CES 2024
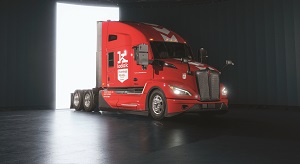
Nick Flaherty reflects on the myriad exciting products on show at CES, Las Vegas
The Consumer Electronics Show (CES) returned to Las Vegas, USA, for its 2024 edition, which ran from January 7-12 in Eureka Park over an exhibition area larger than 2.5 million ft2 – 15% bigger than the previous year’s show.
More than 4300 exhibitors presented their latest innovations for critical areas of tech advancement to the show’s attendees, who numbered over 135,000 and hailed from 150 countries, regions and territories.
Among the most prominent themes were AI, mobility and sustainability, and thus the exhibition floor yielded a plethora of novel solutions, presenting tantalising opportunities to systems integrators in the uncrewed and autonomous world, a selection of which we present henceforth.
Kodiak Robotics, which we previously covered with its 4th-generation, self-driving truck in our 48th issue (February/March 2023), attended CES 2024 to present its 6th-gen truck, slated for scaled deployment, including the company’s driverless operations between Dallas and Houston, which will commence this year.
The truck was showcased at Luminar’s booth, Luminar being Kodiak’s foremost Lidar supplier. The autonomous vehicle and its system architecture, which is transferable to other vehicle types via the Kodiak Driver ‘kit’, are designed with redundancy across all safety-critical functions.
These include: a redundant pneumatic braking system, consisting of three individual brake actuators that are simultaneously controlled by Kodiak’s proprietary software; a dual-redundant steering system using two redundant ZF actuators; a power system split into two completed, isolated subsystems for powering computers, sensors, actuators and so on (such that all safety systems can execute safe fallback amid failures); and Kodiak’s custom-designed, high-integrity Actuation Control Engine (ACE) system, which ensures the truck can be guided safely out of traffic should a critical system fail.
The 6th-gen truck has 12 cameras, four Lidars and six radars, with nVidia GPUs for high-performance sensor data-processing and fusion. The proprietary SensorPods (which resemble traditional wing mirrors, but house the sensors critical to real-time 360° perception) have been upgraded with two automotive-grade Lidars with higher resolutions than those we have previously featured, as well as two additional side-radar sensors for improved long-range object detection.
The SensorPods also integrate extra-bright hazard lights atop, for compliance with the autonomous trucking industry’s application for an exemption to Federal Motor Vehicle Safety Regulation 392.22. This standard requires traditional truck drivers to place warning devices on a roadway after a breakdown, but as driverless trucks cannot do this, the hazard lights will instead alert other drivers to the truck’s presence on the roadside (pending federal approval).
Lastly, the 6th-gen truck integrates microphones for detecting and identifying emergency vehicles or suspicious sounds that could represent a hazard, as well as redundant long-term evolution (LTE) links for robust communications with Kodiak’s redundant command centres in Lancaster, Texas and Mountain View, California.
Kodiak plans to integrate a next-generation Ambarella CV3-AD AI domain system and organisation controller (SoC) into the truck later this year, to improve its sensor and machine-learning capabilities. This will also enable Kodiak to transition to a high-volume SoC solution suited to high-end AI efficiency and performance.
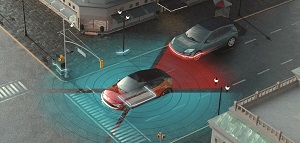
Texas Instruments (TI) debuted a new range of semiconductors, aimed at automotive safety and intelligence.
The first is the AWR2544, a 76-81 GHz millimetre-wave radar-sensor chip, designed for satellite radar architectures. This means that radar sensors are arranged for 360° perception around a vehicle and output semi-processed data to an onboard central processor, making the radars ‘satellites’ in a centralised AI system, which then handles decision-making outputs following sensor-data fusion.
The AWR2544 also integrates TI’s launch-on-package (LoP) technology, which involves integrating a 3D waveguide antenna on the opposite side of the PCB from the sensor chip, reducing the overall size of the sensor by up to 30% and enabling extension of the sensor range beyond 200 m.
A 300 MHz Arm Cortex-R5F is used as the AWR2544’s CPU, with Ethernet, I2C and SPI interfaces available in the system, along with a radar hardware accelerator, and four receivers and transmitters.
The other two new semiconductors are the DRV3946-Q1 integrated contactor driver and the DRV3901-Q1 integrated squib driver (a detonator for applications such as igniting the explosive charges that inflate vehicle airbags) for pyro fuses, which are programmable driver chips with built-in diagnostics, and are also designed to support functional safety for battery management and powertrain systems.
The DRV3946-Q1 measures 9.7 mm x 4.4 mm, features 28 pins, and is designed as a closed-loop, dual-channel solenoid driver, with up to 20 kHz PWM communications.
The DRV3901-Q1 measures 7.3 mm x 4.9 mm, has a similar pin configuration and, in addition to being a squib driver, it can be used for battery disconnect units and junction boxes. Like the DRV3946-Q1, it comes with documentation to aid system design for compliance with ISO26262, up to Automotive Safety Integrity Level (ASIL) C.
CJC Motor exhibited a range of its Brushless DC electric motor designs for high-voltage power output in low-speed, high-torque applications.
Key design points include rotors designed for magnetic-field optimisation that minimise cogging torque to operate smoothly without jitter, regardless of speed. Accurate motion is further aided through the integration of high-resolution encoders and precise control algorithms for translatíng control commands into exact motor movements.
The company’s recommended systems for UAV propulsion include its BL2206, which is designed with a 12N14P slot/pole configuration and has a continuous power output of slightly more than 120 W, and its BL2806, which has a similar magnet and winding configuration, is compatible with 12 in (30.48 cm) propellers and produces just over 150 W continuously. Both systems have a MTBF of at least 500 hours and are built with IP45-rated housings.
CJC also showcased its motor controllers, which embed the company’s high-speed, sensorless, field-oriented control (FOC) algorithm to potentially enable in excess of 150,000 rpm, along with added position precision through closed-loop control and a PID simulation algorithm optimised for fast throttle response.
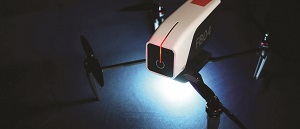
South Korea-based Pablo Air showcased its UrbanLinkX platform for urban air mobility (UAM) traffic management. The software solution is designed for efficient management of UAM vehicles, integrating functions for reducing traffic workloads and mitigating operational risks.
Additional key functions in the platform include subroutines for submitting flight plans for approval by traffic authorities, as well as for managing traffic flows and airborne communications quality.
Data on aerial communications quality is visualised in real time via 3D graphics to enable connectivity (and optimisation) between aircrafts and base stations, and corridor-density metrics are similarly leveraged to inform safe UAV operations.
Pablo Air also unveiled its latest performance UAV, the FireBird 4 (FB04) quadrotor at CES 2024. Its exact specifications have yet to be divulged publicly, but the system is the smallest multirotor in the company’s portfolio (alongside its medium-sized BigBird F-3 UAV, large BigBird F-2 UAV and Waterbird aquatic drone), and principally intended to serve in pyrotechnic air shows.
Panasonic Automotive Systems showed its Neuron High-Performance Compute (HPC) system, aimed at satisfying growing demand for software-defined vehicle advancements across mobility.
Neuron has been designed to integrate and aggregate varying specialised computing zones across CPUs, GPUs and other device types around a centralised processor. Computing is then distributed by the central processor across the specialised zones for a wide range of functional use cases.
The design enables scaling of performance to take advantage of new hardware and software solutions as they become available. For added thermal efficiency, Neuron integrates a liquid cooling system capable of dissipating up to 1 kW of heat.
Additionally, Panasonic Automotive’s VERZEUSE cyber-security suite is installed for robustness against cyber attacks through network data and storage monitoring, and a multi-tiered verification process performed against a trusted source.
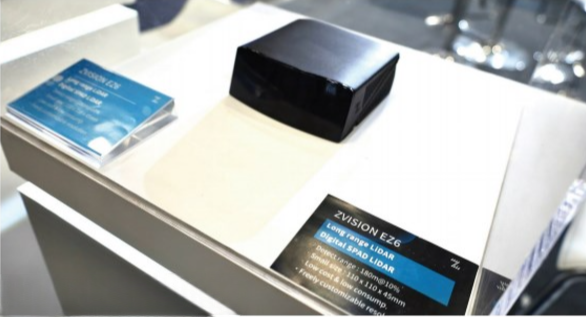
ZVISION launched the EZ6, its latest single-photon avalanche diode (SPAD) Lidar, intended as a cost-effective and hence accessible Lidar system for the automotive industry.
SPAD’s avalanche breakdown is advantageous for timing the arrival of photons, making them increasingly used for Lidar and other 3D imaging methods as SPAD Lidars come with gradually higher resolutions.
The EZ6 has been designed as a 192-channel system to achieve detailed sensing and high-density point clouds. Its pulse output is optimised around forming points into a uniform and structured cloud, minimising engineering adaptation expenses and improving the identification of low-lying obstacles.
It is also embedded with dirt-detection algorithms, to maintain stable point-cloud generation without anomalies, even while exposed to small quantities of dirt, and to report dirt-related information on request. This is a critical challenge in Lidar-based, autonomous vehicle operations, where dirt can cluster on sensor windows and cause faults.
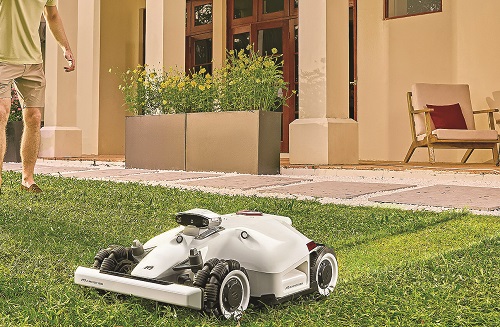
MAMMOTION unveiled its LUBA 2 AWD series of autonomous robotic mowers, which are variations on a UGV design, measuring 690 x 513 x 273 mm and weighing 17 kg. They offer connectivity over wi-fi, Bluetooth and 4G.
The LUBA 2 AWD is engineered to overcome numerous weaknesses of other autonomous mowers. For instance, its all-wheel-drive system enables it to cross 38° inclines, uneven ground, muddy ruts and tree roots without losing momentum, which would confound regular mowers.
It integrates stereo cameras, ultrasonic radars and physical bumpers to detect obstacles as small as 1 in in height, enabling it to manoeuvre around animals, garden hoses and routine hazards without its mowing being interrupted. Positioning can be performed using the vision sensors or via RTK GNSS.
The battery-electric system runs for 180 minutes between charges, with a typical charging time of 120 minutes. A version with a smaller battery is also available, providing 120 minutes of endurance and a 90-minute charging time.
Schaeffler Group attended CES to exhibit a range of its latest motion solutions for automotive, industrial and aerospace applications.
Among them were a number of electromechanical actuator systems aimed at automated driving and intelligent steering, including its RT1-T precision-strain wave-gear (also known as a harmonic drive) unit for robotics fields needing high-performance sensing of force and torque.
The RT1-T integrates specific microelectronics, embedded AI, and proprietary coating for precisely measuring torque within the joint actuator without affecting torsional stiffness.
Schaeffler also demonstrated its CASM-series electromechanical actuator for agricultural and construction systems, designed as an energy efficient and modular alternative to conventional hydraulic cylinders.
Also showcased were the company’s latest SWaP-optimised electric axles, along with electric motors featuring its latest cooling concepts, magnet-free options and stator winding configurations, with Schaeffler’s silicon-based solid-state batteries.
Its electric-powertrain innovations were displayed in a battery-electric truck, and in an eVTOL craft engineered by Austrian company FlyNow, capable of lifting payloads up to 200 kg.
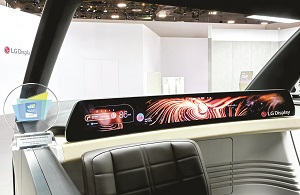
LG Display showcased a series of large automotive displays, including one it claimed to be the world’s largest, aimed at future mobility solutions.
This display measures 57 in (144.78 cm) and is intended as a Pillar-to-Pillar (P2P) LCD, meaning it covers the full length of the dashboard, from the driver’s seat to the front passenger’s seat.
The 57 in P2P screen has a maximum curvature radius of 3,500 mm and is intended to provide various infotainment functions. These include HD displays of driving information, climate controls, movies or games, with touch responsiveness optimised via LG Display’s proprietary In-Cell Touch technology.
Additionally, the P2P LCD functions in temperatures ranging from -40 C to 85 C, unlike conventional displays.
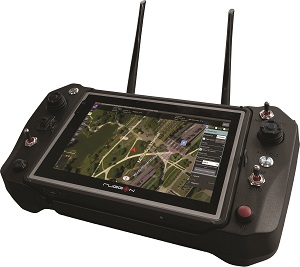
Ruggedised mobile solutions manufacturer RuggON launched its new Drone GCS for UAV control and monitoring. The product, built around the company’s LUNA 3, an 8 in (20.32 cm) rugged tablet, has been developed for compatibility with essentially any UAV, while also providing video feedback, GNSS positioning and tracking.
Video is aided via an embedded low-latency video-decoder software program, enabling real-time, high-resolution viewing and data collection.
The GCS’s standard data link will enable in-the-loop control over distances of up to 30 km, and the installation of joysticks and toggles about the screen enables tangible and intuitive control for users. It is designed to MIL standards for drops, shocks and vibration resilience under extreme conditions.
The LUNA 3 tablet runs as standard on an Intel Core i5 processor (1145G7E) with Intel Iris Xe graphics and Windows OS. Its display is sunlight-readable, facilitating night and stealth modes for all-day availability. A touchscreen option is available. It also comes with Ethernet, optional wi-fi 6 connectivity and 4G LTE.
In other power and energy advancements, Molicel was on hand to showcase its new ‘ultra-high power’ INR-21700-P50B cell.
As the product designation implies, it is a 21700 form-factor Lithium-ion cell, which comes with Molicel’s highest-ever gravimetric energy density of 260 Wh/kg (714Wh/l in volumetric energy density), with each cell containing 5 Ah of energy at capacity.
It can discharge at a power output of at least 400 W, meaning it has Molicel’s highest power-to-energy ratio. It is engineered with fast charging in mind, with a C-rate of 5 (implying 12 minutes of charge time from empty to full).
Leopard Imaging highlighted its Hawk Stereo Camera Hawk and Owl High Speed Camera, two products powered by nVidia’s Jetson AGX Orin solution, and they were demonstrated at the show in Segway Robotics’ Nova Carter UGV.
In the Nova Carter integration, the Hawk 3D stereo camera provides depth-sensing capabilities for optimal object detection and obstacle avoidance, while the Owl cameras give it a 360° surround view for situational awareness.
The nVidia Jetson AGX Orin system is installed in Leopard Imaging’s AI Box, which processes camera data on the UGV in real time for decision-making and adaptive responses in dynamic environments.
The Hawk system has a horizontal field of view (FoV) of 121.5° and a frame rate of 60 fps at 1920 x 1200 resolution. It integrates an IMU for velocity aiding, and its depth performance includes a Z-accuracy of ±2% at 6 m distance and an 80% depth FoV. The Owl, meanwhile, has a horizontal FoV of 202.0° (± 3°) and a frame rate of 120 fps, also at 1920 x 1200 resolution.
Leopard Imaging also unveiled its new LI-AR0830-YUV-MIPI and LI-AR2020-MIPI embedded cameras, which use Onsemi’s AR2020 and AR0830 sensors for capturing images in either linear or enhanced dynamic range modes with a rolling-shutter readout.
The aforementioned Nova Carter UGV was also being exhibited by Segway Robotics at the show. It has been produced as an autonomous robotic development platform to provide versatility and customisation options for uncrewed ground system engineers.
The Nova Carter was co-developed with nVidia. It is built on the nVidia Isaac AMR platform to empower the development of advanced perception (and hence operations in complex environments) for robots via AI and accelerated computing. Developers can use GitHub repositories for the nVidia Isaac ROS to begin working with the UGV.
It weighs 51.2 kg, measures 722 x 500 x 556 mm, and can operate in climates from 0-35 C. The system is powered by a 1 kWh battery and can operate for just over eight hours (with five hours of charging time).
Atop its hull is an XT-32 3D Lidar from Hesai, with additional 2D Lidars at its front and rear, and added 360° visual awareness, with both stereo and fisheye cameras installed around the perimeter of its body.
Supernal LLC, the advanced air mobility (AAM) subsidiary of Hyundai Motor Group, unveiled its S-A2 eVTOL vehicle concept. The four-passenger aircraft is being developed by Supernal to meet commercial aviation safety standards and achieve affordable manufacturing along a roadmap towards market entry in 2028.
The S-A2 flies on a distributed, electric propulsion architecture, featuring eight tilting rotors that provide both vertical and forward thrust (as well as redundancy and zero-emissions operations).
Its hull is designed with a V-tail, as well as wings for lift generation and nacelles, which mount the tiltrotors. The aircraft is expected to cruise at 120 mph (193.121 kph) at an altitude of 1500 ft (457.2 m), and hence satisfy city-length flight requirements of 25-40 mile trips (40-64 km) at entry into service.
The vehicle will additionally emit 65 dB in its VTOL phases of flight and 45 dB while cruising horizontally, hence avoiding excessive noise for passengers.
Supernal anticipates leveraging Hyundai’s mass-production facilities to optimise the cost-effectiveness and quality with which the S-A2s are manufactured (and aid in its efforts to achieve certification).
Ongoing research is being conducted into battery upgradability and interior modularity, with Hyundai Motor Group’s automotive designers having assisted on S-A2’s aesthetics for a clean, intuitive and comfortable interior.
Lenovo Vehicle Computing announced it has been given ISO26262 certification to Level ASIL-D for functional safety management systems from TÜV Rheinland.
The standard is becoming increasingly well known as a requirement for showing minimised risks of electrical and electronic system failures in vehicles, particularly autonomous, connected and electrified vehicles.
ASIL-D, which is the highest level of ISO 26262, comes with the most stringent development process requirements; achieving it means a firm has established a comprehensive development process that is compliant with the highest automotive functional-safety requirements and industry standards.
A month earlier, Lenovo unveiled its vehicle computing roadmap, featuring three new automotive intelligent controllers, based on the nVidia DRIVE Thor AI platform. These are the Lenovo XH1, intended as a central computer unit, the AH1, which will be a Level 2++ ADAS domain-controller unit, and the AD1, a Level 4 autonomous-driving domain-controller unit.
XING Mobility exhibited and discussed its next-generation immersion-cooling technology for battery thermal management.
Rather than using conventional and well-established air or liquid cooling systems, this approach immerses battery cells in a special dielectric fluid, engineered for optimal heat transfer. It surrounds and envelopes each battery cell, thereby facilitating a uniform and rapid rate of cooling around them.
As part of its display, XING also showcased its Immersio cell-to-pack architecture, which can be engineered with a gravitational energy density of up to 200 Wh/kg, as well as a volumetric energy density of up to 400 Wh/L.
The Taiwanese company also exhibited the Immersio XM25, which it positions as the first mass-produced, immersion-cooled battery pack, with each XM25 unit storing 25 kWh of power.
XING Mobility also showcased the results of a three-nail penetration safety test, which it conducted on an Immersio pack at 100% state-of-charge (SoC). The immersion-cooling system successfully contained the resulting thermal runaway and prevented fire propagation.
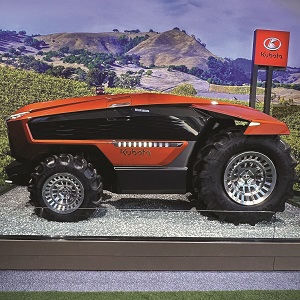
Kubota unveiled its New Agri Concept, an all-electric, multi-purpose vehicle, which is being developed as part of the company’s vision for autonomous and AI-powered solutions for residential or small-acreage growers.
Detailed specifications are not yet available, but key aspects of the technology will include real-time remote monitoring, use of AI to identify crop problems, automatic data aggregation, and a range of grower work functions to address the labour challenges being faced by the agricultural sector.
The New Agri Concept will feature six independent drive motors and a standard, three-point hitch; the latter enabling it to use a wide range of existing farming implements for tasks such as mowing and tilling.
It will also run on an electric powertrain for quiet operation in residential areas or at night, with a battery that is able to fast-charge from 10% to 80% within six minutes to minimise downtime between stretches of work.
UPCOMING EVENTS
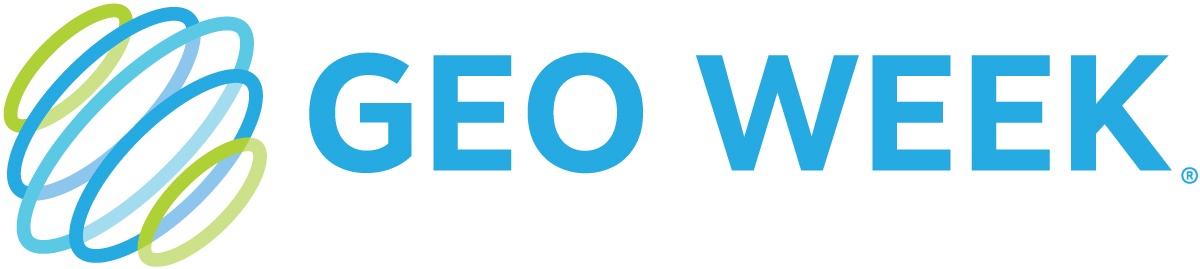
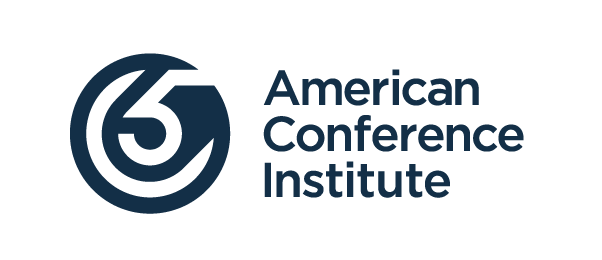
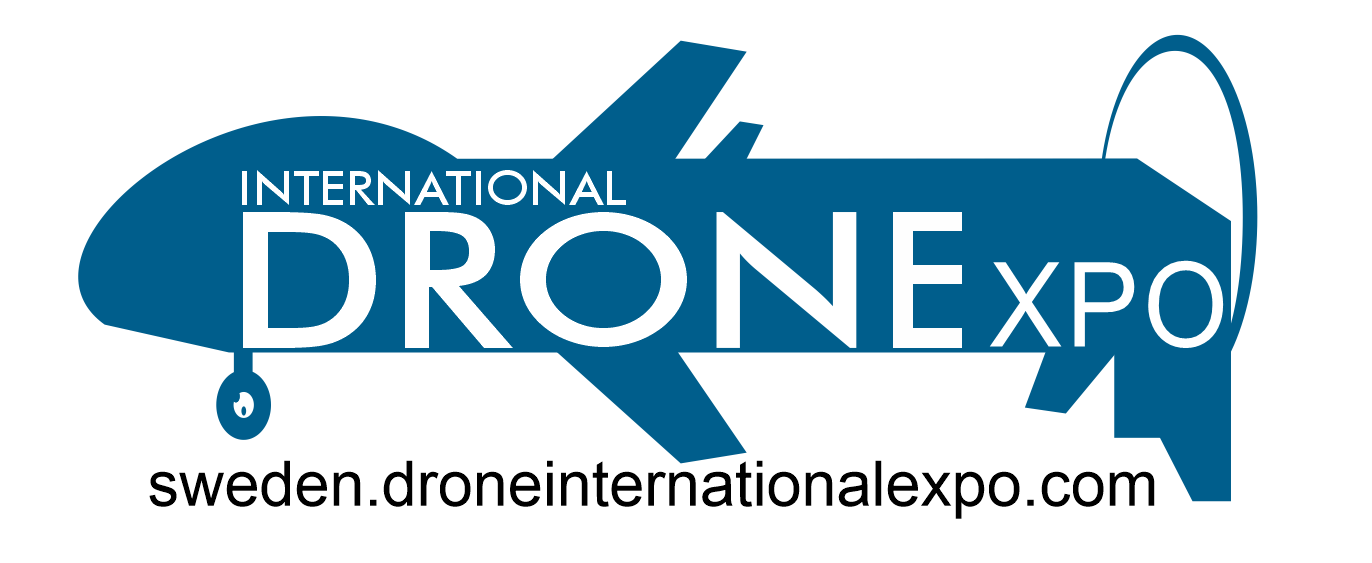
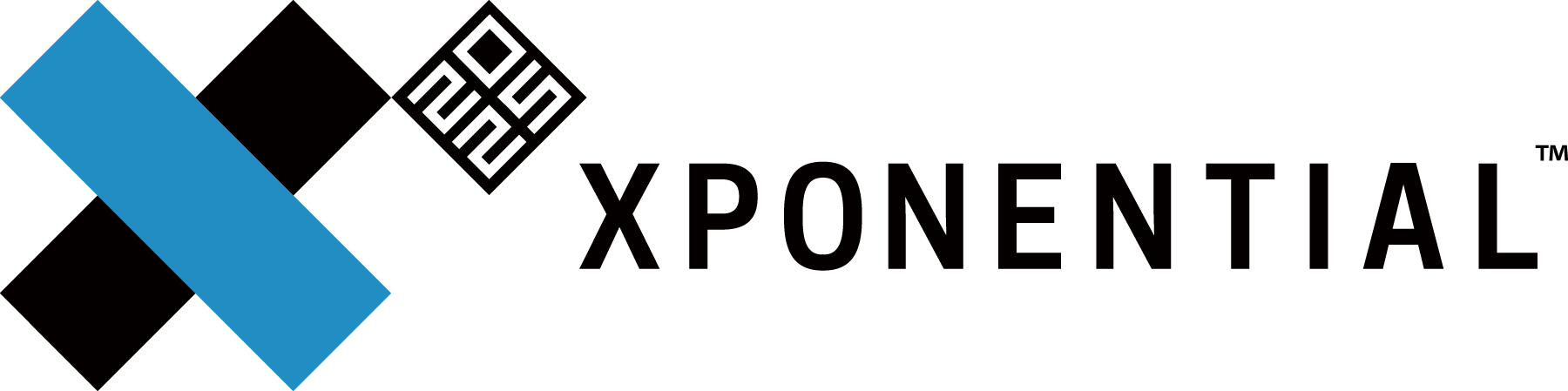
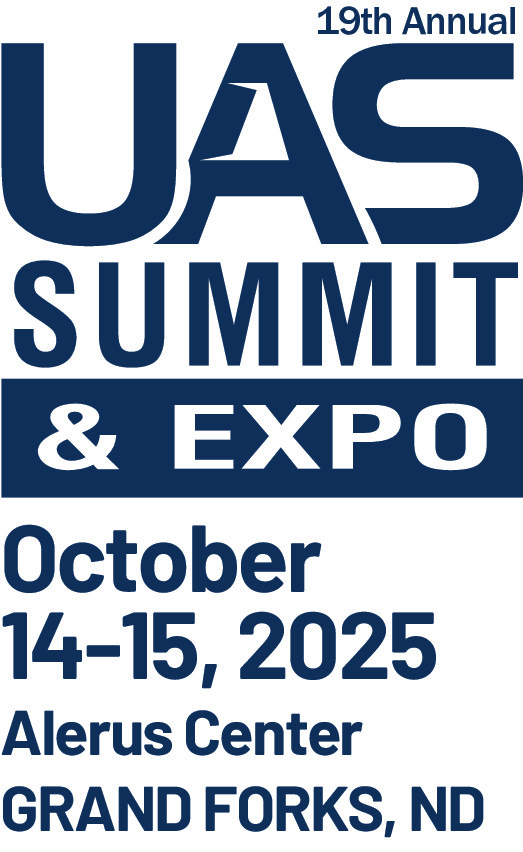

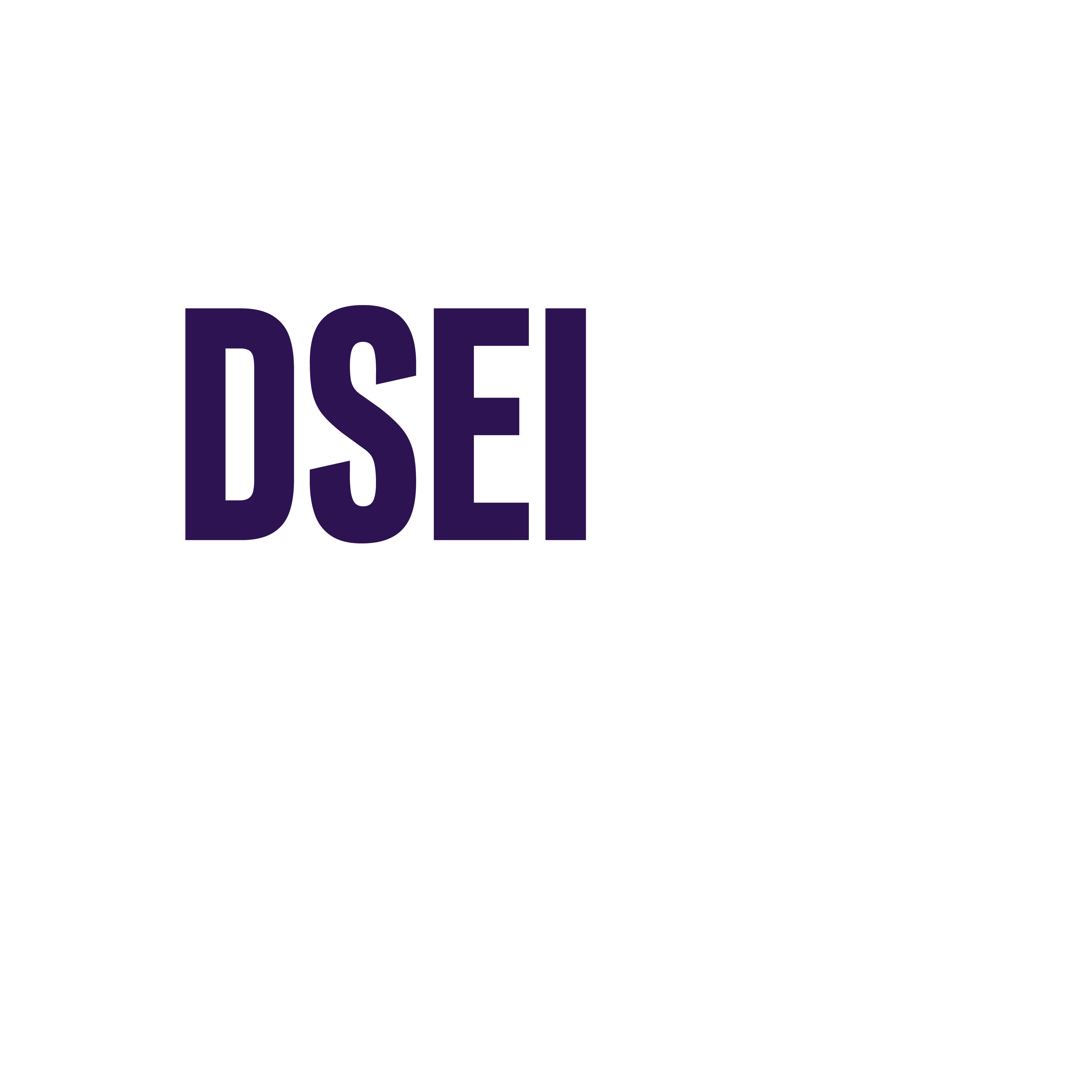
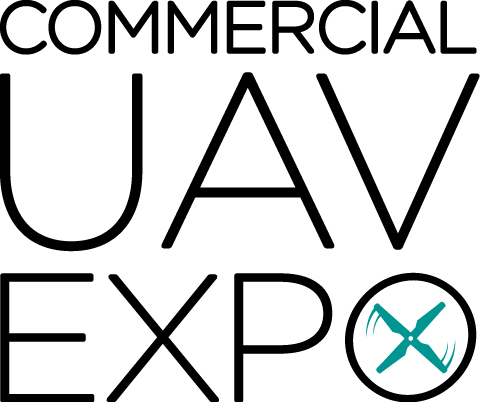
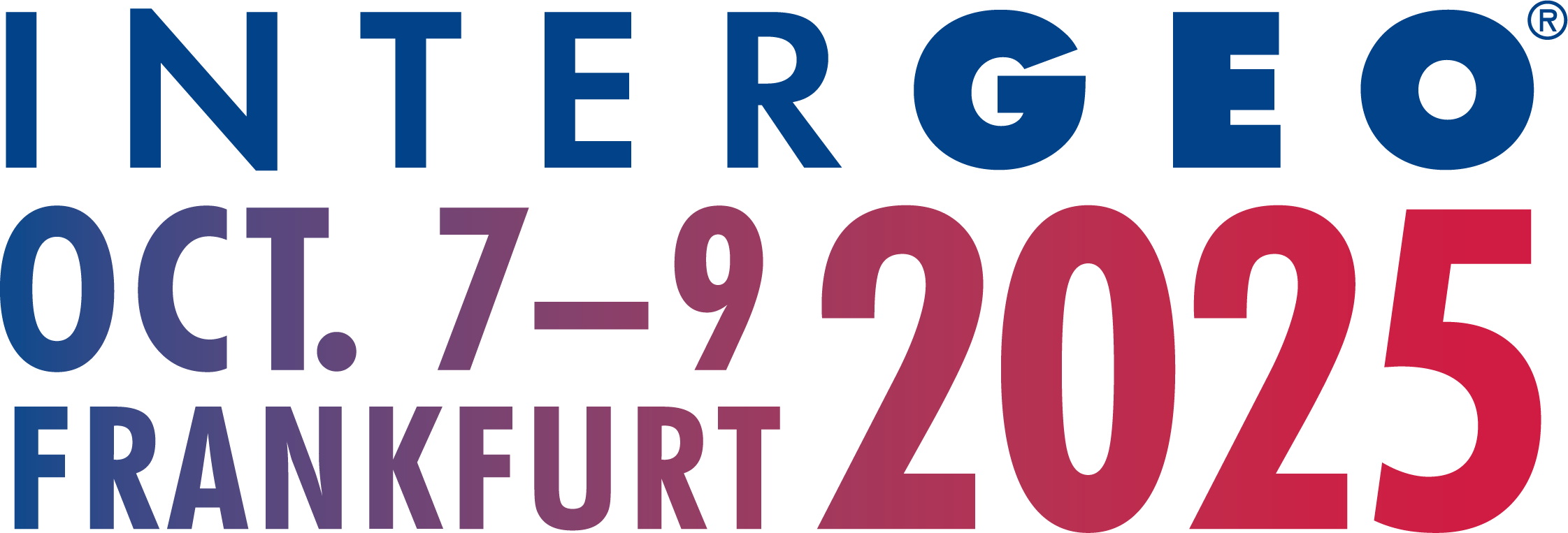
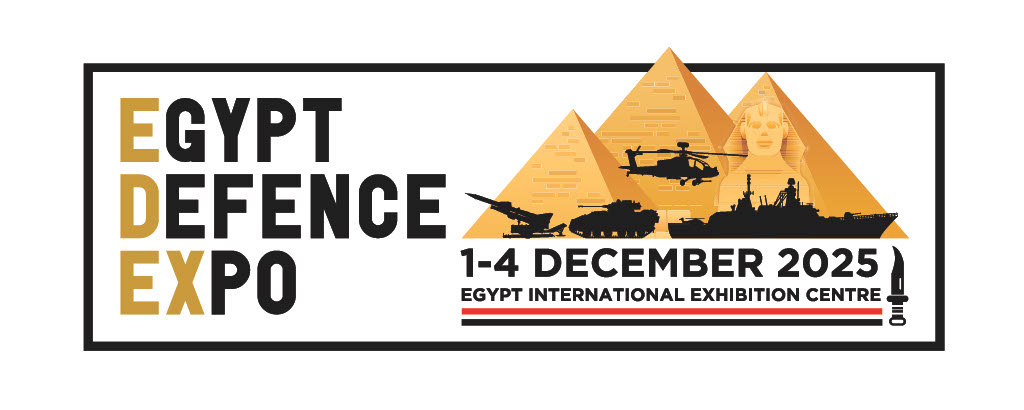
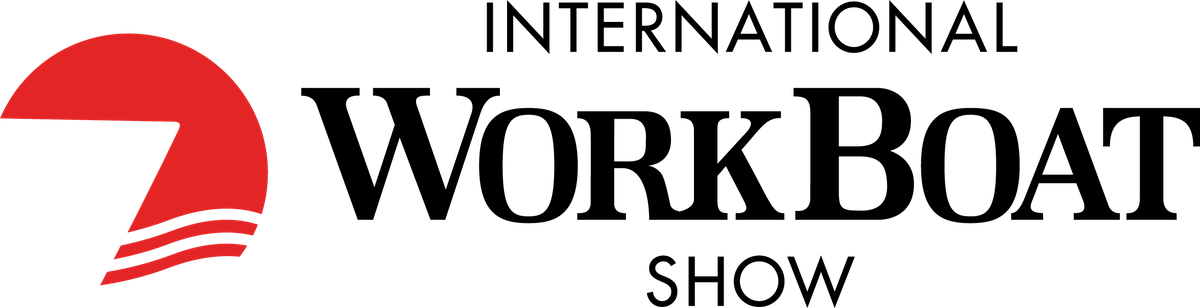