Bayonet 350
In at the shallow end
Design a UGV that can do the work of UAVs and AUVs in shallow waters, and this is one result. Rory Jackson reports
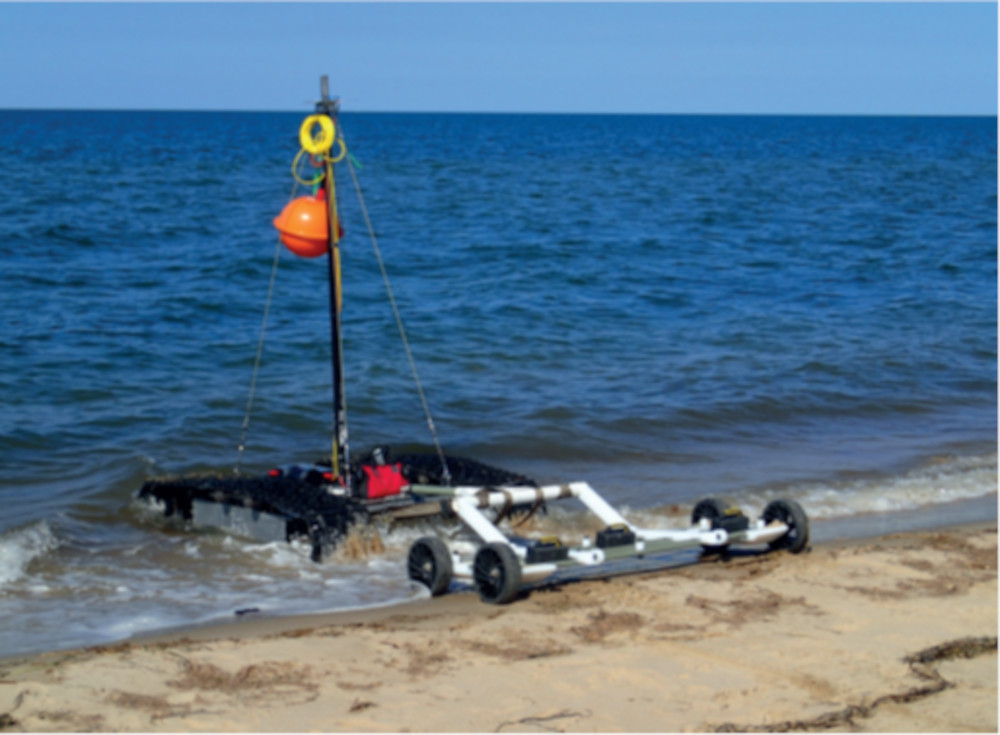
(Images courtesy of Bayonet Ocean Vehicles)
As awareness of autonomous solutions grows among potential customer markets, some among them have begun to feel that UGVs have key benefits over UAVs in low-altitude or indoor applications. For example, UGVs don’t need to hover for close-up inspections (and thus use far less battery energy), they produce far less noise when working among people, and they pose much less of a collision risk in close quarters, especially given their lack of spinning, possibly exposed rotor blades.
UGVs could also have similar advantages over AUVs in some circumstances. Shallow waters in particular pose a risk of beaching or rock collisions – even to micro-AUVs – and much like UAVs, conventional AUVs expend considerable energy in station-keeping for stationary inspection, geophysical surveys and border monitoring tasks. If a UGV could be built to traverse the beds of shallow waters and station-keep in their strong currents, it would be able to carry out various jobs with far greater safety and energy efficiency than AUVs.
That is the idea behind the autonomous underwater ground vehicles (AUGVs) from Bayonet Ocean Vehicles. This Massachusetts-based company designs and manufactures a series of autonomous mobile robots that move around on tracks in order to navigate dry and wet sands without being disrupted by strong currents or uneven terrains.
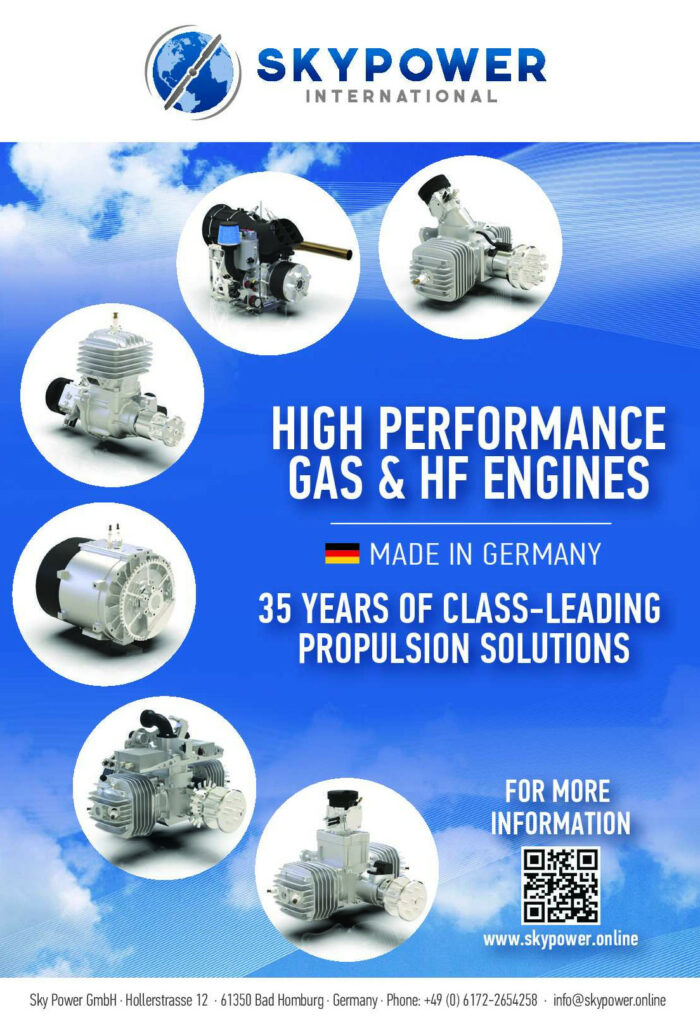
Although the company was not incorporated until March 2022, the actual crawler UGVs it now produces were originally the IP and creation of c-2 Innovations (c-2i). It so happens that c-2i’s engineers used the OpenSea software platform from Greensea Systems for their UGVs, which gradually built a relationship between the two companies until the latter offered to buy the product line of amphibious robots in order to continue their development and commercialisation.
“The idea of an amphibious crawler robot was proposed and pursued as an r&d effort back in the 1980s, well before microprocessors and the internet became part of day-to-day life,” says Mike Farinella, senior engineer at Bayonet (and formerly of c-2i). “I remember from the tests of the resulting systems that onlookers received it really well, but the vast majority of the potential ‘market’ simply refused to believe something like that could possibly work.
“However, the president of c-2i, Arnis Mangolds, continued fostering the development of the crawlers, and eventually won SBIR funding from the US Office of Naval Research, which had taken notice of the robots. That enabled us to develop them into a family of crawlers, the largest to date being the Bayonet 350, which is also our flagship product for US commercial and research markets as well as defence users such as the US Army Corps of Engineers.”
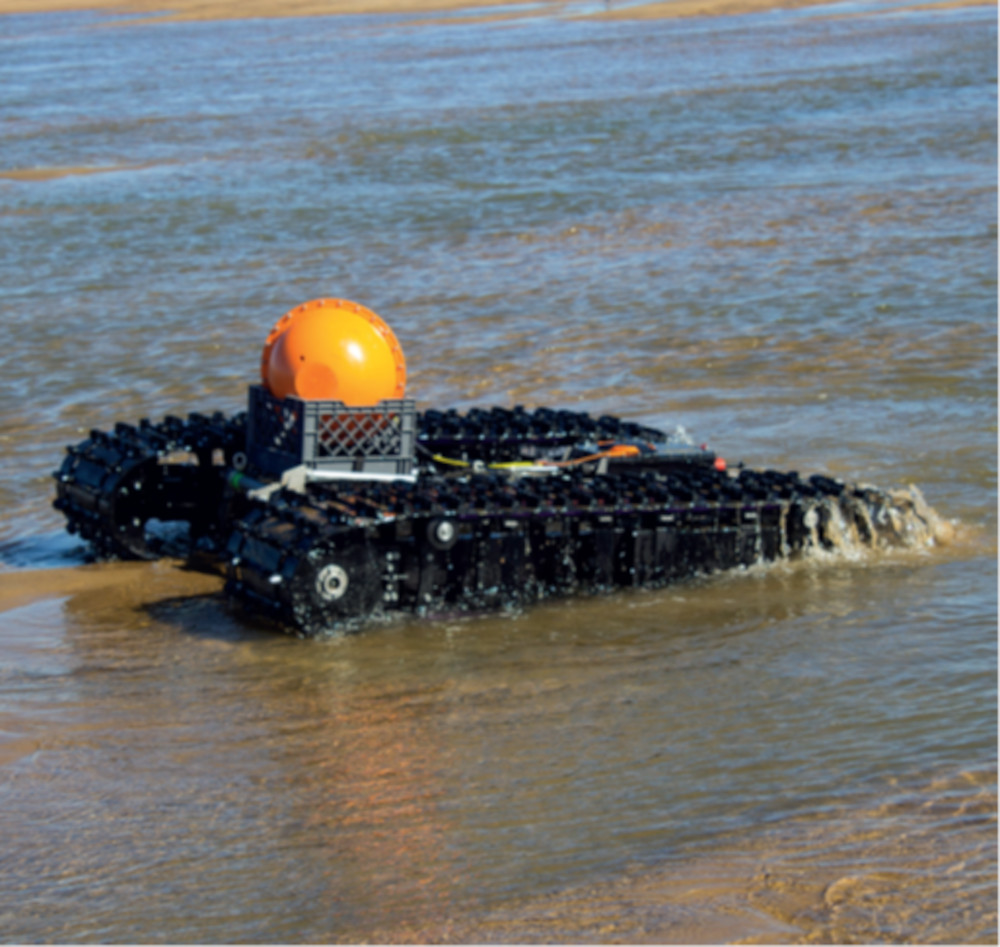
areas from beaches to near-shore waters, tasks
that most UGVs and UUVs are unsuited to
The Bayonet 350 is a flat, wide, battery-electric vehicle that runs on two caterpillar tracks; it measures 1937 mm long, 1522 mm wide and 381 mm in height. Its typical weight is 272 kg, its maximum operating depth is 100 m, and its standard operating speed is 1.8 kph. At that speed it can run for just over 21 hours at a time (with a range slightly greater than 38 km), although the company has found ranges of 64 km or more are achievable if it runs at lower speeds, and improvements in these are anticipated when newer battery technologies are installed.
Farinella says that by sitting still and directly against the seafloor, the Bayonet is perhaps the best platform available for geophysical inspections of the ocean crust, as well as detailed 3D mapping of ocean floor areas (down to 100 m below sea level, that is).
“Even human divers aren’t that great for work in the shallows,” he says. “As soon as the current picks up, they can get kicked around, pulled into rocks, and there’s sometimes wildlife to be wary of. “It can be costly and hazardous, and most often the work is either done poorly or it doesn’t get done at all. You also have sensor buoys as an option, but like AUVs they aren’t necessarily great for station-keeping.
“Our vehicle can go out, perform a data-sampling mission of equivalent scale to multiple buoys, then drive itself back up the beach to its operator without the operator needing to lift a finger to retrieve it. Properly designed UGVs will sit in more energetic natural environments, maintaining an accurate position for extended periods of time and without consuming battery life to maintain that position.”
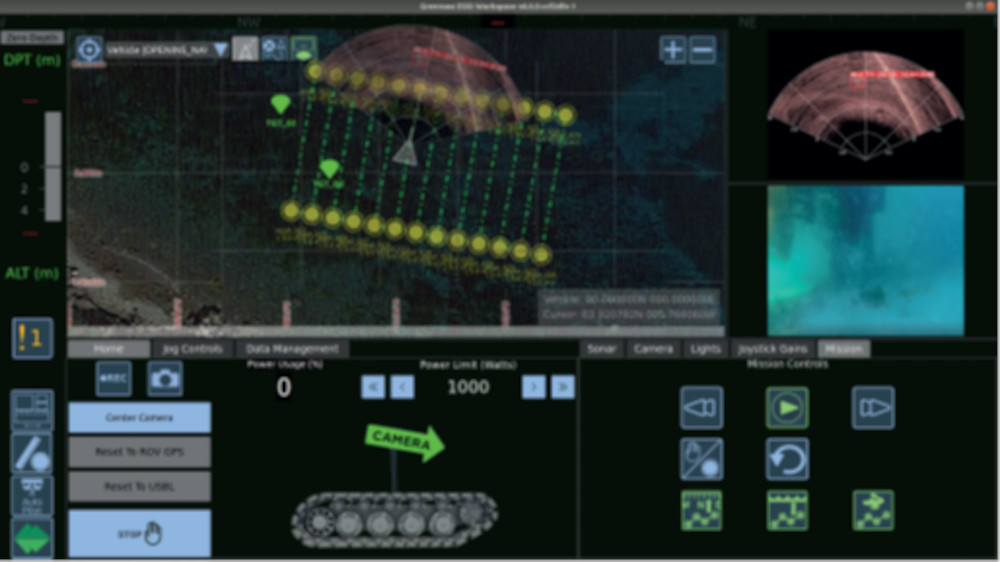
mission and survey data from the Bayonet 350
System architecture
Nick Hartman, Bayonet’s VP for strategy and growth, says, “AUVs and ROVs cover deeper waters with lighter currents, typically for the navy, while the army tends to cover waters that are further inland where the shore starts. Even the army’s ground vehicles aren’t really made for travelling into the surf zone.
“So, we’ve designed the crawler platform to operate in rough sea states and amid breaking waves, where AUVs and divers can’t, and we can carry different payloads to monitor whatever data the customer’s area of interest is.”
The Bayonets are made largely from hard, anodised aluminium structural components. Inside those are typically two battery packs, which send energy to the two motor controllers.
These in turn power and control two electric motors with gearboxes for driving the caterpillar tracks. The track assemblies are referred to in-house as the ‘pontoons’, and are integrated modules each containing one pack, motor controller, e-motor and gearbox, as well as two track wheels.
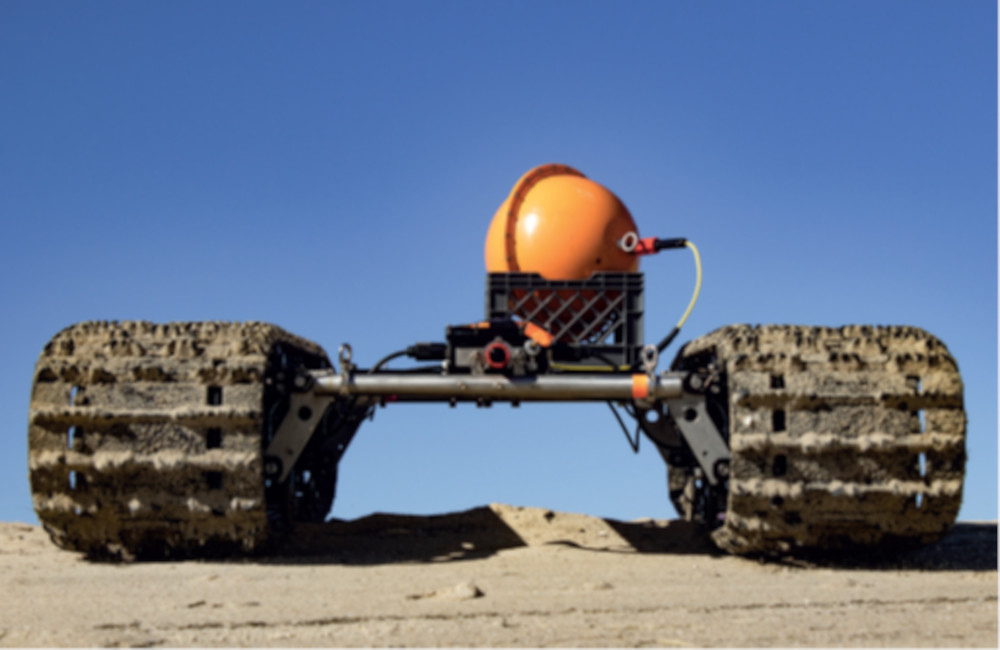
considerable payload mounting space,
with up to 195 kg of sensor capacity
Further up and around the mechanical frame joining the two pontoons is an electronics enclosure containing the computer systems for autonomous navigation and payload operation.
The track assemblies plug into this box to receive instructions for traction, speed and differential steering, with a proprietary single-board computer acting as the ‘brain’ of the AUGV and as the arbiter between the various subsystem-level computers such as the battery management systems, motor controllers and payload computers.
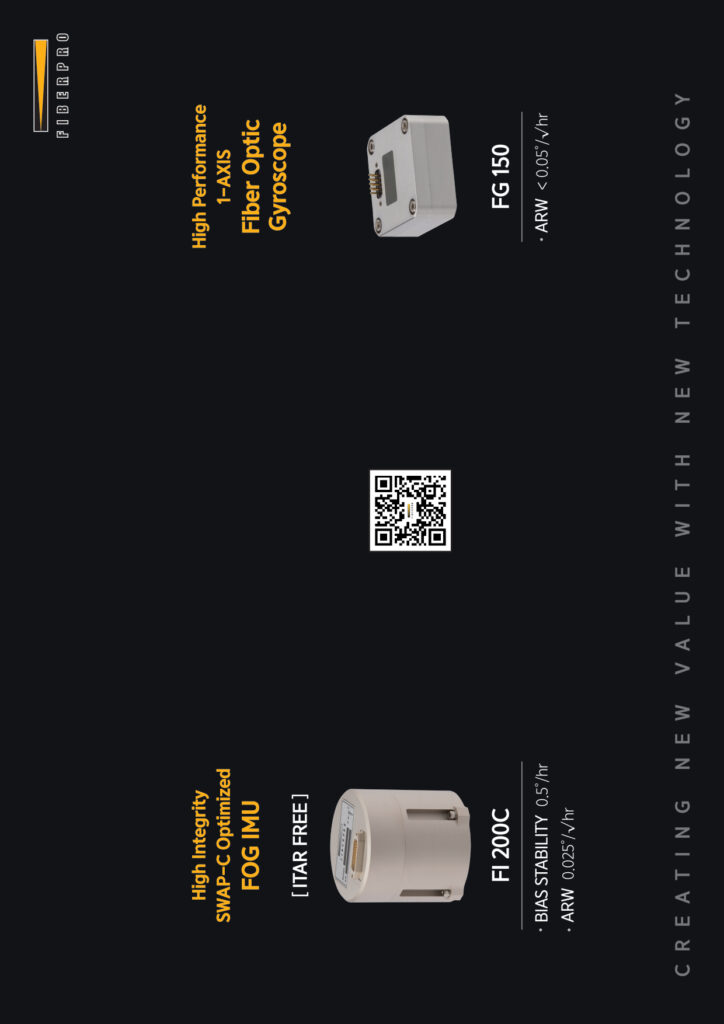
It is also in here that data comms user interface (UI) feedback including information from mission payloads – with up to 195 kg of sensors storable around the remaining volume and atop the deck – are processed before being delivered to the operator, who will typically be seated at their laptop or holding Greensea’s RNAV2 handheld tablet-and-joystick solution. In either case, Greensea’s UI software platform for command, control and data monitoring will be running for visualising the mission planning and its progress.
“The UI gives you feedback on where you’re going, including camera information if one is installed and the data link permits it, or sonar information,” Farinella says. “Control is achieved either through joystick or autonomous waypoint navigation; the autonomy can be interrupted from the joystick to investigate an object of interest, and after investigating it the autonomy can be continued from the last waypoint.”
Payload arrangements
On payload capacity, Hartman says, “We’re flexible with the amount of space we have and how we use it. We want these AUGVs to be the pick-up trucks of amphibious mobile robots – a simple tool that doesn’t take much training to use, and will carry whatever is needed, where it’s needed.”
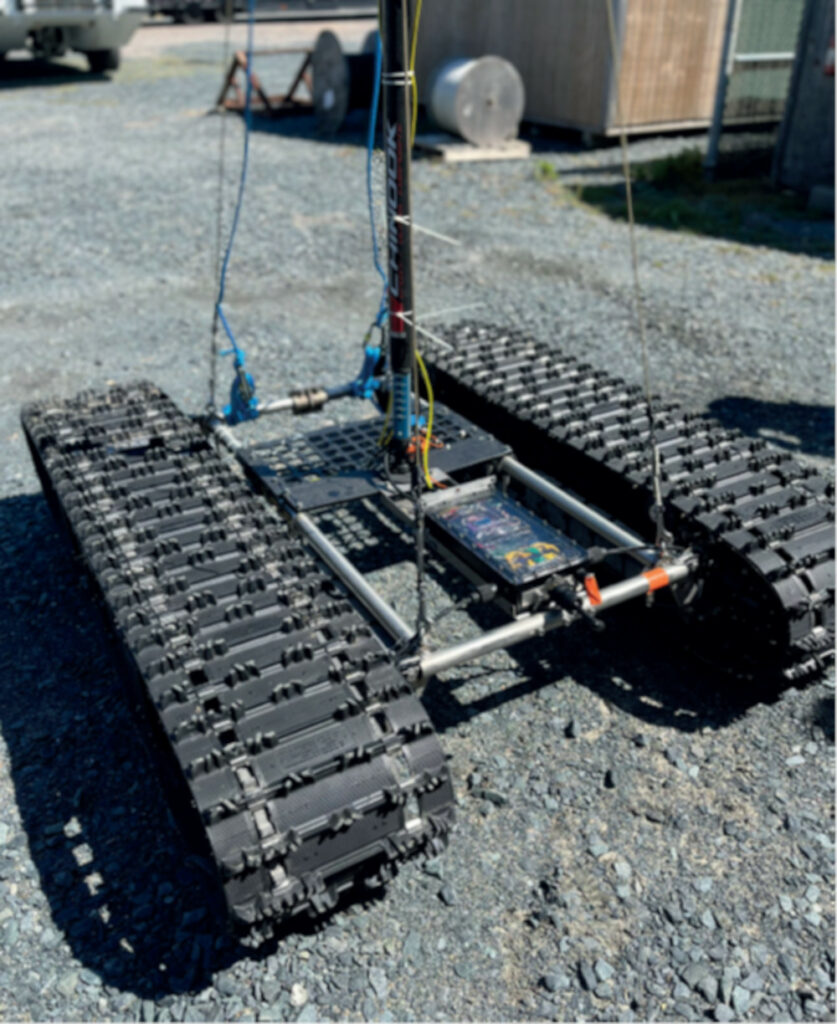
highly effective movement and
station-keeping in a wide range of
terrains, waves and currents
Farinella adds, “We can customise the deck space between the pontoons to make it as wide or as narrow as an end-user needs. We design the 350 as a wide vehicle to begin with, to fit the broadest sensor packages possible, and by virtue of experience and common sense, we can position each sensor wherever it needs to be to work.”
The OpenSea software platform adds a number of key architectural benefits to the UGV itself as well. First, it enables the Bayonets to be largely sensor-agnostic: the electronics network and connectivity arrangement are such that different end-users can plug in different sensors from a multitude of OEMs and gather and retrieve their data through the UGV and its UI mission software.
“Because of the numerous systems that Greensea have worked on to integrate and interface with over the decades, we have a large catalogue of OEM and COTS equipment that we can install – not just sonars, cameras, environmental sensors and other mission payloads, but also acoustic comms equipment, illuminators,” Hartman notes. “And their modules have been proven out over the years on all sorts of UUVs, so we can use them with great confidence in our AUGV.”
Farinella adds, “And of course, there are different kinds of sonars – forward-looking, side-scan, sub-bottom profilers and so on – that we can accommodate, as well as magnetometers and Lidars. At the end of the day the user is after information, and there’s no real limit to the type of data we can gather.”
Typically, side-scan sonars will be installed on a rack elevated above the UGV’s hull to ensure that the swathes travel out and over the pontoons without interruption. Forward-looking sonars, cameras and illuminators will be mounted on the front section of the forward chassis plate, also called the deck plate.
Water quality sensor bottles, depending on how many the customer wants, will typically sit in the space atop the middle of the hull (called the carriage plate), mounted and arranged as necessary for optimal data acquisition. “For instance, if the sensor relies on water flow, we’ll mount its collection aperture to face in the direction the 350 is driving in, or if it doesn’t really matter then we’ll just find some space and screw it in,” Hartman says.
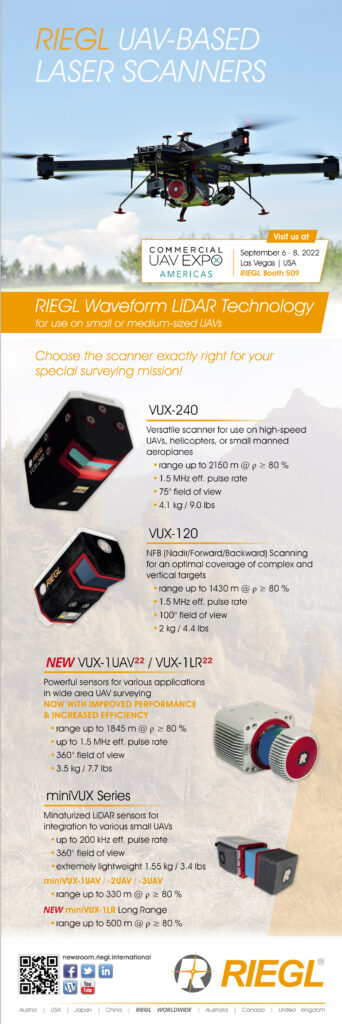
Locomotion and power
The Bayonet 350 runs on COTS rubber tracks. While heavy, by and large, Bayonet Ocean Vehicles has rarely found terrains that they cannot traverse.
“Right now, they are in a front-wheel drive configuration, but we can easily configure a 350 for rear-wheel drive: it’s just a software switch and a slight tweak or two to the usual assembly process,”
Farinella says. “We’re looking into all-wheel drive as well, and that would raise our game in terms of our maximum weight capacity to carry sensors and perhaps even a separate sensor sled towed behind the UGV.”
As mentioned, each pontoon contains a battery pack, a motor controller, an electric motor near the front and a gearbox. In an all-wheel-drive configuration, the 350 would essentially integrate two more e-motors near the back to double the total power to the track.
“The gearbox can be two- or three-stage, and we have different options for gear ratios depending on the speed or torque requirements for whichever Bayonet the end-user has and how they’re operating it,” Farinella says. “Our ratios can go as low as 5:1 and as high as 100:1.
“We have standardised the reduction ratio on the 350 but we’re not disclosing what that is yet; we tend towards higher gear ratios than lower ones though. This is meant to be a work-class vehicle, so our users tend to want to carry more, not less. That drives up the torque requirement, and higher speeds don’t do much to help when you’re carrying out sonar surveys.”
The lithium-ion battery packs are limited to 8 kWh of stored energy (to allow transportation by ship or air), for 16 kWh of total onboard energy, and can deliver up to 60 W around the vehicle at a time. That means up to 120 W is also the peak motor output, which is enough for the UGV’s 1.8 kph peak speed. “We also offer some options as far as power distribution is concerned,” Farinella says.
“We can install a dedicated payload battery with maybe an extra kilowatt-hour or more, or all the onboard systems can plug into either of the pontoon batteries, or we can install a distribution box that can actively switch power delivery between subsystems.
“It’s really a matter of the use case and preference. We’re a new company trying to break into new markets, and not everyone is going to want the same thing, so keeping our systems modular and flexible is a firm requirement.”
There is a charging port on the front of the 350’s control box, although users can also swap in freshly charged batteries without much difficulty. Notably, the 350 is engineered to be assembled in the field of operations without the need for tools.
“All the boxes and structural parts connect or disconnect in about 15 minutes,” Hartman says. “That’s really useful for maintenance logistics, because if you break one piece you just grab a spare one and stick it in.
“It also disassembles into a form factor small enough to fit in an SUV, or it can be carried in a bag upstairs or around tight corners, that sort of thing,” he adds. “The 350’s pontoons need two people to carry them, but that’s as difficult as it gets – the military pushed for that point especially hard, as they wanted the whole Bayonet system to be operated by as few people as possible.”
Navigation
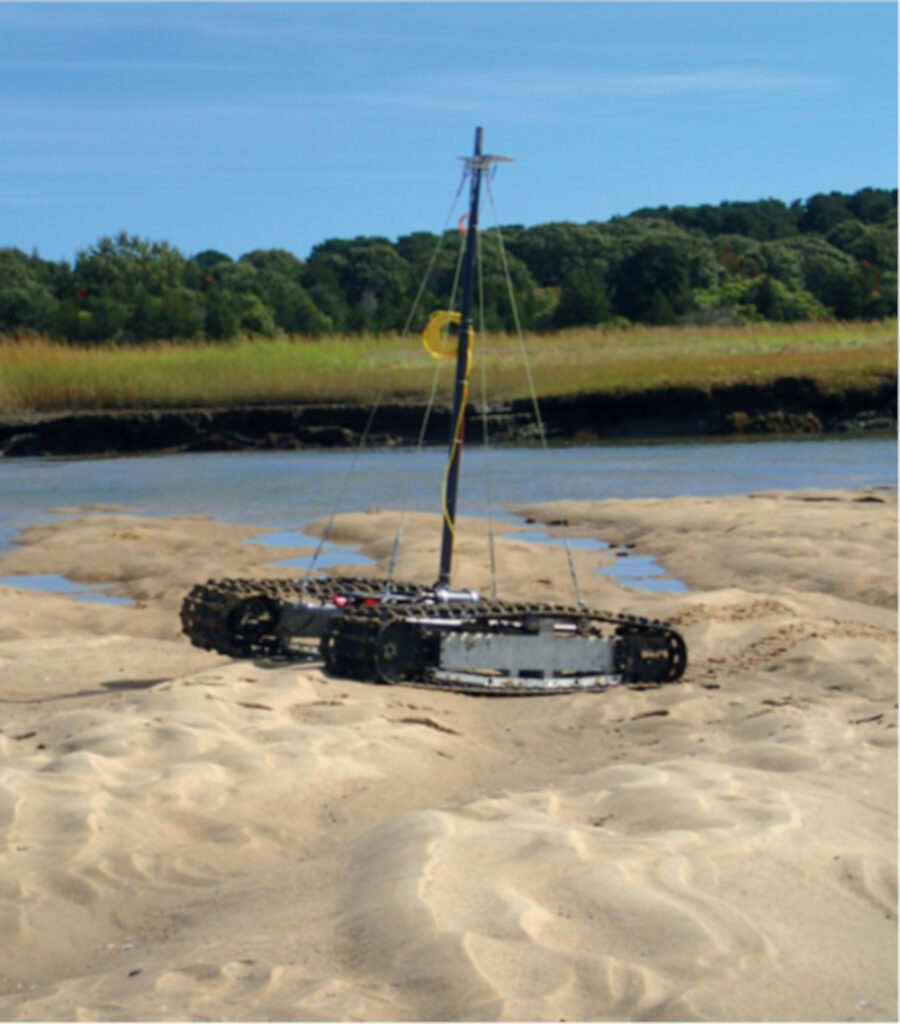
Bayonet 350 is above water, while USBL
is an option for subsea localisation
In essence, the Bayonet 350 has much the same navigational systems and capabilities as an AUV. Fibre-optic gyros (FOGs) are used to minimise GNSS drift during extended periods underwater, and electronic compasses help further in this regard by enabling intermittent ‘resetting’ of heading and drift information.
“Of course, we have no control over altitude – we’re restricted to driving across the seabed – but because we have a depth pressure sensor that’s accurate to 10 cm, and because we know where we are in terms of latitude and longitude, we can use the waypoint pre-programming system,” Hartman says. “We can tell the UGV quite easily where to survey, such as assigning it to a 2 km2 area, and we don’t have to worry about commanding it to go to a specific depth.”
Notably, if an end-user has access to a boat or pier and wants to save the UGV time and energy in navigating to its survey area, the company says it can be dropped into the water without being damaged when it hits the seafloor. However, driving from the beach into the waves is the recommended approach to launching it.
While it’s above the water, the 350 localises itself using GNSS. The GNSS and IMU are packaged and integrated in the Greensea GS4 INS, which in addition to its FOG contains a MEMS accelerometer and supports fusion with forward-looking sonar data for functions such as SLAM or feature-based localisation. It can also use other sensors such as USBL and DVLs.
“Theoretically, any navigation system could plug into our mission computer,” Farinella says. “If an end-user wanted something cheaper and didn’t care much about GNSS fidelity then we could swap something else in.”
Heading fidelity usually stays within 2.0º, which resets to a 0.25º accuracy when the compass is used, and although the compass helps to reset heading information, it cannot help with positioning. For these, USBL and DVL systems have been fitted on the 350’s hull for acoustic-based positioning, as enabled through the GS4.
Hartman adds that the OpenSea navigation algorithm allows sensor inputs to be prioritised. For instance, if the GNSS signal updates deteriorate below a certain threshold, the main computer can switch to basing its estimations using the DVL’s movement readings combined with the gyro and accelerometer.
“The DVL we use is an OEM design, and we get good support from them,” Farinella explains. “We can in theory select any DVL, but our selection is limited by the fact that the crawler is going to mount the DVL looking down.
“Technically, you could mount it looking up, to track the rate of movement against the waves, but what we’re trying to measure is the movement of the ground underneath it.
“That means there’s about 10 in of distance between the DVL’s transducers and the ground, and if a particular DVL can’t handle that short a distance then it’s no good for our application. More and more models these days are able to achieve that in how they’re engineered though.”
Dual RTK-processing for GNSS is also available for helping with survey and heading accuracy in real time, so long as a link through the water is available.
As a final note on the OpenSea underwater navigation platform, Hartman comments that there are three levels to the software’s capabilities.
The first is a basic tier for hands-on, joystick-based control. The second, ‘pro’ version, is geared more towards autonomous operations, with the setting of survey areas and routes, and the highest tier is called EOD Workspace, which encompasses modules and plugins for higher-level autonomy.
“Those modules would be things like automatic target recognition, smart obstacle avoidance and other things that make use of much more heavy-duty sensors and processors, such as forward-looking sonar or HD video to ‘diagnose’ what objects might or might not be, such as a creature or a mine,” Farinella says.
“That’s important, because we also offer three versions of the 350 – the basic version, the pro version and the EOD Workspace version – with payload sensors and software configurations often pre-packaged to fit what the end-user needs. We can put in Greensea’s most advanced offerings and capabilities with the required sensors, in navigation as well as payload terms, but we wouldn’t do that for a customer who just wants the basic version.”
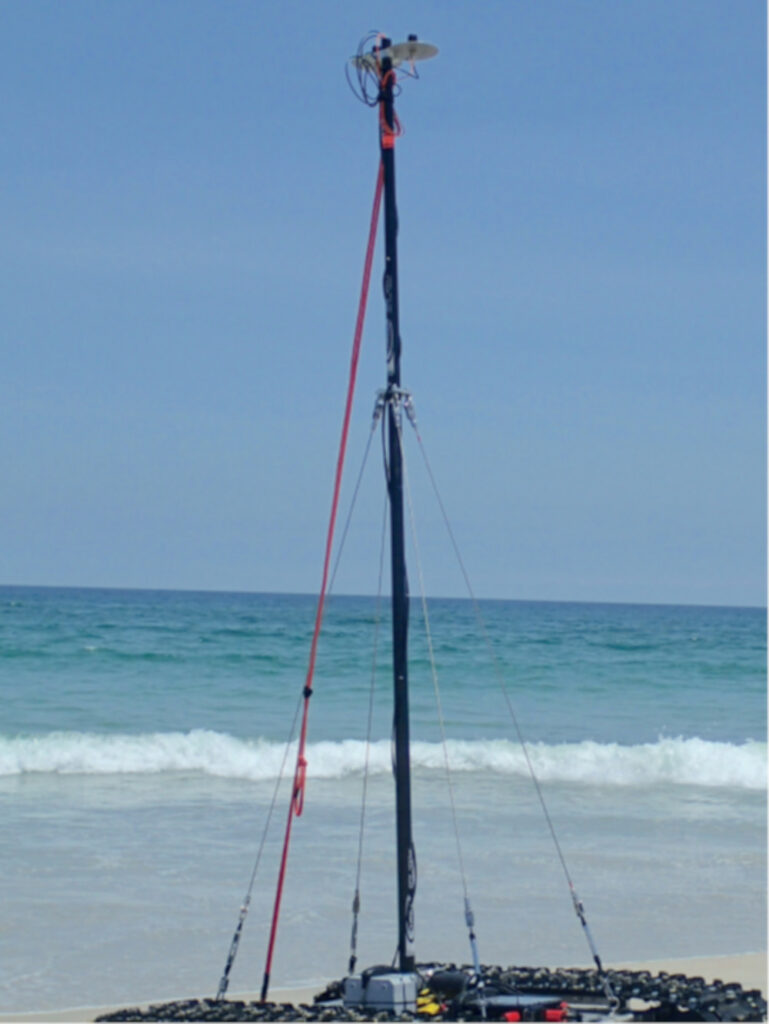
the Bayonet 350’s mast for real-time
data transfers while 5.8 m underwater
Data reception and storage
Various data link options are available for end-users to receive mission and payload telemetry at their console in good order. In principle, wireless RF links can still work while the 350 is submerged, as the waters are often shallow enough that the data fidelity is not completely attenuated over the distances between the UGV and the surface.
“Also, if someone just wants the basic version of the vehicle, by and large they’ll need only minimal radio frequency comms – they’re unlikely to attempt manual operations beyond dipping past the waves every now and then in a straight and predictable line,” Hartman says. “The pro version can also use that ‘wireless tether’, and if it goes too deep for the signal to reach the surface it can still navigate its path well enough until it gets back to a point where there’s a good signal again.
“The EOD Workspace version comes with an added companion computer, which plugs and plays into the main electronics box for extra computational power to handle the extra autonomous decision-making that comes with it. And if that or the pro version need higher bandwidth comms so that the end-user can track what the vehicle is doing, we have some extra options there.”
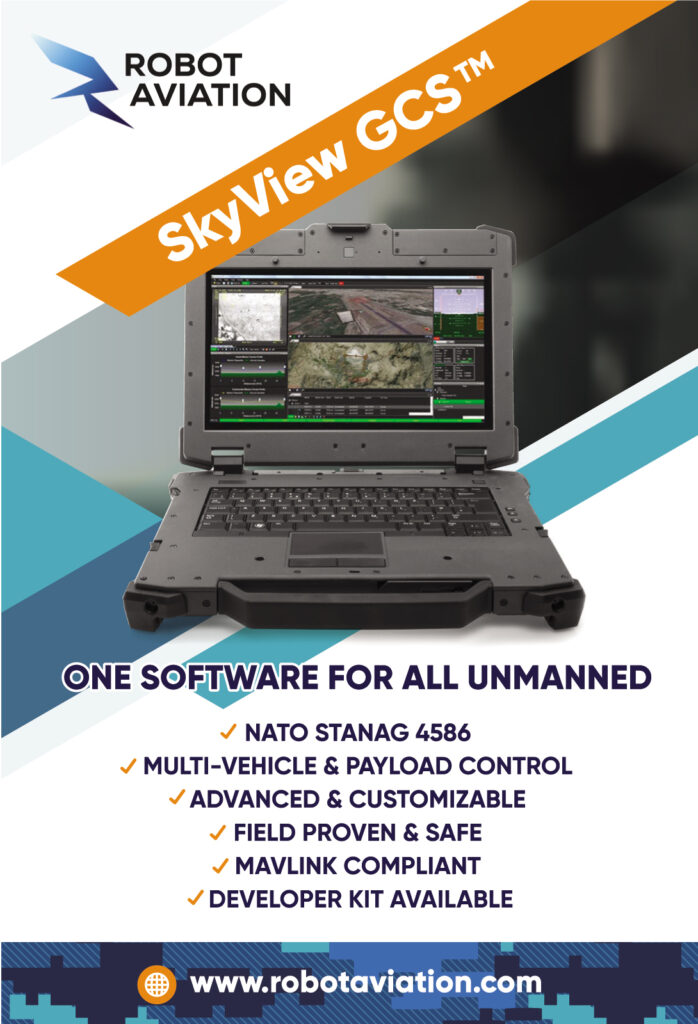
For instance, to perform higher fidelity subsea wireless comms, an acoustic modem with a range of up to 2000 m can be installed. The company cautions however that the actual practical range for reliable and consistent data is likely to be far less, and indeed the 350’s maximum depth is much less, making such ranges unnecessary in the first place.
“Acoustic comms is really the bottleneck for underwater vehicle missions these days; you can’t get a whole lot of information through those systems,” Farinella says. “And the crawler’s collecting an enormous amount of information, so the user has to prioritise what goes up to the operator to achieve a specific mission.”
Hartman adds, “Greensea has worked tirelessly on ordering that within its comms protocols. There’s a specific module within OpenSea that prioritises data for low-bandwidth comms, which is critical for the kilobytes of data we’re limited to with acoustic comms.”
Other options are available for higher bandwidth data transfers. For one, an RF antenna mounted on a long and telescopic mast can be installed atop the 350, and systems up to 5.8 m tall are available in this regard. Alternatively, an RF buoy connected to the 350’s main computer by electrical or fibre-optic tether can float on the surface to provide persistent data streaming over the course of operations.
“In all circumstances, if data links really aren’t available then data will be stored in a 2 Tbyte hard drive on the vehicle, so that when the mission is complete, the user can retrieve the UGV, remove the hard drive and perform their analyses,” Hartman says.
Farinella adds, “We’re also now getting into edge processing, which will allow for copious data to be stored and processed on the vehicle itself. We’re engaged in a research programme that’s looking into how we can best do that in our environment.”
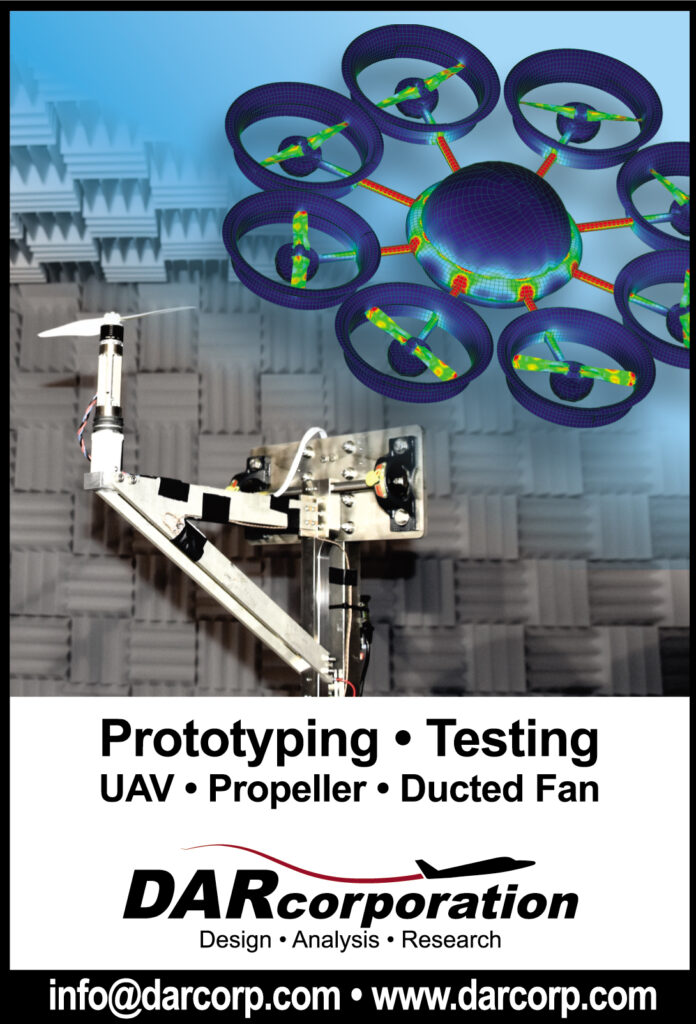
Future plans
Although the technologies on the 350 are largely mature, the company plans to upgrade the power systems in the year ahead, not just for more power density but for smarter and more precise energy management, to gain a better understanding of how energy can be conserved.
“We have a very intelligent comms network throughout the 350 and back to the GCS, and we’d like to make better use of that in how we send and use readily available information on power usage and needs throughout the vehicle – we think there’s a lot to be gained there,” Hartman says.
Farinella adds, “When you look at all the smart things being done in e-mobility, there’s no reason we can’t apply those to our robots on the beaches and below the waves. When the time comes, we’ll be working on larger crawlers, such as a Bayonet 450, and more powerful crawlers further down the line.”
Specifications
Bayonet 350 Underwater UGV
Size: 1.8 x 1.5 x 0.3 m
Weight: 272 kg
Payload capacity: 159 kg
Maximum speed: 1.8 kph
Maximum range: 38 km at 1.8 kph, 64-plus km at slower speeds
Maximum depth: 100 m
UPCOMING EVENTS
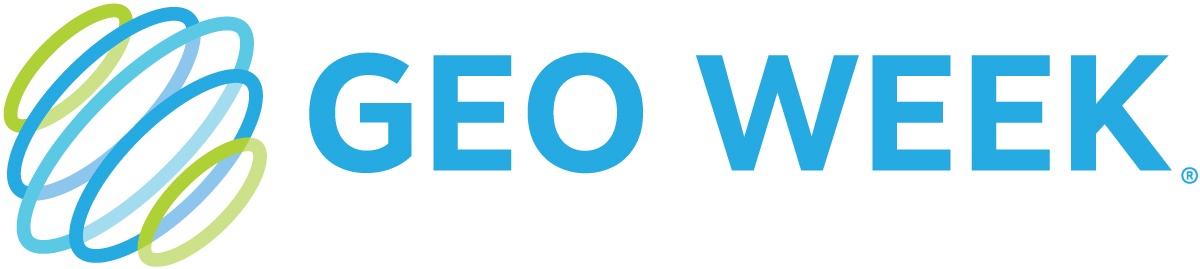
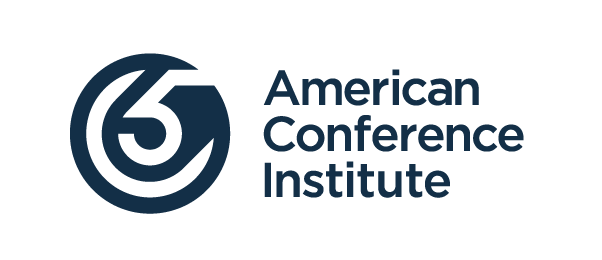
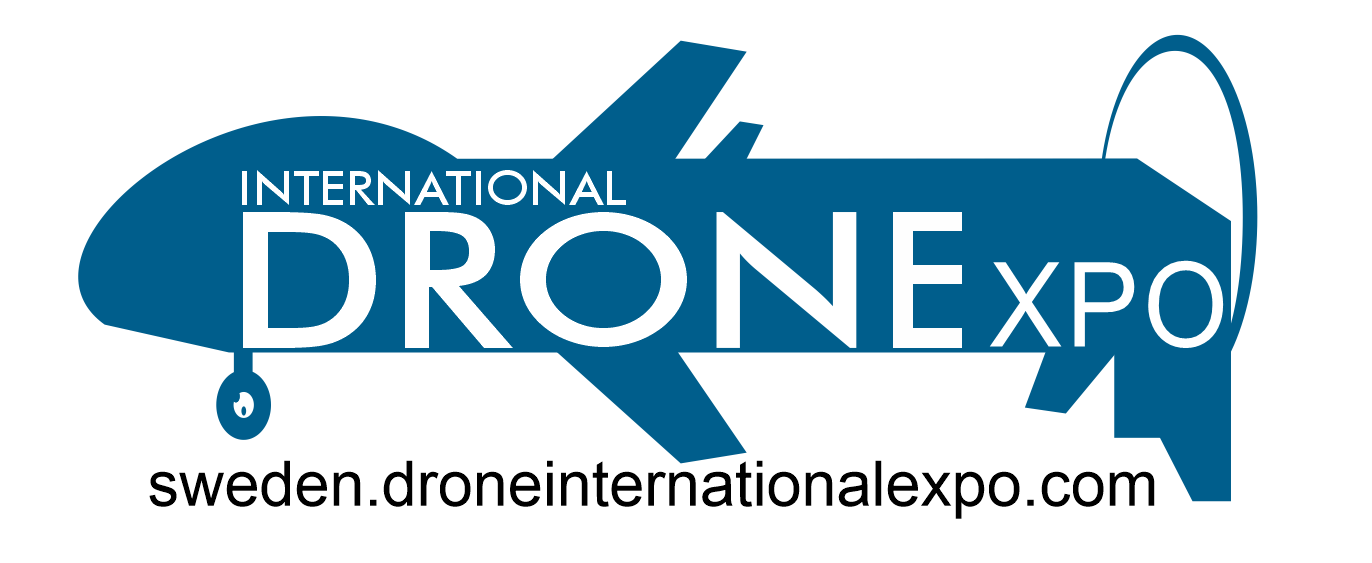
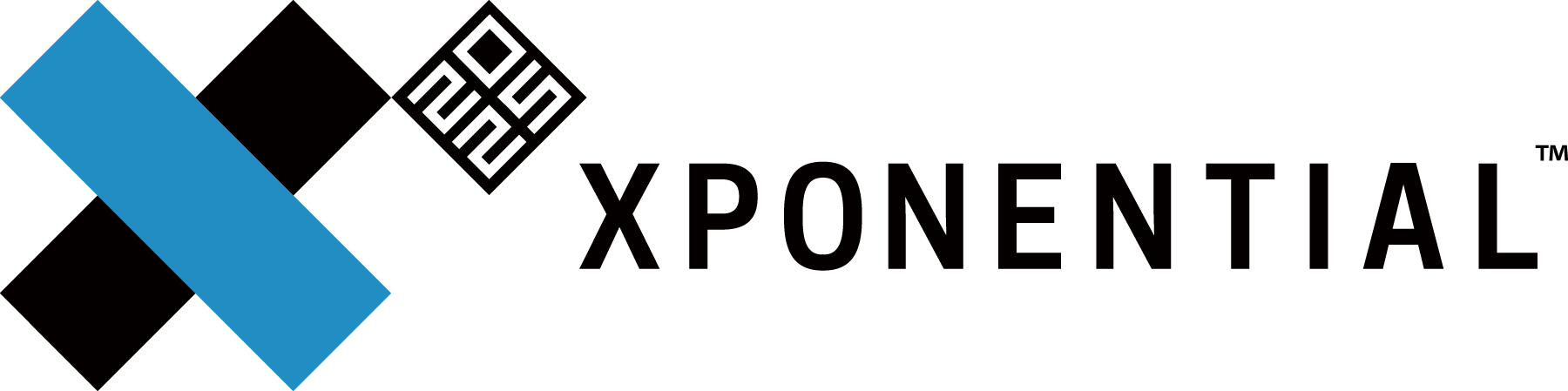
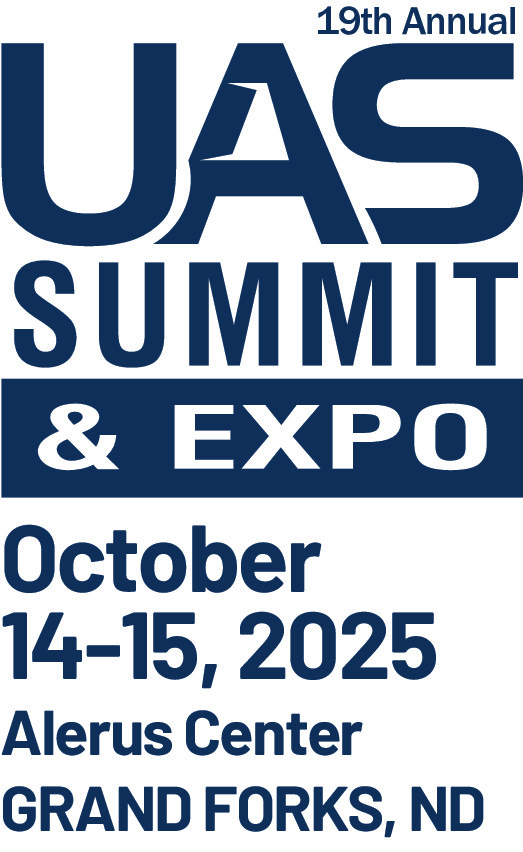

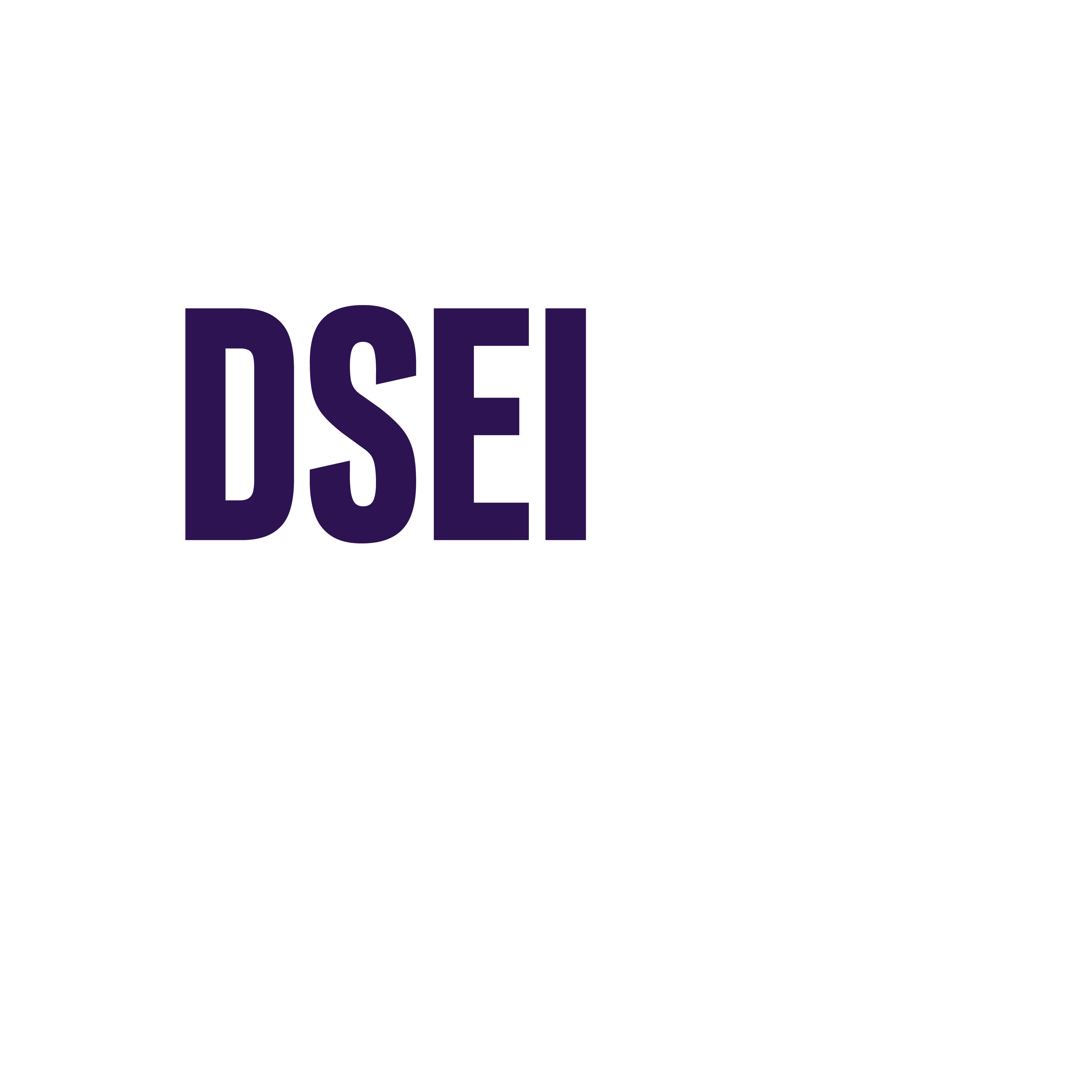
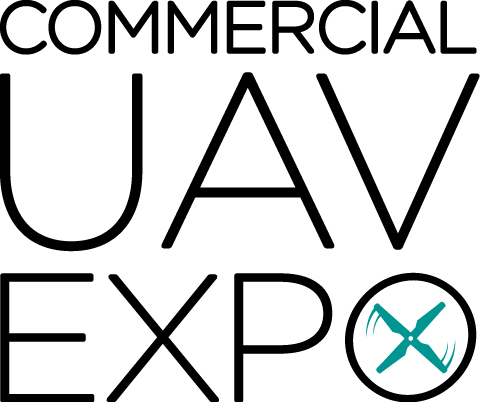
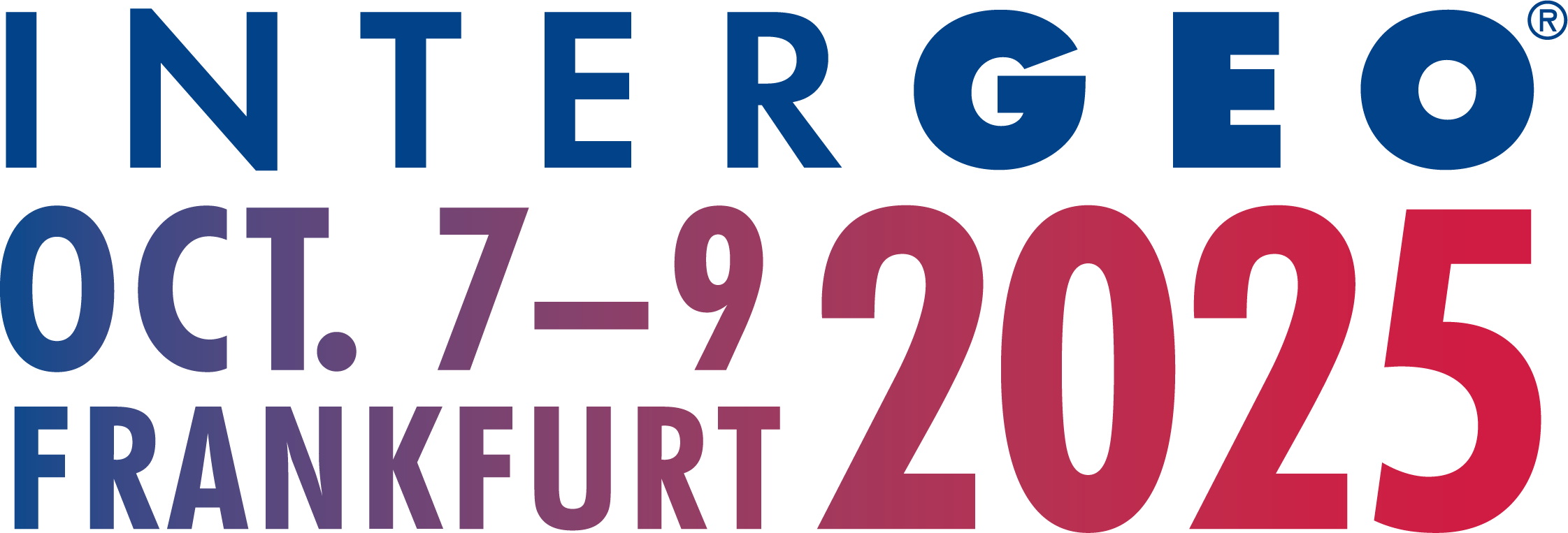
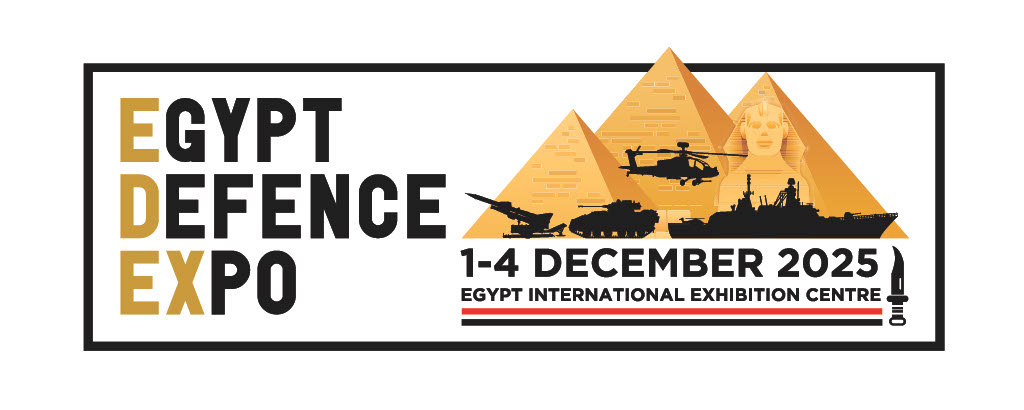
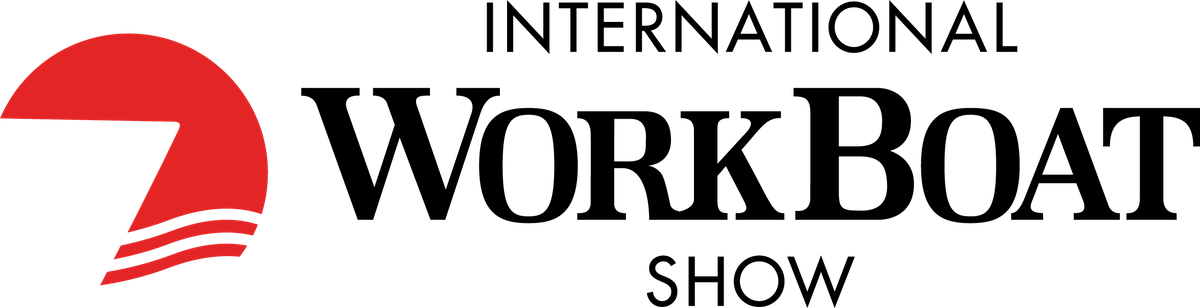