DeltaHawk DHK180
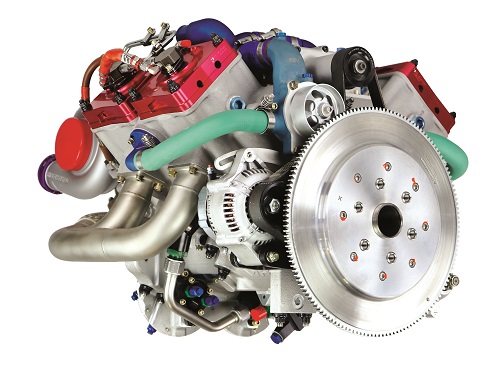
(all images courtesy of DeltaHawk)
Rory Jackson investigates how this compression-ignition two-stroke engine achieved FAA Type Certification
DeltaHawk Engines is a Wisconsin-based company, dedicated to the development of compression-ignition engines for crewed and uncrewed small aircraft. Though seemingly a newcomer among UAV powertrain manufacturers, it was actually founded almost three decades ago, by Diane Doers, Doug Doers and John ‘JP’ Brooks – the former an experienced businessperson and the latter two being military-turned-civilian pilots.
The three were motivated to found DeltaHawk in 1996 by what they saw as conspicuous flaws in general aviation (GA) engine designs. By and large, these were air-cooled engines integrating magnetos, carburettors and other old technologies. Such engines are maintenance-intensive, fuel-inefficient and rarely lasted up to 1000 hours between overhauls.
In their view, modernising GA engines meant creating one that was easier to operate, had far fewer points of failure, was more fuel-efficient and could run on many different fuels. Most GA engines run on avgas, which is limited in availability to Europe and North America (and is being phased out due to its lead content).
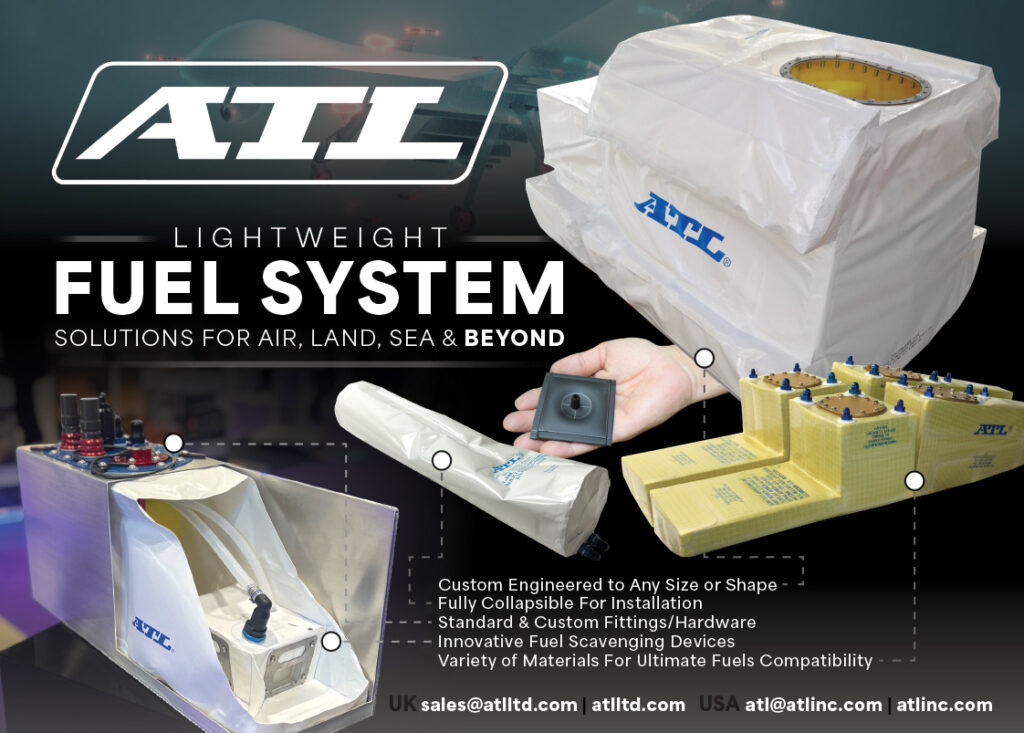
Compression ignition was soon identified as key to making their engine run on widely available fuels such as kerosenes and diesels, and within a year an 80 HP (60 kW) prototype had been produced.
As multi-fuel engines are highly valued among UAV operators, this is the market that DeltaHawk is targeting today, in common with other GA engine companies we have featured, such as Austro Engine (issue 4, Summer 2015) and ULPower (issue 45, August/September 2022).
Over 27 years, the team has accrued investments, key personnel and technologies optimised for their envisioned engine – along with a high number of patents to protect them – and Type Certification from the FAA in 2023, a rarity among UAV powertrains.
That certified powertrain is DeltaHawk’s first commercially available product, the DHK180, a 162 kg, two-stroke engine producing up to 180 HP (134.2 kW). It is certified to run on Jet A and Jet A-1, but it can also run optimally on JP-8, D1, D2 and F-24. It is a liquid-cooled aircraft engine, oiled via dry sump, turbo- and supercharged.
DeltaHawk designed it at each turn for simplicity and redundancy, such that it runs without needing an ECU for any injection, induction, cooling or other requirements. From the first 80 HP prototype to today’s 180 HP product, it has remained a 3.3 L, 90° V4 engine for direct-drive aircraft applications.
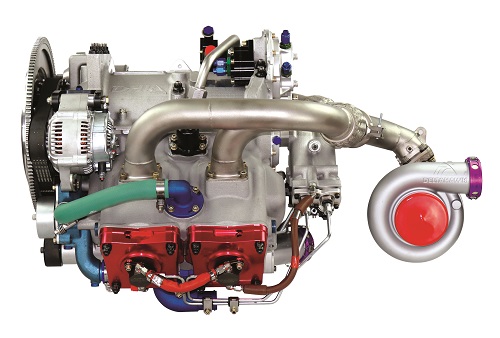
Challenges to solve
However, making it work consistently and reliably has been more challenging, explains Dennis Webb, DeltaHawk’s director of certification, an FAA DER (Designated Engineering Representative and hence the FAA’s eyes on the company), a 2000-hour instrument-rated pilot and also a licensed professional engineer since 1979.
“Over the decades there have been more versions and iterations of the block alone than any of us can really count confidently, until we cast the ideal material and machining geometry. There were literally thousands of engineering problems and subtle issues that we had to resolve,” Webb recounts.
“Here’s one example: typical piston pins are designed for four-stroke engines, where on the end of the exhaust stroke you get a slight gap between the pin and the piston boss, and oil sneaks into that gap so that the pin gets lubricated. That doesn’t happen in two-strokes because you’re always compressing, so getting a piston pin to live long in a high-performance, two-stroke diesel is really hard.
“There are dozens more niche but serious problems like that, which we worked really hard to solve. For instance, we’ve spent millions of dollars developing our unique fuelling system and getting it to work.”
In addition to the FAA and Webb approving roughly 20,000 pages of documents for certification, DeltaHawk has verticalised its production via manufacturing facilities that are fully controlled through electronic monitoring systems. Up to 10,000 DHK180 engines can be supplied and maintained per year at its current facility, which also houses three different types of dynamometer and a quality lab with coordinate measuring machine (CMM) systems, optical comparators, laser measurement devices and other metrology machines.
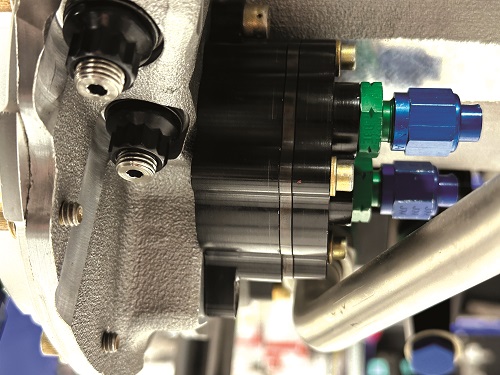
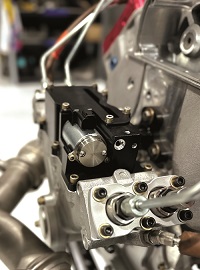
Why a two-stroke?
DeltaHawk has chosen to produce this engine as a two-stroke, but also to not broadcast widely that it is a two-stroke (the term being notably absent from the company’s website).
“When you say ‘two-stroke’, people think of horrible fuel-oil mixtures, terrible emissions, poor fuel efficiency and short TBOs. It isn’t always correct to think that, especially since most of those problems can be attributed to gasoline-fuelled, crankcase-scavenged, air-cooled two-strokes, but many still do,” Webb remarks.
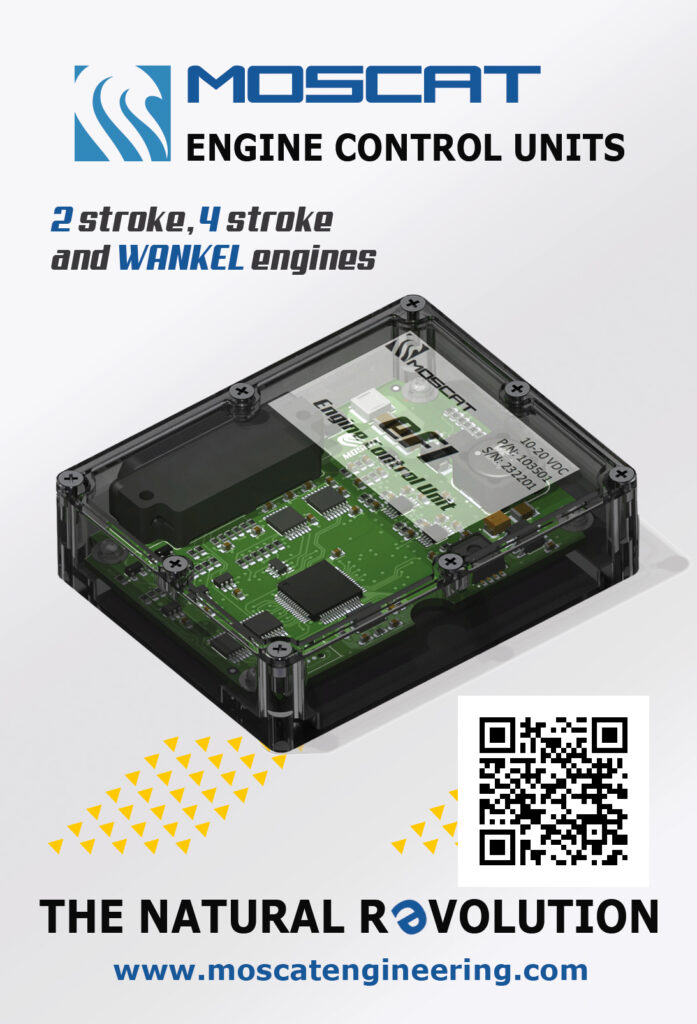
“But a compression-ignition, liquid-cooled two-stroke is completely different. Virtually all large ships use diesel two-strokes, renowned for long life and fuel efficiency. Half of all US locomotive engines historically used diesel two-strokes, with similar reputations. Now, we’re in aviation; certainly, a very different application to both of those, but there’s still several aviation advantages that the two-stroke has over four-strokes that put DeltaHawk on the two-stroke path.”
For one, if an aircraft suffers a flameout at high altitude owing to a primary tank running dry, it must relight, which is very difficult in typical, turbocharged aviation four-strokes. Cooling from the exhaust stroke following each combustion stroke, combined with pressure loss from the sudden absence of exhaust gas to drive the turbocharger, means there is insufficient heat and pressure for ignition.
This limits such four-strokes’ relight altitudes to about 6000-7000 ft (1828.8-2133.6 m) – anything higher and the UAV will lose all engine power. But as two-strokes are constantly compressing and combusting, sufficient heat is created to relight the engine as soon as a backup tank kicks in.
With its mechanical (gear-driven) supercharger to maintain the pressure and volume of air entering the cylinders, Webb estimates the DHK180 has a maximum relight altitude of “somewhere in the high ‘teens’ of thousands of feet” (15,000 to 20,000). He adds: “We want to test it further before publishing an official number, but likely at least 10,000 ft higher than a four-stroke.”
Simplicity and compactness
Other motivations included simplicity: two-strokes operate without the valvetrains or camshafts of four-strokes, resulting in fewer failure points and pieces to replace at intervals. On top of this, DeltaHawk also wanted the simplicity, compactness and light weight of a direct-drive system.
“The most straightforward route for high power is making a four-stroke engine with four valves per cylinder, double overhead cams, EFI and a very high rpm. That’s how Formula One makes power and how most modern cars make power, but there’s always a transmission that follows,” Webb notes.
“Similarly, all our compression-ignition competitors make four-strokes that produce high horsepower by spinning fast, with a transmission to convert that into torque for turning a propeller. Instead, we made a two-stroke V4 with the firing pulses and mass air flow (MAF) of a four-stroke V8, and so we redline at 2600 rpm – whereas an equivalent four-stroke V8 would redline around 5200 rpm – but we produce 492 Nm of maximum torque at 2600 rpm.
“That’s enough for a large propeller, with speed and power pulses low enough that the propeller doesn’t endure the punishment typical of high compression-ratio diesel engines.”
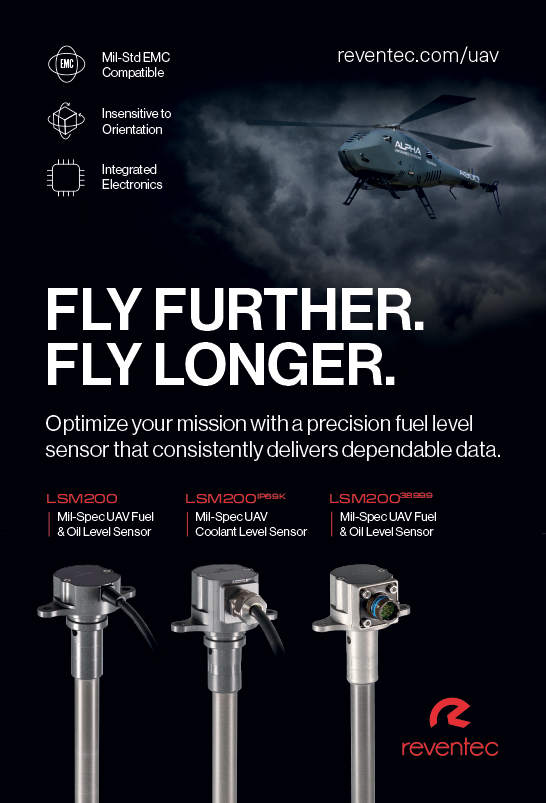
The V4 architecture offered more compactness than the boxer configuration more commonly seen across UAV engines, with one key benchmark for the DHK180’s design being the Lycoming IO-360 – a spark-ignited, four-cylinder four-stroke of similar power, which DeltaHawk aimed to be smaller than.
“The V4 also makes sense operationally; horizontally opposed engines generate huge vibration from cylinders firing against each other, but a vee’s cylinders don’t do that,” Webb adds.
In most tractor-propeller applications, the engine will be mounted as an inverted-vee. This means that high-speed, high-pressure air from the front-mounted propeller backwash can run over the topside of the aircraft for proper aerodynamics, and either the pilot can see ahead without cylinders blocking their view, or in the case of UAVs, the propeller will not hang low within the viewpoint of any payload gimbal carried under the aircraft.
For a pusher-propeller integration, either the conventional or inverted-vee can work. Four mounting points sit on the base plate, such that in the inverted-vee, they are atop the engine, and on the bottom for the regular vee (the engine can also run vertically for helicopter applications).
Several hundred engines’ worth of components have been produced for repeated experiments, testing and iteration – such is DeltaHawk’s satisfaction with the performance and reliability gained by these design properties, and by others to be discussed henceforth.
Starting power and fuel
The engine starts using a conventional 24 V aviation-style Sky-Tec starter from Hartzell, although a 70 A brushless DC alternator from Plane Power is also integrated as standard (driven by an automotive-type poly vee belt, chosen for long life and reliability, compared with other belts).
“The starting method is very traditional: the starter pulses around 200 A from a typical aircraft-type starter battery to get the crankshaft moving,” Webb says. “Each cylinder has a glow plug, as with most diesel engines, which we normally turn on for 10 seconds before starting for preheating.”
Much of what follows, however, is untraditional for modern UAV engines, as the DHK180 has no ECU for managing the fuel and air quantities going into the engine, for the simple reason that it does not need one. Instead, it has been designed to operate using uncomplicated mechanical systems, which feature a minimal number of potential failure points and significant failovers or redundancies compared with many other power units.

Like the WAM-167BB two-stroke diesel from Apple Tree Innovations (ATI), featured in issue 28 (October/November 2019), the DHK180 is a lever-controlled engine, with just a single lever at the back for toggling the quantity of fuel delivered to (and hence power produced by) the engine. A fitting sits at the back of the DHK180, where a control cable or linear actuator can connect to the lever, through which the autopilot can interface with the engine in a simple, straightforward manner.
Fuel delivery occurs via two main pumps: a low-pressure pump atop the engine draws fuel from the UAV’s tanks and feeds a high-pressure fuel pump (HPFP). The low-pressure system is a gear-type pump, driven directly via an internal gear set on the back of the engine.
“In all aviation installations, you’re required to have an electric pump as well for redundancy, and I’m fairly sure you’d want the same in an uncrewed application for redundancy, so we can integrate one of those if needed,” Webb adds.
The HPFP assembly is on the back of the engine, attached to an accessory cover that houses a plethora of gears for driving accessory devices (and the aforementioned control fitting is on the bottom of it for mechanically managing the HPFP), all mounted externally for ease of maintenance.
Four steel lines run from the HPFP – one to each injector – through which fuel sprays directly into the cylinders, as in all diesel engines. Additionally, a considerable amount of fuel bypasses the injectors and returns to the tank (also typical in diesel engines), but rather than returning directly, as is conventional, the DHK180’s bypass fuel is routed to the injector heads to cool them first. That heated fuel can, if needed, be used to pre-heat the incoming fuel through a heat exchanger (if flying in cold regions or weather fronts, for example).
“Inside the HPFP assembly, running into each steel line and hence each cylinder, is its own independent plunger-barrel system; those piston back and forth to govern fuel delivery to the injectors, and are managed via a very small and simple camshaft – not at all the big kind you’d see controlling the valves in a four-stroke – and that camshaft is driven via a spline running off the back of the crankshaft,” Webb explains.
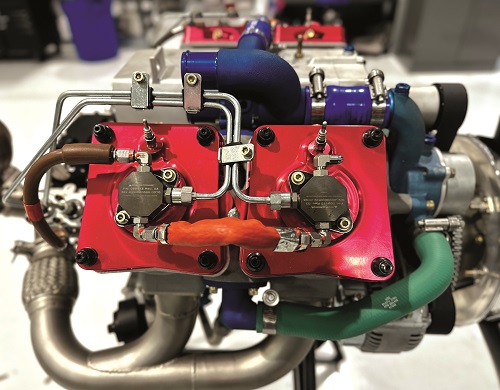
Mechanical control
The aforementioned control lever connects through a mechanism to each of the four high-pressure unit pumps, which controls the effective stroke of the plungers, thus determining (completely mechanically) how much fuel is injected with each cycle.
“In essence, we have four independent fuel-pumping systems, with no electronics needed,” Webb concludes. “ECU hardware, software and wiring harnesses are complex, and hard for technicians to fix in the field. We designed our engine so any aircraft mechanic can fix it with hand tools anywhere around the world.
“There’s no widespread maintenance network out there for aviation ECUs. You can’t turn up at an aircraft mechanic and expect them to know what to do with an ECU-managed compression-ignition engine. They’re not going to have spare MAF or MAP [mass air pressure] sensors in their inventories; they’re not going to have the kind of training in software programming for that.”
He adds that in many cases, the failure of an ECU, a high-pressure fuel rail or a key sensor results in the failure of the engine, and hence the UAV. But if one of the four high-pressure fuel pumps on this engine should mechanically fail, only 25% of power is lost (and tests show no additional vibration, thanks to the three remaining power pulses per rotation), enabling the UAV to either attempt to complete its mission or safely return to land.
Lastly, the absence of an ECU and sensors reduces the electromagnetic interference (EMI) produced by the engine, while also eradicating its own susceptibility to EMI, which is a growing risk to ECU-driven engines with today’s UAVs integrating more high-voltage and thus high EM-emissions devices.
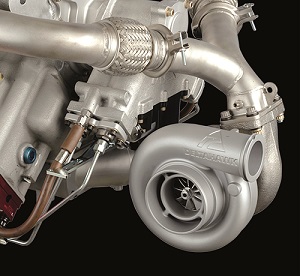
Forced-induction systems
At higher altitudes, natural aspiration is insufficient for the airflow requirements of most compression-ignition engines, so forced induction via a turbocharger and a supercharger enables the DHK180 to maintain adequate intake air volumes, mass flow, and pressure for consistent and precise fuel/air mixing.
A mechanical supercharger sits between the four cylinder heads, above and feeding into a large, open intake plenum, from which all the cylinders draw air. That supercharger is a twin screw-type, with rotors designed to very close tolerances, chosen by DeltaHawk for its high-efficiency, pressure ratio and volume flow.
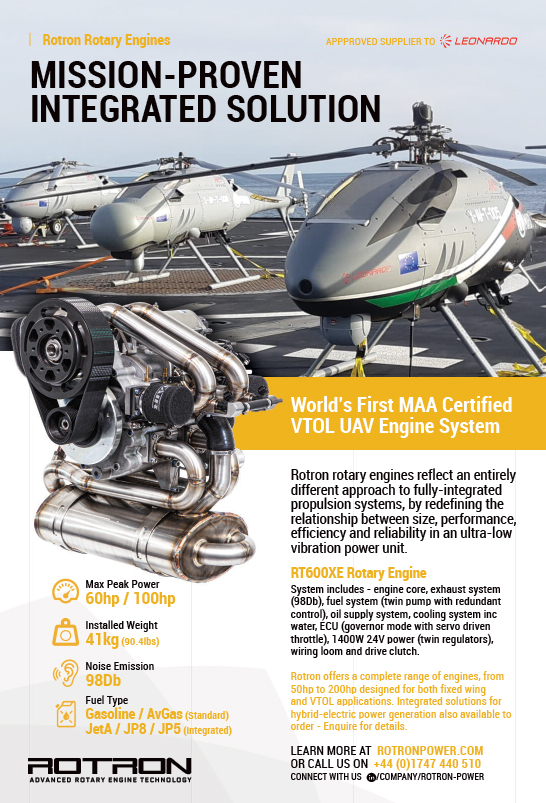
“The supercharger is critical for starting because the mechanical turning of the crankshaft drives the supercharger to stuff air into the plenum. At that point, the turbo can’t run because there’s no exhaust to drive the turbine,” Webb remarks.
“For similar reasons, it also supplies air during idling, lower power settings, and generally at lower altitudes. At higher power and higher altitudes, the turbo does most of the work. And they do run in series: air ideally first comes in through an inlet and filter on the aircraft, the turbocharger draws in air via its compressor and that then goes to an intercooler, and the cooled air then goes into the supercharger.
“They’ve been carefully balanced in how much of the boost is coming from either at each level of speed and power. Both also provide some redundancy; a failure of the supercharger triggers a spring-loaded door underneath to open, so the turbocharger’s air can bypass most of the supercharger straight into the plenum. If the turbo fails, the supercharger keeps running without issue – there’s just some loss of performance at altitude until the problem is fixed.”
The turbocharger has been designed in-house (with some undisclosed third-party help) for the higher air-throughputs, exact exhaust flows, pressure ratios and air volumes of the DHK180 versus those of the four-stroke engines that most COTS turbochargers have been designed for.
“The FAA’s certification requirements are rigorous for turbos. You have to do burst testing to demonstrate shrapnel containment [and] you have to do overspeed testing, along with other tests, so designing our own from scratch really was non-negotiable,” Webb notes.
Considerable CFD analysis contributed not only to the turbo- and supercharger, but also the exhaust channel, which features an ovular cross-section and a bend radius carefully controlled for aerodynamic efficiency, after CFD tests found only the outermost parts of the older, circular channel were being traversed by the exhaust gas.
Each cylinder has three exhaust ports feeding into a welded exhaust pipe, each pipe converging in a Y with that of the adjacent cylinder, and the two combined channels then converge in a block that bolts to the turbocharger at the back of the DHK180.
“Our exhaust system doesn’t use a wastegate,” Webb says. “They’re failure-prone, and moreover we don’t need one because our engine can’t be over-boosted – it’s a two-stroke. If too much forced air goes into the cylinder, the excess just rushes out of the open exhaust port before it can be compressed and combusted, and that actually helps by cooling the exhaust.”
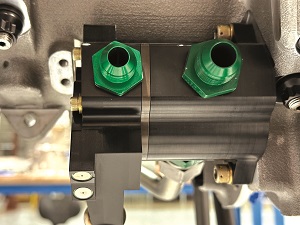
Compression and combustion
One may surmise from this that, unlike the aforementioned ATI two-stroke diesel, the DHK180 is not uniflow-scavenged (when poppet valves govern the exhaust ports to enable the compression of turbo- or supercharged air); nor does it use a rotary exhaust valve to trap the air, as in the REVolution two-stroke gasoline (issue 33, August/September 2020) from Strange Development, now Alpha-Otto Technologies.
The DHK180 is Schnuerle (or ‘loop’) scavenged and piston ported from the plenum (forgoing traditional crankcase compression). Copious amounts of CFD simulation and testing went into optimising the combustion chamber’s internal geometry to ensure sufficient swirl and tumble of intake air coming from each cylinder’s six intake ports, such that any unwanted losses via the three open exhaust ports are prevented (although some ‘losses’ of forced air helps provide cooling, and fuel injection is mechanically timed so some slight air loss does not constitute a parasitic loss in the engine’s power mapping).
“The CFD simulations were vital in optimising port height and placement, and the design of the steering ports. Two of the intake ports fire air in directions that ensure a good, vertical loop as part of the airflow. Without those, all the air would just shoot out of the exhaust,” Webb says.
“Uniflow-scavenged two-strokes can ensure 100% scavenging efficiency, but we still get 97% without needing poppet valves, tappets, rockers, pushrods and so on. It took a lot of computer modelling, cylinder iteration and bench testing of slightly different engines, but it means we’ve maximised the amount of burnt gas evacuated and fresh charge introduced before the pistons close over the exhaust ports.
“And that 3% ‘leftover’ exhaust in the cylinder is useful to an extent, because the radicalised particles become free nuclei in the cylinder for enabling faster light-off and combustion.”
While many details inside the combustion chamber are proprietary, DeltaHawk discloses that it uses a recumbent bowl design, typical of diesel combustion pockets, with a flat rim around it. As the piston completes its compression, the outermost air gets squeezed into the coalescing squish of fuel and air, giving a final rush of turbulence that optimises the mixture and helps it ignite.
“But, of course, diesel is controlled cetane. Jet fuel isn’t. It can be all over the map, so we did a lot of optimising on top of basic recumbent bowl technology, so our internal geometry and steel choices would work for mixing and igniting fuels of varying cetane levels, including very low cetane fuels,” Webb adds.
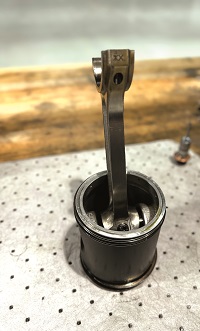
Liquid cooling
The DHK180 operates at roughly 200 F (93.33 C). To keep to that, a cooling pump on the front of the engine pumps water-glycol in two lines – one goes to each of the V4’s two cylinder banks – where it enters jackets running around the cylinders, and up through the cylinder heads to cool the areas heated most by combustion and exhaust. The coolant exits via the back of either bank into two pipes that combine into one for running to the integrator’s radiator.
“In addition to the cooling from the forced induction, and some oil cooling that we’ll get into, but we’ve generally tried to keep the cooling as simple as possible, albeit not as simple as all-air cooling, which wouldn’t have worked for several reasons,” Webb explains.
“Air-cooled engines require really extensive metallurgy and excessive clearances between the piston and rings and cylinders to work well, and it has to work at negative and hot temperatures. Outside airflow is always going to hit one face of the cylinder first. By the time that air flows around to the other side, it has been heated, sometimes with a delta of 2-3 C.
“Add to that the further flow distance of an inline engine or a boxer with four or more cylinders, and you’ll find that air-cooled engines experience extraordinary thermal management shocks, and need sloppy clearances to compensate for the metal expanding and contracting. It’s not unusual for high-performance air-cooled aviation engines to need cylinders replaced halfway to TBO.”
As an FAA-certified engine, DeltaHawk is awaiting the FAA’s official declaration of an exact TBO for the DHK180.
However, Webb notes: “Our design life based on observed wear rates is 3000 hours, possibly more, for three reasons: the liquid cooling keeping the piston and cylinder clearances stable; the lack of a valvetrain and all the tiny parts there that constantly get burnt or otherwise worn out; and all the remaining moving parts are thermally isolated things, like our supercharger, turbocharger and fuel pumps.”
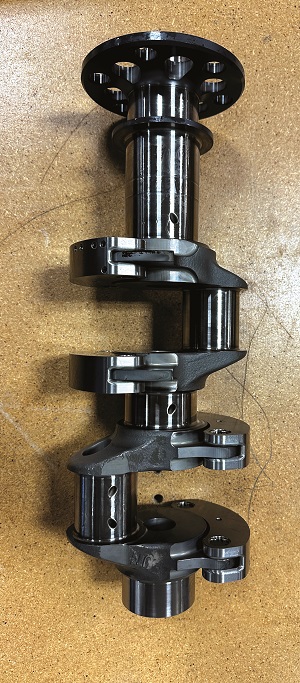
Lubrication
DeltaHawk has designed the DHK180 as a dry sump engine for two reasons. First, as a wet sump must be open and largely conformal with the crankcase, and hence must mount under the crankcase in a vee-engine, using a wet sump would have made the inverted-vee orientation impossible (the cylinders occupying the underside of the crankcase).
Second, designing a wet sump largely fixes the oil quantity (relative to the size of the oil pan), whereas the dry sump approach enables integrators to change the size of the oil tank, such as increasing or decreasing it for longer or shorter endurance missions by virtue of having an external oil tank instead of one integral to the engine.
Another advantage closely associated with that is maintenance: when the time comes to check or replace the sump, rather than having to unscrew an oil pan from the engine (which often means extracting the entire engine from the UAV), technicians need only remove the external dry sump. It also makes it easier to check or replace oil pumps and filters, as they are also mounted externally as a result of the dry sump approach.
Oil for the DHK180 is first drawn from the tank, through a filter, then through a cooler, and into the back of the engine. There, it runs into an oil gallery, which feeds the crank journal bearings, and by extension the gudgeon pin and piston rings via pressure-lubrication up the con rod.
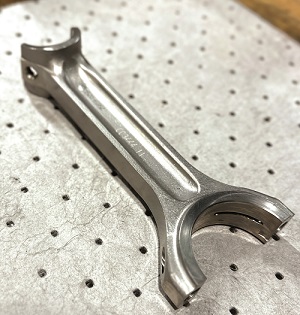
“We also use four oil squirters, one per cylinder, to jet a good amount of oil at the bottoms of the pistons to cool them. They are basically the kind you’ll find in any high-performance engine, and in most of our competitors in the four-stroke diesel world,” Webb adds.
“The second section of our oil pump functions as a very high-power scavenge pump: it sucks the oil out via the bedplate, whether that’s at the top because the end-user chose the inverted-vee or at the bottom of a regular vee integration. The inlet to the scavenge pump has a second filter – a wire-screen device to remove any particles from inside the engine before the oil can return to the tank.”
Both the oil tank and pump were designed in-house. The pump is a standard gear-drive device, running from a gear that sits on the engine’s accessory cover, and it is driven by the crank’s output shaft. The pump also features an integral spring-and-piston component for pressure regulation, so the piston moves in response to excess oil pressure, allowing some of the oil to bypass entry into the engine, relieving pressure that could otherwise overwhelm the seals.
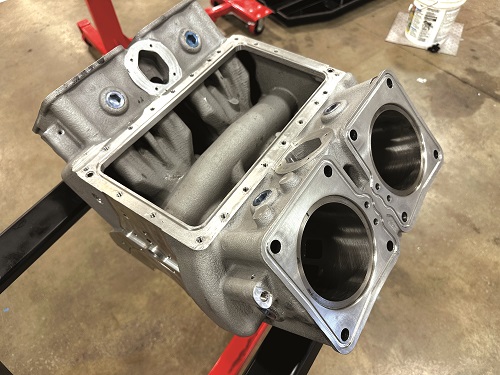
Inside the crankcase
A total of eight plain journal bearings require lubrication in the DHK180. Needle and ball bearings can have trouble lasting in compression-ignition engines, whereas plain bearings (assuming optimal design of components and sufficient oil viscosity) run with a hydrodynamic film separating crankshaft from bearing and preventing metal-to-metal contact.
The rear-most main bearing sits at the back of the engine near the high-pressure fuel pump, forward of which are two more bearings sitting in the third and fourth con-rod big ends. Ahead of those is a central main journal bearing and bulkhead, separating the rearward third and fourth con-rod crankcase half from the first and second con-rod crankcase half, followed by two more big-end bearings in each of those con rods.
Two more combined main and thrust bearings run in the front of the crankcase (which collectively handle gyroscopic and thrust loads from the propeller, be it a pusher or tractor prop), making for four main bearings and about 8 in of bearing length in total across the crankshaft.
The crankshaft is designed with two crankpin journals, each holding two con-rod big ends, with the surfaces polished smooth to prevent wear. Webb notes that having more journals would have added more weight, and thanks to the 90° vee two-stroke configuration, a smooth and manageable firing order can be achieved with two con rods and hence cylinders per journal.
Moving up the con rods, one does not find the usual free-floating gudgeon pins (held by three bearing surfaces across the con-rod small end and the two piston bosses) that are typical in four-strokes. The two-stroke and highly loaded nature of the DHK180 gudgeon pin has motivated DeltaHawk to instead opt for a trunnion-style gudgeon pin.
“That means our con-rod small end is U-shaped instead of circular, and it bolts to the wrist pin [US English for gudgeon pin],” Webb explains. “There’s a number of reasons why we do that. Number one, it forces articulation of the wrist pin; it’s rolling back and forth with the motion of the con rod. Second, we don’t have an exhaust stroke; all strokes into the cylinder are compression strokes, and that means we can have a full-length wrist pin-to-piston bearing surface.
“A highly loaded two-stroke will impart a lot of force on the wrist pin, and that needs to distribute over the surfaces it is in contact with. The traditional piston-to-pin interface concentrates loading in very tight sections of the piston body and circlips, whereas the metal of the bottom of our piston goes across the entire wrist pin. To ensure enough oil for all these components, we cut some very precise grooves into the piston-bearing surface, such that squirted oil runs full-length across the wrist pin as it articulates.”
This approach was first proposed for the DHK180 by Doug Doers, with subsequent engineers and iterations optimising the bearing surface and adding the piston’s lubrication grooves. The company also cites the Detroit Diesel Series 71 and Electro-Motive Diesel 645 engines as precedents for this type of gudgeon pin.
The pistons additionally feature two compression rings (an upper ring for primary sealing and a lower ring serving as a backup), which sit at ringlands in the steel piston crown; their shape is typical for compression-ignition piston rings from a proprietary material.
Two more rings sit at the bottom of each piston. The lowest is an oil-control ring, while the higher is called a ‘scraper ring’ in-house, which serves as an air seal and for added oil control.
“But the biggest reason for those extra rings is because of two-stroke ports: your oil-control ring can’t cross your ports, not without exposing your crankcase,” Webb says.
“Some four-stroke diesels get around that by using very short pistons, but we can’t do that: our pistons need to be around 4 in long. So, the compression rings do cross the ports – the piston crown has to drop below the ports to allow intake and exhaust – but the extra rings are always below the ports and provide critical extra oil control.”
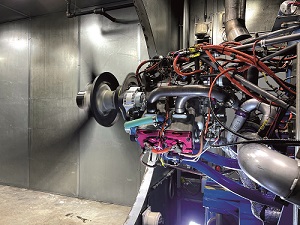
The way ahead
DeltaHawk emphasises that the DHK180 is an introductory engine, intended as a product but also as a proving ground for its technical IP. New models with substantially higher power and lower weight will be introduced in the coming months using the same V-4 architecture, followed by models with more cylinders and higher power in the near future.
“We have already tested 200 HP and 235 HP versions of the engine, with the exact same weight and form factor. All it took was some turbo changes for increased MAF, with no changes to the engine block,” Webb says.
“We’ve had requests from several UAV manufacturers for higher-altitude performance, particularly from defence-oriented folks wanting 20,000-30,000 ft, and we can do all that with turbocharger changes on the same block.”
Also being developed is a V6 engine that will produce over 300 HP, without being dissimilar in maximum volume to the DHK180 (some ancillaries will be moved around to compensate for a longer block).
The company has further irons in the fire for future development, with one of the larger categories for these being optimisations for cleaner power outputs. While already a relatively clean design, owing to the absence of oil in its fuels, the DHK180 is being trialled with bigger alternators for hybrid applications.
DeltaHawk also expresses interest in burning not only sustainable aviation fuels, but particularly hydrogen for zero-carbon horsepower, pending the right investor and customer to ensure it is developed with an end in mind.
This precise sentiment was expressed to us previously by other companies privately (in UAVs and other applications), possibly indicating a large shift towards clean fuels in the next generation of UAVs and their powertrains.
Anatomy
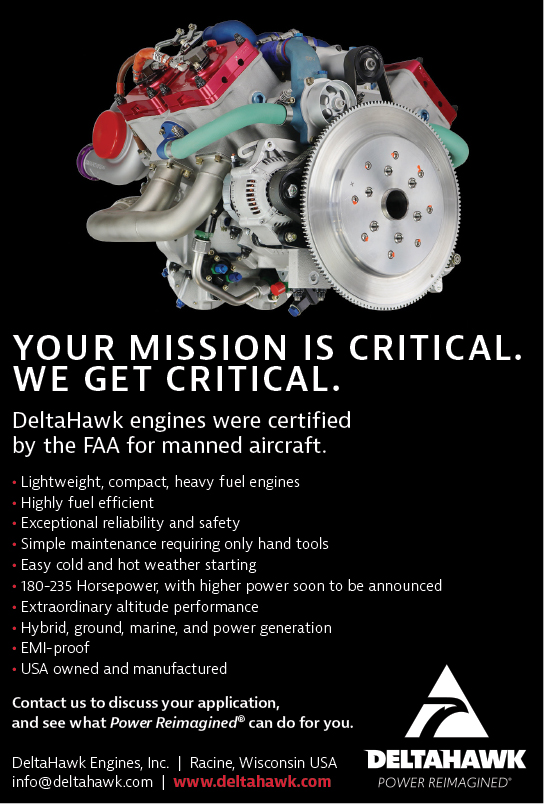
The DHK180’s engine block is cast as upper and lower halves from a variation of A356 aluminium alloy, with proprietary additives for high strength and durability for the engine’s high torque and operating pressures, with high-strength studs bonding the halves together.
The plenum is integral to the cast block (and the supercharger mounts under the plenum, assuming an inverted-vee installation), as are the cylinders, each of those having a replaceable steel liner inserted, which runs the length of the cylinder.
The piston crown is also steel, as is the fireplate that sits inside the cylinder head (hence all combustion-exposed surfaces are steel). The liners are machine-cut with the required lengths and port apertures, and bonded to the block via an interference fit, during which the block is heated and then cools around the liners.
The cylinder heads are machined from high-strength aluminium billet, anodised and then bolted to the cylinder atop the fireplates to bond them in place, with seals between the fireplate and liner (each head also features a coolant inlet and outlet, which line up with jackets in the cylinder for water-glycol circulation).
The piston bodies are cut from aluminium billet for weight saving (as the reciprocating mass of a totally steel piston would have increased wear and parasitic losses for the engine) and the gudgeon pin is of machined steel. While the steel piston crowns were previously threaded directly on to the aluminium piston bodies, they are now screwed together with custom bolts.
The connecting rods are forged from titanium, with a cap then bolted on to each one at the big end, before the U-shaped small end is bolted to the wristpin. The choice of titanium came down to increasing strength and reducing weight compared with other options, particularly in the hunt to remove mass from reciprocating elements, and thereby reduce counterweighting and balancing mass needed at the crankshaft.
Most of the crankshaft is forged and subsequently machined to close tolerances as one piece from nickel-chromium-molybdenum steel. The shaft’s four counterweights feature pendulum dampers designed to tune out the engine’s vibration and prevent undesirable frequencies from reaching the propeller; each one moves on pins bonding it to the counterweight, thereby smoothing out the crankshaft’s motion amid torque pulses from the firing order.
The camshaft driving the fuel pumps is of machined steel. The turbocharger’s turbine housing is of cast iron, its compressor housing is cut from aluminium, and its compressor impeller is machined 2000-series billet aluminium, while the turbine impeller is cast Inconel. The components are bolted together, with a full-length O-ring for sealing, and then bolted to the plenum.
Specifications
- DHK180
- Two stroke
- Compression ignition
- Forced induction (turbo- and supercharged, or twin-charged)
- Direct injection
- Liquid cooled
- Mechanically governed
- Aluminium block
- Steel liners
- Displacement: 3.3 L
- Bore x stroke: 10.2 x 10.2 cm
- Dimensions: 84 x 61 x 56 cm
- Dry weight (including ancillaries): 162 kg
- Maximum power: 180 HP (134.2 kW)
- Maximum torque: 492 Nm at 2600 rpm
- Maximum speed: 2700 rpm
- Cruising SFC: 7.3 gal/hr (27.6 L/hr) at 135 HP
- Maximum SFC: 10.8 gal/hr (40.9 L/hr) at 180 HP
- Fuels: Jet A and Jet A-1 (certified); JP-8, D1, D2 and F-24 (not yet certified)
- TBO: est. 3000 hours, possibly longer (not yet officially verified)
Some key suppliers
- Starter: Hartzell Engine Technologies
- Alternator: Plane-Power
- Oil filter: Champion Aerospace
- Coolant: Maxima
- Oil: Philips
UPCOMING EVENTS
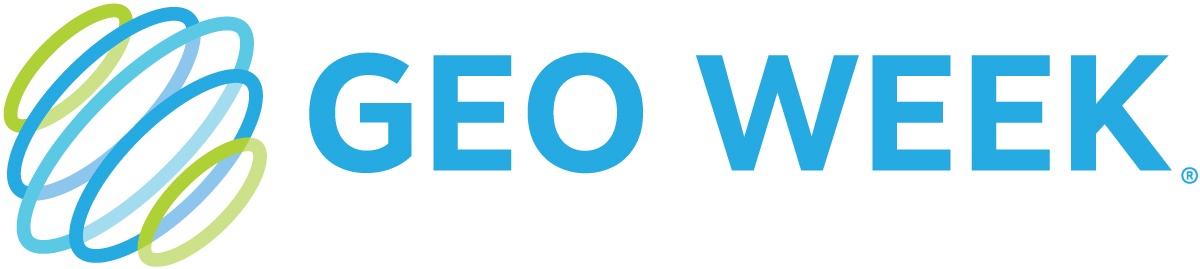
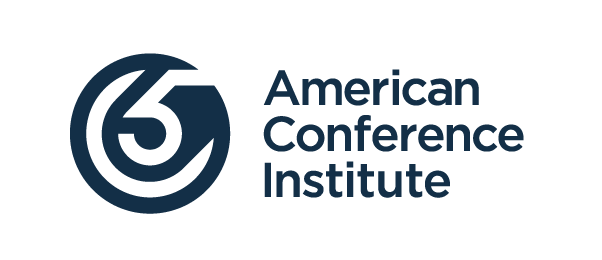
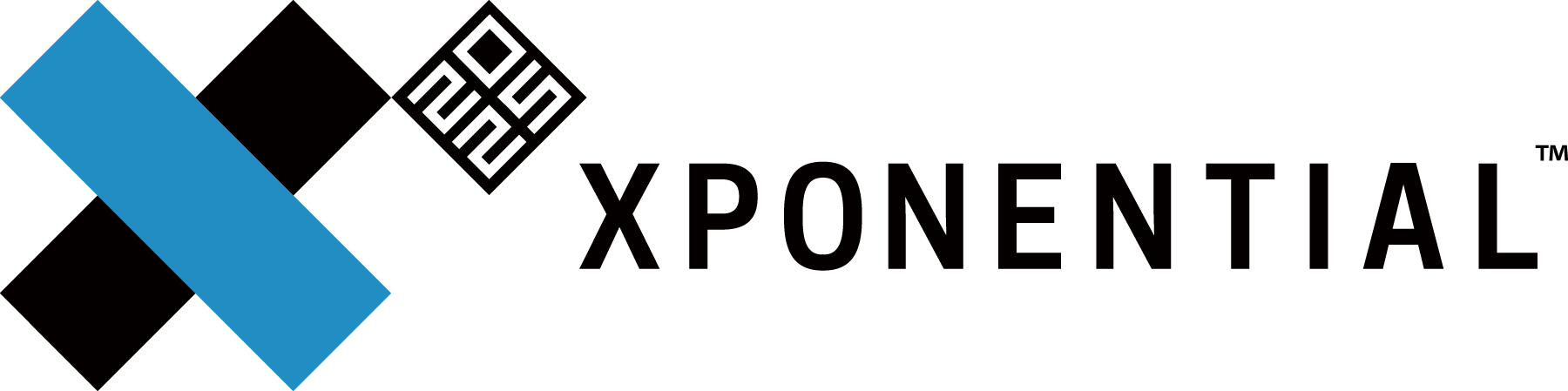
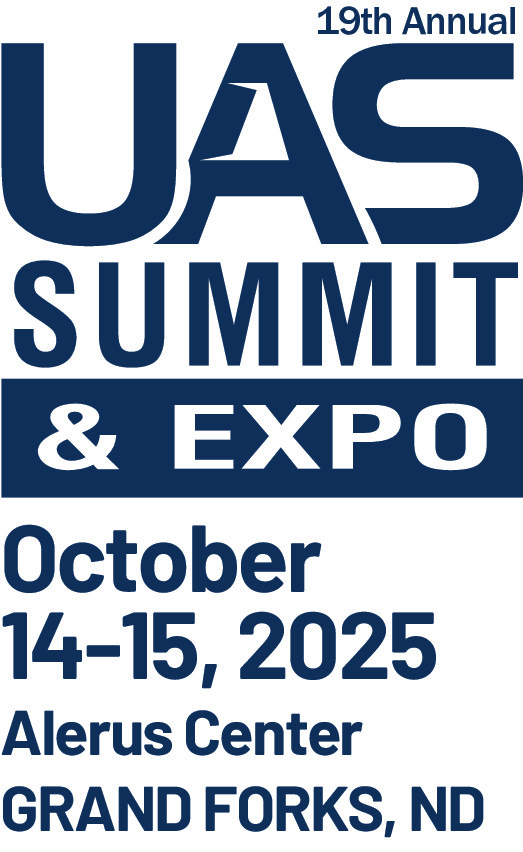
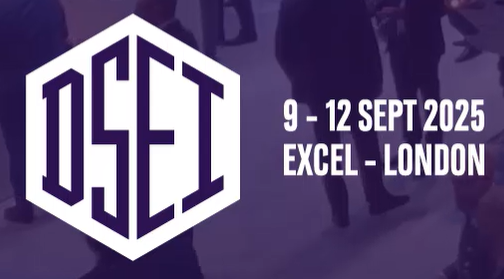
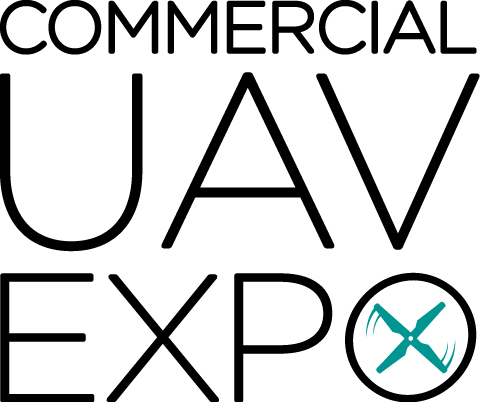
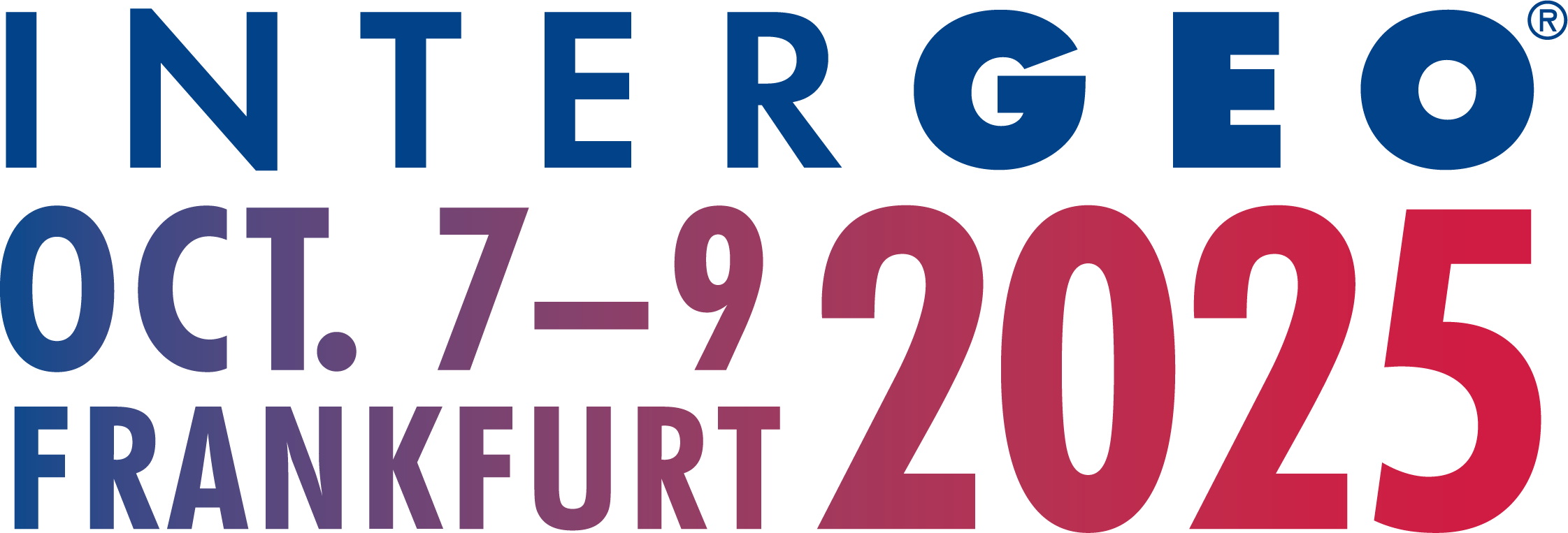
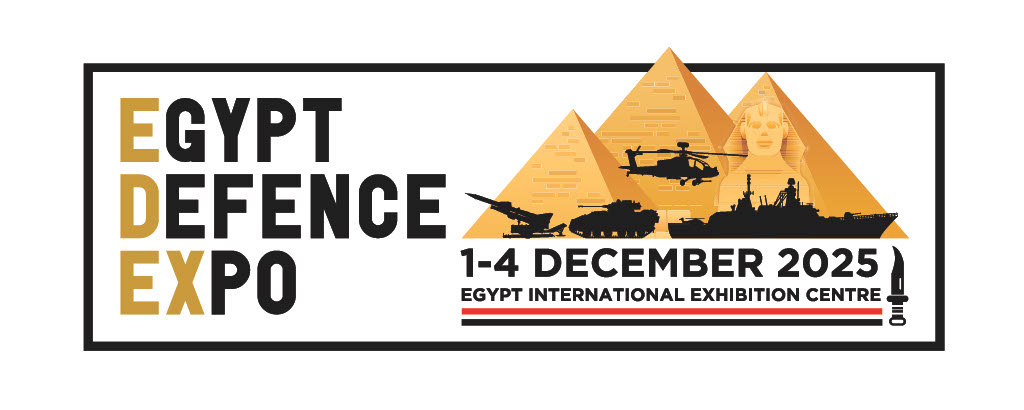
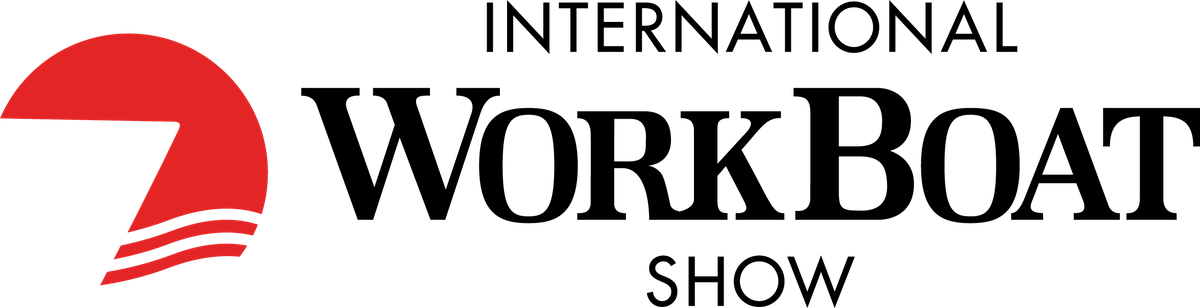
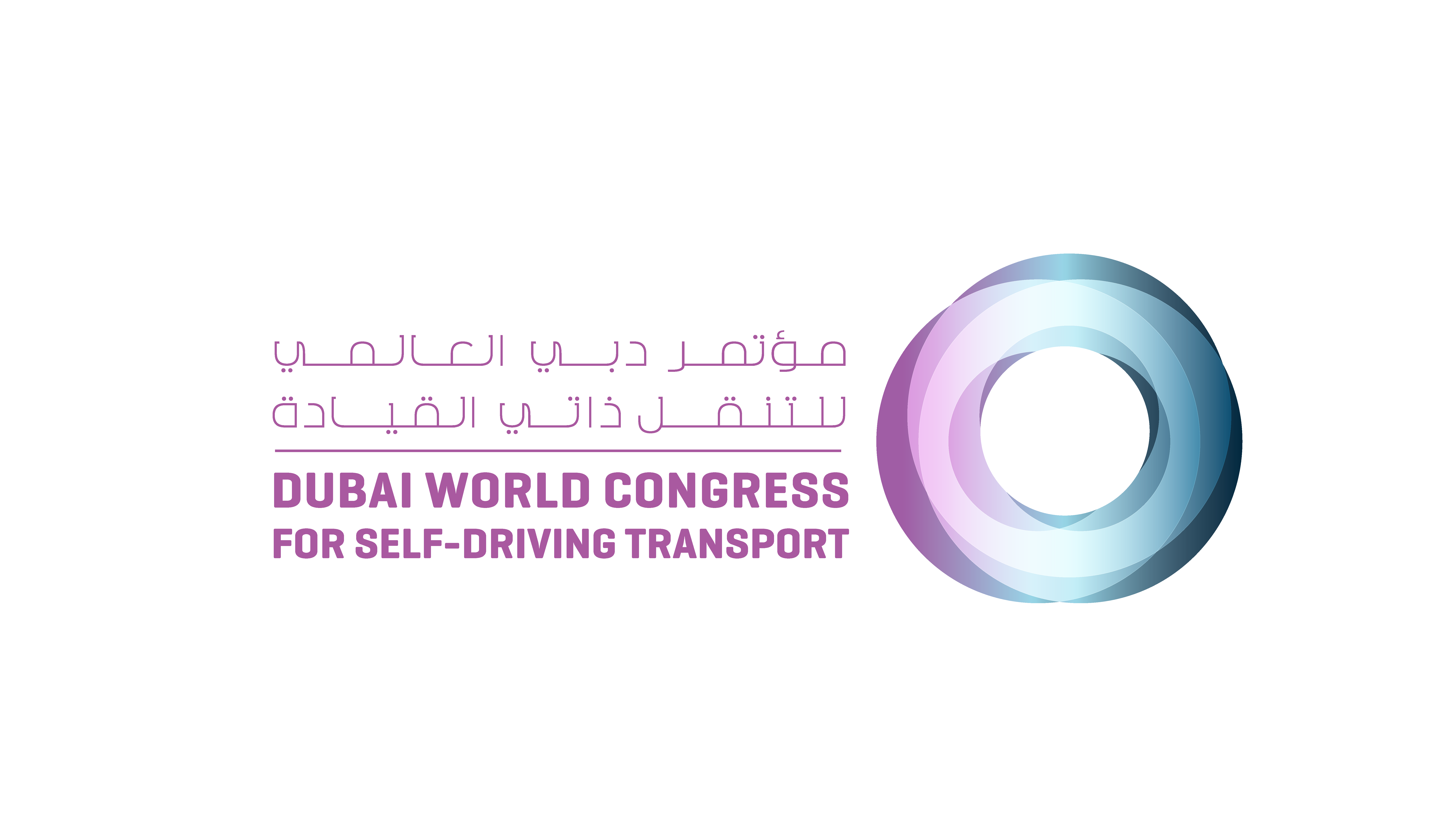
