Blueflite
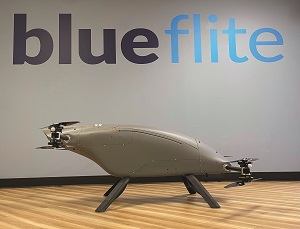
(All images courtesy of Blueflite)
Peter Donaldson reports on two smarter, more autonomous UAVs that are able to fly in any weather
Under development by Blueflite, Slate and Cobalt are a pair of uncrewed, tiltrotor cargo vehicles with payload capacities of 2-5 kg, ranges from 20-90 miles and potential speeds of up to the 100 mph limit for UAVs in their weight class.
The company’s CEO, Frank Noppel, says the UAVs are variants of a common platform with different propulsion and lift systems. Both have four pairs of propellers on tilting mounts that allow for thrust vectoring, but while Slate has wings to give it more range and speed, the wingless Cobalt boasts a larger payload and better hover performance. Blueflite has facilities in Michigan and New York State.
An entrepreneur by inclination, Noppel has a passion for aerospace, backed up by bachelor’s and master’s degrees in engineering from Karlsruhe University of Applied Sciences, and a PhD in aerospace and aeronautical engineering from Cranfield University.
His resume includes full-time posts with Airbus and Rolls-Royce. His first start-up was Ambeo, a UK-based air-taxi operator, formed in 2008. Ambeo flew Citation Mustang very light jets between airfields around Europe up until the company’s dissolution in 2013.
The idea that became Blueflite dates back to 2017, when Noppel was working for McKinsey and Company, a global management consulting firm.
“I was looking for an opportunity and, based on previous experience, there were two ingredients that I thought essential,” he says. “One is passion; setting up a company and making it work is a marathon that can go on for years. The other is high growth potential. I’m passionate about aerospace and robotics, so I was looking at the drone space, but it was when I considered the logistics angle that it clicked.”
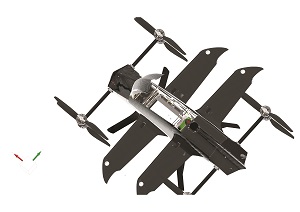
Key decisions
At that stage it was still unclear whether the prospective company would build or operate UAVs or make the components for them. “There were a lot of unanswered questions, but the first and most important was how seriously you take the idea, and whether you want to quit your job and do it,” Noppel says.
An important factor in making that decision was an early confidence boost in the form of an investment from renowned startup “accelerator” Techstars, he recalls, which encouraged him to set up Blueflite in January 2018, and also helped to set its direction.
“The first couple of months were mainly about figuring out where to play in the space and we landed on making drones,” he says. “Our talent is more in tech than operations, and we also think it’s the tech part that creates the long-term value, so the OEM model is what we established in the first six months.
“Then we took a lot of time talking to the potential customer base to understand the problem we wanted to solve, and with that knowledge, started building the tech around it.”
Chief technology officer James McClearen also joined Blueflite in 2018, bringing 15 years of design engineering experience in the automotive industry at companies such as AVL and Toyota, along with bachelor’s and master’s degrees in engineering from the Georgia Institute of Technology.
Noppel adds that the idea took some time to develop fully, in no small part because there were still many unknowns in an evolving industry. Knowing they wanted to be involved with UAVs and logistics, they worked out step-by-step how to make it happen.
Since the project’s genesis, Blueflite has put a lot of effort into understanding the requirements that a cargo UAV system must meet. At the highest level, these are reliability and operating economics, says Noppel.
“Reliability is important because these vehicles will be used for package delivery, regardless of weather and environmental conditions. They need to be rugged to withstand repeated use. Attractive operating economics are achieved through a high degree of automation and by optimising lifecycle cost without the need for significant ground infrastructure,” he explains.
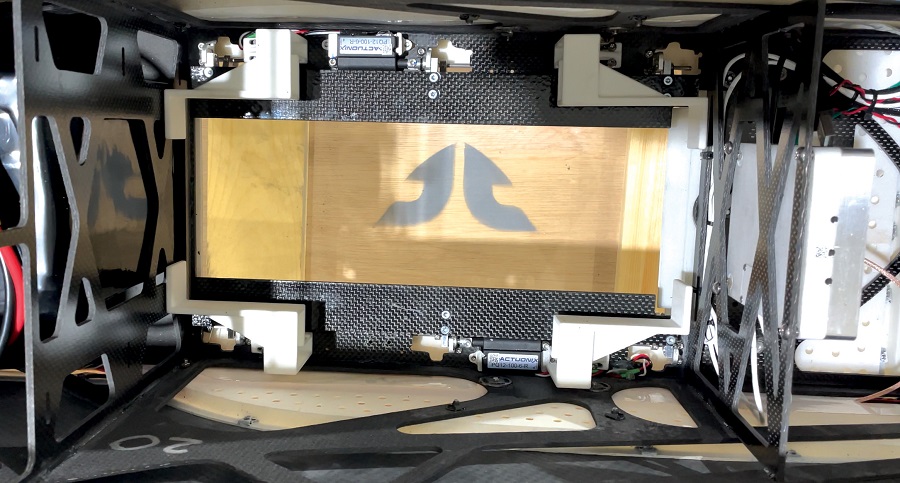
Operating concepts
Blueflite receives the most requests from three sectors: healthcare, remote industrial delivery and e-commerce delivery.
“Lately, we have been seeing that companies in these sectors are interested in setting up their own drone operations, which we can help them with. The platform is a dual-use technology that also appeals to public sector and government customers,” says Noppel. “This is increasingly important in the evolving political landscape and helps reduce risk for Blueflite because it adds another potential customer base.”
The intended operating concept encompasses hub-to-hub, hub-to-spoke and point-to-point flights. As each category involves more complexity than the one before it, most early use cases fall under hub-to-hub.
In a representative mission, once the operator is notified of the need to transport something, the item is loaded into the UAV, or a UAV pre-loaded with an item such as emergency medical equipment is allocated to the flight. Next, the flight plan is created and cleared, the UAV takes off, and the operating staff monitor the flight.
Once the UAV arrives at its destination, there are several options for payload delivery, including landing the vehicle so that it can be retrieved manually, or either dropping the item or winching it down to the ground. Finally, the UAV returns to base.
Blueflite is also working with manufacturers of automated parking/recharging stations and is developing a means of operating the UAVs from a remote-control centre.
Patented and unique
The overall design and architecture of the vehicles are Blueflite’s intellectual property, protected by a patent, Noppel says. US utility patent number 11492106 covers the entire design and functionality, including the independent tilt mechanics, staggered wings, integrated cargo bay and modularity. “We integrate third-party supplied components, such as propulsion systems and micro-electronics, which adhere to our standards and meet technical requirements. We carefully select the best to steadily raise the bar.”
He emphasises that Blueflite provides a turnkey solution, encompassing the vehicle hardware, the onboard software stack and the operations software. “Only being in control of all three elements enables us to meet the stringent requirements to serve as a delivery drone platform provider,” he says.
The vehicles have several patented features that Noppel describes as unique. These include vectored thrust for agile and precise flying characteristics, and energy-efficient, high-speed cruise, and a high degree of modularity.
Another feature is an internal payload bay with a volume of about 0.1 cubic metres and multiple access points, including an automated belly door. Payloads can be dropped or winched down, and potentially loaded using an automated system. They can also be manually loaded and unloaded through a top hatch, which could be automated.
Noppel emphasises that the vehicles’ support of autonomous loading and unloading limits their human interaction to professional and qualified people, minimising the risk from the open rotors.
“We have also developed plug-and-play technology that enables the operator to assemble and disassemble the vehicles in the field in a short time, without much hassle,” he adds.
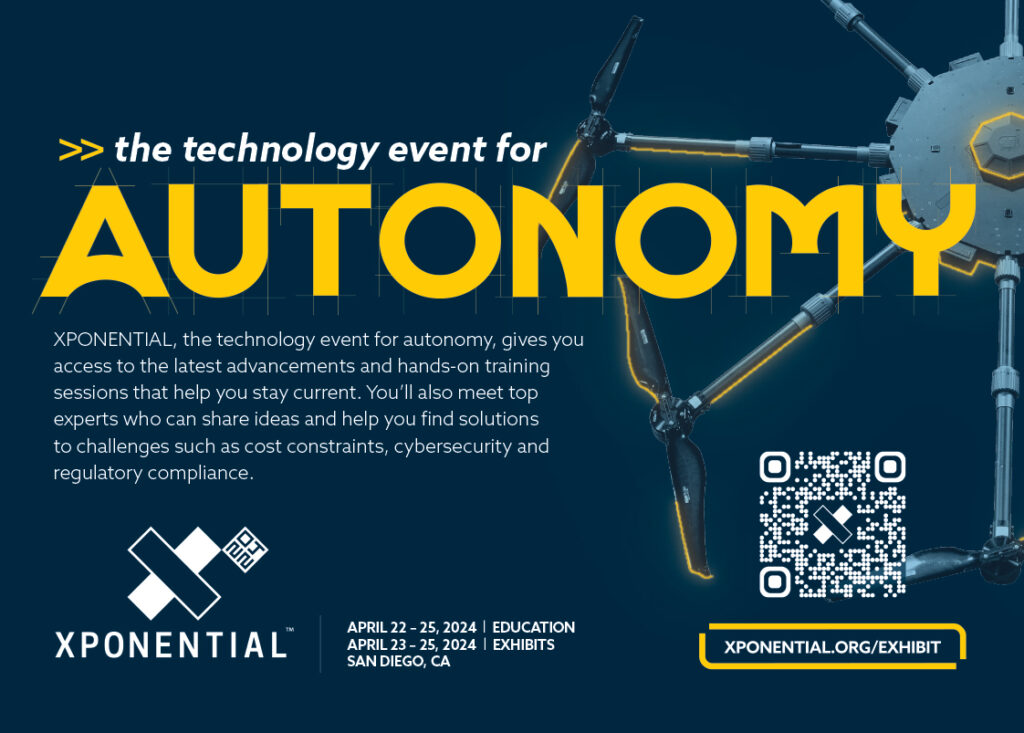
A question of size
Cobalt and Slate measure about 1.5 m x 1.5 m, with the propellers defining the extremities, but they are scalable. “Right now, we are keeping the all-up weight below 55 lb to stick to regulatory requirements, but larger and smaller versions are conceivable. This limit does not apply to military drones,” says Noppel.
The fuselage has a 3D-printed load-bearing framework, to which stressed carbon-fibre panels are attached. Two grades of carbon fibre – 3K and 6K – in resin-impregnated “prepreg” cloth form are used. The K grades refer to the modulus, or stiffness, of the carbon strands, with the figure indicating the number of single carbon fibres twisted together to form each strand, with higher numbers denoting greater stiffness.
With a payload of up to 5 kg, Cobalt is intended for relatively short-range operations, during which it will need to hover for an extended period of time and may lift objects off the ground. Its large-diameter propellers are spun at relatively low rpm by high-torque motors, achieving a top speed of about 45 mph and a range of 20-30 miles, depending on the payload.
With about half of Cobalt’s payload capacity, Slate has different propellers, optimised for speed and range. As it has poor energy efficiency in the hover, it needs to transition to wing-borne flight to make the most of its battery charge. Slate’s motors are optimised to cover a different operating envelope, using higher rpm to achieve the required power and airspeed. Blueflight expects Slate to reach the 100 mph limit for civil UAVs, with a projected range of up to 90 miles.
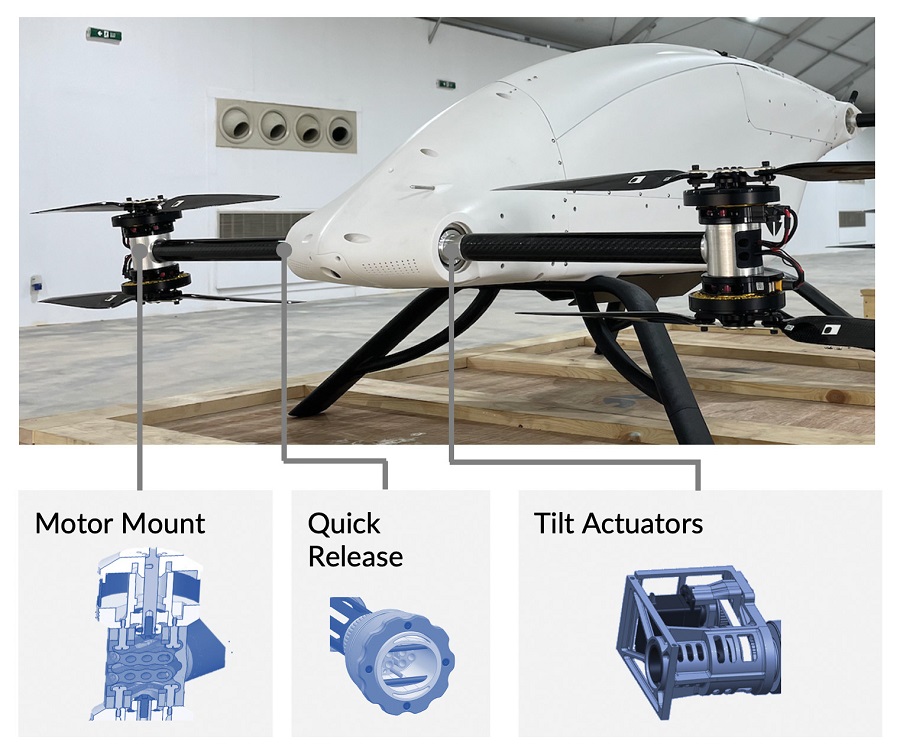
Modular propulsion
Cobalt’s propulsion motors are in Vertiq 81-08 modules, where they are tightly integrated with a 60 A electronic speed controller (ESC), designed for use with lithium polymer (LiPo) batteries in 12S format, which have 12 cells connected in series. Each motor has an embedded position sensor, and the ESC runs advanced calibration and control algorithms.
They are available with different voltage constants of 85 Kv, 150 Kv and 220 Kv. Maximum continuous torque is 2.3 Nm in flowing air. In general, motors with higher Kv values spin at higher speeds but provide less torque, while those with lower Kv values tend to produce more torque at lower speeds.
Each pair of motors is supported on the end of a carbon-fibre arm by an aluminium mount. The arm is rotated in pitch by its actuator, while each tilt actuator is controlled independently, allowing for very precise and agile flying characteristics, Noppel says.
“The drone can respond quickly and better operate in difficult weather conditions, such as high winds. It can also reduce time in the hover to save battery charge; for example, during take-off, landing and delivery. Independent tilting of the rotors makes the vehicles extremely responsive and agile, even in adverse wind. We are testing the limits of the overall system and would expect precision performance well above 25 kt gusting,” he adds.
Mounting the motors on dedicated arms makes the dual configuration much simpler to achieve than it would be if Slate’s motors were mounted on the wings, he notes. The propulsion system draws about 750 W to 2500, depending on the payload and flight mode.
LiPo batteries, then fuel cells
Cobalt and Slate both use LiPo batteries, paired to enable hot swapping, so the UAVs do not need to be powered down.
Customers can choose which brand of battery to use, but Blueflite prefers those of US firm Maxamps. “They make high-quality batteries, customise their systems to meet our requirements and we’re happy with them,” Noppel says.
However, Blueflite is looking to increase the ability of future variants to carry worthwhile payloads over longer ranges with a fuel-cell system.
Modular construction, along with plug-and-play interfaces, allows for easy replacement of parts in case of damage. “We track parts usage through our digital solution, so the operator knows when to change a certain part, and we also use artificial intelligence (AI) to predict failures before they can occur,” he says.
Noppel says modularity allows more flexibility, as modifications such as adding an extra antenna or sensor are relatively simple, as are assembly and disassembly for transport and storage.
Redundancy is an important part of Blueflite’s approach to reliability. With eight motors, the UAV can continue flying after several failures, even using the rotor tilt mechanism to compensate for resulting thrust asymmetry. The control system allows flight with one failed tilt mechanism and two failed propeller drives on that same arm. These mechanisms also enable the vehicle to operate in unusual attitudes, such as hovering nose-up or nose-down. Both UAVs can be fitted with an emergency recovery parachute.
Predictive maintenance enabled by AI software, and a non-conventional approach to the development of flight-control algorithms, centred on extensive use of simulation, are also key to Blueflite’s approach to design for reliability.
Mean time between failures (MTBF) is a key measure of reliability. Blueflite has this data from suppliers and has performed analysis on their components to help determine the vehicles’ MTBF. “Each part on our drones is barcoded and registered in our digital cloud system for utilisation tracking, and the flight data is used for predictive maintenance,” Noppel says.
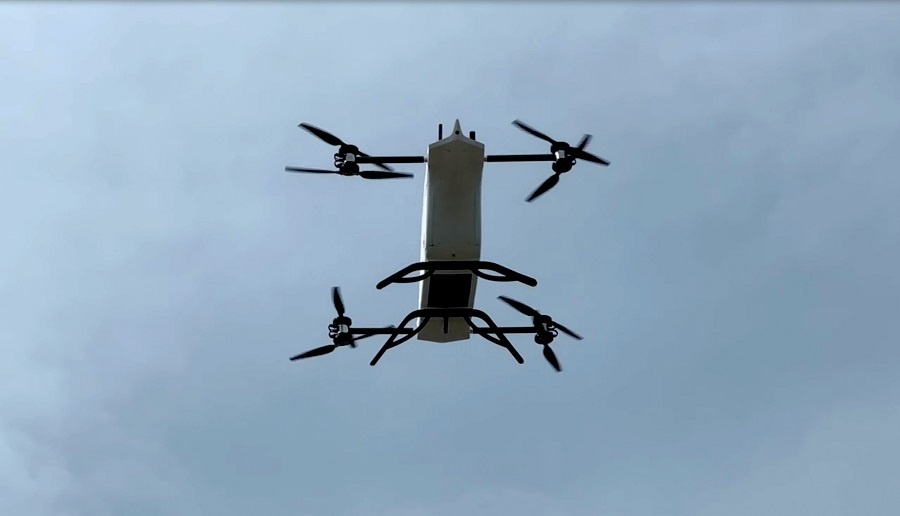
Navigate and communicate
Blueflite has engineered redundancy into its navigation and communication systems. Modern global navigation satellite system (GNSS) receivers routinely use signals from two or more navigation satellite constellations, such as GPS, Galileo, GLONASS and Beidou – Blueflight has integrated two receivers.
Noppel admits there is nothing ground-breaking in using more than one receiver that talks to more than one constellation, but he emphasises the importance of receiver quality, along with their number and placement, to a reliable and redundant navigation system.
Independence from GNSS is also implemented with new software from Wonder Robotics, which Blueflite plans to test using the UAVs’ bottom-mounted stereo camera as the primary sensor.
In terms of the main communications bearers, the three options offered by Blueflite are mesh ratio, LTE cellular and satcom. “All three can operate simultaneously on the drone, and switch to the system with best connectivity to connect to blueDigital and blueControl [explained below]. Operators can choose which configuration they prefer,” Noppel explains. “All data channels are encrypted and use secure access technology.”
The full suite of sensors also includes: Automatic Dependent Surveillance – Broadcast (ADS-B) and FLARM (‘flight alarm’) collision-warning systems; an inertial measurement unit (IMU), and an airspeed-measurement system. There are also multiple temperature sensors around the vehicle, sensors to provide feedback from components over the controller area network (CAN) bus, vibration sensors and load-bay monitoring signals.
Stacks of software
Blueflight has developed its own software, which includes the autopilot stack aboard the vehicle, the ground station and a fleet operations tool, all with ‘blue’ branding. In the ground station, blueControl provides mission-planning and execution, and it will be integrated with the blueDigital fleet operations tool.
BlueDigital is focused on fleet management, maintenance, data management, and the integration of third-party software such as uncrewed traffic management (UTM) and logistics tools. It also assists with quality assurance, with repositories of digital documents and tools to help generate reports for regulators.
The bluePilot package contains the lower-level flight-control algorithms. It also monitors the UAV’s health and provides this data to the blueControl and blueDigital packages. The UAVs can be flown manually with a handheld controller, and first-person view (FPV) functionality is available. An extension of bluePilot, called blueBrain, carries out the higher-level autopilot functions.
In addition to following flight plans automatically, the autopilot supports several autonomous safety features. “We are working with selected third-party suppliers to provide this function, as operators may have different preferences regarding these systems,” Noppel says. “We currently integrate collision-avoidance systems and obstacle-avoidance systems. Automatic rerouting is part of the UTM system integration.”
Noppel says 15 vehicles have been built so far, not including prototypes, at its in-house development facility. Research and development on the basic vehicle platform are complete, and the wingless Cobalt is now available to customers.
Testing of Cobalt and Slate continues, however, with a focus on FAA Part 135 certification and flights in extreme environments and situations. “The same is true for the software – there’s a beta version and we are constantly improving it with the help of a testing partner.”
Series production vehicles will be built in the central region of New York state, and Blueflite is working with partners to set up an assembly line there. Noppel anticipates a production rate of 1000-plus vehicles per year within seven years. The state’s GENIUS NY UAS accelerator programme awarded Blueflite its US $1 m grand prize last October.
Future work
Noppel expects to commercialise Slate this year and progress the integration of third-party equipment, including collision-avoidance systems. Blueflite expects to finalise integration of the fuel-cell system this year too, and is planning fully 3D-printed versions of the vehicles.
“On the software side, blueDigital is in constant development to enhance functionality, move everything to the cloud and increase compatibility with other systems. The onboard software is also going through revision to make the drone smarter and more autonomous.”
UPCOMING EVENTS
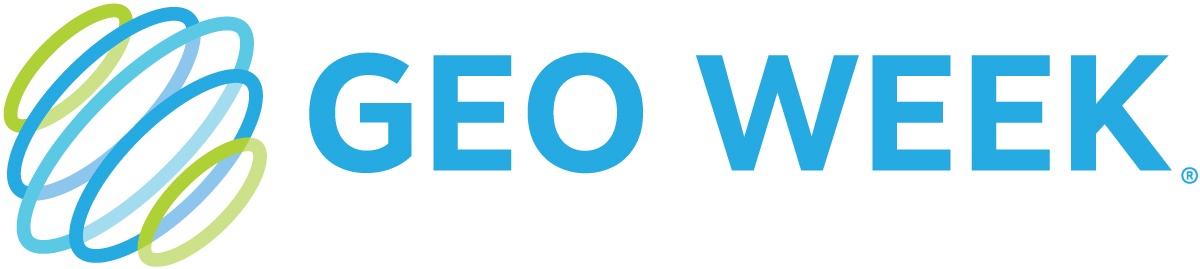
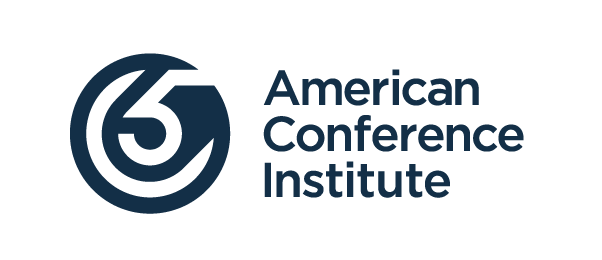
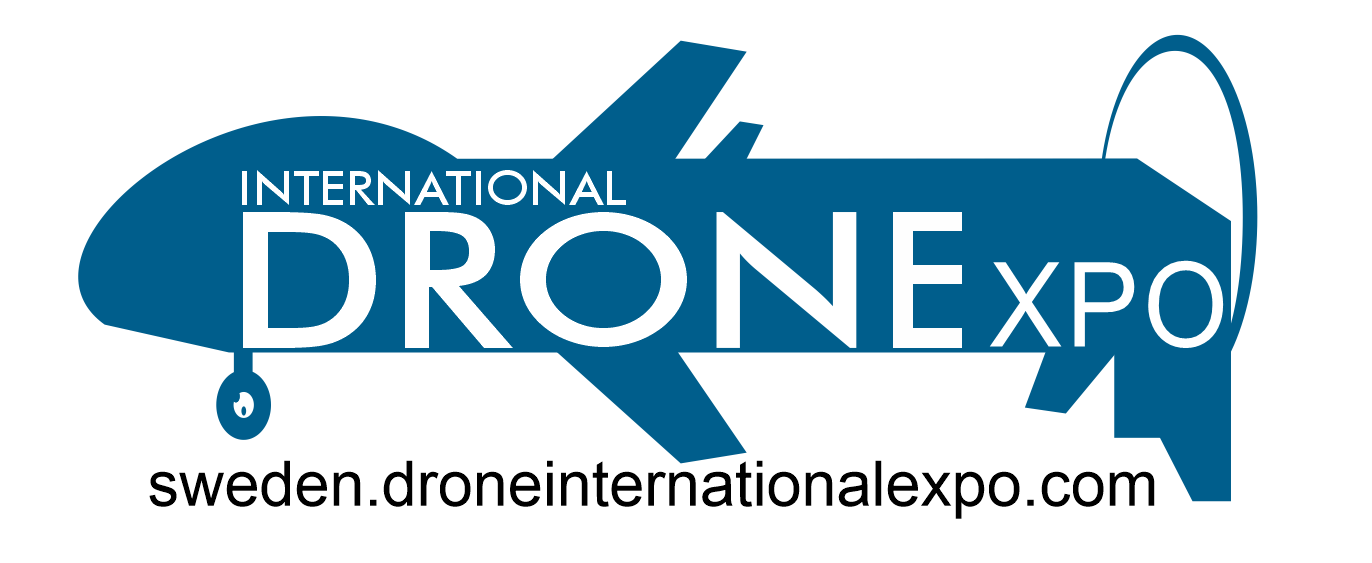
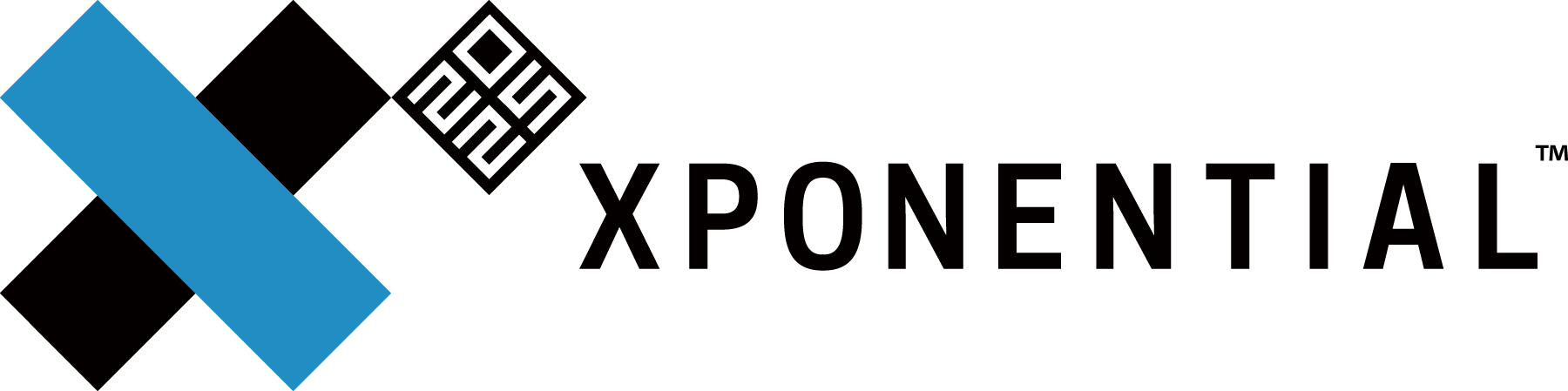
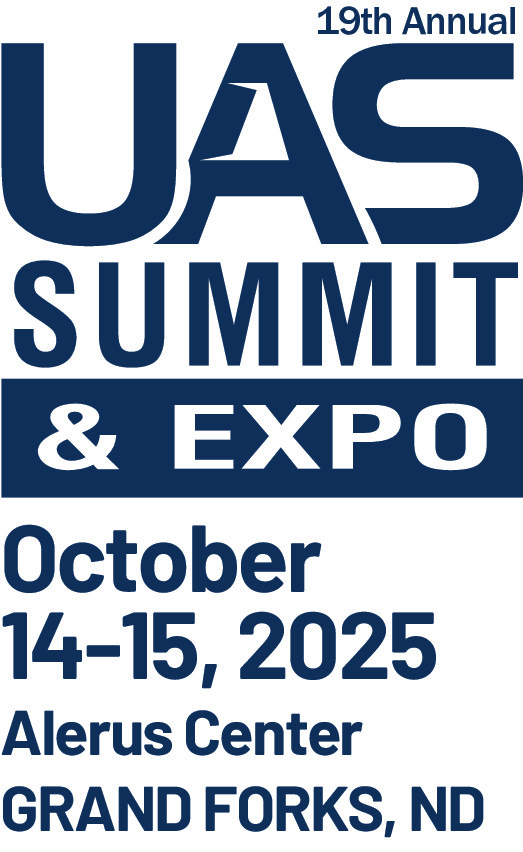

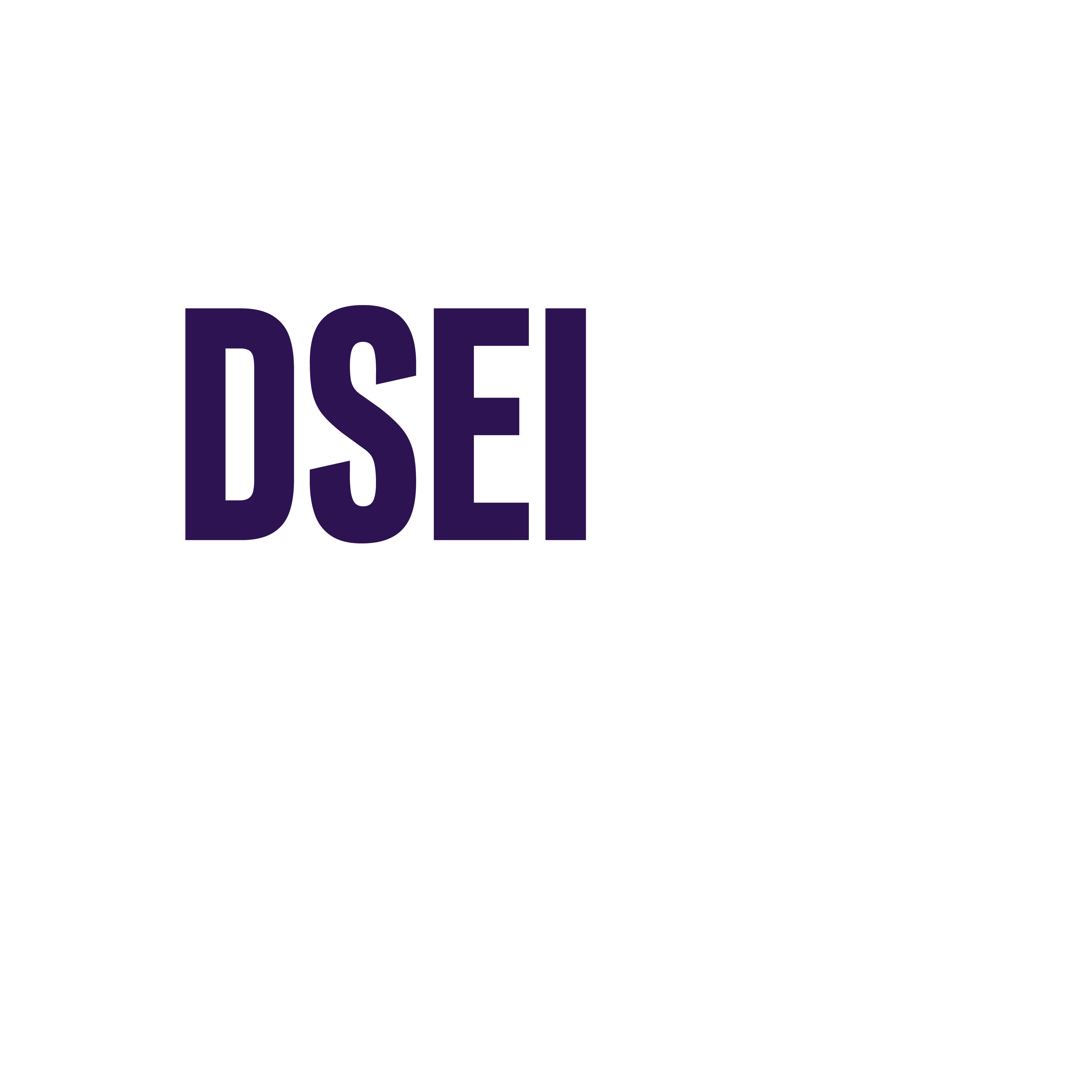
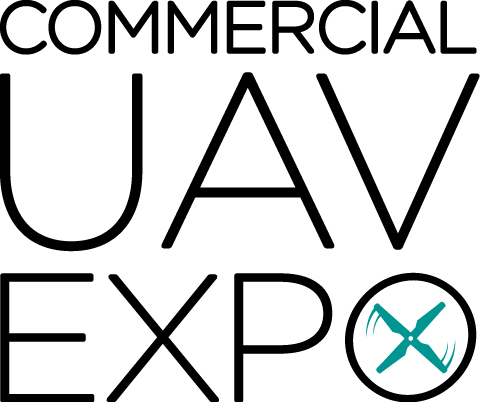
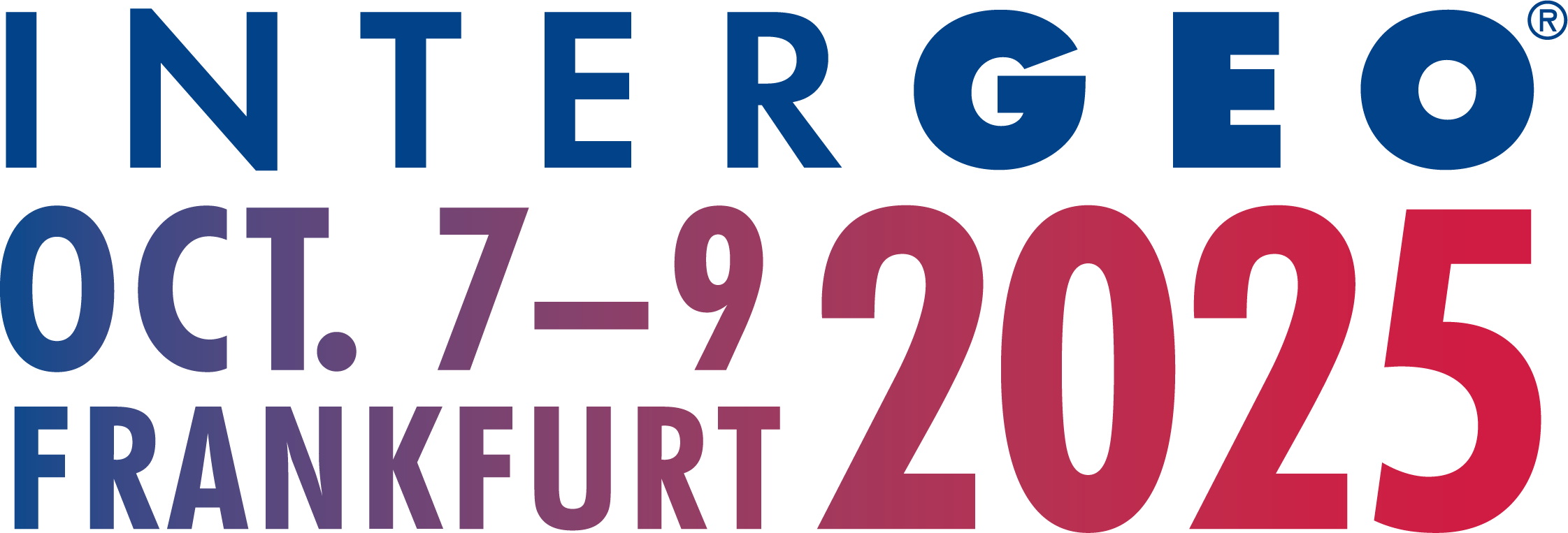
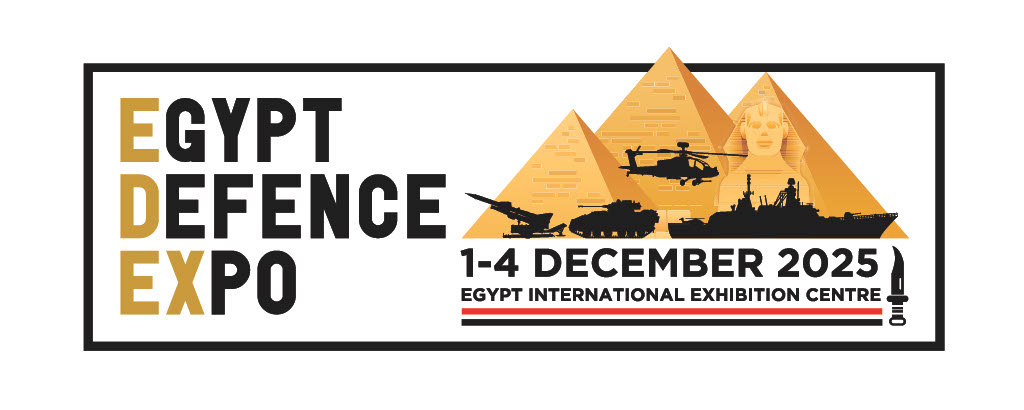
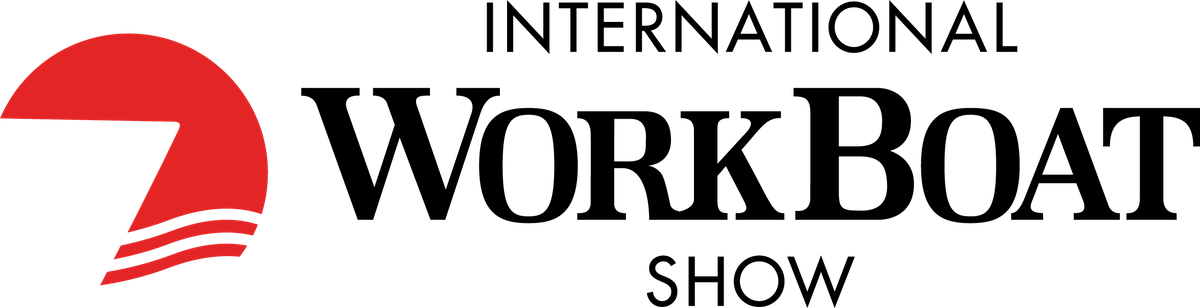