Bedrock Ocean UAV
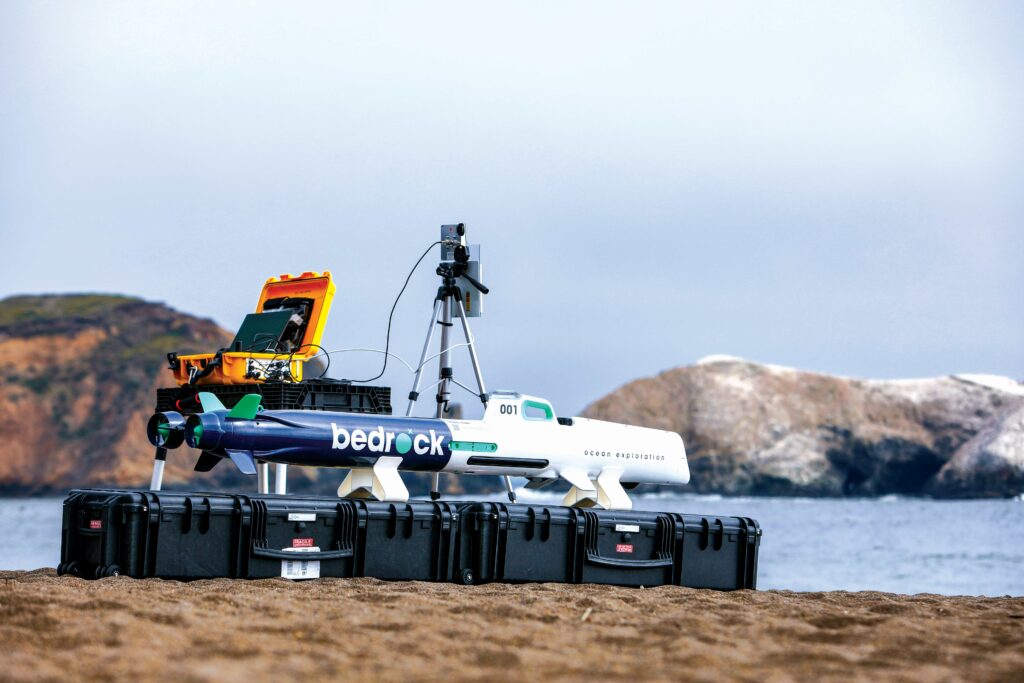
Designed to fit Bedrock Ocean Exploration’s exact subsea mapping needs, the AUV measures 2.4 m long and weighs 60 kg in air (Images courtesy of Bedrock, except where otherwise stated)
If you’re mapping the oceans, why not design your own AUV to do it? One company did just that, as Rory Jackson finds out
Founded in January 2020, Bedrock Ocean Exploration’s original ambition was the scalable and efficient collection of high-quality oceanological data, inspired by the concerns and challenges regarding the missing Malaysia Airlines Flight 370, and the need to better understand and protect our seas. The company did not, however, envisage designing and engineering its own AUV.
“To start with, we thought the most logical plan to market was to buy an off-the-shelf AUV, run third-party mission-planning and control software on it, and focus on writing a higher-level system governor, sensor integrations and automated data analysis infrastructure to get to market sooner,” recounts Bedrock’s CEO and CTO, Charles Chiau.
“First, we had trouble finding a good number of vendors whose products had the qualifications and price points we wanted. There were also great systems that we couldn’t afford or were too big. Then we ran into the perennial integration challenges of getting different suppliers’ electronics to interface together smoothly.
“We quickly started just ripping pieces out of our systems and subsystems, removing boards, [and] bypassing software, propulsion and actuation components, and so on that we didn’t like, because they either weren’t helping us meet performance targets or they were getting in the way of us controlling and fine-tuning the AUV’s development.”
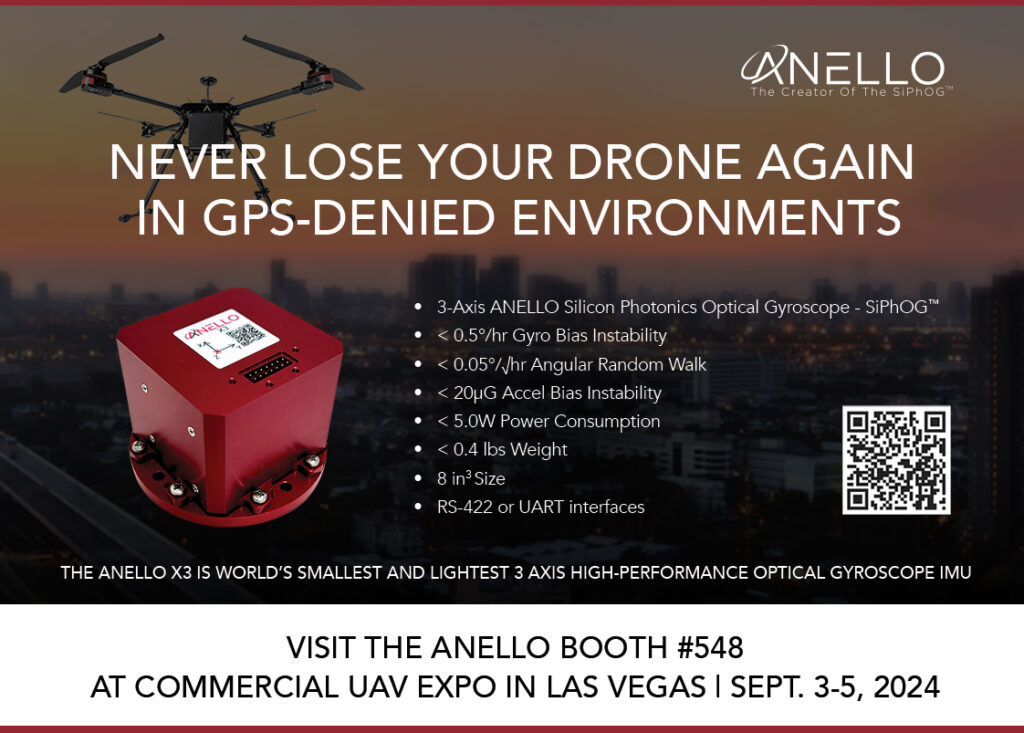
Before they knew it, Chiau and his fellow engineers had rebuilt the entire vehicle system into their own creation, from the batteries and propulsion to payloads, GNC (guidance, navigation and control), full autonomy system, post-mission analysis tools, a web-based mission planner and a data platform designed for global operations. Even sonars were custom-designed with their vendors to create the most accurate, modular and highly portable AUV for the kinds of data-gathering missions that Bedrock’s customers wanted.
Seven of Bedrock’s AUV have been built so far. It measures 2.4 m long, weighs 60 kg in air, and moves at an operating speed of 3 knots. As well as its 300 m depth rating, it typically operates for up to 10 hours before needing to recharge, which Chiau believes is significant endurance for an AUV of this size and payload capabilities (with 30-40% of the mass being survey sensors).
As the AUV is not Bedrock’s product to be sold – ocean data is – each of the seven that have been built and operated has its own name, corresponding to its colour or serial number to simplify operational identification. A white unit is named Beluga, while one with serial number 007 is called James Bond and a yellow unit is Oppenheimer (for the nuclear scientist’s association with Yellowstone).
Development history
While data collection occupied centre-stage at Bedrock, Chiau confesses that the AUV’s design and scalable fleet systems were conceived and formulated in his head for years. “I’ve worked at SpaceX, at Reliable Robotics, SRI and elsewhere on different types of land, sea, air and space systems, and before that I was a submarine pilot and had engineered crewed submersibles at DeepFlight.
“I knew for a long time that there was a need for a modular, scalable, precise and cost-effective AUV, so I’d been sketching something like this for a while before there was ever the exact right opportunity to build it.”
Following Bedrock’s founding, the first version of the AUV (based on all COTS vehicle and subsystem parts) was launched in six months, from the first team drawings to the first water trials. After some time spent realising the limitations of working with COTS and third-party systems, four months of deeper engineering followed.
“The second version started trials in mid-2021, and we had basically rebuilt the core architecture into the first prototype of an all-Bedrock vehicle from scratch: all-new PCBs, batteries; we replaced the propulsion unit with one we’d made; we even built our own submersible antennas, and so on,” Chiau says.
That vehicle outwardly bore close resemblance to the AUV seen today. Soon after, Bedrock and its control system provider weren’t a match hence Bedrock opted to rewrite the entire GNC software in-house, including cloud-based mission-planning interfaces, behavioural subroutines, data and telemetry monitoring, and more.
“That took another year, so in summer 2022, we ran a fully autonomous mission – with our entire software and hardware architecture – for the first time, in Lake Tahoe,” Chiau says. “We managed our ‘lawnmowing’ survey patterns and smart behaviours pretty well, but ran into issues with the inertial navigation sensor, and then we found out that our chosen INS had actually reached its production end of life.”
While running on spare units of the otherwise defunct inertial system, Bedrock had to revisit its supply chain strategy, aiming for the highest-grade solution feasible. Chiau and his team always knew that Exail’s Phins C3 INS was a standard choice and the closest match for its performance needs, but it wouldn’t fit the AUV’s available installation volume, optimised for packed sonars and minimising transport volume.
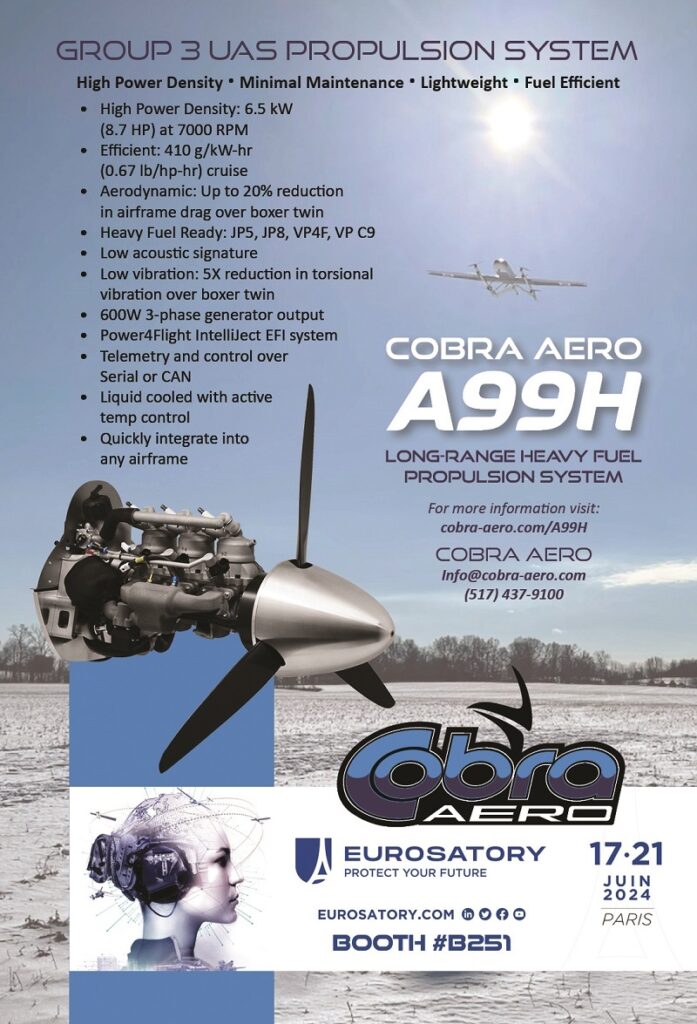
This posed a critical hurdle to the precise guidance and survey data resolutions that Bedrock’s target markets needed, particularly offshore wind and other marine construction. The company was particularly determined to achieve such precision without needing a surface-based USBL system, or a larger and more unwieldy AUV design.
“So, we and Exail visited each other, and had big discussions about future plans and roadmap alignments. They saw we weren’t just building stuff in a home garage, that we actually had a serious production facility with hand-picked engineers, and laid out methodologies and traceability, reflecting our team’s experience in aerospace, military, consumer electronics and long-term vision,” Chiau says.
“After that, we were the first ones to get to dive with the Phins 9 Compact, which we still use today. It has the performance of their C5, but in a much smaller form factor, about half the size of a C3. It was made to fit our AUV.”
In February 2023, six months after the Lake Tahoe trial, Bedrock deployed its single prototype in the ocean for the first time at Monterey Bay, thus proving to many prospective but (then) sceptical customers that the first-time AUV manufacturer had engineered something both functional and precise in its autonomous surveying. By October that year, the company had built two more AUVs, and carried out its first subsea corridor survey using all the vehicles.
Of the seven Bedrock AUVs running today, four are first-generation models running the technically defunct INS, while three are the second-generation AUV (which the company regards as its premier, commercial-grade tool for data collection) using the Exail Phins 9 Compact, as well as several other carefully selected navigation and commercial-grade survey sensors. Five additional systems have been built, consisting of the first MVP prototype, various testbed AUVs and a USV platform used in r&d.
“The first-gen had an endurance of 12-plus hours, a few hours or so longer than the second-gen, but the latter is much more productive: in eight to 10 hours [survey condition dependent], it covers about 108% more seafloor area while running the same mission,” Chiau notes. “It is significantly faster to launch and easier to operate. Its efficiency unlocks more ways to optimise data quality and rate-of-acquisition coverage.
“That makes the newer version much cheaper to run on a per-hour or per-dataset basis, and as an added measure to ease operating costs, we’ve gone through FAA and DoT clearances, allowing our lithium batteries to be flown to survey locations, enabling rapid response.”
Flying high and low
Bedrock’s AUV consists of two halves, which are designed to fit together via self-aligning connectors and mechanical latches, thereby minimising mission equipment requirements. This tool-free approach also prevents a range of minor hazards, such as a loose screw or a screwdriver rolling off a ship deck during assembly and delaying a survey by hours – a setback that Chiau has experienced in past projects.
The front half is referred to as the payload section. Currently, two different hot-swappable front halves exist, each with a varying survey sensor arrangement. The first is the “high fly” configuration, designed for bathymetry over a wide area. This integrates a Norbit OEM MBES-42 multibeam sonar, which scans at 400 kHz with a 130° swath and 512 beams, a Blueprint Subsea Starfish 454 side-scan sonar and an Ocean Floor Geophysics’ Self-Compensating Magnetometer.
The second is the “low fly” payload section, intended to complement the “high fly” AUV to fulfil geophysical surveys very close to the seafloor, which uses the same magnetometer, along with the Norbit SBP-42 sub-bottom profiler and Blueprint Subsea’s Starfish 992 side-scan sonar.
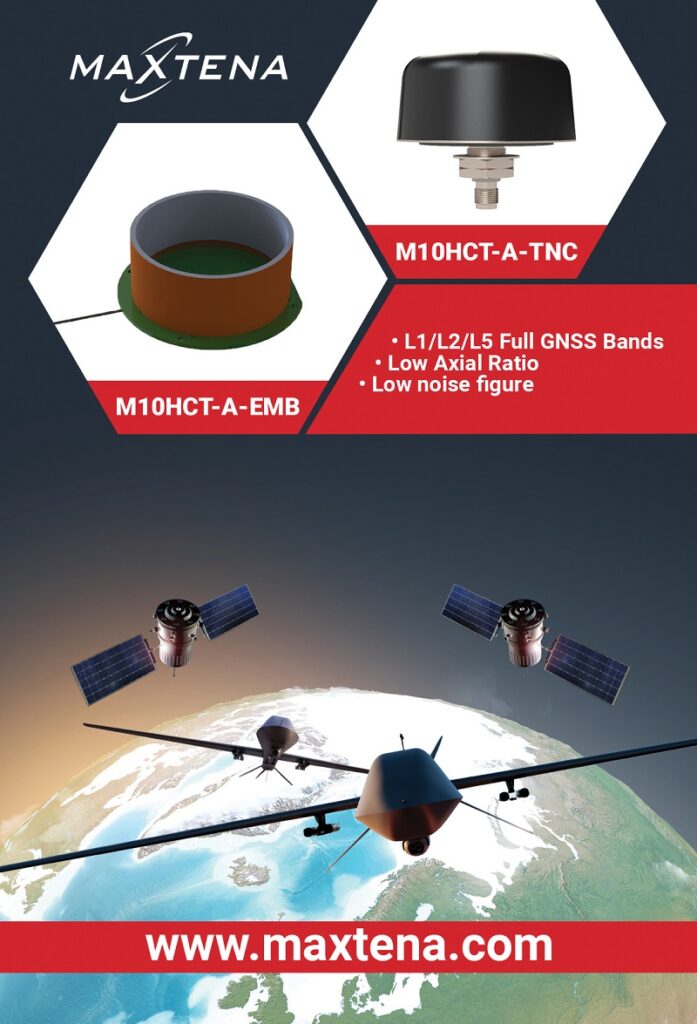
Within both payload section designs is a dry enclosure, which tightly houses the AUV’s main computers, the navigation (inertial, GNSS and aiding DVL) systems, a communications module and a wet section that arranges the sonars. Within the survey sonars, those include a forward-looking sonar (FLS) for perception, constant altitude terrain-following and obstacle avoidance.
The rear half is the propulsion section. This contains a battery, designed and built in-house to the optimal form factor, as well as two shrouded electric thrusters, their two respective ESCs and four servo-actuated rudder fins in an X-configuration. Replacement of these electrical components does require an Allen key, as they are secured into the AUV’s back half via six bolts with O-ring seals, but such maintenance would not form nominal daily operations.
“But we do pride ourselves at removing opportunities for human error, so there’s no cabling between the two halves. Try to fit two halves of an AUV together with a cable in there, and it will dangle or snag or shear on something. With the design we’ve chosen, the two halves can be mated while blindfolded,” Chiau notes.
“Every mistake all of us at Bedrock have experienced or learned about in the past on AUVs, field operations, system design, we pooled together and put a hard ‘no’ against having any of them in this system. We want to look out for the field ops teams, for whom normal things become five times harder purely because they’re at sea, so we design-out the issues, rather than relying on procedure or memory.”
Despite the different designs and componentry in either half, the AUV’s centre of buoyancy is roughly at the joint between them, such that it remains level when submerged or surfaced. It is also slightly positively buoyant as a safety default: if one or multiple systems should fail, the vehicle will float up to the surface where it can be retrieved.
Navigation
The benchmark defining Bedrock’s navigation requirement was a set of very tight horizontal and vertical survey path tolerances (especially challenging in shallower water of less than 40 m), which customers in the offshore construction space expect of surveyors. If such parties are to trust that an enormous, expensive monopile or pylon should be safely installed at a given location, they must completely trust that the AUV knows exactly wherever it is in the water column at every moment of the survey, relative to the areas it scans.
“Most survey regulations on those are written for ships, which have constant GNSS corrections; there are few, if any, such rules for AUVs, especially here in the US, which is why it has been so hard for AUVs to break into construction-grade or equivalent offshore surveys in addition to the industry being risk averse,” Chiau explains.
“If we could hit those navigation accuracy tolerances, a huge market would open up to us, especially as the US has an initiative to hit 30 GW of clean energy by 2030. That’s a target of at least 2000 active offshore turbines. The US has approximately eight and only recently started providing power. That’s a gaping chasm between demand and supply.”
The Phins 9 Compact occupies an 88.9 mm (diameter) by 130 mm cylindrical space inside the payload half’s dry section, and through its FOG IMU it maintains a position accuracy within 0.02% of the distance travelled when aided by DVL. This is sufficient for Bedrock’s needs as most initial offshore construction products will run no deeper than 100 m, so the AUV can surface quickly and often enough to regain its GNSS position. With a runtime exceeding 10 hours, concerns over the energy efficiency of constant surfacing and diving can be deemed unnecessary.
Additionally, the AUV’s Nortek DVL500 maintains bottom velocity readings from a 0.1 m to 200 m distance from the seafloor, up to an 8 Hz ping rate, and with an accuracy of 0.01 mm/s. A custom housing for the navigation system has been made by Bedrock, and after integration the DVL is bolted to the Phins 9 Compact and calibrated in-house based on close advisement from Exail.
A Blueprint USBL/ACOMM transceiver is installed onboard as well, should an end-user want such real-time position querying at their GCS and lack qualms about the extra surface-side equipment needed. This also preserves the option for vehicle-to-vehicle comms for teaming and advanced autonomous docking behaviour.
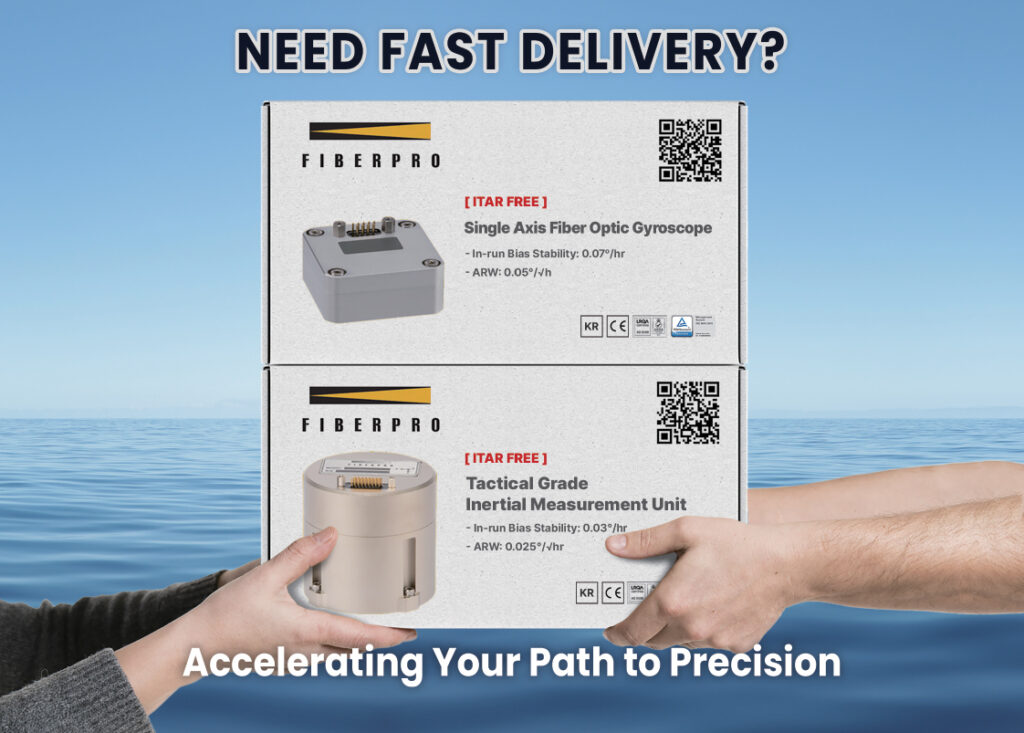
Collision avoidance
The first design of Bedrock’s forward perception system used a single-beam echosounder. “That would simply tell us whether there was something forward of the AUV or not – a very binary ‘go or don’t go’ approach, because the minimum viable product goal of the first-gen perception system was to just not hit anything,” Chiau muses.
“But, as you operate nearer to the seafloor, terrain changes much more chaotically, so your reaction time to your surroundings needs to speed up while staying within the control bandwidth of the vehicle.”
Knowing better systems were needed, Bedrock went directly to Norbit, much as it had with Exail. As the former was already using the latter’s multibeam sonar, the American company asked the Norwegian supplier if it could build a low-power, wide-swath, forward-looking sonar, now dubbed the FLS-42 (it was also at this time that Bedrock asked after the aforementioned SBP-42 sub-bottom profiler, now used in its low-fly AUV configuration).
“It is more reliable to scan farther ahead, because then you can process the terrain, having mapped the contours, and feed it into the path planning to achieve the best constant altitude path for the sensors without phase lag; for instance, by waiting for a notable ‘bump’ before finally adjusting its height,” Chiau says.
That means Bedrock’s OEM version of the FLS-42 has a 90° vertical swath, resulting in a large, 400 kHz fan that extends above and below the front of the AUV, and detects terrain changes up to 50 m away.
“Now, not only do we not hit anything, but that FLS enables us to run all kinds of algorithms for terrain-centric navigation and obstacle avoidance,” Chiau says.
“For instance, if we’re surveying under a structure, we can put in a special command to avoid surfacing if an object has been detected upwards of the AUV, or in a ‘keep out’ zone, and there’s all sorts of other behaviours we can tailor, based on perception-based risk factors like that.”
Importantly, neither the FLS-42 or other sonars on Bedrock’s AUV emit frequencies below 200 kHz, which has been a crucial design choice for gaining clearance for near-shore operations from governmental environment agencies as such frequencies are harmless to marine mammals. This prevents the need for requiring third-party protected species observers or Incident Take Authorisations.
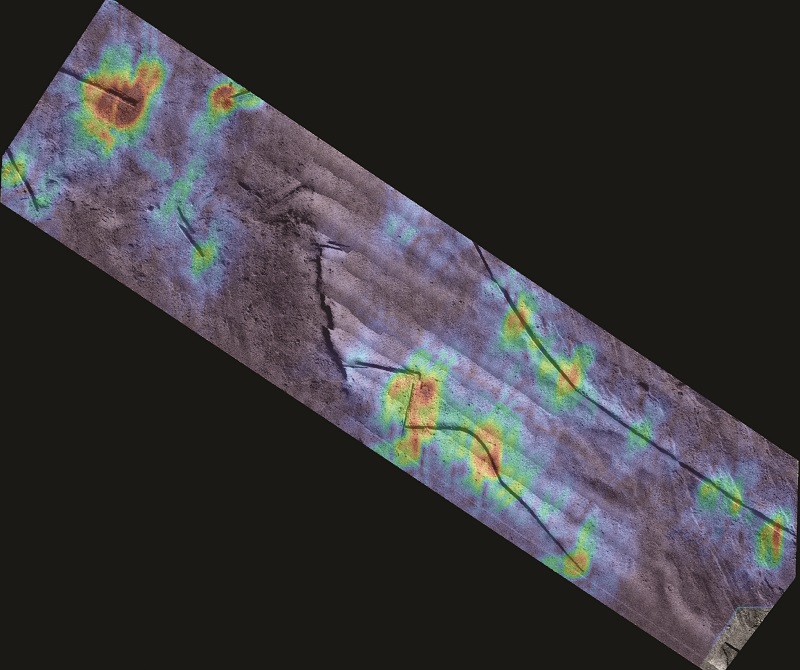
Main computer
Standard microprocessors serve as the AUV’s low-level control system, while an nVidia Jetson TX2 runs the algorithms for perception and intelligent behaviour, as well as real-time processing of live survey data, and provides significant space for future expansion of data-driven autonomy.
“We chose the TX2 as the primary GPU solution that could fit at the time, balancing power, supply chains and a Covid pandemic. We wanted to do high-rate data-processing onboard, because shipping data around has been the biggest challenge in virtually every survey we’ve seen,” Chiau explains.
“Moving terabytes of hard drives around the world in FedEx boxes, which get lost, is fundamentally unsound. We knew we had to compute at the edge and do everything we could onboard, which is also how we can get the AUV making intelligent decisions. That feeds into the tailorable behaviours I mentioned earlier: we can get the AUV to track the quality of incoming data to notice and maintain a minimum data spec to quality control the data collected.
“Surfacing to beam the raw data via Starlink to a cloud-based processing server isn’t realistic either, and we can’t wait six months to process; we need it in real-time to respond to it in real-time, and that’s what the compute architecture was designed to achieve, at least an order of magnitude faster. Time, data volume and energy are our main constraints to overcome, not the AUV.”
One 2 TB SSD is installed on each AUV. Chiau reports that this is more than is necessary per survey, but to maximise value from each morning launch, Bedrock typically carries out multiple mission types per survey day, thus filling up and making better use of the hard-drive space before recovery at day’s end.
“We have active onboard data monitoring and can view selected survey lines of data transmitted during surface intervals for GNSS fix to ensure mission success near real time,” he adds.
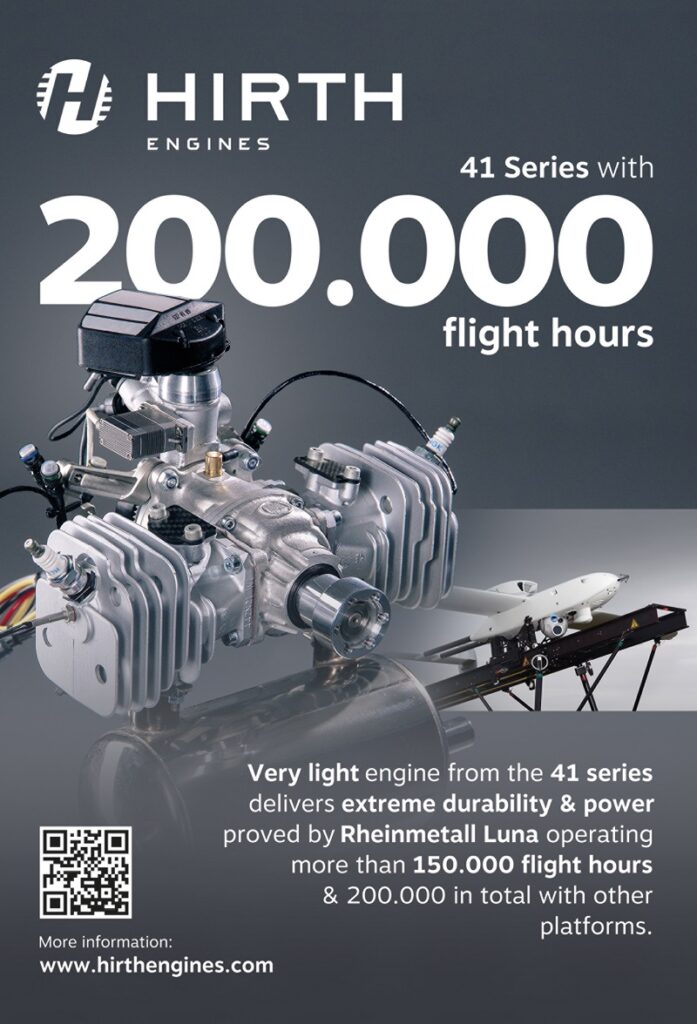
Driven by research
While Chiau had previously built battery packs around cylindrical, pouch and prismatic cells, using dry, flooded and oil-filled housings, the pack in its AUV today is made from 18650-type cylindrical, lithium-ion cells (with total energy of 3 kWh) for simplicity’s sake.
“We needed something that was reliable enough, and could be bought in batch and flown. We packed them together, used our normal QC and testing processes, as informed by UN 38.3 guidelines, and built a compact and reliable battery pack with multiple redundancies,” Chiau says.
“We’re always researching new cells and battery management solutions, but since the pack is made in-house we can change it and scale it at will out of necessity. We never wanted to build batteries, cast antennas or make interconnect systems, but now we can make anything and be fairly self-sufficient – and supply-chain resilient – in critical core technologies.”
The pack is split into four independent and hence redundant strings onboard, with a power-management system that routes power from different batteries as needed across the (also redundant) power bus, and several configurations of redundant detection across charging and discharge systems. This ensures tolerance for faults or failures of individual batteries or bus connections to ensure return to surface, and basic mission flythrough in some controlled instances.
While Bedrock is satisfied enough with its battery for now, Chiau conversely describes AUV powertrains as “an r&d black hole. You basically choose propellers, brushless electric motors and a motor controller that match the output you’re looking for against the power system and mission requirements. Ours isn’t very different from anyone else’s, the dual-thruster configuration aside. It is fascinating engineering, but it’s a trap, with countless PhD papers on this. It just needs to move enough for the economics.”
He concedes that some work went into choosing a motor controller that could output detailed telemetry – around 2000 different operational parameters are recorded onboard, including exact torques of servo shafts, exact motor rpms and currents. Such data is critical for driving Bedrock’s fault detection, isolation and recovery system (FDIR) of logic, maintenance and behaviour algorithms.
“But we’ve not had time to optimise the powertrain until now. Short of winding our own stators, we just bought COTS units that did 80% of what we wanted,” Chiau says.
“Now we’re at a place where we want higher reliability and much higher performance. We want to spin bigger props, more torque, lower rpm, but also speed to unlock harsher environmental operating envelopes. You can’t just equip some new motor controller to get all that; you have to match a propeller to a motor to a motor controller, and then that will drive the battery design to match the loads and interfaces across the architecture. It will mean holistic transformation of the propulsion section while still retaining high-level parameters and lessons for smooth operation and buoyancy.”
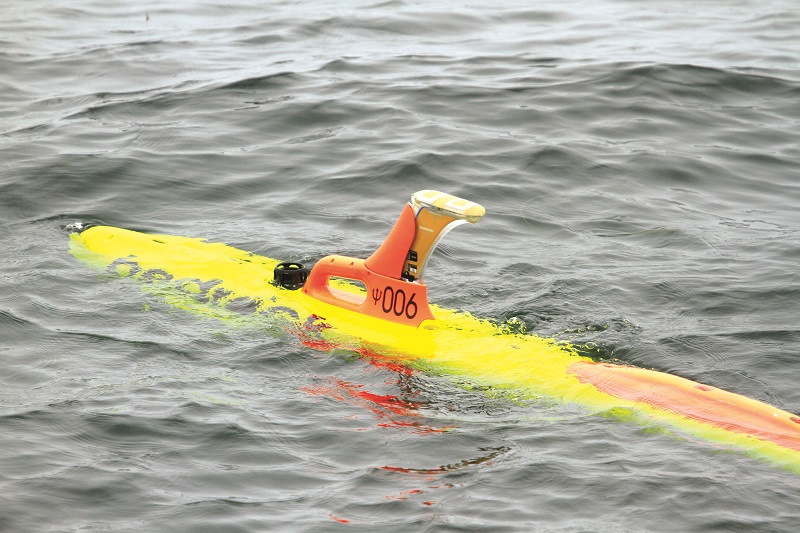
Wireless connectivity
Most AUVs today feature a dorsal pod or mast with antennas for comms and GNSS when surfaced, and significant customisation went into Bedrock’s model as it could not find a COTS solution with the right antenna count, depth rating and form factor. The latter point was important, as many off-the-shelf submersible antenna masts would have made the 60 kg AUV cumbersomely bulky.
“Instead, we made ours resemble a fin atop the AUV. Inside that are all of our antennas etched on a PCB,” Chiau says. “Custom patch elements covering GNSS, iridium, long-range radio and wi-fi, while also carrying NAV lights, status indicators and emergency strobes, both visible and IR. The individual radio and GNSS chips are standard COTS parts, including a u-blox GNSS receiver, which we can PPP (Precise Point Positioning) process for added accuracy post-mission.”
Additionally, an acoustic modem integrates with the USBL system as a recovery assistance and communication device. Integrating its own GPS receiver and antenna, it can pull inertial data from the dry compute section to ping out a packet of location data for end-users to recover. The power-management system prioritises its power distribution such that this pinger remains active even if most other systems fail – it actually “fails on”, as Chiau puts it.
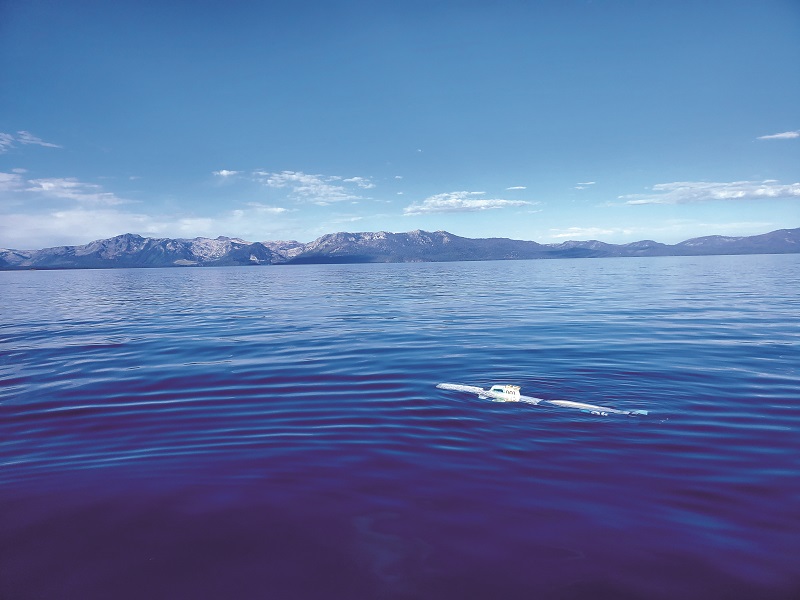
SLA-printed hull
Bedrock assembles its pressure housings in-house from two aluminium end-caps bonded either side of composite tubes. Aluminium heat sinking is built-in throughout the design (in the end-caps and elsewhere) to compensate for the composite’s lower thermal conductivity, and take advantage of the water heat-sink flooding elsewhere in the vehicle body.
The AUV’s internal structure is aluminium, while the outer fairings are printed via large additive manufacturing (AM) via stereolithography (SLA), with syntactic foam placements at the midsection for flotation. AM appealed to Bedrock for its rapidity and how it enables easy adjustment of the vehicle body, compared with fibreglass manufacturing.
“There was a lot of early hydrodynamics testing, and we frequently wanted to change fins, control surfaces, and just the whole outer shape,” Chiau notes.
“That was for improving internal packaging space, aesthetics and impact tolerance. On that latter point, you’ll see a structural ring in the front of the vehicle, always farthest ahead, because that is the first thing we want to weather an impact, and it’s mechanically linked to the robust, aluminium skeleton, which can handle hard bumps easily. It also provides the primary load path for launch and recovery latching.”
In SLA, a bath of resin is fused into solid layers of printed structural patterns by UV lasers, which cause the resin’s monomers and oligomers to cross-link and form polymers, higher and higher over time until the uploaded CAD structure is complete. While prized for the intricate detail it can achieve, SLA’s specific appeal to Bedrock came more from an undisclosed material it enabled them to use, which matched ABS (acrylonitrile butadiene styrene) for impact resistance, acoustic transparency and other mission-critical qualities.
Bedrock anticipates potentially switching to thermoplastic moulding machines or other mass-production strategies that match specific use cases for the body fairings, once the company’s growth justifies constructing its AUVs in high volumes (with the associated expense of making large, metallic moulds for large production runs) to reach coasts and oceans far and wide.
Durability is also a critical future target. As Chiau comments: “I want to chuck these like I can with a kayak or throw them from a moving platform.”
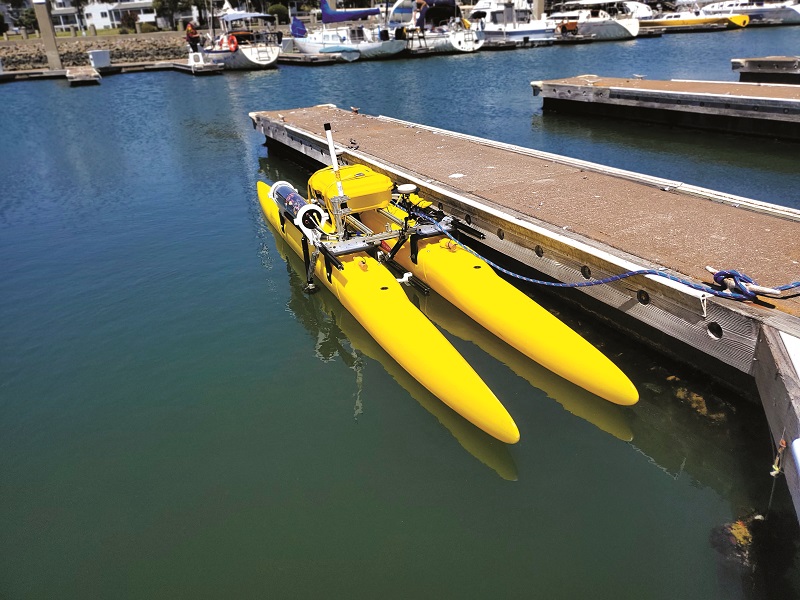
Strange new waters
Bedrock’s r&d plans target continued expansion of its vehicle intelligence, by which Blue Economy companies can increasingly remove humans from data collection (with all their potential for error and injury) where AUVs can specialise, and instead place them into data analysis and response actions.
“While we have achieved over-the-horizon C2 in our operations, the end-goal really is over-the-horizon launch and recovery of fleet systems. The launch and recovery bottleneck is going to be the last big hurdle that stops AUVs from being scalable,” Chiau notes.
“Solving the problem of needing humans to operate an A-frame, or to carry the AUV to a drop-point, is very challenging. Some teams have tried solving it, but those are usually one-AUV-at-a-time solutions, and we need to get to a place where large numbers of these vehicles can be automatically deployed and recaptured, and then deployed repeatedly.”
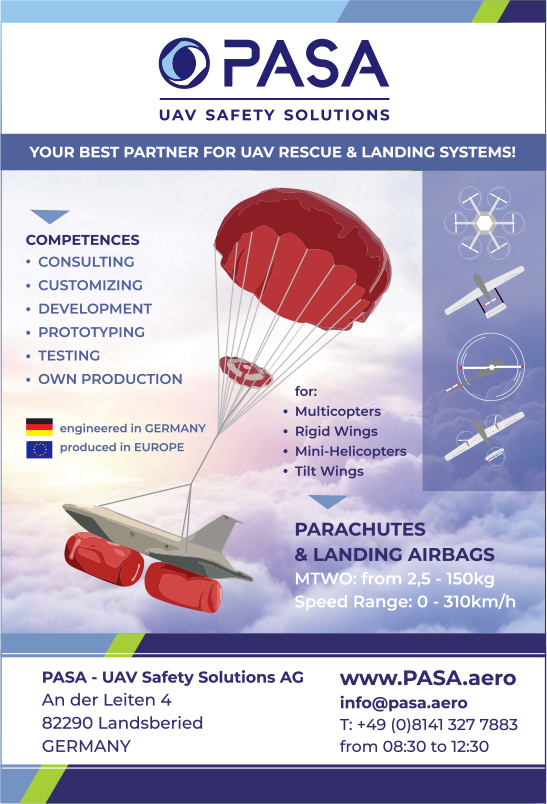
Beyond innovating these types of mechanisms, automation down the chain of data processing, analytics and accessibility is also on Bedrock’s roadmap, with future r&d to comprise critical targets across the ecosystem of data solutions, including AUV fleet communications technologies that could enable swarm collection, cloud-sharing and reactions to edge-processed ocean data.
“Data will be at the core for deciding humanity’s and the environment’s future,” Chiau says. “And garbage in, garbage out. So, we want to ensure data quality, as a consistent and trustworthy source of decision-making for real impact. AI requires data, so we started there.”
“We are looking at going into deeper waters as offshore construction moves in that direction, such as floating wind farms, subsea cable monitoring and mining impact assessments. Because we’ve built a modular architecture, much of our IP will work anywhere in the ocean once paired with appropriate subsystems and software.
“On that note, future launch and recovery will need a surface asset of some kind. There is no reason it couldn’t be a USV of some sort we make next. That would make our data-acquisition and vehicle-handling entities into fully uncrewed systems, enabling users to point and click anywhere on Earth, and receive insights straight to their screens.”
Specifications
- Bedrock Ocean Exploration AUV
- Battery-electric
- Positively buoyant
- Length: 2.4 m
- Diameter: 0.23 m hull (0.45 m including control surfaces)
- Weight in air: 60 kg in air
- Operating speed: 3 knots
- Endurance: Just over 10 hours
- Maximum depth: 300 m
Some key suppliers
- Inertial navigation systems: Exail
- DVLs: Nortek
- GNSS: u-blox
- Forward-looking sonars: Norbit
- Side-scan sonars: Blueprint Subsea
- USBL/ACOMM: Blueprint Subsea
- Pressure sensors: AML Oceanographic
- Conductivity, temperature, depth (CTD) sensors: SonTek
- Magnetometers: Ocean Floor Geophysics
- Acoustic pingers: Sonotronics
UPCOMING EVENTS
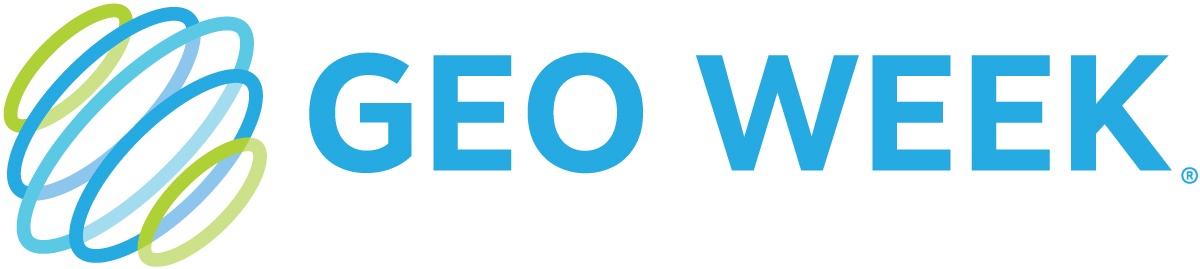
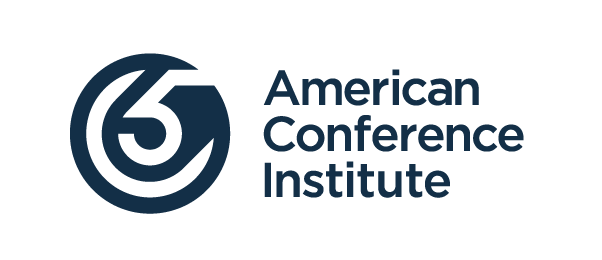
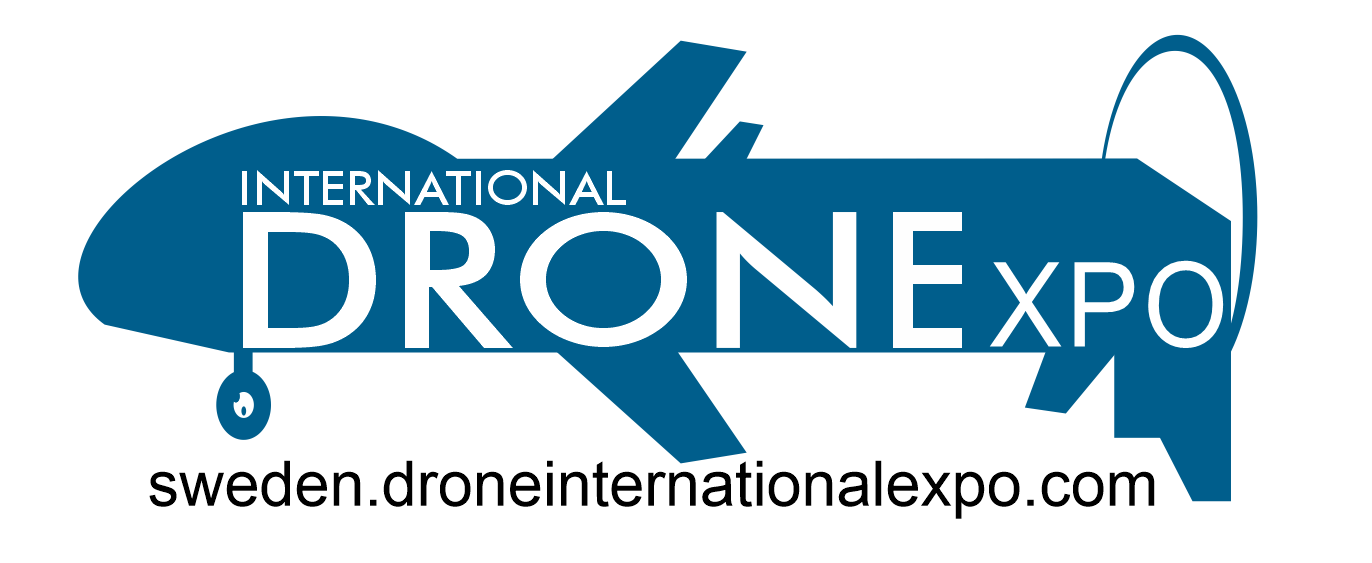
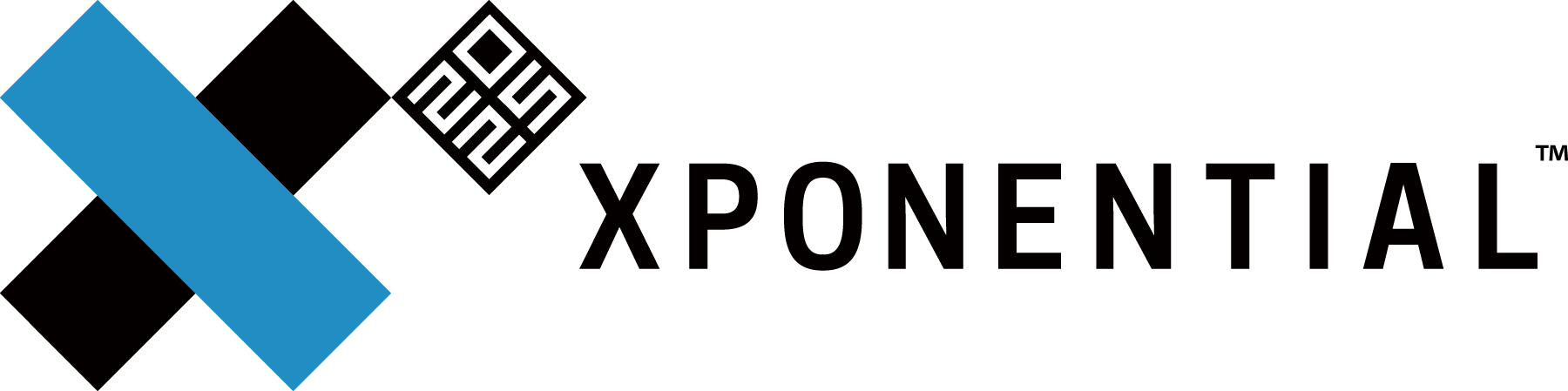
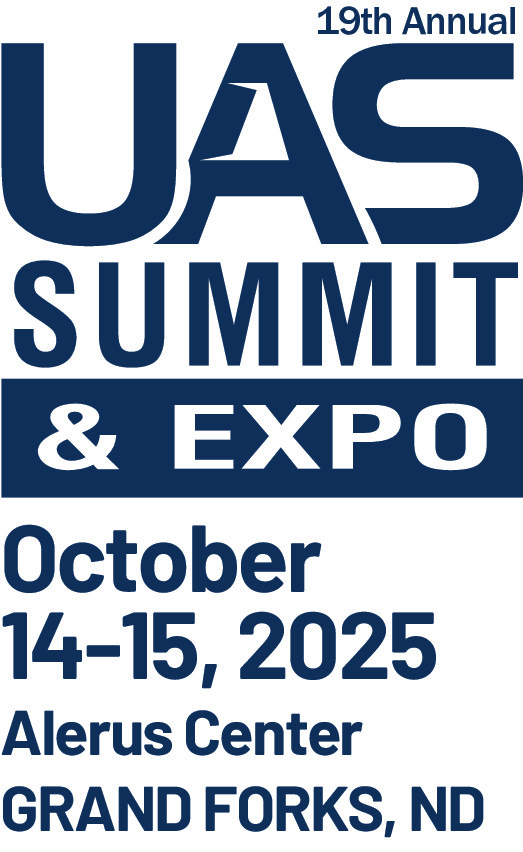

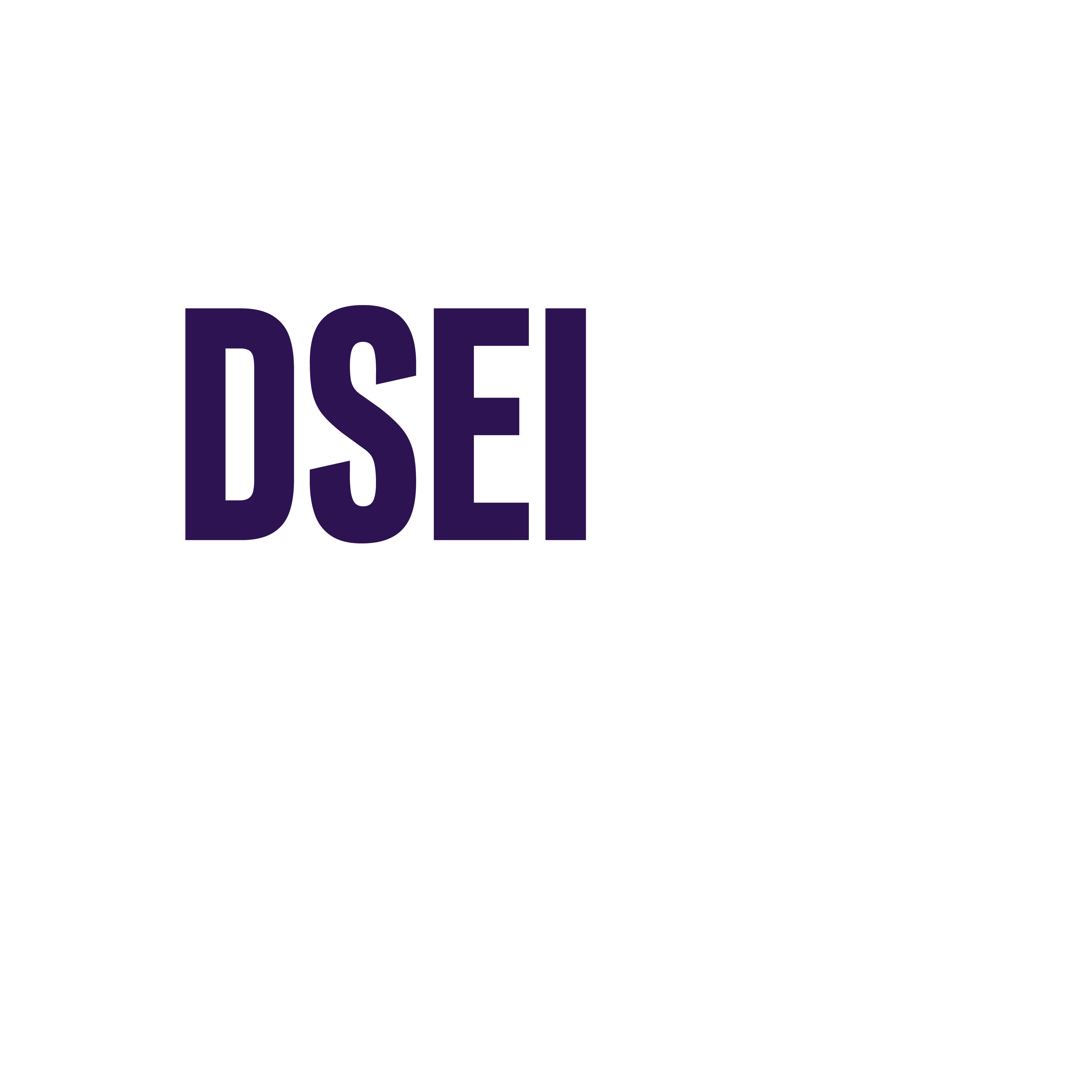
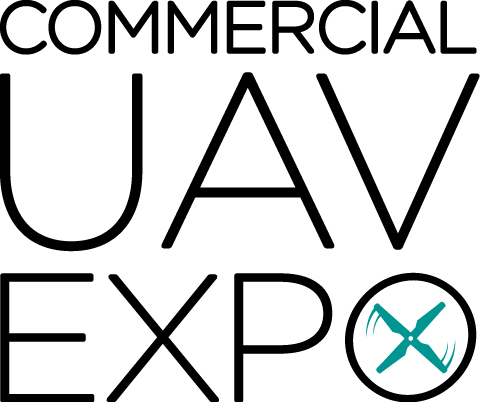
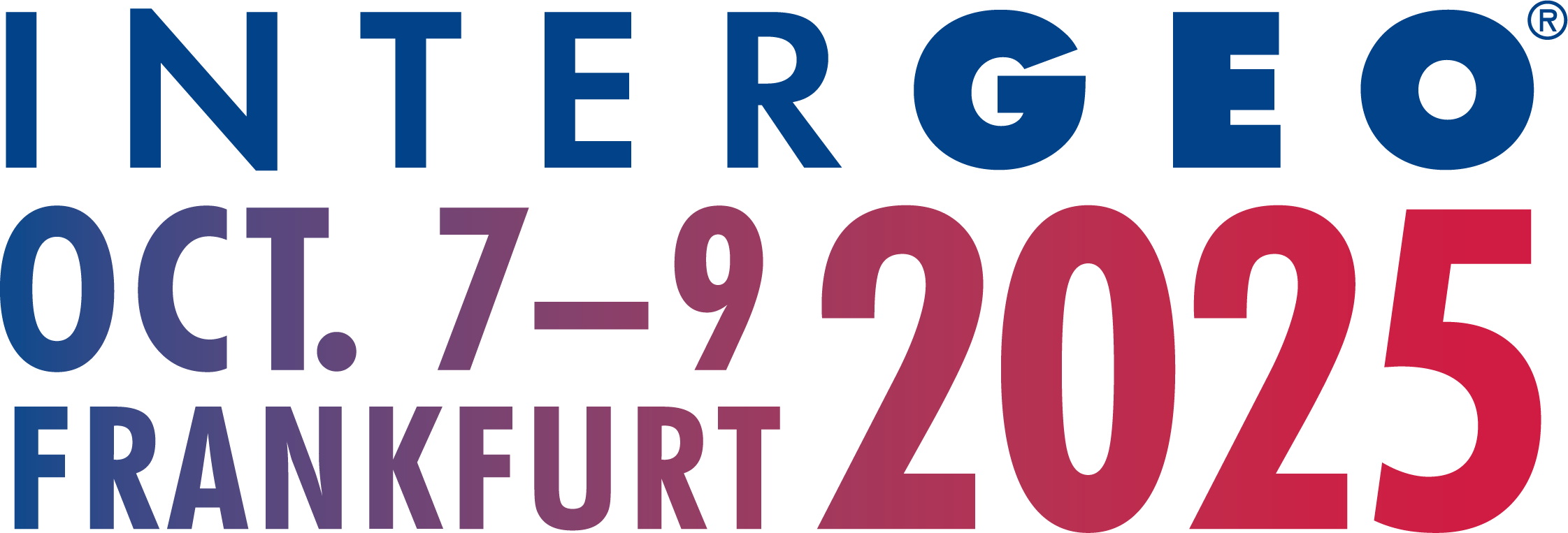
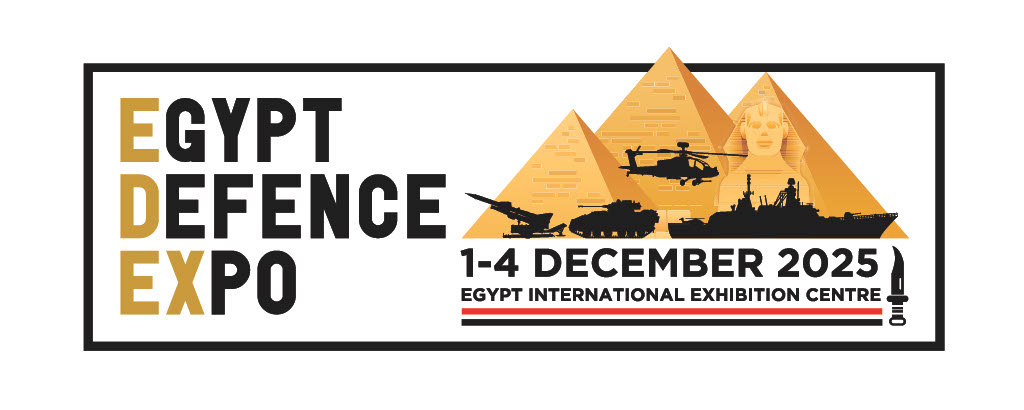
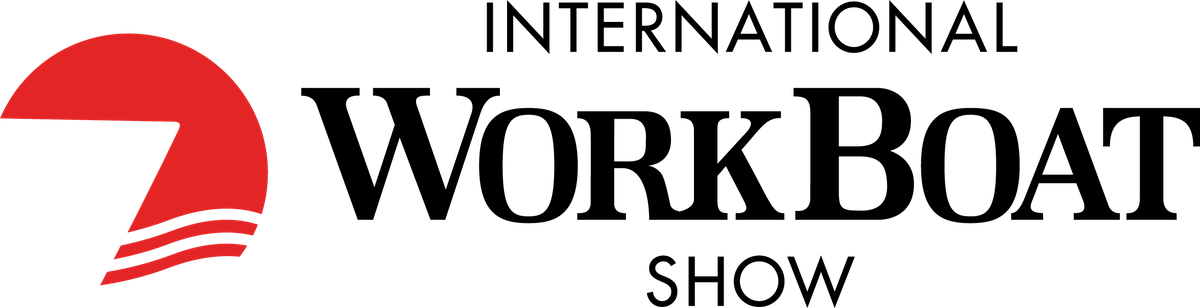