Clevon 1
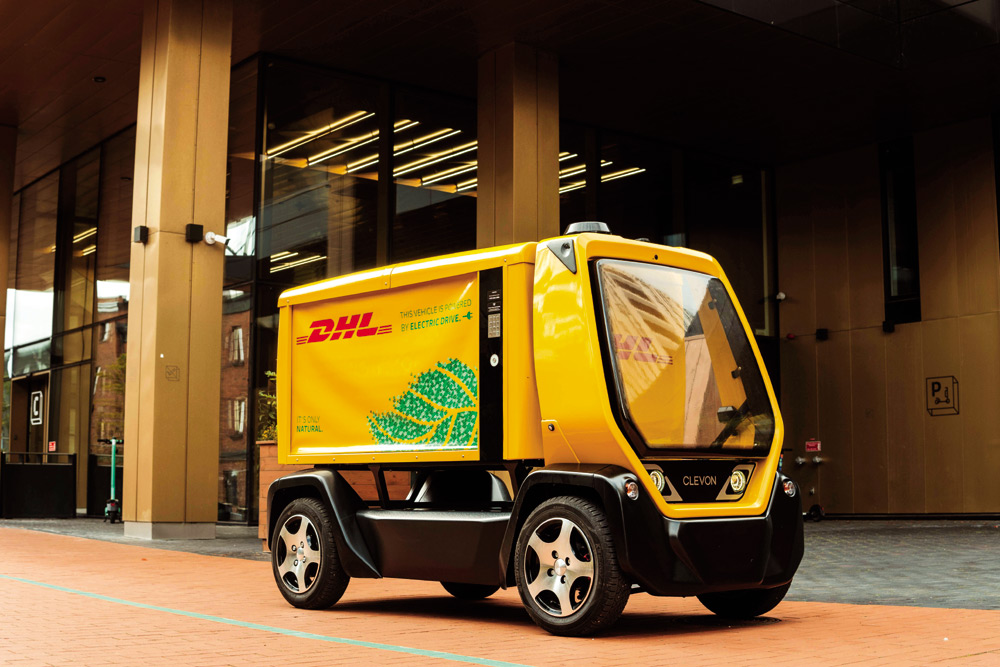
(Images courtesy of Clevon)
Part and parcel
Rory Jackson explains how this autonomous road vehicle is setting new standards of productivity in last-mile deliveries
The ideal logistics company is a well-oiled machine, with packages arriving on or ahead of schedule via the most efficient routes, taking up storage space for the minimum amount of time, and never going missing.
Helping logistics firms achieve these goals was what made Estonia-based Cleveron’s automation technologies – smart lockers and robotic parcel terminals, to be specific – a commercial success in the 2000s. And just as automation can eliminate human error, so autonomy can add human intelligence – and hence safety, reliability and productivity – to logistics processes.
“Having installed its automated parcel machines [APMs] around the world, Cleveron started thinking about what the future of logistics might be, particularly how to automate the process of actually getting the parcels into their lockers and terminals,” recounts Sander Sebastian Agur, CEO of Clevon (which was spun off from Cleveron in April 2022).
“Initially we developed a fleet of UAVs that we felt would fit well with our APMs, but tests indicated too many sources of interference that could potentially bring our service down that way. So in our use case, autonomous delivery cars presented a much more reliable and repeatable means of creating smart connections between our customers’ warehouses and their Cleveron APMs, and that opened up the possibility of mass cost-effective last-mile deliveries, so we put together a work group to design and build the cars.”
Cleveron spun out its Team Mobility in 2022 as Clevon, with a mandate to form a business out of its autonomous car. That car is called the Clevon 1, a compact, autonomous road vehicle measuring 1150 mm in width, 1550 mm in height and 2500 mm in length.
Each one can carry up to 100 kg of freight at speeds of up to 50 kph, although legislation for real-world street traffic tests thus far require it to stay under 25 kph during operations. With clean mobility being a key goal, it is fully electric and can go for 80 km – or
5 hours – between charges. With logistics productivity being another goal, its data link has successfully allowed one teleoperator, in Estonia, to control a test vehicle in Texas, 8500 km away (during which latency stayed below 200 ms at all times).
These days, the Clevon 1 is engaged in commercial operations with international couriers DPD Estonia and DHL Express Estonia, as well as in pilot programmes across Europe, with scale production to follow soon. The company’s engineers aim to continue improving the platform, the goal being SAE Level 4 autonomy by 2024.
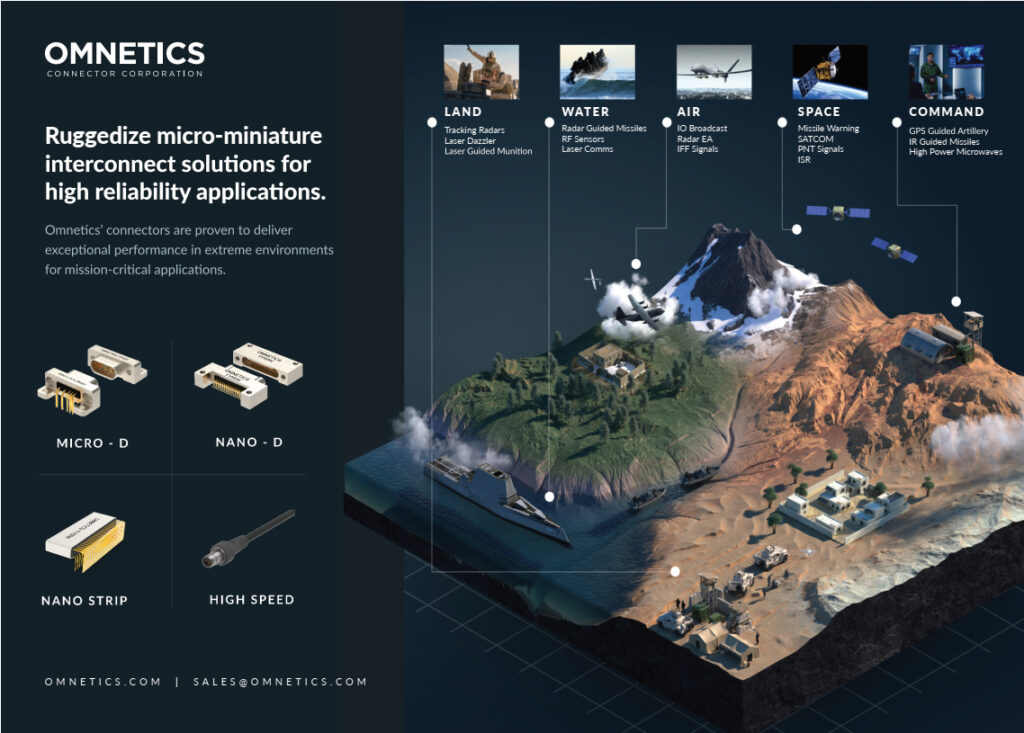
Concept and development
Three generations of the Clevon 1 have been developed, with the first prototype (named the Lotte) having been built in 2017. The second prototype, called the Cleveron 701, was released in 2020 and soon became the first uncrewed vehicle in Europe to receive a licence to operate on public roads. The current Clevon 1 is the third-generation vehicle, and was unveiled in March 2022; this is the version that has been deployed in commercial trials.
The Lotte was largely a proof-of-concept prototype, designed with a number of key functional targets for retail and logistics end-users in mind, including how many parcels needed to be delivered per hour – three to five orders being the ‘sweet spot’.
“Also, the vehicle had to be compact to make it efficient,” Agur adds. “It could not be too bulky to zip in and out of inner-city traffic or delivery yards, so its dimensions of 2.5 x 1.55 x 1.15 m make it around half the length of a typical delivery van, and shorter than most workers. This was also key to it not being lumped in with trucks or cars during homologation.”
Work on the Cleveron 701 began in the summer of 2019. Having advanced past concept work, Cleveron’s engineers drew up new targets to specify what their vehicle had to be capable of.
As Martin Appo, head of autonomous driving at Clevon, recalls, “Cleveron’s CEO wanted responsible innovation from us, so it followed that the vehicle had to be lightweight. From an energy efficiency standpoint, he hated seeing 2 t vans being used to deliver 300 g pizzas for example, and from a safety perspective, a lighter vehicle is inherently safer for pedestrians in the event of a crash.”
In particular though, no-one in Cleveron wanted the vehicle to carry a driver; it had to be totally uncrewed, not just self-driving with a crew member on board. If the vehicle was to be lightweight then a 100 kg driver, 100 kg seat and 100 kg of driver’s cabin and safety systems were all non-starters.
“With those broad targets, we prototyped very rapidly and had many test models besides the 701 models that we’d later unveil,” Appo says. “It was very much the ‘fail fast’ approach – we put together different versions, tested them, and when they failed we threw them away and made a better version using the lessons learned.”
Agur adds, “The Clevon 1 is essentially a larger version of the 701, which fits our homologation targets, but it is still SWaP-efficient. It incorporates not only what our original team learned over time about intelligent software, the mechanics and electronics, but also contributions from new members over time. Initially none of us knew how to build four-wheeled cars, but in time we even had engineers from [high-performance sportscar manufacturer] Koenigsegg bringing in vital powertrain, structural and other expertise.”
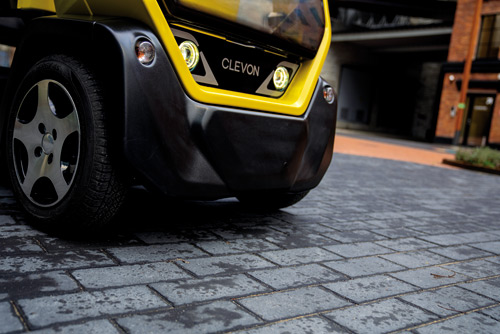
The Clevon 1’s anatomy
Although Clevon is planning a smattering of minor upgrades and market-specific tweaks to the vehicle’s design, most of the architecture and parts will stay the same between versions. In particular, it will remain a four-wheeled system with a rear flatbed and a forward ‘tower’ section.
At the heart of this architecture is a main computer with multiple interfaces and peripherals, managing a distributed network of embedded nodes for functions such as power, steering, navigation and so on.
The network also manages a set of cameras that give a high-resolution 360º FoV about the vehicle, as well as a forward-facing radar, for perception. These inputs are fused on board the Clevon 1, and information is transmitted to and from the vehicle using dual 4G modems on different radio access networks for data redundancy and improved reliability.
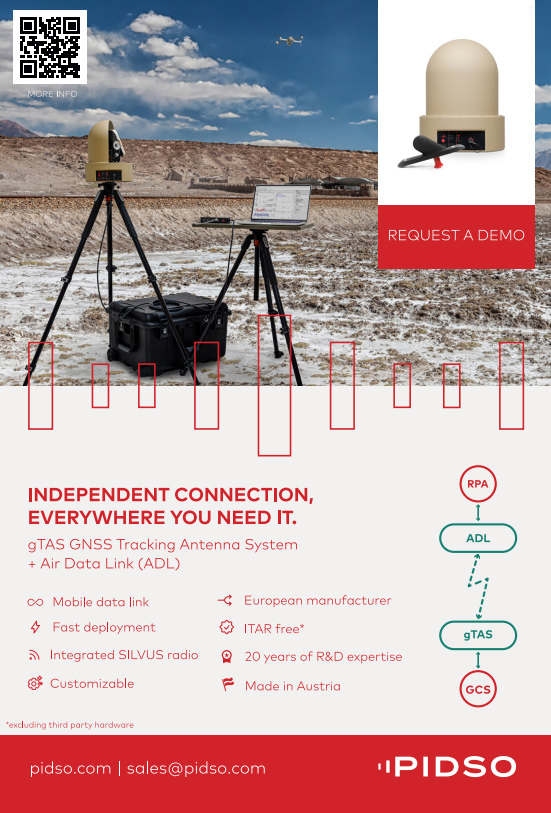
“Also on the Clevon 1 is a GNSS system, which is actually managed through our network comms node, because technically it is a receiver-antenna system that communicates with satellites,” Appo says.
“There is an IMU, two electric motors and inverters at the rear, and a battery pack in the middle. Beneath the front bumper is a wireless charging pad, which ensures that charging is autonomous along with the driving, and helps with work efficiency because it can recharge while being loaded or unloaded.”
The payload system is the Clevon CargoBox, a 1.6 x 1.0 x 0.8 m container with 1 m3 of storage space and up to 150 kg carrying capacity (although 100 kg is recommended). Its shutter door fastens securely to the Clevon 1’s flatbed, and it is electronically sealed so it can only be opened with a designated code. An internal camera also provides the teleoperator with a live feed of the internal cargo.
Structural concept and materials
In its current form, the Clevon 1 weighs 470 kg when fully loaded, and 320 kg without cargo. In operation it consumes 42 Wh/km, a low figure among goods transportation vehicles, given that some electric vans consume 1800 Wh/km.
“Of course though, we might make bigger versions in the future to suit different loading or throughput requirements,” Agur says.
Despite having considerable composites expertise in-house, the structure uses no carbon fibre, since carbon composite is expensive compared with other options that were available. “When we did some market research on some of our competitors in autonomous last-mile and point-to-point logistics, we found that some of their starting prices were around six or seven figures, which just won’t fly with the customers we’re courting,” Agur says.
“So we couldn’t use carbon fibre if we wanted to keep costs down, and we don’t want to be one of those companies that needs billions in seed capital before they’ve even sold a vehicle. It’s far safer to be cash-positive from the start, so we keep our production costs within our ability to pay.”
Instead, simplicity has been the goal for selecting materials. The vehicle’s frame is therefore made from steel parts produced in-house, and the covers are made of ABS, some of which are vacuum-moulded.
“Naturally, the steel is an area where we’ll explore alternatives for saving weight in the future, but we generally opt for widely available automotive parts for ease of cost and supply, adding in extra capabilities where we can from body to wheel,” Agur says. “For instance, the Clevon 1 has 13 in [33 cm] tyres for operating throughout the year in snowy and icy conditions, which the previous versions didn’t have.”
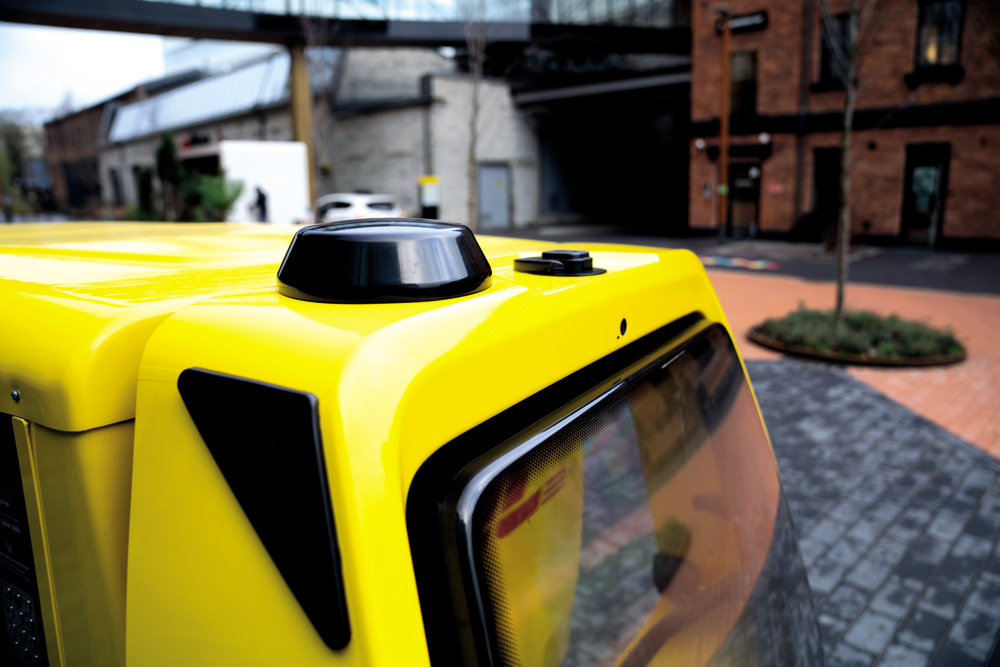
Power technologies
Traction comes from two in-wheel permanent magnet hub motors at the rear axle, each outputting 3 kW for a total of 6 kW (8.15 bhp), with the batteries placed below the undercarriage to keep the centre of gravity as low as possible.
“The battery modules use lithium titanate oxide [LTO] cells from Toshiba,” Agur says. “It’s a fantastically safe cathode chemistry, and means you can literally hammer a nail through the pack and it doesn’t leak or catch fire, which is huge for operating safely on roads alongside human drivers.
“It also allows for fast charging without reducing their lifespan – we can go from 20% to 80% in 45 minutes, and since we use wireless charging technology, we can top up while loading or unloading. That means we can theoretically keep each Clevon 1 working 24/7. And Toshiba is a mass-manufacturer of these systems, which suits our supply chain and production requirements neatly.
“Moreover, the capacities of LTO cells do not decrease significantly with time, so there’s no need to change the batteries over the vehicle’s lifespan. That lowers the total cost of ownership because, as is widely known, battery replacement costs are often the most expensive part of EV maintenance.”
By default, four battery modules with 5 kWh altogether are installed (hence 1.25 kWh each, or Clevon can integrate just two modules with 2.5 kWh each), but the vehicle can carry less energy if the use case does not need 5 hours between charges.
The wireless charging module is Wiferion’s etaLINK 3000, which allows up to 3000 W of charging (at up to 93% efficiency) on 30-60 V, functional within 40 mm distance from emitter to receiver.
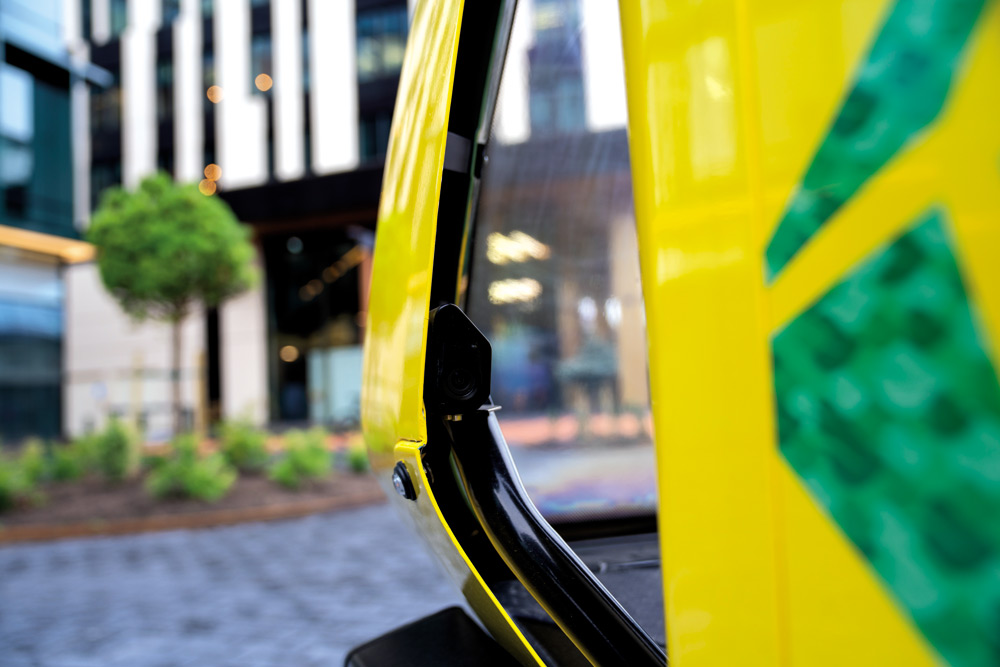
Computers and internal network
The ‘brain’ of the Clevon 1 is a Drive AGX Xavier computer, powered by two eight-core Carmel CPUs based on the ARMv8 instruction set architecture.
It features deep-learning accelerators functioning at 10 TOPS (when using INT8 quantisation) or 5 TFLOPS (in FP16), Nvidia’s Volta integrated GPU, programmable vision accelerators, a 1.5 Gpixel/s image signal processor, a 1.2 Gpixel/s video encoder and a 1.8 Gpixel/s video decoder, with 136 Gbyte/s memory bandwidth.
“There aren’t a lot of development kits out there for commercial-grade autonomous vehicles, but Nvidia offers very good support for companies in the start-up phase of r&d – we’re definitely planning to go with them in the long term,” Appo says.
“And we were able to get the production-ready variants of the AGX Xaviers, so they were already in compact, integrated form factors when we took delivery of them. Their computational power was certainly good when we started development, but we’re already looking towards Nvidia’s Orin as the next generation of self-driving computer as we develop each user’s applications and edge cases.”
Agur adds, “Nvidia have said we’ve gone the furthest of any autonomous car using their technology, so at this point it’s more of a partnership than a supplier relationship.”
A distributed network spreads outwards from the AGX Xaviers for control and comms with the UGV’s subsystems. The lower-level computations are handled by seven STM32-powered embedded microcontrollers, although the company notes that they might be overpowered for isolated, subsystem-specific microcontrollers, but their cost-effectiveness was viewed as valuable for future-proofing much of the internal network at a low price.
The main and sub-level computers communicate via CAN FD, an extended version of CAN designed for use in high-performance vehicle ECUs, which Appo notes can push up to 5 Mbit/s of data over each CAN line.
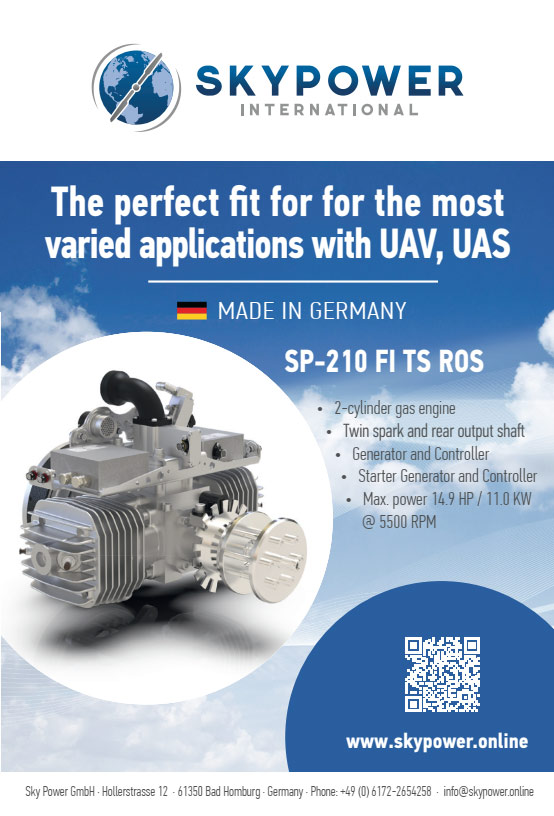
“CAN FD is very leading edge in the automotive sector, but its use in robotics has also grown,” he says. “We’re also using it to communicate between the main computer and the radar, but as the computer has multiple CAN interfaces we use one line for the embedded computers and another, separate line for the radar.
“Meanwhile, the cameras’ outputs are received over GSML2 links; serial is used for the IMU, and automotive Ethernet for comms from the main computer. The software was developed using the latest C++ standards – C++20 and C++23 for embedded and high-level software respectively – with custom toolchains and powerful servers used for cross-compiling.
“And for all our updates, we start with binary code going to the main computer, which then updates the embedded modules over CAN. Custom tools were key to keeping our development and testing loops tight – we can build the C++ code for our core software from scratch in 20 seconds, that’s literally how fast it goes.”
GNSS inertial systems
The Clevon 1’s IMU is made in-house using a reference design from CEVA Technologies, specifically its BNO080 MEMS IMU.
“It’s an especially popular chip design for mobile phones,” Appo says. “And RTK GNSS on top of that achieves centimetric accuracy in traffic and narrow roads.”
The GNSS antenna sits centrally atop the Clevon 1’s tower section, which connects via coaxial cable to a u-blox receiver module inside the company’s network comms module. This is a custom router built in-house that contains the u-blox chip, multiple Ethernet I/Os and a main network controller.
“For RTK updates, we can use NTRIP services or our own base stations,” Appo says. “And to simplify our comms systems further for our next vehicle iterations, we’re looking into getting an antenna module from Techship or INPAQ to integrate our GNSS antenna and two 4G antennas inside its single enclosure.”
Clevon anticipates that its new antenna system will integrating 2 x 2 MIMO 5G non-mmWave, wi-fi 6e with integrated Bluetooth and dual V2X channels, along with GNSS.
“We’ve developed our extended Kalman filters in-house, which was a complicated process, not only for fusing GNSS and IMU data but remember that we have odometry – both wheel position and current speed – and all the other information we can get from the car,” Appo notes.
“We refer to it as our self-estimation algorithm. We’re able to localise our vehicle in a way that achieves very precise path-following, and we’re continually refining the algorithm to add more sensor information and smoothness of data handling.”
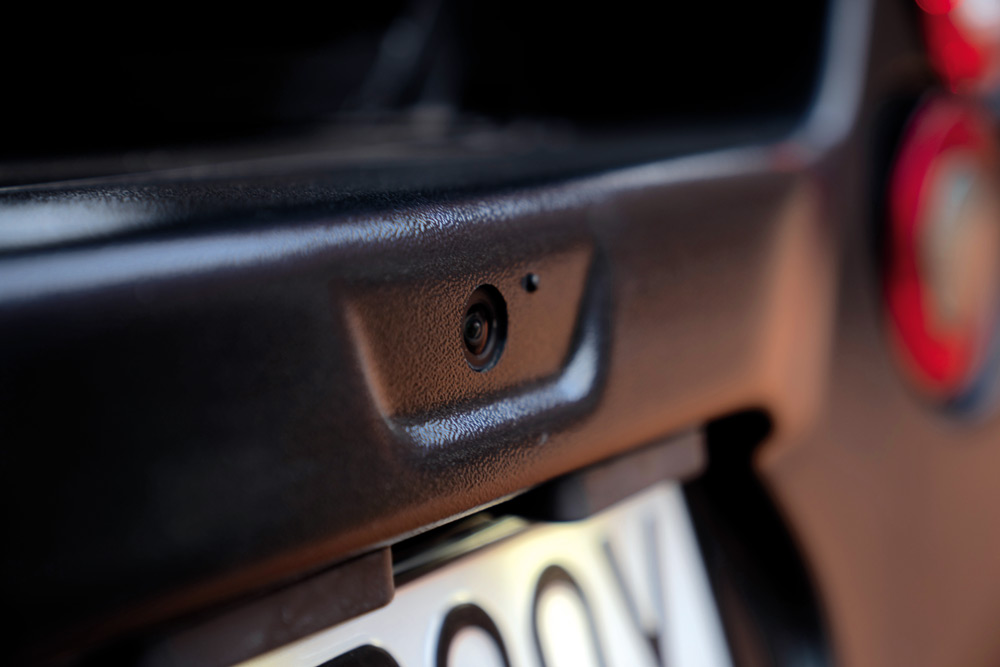
Perception systems
Clevon’s engineers know however that working in logistics means driving through urban canyons and infrastructure that can render GNSS unsafe. That, and the need to drive through real-world traffic, means a multi-sensor suite for live 3D perception and localisation (with the use of deep neural networks for intelligent comprehension of surroundings) is critical.
For vision and object detection, classification and avoidance (with colour), six automotive-grade Sekonix cameras are fitted around the Clevon 1, each providing a 120º (overlapping) horizontal FoV and a 60º vertical FoV. A liquid spray system is remotely triggered by the teleoperator to wash the camera lenses, although Appo comments that in the future, cleaning will be performed autonomously using the computer vision to recognise signs of dirt.
“We’re not currently using Lidar for anything because a decent one costs as much as a Clevon 1,” Appo says. “Also, we’d need more than one for full FoV awareness, so at around $10,000 per Lidar unit it just doesn’t make sense for us.
“However, as the technology evolves and prices come down we’ll probably adopt it. The real-time 3D data density of Lidar point clouds could be really valuable for faster or bigger variations of our vehicle.”
The forward-facing radar beneath the tower section is built using a Texas Instruments chipset, with in-house r&d having determined the ideal antenna configurations for the desired detection range (currently 100 m) for avoiding frontal collisions.
The radar has a 180º FoV, a refresh rate of 30 Hz, a range detection resolution of 10 cm, an angular resolution of 10º and a velocity range of -30 to +30 m/s.
Future, longer versions of the Clevon 1 might incorporate more radars for more safety, potentially up to three on the front, one on the rear, and a higher number on the sides. Appo notes that CAN FD is an easily extendable protocol for connecting more radars to the Nvidia computer, and since radars work through plastic, the team can mechanically integrate them beneath the vehicle covers without issue.
Agur adds, “Our customers have also tested Chinese autonomous cars, and found that the Lidars on these actually didn’t work very well in snow, heavy rain, hail and so on: essentially they created a wall through which the laser pulses couldn’t effectively penetrate. Radars don’t have that problem, they work in all kinds of weather.”
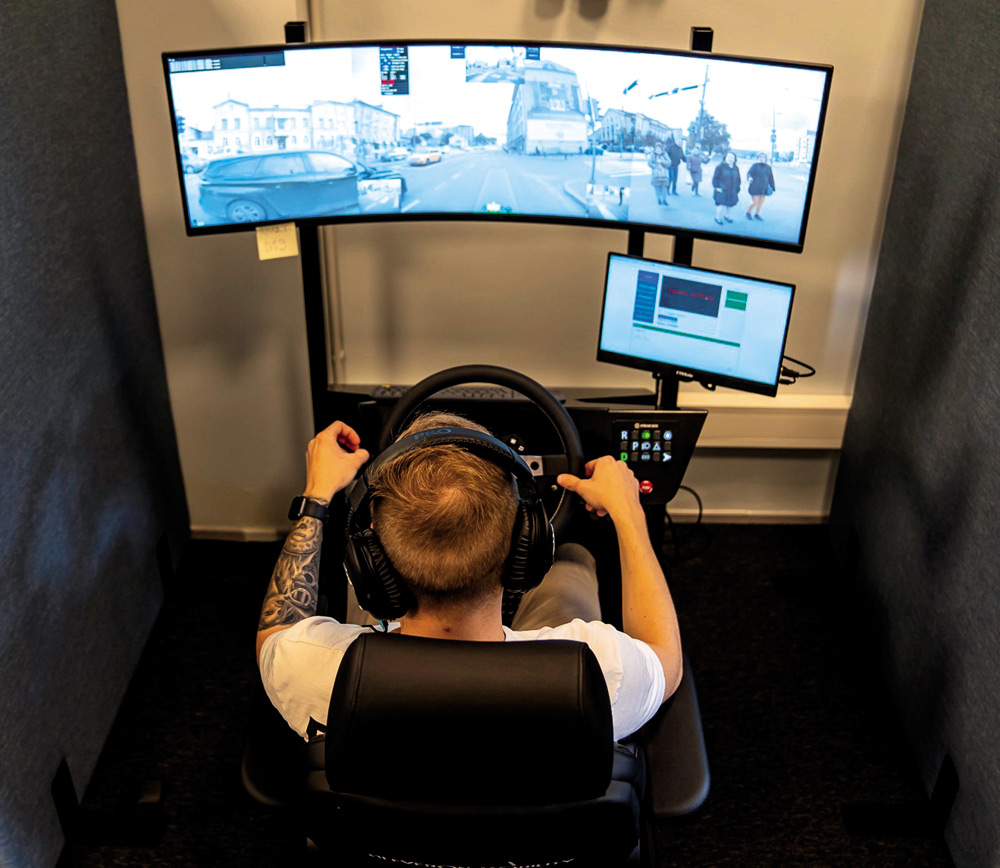
Driving safety and intelligence
As SLAM would be laborious and unsafe for driving on roads, Clevon pre-maps all the potential driving areas itself using RTK-GNSS, and integrates that data with all the other information it can fuse on the static and dynamic content of the streets to be travelled, such as crosswalks and pedestrians.
“That way the system knows where it most needs to be prepared to stop or yield on the roads,” Appo says. “Rough routes for the vehicles are calculated on a separate routing server that contains all the maps, and are then fused with our pre-mapped routes to output a route for each vehicle to drive.
“For object avoidance, a lot of work went into prediction and behavioural analysis of how pedestrians, other vehicles and other dynamic objects will move. The vehicle creates a 4D collision map to predict possible future movements and stamps them for time. On the basis of those predictions it can slow down to prevent possible accidents.”
The Clevon 1’s planning behaviours also integrate traffic laws, to comply with rules on safely giving way at intersections or crossings for instance. As Appo explains, “The Clevon 1 can automatically detect whether it is operating in a capable ODD [operational design domain] and act accordingly.”
ODD describes the situation and environment where the vehicle is operating, including patterns in pedestrian densities, number of other vehicles and lanes, the presence and height of structures, and so on. As a final safety measure, the teleoperator can take over the control of the vehicle.
“In closed areas, the Clevon 1 can therefore be run 100% autonomously,” Appo says. “But in major cities, with their complicated and dynamic driving situations, we’re currently running with 20% autonomy, 80% teleoperation. Pending ongoing technology refinements and the openness of regulators to road autonomy, we aim to get that latter figure to 50/50 in about 6 months.”
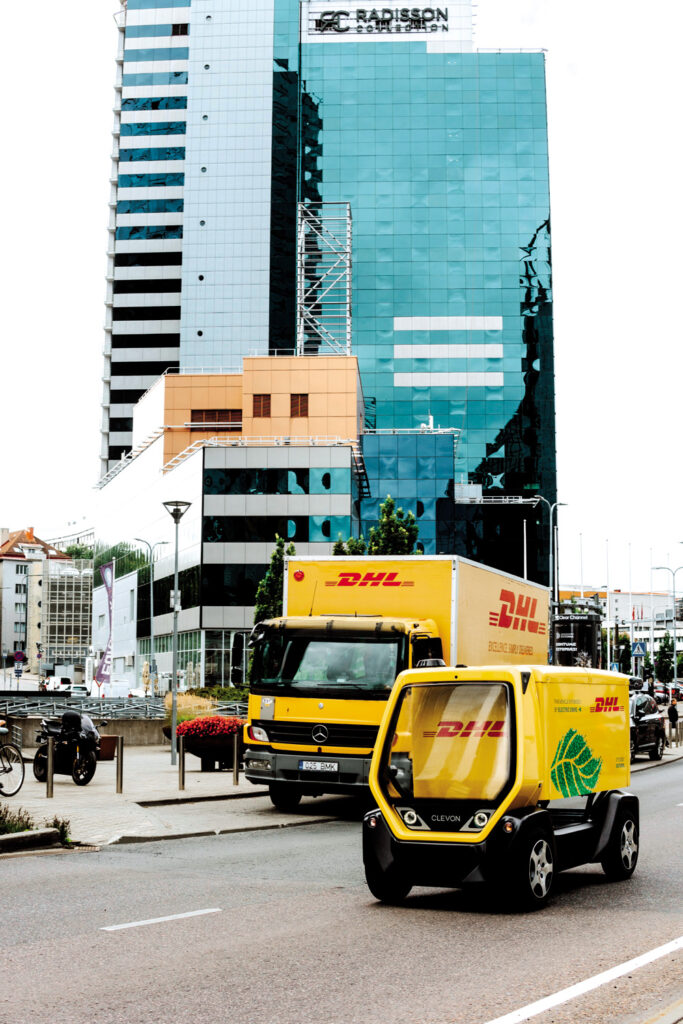
Operating sites
The teleoperators monitor or take control as necessary from high-end Linux desktop computers with AMD RDNA2 graphics cards and large, curving flatscreen monitors, specifically Samsung Odyssey CRG9 QLED Freesync units, as well as steering wheels, pedals and additional control interfaces from Fanatec.
“At the operating sites we also have some very powerful in-rack routers handling the comms between the GCSs and UGVs,” Appo says.
“All the teleoperation software is also fully custom made, including the 3D renderings, to lower the latencies as much as possible,” he adds. “Glass-to-glass latency, from when each photon goes into the camera lens to when the pixel changes on the monitor, is about 180-200 ms.”
In addition to the controls, the teleoperator has an emergency stop button – another reason why this data link uses powerful routers to keep the 4G connection to the Clevon 1 secure. The vehicle also has intelligence layers for identifying when a situation is dangerous enough to merit coming to a safe stop.
“We’ve also developed all this teleoperation and network software with cybersecurity in mind,” Appo notes “We can’t use VPNs and still get low latencies, so instead we’ve developed our own encryption software and embedded it into the routers to protect data comms at the socket level.”
Future growth
Clevon is continuing to expand its operations in Europe with customers such as DPD Estonia, DHL Express Estonia and Iki (a grocery retailer and the largest company in Lithuania, where Clevon is now licensed to operate on public roads). Further end-users in Belgium and elsewhere are expected to be announced in the near future.
More recently, in September 2022, the company opened offices in the Dallas-Fort Worth area in the US to enter the North American market. American customers are being secured, although they cannot be disclosed for now.
“Non-logistics users are also expressing an interest in the Clevon 1,” Agur says. “Upon request, for example, we’ve showcased a version of it fitted with speed cameras, so that police can track drivers autonomously and on the move. Based on that and our current customers’ usage, we anticipate having at least 2000 vehicles on the road by 2023.”
Specifications:
- Clevon 1
- Size: 2500 x 1550 x 1150 mm
- Net weight: 320 kg
- Gross weight: 470 kg
- Payload capacity: 150 kg
- Top speed: 50 kph
- Operating speed: 25 kph
- Endurance: 5 hours
- Range between charges: 80 km
Some key suppliers
- Main computer: Nvidia
- Microcontrollers: STMicroelectronics
- Cameras: Sekonix
- Radars: Texas Instruments
- Modems: COTS
- Wireless charging pads: Wiferion
- GNSS: u-blox
- MEMS IMU reference design: CEVA
- LTO batteries: Toshiba
- Operating station monitor: Samsung
- Operating station pedals: Fanatec
- Operating station graphics card: AMD
UPCOMING EVENTS
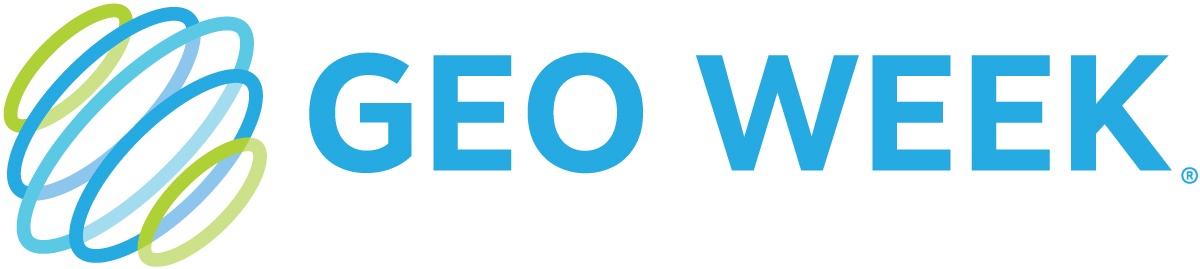
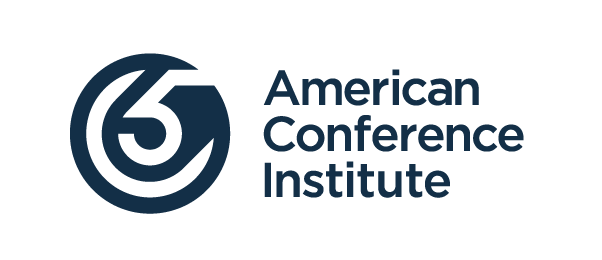
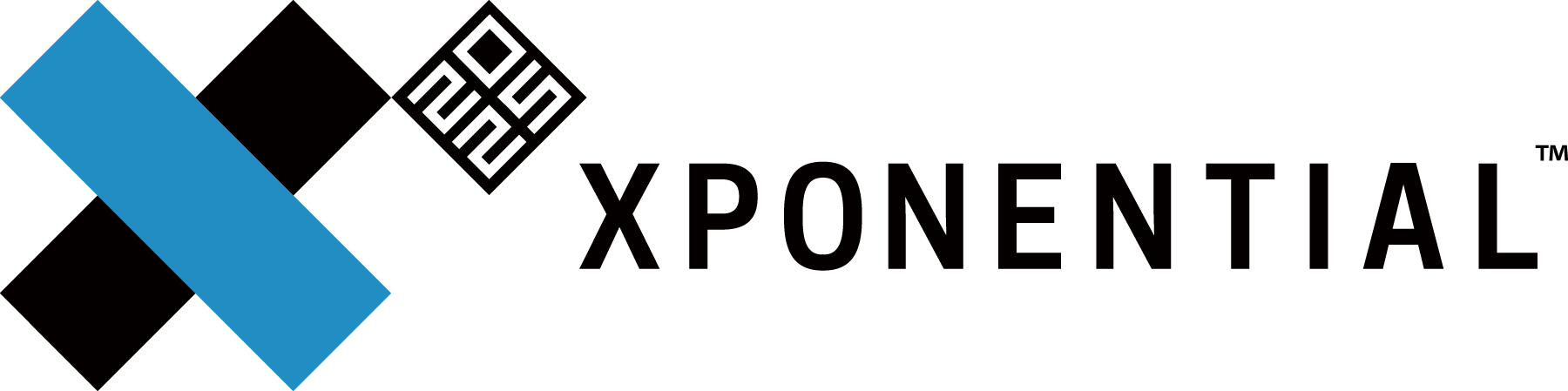
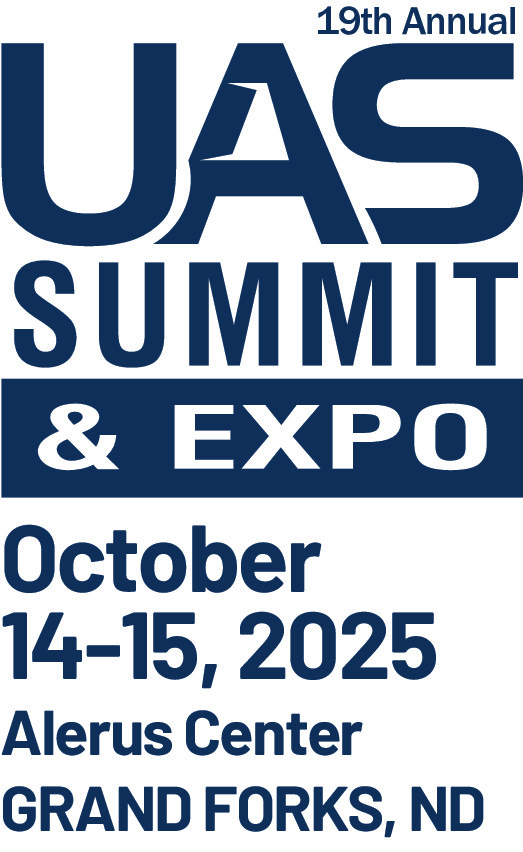
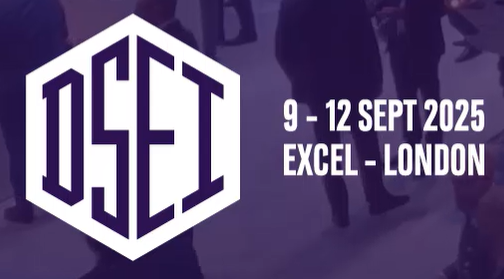
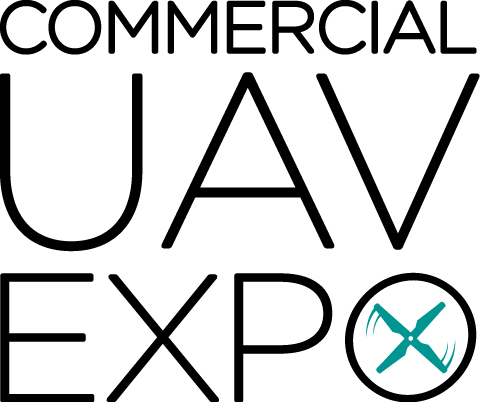
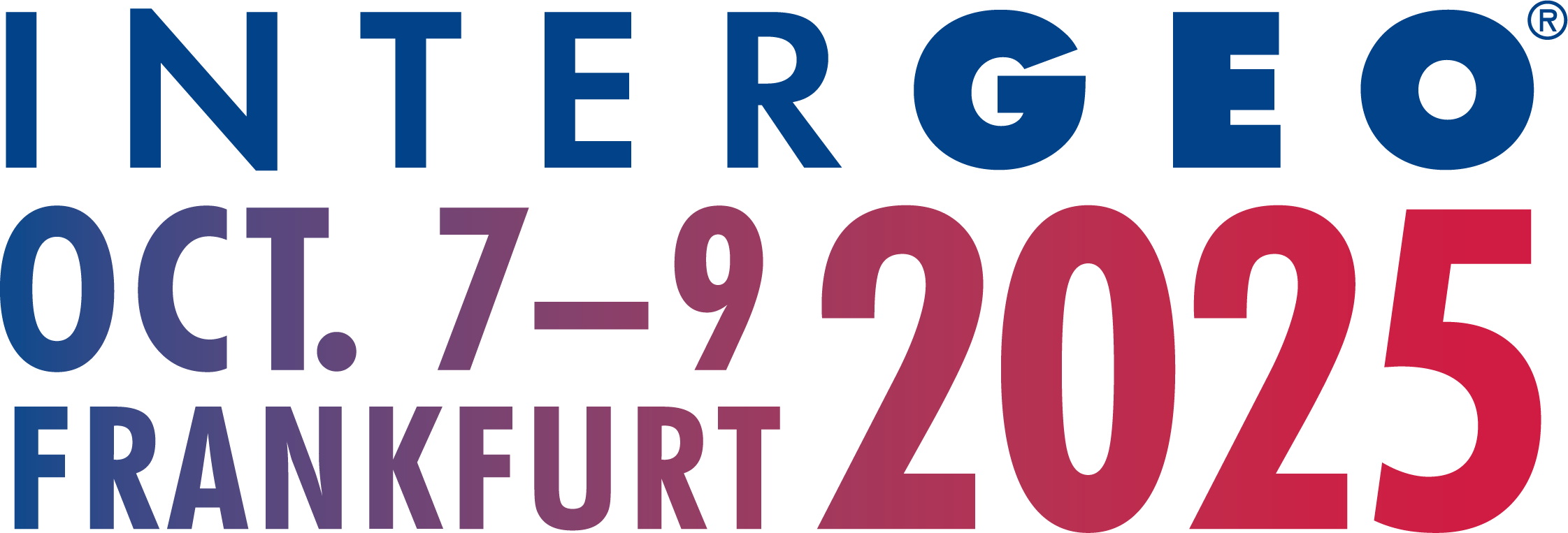
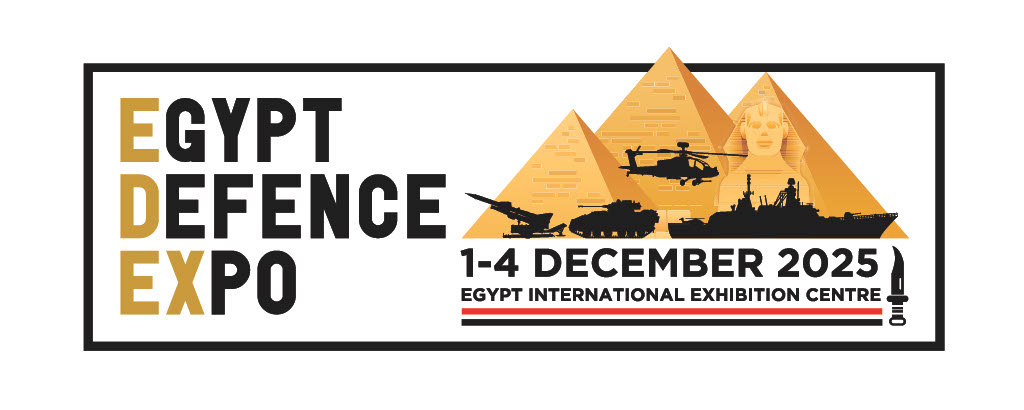
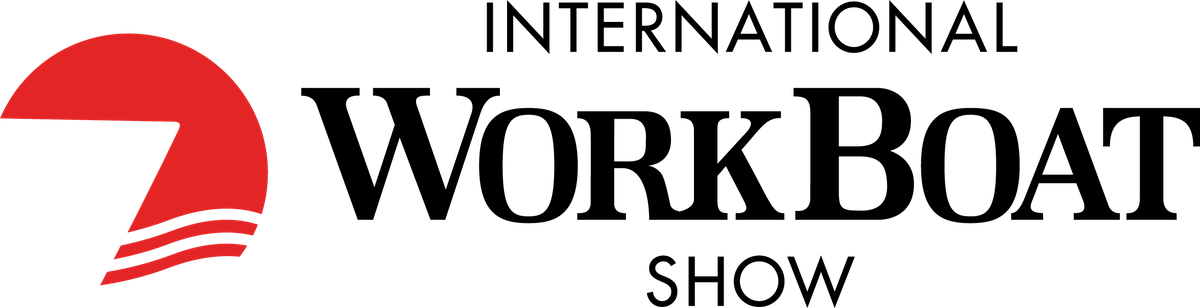
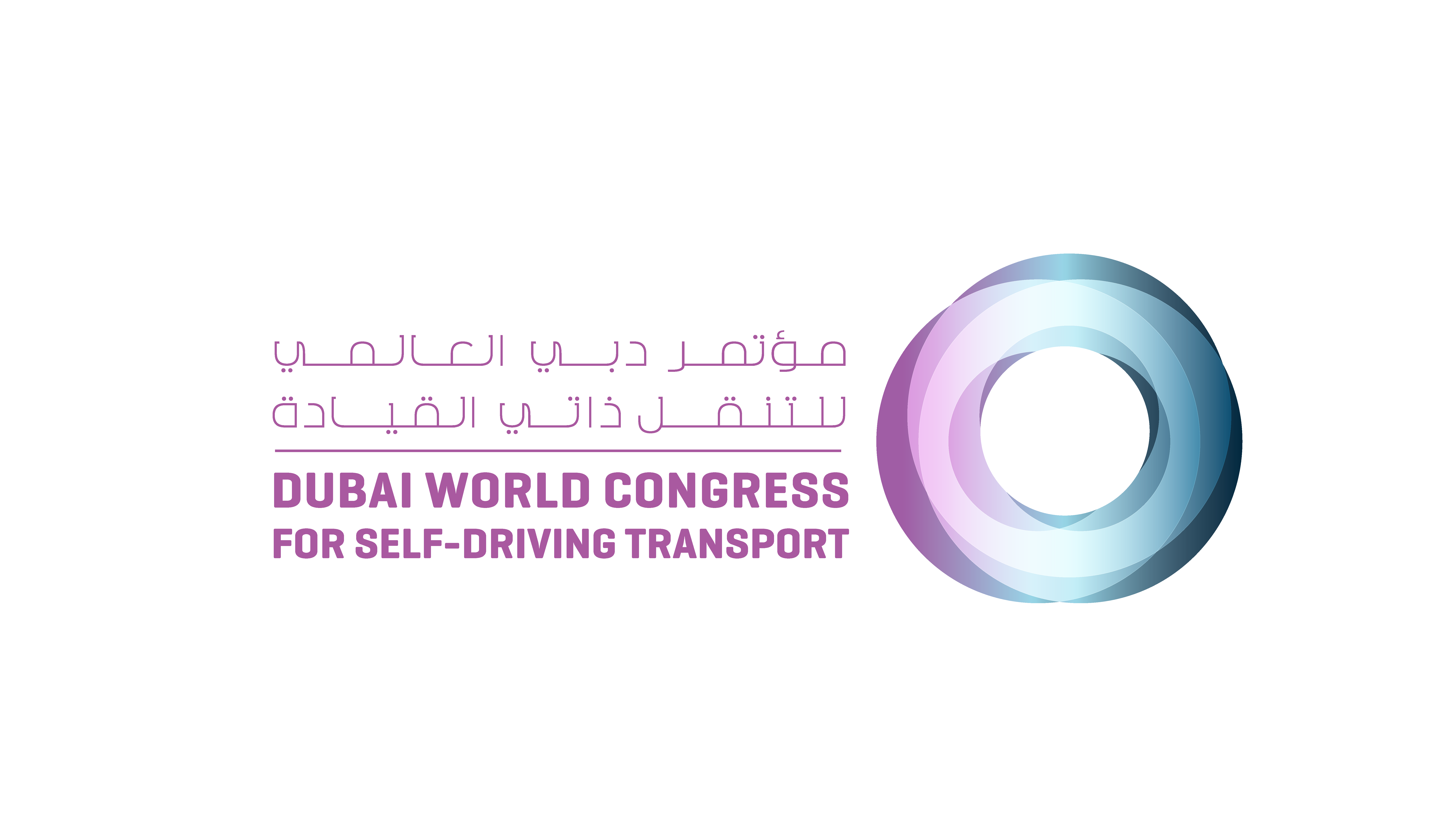
