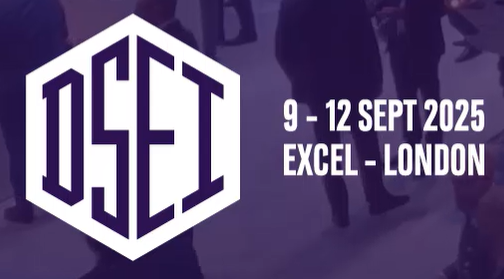
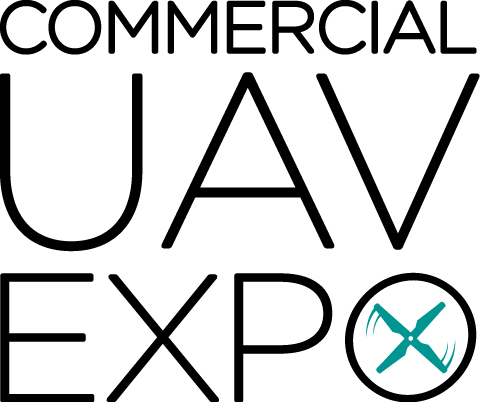
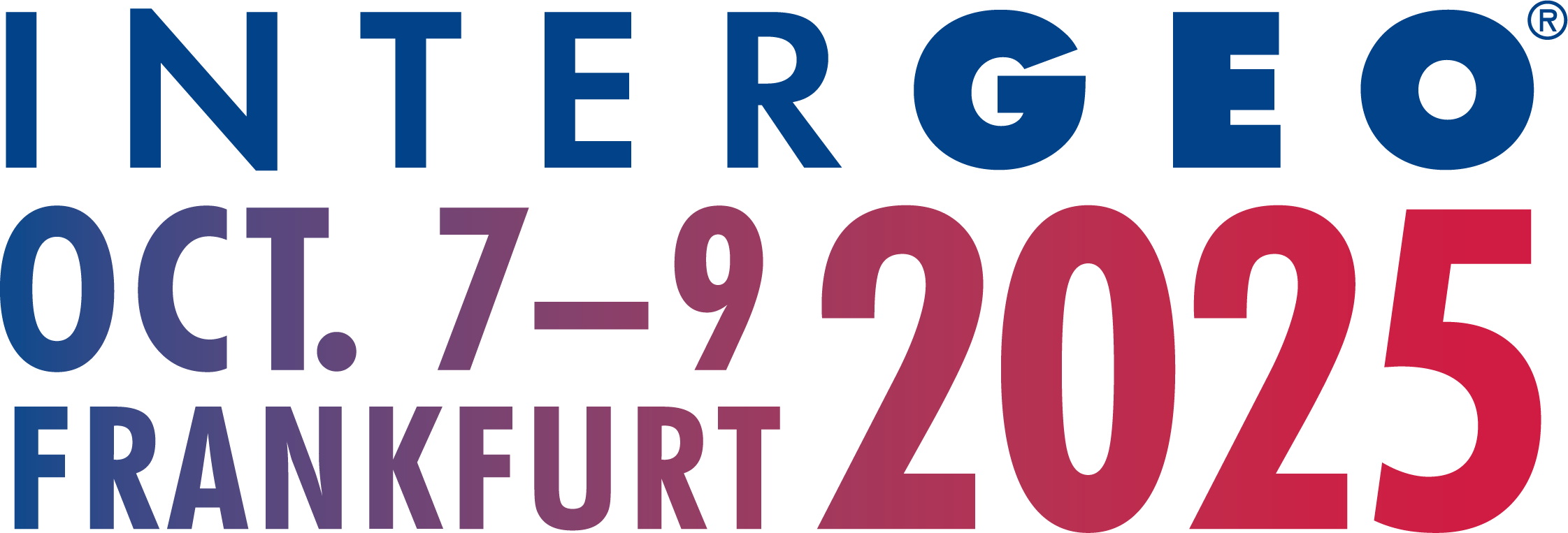
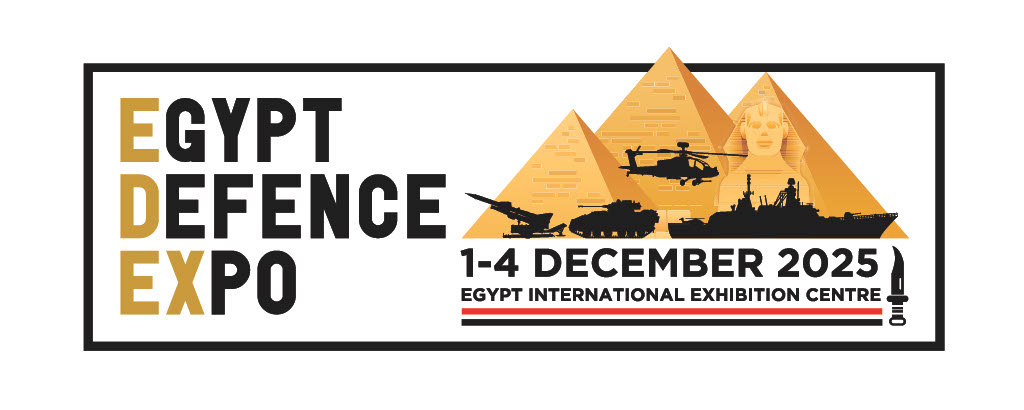
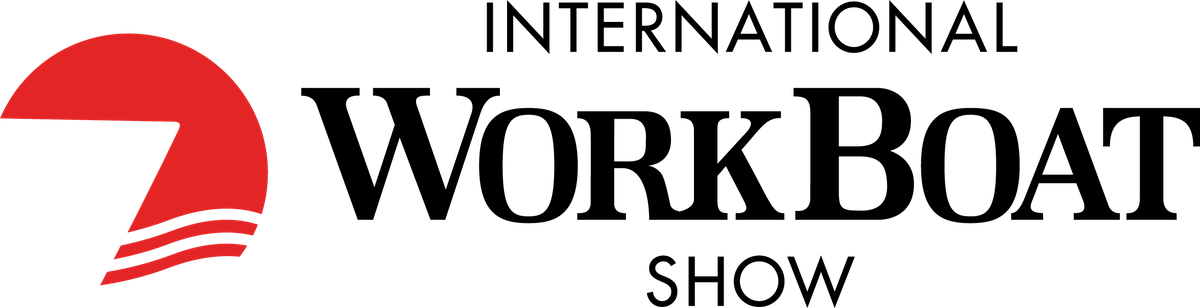
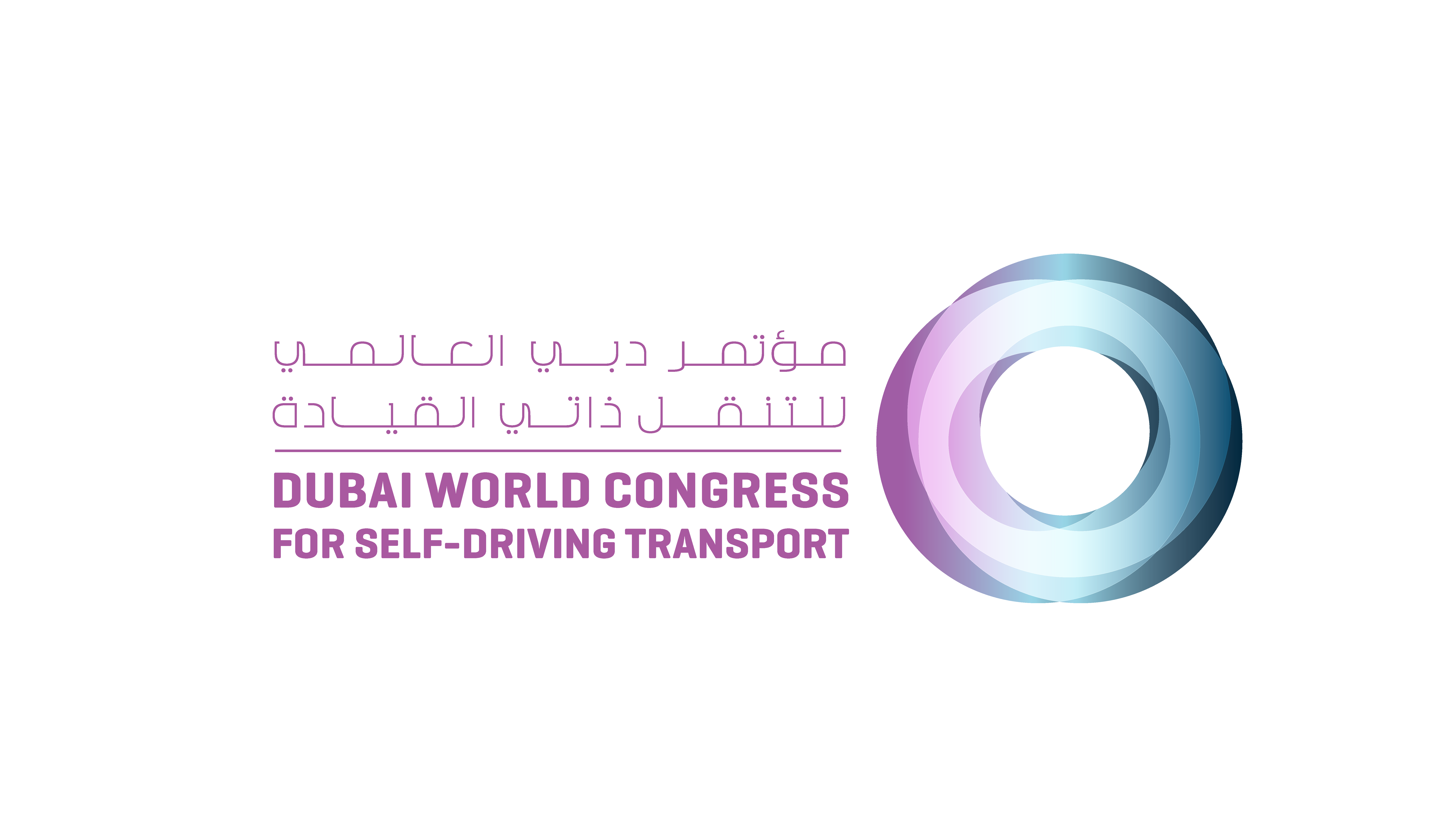
