Clogworks Dark Matter
A view to the future
Peter Donaldson finds out how this all-weather BVLOS hexacopter was developed, in anticipation of future applications…
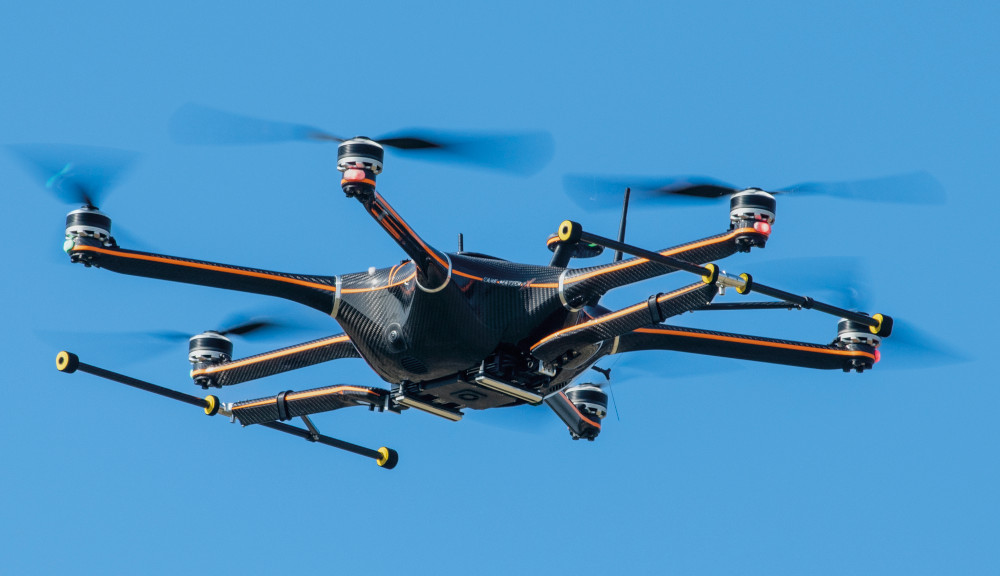
(Images courtesy of Clogworks)
While the multi-copter is almost the default configuration for VTOL UAVs, those designed for professional use and BVLOS operations in all weathers are something of a breed apart, particularly when it comes to safety and reliability. Known for the Dark Matter hexacopter, Clogworks recently launched its extensively updated hX Gen2 variant, which incorporates enhancements in both these areas.
“It was clear even when the company was born in 2014 that all-weather BVLOS flights would be a crucial element for future applications, and where the drone industry would be heading at some stage,” says Clogworks’ founder and CEO Peter Opdam.
“That meant we needed traceability on raw materials, high-quality components and rigorous build and testing procedures to pass airworthiness tests,” he says. “The weather resistance was also critical, as when you fly for a long distance and duration you can encounter any type of weather – especially in the UK.”
In addition to the usual need for low weight, rigidity and aerodynamic efficiency to maximise performance and endurance from the available power, the original Dark Matter airframe also had to protect sensitive components including batteries and electronics from the elements. That led to the design of a ‘sculpted’ carbon fibre-reinforced polymer (CFRP) shell.
The low-drag shell is a key element in the West Yorkshire, UK, company’s drive for aerodynamic efficiency, as in general that was – and remains – key to range and endurance, Opdam argues.
“When the original hX first flew in 2016 it could fly for 48 minutes, here on the moors in real conditions. Most similar sized drones could not match that level of performance, and barely managed half that,” he says.
“When you get the most out of your standard system in terms of efficiency, it allows you to get excellent performance with added extras. Most of our customers want tailored solutions with some specific requirements of extra hardware, but still want an optimum range, endurance, speed and the ability to operate in adverse environments.
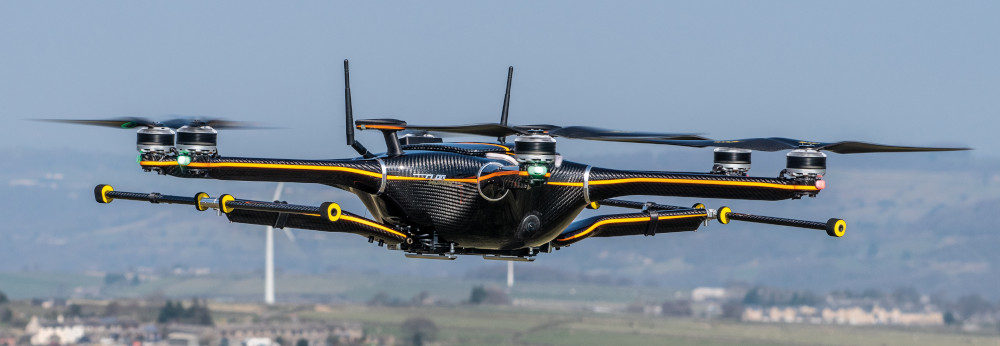
”Opdam says that, with the exception of the motors, propellers and some electronic components, the entire aircraft is designed, manufactured, assembled and tested in-house with the company’s own tooling. “The early-stage investment in machinery and equipment allowed us to develop the aircraft, and it gives us total control over how every component is made,” he explains.
That, he adds, improves quality control while enabling r&d and the tailoring of products to individual customer requirements.
Opdam describes the Dark MatterGen2 as a natural evolution resulting from customer feedback and embodying many refinements, particularly in terms of flight performance, endurance and payload capacity. He says the CFRP airframe is 30% lighter and stronger than its predecessor thanks to a change in manufacturing techniques, while operation has been simplified.
The Gen2 features the Pixhawk Cube autopilot with more safety features and support for several additional sensors, he notes, emphasising that the associated Arducopter firmware and software are not only “excellent” but also under constant development and testing by a worldwide community of thousands of users. The autopilot also has the option for end-users to add their own features.
The Pixhawk Cube also has a triple-redundant, temperature-stabilised IMU,and supports many different sensors, forms of communication and other hardware, Opdam notes, supporting further specialist development.
The original Dark Matter hX was launched at the end of 2016, followed by the smaller qD quadcopter variant in2019. These are in service with various organisations around the world, such as defence contractors, police forces, surveyors, package delivery companies and humanitarian organisations.
“A few customers are now asking us to convert their Gen1 vehicles to Gen2standard, which is something we are happily doing – for a fee – as the Dark Matter was conceived to be modular and upgradable.
”Clogworks expects the Gen2 to broaden its customer base. “We already had survey customers coming to us for the Gen2 because of its compatibility with various GCS applications, including Q GroundControl, Mission Planner and UGCS, which the vast majority of them use, and for the extra safety and redundancy.”
Design for reliability
The Dark Matter Gen2 features a number of duplicated systems, indicating that redundancy is a key element of Clogworks’ approach to safety and reliability. “The manned aviation industry is all about safety and trying to remove any single points of failure, and we can and should learn a lot from that,” Opdam says.
“From day one we have taken safety very seriously,” he emphasises. “Some applications are near or in densely populated areas, so any failures have to be prevented or mitigated to ensure that operational risks are as low as reasonably possible. Also, we believe that as drones are used more, the safety requirements will become more stringent.
”Customers are also needing to carry expensive payloads such as large Lidars more often, so it is increasingly important for them to have confidence in the aircraft’s ability to perform safely.
The original test programme focused on airframe structure, flight performance and efficiency, and the Gen2 programme built on this. “For example, we improved overall airframe rigidity, temperature resistance and component strength, to name a few,” Opdam explains. “Testing includes destructive and non-destructive testing of carbon parts, endurance testing, dyno testing, in-house ingress testing and more.
”The Dark Matter Gen2 family has the option for dual batteries, along with triple temperature-controlled IMUs, dual GPS masts, six electric motors in the case of the hX model, and the option of redundancy in the control and payload data links.
However, this approach can only go so far in maximising the MTBF of any system. “The MTBF also depends on the operating conditions, so it is important for customers to keep to the maintenance and servicing regime we suggest”, Opdam explains.
Structure and materials
A weight saving of more than 30%over the Gen1 has been accomplishedwith a range of measures, primarilythrough the way the CFRP fuselage isproduced, Opdam says. However, othercontributions have come from optimisingparts machined from aircraft-gradealuminium, re-engineering 3D-printedfittings and improved integration of theUAV’s electronics.
All Dark Matter UAVs are of monocoque construction, meaning that the outer skin forms the load-bearing structure that handles all the static and dynamic loads on the aircraft. Opdam points out that producing all the CFRP parts in-house gives the company’s engineers full control over where and how to reinforce the structure.
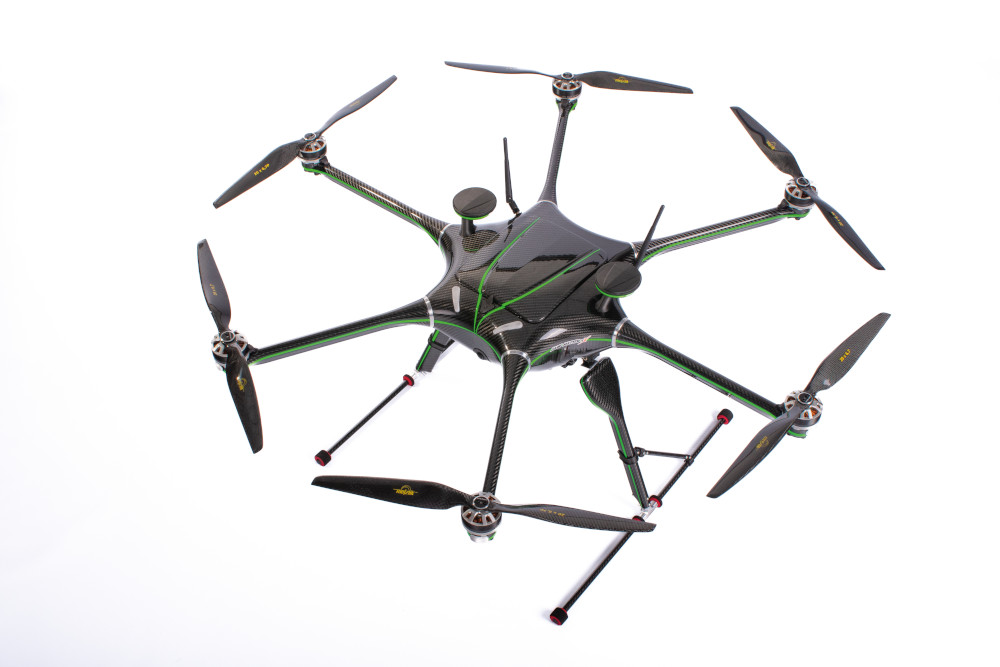
The composite material that Clogworks uses is a certified 3K prepreg carbon that offers the flexibility in layup needed to form the airframe’s complex shapes, and offers an excellent surface finish when cured, he explains. “The raw material has a very low VOC [volatile organic compounds] content with no added solvents during manufacture, and cures at a relatively low temperature. The finished parts offer great mechanical properties,” he says.
Where precision metal fittings are required, such as where the arms that support the motors and propellers attach to the core of the fuselage, they are CNC-machined from aircraft-grade aluminium alloy.
The arms themselves are an example of the UAV’s modularity, as they can be detached quickly in case they need to be replaced, and they are interchangeable between the six-motor and four-motor models. “It is important that they are standalone, as you can replace an arm like-for-like in the field if needed, or quickly replace arms when motor maintenance is due and downtime is notan option,” Opdam says.
Options for retractable or fixed landing gear also fits Clogworks’ modularity philosophy. Retractable gear, he explains, allows for an unobstructed 360ºhorizontal view from a payload camera.
“For the Gen2 we have a better and more robust retractable solution,” he says. “The new design features moulded T-shaped CFRP legs under the main shell that pivot upwards on take-off, with retraction and extension controlled by servo motors. When fully retracted, the gear legs lie roughly parallel to the UAV’s arms.
“Other applications, such as package delivery, might not need retractable gear, but do require more ground clearance and greater strength to cope with landing at higher weights.
”Opdam explains that the hexacopter configuration was chosen for the Dark Matter hX because it provides six points of thrust and an overall footprint that is optimal in terms of size, efficiency and power-to-weight ratio, while also offering arm and motor redundancy.
“The size of the core is important for best placement of antennas, GPS masts and any extra systems that may be required,” he says.
While Clogworks keeps an eye on the market for high-quality propulsion system components on offer from other manufacturers, it uses motors and electronic speed controllers from KDE Direct. He notes that KDE quotes an MTBF of many hundreds of hours for the motors, and says they need minimal servicing.
He adds that there is a choice of set-ups for the Dark Matter hX drivetrain, one optimised for maximum efficiency and the other optimised for power to provide a heavy-lift capability with payloads of up to 6 kg.
“Even when lifting its maximum payload, the system still operates well within an acceptable performance window in terms of current draw and temperature, so it can be operated all day, every day,” Opdam says.
The Gen2 Dark Matter can use either lithium-polymer (LiPo) or solid-state flight batteries in forms between 6S and 12S,the figures indicating the number of cells connected in series that form the battery. A typical battery for free flight is either a 22,000 mAh or 30,000 mAh standard LiPo or solid state, and both the DarkMatter hX and qD core can fit two of them, he explains.
All these batteries are hot-swappable so that the UAV can be left powered up while the swap takes place, he adds. “Most customers have enough flight time to complete their mission using one set of batteries and swap them for one or two new ones if needed while briefly powering down the system,” he says.
A question of control
Having followed the evolution of the Ardupilot-Cube combination over many years, Opdam decided it was the logical choice for the Dark Matter vehicles.
Ardupilot is an open source UAV autopilot software suite that comes in ‘Plane’, ‘Copter’, ‘Rover’, ‘Antenna Tracker’ and ‘Sub’ variants. Naturally, the Copter version is aimed at rotary-wing craft, including conventional helicopters and multi-copters.
The system includes an autopilot computer loaded with Copter firmware, mission planning software with point-and-click set-up and configuration, and aground control interface, along with other essentials such as data radios for two-way telemetry and control.
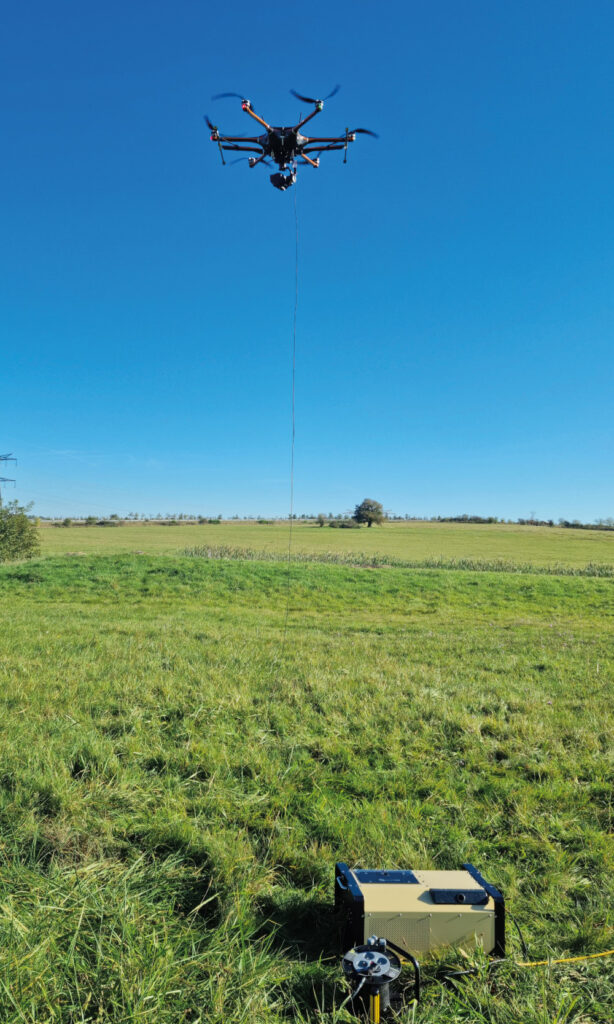
Cube is the autopilot hardware, an evolution of the Pixhawk designed for commercial systems and UAV manufacturers who want to integrate an open source autopilot into their systems.
It is the Cube that contains the three sets of inertial sensors referred to above for extra redundancy, two of which are isolated mechanically from vibration to improve the system’s state estimation performance. Resistance heaters are used to maintain the IMUs at the iroptimum temperature.
Opdam notes that the system’s combination of hardware and firmware provides a lot of scope for configuration and tuning. It also allows for the integration of many sensors and payloads without relying on a third party, allowing the company to offer a wide variety of solutions.
“From a software perspective, the Cube firmware is constantly developed and tested by many experienced developers as well as ourselves, before a new stable release is signed off and we use it for our customers’ systems,” he adds. “From a hardware perspective, the semiconductors and sensors are excellent, and there is plenty of scope for communication and expansion.
“You can still add your bit of knowledge to it, but most of the work is done in a very timely manner, at no cost to the end-user, and is being thoroughly tested so that you or your customers do not feel like beta testers but are using a proven, reliable product.”
The system comes with some autonomy features as standard, including actions to be followed after a failsafe is triggered, such as a low battery warning or a temporary loss off comms owing to external factors. Other autonomy feature scan be configured when additional sensors have been installed.
“The autopilot also offers users the option to write their own scripts and add their own custom autonomous features,” he notes. The autopilot also supports different manually selected control modes, including loiter, altitude hold, stabilised, return to launch point, GPS waypoint navigation(with automatic take-off and landing) and ‘fly here and follow me’ modes.
Like all Clogworks’ UAVs, the hXGen2 is fitted with a pilot’s point of view camera, so PoV piloting via a compatible VR headset is feasible.
Navigation sources
A multi-constellation GNSS system is standard, combining GPS L1C/A,GLONASS L10F and Beidou B1receivers. The navigation system is also ready for RTK enhancement to reduce positioning errors to 1 or 2 cm in the best installations.
RTK exploits the fundamental properties of a GNSS signal, particularly its phase, in addition to the information encoded in it to calculate corrections that it transmits to mobile receivers within range. Inevitably, the base station is extra.
Opdam stresses that the quality of the hardware installation dictates how reliably RTK will work and the accuracy that can be achieved in any UAV.
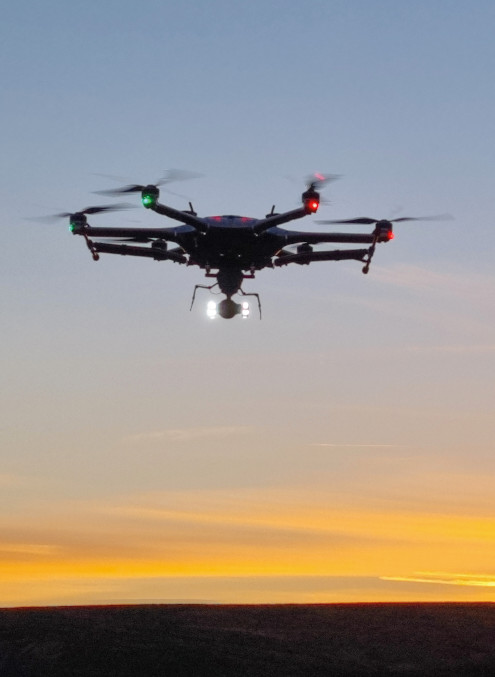
As yet, the vehicles have no GNSS-independent navigation capability, but Clogworks is cooperating with companies who are developing software to control the UAVs’ flightpath without recourse to satellite signals.
Among the safety-of-navigation enhancements made to the Gen2machines is a lighting system to improve their visibility to other air space users. The system includes two extra status lights in the two GPS masts on the top of the fuselage and a conspicuous flashing green LED light at the back of the aircraft as standard, plus a red headlight on top of the 3 W navigation lights placed at the end of each arm, while all the LED lenses on the Gen2 aircraft have been tuned for maximum visibility.
“We can also offer additional lighting options where required for specific applications, such as a remote controlled high-visibility beacon with multiple modes that can be clearly seen even at distances of more than 500 m,” Opdam says.
Being seen electronically by other aircraft and air traffic management systems is also crucial, and to that end the company has integrated the PingRX and Ping 1090i ADS-B systems from Uavionix. These transmit the UAV’s identity along with its position derived from its navigation system to compatible receivers in other aircraft and on the ground.
Optimum placement of the antennas is one of the most important aspects of the hardware integration, Opdam notes, but there can also be regulatory issues. “Depending on the ADS-B system, you might have to ask for an Ofcom licence in the UK.”
Clogworks has also integrated sense &avoid systems into Dark Matter vehicles.
Comms and control
In addition to the standard options for comms bearers that Clogworks installs in its systems, the company also integrates customer-specific links that offer AES128/256 encryption.
It offers three ground control system options as well – Ardupilot Mission Planner, Q GroundControl and UgCS. Outlining the thinking behind this, Opdam says some customers are used to a specific GCS, sometimes for historical reasons and sometimes because of their specific application, so Clogworks is happy to accommodate that need.
“They all do pretty much the same thing, but the main difference is how the interface is displayed and laid out,” he notes. “UgCS has perhaps a few extra features for the automated mission planning.
”One major advantage from a UAV developer’s perspective of using these systems is that it keeps the effort involved in getting the vehicle to work with them, through writing code for example, to a minimum, as all three are fully Pixhawk-compatible, he adds.
Payload support
The company has integrated a variety of payloads so far, including DSLR, EOand EO/IR cameras, along with Lidars, searchlights, loudspeakers, telecoms transmitters and delivery boxes.
The hX has demonstrated the ability to carry three different payloads at once, the only restrictions being the maximum gross weight of the craft and the physical footprint of the combination of payloads.
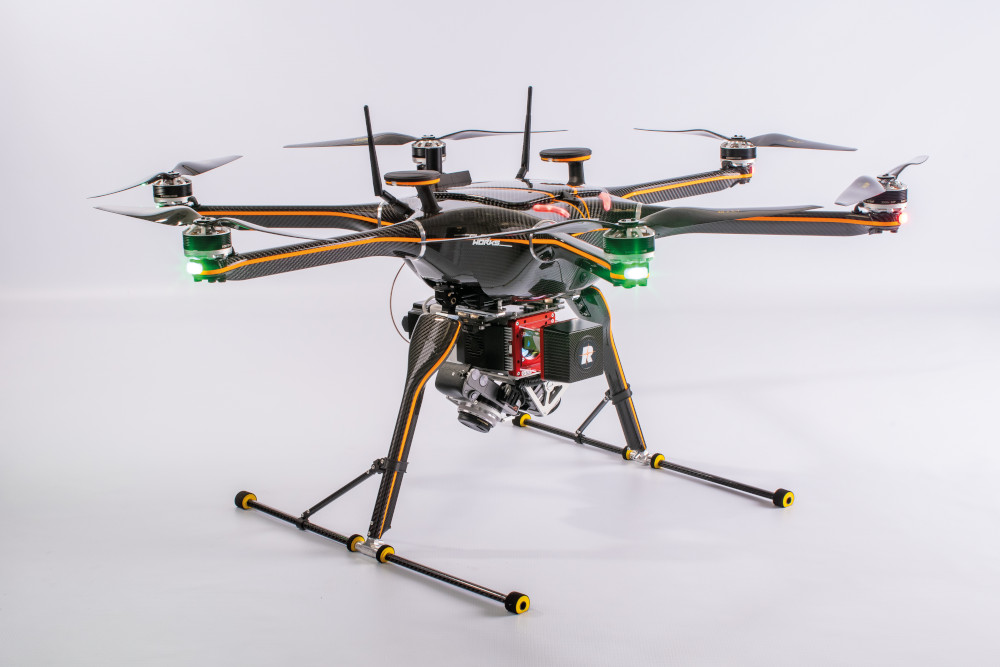
All payloads are attached to the vehicle via a rail system designed in-house that allows for quick attachment and release of each device, and enables any payload within the weight and volume limits to be carried.
Generally, payloads are powered by the vehicle. “Most of the time it is more efficient to draw power from the main power battery, otherwise you can end up carrying unnecessary weight,” Opdam explains. “Payloads tend to use very little power compared to the overall system during flight.”
Maintenance, diagnostics and repair
From the operator’s perspective, routine maintenance boils down to close visual inspection of all aspects of the aircraft, which is detailed in the manual, and Clogworks has developed its own techniques to locate any faults quickly.
“We have become very familiar with all the parts and components, so it is pretty easy for an engineer to track down an issue,” Opdam says. “We also analyse recorded flight logs to help verify the health of a system and, if necessary, take corrective action before an actual fault occurs.
”He emphasises that each part has been designed to be easy to disassemble fully for maintenance inClogworks’ facilities. “When we get anaircraft back here, we use special toolsto access the inside of the arms andremove the internal panels in the core toaccess most of the electronics,” he says.
“If required, we can completely strip an aircraft and then rebuild it with new parts and/or the next generation of electronics. That allows us to upgrade an original Dark Matter system to Gen2 specification, for example, protecting the customer’s investment.”
In terms of development, Opdam says the Gen2 hX is where they want it to before the moment, although the company is constantly looking to make marginal gains and refinements, and will continue to work on options and add-ons for theGen2 systems. Further enhancements are likely in response to customer requests and changing legislation, and these will be embodied in future releases of the Gen2 platform.
Specifications
Maximum take-off weight: 18 kg
Typical empty weight: 4.7 kg (standard motor), 6 kg (larger motors)
Maximum payload: 6 kg
Overall dimensions: 1.565 x 1.432 x 0.650 m with props extended
Propeller diameter: 20 in, non-folding
Nominal battery voltage: 6S, 22.2 V
Flight endurance: more than 55 minutes
Maximum horizontal speed: 20 m/s
Maximum vertical speed:6 m/s
Wind tolerance: 12 m/s
Operating temperature: -20 C to +45 C
Some key suppliers
ADS-B receiver: Uavionix
Autopilot software: Ardupilot
Autopilot hardware: CubePilot
Gimbals: Gremsy
Payloads: Shenzhen Viewpro
Payloads: Workswell
Lidars: Riegl
Motors: KDE Direct
Electronic speed controllers: KDE Direct
Propellers: Mejzlik
UPCOMING EVENTS
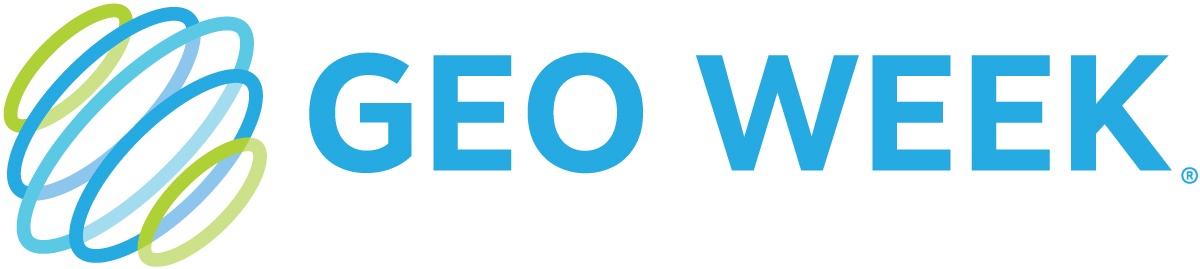
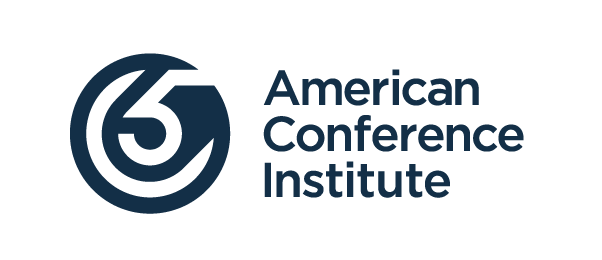
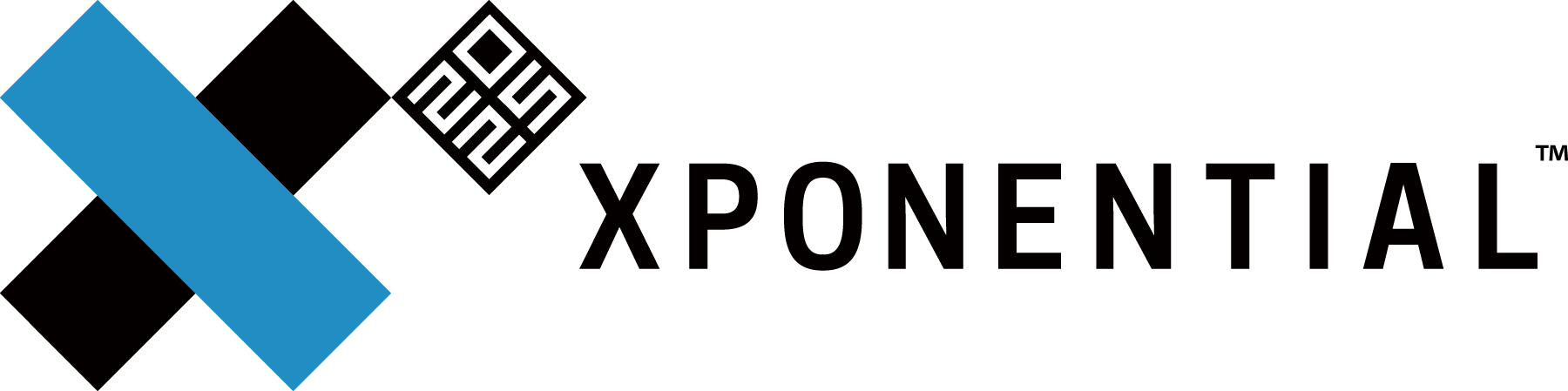
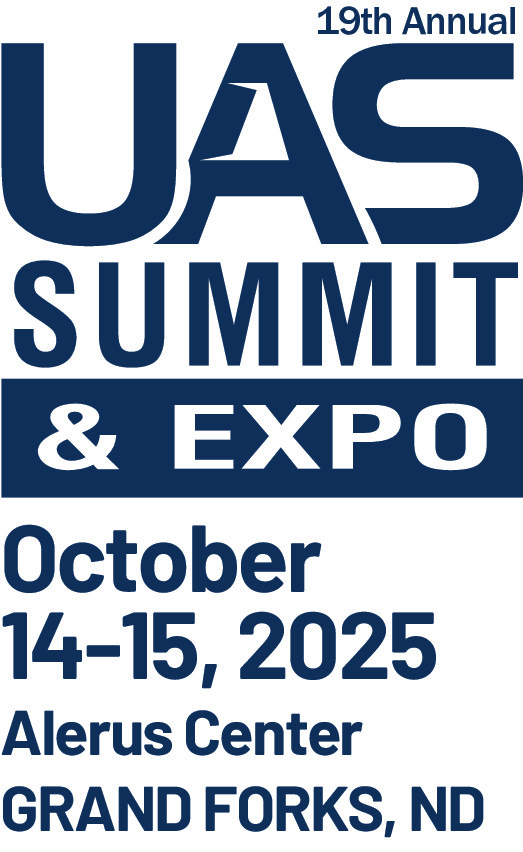
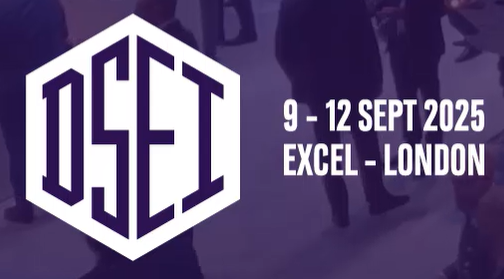
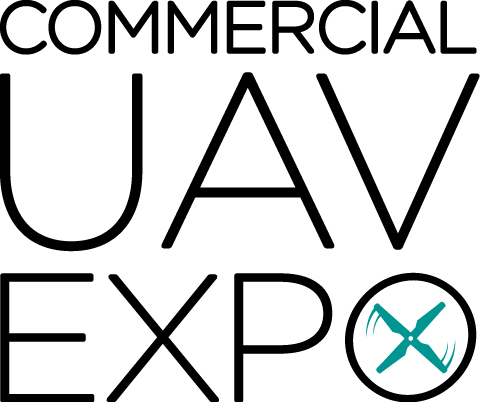
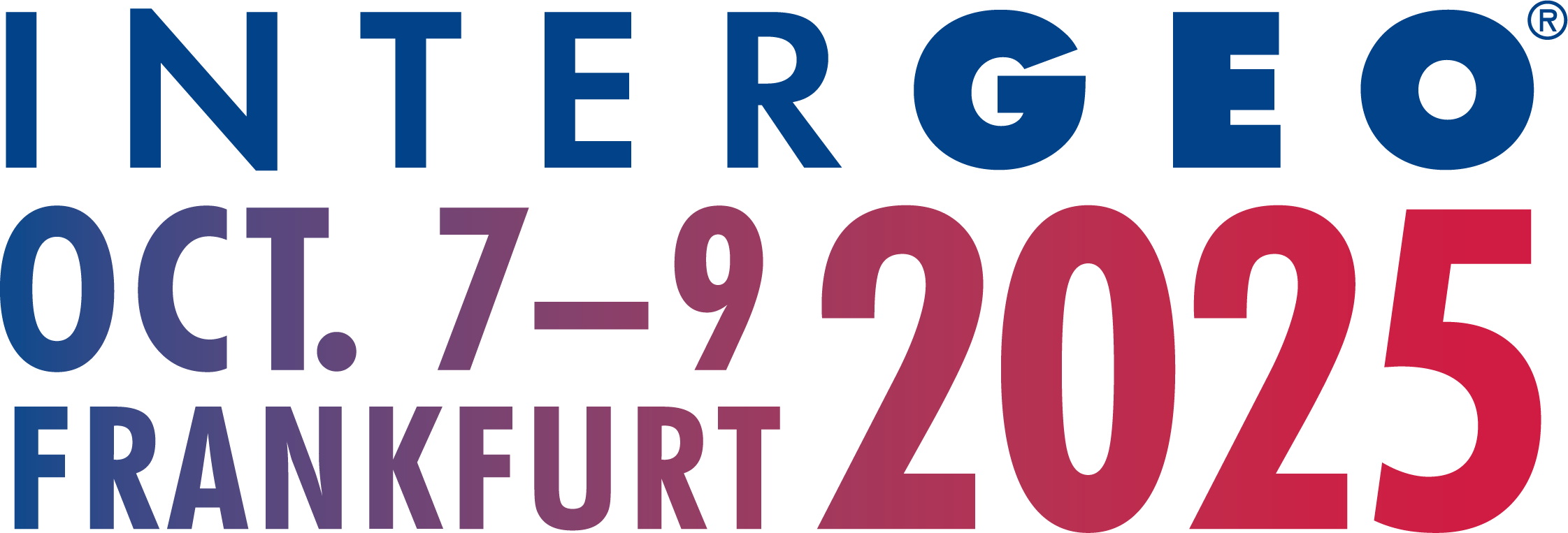
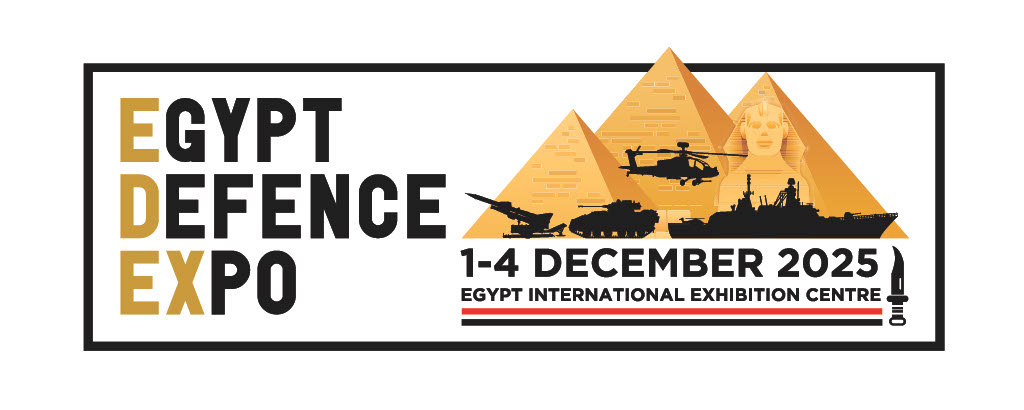
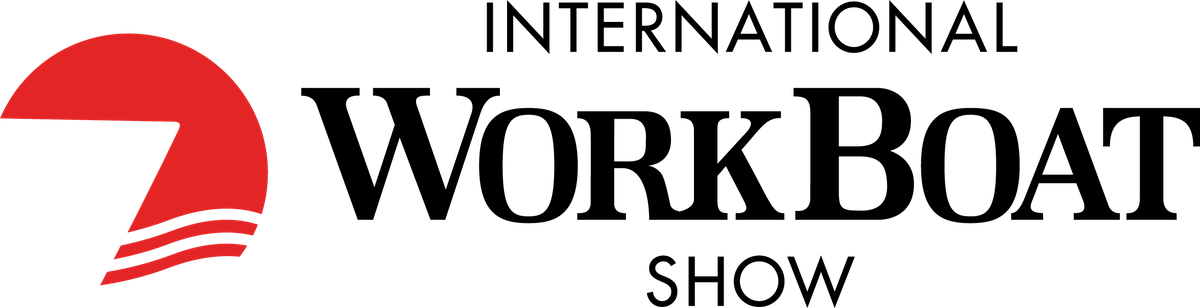
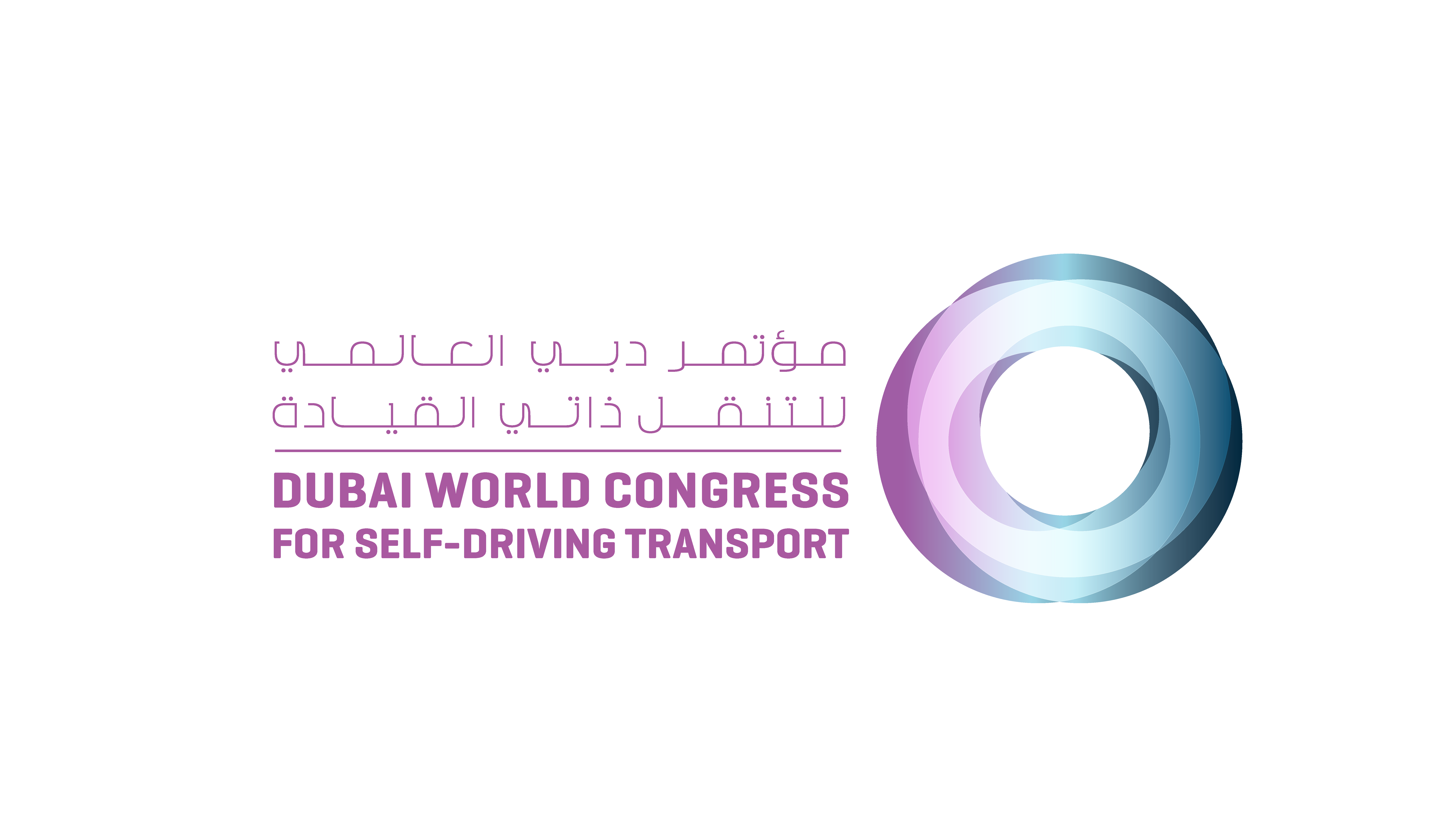

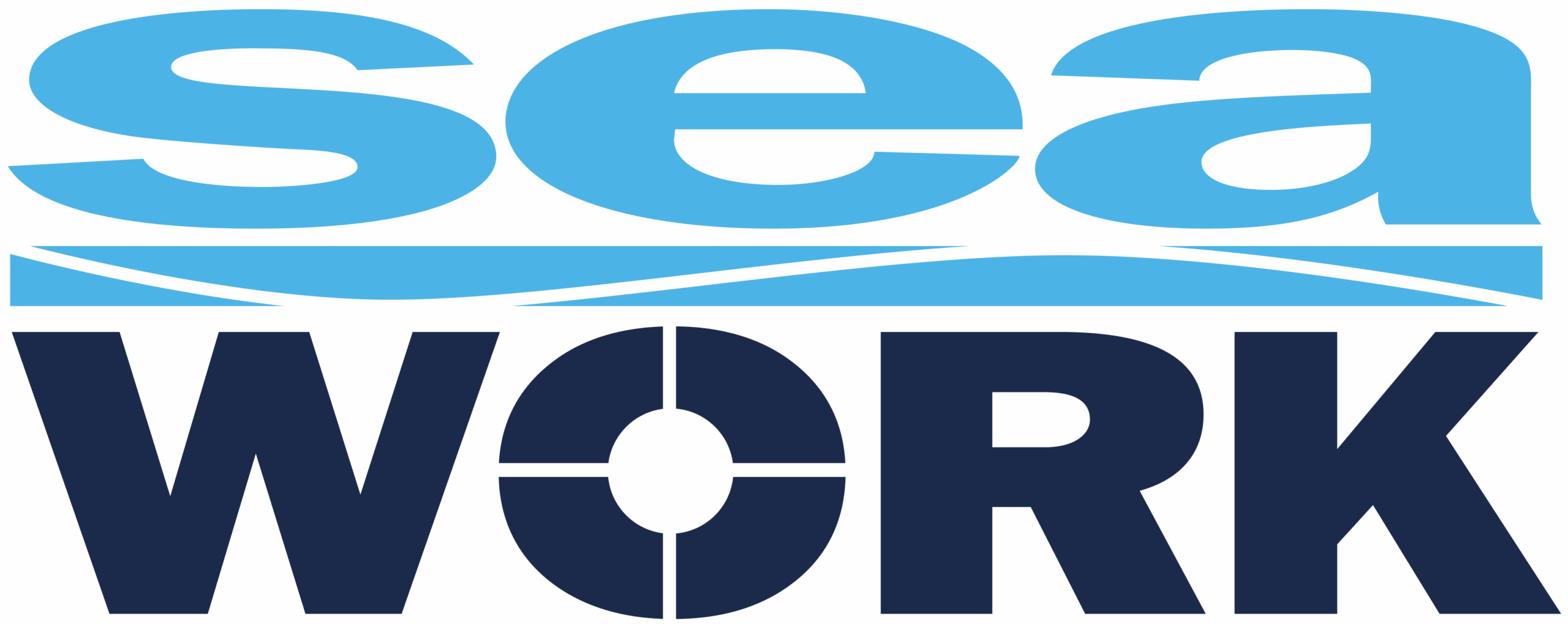