Marine Advanced Robotics WAM-V
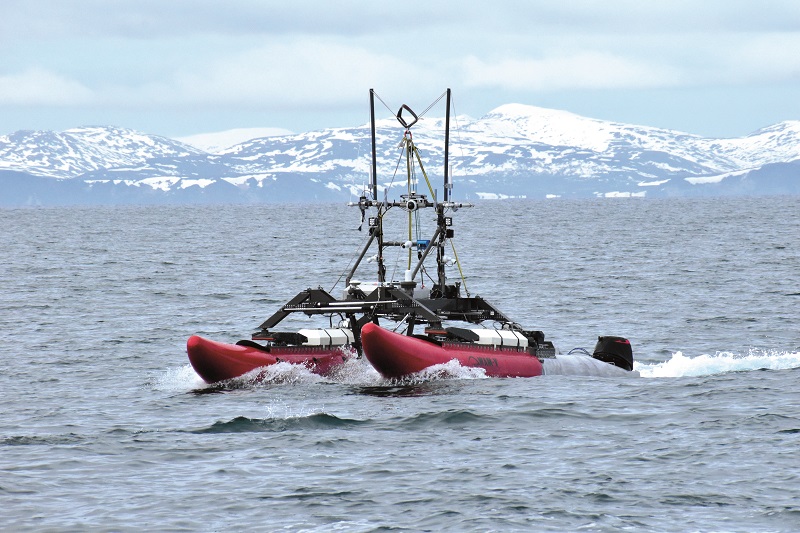
Steady as she goes
Chronic seasickness spurred the development of this USV and its patented suspension and articulation system. Rory Jackson has the details
Anyone with first-hand experience of seasickness will know how unpleasant it is, and the range of measures available to avoid feeling it again. For the creators of the Wave Adaptive Modular Vessel (WAM-V) though, it sparked the birth and evolution of one of the most in-demand USVs in the maritime data market.
The story of the WAM-V begins in the 1970s, when Drs Ugo and Isabella Conti took a round-the-world trip with their family on a 50 ft ketch, a journey spoiled by Ugo’s continuous seasickness. That drove him to envision engineering solutions to the boat’s rolling and crashing motions that had so upset his health.
Eventually, in the late 1990s, the idea of a passively self-adjusting mechanical platform took hold in their minds, motivating them to found Marine Advanced Research in 2004. The company is now called Marine Advanced Robotics (MAR), to emphasise its focus on developing the WAM-V as a series of uncrewed platforms rather than crewed vessels (as the mechanisms originally developed to prevent seasickness also make for a survey platform that can remain highly stable amid rough seas), and is owned by Ocean Power Technologies (OPT), which acquired it in November 2021.
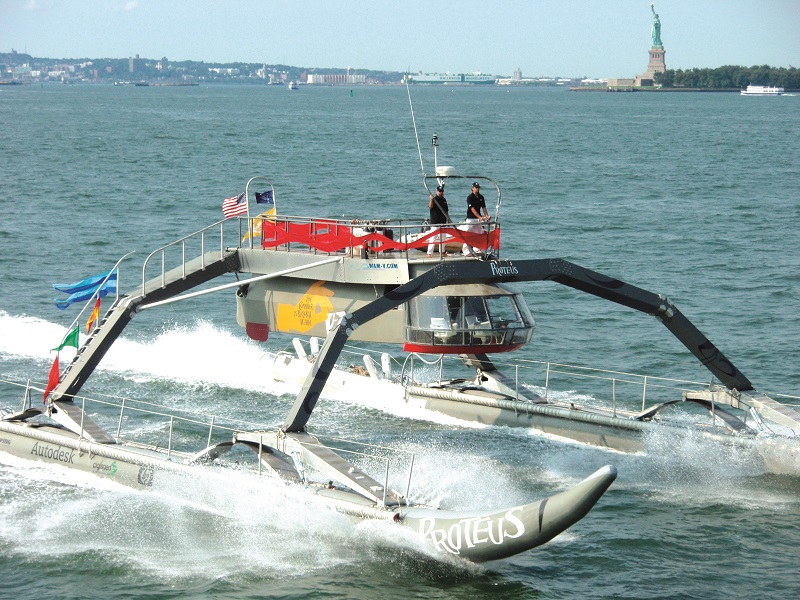
Although the WAM-V as a concept is highly modular, with an inflatable catamaran hull design and a patented suspension system scaling up to potentially enormous systems, at present MAR is focused on making three models: the 2.5 m-long WAM-V 8, the 5 m WAM-V 16 and the 7 m WAM-V 22.
As Mark Gundersen, formerly CEO of MAR and now VP of autonomous vehicles at OPT tells us, the ‘22’ is the main focus of the company’s effort, so its development forms the bulk of this article. By coincidence it was unveiled in 2022, while the 8 had been launched in 2020 and the 16 in 2012 (being the first production-focused iteration).
The WAM-V 22 measures 7 x 3.66 x 0.56 m, weighs 1134 kg without payload, batteries or fuel (with a payload limit of 270 kg), and has a mission endurance of up to 72 hours, as well as a top speed of 20 knots, which is high for a USV.
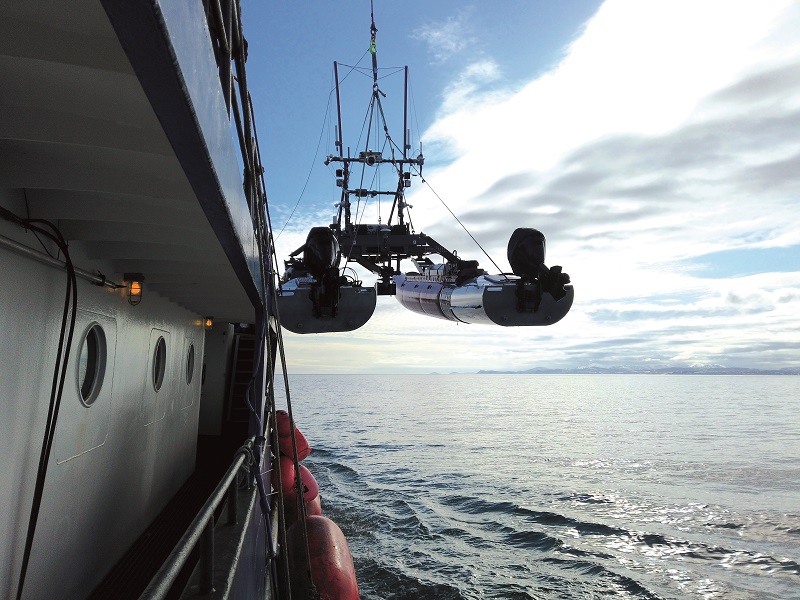
From crewed to uncrewed
Although we have featured the WAM-V in short updates since our first encounter with it at Oceanology International 2018 (UST 19, April/May 2018), a brief reminder of its patented suspension is in order.
Its design is based around two pontoons with at least two legs each (for at least four in total) that support a central platform on top, where typically the electronics are mounted.
The forward legs support the forward part of the central body via a ball joint. This joint is spring-supported and allows the forward legs to rotate as a unit relative to the central body, and the joints’ lower ends attach to forward sections of the pontoons. The stern legs are rigidly coupled to the central body, with their lower ends connected to the aft parts of the pontoons, allowing the legs to rotate vertically and transversely but not longitudinally.
This suspension and articulation keeps the central platform highly stable, even in high waves and sea states. That provides a comfortable ride for passengers and crew, and an inherently stable system for any cameras, Lidars, sonars and other data-gathering sensors.
“I joined in 2005 after the Contis had raised funds from angel investors and developed a proof-of-concept catamaran featuring a central top platform that was kept stable by a set of composite legs below,” explains Gundersen.
“That concept soon morphed into what would become the Proteus, our 100 ft-long crewed WAM-V demonstrator. No computer model existed that could come anywhere close to simulating the motions of the vessel, so we built one ourselves and started testing.”
The Proteus was unofficially launched in Washington state in the summer of 2006, with sea trials following in the Puget Sound before being relocated to California, for tests from San Francisco to Richmond, where MAR is now headquartered. Its official launch and unveiling came in 2007, and it went on to complete 3000 nautical miles of testing across the Pacific and Atlantic oceans, as well as the Mediterranean.
“Those 3000 miles on the crewed prototype gave us a vast amount of data and a front row seat on how the WAM-V would move, and how its suspension, articulation, hinged engine pods and elevated central structure would work individually and together in a practical sense,” Gundersen says.
These observations and some collaborative projects along the way gave the Contis and Gundersen some technical insights that informed the second generation of the WAM-V.
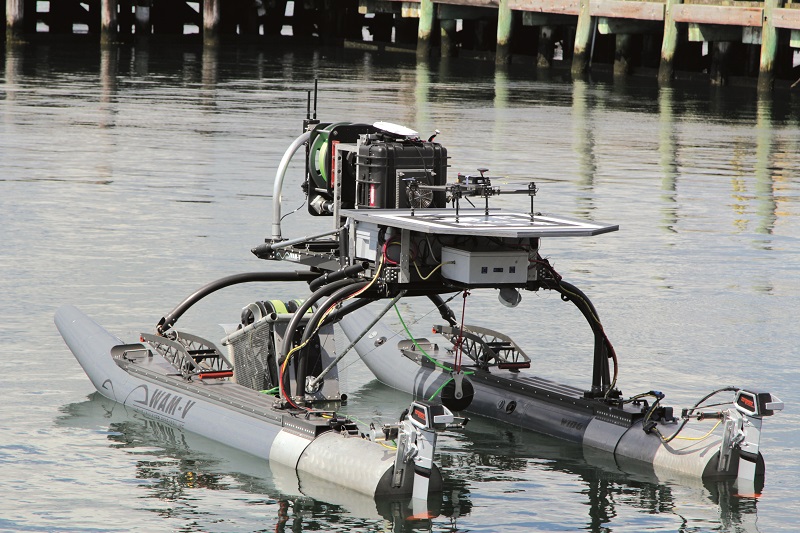
“For instance, the Proteus had suspension parts installed fore and aft, but on the second generation we eliminated the aft suspension because we’d realised the front suspension was really the key to the WAM-V handling the waves and mitigating the wave-imparted motion as it crossed forwards into them,” Gundersen explains.
“We also added a rigid horizontal structure we call our ‘ski’ on top of the inflatable hulls, which allowed us to do a couple of things. One, it made a good mechanical connection between the front and rear arches; and two, it allowed us to reduce the pressure in the hulls so they could better absorb wave motions.
“The Proteus’ hulls were inflated to about 7 psi – which is really high – but now we’re running the hulls at around 1.5-2.5 psi.”
Several further iterations followed, to explore different concepts. Critical among these was a 33 ft (10 m) version that folded to fit into a standard 20 ft container, which was vital to demonstrating the WAM-V’s transportability using existing infrastructure and trailers. The smaller WAM-Vs in production now therefore also break down into small, industry-standard container grades for easy shipping, including as air cargo.
“The WAM-V 16 was developed in about 2012 for our first production run, so it was the first to be configured for manufacturing in significant quantities,” Gundersen recalls.
At around that time the company also began ramping up its r&d into the uncrewed version of the WAM-V, particularly autonomous control systems, as far fewer marine autopilots were available at that period compared with now, and none were optimised for the wave motions handled by the WAM-V.
Incremental progress in a WAM-V autopilot followed from 2013 until 2017, when Joshua Mehlman (VP of engineering at MAR and now senior director of engineering at OPT) joined. “Josh steered us towards the prospect of making the WAM-V a great sensor deployment platform, with its stability inherently making it more suited for gathering inspection and monitoring data than most USVs,” Gundersen says.
“That got us thinking not just about different kinds of multi-beam sonars to install, but also stowing, launching and recovering other uncrewed systems, with the WAM-V potentially working as a mothership for subsurface as well as aerial vehicles.”
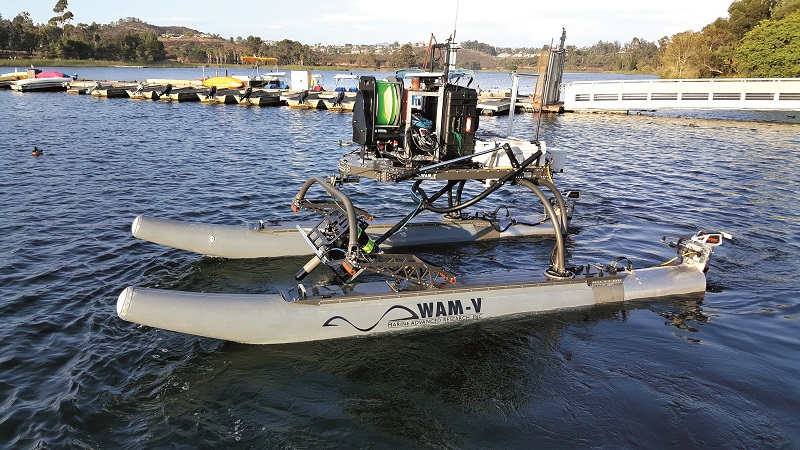
Teaming and swarming
In 2017, MAR accomplished its first ROV and UAV deployments from the WAM-Vs, at the US Navy base at San Diego. This was a maritime security scenario in which an unidentified object was dropped from a vessel in restricted waters, and uncrewed assets had to be quickly deployed to acquire information about its nature.
“That was a really successful learning experience, and then almost immediately after it we did a similar demonstration at NUWC in Newport, RI,” Gundersen says. “In that one though we deployed a UAV and ROV from a single WAM-V, as an all-in-one solution, rather than on separate WAM-Vs as in San Diego.”
This CONOPS forms a key part of the WAM-V’s most in-demand use case, particularly in the defence market. The stabilisation of its central platform as well as its open frame design make it ideal as a launch & recovery base for swarming teams of uncrewed systems.
“In 2020 we paired a WAM-V with a UAV from Overwatch Aero to identify illegal fishing in protected marine areas, where we autonomously homed in on a boat and zoomed in with the UAV’s camera to see precisely what the boat was doing,” Gundersen recounts.
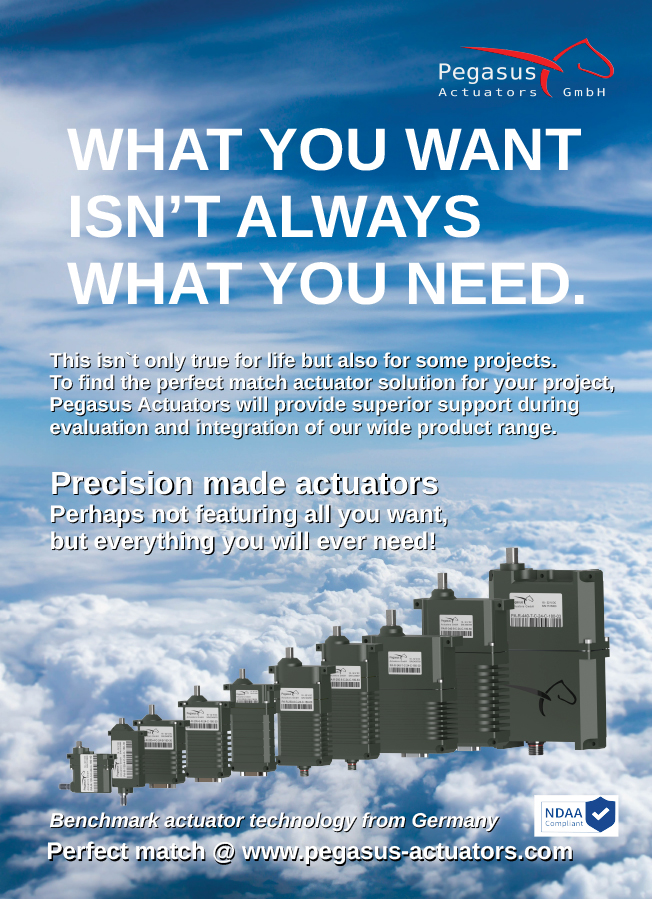
“The boat was fishing legally, but we could see individual lobsters on its deck while maintaining a considerable distance and degree of stealth from them. The whole idea with monitoring for illegal fishing is that you’re supposed to gather irrefutable evidence of criminals in the act, which you can then take to court and charge the crew with.”
The following years have seen this USV-UAV teaming capability become more mature, and includes major collaborations with Planck Aero using the latter’s Shearwater UAV (UST 25, April/May 2019) for its ability to land on and launch from moving platforms. More than 100 autonomous launches and recoveries of Planck’s UAV were performed from the WAM-V over a 2-day period in the San Francisco bay in 2021 (with around 250 lb of equipment on the USV fully supporting the 2 lb UAV), to show that such operations could be performed repeatably and without human intervention.
As Mehlman explains, “That involves not just good autopilots but a lot of consistent and intelligent comms between the USV and UAV, for things like planning recovery manoeuvres when the UAV’s battery or fuel runs low, or communicating wind speeds and directions from the USV’s wind sensor to the UAV. That means the latter can determine its best approach and rotor commands for a safe landing.”
The kind of mesh or swarm the team creates will vary according to end-users’ requirements. Mehlman notes that while command links between the USV and its GCS work very well – particularly given the large and powerful radios the WAM-V can carry – if a UAV is present as part of the swarm then the user will sometimes choose to have the UAV act as a comms bridge between it and the operator, given its greater altitude and visibility relative to any surface vessel.
“In addition to the WAM-V being able to carry more radio power than the UAV, the fact that it can carry more computing power means we can outsource some edge computing and hence AI capability to the surface vessel,” he adds.
The USVs are also being developed for crewed-uncrewed operations as autonomous force multipliers. In 2019 for instance, two WAM-V 16s were teamed with a crewed vessel for a hydrographic survey project with the US National Oceanic & Atmospheric Administration in the Great Lakes. The uncrewed systems integrated multi-beam sonars, and the crewed ship carried a networked GCS portal so that all the data (from the USVs and the crewed ship) was acquired and presented in a single UI in real time.
“That hadn’t really been done before,” Gundersen notes. “All the vessels were contributing to a single map simultaneously, which meant they knew whether there were gaps or overlaps in the parts of the lakes they were mapping. That’s something you don’t usually find out until after returning to shore for post-processing.”
Mehlman adds, “In hydrographic mapping, a lot of the time you either get gaps in your data, meaning you have to go back out and essentially do it again, or you get something like 50% overlap in survey paths, which means you’re not being fuel-efficient. So being able to optimise that in real time – and autonomously – makes a huge difference.”
More recently, in 2022, similar missions have been performed around Alaska, including repeated launches & recoveries of a WAM-V 22 from a 115 ft vessel.
“On some days around Alaska we were surveying at 8 knots,” Mehlman notes. “That’s faster than usual for hydrographic surveys, but crewed-uncrewed teaming is really pushing demands for speed in our USVs. The more area we can map per launch, the better, and in our experience if you can’t keep up with the crewed vessel, it deters its captain from using your USV again.”
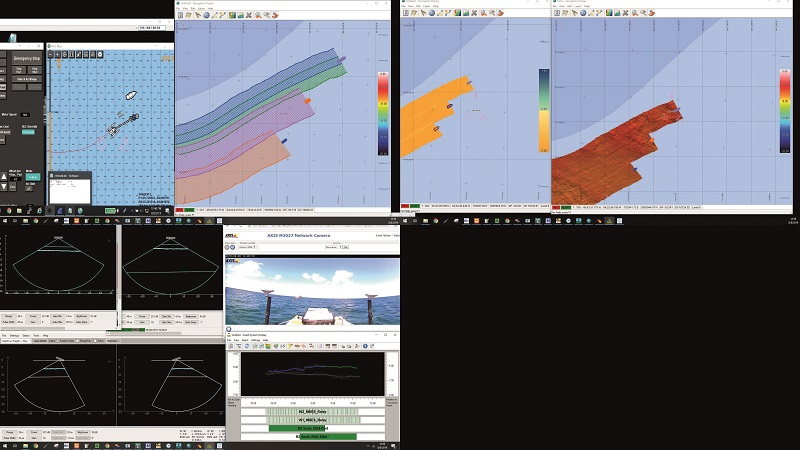
WAM-V architecture
The largest and hence most visually noticeable parts of the WAM-V are its inflatable hulls (or pontoons) at the bottom, either side of the superstructure, which provide flotation and some wave absorption. Above those are the suspension parts and the ski structure that leads up to the front and rear arches. These support the central payload tray, which also supports the enclosures for autonomy, controls and navigation, as well as space for a UAV platform and UUV winch.
“Beneath that tray, we can talk about having a moon pool, although really, the entire WAM-V is a moon pool, given the space between the inflatable hulls,” Mehlman says.
“There we can install sonars, ROVs, towfish, gliders, all sorts, and in so many different configurations. But we generally put them in and out of the water during missions using our retractable sensor mount [RSM].”
Also on top of the tray is a comms mast, which can be configured as an arch or pole, while behind each pontoon is a motor pod. These are interchangeable to cater for different missions and users who might want different speeds, power, torque, noise, carbon emissions and drafts; various outboards, waterjets and other boat engines have been used.
“Also, our rudders can be operated in a conventional catamaran style or in differential, tank-type steering,” Mehlman says. “Our control system can do a lot in autonomous mode to decide the best way of steering the WAM-V in different conditions, particularly to optimise the turning radius at different speeds.”
Inflatable and metal structures
The two pontoons are usually made from a Nylon fabric with a polyurethane exterior and a UV-resistant coating. “That’s all done by a company called Wing Inflatables that we’ve been working with since the Proteus days,” Gundersen says.
“The Proteus’ inflatables had six individual chambers, three of which contained a 300 gallon fuel bladder. That allowed a lot of fuel to be securely contained in a pressurised hull, and by using the air pressure in the hulls you could smoothly transfer fuel back to the day tank [a dedicated tank typically sitting between a bulk storage tank and an engine, into which fuel is pumped or gravity fed for consumption by the engine], without needing a dedicated fuel pump.”
The geometry of each pontoon is intended to lend the WAM-V towards riding on top of waves, rather than ploughing through or piercing them. That enables it to navigate through rough sea states and over very short, steep waves while minimising any loss of forward momentum and any severe movement of the central tray.
Naturally, the shape and materials can vary between users. Mehlman notes for example that Hypalon hulls have proven more popular among the company’s European customers.
The metal parts used in mounting the WAM-V’s thrusters – along with any others likely to be submerged, depending on the use case – are typically made from a 5000-series aluminium. 6061 aluminium with a Type III hard anodising coat treatment is used for all the metal components above the waterline, such as the tray and legs, for corrosion protection.
“Dr Conti has a particular love of titanium and its mechanical properties, so almost every WAM-V has at least one titanium part,” Mehlman adds.
“Our modularity also allows us to try different materials and swap metals or fastening techniques where we can, such as different grades of aluminium within the acceptable series, or doing a weld in place of a rivet, or vice versa. That means we can be flexible with materials so long as we keep the primary concept of the articulating structure on top of the inflatable hulls.”
Assembling and disassembling the WAM-V relies mostly on tool-less quick connect/disconnect devices, including the fuel lines and HV and LV connectors, with only a 13 mm box wrench needed for the battery cable. Multiple pins are found at each mounting point (such as for payloads and thrusters) to prevent any section hingeing on a single failure point.
“And since the WAM-V 22 is quite large, when the user wants to fold it for transportation, it uses servo actuators so that with the push of a button it folds itself electromechanically, rather than them having to go through a disassembly process,” Gundersen notes.
“It can also unfold the same way. Electromechanical locks secure the structure together after unfolding, it then runs a safety check to make sure all the locks are in place, and it detects any resistance to the fold so that if anyone’s finger for example should somehow get in the way, it immediately backs off.”
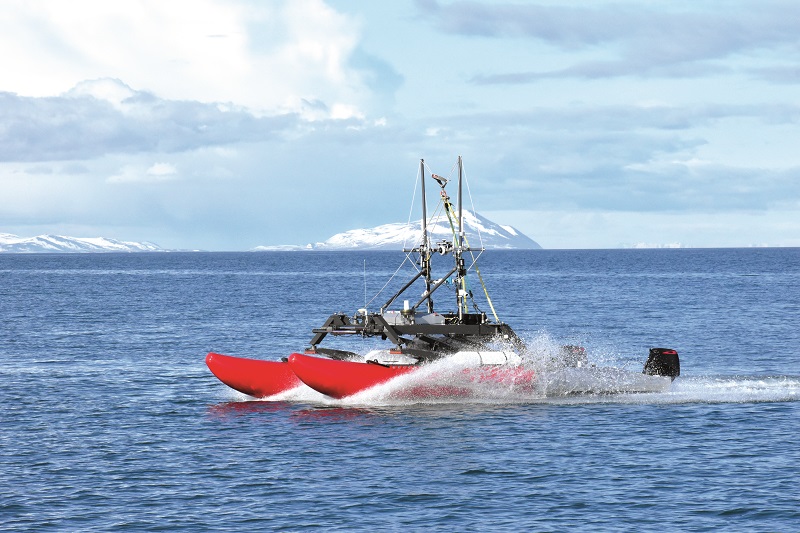
Computing and control systems
The WAM-V’s main computer can be rapidly configured for a wide range of connection pins, both digital and analogue. That is crucial to the USV’s modularity, as it allows any user to fit their preferred electronics, batteries, thrusters and so on.
“We use a card-based system, in which we can take an approximation of each end-user’s requirements and I can whip up a circuit card for that, and click it into place. Everything the user could need for a totally new or unusual instrumentation set is then ready,” Mehlman explains.
“It’s taken quite a bit more effort to configure our computer network to accept modular additions of new algorithmic blocks as easily as possible. But the card system is easier, and it’s meant for instance that when I wanted to install a new anemometer for wind readings, it took maybe a day to hand-solder a new card to integrate it.”
On the WAM-V’s computational limits, Mehlman estimates that around 500 W is the usual cap on power from the battery to the computer systems, and that about 1 m3 of volume is a safe amount of space to set aside. Around 500 Gbytes of SSD storage comes as standard, with three network ports and an environmental temperature tolerance of up to +70 oC, but again these are not sticking points for the USV.
Just as the computer system is flexible, so is the range of AI functions that can be installed. While object recognition, SLAM and sense & avoid are among those used by the WAM-Vs, smart following has formed most of the intelligent capabilities requested by the USV’s end-users.
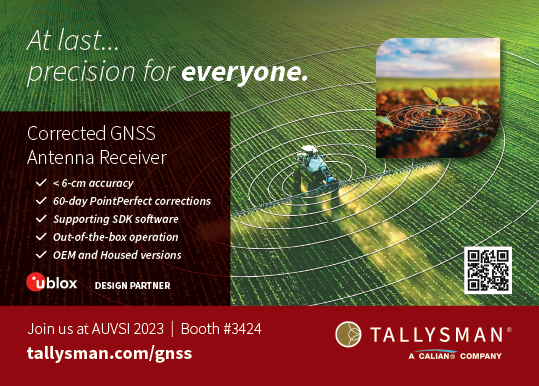
“That’s for the WAM-V following a crewed vessel as well as a UAV following the WAM-V,” Mehlman says. “We can output commands for the aerial autopilot to follow the USV’s GNSS position, with a specific offset or at a defined perimeter or geofence to keep it outside a certain distance or area. So the USV isn’t just a landing station but a comms link as well.”
The computer network’s architecture consists first and foremost as a control layer for real-time actuation of the propulsion systems and rudders, which tends to be run on a rugged and lightweight microcontroller with a high number of analogue and digital I/Os. After running through the microcontroller, the commands are delivered to a more powerful computer to process them into signals that the lower-level actuation ECUs can interpret and execute for precise control output.
“Neither the microcontroller nor the computer for actuation is ever a high-power system though; they won’t draw a lot of current or produce a lot of heat,” Mehlman says. “That’s most of our autonomy stack right there, but the computer will want to cross-reference waypoint and following information with data from other computational systems, such as camera, Lidar, sonar and GCS systems, and that happens through our IP network.
“People talk about TCP and IP as though they’re joined at the hip, but you don’t usually want to control a robot over TCP; UDP is the preferred layer. But payload connections can be done over TCP, along with a transparent radio bridge so that our customers can see their payload data very easily in real time.”
To ensure a secure and robust network on board the USV, cables and connectors had to be selected and integrated for protection against saltwater incursion and ultraviolet radiation, both of which are severely detrimental to robotic and computer systems.
“On top of that, availability is a huge issue for how we work,” Mehlman says. “We can’t afford lengthy design lead times or supply chains with our connector or harness specs.
“Most of our LV systems are standardised M12 circular connectors, as they’re very easy to obtain from various sources, and naturally we like wet-mateable systems, but those suffer from supply chain difficulties, so we often avoid them.”
The HV connection systems are highly dependent on exact voltages, but all of them are IP68-rated as a hard requirement for approval, to ensure full protection against saltwater ingress.
And for both the LV and HV networks, materials in cable jackets and plugs are also selected to ensure survivability against UV light, which inherently breaks down polymers over time. That is especially concerning in the marine environment, as UV rays come as a reflection from the water as well as directly from the Sun.
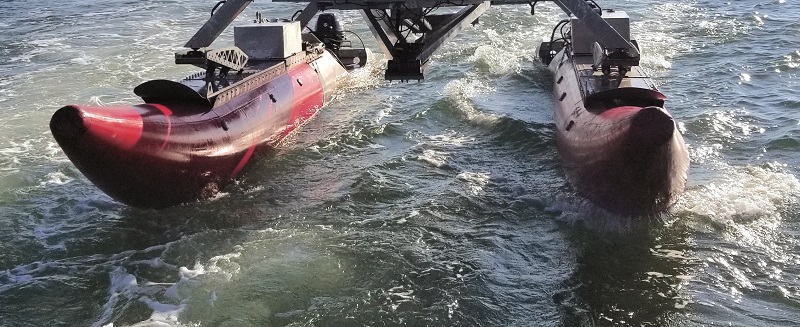
Comms and interoperability
The flexibility of the WAM-V’s engineering philosophy is such that several different solutions have been used as the primary radio for vehicle and payload data transmission. These include Kongsberg Maritime’s MBR (Maritime Broadband Radio) as well as radios from Microhard, Silvus and Rajant. MAR does not want to be limited to a single system so long as customer requests continue to be so varied.
In addition to running over satellite and cellular networks, it is also now possible to use Starlink Maritime for over-the-horizon command and control. At the time of writing, MAR was demonstrating the control of a WAM-V using Starlink for the US Navy.
A secondary radio for remotely operated functions is typically installed alongside the primary radio for tasks such as control hand-off from one operator to another, in ship-to-shore mission patterns or other arrangements.
A wide array of antennas have been integrated and used on the comms mast on the central tray, including fixed omnidirectional systems and gimballed directional antennas.
A critical objective of the comms mast’s design (whether arched or pole-shaped), as well its antennas, is sufficient height. As the WAM-Vs and their GCSs (on crewed vessels or in harbour offices) can become separated by considerable distances during their missions, it is not impossible that the Earth’s curvature will eventually come between the line-of sight RF links needed for connecting the USVs as well as any crewed or uncrewed assets they are teamed with.
“Although the WAM-V’s height is useful for maintaining that link, we consult with experts at the radio vendors, as well as the GNSS vendors, to work through any issues we might get with our antennas,” Mehlman says.
“As a result, our ideal network configuration is maintained in a way that any vehicle in the swarm persistently lets every other asset know where it is, not just all the uncrewed vehicles connected over our radio network but also any person with a connected GCS or similar portal.
“That includes AIS information if a user has elected to include an AIS transponder in their USV. To be honest though, we don’t consider an AIS data point on the navigational chart to be as reliable as one inside our network, because you’re relying on the AIS operator on that other vessel to have mounted their antenna correctly.
“But we do recommend our users have us integrate AIS so they’re putting out that information for third parties and for general maritime safety.”
One or two industry-standard ruggedised laptops are generally provided with a WAM-V order, which in turn are installed in crates where extra saltwater and UV protection is needed, such as when the USVs are likely to be operated from a beach or a small vessel. In most cases, one computer is used by an operator for in-the-loop monitoring as well as command & control where necessary, and a second computer is used by an analyst for real-time scrutiny of payload data.
The GCS software has been developed in-house, and can be separated into two interfaces. One is a pre-mission planning chart system that can be customised using interface configuration tools or importing mission plans prepared previously using MAR’s software. The other is an in-mission live telemetry display UI, where parameters such as vehicle speed, GNSS quality, engine health and actuator diagnostics can be viewed.
“Naturally you can also use the planning chart to change your mission’s waypoints or payload usage on the fly, and check live telemetry before launching the WAM-V to confirm the health and correct performance of all your subsystems, as well as seeing your camera, sonar and inertial data in real time,” Mehlman adds.
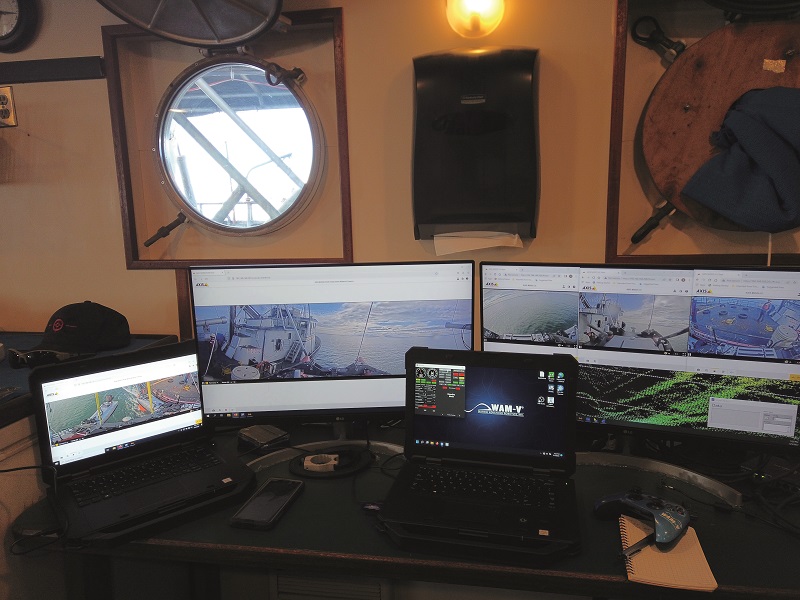
GNSS
To prevent excessive chatter from the control system affecting the performance of the payloads, and to maximise control system reliability, the payload is decoupled from the command & control and run on a separate computer.
That means for instance that two GNSSs are usually installed on the WAM-V: one for the navigation system and the other for geostamping the payload data. Mehlman says, “We go with one large and powerful GNSS to get very precise data from the latter, and then for the main computer’s navigation functions we actually get away with using a smaller, more right-sized system.”
The larger GNSS can also be used for navigation if more precision is required. This tends to be a POSMV from Trimble Applanix, chosen for its reliability although it will often be disengaged during transit to save energy. The smaller navigation system is from VectorNav, SWaP-optimised and ruggedised as it is for various defence and industrial tasks.
“We have also performed missions where the smaller VectorNav GNSS-IMU provided readings for both navigation and sensor referencing,” Mehlman says. “We try to be flexible, so we’ve used navigation systems that are serial-based, Ethernet-based, the list goes on; there’s no real limit.”
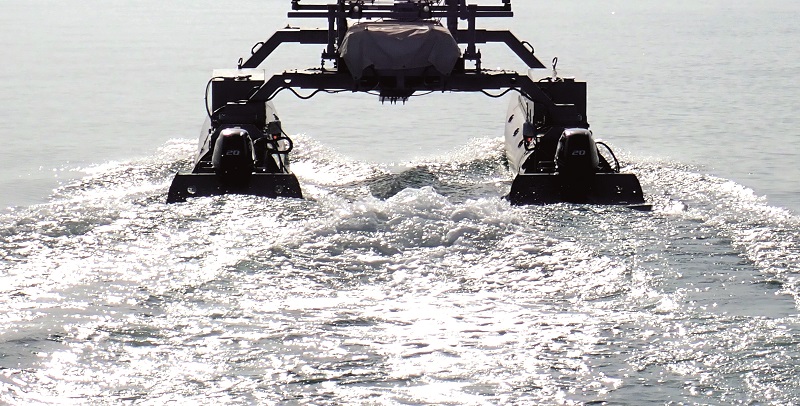
Power
Unlike the 16 and 8 versions, which are fully electric, the WAM-V 22 is typically fuel-powered. As indicated, the propulsion system is as modular as the rest of the craft: MAR uses Torqeedo gasoline outboards on the WAM-V 8 and 16, while systems from Honda and Suzuki have been used on the WAM-V 22. The target is for two 20 or 30 bhp thrusters – one for each pontoon – integrated at the back of the USV.
“The computer system itself is agnostic. No matter the thruster pod, it’s running the same comms protocol,” Mehlman says.
“On the 22, we tend to install the fuel tank on the skis, its size depending on the size of the payload. The USV has a flotation budget, so if you want to carry say a heavy ROV, that weight needs to be taken out from elsewhere, such as the fuel.
“If you’re just carrying a light water-quality sonde though, then obviously a lot more fuel can be carried. For instance, the vehicle we had running in Alaska had about 40 gallons [151 litres] of fuel, which was enough for about a day of surveying.”
Each outboard on the WAM-V 22 typically integrates a 15 A alternator, and MAR tends to use the one shipped with it, rather than using a new one and potentially introducing a new error. The company has also installed marine generator sets onto the WAM-V 16 to get more range when needed, adding to the modularity of the powertrains.
In addition to the fuel serving as the primary energy storage, one battery pack provides the regulated power output needed by the payloads and other electronics. This has included instances of charging Planck’s Shearwater UAV while it was sitting on top of the WAM-V, using conductive or inductive receptacles. A separate battery is used for starting the engines.
Although the BMS varies in its combination of in-house and third-party designs and programming aspects, a consistent role for it is to isolate those two packs and their respective buses from each other.
“One important reason for this BMS role in each WAM-V is ensuring the safety of the alternator – we don’t want to have to be constantly spinning the alternators, as that will lead to damage,” Mehlman says. “We might also be using different cell chemistries in each battery. The starter battery is almost always going to be some kind of lead-acid device, or it can be larger for more back-up energy if needed.
“Meanwhile, the payload battery will often be a lithium-ion system, or even a nickel-metal system depending on what’s necessary or available. The BMS therefore manages each pack separately and isolates them to prevent mismanagement.”
Payload integration
At maximum loading, the WAM-V 22 can carry 270 kg of payload and
333 litres of fuel. If a user were to
add an extra 50 kg of fuel then the payload would need to be capped at 220 kg to maintain stable flotation.
As noted, the payload mass can be distributed about the tray, hulls and ski as needed, while the RSM comes in different versions to account for the sensors and their sizes that end-users might want to use.
For instance, multi-beam sonar arms have been installed, and these are mounted on the back of the tray along with a linear actuator, with the sonar integrated at the front. This results in a downwards-rotating motion of the arm, from a tucked position against the underside of the tray, to sticking vertically downwards with the sonar until sufficiently submerged for producing clear survey data.
With other payloads, such as a glider or sub-bottom profiler, a mechanical linkage couples the system to the tray until disengaged, at which point the subsystem drops into the water. Telescopic arms have also been used, along with other systems as appropriate.
Also, through the dedicated battery, payload power can be remotely shut off or reactivated, to conserve power or if a sonar, Lidar or similar fails and needs a hard reset.
“Failures tend to be rarer with our USV design than in a typical monohull aluminium vessel,” Mehlman adds. “We’re not hitting the waves anywhere near as hard, which translates all the way down the stack. Payloads and other customer equipment is very well protected, both by that and by the WAM-V having a lot of integration space for sensors to be installed somewhere far from where waves will be striking.”
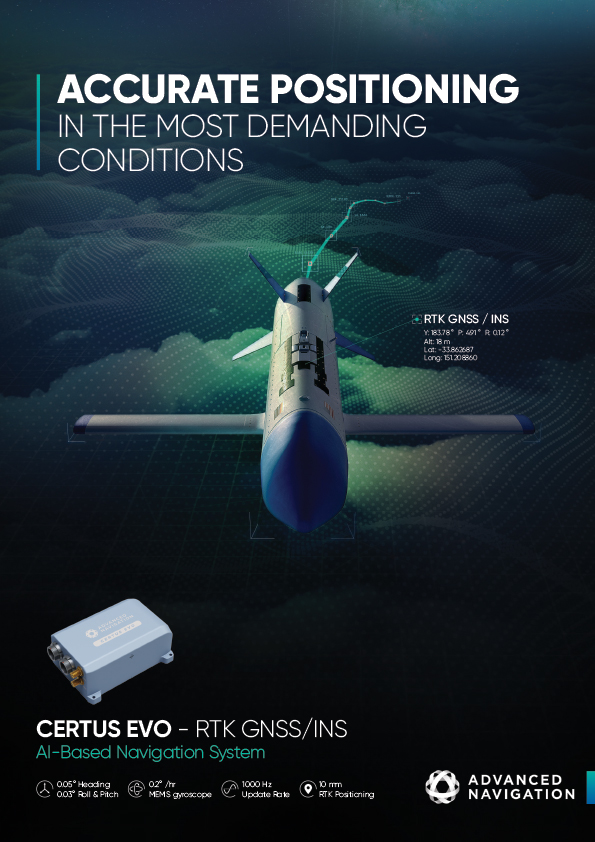
Future plans
In addition to manufacturing and selling the WAM-V 8, 16 and 22, MAR has been developing its Robotics-as-a-Service (RaaS) business model, particularly for customers who need USVs on a less predictable, ad hoc basis. So, as well as selling WAM-Vs, it anticipates increasingly leasing or operating units on behalf of ocean data customers.
Further use cases of simultaneous UAV and UUV deployments from the USV will also be explored, with illegal fishing missions having showcased the benefit of having simultaneous aquatic and aerial assets working together for persistent maritime security awareness as much as repeatable marine infrastructure inspections.
Specifications
- WAM-V 22
- Length: 7 m
- Beam: 3.66 m
- Draft: 0.56 m
- Speed: Up to 20 knots
- Weight: 1134 kg (without fuel,oil or payload)
- Endurance: Up to 72 hours at 8 knots
- Propulsion: 2 x 20/30 bhp, gasoline
- Payload: 270 kg
- Fuel capacity: 151 litres
Some key suppliers
- GNSS: Applanix
- GNSS: VectorNav
- Actuators: Lenco
- Electric thrusters: BlueROV
- Electric thrusters: Torqeedo
- Gasoline thrusters: Honda
- Gasoline thrusters: Suzuki
- Radios: Kongsberg Maritime
- Radios: Microhard
- Radios: Rajant
- Radios: Silvus
- Satcom: Starlink Maritime
- Rigid inflatable hull sections: Wing Inflatables
UPCOMING EVENTS
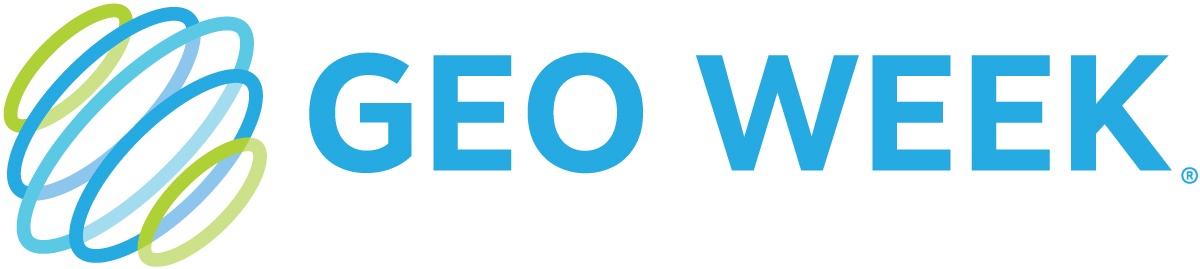
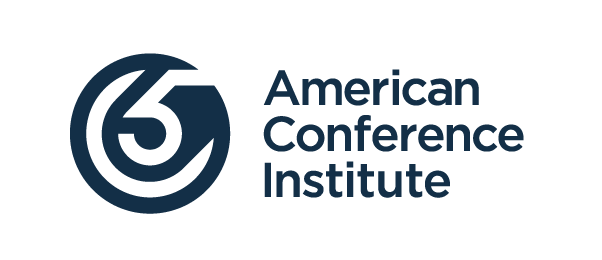
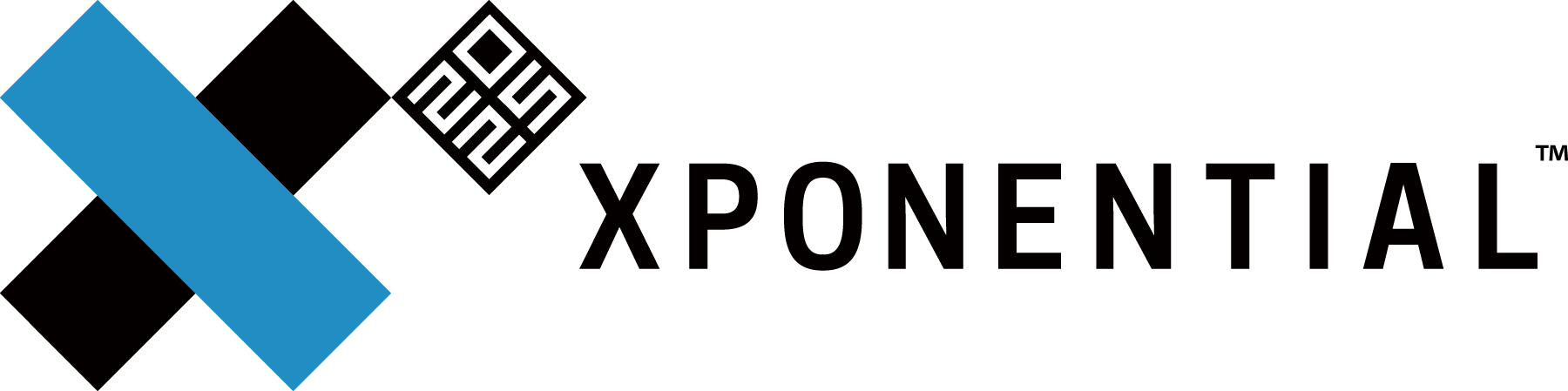
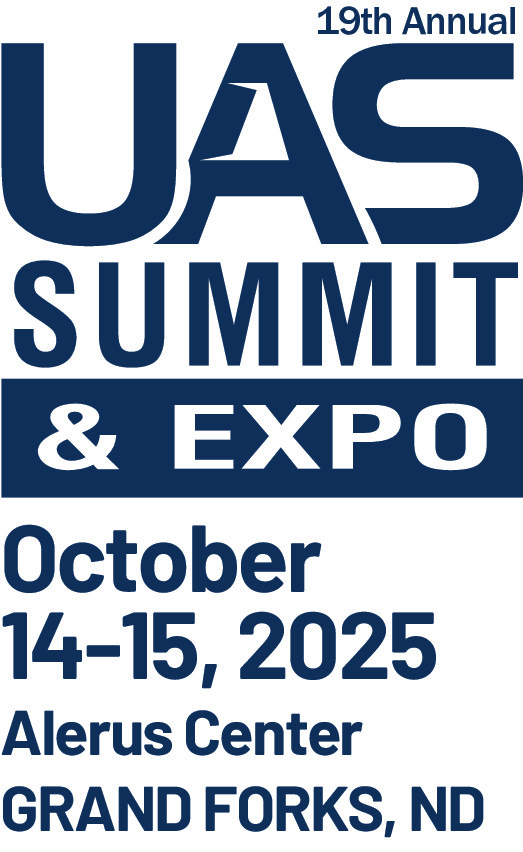
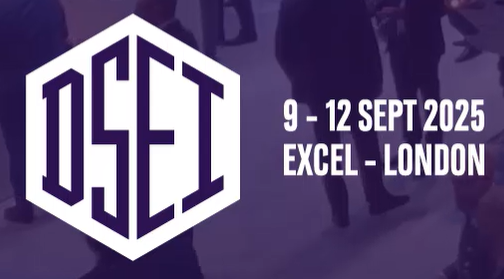
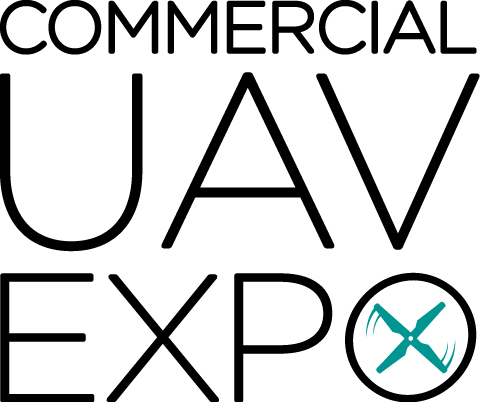
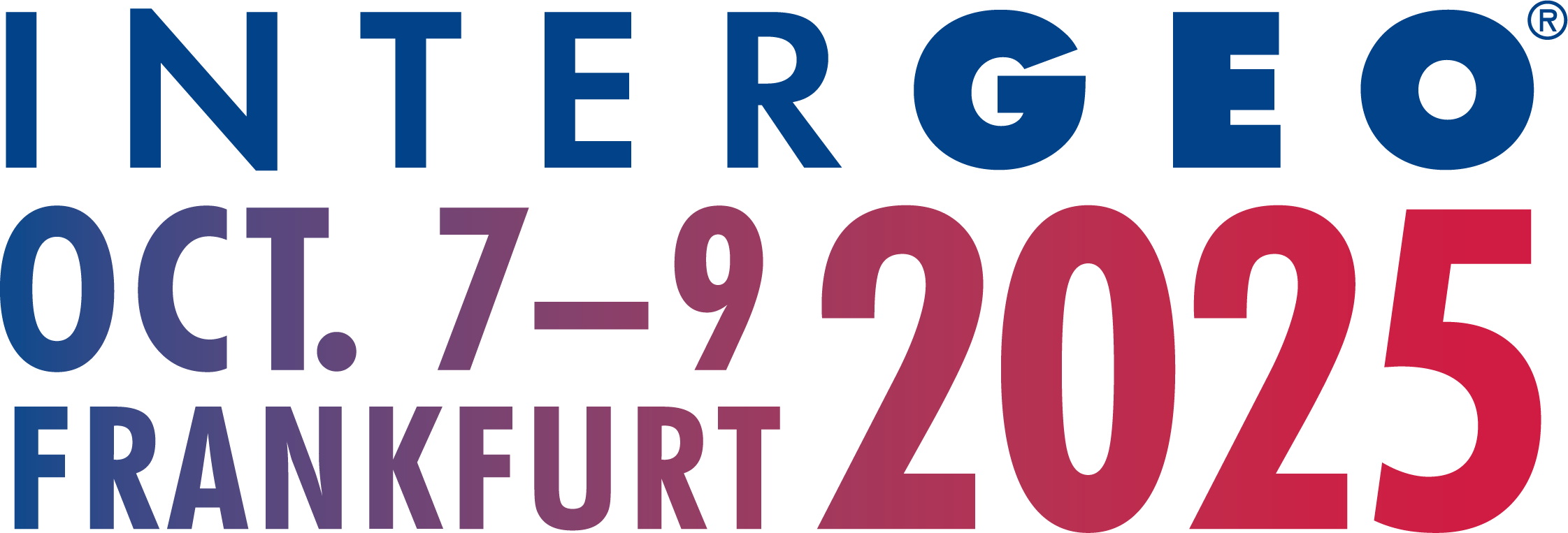
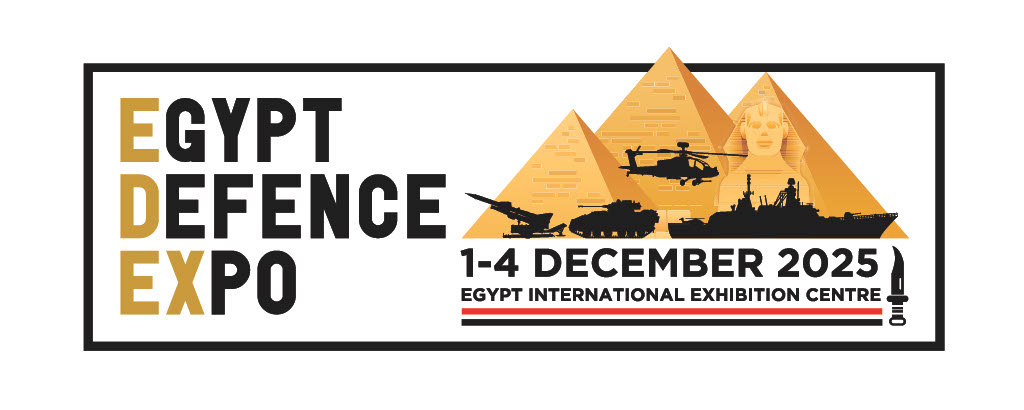
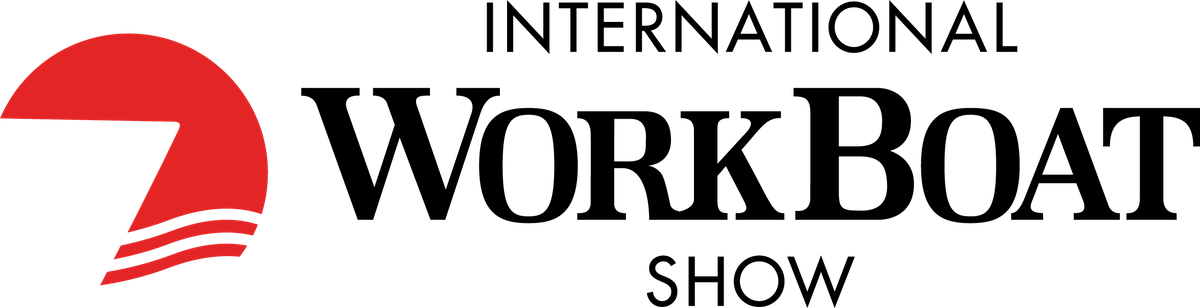
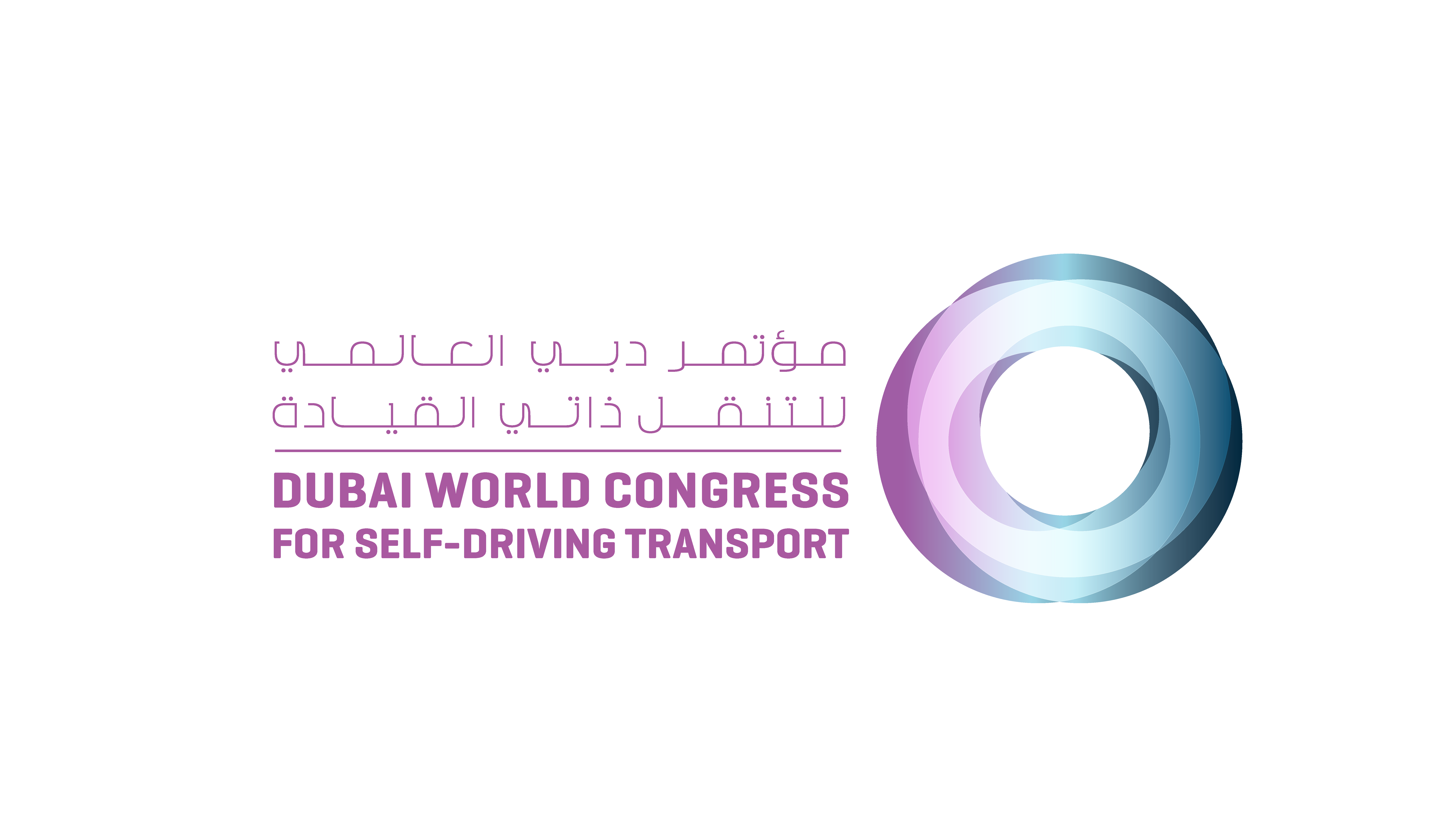
