AUVSI Xponential 2022
Extra credits
Following his highlights in issue 44, Rory Jackson offers another wealth of new products and services announced at this year’s expo for the uncrewed industry…
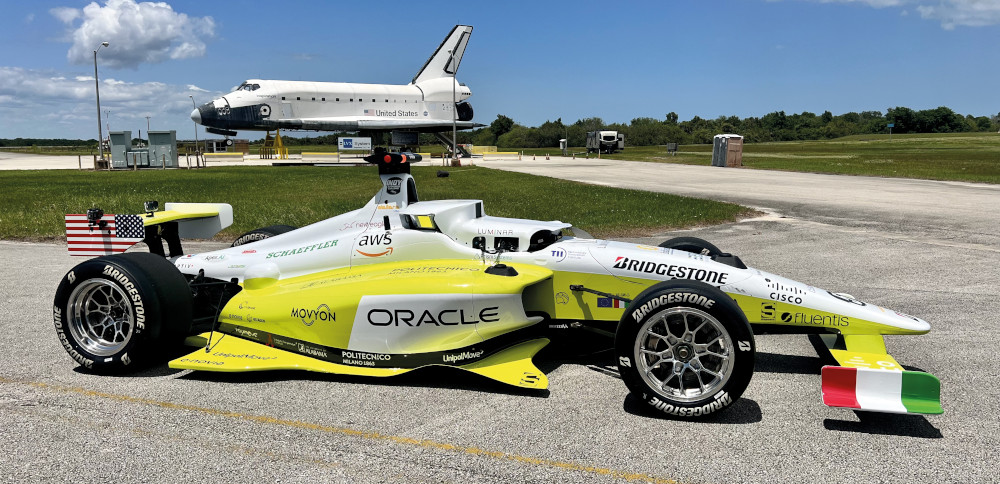
(Courtesy of the Indy Autonomous Challenge)
The AUVSI Xponential show is the largest annual technology exposition in the world for the autonomous and robotic vehicles industry. With so many new systems and subsystems making headlines, and companies looking to share their latest innovations with us, the challenge of fitting all the news into one issue of this magazine rears its head every year.
To that end, we present this second half of tech announcements and new developments from the show, to round off the remaining – but by no measure less newsworthy – items we encountered at that seminal event.
Team PoliMove of the Indy Autonomous Challenge (IAC) dominated headlines for the second day of Xponential by achieving the world land speed record for an autonomous vehicle.
The record was set at the Kennedy Space Center’s Shuttle landing strip – the world’s longest runway, at 5 miles long, and therefore an ideal place for high-speed tests – with the standards for the record having been published by the FIA.
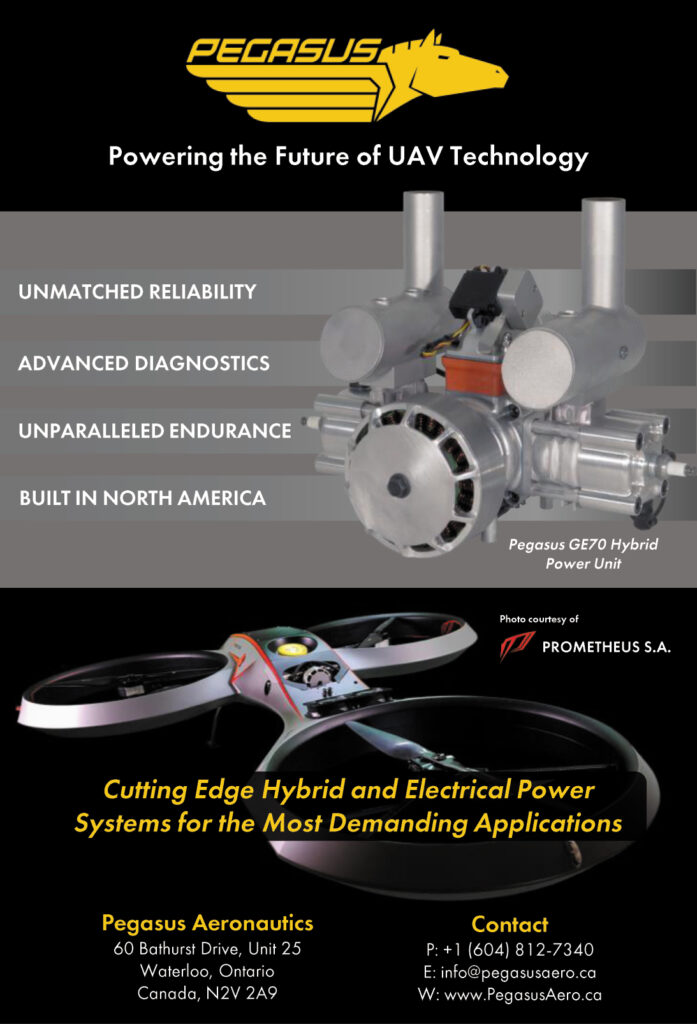
“They require that you take the average speed of two consecutive runs: out and then back again, a kilometre in both directions, and we achieved an average speed of 192.2 mph, or 309.3 kph, over the old record of 175.5 mph,” said Paul Mitchell, president of the IAC.
“The IAC racecar is manufactured by Dallara, and is powered by a four-cylinder Honda Performance engine, modified with some turbos for additional speed. We wanted to make sure all the teams had the same car, same hardware, same initial base software, and the same tried-and-true engine.
“That was largely because there’s so much complexity in the autonomy system that we didn’t want teams to have to look after some exotic powertrain with untested parts – at least not in the initial2021 and 2022 events.
”The autonomy stack on each racecar is designed and integrated by the teams themselves. Typically, it consists of some combination of perception sensors such as Lidar, radar and EO cameras, the drive-by-wire system, GNSS for localisation, a Cisco wireless link for sending car data back to race control, and a main computer consisting of an Intel CPU and an Nvidia GPU, both supplied by ADLINK Technology, for processing sensor data.
“Lidar has been the most critical perception sensor for this competition, given the speeds the cars are moving at and the importance of detecting turns or other cars if they’re racing head to head as they did for the CES 2022 challenge, ”Mitchell noted.
“Luminar is the official Lidar supplier to the IAC. They have a great product, and the teams have been pleased with it, but technically speaking there’s a wide range of sensor types they could choose from.
”Professor Sergio Matteo Savaresi, team leader of Team PoliMove, said, “To win the head-to-head challenge at CES, we needed a full autonomy software stack for optimising localisation, control of dynamics, perception, and many other elements and functions.
“What we also needed in the land speed record attempt was in some ways simpler but in others more complex and critical. The two things most important in autonomously handling a really high-speed straight are maintaining control, which is not easy at 300 kph, and prediction of trajectory.
“GPS can give you a good position output, but when you’re moving close to100 m/s, a seasoned human racer can automatically predict well what they’ll need to do in 100 m but the computer can’t without the right programming. If it makes errors in that, the controls pull in the wrong direction and there are huge risks of instability in the car. That’s the technical challenge we had to face, and no-one’s ever deployed an autonomous car in that way before.
”The ECU was left largely untouched for the record drive, other than ensuring it kept the Honda engine producing 500bhp. The perception software meanwhile was configured to enable sensor data to be processed by the main computer and output control decisions to the steering actuator in a continuous loop updated every millisecond.
“We are using an ROS-2 framework based on a Linux machine,” Savaresi added. “Within that, we use a high-level Simulink software code as well as more traditional C# code.”
“ROS-2 is flexible like that. You can use many different programming tools, which is important because you have many different issues to solve in high-speed autonomous driving. Processing Lidar signals for instance is very intensive from a data point of view, so you need a very capable GPU as the platform for it. Also, doing traditional things alongside that such as managing IMU data requires a lot of different software skillsets.”
The largest static display in the expo hall was Aergility’s ATLIS VTOL UAV, which the company unveiled in its full-size form, ready for long-range heavy-lift cargo delivery in disaster aid relief, defence and other critical supply applications.
“The ATLIS’ VTOL capability means it doesn’t need landing ports – it directly loads and unloads supplies exactly where they need to be,” said Jim Vander Mey.
“That includes medical and food supplies to remote islands, hundreds of thousands of villages in Africa without easily serviceable roads, and even equipment and water to frontline military operating bases, without putting human pilots, truck drivers or logistics officers at risk and without incurring high costs.”
The ATLIS lifts off using battery energy to power six fixed-pitch rotors, then uses a turboprop to transition into forward flight with the e-motors transitioning into autorotation. In this mode, the rotors still provide lift but do so passively, without consuming any net power.
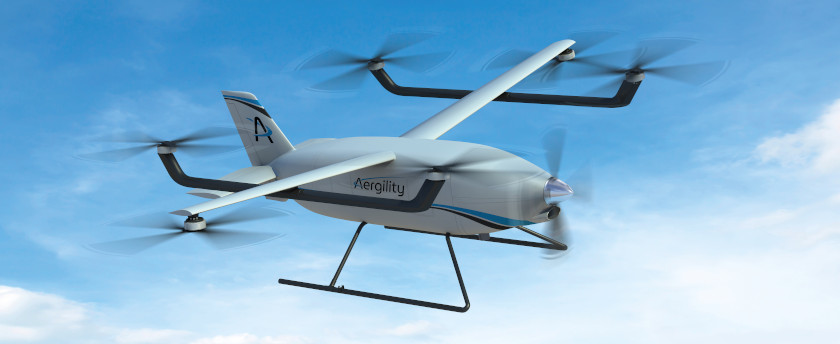
“That’s our patented ‘managed autorotation’ technology. When we bank right, we draw power from the right-hand rotors, and put power into the rotors on the left,” Vander Mey explained. “So we use no control actuators for banking, roll or pitch, and in cruise mode the e-rotors become highly efficient thanks to the passive lift from the ATLIS’ small wings carrying half the load.”
The craft is powered by a TP-R90microturbine engine from Turbotech SAS(an engine explored in detail in UST31, April/May 2020) that produces 90kW and consumes just 22.5 litres/hour.Emrax, in Slovenia, custom-designed itsaxial-flux electric motors using specialisedwindings and bearings for optimising theefficiency with which power is producedand regenerated (and as mentioned inissue 31, the motors are driven by newSiC ESCs from Advanced Power Drives).
The ATLIS was designed by Aergility using CFD simulations and multiple generations of scale aircraft flight testing, optimised for manufacture by Airboss, and manufactured by Composites Universal Group.
“The mean TBO for the micro turbine engine is 3000 hours, and almost everything else on the aircraft lasts longer still, so our maintenance requirements are as minimal as our energy requirements,” Vander Mey added. “All that combines to create a rapidly deployable and cost-effective tool for humanitarian aid and resupply organisations around the world.
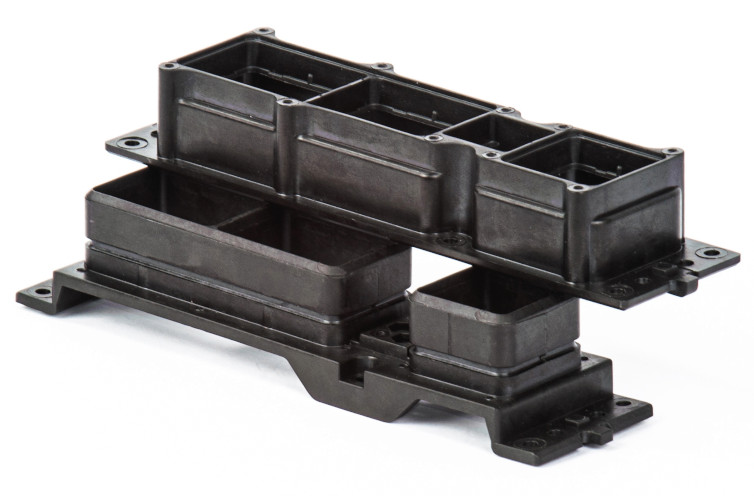
”First-time exhibitor AlpineAdvancedMaterials showcased its HX5 material,an injection-mouldable nanocomposite reinforced with carbon fibres, and discussed some its history and qualities.
“HX5 was developed for the F-35program at Lockheed Martin over 8years and $50 million in r&d, and led to a formulation for a direct replacement for 6000-series aluminium,” explained Jeremy Smith.
Alpine holds the exclusive, global, perpetual licence to distribute HX5,which it offers to aerospace, defence, space and other markets. It has a tensile strength of 38.3 ksi at 22.7 C, and at 122C still has 27 ksi of strength.
“It’s a high-temperature material, with 93% of the tensile strength of 6000-Aland half the weight, so gram for gram it’s much stronger than aluminium, ”Smith added. “It also has some unique characteristics such as a high surface energy, which allows it to be painted or plated with a wide range of function alor decorative coatings including high-temperature ceramic coatings.
“It also has a low viscosity and so it flows very well into complex moulds and shapes. Traditional composites have trouble achieving that while matching our strength and temperature performance. UAVs are a great beneficiary from the strength-to-weight increases that HX5can drive, without sacrificing parameters such as performance, lifetime and ruggedness in harsh environments.”
HX5 is non-hygroscopic and resistant to scratches, abrasion and galvanic corrosion, as well as chemicals including solvents, fuels and lubricants. It can also be machined and bonded for combination with other materials and structures without much difficulty, while meeting industry guidelines on performance amid flames, smoke and toxic environments.
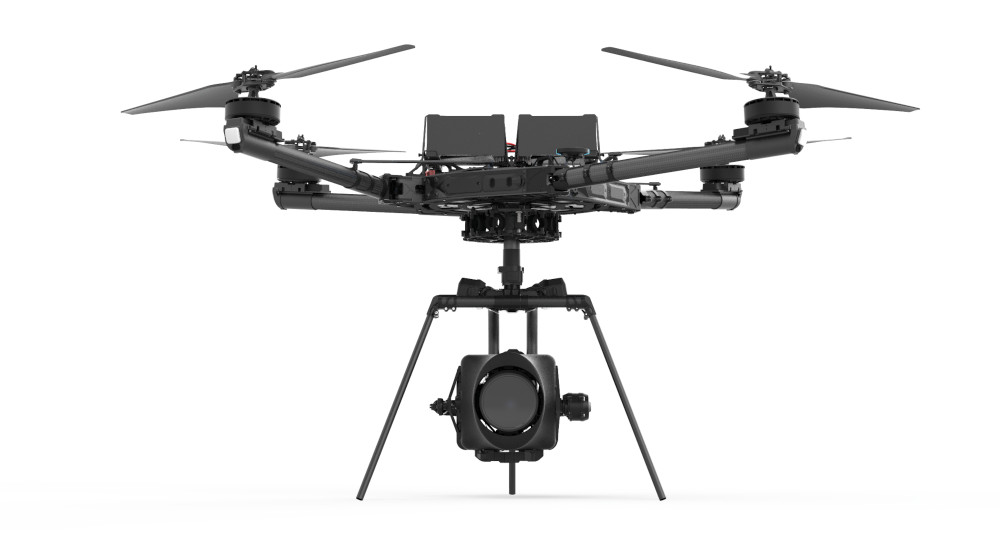
In addition to unveiling its Astro UAV (as discussed on page 58) FreeflySystems also attended the show to promote the continued development of its Alta X UAV. It has been designed principally as a multi-role heavy-lift system capable of flying for long durations and at high altitudes, and modularly configurable for a wide range of operations.
“Its first adopters were those in the cinematography market, who remain our core customers to date,” said Matt Isenbarger. “They use it because it can safely carry huge camera packages while performing highly dynamic flight manoeuvres. It also has very robust vibration isolation, so that even during its most extreme manoeuvres and power outputs the video still looks pristine.
“It has very large props as well, so they can spin at a relatively low speed, reducing noise, which is enabling filming of wildlife in a way that wasn’t possible before. It’s also important for a lot of sports, with Red Bull for instance being a key customer for filming the sports and athletes they sponsor across golf, motorsport and elsewhere.
”To succeed in the cinematography market, a UAV must be long-lasting and robust, or it could crash and destroy a $200,000 camera or lens each day. Isenbarger’s colleague Tabb Firchausaid one customer has used an Alta X to take shots of crewed aircraft flying at 200knots, as well as to inspect more than8000 miles of power lines.
Freefly Systems is now working with a range of potential customers who are exploring ways to use the Alta X in firefighting and logging, particularly in the high-speed transport of critical tools or supplies across difficult terrain.
“The Alta’s proprietary Activeblade technology is designed around pushing the prop size as large as we can go, with the blades ‘flapping’ slightly to equalise the centre of pressure across the disc during forward flight,” added Firchau “That reduces vibration to a similar level of helicopters’ tail rotors, making it desirable for customers besides just film crews.”
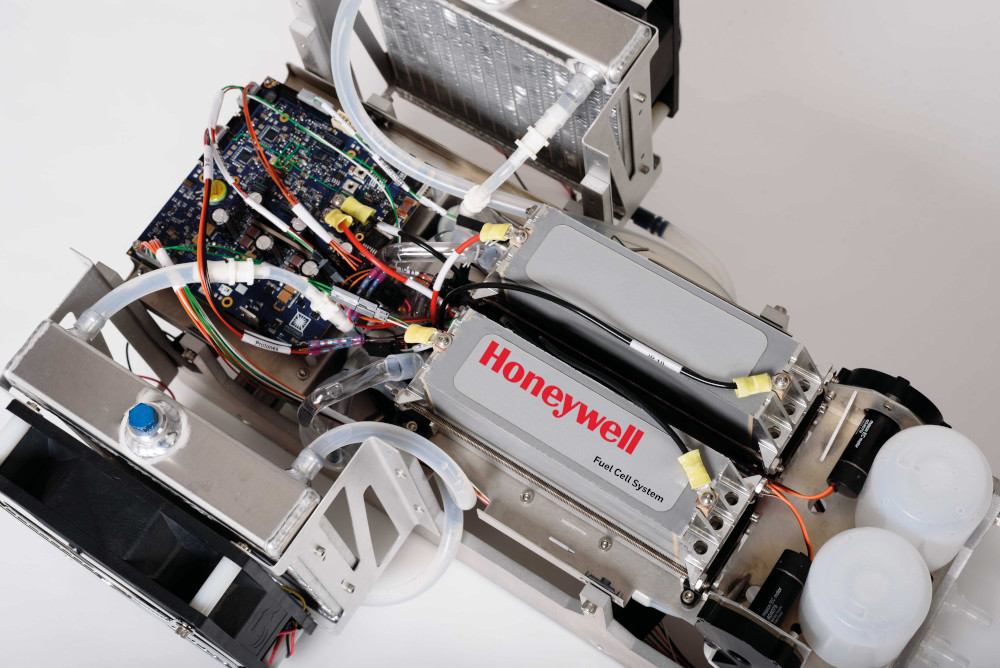
Honeywell Aerospace attended the show to launch and promote a range of new products for the autonomous world, for applications including navigation, collision avoidance and power.
The first was the Honeywell HGuideo360, a GNSS/INS developed as a single-card OEM version of the company’s previous and more ruggedly housed n380 INS. The o360 is RTK- and dual antenna-compatible, with horizontal position accuracy to 1 cm and vertical position accuracy to 2.5 cm under RTK processing, as well as giving heading readings to within 0.06ºand pitch and roll accurate to 0.015º.
“It’s a very similar sensor package in the o360 as to the n380, including our i300 MEMS inertial sensor system and a GNSS on the card, to help UAV and other uncrewed systems engineers perform straightforward board installations of their navigation systemin as flat a package as possible,” said Andrew Bundermann.
“We’re also launching our new g080,which is a GNSS-only system. It’s a similar enclosure-less OEM design, and Honeywell’s first foray into single-card receivers.
”The g080 is compatible with GPS,GLONASS, Galileo, Beidou, IRNSS and QZSS signals, with options for L-band correction inputs and full ROS support. GNSS data is output at 10 Hz as standard, but higher rates are available on request.
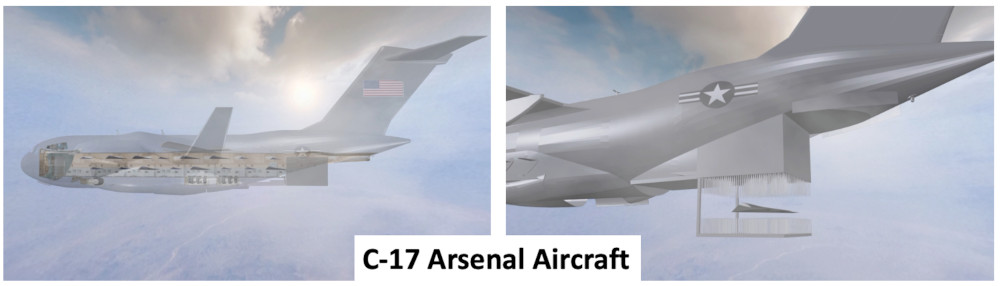
Honeywell also showcased its low-SWaP Resilient Nav system, which is designed to enable multiple layers of navigational safety for UAVs working in GPS-denied or -degraded conditions. The first layer of resiliency is an anti-jamming system – GPS dome – which provides protection to GPS signals while operating in low-power jamming environments.
The second layer in the system is Honeywell’s Compact INS (HCINS),which provides accurate positioning during intermittent GNSS disruptions. Finally, Honeywell’s Radar Velocity System (HRVS) is the last layer of protection, for longer GPS disruptions. HRVS in combination with HCINS &GPS dome will provide position with an accuracy of 1-3% of distance travel lederror, to allow UAVs to navigate BVLOS autonomous missions without GPS.
Honeywell also showcased a UAV that integrates the first version of its IntuVueRDR-84K band radar system, which has been designed as an airborne collision avoidance system. The RF antenna, algorithm, and tracker technology from the company’s radars used on Boeing 747s have effectively been miniaturised into a form factor that Part 107-compliant UAVs could carry to detect non-cooperative UAVs that fail to broadcast transponder codes or ADS-B information.
Flight trials of the system consisted off lying the IntuVue-equipped UAV within distance of another, non-cooperative UAV moving at similar altitudes. The first aircraft successfully detected the second and calculated optimal trajectories for steering around it, before returning to its original course. These functions were all performed autonomously and without incidentroughly 300 ft above the ground.
With the concept now fully proven, Honeywell anticipates designing future IntuVue products for small, Class 1UAVs up to very large advanced air mobility craft and heavy-freight UASs. The upcoming Version 2 radar will weigh1.5 lb and consume 65 W on a 28 VDC supply. Commercial availability is expected by either late this year or early2023, with initial fabrication runs having being completed at the time of writing and testing phases being imminent.
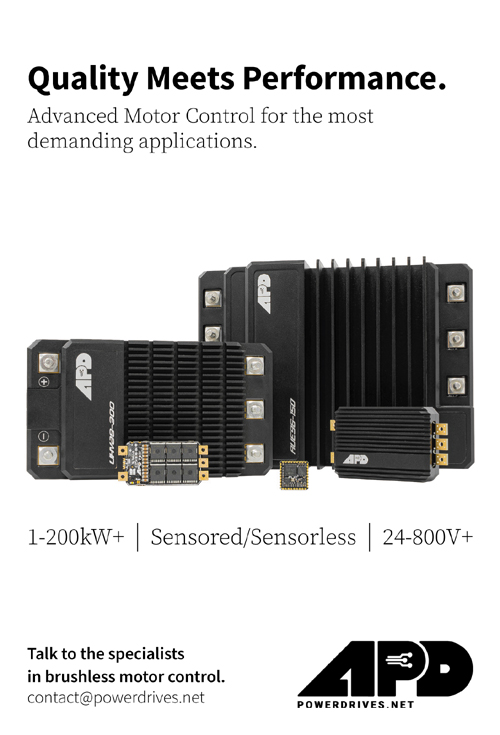
Lastly, Honeywell also displayed its range of hydrogen fuel cell systems. Two products currently exist – the 600u, a600 W liquid-cooled PEM fuel cell, and the 1200u, a 1200 W version, which is effectively a dual, modular assembly of the 600u – although the company plans to go to 2-3 kW solutions in the future as commercial and defence UAVs continu eto be built larger and heavier.
The solutions currently available are aimed at smaller hexacopters and octocopters, as well as some fixed-wing VTOL-transitioning designs that can leverage the fuel cells’ power better for long-endurance missions through low-power cruise airspeeds. Both systems have an MTBF of 1000hours for the balance of plant and3000 hours for the fuel cell stack. They operate from 5 C to 45 C, and consume hydrogen gas at a rate of 53 g/kWh when outputting 200 W.
Both systems extend flight range and duration to about three times that of an equivalent battery-powered system. For example, multi-rotor that flies for 20minutes on battery can fly for an hour on hydrogen, while a fixed-wing craft that flies for 2 hours on battery can fly for 6 on hydrogen. The systems weigh about 2 kg for 600 W, or 4 kg for 1200W, and are designed to work as range extenders with lithium-ion or lithium-polymer batteries.
Target Arm had a working display of its Tular 3.0 launch & recovery system(LARS) for small UAVs, and the company’s Jeffrey McChesney was on hand to discuss the system and its latest developments.
“The Tular is designed around not only being a LARS for both rotary and fixed-wing UAVs, but also being able to function autonomously, and perform that duty from any moving vehicle,” he explained.
“To date, we’ve successfully performed stable UAV deployments at 65 mph and captures at 35 mph – consistent with the speed limitations of rotary UAVs – in military as well as commercial use cases. We’ve had six contracts with the US military, one with BAE Systems, and others we can announce later this year for first responders, oil & gas, and other applications.
”The Tular consists of two opposing ‘beds’ of pins that gently encapsulate a UAV by closing about it from above and below. It has rubber balls on the end of each pin to compress softly instead of scratching or piercing, preventing the UAV from veering off or being blown away, as can happen with some LARS systems.
“Launch is actually the easier of the two processes, as the UAV can stabilise itself easily after release before flying away, ”McChesney added. “We’re currently at a TRL of 7 out of 9 in terms of the technology’s maturity; we’re now mainly just looking into ways of ruggedising and hardening the system, consolidating the electric subsystems and finalising our technical documentation.
“Those are all happening later this year, and we expect to release them with what we’re going to call our Tular Next-Generation, which we might alternatively brand as Tular 4.0.
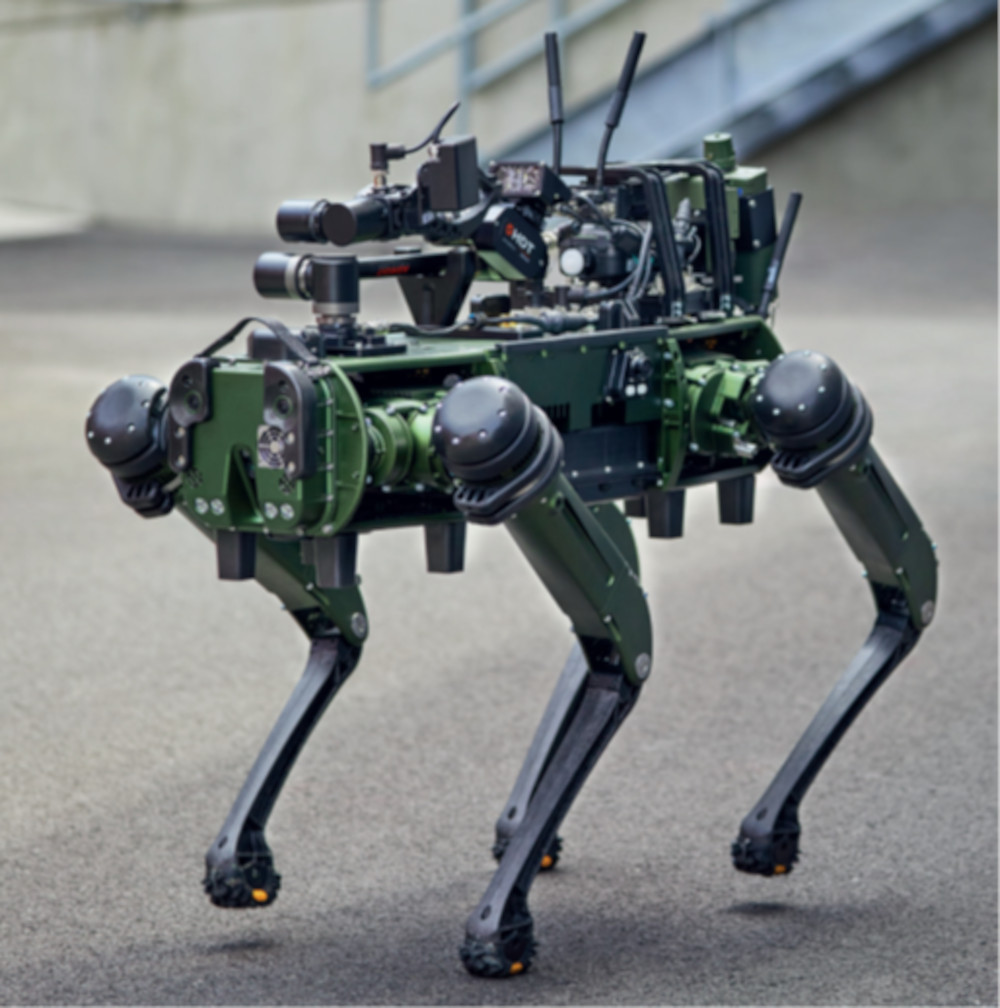
“We anticipate a lot of different kinds of users as we productionise that system, as a high-speed LARS opens up a cost-efficient means of package deliveries ,infrastructure inspections, firefighting awareness and many other applications.”
Ghost Robotics brought its Vision60 four-legged Q-UGV [quadrupedal uncrewed ground vehicle] to the exhibition floor.
“Ghost Robotics started in late 2015as a spin-out from the University of Pennsylvania,” Michael Subhan said.
“Our founders, Dr Gavin Kenneally and Dr Avik De, did their research on legged robotics and mammal locomotion, which has driven us to our commercially available solutions you can see autonomously roaming the halls – 90% of which work for defence customers in the US and allied governments, as well as large enterprise companies such as Verizon and AT&T.”
He added that defence applications for the UGV include persistent ground security for bases and other assets. For example, at the time of writing, the nearby Tyndall Air Force Base was using four Vision60s with wireless charging pads.
EOD and CBRN solutions are also available, the ability to install different sensors, cameras and manipulator arms modularly on the Vision60’s back being key to its versatility. Most noticeably, a Vision60 that was walking the expo aisles had a Lockheed Martin Indago 3 multicopter sitting on its back.
“That’s there because we’re working with Lockheed to launch and recover one of their UAVs from our robot,” Subhan explained. “Small electric UAVs don’t have great endurance, but the Vision60 has 3.5 hours of battery life, so that effectively extends the lifetime of the UAV.
“About 20-22 lb of payload capacity is optimal; users can add more but that starts to degrade the performance and lifespan between charges,” he added.
“The robot itself weighs about 100 lb when unloaded, so about 120 lb when loaded optimally, and we’ve ruggedised it to IP67, so you can submerge it in 1 m of water for 30 minutes, pull it out and it’ll still function normally. It can also walk through sand, snow, rocks and all sorts of hazardous terrain without notable issues.”
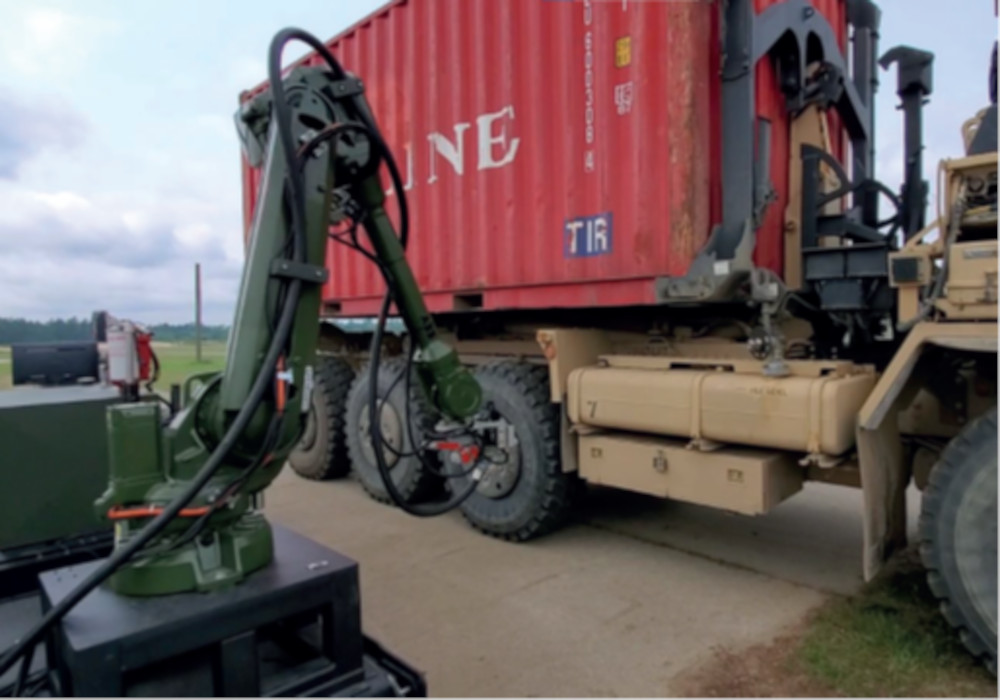
Stratom showcased its Rapid system for autonomous refuelling and recharging of uncrewed and human-operated vehicle systems. It consists broadly of a robotic arm mounting a fuel line and connector, designed with sensors and intelligence to enable the necessary pose and motion control for safe insertion and retraction of the nozzle.
“The ‘Rapid’ name relates to the high flow rates it achieves with diesel, although it can also be designed for gas, other fuels and recharging electric vehicles and other devices,” said Ross Wehner. “We just quickly change the end-effector and some line parts to suit the mission vehicle.
“We have two versions of Rapid now, one of which is for heavy trucks. They pull up to our device, and the device does a preliminary Lidar and camera scan to identify where the fuel tank or battery is, then does a secondary scan to localise the input nozzle, and then it calculates the actions needed to mate and begin pumping fuel or charge.
“That’s generally commanded via a tablet interface that can be built into the vehicle, or from the operator’s GCS if it’s an autonomous vehicle.
“The other version is for helicopters, which land by our device. Their rotors keep spinning, and the Rapid can successfully begin refuelling or recharging as the aircraft keeps oscillating a little, as is common during rough or fast landings. We’ve learned how to compensate for that mechanically and with software,”
The Rapid system can be mounted on surfaces such as fixed bases, mobile vehicle platforms and telescopic rails. Its reach and payload can be configured for user requirements.

a strong fabric with a polyurethane coating
Fuel Safe Systems displayed a range of its lightweight fuel bladders for autonomous vehicles.
“We have decades of experience in fuel bladder manufacturing for NASCAR, IndyCar and other race series, and found that these lightweight, high-strength technologies transitioned well to the aviation and UAV world,” said Dan Tynan.
“For safety, our fuel bladders are made largely from a high-strength fabric with a polyurethane coating. The coating provides fuel containment while the fabric provides puncture strength, tensile strength and general crashworthiness.”
Tynan added that for some UAVs, crashworthiness might not be needed, so the fabric can be dispensed with to save cost and weight. The polyurethane alone enables a highly elastic and user-friendly fuel bladder, particularly during integration or maintenance.
“Our lead times are around 4-5 weeks,” he said. “We try to complete the design phase back and forth with customers in about a week or two, then we go through the production process.
“We generally encourage customers to give us a CAD model of the cavity they want to put the fuel bladder in, then we take that and translate it into either flat patterns for the fabric or use the CAD model to 3D-print a vacuum-forming toolset that allows us to manufacture the bladder to the exact shape.”
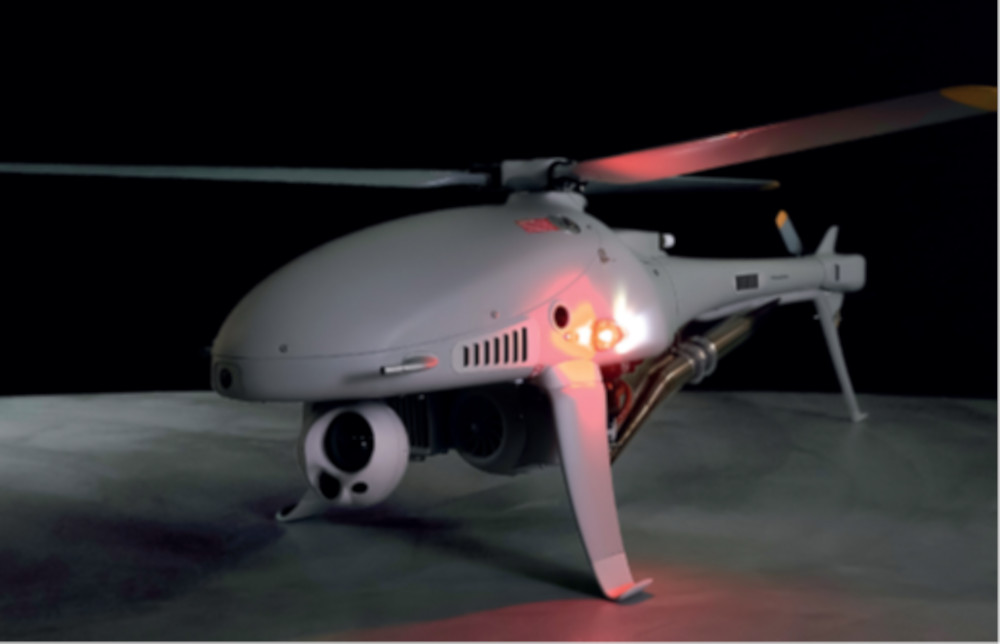
High Eye was displaying its latest helicopter UAV, the Airboxer, which runs on an 80 cc two-stroke engine to achieve an endurance of 3-4 hours depending on payload and weather conditions.
“We buy the two-cylinder, fuel-injected power unit from Zenoah before stripping it down, making our own modifications and installing some original parts for thermal management and such,” said Jesse La Porte.
“We’ve done considerable testing of the system, including FAR33 endurance testing, running it on jet fuel and designing it with IP67 ruggedness and EMI shielding to appeal to maritime users in particular.”
Notably, EMI frequencies of 1 MHz to 18 GHz and field strengths of 200 V/m have no impact on the Airboxer’s operations. The aircraft can also tolerate winds of up to 25 knots during take-off and landing, as well as moderate amounts of rain, snow and hail, with recommended operating limits in temperatures of -20 C to +45 C.
The system has a standard data link range of around 50 km, it can carry up to 7 kg of payload within a MTOW of 32 kg, and its top speed is 70 knots. With a 2 kg payload, it can cruise at 30 knots for an endurance of slightly above 3 hours.
Its powertrain uses main and tail rotor gearboxes based on over-dimensioned gearsets and titanium shafts, which are enclosed and environmentally sealed with permanent lubrication. Both the gearboxes and the rotors are validated to a TBO of 1000 hours in standard operating conditions.
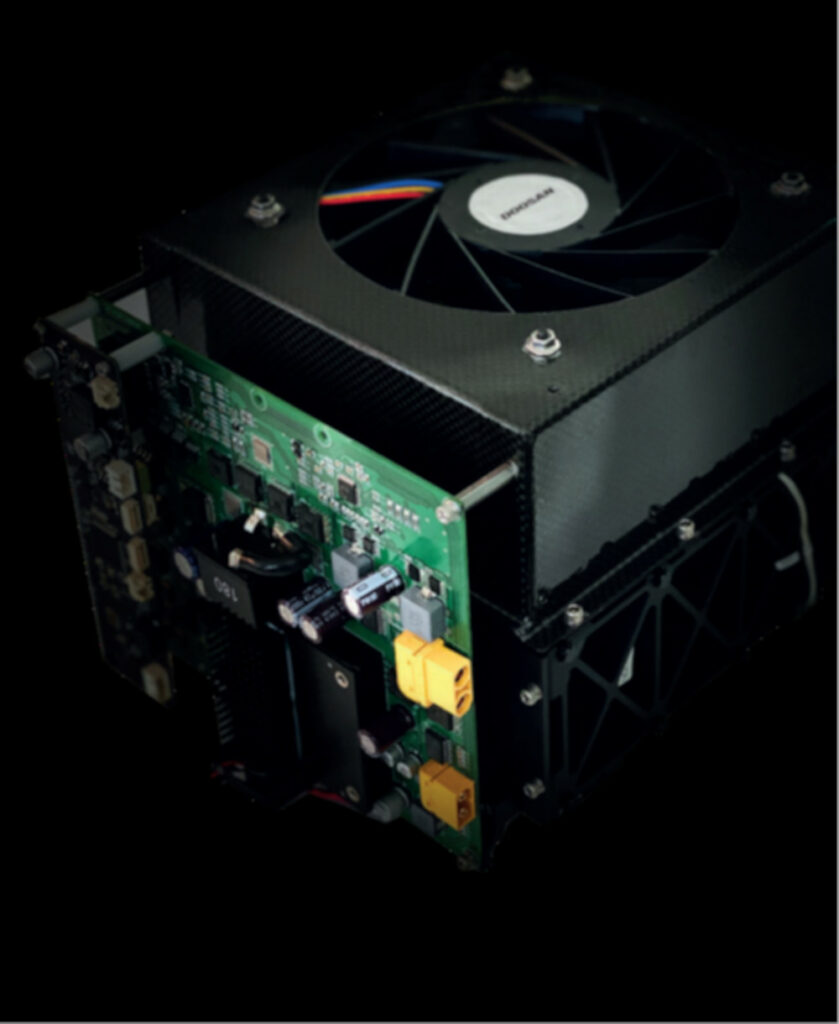
Doosan Mobility Innovations showcased many solutions in its ever-expanding range of products designed around hydrogen-electric mobility for autonomous vehicles. One of the most notable was the DM15, its most SWaP-optimised PEM fuel cell system to date. “The DM15 is a turnkey fuel cell solution with a 1.4 kW rated power output aimed principally at fixed-wing UAVs,” said Soonsuk Roh.
“In our previous fuel cell power pack solution, the DP30M2S, the hydrogen tank was included inside the product enclosure, but with the DM15 the tank is separate. That’s so that UAV manufacturers can install their hydrogen storage in their fuselage in the location and form factor that makes the most sense to them in terms of volume constraints, weight distribution and so on.” Up to 3 kW of power can be generated by the DM15 at its peak output level.
As standard, it supplies DC power over a 50 V bus, and can operate safely in temperatures from 0 C to 35 C. Its enclosure measures 260 mm wide, 250 mm long, and 170 mm in height, with a total system weight of 7.6 kg, this figure also including the weight of a 10.8 litre hydrogen tank.
As discussed on page 58, Cobra International is a composites manufacturer based in Thailand, and it attended Xponential to showcase its capabilities in strength, weight minimisation, and aesthetic qualities of its composite materials.
“Our facilities cover the full range of processes needed for users across the autonomous space, from design and development through to serial production of composite parts,” explained Danu Chotikapanich. “We can optimise for high, medium and low-end requirements depending on end-users’ budgets.
“We also offer assembly of UAV parts and airframes, allowing customers to focus more on their electrical, electronic, software or business development activities and leave the composites optimisation to us.”
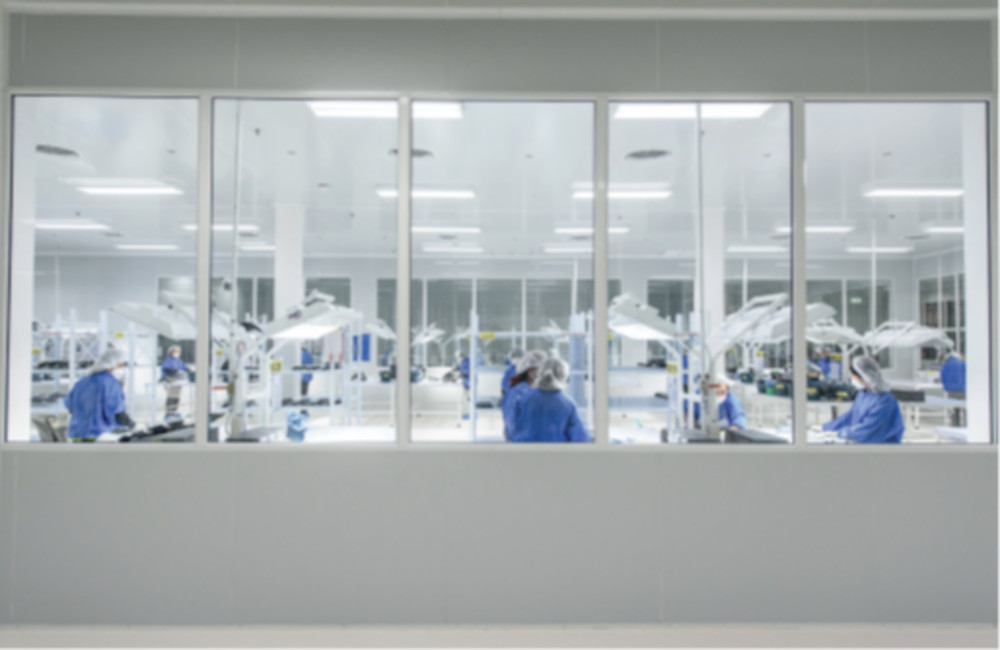
The company offers carbon fibre, fibreglass and natural fibres (sustainable fibres from sources such as banana, coconut and flax) among other reinforcement materials, along with bio-based or recyclable epoxy options as well as standard epoxy resins and other thermoplastic and thermoset matrix materials.
Its development technologies include additive printing machines and other rapid prototyping methods, and it also offers a range of finishing techniques including thermoforming, screen printing and surface polishing, along with trimming, gluing and sanding to specified tolerances.
CR Flight discussed its latest r&d for its propulsion systems that feature its patented eVector contra-rotation technology.
“On a standard motor configuration, rotational torque is imparted on fixed-wing airframes by their pusher or tractor propeller,” said Jason Emigh. “That means if too much power is run through the prop, the UAV will want to flip over, especially during take-off.
“Our coaxial single-motor systems are getting a lot of interest from the heavy-lift fixed-wing STOL UAV market, because we’re a form factor drop-in replacement for conventional e-motor propulsion units, but the counter-rotating propeller system means you don’t have that torque issue [also known as the P-factor].
“You can put full power into one of our motors instantaneously and you still get a very stable, linear runway take-off,” Emigh said. “As the UAV industry moves towards larger aircraft, the issue of excess propeller tip speeds can be resolved.
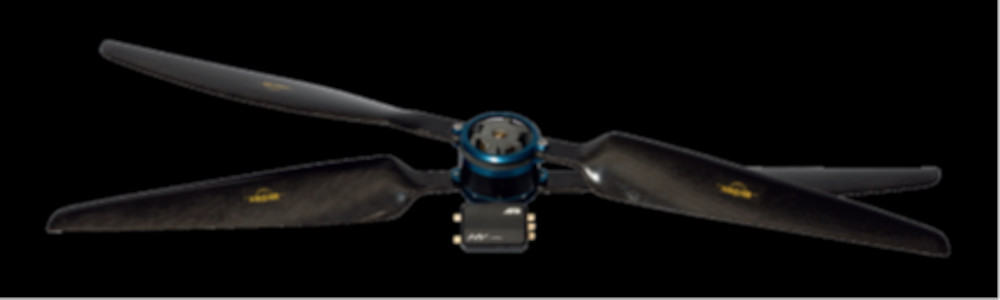
As each of our motors turns two props, we can achieve the same total rpm and power that some manufacturers want by having each propeller carry just half the rpm.”
The counter-rotation of two props and shafts from a single BLDC motor is enabled through the use of a rotary conductor that allows the ‘stator’ armature to spin freely in reaction to the rotational motion of the rotor, once it’s induced electromagnetically by the armature. This is an innovation that forms the basis for the company’s eVector technology.
Advanced Innovative Engineering, last featured in issue 7 (April/May 2016) for its 225CS Wankel rotary engine, attended Xponential to display the latest iterations of its UAV power units and discuss how they have been updated over 6 years of r&d.
“Both our 225CS and 80S engines have been optimised for extremely high power density, very little vibration and multi-fuel efficiency for UAVs in shipborne and coastal operations,” said Alexander Vaughn. “We’ve also worked closely on better integrating the ancillary systems to run more smoothly and efficiently off the engine, and we’re even starting to look into burning hydrogen for zero-emissions propulsion.”
The 225CS weighs 10 kg and outputs up to 30 kW, while the 80S weighs 5 kg and produces a peak power of 9 kW.
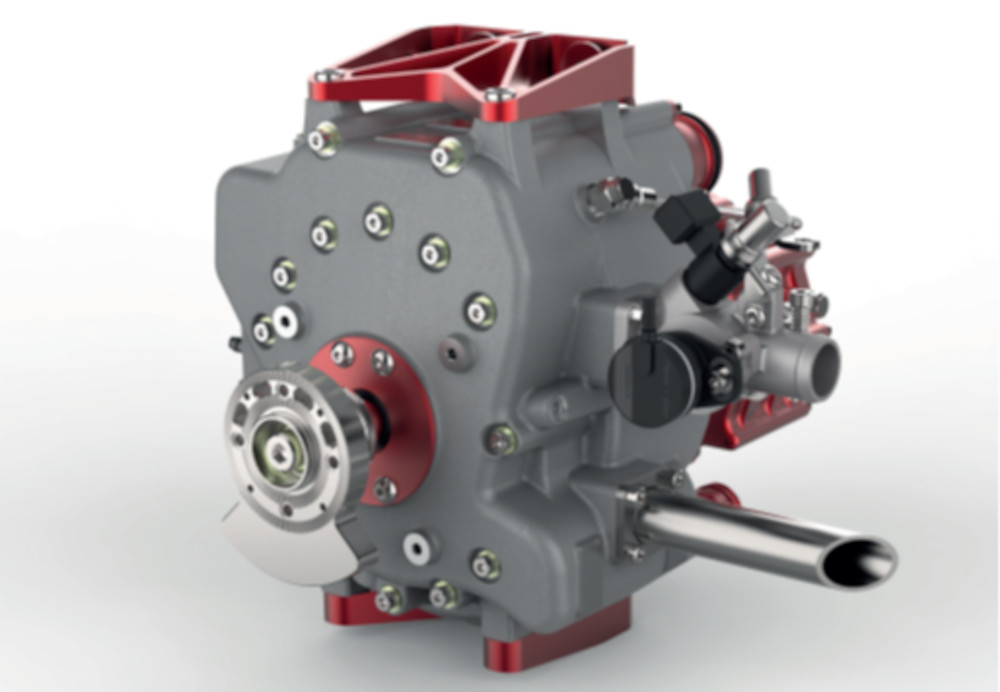
Both engines integrate the company’s patented SPARCS (Self-Pressurising Air Rotor Cooling System) technology, which uses blow-by gases captured via side vents as a cooling medium.
That enables efficient thermal management of the rotor as well as recapturing oil lost during compression, and preventing the high oil consumption and related emissions typical of some Wankel configurations. The system’s heat exchanger can be mounted outside the engine or inside the rotor housing, with the latter configuration patented as Compact SPARCS.
Amprius exhibited the latest products in its range of highly SWaP optimised lithium-ion battery cells, which have been developed around a patented silicon nanowire anode technology to achieve a range of useful performance parameters.
“Silicon nanowire has a higher capacity than conventional graphite anodes – 10 times higher in fact,” explained Daniel Seo.
“That means we can use much less anode material than in conventional cells, which reduces the weight of our cells without lowering their energy capacity. In general, that equates to higher energy density – a mission-critical quality for UAVs.”
He added that the high surface area of nanowires can also be used in their designs to contribute to a higher power charge and discharge capability (with lower chance of lithium dendrite build ups). That can be vital for sensors, processing, propulsion and other key functions of many autonomous systems.
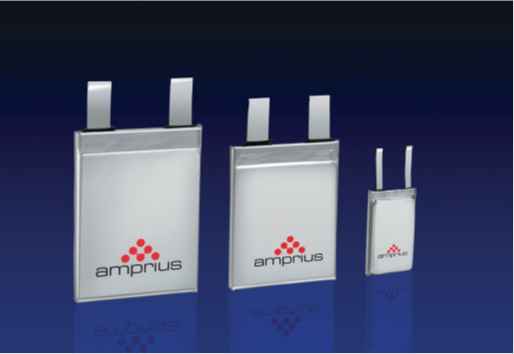
Among the company’s product portfolio are a high energy density cell that weighs 46.5 g and contains up to 21 Wh and 5.8 Ah. It charges and discharges at a constant rate of 1.16 A at 5C, between 2.75 and 4.42 V.
Amprius also has a high-power fast charge cell that carries up to 10 Wh and 2.75 Ah, charges at a constant rate of 2.75 A (1C) and discharges at 8.25 A (3C) up to a peak continuous discharge rate of 12.5 A (5C), while weighing 28 g. Both cells are assembled with lithium cobalt oxide cathodes, while the company’s 44 g high energy density power cell uses an NMC cathode to achieve a 15.6 A maximum continuous discharge (at 3C) from its 18 Wh energy store.
UPCOMING EVENTS
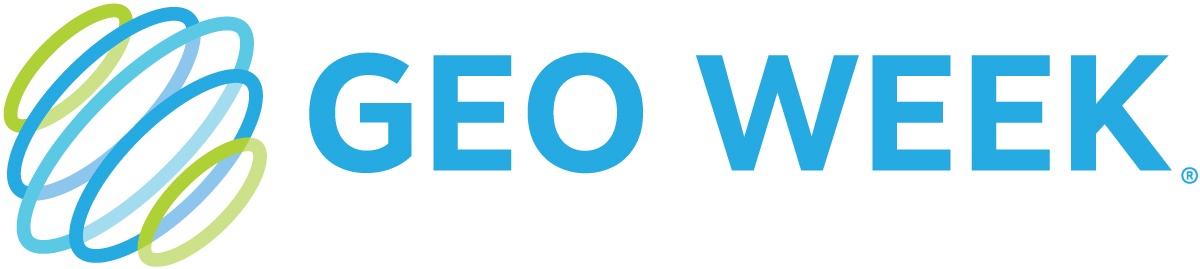
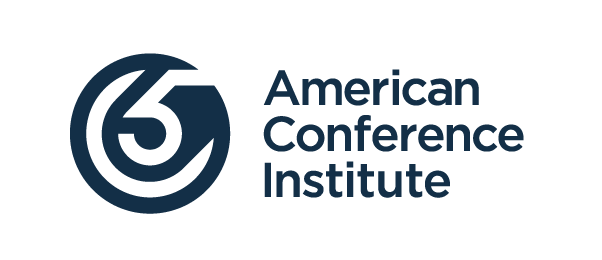
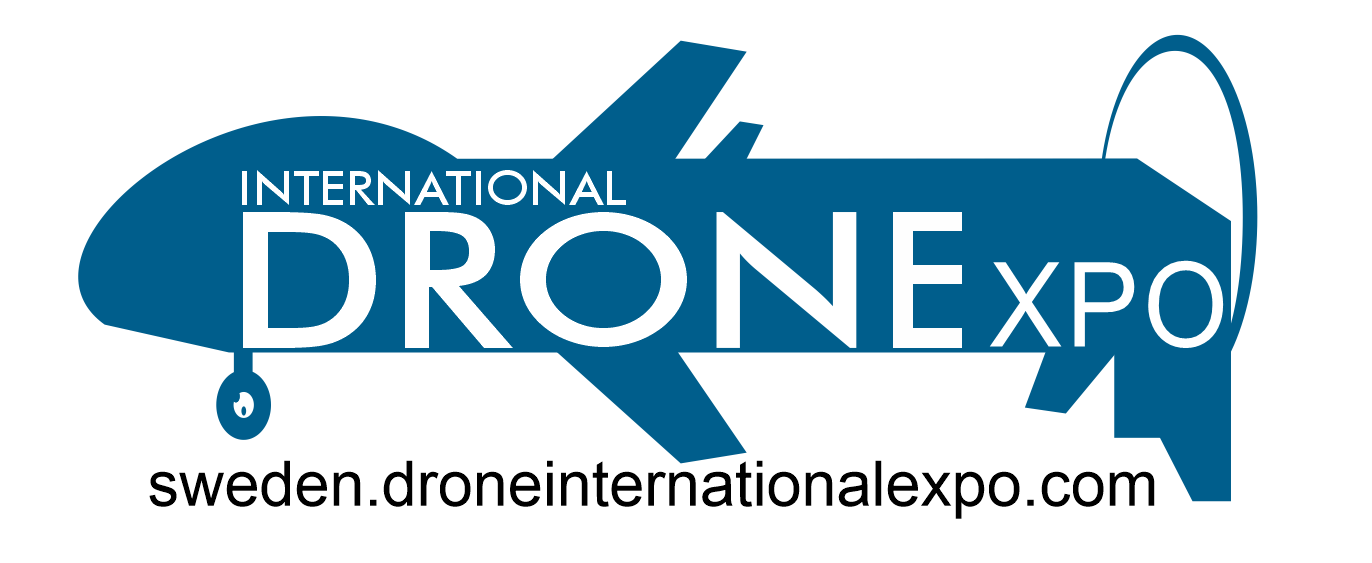
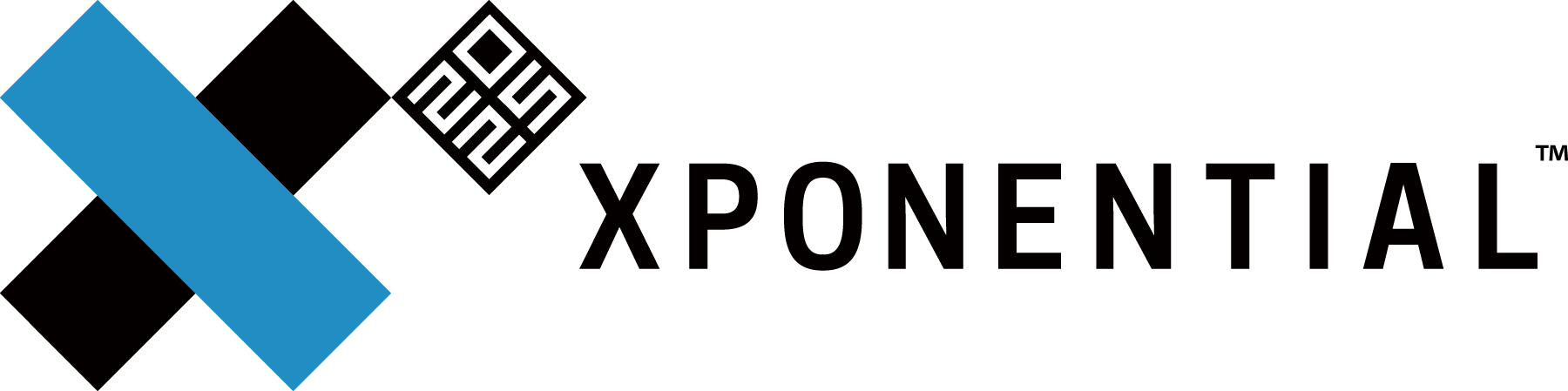
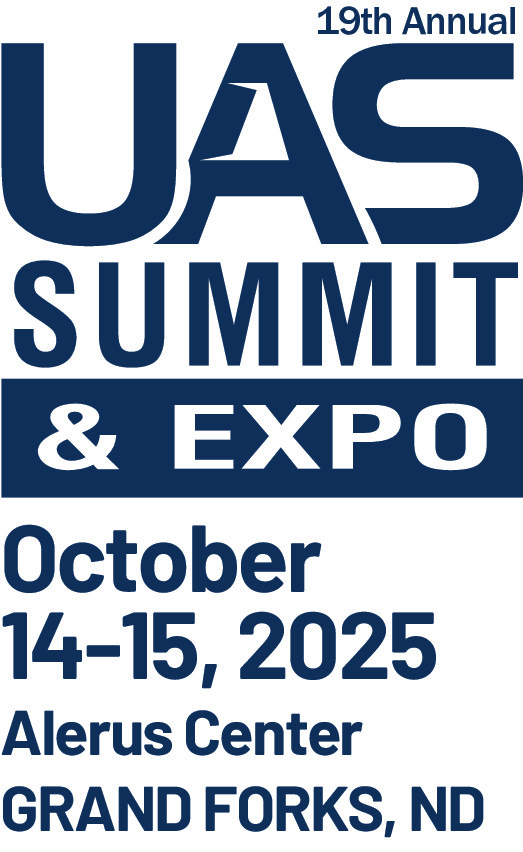

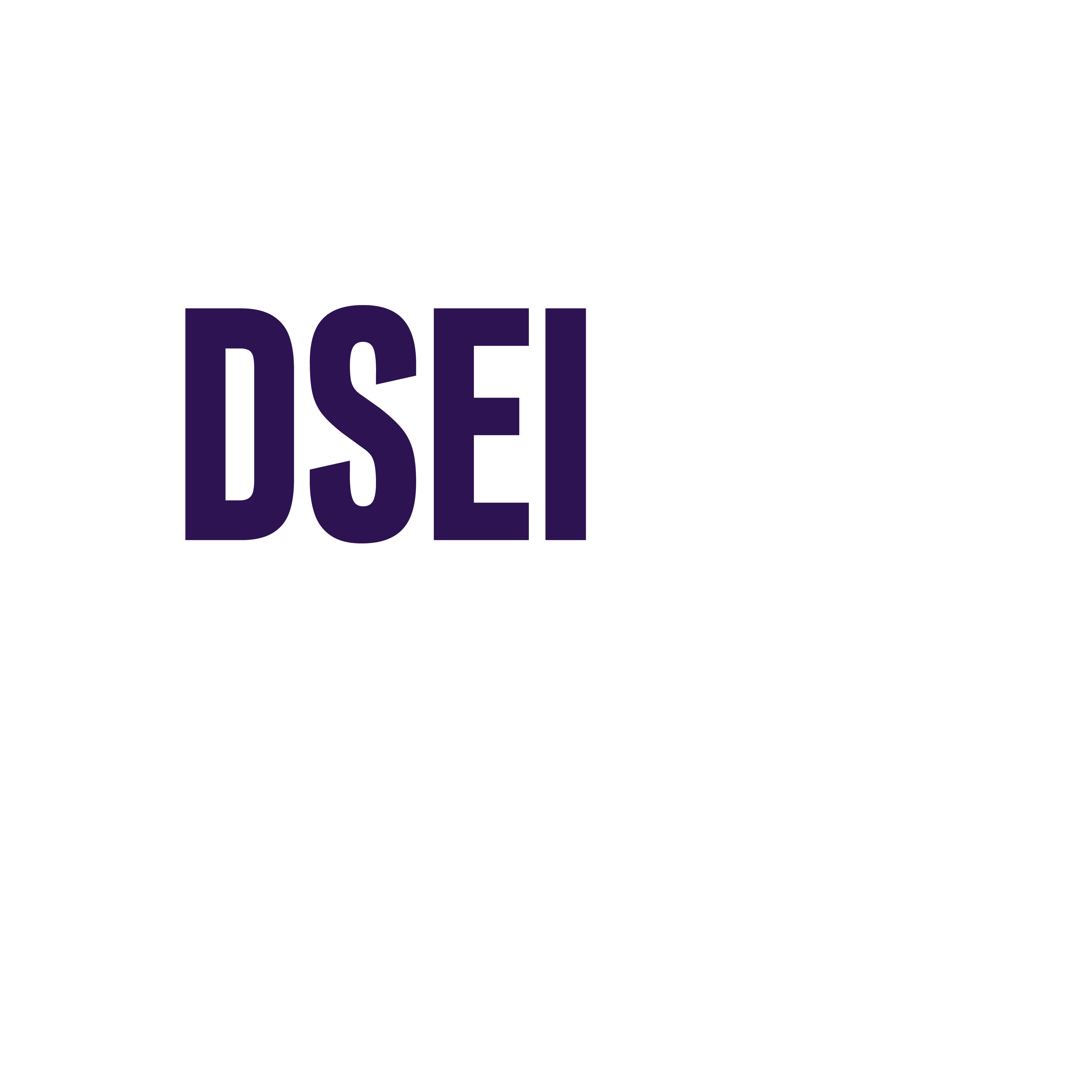
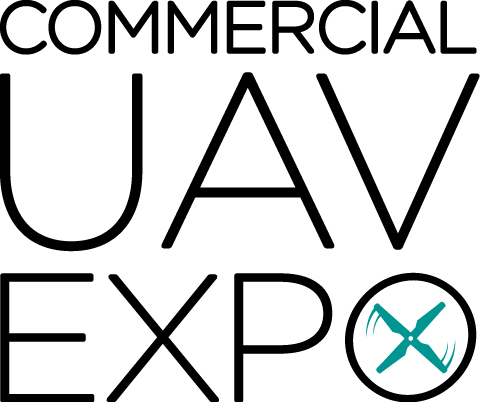
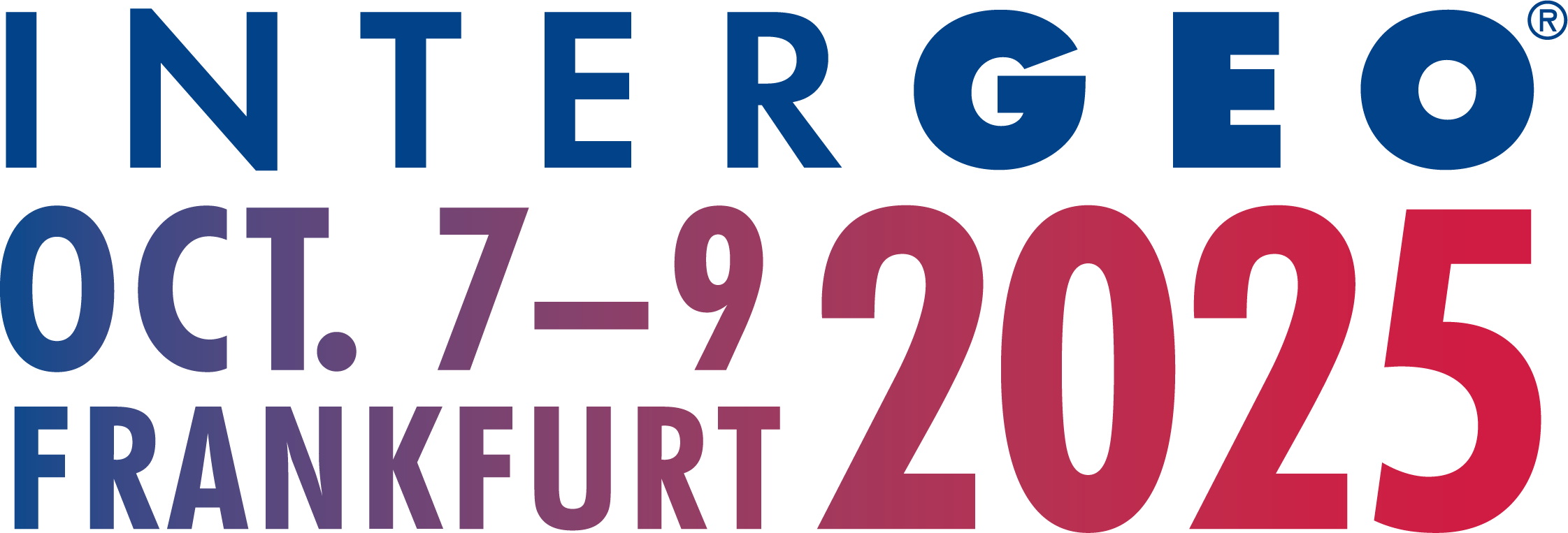
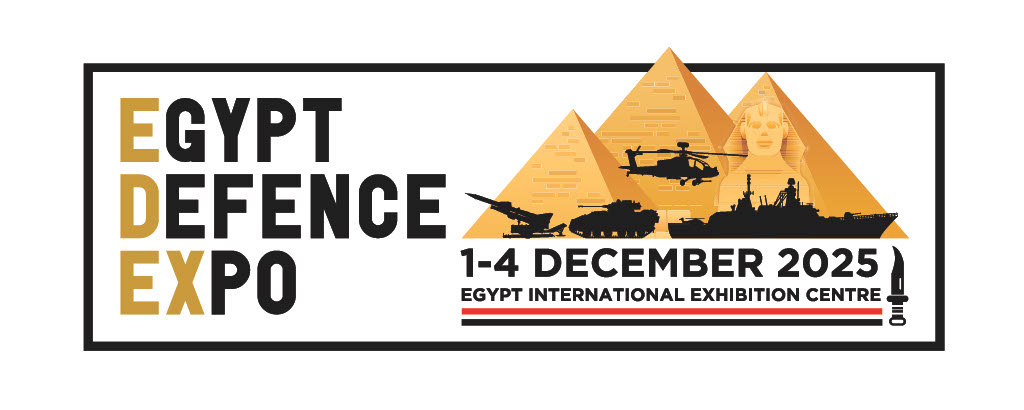
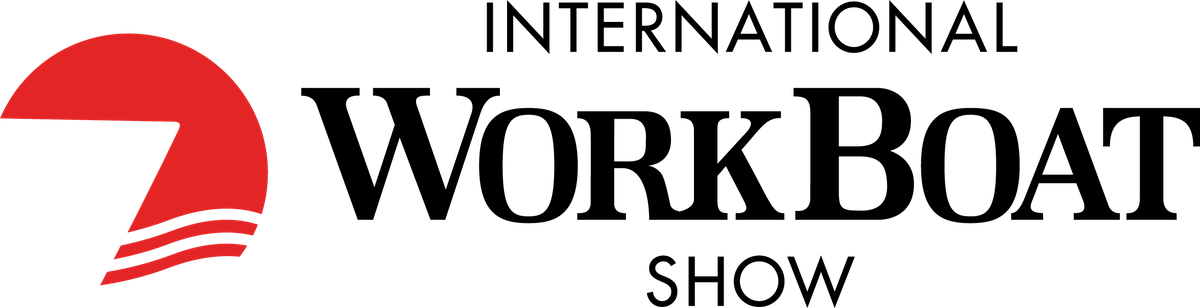